NISSAN PULSAR 1987 Workshop Manual
Manufacturer: NISSAN, Model Year: 1987, Model line: PULSAR, Model: NISSAN PULSAR 1987Pages: 238, PDF Size: 28.91 MB
Page 121 of 238
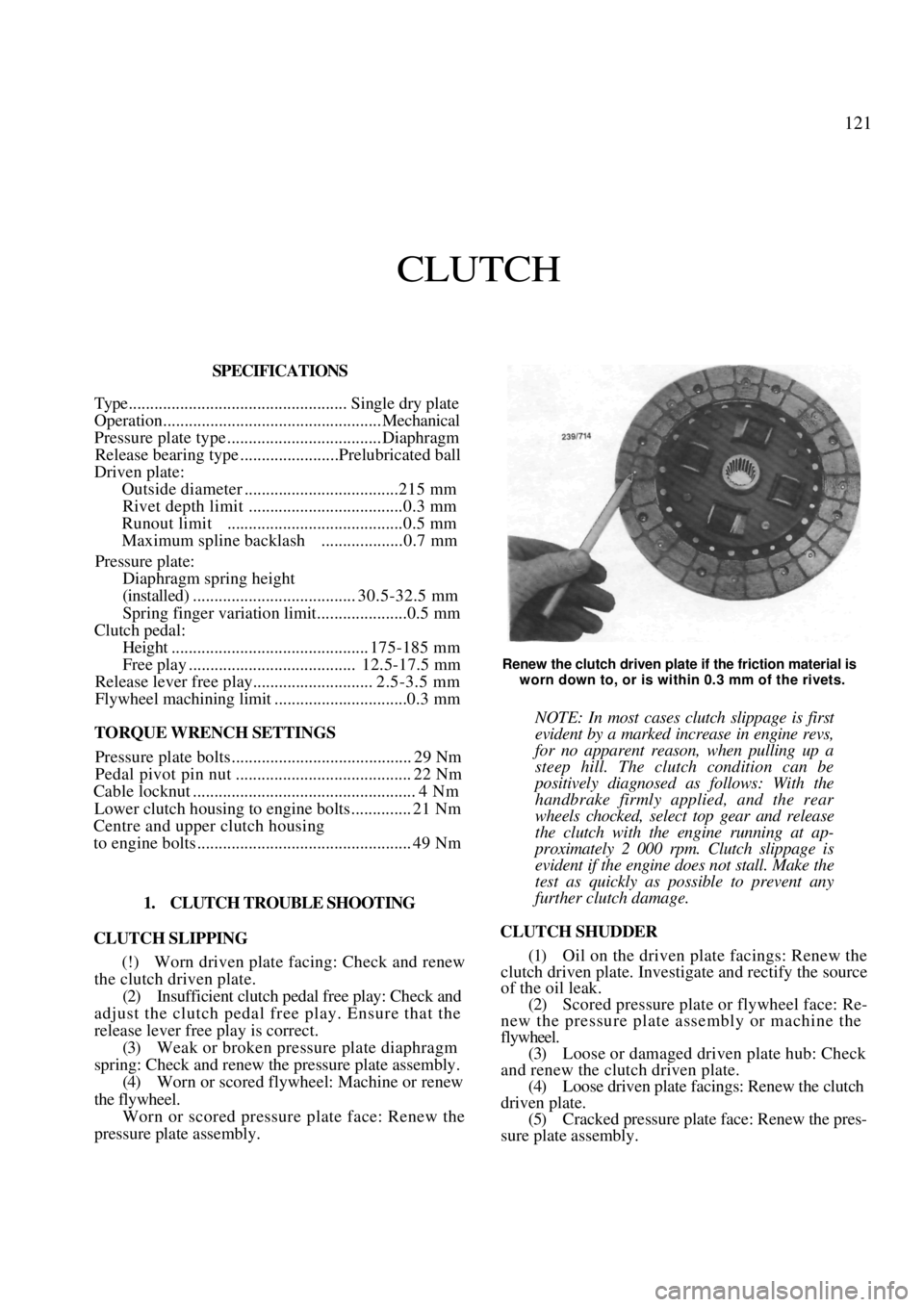
121
CLUTCH
SPECIFICATIONS
Type................................................... Single dry plate
Operation................................................... Mechanical
Pressure plate type .................................... Diaphragm
Release bearing type .......................Prelubri cated ball
Driven plate:
Outside diameter .................................... 215 mm
Rivet depth limit ....................................0.3 mm
Runout limit .........................................0.5 mm
Maximum spline backlash ...................0.7 mm
Pressure plate:
Diaphragm spring height
(installed) ...................................... 30.5-32.5 mm
Spring finger vari ation limit.....................0.5 mm
Clutch pedal:
Height .............................................. 175-185 mm
Free play ....................................... 12.5-17.5 mm
Release lever free play............................ 2.5-3.5 mm
Flywheel machining limit ...............................0.3 mm
TORQUE WRENCH SETTINGS
Pressure plate bolts.......................................... 29 Nm
Pedal pivot pin nut ......................................... 22 Nm
Cable loc knut.................................................... 4 Nm
Lower clutch housing to engine bolts.............. 21 Nm
Centre and upper clutch housing
to engine bolts .................................................. 49 Nm
1. CLUTCH TROUBLE SHOOTING
CLUTCH SLIPPING
(!) Worn driven plate facing: Check and renew
the clutch driven plate.
(2) Insufficient clutch pedal free play: Check and
adjust the clutch pedal free play. Ensure that the
release lever free play is correct.
(3) Weak or broken pressure plate diaphragm
spring: Check and renew the pressure plate assembly. (4) Worn or scored flywh eel: Machine or renew
the flywheel. Worn or scored pressure plate face: Renew the
pressure plate assembly.
Renew the clutch driven plate if the friction material is
worn down to, or is within 0.3 mm of the rivets.
NOTE: In most cases clutch slippage is first
evident by a marked increase in engine revs,
for no apparent reason, when pulling up a
steep hill. The clutch condition can be
positively diagnosed as follows: With the
handbrake firmly applied, and the rear
wheels chocked, select top gear and release
the clutch with the engine running at ap-
proximately 2 000 rpm. Clutch slippage is
evident if the engine does not stall. Make the
test as quickly as possible to prevent any
further clutch damage.
CLUTCH SHUDDER
(1) Oil on the driven plate facings: Renew the
clutch driven plate. Invest igate and rectify the source
of the oil leak.
(2) Scored pressure plate or flywheel face: Re-
new the pressure plate assembly or machine the
flywheel. (3) Loose or damaged driven plate hub: Check
and renew the clutch driven plate. (4) Loose driven plate facings: Renew the clutch
driven plate. (5) Cracked pressure plate face: Renew the pres-
sure plate assembly.
Page 122 of 238
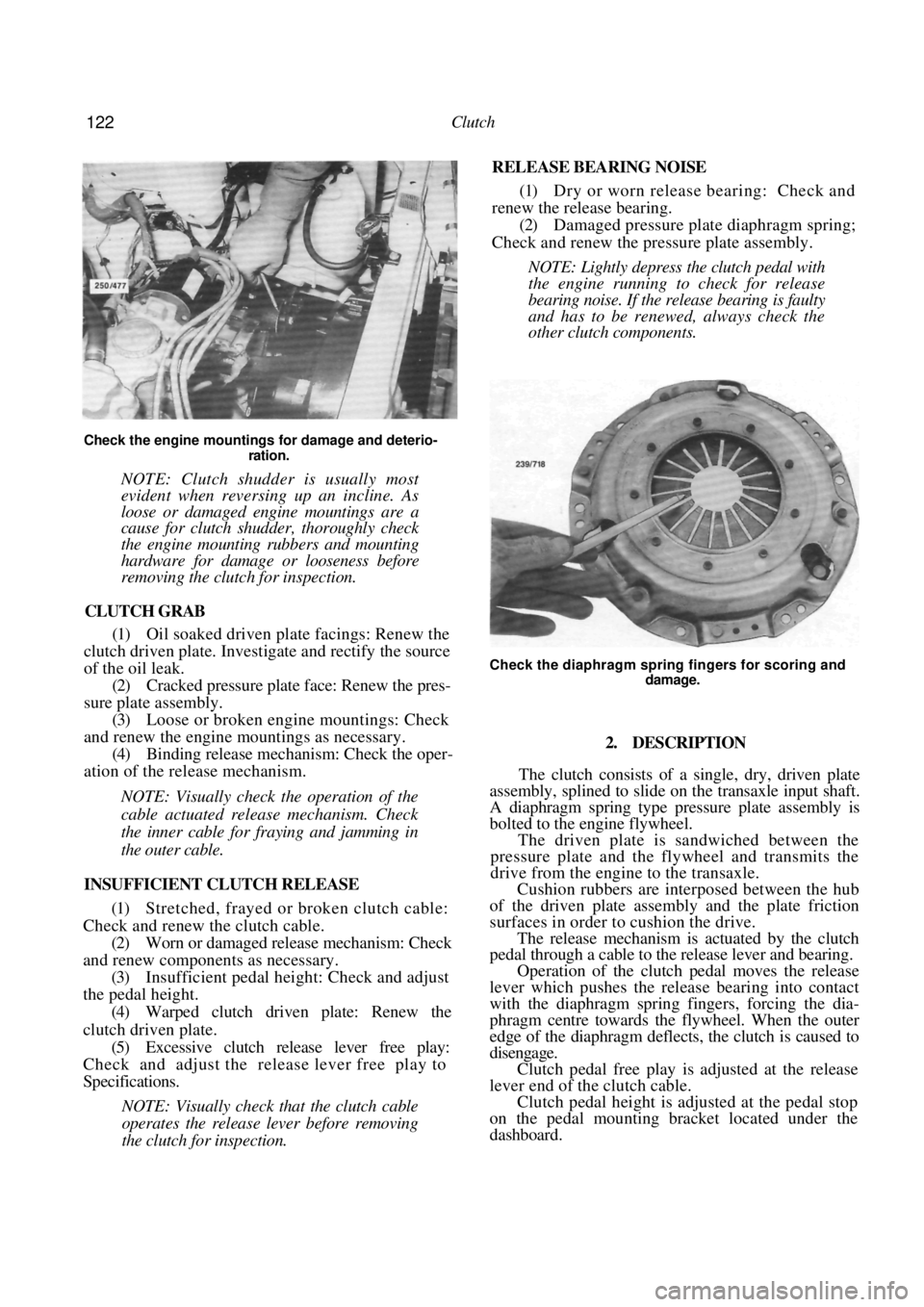
122 Clutch
Check the engine mountings for damage and deterio- ration.
NOTE: Clutch shudder is usually most
evident when reversing up an incline. As
loose or damaged engine mountings are a
cause for clutch shudder, thoroughly check
the engine mounting rubbers and mounting
hardware for damage or looseness before
removing the clutch for inspection.
CLUTCH GRAB
(1) Oil soaked driven plate facings: Renew the
clutch driven plate. Invest igate and rectify the source
of the oil leak.
(2) Cracked pressure plate face: Renew the pres-
sure plate assembly. (3) Loose or broken engine mountings: Check
and renew the engine mountings as necessary.
(4) Binding release mechanism: Check the oper-
ation of the release mechanism.
NOTE: Visually check the operation of the
cable actuated release mechanism. Check
the inner cable for fraying and jamming in
the outer cable.
INSUFFICIENT CLUTCH RELEASE
(1) Stretched, frayed or broken clutch cable:
Check and renew the clutch cable. (2) Worn or damaged release mechanism: Check
and renew components as necessary. (3) Insufficient pedal height: Check and adjust
the pedal height.
(4) Warped clutch driven plate: Renew the
clutch driven plate. (5) Excessive clutch release lever free play:
Check and adjust the release lever free play to
Specifications.
NOTE: Visually check that the clutch cable
operates the release lever before removing
the clutch for inspection.
RELEASE BEARING NOISE
(1) Dry or worn release bearing: Check and
renew the release bearing.
(2) Damaged pressure plate diaphragm spring;
Check and renew the pressure plate assembly.
NOTE: Lightly depress the clutch pedal with
the engine running to check for release
bearing noise. If the release bearing is faulty
and has to be renewed, always check the
other clutch components.
Check the diaphragm spring fingers for scoring and damage.
2. DESCRIPTION
The clutch consists of a single, dry, driven plate
assembly, splined to slide on the transaxle input shaft.
A diaphragm spring type pr essure plate assembly is
bolted to the engine flywheel.
The driven plate is sandwiched between the
pressure plate and the flywheel and transmits the
drive from the engine to the transaxle.
Cushion rubbers are interposed between the hub
of the driven plate assembly and the plate friction
surfaces in order to cushion the drive.
The release mechanism is actuated by the clutch
pedal through a cable to the release lever and bearing.
Operation of the clutch pedal moves the release
lever which pushes the release bearing into contact
with the diaphragm spring fingers, forcing the dia-
phragm centre towards the flywheel. When the outer
edge of the diaphragm deflects, the clutch is caused to
disengage.
Clutch pedal free play is adjusted at the release
lever end of the clutch cable.
Clutch pedal height is adjusted at the pedal stop
on the pedal mounting bracket located under the
dashboard.
Page 123 of 238
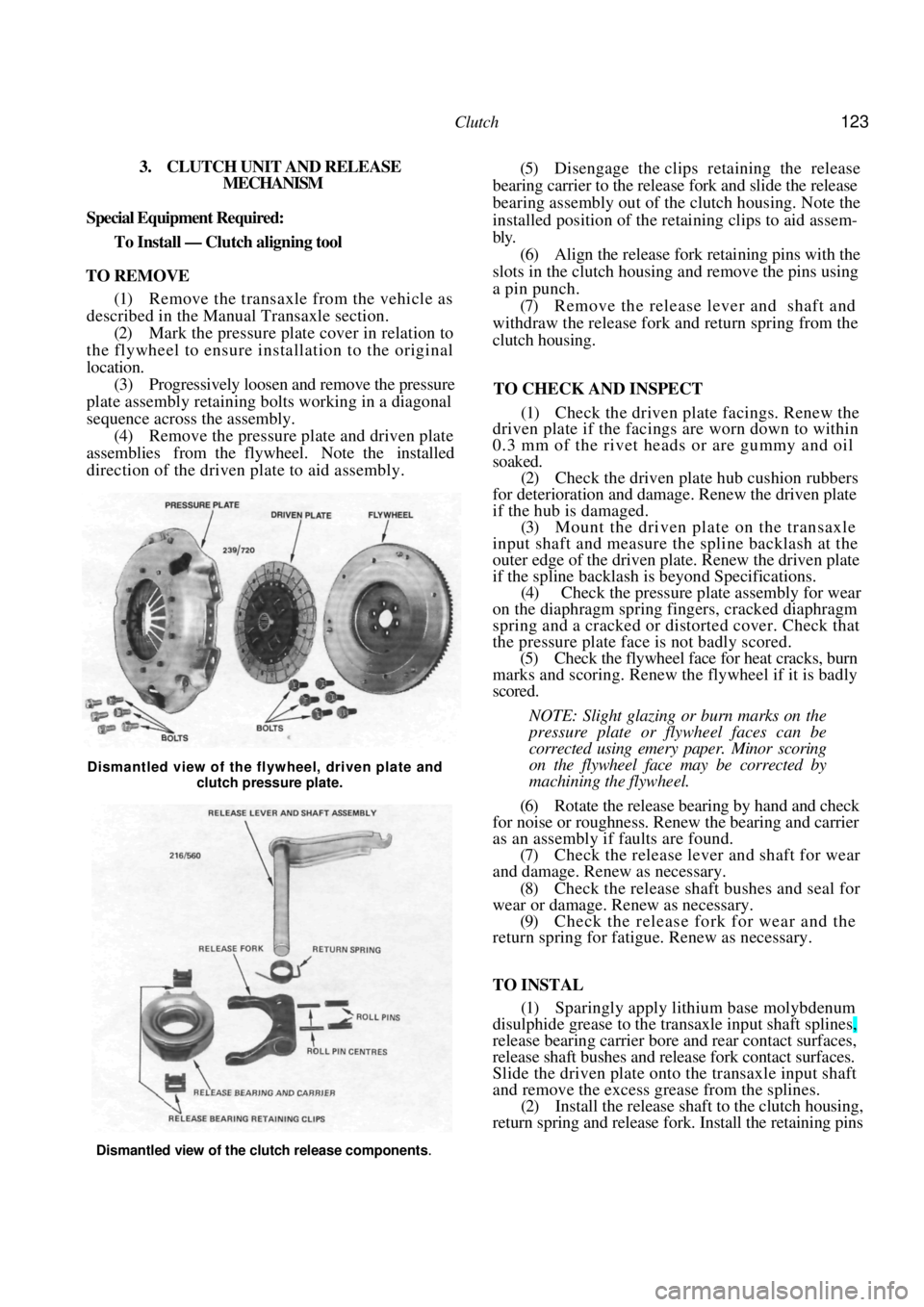
Clutch 123
3. CLUTCH UNIT AND RELEASE MECHANISM
Special Equipment Required:
To Install — Clutch aligning tool
TO REMOVE
(1) Remove the transaxle from the vehicle as
described in the Manual Transaxle section. (2) Mark the pressure plate cover in relation to
the flywheel to ensure installation to the original
location. (3) Progressively loosen and remove the pressure
plate assembly retaining bolts working in a diagonal
sequence across the assembly. (4) Remove the pressure plate and driven plate
assemblies from the flywheel. Note the installed
direction of the driven plate to aid assembly.
(5) Disengage the clips retaining the release
bearing carrier to the release fork and slide the release
bearing assembly out of the clutch housing. Note the
installed position of the re taining clips to aid assem-
bly. (6) Align the release fork retaining pins with the
slots in the clutch housing and remove the pins using
a pin punch.
(7) Remove the release lever and shaft and
withdraw the release fork and return spring from the
clutch housing.
TO CHECK AND INSPECT
(1) Check the driven plate facings. Renew the
driven plate if the facings are worn down to within
0.3 mm of the rivet heads or are gummy and oil
soaked.
(2) Check the driven plate hub cushion rubbers
for deterioration and damage. Renew the driven plate
if the hub is damaged. (3) Mount the driven plate on the transaxle
input shaft and measure the spline backlash at the
outer edge of the driven plate. Renew the driven plate
if the spline backlash is beyond Specifications. (4) Check the pressure pl ate assembly for wear
on the diaphragm spring fingers, cracked diaphragm
spring and a cracked or distorted cover. Check that
the pressure plate face is not badly scored.
(5) Check the flywheel face for heat cracks, burn
marks and scoring. Renew the flywheel if it is badly
scored.
NOTE: Slight glazing or burn marks on the
pressure plate or flywheel faces can be
corrected using emery paper. Minor scoring
on the flywheel face may be corrected by
machining the flywheel.
(6) Rotate the release bearing by hand and check
for noise or roughness. Renew the bearing and carrier
as an assembly if fa ults are found.
(7) Check the release lever and shaft for wear
and damage. Renew as necessary.
(8) Check the release shaft bushes and seal for
wear or damage. Renew as necessary.
(9) Check the release fork for wear and the
return spring for fatigue. Renew as necessary.
TO INSTAL
(1) Sparingly apply lithium base molybdenum
disulphide grease to the tr ansaxle input shaft splines,
release bearing carrier bore and rear contact surfaces,
release shaft bushes and release fork contact surfaces.
Slide the driven plate onto the transaxle input shaft
and remove the excess grease from the splines. (2) Install the release shaft to the clutch housing,
return spring and release fork. Install the retaining pins
Dismantled view of the flywheel, driven plate and
clutch pressure plate.
Dismantled view of the clutch release components.
Page 124 of 238
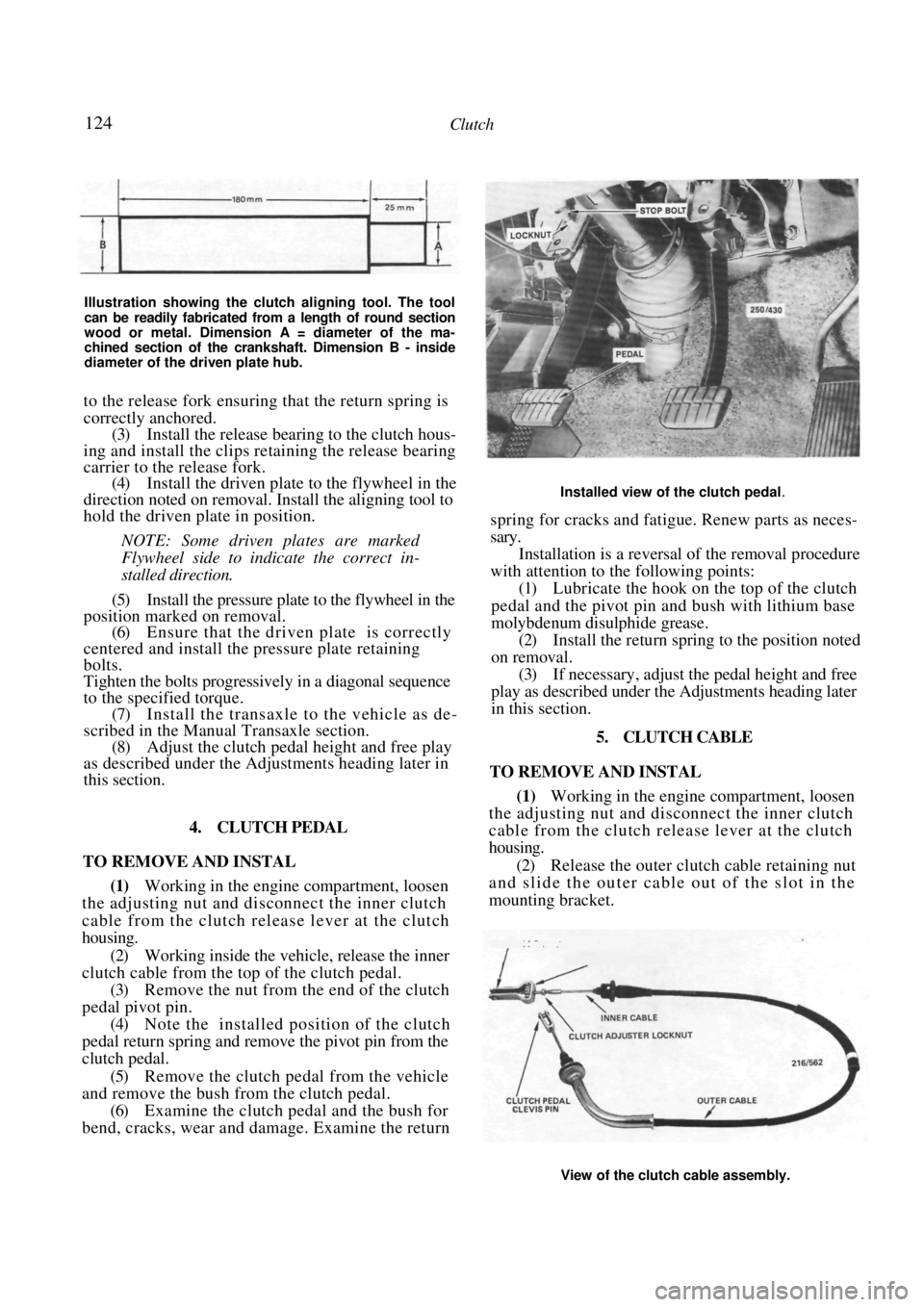
124 Clutch
Illustration showing the clutch aligning tool. The tool
can be readily fabricated from a length of round section
wood or metal. Dimension A = diameter of the ma-
chined section of the crankshaft. Dimension B - inside
diameter of the driven plate hub.
to the release fork ensuring that the return spring is
correctly anchored.
(3) Install the release bearing to the clutch hous-
ing and install the clips re taining the release bearing
carrier to the release fork. (4) Install the driven plate to the flywheel in the
direction noted on removal. Install the aligning tool to
hold the driven plate in position.
NOTE: Some driven plates are marked
Flywheel side to indicate the correct in-
stalled direction.
(5) Install the pressure plate to the flywheel in the
position marked on removal. (6) Ensure that the driven plate is correctly
centered and install the pressure plate retaining
bolts.
Tighten the bolts progressively in a diagonal sequence
to the specified torque. (7) Install the transaxle to the vehicle as de-
scribed in the Manual Transaxle section. (8) Adjust the clutch pedal height and free play
as described under the Adjustments heading later in
this section.
4. CLUTCH PEDAL
TO REMOVE AND INSTAL
(1) Working in the engine compartment, loosen
the adjusting nut and disconnect the inner clutch
cable from the clutch release lever at the clutch
housing.
(2) Working inside the vehicle, release the inner
clutch cable from the top of the clutch pedal.
(3) Remove the nut from the end of the clutch
pedal pivot pin. (4) Note the installed position of the clutch
pedal return spring and remove the pivot pin from the
clutch pedal.
(5) Remove the clutch pedal from the vehicle
and remove the bush from the clutch pedal. (6) Examine the clutch pedal and the bush for
bend, cracks, wear and damage. Examine the return
Installed view of the clutch pedal.
spring for cracks and fatigue. Renew parts as neces-
sary.
Installation is a reversal of the removal procedure
with attention to the following points:
(1) Lubricate the hook on the top of the clutch
pedal and the pivot pin and bush with lithium base
molybdenum disulphide grease. (2) Install the return spring to the position noted
on removal. (3) If necessary, adjust the pedal height and free
play as described under the Adjustments heading later
in this section.
5. CLUTCH CABLE
TO REMOVE AND INSTAL
(1) Working in the engine compartment, loosen
the adjusting nut and disconnect the inner clutch
cable from the clutch release lever at the clutch
housing.
(2) Release the outer clutch cable retaining nut
and slide the outer cable out of the slot in the
mounting bracket.
View of the clutch cable assembly.
Page 125 of 238
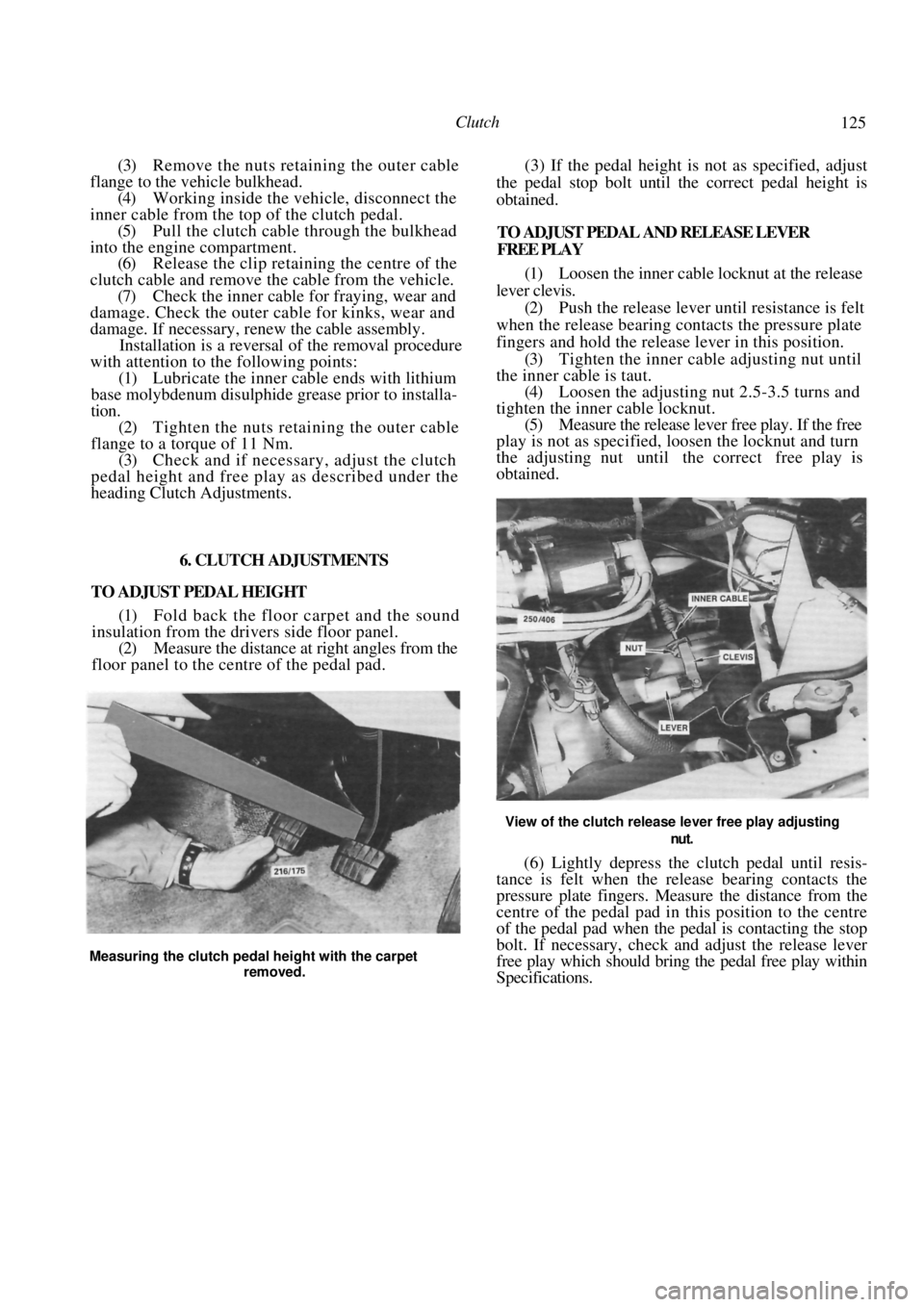
Clutch 125
(3) Remove the nuts retaining the outer cable
flange to the vehicle bulkhead.
(4) Working inside the ve hicle, disconnect the
inner cable from the top of the clutch pedal. (5) Pull the clutch cable through the bulkhead
into the engine compartment. (6) Release the clip retaining the centre of the
clutch cable and remove the cable from the vehicle. (7) Check the inner cable for fraying, wear and
damage. Check the outer cable for kinks, wear and
damage. If necessary, renew the cable assembly. Installation is a reversal of the removal procedure
with attention to the following points:
(1) Lubricate the inner cable ends with lithium
base molybdenum disulphide grease prior to installa-
tion. (2) Tighten the nuts retaining the outer cable
flange to a torque of 11 Nm. (3) Check and if necessary , adjust the clutch
pedal height and free play as described under the
heading Clutch Adjustments.
6. CLUTCH ADJUSTMENTS
TO ADJUST PEDAL HEIGHT (1) Fold back the floor carpet and the sound
insulation from the drivers side floor panel.
(2) Measure the distance at right angles from the
floor panel to the centre of the pedal pad. (3) If the pedal height is not as specified, adjust
the pedal stop bolt until the correct pedal height is
obtained.
TO ADJUST PEDAL AND RELEASE LEVER
FREE PLAY
(1) Loosen the inner cable locknut at the release
lever clevis. (2) Push the release lever until resistance is felt
when the release bearing contacts the pressure plate
fingers and hold the release lever in this position.
(3) Tighten the inner cable adjusting nut until
the inner cable is taut.
(4) Loosen the adjusting nut 2.5-3.5 turns and
tighten the inner cable locknut. (5) Measure the release lever free play. If the free
play is not as specified, loosen the locknut and turn
the adjusting nut until the correct free play is
obtained.
View of the clutch release lever free play adjusting
nut.
(6) Lightly depress the clutch pedal until resis-
tance is felt when the release bearing contacts the
pressure plate fingers. Measure the distance from the
centre of the pedal pad in this position to the centre
of the pedal pad when the pedal is contacting the stop
bolt. If necessary, check and adjust the release lever
free play which should bring the pedal free play within
Specifications.
Measuring the clutch pedal height with the carpet
removed.
Page 126 of 238
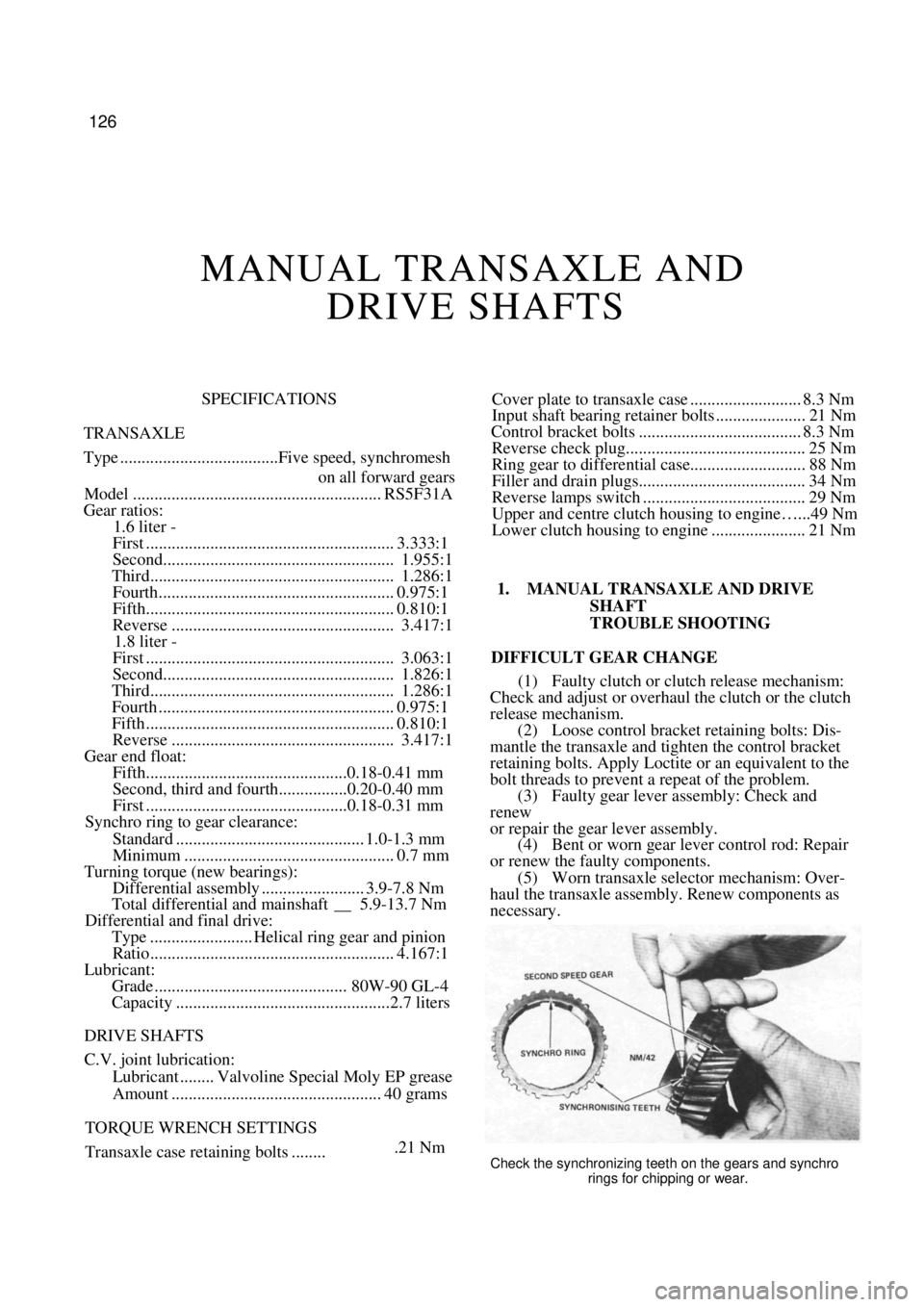
126
MANUAL TRANSAXLE AND DRIVE SHAFTS
SPECIFICATIONS
TRANSAXLE
Type .....................................Five speed, synchromesh
on all forward gears
Model .......................................................... RS5F31A
Gear ratios: 1.6 liter -
First .......................................................... 3.333:1
Second...................................................... 1.955:1
Third......................................................... 1.286:1
Fourth....................................................... 0.975:1
Fifth.......................................................... 0.810:1
Reverse .................................................... 3.417:1
1.8 liter -
First .......................................................... 3.063:1
Second...................................................... 1.826:1
Third......................................................... 1.286:1
Fourth ....................................................... 0.975:1
Fifth.......................................................... 0.810:1
Reverse .................................................... 3.417:1
Gear end float:
Fifth...............................................0.18-0.41 mm
Second, third and fourth................0.20-0.40 mm
First ...............................................0.18-0.31 mm
Synchro ring to gear clearance:
Standard ............................................ 1.0-1.3 mm
Minimum ................................................. 0.7 mm
Turning torque (new bearings):
Differential assembly ........................ 3.9-7.8 Nm
Total differential and mainshaft __ 5.9-13.7 Nm
Differential and final drive:
Type ........................ Helical ring gear and pinion
Ratio......................................................... 4.167:1
Lubricant:
Grade ............................................. 80W-90 GL-4
Capacity ..................................................2.7 liters
DRIVE SHAFTS
C.V. joint lubrication:
Lubricant ........ Valvoline Special Moly EP grease
Amount ................................................. 40 grams
TORQUE WRENCH SETTINGS
Transaxle case retaining bolts ........
Cover plate to transaxle case .......................... 8.3 Nm
Input shaft bearing retainer bolts ..................... 21 Nm
Control bracket bolts ...................................... 8.3 Nm
Reverse check plug.......................................... 25 Nm
Ring gear to differential case........................... 88 Nm
Filler and drain plugs....................................... 34 Nm
Reverse lamps switch ...................................... 29 Nm
Upper and centre clutch housing to engine…...49 Nm
Lower clutch housing to engine ...................... 21 Nm
1. MANUAL TRANSAXLE AND DRIVE
SHAFT
TROUBLE SHOOTING
DIFFICULT GEAR CHANGE
(1) Faulty clutch or clutch release mechanism:
Check and adjust or overhaul the clutch or the clutch
release mechanism. (2) Loose control bracket retaining bolts: Dis-
mantle the transaxle and tighten the control bracket
retaining bolts. Apply Loctite or an equivalent to the
bolt threads to prevent a repeat of the problem.
(3) Faulty gear lever assembly: Check and
renew
or repair the gear lever assembly. (4) Bent or worn gear lever control rod: Repair
or renew the faulty components. (5) Worn transaxle selector mechanism: Over-
haul the transaxle assembly. Renew components as
necessary.
.21 NmCheck the synchronizing teeth on the gears and synchro
rings for chipping or wear.
Page 127 of 238
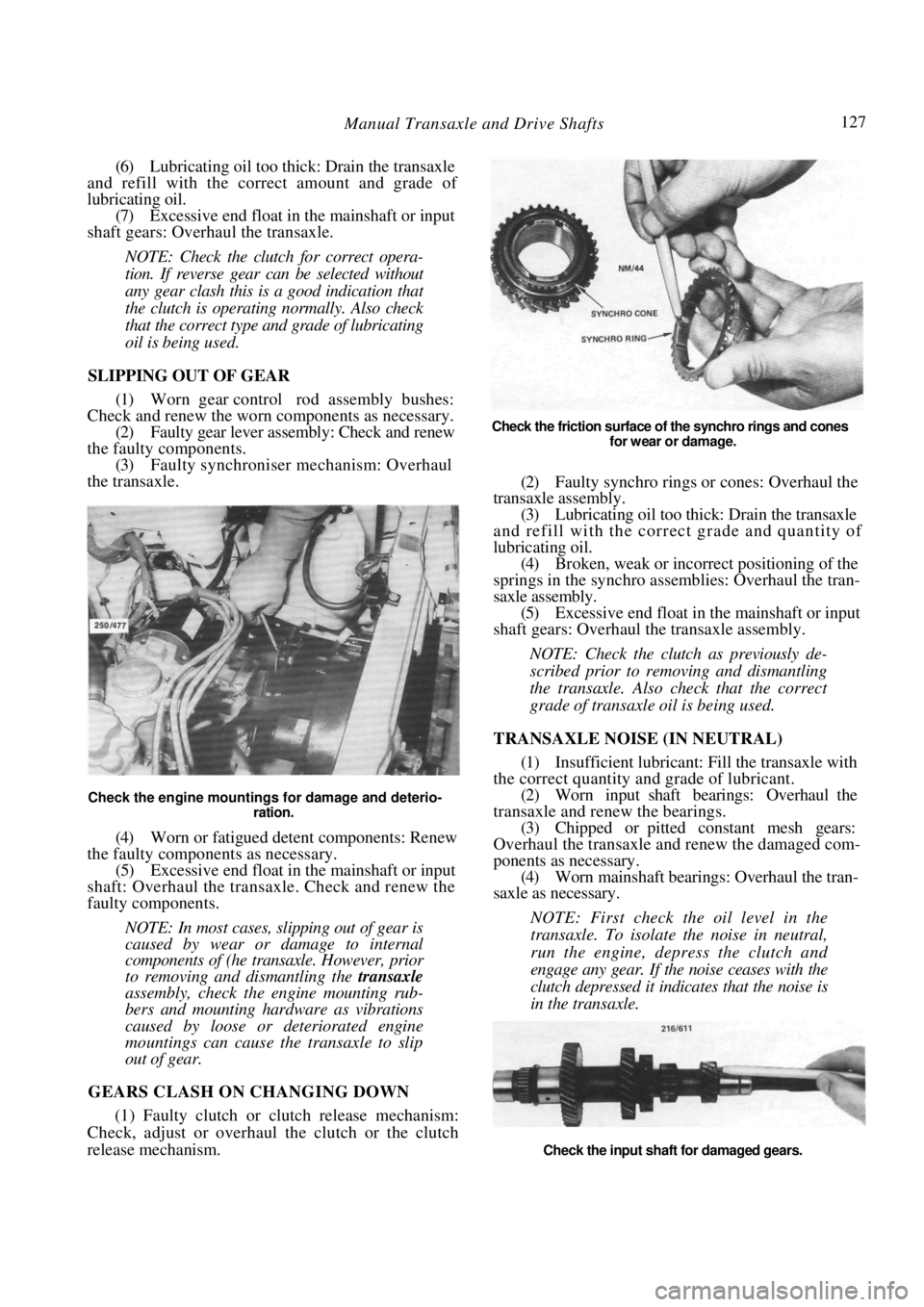
Manual Transaxle and Drive Shafts 127
(6) Lubricating oil too thick: Drain the transaxle
and refill with the corre ct amount and grade of
lubricating oil. (7) Excessive end float in the mainshaft or input
shaft gears: Overhaul the transaxle.
NOTE: Check the clutch for correct opera-
tion. If reverse gear can be selected without
any gear clash this is a good indication that
the clutch is operating normally. Also check
that the correct type and grade of lubricating
oil is being used.
SLIPPING OUT OF GEAR
(1) Worn gear control rod assembly bushes:
Check and renew the worn components as necessary. (2) Faulty gear lever assembly: Check and renew
the faulty components. (3) Faulty synchroniser mechanism: Overhaul
the transaxle.
Check the engine mountings for damage and deterio-
ration.
(4) Worn or fatigued detent components: Renew
the faulty components as necessary.
(5) Excessive end float in the mainshaft or input
shaft: Overhaul the transaxle. Check and renew the
faulty components.
NOTE: In most cases, slipping out of gear is
caused by wear or damage to internal
components of (he tran saxle. However, prior
to removing and dismantling the transaxle
assembly, check the engine mounting rub-
bers and mounting hardware as vibrations
caused by loose or deteriorated engine
mountings can cause the transaxle to slip
out of gear.
GEARS CLASH ON CHANGING DOWN
(1) Faulty clutch or clutch release mechanism:
Check, adjust or overhaul the clutch or the clutch
release mechanism.
Check the friction surface of the synchro rings and cones
for wear or damage.
(2) Faulty synchro rings or cones: Overhaul the
transaxle assembly.
(3) Lubricating oil too thick: Drain the transaxle
and refill with the correct grade and quantity of
lubricating oil. (4) Broken, weak or incorrect positioning of the
springs in the synchro asse mblies: Overhaul the tran-
saxle assembly.
(5) Excessive end float in the mainshaft or input
shaft gears: Overhaul the transaxle assembly.
NOTE: Check the clutch as previously de-
scribed prior to removing and dismantling
the transaxle. Also check that the correct
grade of transaxle oil is being used.
TRANSAXLE NOISE (IN NEUTRAL)
(1) Insufficient lubricant: Fill the transaxle with
the correct quantity and grade of lubricant. (2) Worn input shaft bearings: Overhaul the
transaxle and renew the bearings. (3) Chipped or pitted constant mesh gears:
Overhaul the transaxle and renew the damaged com-
ponents as necessary. (4) Worn mainshaft bearings: Overhaul the tran-
saxle as necessary.
NOTE: First check the oil level in the
transaxle. To isolate the noise in neutral,
run the engine, depress the clutch and
engage any gear. If the noise ceases with the
clutch depressed it indicates that the noise is
in the transaxle.
Check the input shaft for damaged gears.
Page 128 of 238
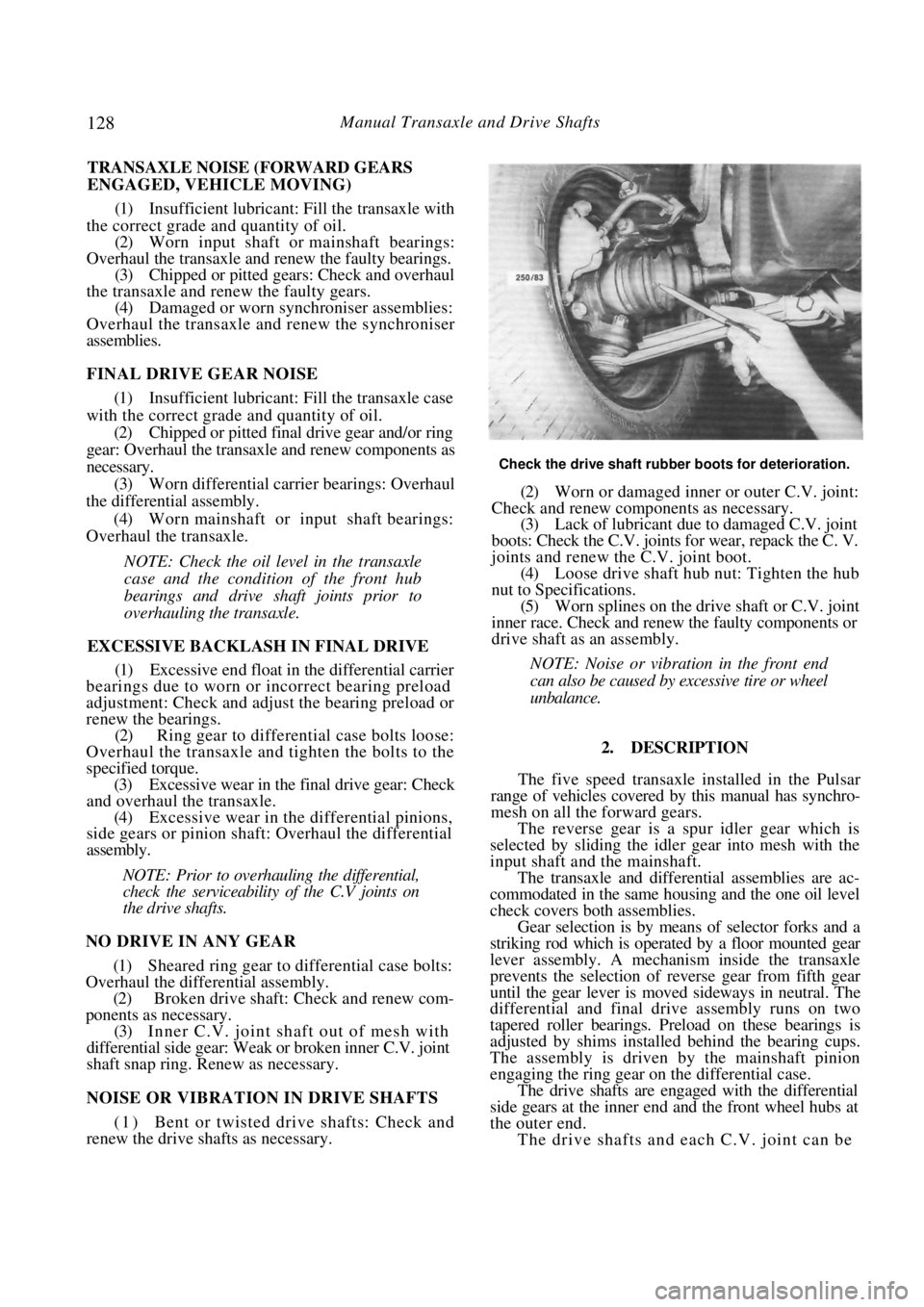
128 Manual Transaxle and Drive Shafts
TRANSAXLE NOISE (FORWARD GEARS
ENGAGED, VEHICLE MOVING)
(1) Insufficient lubricant: Fill the transaxle with
the correct grade and quantity of oil. (2) Worn input shaft or mainshaft bearings:
Overhaul the transaxle and renew the faulty bearings. (3) Chipped or pitted gears: Check and overhaul
the transaxle and renew the faulty gears. (4) Damaged or worn sync hroniser assemblies:
Overhaul the transaxle and renew the synchroniser
assemblies.
FINAL DRIVE GEAR NOISE
(1) Insufficient lubricant: Fill the transaxle case
with the correct grade and quantity of oil. (2) Chipped or pitted final drive gear and/or ring
gear: Overhaul the transaxle and renew components as
necessary. (3) Worn differential carrier bearings: Overhaul
the differential assembly.
(4) Worn mainshaft or input shaft bearings:
Overhaul the transaxle.
NOTE: Check the oil level in the transaxle
case and the condition of the front hub
bearings and drive shaft joints prior to
overhauling the transaxle.
EXCESSIVE BACKLASH IN FINAL DRIVE
(1) Excessive end float in the differential carrier
bearings due to worn or incorrect bearing preload
adjustment: Check and adjust the bearing preload or
renew the bearings.
(2) Ring gear to differential case bolts loose:
Overhaul the transaxle and tighten the bolts to the
specified torque.
(3) Excessive wear in the final drive gear: Check
and overhaul the transaxle. (4) Excessive wear in the differential pinions,
side gears or pinion shaft: Overhaul the differential
assembly.
NOTE: Prior to overhauling the differential,
check the serviceability of the C.V joints on
the drive shafts.
NO DRIVE IN ANY GEAR
(1) Sheared ring gear to differential case bolts:
Overhaul the differential assembly.
(2) Broken drive shaft: Check and renew com-
ponents as necessary.
(3) Inner C.V. joint shaft out of mesh with
differential side gear: Weak or broken inner C.V. joint
shaft snap ring. Renew as necessary.
NOISE OR VIBRATION IN DRIVE SHAFTS
( 1 ) Bent or twisted drive shafts: Check and
renew the drive shafts as necessary.
Check the drive shaft rubber boots for deterioration.
(2) Worn or damaged inner or outer C.V. joint:
Check and renew components as necessary. (3) Lack of lubricant due to damaged C.V. joint
boots: Check the C.V. joints for wear, repack the C. V.
joints and renew th e C.V. joint boot.
(4) Loose drive shaft hub nut: Tighten the hub
nut to Specifications. (5) Worn splines on the drive shaft or C.V. joint
inner race. Check and renew the faulty components or
drive shaft as an assembly.
NOTE: Noise or vibration in the front end
can also be caused by excessive tire or wheel
unbalance.
2. DESCRIPTION
The five speed transaxle installed in the Pulsar
range of vehicles covered by this manual has synchro-
mesh on all the forward gears.
The reverse gear is a spur idler gear which is
selected by sliding the idler gear into mesh with the
input shaft and the mainshaft.
The transaxle and differential assemblies are ac-
commodated in the same housing and the one oil level
check covers both assemblies.
Gear selection is by mean s of selector forks and a
striking rod which is operated by a floor mounted gear
lever assembly. A mechanism inside the transaxle
prevents the selection of re verse gear from fifth gear
until the gear lever is moved sideways in neutral. The
differential and final dr ive assembly runs on two
tapered roller bearings. Pr eload on these bearings is
adjusted by shims installed behind the bearing cups.
The assembly is driven by the mainshaft pinion
engaging the ring gear on the differential case.
The drive shafts are engaged with the differential
side gears at the inner end and the front wheel hubs at
the outer end.
The drive shafts and each C.V. joint can be
Page 129 of 238
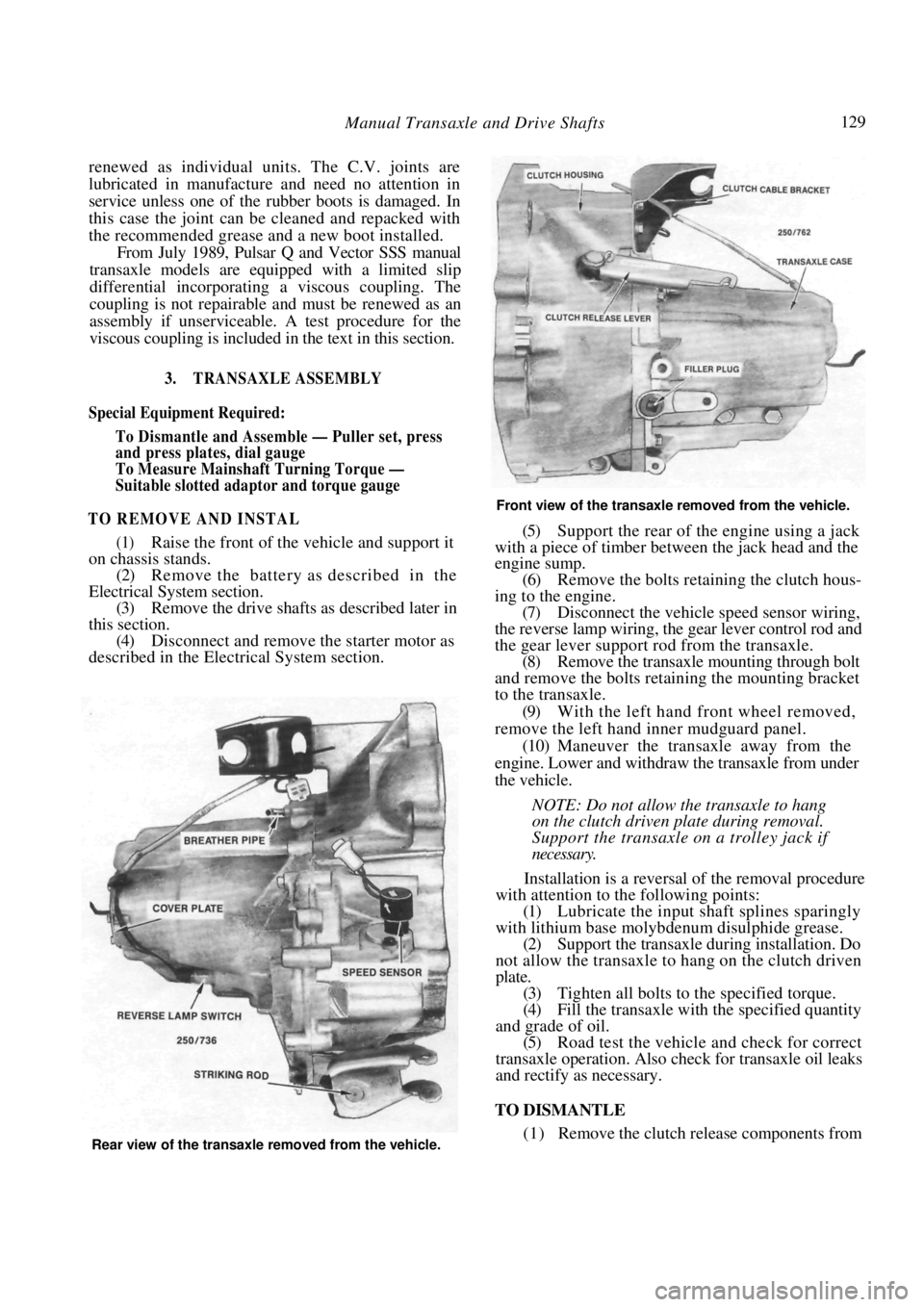
Manual Transaxle and Drive Shafts 129
renewed as individual units. The C.V. joints are
lubricated in manufacture and need no attention in
service unless one of the r ubber boots is damaged. In
this case the joint can be cl eaned and repacked with
the recommended grease and a new boot installed.
From July 1989, Pulsar Q and Vector SSS manual
transaxle models are equipped with a limited slip
differential incorporating a viscous coupling. The
coupling is not repairable and must be renewed as an
assembly if unserviceable. A test procedure for the
viscous coupling is included in the text in this section.
3. TRANSAXLE ASSEMBLY
Special Equipment Required:
To Dismantle and Assemble — Puller set, press
and press plates, dial gauge
To Measure Mainshaft Turning Torque —
Suitable slotted adaptor and torque gauge
TO REMOVE AND INSTAL
(1) Raise the front of the vehicle and support it
on chassis stands.
(2) Remove the battery as described in the
Electrical System section. (3) Remove the drive shafts as described later in
this section. (4) Disconnect and remove the starter motor as
described in the Elect rical System section.
Front view of the transaxle removed from the vehicle.
(5) Support the rear of the engine using a jack
with a piece of timber between the jack head and the
engine sump.
(6) Remove the bolts retaining the clutch hous-
ing to the engine. (7) Disconnect the vehicle speed sensor wiring,
the reverse lamp wiring, the gear lever control rod and
the gear lever support rod from the transaxle. (8) Remove the transaxle mounting through bolt
and remove the bolts retaining the mounting bracket
to the transaxle.
(9) With the left hand front wheel removed,
remove the left hand inner mudguard panel. (10) Maneuver the transaxle away from the
engine. Lower and withdraw the transaxle from under
the vehicle.
NOTE: Do not allow the transaxle to hang
on the clutch driven plate during removal.
Support the transaxle on a trolley jack if
necessary.
Installation is a reversal of the removal procedure
with attention to the following points:
(1) Lubricate the input shaft splines sparingly
with lithium base molybdenum disulphide grease. (2) Support the transaxle during installation. Do
not allow the transaxle to hang on the clutch driven
plate. (3) Tighten all bolts to the specified torque.
(4) Fill the transaxle with the specified quantity
and grade of oil. (5) Road test the vehicle and check for correct
transaxle operation. Also ch eck for transaxle oil leaks
and rectify as necessary.
TO DISMANTLE
(1) Remove the clutch release components from Rear view of the transaxle removed from the vehicle.
Page 130 of 238
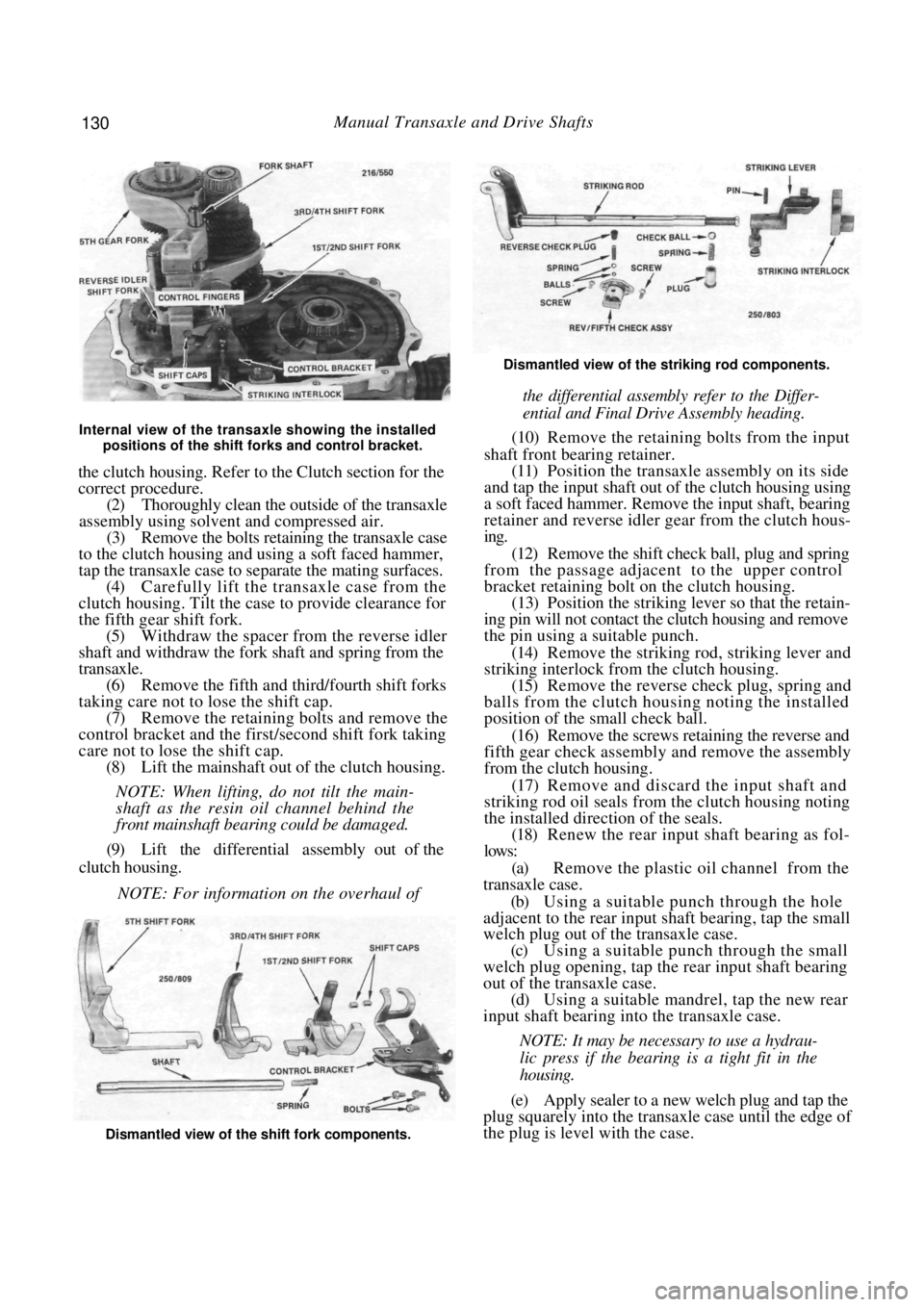
130 Manual Transaxle and Drive Shafts
Internal view of the transaxle showing the installed positions of the shift forks and control bracket.
the clutch housing. Refer to the Clutch section for the
correct procedure.
(2) Thoroughly clean the outsi de of the transaxle
assembly using solvent and compressed air. (3) Remove the bolts retaining the transaxle case
to the clutch housing and using a soft faced hammer,
tap the transaxle case to separate the mating surfaces.
(4) Carefully lift the transaxle case from the
clutch housing. Tilt the cas e to provide clearance for
the fifth gear shift fork. (5) Withdraw the spacer from the reverse idler
shaft and withdraw the fork shaft and spring from the
transaxle. (6) Remove the fifth and third/fourth shift forks
taking care not to lose the shift cap. (7) Remove the retaining bolts and remove the
control bracket and the first/second shift fork taking
care not to lose the shift cap. (8) Lift the mainshaft out of the clutch housing.
NOTE: When lifting, do not tilt the main-
shaft as the resin oil channel behind the
front mainshaft bearing could be damaged.
(9) Lift the differential assembly out of the
clutch housing.
NOTE: For information on the overhaul of
Dismantled view of the striking rod components.
the differential assembly refer to the Differ-
ential and Final Drive Assembly heading.
(10) Remove the retaining bolts from the input
shaft front bearing retainer. (11) Position the transaxle assembly on its side
and tap the input shaft out of the clutch housing using
a soft faced hammer. Remove the input shaft, bearing
retainer and reverse idler gear from the clutch hous-
ing.
(12) Remove the shift check ball, plug and spring
from the passage adjacent to the upper control
bracket retaining bolt on the clutch housing.
(13) Position the striking lever so that the retain-
ing pin will not contact the clutch housing and remove
the pin using a suitable punch.
(14) Remove the striking rod, striking lever and
striking interlock from the clutch housing.
(15) Remove the reverse check plug, spring and
balls from the clutch housing noting the installed
position of the small check ball.
(16) Remove the screws retaining the reverse and
fifth gear check assembly and remove the assembly
from the clutch housing.
(17) Remove and discard the input shaft and
striking rod oil seals from the clutch housing noting
the installed direction of the seals.
(18) Renew the rear input shaft bearing as fol-
lows:
(a) Remove the plastic oil channel from the
transaxle case.
(b) Using a suitable punch through the hole
adjacent to the r ear input shaft bearing, tap the small
welch plug out of the transaxle case.
(c) Using a suitable punch through the small
welch plug opening, tap the rear input shaft bearing
out of the transaxle case. (d) Using a suitable mandrel, tap the new rear
input shaft bearing into the transaxle case.
NOTE: It may be necessary to use a hydrau-
lic press if the bearing is a tight fit in the
housing.
(e) Apply sealer to a new welch plug and tap the
plug squarely into the transaxle case until the edge of
the plug is level with the case.
Dismantled view of the shift fork components.