MITSUBISHI COLT 2006 Service Repair Manual
Manufacturer: MITSUBISHI, Model Year: 2006, Model line: COLT, Model: MITSUBISHI COLT 2006Pages: 364, PDF Size: 11.65 MB
Page 131 of 364
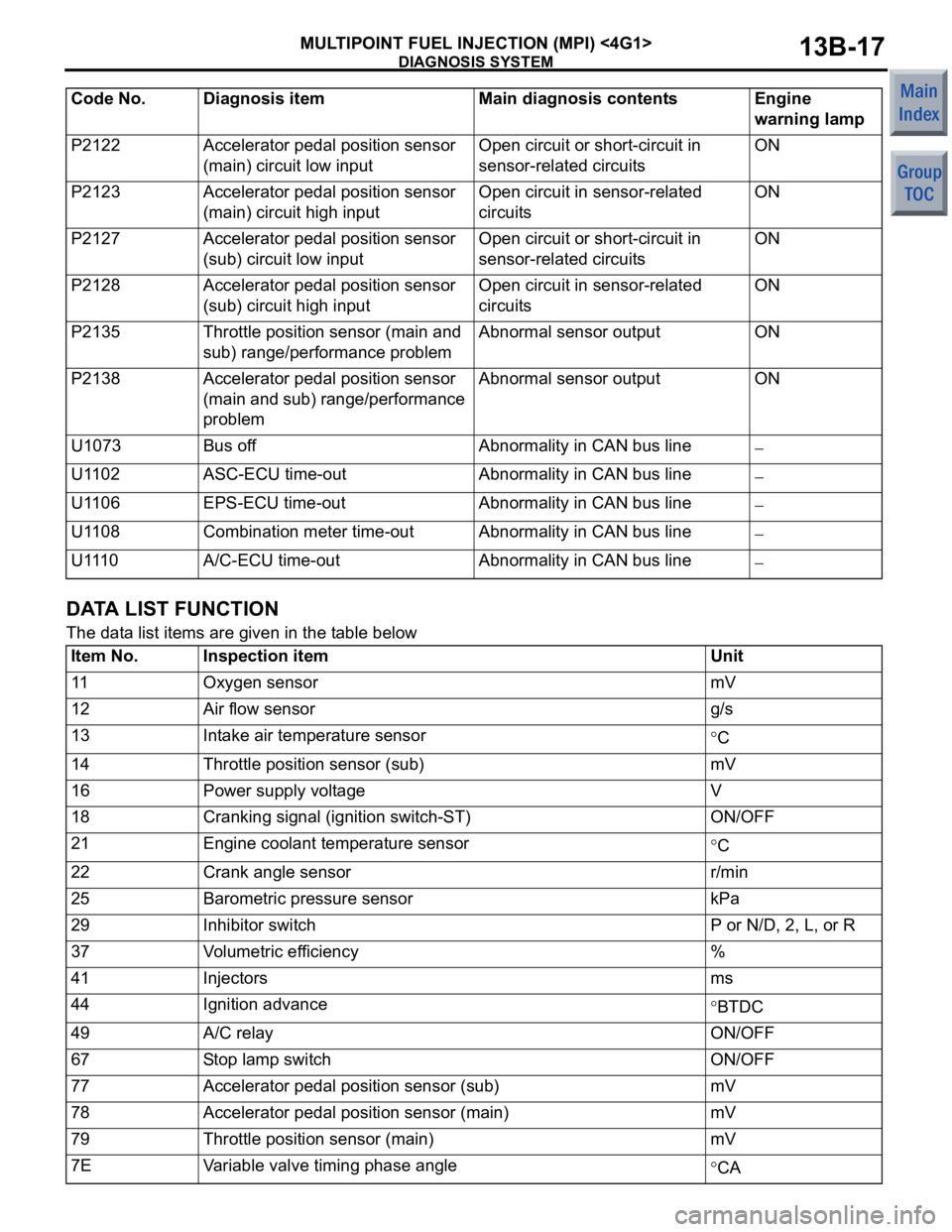
DIAGNOSIS SYSTEM
MULTIPOINT FUEL INJECTION (MPI) <4G1>13B-17
DATA LIST FUNCTION
The data list items are given in the table below
P2122Accelerator pedal position sensor
(main) circuit low inputOpen circuit or short-circuit in
sensor-related circuitsON
P2123Accelerator pedal position sensor
(main) circuit high inputOpen circuit in sensor-related
circuitsON
P2127Accelerator pedal position sensor
(sub) circuit low inputOpen circuit or short-circuit in
sensor-related circuitsON
P2128Accelerator pedal position sensor
(sub) circuit high inputOpen circuit in sensor-related
circuitsON
P2135Throttle position sensor (main and
sub) range/performance problemAbnormal sensor outputON
P2138Accelerator pedal position sensor
(main and sub) range/performance
problemAbnormal sensor outputON
U1073Bus offAbnormality in CAN bus line−
U1102ASC-ECU time-outAbnormality in CAN bus line−
U1106EPS-ECU time-outAbnormality in CAN bus line−
U1108Combination meter time-outAbnormality in CAN bus line−
U 111 0A/C-ECU time-outAbnormality in CAN bus line−
Code No. Diagnosis item Main diagnosis contents Engine
warning lamp
Item No.Inspection itemUnit
11Oxygen sensormV
12Air flow sensorg/s
13Intake air temperature sensor°C
14Throttle position sensor (sub)mV
16Power supply voltageV
18Cranking signal (ignition switch-ST)ON/OFF
21Engine coolant temperature sensor°C
22Crank angle sensorr/min
25Barometric pressure sensorkPa
29Inhibitor switchP or N/D, 2, L, or R
37Volumetric efficiency%
41Injectorsms
44Ignition advance°BTDC
49A/C relayON/OFF
67Stop lamp switchON/OFF
77Accelerator pedal position sensor (sub)mV
78Accelerator pedal position sensor (main)mV
79Throttle position sensor (main)mV
7EVariable valve timing phase angle°CA
Page 132 of 364
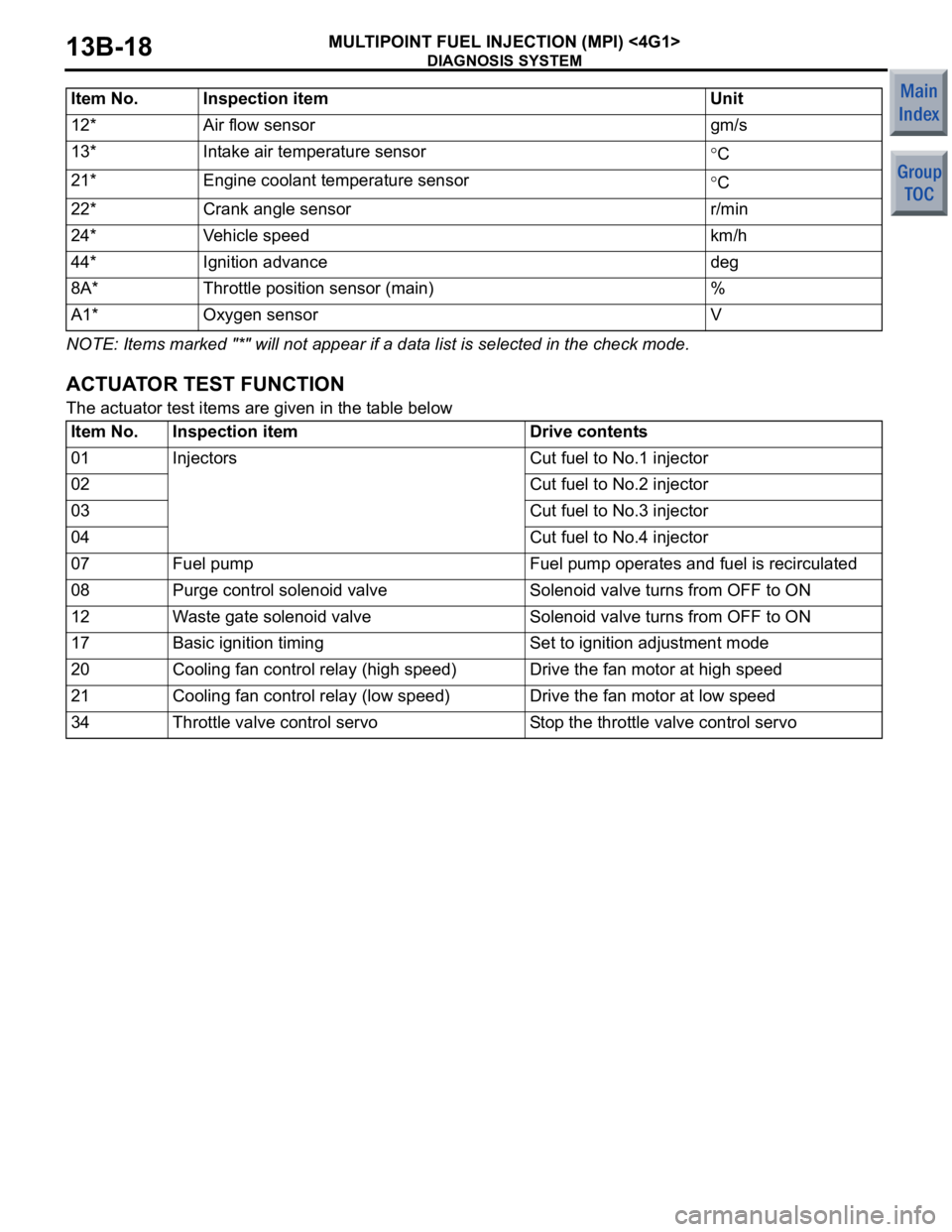
DIAGNOSIS SYSTEM
MULTIPOINT FUEL INJECTION (MPI) <4G1>13B-18
NOTE: Items marked "*" will not appear if a data list is selected in the check mode.
ACTUATOR TEST FUNCTION
The actuator test items are given in the table below
Item No.Inspection itemDrive contents
01InjectorsCut fuel to No.1 injector
02Cut fuel to No.2 injector
03Cut fuel to No.3 injector
04Cut fuel to No.4 injector
07Fuel pumpFuel pump operates and fuel is recirculated
08Purge control solenoid valveSolenoid valve turns from OFF to ON
12Waste gate solenoid valveSolenoid valve turns from OFF to ON
17Basic ignition timingSet to ignition adjustment mode
20Cooling fan control relay (high speed)Drive the fan motor at high speed
21Cooling fan control relay (low speed)Drive the fan motor at low speed
34Throttle valve control servoStop the throttle valve control servo
12*Air flow sensorgm/s
13*Intake air temperature sensor°C
21*Engine coolant temperature sensor°C
22*Crank angle sensorr/min
24*Vehicle speedkm/h
44*Ignition advancedeg
8A*Throttle position sensor (main)%
A1*Oxygen sensorV
Item No. Inspection item Unit
Page 133 of 364
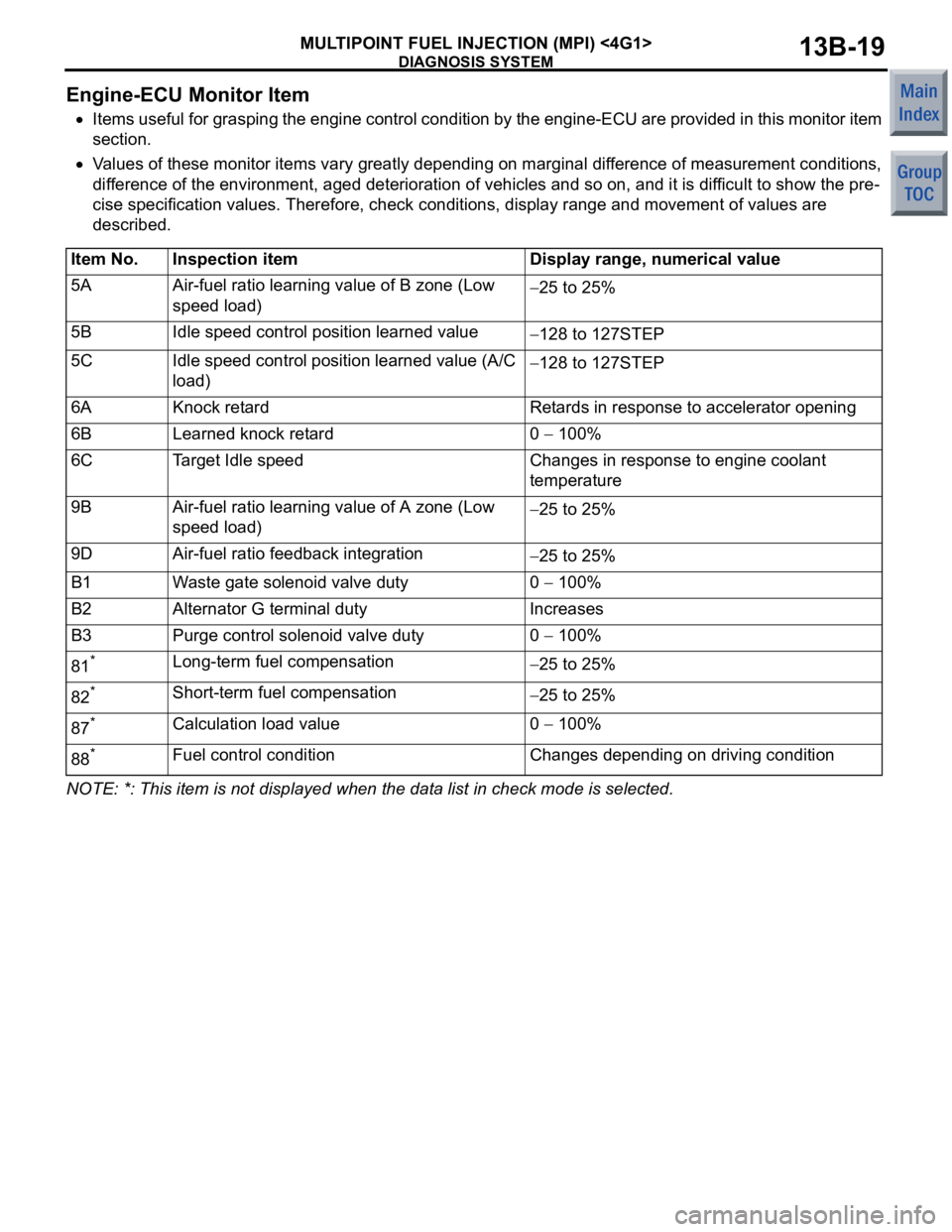
DIAGNOSIS SYSTEM
MULTIPOINT FUEL INJECTION (MPI) <4G1>13B-19
Engine-ECU Monitor Item
•Items useful for grasping the engine control condition by the engine-ECU are provided in this monitor item
section.
•Values of these monitor items vary greatly depending on marginal difference of measurement conditions,
difference of the environment, aged deterioration of vehicl es and so on, and it is difficult to show the pre
-
cise specification values. Therefore, check conditions, display range and movement of values are
described.
Item No.Inspection itemDisplay range, numerical value
5AAir-fuel ratio learning value of B zone (Low
speed load)−25 to 25%
5BIdle speed control position learned value−128 to 127STEP
5CIdle speed control position learned value (A/C
load)−128 to 127STEP
6AKnock retardRetards in response to accelerator opening
6BLearned knock retard0 − 100%
6CTarget Idle speedChanges in response to engine coolant
temperature
9BAir-fuel ratio learning value of A zone (Low
speed load)−25 to 25%
9DAir-fuel ratio feedback integration−25 to 25%
B1Waste gate solenoid valve duty0 − 100%
B2Alternator G terminal dutyIncreases
B3Purge control solenoid valve duty0 − 100%
81*Long-term fuel compensation−25 to 25%
82*Short-term fuel compensation−25 to 25%
87*Calculation load value0 − 100%
88*Fuel control conditionChanges depending on driving condition
NOTE: *: This item is not displayed when the data list in check mode is selected.
Page 134 of 364
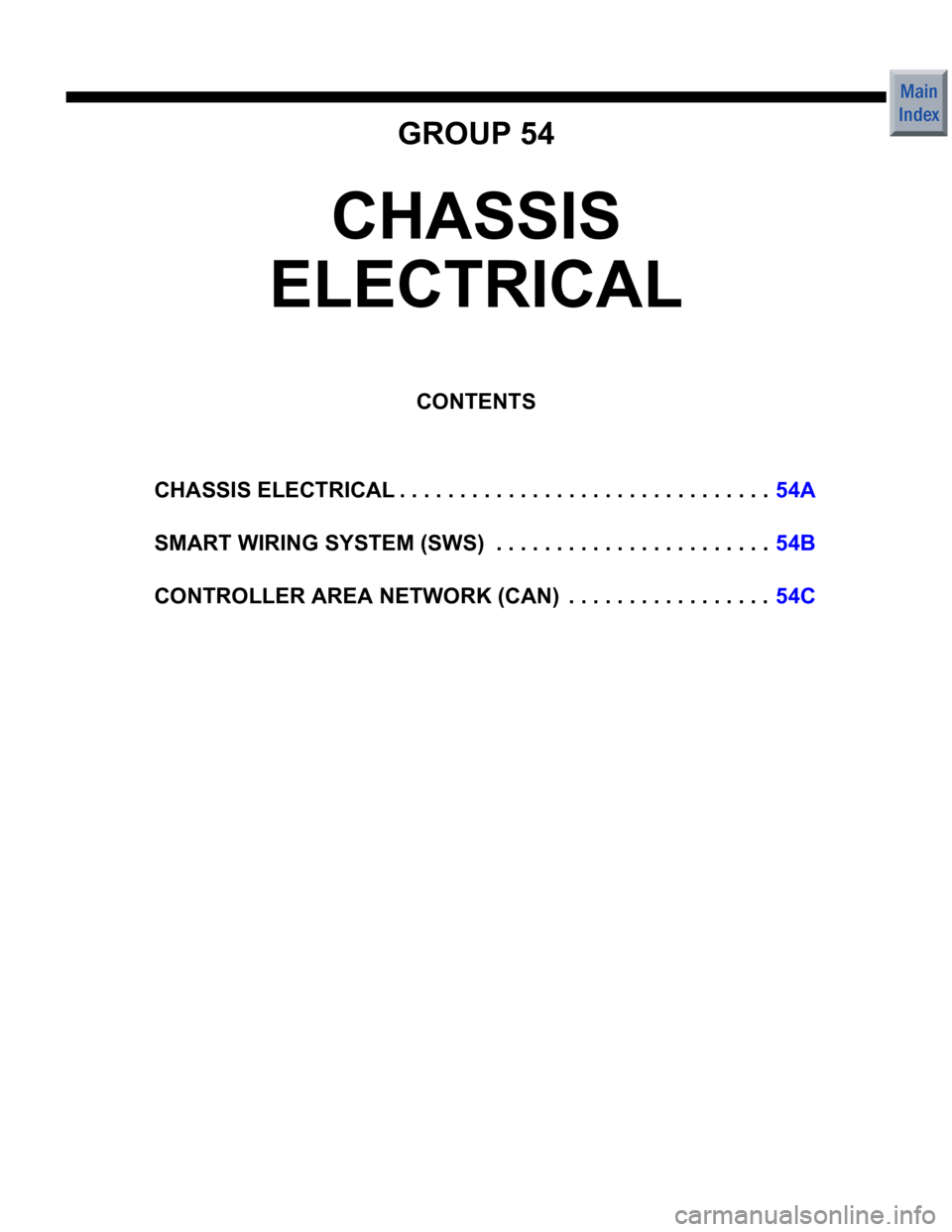
GROUP 54
CHASSIS
ELECTRICAL
CONTENTS
CHASSIS ELECTRICAL . . . . . . . . . . . . . . . . . . . . . . . . . . . . . . .54A
SMART WIRING SYSTEM (SWS) . . . . . . . . . . . . . . . . . . . . . . .54B
CONTROLLER AREA NETWORK (CAN) . . . . . . . . . . . . . . . . .54C
Page 135 of 364
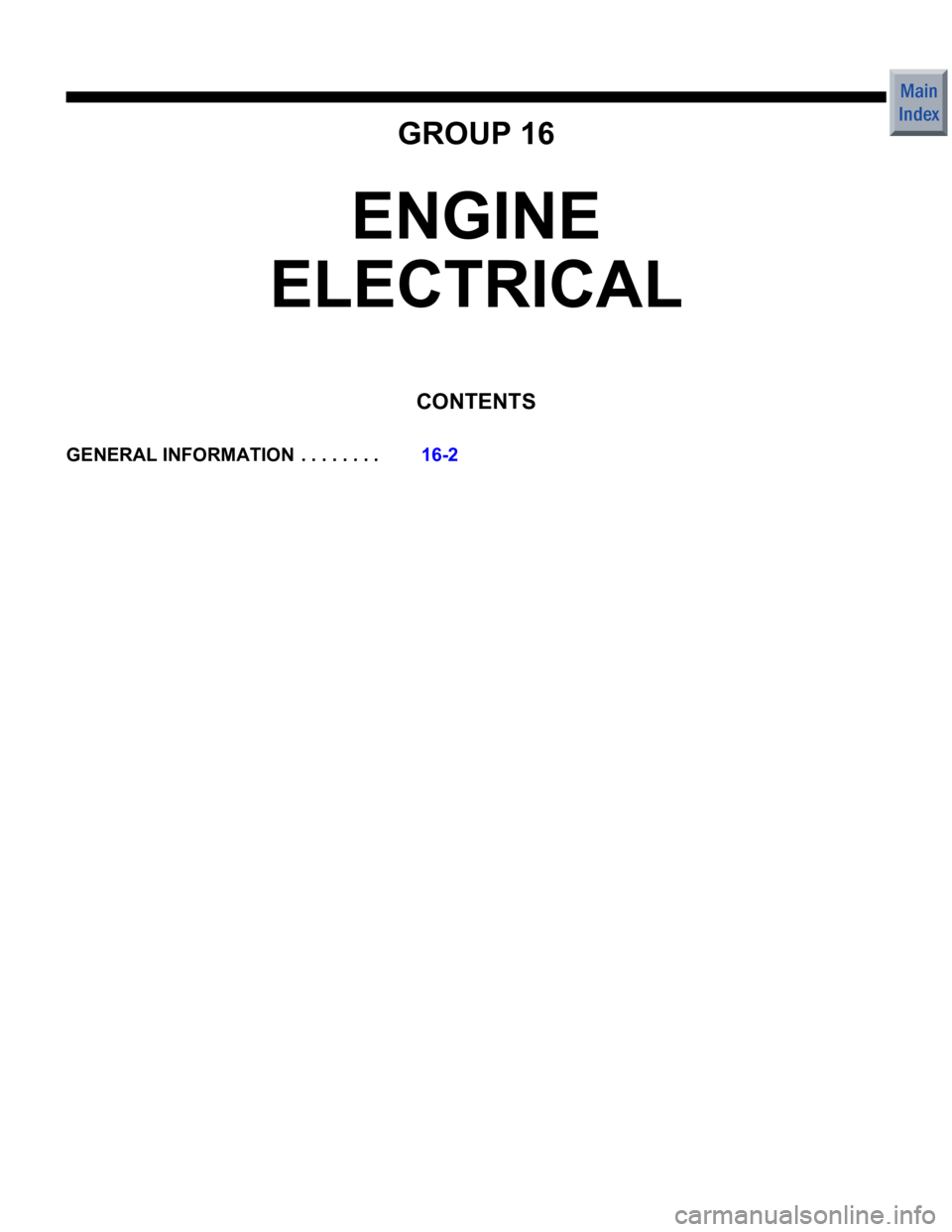
GROUP 16
ENGINE
ELECTRICAL
CONTENTS
GENERAL INFORMATIO N . . . . . . . .16-2
Page 136 of 364
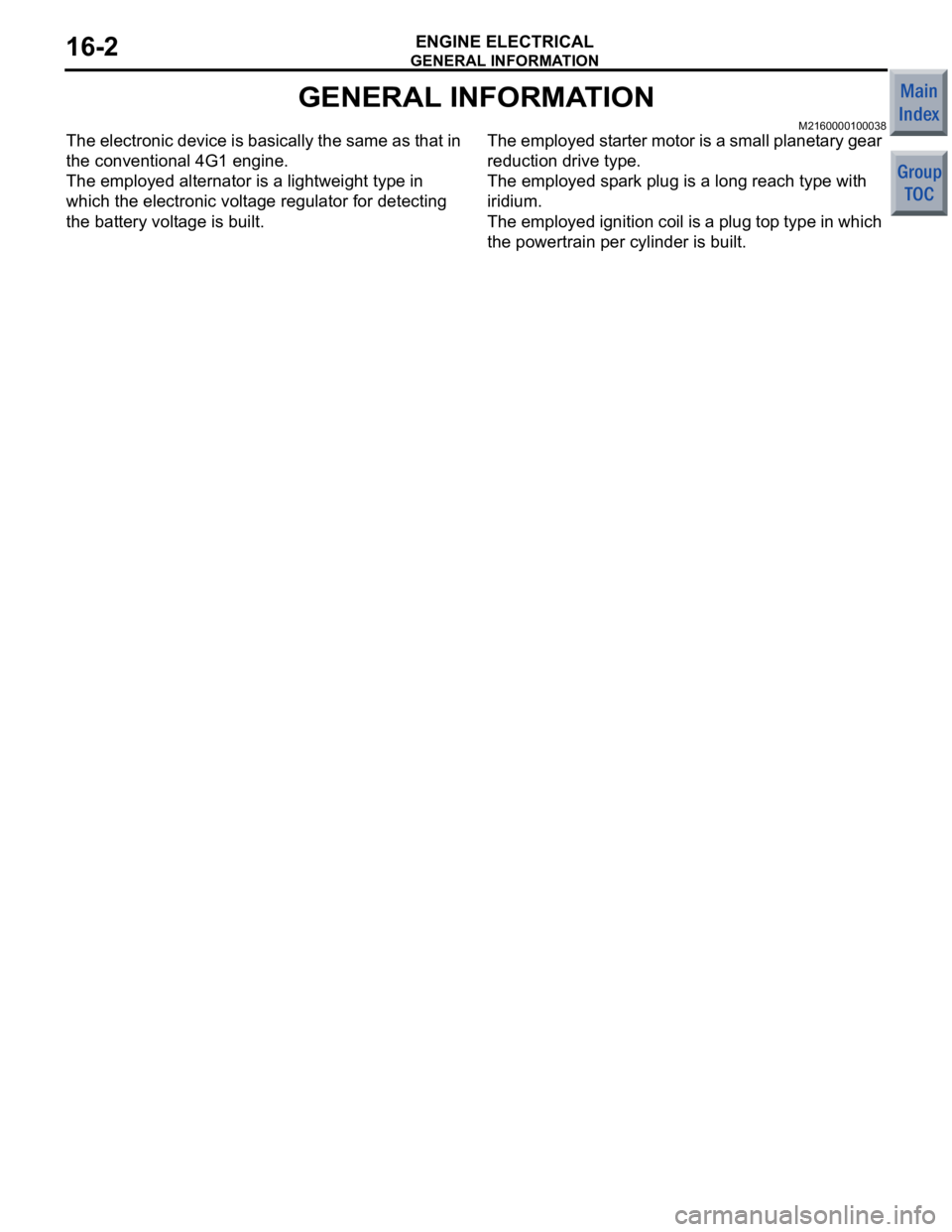
GENERAL INFORMATION
ENGINE ELECTRICAL16-2
GENERAL INFORMATION
M2160000100038
The electronic device is basically the same as that in
the conventional 4G1 engine.
The employed alternator is a lightweight type in
which the electronic voltage regulator for detecting
the battery voltage is built.
The employed starter motor is a small planetary gear
reduction drive type.
The employed spark plug is a long reach type with
iridium.
The employed ignition coil is a plug top type in which
the powertrain per cylinder is built.
Page 137 of 364
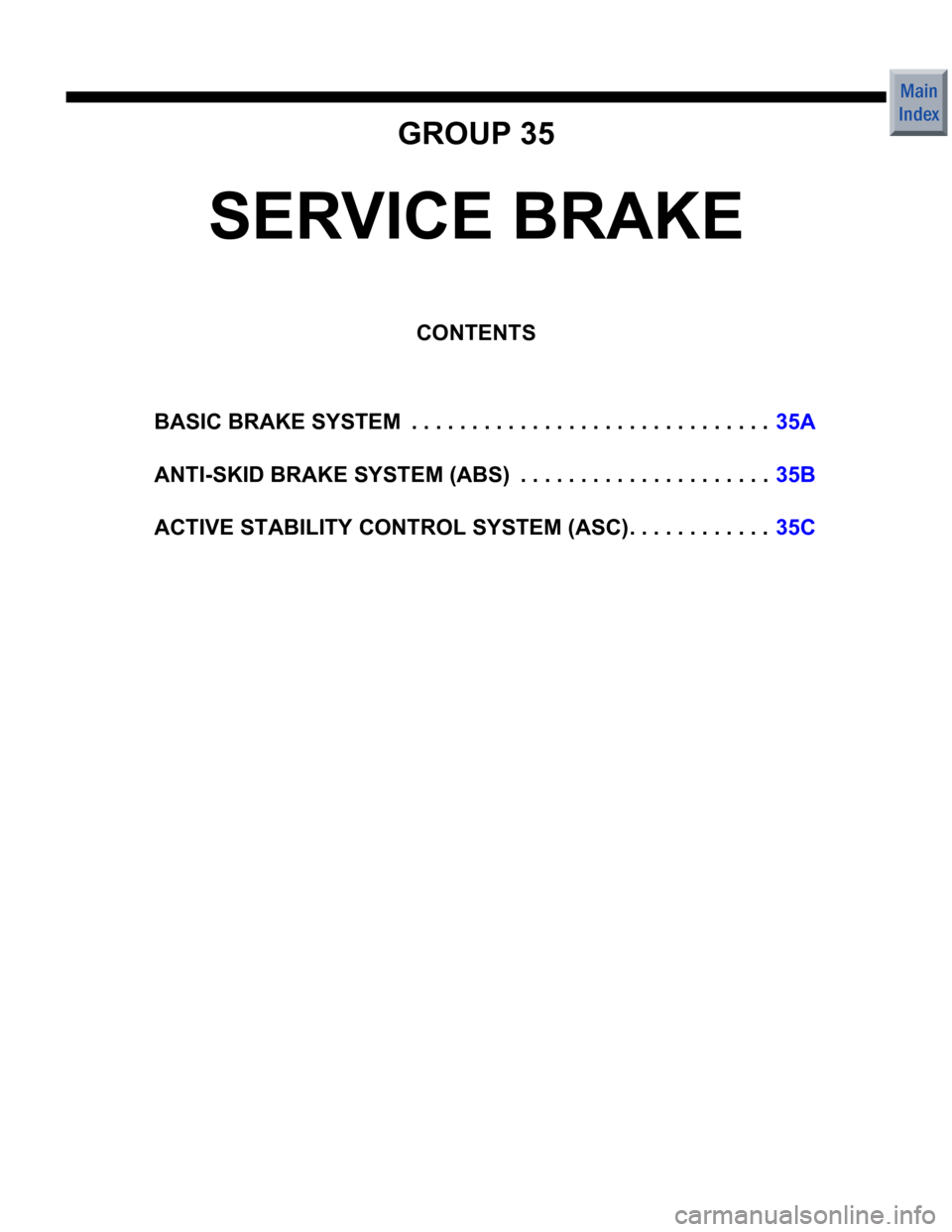
GROUP 35
SERVICE BRAKE
CONTENTS
BASIC BRAKE SYSTEM . . . . . . . . . . . . . . . . . . . . . . . . . . . . . .35A
ANTI-SKID BRAKE SYSTEM (ABS) . . . . . . . . . . . . . . . . . . . . .35B
ACTIVE STABILITY CONTROL SYSTEM (ASC). . . . . . . . . . . .35C
Page 138 of 364
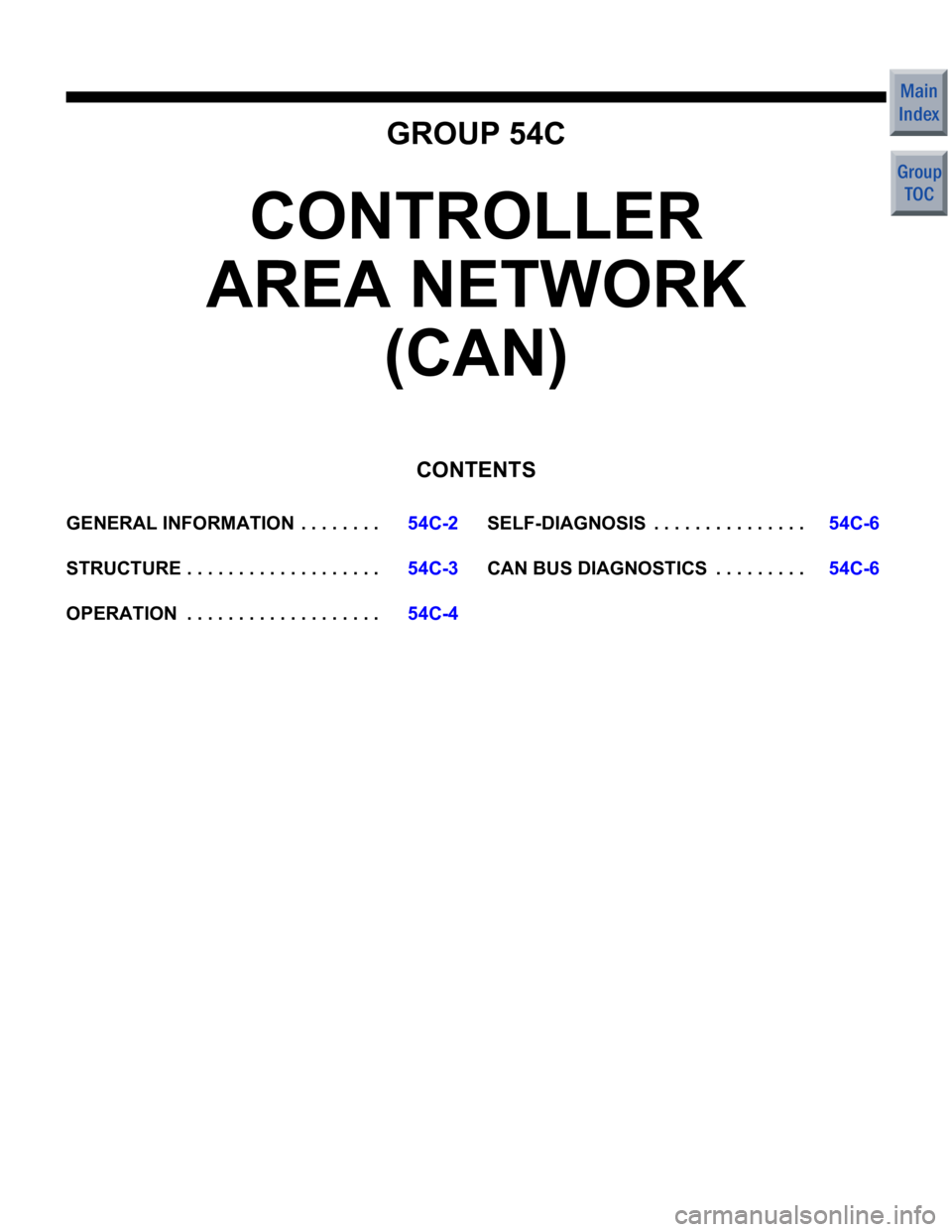
GROUP 54C
CONTROLLER
AREA NETWORK
(CAN)
CONTENTS
GENERAL INFORMATIO N . . . . . . . .54C-2
STRUCTURE . . . . . . . . . . . . . . . . . . .54C-3
OPERATION . . . . . . . . . . . . . . . . . . .54C-4
SELF-DIAGNOSIS . . . . . . . . . . . . . . .54C-6
CAN BUS DIAGNOSTICS . . . . . . . . .54C-6
Page 139 of 364
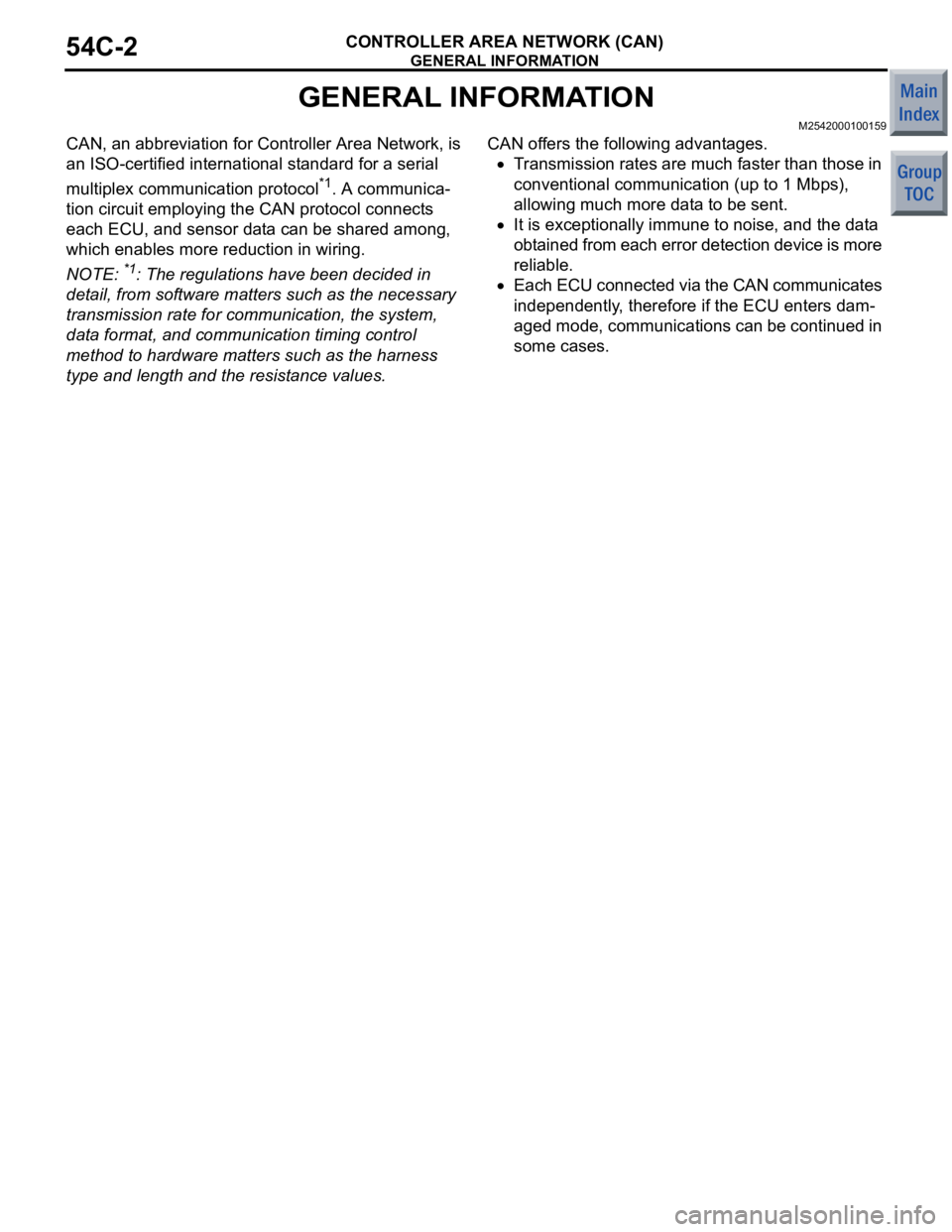
GENERAL INFORMATION
CONTROLLER AREA NETWORK (CAN)54C-2
GENERAL INFORMATION
M2542000100159
CAN, an abbreviation for Controller Area Network, is
an ISO-certified international standard for a serial
multiplex communication protocol
*1. A communica-
tion circuit employing the CAN protocol connects
each ECU, and sensor data can be shared among,
which enables more reduction in wiring.
NOTE: *1: The regulations have been decided in
detail, from software matters such as the necessary
transmission rate for communication, the system,
data format, and communication timing control
method to hardware matters such as the harness
type and length and the resistance values.
CAN offers the following advantages.
•Transmission rates are much faster than those in
conventional communication (up to 1 Mbps),
allowing much more data to be sent.
•It is exceptionally immune to noise, and the data
obtained from each error detection device is more
reliable.
•Each ECU connected via the CAN communicates
independently, therefore if the ECU enters dam
-
aged mode, communications can be continued in
some cases.
Page 140 of 364
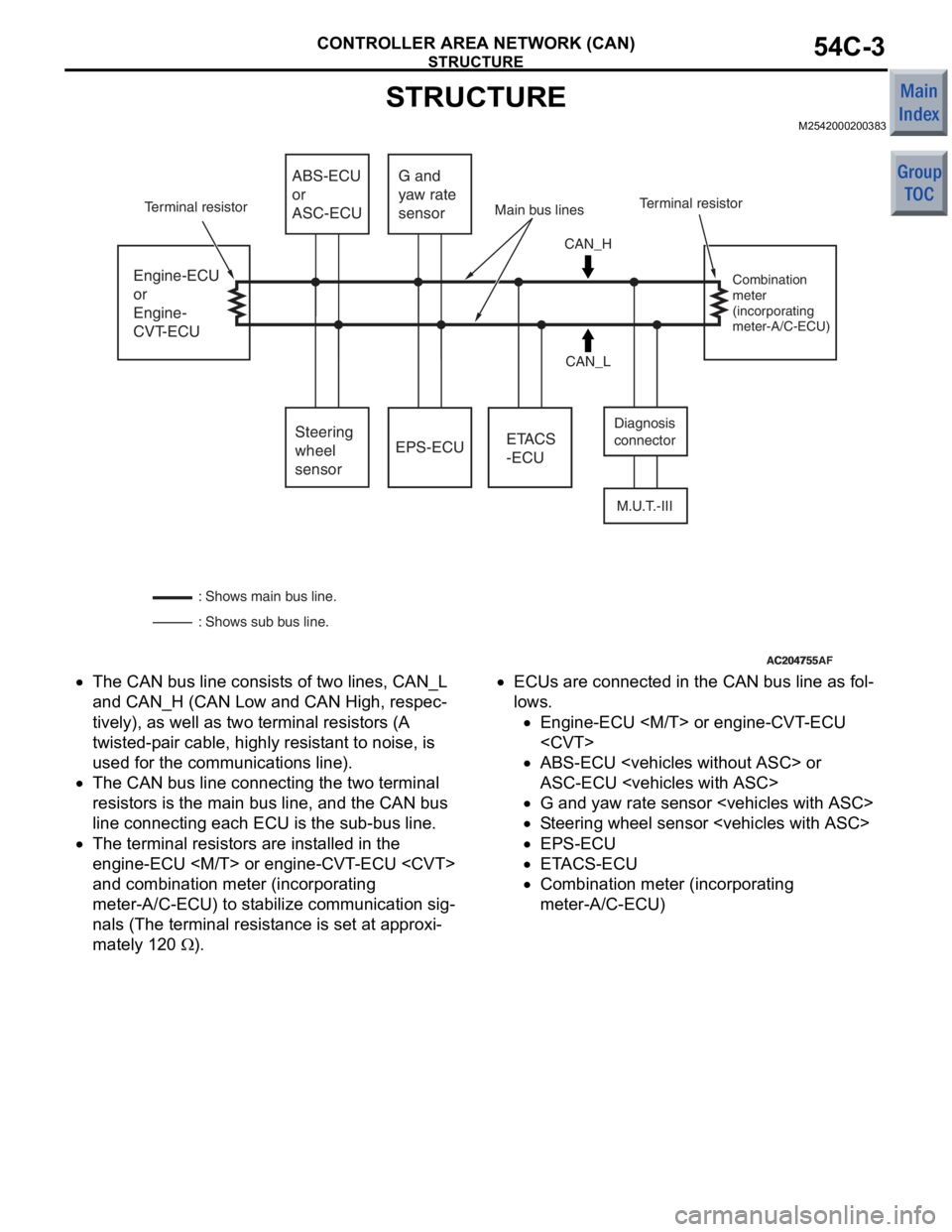
STRUCTURE
CONTROLLER AREA NETWORK (CAN)54C-3
STRUCTURE
M2542000200383
AC204755AC204755AF
Engine-ECU
or
Engine-
CVT-ECUEPS-ECU
M.U.T.-III
ETACS
-ECU
ABS-ECU
or
ASC-ECU
Steering
wheel
sensor G and
yaw rate
sensor
CAN_H
CAN_L Diagnosis
connector
Combination
meter
(incorporating
meter-A/C-ECU)
: Shows sub bus line. : Shows main bus line. Terminal resistor
Terminal resistor Main bus lines
•The CAN bu s line consist s of two lines, CAN_L
and
CAN_H (CAN Low and CAN Hig h , respec
-
tively), as well as two terminal re sistors (A
twisted-p
a ir cable, highly resist ant to noise, is
used for
the communicatio n s line) .
•The CAN bu s line connectin g the two terminal
resist
ors is th e main bus line, an d the CAN bus
line connecting
each ECU is th e su b-bus lin e.
•The terminal resistors are inst alled in the
eng
ine-ECU
and
combin ation mete r (incorpora t ing
meter-A/C-ECU) to st
abi lize co mmunicatio n sig
-
nals (The terminal resist ance is se t at ap proxi-
mately 120 Ω).
•ECUs are conn ected in th e CAN bus line as fo l-
lows.
•En gine -ECU
•ABS-ECU
A
S C-ECU
•G and ya w ra te se nsor
•St e e ring wh eel sensor
•EPS-ECU
•E T ACS-ECU
•Co mbinatio n me ter (in c orpo rating
meter-A/C-ECU)