sensor MITSUBISHI LANCER EVOLUTION 2007 Service Repair Manual
[x] Cancel search | Manufacturer: MITSUBISHI, Model Year: 2007, Model line: LANCER EVOLUTION, Model: MITSUBISHI LANCER EVOLUTION 2007Pages: 1449, PDF Size: 56.82 MB
Page 941 of 1449
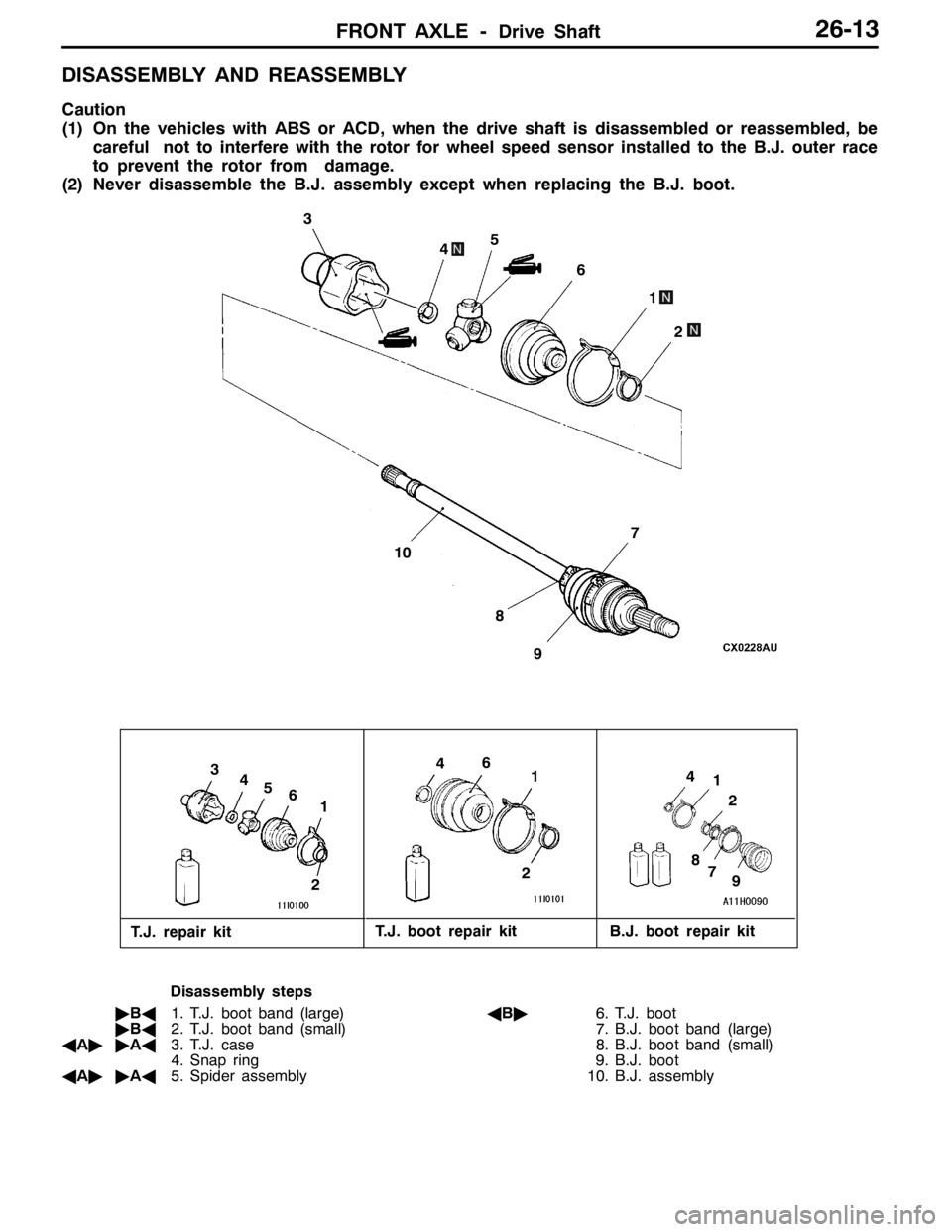
FRONT AXLE -Drive Shaft26-13
DISASSEMBLY AND REASSEMBLY
Caution
(1) On the vehicles with ABS or ACD, when the drive shaft is disassembled or reassembled, be
careful not to interfere with the rotor for wheel speed sensor installed to the B.J. outer race
to prevent the rotor from damage.
(2) Never disassemble the B.J. assembly except when replacing the B.J. boot.
2
6
4
3
5
7
1
4
2
43
61
2
4
51
2
9
10
1
8
8
97
6
T.J. repair kitT.J. boot repair kit B.J. boot repair kit
Disassembly steps
"BA1. T.J. boot band (large)
"BA2. T.J. boot band (small)
AA""AA3. T.J. case
4. Snap ring
AA""AA5. Spider assemblyAB"6. T.J. boot
7. B.J. boot band (large)
8. B.J. boot band (small)
9. B.J. boot
10. B.J. assembly
Page 949 of 1449
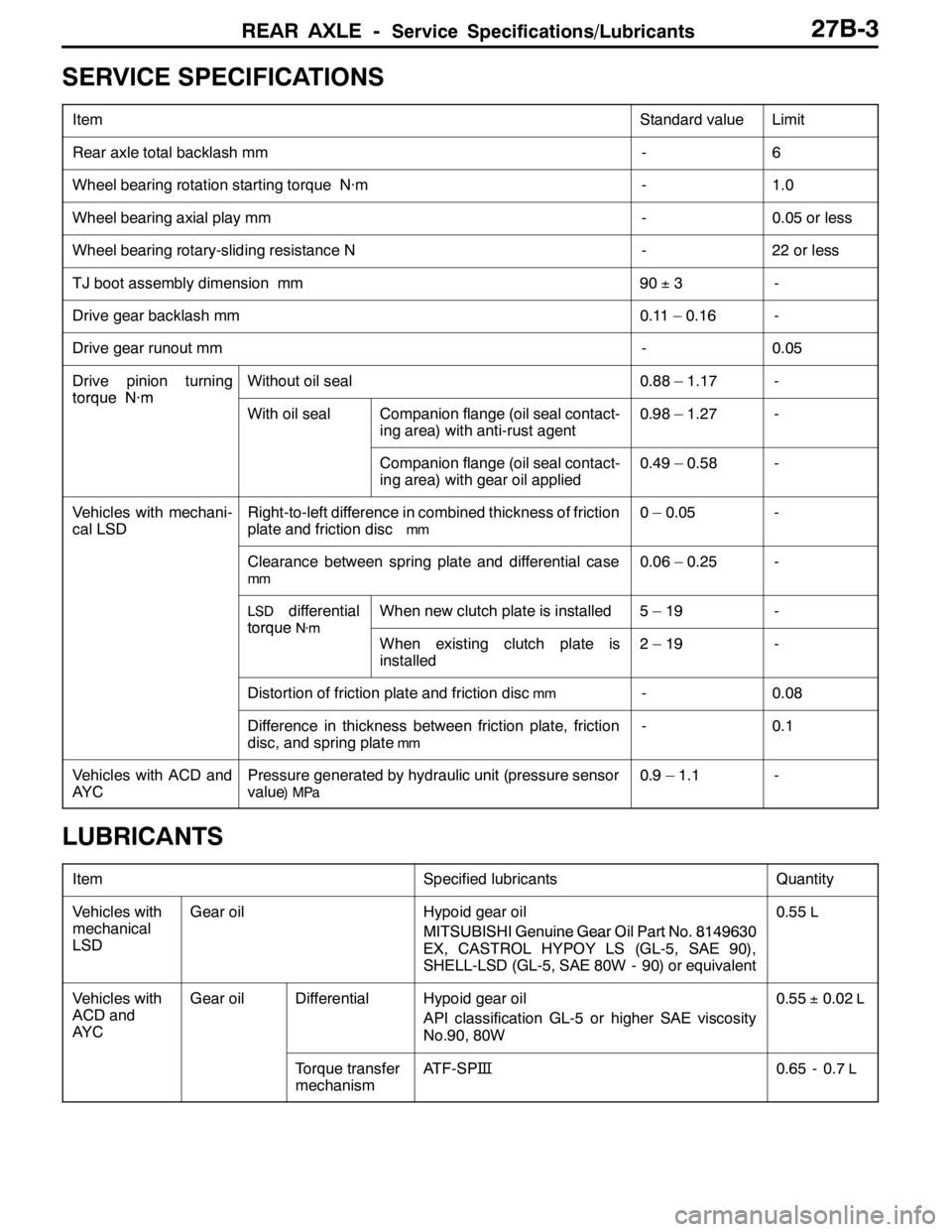
REAR AXLE -Service Specifications/Lubricants27B-3
SERVICE SPECIFICATIONS
ItemStandard valueLimit
Rear axle total backlash mm-6
Wheel bearing rotation starting torque N·m-1.0
Wheel bearing axial play mm-0.05 or less
Wheel bearing rotary-sliding resistance N-22 or less
TJ boot assembly dimension mm90±3-
Drive gear backlash mm0.11 – 0.16-
Drive gear runout mm-0.05
Drive pinion turning
torqueN·m
Without oil seal0.88 – 1.17-
torqueN·m
With oil sealCompanion flange (oil seal contact-
ing area) with anti-rust agent0.98 – 1.27-
Companion flange (oil seal contact-
ing area) with gear oil applied0.49 – 0.58-
Vehicles with mechani-
cal LSDRight-to-left difference in combined thickness of friction
plate and friction disc
mm
0 – 0.05-
Clearance between spring plate and differential case
mm
0.06 – 0.25-
LSDdifferential
torqueN·m
When new clutch plate is installed5–19-
torqueN·m
When existing clutch plate is
installed2–19-
Distortion of friction plate and friction discmm-0.08
Difference in thickness between friction plate, friction
disc, and spring plate
mm
-0.1
Vehicles with ACD and
AY CPressure generated by hydraulic unit (pressure sensor
value
)MPa
0.9 – 1.1-
LUBRICANTS
ItemSpecified lubricantsQuantity
Vehicles with
mechanical
S
Gear oilHypoid gear oil
MITSUBISHI Genuine Gear Oil Part No. 81496300.55L
LSDMITSUBISHIGenuineGearOilPartNo.8149630
EX, CASTROL HYPOY LS (GL-5, SAE 90),
SHELL-LSD (GL-5, SAE 80W - 90) or equivalent
Vehicles with
ACD and
AY CGear oilDifferentialHypoid gear oil
API classification GL-5 or higher SAE viscosity
No.90, 80W0.55±0.02L
Torque transfer
mechanismATF-SP™0.65 - 0.7L
Page 955 of 1449
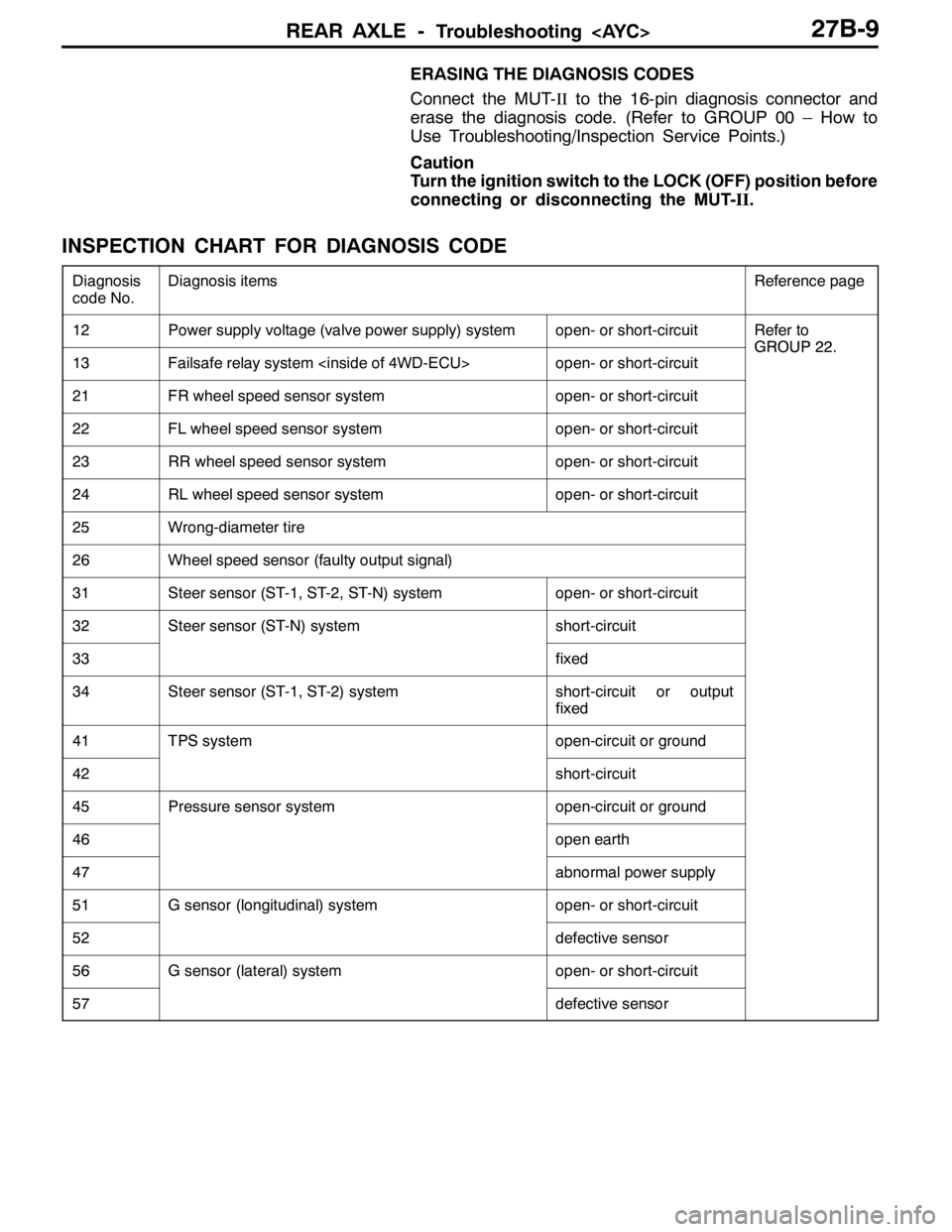
REAR AXLE -Troubleshooting
ERASING THE DIAGNOSIS CODES
Connect the MUT-IIto the 16-pin diagnosis connector and
erase the diagnosis code. (Refer to GROUP 00 – How to
Use Troubleshooting/Inspection Service Points.)
Caution
Turn the ignition switch to the LOCK (OFF) position before
connecting or disconnecting the MUT-II.
INSPECTION CHART FOR DIAGNOSIS CODE
Diagnosis
code No.Diagnosis itemsReference page
12Power supply voltage (valve power supply) systemopen- or short-circuitRefer to
GROUP22
13Failsafe relay system
GROUP22.
21FR wheel speed sensor systemopen- or short-circuit
22FL wheel speed sensor systemopen- or short-circuit
23RR wheel speed sensor systemopen- or short-circuit
24RL wheel speed sensor systemopen- or short-circuit
25Wrong-diameter tire
26Wheel speed sensor (faulty output signal)
31Steer sensor (ST-1, ST-2, ST-N) systemopen- or short-circuit
32Steer sensor (ST-N) systemshort-circuit
33fixed
34Steer sensor (ST-1, ST-2) systemshort-circuit or output
fixed
41TPS systemopen-circuit or ground
42short-circuit
45Pressure sensor systemopen-circuit or ground
46open earth
47abnormal power supply
51G sensor (longitudinal) systemopen- or short-circuit
52defective sensor
56G sensor (lateral) systemopen- or short-circuit
57defective sensor
Page 956 of 1449
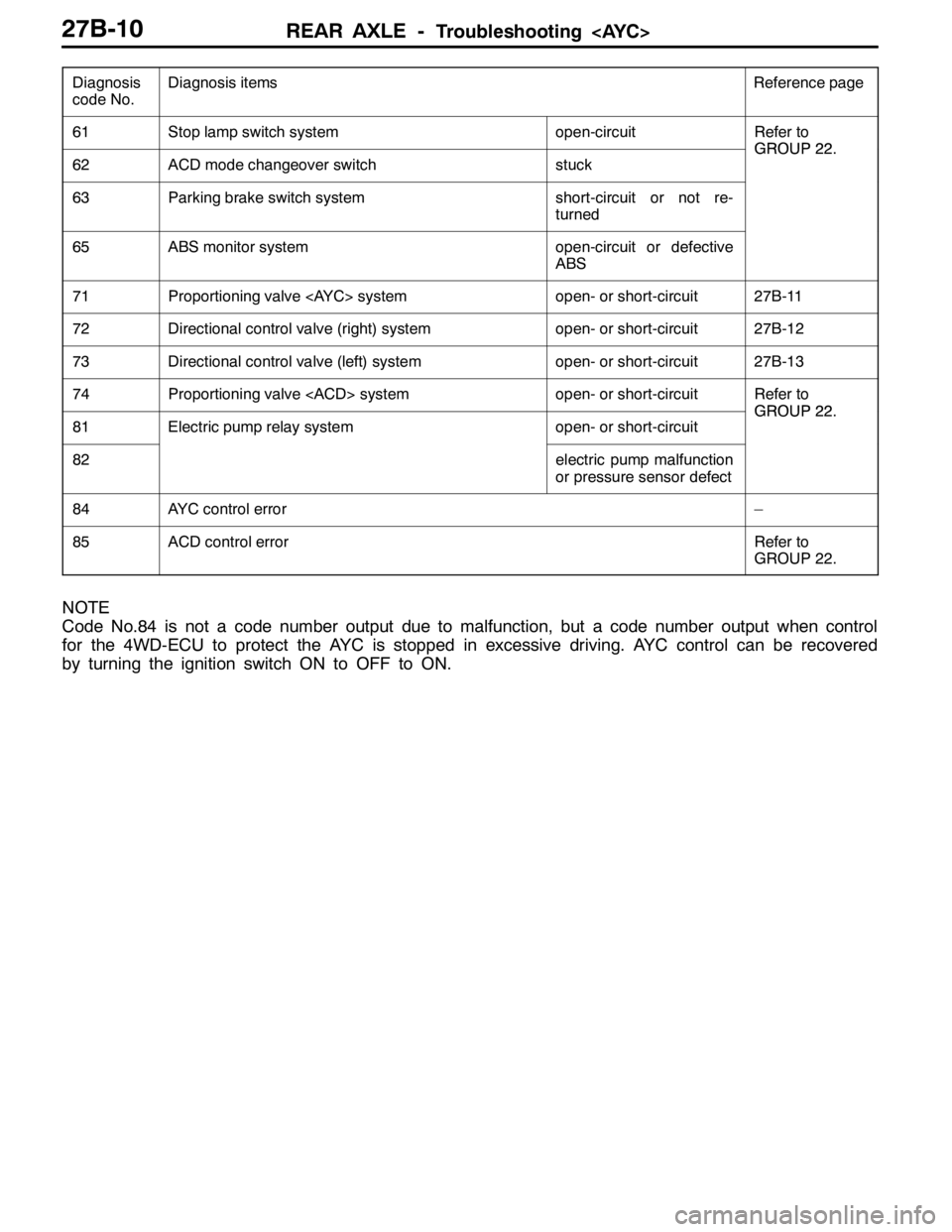
REAR AXLE -Troubleshooting
Diagnosis
code No.Reference page Diagnosis items
61Stop lamp switch systemopen-circuitRefer to
GROUP22
62ACD mode changeover switchstuck
GROUP22.
63Parking brake switch systemshort-circuit or not re-
turned
65ABS monitor systemopen-circuit or defective
ABS
71Proportioning valve
72Directional control valve (right) systemopen- or short-circuit27B-12
73Directional control valve (left) systemopen- or short-circuit27B-13
74Proportioning valve
GROUP22
81Electric pump relay systemopen- or short-circuit
GROUP22.
82electric pump malfunction
or pressure sensor defect
84AYC control error–
85ACD control errorRefer to
GROUP 22.
NOTE
Code No.84 is not a code number output due to malfunction, but a code number output when control
for the 4WD-ECU to protect the AYC is stopped in excessive driving. AYC control can be recovered
by turning the ignition switch ON to OFF to ON.
Page 974 of 1449
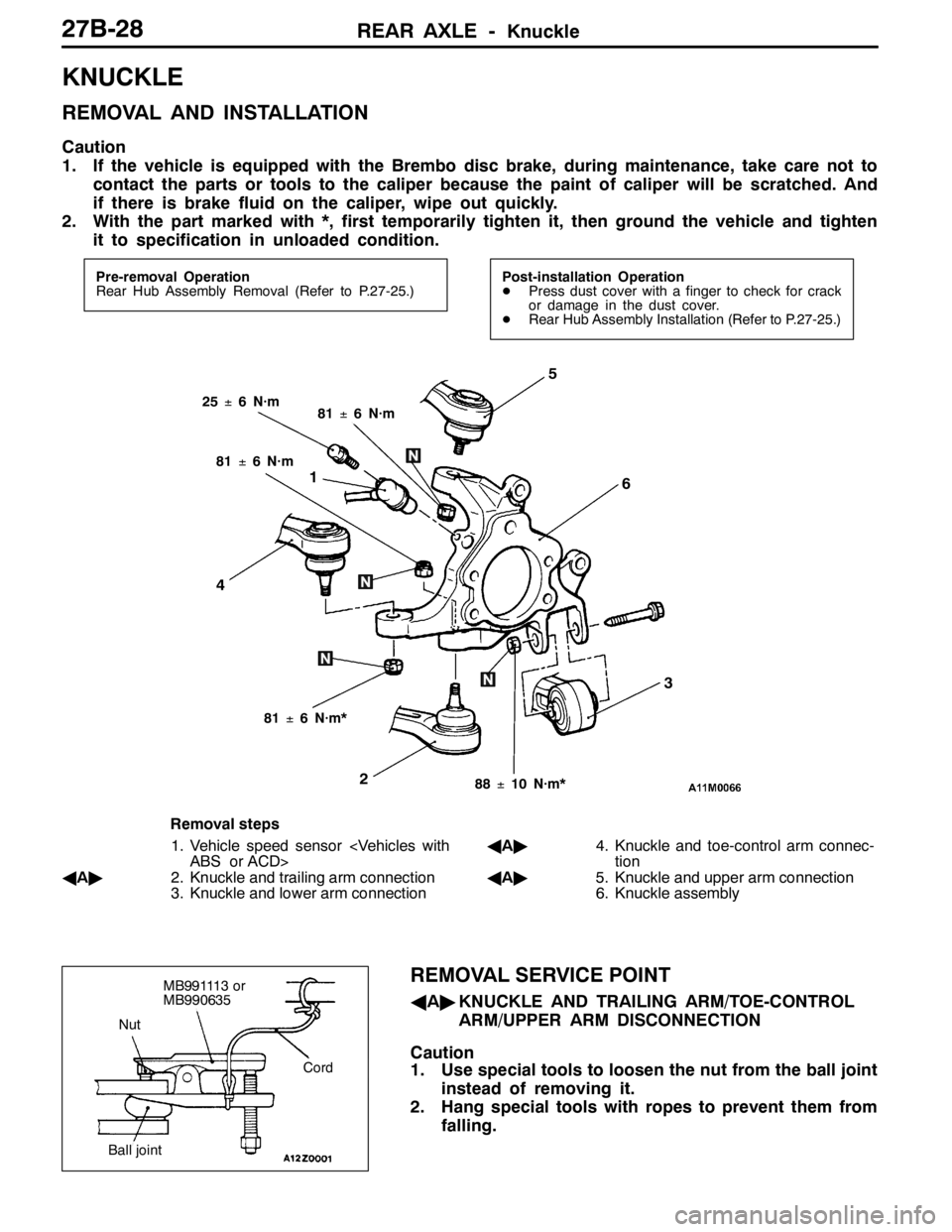
REAR AXLE -Knuckle27B-28
KNUCKLE
REMOVAL AND INSTALLATION
Caution
1. If the vehicle is equipped with the Brembo disc brake, during maintenance, take care not to
contact the parts or tools to the caliper because the paint of caliper will be scratched. And
if there is brake fluid on the caliper, wipe out quickly.
2. With the part marked with *, first temporarily tighten it, then ground the vehicle and tighten
it to specification in unloaded condition.
Pre-removal Operation
Rear Hub Assembly Removal (Refer to P.27-25.)Post-installation Operation
DPress dust cover with a finger to check for crack
or damage in the dust cover.
DRear Hub Assembly Installation (Refer to P.27-25.)
1
2
3
4
5
6
25±6 N·m81±6 N·m
81±6 N·m*
88±10 N·m*
81±6 N·m
Removal steps
1. Vehicle speed sensor
AA"2. Knuckle and trailing arm connection
3. Knuckle and lower arm connectionAA"4. Knuckle and toe-control arm connec-
tion
AA"5. Knuckle and upper arm connection
6. Knuckle assembly
REMOVAL SERVICE POINT
AA"KNUCKLE AND TRAILING ARM/TOE-CONTROL
ARM/UPPER ARM DISCONNECTION
Caution
1. Use special tools to loosen the nut from the ball joint
instead of removing it.
2. Hang special tools with ropes to prevent them from
falling.
Nut
Cord
Ball joint
MB991113 or
MB990635
Page 975 of 1449
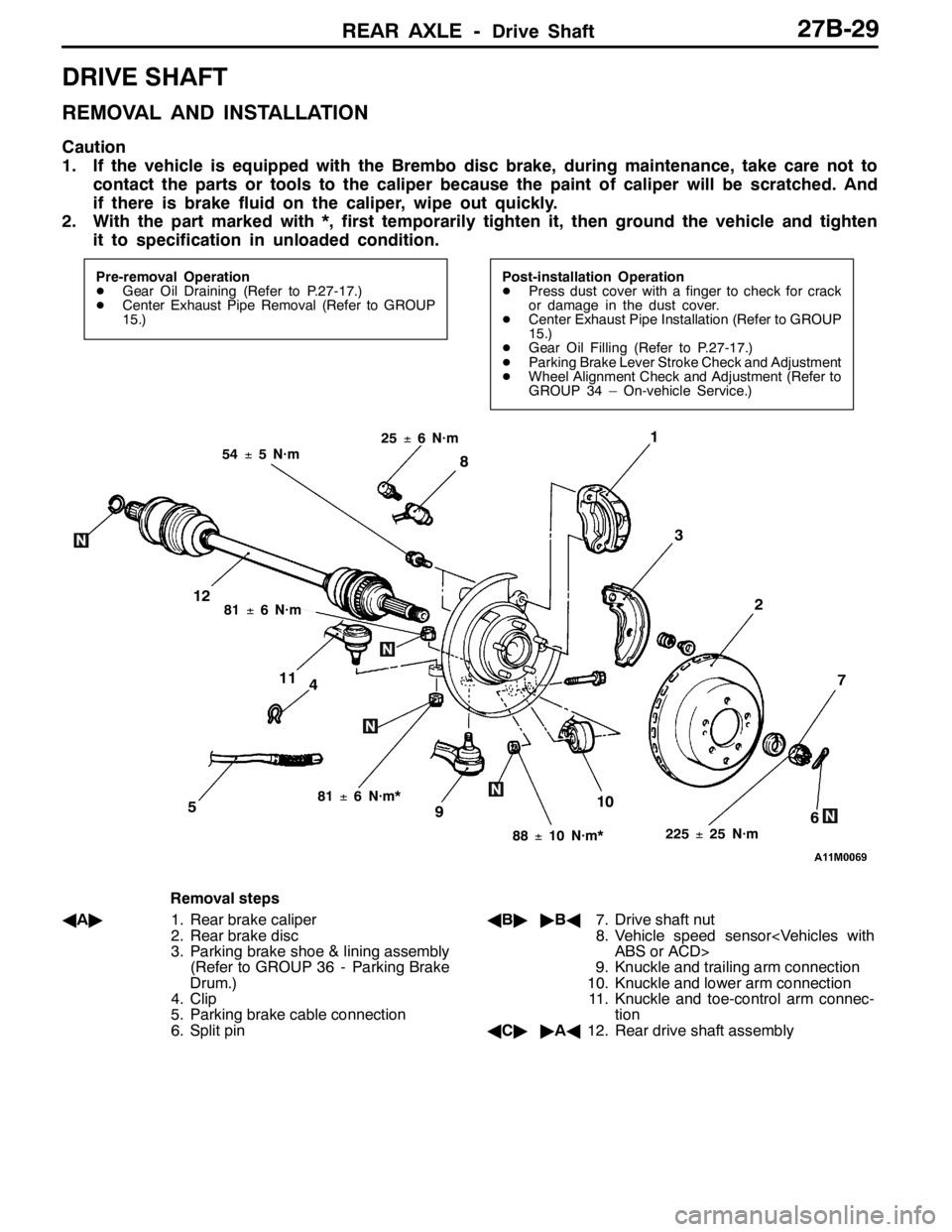
REAR AXLE -Drive Shaft27B-29
DRIVE SHAFT
REMOVAL AND INSTALLATION
Caution
1. If the vehicle is equipped with the Brembo disc brake, during maintenance, take care not to
contact the parts or tools to the caliper because the paint of caliper will be scratched. And
if there is brake fluid on the caliper, wipe out quickly.
2. With the part marked with *, first temporarily tighten it, then ground the vehicle and tighten
it to specification in unloaded condition.
Pre-removal Operation
DGear Oil Draining (Refer to P.27-17.)
DCenter Exhaust Pipe Removal (Refer to GROUP
15.)Post-installation Operation
DPress dust cover with a finger to check for crack
or damage in the dust cover.
DCenter Exhaust Pipe Installation (Refer to GROUP
15.)
DGear Oil Filling (Refer to P.27-17.)
DParking Brake Lever Stroke Check and Adjustment
DWheel Alignment Check and Adjustment (Refer to
GROUP 34 – On-vehicle Service.)
4
1
3
7
6510
2
8
9
11
12
225±25 N·m
54±5 N·m
88±10 N·m*
81±6 N·m*
81±6 N·m
25±6 N·m
Removal steps
AA"1. Rear brake caliper
2. Rear brake disc
3. Parking brake shoe & lining assembly
(Refer to GROUP 36 - Parking Brake
Drum.)
4. Clip
5. Parking brake cable connection
6. Split pinAB""BA7. Drive shaft nut
8. Vehicle speed sensor
9. Knuckle and trailing arm connection
10. Knuckle and lower arm connection
11. Knuckle and toe-control arm connec-
tion
AC""AA12. Rear drive shaft assembly
Page 978 of 1449
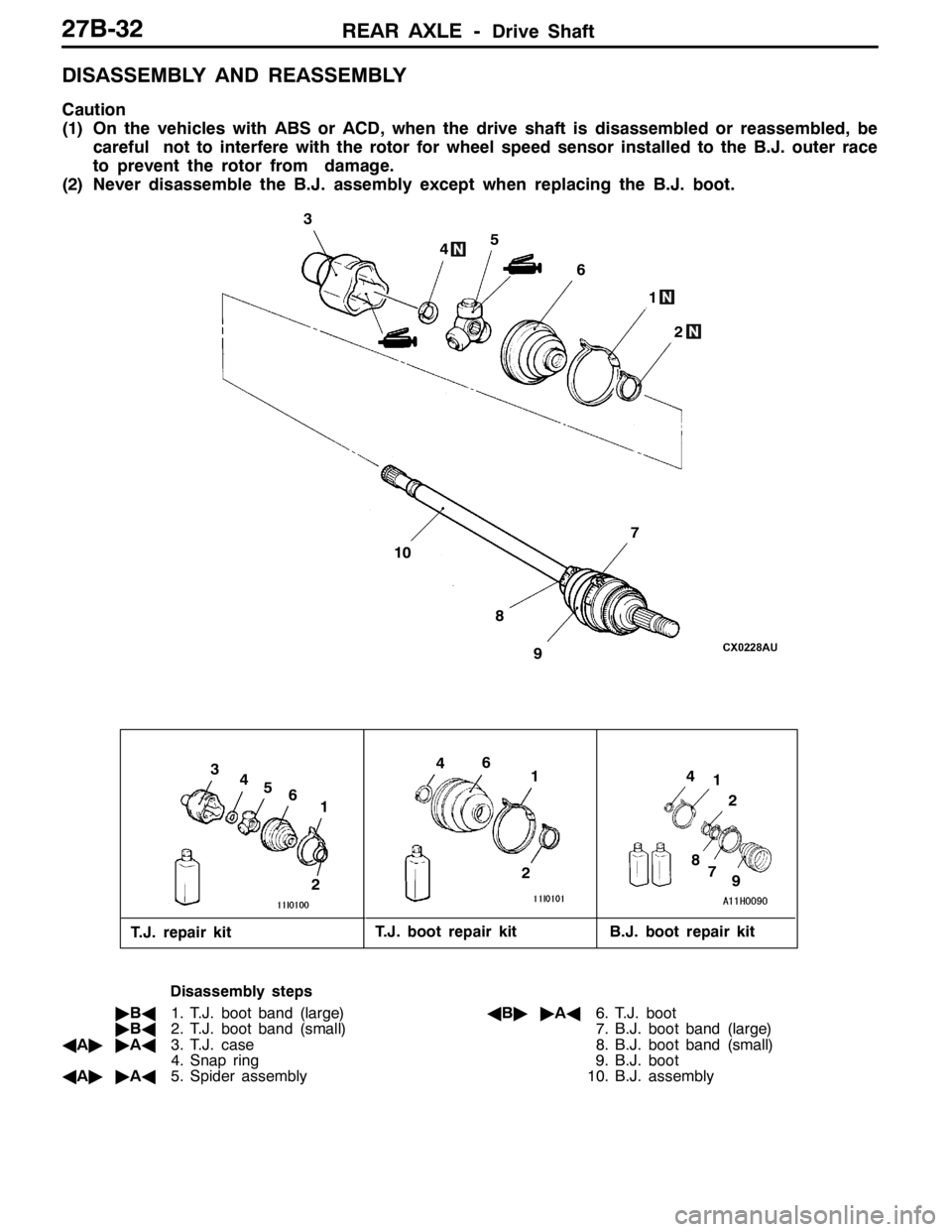
REAR AXLE -Drive Shaft27B-32
DISASSEMBLY AND REASSEMBLY
Caution
(1) On the vehicles with ABS or ACD, when the drive shaft is disassembled or reassembled, be
careful not to interfere with the rotor for wheel speed sensor installed to the B.J. outer race
to prevent the rotor from damage.
(2) Never disassemble the B.J. assembly except when replacing the B.J. boot.
2
6
4
3
5
7
1
4
2
43
61
2
4
51
2
9
10
1
8
8
97
6
T.J. repair kitT.J. boot repair kit B.J. boot repair kit
Disassembly steps
"BA1. T.J. boot band (large)
"BA2. T.J. boot band (small)
AA""AA3. T.J. case
4. Snap ring
AA""AA5. Spider assemblyAB""AA6. T.J. boot
7. B.J. boot band (large)
8. B.J. boot band (small)
9. B.J. boot
10. B.J. assembly
Page 1032 of 1449
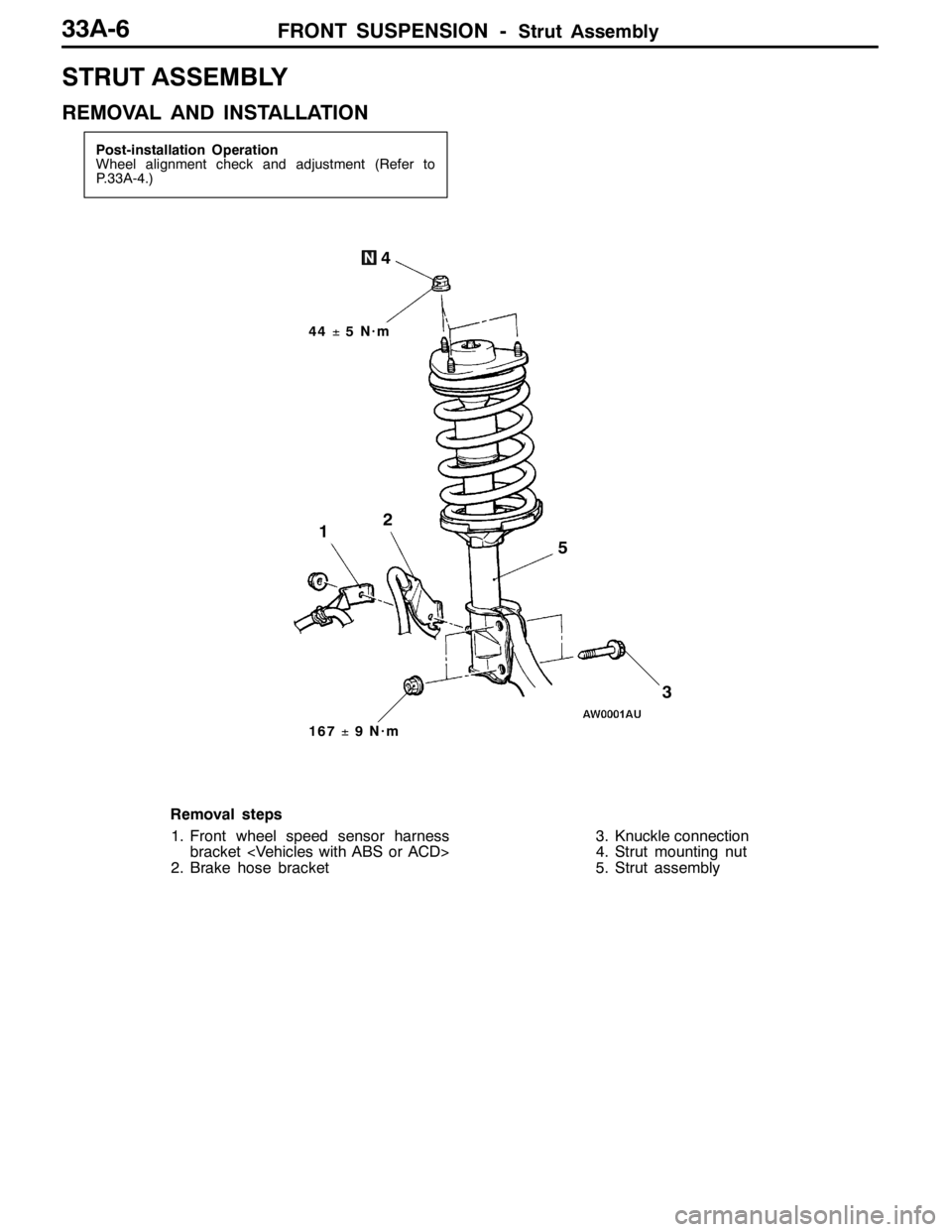
FRONT SUSPENSION -Strut Assembly33A-6
STRUT ASSEMBLY
REMOVAL AND INSTALLATION
Post-installation Operation
Wheel alignment check and adjustment (Refer to
P.33A-4.)
44±5N·m
3
21
167±9N·m
4
5
Removal steps
1. Front wheel speed sensor harness
bracket
2. Brake hose bracket3. Knuckle connection
4. Strut mounting nut
5. Strut assembly
Page 1044 of 1449
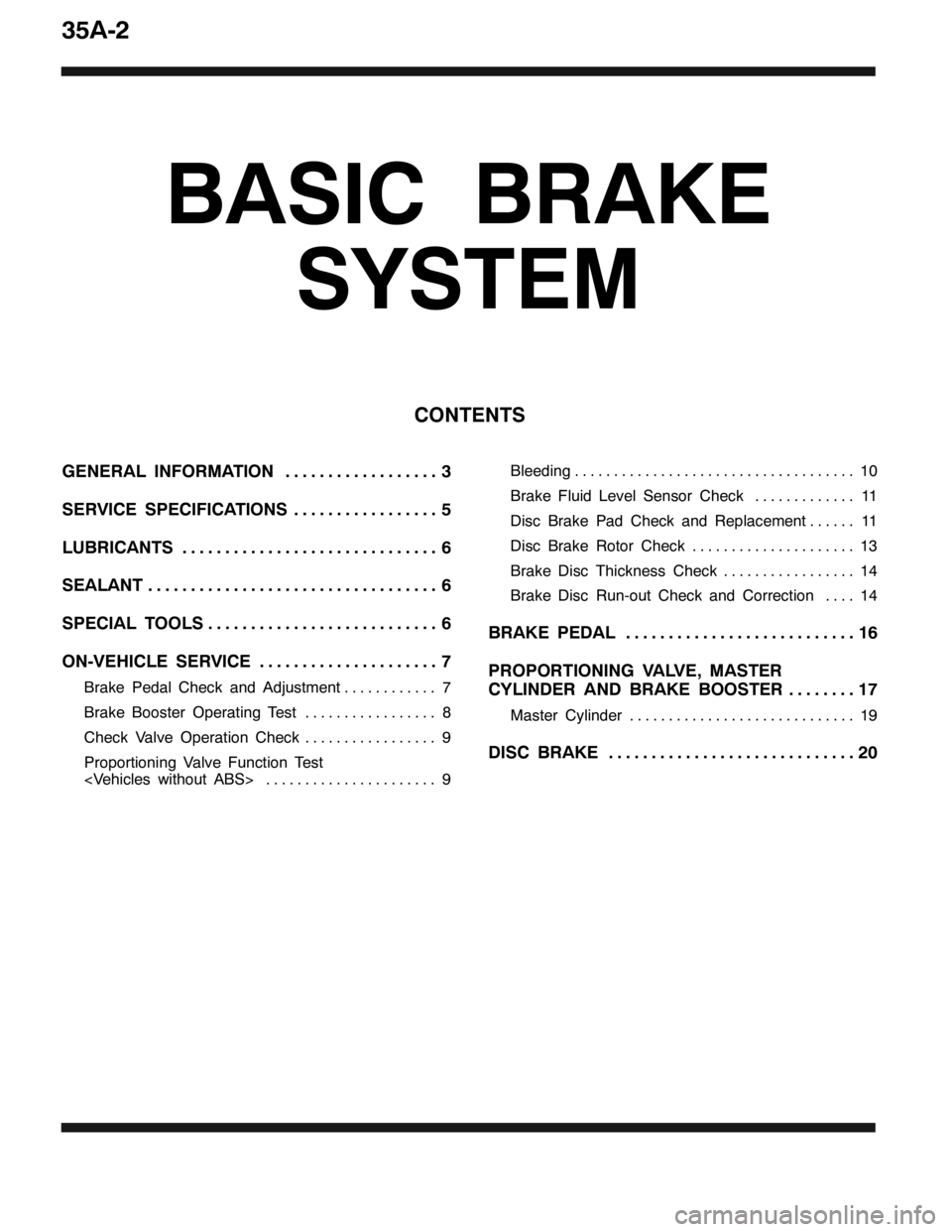
35A-2
BASIC BRAKE
SYSTEM
CONTENTS
GENERAL INFORMATION 3..................
SERVICE SPECIFICATIONS 5.................
LUBRICANTS 6..............................
SEALANT 6..................................
SPECIAL TOOLS 6...........................
ON-VEHICLE SERVICE 7.....................
Brake Pedal Check and Adjustment 7............
Brake Booster Operating Test 8.................
Check Valve Operation Check 9.................
Proportioning Valve Function Test
Brake Fluid Level Sensor Check 11.............
Disc Brake Pad Check and Replacement 11......
Disc Brake Rotor Check 13.....................
Brake Disc Thickness Check 14.................
Brake Disc Run-out Check and Correction 14....
BRAKE PEDAL 16...........................
PROPORTIONING VALVE, MASTER
CYLINDER AND BRAKE BOOSTER 17........
Master Cylinder 19.............................
DISC BRAKE 20.............................
Page 1053 of 1449
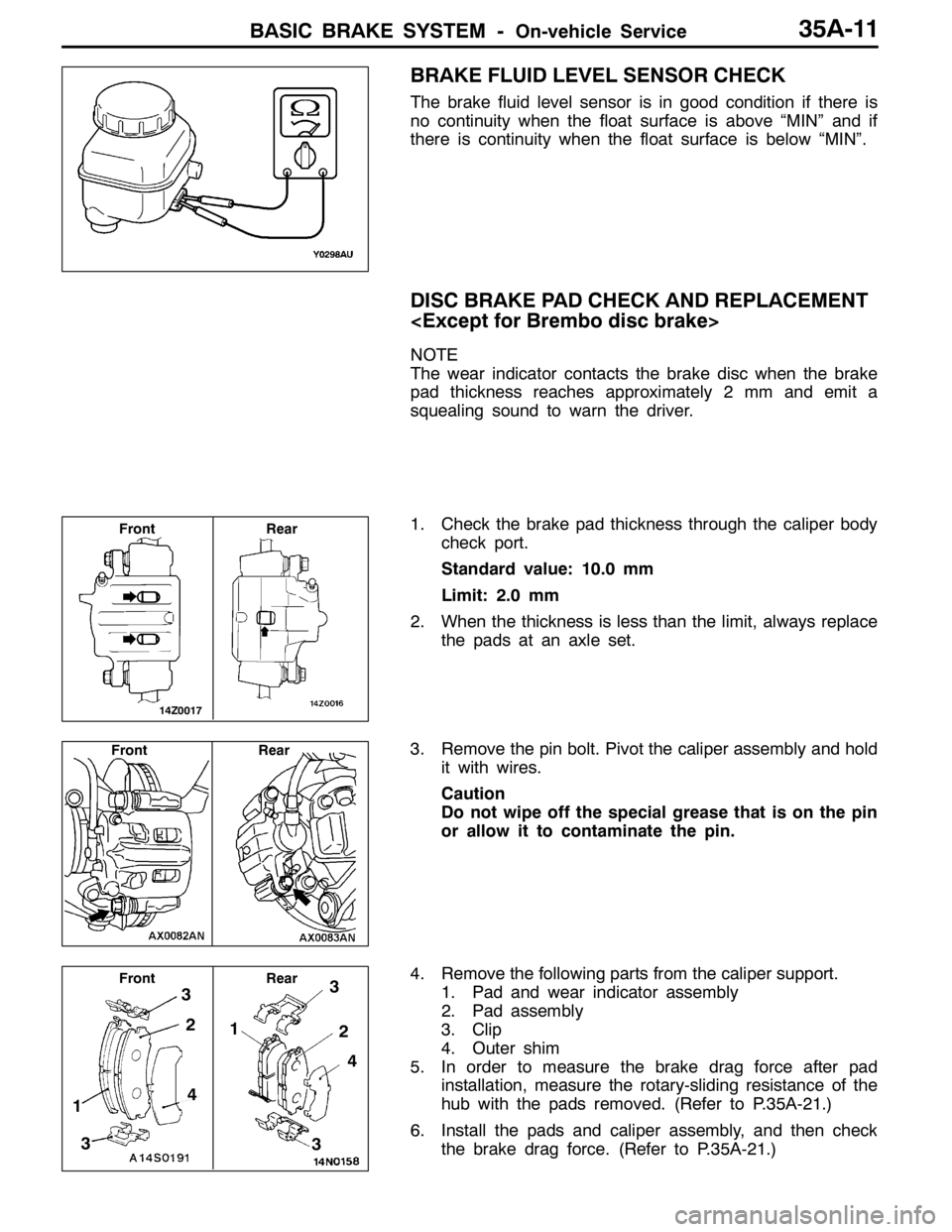
BASIC BRAKE SYSTEM -On-vehicle Service35A-11
BRAKE FLUID LEVEL SENSOR CHECK
The brake fluid level sensor is in good condition if there is
no continuity when the float surface is above “MIN” and if
there is continuity when the float surface is below “MIN”.
DISC BRAKE PAD CHECK AND REPLACEMENT
NOTE
The wear indicator contacts the brake disc when the brake
pad thickness reaches approximately 2 mm and emit a
squealing sound to warn the driver.
1. Check the brake pad thickness through the caliper body
check port.
Standard value: 10.0 mm
Limit: 2.0 mm
2. When the thickness is less than the limit, always replace
the pads at an axle set.
3. Remove the pin bolt. Pivot the caliper assembly and hold
it with wires.
Caution
Do not wipe off the special grease that is on the pin
or allow it to contaminate the pin.
4. Remove the following parts from the caliper support.
1. Pad and wear indicator assembly
2. Pad assembly
3. Clip
4. Outer shim
5. In order to measure the brake drag force after pad
installation, measure the rotary-sliding resistance of the
hub with the pads removed. (Refer to P.35A-21.)
6. Install the pads and caliper assembly, and then check
the brake drag force. (Refer to P.35A-21.)
14Z0017
Front Rear
Front Rear
Front Rear
12 34
3
1
2 3
4
3