ECU OPEL FRONTERA 1998 Workshop Manual
[x] Cancel search | Manufacturer: OPEL, Model Year: 1998, Model line: FRONTERA, Model: OPEL FRONTERA 1998Pages: 6000, PDF Size: 97 MB
Page 4308 of 6000
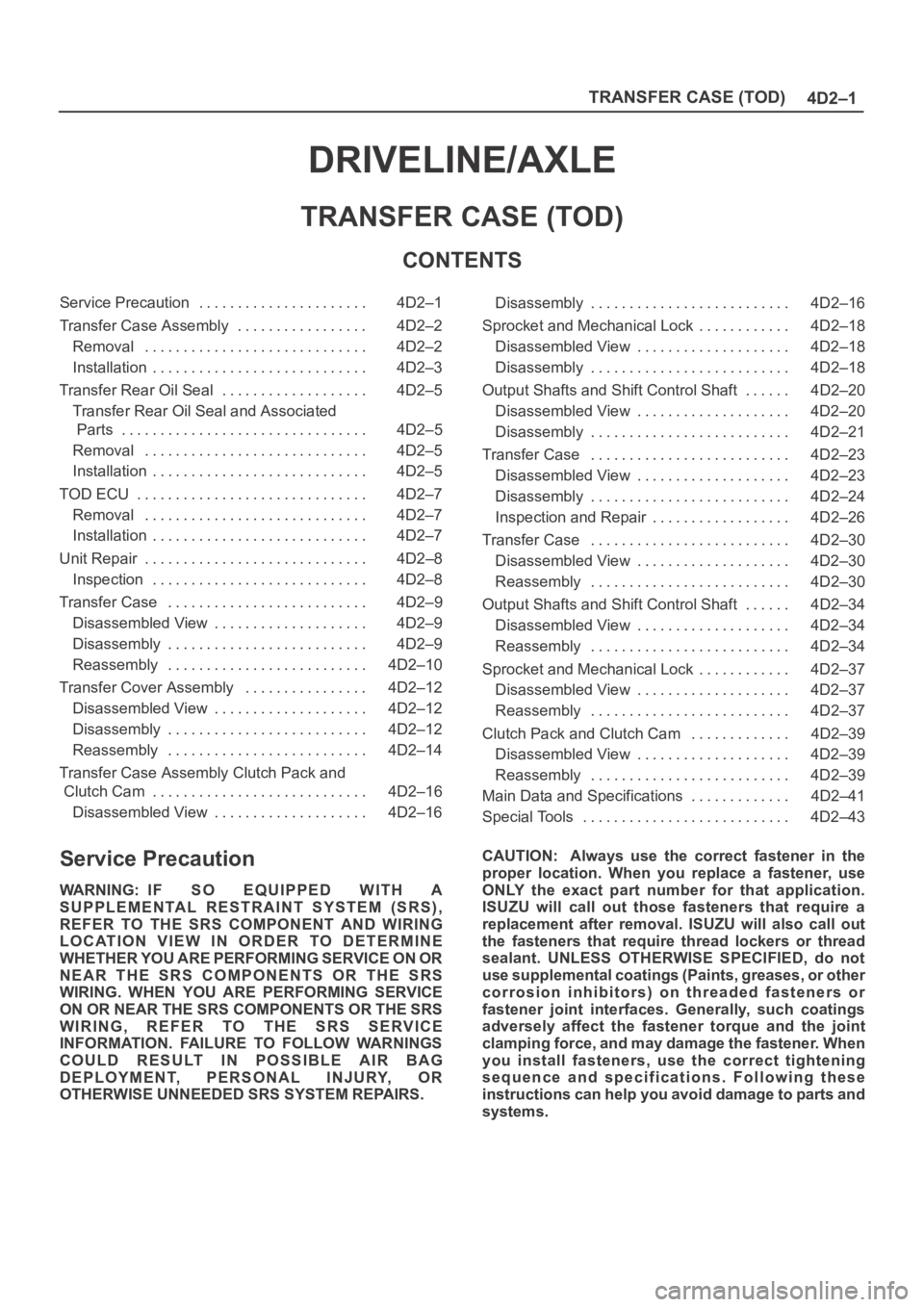
4D2–1 TRANSFER CASE (TOD)
DRIVELINE/AXLE
TRANSFER CASE (TOD)
CONTENTS
Service Precaution 4D2–1. . . . . . . . . . . . . . . . . . . . . .
Transfer Case Assembly 4D2–2. . . . . . . . . . . . . . . . .
Removal 4D2–2. . . . . . . . . . . . . . . . . . . . . . . . . . . . .
Installation 4D2–3. . . . . . . . . . . . . . . . . . . . . . . . . . . .
Transfer Rear Oil Seal 4D2–5. . . . . . . . . . . . . . . . . . .
Transfer Rear Oil Seal and Associated
Parts 4D2–5. . . . . . . . . . . . . . . . . . . . . . . . . . . . . . . .
Removal 4D2–5. . . . . . . . . . . . . . . . . . . . . . . . . . . . .
Installation 4D2–5. . . . . . . . . . . . . . . . . . . . . . . . . . . .
TOD ECU 4D2–7. . . . . . . . . . . . . . . . . . . . . . . . . . . . . .
Removal 4D2–7. . . . . . . . . . . . . . . . . . . . . . . . . . . . .
Installation 4D2–7. . . . . . . . . . . . . . . . . . . . . . . . . . . .
Unit Repair 4D2–8. . . . . . . . . . . . . . . . . . . . . . . . . . . . .
Inspection 4D2–8. . . . . . . . . . . . . . . . . . . . . . . . . . . .
Transfer Case 4D2–9. . . . . . . . . . . . . . . . . . . . . . . . . .
Disassembled View 4D2–9. . . . . . . . . . . . . . . . . . . .
Disassembly 4D2–9. . . . . . . . . . . . . . . . . . . . . . . . . .
Reassembly 4D2–10. . . . . . . . . . . . . . . . . . . . . . . . . .
Transfer Cover Assembly 4D2–12. . . . . . . . . . . . . . . .
Disassembled View 4D2–12. . . . . . . . . . . . . . . . . . . .
Disassembly 4D2–12. . . . . . . . . . . . . . . . . . . . . . . . . .
Reassembly 4D2–14. . . . . . . . . . . . . . . . . . . . . . . . . .
Transfer Case Assembly Clutch Pack and
Clutch Cam 4D2–16. . . . . . . . . . . . . . . . . . . . . . . . . . . .
Disassembled View 4D2–16. . . . . . . . . . . . . . . . . . . . Disassembly 4D2–16. . . . . . . . . . . . . . . . . . . . . . . . . .
Sprocket and Mechanical Lock 4D2–18. . . . . . . . . . . .
Disassembled View 4D2–18. . . . . . . . . . . . . . . . . . . .
Disassembly 4D2–18. . . . . . . . . . . . . . . . . . . . . . . . . .
Output Shafts and Shift Control Shaft 4D2–20. . . . . .
Disassembled View 4D2–20. . . . . . . . . . . . . . . . . . . .
Disassembly 4D2–21. . . . . . . . . . . . . . . . . . . . . . . . . .
Transfer Case 4D2–23. . . . . . . . . . . . . . . . . . . . . . . . . .
Disassembled View 4D2–23. . . . . . . . . . . . . . . . . . . .
Disassembly 4D2–24. . . . . . . . . . . . . . . . . . . . . . . . . .
Inspection and Repair 4D2–26. . . . . . . . . . . . . . . . . .
Transfer Case 4D2–30. . . . . . . . . . . . . . . . . . . . . . . . . .
Disassembled View 4D2–30. . . . . . . . . . . . . . . . . . . .
Reassembly 4D2–30. . . . . . . . . . . . . . . . . . . . . . . . . .
Output Shafts and Shift Control Shaft 4D2–34. . . . . .
Disassembled View 4D2–34. . . . . . . . . . . . . . . . . . . .
Reassembly 4D2–34. . . . . . . . . . . . . . . . . . . . . . . . . .
Sprocket and Mechanical Lock 4D2–37. . . . . . . . . . . .
Disassembled View 4D2–37. . . . . . . . . . . . . . . . . . . .
Reassembly 4D2–37. . . . . . . . . . . . . . . . . . . . . . . . . .
Clutch Pack and Clutch Cam 4D2–39. . . . . . . . . . . . .
Disassembled View 4D2–39. . . . . . . . . . . . . . . . . . . .
Reassembly 4D2–39. . . . . . . . . . . . . . . . . . . . . . . . . .
Main Data and Specifications 4D2–41. . . . . . . . . . . . .
Special Tools 4D2–43. . . . . . . . . . . . . . . . . . . . . . . . . . .
Service Precaution
WARNING: IF SO EQUIPPED WITH A
SUPPLEMENTAL RESTRAINT SYSTEM (SRS),
REFER TO THE SRS COMPONENT AND WIRING
LOCATION VIEW IN ORDER TO DETERMINE
WHETHER YOU ARE PERFORMING SERVICE ON OR
NEAR THE SRS COMPONENTS OR THE SRS
WIRING. WHEN YOU ARE PERFORMING SERVICE
ON OR NEAR THE SRS COMPONENTS OR THE SRS
WIRING, REFER TO THE SRS SERVICE
INFORMATION. FAILURE TO FOLLOW WARNINGS
COULD RESULT IN POSSIBLE AIR BAG
DEPLOYMENT, PERSONAL INJURY, OR
OTHERWISE UNNEEDED SRS SYSTEM REPAIRS.CAUTION: Always use the correct fastener in the
proper location. When you replace a fastener, use
ONLY the exact part number for that application.
ISUZU will call out those fasteners that require a
replacement after removal. ISUZU will also call out
the fasteners that require thread lockers or thread
sealant. UNLESS OTHERWISE SPECIFIED, do not
use supplemental coatings (Paints, greases, or other
corrosion inhibitors) on threaded fasteners or
fastener joint interfaces. Generally, such coatings
adversely affect the fastener torque and the joint
clamping force, and may damage the fastener. When
you install fasteners, use the correct tightening
sequence and specifications. Following these
instructions can help you avoid damage to parts and
systems.
Page 4314 of 6000
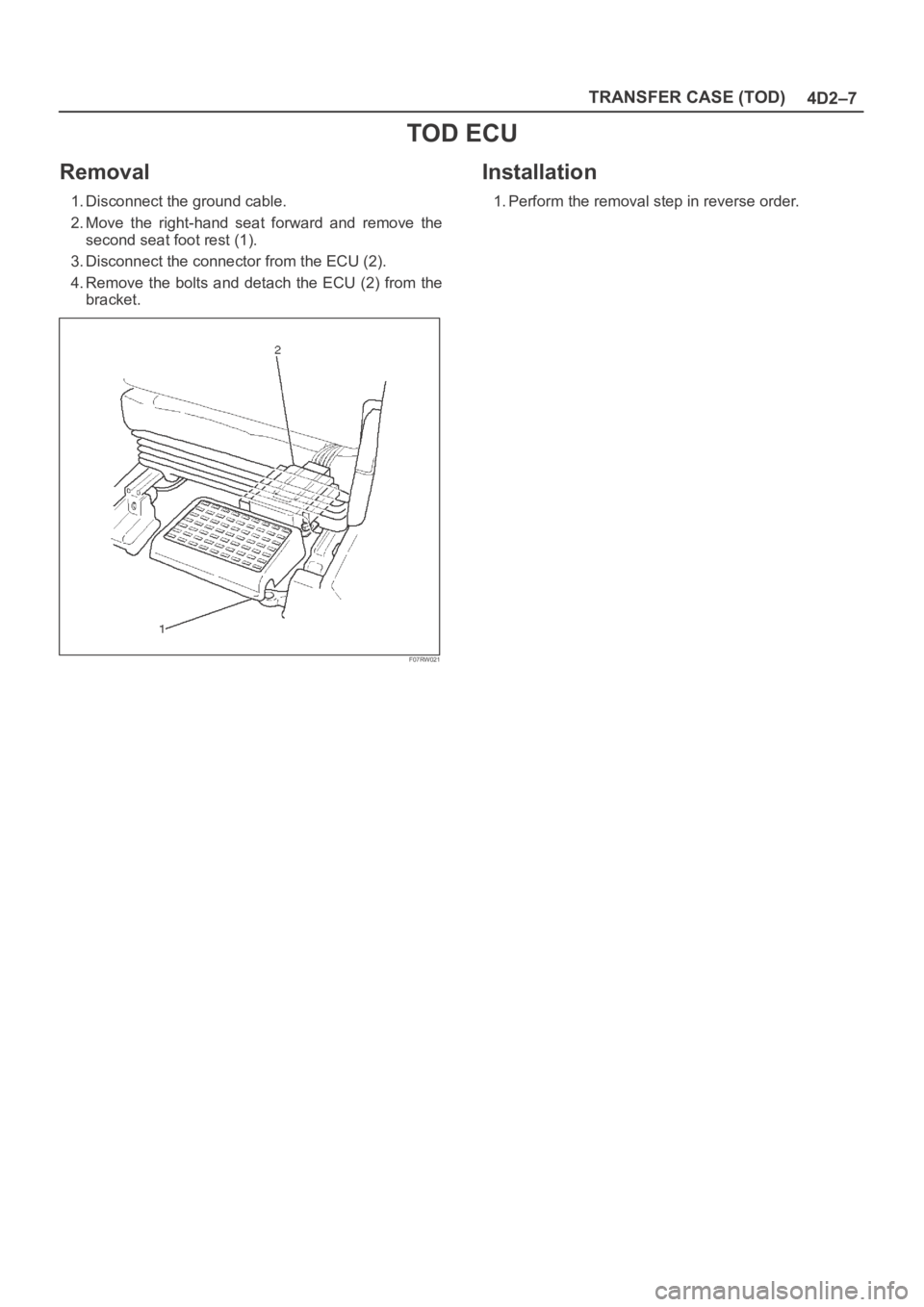
4D2–7 TRANSFER CASE (TOD)
TOD ECU
Removal
1. Disconnect the ground cable.
2. Move the right-hand seat forward and remove the
second seat foot rest (1).
3. Disconnect the connector from the ECU (2).
4. Remove the bolts and detach the ECU (2) from the
bracket.
F07RW021
Installation
1. Perform the removal step in reverse order.
Page 4318 of 6000
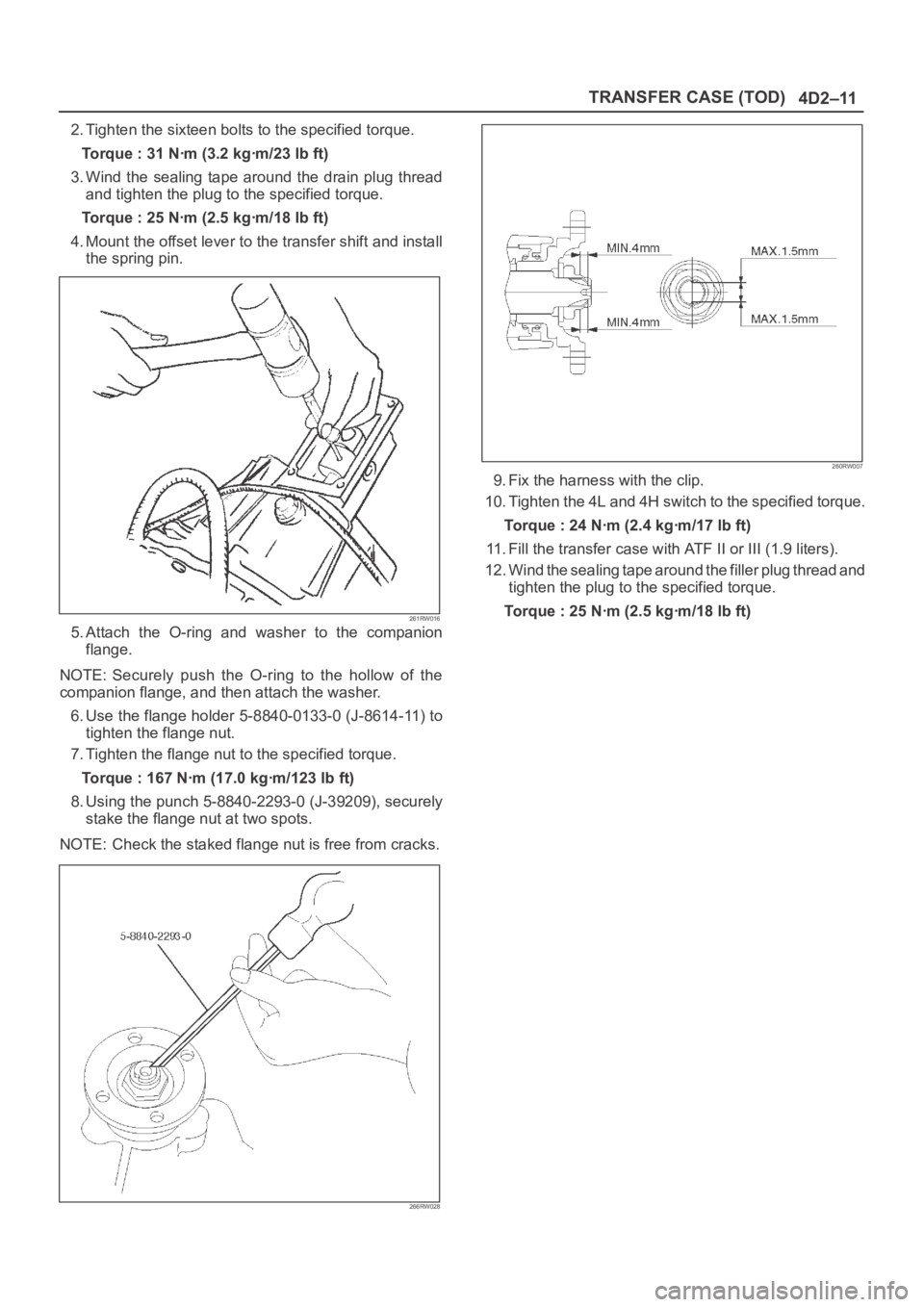
4D2–11 TRANSFER CASE (TOD)
2. Tighten the sixteen bolts to the specified torque.
Torque : 31 Nꞏm (3.2 kgꞏm/23 lb ft)
3. Wind the sealing tape around the drain plug thread
and tighten the plug to the specified torque.
Torque : 25 Nꞏm (2.5 kgꞏm/18 lb ft)
4. Mount the offset lever to the transfer shift and install
the spring pin.
261RW016
5. Attach the O-ring and washer to the companion
flange.
NOTE: Securely push the O-ring to the hollow of the
companion flange, and then attach the washer.
6. Use the flange holder 5-8840-0133-0 (J-8614-11) to
tighten the flange nut.
7. Tighten the flange nut to the specified torque.
Torque : 167 Nꞏm (17.0 kgꞏm/123 lb ft)
8. Using the punch 5-8840-2293-0 (J-39209), securely
stake the flange nut at two spots.
NOTE: Check the staked flange nut is free from cracks.
266RW028
260RW007
9. Fix the harness with the clip.
10. Tighten the 4L and 4H switch to the specified torque.
Torque : 24 Nꞏm (2.4 kgꞏm/17 lb ft)
11. Fill the transfer case with ATF II or III (1.9 liters).
12. Wind the sealing tape around the filler plug thread and
tighten the plug to the specified torque.
Torque : 25 Nꞏm (2.5 kgꞏm/18 lb ft)
Page 4322 of 6000
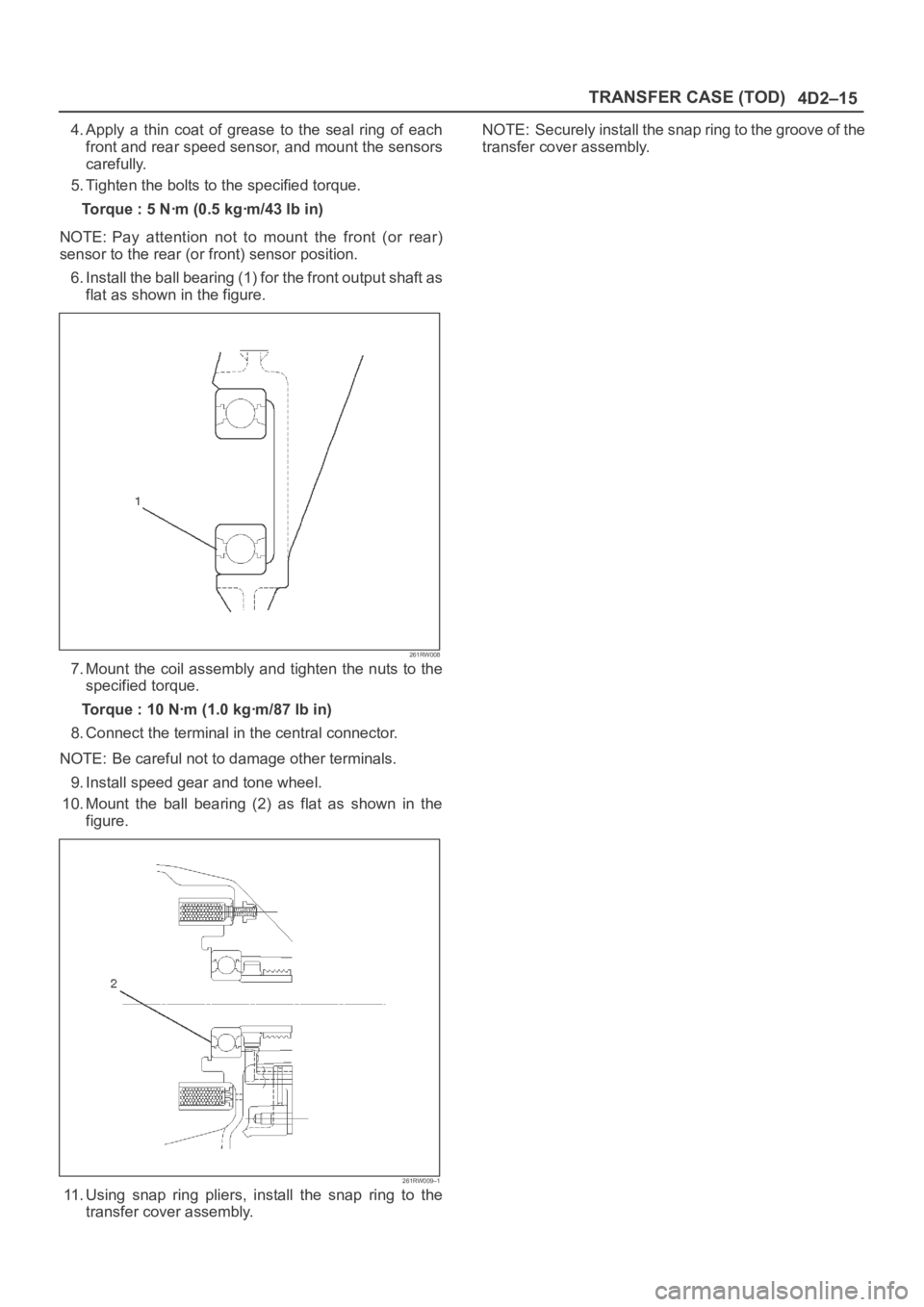
4D2–15 TRANSFER CASE (TOD)
4. Apply a thin coat of grease to the seal ring of each
front and rear speed sensor, and mount the sensors
carefully.
5. Tighten the bolts to the specified torque.
Torque : 5 Nꞏm (0.5 kgꞏm/43 lb in)
NOTE: Pay attention not to mount the front (or rear)
sensor to the rear (or front) sensor position.
6. Install the ball bearing (1) for the front output shaft as
flat as shown in the figure.
261RW008
7. Mount the coil assembly and tighten the nuts to the
specified torque.
Torque : 10 Nꞏm (1.0 kgꞏm/87 lb in)
8. Connect the terminal in the central connector.
NOTE: Be careful not to damage other terminals.
9. Install speed gear and tone wheel.
10. Mount the ball bearing (2) as flat as shown in the
figure.
261RW009–1
11. Using snap ring pliers, install the snap ring to the
transfer cover assembly.NOTE: Securely install the snap ring to the groove of the
transfer cover assembly.
Page 4340 of 6000
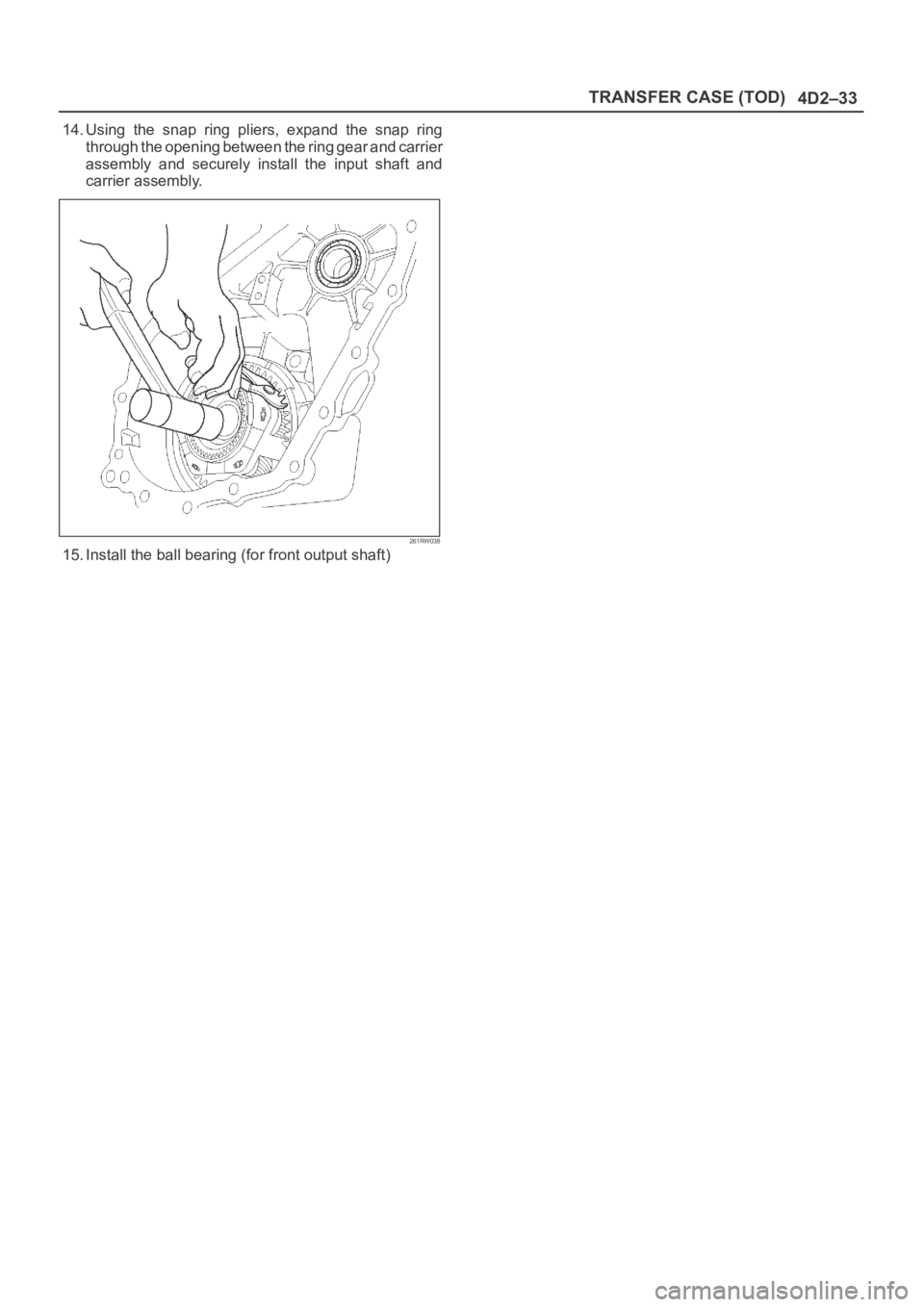
4D2–33 TRANSFER CASE (TOD)
14. Using the snap ring pliers, expand the snap ring
through the opening between the ring gear and carrier
assembly and securely install the input shaft and
carrier assembly.
261RW038
15. Install the ball bearing (for front output shaft)
Page 4397 of 6000
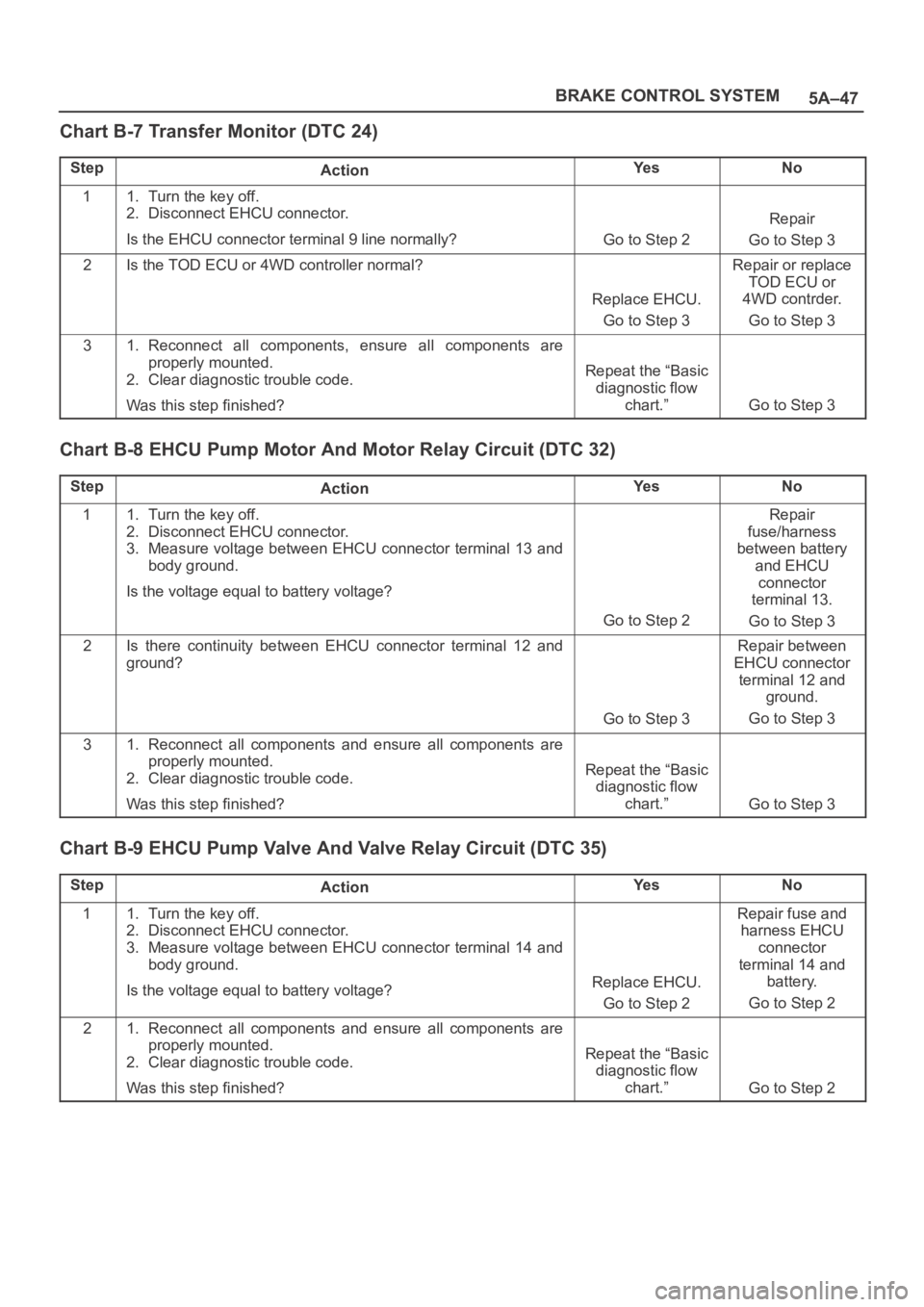
5A–47 BRAKE CONTROL SYSTEM
Chart B-7 Transfer Monitor (DTC 24)
StepActionYe sNo
11. Turn the key off.
2. Disconnect EHCU connector.
Is the EHCU connector terminal 9 line normally?
Go to Step 2
Repair
Go to Step 3
2Is the TOD ECU or 4WD controller normal?
Replace EHCU.
Go to Step 3
Repair or replace
TOD ECU or
4WD contrder.
Go to Step 3
31. Reconnect all components, ensure all components are
properly mounted.
2. Clear diagnostic trouble code.
Was this step finished?
Repeat the “Basic
diagnostic flow
chart.”
Go to Step 3
Chart B-8 EHCU Pump Motor And Motor Relay Circuit (DTC 32)
StepActionYe sNo
11. Turn the key off.
2. Disconnect EHCU connector.
3. Measure voltage between EHCU connector terminal 13 and
body ground.
Is the voltage equal to battery voltage?
Go to Step 2
Repair
fuse/harness
between battery
and EHCU
connector
terminal 13.
Go to Step 3
2Is there continuity between EHCU connector terminal 12 and
ground?
Go to Step 3
Repair between
EHCU connector
terminal 12 and
ground.
Go to Step 3
31. Reconnect all components and ensure all components are
properly mounted.
2. Clear diagnostic trouble code.
Was this step finished?
Repeat the “Basic
diagnostic flow
chart.”
Go to Step 3
Chart B-9 EHCU Pump Valve And Valve Relay Circuit (DTC 35)
StepActionYe sNo
11. Turn the key off.
2. Disconnect EHCU connector.
3. Measure voltage between EHCU connector terminal 14 and
body ground.
Is the voltage equal to battery voltage?
Replace EHCU.
Go to Step 2
Repair fuse and
harness EHCU
connector
terminal 14 and
battery.
Go to Step 2
21. Reconnect all components and ensure all components are
properly mounted.
2. Clear diagnostic trouble code.
Was this step finished?
Repeat the “Basic
diagnostic flow
chart.”
Go to Step 2
Page 4516 of 6000
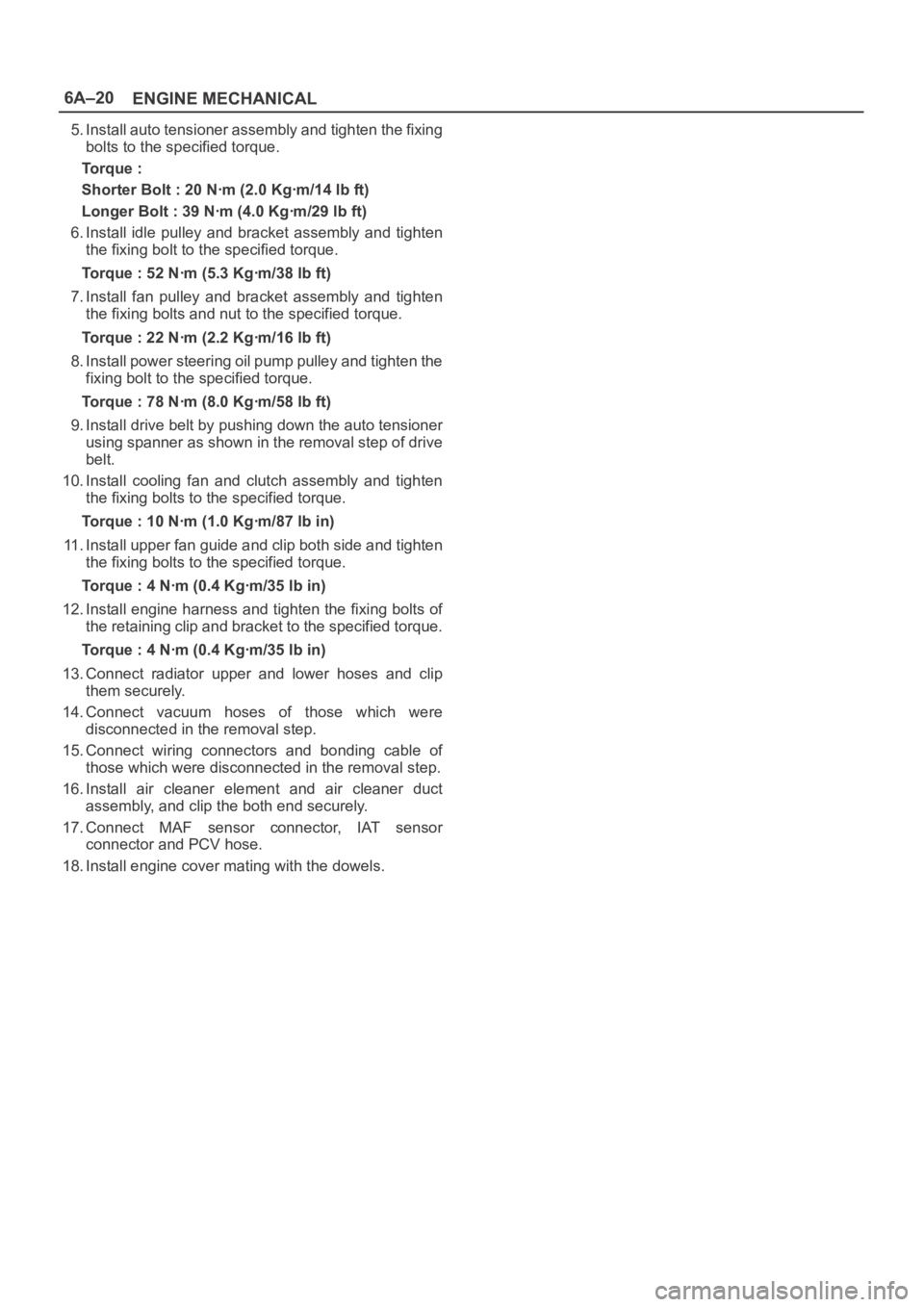
6A–20
ENGINE MECHANICAL
5. Install auto tensioner assembly and tighten the fixing
bolts to the specified torque.
Torque :
Shorter Bolt : 20 Nꞏm (2.0 Kgꞏm/14 lb ft)
Longer Bolt : 39 Nꞏm (4.0 Kgꞏm/29 lb ft)
6. Install idle pulley and bracket assembly and tighten
the fixing bolt to the specified torque.
Torque : 52 Nꞏm (5.3 Kgꞏm/38 lb ft)
7. Install fan pulley and bracket assembly and tighten
the fixing bolts and nut to the specified torque.
Torque : 22 Nꞏm (2.2 Kgꞏm/16 lb ft)
8. Install power steering oil pump pulley and tighten the
fixing bolt to the specified torque.
Torque : 78 Nꞏm (8.0 Kgꞏm/58 lb ft)
9. Install drive belt by pushing down the auto tensioner
using spanner as shown in the removal step of drive
belt.
10. Install cooling fan and clutch assembly and tighten
the fixing bolts to the specified torque.
Torque : 10 Nꞏm (1.0 Kgꞏm/87 lb in)
11. Install upper fan guide and clip both side and tighten
the fixing bolts to the specified torque.
Torque : 4 Nꞏm (0.4 Kgꞏm/35 lb in)
12. Install engine harness and tighten the fixing bolts of
the retaining clip and bracket to the specified torque.
Torque : 4 Nꞏm (0.4 Kgꞏm/35 lb in)
13. Connect radiator upper and lower hoses and clip
them securely.
14. Connect vacuum hoses of those which were
disconnected in the removal step.
15. Connect wiring connectors and bonding cable of
those which were disconnected in the removal step.
16. Install air cleaner element and air cleaner duct
assembly, and clip the both end securely.
17. Connect MAF sensor connector, IAT sensor
connector and PCV hose.
18. Install engine cover mating with the dowels.
Page 4519 of 6000
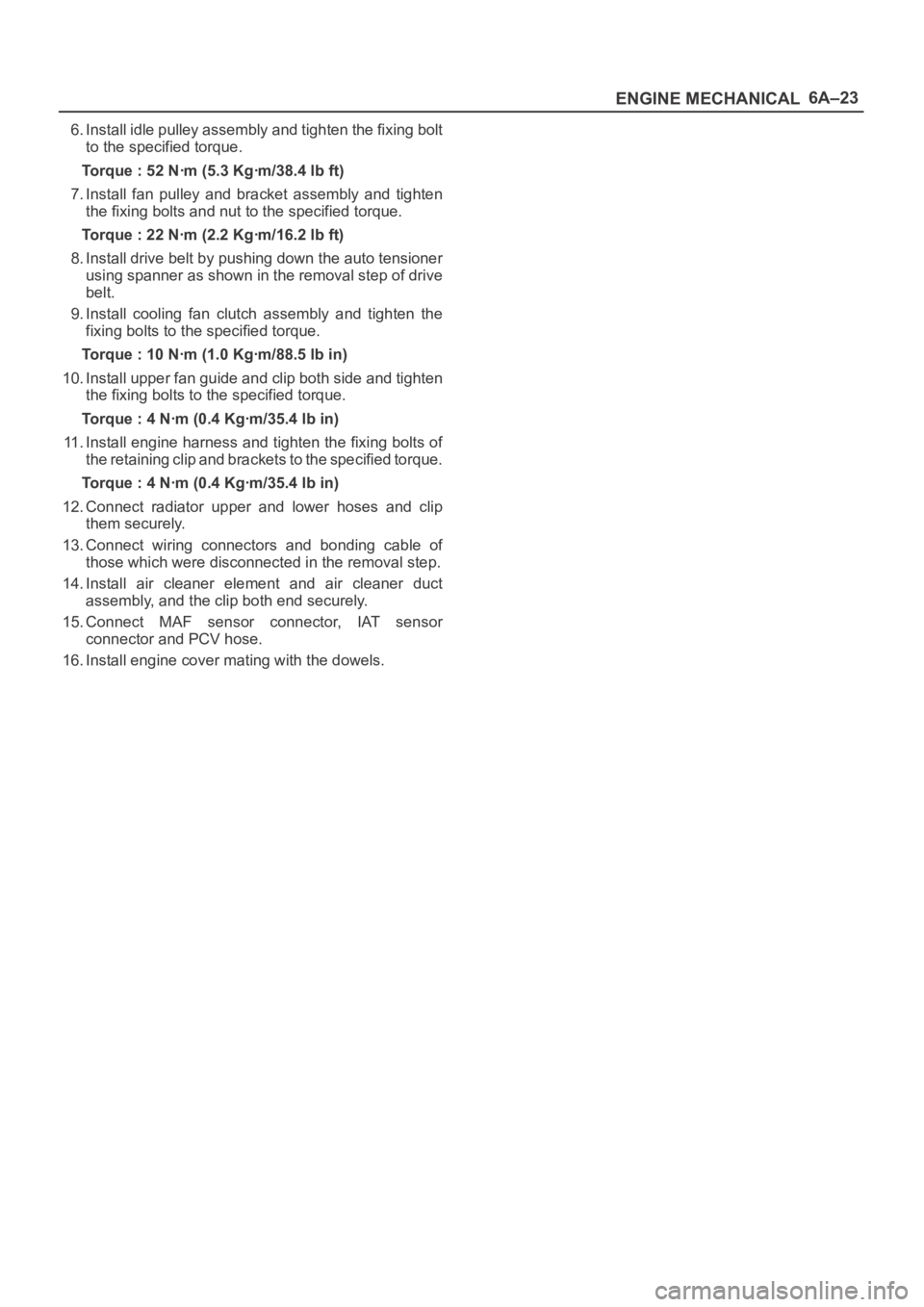
6A–23
ENGINE MECHANICAL
6. Install idle pulley assembly and tighten the fixing bolt
to the specified torque.
Torque : 52 Nꞏm (5.3 Kgꞏm/38.4 lb ft)
7. Install fan pulley and bracket assembly and tighten
the fixing bolts and nut to the specified torque.
Torque : 22 Nꞏm (2.2 Kgꞏm/16.2 lb ft)
8. Install drive belt by pushing down the auto tensioner
using spanner as shown in the removal step of drive
belt.
9. Install cooling fan clutch assembly and tighten the
fixing bolts to the specified torque.
Torque : 10 Nꞏm (1.0 Kgꞏm/88.5 lb in)
10. Install upper fan guide and clip both side and tighten
the fixing bolts to the specified torque.
Torque : 4 Nꞏm (0.4 Kgꞏm/35.4 lb in)
11. Install engine harness and tighten the fixing bolts of
the retaining clip and brackets to the specified torque.
Torque : 4 Nꞏm (0.4 Kgꞏm/35.4 lb in)
12. Connect radiator upper and lower hoses and clip
them securely.
13. Connect wiring connectors and bonding cable of
those which were disconnected in the removal step.
14. Install air cleaner element and air cleaner duct
assembly, and the clip both end securely.
15. Connect MAF sensor connector, IAT sensor
connector and PCV hose.
16. Install engine cover mating with the dowels.
Page 4527 of 6000
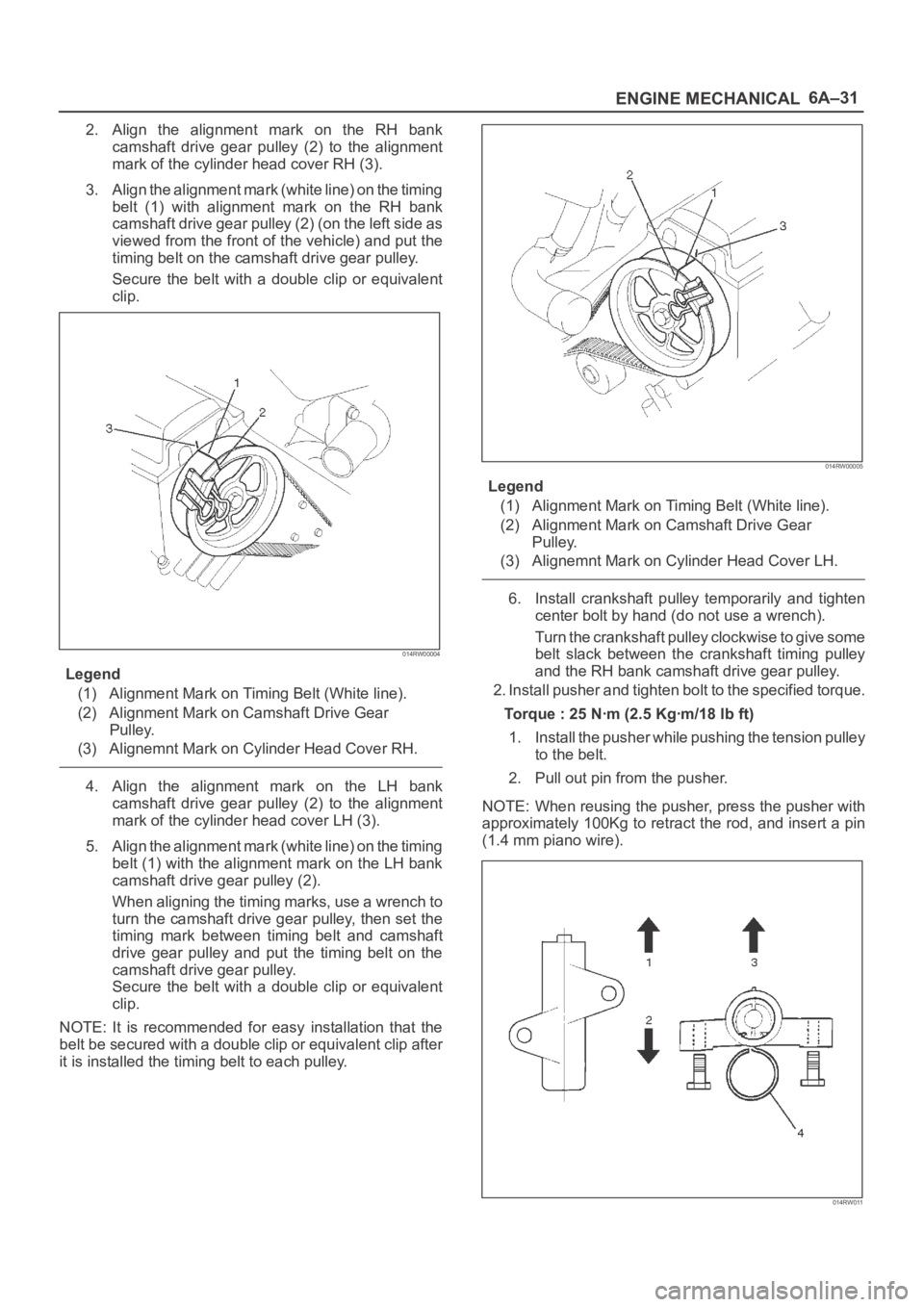
6A–31
ENGINE MECHANICAL
2. Align the alignment mark on the RH bank
camshaft drive gear pulley (2) to the alignment
mark of the cylinder head cover RH (3).
3. Align the alignment mark (white line) on the timing
belt (1) with alignment mark on the RH bank
camshaft drive gear pulley (2) (on the left side as
viewed from the front of the vehicle) and put the
timing belt on the camshaft drive gear pulley.
Secure the belt with a double clip or equivalent
clip.
014RW00004
Legend
(1) Alignment Mark on Timing Belt (White line).
(2) Alignment Mark on Camshaft Drive Gear
Pulley.
(3) Alignemnt Mark on Cylinder Head Cover RH.
4. Align the alignment mark on the LH bank
camshaft drive gear pulley (2) to the alignment
mark of the cylinder head cover LH (3).
5. Align the alignment mark (white line) on the timing
belt (1) with the alignment mark on the LH bank
camshaft drive gear pulley (2).
When aligning the timing marks, use a wrench to
turn the camshaft drive gear pulley, then set the
timing mark between timing belt and camshaft
drive gear pulley and put the timing belt on the
camshaft drive gear pulley.
Secure the belt with a double clip or equivalent
clip.
NOTE: It is recommended for easy installation that the
belt be secured with a double clip or equivalent clip after
it is installed the timing belt to each pulley.
014RW00005
Legend
(1) Alignment Mark on Timing Belt (White line).
(2) Alignment Mark on Camshaft Drive Gear
Pulley.
(3) Alignemnt Mark on Cylinder Head Cover LH.
6. Install crankshaft pulley temporarily and tighten
center bolt by hand (do not use a wrench).
Turn the crankshaft pulley clockwise to give some
belt slack between the crankshaft timing pulley
and the RH bank camshaft drive gear pulley.
2. Install pusher and tighten bolt to the specified torque.
Torque : 25 Nꞏm (2.5 Kgꞏm/18 lb ft)
1. Install the pusher while pushing the tension pulley
to the belt.
2. Pull out pin from the pusher.
NOTE: When reusing the pusher, press the pusher with
approximately 100Kg to retract the rod, and insert a pin
(1.4 mm piano wire).
014RW011
Page 4604 of 6000
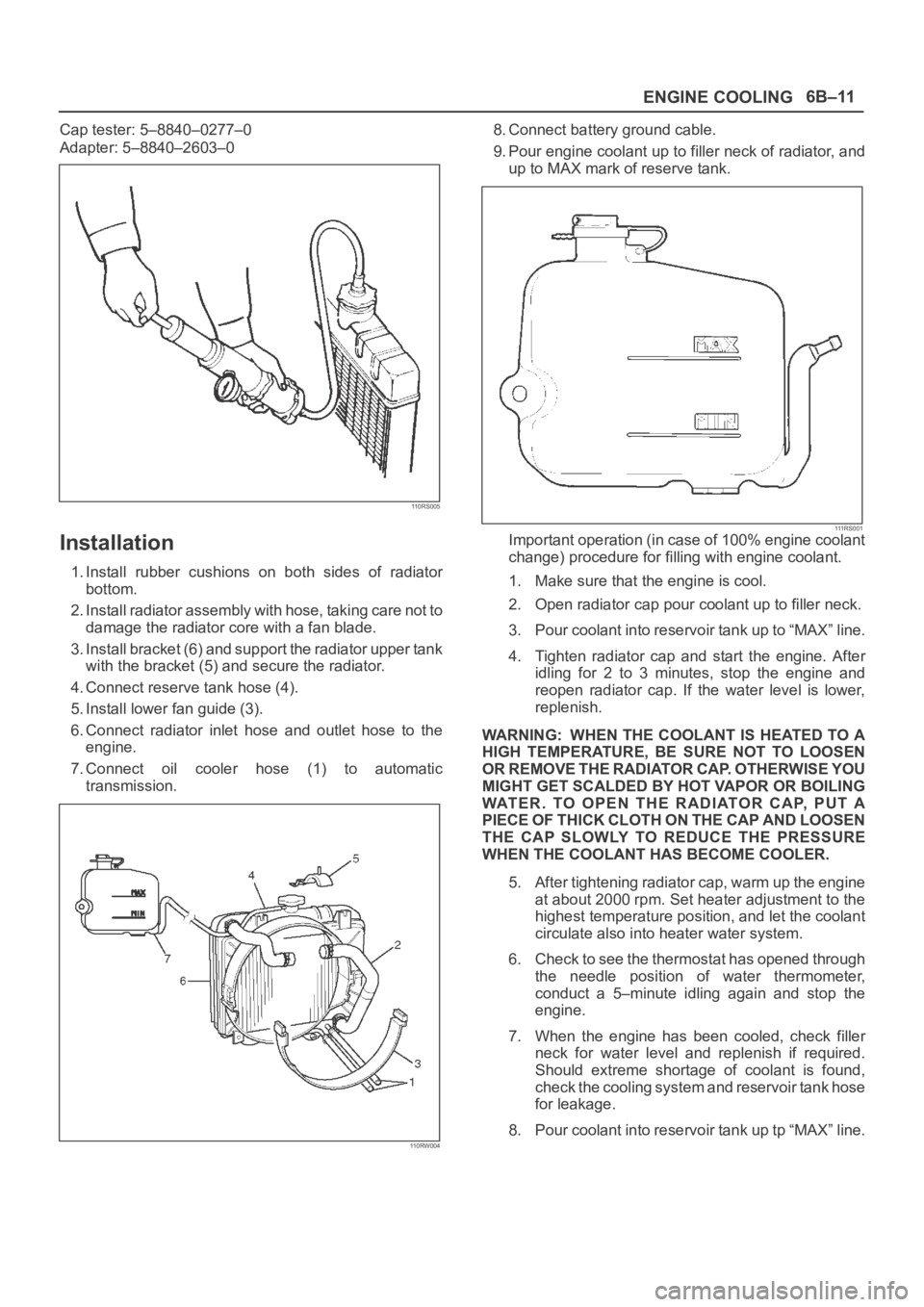
ENGINE COOLING6B–11
Cap tester: 5–8840–0277–0
Adapter: 5–8840–2603–0
110RS005
Installation
1. Install rubber cushions on both sides of radiator
bottom.
2. Install radiator assembly with hose, taking care not to
damage the radiator core with a fan blade.
3. Install bracket (6) and support the radiator upper tank
with the bracket (5) and secure the radiator.
4. Connect reserve tank hose (4).
5. Install lower fan guide (3).
6. Connect radiator inlet hose and outlet hose to the
engine.
7. Connect oil cooler hose (1) to automatic
transmission.
110RW004
8. Connect battery ground cable.
9. Pour engine coolant up to filler neck of radiator, and
up to MAX mark of reserve tank.
111 R S 0 0 1Important operation (in case of 100% engine coolant
change) procedure for filling with engine coolant.
1. Make sure that the engine is cool.
2. Open radiator cap pour coolant up to filler neck.
3. Pour coolant into reservoir tank up to “MAX” line.
4. Tighten radiator cap and start the engine. After
idling for 2 to 3 minutes, stop the engine and
reopen radiator cap. If the water level is lower,
replenish.
WARNING: WHEN THE COOLANT IS HEATED TO A
HIGH TEMPERATURE, BE SURE NOT TO LOOSEN
OR REMOVE THE RADIATOR CAP. OTHERWISE YOU
MIGHT GET SCALDED BY HOT VAPOR OR BOILING
WATER. TO OPEN THE RADIATOR CAP, PUT A
PIECE OF THICK CLOTH ON THE CAP AND LOOSEN
THE CAP SLOWLY TO REDUCE THE PRESSURE
WHEN THE COOLANT HAS BECOME COOLER.
5. After tightening radiator cap, warm up the engine
at about 2000 rpm. Set heater adjustment to the
highest temperature position, and let the coolant
circulate also into heater water system.
6. Check to see the thermostat has opened through
the needle position of water thermometer,
conduct a 5–minute idling again and stop the
engine.
7. When the engine has been cooled, check filler
neck for water level and replenish if required.
Should extreme shortage of coolant is found,
check the cooling system and reservoir tank hose
for leakage.
8. Pour coolant into reservoir tank up tp “MAX” line.