NISSAN PULSAR 1987 Workshop Manual
Manufacturer: NISSAN, Model Year: 1987, Model line: PULSAR, Model: NISSAN PULSAR 1987Pages: 238, PDF Size: 28.91 MB
Page 141 of 238
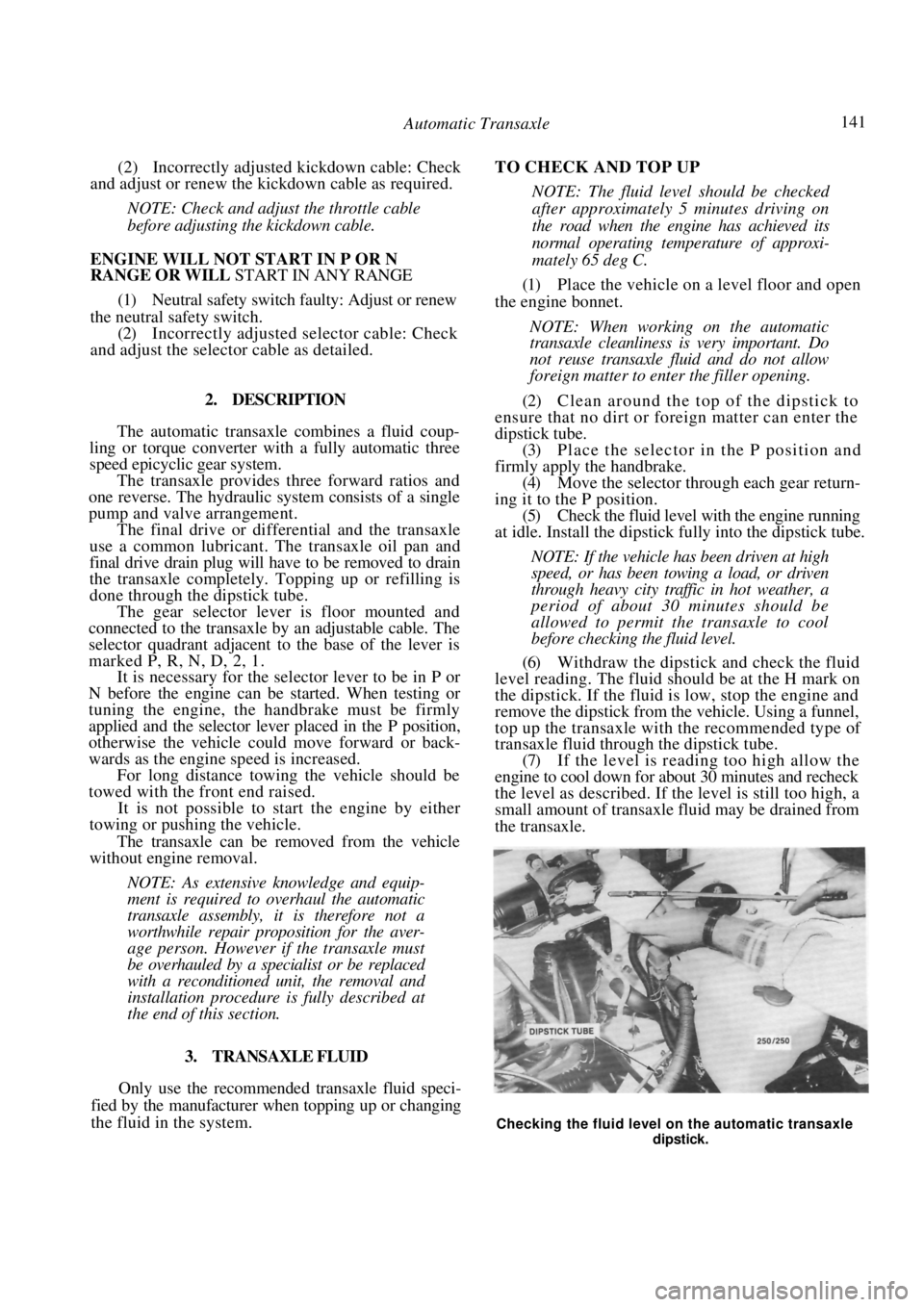
Automatic Transaxle 141
(2) Incorrectly adjusted kickdown cable: Check
and adjust or renew the kickdown cable as required.
NOTE: Check and adjust the throttle cable
before adjusting the kickdown cable.
ENGINE WILL NOT START IN P OR N
RANGE OR WILL START IN ANY RANGE
(1) Neutral safety switch faulty: Adjust or renew
the neutral safety switch. (2) Incorrectly adjusted selector cable: Check
and adjust the selector cable as detailed.
2. DESCRIPTION
The automatic transaxle combines a fluid coup-
ling or torque converter with a fully automatic three
speed epicyclic gear system.
The transaxle provides th ree forward ratios and
one reverse. The hydraulic system consists of a single
pump and valv e arrangement.
The final drive or differential and the transaxle
use a common lubricant. The transaxle oil pan and
final drive drain plug will have to be removed to drain
the transaxle completely. Topping up or refilling is
done through the dipstick tube.
The gear selector lever is floor mounted and
connected to the transaxle by an adjustable cable. The
selector quadrant adjacent to the base of the lever is
marked P, R, N, D, 2, 1.
It is necessary for the selector lever to be in P or
N before the engine can be started. When testing or
tuning the engine, the handbrake must be firmly
applied and the selector lever placed in the P position,
otherwise the vehicle could move forward or back-
wards as the engine speed is increased.
For long distance towing the vehicle should be
towed with the front end raised.
It is not possible to start the engine by either
towing or pushing the vehicle.
The transaxle can be removed from the vehicle
without engine removal.
NOTE: As extensive knowledge and equip-
ment is required to overhaul the automatic
transaxle assembly, it is therefore not a
worthwhile repair proposition for the aver-
age person. However if the transaxle must
be overhauled by a specialist or be replaced
with a reconditioned unit, the removal and
installation procedure is fully described at
the end of this section.
3. TRANSAXLE FLUID
Only use the recommended transaxle fluid speci-
fied by the manufacturer when topping up or changing
the fluid in the system.
TO CHECK AND TOP UP
NOTE: The fluid level should be checked
after approximately 5 minutes driving on
the road when the engine has achieved its
normal operating temperature of approxi-
mately 65 deg C.
(1) Place the vehicle on a level floor and open
the engine bonnet.
NOTE: When working on the automatic
transaxle cleanliness is very important. Do
not reuse transaxle fluid and do not allow
foreign matter to enter the filler opening.
(2) Clean around the top of the dipstick to
ensure that no dirt or foreign matter can enter the
dipstick tube.
(3) Place the selector in the P position and
firmly apply the handbrake. (4) Move the selector thro ugh each gear return-
ing it to the P position.
(5) Check the fluid level with the engine running
at idle. Install the dipstick fully into the dipstick tube.
NOTE: If the vehicle has been driven at high
speed, or has been towing a load, or driven
through heavy city traffic in hot weather, a
period of about 30 minutes should be
allowed to permit the transaxle to cool
before checking the fluid level.
(6) Withdraw the dipstick and check the fluid
level reading. The fluid should be at the H mark on
the dipstick. If the fluid is low, stop the engine and
remove the dipstick from the vehicle. Using a funnel,
top up the transaxle with the recommended type of
transaxle fluid through the dipstick tube. (7) If the level is reading too high allow the
engine to cool down for about 30 minutes and recheck
the level as described. If the level is still too high, a
small amount of transaxle fluid may be drained from
the transaxle.
Checking the fluid level on the automatic transaxle
dipstick.
Page 142 of 238
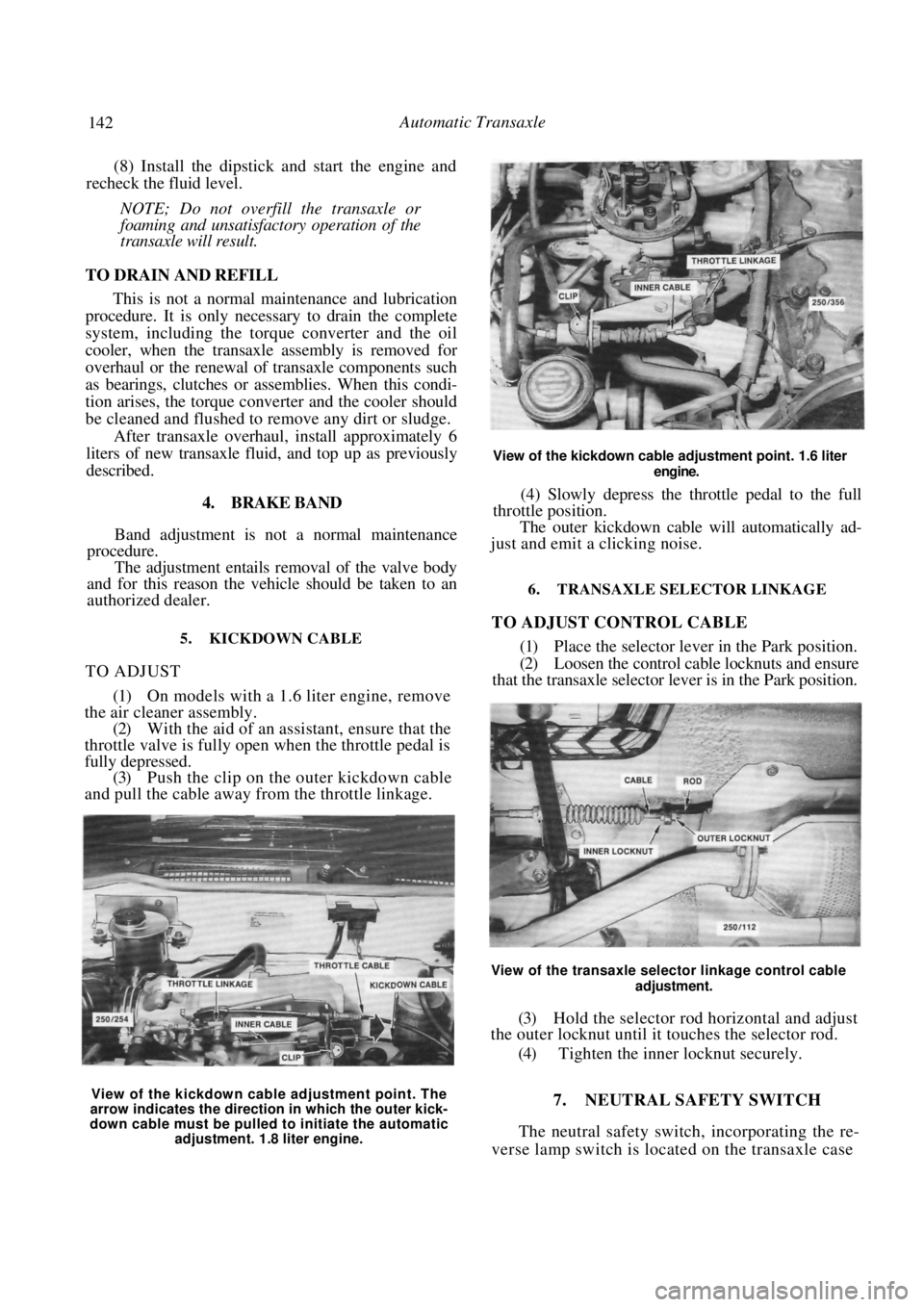
142 Automatic Transaxle
(8) Install the dipstick and start the engine and
recheck the fluid level.
NOTE; Do not overfill the transaxle or
foaming and unsatisfactory operation of the
transaxle will result.
TO DRAIN AND REFILL
This is not a normal maintenance and lubrication
procedure. It is only necessary to drain the complete
system, including the torq ue converter and the oil
cooler, when the transaxle assembly is removed for
overhaul or the renewal of transaxle components such
as bearings, clutches or as semblies. When this condi-
tion arises, the torque converter and the cooler should
be cleaned and flushed to remove any dirt or sludge.
After transaxle overhaul, install approximately 6
liters of new transaxle fluid, and top up as previously
described.
4. BRAKE BAND
Band adjustment is not a normal maintenance
procedure.
The adjustment entails removal of the valve body
and for this reason the vehicle should be taken to an
authorized dealer.
5. KICKDOWN CABLE
TO ADJUST
(1) On models with a 1.6 liter engine, remove
the air cleaner assembly. (2) With the aid of an assistant, ensure that the
throttle valve is fully open when the throttle pedal is
fully depressed. (3) Push the clip on the outer kickdown cable
and pull the cable away from the throttle linkage.
View of the kickdown cable adjustment point. 1.6 liter
engine.
(4) Slowly depress the throttle pedal to the full
throttle position.
The outer kickdown cable will automatically ad-
just and emit a clicking noise.
6. TRANSAXLE SELECTOR LINKAGE
TO ADJUST CONTROL CABLE
(1) Place the selector lever in the Park position.
(2) Loosen the control cable locknuts and ensure
that the transaxle selector lever is in the Park position.
View of the transaxle selector linkage control cable
adjustment.
(3) Hold the selector rod horizontal and adjust
the outer locknut until it touches the selector rod.
(4) Tighten the inner locknut securely.
7. NEUTRAL SAFETY SWITCH
The neutral safety switch, incorporating the re-
verse lamp switch is located on the transaxle case
View of the kickdown cable adjustment point. The
arrow indicates the direction in which the outer kick-
down cable must be pulled to initiate the automatic adjustment. 1.8 liter engine.
Page 143 of 238
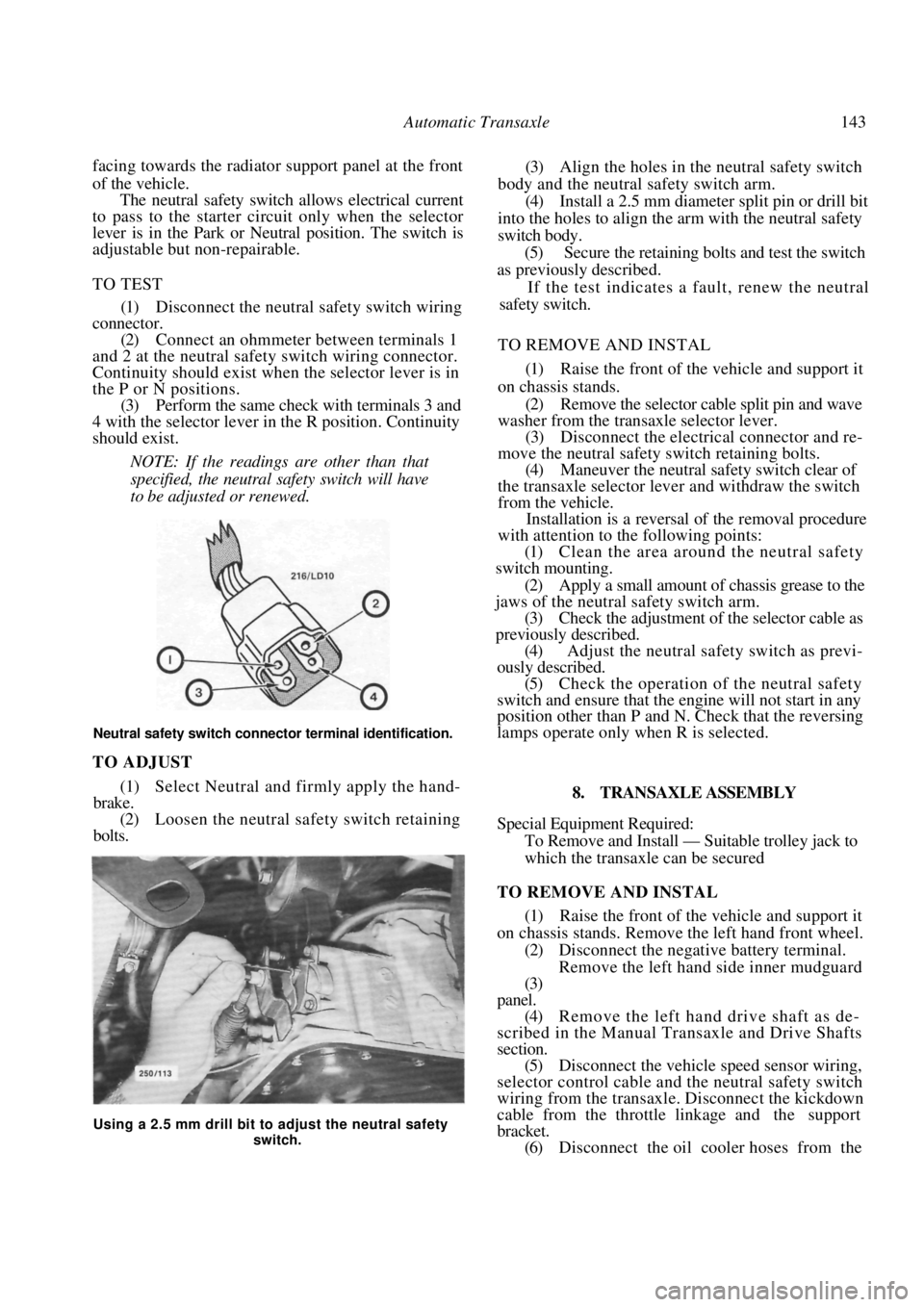
Automatic Transaxle 143
facing towards the radiator support panel at the front
of the vehicle.
The neutral safety switch allows electrical current
to pass to the starter circ uit only when the selector
lever is in the Park or Neutral position. The switch is
adjustable but non-repairable.
TO TEST
(1) Disconnect the neutral safety switch wiring
connector.
(2) Connect an ohmmeter between terminals 1
and 2 at the neutral safety switch wiring connector.
Continuity should exist when the selector lever is in
the P or N positions. (3) Perform the same check with terminals 3 and
4 with the selector lever in the R position. Continuity
should exist.
NOTE: If the readings are other than that
specified, the neutral safety switch will have
to be adjusted or renewed.
Neutral safety switch connector terminal identification.
TO ADJUST
(1) Select Neutral and firmly apply the hand-
brake. (2) Loosen the neutral safety switch retaining
bolts.
(3) Align the holes in the neutral safety switch
body and the neutral safety switch arm. (4) Install a 2.5 mm diameter split pin or drill bit
into the holes to align the arm with the neutral safety
switch body. (5) Secure the retaining bolts and test the switch
as previously described.
If the test indicates a fault, renew the neutral
safety switch.
TO REMOVE AND INSTAL
(1) Raise the front of the vehicle and support it
on chassis stands. (2) Remove the selector cable split pin and wave
washer from the transaxle selector lever.
(3) Disconnect the electric al connector and re-
move the neutral safety switch retaining bolts. (4) Maneuver the neutral safety switch clear of
the transaxle selector lever and withdraw the switch
from the vehicle. Installation is a reversal of the removal procedure
with attention to the following points:
(1) Clean the area around the neutral safety
switch mounting.
(2) Apply a small amount of chassis grease to the
jaws of the neutral safety switch arm. (3) Check the adjustment of the selector cable as
previously described. (4) Adjust the neutral safety switch as previ-
ously described.
(5) Check the operation of the neutral safety
switch and ensure that the engine will not start in any
position other than P and N. Check that the reversing
lamps operate only when R is selected.
8. TRANSAXLE ASSEMBLY
Special Equipment Required:
To Remove and Install — Suitable trolley jack to
which the transaxle can be secured
TO REMOVE AND INSTAL
(1) Raise the front of the vehicle and support it
on chassis stands. Remove the left hand front wheel.
(2) Disconnect the negative battery terminal. Remove the left hand side inner mudguard
(3)
panel.
(4) Remove the left hand drive shaft as de-
scribed in the Manual Tran saxle and Drive Shafts
section. (5) Disconnect the vehicle speed sensor wiring,
selector control cable and the neutral safety switch
wiring from the transaxle. Disconnect the kickdown
cable from the throttle linkage and the support
bracket. (6) Disconnect the oil cooler hoses from the
Using a 2.5 mm drill bit to adjust the neutral safety
switch.
Page 144 of 238
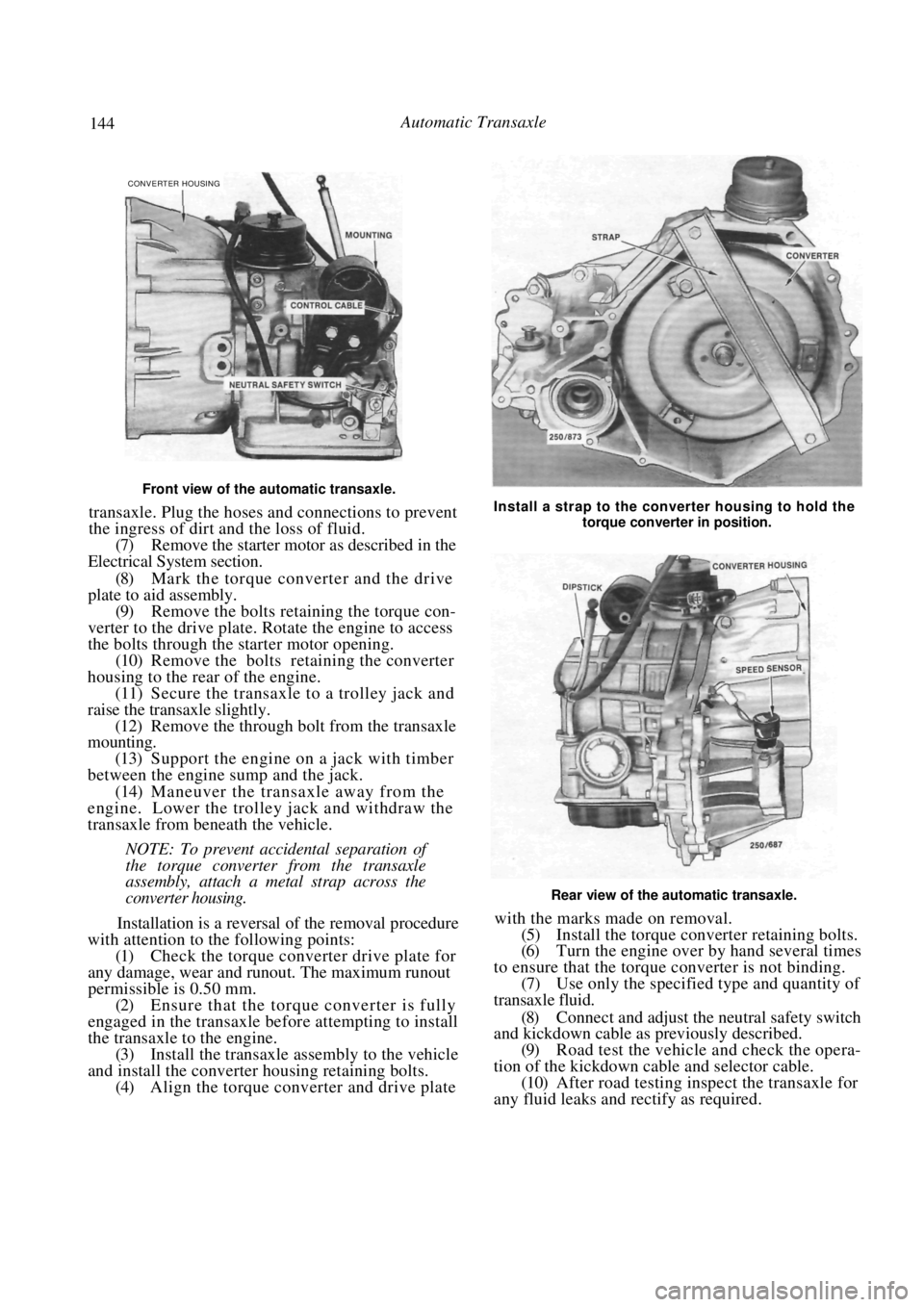
144 Automatic Transaxle
Front view of the automatic transaxle.
transaxle. Plug the hoses and connections to prevent
the ingress of dirt and the loss of fluid.
(7) Remove the starter motor as described in the
Electrical System section.
(8) Mark the torque converter and the drive
plate to aid assembly.
(9) Remove the bolts retaining the torque con-
verter to the drive plate. Rotate the engine to access
the bolts through the starter motor opening. (10) Remove the bolts retaining the converter
housing to the rear of the engine. (11) Secure the transaxle to a trolley jack and
raise the transaxle slightly. (12) Remove the through bolt from the transaxle
mounting.
(13) Support the engine on a jack with timber
between the engine sump and the jack. (14) Maneuver the transaxle away from the
engine. Lower the trolley jack and withdraw the
transaxle from beneath the vehicle.
NOTE: To prevent accidental separation of
the torque converter from the transaxle
assembly, attach a metal strap across the
converter housing.
Installation is a reversal of the removal procedure
with attention to the following points:
(1) Check the torque converter drive plate for
any damage, wear and runout. The maximum runout
permissible is 0.50 mm.
(2) Ensure that the torque converter is fully
engaged in the transaxle be fore attempting to install
the transaxle to the engine. (3) Install the transaxle assembly to the vehicle
and install the converter housing retaining bolts. (4) Align the torque converter and drive plate
Install a strap to the converter housing to hold the
torque converter in position.
Rear view of the automatic transaxle.
with the marks made on removal.
(5) Install the torque converter retaining bolts.
(6) Turn the engine over by hand several times
to ensure that the torque converter is not binding. (7) Use only the specified type and quantity of
transaxle fluid.
(8) Connect and adjust the neutral safety switch
and kickdown cable as previously described.
(9) Road test the vehicle and check the opera-
tion of the kickdown cable and selector cable. (10) After road testing inspect the transaxle for
any fluid leaks and rectify as required.
CONVERTER HOUSING
Page 145 of 238
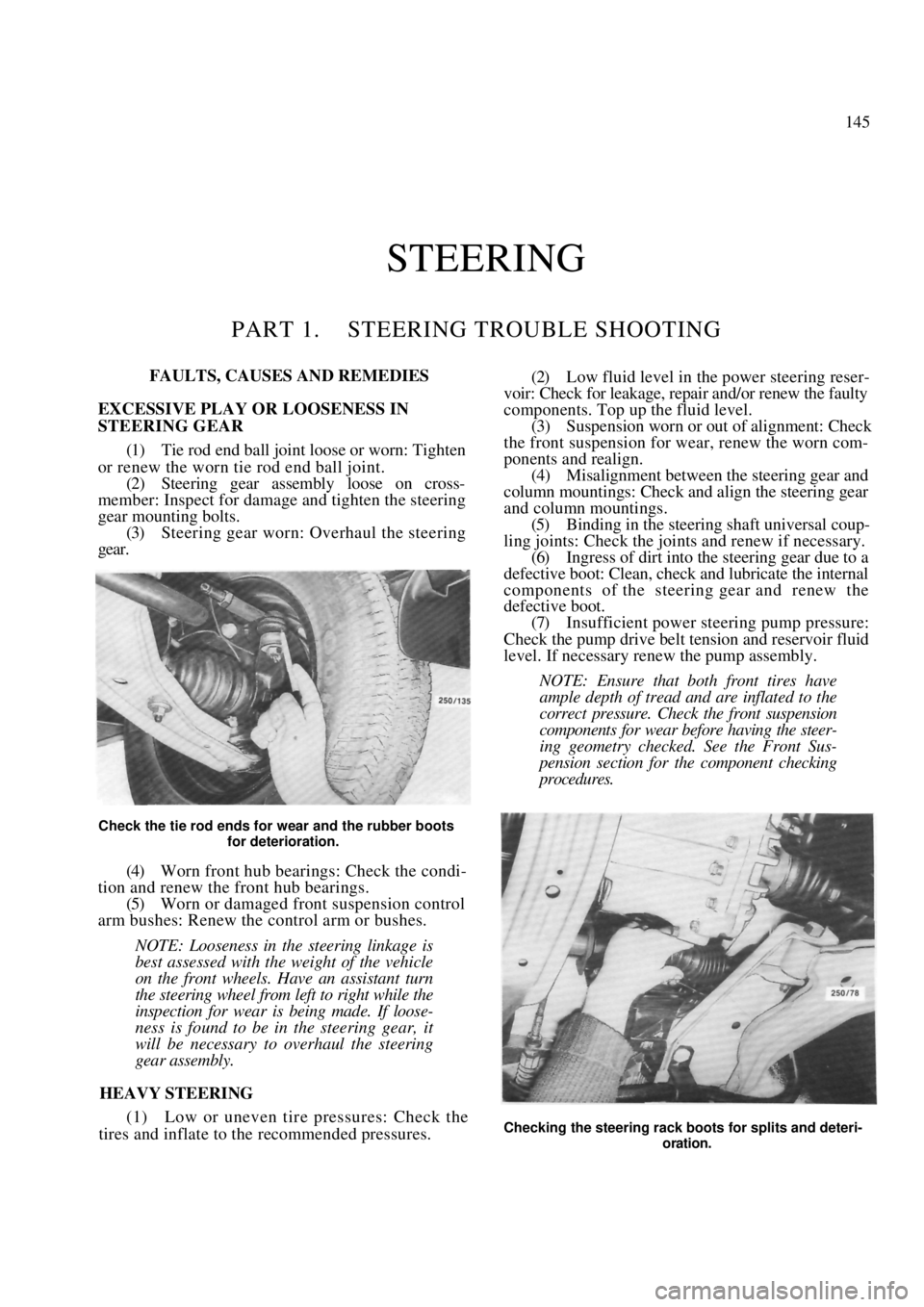
145
STEERING
PART 1. STEERING TROUBLE SHOOTING
FAULTS, CAUSES AND REMEDIES
EXCESSIVE PLAY OR LOOSENESS IN
STEERING GEAR
(1) Tie rod end ball joint loose or worn: Tighten
or renew the worn tie rod end ball joint. (2) Steering gear assembly loose on cross-
member: Inspect for damage and tighten the steering
gear mounting bolts. (3) Steering gear worn: Overhaul the steering
gear.
(2) Low fluid level in the power steering reser-
voir: Check for leakage, repa ir and/or renew the faulty
components. Top up the fluid level.
(3) Suspension worn or out of alignment: Check
the front suspension for wear, renew the worn com-
ponents and realign. (4) Misalignment between the steering gear and
column mountings: Check and align the steering gear
and column mountings. (5) Binding in the steering shaft universal coup-
ling joints: Check the join ts and renew if necessary.
(6) Ingress of dirt into the steering gear due to a
defective boot: Clean, check and lubricate the internal
components of the steering gear and renew the
defective boot. (7) Insufficient power steering pump pressure:
Check the pump drive belt tension and reservoir fluid
level. If necessary renew the pump assembly.
NOTE: Ensure that both front tires have
ample depth of tread and are inflated to the
correct pressure. Check the front suspension
components for wear before having the steer-
ing geometry checked. See the Front Sus-
pension section for the component checking
procedures.
Check the tie rod ends for wear and the rubber boots for deterioration.
(4) Worn front hub bearings: Check the condi-
tion and renew the front hub bearings. (5) Worn or damaged front suspension control
arm bushes: Renew the control arm or bushes.
NOTE: Looseness in th e steering linkage is
best assessed with the weight of the vehicle
on the front wheels. Have an assistant turn
the steering wheel from left to right while the
inspection for wear is being made. If loose-
ness is found to be in the steering gear, it
will be necessary to overhaul the steering
gear assembly.
HEAVY STEERING
(1) Low or uneven tir e pressures: Check the
tires and inflate to the recommended pressures.
Checking the steering rack boot s for splits and deteri-
oration.
Page 146 of 238
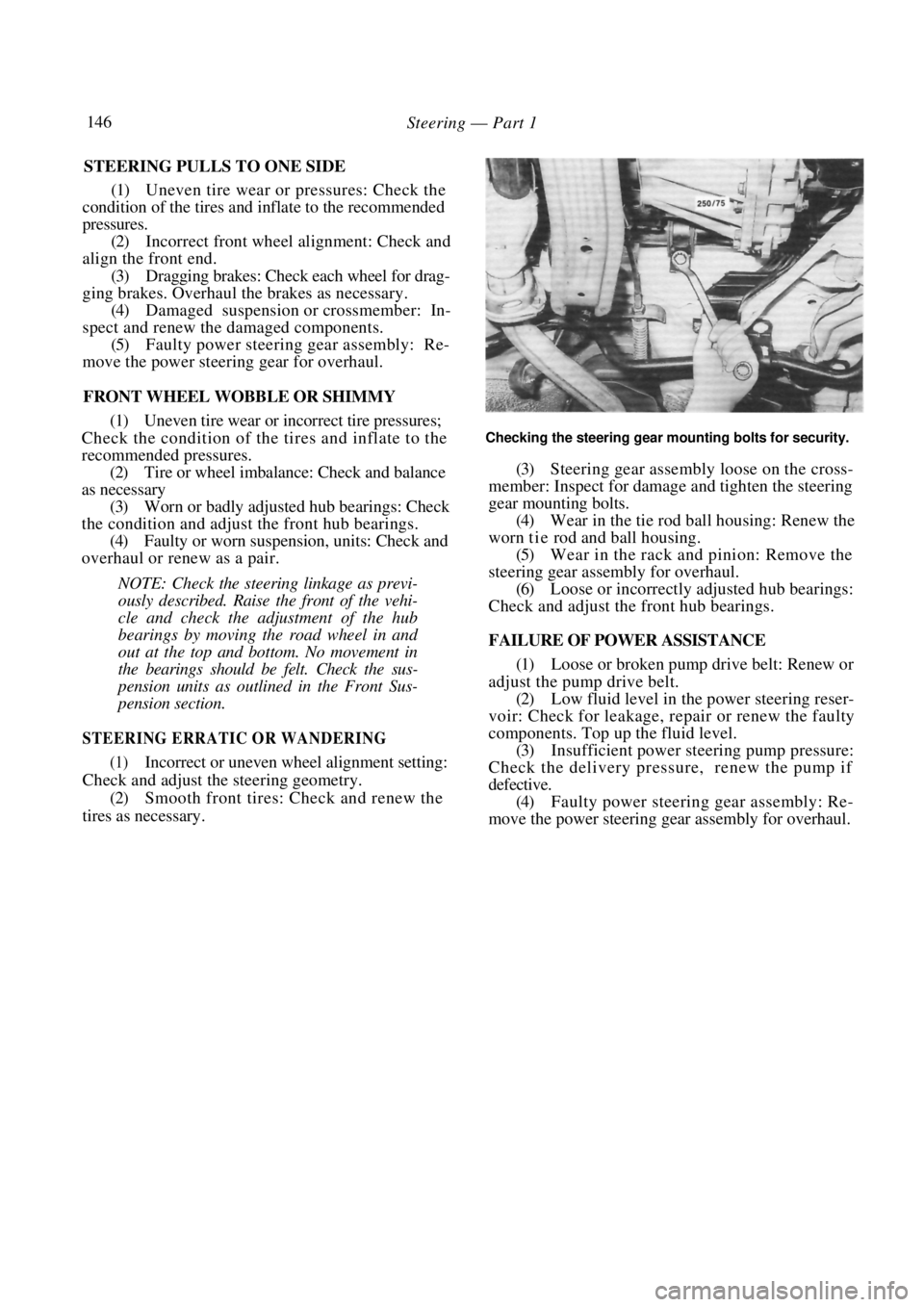
146 Steering — Part 1
STEERING PULLS TO ONE SIDE
(1) Uneven tire wear or pressures: Check the
condition of the tires and inflate to the recommended
pressures.
(2) Incorrect front wheel alignment: Check and
align the front end.
(3) Dragging brakes: Check each wheel for drag-
ging brakes. Overhaul the brakes as necessary. (4) Damaged suspension or crossmember: In-
spect and renew the damaged components. (5) Faulty power steering gear assembly: Re-
move the power steering gear for overhaul.
FRONT WHEEL WOBBLE OR SHIMMY
(1) Uneven tire wear or incorrect tire pressures;
Check the condition of the tires and inflate to the
recommended pressures. (2) Tire or wheel imbalance: Check and balance
as necessary (3) Worn or badly adjusted hub bearings: Check
the condition and adjust the front hub bearings.
(4) Faulty or worn suspension, units: Check and
overhaul or renew as a pair.
NOTE: Check the steering linkage as previ-
ously described. Raise the front of the vehi-
cle and check the adjustment of the hub
bearings by moving the road wheel in and
out at the top and bottom. No movement in
the bearings should be felt. Check the sus-
pension units as outlined in the Front Sus-
pension section.
STEERING ERRATIC OR WANDERING
(1) Incorrect or uneven wheel alignment setting:
Check and adjust th e steering geometry.
(2) Smooth front tires: Check and renew the
tires as necessary.
Checking the steering gear mounting bolts for security.
(3) Steering gear assembly loose on the cross-
member: Inspect for damage and tighten the steering
gear mounting bolts.
(4) Wear in the tie rod ball housing: Renew the
worn t i e rod and ball housing. (5) Wear in the rack and pinion: Remove the
steering gear assembly for overhaul. (6) Loose or incorrectly adjusted hub bearings:
Check and adjust the front hub bearings.
FAILURE OF POWER ASSISTANCE
(1) Loose or broken pump drive belt: Renew or
adjust the pump drive belt.
(2) Low fluid level in the power steering reser-
voir: Check for leakage, repair or renew the faulty
components. Top up the fluid level. (3) Insufficient power steering pump pressure:
Check the delivery pressure, renew the pump if
defective. (4) Faulty power steering gear assembly: Re-
move the power steering gear assembly for overhaul.
Page 147 of 238
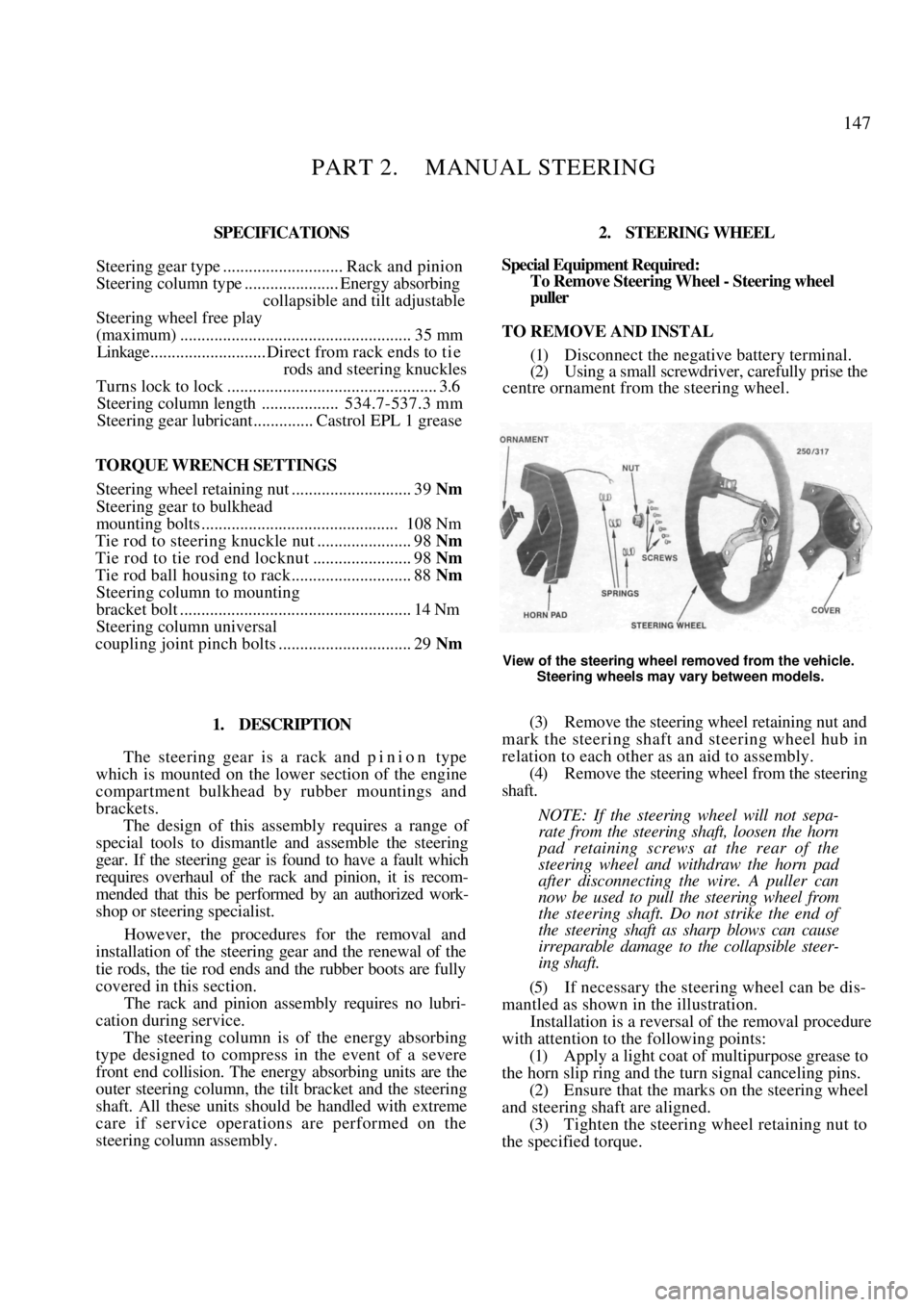
147
PART 2. MANUAL STEERING
SPECIFICATIONS
Steering gear type ............................ Rack and pinion
Steering column type ...................... Energy absorbing
collapsible and tilt adjustable
Steering wheel free play
(maximum ) ...................................................... 35 mm
Linkage........................... Direct from rack ends to t i e
rods and steering knuckles
Turns lock to lock ................................................. 3.6
Steering column length .................. 534.7-537.3 mm
Steering gear lubricant.............. Castrol EPL 1 grease
TORQUE WRENCH SETTINGS
Steering wheel retaining nut ............................ 39 Nm
Steering gear to bulkhead
mounting bolts .............................................. 108 Nm
Tie rod to steering knuckle nut...................... 98 Nm
Tie rod to tie rod end locknut ....................... 98 Nm
Tie rod ball housing to rack............................ 88 Nm
Steering column to mounting
bracket bolt ...................................................... 14 Nm
Steering column universal
coupling joint pinch bolts ............................... 29 Nm
2. STEERING WHEEL
Special Equipment Required:
To Remove Steering Wheel - Steering wheel
puller
TO REMOVE AND INSTAL
(1) Disconnect the negative battery terminal.
(2) Using a small screwdriver, carefully prise the
centre ornament from the steering wheel.
View of the steering wheel removed from the vehicle.
Steering wheels may vary between models.
1. DESCRIPTION
The steering gear is a rack and p i n i o n type
which is mounted on the lower section of the engine
compartment bulkhead by rubber mountings and
brackets.
The design of this assembly requires a range of
special tools to dismantle and assemble the steering
gear. If the steering gear is found to have a fault which
requires overhaul of the rack and pinion, it is recom-
mended that this be performed by an authorized work-
shop or steering specialist.
However, the procedures for the removal and
installation of the steering gear and the renewal of the
tie rods, the tie rod ends and the rubber boots are fully
covered in this section.
The rack and pinion assembly requires no lubri-
cation during service.
The steering column is of the energy absorbing
type designed to compress in the event of a severe
front end collision. The energy absorbing units are the
outer steering column, the tilt bracket and the steering
shaft. All these units shoul d be handled with extreme
care if service operations are performed on the
steering column assembly.
(3) Remove the steering wh eel retaining nut and
mark the steering shaft and steering wheel hub in
relation to each other as an aid to assembly.
(4) Remove the steering wheel from the steering
shaft.
NOTE: If the steering wheel will not sepa-
rate from the steering shaft, loosen the horn
pad retaining screws at the rear of the
steering wheel and withdraw the horn pad
after disconnecting the wire. A puller can
now be used to pull the steering wheel from
the steering shaft. Do not strike the end of
the steering shaft as sharp blows can cause
irreparable damage to the collapsible steer-
ing shaft.
(5) If necessary the steering wheel can be dis-
mantled as shown in the illustration.
Installation is a reversal of the removal procedure
with attention to the following points:
(1) Apply a light coat of multipurpose grease to
the horn slip ring and the turn signal canceling pins.
(2) Ensure that the marks on the steering wheel
and steering shaf t are aligned.
(3) Tighten the steering wheel retaining nut to
the specified torque.
Page 148 of 238
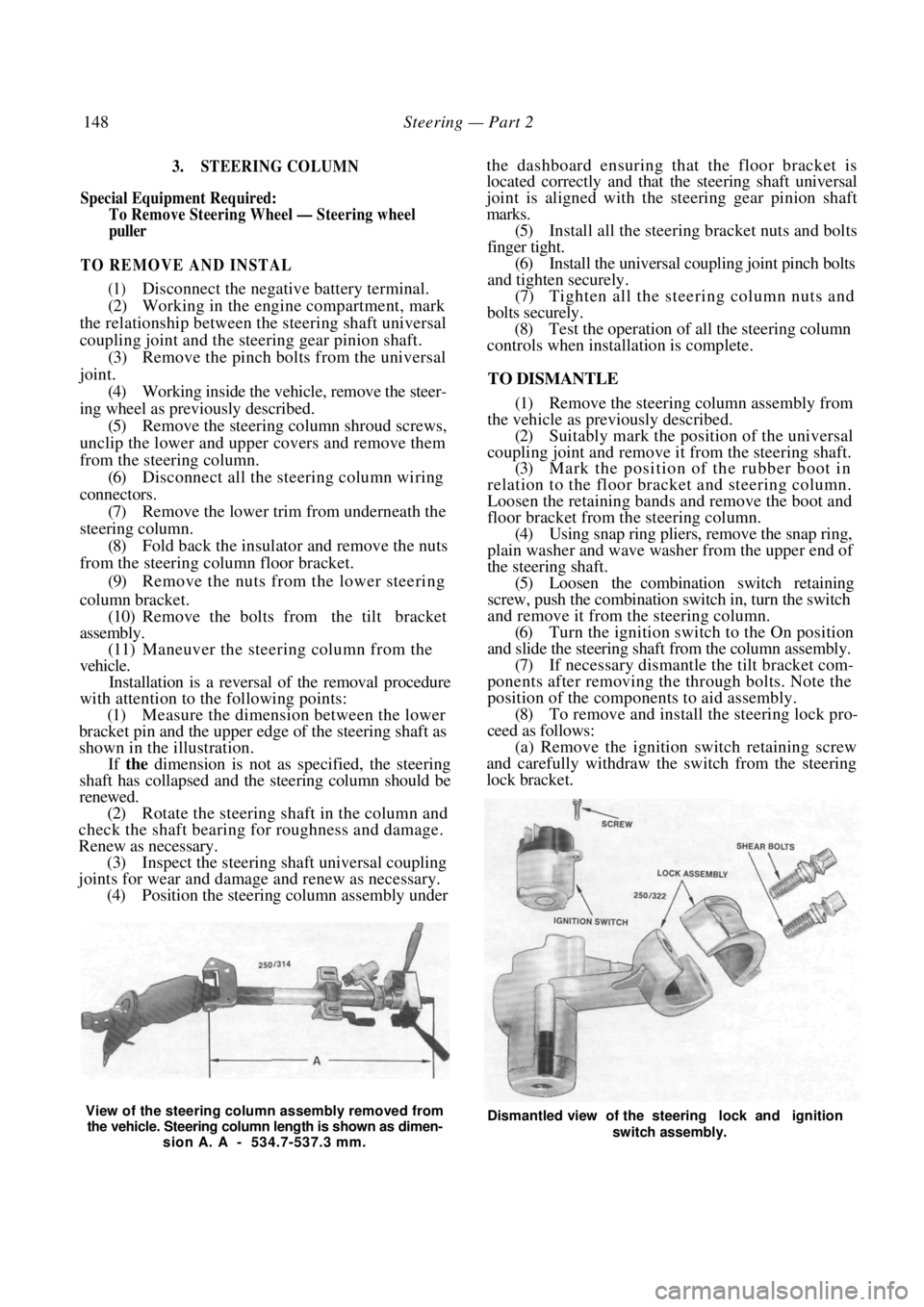
148 Steering — Part 2
3. STEERING COLUMN
Special Equipment Required:
To Remove Steering Wheel — Steering wheel
puller
TO REMOVE AND INSTAL
(1) Disconnect the negative battery terminal.
(2) Working in the engine compartment, mark
the relationship between the steering shaft universal
coupling joint and the steering gear pinion shaft. (3) Remove the pinch bolts from the universal
joint. (4) Working inside the vehi cle, remove the steer-
ing wheel as previously described. (5) Remove the steering column shroud screws,
unclip the lower and upper covers and remove them
from the steering column. (6) Disconnect all the steering column wiring
connectors. (7) Remove the lower trim from underneath the
steering column.
(8) Fold back the insulator and remove the nuts
from the steering colu mn floor bracket.
(9) Remove the nuts from the lower steering
column bracket. (10) Remove the bolts from the tilt bracket
assembly. (11) Maneuver the steering column from the
vehicle.
Installation is a reversal of the removal procedure
with attention to the following points:
(1) Measure the dimension between the lower
bracket pin and the upper edge of the steering shaft as
shown in the illustration.
If the dimension is not as specified, the steering
shaft has collapsed and the steering column should be
renewed.
(2) Rotate the steering shaft in the column and
check the shaft bearing for roughness and damage.
Renew as necessary. (3) Inspect the steering shaft universal coupling
joints for wear and damage and renew as necessary. (4) Position the steering column assembly under
the dashboard ensuring that the floor bracket is
located correctly and that the steering shaft universal
joint is aligned with the steering gear pinion shaft
marks.
(5) Install all the steering bracket nuts and bolts
finger tight. (6) Install the universal coupling joint pinch bolts
and tighten securely.
(7) Tighten all the stee ring column nuts and
bolts securely. (8) Test the operation of all the steering column
controls when installation is complete.
TO DISMANTLE
(1) Remove the steering column assembly from
the vehicle as previously described. (2) Suitably mark the position of the universal
coupling joint and remove it from the steering shaft. (3) Mark the position of the rubber boot in
relation to the floor bracket and steering column.
Loosen the retaining bands and remove the boot and
floor bracket from th e steering column.
(4) Using snap ring pliers, remove the snap ring,
plain washer and wave washer from the upper end of
the steering shaft. (5) Loosen the combination switch retaining
screw, push the combination switch in, turn the switch
and remove it from the steering column. (6) Turn the ignition switch to the On position
and slide the steering shaft from the column assembly. (7) If necessary dismantle the tilt bracket com-
ponents after removing the through bolts. Note the
position of the components to aid assembly. (8) To remove and install the steering lock pro-
ceed as follows: (a) Remove the ignition switch retaining screw
and carefully withdraw the switch from the steering
lock bracket.
View of the steering column assembly removed from
the vehicle. Steering column length is shown as dimen- sion A. A - 534.7-537.3 mm. Dismantled view of the steering lock and ignition
switch assembly.
Page 149 of 238
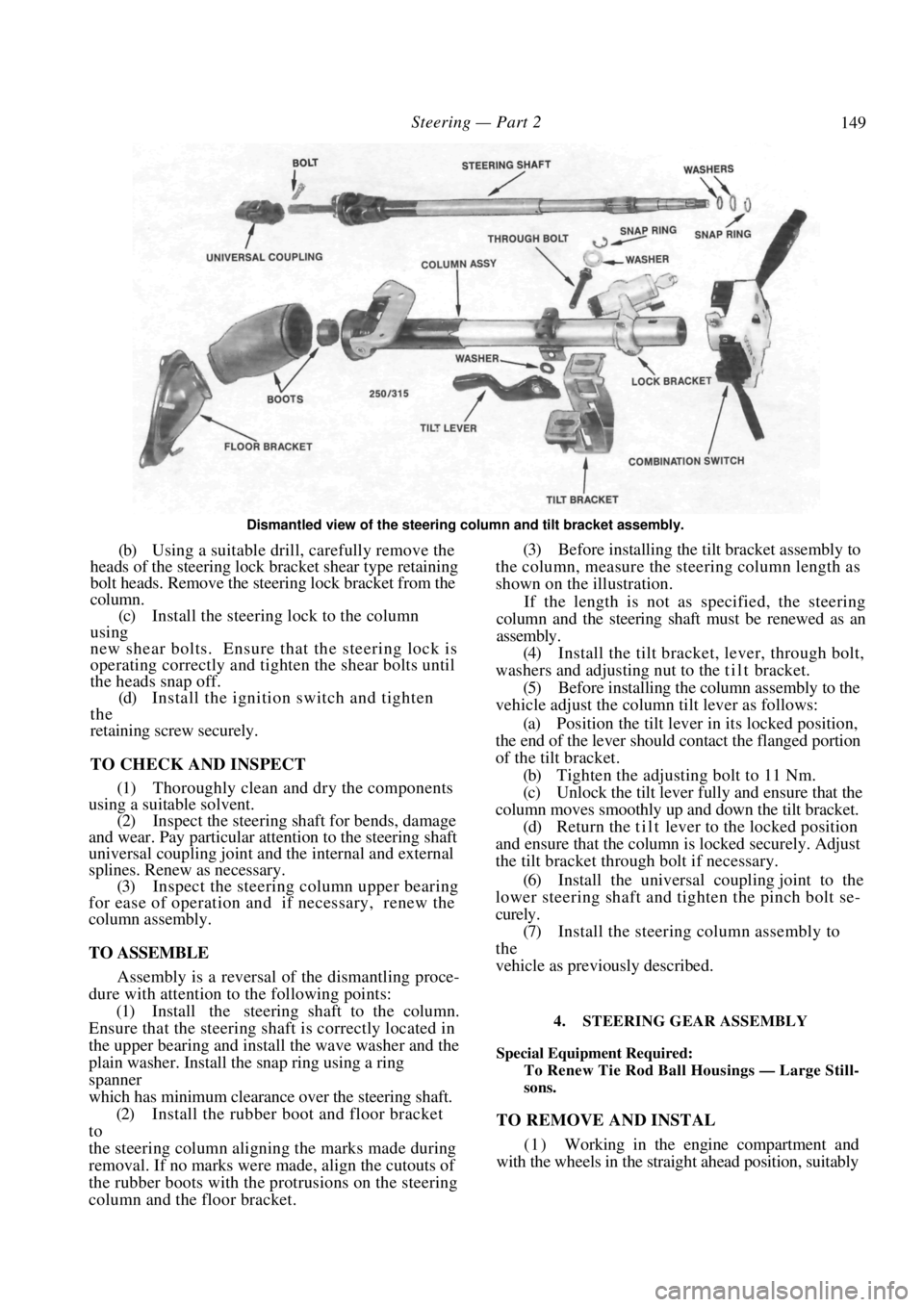
Steering — Part 2 149
Dismantled view of the steering column and tilt bracket assembly.
(b) Using a suitable drill, carefully remove the
heads of the steering lock br acket shear type retaining
bolt heads. Remove the steering lock bracket from the
column.
(c) Install the steering lock to the column
using
new shear bolts. Ensure that the steering lock is
operating correctly and tigh ten the shear bolts until
the heads snap off.
(d) Install the ignition switch and tighten
the
retaining screw securely.
TO CHECK AND INSPECT
(1) Thoroughly clean and dry the components
using a suitable solvent.
(2) Inspect the steering shaft for bends, damage
and wear. Pay particular attention to the steering shaft
universal coupling joint and the internal and external
splines. Renew as necessary. (3) Inspect the steering column upper bearing
for ease of operation and if necessary, renew the
column assembly.
TO ASSEMBLE
Assembly is a reversal of the dismantling proce-
dure with attention to the following points:
(1) Install the steering shaft to the column.
Ensure that the steering shaft is correctly located in
the upper bearing and insta ll the wave washer and the
plain washer. Install the snap ring using a ring
spanner
which has minimum clearan ce over the steering shaft.
(2) Install the rubber boot and floor bracket
to
the steering column aligning the marks made during
removal. If no marks were made, align the cutouts of
the rubber boots with the protrusions on the steering
column and the floor bracket. (3) Before installing the tilt bracket assembly to
the column, measure the steering column length as
shown on the illustration.
If the length is not as specified, the steering
column and the steering shaft must be renewed as an
assembly.
(4) Install the tilt bracket, lever, through bolt,
washers and adjusting nu t to the t i l t bracket.
(5) Before installing the column assembly to the
vehicle adjust the column tilt lever as follows:
(a) Position the tilt lever in its locked position,
the end of the lever should contact the flanged portion
of the tilt bracket.
(b) Tighten the adjusting bolt to 11 Nm.
(c) Unlock the tilt lever fully and ensure that the
column moves smoothly up and down the tilt bracket. (d) Return the tilt lever to the locked position
and ensure that the column is locked securely. Adjust
the tilt bracket thro ugh bolt if necessary.
(6) Install the universal coupling joint to the
lower steering shaft and tighten the pinch bolt se-
curely.
(7) Install the steering column assembly to
the
vehicle as previously described.
4. STEERING GEAR ASSEMBLY
Special Equipment Required:
To Renew Tie Rod Ball Housings — Large Still-
sons.
TO REMOVE AND INSTAL
( 1 ) Working in the engine compartment and
with the wheels in the straight ahead position, suitably
Page 150 of 238
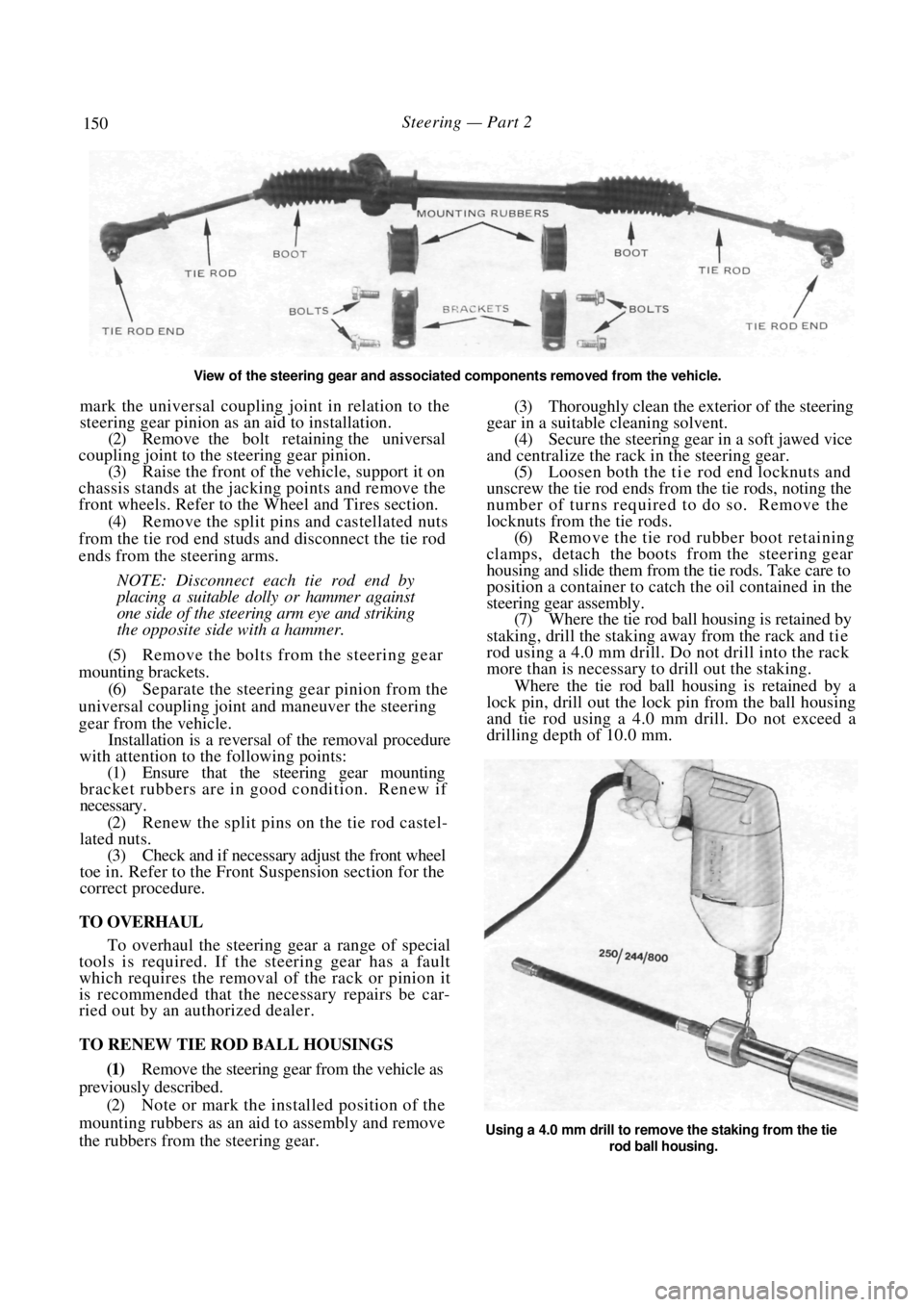
150 Steering — Part 2
View of the steering gear and associated components removed from the vehicle.
mark the universal coupling joint in relation to the
steering gear pinion as an aid to installation.
(2) Remove the bolt retaining the universal
coupling joint to the steering gear pinion. (3) Raise the front of the vehicle, support it on
chassis stands at the jack ing points and remove the
front wheels. Refer to the Wheel and Tires section.
(4) Remove the split pins and castellated nuts
from the tie rod end studs and disconnect the tie rod
ends from the steering arms.
NOTE: Disconnect each tie rod end by
placing a suitable dolly or hammer against
one side of the steer ing arm eye and striking
the opposite side with a hammer.
(5) Remove the bolts from the steering gear
mounting brackets. (6) Separate the steering gear pinion from the
universal coupling joint and maneuver the steering
gear from the vehicle. Installation is a reversal of the removal procedure
with attention to the following points:
(1) Ensure that the steering gear mounting
bracket rubbers are in good condition. Renew if
necessary.
(2) Renew the split pins on the tie rod castel-
lated nuts.
(3) Check and if necessary adjust the front wheel
toe in. Refer to the Front Suspension section for the
correct procedure.
TO OVERHAUL
To overhaul the steering gear a range of special
tools is required. If the steering gear has a fault
which requires the removal of the rack or pinion it
is recommended that the necessary repairs be car-
ried out by an authorized dealer.
TO RENEW TIE ROD BALL HOUSINGS
(1) Remove the steering gear from the vehicle as
previously described.
(2) Note or mark the installed position of the
mounting rubbers as an aid to assembly and remove
the rubbers from the steering gear.
(3) Thoroughly clean the exterior of the steering
gear in a suitable cleaning solvent.
(4) Secure the steering gear in a soft jawed vice
and centralize the rack in the steering gear. (5) Loosen both the ti e rod end locknuts and
unscrew the tie rod ends from the tie rods, noting the
number of turns required to do so. Remove the
locknuts from the tie rods. (6) Remove the tie rod rubber boot retaining
clamps, detach the boot s from the steering gear
housing and slide them from the tie rods. Take care to
position a container to catch the oil contained in the
steering gear assembly. (7) Where the tie rod ball housing is retained by
staking, drill the staking away from the rack and t i e
rod using a 4.0 mm drill. Do not drill into the rack
more than is necessary to drill out the staking.
Where the tie rod ball housing is retained by a
lock pin, drill out the lock pin from the ball housing
and tie rod using a 4.0 mm drill. Do not exceed a
drilling depth of 10.0 mm.
Using a 4.0 mm drill to remove the staking from the tie
rod ball housing.