fuel pressure RENAULT KANGOO 1997 KC / 1.G Engine And Peripherals User Guide
[x] Cancel search | Manufacturer: RENAULT, Model Year: 1997, Model line: KANGOO, Model: RENAULT KANGOO 1997 KC / 1.GPages: 208
Page 89 of 208
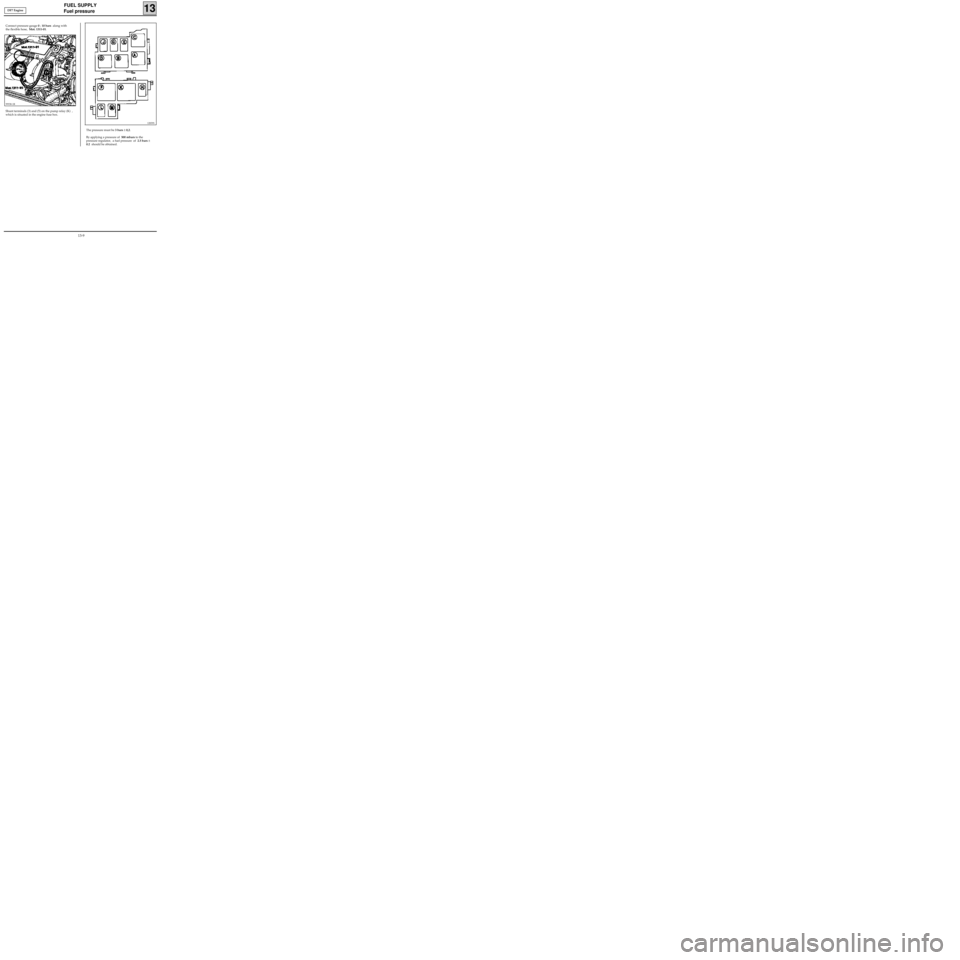
FUEL SUPPLY
Fuel pressure
13
Connect pressure gauge 0 ; 10 bars along with
the flexible hose, Mot. 1311-01.
Shunt terminals (3) and (5) on the pump relay (K) ,
which is situated in the engine fuse box.
99938-1R
12839S
The pressure must be 3 bars ± 0,2.
By applying a pressure of 500 mbars to the
pressure regulator, a fuel pressure of 2.5 bars ±
0.2 should be obtained. DF7 Engine
13-9
Page 90 of 208
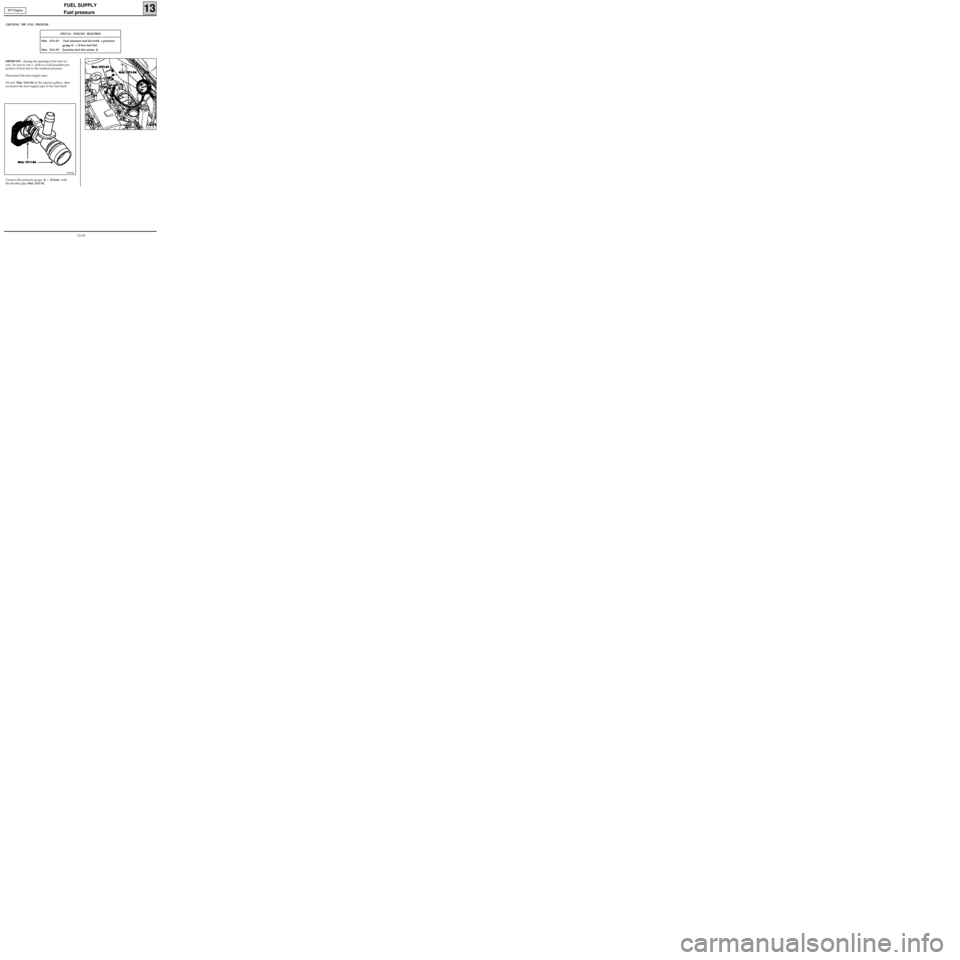
FUEL SUPPLY
Fuel pressure
13
CHECKING THE FUEL PRESSURE
SPECIAL TOOLING REQUIRED
Mot. 1311-01 Fuel pressure test kit (with a pressure
gauge 0; + 10 bar tool kit)
Mot. 1311-05 Junction tool (for union J)
IMPORTANT : during the opening of the fuel cir-
cuit , be sure to use a cloth to avoid possible pro-
jections of fuel due to the residual pressure.
Disconnect the fuel supply pipe.
Fit tool Mot. 1311-04 on the injector gallery, then
reconnect the fuel supply pipe to the tool itself.
13244-1R
EF7 Engine
Connect the pressure gauge 0; + 10 bars with
the flexible pipe Mot. 1311-01.
99376R
13-10
Page 91 of 208
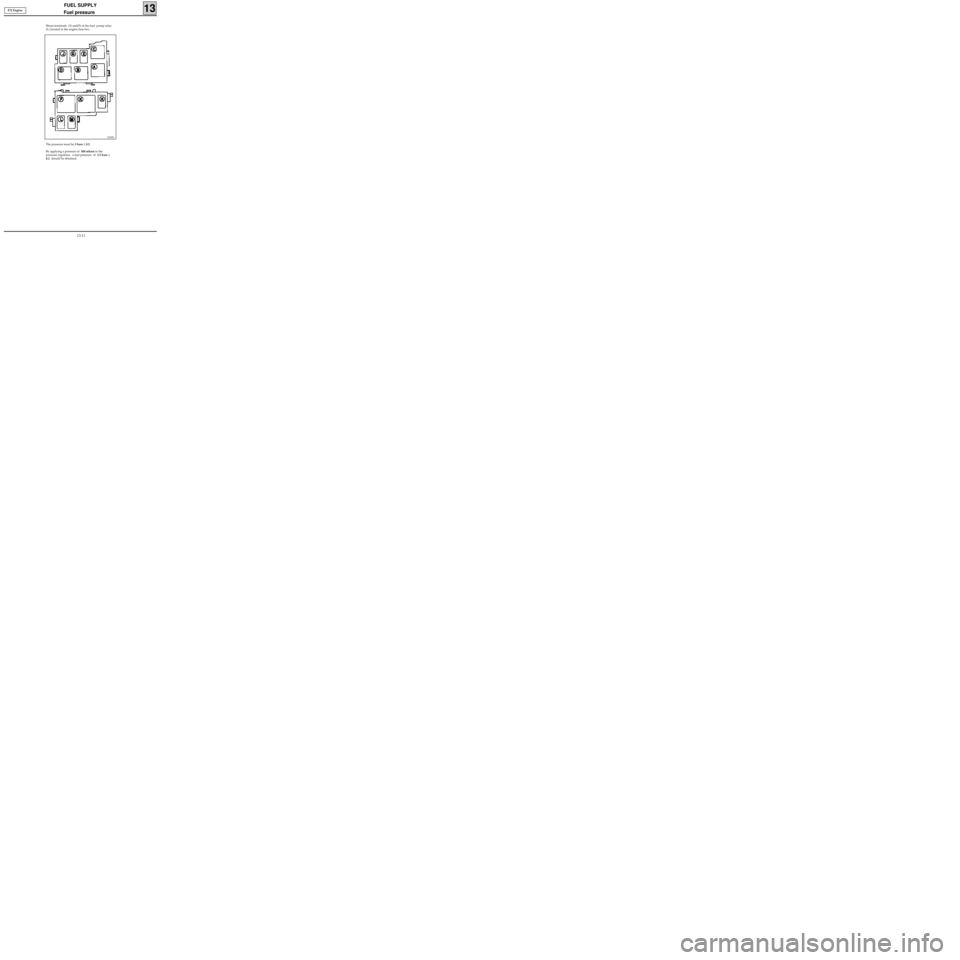
FUEL SUPPLY
Fuel pressure
13E7J Engine
Shunt terminals (3) and(5) of the fuel pump relay
(L) located in the engine fuse box .
12839S
The pressure must be 3 bars ± 0.2.
By applying a pressure of 500 mbars to the
pressure regulator, a fuel pressure of 2.5 bars ±
0.2 should be obtained.
13-11
Page 120 of 208
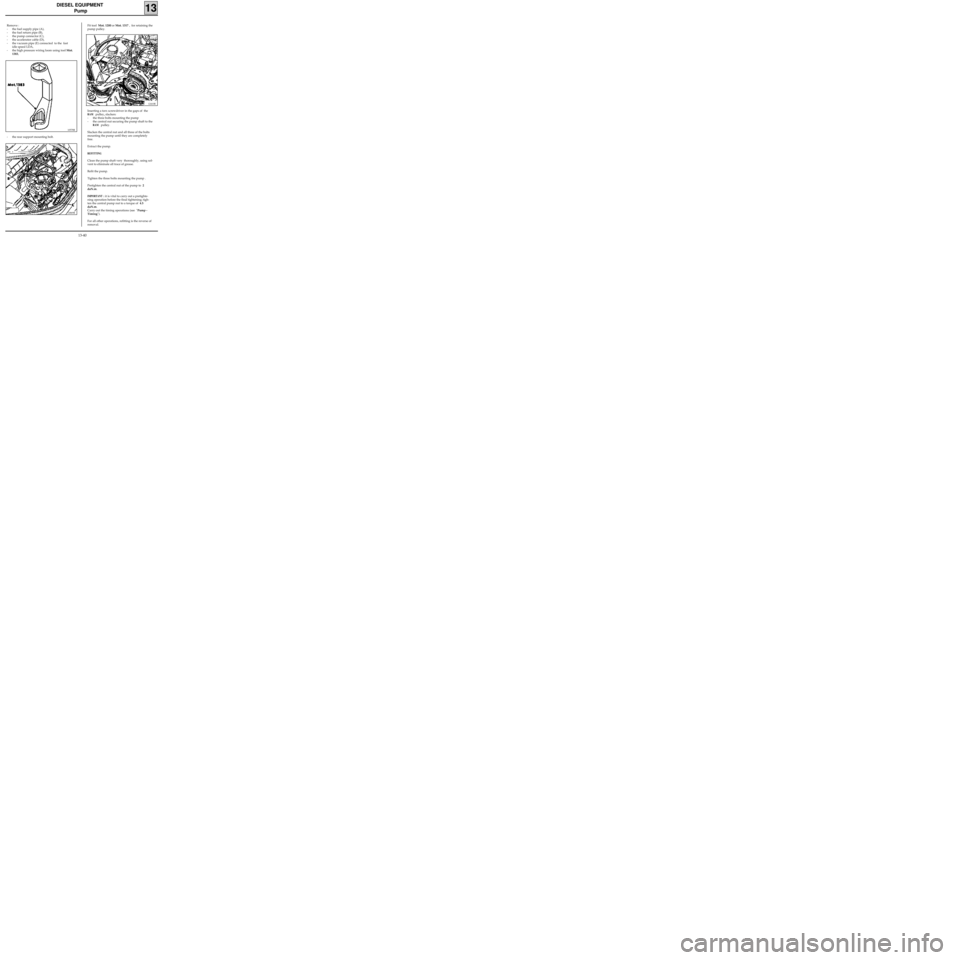
DIESEL EQUIPMENT
Pump
13
Remove :
- the fuel supply pipe (A),
- the fuel return pipe (B),
- the pump connector (C),
- the accelerator cable (D),
- the vacuum pipe (E) connected to the fast
idle speed LDA,
- the high pressure wiring loom using tool Mot.
1383,
10578R
- the rear support mounting bolt.
12869R
Fit tool Mot. 1200 or Mot. 1317 , for retaining the
pump pulley.
12410R
Inserting a torx screwdriver in the gaps of the
RAM pulley, slacken:
- the three bolts mounting the pump
- the central nut securing the pump shaft to the
RAM pulley.
Slacken the central nut and all three of the bolts
mounting the pump until they are completely
free.
Extract the pump.
REFITTING
Clean the pump shaft very thoroughly, using sol-
vent to eliminate all trace of grease.
Refit the pump.
Tighten the three bolts mounting the pump .
Pretighten the central nut of the pump to 2
daN.m.
IMPORTANT : it is vital to carry out a pretighte-
ning operation before the final tightening; tigh-
ten the central pump nut to a torque of 4.5
daN.m.
Carry out the timing operations (see "Pump -
Timing").
For all other operations, refitting is the reverse of
removal.
13-40
Page 130 of 208
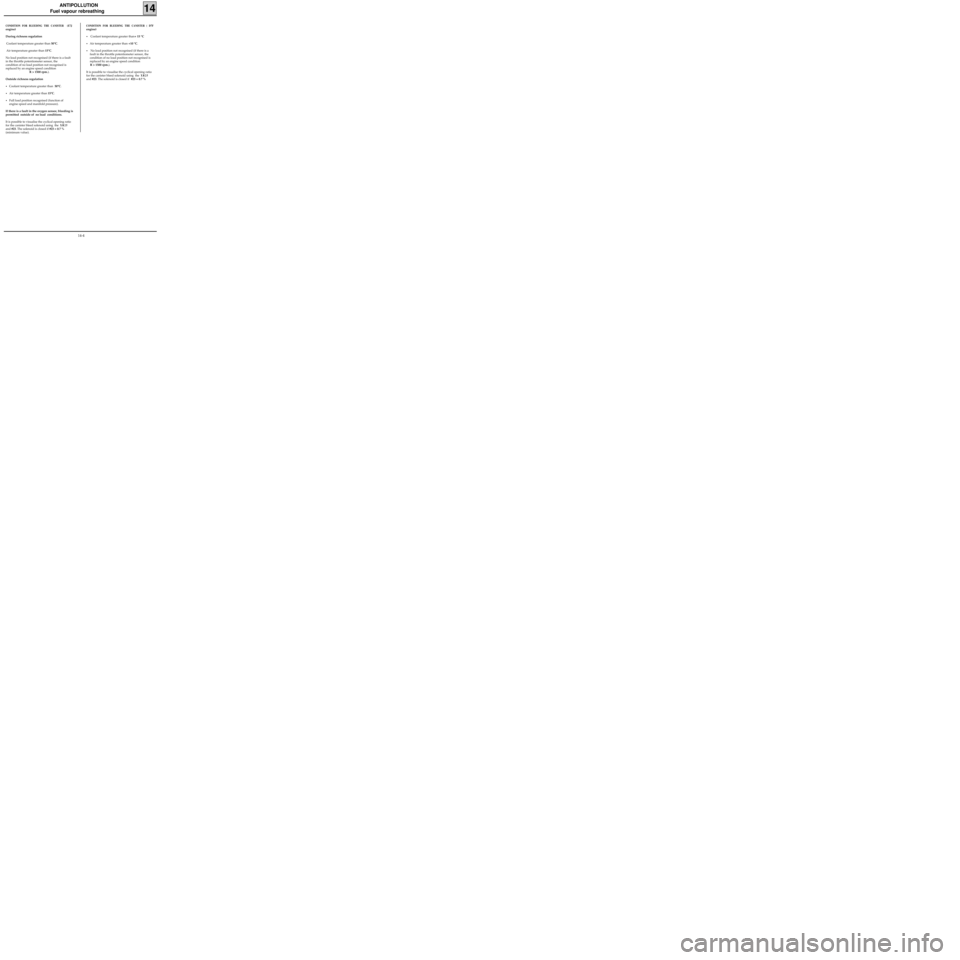
ANTIPOLLUTION
Fuel vapour rebreathing
14
CONDITION FOR BLEEDING THE CANISTER ( D7F
engine)
• Coolant temperature greater than+ 15 °C
•Air temperature greater than +10 °C.
• No load position not recognised (if there is a
fault in the throttle potentiometer sensor, the
condition of no load position not recognised is
replaced by an engine speed condition
R > 1500 rpm.).
It is possible to visualise the cyclical opening ratio
for the canister bleed solenoid using the
XR25
and #23. The solenoid is closed if #23 = 0.7 %
CONDITION FOR BLEEDING THE CANISTER (E7J
engine)
During richness regulation
Coolant temperature greater than 50°C.
Air temperature greater than 15°C.
No load position not recognised (if there is a fault
in the throttle potentiometer sensor, the
condition of no load position not recognised is
replaced by an engine speed condition
R > 1500 rpm.).
Outside richness regulation
•Coolant temperature greater than 50°C.
•Air temperature greater than 15°C.
•Full load position recognised (function of
engine speed and manifold pressure).
If there is a fault in the oxygen sensor, bleeding is
permitted outside of no load conditions.
It is possible to visualise the cyclical opening ratio
for the canister bleed solenoid using the
XR25
and #23. The solenoid is closed if #23 = 0.7 %
(minimum value).
14-4
Page 131 of 208
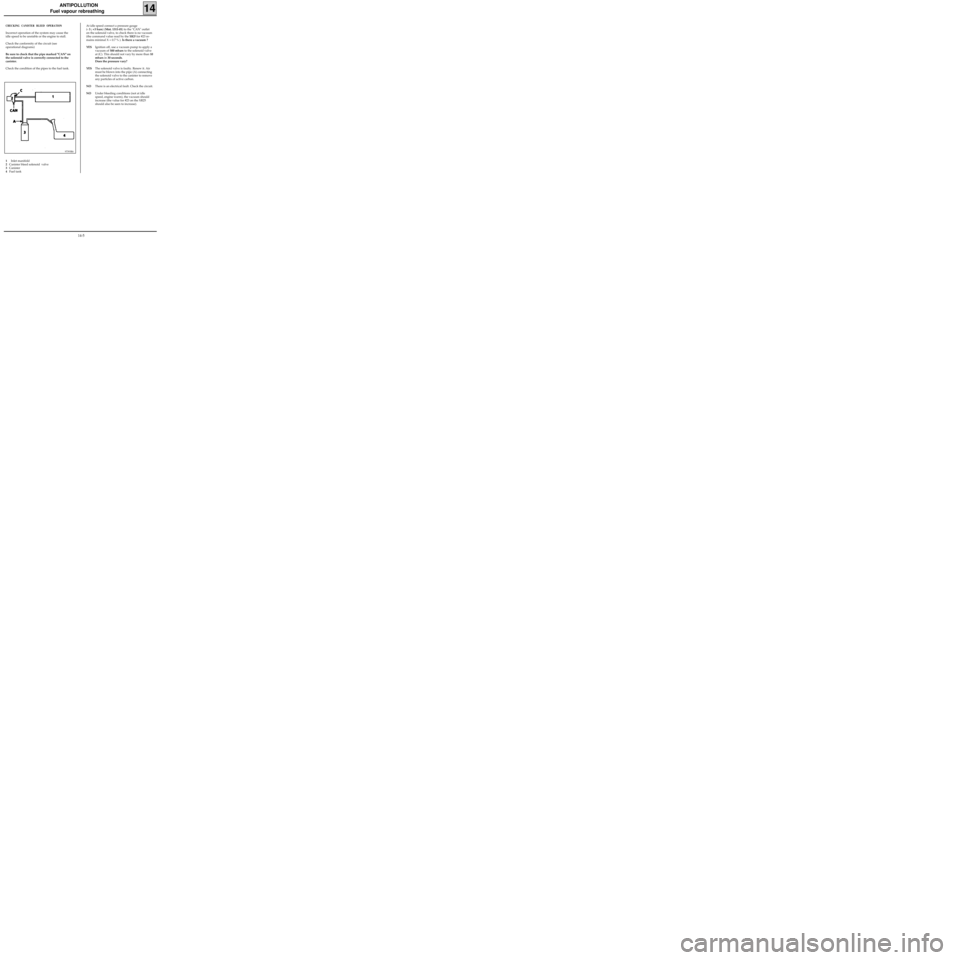
ANTIPOLLUTION
Fuel vapour rebreathing
14
CHECKING CANISTER BLEED OPERATION
Incorrect operation of the system may cause the
idle speed to be unstable or the engine to stall.
Check the conformity of the circuit (see
operational diagrams)
Be sure to check that the pipe marked "CAN" on
the solenoid valve is correctly connected to the
canister.
Check the condition of the pipes to the fuel tank.
97393R6
1Inlet manifold
2Canister bleed solenoid valve
3Canister
4Fuel tankAt idle speed connect a pressure gauge
(- 3 ; +3 bars) (Mot. 1311-01) to the "CAN" outlet
on the solenoid valve, to check there is no vacuum
(the command value read by the
XR25 for #23 re-
mains minimal X = 0.7 % ). Is there a vacuum ?
YESIgnition off, use a vacuum pump to apply a
vacuum of 500 mbars to the solenoid valve
at (C). This should not vary by more than 10
mbars in 30 seconds.
Does the pressure vary?
YESThe solenoid valve is faulty. Renew it. Air
must be blown into the pipe (A) connecting
the solenoid valve to the canister to remove
any particles of active carbon.
NOThere is an electrical fault. Check the circuit.
NOUnder bleeding conditions (not at idle
speed, engine warm), the vacuum should
increase (the value for #23 on the XR25
should also be seen to increase).
14-5
Page 156 of 208
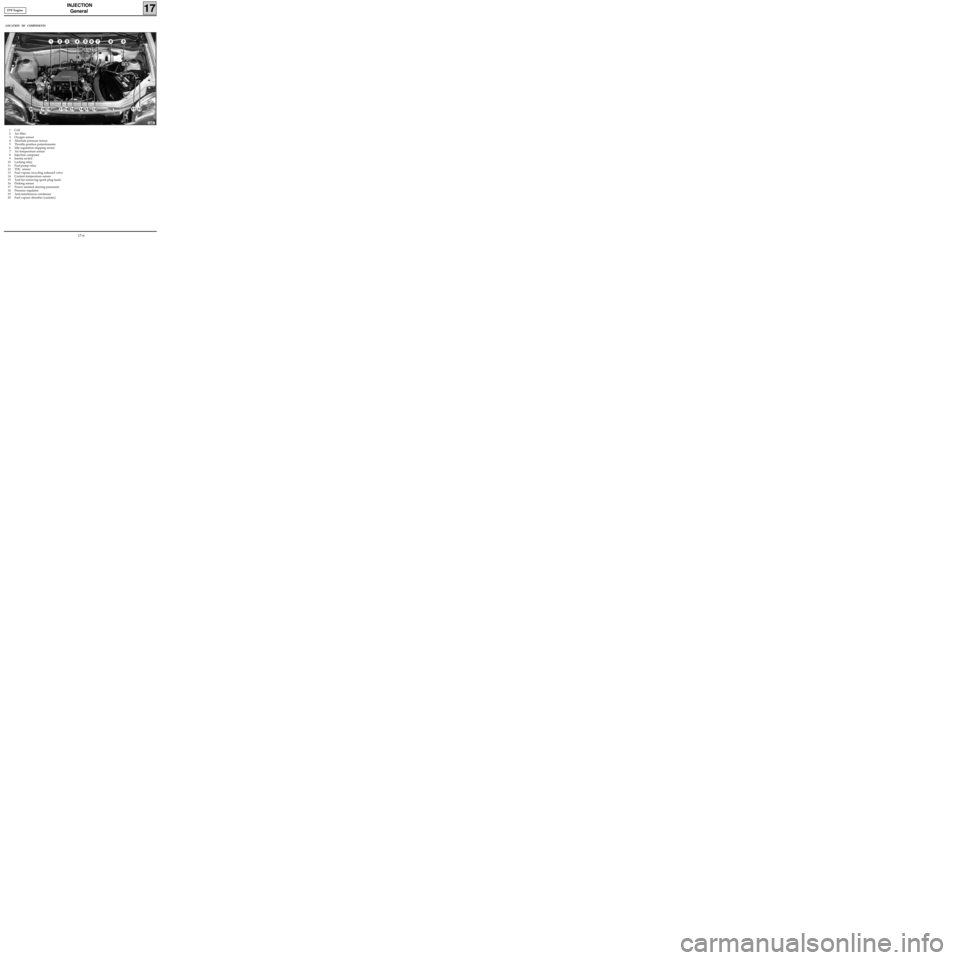
INJECTION
General
17
1 Coil
2 Air filter
3 Oxygen sensor
4 Absolute pressure sensor
5 Throttle position potentiometer
6 Idle regulation stepping motor
7 Air temperature sensor
8 Injection computer
9 Inertia switch
10 Locking relay
11 Fuel pump relay
12 TDC sensor
13 Fuel vapour recycling solenoid valve
14 Coolant temperature sensor
15 Tool for removing spark plug leads
16 Pinking sensor
17 Power assisted steering pressostat
18 Pressure regulator
19 Anti-interference condenser
20 Fuel vapour absorber (canister)
LOCATION OF COMPONENTS
13081
D7F Engine
17-6
Page 157 of 208
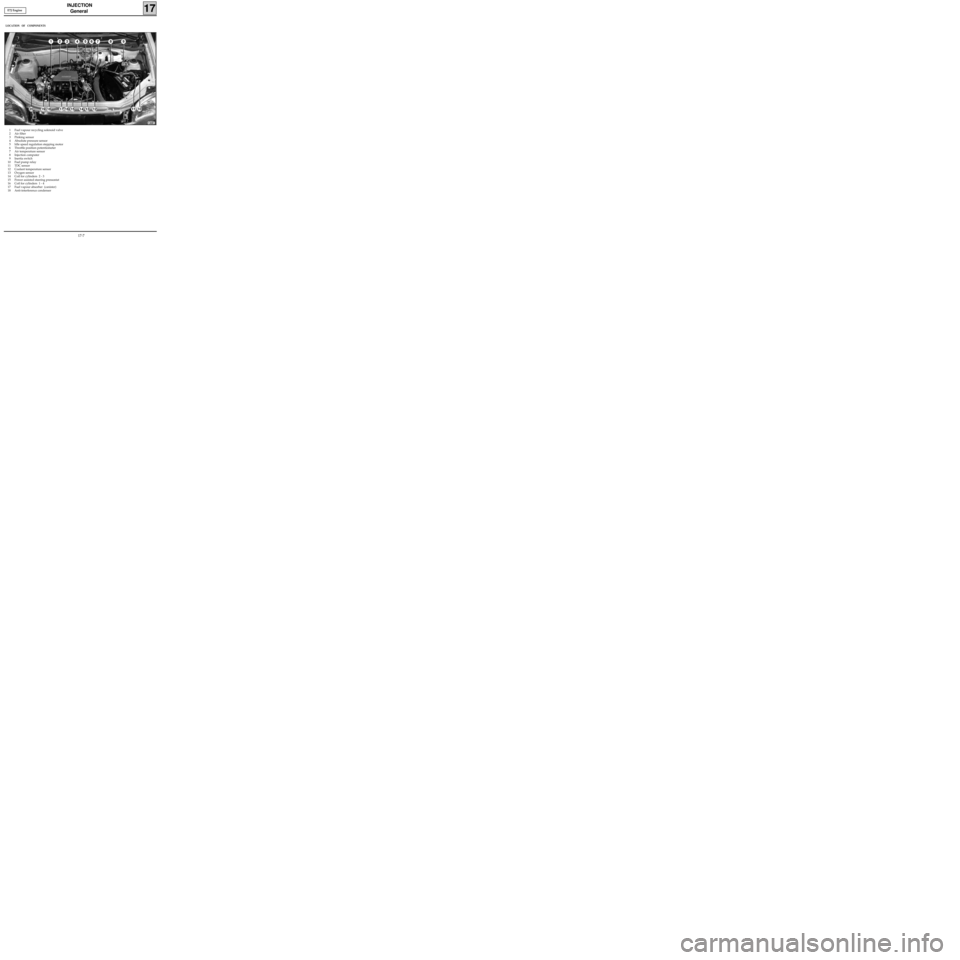
INJECTION
General
17
1 Fuel vapour recycling solenoid valve
2 Air filter
3 Pinking sensor
4 Absolute pressure sensor
5 Idle speed regulation stepping motor
6 Throttle position potentiometer
7 Air temperature sensor
8 Injection computer
9 Inertia switch
10 Fuel pump relay
11 TDC sensor
12 Coolant temperature sensor
13 Oxygen sensor
14 Coil for cylinders 2 - 3
15 Power assisted steering pressostat
16 Coil for cylinders 1 - 4
17 Fuel vapour absorber (canister)
18 Anti-interference condenser
LOCATION OF COMPONENTS
13082
E7J Engine
17-7
Page 158 of 208
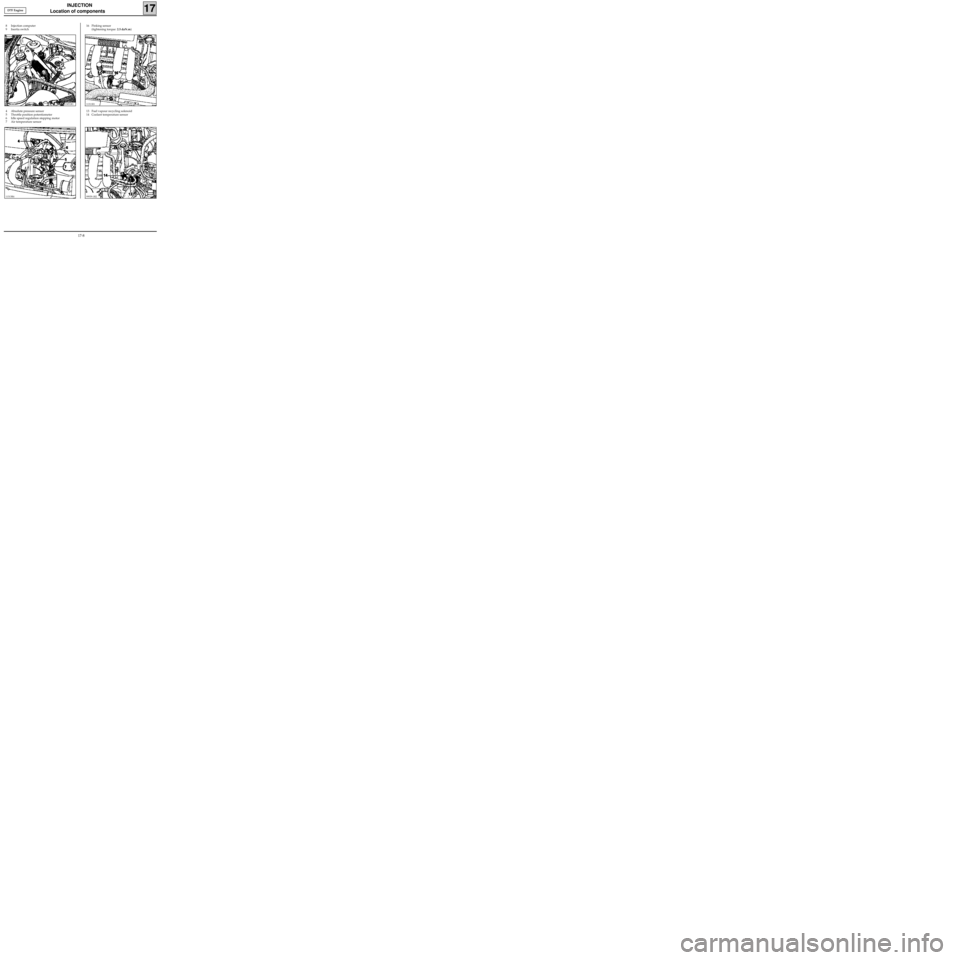
INJECTION
Location of components
17
4 Absolute pressure sensor
5 Throttle position potentiometer
6 Idle speed regulation stepping motor
7 Air temperature sensor13 Fuel vapour recycling solenoid
14 Coolant temperature sensor 16 Pinking sensor
(tightening torque: 2.5 daN.m)
11313R4
11311R1
99939-1R2
8 Injection computer
9 Inertia switch
13051R1
D7F Engine
17-8
Page 161 of 208
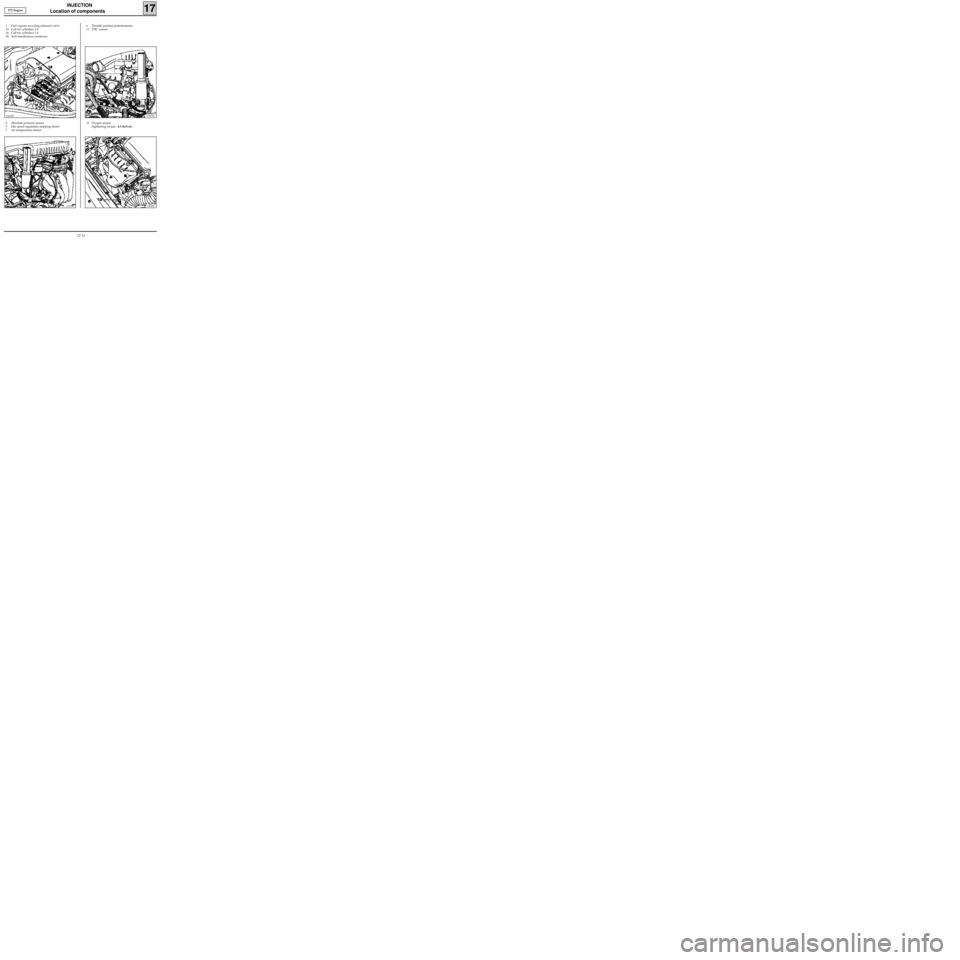
INJECTION
Location of components
17
4 Absolute pressure sensor
5 Idle speed regulation stepping motor
7 Air temperature sensor6 Throttle position potentiometer
11 TDC sensor
13337R
1 Fuel vapour recycling solenoid valve
14 Coil for cylinders 2-3
16 Coil for cylinders 1-4
18 Anti-interference condenser
13242R1
13339R
13 Oxygen sensor
(tightening torque : 4.5 daN.m)
13243R
E7J Engine
17-11