MITSUBISHI LANCER 2005 Workshop Manual
Manufacturer: MITSUBISHI, Model Year: 2005, Model line: LANCER, Model: MITSUBISHI LANCER 2005Pages: 788, PDF Size: 45.98 MB
Page 151 of 788
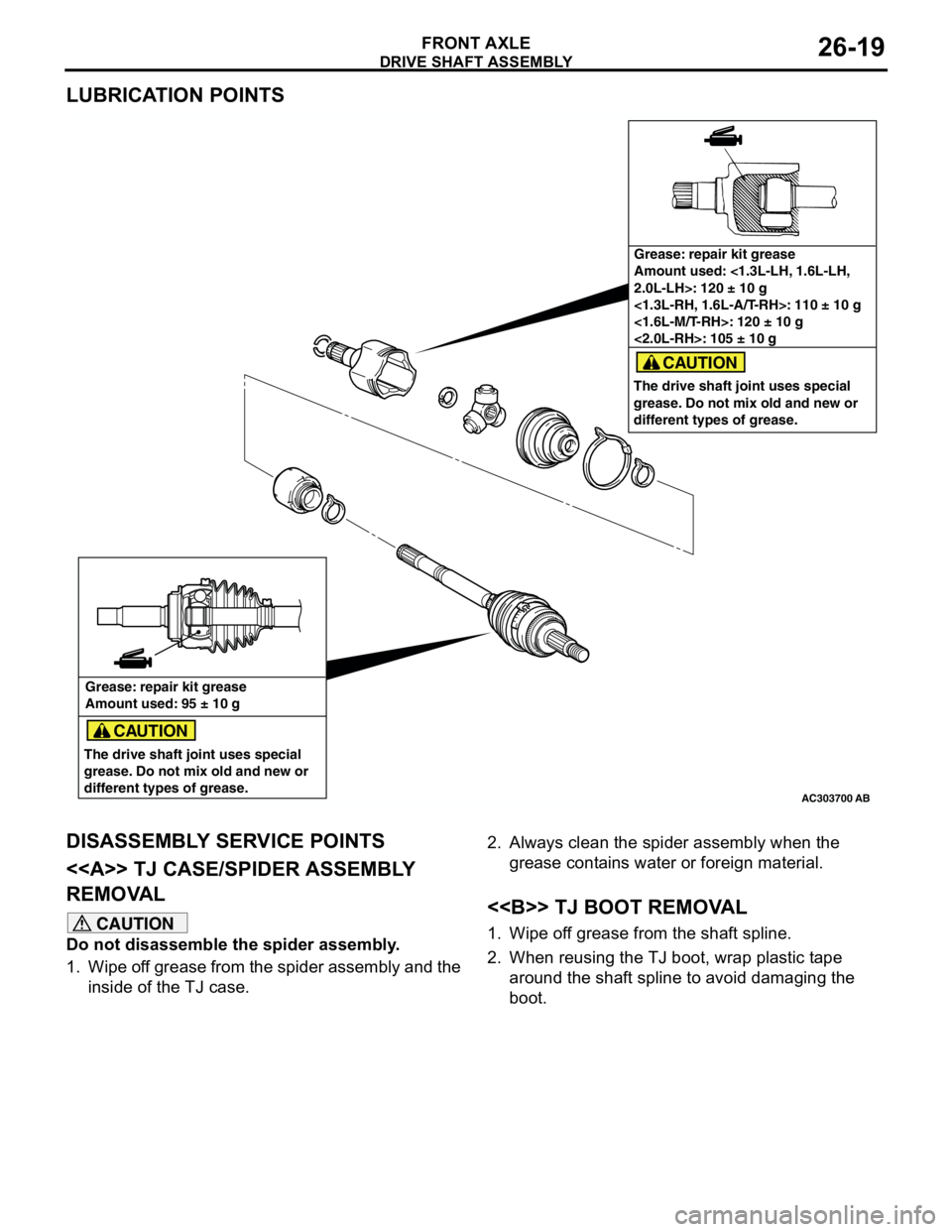
Page 152 of 788
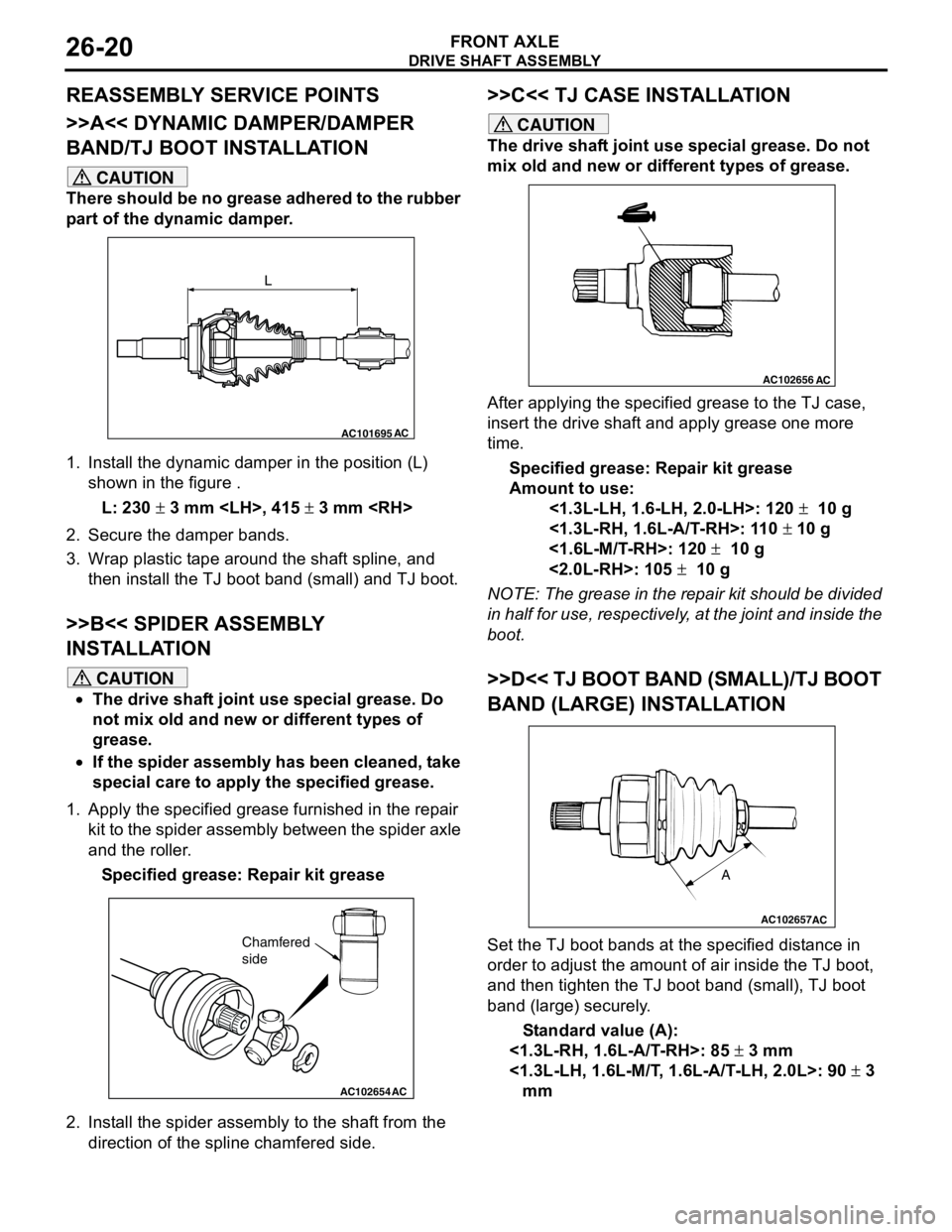
DRIVE SHAFT ASSEMBLY
FRONT AXLE26-20
REASSEMBLY SERVICE POINTS
>>A<< DYNAMIC DAMPER/DAMPER
BAND/TJ BOOT INSTALLATION
CAUTION
There should be no grease adhered to the rubber
part of the dynamic damper.
1. Install the dynamic damper in the position (L)
shown in the figure .
L: 230 ± 3 mm
2. Secure the damper bands.
3. Wrap plastic tape around the shaft spline, and
then install the TJ boot band (small) and TJ boot.
>>B<< SPIDER ASSEMBLY
INSTALLATION
CAUTION
•The drive shaft joint use special grease. Do
not mix old and new or different types of
grease.
•If the spider assembly has been cleaned, take
special care to apply the specified grease.
1. Apply the specified grease furnished in the repair
kit to the spider assembly between the spider axle
and the roller.
Specified grease: Repair kit grease
2. Install the spider assembly to the shaft from the
direction of the spline chamfered side.
>>C<< TJ CASE INSTALLATION
CAUTION
The drive shaft joint use special grease. Do not
mix old and new or different types of grease.
After applying the specified grease to the TJ case,
insert the drive shaft and apply grease one more
time.
Specified grease: Repair kit grease
Amount to use:
<1.3L-LH, 1.6-LH, 2.0-LH>: 120 ± 10 g
<1.3L-RH, 1.6L-A/T-RH>: 110 ± 10 g
<1.6L-M/T-RH>: 120 ± 10 g
<2.0L-RH>: 105 ± 10 g
NOTE: The grease in the repair kit should be divided
in half for use, respectively, at the joint and inside the
boot.
>>D<< TJ BOOT BAND (SMALL)/TJ BOOT
BAND (LARGE) INSTALLATION
Set the TJ boot bands at the specified distance in
order to adjust the amount of air inside the TJ boot,
and then tighten the TJ boot band (small), TJ boot
band (large) securely.
Standard value (A):
<1.3L-RH, 1.6L-A/T-RH>: 85 ± 3 mm
<1.3L-LH, 1.6L-M/T, 1.6L-A/T-LH, 2.0L>: 90 ± 3
mm
AC101695AC
L
AC102654AC
Chamfered
side
AC102656AC
AC102657
A
AC
Page 153 of 788
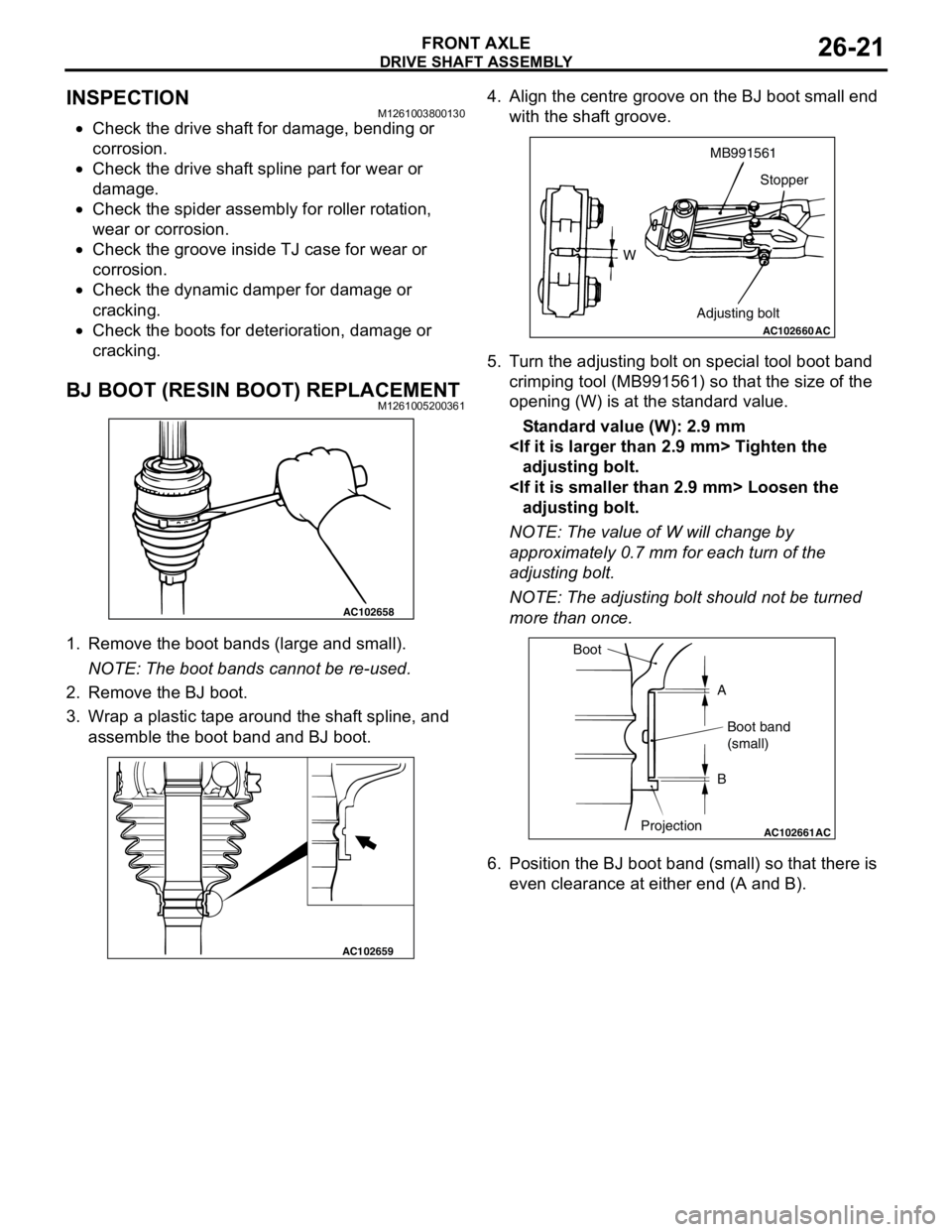
DRIVE SHAFT ASSEMBLY
FRONT AXLE26-21
INSPECTIONM1261003800130
•Check the drive shaft for damage, bending or
corrosion.
•Check the drive shaft spline part for wear or
damage.
•Check the spider assembly for roller rotation,
wear or corrosion.
•Check the groove inside TJ case for wear or
corrosion.
•Check the dynamic damper for damage or
cracking.
•Check the boots for deterioration, damage or
cracking.
BJ BOOT (RESIN BOOT) REPLACEMENTM1261005200361
1. Remove the boot bands (large and small).
NOTE: The boot bands cannot be re-used.
2. Remove the BJ boot.
3. Wrap a plastic tape around the shaft spline, and
assemble the boot band and BJ boot.4. Align the centre groove on the BJ boot small end
with the shaft groove.
5. Turn the adjusting bolt on special tool boot band
crimping tool (MB991561) so that the size of the
opening (W) is at the standard value.
Standard value (W): 2.9 mm
adjusting bolt.
adjusting bolt.
NOTE: The value of W will change by
approximately 0.7 mm for each turn of the
adjusting bolt.
NOTE: The adjusting bolt should not be turned
more than once.
6. Position the BJ boot band (small) so that there is
even clearance at either end (A and B).
AC102658
AC102659
AC102660
WMB991561
Stopper
Adjusting bolt
AC
AC102661AC
Boot
A
Boot band
(small)
B
Projection
Page 154 of 788
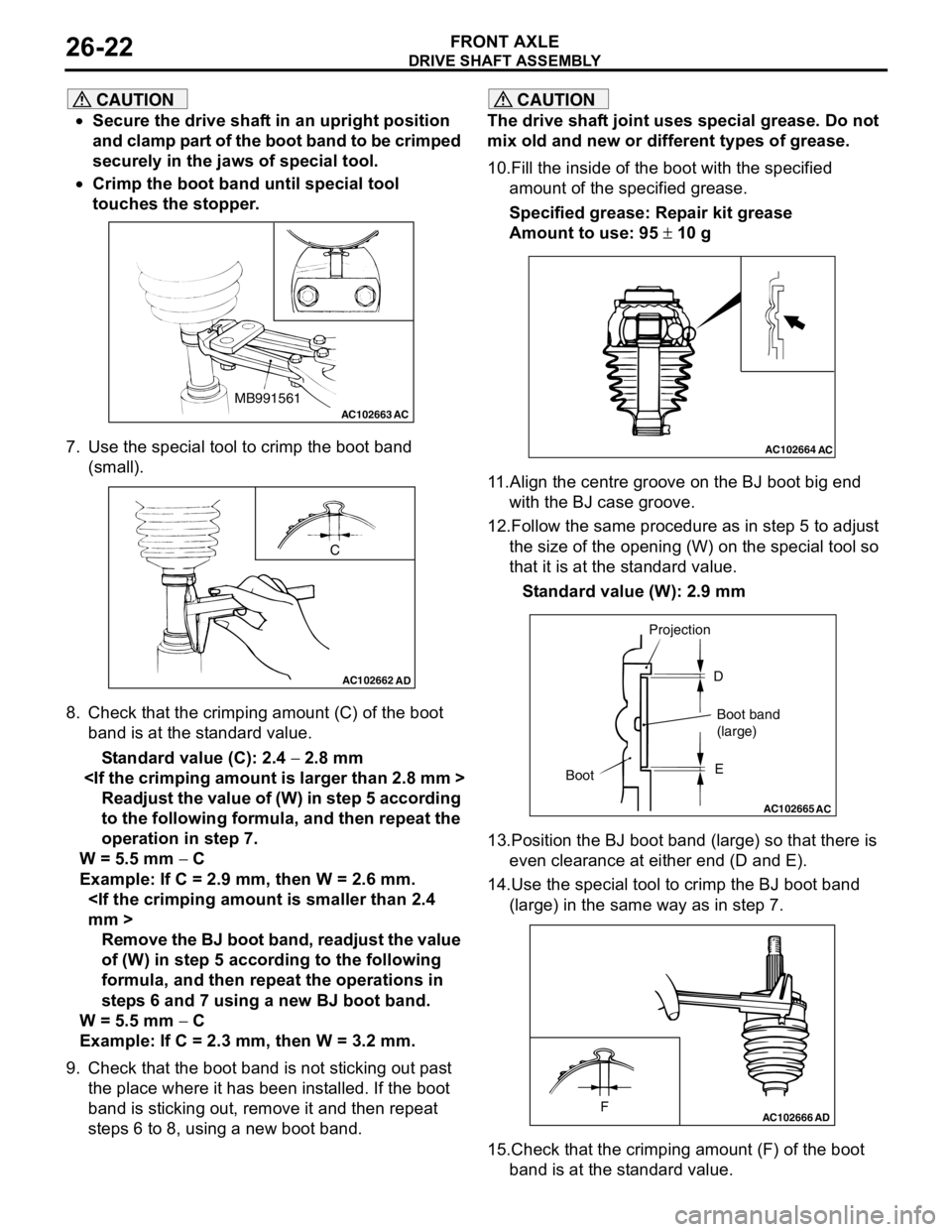
DRIVE SHAFT ASSEMBLY
FRONT AXLE26-22
CAUTION
•Secure the drive shaft in an upright position
and clamp part of the boot band to be crimped
securely in the jaws of special tool.
•Crimp the boot band until special tool
touches the stopper.
7. Use the special tool to crimp the boot band
(small).
8. Check that the crimping amount (C) of the boot
band is at the standard value.
Standard value (C): 2.4 − 2.8 mm
Readjust the value of (W) in step 5 according
to the following formula, and then repeat the
operation in step 7.
W = 5.5 mm − C
Example: If C = 2.9 mm, then W = 2.6 mm.
Remove the BJ boot band, readjust the value
of (W) in step 5 according to the following
formula, and then repeat the operations in
steps 6 and 7 using a new BJ boot band.
W = 5.5 mm − C
Example: If C = 2.3 mm, then W = 3.2 mm.
9. Check that the boot band is not sticking out past
the place where it has been installed. If the boot
band is sticking out, remove it and then repeat
steps 6 to 8, using a new boot band.
CAUTION
The drive shaft joint uses special grease. Do not
mix old and new or different types of grease.
10.Fill the inside of the boot with the specified
amount of the specified grease.
Specified grease: Repair kit grease
Amount to use: 95 ± 10 g
11.Align the centre groove on the BJ boot big end
with the BJ case groove.
12.Follow the same procedure as in step 5 to adjust
the size of the opening (W) on the special tool so
that it is at the standard value.
Standard value (W): 2.9 mm
13.Position the BJ boot band (large) so that there is
even clearance at either end (D and E).
14.Use the special tool to crimp the BJ boot band
(large) in the same way as in step 7.
15.Check that the crimping amount (F) of the boot
band is at the standard value.
AC102663 ACMB991561
AC102662
C
AD
AC102664AC
AC102665
AC
BootProjection
Boot band
(large) D
E
AC102666FAD
Page 155 of 788
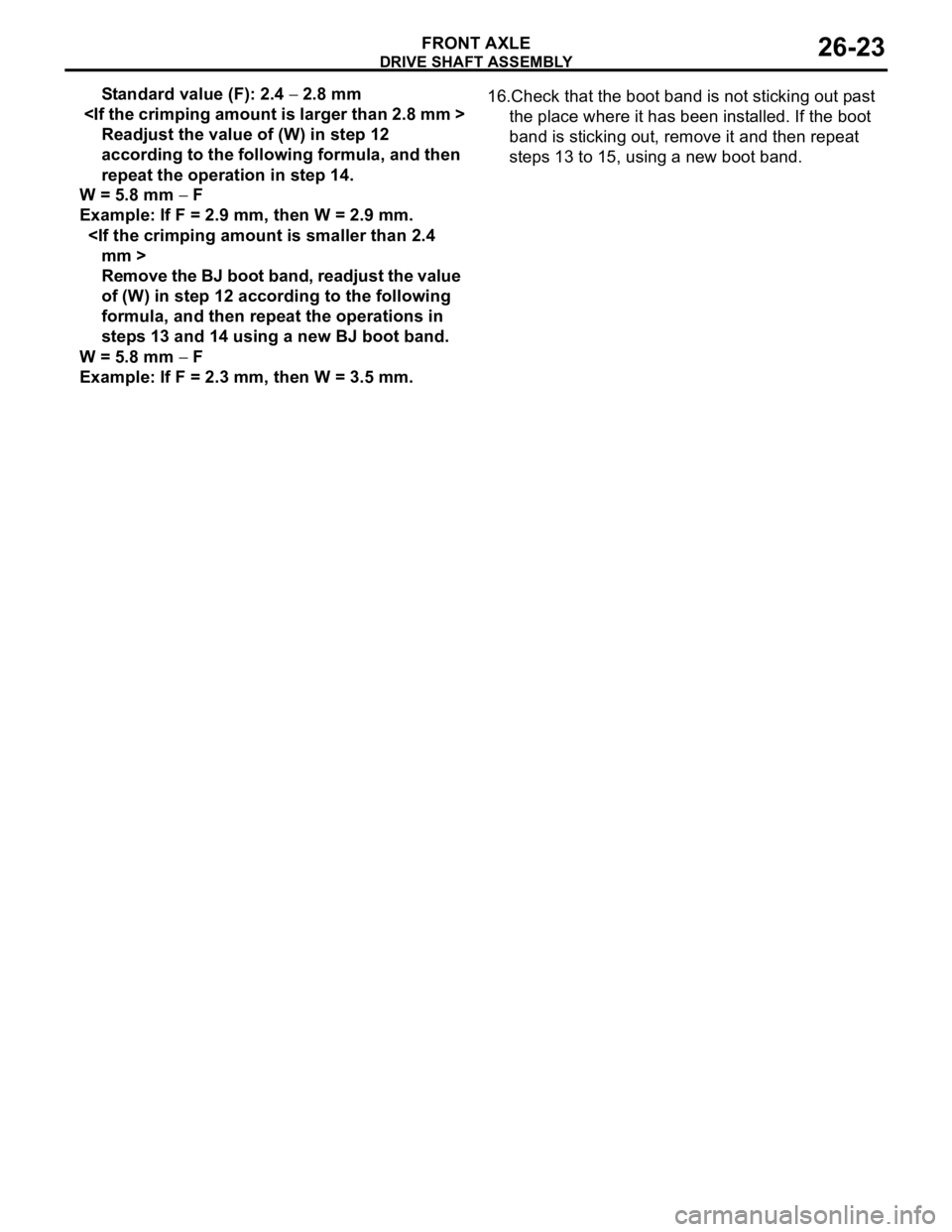
DRIVE SHAFT ASSEMBLY
FRONT AXLE26-23
Standard value (F): 2.4 − 2.8 mm
Readjust the value of (W) in step 12
according to the following formula, and then
repeat the operation in step 14.
W = 5.8 mm − F
Example: If F = 2.9 mm, then W = 2.9 mm.
Remove the BJ boot band, readjust the value
of (W) in step 12 according to the following
formula, and then repeat the operations in
steps 13 and 14 using a new BJ boot band.
W = 5.8 mm − F
Example: If F = 2.3 mm, then W = 3.5 mm.16.Check that the boot band is not sticking out past
the place where it has been installed. If the boot
band is sticking out, remove it and then repeat
steps 13 to 15, using a new boot band.
Page 156 of 788
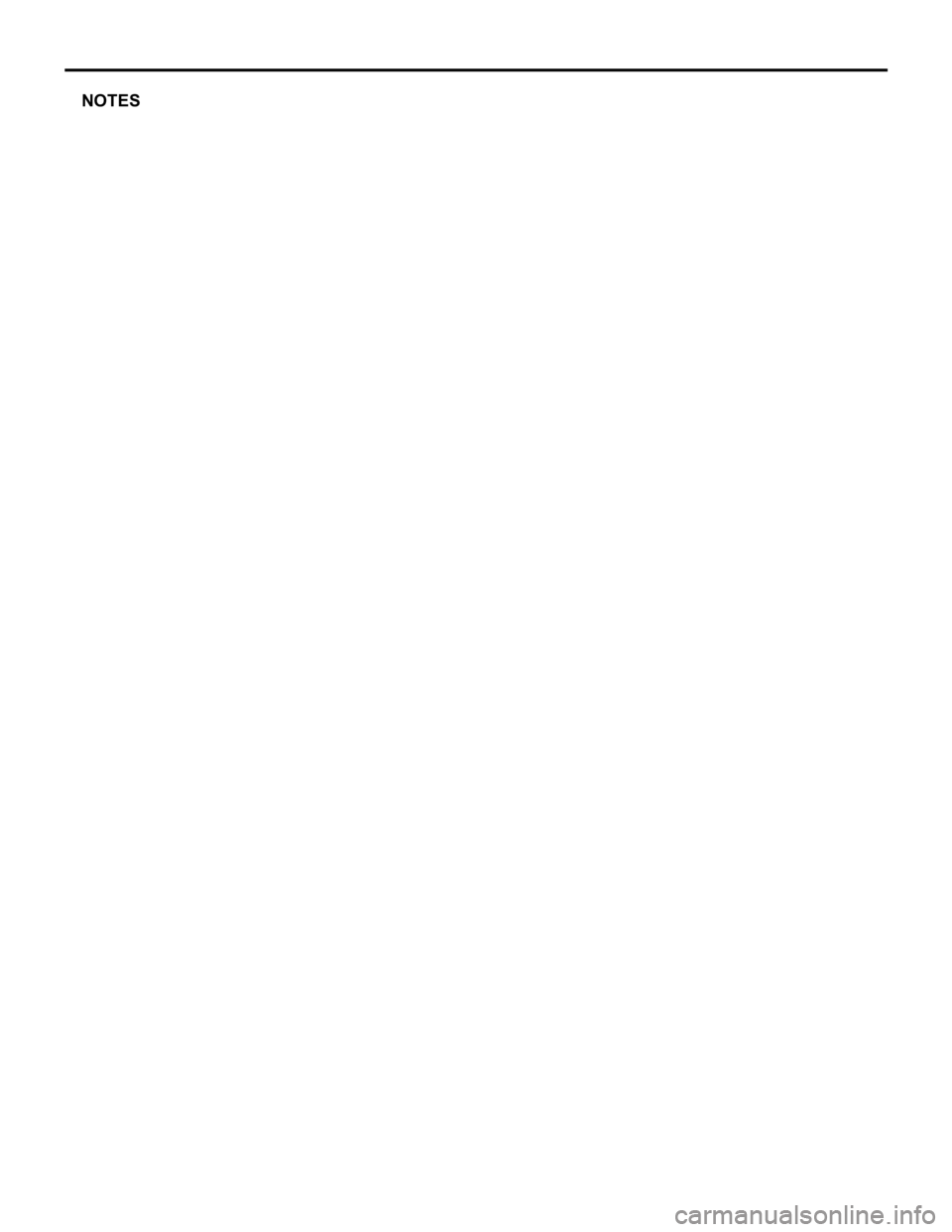
NOTES
Page 157 of 788
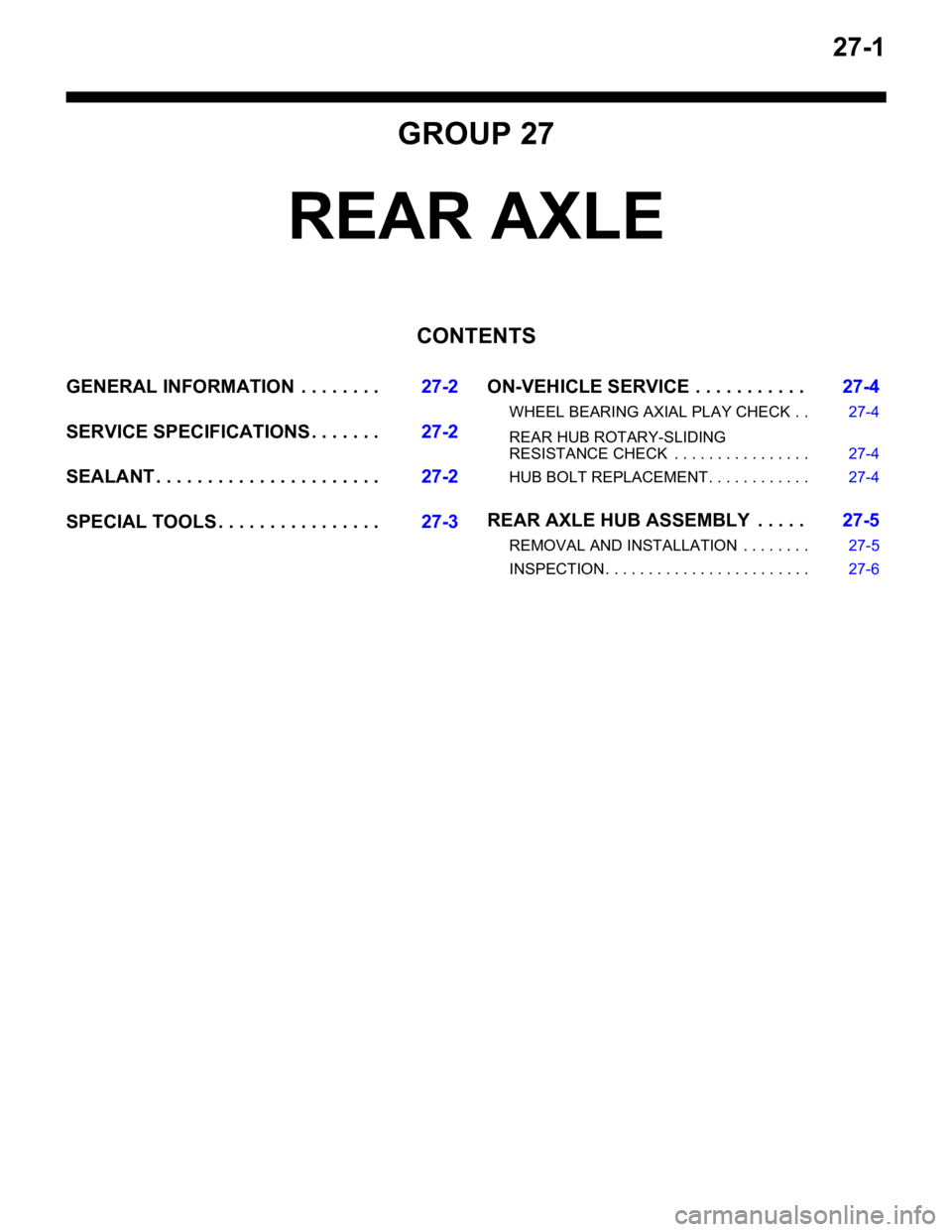
27-1
GROUP 27
REAR AXLE
CONTENTS
GENERAL INFORMATION . . . . . . . .27-2
SERVICE SPECIFICATIONS . . . . . . .27-2
SEALANT . . . . . . . . . . . . . . . . . . . . . .27-2
SPECIAL TOOLS . . . . . . . . . . . . . . . .27-3ON-VEHICLE SERVICE . . . . . . . . . . .27-4
WHEEL BEARING AXIAL PLAY CHECK . . 27-4
REAR HUB ROTARY-SLIDING
RESISTANCE CHECK . . . . . . . . . . . . . . . . 27-4
HUB BOLT REPLACEMENT . . . . . . . . . . . . 27-4
REAR AXLE HUB ASSEMBLY . . . . .27-5
REMOVAL AND INSTALLATION . . . . . . . . 27-5
INSPECTION . . . . . . . . . . . . . . . . . . . . . . . . 27-6
Page 158 of 788
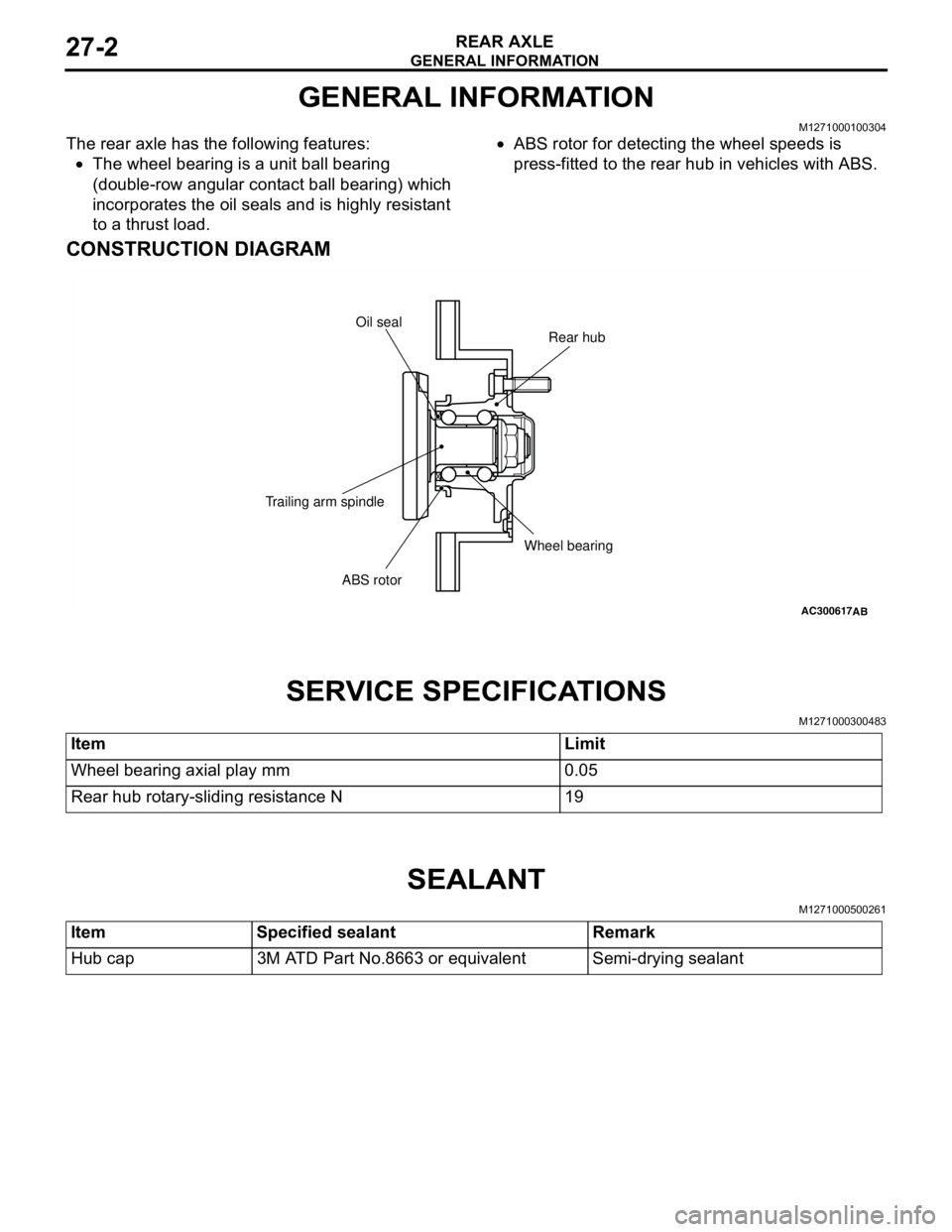
GENERAL INFORMATION
REAR AXLE27-2
GENERAL INFORMATION
M1271000100304
The rear axle has the following features:
•The wheel bearing is a unit ball bearing
(double-row angular contact ball bearing) which
incorporates the oil seals and is highly resistant
to a thrust load.•ABS rotor for detecting the wheel speeds is
press-fitted to the rear hub in vehicles with ABS.
CONSTRUCTION DIAGRAM
SERVICE SPECIFICATIONS
M1271000300483
SEALANT
M1271000500261
AC300617AB
Rear hub Oil seal
Wheel bearing
ABS rotor Trailing arm spindle
Item Limit
Wheel bearing axial play mm 0.05
Rear hub rotary-sliding resistance N 19
Item Specified sealant Remark
Hub cap 3M ATD Part No.8663 or equivalent Semi-drying sealant
Page 159 of 788
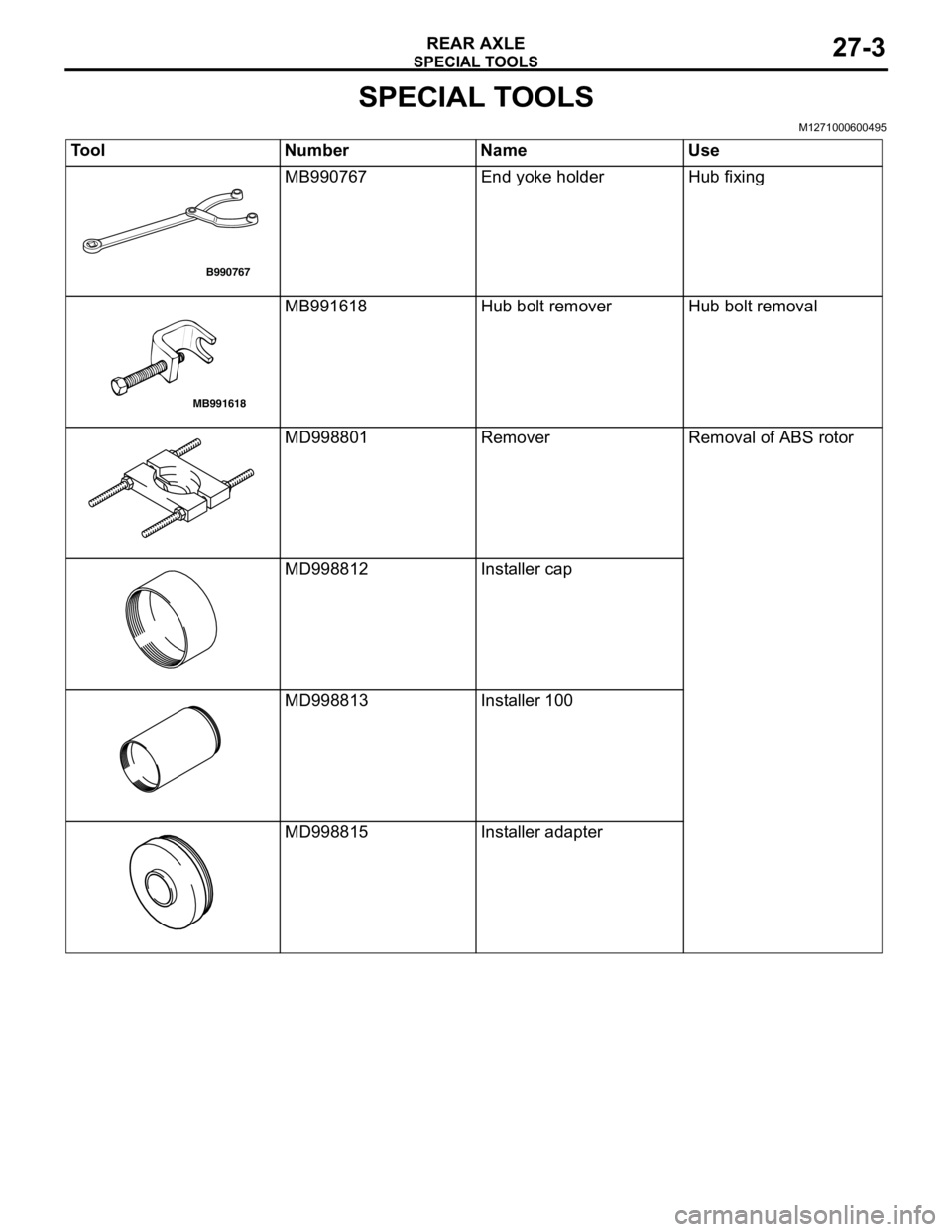
SPECIAL TOOLS
REAR AXLE27-3
SPECIAL TOOLS
M1271000600495
Tool Number Name Use
MB990767 End yoke holder Hub fixing
MB991618 Hub bolt remover Hub bolt removal
MD998801 Remover Removal of ABS rotor
MD998812 Installer cap
MD998813 Installer 100
MD998815 Installer adapter
B990767
MB991618
Page 160 of 788
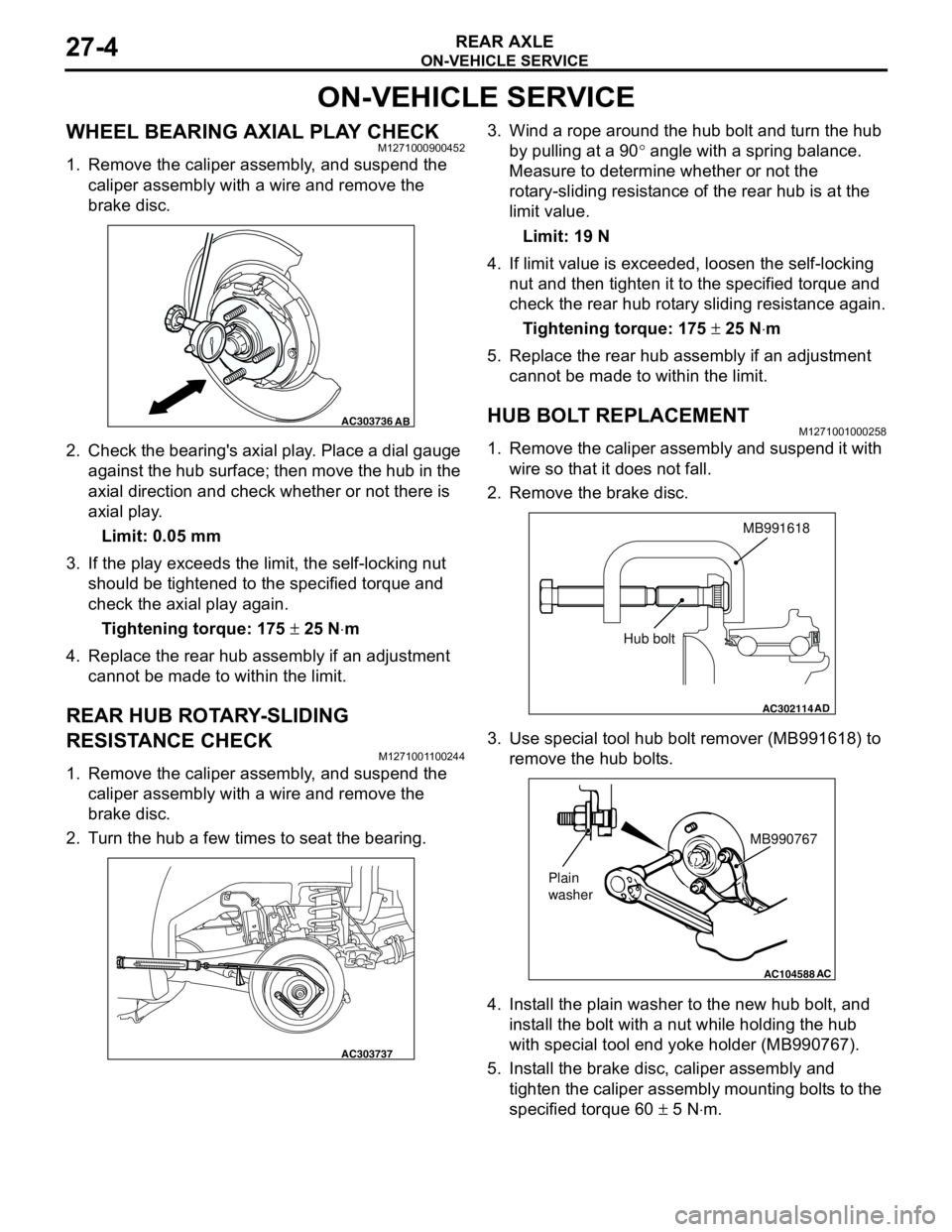
ON-VEHICLE SERVICE
REAR AXLE27-4
ON-VEHICLE SERVICE
WHEEL BEARING AXIAL PLAY CHECKM1271000900452
1. Remove the caliper assembly, and suspend the
caliper assembly with a wire and remove the
brake disc.
2. Check the bearing's axial play. Place a dial gauge
against the hub surface; then move the hub in the
axial direction and check whether or not there is
axial play.
Limit: 0.05 mm
3. If the play exceeds the limit, the self-locking nut
should be tightened to the specified torque and
check the axial play again.
Tightening torque: 175 ± 25 N⋅m
4. Replace the rear hub assembly if an adjustment
cannot be made to within the limit.
REAR HUB ROTARY-SLIDING
RESISTANCE CHECK
M1271001100244
1. Remove the caliper assembly, and suspend the
caliper assembly with a wire and remove the
brake disc.
2. Turn the hub a few times to seat the bearing.3. Wind a rope around the hub bolt and turn the hub
by pulling at a 90° angle with a spring balance.
Measure to determine whether or not the
rotary-sliding resistance of the rear hub is at the
limit value.
Limit: 19 N
4. If limit value is exceeded, loosen the self-locking
nut and then tighten it to the specified torque and
check the rear hub rotary sliding resistance again.
Tightening torque: 175 ± 25 N⋅m
5. Replace the rear hub assembly if an adjustment
cannot be made to within the limit.
HUB BOLT REPLACEMENTM1271001000258
1. Remove the caliper assembly and suspend it with
wire so that it does not fall.
2. Remove the brake disc.
3. Use special tool hub bolt remover (MB991618) to
remove the hub bolts.
4. Install the plain washer to the new hub bolt, and
install the bolt with a nut while holding the hub
with special tool end yoke holder (MB990767).
5. Install the brake disc, caliper assembly and
tighten the caliper assembly mounting bolts to the
specified torque 60 ± 5 N⋅m.
AC303736AB
AC303737
AC302114
MB991618
AD
Hub bolt
AC104588
MB990767
Plain
washer
AC