NISSAN PULSAR 1987 Workshop Manual
Manufacturer: NISSAN, Model Year: 1987, Model line: PULSAR, Model: NISSAN PULSAR 1987Pages: 238, PDF Size: 28.91 MB
Page 131 of 238
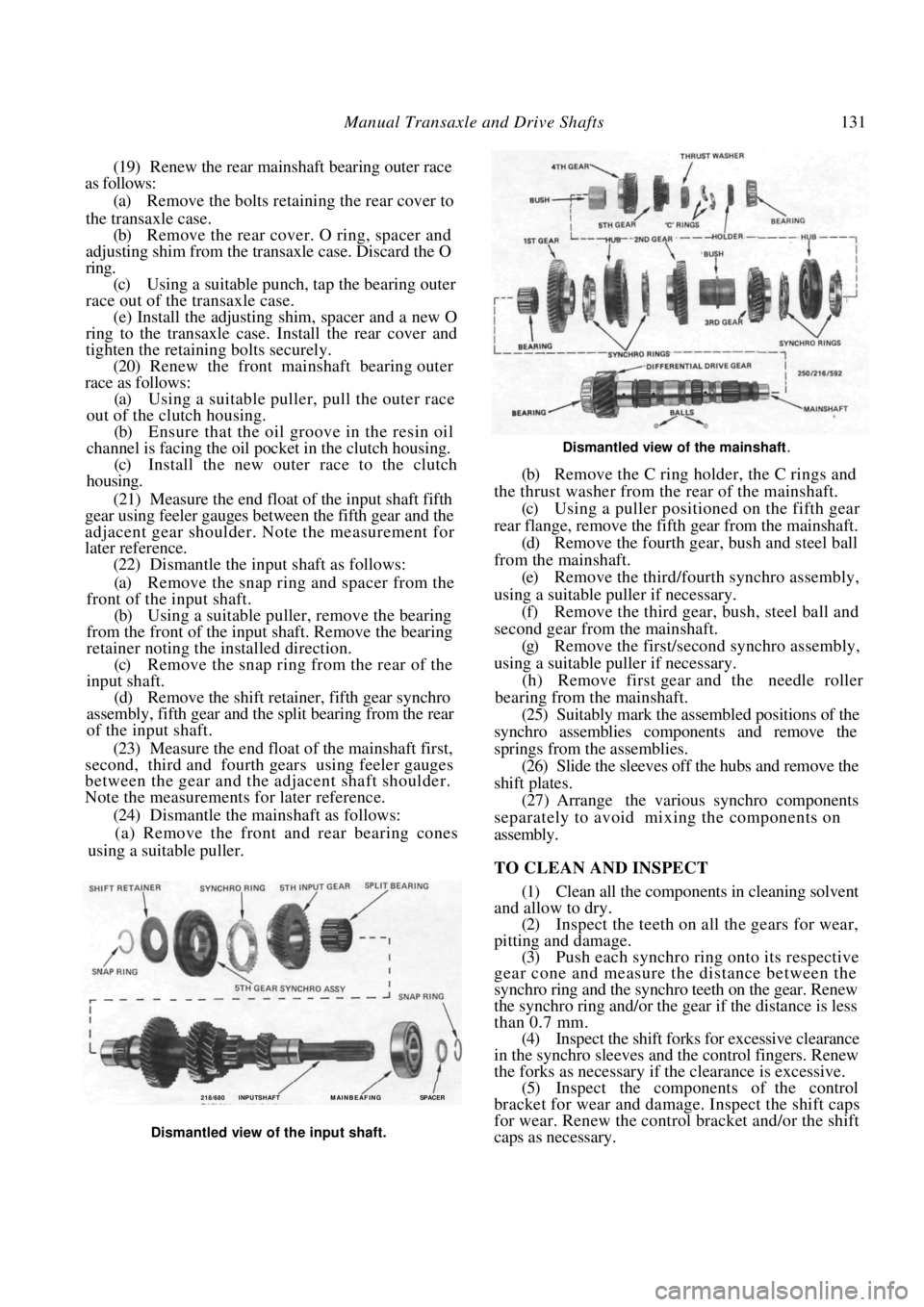
Manual Transaxle and Drive Shafts 131
(19) Renew the rear mainshaft bearing outer race
as follows:
(a) Remove the bolts retaining the rear cover to
the transaxle case. (b) Remove the rear cover. O ring, spacer and
adjusting shim from the transaxle case. Discard the O
ring. (c) Using a suitable punch, tap the bearing outer
race out of the transaxle case. (e) Install the adjusting shim, spacer and a new O
ring to the transaxle case. Install the rear cover and
tighten the retain ing bolts securely.
(20) Renew the front mainshaft bearing outer
race as follows:
(a) Using a suitable puller, pull the outer race
out of the clutch housing.
(b) Ensure that the oil groove in the resin oil
channel is facing the oil pocket in the clutch housing. (c) Install the new outer race to the clutch
housing.
(21) Measure the end float of the input shaft fifth
gear using feeler gauges betw een the fifth gear and the
adjacent gear shoulder. Note the measurement for
later reference.
(22) Dismantle the input shaft as follows:
(a) Remove the snap ring and spacer from the
front of the input shaft. (b) Using a suitable puller, remove the bearing
from the front of the input shaft. Remove the bearing
retainer noting the installed direction. (c) Remove the snap ring from the rear of the
input shaft. (d) Remove the shift retainer, fifth gear synchro
assembly, fifth gear and th e split bearing from the rear
of the input shaft.
(23) Measure the end float of the mainshaft first,
second, third and fourth gears using feeler gauges
between the gear and the adjacent shaft shoulder.
Note the measurements for later reference.
(24) Dismantle the mainshaft as follows:
(a) Remove the front and rear bearing cones
using a suitable puller.
Dismantled view of the mainshaft.
(b) Remove the C ring holder, the C rings and
the thrust washer from the rear of the mainshaft. (c) Using a puller positioned on the fifth gear
rear flange, remove the fifth gear from the mainshaft. (d) Remove the fourth gear , bush and steel ball
from the mainshaft. (e) Remove the third/fourth synchro assembly,
using a suitable puller if necessary. (f) Remove the third gear, bush, steel ball and
second gear from the mainshaft. (g) Remove the first/second synchro assembly,
using a suitable puller if necessary. (h) Remove first gear and the needle roller
bearing from the mainshaft.
(25) Suitably mark the assembled positions of the
synchro assemblies components and remove the
springs from the assemblies.
(26) Slide the sleeves off the hubs and remove the
shift plates.
(27) Arrange the various synchro components
separately to avoid mixing the components on
assembly.
TO CLEAN AND INSPECT
(1) Clean all the components in cleaning solvent
and allow to dry.
(2) Inspect the teeth on all the gears for wear,
pitting and damage. (3) Push each synchro ring onto its respective
gear cone and measure the distance between the
synchro ring and the synchro teeth on the gear. Renew
the synchro ring and/or the gear if the distance is less
than 0.7 mm.
(4) Inspect the shift forks for excessive clearance
in the synchro sleeves and the control fingers. Renew
the forks as necessary if the clearance is excessive. (5) Inspect the components of the control
bracket for wear and damage. Inspect the shift caps
for wear. Renew the control bracket and/or the shift
caps as necessary.
218/680 INPUTSHAFT M AI N B E AF I N G SPACER
Dismantled view of the input shaft.
Page 132 of 238
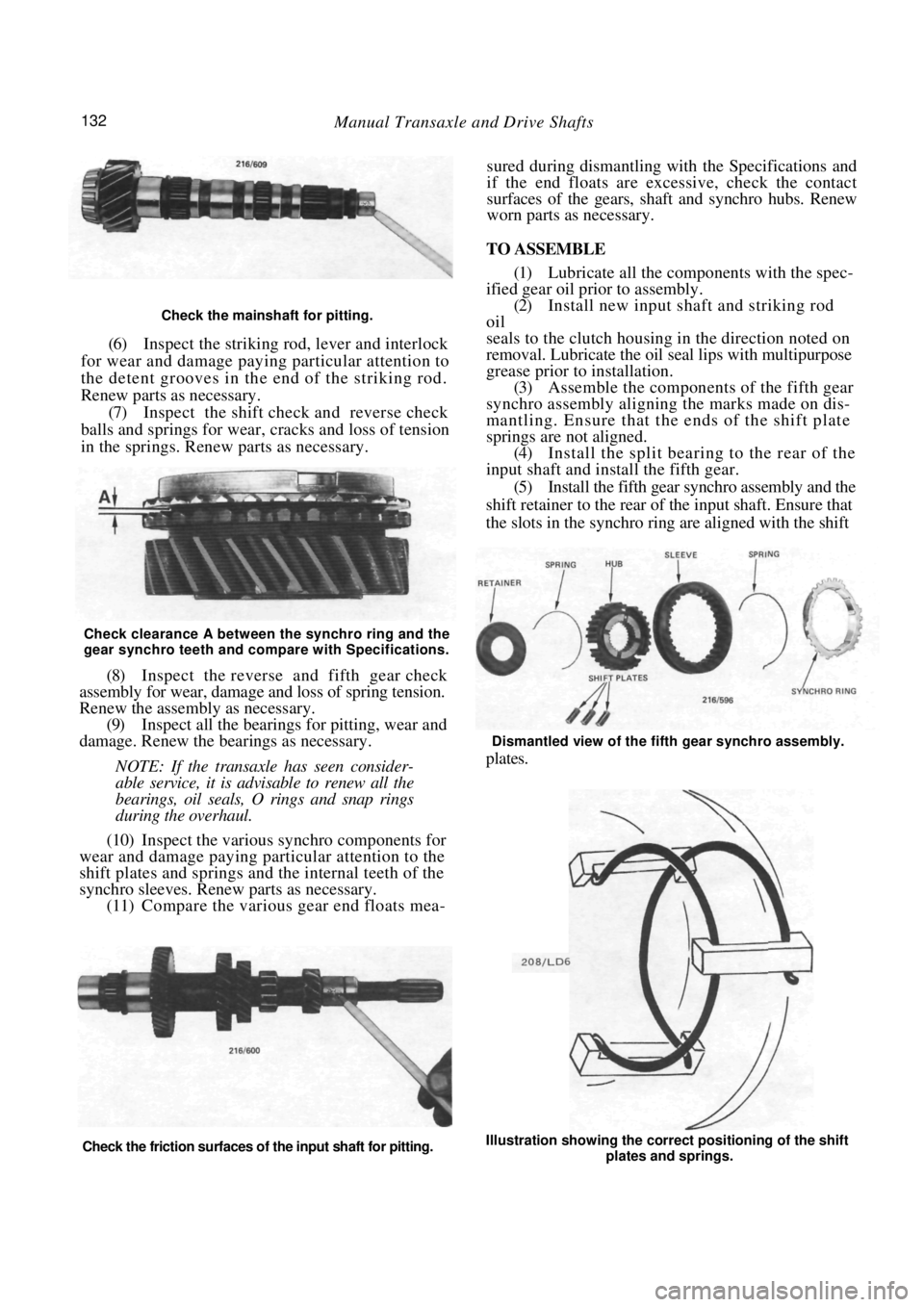
132 Manual Transaxle and Drive Shafts
Check the mainshaft for pitting.
(6) Inspect the striking rod, lever and interlock
for wear and damage paying particular attention to
the detent grooves in the end of the striking rod.
Renew parts as necessary. (7) Inspect the shift check and reverse check
balls and springs for wear, cracks and loss of tension
in the springs. Renew parts as necessary.
Check clearance A between the synchro ring and the
gear synchro teeth and compare with Specifications.
(8) Inspect the reverse and fifth gear check
assembly for wear, damage and loss of spring tension.
Renew the assembly as necessary. (9) Inspect all the bearings for pitting, wear and
damage. Renew the bearings as necessary.
NOTE: If the transaxle has seen consider-
able service, it is advisable to renew all the
bearings, oil seals, O rings and snap rings
during the overhaul.
(10) Inspect the various synchro components for
wear and damage paying par ticular attention to the
shift plates and springs and the internal teeth of the
synchro sleeves. Renew parts as necessary. (11) Compare the various gear end floats mea- sured during dismantling with the Specifications and
if the end floats are excessive, check the contact
surfaces of the ge
ars, shaft and synchro hubs. Renew
worn parts as necessary.
TO ASSEMBLE
(1) Lubricate all the components with the spec-
ified gear oil prior to assembly. (2) Install new input shaft and striking rod
oil
seals to the clutch housing in the direction noted on
removal. Lubricate the oil seal lips with multipurpose
grease prior to installation. (3) Assemble the components of the fifth gear
synchro assembly aligning the marks made on dis-
mantling. Ensure that the ends of the shift plate
springs are not aligned.
(4) Install the split bearing to the rear of the
input shaft and install the fifth gear.
(5) Install the fifth gear sy nchro assembly and the
shift retainer to the rear of the input shaft. Ensure that
the slots in the synchro ring are aligned with the shift
plates.
Check the friction surfaces of the input shaft for pitting. Dismantled view of the fifth gear synchro assembly.
Illustration showing the correct positioning of the shift plates and springs.
Page 133 of 238
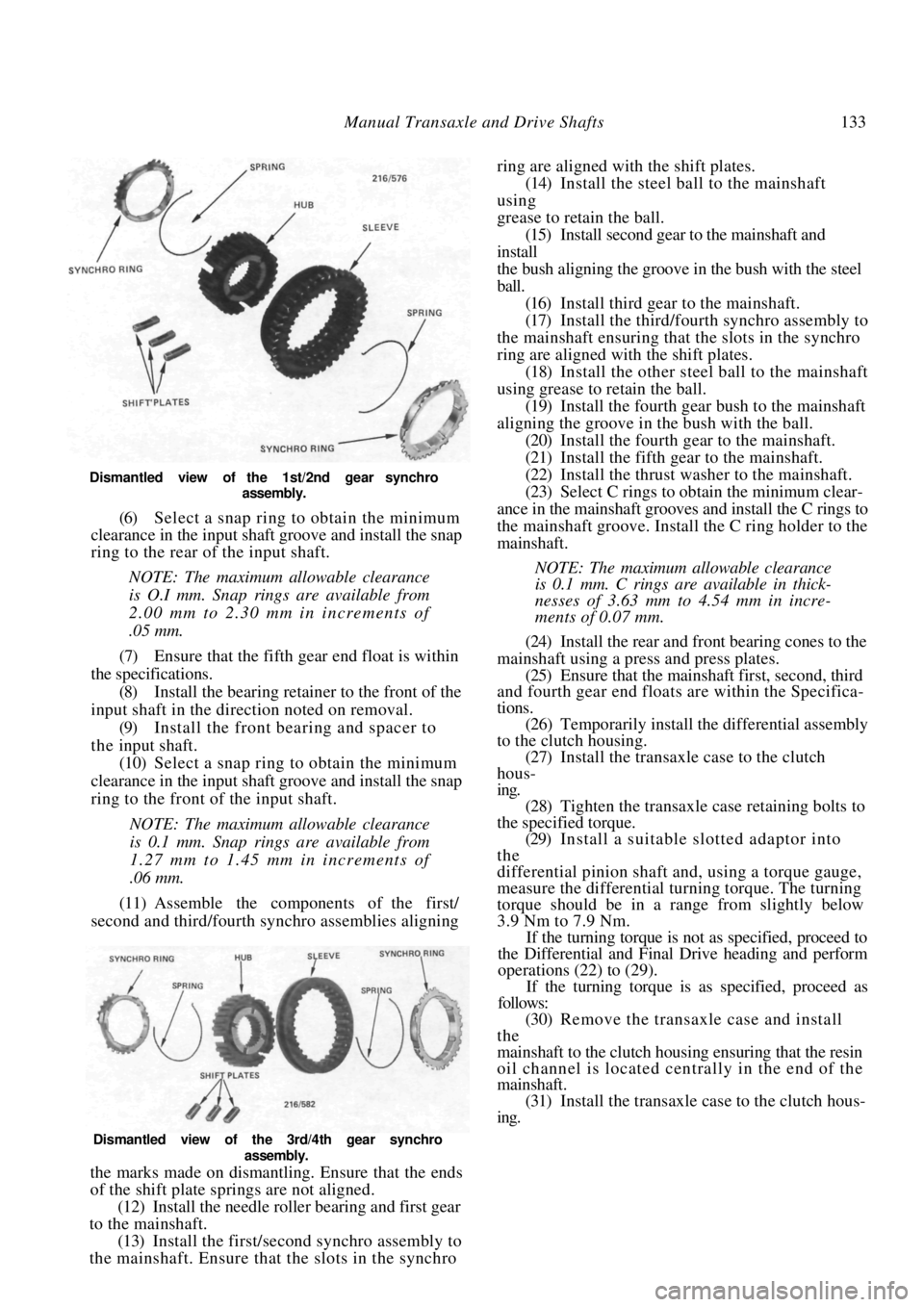
Manual Transaxle and Drive Shafts 133
Dismantled view of the 1st/2nd gear synchro assembly.
(6) Select a snap ring to obtain the minimum
clearance in the input shaft groove and install the snap
ring to the rear of the input shaft.
NOTE: The maximum allowable clearance
is O.I mm. Snap rings are available from
2.00 mm to 2.30 mm in increments of
.05 mm.
(7) Ensure that the fifth gear end float is within
the specifications. (8) Install the bearing retain er to the front of the
input shaft in the direction noted on removal.
(9) Install the front bearing and spacer to
the input shaft. (10) Select a snap ring to obtain the minimum
clearance in the input shaft groove and install the snap
ring to the front of the input shaft.
NOTE: The maximum allowable clearance
is 0.1 mm. Snap rings are available from
1.27 mm to 1.45 mm in increments of
.06 mm.
(11) Assemble the components of the first/
second and third/fourth sy nchro assemblies aligning
the marks made on dismantling. Ensure that the ends
of the shift plate springs are not aligned.
(12) Install the needle roller bearing and first gear
to the mainshaft.
(13) Install the firs t/second synchro assembly to
the mainshaft. Ensure that the slots in the synchro ring are aligned with the shift plates.
(14) Install the steel ball to the mainshaft
using
grease to retain the ball. (15) Install second gear to the mainshaft and
install
the bush aligning the groove in the bush with the steel
ball. (16) Install third gear to the mainshaft.
(17) Install the third/fourth synchro assembly to
the mainshaft ensuring that the slots in the synchro
ring are aligned with the shift plates.
(18) Install the other steel ball to the mainshaft
using grease to retain the ball. (19) Install the fourth gear bush to the mainshaft
aligning the groove in the bush with the ball. (20) Install the fourth gear to the mainshaft.
(21) Install the fifth gear to the mainshaft.
(22) Install the thrust washer to the mainshaft.
(23) Select C rings to obtain the minimum clear-
ance in the mainshaft grooves and install the C rings to
the mainshaft groove. Install the C ring holder to the
mainshaft.
NOTE: The maximum allowable clearance
is 0.1 mm. C rings are available in thick-
nesses of 3.63 mm to 4.54 mm in incre-
ments of 0.07 mm.
(24) Install the rear and front bearing cones to the
mainshaft using a press and press plates. (25) Ensure that the mainshaft first, second, third
and fourth gear end floats are within the Specifica-
tions.
(26) Temporarily install the differential assembly
to the clutch housing. (27) Install the transaxle case to the clutch
hous-
ing. (28) Tighten the transaxle case retaining bolts to
the specified torque. (29) Install a suitable slotted adaptor into
the
differential pinion shaft a nd, using a torque gauge,
measure the differential tu rning torque. The turning
torque should be in a range from slightly below
3.9 Nm to 7.9 Nm. If the turning torque is not as specified, proceed to
the Differential and Final Drive heading and perform
operations (22) to (29).
If the turning torque is as specified, proceed as
follows:
(30) Remove the transaxle case and install
the
mainshaft to the clutch housing ensuring that the resin
oil channel is located centrally in the end of the
mainshaft. (31) Install the transaxle case to the clutch hous-
ing.
Dismantled view of the 3rd/4th gear synchro
assembly.
Page 134 of 238
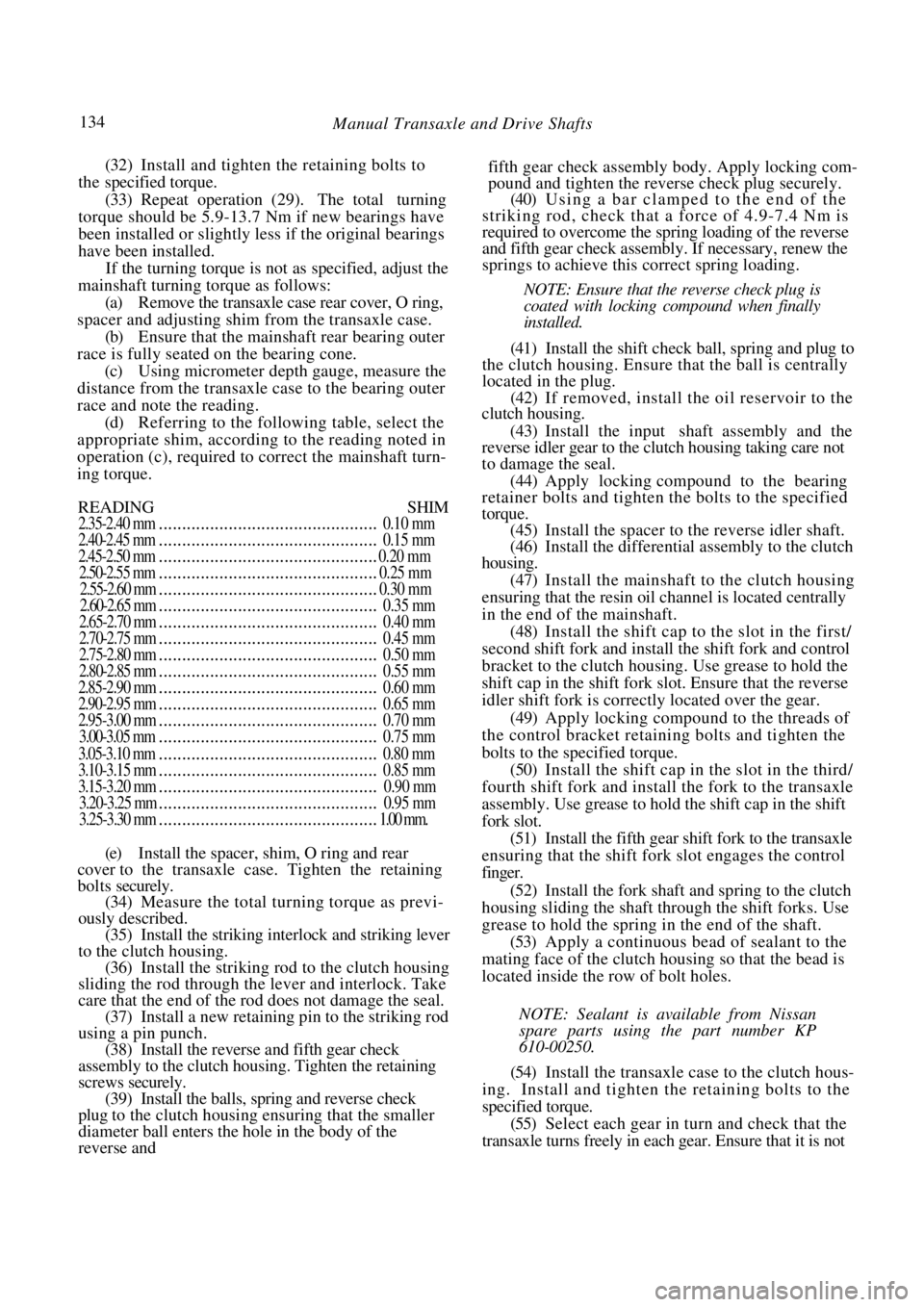
134 Manual Transaxle and Drive Shafts
(32) Install and tighten the retaining bolts to
the specified torque.
(33) Repeat operation (29). The total turning
torque should be 5.9-13.7 Nm if new bearings have
been installed or slightly l ess if the original bearings
have been installed. If the turning torque is no t as specified, adjust the
mainshaft turning torque as follows:
(a) Remove the transaxle case rear cover, O ring,
spacer and adjusting shim from the transaxle case.
(b) Ensure that the mainsh aft rear bearing outer
race is fully seated on the bearing cone. (c) Using micrometer depth gauge, measure the
distance from the transaxle case to the bearing outer
race and note the reading. (d) Referring to the following table, select the
appropriate shim, according to the reading noted in
operation (c), required to correct the mainshaft turn-
ing torque.
READING SHIM
2.35-2.40 mm............................................... 0.10 mm
2.40-2.45 mm............................................... 0.15 mm
2.45-2.50 mm...............................................0.20 mm
2.50-2.55 mm...............................................0.25 mm
2.55-2.60 mm...............................................0.30 mm
2.60-2.65 mm............................................... 0.35 mm
2.65-2.70 mm............................................... 0.40 mm
2.70-2.75 mm............................................... 0.45 mm
2.75-2.80 mm............................................... 0.50 mm
2.80-2.85 mm............................................... 0.55 mm
2.85-2.90 mm............................................... 0.60 mm
2.90-2.95 mm............................................... 0.65 mm
2.95-3.00 mm............................................... 0.70 mm
3.00-3.05 mm............................................... 0.75 mm
3.05-3.10 mm............................................... 0.80 mm
3.10-3.15 mm............................................... 0.85 mm
3.15-3.20 mm............................................... 0.90 mm
3.20-3.25 mm............................................... 0.95 mm
3.25-3.30 mm...............................................1.00 mm.
(e) Install the spacer, shim, O ring and rear
cover to the transaxle case. Tighten the retaining
bolts securely.
(34) Measure the total turning torque as previ-
ously described. (35) Install the striking interlock and striking lever
to the clutch housing. (36) Install the striking ro d to the clutch housing
sliding the rod through the lever and interlock. Take
care that the end of the rod does not damage the seal. (37) Install a new retaining pin to the striking rod
using a pin punch. (38) Install the reverse and fifth gear check
assembly to the clutch housing. Tighten the retaining
screws securely. (39) Install the balls, spring and reverse check
plug to the clutch housing ensuring that the smaller
diameter ball enters the hole in the body of the
reverse and fifth gear check assembly body. Apply locking com-
pound and tighten the reverse check plug securely.
(40) Using a bar clamped to the end of the
striking rod, check that a force of 4.9-7.4 Nm is
required to overcome the spring loading of the reverse
and fifth gear check assembly. If necessary, renew the
springs to achieve this correct spring loading.
NOTE: Ensure that the reverse check plug is
coated with locking compound when finally
installed.
(41) Install the shift check ball, spring and plug to
the clutch housing. Ensure that the ball is centrally
located in the plug.
(42) If removed, install the oil reservoir to the
clutch housing.
(43) Install the input shaft assembly and the
reverse idler gear to the clutch housing taking care not
to damage the seal.
(44) Apply locking compound to the bearing
retainer bolts and tighten the bolts to the specified
torque.
(45) Install the spacer to the reverse idler shaft.
(46) Install the differential assembly to the clutch
housing.
(47) Install the mainshaft to the clutch housing
ensuring that the resin oil ch annel is located centrally
in the end of the mainshaft. (48) Install the shift cap to the slot in the first/
second shift fork and install the shift fork and control
bracket to the clutch housing. Use grease to hold the
shift cap in the shift fork slot. Ensure that the reverse
idler shift fork is correctly located over the gear.
(49) Apply locking compound to the threads of
the control bracket retaining bolts and tighten the
bolts to the specified torque. (50) Install the shift cap in the slot in the third/
fourth shift fork and install the fork to the transaxle
assembly. Use grease to hold the shift cap in the shift
fork slot. (51) Install the fifth gear shift fork to the transaxle
ensuring that the shift fork slot engages the control
finger.
(52) Install the fork shaft an d spring to the clutch
housing sliding the shaft through the shift forks. Use
grease to hold the spring in the end of the shaft. (53) Apply a continuous bead of sealant to the
mating face of the clutch housing so that the bead is
located inside the row of bolt holes.
NOTE: Sealant is available from Nissan
spare parts using the part number KP
610-00250.
(54) Install the transaxle case to the clutch hous-
ing. Install and tighten the retaining bolts to the
specified torque. (55) Select each gear in turn and check that the
transaxle turns freely in each gear. Ensure that it is not
Page 135 of 238
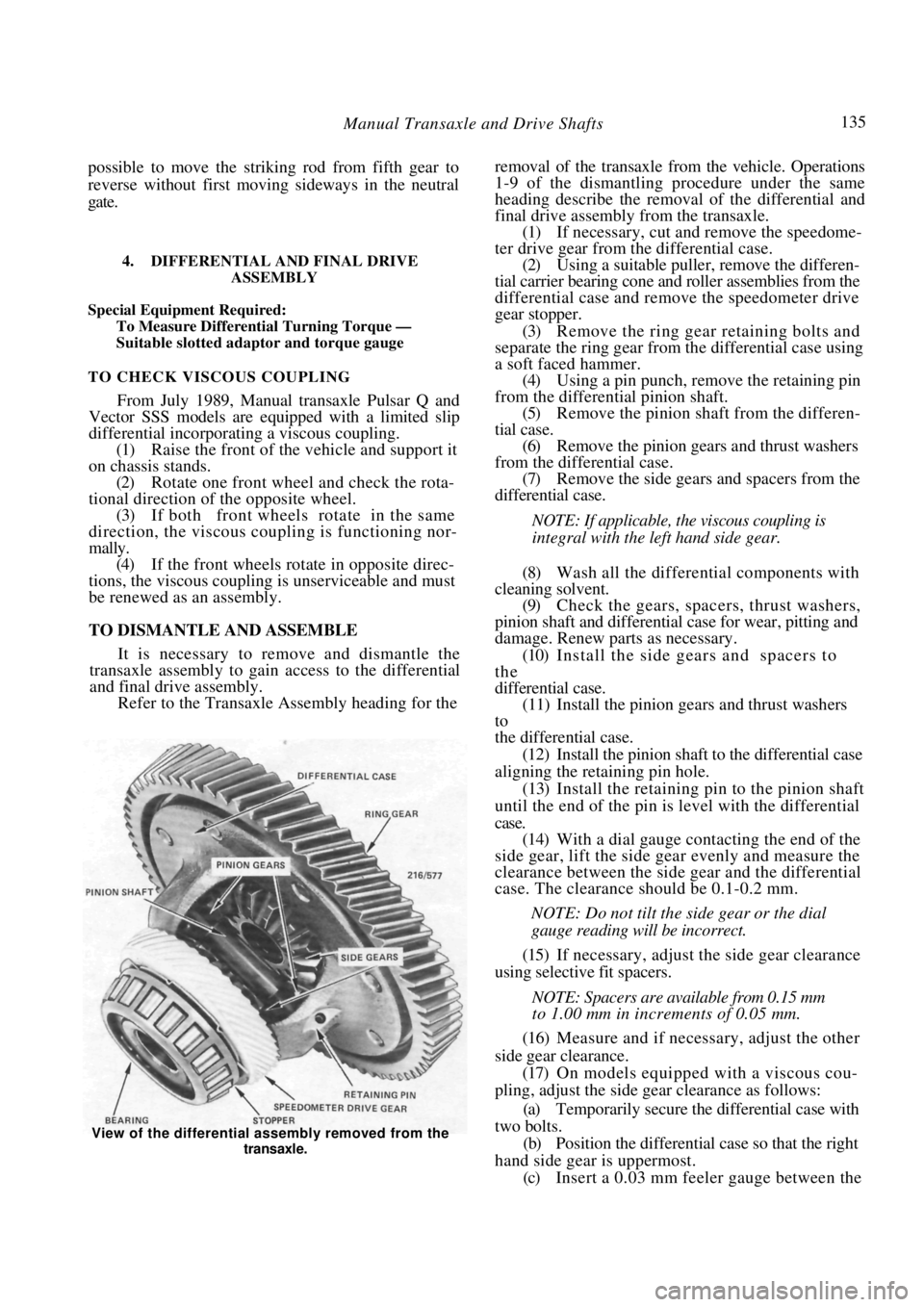
Manual Transaxle and Drive Shafts 135
possible to move the striking rod from fifth gear to
reverse without first moving sideways in the neutral
gate.
4. DIFFERENTIAL AND FINAL DRIVE ASSEMBLY
Special Equipment Required:
To Measure Differential Turning Torque —
Suitable slotted adaptor and torque gauge
TO CHECK VISCOUS COUPLING
From July 1989, Manual transaxle Pulsar Q and
Vector SSS models are equipped with a limited slip
differential incorporating a viscous coupling.
(1) Raise the front of the vehicle and support it
on chassis stands. (2) Rotate one front wheel and check the rota-
tional direction of the opposite wheel. (3) If both front wheels rotate in the same
direction, the viscous coupling is functioning nor-
mally. (4) If the front wheels rota te in opposite direc-
tions, the viscous coupling is unserviceable and must
be renewed as an assembly.
TO DISMANTLE AND ASSEMBLE
It is necessary to remove and dismantle the
transaxle assembly to gain access to the differential
and final drive assembly.
Refer to the Transaxle Assembly heading for the
removal of the transaxle from the vehicle. Operations
1-9 of the dismantling procedure under the same
heading describe the removal of the differential and
final drive assembly from the transaxle.
(1) If necessary, cut and remove the speedome-
ter drive gear from the differential case. (2) Using a suitable puller, remove the differen-
tial carrier bearing cone and roller assemblies from the
differential case and remove the speedometer drive
gear stopper.
(3) Remove the ring gear retaining bolts and
separate the ring gear from the differential case using
a soft faced hammer.
(4) Using a pin punch, remove the retaining pin
from the differential pinion shaft.
(5) Remove the pinion shaft from the differen-
tial case. (6) Remove the pinion gears and thrust washers
from the differential case. (7) Remove the side gears and spacers from the
differential case.
NOTE: If applicable, the viscous coupling is
integral with the left hand side gear.
(8) Wash all the differential components with
cleaning solvent. (9) Check the gears, spacer s, thrust washers,
pinion shaft and differential case for wear, pitting and
damage. Renew parts as necessary.
(10) Install the side gears and spacers to
the
differential case.
(11) Install the pinion gear s and thrust washers
to
the differential case.
(12) Install the pinion shaft to the differential case
aligning the retaining pin hole. (13) Install the retaining pin to the pinion shaft
until the end of the pin is level with the differential
case. (14) With a dial gauge contacting the end of the
side gear, lift the side gear evenly and measure the
clearance between the side gear and the differential
case. The clearance should be 0.1-0.2 mm.
NOTE: Do not tilt the side gear or the dial
gauge reading will be incorrect.
(15) If necessary, adjust the side gear clearance
using selective fit spacers.
NOTE: Spacers are available from 0.15 mm
to 1.00 mm in increments of 0.05 mm.
(16) Measure and if necessary, adjust the other
side gear clearance. (17) On models equipped with a viscous cou-
pling, adjust the side gear clearance as follows:
(a) Temporarily secure the differential case with
two bolts. (b) Position the differential case so that the right
hand side gear is uppermost. (c) Insert a 0.03 mm feeler gauge between the
View of the differential ass embly removed from the
transaxle.
Page 136 of 238
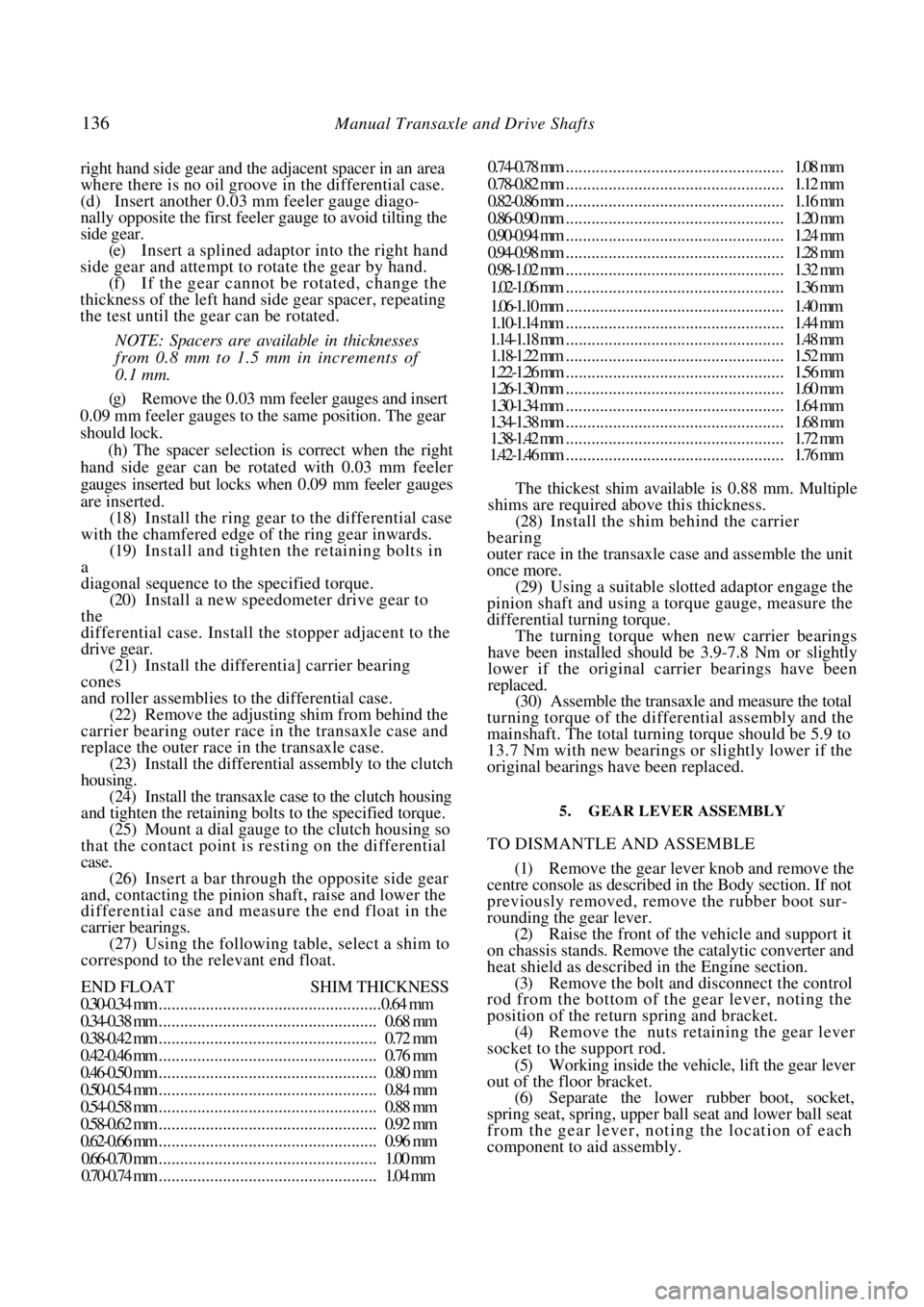
136 Manual Transaxle and Drive Shafts
right hand side gear and the adjacent spacer in an area
where there is no oil groove in the differential case.
(d) Insert another 0.03 mm feeler gauge diago-
nally opposite the first feeler gauge to avoid tilting the
side gear.
(e) Insert a splined adaptor into the right hand
side gear and attempt to rotate the gear by hand.
(f) If the gear cannot be rotated, change the
thickness of the left hand side gear spacer, repeating
the test until the gear can be rotated.
NOTE: Spacers are available in thicknesses
from 0.8 mm to 1.5 mm in increments of
0.1 mm.
(g) Remove the 0.03 mm feel er gauges and insert
0.09 mm feeler gauges to the same position. The gear
should lock.
(h) The spacer selection is correct when the right
hand side gear can be rotated with 0.03 mm feeler
gauges inserted but locks when 0.09 mm feeler gauges
are inserted.
(18) Install the ring gear to the differential case
with the chamfered edge of the ring gear inwards. (19) Install and tighten the retaining bolts in
a
diagonal sequence to the specified torque.
(20) Install a new speedometer drive gear to
the
differential case. Install the stopper adjacent to the
drive gear.
(21) Install the differentia] carrier bearing
cones
and roller assemblies to the differential case.
(22) Remove the adjusting shim from behind the
carrier bearing outer race in the transaxle case and
replace the outer race in the transaxle case.
(23) Install the differential assembly to the clutch
housing. (24) Install the transaxle case to the clutch housing
and tighten the retaining bolts to the specified torque.
(25) Mount a dial gauge to the clutch housing so
that the contact point is resting on the differential
case. (26) Insert a bar through the opposite side gear
and, contacting the pinion shaft, raise and lower the
differential case and measure the end float in the
carrier bearings. (27) Using the following table, select a shim to
correspond to the relevant end float.
END FLOAT SHIM THICKNESS
0.30-0.34 mm....................................................0.64 mm
0.34-0.38 mm................................................... 0.68 mm
0.38-0.42 mm................................................... 0.72 mm
0.42-0.46 mm................................................... 0.76 mm
0.46-0.50 mm................................................... 0.80 mm
0.50-0.54 mm................................................... 0.84 mm
0.54-0.58 mm................................................... 0.88 mm
0.58-0.62 mm................................................... 0.92 mm
0.62-0.66 mm................................................... 0.96 mm
0.66-0.70 mm................................................... 1.00 mm
0.70-0.74 mm................................................... 1.04 mm
0.74-0.78 mm ................................................... 1.08 mm
0.78-0.82 mm ................................................... 1.12 mm
0.82-0.86 mm ................................................... 1.16 mm
0.86-0.90 mm ................................................... 1.20 mm
0.90-0.94 mm ................................................... 1.24 mm
0.94-0.98 mm ................................................... 1.28 mm
0.98-1.02 mm ................................................... 1.32 mm
1.02-1.06 mm ................................................... 1.36 mm
1.06-1.10 mm ................................................... 1.40 mm
1.10-1.14 mm ................................................... 1.44 mm
1.14-1.18 mm ................................................... 1.48 mm
1.18-1.22 mm ................................................... 1.52 mm
1.22-1.26 mm ................................................... 1.56 mm
1.26-1.30 mm ................................................... 1.60 mm
1.30-1.34 mm ................................................... 1.64 mm
1.34-1.38 mm ................................................... 1.68 mm
1.38-1.42 mm ................................................... 1.72 mm
1.42-1.46 mm ................................................... 1.76 mm
The thickest shim available is 0.88 mm. Multiple
shims are required above this thickness.
(28) Install the shim behind the carrier
bearing
outer race in the transaxle case and assemble the unit
once more. (29) Using a suitable slotted adaptor engage the
pinion shaft and using a to rque gauge, measure the
differential turning torque. The turning torque when new carrier bearings
have been installed should be 3.9-7.8 Nm or slightly
lower if the original carrier bearings have been
replaced.
(30) Assemble the transaxle and measure the total
turning torque of the diff erential assembly and the
mainshaft. The total turning torque should be 5.9 to
13.7 Nm with new bearings or slightly lower if the
original bearings have been replaced.
5. GEAR LEVER ASSEMBLY
TO DISMANTLE AND ASSEMBLE
(1) Remove the gear lever knob and remove the
centre console as described in the Body section. If not
previously removed, remove the rubber boot sur-
rounding the gear lever. (2) Raise the front of the vehicle and support it
on chassis stands. Remove the catalytic converter and
heat shield as described in the Engine section.
(3) Remove the bolt and disconnect the control
rod from the bottom of the gear lever, noting the
position of the return spring and bracket.
(4) Remove the nuts retaining the gear lever
socket to the support rod. (5) Working inside the vehicle, lift the gear lever
out of the floor bracket. (6) Separate the lower rubber boot, socket,
spring seat, spring, upper ball seat and lower ball seat
from the gear lever, noting the location of each
component to aid assembly.
Page 137 of 238
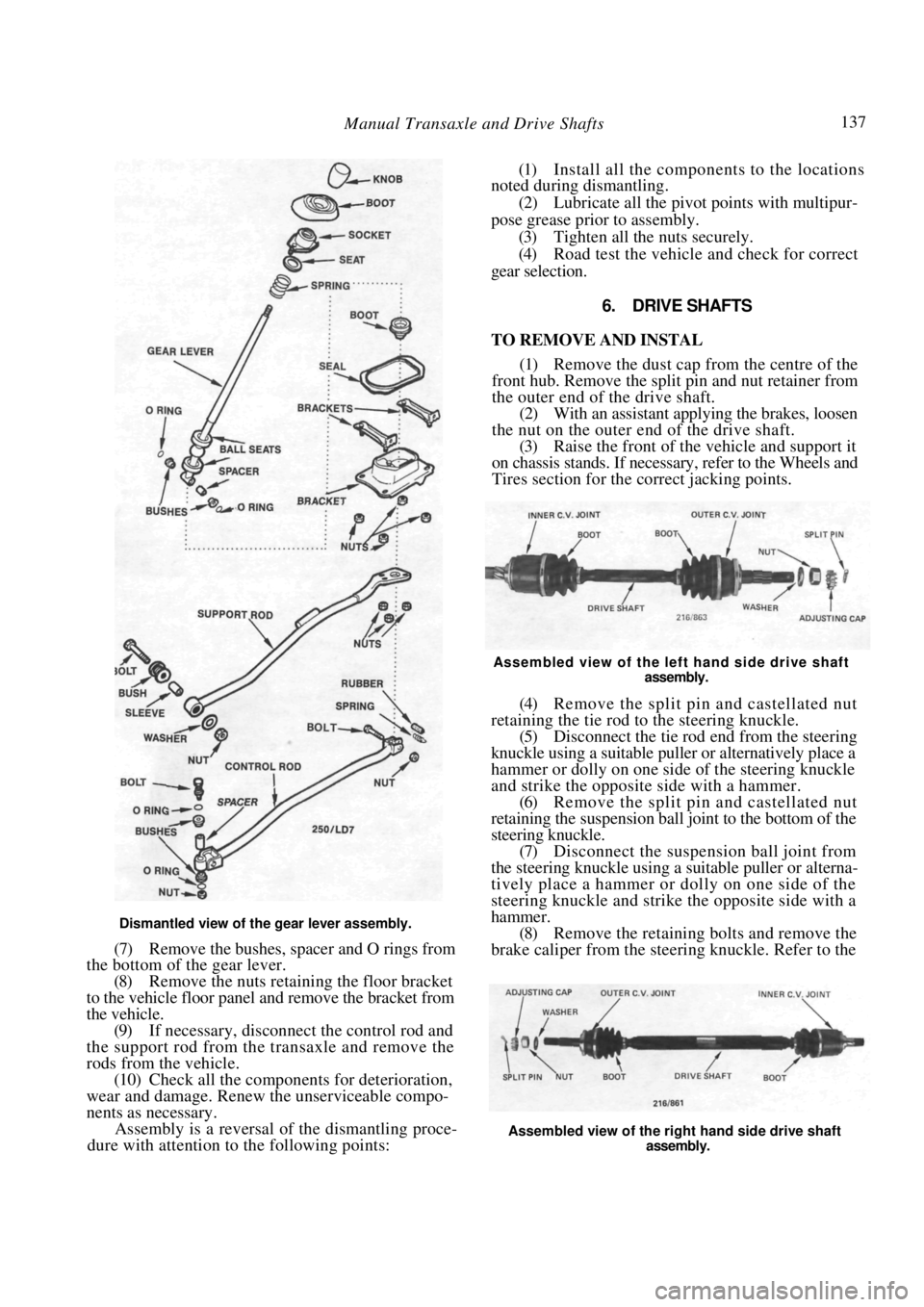
Manual Transaxle and Drive Shafts 137
Dismantled view of the gear lever assembly.
(7) Remove the bushes, spacer and O rings from
the bottom of the gear lever.
(8) Remove the nuts retaining the floor bracket
to the vehicle floor panel and remove the bracket from
the vehicle. (9) If necessary, disconnect the control rod and
the support rod from the transaxle and remove the
rods from the vehicle. (10) Check all the components for deterioration,
wear and damage. Renew the unserviceable compo-
nents as necessary. Assembly is a reversal of the dismantling proce-
dure with attention to the following points:
(1) Install all the components to the locations
noted during dismantling.
(2) Lubricate all the pivot points with multipur-
pose grease prior to assembly. (3) Tighten all the nuts securely.
(4) Road test the vehicle and check for correct
gear selection.
6. DRIVE SHAFTS
TO REMOVE AND INSTAL
(1) Remove the dust cap from the centre of the
front hub. Remove the split pin and nut retainer from
the outer end of the drive shaft. (2) With an assistant applying the brakes, loosen
the nut on the outer end of the drive shaft.
(3) Raise the front of the vehicle and support it
on chassis stands. If necessary, refer to the Wheels and
Tires section for the correct jacking points.
Assembled view of the left hand side drive shaft
assembly.
(4) Remove the split pin and castellated nut
retaining the tie rod to the steering knuckle. (5) Disconnect the tie rod end from the steering
knuckle using a suitable puller or alternatively place a
hammer or dolly on one side of the steering knuckle
and strike the opposite side with a hammer.
(6) Remove the split pin and castellated nut
retaining the suspension ball joint to the bottom of the
steering knuckle. (7) Disconnect the suspension ball joint from
the steering knuckle using a suitable puller or alterna-
tively place a hammer or dolly on one side of the
steering knuckle and strike the opposite side with a
hammer. (8) Remove the retaining bolts and remove the
brake caliper from the stee ring knuckle. Refer to the
Assembled view of the right hand side drive shaft
assembly.
Page 138 of 238
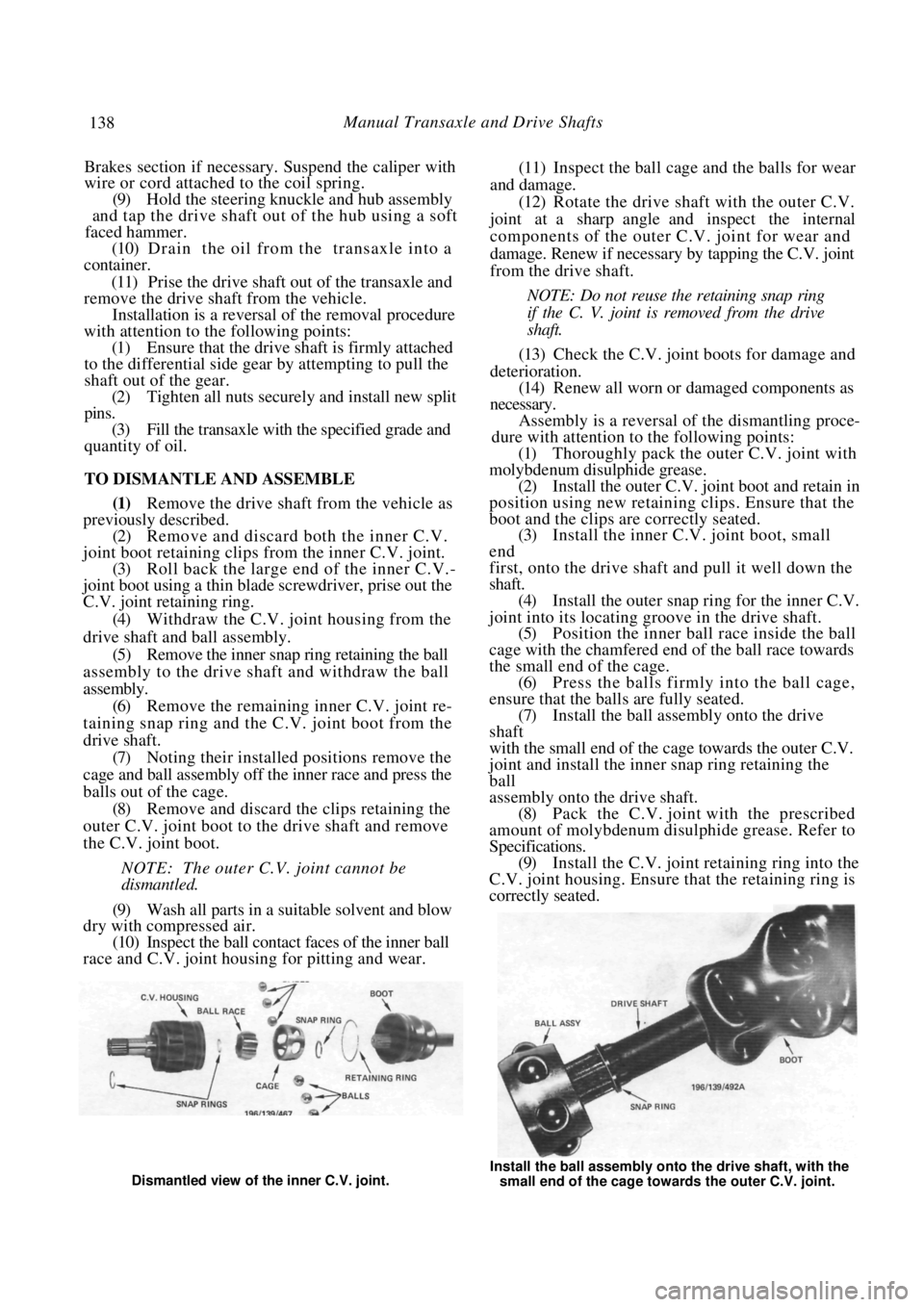
138 Manual Transaxle and Drive Shafts
Brakes section if necessary. Suspend the caliper with
wire or cord attached to the coil spring.
(9) Hold the steering knuckle and hub assembly
and tap the drive shaft out of the hub using a soft
faced hammer.
(10) Drain the oil from the transaxle into a
container.
(11) Prise the drive shaft out of the transaxle and
remove the drive shaft from the vehicle.
Installation is a reversal of the removal procedure
with attention to the following points:
(1) Ensure that the drive sh aft is firmly attached
to the differential side gear by attempting to pull the
shaft out of the gear. (2) Tighten all nuts securely and install new split
pins. (3) Fill the transaxle with the specified grade and
quantity of oil.
TO DISMANTLE AND ASSEMBLE
(1) Remove the drive shaft from the vehicle as
previously described.
(2) Remove and discard both the inner C.V.
joint boot retaining clips from the inner C.V. joint. (3) Roll back the large en d of the inner C.V.-
joint boot using a thin blade screwdriver, prise out the
C.V. joint retaining ring.
(4) Withdraw the C.V. joint housing from the
drive shaft and ball assembly. (5) Remove the inner snap ring retaining the ball
assembly to the drive shaft and withdraw the ball
assembly. (6) Remove the remaining inner C.V. joint re-
taining snap ring and the C.V. joint boot from the
drive shaft. (7) Noting their installed positions remove the
cage and ball assembly off the inner race and press the
balls out of the cage. (8) Remove and discard the clips retaining the
outer C.V. joint boot to the drive shaft and remove
the C.V. joint boot.
NOTE: The outer C.V. joint cannot be
dismantled.
(9) Wash all parts in a suitable solvent and blow
dry with compressed air.
(10) Inspect the ball contact faces of the inner ball
race and C.V. joint housing for pitting and wear.
(11) Inspect the ball cage and the balls for wear
and damage. (12) Rotate the drive shaft with the outer C.V.
joint at a sharp angle and inspect the internal
components of the outer C.V. joint for wear and
damage. Renew if necessary by tapping the C.V. joint
from the drive shaft.
NOTE: Do not reuse the retaining snap ring
if the C. V. joint is removed from the drive
shaft.
(13) Check the C.V. joint boots for damage and
deterioration. (14) Renew all worn or damaged components as
necessary. Assembly is a reversal of the dismantling proce-
dure with attention to the following points:
(1) Thoroughly pack the outer C.V. joint with
molybdenum disulphide grease. (2) Install the outer C.V. joint boot and retain in
position using new retaining clips. Ensure that the
boot and the clips ar e correctly seated.
(3) Install the inner C.V. joint boot, small
end
first, onto the drive shaft and pull it well down the
shaft. (4) Install the outer snap ri ng for the inner C.V.
joint into its locating groove in the drive shaft. (5) Position the inner ball race inside the ball
cage with the chamfered end of the ball race towards
the small end of the cage. (6) Press the balls firmly into the ball cage,
ensure that the balls are fully seated. (7) Install the ball assem bly onto the drive
shaft
with the small end of the cage towards the outer C.V.
joint and install the inner snap ring retaining the
ball
assembly onto the drive shaft.
(8) Pack the C.V. joint with the prescribed
amount of molybdenum disul phide grease. Refer to
Specifications. (9) Install the C.V. joint retaining ring into the
C.V. joint housing. Ensure that the retaining ring is
correctly seated.
Dismantled view of the inner C.V. joint. Install the ball assembly onto the drive shaft, with the
small end of the cage towards the outer C.V. joint.
Page 139 of 238
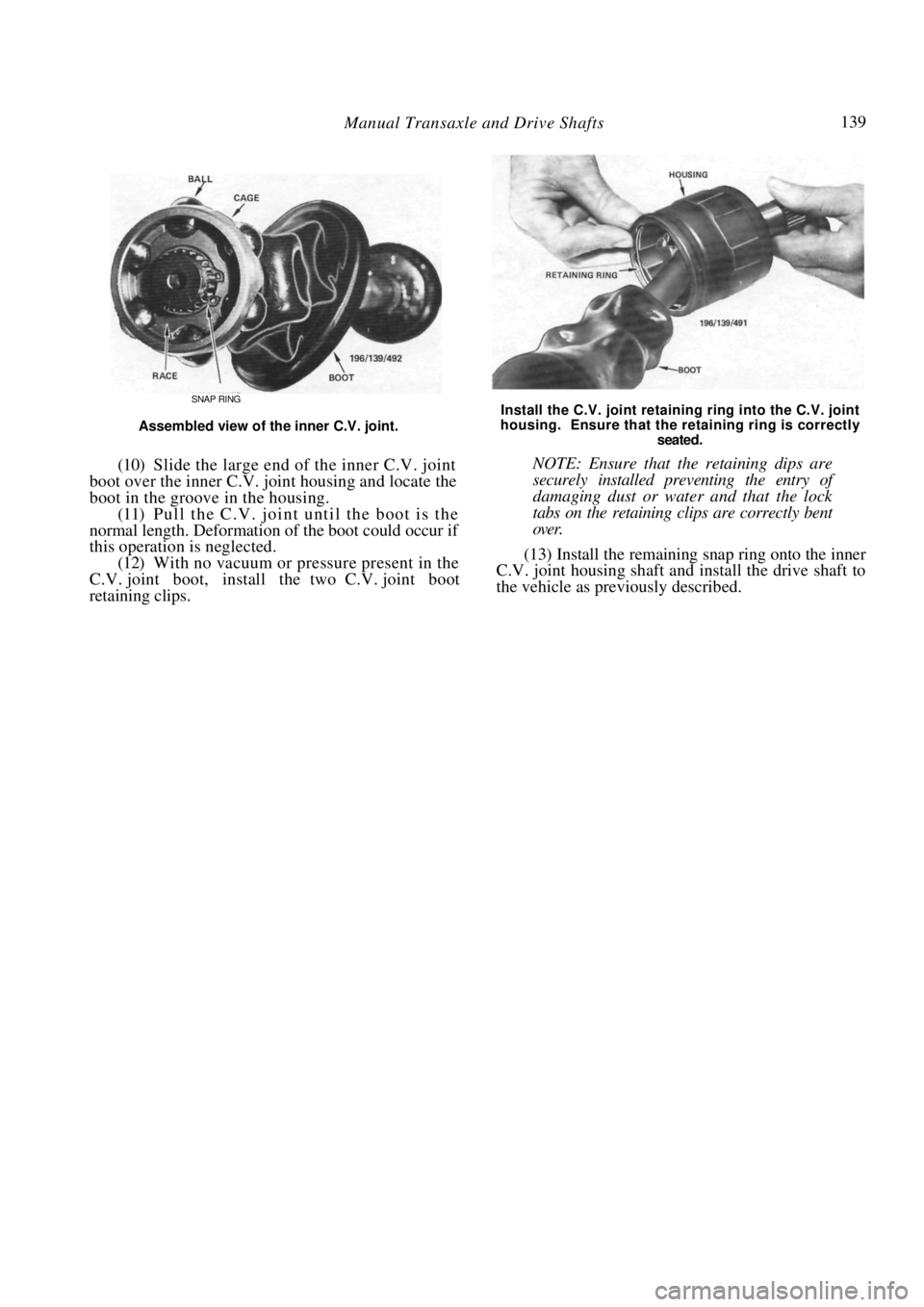
Manual Transaxle and Drive Shafts 139
SNAP RING
Assembled view of the inner C.V. joint.
(10) Slide the large end of the inner C.V. joint
boot over the inner C.V. joint housing and locate the
boot in the groove in the housing.
(11) Pull the C.V. joint until the boot is the
normal length. Deformation of the boot could occur if
this operation is neglected. (12) With no vacuum or pressure present in the
C.V. joint boot, install the two C.V. joint boot
retaining clips.
Install the C.V. joint retain ing ring into the C.V. joint
housing. Ensure that the retaining ring is correctly
seated.
NOTE: Ensure that the retaining dips are
securely installed preven ting the entry of
damaging dust or water and that the lock
tabs on the retaining clips are correctly bent
over.
(13) Install the remaining snap ring onto the inner
C.V. joint housing shaft and install the drive shaft to
the vehicle as previously described.
Page 140 of 238
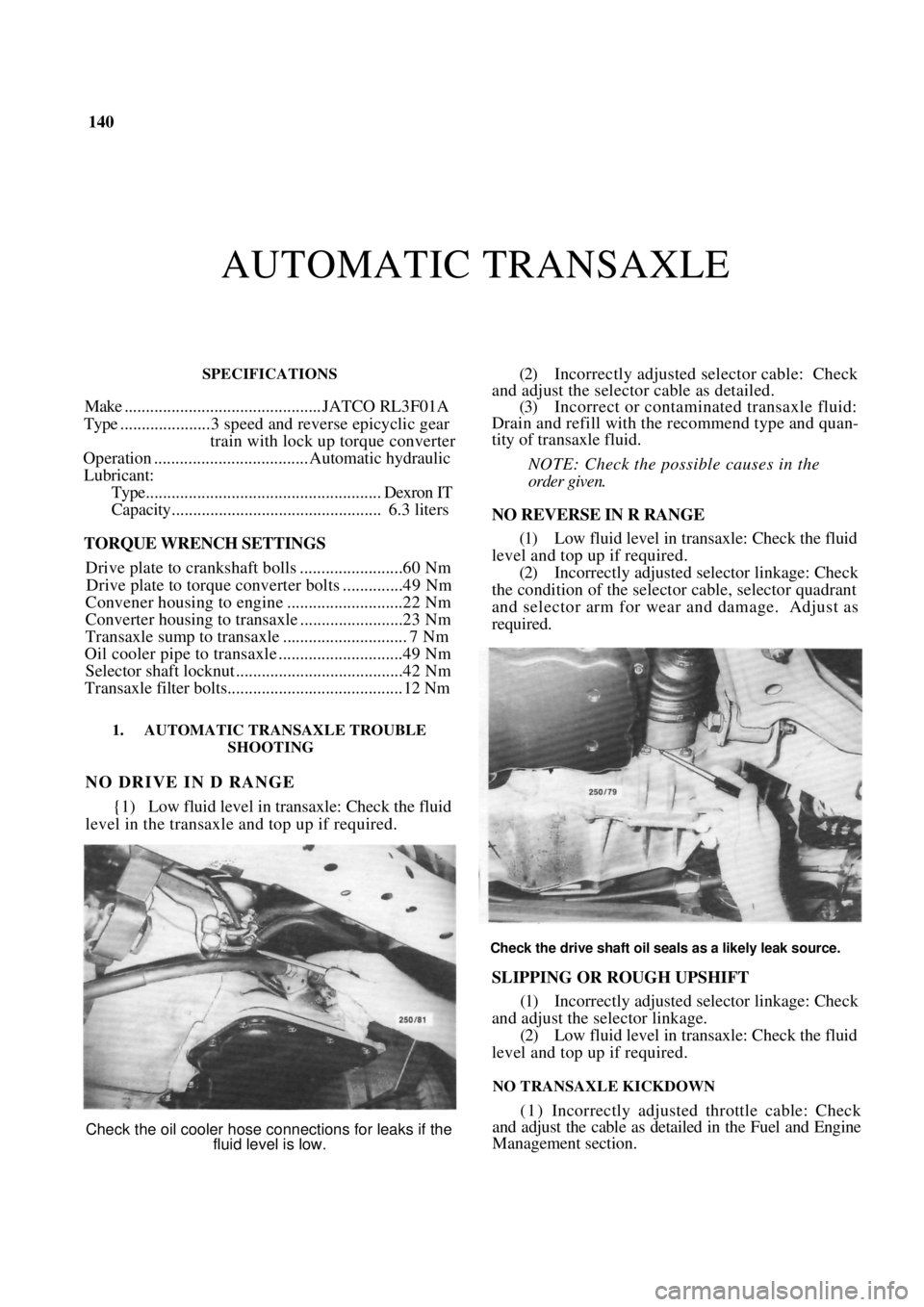
140
AUTOMATIC TRANSAXLE
SPECIFICATIONS
Make .............................................. JATCO RL3F01A
Type .....................3 speed and reverse epicyclic gear
train with lock up torque converter
Operation .................................... Automatic hydraulic
Lubricant:
Type....................................................... Dexron IT
Capacity................................................. 6.3 liters
TORQUE WRENCH SETTINGS
Drive plate to crankshaft bolls ........................60 Nm
Drive plate to torque converter bolts ..............49 Nm
Convener housing to engine ...........................22 Nm
Converter housing to transaxle ........................23 Nm
Transaxle sump to transaxle ............................. 7 Nm
Oil cooler pipe to transaxle .............................49 Nm
Selector shaft locknut .......................................42 Nm
Transaxle filter bolts.........................................12 Nm
1. AUTOMATIC TRANSAXLE TROUBLE SHOOTING
NO DRIVE IN D RANGE
{1) Low fluid level in transaxle: Check the fluid
level in the transaxle and top up if required.
(2) Incorrectly adjusted selector cable: Check
and adjust the selector cable as detailed. (3) Incorrect or contaminated transaxle fluid:
Drain and refill with the recommend type and quan-
tity of transaxle fluid.
NOTE: Check the possible causes in the
order given.
NO REVERSE IN R RANGE
(1) Low fluid level in transaxle: Check the fluid
level and top up if required. (2) Incorrectly adjusted selector linkage: Check
the condition of the selector cable, selector quadrant
and selector arm for wear and damage. Adjust as
required.
Check the drive shaft oil seals as a likely leak source.
SLIPPING OR ROUGH UPSHIFT
(1) Incorrectly adjusted selector linkage: Check
and adjust the selector linkage. (2) Low fluid level in transaxle: Check the fluid
level and top up if required.
NO TRANSAXLE KICKDOWN
(1) Incorrectly adjusted throttle cable: Check
and adjust the cable as detailed in the Fuel and Engine
Management section.
Check the oil cooler hose connections for leaks if the
fluid level is low.