sensor SSANGYONG MUSSO 2003 Manual PDF
[x] Cancel search | Manufacturer: SSANGYONG, Model Year: 2003, Model line: MUSSO, Model: SSANGYONG MUSSO 2003Pages: 1574, PDF Size: 26.41 MB
Page 675 of 1574
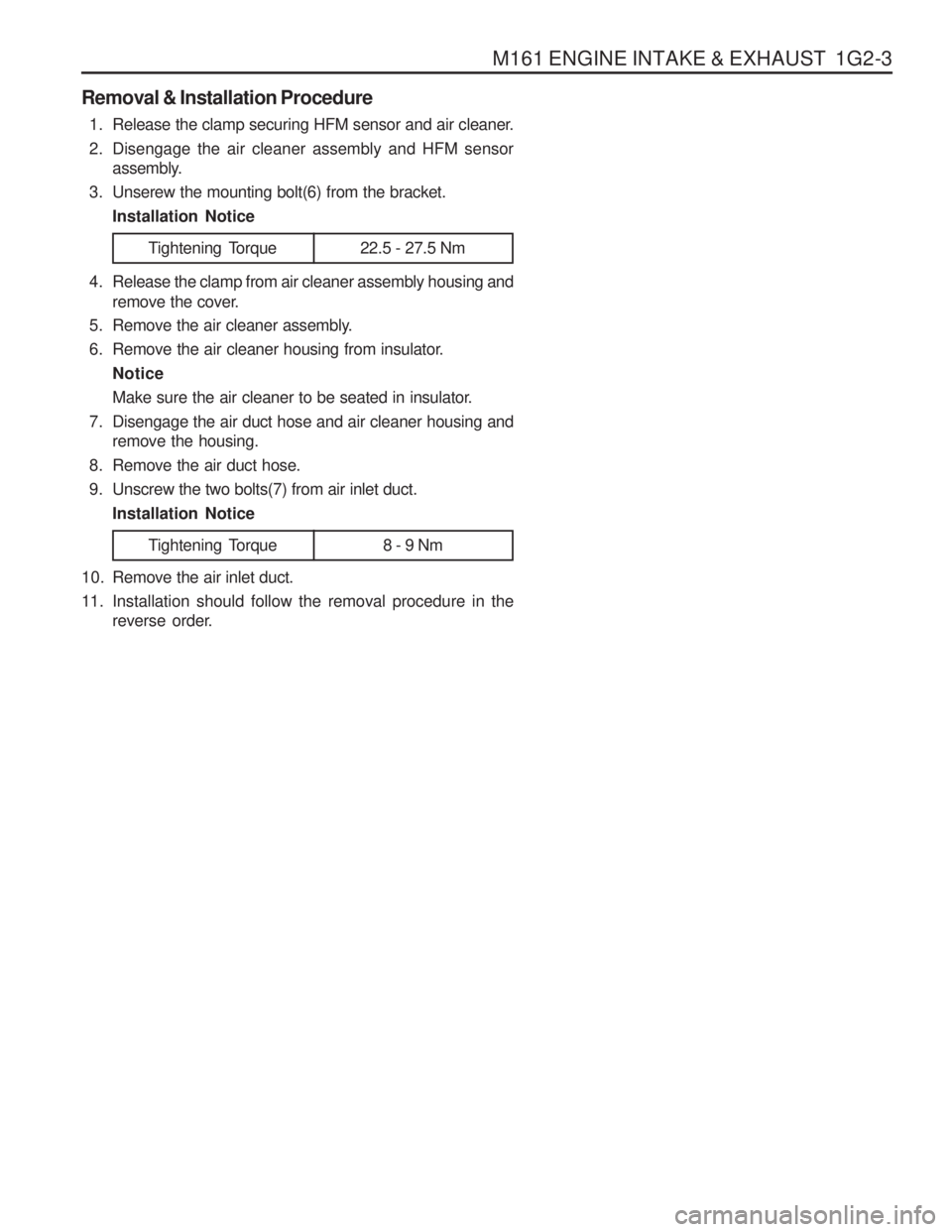
M161 ENGINE INTAKE & EXHAUST 1G2-3
Removal & Installation Procedure1. Release the clamp securing HFM sensor and air cleaner.
2. Disengage the air cleaner assembly and HFM sensor assembly.
3. Unserew the mounting bolt(6) from the bracket.
Installation Notice
Tightening Torque 22.5 - 27.5 Nm
4. Release the clamp from air cleaner assembly housing and remove the cover.
5. Remove the air cleaner assembly.
6. Remove the air cleaner housing from insulator.
Notice
Make sure the air cleaner to be seated in insulator.
7. Disengage the air duct hose and air cleaner housing and remove the housing.
8. Remove the air duct hose.
9. Unscrew the two bolts(7) from air inlet duct. Installation Notice
10. Remove the air inlet duct.
11. Installation should follow the removal procedure in the reverse order.
Tightening Torque 8 - 9 Nm
Page 677 of 1574
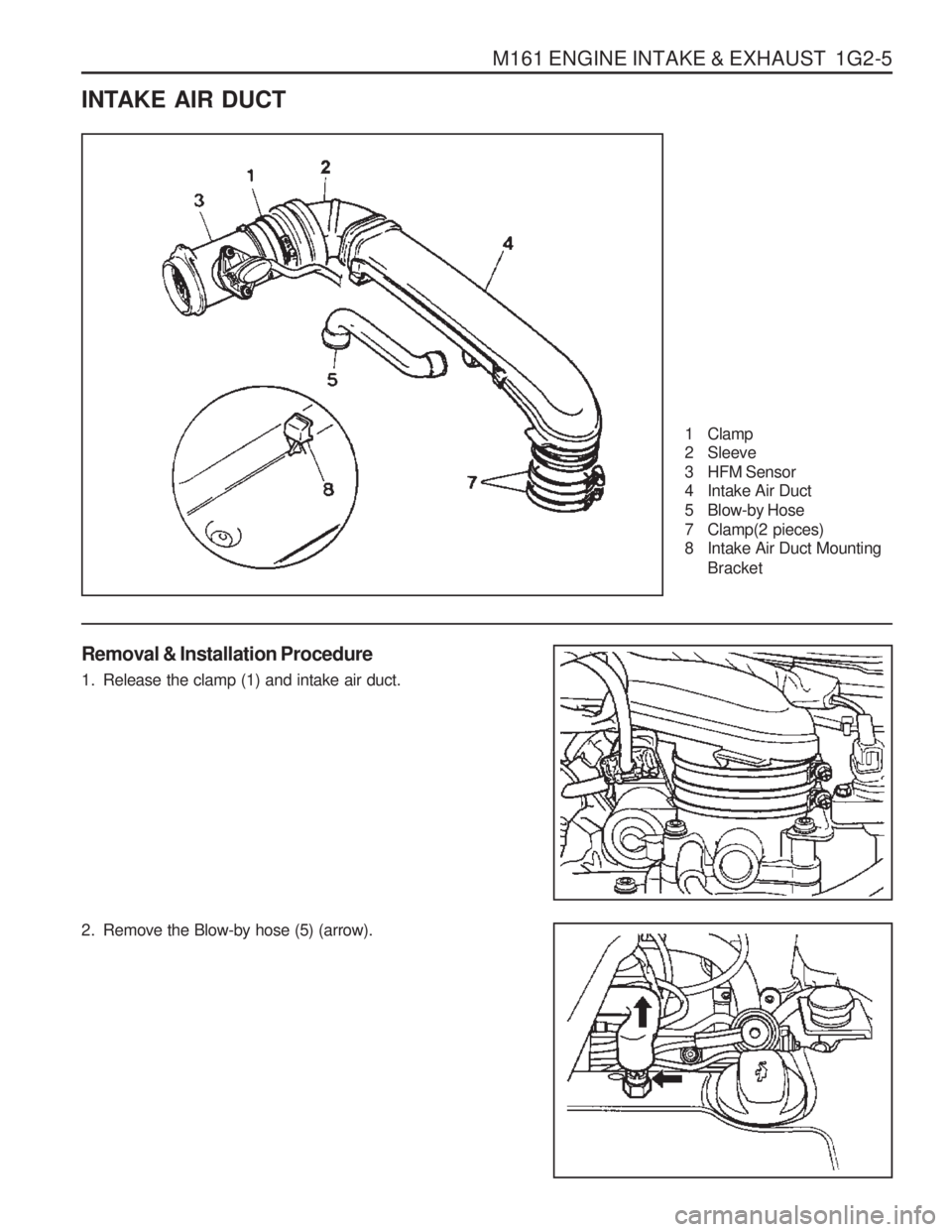
M161 ENGINE INTAKE & EXHAUST 1G2-5
INTAKE AIR DUCT
1 Clamp
2 Sleeve
3 HFM Sensor
4 Intake Air Duct
5 Blow-by Hose
7 Clamp(2 pieces)
8 Intake Air Duct MountingBracket
Removal & Installation Procedure
1. Release the clamp (1) and intake air duct.
2. Remove the Blow-by hose (5) (arrow).
Page 681 of 1574
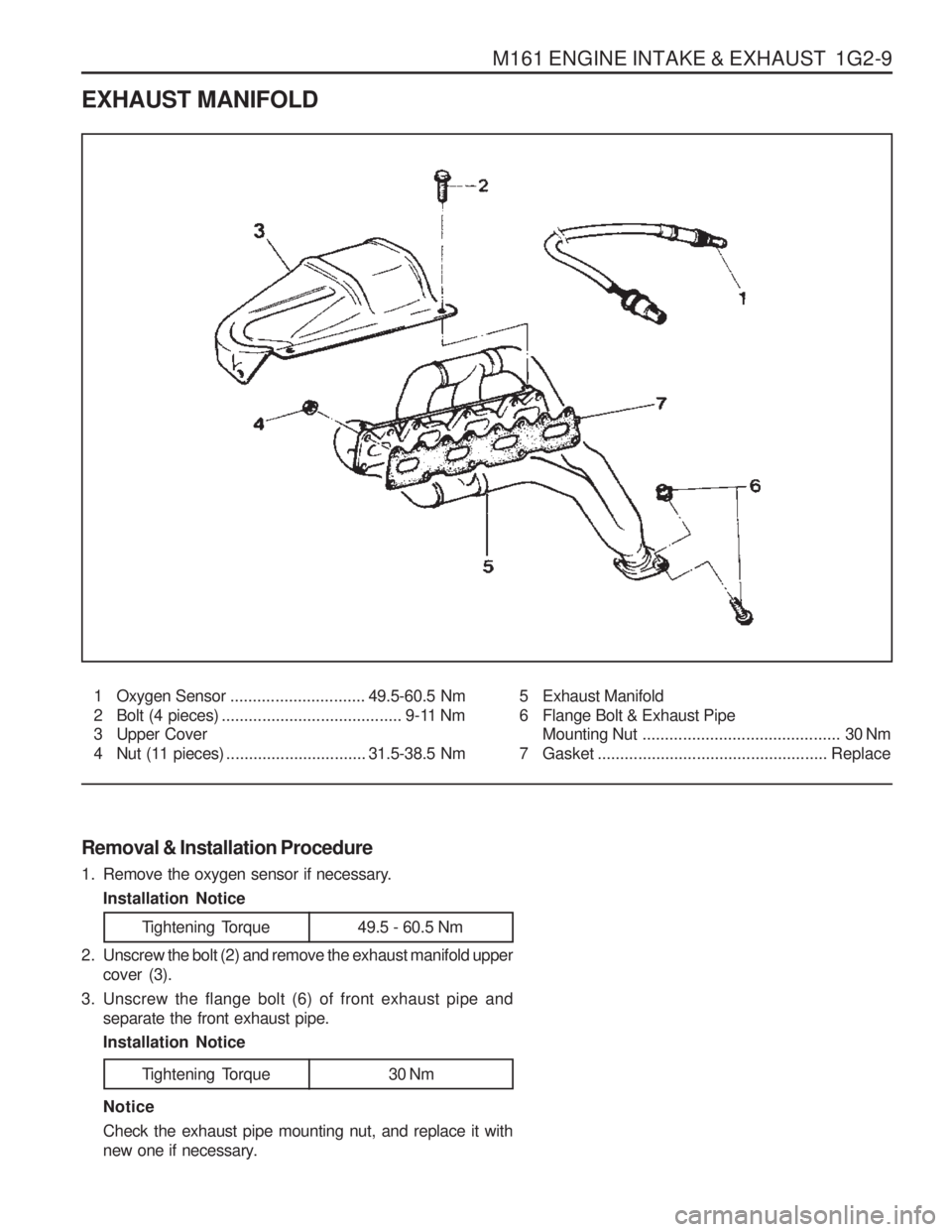
M161 ENGINE INTAKE & EXHAUST 1G2-9
EXHAUST MANIFOLD
1 Oxygen Sensor.............................. 49.5-60.5 Nm
2 Bolt (4 pieces) ........................................ 9-11 Nm
3 Upper Cover
4 Nut (11 pieces) ............................... 31.5-38.5 Nm 5 Exhaust Manifold
6 Flange Bolt & Exhaust Pipe
Mounting Nut ............................................ 30 Nm
7 Gasket ................................................... Replace
Removal & Installation Procedure
1. Remove the oxygen sensor if necessary. Installation Notice
Tightening Torque 49.5 - 60.5 Nm
2. Unscrew the bolt (2) and remove the exhaust manifold upper cover (3).
3. Unscrew the flange bolt (6) of front exhaust pipe and separate the front exhaust pipe. Installation Notice
Tightening Torque 30 Nm
Notice Check the exhaust pipe mounting nut, and replace it with
new one if necessary.
Page 690 of 1574
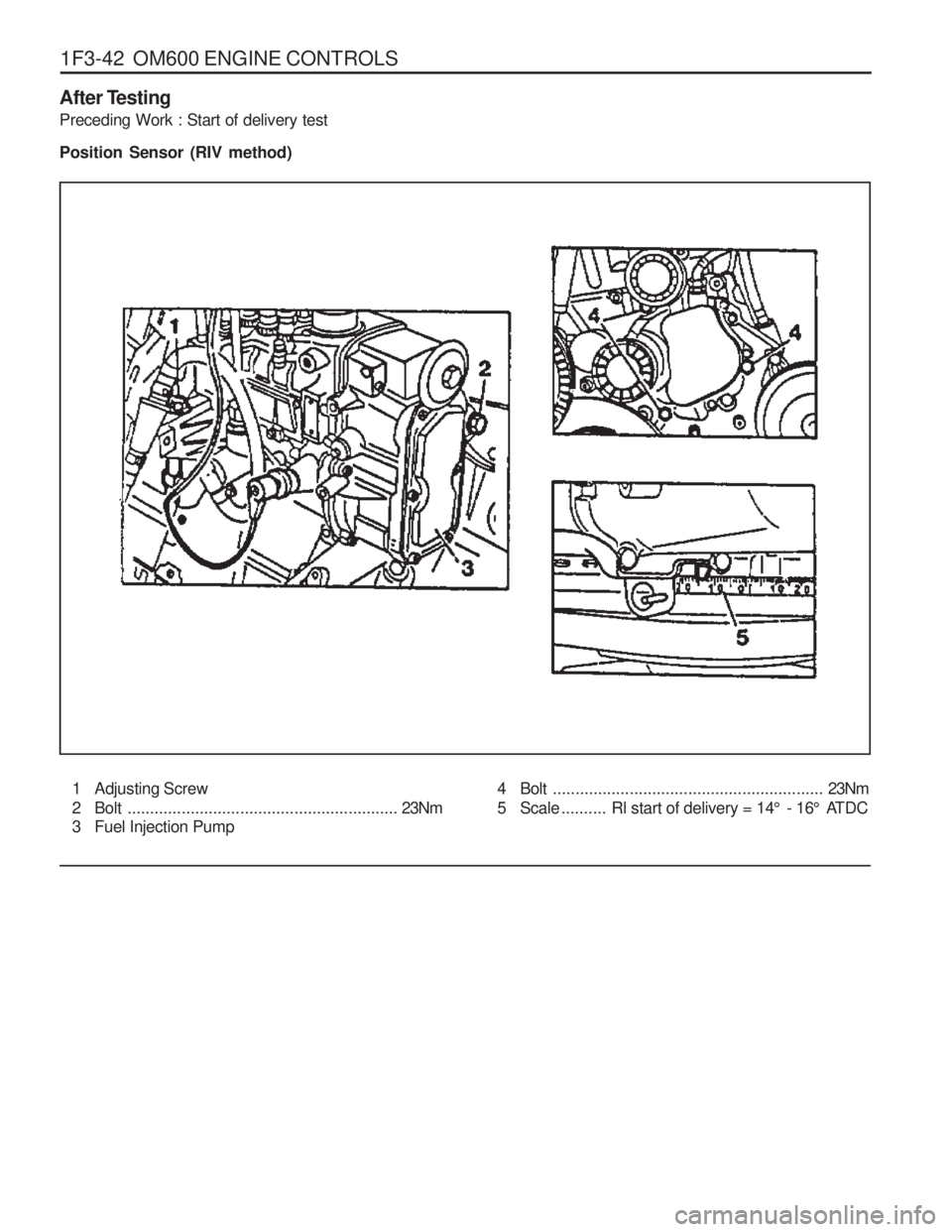
1F3-42 OM600 ENGINE CONTROLS
After Testing Preceding Work : Start of delivery test Position Sensor (RIV method)
1 Adjusting Screw
2 Bolt ............................................................ 23Nm
3 Fuel Injection Pump 4 Bolt
............................................................ 23Nm
5 Scale .......... Rl start of delivery = 14 ° - 16 ° ATDC
Page 699 of 1574
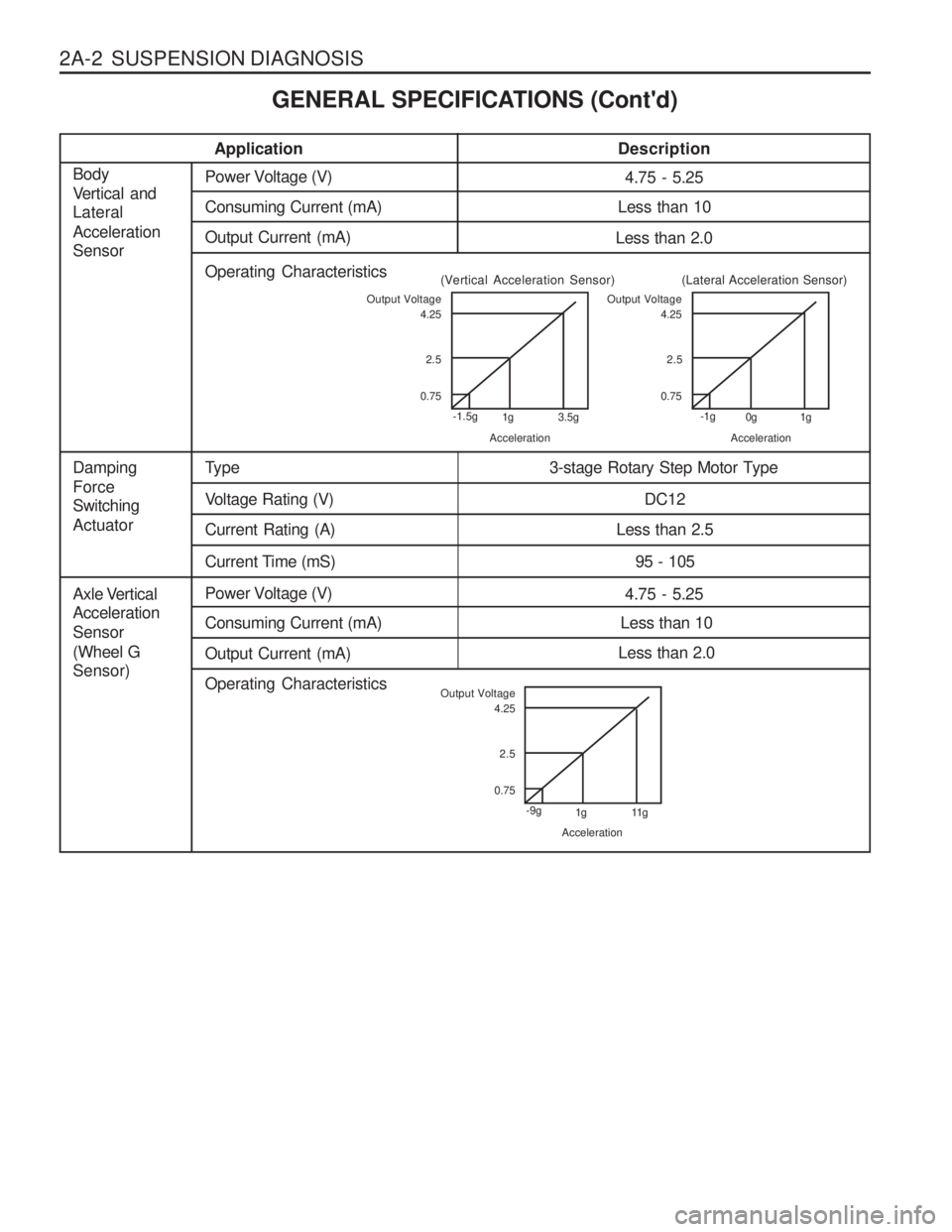
2A-2 SUSPENSION DIAGNOSISApplication
Description
4.75 - 5.25Power Voltage (V)
Axle Vertical Acceleration Sensor(Wheel G Sensor) Less than 10
Consuming Current (mA)
Less than 2.0
Output Current (mA)
Operating Characteristics
Type
Damping Force Switching Actuator3-stage Rotary Step Motor Type
Voltage Rating (V)
DC12
Current Rating (A)
Less than 2.5
Current Time (mS) 95 - 105
4.75 - 5.25Power Voltage (V)
Body
Vertical and Lateral Acceleration Sensor
Less than 10
Consuming Current (mA)
Less than 2.0
Output Current (mA)
Operating Characteristics
Output Voltage
0.752.5
4.25
-1.5g 1g 3.5g
Acceleration
(Vertical Acceleration Sensor)Output Voltage
0.752.5
4.25
-1g 0g 1g
Acceleration
(Lateral Acceleration Sensor)
Output Voltage
0.752.5
4.25
-9g 1g 11g
Acceleration
GENERAL SPECIFICATIONS (Cont'd)
Page 702 of 1574
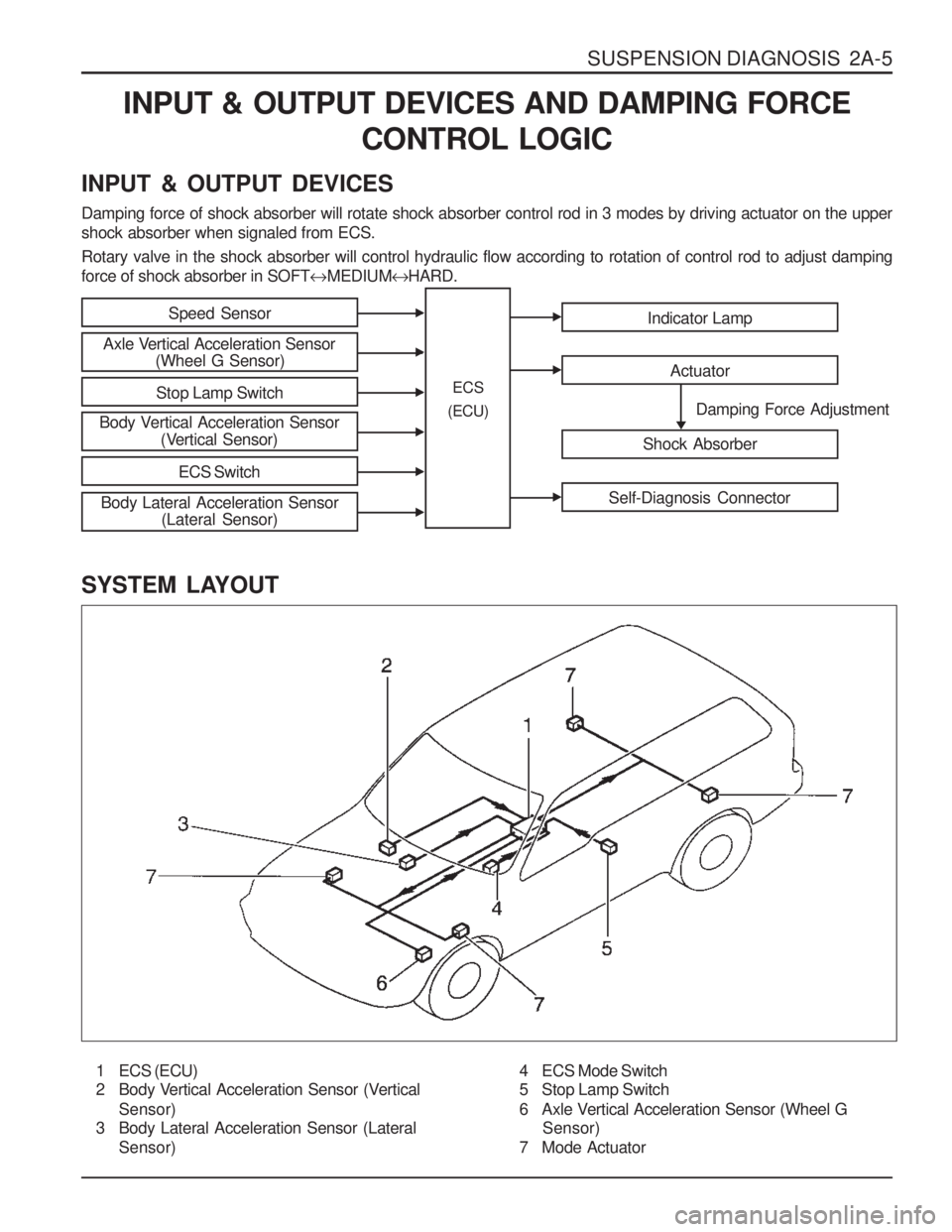
SUSPENSION DIAGNOSIS 2A-5
INPUT & OUTPUT DEVICES AND DAMPING FORCECONTROL LOGIC
INPUT & OUTPUT DEVICES Damping force of shock absorber will rotate shock absorber control rod in 3 modes by driving actuator on the upper shock absorber when signaled from ECS. Rotary valve in the shock absorber will control hydraulic flow according to rotation of control rod to adjust damping force of shock absorber in SOFT MEDIUM HARD.
SYSTEM LAYOUT
1 ECS (ECU)
2 Body Vertical Acceleration Sensor (Vertical Sensor)
3 Body Lateral Acceleration Sensor (Lateral
Sensor)
Speed Sensor
Axle Vertical Acceleration Sensor (Wheel G Sensor)
Stop Lamp Switch
Body Vertical Acceleration Sensor (Vertical Sensor)
ECS Switch
Indicator Lamp
Actuator
Shock Absorber
Self-Diagnosis Connector
Damping Force Adjustment
ECS
(ECU)
Body Lateral Acceleration Sensor (Lateral Sensor)
4 ECS Mode Switch
5 Stop Lamp Switch
6 Axle Vertical Acceleration Sensor (Wheel G
Sensor)
7 Mode Actuator
Page 703 of 1574
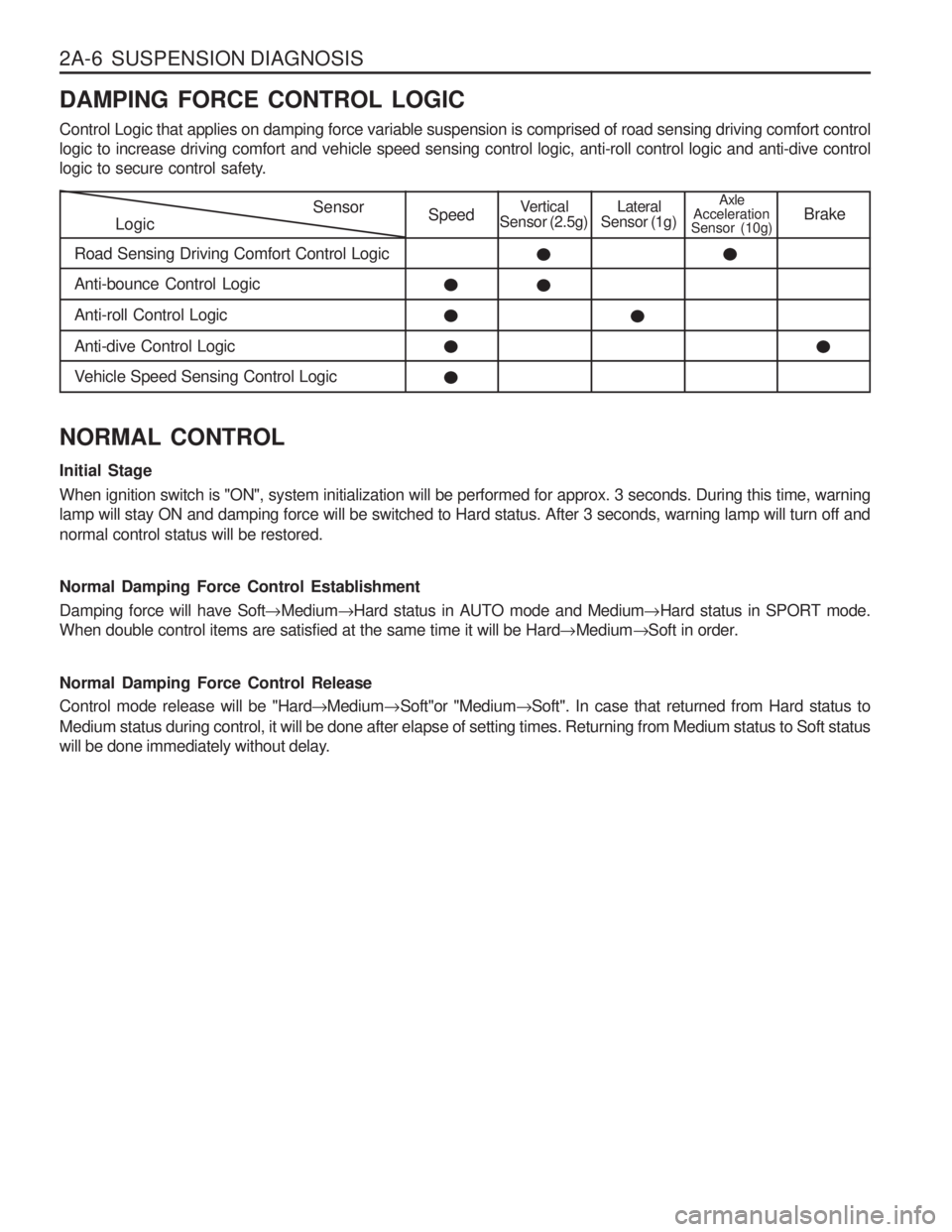
2A-6 SUSPENSION DIAGNOSIS DAMPING FORCE CONTROL LOGIC Control Logic that applies on damping force variable suspension is comprised of road sensing driving comfort control logic to increase driving comfort and vehicle speed sensing control logic, anti-roll control logic and anti-dive control
logic to secure control safety.
LogicSensor
Road Sensing Driving Comfort Control LogicSpeedVertical
Sensor (2.5g)Lateral
Sensor (1g)Axle
Acceleration
Sensor (10g) Brake
Anti-bounce Control Logic Anti-roll Control LogicAnti-dive Control Logic
Vehicle Speed Sensing Control Logic
NORMAL CONTROL Initial Stage When ignition switch is "ON", system initialization will be performed for approx. 3 seconds. During this time, warning lamp will stay ON and damping force will be switched to Hard status. After 3 seconds, warning lamp will turn off and normal control status will be restored. Normal Damping Force Control Establishment Damping force will have Soft Medium Hard status in AUTO mode and Medium Hard status in SPORT mode.
When double control items are satisfied at the same time it will be Hard Medium Soft in order.
Normal Damping Force Control Release Control mode release will be "Hard Medium Soft"or "Medium Soft". In case that returned from Hard status to
Medium status during control, it will be done after elapse of setting times. Returning from Medium status to Soft status
will be done immediately without delay.
Page 704 of 1574
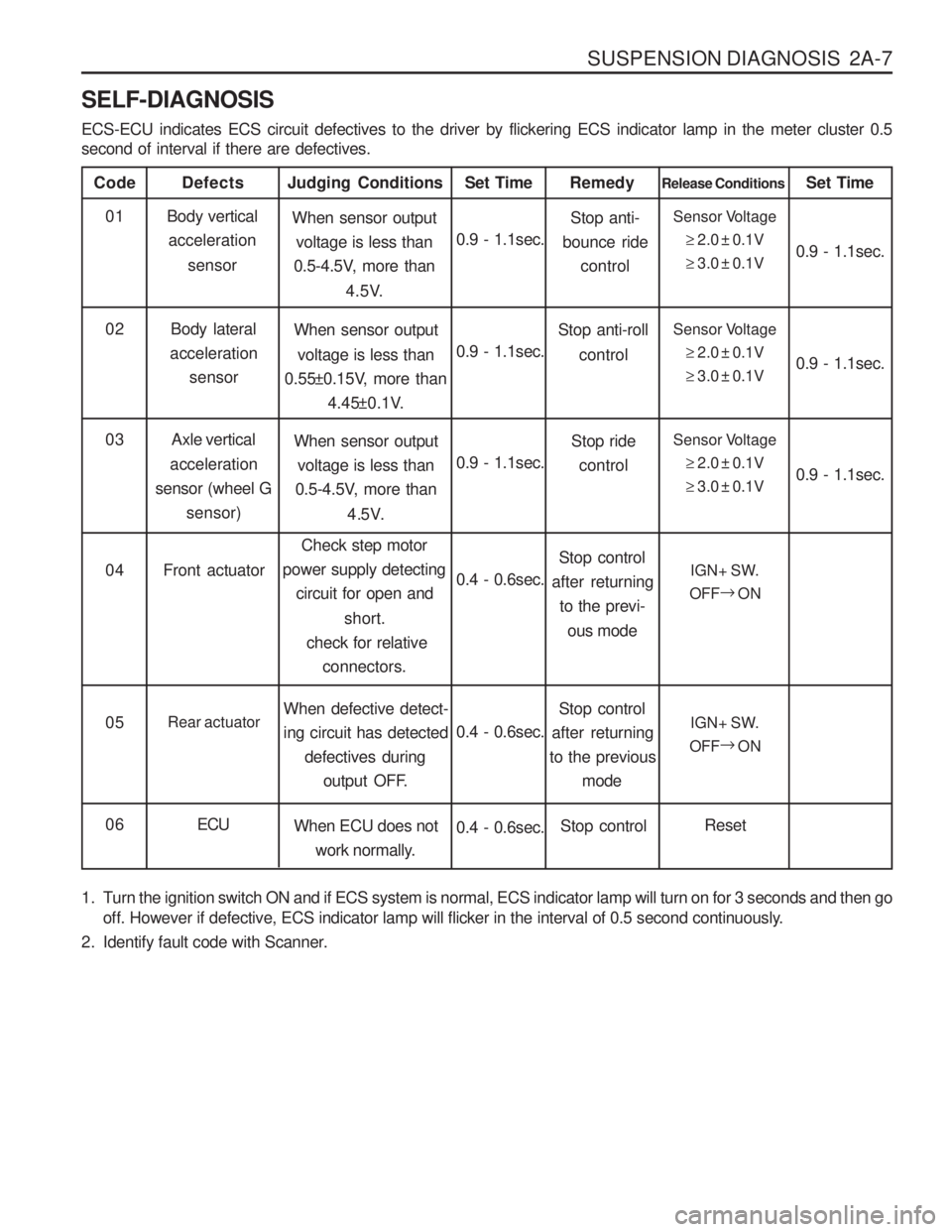
SUSPENSION DIAGNOSIS 2A-7
SELF-DIAGNOSIS ECS-ECU indicates ECS circuit defectives to the driver by flickering ECS indicator lamp in the meter cluster 0.5 second of interval if there are defectives.
Code
Body verticalacceleration
sensor
Defects
When sensor outputvoltage is less than
0.5-4.5V, more than
4.5V.
Judging Conditions01
0.9 - 1.1sec.Set TimeSensor Voltage
2.0 ± 0.1V
3.0 ± 0.1V
Release Conditions
0.9 - 1.1sec.
Set Time
Body lateral
acceleration sensor When sensor output
voltage is less than
0.55±0.15V, more than
4.45±0.1V.
02
0.9 - 1.1sec.Sensor Voltage
2.0 ± 0.1V
3.0 ± 0.1V 0.9 - 1.1sec.
Stop anti-
bounce ride
control
Remedy
Stop anti-roll control
Axle vertical
acceleration
sensor (wheel G sensor) When sensor output
voltage is less than
0.5-4.5V, more than
4.5V.
03
0.9 - 1.1sec.Sensor Voltage
2.0 ± 0.1V
3.0 ± 0.1V 0.9 - 1.1sec.
Stop ride
control
Front actuator Check step motor
power supply detecting
circuit for open and
short.
check for relative connectors.
04
0.4 - 0.6sec.IGN+ SW.
OFF
ON
Stop control
after returning to the previ-
ous mode
Rear actuator When defective detect- ing circuit has detected
defectives during
output OFF.
05
0.4 - 0.6sec.IGN+ SW.
OFF
ON
Stop control
after returning
to the previous
mode
ECU When ECU does not
work normally.
06
0.4 - 0.6sec.Reset
Stop control
1. Turn the ignition switch ON and if ECS system is normal, ECS indicator lamp will turn on for 3 seconds and then go off. However if defective, ECS indicator lamp will flicker in the interval of 0.5 second continuously.
2. Identify fault code with Scanner.
Page 708 of 1574
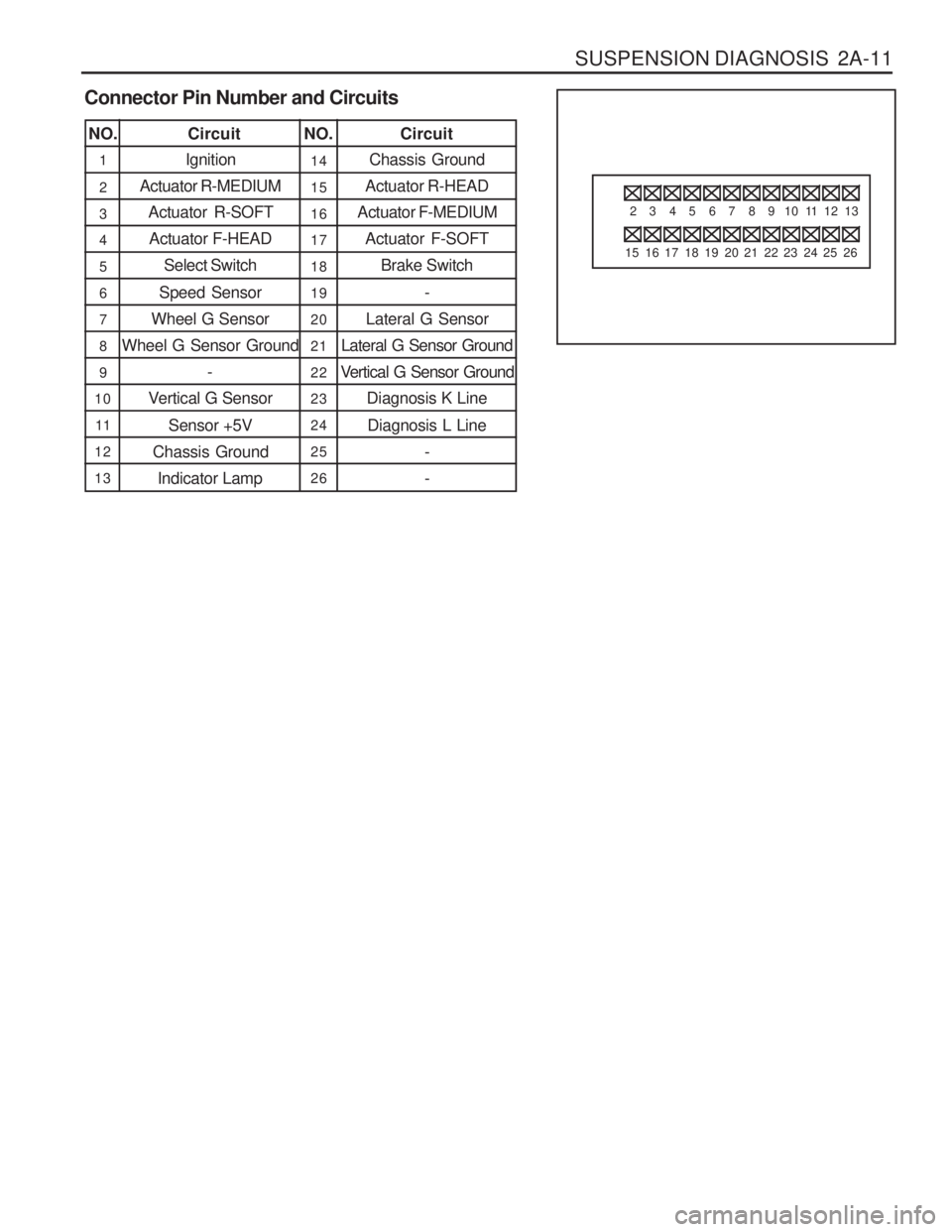
SUSPENSION DIAGNOSIS 2A-11
Connector Pin Number and Circuits
2
15
3
16
4
17
5
18
6
19
7
20
8
21
9
22
10
23
11
24
12
25
13
26
Ignition
Actuator R-MEDIUM Actuator R-SOFT
Actuator F-HEAD Select Switch
Speed Sensor
Wheel G Sensor
Wheel G Sensor Ground
-
Vertical G Sensor
Sensor +5V
Chassis Ground Indicator Lamp
NO. CircuitNO. Circuit
1 14
21 5
316
417
518
619
720
821
922
10 23
11 2 4
12 25
13 26 Chassis Ground
Actuator R-HEAD
Actuator F-MEDIUM
Actuator F-SOFT Brake Switch
-
Lateral G Sensor
Lateral G Sensor Ground
Vertical G Sensor Ground Diagnosis K Line
Diagnosis L Line - -
Page 709 of 1574
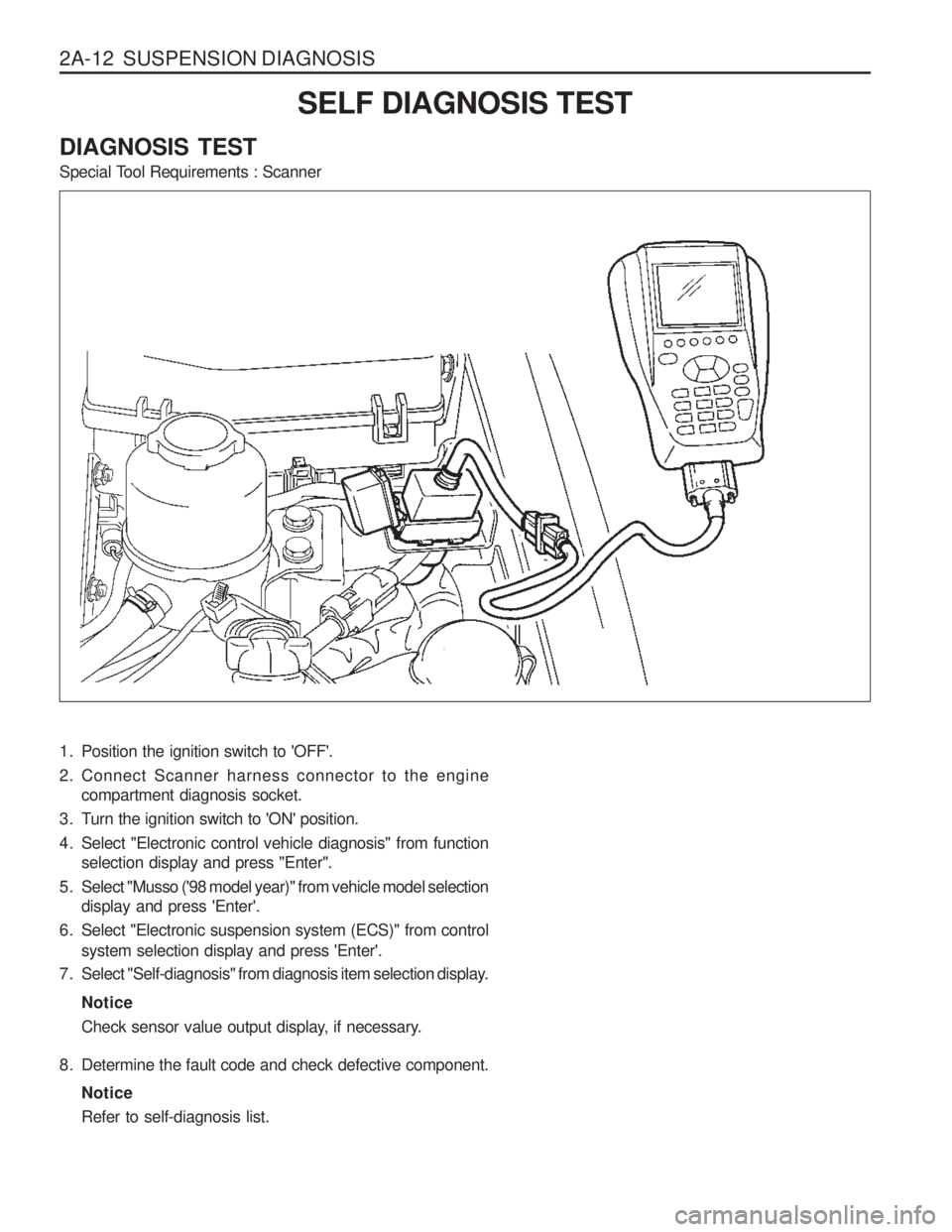
2A-12 SUSPENSION DIAGNOSISSELF DIAGNOSIS TEST
DIAGNOSIS TEST
Special Tool Requirements : Scanner
1. Position the ignition switch to 'OFF'.
2. Connect Scanner harness connector to the engine compartment diagnosis socket.
3. Turn the ignition switch to 'ON' position.
4. Select "Electronic control vehicle diagnosis" from function selection display and press "Enter".
5. Select "Musso ('98 model year)" from vehicle model selection display and press 'Enter'.
6. Select "Electronic suspension system (ECS)" from control system selection display and press 'Enter'.
7. Select "Self-diagnosis" from diagnosis item selection display.
Notice
Check sensor value output display, if necessary.
8. Determine the fault code and check defective component. NoticeRefer to self-diagnosis list.