alternator RENAULT KANGOO 1997 KC / 1.G Engine And Peripherals Workshop Manual
[x] Cancel search | Manufacturer: RENAULT, Model Year: 1997, Model line: KANGOO, Model: RENAULT KANGOO 1997 KC / 1.GPages: 208
Page 4 of 208
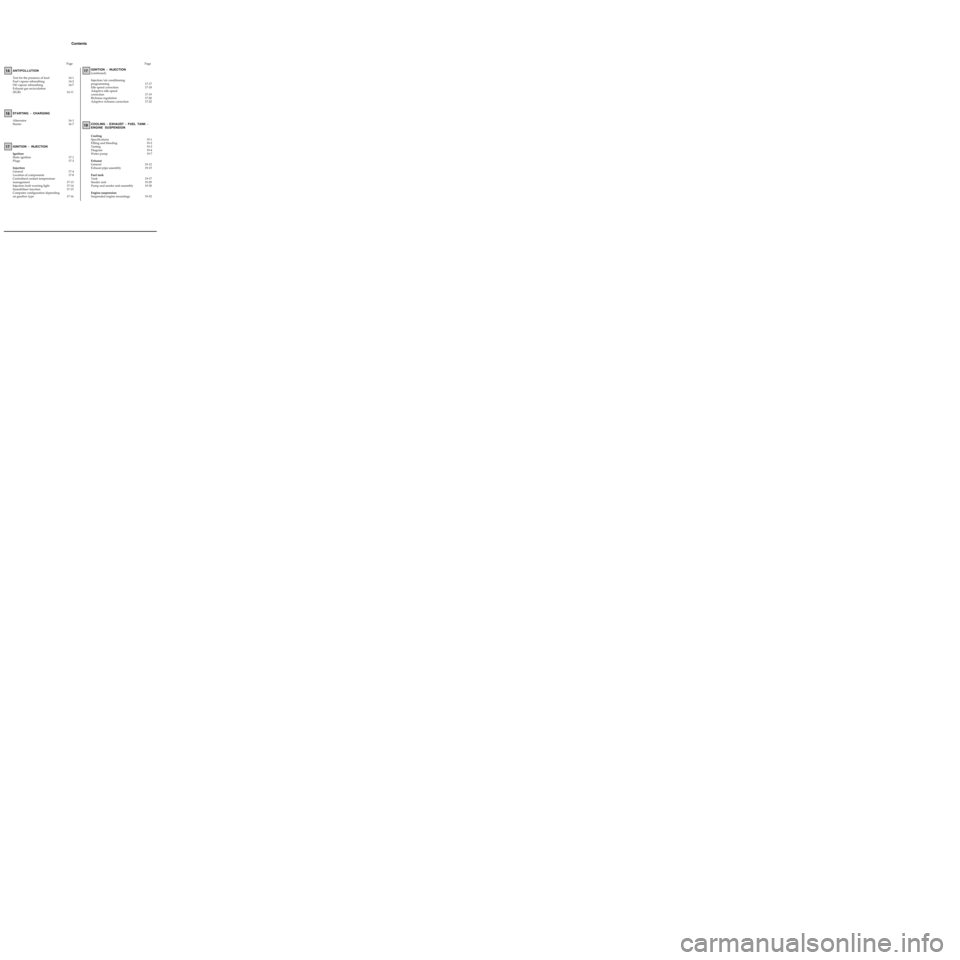
Page
Cooling
Specifications
Filling and bleeding
Testing
Diagram
Water pump
Exhaust
General
Exhaust pipe assembly
Fuel tank
Tank
Sender unit
Pump and sender unit assembly
Engine suspension
Suspended engine mountings19-1
19-2
19-3
19-4
19-7
19-12
19-15
19-17
19-29
19-30
19-32 COOLING - EXHAUST - FUEL TANK -
ENGINE SUSPENSION
19
16-1
16-7 STARTING - CHARGING
Alternator
Starter
16
IGNITION - INJECTION
Ignition
Static ignition
Plugs
Injection
General
Location of components
Centralised coolant temperature
management
Injection fault warning light
Immobiliser function
Computer configuration depending
on gearbox type17
14-1
14-2
14-7
14-11 ANTIPOLLUTION
Test for the presence of lead
Fuel vapour rebreathing
Oil vapour rebreathing
Exhaust gas recirculation
(EGR)
14
17-17
17-18
17-19
17-20
17-22 IGNITION - INJECTION
(continued)
Injection/air conditioning
programming
Idle speed correction
Adaptive idle speed
correction
Richness regulation
Adaptive richness correction
17
Page
17-1
17-3
17-4
17-8
17-13
17-14
17-15
17-16
Contents
Page 35 of 208
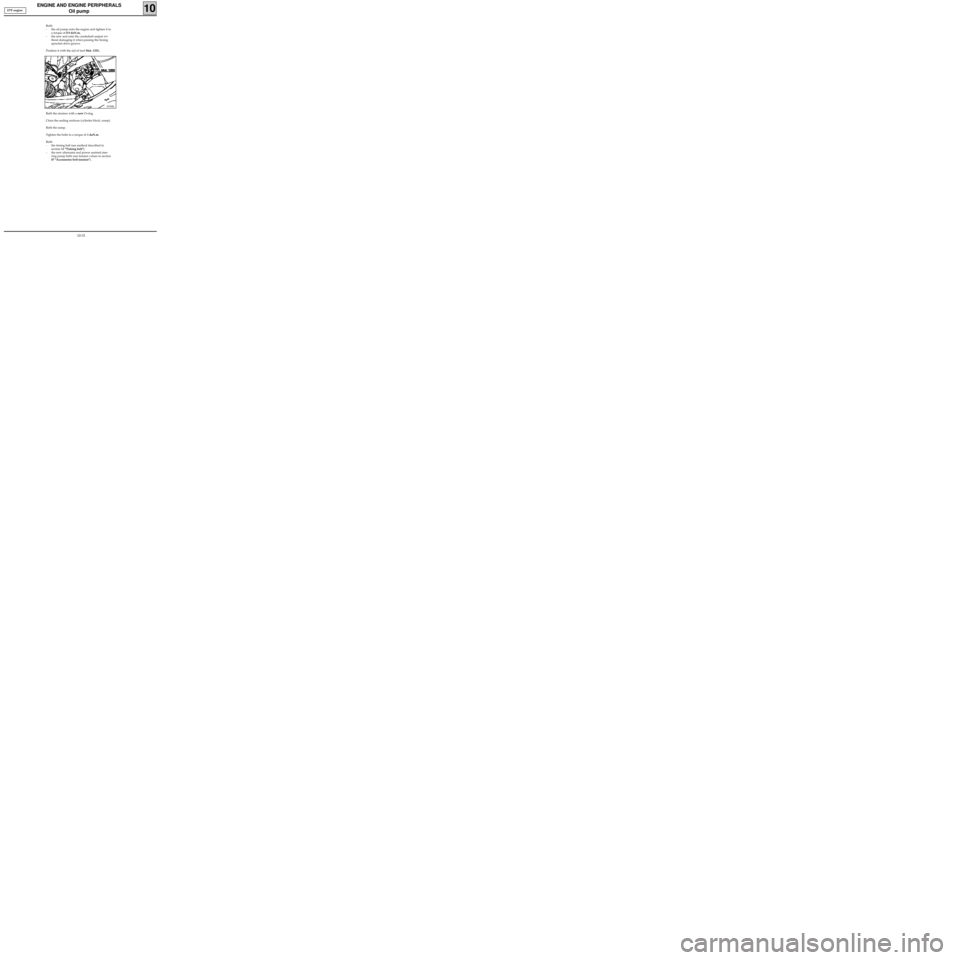
ENGINE AND ENGINE PERIPHERALS
Oil pump
10
Refit:
- the oil pump onto the engine and tighten it to
a torque of 0.9 daN.m,
- the new seal onto the crankshaft output wi-
thout damaging it when passing the timing
sprocket drive groove.
Position it with the aid of tool Mot. 1355..
99788R
Refit the strainer with a new O-ring.
Clean the sealing surfaces (cylinder block, sump).
Refit the sump.
Tighten the bolts to a torque of 1 daN.m.
Refit:
- the timing belt (see method described in
section 11 "Timing belt"),
- the new alternator and power assisted stee-
ring pump belts (see tension values in section
07 "Accessories belt tension"). D7F engine
10-31
Page 36 of 208

TIGHTENING TORQUES (in daN.m)
TOP AND FRONT OF ENGINE
Timing belt
REMOVAL
Place the vehicle on a two post lift.
Disconnect the battery.
Remove :
- the front right hand wheel,
- the belt from the alternator and the power
assisted steering pump if fitted (see section
07),
- the crankshaft accessories pulley.
11
10267R
SPECIAL TOOLING REQUIRED
Crankshaft accessories pulley
mounting bolt 2 + 90°
Mounting bolt for front right
suspended engine mounting
on engine 6.2
Mounting bolt for front right
suspended engine mounting
on vehicle body 6.2
Timing belt tension wheel nut 5
Mot. 1054TDC pin
Mot. 1135-01 Tool for tensioning timing
belt
Mot. 1273 Tool for checking belt tension
Mot. 1379 Tool for securing engine to
subframe
Mot. 1386 Tool for pre-tensioning timing
belt
Fit tool Mot. 1379. D7F engine
11-1
Page 40 of 208
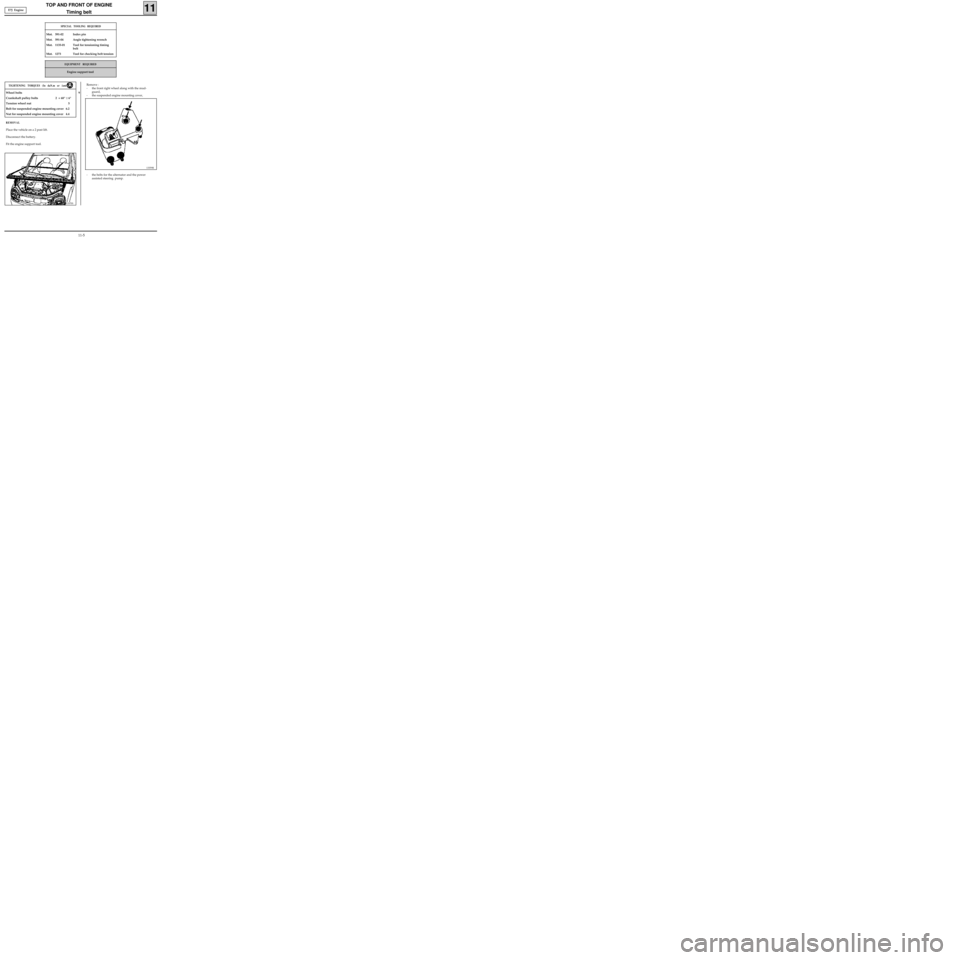
TOP AND FRONT OF ENGINE
Timing belt
REMOVAL
Place the vehicle on a 2 post lift.
Disconnect the battery.
Fit the engine support tool.
11
13370S
SPECIAL TOOLING REQUIRED
Mot. 591-02 Index pin
Mot. 591-04 Angle tightening wrench
Mot. 1135-01 Tool for tensioning timing
belt
Mot. 1273 Tool for checking belt tension
Wheel bolts 9
Crankshaft pulley bolts 2 + 68° ± 6°
Tension wheel nut 5
Bolt for suspended engine mounting cover 6.2
Nut for suspended engine mounting cover 4.4
13359R
Remove :
- the front right wheel along with the mud-
guard,
- the suspended engine mounting cover,
EQUIPMENT REQUIRED
Engine support tool
- the belts for the alternator and the power
assisted steering pump.
TIGHTENING TORQUES (In daN.m or /and°)
E7J Engine
11-5
Page 54 of 208
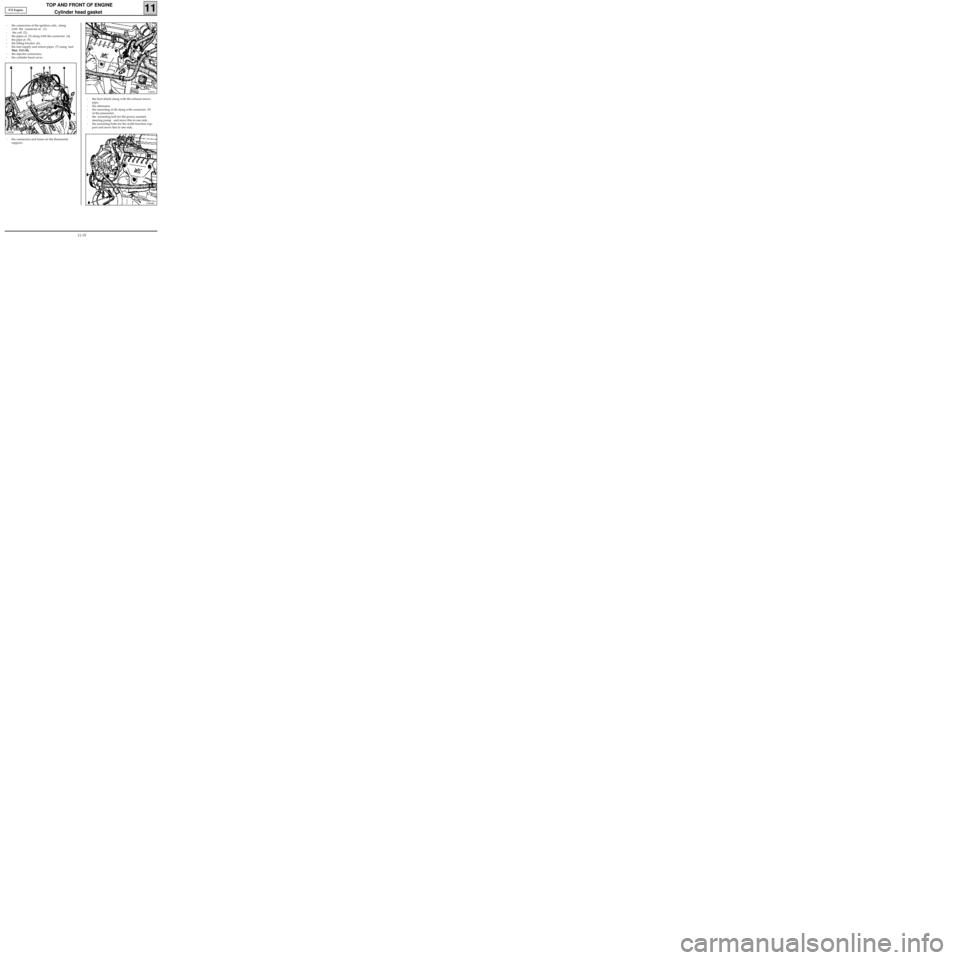
- the heat shield along with the exhaust down-
pipe,
- the alternator,
- the mounting at (8) along with connector (9)
of the pressostat,
- the mounting bolt for the power assisted
steering pump and move this to one side ,
- the mounting bolts for the multi-function sup-
port and move this to one side,
TOP AND FRONT OF ENGINE
Cylinder head gasket
11
13365S
13364R1
13360R
- the connectors and hoses on the thermostat
support , - the connectors of the ignition coils, along
with the connector at (1),
- the coil (2),
- the pipes at (3) along with the connector (4),
- the pipe at (5),
- the lifting bracket (6),
- the fuel supply and return pipes (7) using tool
Mot. 1311-06,
- the injector connectors,
- the cylinder head cover , E7J Engine
11-19
Page 140 of 208
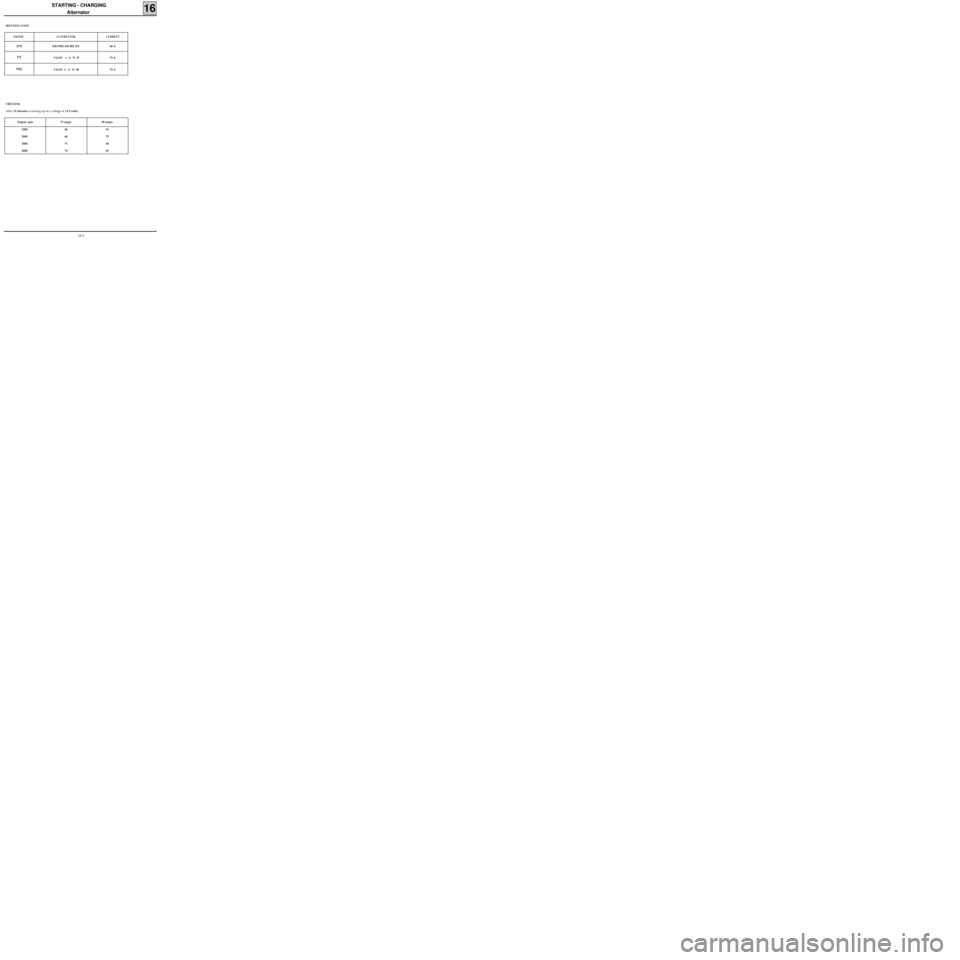
CHECKING
After 15 minutes warming up at a voltage of 13.5 volts.
STARTING - CHARGING
Alternator
16
IDENTIFICATION
ENGINE ALTERNATOR CURRENT
D7F DELPHI 104 802 215 80 A
E7J
VALEO A 11 VI 8775 A
F8Q
VALEO A 11 VI 8875 A
Engine rpm 75 amps 80 amps
1000
2000
3000
400046
68
71
7254
75
80
82
16-1
Page 141 of 208
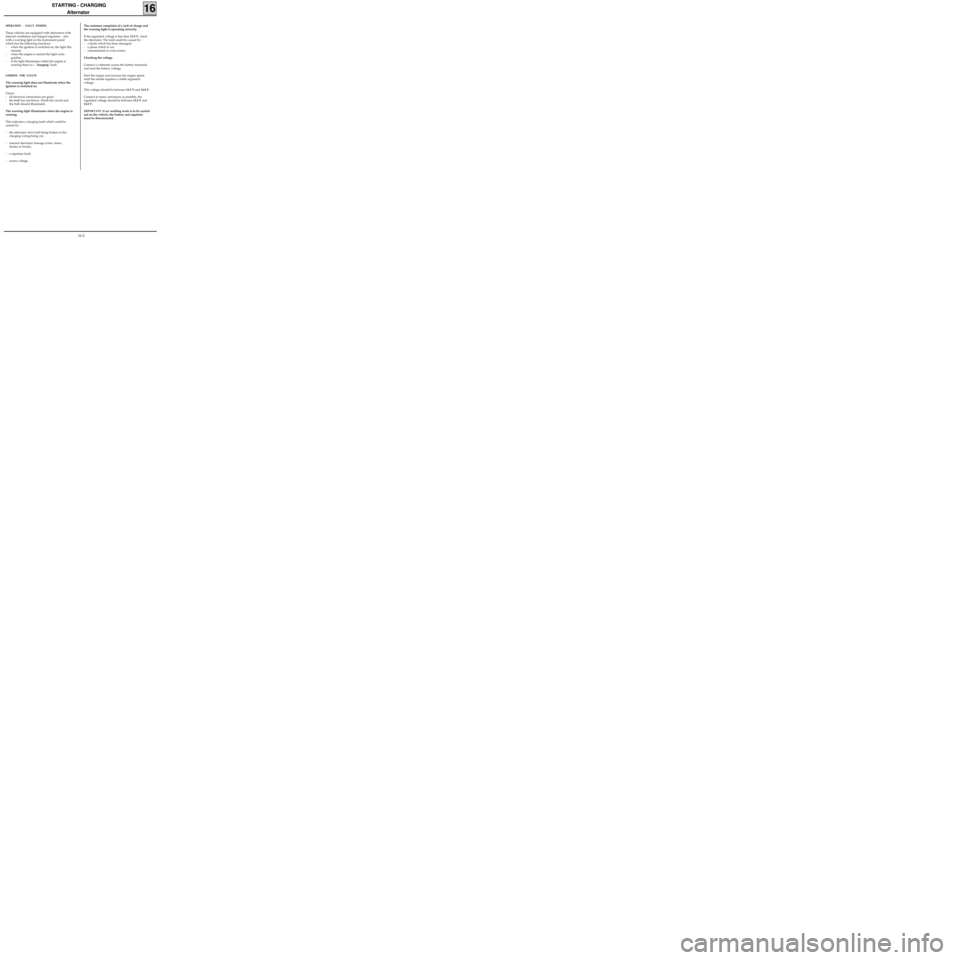
STARTING - CHARGING
Alternator
16
OPERATION - FAULT FINDING
These vehicles are equipped with alternators with
internal ventilation and integral regulator, also
with a warning light on the instrument panel
which has the following functions :
- when the ignition is switched on, the light illu-
minates
- when the engine is started the light extin-
guishes,
- if the light illuminates whilst the engine is
running there is a "charging "fault.
LOOKING FOR FAULTS
The warning light does not illuminate when the
ignition is switched on.
Check:
- all electrical connections are good.
- the bulb has not blown. (Earth the circuit and
the bulb should illuminate).
The warning light illuminates when the engine is
running.
This indicates a charging fault which could be
caused by :
- the alternator drive belt being broken or the
charging wiring being cut,
- internal alternator damage (rotor, stator,
diodes or brush),
- a regulator fault,
- excess voltage.The customer complains of a lack of charge and
the warning light is operating correctly.
If the regulated voltage is less than 13.5 V, check
the alternator. The fault could be caused by :
- a diode which has been damaged,
- a phase which is cut,
- contaminated or worn tracks.
Checking the voltage
Connect a voltmeter across the battery terminals
and read the battery voltage.
Start the engine and increase the engine speed
until the needle registers a stable regulated
voltage.
This voltage should be between 13.5 V and 14.8 V.
Connect as many consumers as possible, the
regulated voltage should be between 13.5 V and
14.8 V.
IMPORTANT: if arc welding work is to be carried
out on the vehicle, the battery and regulator
must be disconnected.
16-2
Page 142 of 208
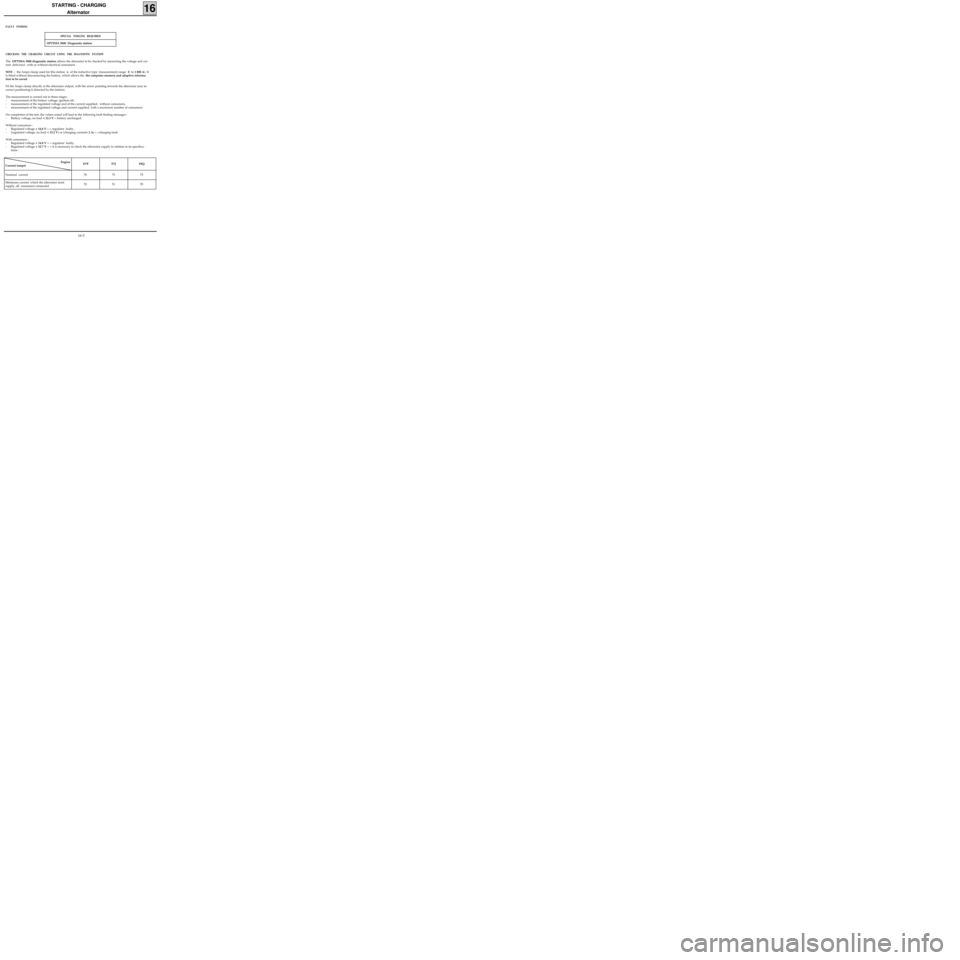
STARTING - CHARGING
Alternator
16
OPTIMA 5800 Diagnostic station
CHECKING THE CHARGING CIRCUIT USING THE DIAGNOSTIC STATION
The OPTIMA 5800 diagnostic station allows the alternator to be checked by measuring the voltage and cur-
rent delivered , with or without electrical consumers .
NOTE : the Amps clamp used for this station is of the inductive type (measurement range: 0 to 1 000 A). It
is fitted without disconnecting the battery, which allows the the computer memory and adaptive informa-
tion to be saved.
Fit the Amps clamp directly at the alternator output, with the arrow pointing towards the alternator (any in-
correct positioning is detected by the station).
The measurement is carried out in three stages :
- measurement of the battery voltage, ignition off,
- measurement of the regulated voltage and of the current supplied, without consumers,
- measurement of the regulated voltage and current supplied, with a maximum number of consumers.
On completion of the test, the values noted will lead to the following fault finding messages :
- Battery voltage, no load < 12.3 V = battery uncharged.
Without consumers :
- Regulated voltage > 14,8 V = > regulator faulty ,
- (regulated voltage, no load < 13.2 V) or (charging current< 2 A) = >charging fault.
With consumers :
- Regulated voltage > 14.8 V = > regulator faulty,
- Regulated voltage < 12.7 V = > it is necessary to check the alternator supply in relation to its specifica-
tions :
Engine
Current (amps)D7F E7J F8Q
Nominal current 70 75 75
Minimum current which the alternator must
supply, all consumers connected 53 51 55
FAULT FINDING
SPECIAL TOOLING REQUIRED
16-3
Page 143 of 208
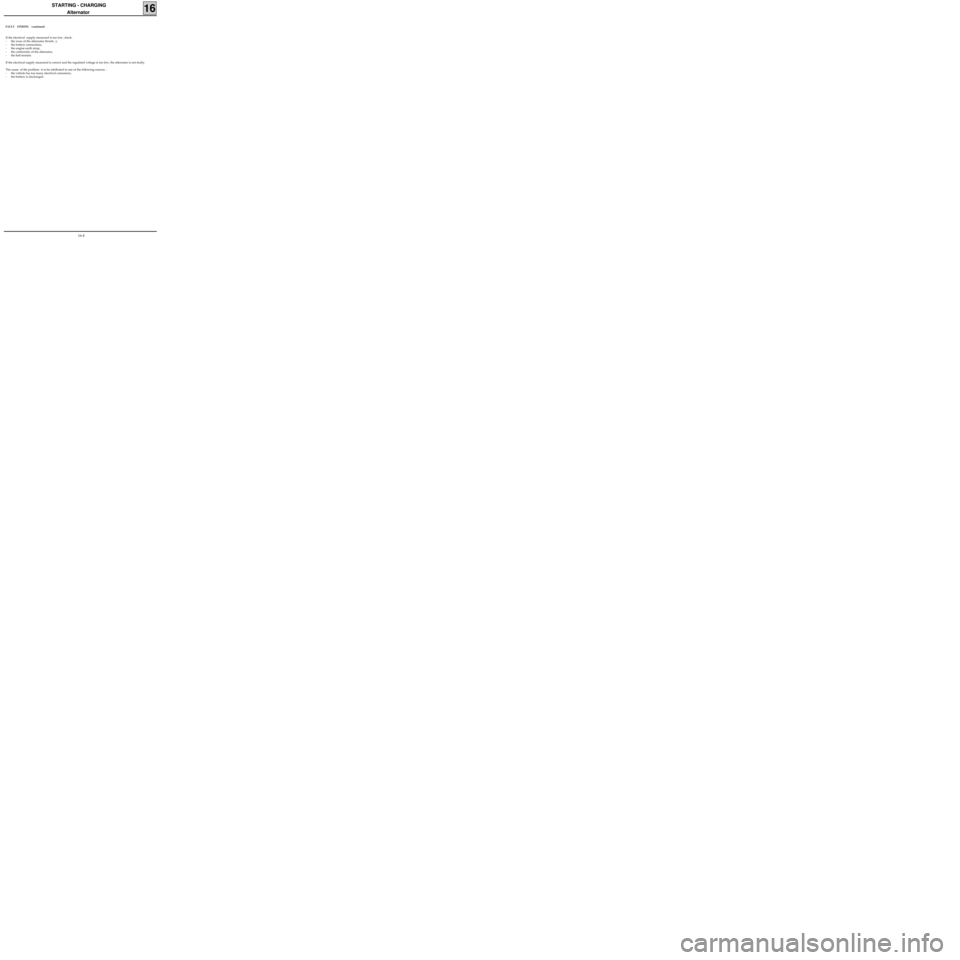
STARTING - CHARGING
Alternator
16
If the electrical supply measured is too low, check:
- the wear of the alternator (brush...),
- the battery connections,
- the engine earth strap,
- the conformity of the alternator,
- the belt tension.
If the electrical supply measured is correct and the regulated voltage is too low, the alternator is not faulty.
The cause of the problem is to be attributed to one of the following sources :
- the vehicle has too many electrical consumers,
- the battery is discharged.
FAULT FINDING (continued)
16-4
Page 144 of 208
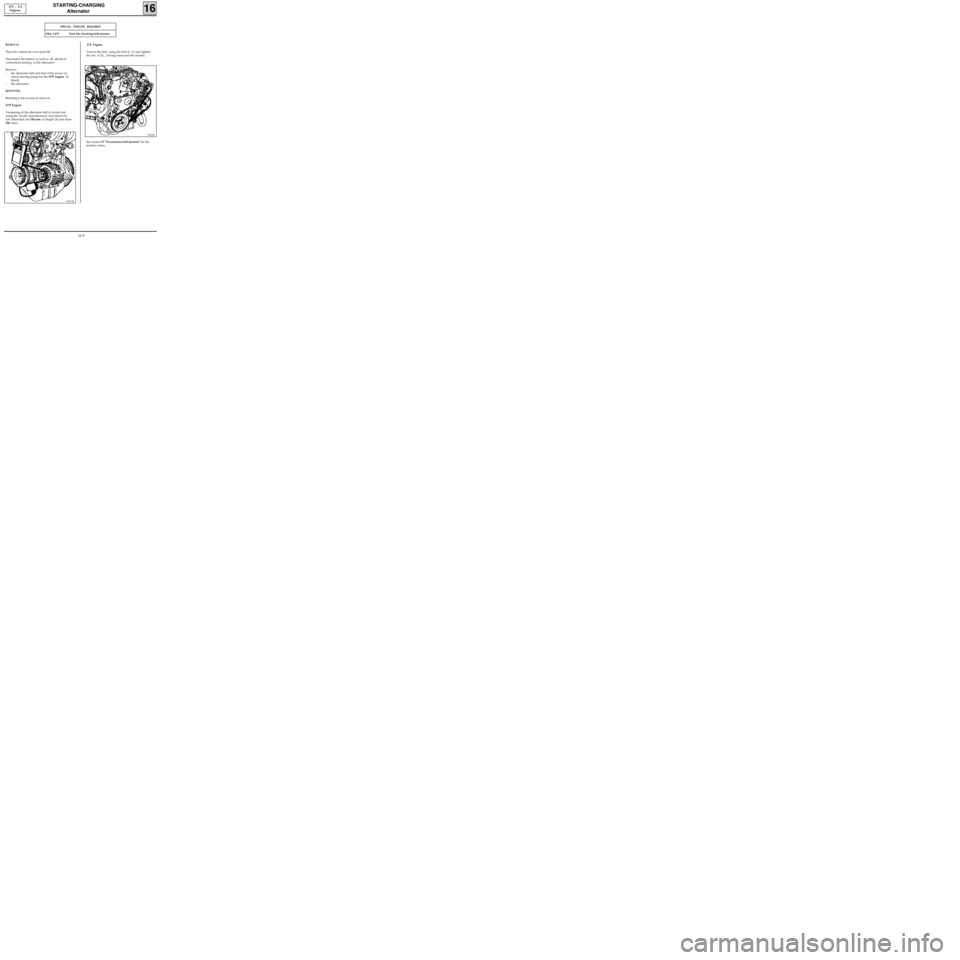
STARTING-CHARGING
Alternator
16
REMOVAL
Place the vehicle on a two post lift .
Disconnect the battery as well as all electrical
connections leading to the alternator.
Remove :
- the alternator belt and that of the power as-
sisted steering pump for the D7F engine (if
fitted),
- the alternator.
REFITTING
Refitting is the reverse of removal.
D7F Engine
Tensioning of the alternator belt is carried out
using the locally manufactured tool shown be-
low (threaded rod 100 mm in length (X) and three
M6 nuts).
D7F / E7J
Engines
SPECIAL TOOLING REQUIRED
Mot. 1273 Tool for checking belt tension
10617R
E7J Engine
Tension the belt using the bolt at (1) and tighten
the nut at (2) , having measured the tension.
13363R
See section 07 "Accessories belt tension" for the
tension values.
16-5