steering MITSUBISHI ECLIPSE 1990 User Guide
[x] Cancel search | Manufacturer: MITSUBISHI, Model Year: 1990, Model line: ECLIPSE, Model: MITSUBISHI ECLIPSE 1990Pages: 391, PDF Size: 15.27 MB
Page 163 of 391
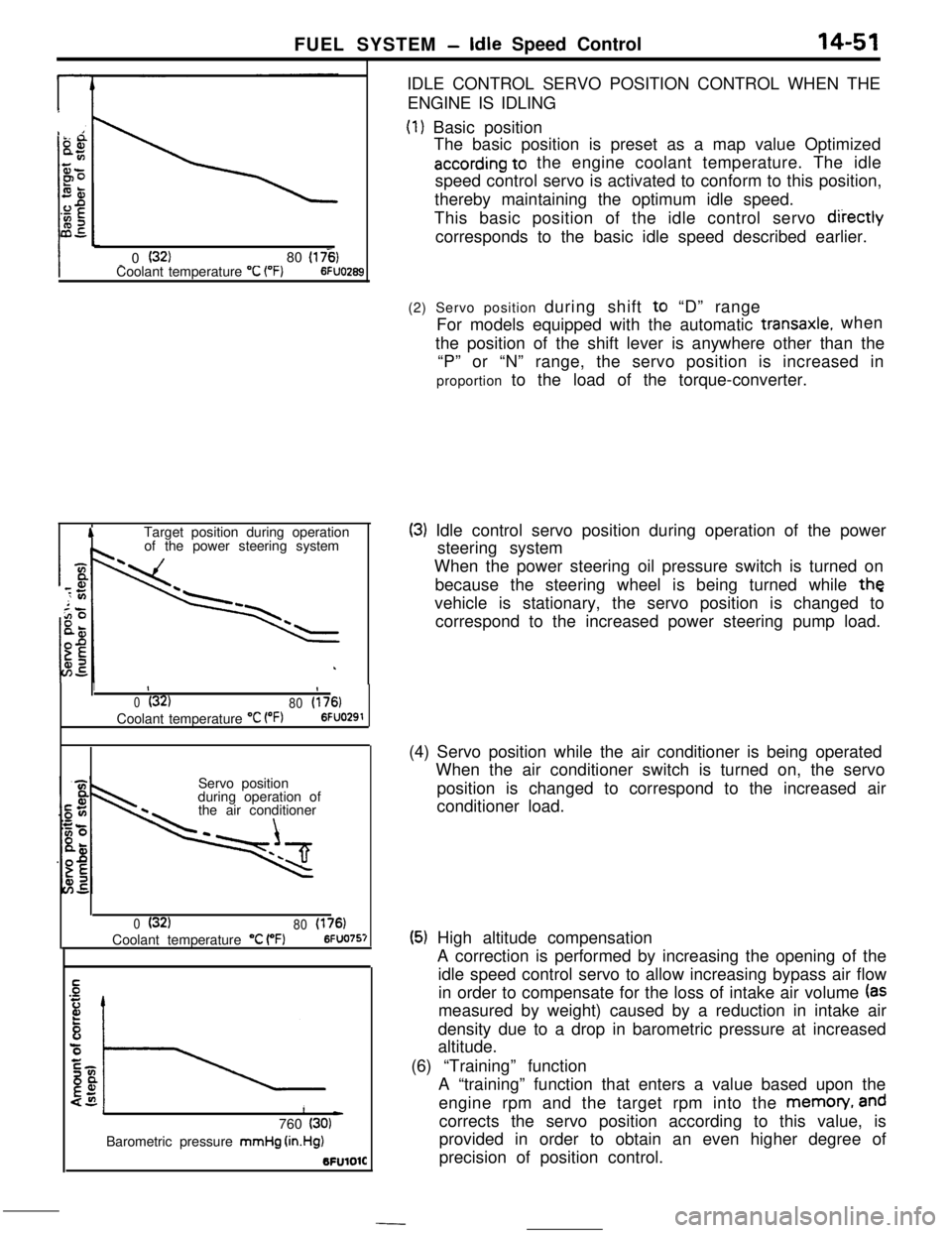
FUEL SYSTEM -Idle Speed Control14-51
_ 0 (32)80 (175)Coolant temperature “C (“F)6FUO2653
ATarget position during operation
of the power steering systemIDLE CONTROL SERVO POSITION CONTROL WHEN THE
ENGINE IS IDLING
(1) Basic position
The basic position is preset as a map value Optimized
according to the engine coolant temperature. The idle
speed control servo is activated to conform to this position,
thereby maintaining the optimum idle speed.
This basic position of the idle control servo
diiectlycorresponds to the basic idle speed described earlier.
1II
0(32)
80(176)Coolant temperature
“C VW6FUO291Servo position
during operation of
the air conditioner
0(32)
80(176)Coolant temperature “C (“F)6FUO757
1L)760 (30)Barometric pressure mmHg
(in.Hg)BFUlOlC(2) Servo position during shift to “D” range
For models equipped with the automatic
transaxle.when
the position of the shift lever is anywhere other than the
“P” or “N” range, the servo position is increased in
proportion to the load of the torque-converter.
(3) Idle control servo position during operation of the power
steering system
When the power steering oil pressure switch is turned on
because the steering wheel is being turned while
thevehicle is stationary, the servo position is changed to
correspond to the increased power steering pump load.
(4) Servo position while the air conditioner is being operated
When the air conditioner switch is turned on, the servo
position is changed to correspond to the increased air
conditioner load.
(5) High altitude compensation
A correction is performed by increasing the opening of the
idle speed control servo to allow increasing bypass air flow
in order to compensate for the loss of intake air volume
(asmeasured by weight) caused by a reduction in intake air
density due to a drop in barometric pressure at increased
altitude.
(6) “Training” function
A “training” function that enters a value based upon the
engine rpm and the target rpm into the memon/,
andcorrects the servo position according to this value, is
provided in order to obtain an even higher degree of
precision of position control.
Page 188 of 391
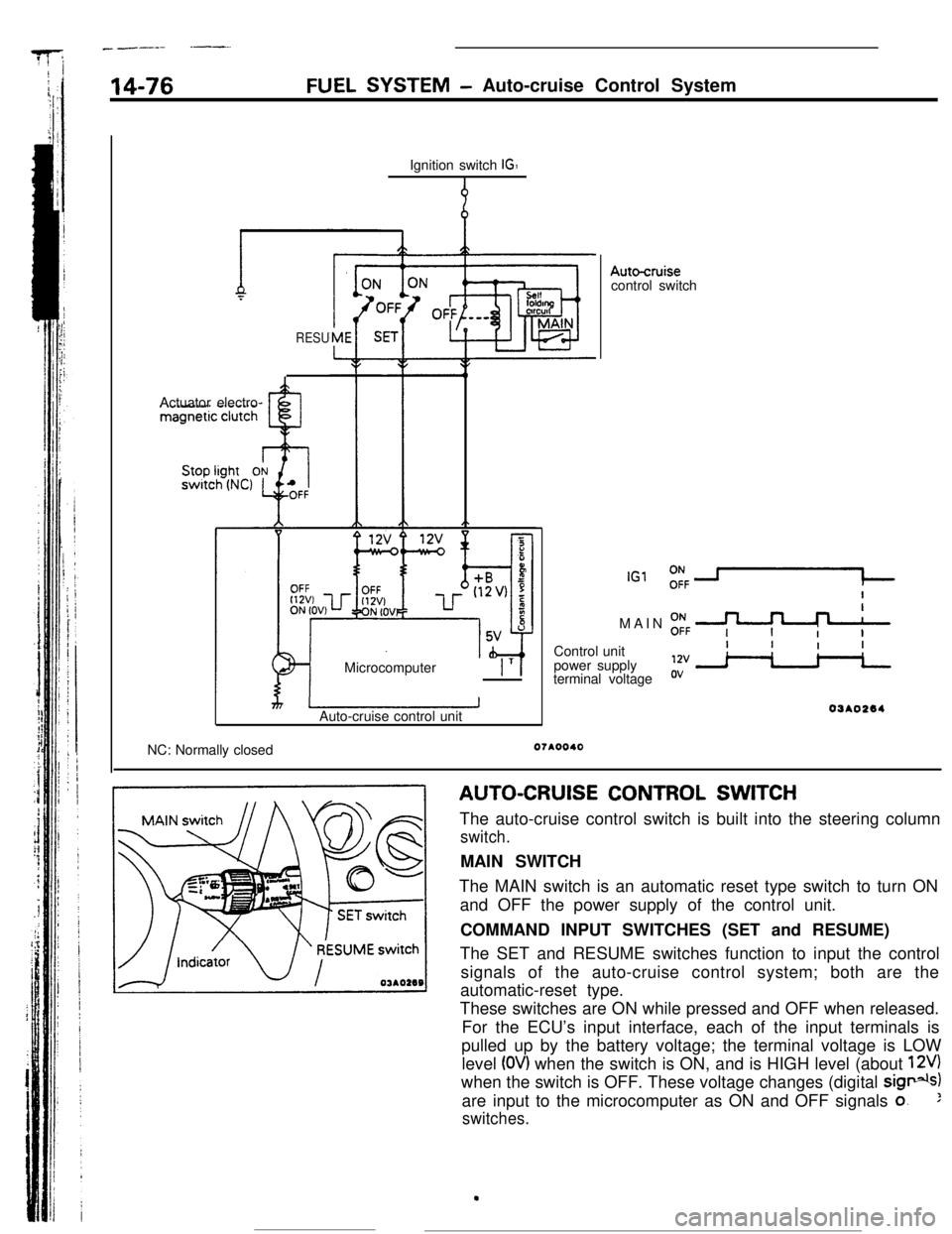
- -----.--..
14-76FUEL SYSTEM -Auto-cruise Control System
Ignition switch
IGI
9
RESUActuator electro-
Microcomputer
1 T 1
rn’Auto-cruise control unit
Autocruisecontrol switch
IGlMAIN
;FF -+++&Control unit
power supply
terminal voltage
03AO264NC: Normally closed
07*0040
AUTO-CRUISE CONTROL SWITCH
The auto-cruise control switch is built into the steering column
switch.MAIN SWITCH
The MAIN switch is an automatic reset type switch to turn ON
and OFF the power supply of the control unit.
COMMAND INPUT SWITCHES (SET and RESUME)
The SET and RESUME switches function to input the control
signals of the auto-cruise control system; both are the
automatic-reset type.
These switches are ON while pressed and OFF when released.
For the ECU’s input interface, each of the input terminals is
pulled up by the battery voltage; the terminal voltage is LOW
level
(OV) when the switch is ON, and is HIGH level (about 12V)when the switch is OFF. These voltage changes (digital
sig*)are input to the microcomputer as ON and OFF signals
o.:
switches.
.
Page 201 of 391
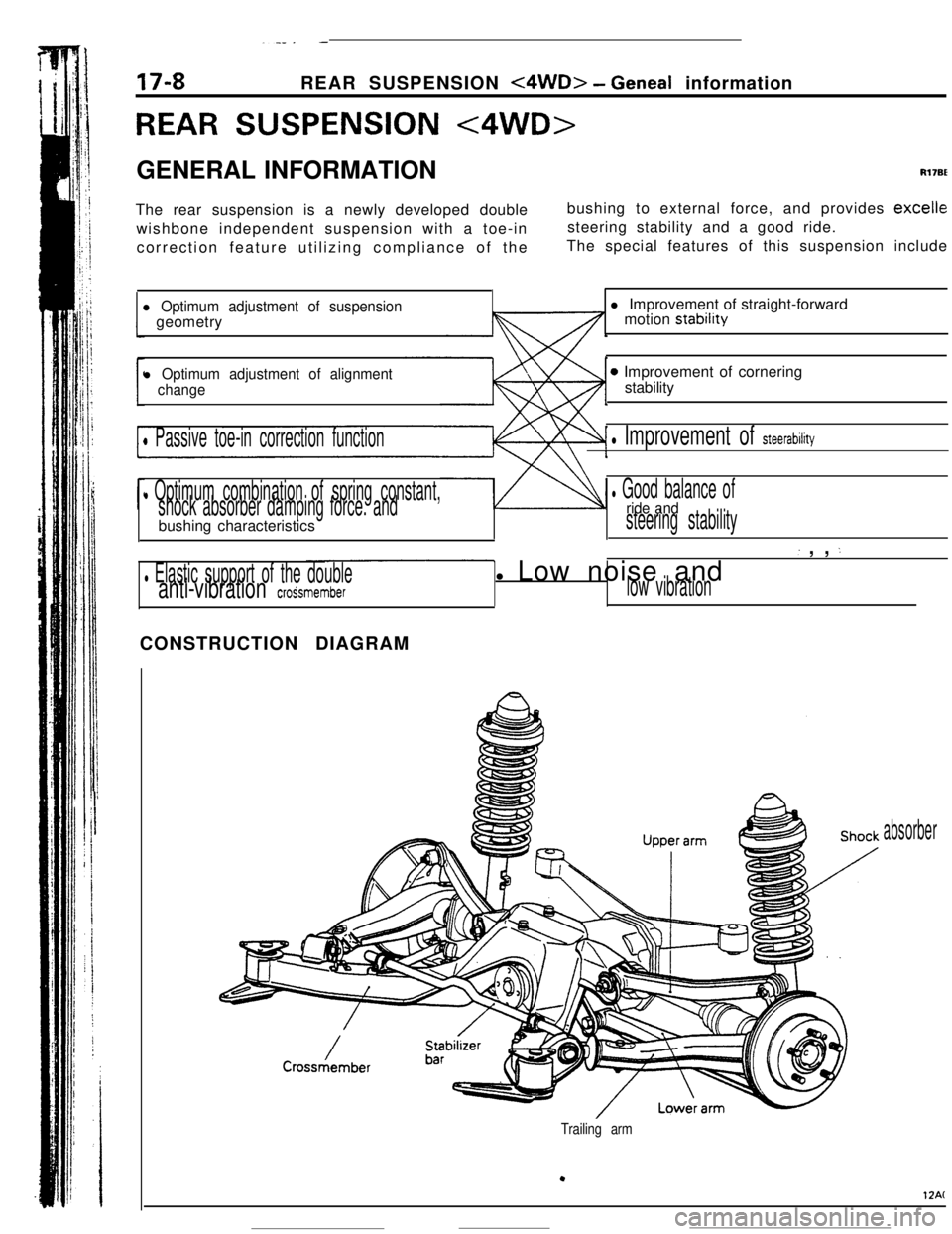
.-_. -
17-8REAR SUSPENSION <4WD> - Geneal information
REAR SUSPENSION <4WD>GENERAL INFORMATION
Rl7BEThe rear suspension is a newly developed double
wishbone independent suspension with a toe-in
correction feature utilizing compliance of thebushing to external force, and provides
excellesteering stability and a good ride.
The special features of this suspension include
l Optimum adjustment of suspensiongeometry
l Optimum adjustment of alignment
change
0 Passive toe-in correction function
l Optimum combination of spring constant,
shock absorber damping force. andbushing characteristics
l Elastic support of the doubleanti-vibration croSsmemberl Improvement of straight-forward
motion stability
0 Improvement of cornering
stability
l Improvement of steerability
l Good balance ofride andsteering stability
( , , :l Low noise and
low vibrationCONSTRUCTION DIAGRAM
absorber
Trailing arm
.
12AC
Page 204 of 391
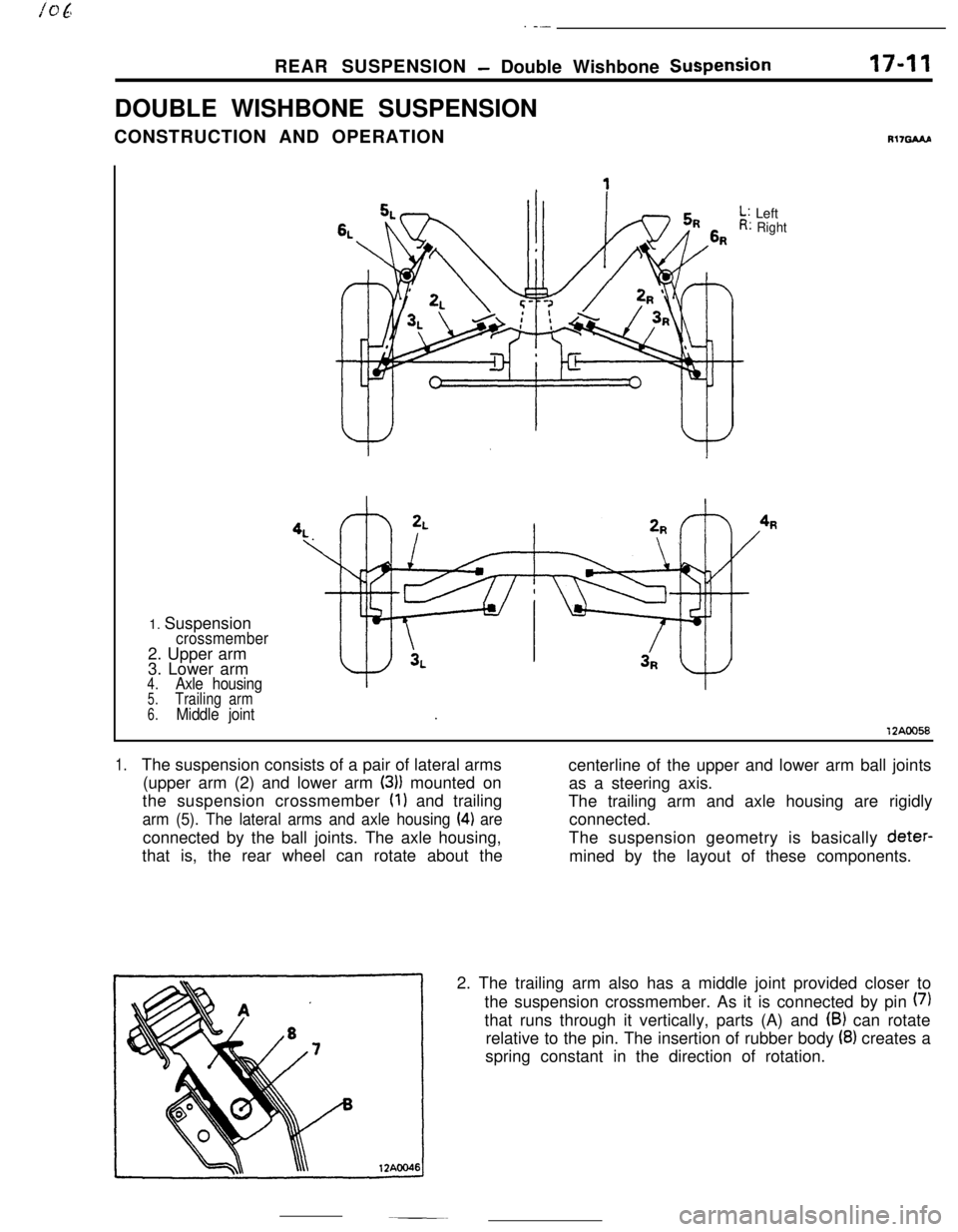
. -.-REAR SUSPENSION
- Double Wishbone SuspensionDOUBLE WISHBONE SUSPENSION
CONSTRUCTION AND OPERATION17-11
R17GAAP1. Suspension
crossmember2. Upper arm
3. Lower arm
4.Axle housing5.Trailing arm
6.Middle jointLeft
Right
12AOO58
1.The suspension consists of a pair of lateral arms
centerline of the upper and lower arm ball joints
(upper arm (2) and lower arm
(3)) mounted on
as a steering axis.
the suspension crossmember
(1) and trailing
The trailing arm and axle housing are rigidly
arm (5). The lateral arms and axle housing (4) areconnected.
connected by the ball joints. The axle housing,The suspension geometry is basically deter-
that is, the rear wheel can rotate about the
mined by the layout of these components.
2. The trailing arm also has a middle joint provided closer to
the suspension crossmember. As it is connected by pin
(7)that runs through it vertically, parts (A) and
(B) can rotate
relative to the pin. The insertion of rubber body
(8) creates a
spring constant in the direction of rotation.
Page 205 of 391
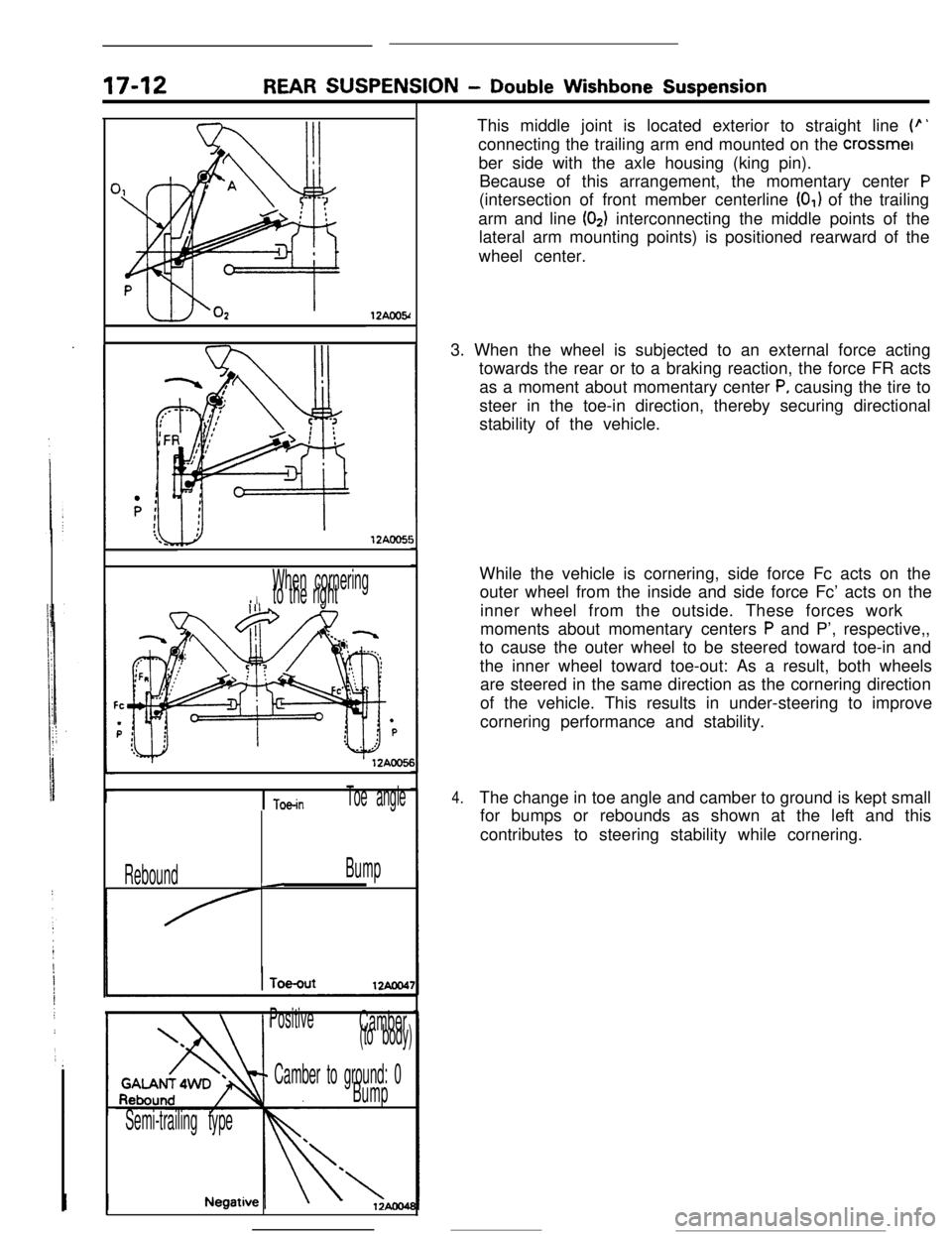
17-12REAR SUSPENSION - Double Wishbone Suspension
12AWY
lZAOOS!
When cornering. I.to the right
I Toe-inToe angle
ReboundBump-
PositiveCamber(to body)
- Camber to ground: 0
Bump
Semi-trailing typeThis middle joint is located exterior to straight line
(p’connecting the trailing arm end mounted on the crossmet
ber side with the axle housing (king pin).
Because of this arrangement, the momentary center
P(intersection of front member centerline
(0,) of the trailing
arm and line
(02) interconnecting the middle points of the
lateral arm mounting points) is positioned rearward of the
wheel center.
3. When the wheel is subjected to an external force acting
towards the rear or to a braking reaction, the force FR acts
as a moment about momentary center
P, causing the tire to
steer in the toe-in direction, thereby securing directional
stability of the vehicle.
While the vehicle is cornering, side force Fc acts on the
outer wheel from the inside and side force Fc’ acts on the
inner wheel from the outside. These forces work
moments about momentary centers
P and P’, respective,,
to cause the outer wheel to be steered toward toe-in and
the inner wheel toward toe-out: As a result, both wheels
are steered in the same direction as the cornering direction
of the vehicle. This results in under-steering to improve
cornering performance and stability.
4.The change in toe angle and camber to ground is kept small
for bumps or rebounds as shown at the left and this
contributes to steering stability while cornering.
Page 206 of 391
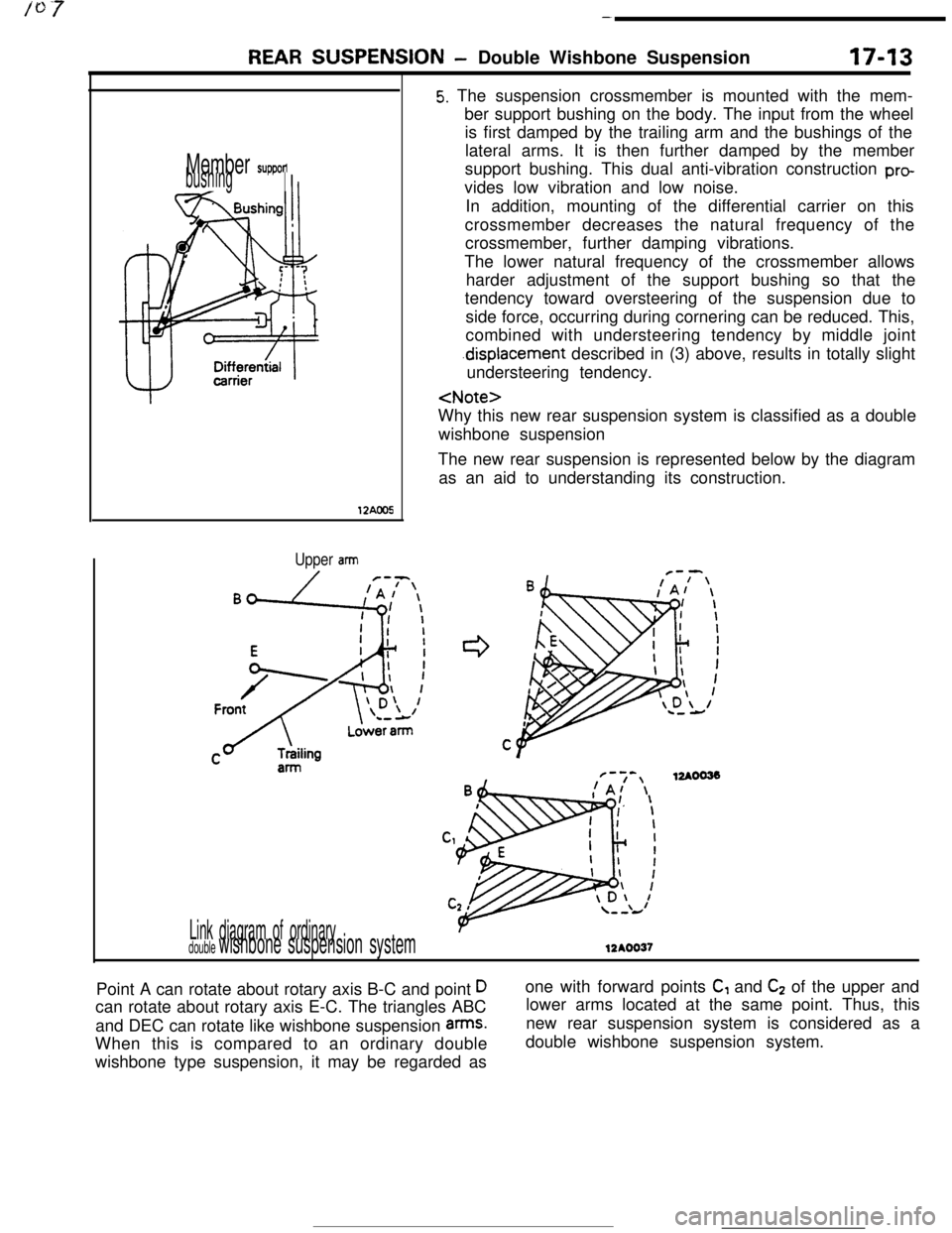
-
REAR SUSPENSION -Double Wishbone Suspension17-13
Member supponbushingI
12AOO5
Upper arm
Link diagram of ordinarydouble wishbone suspension system
5. The suspension crossmember is mounted with the mem-
ber support bushing on the body. The input from the wheel
is first damped by the trailing arm and the bushings of the
lateral arms. It is then further damped by the member
support bushing. This dual anti-vibration construction
provides low vibration and low noise.
In addition, mounting of the differential carrier on this
crossmember decreases the natural frequency of the
crossmember, further damping vibrations.
The lower natural frequency of the crossmember allows
harder adjustment of the support bushing so that the
tendency toward oversteering of the suspension due to
side force, occurring during cornering can be reduced. This,
combined with understeering tendency by middle joint
.displacement described in (3) above, results in totally slight
understeering tendency.
wishbone suspension
The new rear suspension is represented below by the diagram
as an aid to understanding its construction.
F-7-,12AOO33!A/ \
12AOO37Point A can rotate about rotary axis B-C and point
Dcan rotate about rotary axis E-C. The triangles ABC
and DEC can rotate like wishbone suspension
arms.When this is compared to an ordinary double
wishbone type suspension, it may be regarded asone with forward points
C, and C2 of the upper and
lower arms located at the same point. Thus, this
new rear suspension system is considered as a
double wishbone suspension system.
Page 210 of 391
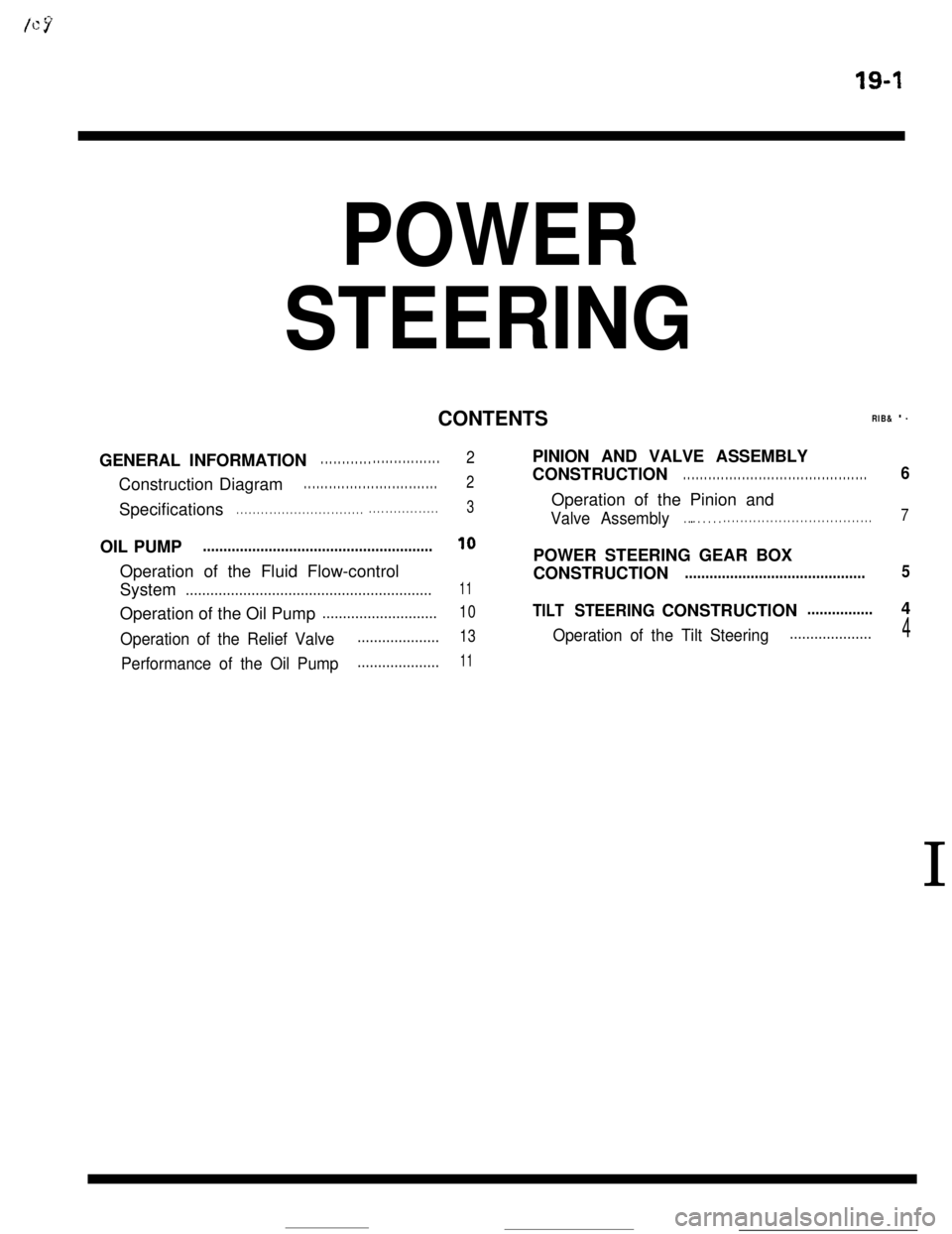
19-I
POWER
_
GENERAL INFORMATION
.._ . . . . .
OIL PUMP ........................................................10POWER STEERING GEAR BOX
Page 211 of 391
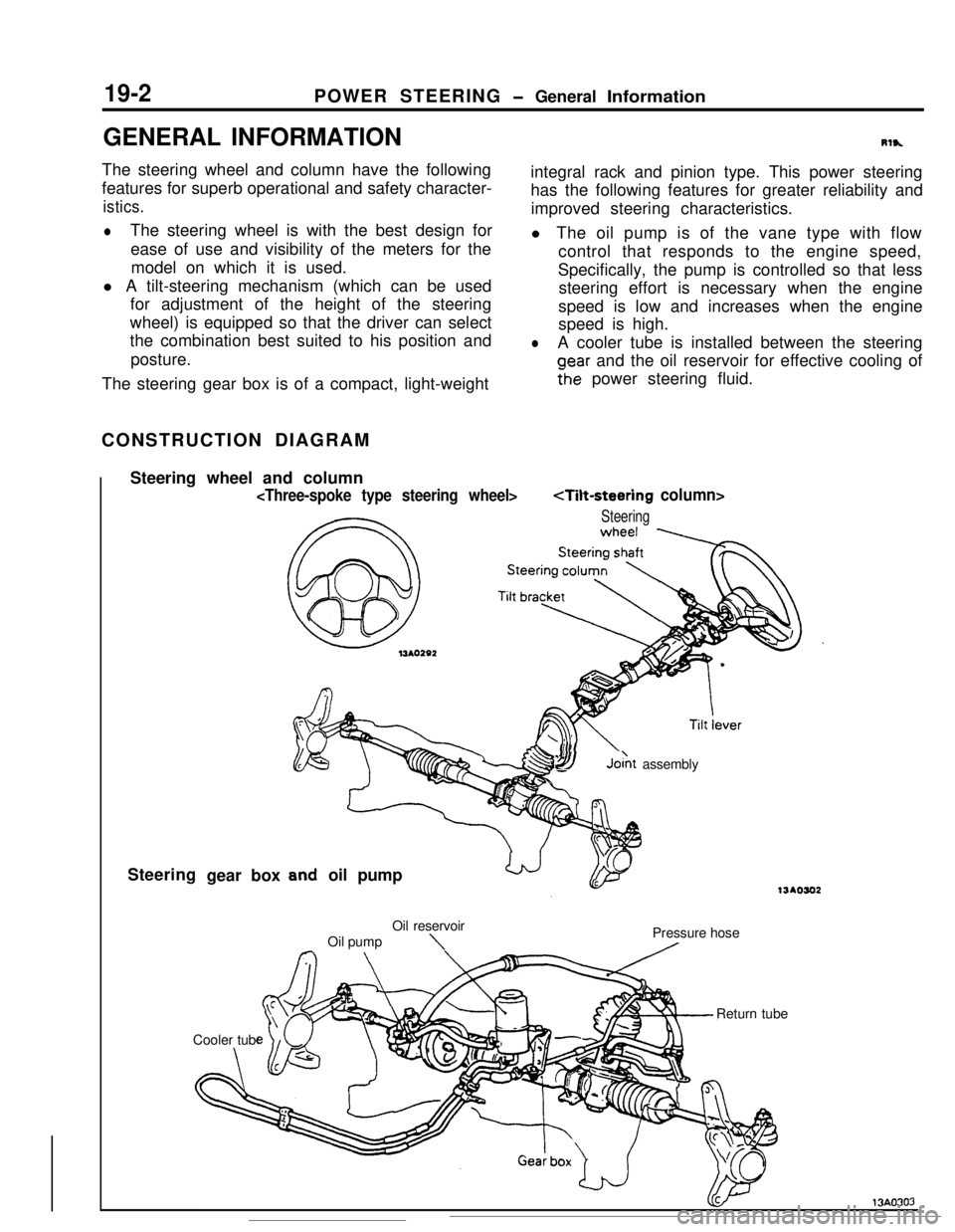
19-2 POWER STEERING
Rlh
integral rack and pinion type. This power steering
oear and the oil reservoir for effective cooling of
Fhe power steering fluid.The steering gear box is of a compact, light-weight
Steering
SYJo& assembly
oil pump
\Pressure hose
A
Page 212 of 391
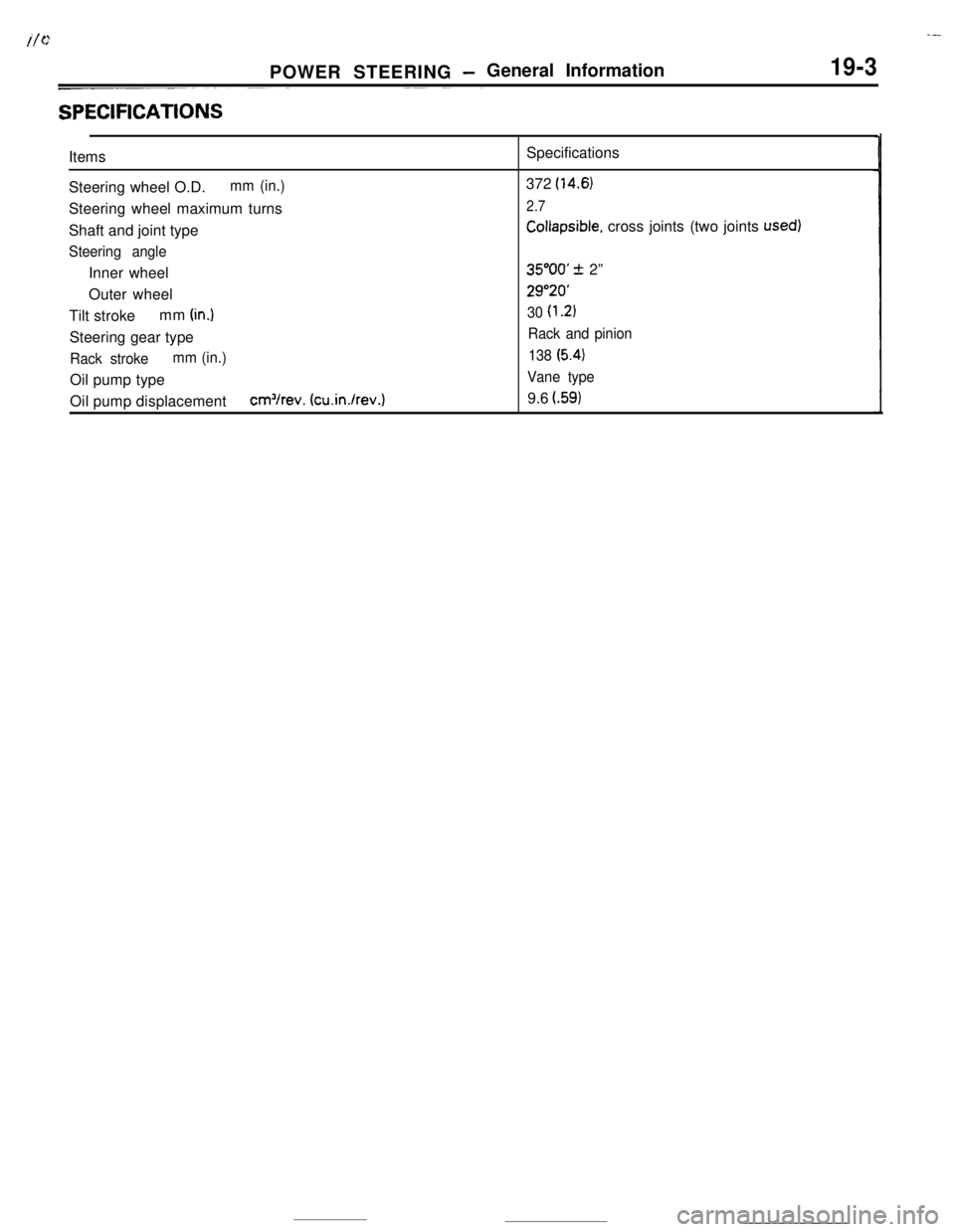
POWER STEERING- General Information19-3
SPEClFlCATlONSItems
Steering wheel O.D.
mm (in.)Steering wheel maximum turns
Shaft and joint type
Steering angleInner wheel
Outer wheel
Tilt strokemm
(in.1Steering gear type
Rack strokemm (in.)Oil pump type
Oil pump displacement
cm3/rev. (cu.in./rev.)Specifications
372
(14.6)
2.7
Collapsible, cross joints (two joints used)
35”OO’ + 2”
29”20’
30
(1.2)
Rack and pinion
138
(5.41
Vane type9.6
l.59)
Page 213 of 391
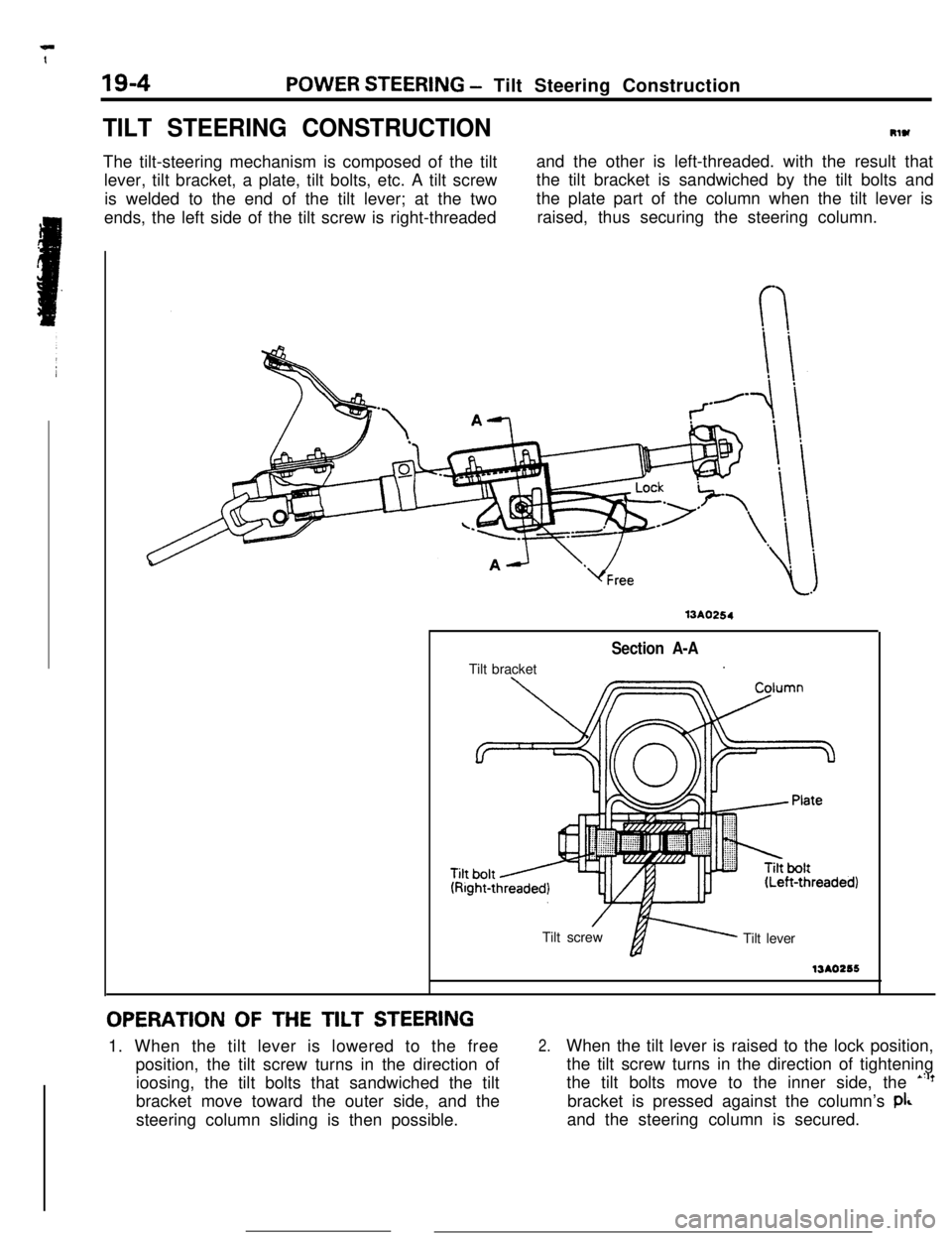
19-4POWER STEERING - Tilt Steering Construction
TILT STEERING CONSTRUCTIONRlW
The tilt-steering mechanism is composed of the tilt
lever, tilt bracket, a plate, tilt bolts, etc. A tilt screw
is welded to the end of the tilt lever; at the two
ends, the left side of the tilt screw is right-threadedand the other is left-threaded. with the result that
the tilt bracket is sandwiched by the tilt bolts and
the plate part of the column when the tilt lever is
raised, thus securing the steering column.
13A0254Tilt bracket
Section A-A.
’Tilt screwfi Tilt lever13AO256
OPERATION OF THE TILT STEERING1. When the tilt lever is lowered to the free
position, the tilt screw turns in the direction of
ioosing, the tilt bolts that sandwiched the tilt
bracket move toward the outer side, and the
steering column sliding is then possible.
2.When the tilt lever is raised to the lock position,
the tilt screw turns in the direction of tightening
the tilt bolts move to the inner side, the
*“?bracket is pressed against the column’s
pi&and the steering column is secured.