NISSAN PULSAR 1987 Owners Manual
Manufacturer: NISSAN, Model Year: 1987, Model line: PULSAR, Model: NISSAN PULSAR 1987Pages: 238, PDF Size: 28.91 MB
Page 91 of 238
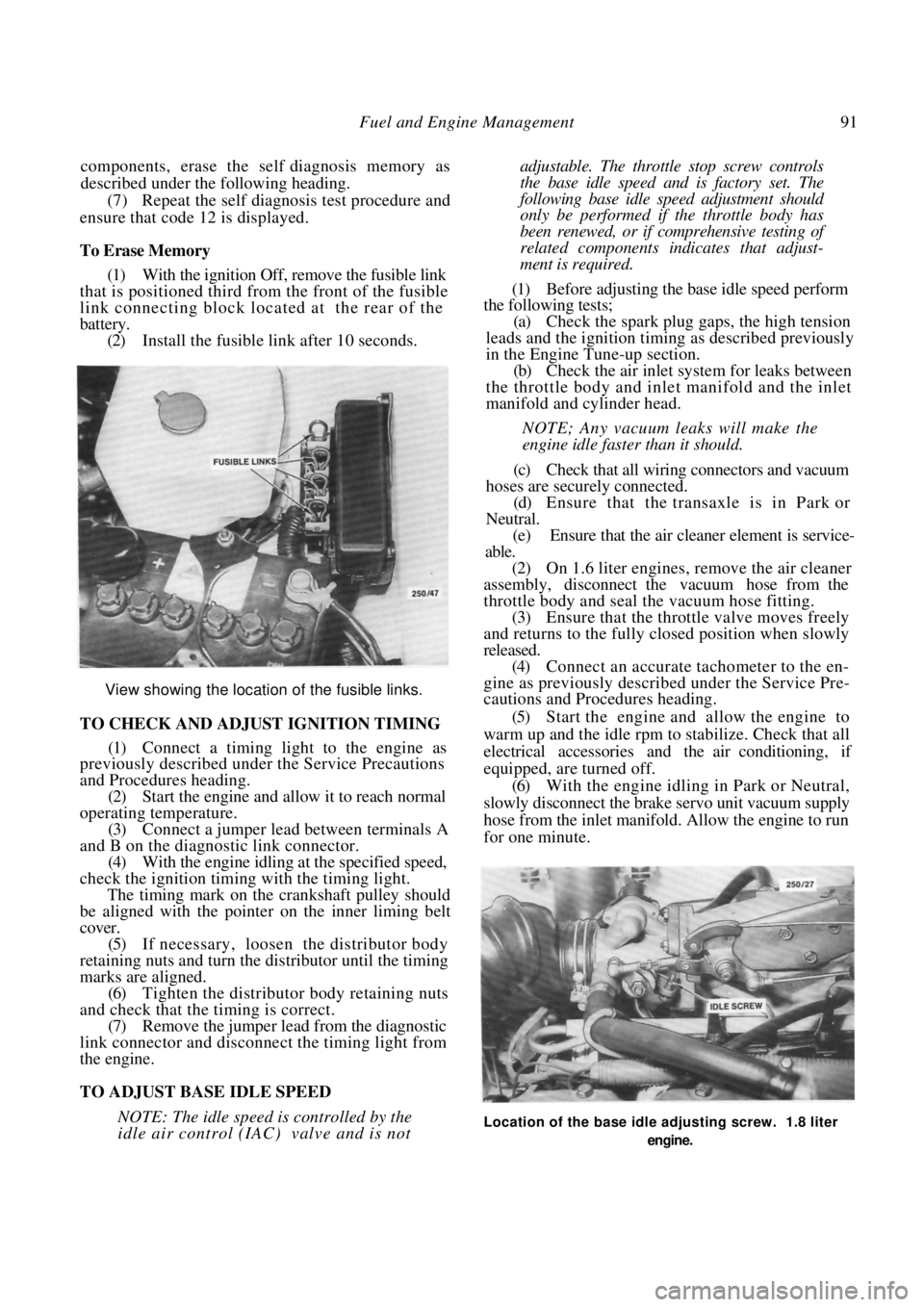
Fuel and Engine Management 91
components, erase the self diagnosis memory as
described under the following heading.
(7) Repeat the self diagnosis test procedure and
ensure that code 12 is displayed.
To Erase Memory
(1) With the ignition Off, remove the fusible link
that is positioned third from the front of the fusible
link connecting block located at the rear of the
battery. (2) Install the fusible link after 10 seconds.
View showing the location of the fusible links.
TO CHECK AND ADJUST IGNITION TIMING
(1) Connect a timing light to the engine as
previously described under the Service Precautions
and Procedures heading.
(2) Start the engine and allow it to reach normal
operating temperature. (3) Connect a jumper lead between terminals A
and B on the diagnostic link connector. (4) With the engine idling at the specified speed,
check the ignition timing with the timing light.
The timing mark on the crankshaft pulley should
be aligned with the pointer on the inner liming belt
cover.
(5) If necessary, loosen the distributor body
retaining nuts and turn the distributor until the timing
marks are aligned. (6) Tighten the distributor body retaining nuts
and check that the timing is correct. (7) Remove the jumper lead from the diagnostic
link connector and disconnect the timing light from
the engine.
TO ADJUST BASE IDLE SPEED
NOTE: The idle speed is controlled by the
idle air control (IAC) valve and is not
adjustable. The throttle stop screw controls
the base idle speed a nd is factory set. The
following base idle speed adjustment should
only be performed if the throttle body has
been renewed, or if comprehensive testing of
related components indicates that adjust-
ment is required.
(1) Before adjusting the base idle speed perform
the following tests;
(a) Check the spark plug gaps, the high tension
leads and the ignition timin g as described previously
in the Engine Tune-up section.
(b) Check the air inlet syst em for leaks between
the throttle body and inlet manifold and the inlet
manifold and cylinder head.
NOTE; Any vacuum leaks will make the
engine idle faster than it should.
(c) Check that all wiring connectors and vacuum
hoses are securely connected. (d) Ensure that the transaxle is in Park or
Neutral. (e) Ensure that the air cleaner element is service-
able.
(2) On 1.6 liter engines, remove the air cleaner
assembly, disconnect the vacuum hose from the
throttle body and seal the vacuum hose fitting.
(3) Ensure that the throttle valve moves freely
and returns to the fully closed position when slowly
released. (4) Connect an accurate tachometer to the en-
gine as previously descri bed under the Service Pre-
cautions and Procedures heading.
(5) Start the engine and allow the engine to
warm up and the idle rpm to stabilize. Check that all
electrical accessories and the air conditioning, if
equipped, are turned off. (6) With the engine idling in Park or Neutral,
slowly disconnect the brake servo unit vacuum supply
hose from the inlet manifold. Allow the engine to run
for one minute.
Location of the base idle adjusting screw. 1.8 liter
engine.
Page 92 of 238
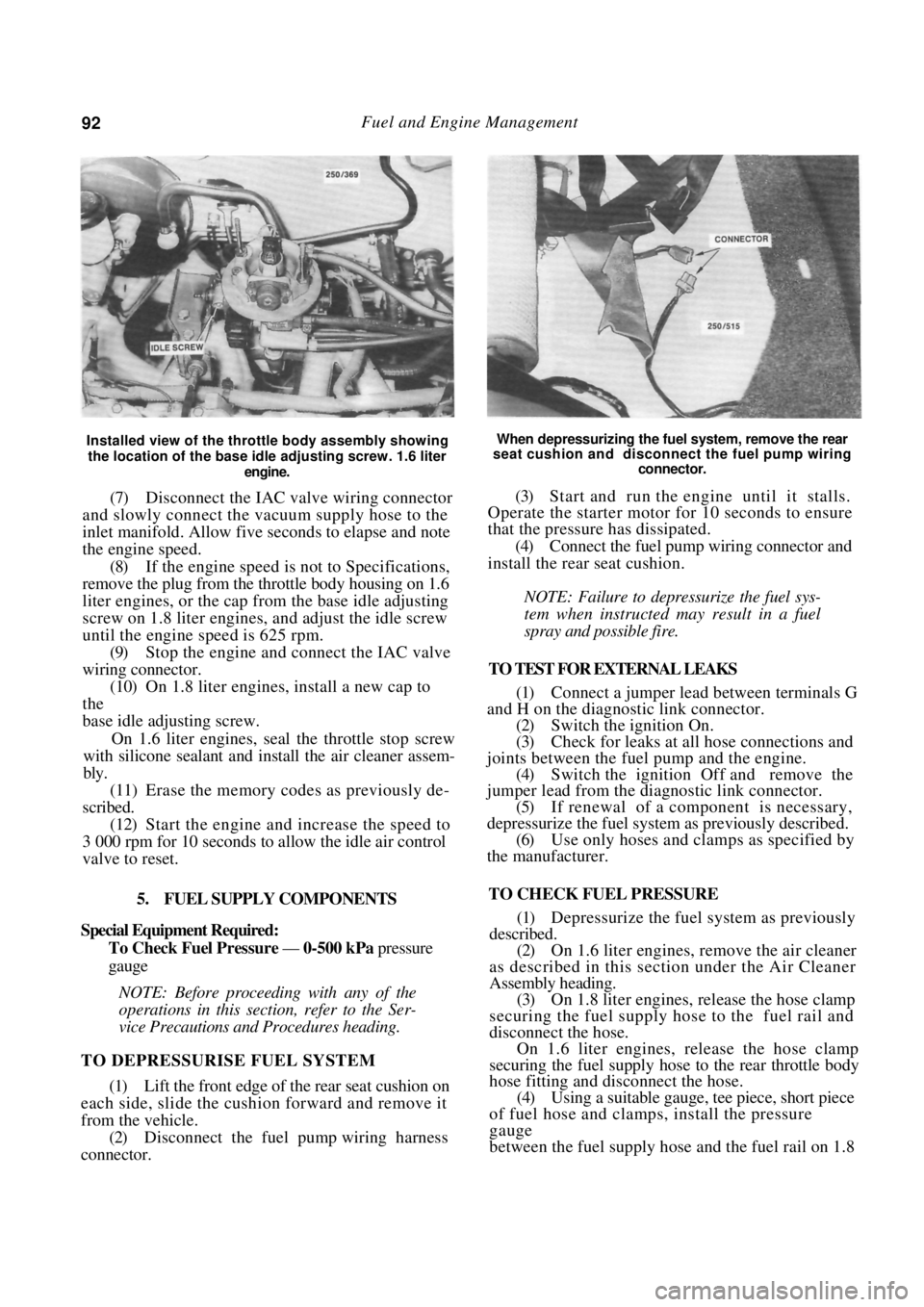
92 Fuel and Engine Management
Installed view of the throttle body assembly showing
the location of the base idle adjusting screw. 1.6 liter
engine.
(7) Disconnect the IAC valve wiring connector
and slowly connect the vacuum supply hose to the
inlet manifold. Allow five seconds to elapse and note
the engine speed.
(8) If the engine speed is not to Specifications,
remove the plug from the throttle body housing on 1.6
liter engines, or the cap from the base idle adjusting
screw on 1.8 liter engines, and adjust the idle screw
until the engine speed is 625 rpm. (9) Stop the engine and connect the IAC valve
wiring connector. (10) On 1.8 liter engines, install a new cap to
the
base idle adjusting screw.
On 1.6 liter engines, seal the throttle stop screw
with silicone sealant and install the air cleaner assem-
bly.
(11) Erase the memory codes as previously de-
scribed.
(12) Start the engine and increase the speed to
3 000 rpm for 10 seconds to allow the idle air control
valve to reset.
5. FUEL SUPPLY COMPONENTS
Special Equipment Required:
To Check Fuel Pressure — 0-500 kPa pressure
gauge
NOTE: Before proceeding with any of the
operations in this section, refer to the Ser-
vice Precautions and Procedures heading.
TO DEPRESSURISE FUEL SYSTEM
(1) Lift the front edge of the rear seat cushion on
each side, slide the cushion forward and remove it
from the vehicle. (2) Disconnect the fuel pump wiring harness
connector.
When depressurizing the fuel system, remove the rear
seat cushion and disconnect the fuel pump wiring
connector.
(3) Start and run the engine until it stalls.
Operate the starter motor for 10 seconds to ensure
that the pressure has dissipated.
(4) Connect the fuel pump wiring connector and
install the rear seat cushion.
NOTE: Failure to depressurize the fuel sys-
tem when instructed may result in a fuel
spray and possible fire.
TO TEST FOR EXTERNAL LEAKS
(1) Connect a jumper lead between terminals G
and H on the diagnostic link connector.
(2) Switch the ignition On.
(3) Check for leaks at all hose connections and
joints between the fuel pump and the engine. (4) Switch the ignition Off and remove the
jumper lead from the diagnostic link connector.
(5) If renewal of a component is necessary,
depressurize the fuel system as previously described. (6) Use only hoses and clamps as specified by
the manufacturer.
TO CHECK FUEL PRESSURE
(1) Depressurize the fuel system as previously
described. (2) On 1.6 liter engines, remove the air cleaner
as described in this section under the Air Cleaner
Assembly heading. (3) On 1.8 liter engines, release the hose clamp
securing the fuel supply hos e to the fuel rail and
disconnect the hose. On 1.6 liter engines, release the hose clamp
securing the fuel supply hose to the rear throttle body
hose fitting and disconnect the hose.
(4) Using a suitable gauge, tee piece, short piece
of fuel hose and clamps, install the pressure
gauge
between the fuel supply ho se and the fuel rail on 1.8
Page 93 of 238
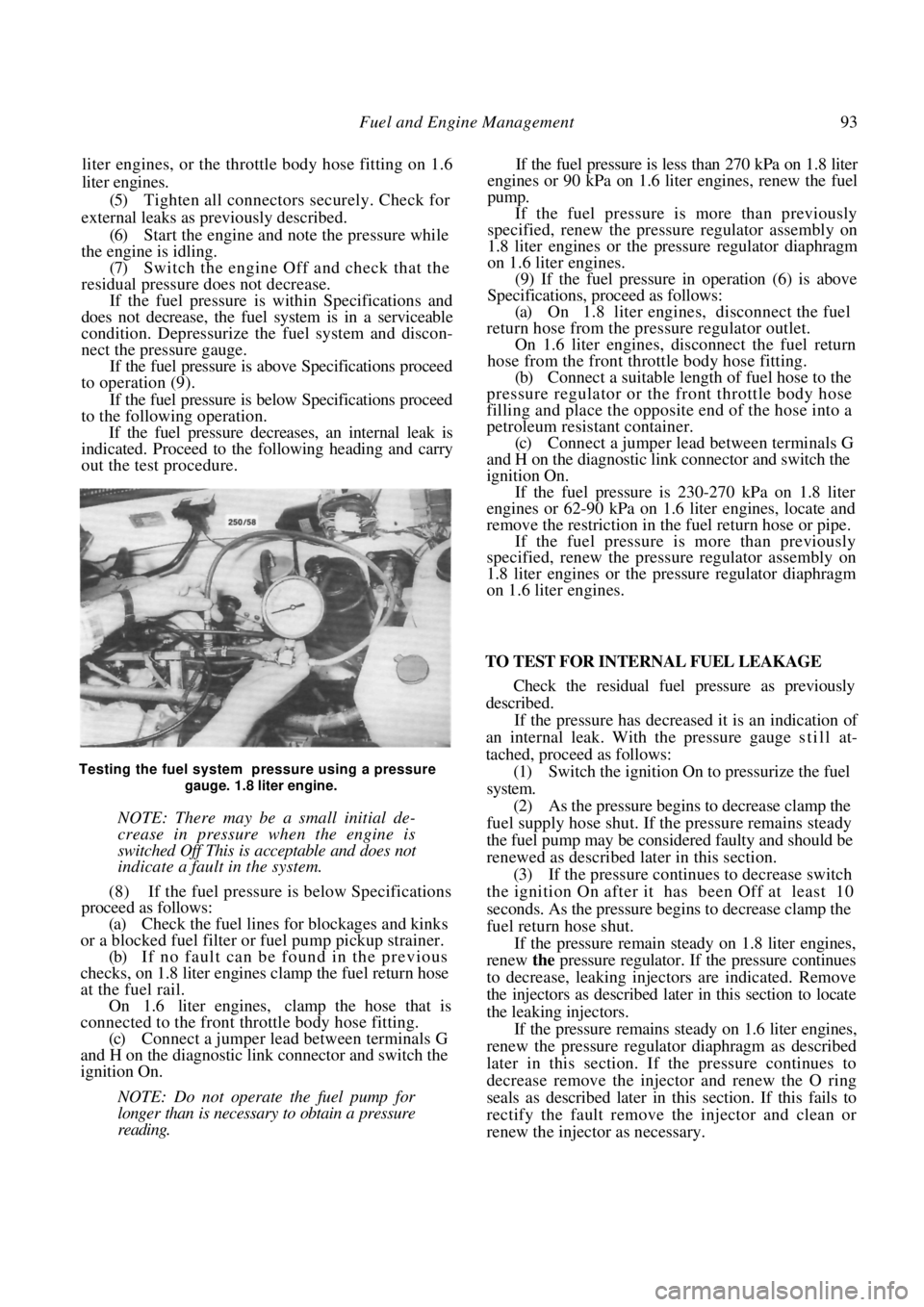
Fuel and Engine Management 93
liter engines, or the throttle body hose fitting on 1.6
liter engines.
(5) Tighten all connectors securely. Check for
external leaks as previously described. (6) Start the engine and note the pressure while
the engine is idling.
(7) Switch the engine Off and check that the
residual pressure does not decrease.
If the fuel pressure is within Specifications and
does not decrease, the fuel system is in a serviceable
condition. Depressurize the fuel system and discon-
nect the pressure gauge.
If the fuel pressure is a bove Specifications proceed
to operation (9).
If the fuel pressure is below Specifications proceed
to the following operation.
If the fuel pressure decreases, an internal leak is
indicated. Proceed to the following heading and carry
out the test procedure.
Testing the fuel system pressure using a pressure
gauge. 1.8 liter engine.
NOTE: There may be a small initial de-
crease in pressure when the engine is
switched Off This is acceptable and does not
indicate a fault in the system.
(8) If the fuel pressure is below Specifications
proceed as follows:
(a) Check the fuel lines for blockages and kinks
or a blocked fuel filter or fuel pump pickup strainer. (b) If no fault can be found in the previous
checks, on 1.8 liter engines clamp the fuel return hose
at the fuel rail. On 1.6 liter engines, clamp the hose that is
connected to the front throttle body hose fitting.
(c) Connect a jumper lead between terminals G
and H on the diagnostic link connector and switch the
ignition On.
NOTE: Do not operate the fuel pump for
longer than is necessary to obtain a pressure
reading.
If the fuel pressure is less than 270 kPa on 1.8 liter
engines or 90 kPa on 1.6 liter engines, renew the fuel
pump.
If the fuel pressure is more than previously
specified, renew the pressure regulator assembly on
1.8 liter engines or the pressure regulator diaphragm
on 1.6 liter engines.
(9) If the fuel pressure in operation (6) is above
Specifications, proceed as follows:
(a) On 1.8 liter engines, disconnect the fuel
return hose from the pressure regulator outlet.
On 1.6 liter engines, disc onnect the fuel return
hose from the front throttle body hose fitting.
(b) Connect a suitable length of fuel hose to the
pressure regulator or the front throttle body hose
filling and place the opposite end of the hose into a
petroleum resistant container. (c) Connect a jumper lead between terminals G
and H on the diagnostic link connector and switch the
ignition On. If the fuel pressure is 230-270 kPa on 1.8 liter
engines or 62-90 kPa on 1.6 liter engines, locate and
remove the restriction in the fuel return hose or pipe.
If the fuel pressure is more than previously
specified, renew the pressure regulator assembly on
1.8 liter engines or the pressure regulator diaphragm
on 1.6 liter engines.
TO TEST FOR INTERNAL FUEL LEAKAGE
Check the residual fuel pressure as previously
described.
If the pressure has decreased it is an indication of
an internal leak. With the pressure gauge still at-
tached, proceed as follows:
(1) Switch the ignition On to pressurize the fuel
system.
(2) As the pressure begins to decrease clamp the
fuel supply hose shut. If the pressure remains steady
the fuel pump may be consid ered faulty and should be
renewed as described later in this section. (3) If the pressure continues to decrease switch
the ignition On after it has been Off at least 10
seconds. As the pressure begi ns to decrease clamp the
fuel return hose shut. If the pressure remain steady on 1.8 liter engines,
renew the pressure regulator. If the pressure continues
to decrease, leaking inject ors are indicated. Remove
the injectors as described later in this section to locate
the leaking injectors.
If the pressure remains stea dy on 1.6 liter engines,
renew the pressure regulator diaphragm as described
later in this section. If the pressure continues to
decrease remove the injector and renew the O ring
seals as described later in this section. If this fails to
rectify the fault remove the injector and clean or
renew the injector as necessary.
Page 94 of 238

94 Fuel and Engine Management
FUEL FILTER
To Remove and Install
Refer to the Engine Tune-up section for the
procedure to remove and install the fuel filter.
FUEL PUMP
To Test Electrical Circuit
Refer to the EGI and Fuel Pump Relays heading
later in this section for the test procedures.
To Remove and Install
(1) Depressurize the fuel system as previously
described.
(2) Disconnect the negative battery terminal.
(3) Remove the rear seat backrest as described
under the Seats heading in the Body section.
(4) Remove the bolts securing the fuel pump
cover plate to the floor pa nel, remove the rubber
grommet and slide the cover plate from the wiring
harness. (5) Mark the fuel hoses to ensure correct install-
lation and disconnect the hoses from the fuel pump. (6) Remove the fuel pump retaining screws and
carefully remove the fuel pump from the fuel tank.
View of the fuel pump cover plate removed, showing
the fuel pump installed.
Installation is a reversal of the removal procedure
with attention to the following points:
(1) Ensure that a new fuel pump O ring seal is
installed. (2) Tighten the fuel pump retaining screws and
the fuel hose clamps securely.
(3) Ensure that the rubber grommet is seated
correctly in the fuel pump cover plate. (4) Install the fuel pump cover plate ensuring
that the arrow on the plate is facing the front of the
vehicle. (5) Connect the negative battery terminal, start
the engine and test for leaks as previously described.
Rectify as necessary.
FUEL PRESSURE REGULATOR
To Remove and Install — 1.8 Liter Engine
(1) Depressurize the fuel system as previously
described.
(2) Disconnect the negative battery terminal.
View of the fuel pump assembly removed from the fuel
tank. Installed view of the fuel pressure regulator. 1.8 liter
engine.
Page 95 of 238
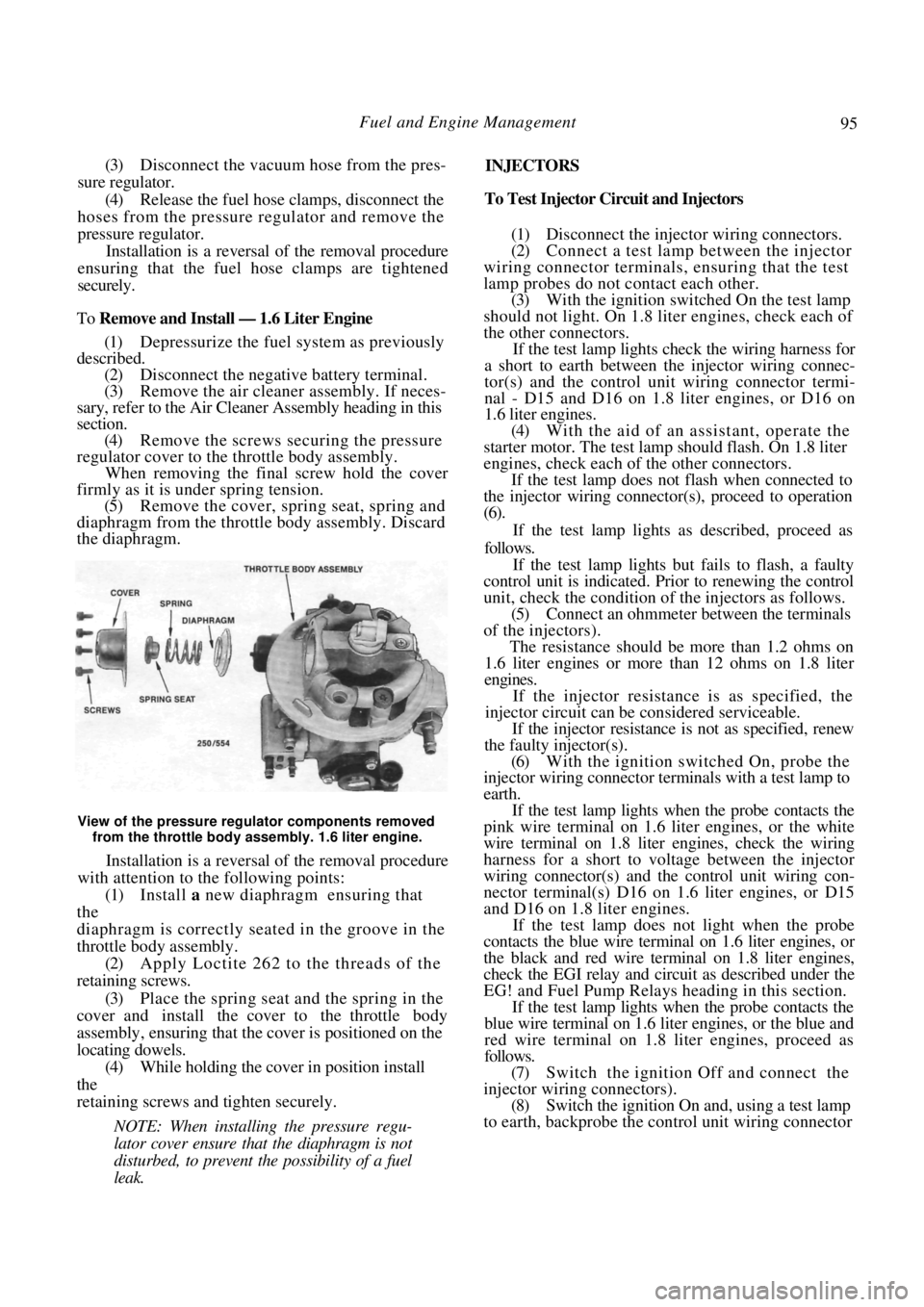
Fuel and Engine Management 95
(3) Disconnect the vacuum hose from the pres-
sure regulator.
(4) Release the fuel hose clamps, disconnect the
hoses from the pressure regulator and remove the
pressure regulator. Installation is a reversal of the removal procedure
ensuring that the fuel hose clamps are tightened
securely.
To Remove and Install — 1.6 Liter Engine
(1) Depressurize the fuel system as previously
described. (2) Disconnect the negative battery terminal.
(3) Remove the air cleaner assembly. If neces-
sary, refer to the Air Cleane r Assembly heading in this
section. (4) Remove the screws securing the pressure
regulator cover to the throttle body assembly. When removing the final screw hold the cover
firmly as it is under spring tension.
(5) Remove the cover, spring seat, spring and
diaphragm from the thrott le body assembly. Discard
the diaphragm.
View of the pressure regulator components removed
from the throttle body assembly. 1.6 liter engine.
Installation is a reversal of the removal procedure
with attention to the following points:
(1) Install a new diaphragm ensuring that
the
diaphragm is correctly seat ed in the groove in the
throttle body assembly. (2) Apply Loctite 262 to the threads of the
retaining screws.
(3) Place the spring seat and the spring in the
cover and install the cover to the throttle body
assembly, ensuring that the cover is positioned on the
locating dowels. (4) While holding the cover in position install
the
retaining screws and tighten securely.
NOTE: When installing the pressure regu-
lator cover ensure that the diaphragm is not
disturbed, to prevent the possibility of a fuel
leak.
INJECTORS
To Test Injector Circuit and Injectors
(1) Disconnect the injector wiring connectors.
(2) Connect a test lamp between the injector
wiring connector terminals, ensuring that the test
lamp probes do not contact each other. (3) With the ignition switched On the test lamp
should not light. On 1.8 liter engines, check each of
the other connectors.
If the test lamp lights check the wiring harness for
a short to earth between the injector wiring connec-
tor(s) and the control unit wiring connector termi-
nal - D15 and D16 on 1.8 liter engines, or D16 on
1.6 liter engines.
(4) With the aid of an assistant, operate the
starter motor. The test lamp should flash. On 1.8 liter
engines, check each of the other connectors.
If the test lamp does not flash when connected to
the injector wiring connecto r(s), proceed to operation
(6).
If the test lamp lights as described, proceed as
follows.
If the test lamp lights but fails to flash, a faulty
control unit is indicated. Pr ior to renewing the control
unit, check the condition of the injectors as follows.
(5) Connect an ohmmeter between the terminals
of the injectors).
The resistance should be more than 1.2 ohms on
1.6 liter engines or more than 12 ohms on 1.8 liter
engines.
If the injector resistance is as specified, the
injector circuit can be considered serviceable.
If the injector resistance is not as specified, renew
the faulty injector(s).
(6) With the ignition switched On, probe the
injector wiring connector terminals with a test lamp to
earth.
If the test lamp lights when the probe contacts the
pink wire terminal on 1.6 liter engines, or the white
wire terminal on 1.8 liter engines, check the wiring
harness for a short to volt age between the injector
wiring connector(s) and the control unit wiring con-
nector terminal(s) D16 on 1.6 liter engines, or D15
and D16 on 1.8 liter engines.
If the test lamp does not light when the probe
contacts the blue wire termin al on 1.6 liter engines, or
the black and red wire term inal on 1.8 liter engines,
check the EGI relay and circ uit as described under the
EG! and Fuel Pump Relays heading in this section.
If the test lamp lights when the probe contacts the
blue wire terminal on 1.6 lite r engines, or the blue and
red wire terminal on 1.8 liter engines, proceed as
follows.
(7) Switch the ignition Off and connect the
injector wiring connectors). (8) Switch the ignition On and, using a test lamp
to earth, backprobe the cont rol unit wiring connector
Page 96 of 238
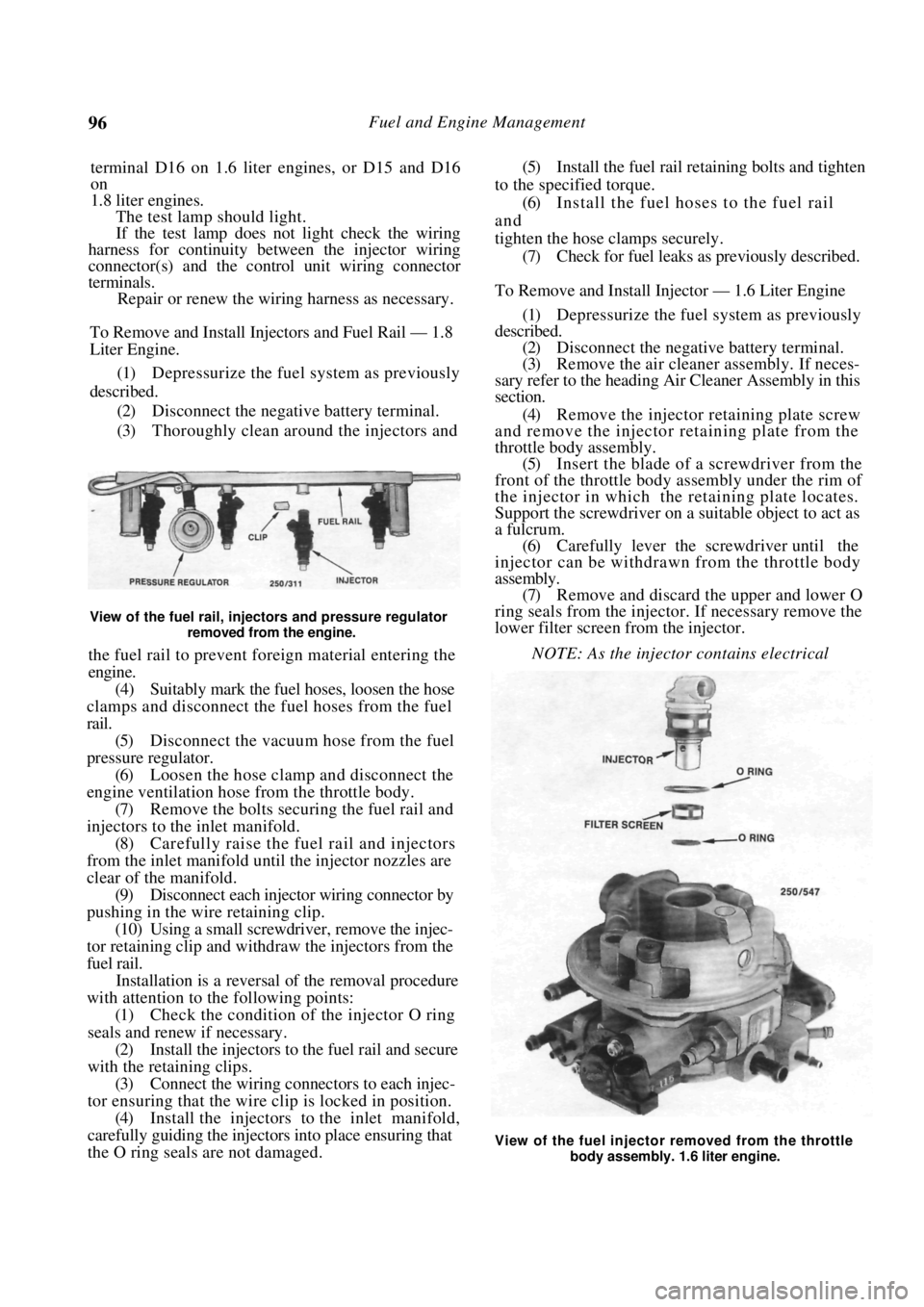
96 Fuel and Engine Management
terminal D16 on 1.6 liter engines, or D15 and D16
on
1.8 liter engines.
The test lamp should light.
If the test lamp does not light check the wiring
harness for continuity between the injector wiring
connector(s) and the control unit wiring connector
terminals.
Repair or renew the wiring harness as necessary.
To Remove and Install Injectors and Fuel Rail — 1.8
Liter Engine.
(1) Depressurize the fuel system as previously
described.
(2) Disconnect the negative battery terminal.
(3) Thoroughly clean around the injectors and
View of the fuel rail, injectors and pressure regulator
removed from the engine.
the fuel rail to prevent foreign material entering the
engine.
(4) Suitably mark the fuel hoses, loosen the hose
clamps and disconnect the fuel hoses from the fuel
rail. (5) Disconnect the vacuum hose from the fuel
pressure regulator. (6) Loosen the hose clamp and disconnect the
engine ventilation hose from the throttle body. (7) Remove the bolts securing the fuel rail and
injectors to the inlet manifold. (8) Carefully raise the fuel rail and injectors
from the inlet manifold until the injector nozzles are
clear of the manifold. (9) Disconnect each injector wiring connector by
pushing in the wire retaining clip.
(10) Using a small screwdriver, remove the injec-
tor retaining clip and withdraw the injectors from the
fuel rail.
Installation is a reversal of the removal procedure
with attention to the following points:
(1) Check the condition of the injector O ring
seals and renew if necessary. (2) Install the injectors to the fuel rail and secure
with the retaining clips. (3) Connect the wiring connectors to each injec-
tor ensuring that the wire clip is locked in position. (4) Install the injectors to the inlet manifold,
carefully guiding the injectors into place ensuring that
the O ring seals are not damaged.
(5) Install the fuel rail retaining bolts and tighten
to the specified torque. (6) Install the fuel hoses to the fuel rail
and
tighten the hose clamps securely.
(7) Check for fuel leaks as previously described.
To Remove and Install Injector — 1.6 Liter Engine
(1) Depressurize the fuel system as previously
described. (2) Disconnect the negative battery terminal.
(3) Remove the air cleaner assembly. If neces-
sary refer to the heading Air Cleaner Assembly in this
section.
(4) Remove the injector retaining plate screw
and remove the injector retaining plate from the
throttle body assembly. (5) Insert the blade of a screwdriver from the
front of the throttle body assembly under the rim of
the injector in which the retaining plate locates.
Support the screwdriver on a suitable object to act as
a fulcrum. (6) Carefully lever the screwdriver until the
injector can be withdrawn from the throttle body
assembly.
(7) Remove and discard the upper and lower O
ring seals from the injector . If necessary remove the
lower filter screen from the injector.
NOTE: As the injector contains electrical
View of the fuel injector removed from the throttle body assembly. 1.6 liter engine.
Page 97 of 238
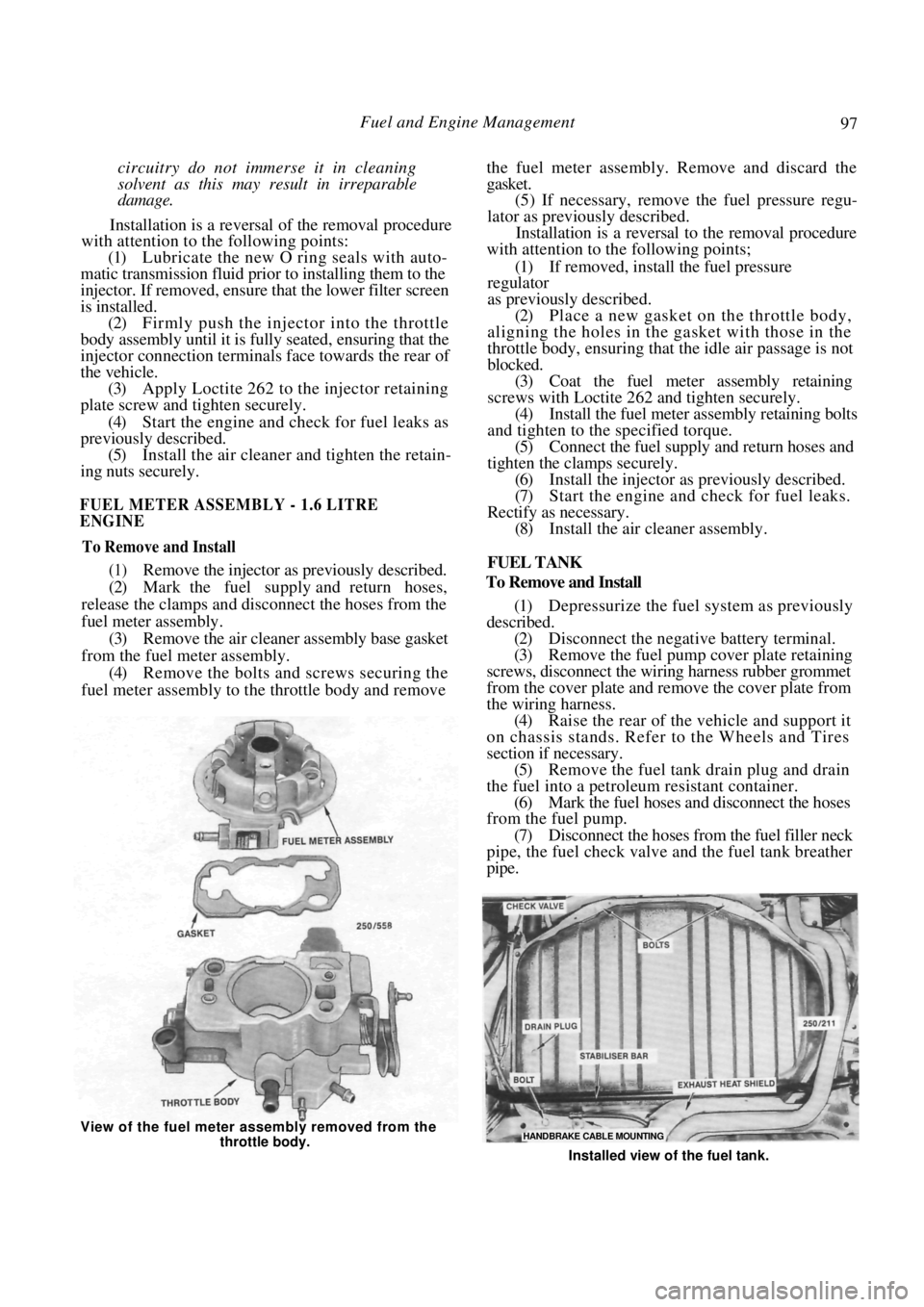
Fuel and Engine Management 97
circuitry do not immerse it in cleaning
solvent as this may result in irreparable
damage.
Installation is a reversal of the removal procedure
with attention to the following points:
(1) Lubricate the new O ring seals with auto-
matic transmission fluid prior to installing them to the
injector. If removed, ensure that the lower filter screen
is installed. (2) Firmly push the injector into the throttle
body assembly until it is fully seated, ensuring that the
injector connection terminals face towards the rear of
the vehicle.
(3) Apply Loctite 262 to the injector retaining
plate screw and tighten securely.
(4) Start the engine and check for fuel leaks as
previously described.
(5) Install the air cleaner and tighten the retain-
ing nuts securely.
FUEL METER ASSEMBLY - 1.6 LITRE
ENGINE
To Remove and Install
(1) Remove the injector as previously described.
(2) Mark the fuel supp ly and return hoses,
release the clamps and disconnect the hoses from the
fuel meter assembly.
(3) Remove the air cleaner assembly base gasket
from the fuel meter assembly. (4) Remove the bolts and screws securing the
fuel meter assembly to the throttle body and remove the fuel meter assembly. Remove and discard the
gasket.
(5) If necessary, remove the fuel pressure regu-
lator as previously described.
Installation is a reversal to the removal procedure
with attention to the following points;
(1) If removed, install the fuel pressure
regulator
as previously described.
(2) Place a new gasket on the throttle body,
aligning the holes in the gasket with those in the
throttle body, ensuring that the idle air passage is not
blocked. (3) Coat the fuel meter assembly retaining
screws with Loctite 26 2 and tighten securely.
(4) Install the fuel meter assembly retaining bolts
and tighten to the specified torque.
(5) Connect the fuel supply and return hoses and
tighten the clamps securely. (6) Install the injector as previously described.
(7) Start the engine and check for fuel leaks.
Rectify as necessary. (8) Install the air cleaner assembly.
FUEL TANK
To Remove and Install
(1) Depressurize the fuel system as previously
described.
(2) Disconnect the negative battery terminal.
(3) Remove the fuel pump cover plate retaining
screws, disconnect the wi ring harness rubber grommet
from the cover plate and remove the cover plate from
the wiring harness. (4) Raise the rear of the vehicle and support it
on chassis stands. Refer to the Wheels and Tires
section if necessary. (5) Remove the fuel tank drain plug and drain
the fuel into a petroleum resistant container. (6) Mark the fuel hoses and disconnect the hoses
from the fuel pump.
(7) Disconnect the hoses from the fuel filler neck
pipe, the fuel check valve and the fuel tank breather
pipe.
View of the fuel meter assembly removed from the
throttle body. HANDBRAKE CABLE MOUNTING
Installed view of the fuel tank.
Page 98 of 238
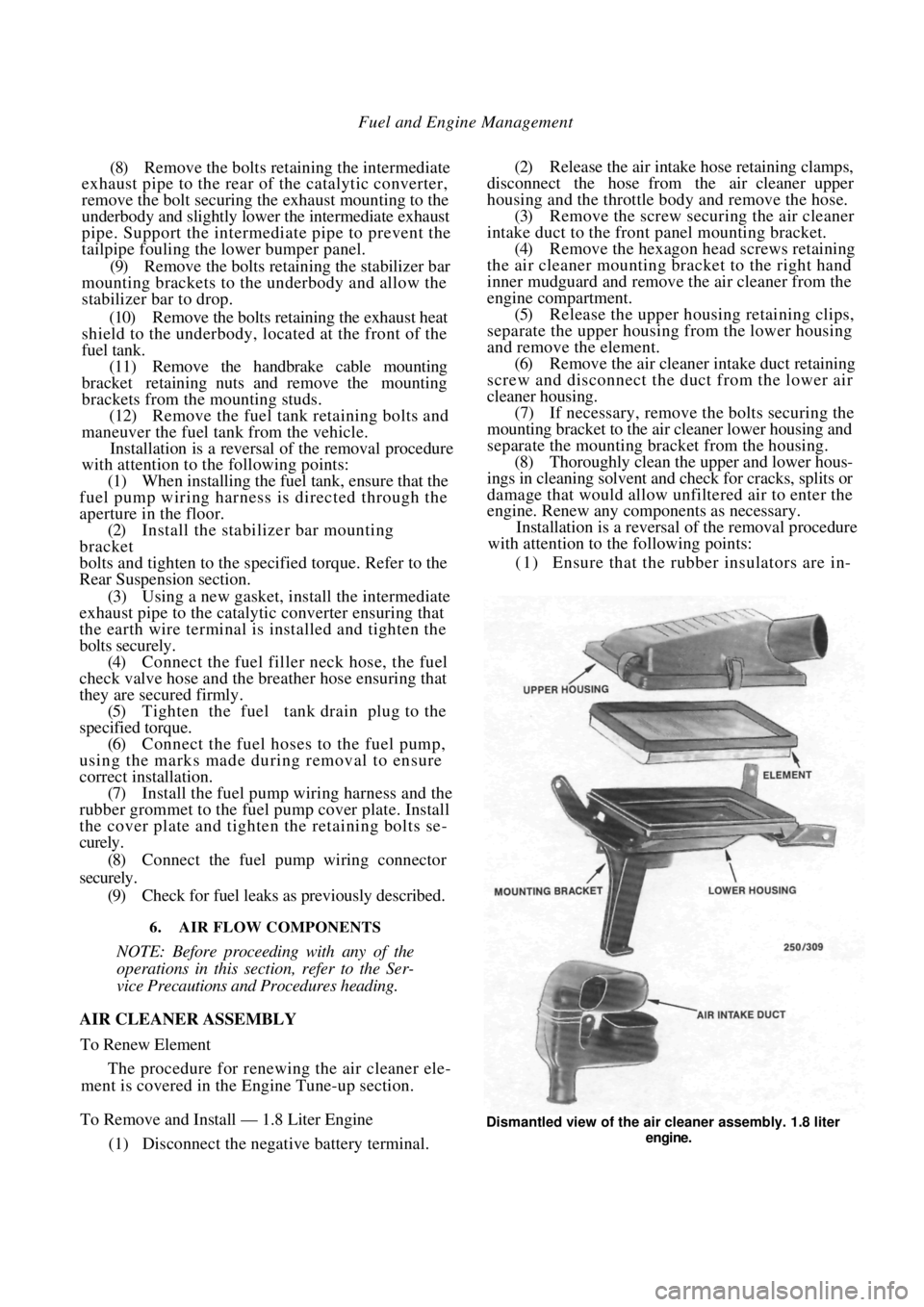
Fuel and Engine Management
(8) Remove the bolts retaining the intermediate
exhaust pipe to the rear of the catalytic converter,
remove the bolt securing the exhaust mounting to the
underbody and slightly lower the intermediate exhaust
pipe. Support the intermediate pipe to prevent the
tailpipe fouling the lower bumper panel.
(9) Remove the bolts retaining the stabilizer bar
mounting brackets to the underbody and allow the
stabilizer bar to drop.
(10) Remove the bolts retaining the exhaust heat
shield to the underbody, located at the front of the
fuel tank. (11) Remove the handbrake cable mounting
bracket retaining nuts and remove the mounting
brackets from the mounting studs. (12) Remove the fuel tank retaining bolts and
maneuver the fuel tank from the vehicle. Installation is a reversal of the removal procedure
with attention to the following points:
(1) When installing the fuel tank, ensure that the
fuel pump wiring harness is directed through the
aperture in the floor. (2) Install the stabilizer bar mounting
bracket
bolts and tighten to the specified torque. Refer to the
Rear Suspension section.
(3) Using a new gasket, install the intermediate
exhaust pipe to the catalyti c converter ensuring that
the earth wire terminal is installed and tighten the
bolts securely. (4) Connect the fuel filler neck hose, the fuel
check valve hose and the breat her hose ensuring that
they are secured firmly. (5) Tighten the fuel tank drain plug to the
specified torque. (6) Connect the fuel hoses to the fuel pump,
using the marks made during removal to ensure
correct installation. (7) Install the fuel pump wiring harness and the
rubber grommet to the fuel pump cover plate. Install
the cover plate and tighten the retaining bolts se-
curely.
(8) Connect the fuel pump wiring connector
securely. (9) Check for fuel leaks as previously described.
6. AIR FLOW COMPONENTS
NOTE: Before proceeding with any of the
operations in this section, refer to the Ser-
vice Precautions and Procedures heading.
AIR CLEANER ASSEMBLY
To Renew Element
The procedure for renewing the air cleaner ele-
ment is covered in the Engine Tune-up section.
To Remove and Install — 1.8 Liter Engine
(1) Disconnect the negative battery terminal.
(2) Release the air intake hose retaining clamps,
disconnect the hose from the air cleaner upper
housing and the throttle body and remove the hose. (3) Remove the screw securing the air cleaner
intake duct to the front panel mounting bracket. (4) Remove the hexagon head screws retaining
the air cleaner mounting bracket to the right hand
inner mudguard and remove the air cleaner from the
engine compartment. (5) Release the upper housing retaining clips,
separate the upper housing from the lower housing
and remove the element. (6) Remove the air cleaner intake duct retaining
screw and disconnect the duct from the lower air
cleaner housing. (7) If necessary, remove the bolts securing the
mounting bracket to the ai r cleaner lower housing and
separate the mounting bracket from the housing. (8) Thoroughly clean the upper and lower hous-
ings in cleaning solvent and check for cracks, splits or
damage that would allow unfiltered air to enter the
engine. Renew any components as necessary.
Installation is a reversal of the removal procedure
with attention to the following points:
(1) Ensure that the r ubber insulators are in-
Dismantled view of the ai r cleaner assembly. 1.8 liter
engine.
Page 99 of 238
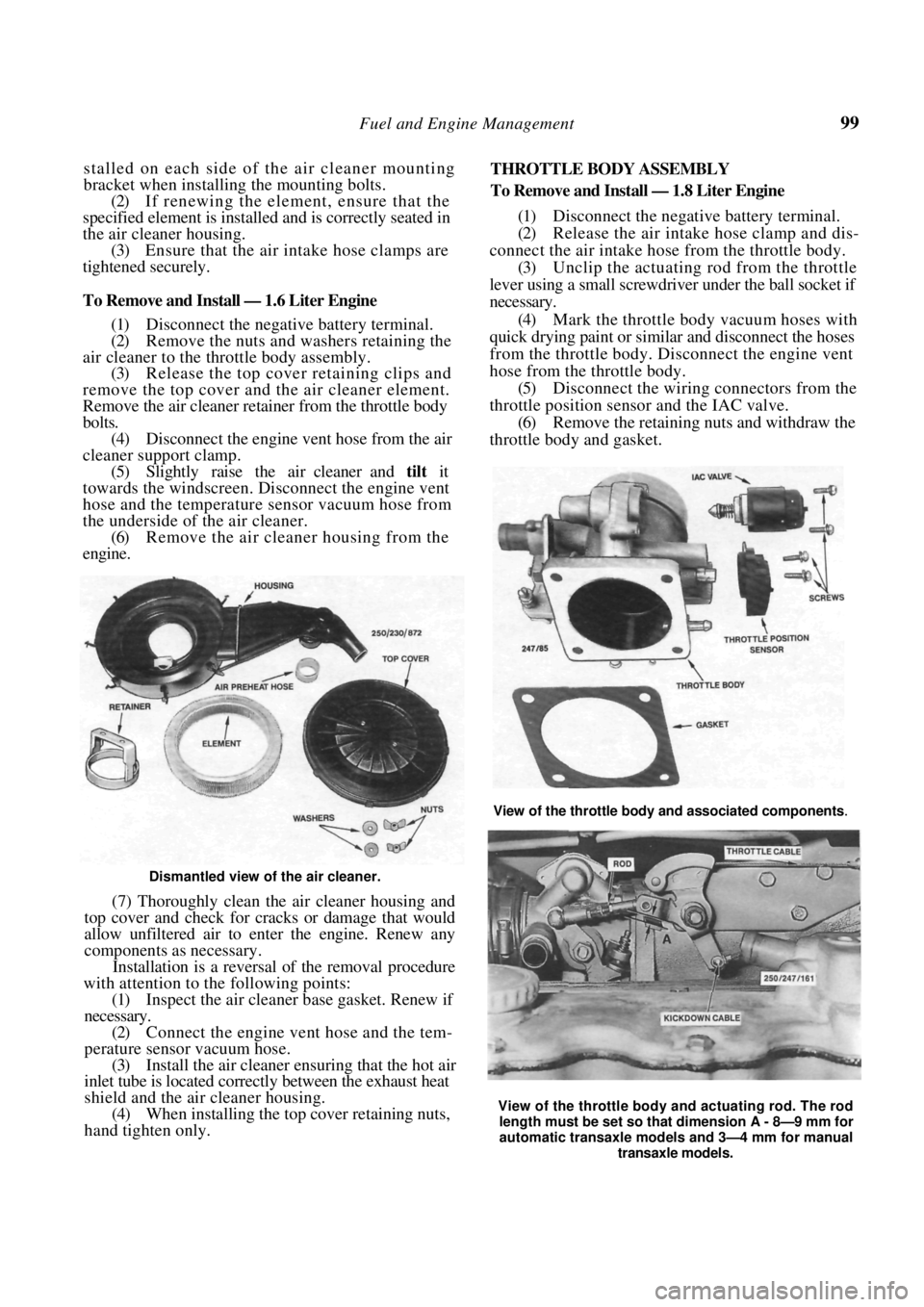
Fuel and Engine Management 99
stalled on each side of the air cleaner mounting
bracket when installing the mounting bolts.
(2) If renewing the element, ensure that the
specified element is installed and is correctly seated in
the air cleaner housing. (3) Ensure that the air intake hose clamps are
tightened securely.
To Remove and Install — 1.6 Liter Engine
(1) Disconnect the negative battery terminal.
(2) Remove the nuts and washers retaining the
air cleaner to the throttle body assembly. (3) Release the top cover retaining clips and
remove the top cover and the air cleaner element.
Remove the air cleaner retainer from the throttle body
bolts. (4) Disconnect the engine vent hose from the air
cleaner support clamp. (5) Slightly raise the air cleaner and tilt it
towards the windscreen. Disc onnect the engine vent
hose and the temperature sensor vacuum hose from
the underside of the air cleaner. (6) Remove the air cleaner housing from the
engine.
Dismantled view of the air cleaner.
(7) Thoroughly clean the air cleaner housing and
top cover and check for cracks or damage that would
allow unfiltered air to enter the engine. Renew any
components as necessary.
Installation is a reversal of the removal procedure
with attention to the following points:
(1) Inspect the air cleaner base gasket. Renew if
necessary. (2) Connect the engine vent hose and the tem-
perature sensor vacuum hose. (3) Install the air cleaner ensuring that the hot air
inlet tube is located correc tly between the exhaust heat
shield and the air cleaner housing. (4) When installing the top cover retaining nuts,
hand tighten only. THROTTLE BODY ASSEMBLY
To Remove and Install — 1.8 Liter Engine
(1)
Disconnect the negative battery terminal.
(2) Release the air intake hose clamp and dis-
connect the air intake hose from the throttle body. (3) Unclip the actuating rod from the throttle
lever using a small screwdriver under the ball socket if
necessary.
(4) Mark the throttle body vacuum hoses with
quick drying paint or similar and disconnect the hoses
from the throttle body. Disconnect the engine vent
hose from the throttle body. (5) Disconnect the wiring connectors from the
throttle position sensor and the IAC valve.
(6) Remove the retaining nuts and withdraw the
throttle body and gasket.
View of the throttle body and actuating rod. The rod
length must be set so that dimension A - 8—9 mm for
automatic transaxle models and 3—4 mm for manual
transaxle models.
View of the throttle body and associated components.
Page 100 of 238
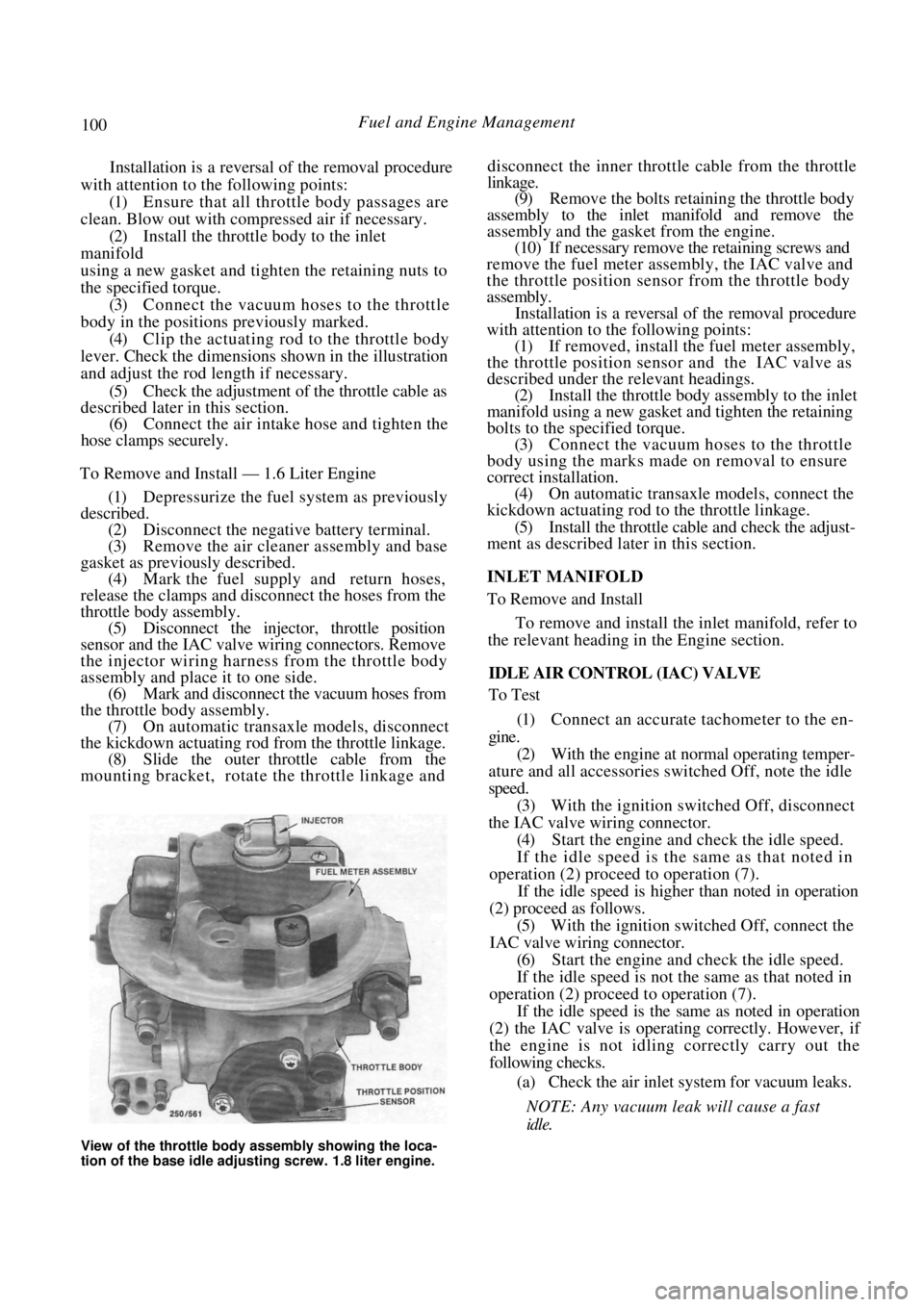
100 Fuel and Engine Management
Installation is a reversal of the removal procedure
with attention to the following points:
(1) Ensure that all throttle body passages are
clean. Blow out with compressed air if necessary. (2) Install the throttle body to the inlet
manifold
using a new gasket and tighten the retaining nuts to
the specified torque. (3) Connect the vacuum hoses to the throttle
body in the positions previously marked. (4) Clip the actuating rod to the throttle body
lever. Check the dimensions shown in the illustration
and adjust the rod length if necessary.
(5) Check the adjustment of the throttle cable as
described later in this section.
(6) Connect the air intake hose and tighten the
hose clamps securely.
To Remove and Install — 1.6 Liter Engine
(1) Depressurize the fuel system as previously
described. (2) Disconnect the negative battery terminal.
(3) Remove the air cleane r assembly and base
gasket as previously described. (4) Mark the fuel supply and return hoses,
release the clamps and disconnect the hoses from the
throttle body assembly. (5) Disconnect the injector, throttle position
sensor and the IAC valve wiring connectors. Remove
the injector wiring harness from the throttle body
assembly and place it to one side.
(6) Mark and disconnect the vacuum hoses from
the throttle body assembly. (7) On automatic transaxle models, disconnect
the kickdown actuating rod from the throttle linkage.
(8) Slide the outer throttle cable from the
mounting bracket, rotate the throttle linkage and disconnect the inner throttle cable from the throttle
linkage.
(9)
Remove the bolts retaining the throttle body
assembly to the inlet manifold and remove the
assembly and the gasket from the engine. (10) If necessary remove the retaining screws and
remove the fuel meter assembly, the IAC valve and
the throttle position sensor from the throttle body
assembly. Installation is a reversal of the removal procedure
with attention to the following points:
(1) If removed, install the fuel meter assembly,
the throttle position sensor and the IAC valve as
described under the relevant headings. (2) Install the throttle body assembly to the inlet
manifold using a new gasket and tighten the retaining
bolts to the specified torque. (3) Connect the vacuum ho ses to the throttle
body using the marks made on removal to ensure
correct installation. (4) On automatic transaxle models, connect the
kickdown actuating rod to the throttle linkage.
(5) Install the throttle cable and check the adjust-
ment as described later in this section.
INLET MANIFOLD
To Remove and Install
To remove and install the inlet manifold, refer to
the relevant heading in the Engine section.
IDLE AIR CONTROL (IAC) VALVE
To Test
(1) Connect an accurate tachometer to the en-
gine. (2) With the engine at normal operating temper-
ature and all accessories switched Off, note the idle
speed.
(3) With the ignition switched Off, disconnect
the IAC valve wiring connector. (4) Start the engine and check the idle speed.
If the idle speed is the same as that noted in
operation (2) proceed to operation (7).
If the idle speed is higher than noted in operation
(2) proceed as follows.
(5) With the ignition switched Off, connect the
IAC valve wiring connector.
(6) Start the engine and check the idle speed.
If the idle speed is not the same as that noted in
operation (2) proceed to operation (7).
If the idle speed is the same as noted in operation
(2) the IAC valve is operating correctly. However, if
the engine is not idling correctly carry out the
following checks.
(a) Check the air inlet system for vacuum leaks.
NOTE: Any vacuum leak will cause a fast
idle.
View of the throttle body assembly showing the loca-
tion of the base idle adjusting screw. 1.8 literengine.