sensor RENAULT KANGOO 1997 KC / 1.G Engine And Peripherals Workshop Manual
[x] Cancel search | Manufacturer: RENAULT, Model Year: 1997, Model line: KANGOO, Model: RENAULT KANGOO 1997 KC / 1.GPages: 208
Page 3 of 208
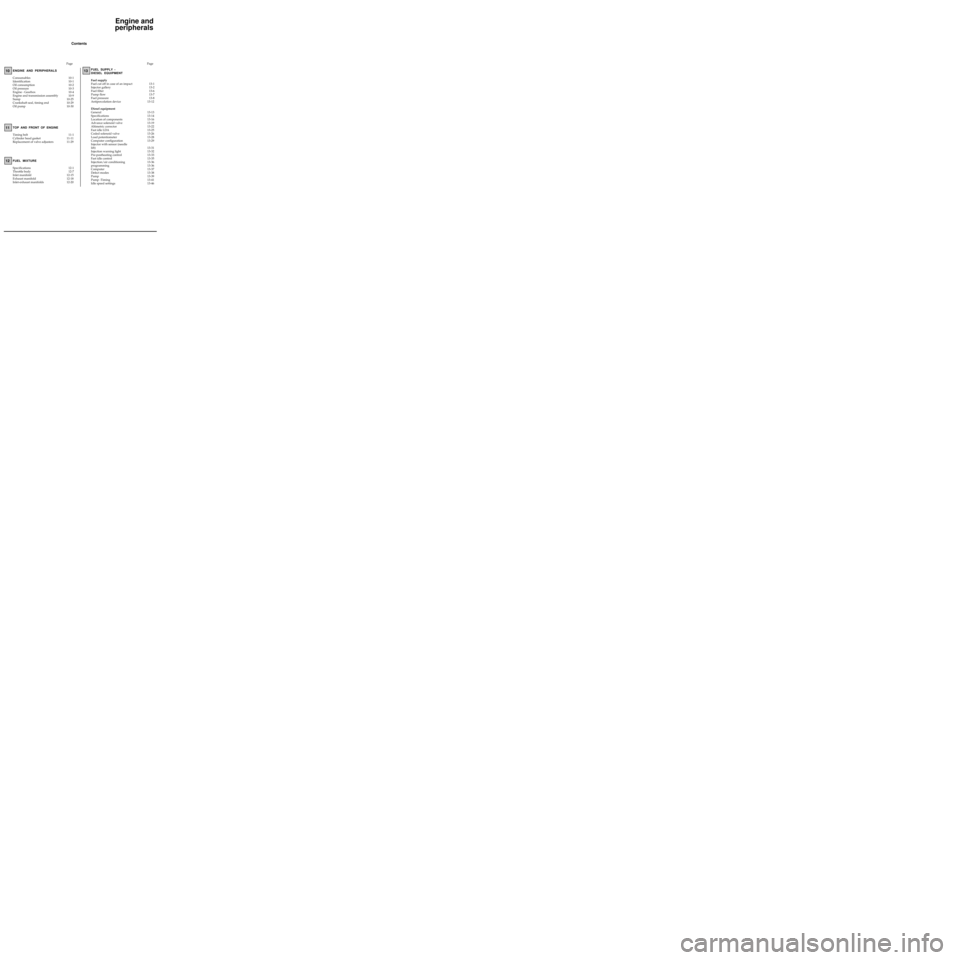
Contents
Consumables
Identification
Oil consumption
Oil pressure
Engine - Gearbox
Engine and transmission assembly
Sump
Crankshaft seal, timing end
Oil pump10-1
10-1
10-2
10-3
10-4
10-9
10-25
10-29
10-30
TOP AND FRONT OF ENGINE
Timing belt
Cylinder head gasket
Replacement of valve adjustersPage Page
11
Engine and
peripherals
11-1
11-11
11-29 ENGINE AND PERIPHERALS
10FUEL SUPPLY -
DIESEL EQUIPMENT
Fuel supply
Fuel cut off in case of an impact
Injector gallery
Fuel filter
Pump flow
Fuel pressure
Antipercolation device
Diesel equipment
General
Specifications
Location of components
Advance solenoid valve
Altimetric corrector
Fast idle LDA
Coded solenoid valve
Load potentiometer
Computer configuration
Injector with sensor (needle
lift)
Injection warning light
Pre-postheating control
Fast idle control
Injection/air conditioning
programming
Computer
Defect modes
Pump
Pump -Timing
Idle speed settings13-1
13-2
13-6
13-7
13-8
13-12
13-13
13-14
13-16
13-19
13-22
13-25
13-26
13-28
13-29
13-31
13-32
13-33
13-35
13-36
13-36
13-37
13-38
13-39
13-41
13-4613
FUEL MIXTURE
Specifications
Throttle body
Inlet manifold
Exhaust manifold
Inlet-exhaust manifolds12-1
12-7
12-15
12-18
12-2012
Page 10 of 208
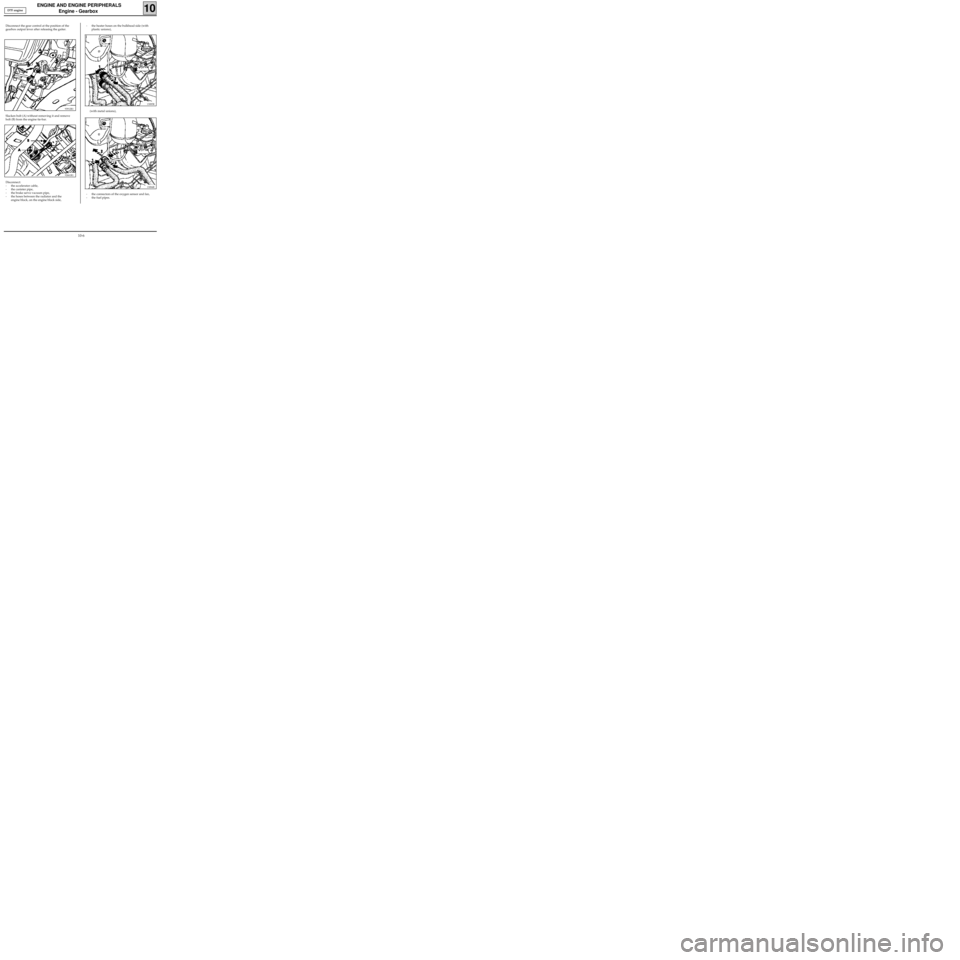
ENGINE AND ENGINE PERIPHERALS
Engine - Gearbox
- the heater hoses on the bulkhead side (with
plastic unions),
10
Disconnect the gear control at the position of the
gearbox output lever after releasing the gaiter.
93912R1
Slacken bolt (A) without removing it and remove
bolt (B) from the engine tie-bar.
92661R1
Disconnect:
- the accelerator cable,
- the canister pipe,
- the brake servo vacuum pipe,
- the hoses between the radiator and the
engine block, on the engine block side,
13085R
(with metal unions),
13084R
- the connectors of the oxygen sensor and fan,
- the fuel pipes. D7F engine
10-6
Page 14 of 208
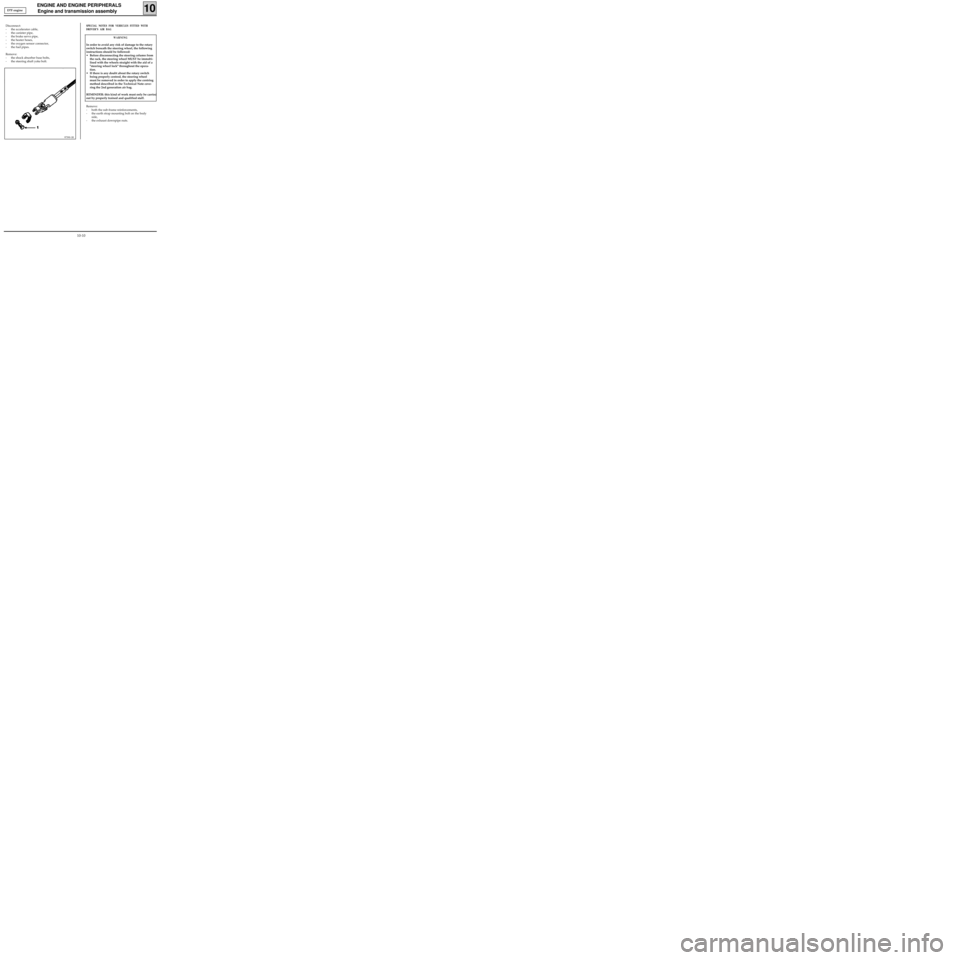
ENGINE AND ENGINE PERIPHERALS
Engine and transmission assembly
Disconnect:
- the accelerator cable,
- the canister pipe,
- the brake servo pipe,
- the heater hoses,
- the oxygen sensor connector,
- the fuel pipes.
Remove:
- the shock absorber base bolts,
- the steering shaft yoke bolt.
10
97390-1R
SPECIAL NOTES FOR VEHICLES FITTED WITH
DRIVER’S AIR BAG
WARNING
In order to avoid any risk of damage to the rotary
switch beneath the steering wheel, the following
instructions should be followed:
• Before disconnecting the steering column from
the rack, the steering wheel MUST be immobi-
lised with the wheels straight with the aid of a
"steering wheel lock" throughout the opera-
tion.
• If there is any doubt about the rotary switch
being properly centred, the steering wheel
must be removed in order to apply the centring
method described in the Technical Note cove-
ring the 2nd generation air bag.
REMINDER: this kind of work must only be carried
out by properly trained and qualified staff.
Remove:
- both the sub-frame reinforcements,
- the earth strap mounting bolt on the body
side,
- the exhaust downpipe nuts. D7F engine
10-10
Page 29 of 208
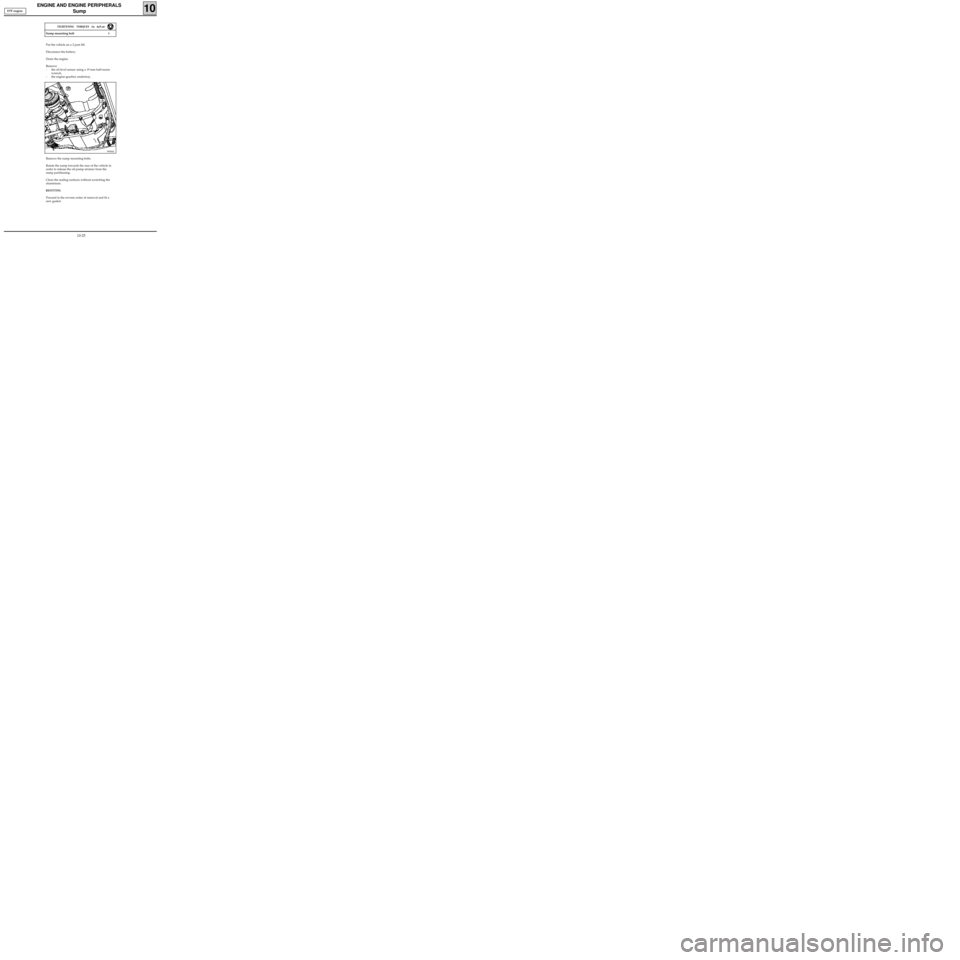
ENGINE AND ENGINE PERIPHERALS
Sump
10
Sump mounting bolt 1
TIGHTENING TORQUES (in daN.m)
Put the vehicle on a 2 post lift.
Disconnect the battery.
Drain the engine.
Remove:
- the oil level sensor using a 19 mm half-moon
wrench,
- the engine-gearbox undertray.
99900S
Remove the sump mounting bolts.
Rotate the sump towards the rear of the vehicle in
order to release the oil pump strainer from the
sump partitioning.
Clean the sealing surfaces without scratching the
aluminium.
REFITTING
Proceed in the reverse order of removal and fit a
new gasket. D7F engine
10-25
Page 34 of 208
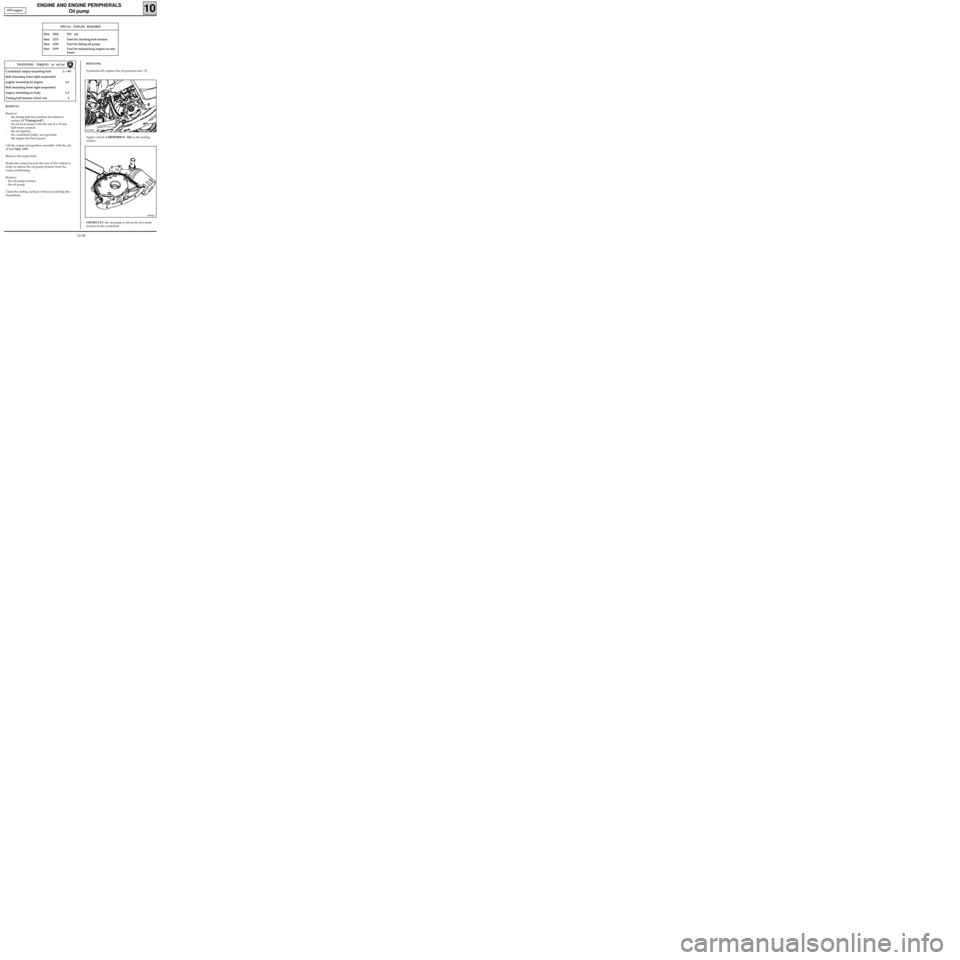
ENGINE AND ENGINE PERIPHERALS
Oil pump
10
Crankshaft output mounting bolt 2 + 90°
Bolt mounting front right suspended
engine mounting on engine 6.2
Bolt mounting front right suspended
engine mounting on body 6.2
Timing belt tension wheel nut 5
TIGHTENING TORQUES (in daN.m)
REMOVAL
Remove:
- the timing belt (see method described in
section 11 "Timing belt"),
- the oil level sensor with the aid of a 19 mm
half-moon wrench,
- the oil dipstick,
- the crankshaft pulley and sprocket,
- the engine flywheel guard.
Lift the engine and gearbox assembly with the aid
of tool Mot. 1379.
Remove the sump bolts.
Rotate the sump towards the rear of the vehicle in
order to release the oil pump strainer from the
sump partitioning.
Remove:
- the oil pump strainer
- the oil pump
Clean the sealing surfaces without scratching the
aluminium.
SPECIAL TOOLING REQUIRED
Mot. 1054TDC pin
Mot. 1273 Tool for checking belt tension
Mot. 1355 Tool for fitting oil pump
Mot. 1379 Tool for maintaining engine on sub-
frame
REFITTING
Systematically replace the oil pressure seal (3).
99790R
Apply a bead of RHODORSEAL 5661 to the sealing
surface.
98964S
IMPORTANT: the oil pump is driven by two studs
located on the crankshaft. D7F engine
10-30
Page 38 of 208
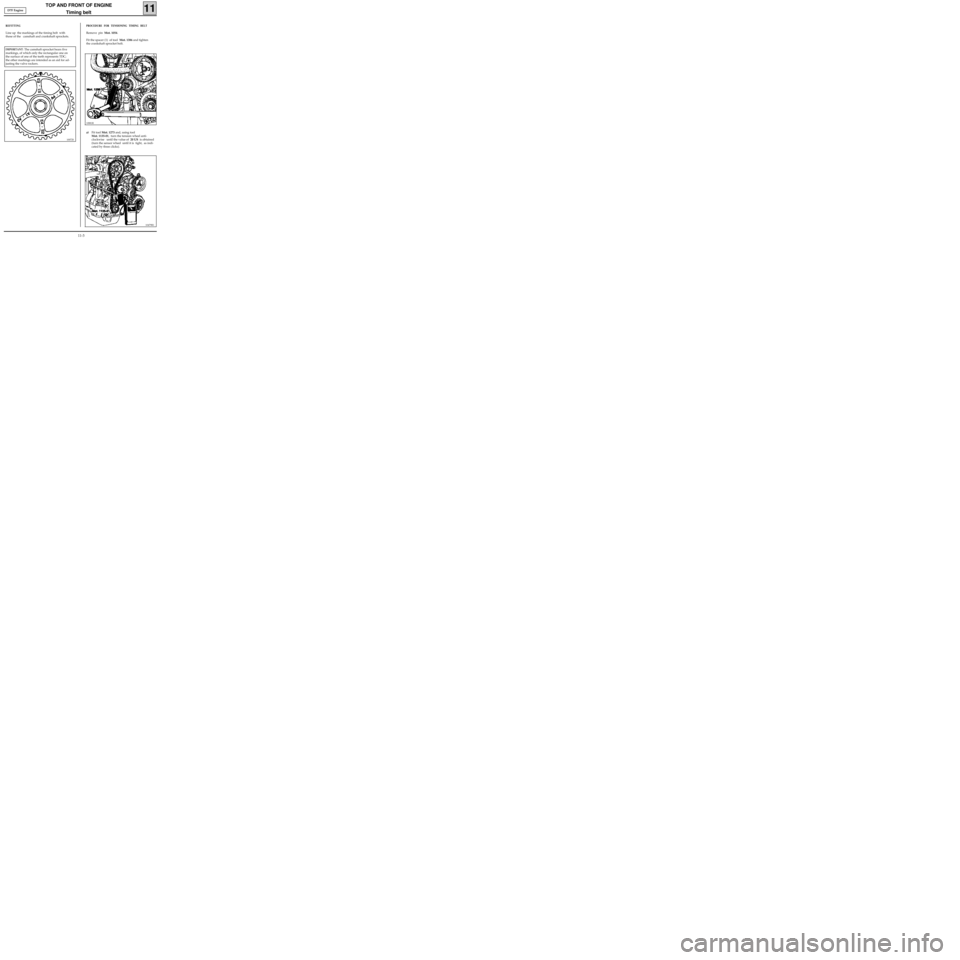
TOP AND FRONT OF ENGINE
Timing belt
11
REFITTING
Line up the markings of the timing belt with
those of the camshaft and crankshaft sprockets.
10072S
PROCEDURE FOR TENSIONING TIMING BELT
Remove pin Mot. 1054.
Fit the spacer (1) of tool Mot. 1386 and tighten
the crankshaft sprocket bolt.
10881R
a)Fit tool Mot. 1273 and, using tool
Mot. 1135-01, turn the tension wheel anti-
clockwise until the value of 20 US is obtained
(turn the sensor wheel until it is tight, as indi-
cated by three clicks).
10479R1
IMPORTANT: The camshaft sprocket bears five
markings, of which only the rectangular one on
the surface of one of the teeth represents TDC;
the other markings are intended as an aid for ad-
justing the valve rockers.
D7F Engine
11-3
Page 47 of 208
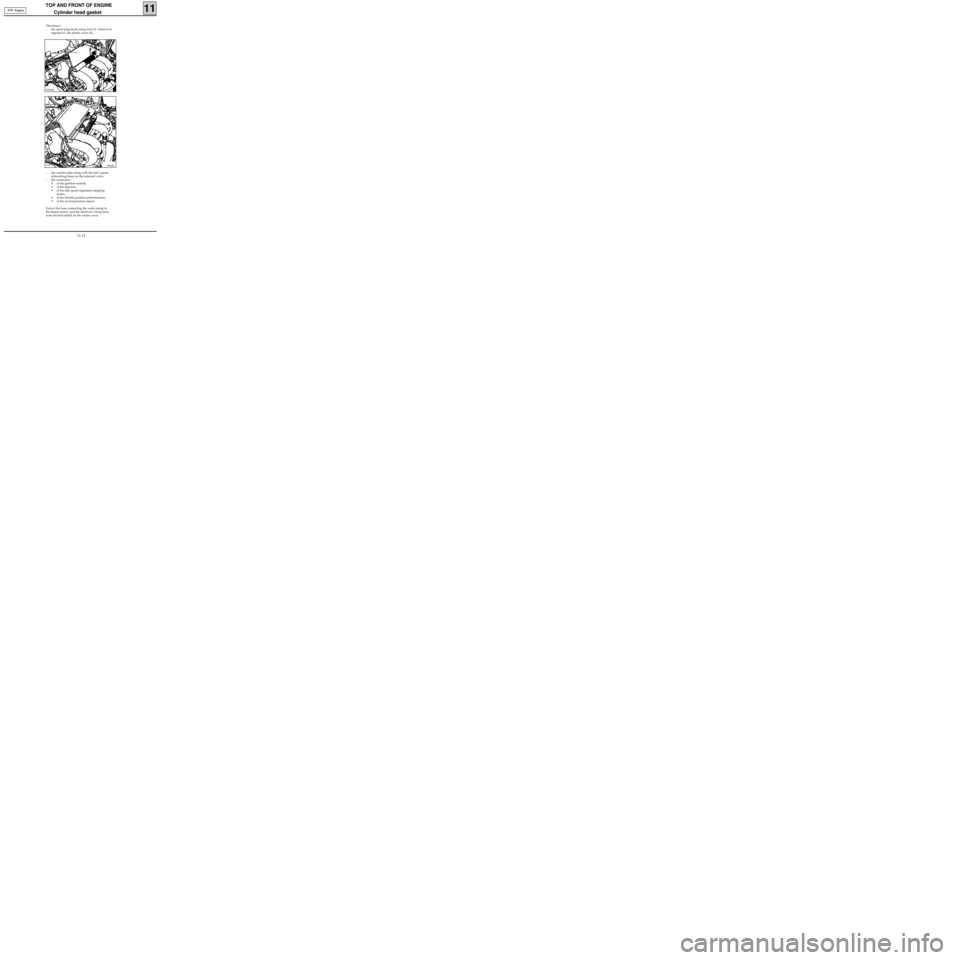
TOP AND FRONT OF ENGINE
Cylinder head gasket
11
- the canister pipe along with the fuel vapour
rebreathing hoses on the solenoid valve,
- the connectors :
• of the ignition module,
• of the injectors,
• of the idle speed regulation stepping
motor,
• of the throttle position potentiometer,
• of the air temperature sensor.
Extract the hose connecting the water pump to
the heater matrix, and the electrical wiring loom
from the heat shield on the rocker cover.
99940R
Disconnect :
- the spark plug leads using tool (3) which is in-
tegrated to the plastic cover (4),
99894R1
D7F Engine
11-12
Page 53 of 208
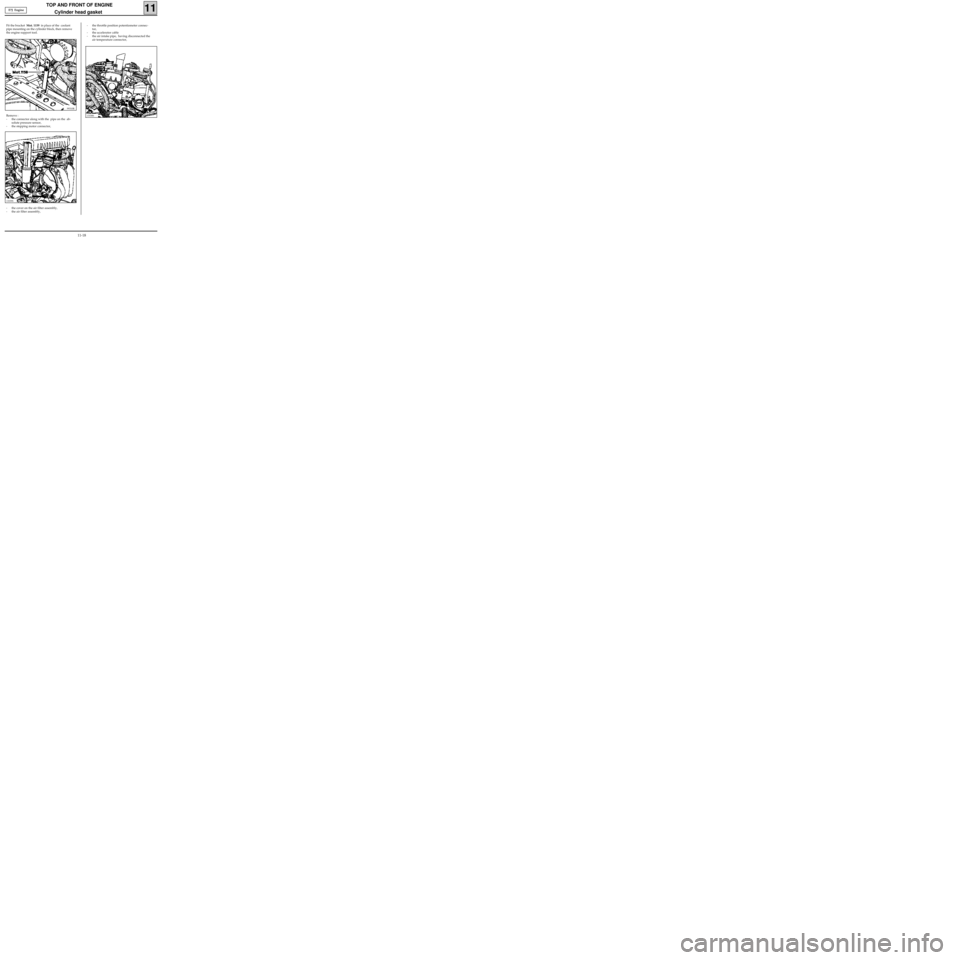
TOP AND FRONT OF ENGINE
Cylinder head gasket
11
13339S
- the cover on the air filter assembly,
- the air filter assembly,
13338S
99310R
Remove :
- the connector along with the pipe on the ab-
solute pressure sensor,
- the stepping motor connector, Fit the bracket Mot. 1159 in place of the coolant
pipe mounting on the cylinder block, then remove
the engine support tool.- the throttle position potentiometer connec-
tor,
- the accelerator cable
- the air intake pipe, having disconnected the
air temperature connector, E7J Engine
11-18
Page 59 of 208
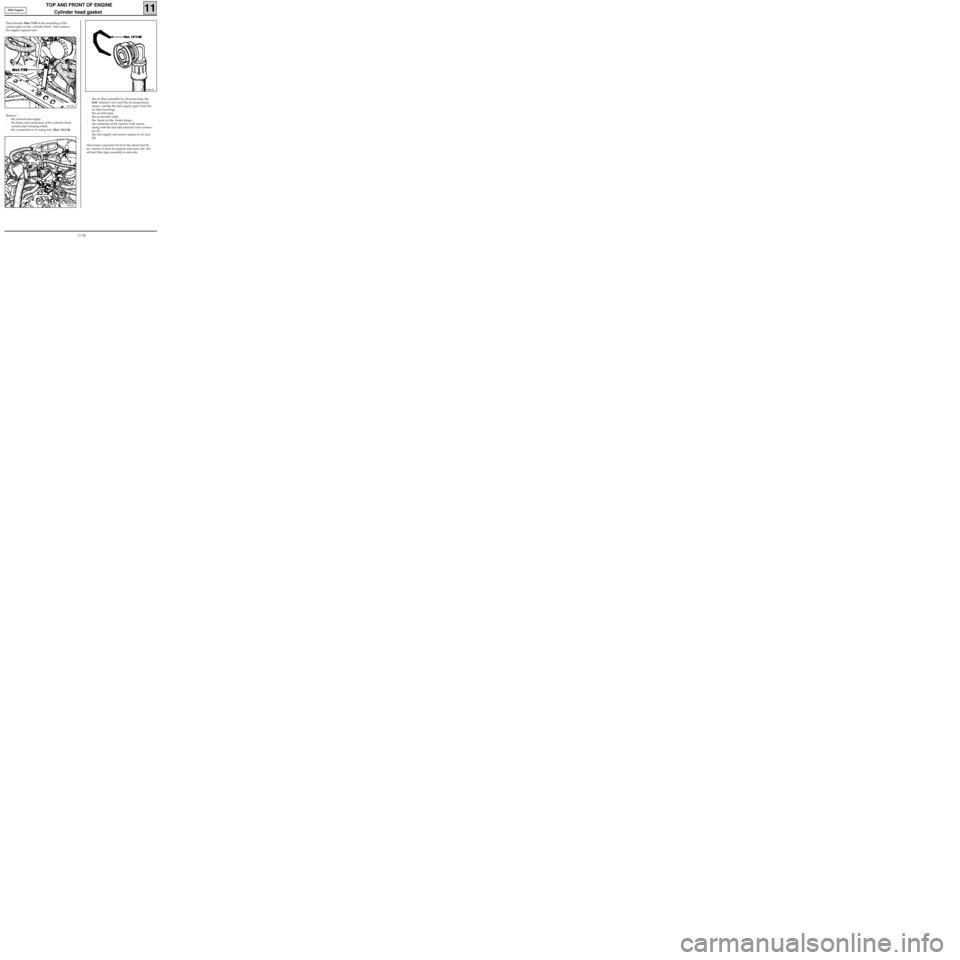
TOP AND FRONT OF ENGINE
Cylinder head gasket
11
Remove :
- the exhaust downpipe,
- the hoses and connectors of the cylinder head
coolant pipe housing outlet,
- the connection at (1) using tool Mot. 1311-06,
13097R
99461R
- the air filter assembly by disconnecting the
EGR solenoid valve and the air temperature
sensor (unclip the fuel supply pipes from the
air filter housing),
- the air inlet pipe
- the accelerator cable
- the feeds for the heater plugs ,
- the connector of the injector with sensor,
along with the fast idle solenoid valve connec-
tor (5),
- the fuel supply and return unions at (A) and
(B).
Disconnect connector (6) from the diesel fuel fil-
ter, remove it from its support and move the die-
sel fuel filter pipe assembly to one side. Place bracket Mot. 1159 at the mounting of the
coolant pipe on the cylinder block, then remove
the engine support tool.
99310R
F8Q Engine
11-24
Page 66 of 208
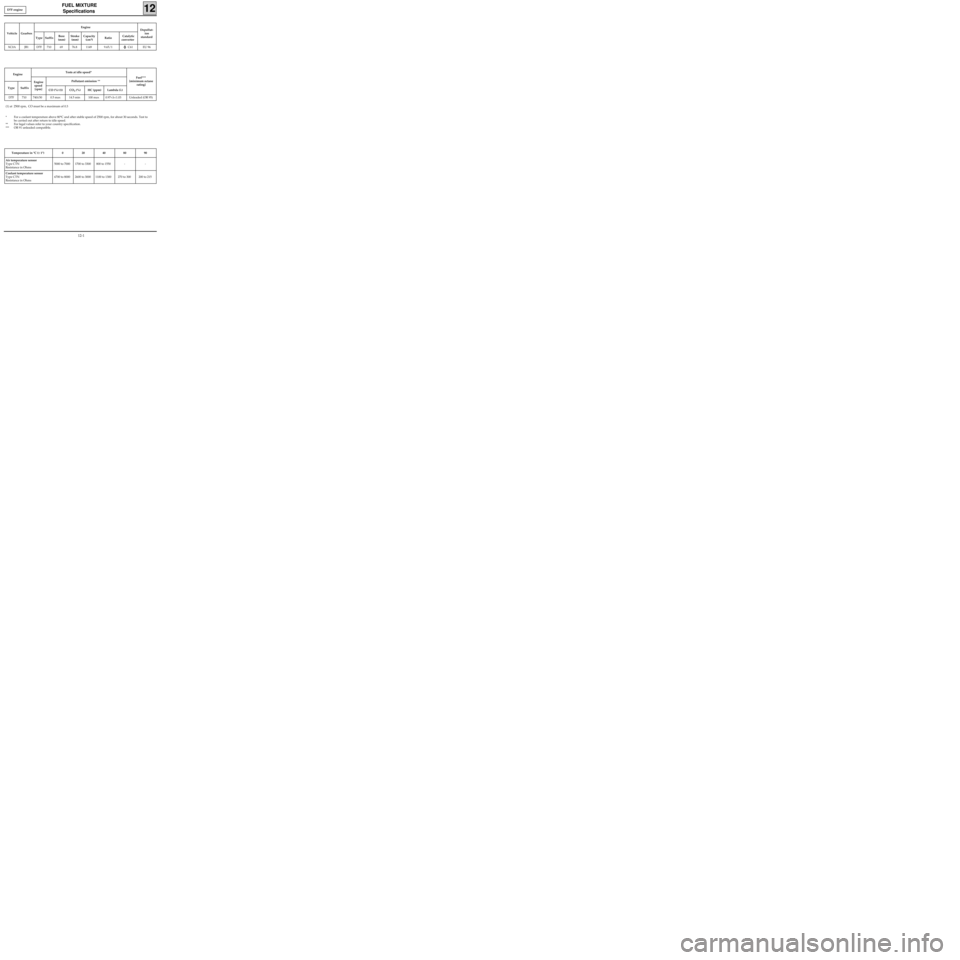
FUEL MIXTURE
Specifications
12
Vehicle GearboxEngine
Type SuffixBore
(mm)Stroke
(mm)Capacity
(cm
3)RatioCatalytic
converterDepollut-
ion
standard
XC0A JB1 D7F 710 69 76.8 1149 9.65/1 C61 EU 96
Temperature in °C (± 1°) 0 20 40 80 90
Air temperature sensor
Type CTN
Resistance in Ohms5000 to 7000 1700 to 3300 800 to 1550 - -
Coolant temperature sensor
Type CTN
Resistance in Ohms6700 to 8000 2600 to 3000 1100 to 1300 270 to 300 200 to 215
Engine
Type SuffixTests at idle speed*
Engine
speed
[rpm]Pollutant emission **
CO (%) (1) CO
2 (%) HC (ppm) Lambda (λ)Fuel***
[minimum octane
rating]
D7F 710 740±50 0.5 max 14.5 min 100 max 0.97<λ<1.03 Unleaded (OR 95)
(1) at 2500 rpm, CO must be a maximum of 0.3
* For a coolant temperature above 80°C and after stable speed of 2500 rpm, for about 30 seconds. Test to
be carried out after return to idle speed.
** For legal values refer to your country specification.
*** OR 91 unleaded compatible.D7F engine
12-1