SUZUKI SWIFT 2000 1.G RG413 Service Workshop Manual
[x] Cancel search | Manufacturer: SUZUKI, Model Year: 2000, Model line: SWIFT, Model: SUZUKI SWIFT 2000 1.GPages: 698, PDF Size: 16.01 MB
Page 511 of 698
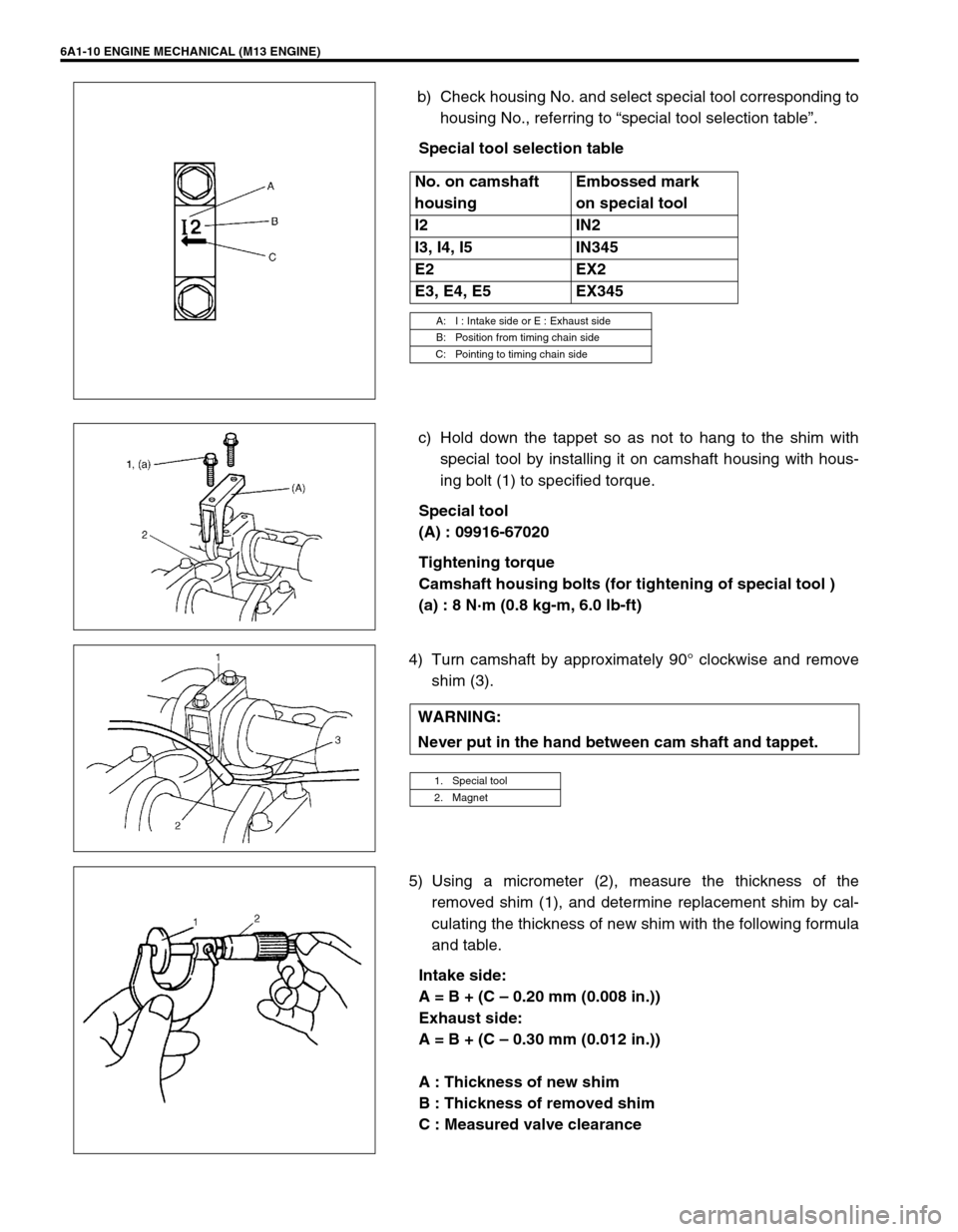
6A1-10 ENGINE MECHANICAL (M13 ENGINE)
b) Check housing No. and select special tool corresponding to
housing No., referring to “special tool selection table”.
Special tool selection table
c) Hold down the tappet so as not to hang to the shim with
special tool by installing it on camshaft housing with hous-
ing bolt (1) to specified torque.
Special tool
(A) : 09916-67020
Tightening torque
Camshaft housing bolts (for tightening of special tool )
(a) : 8 N·m (0.8 kg-m, 6.0 lb-ft)
4) Turn camshaft by approximately 90° clockwise and remove
shim (3).
5) Using a micrometer (2), measure the thickness of the
removed shim (1), and determine replacement shim by cal-
culating the thickness of new shim with the following formula
and table.
Intake side:
A = B + (C – 0.20 mm (0.008 in.))
Exhaust side:
A = B + (C – 0.30 mm (0.012 in.))
A : Thickness of new shim
B : Thickness of removed shim
C : Measured valve clearance No. on camshaft
housingEmbossed mark
on special tool
I2 IN2
I3, I4, I5 IN345
E2 EX2
E3, E4, E5 EX345
A: I : Intake side or E : Exhaust side
B: Position from timing chain side
C: Pointing to timing chain side
WARNING:
Never put in the hand between cam shaft and tappet.
1. Special tool
2. Magnet
Page 512 of 698
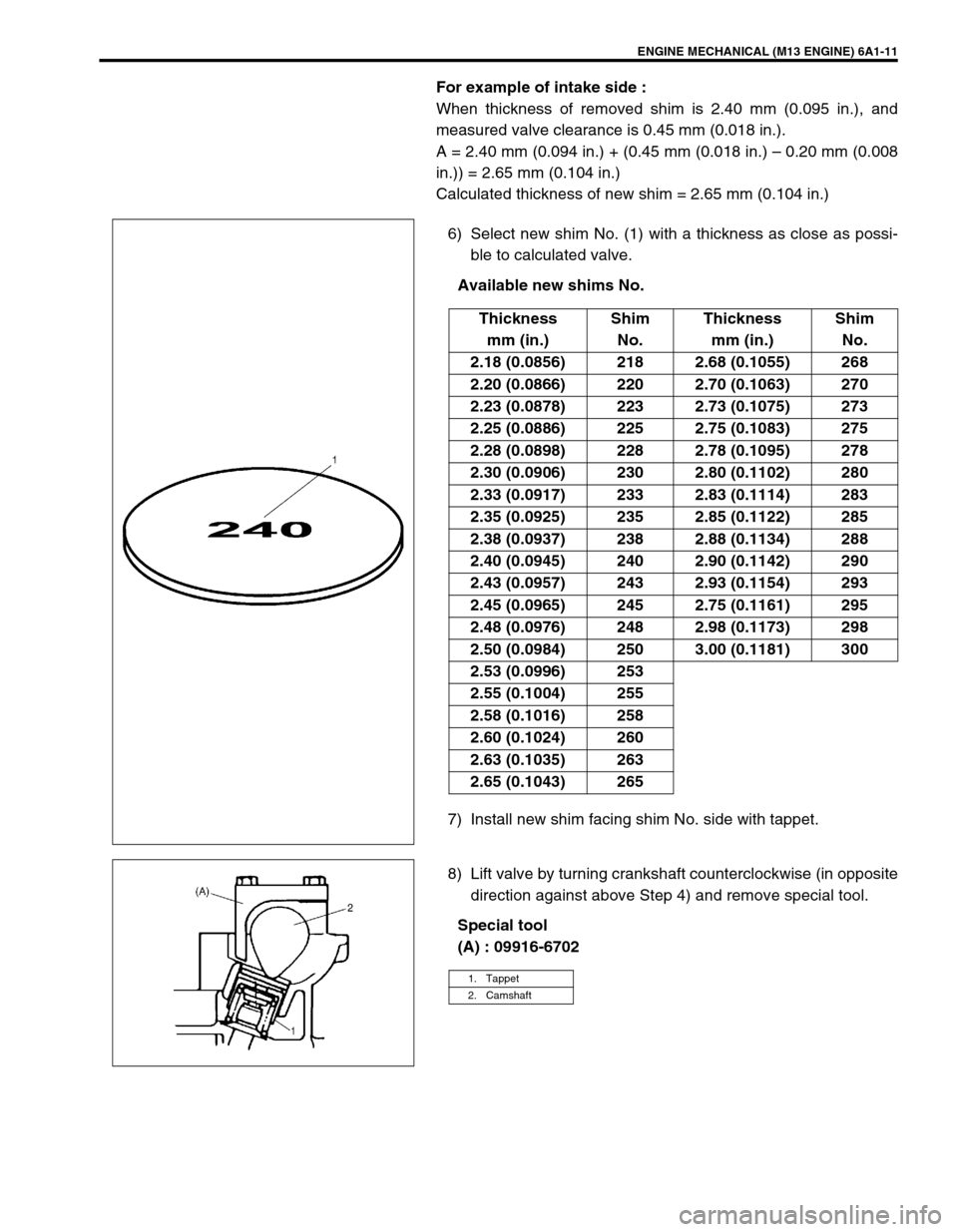
ENGINE MECHANICAL (M13 ENGINE) 6A1-11
For example of intake side :
When thickness of removed shim is 2.40 mm (0.095 in.), and
measured valve clearance is 0.45 mm (0.018 in.).
A = 2.40 mm (0.094 in.) + (0.45 mm (0.018 in.) – 0.20 mm (0.008
in.)) = 2.65 mm (0.104 in.)
Calculated thickness of new shim = 2.65 mm (0.104 in.)
6) Select new shim No. (1) with a thickness as close as possi-
ble to calculated valve.
Available new shims No.
7) Install new shim facing shim No. side with tappet.
8) Lift valve by turning crankshaft counterclockwise (in opposite
direction against above Step 4) and remove special tool.
Special tool
(A) : 09916-6702Thickness
mm (in.)Shim
No.Thickness
mm (in.)Shim
No.
2.18 (0.0856) 218 2.68 (0.1055) 268
2.20 (0.0866) 220 2.70 (0.1063) 270
2.23 (0.0878) 223 2.73 (0.1075) 273
2.25 (0.0886) 225 2.75 (0.1083) 275
2.28 (0.0898) 228 2.78 (0.1095) 278
2.30 (0.0906) 230 2.80 (0.1102) 280
2.33 (0.0917) 233 2.83 (0.1114) 283
2.35 (0.0925) 235 2.85 (0.1122) 285
2.38 (0.0937) 238 2.88 (0.1134) 288
2.40 (0.0945) 240 2.90 (0.1142) 290
2.43 (0.0957) 243 2.93 (0.1154) 293
2.45 (0.0965) 245 2.75 (0.1161) 295
2.48 (0.0976) 248 2.98 (0.1173) 298
2.50 (0.0984) 250 3.00 (0.1181) 300
2.53 (0.0996) 253
2.55 (0.1004) 255
2.58 (0.1016) 258
2.60 (0.1024) 260
2.63 (0.1035) 263
2.65 (0.1043) 265
1. Tappet
2. Camshaft
Page 513 of 698
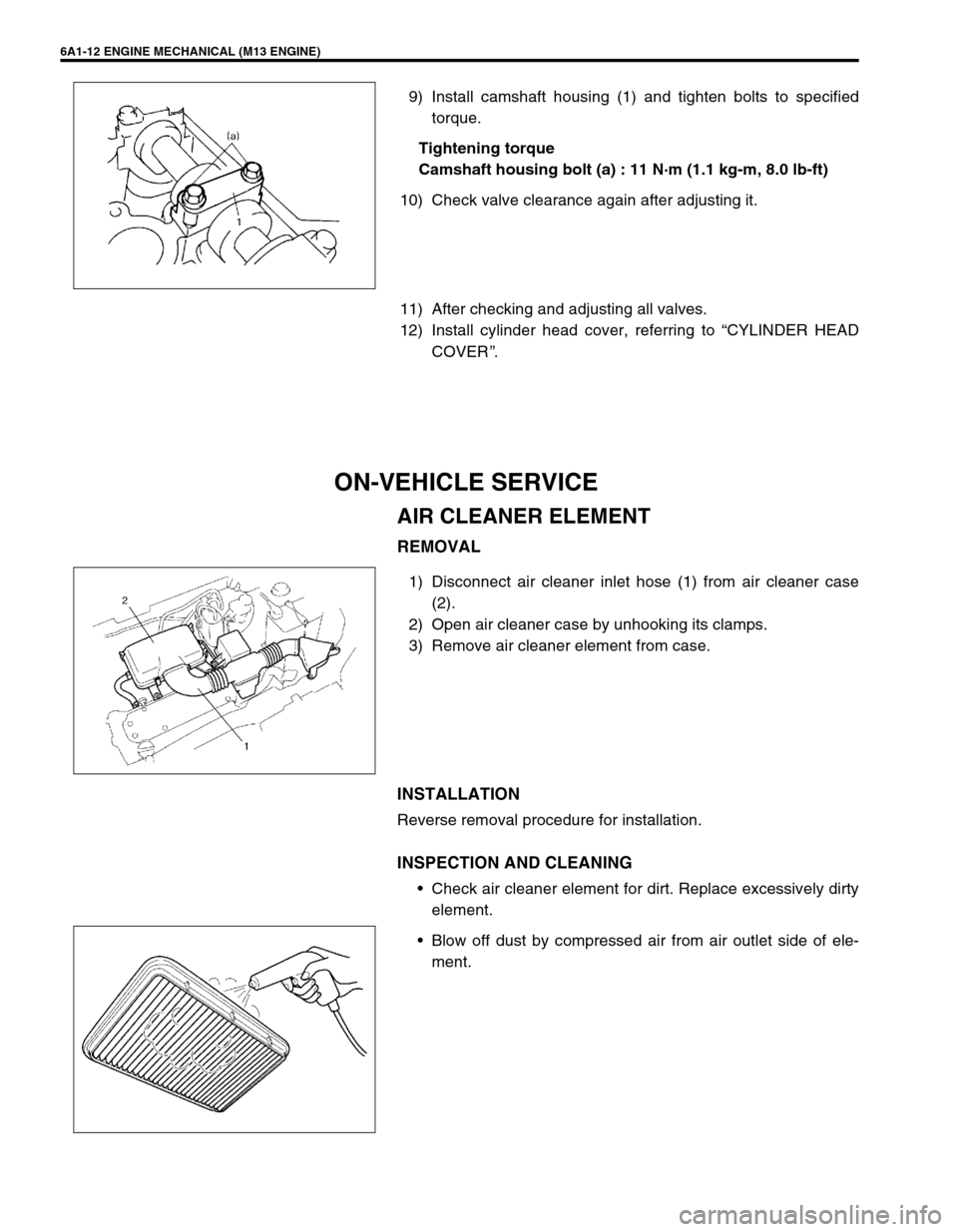
6A1-12 ENGINE MECHANICAL (M13 ENGINE)
9) Install camshaft housing (1) and tighten bolts to specified
torque.
Tightening torque
Camshaft housing bolt (a) : 11 N·m (1.1 kg-m, 8.0 lb-ft)
10) Check valve clearance again after adjusting it.
11) After checking and adjusting all valves.
12) Install cylinder head cover, referring to “CYLINDER HEAD
COVER”.
ON-VEHICLE SERVICE
AIR CLEANER ELEMENT
REMOVAL
1) Disconnect air cleaner inlet hose (1) from air cleaner case
(2).
2) Open air cleaner case by unhooking its clamps.
3) Remove air cleaner element from case.
INSTALLATION
Reverse removal procedure for installation.
INSPECTION AND CLEANING
Check air cleaner element for dirt. Replace excessively dirty
element.
Blow off dust by compressed air from air outlet side of ele-
ment.
Page 514 of 698
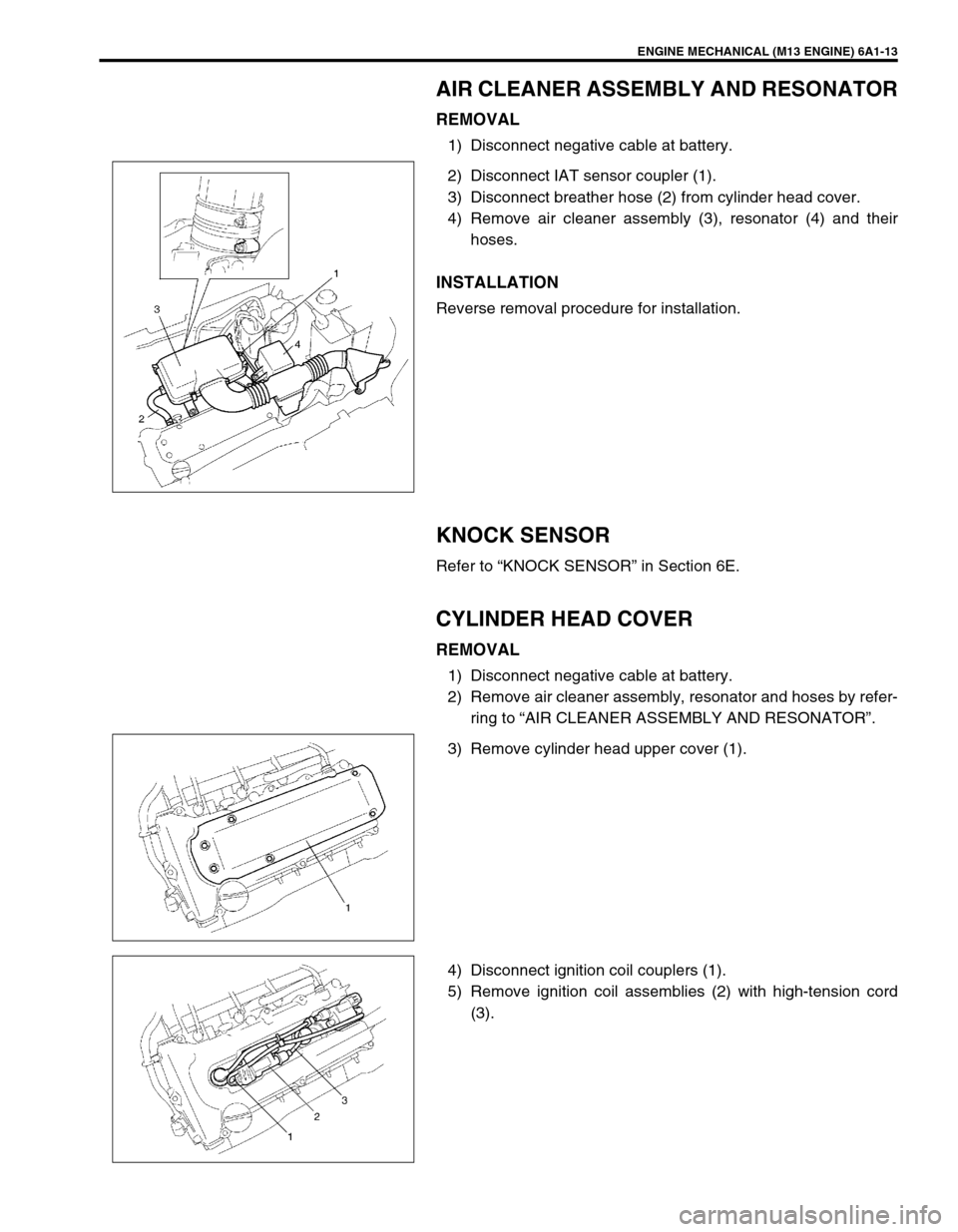
ENGINE MECHANICAL (M13 ENGINE) 6A1-13
AIR CLEANER ASSEMBLY AND RESONATOR
REMOVAL
1) Disconnect negative cable at battery.
2) Disconnect IAT sensor coupler (1).
3) Disconnect breather hose (2) from cylinder head cover.
4) Remove air cleaner assembly (3), resonator (4) and their
hoses.
INSTALLATION
Reverse removal procedure for installation.
KNOCK SENSOR
Refer to “KNOCK SENSOR” in Section 6E.
CYLINDER HEAD COVER
REMOVAL
1) Disconnect negative cable at battery.
2) Remove air cleaner assembly, resonator and hoses by refer-
ring to “AIR CLEANER ASSEMBLY AND RESONATOR”.
3) Remove cylinder head upper cover (1).
4) Disconnect ignition coil couplers (1).
5) Remove ignition coil assemblies (2) with high-tension cord
(3).
Page 515 of 698
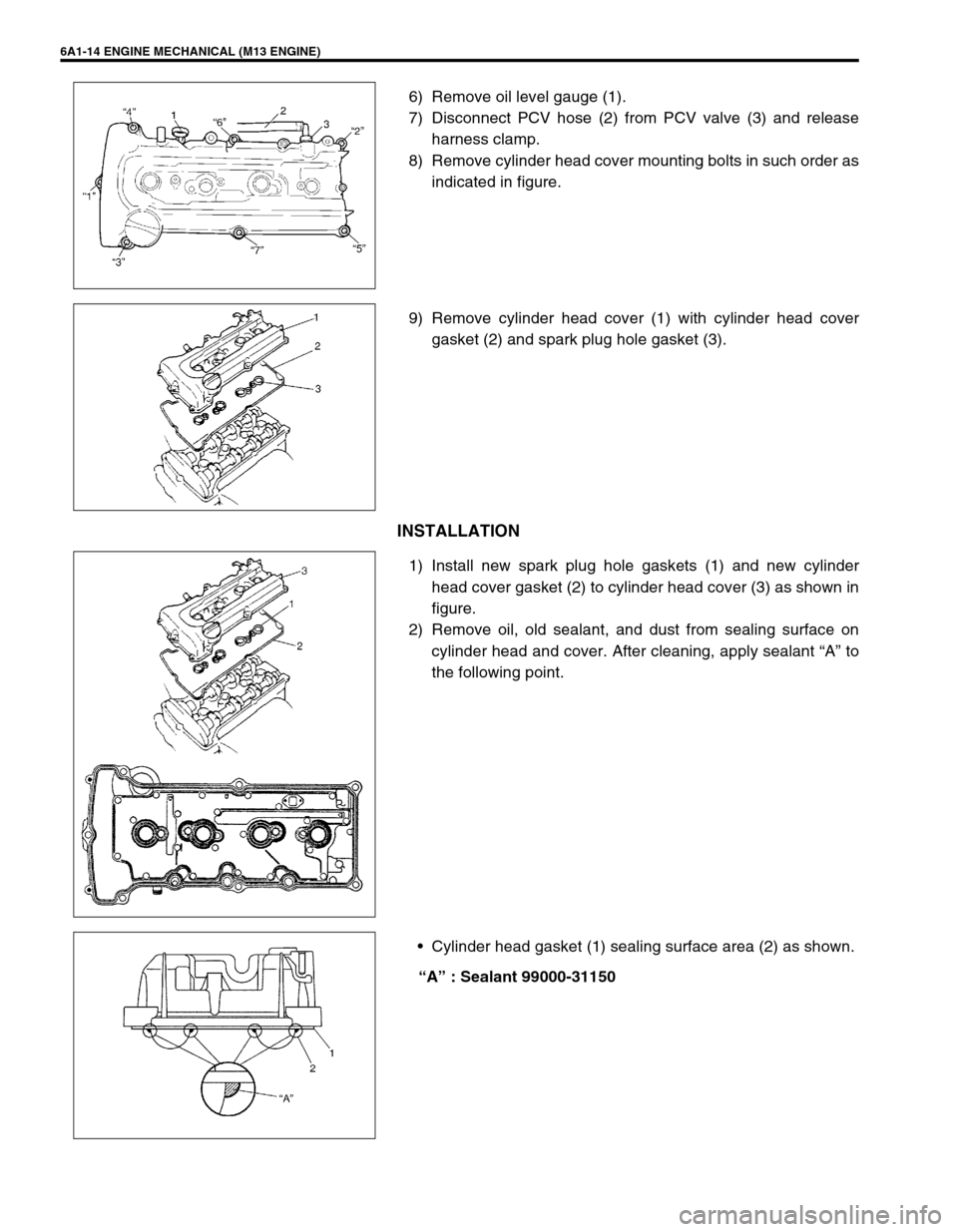
6A1-14 ENGINE MECHANICAL (M13 ENGINE)
6) Remove oil level gauge (1).
7) Disconnect PCV hose (2) from PCV valve (3) and release
harness clamp.
8) Remove cylinder head cover mounting bolts in such order as
indicated in figure.
9) Remove cylinder head cover (1) with cylinder head cover
gasket (2) and spark plug hole gasket (3).
INSTALLATION
1) Install new spark plug hole gaskets (1) and new cylinder
head cover gasket (2) to cylinder head cover (3) as shown in
figure.
2) Remove oil, old sealant, and dust from sealing surface on
cylinder head and cover. After cleaning, apply sealant “A” to
the following point.
Cylinder head gasket (1) sealing surface area (2) as shown.
“A” : Sealant 99000-31150
Page 516 of 698
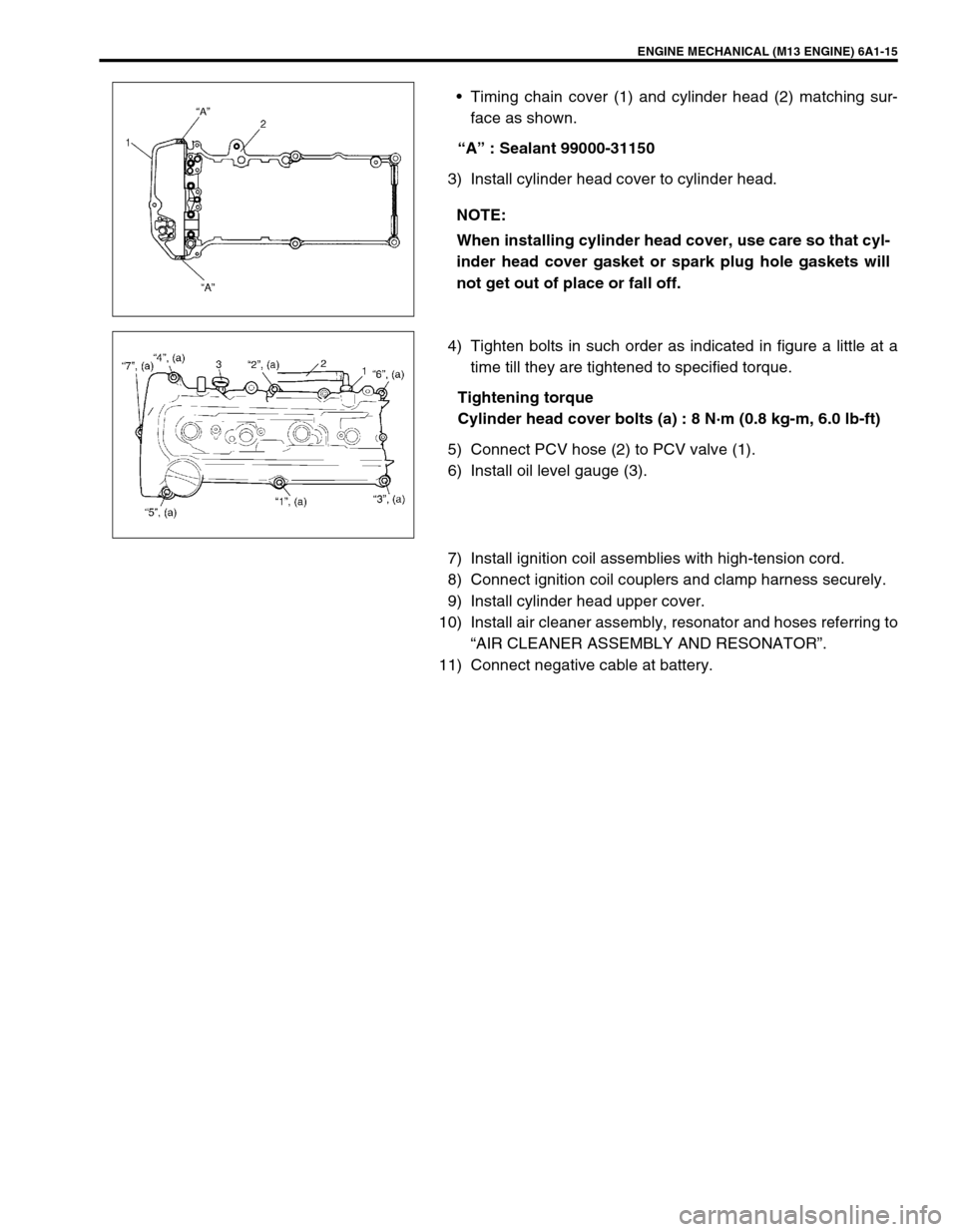
ENGINE MECHANICAL (M13 ENGINE) 6A1-15
Timing chain cover (1) and cylinder head (2) matching sur-
face as shown.
“A” : Sealant 99000-31150
3) Install cylinder head cover to cylinder head.
4) Tighten bolts in such order as indicated in figure a little at a
time till they are tightened to specified torque.
Tightening torque
Cylinder head cover bolts (a) : 8 N·m (0.8 kg-m, 6.0 lb-ft)
5) Connect PCV hose (2) to PCV valve (1).
6) Install oil level gauge (3).
7) Install ignition coil assemblies with high-tension cord.
8) Connect ignition coil couplers and clamp harness securely.
9) Install cylinder head upper cover.
10) Install air cleaner assembly, resonator and hoses referring to
“AIR CLEANER ASSEMBLY AND RESONATOR”.
11) Connect negative cable at battery.NOTE:
When installing cylinder head cover, use care so that cyl-
inder head cover gasket or spark plug hole gaskets will
not get out of place or fall off.
Page 517 of 698
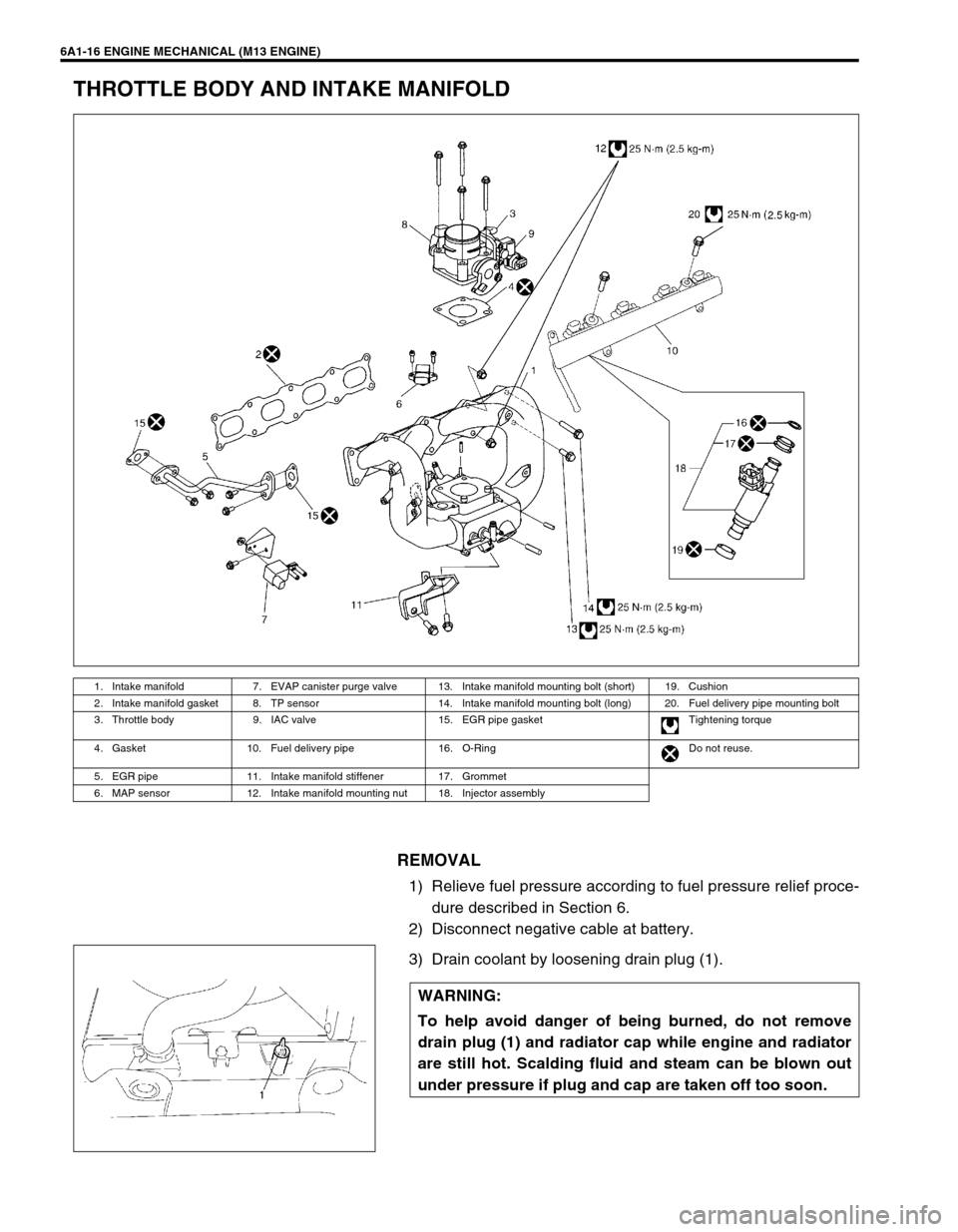
6A1-16 ENGINE MECHANICAL (M13 ENGINE)
THROTTLE BODY AND INTAKE MANIFOLD
REMOVAL
1) Relieve fuel pressure according to fuel pressure relief proce-
dure described in Section 6.
2) Disconnect negative cable at battery.
3) Drain coolant by loosening drain plug (1).
1. Intake manifold 7. EVAP canister purge valve 13. Intake manifold mounting bolt (short) 19. Cushion
2. Intake manifold gasket 8. TP sensor 14. Intake manifold mounting bolt (long) 20. Fuel delivery pipe mounting bolt
3. Throttle body 9. IAC valve 15. EGR pipe gasket Tightening torque
4. Gasket 10. Fuel delivery pipe 16. O-Ring Do not reuse.
5. EGR pipe 11. Intake manifold stiffener 17. Grommet
6. MAP sensor 12. Intake manifold mounting nut 18. Injector assembly
WARNING:
To help avoid danger of being burned, do not remove
drain plug (1) and radiator cap while engine and radiator
are still hot. Scalding fluid and steam can be blown out
under pressure if plug and cap are taken off too soon.
Page 518 of 698
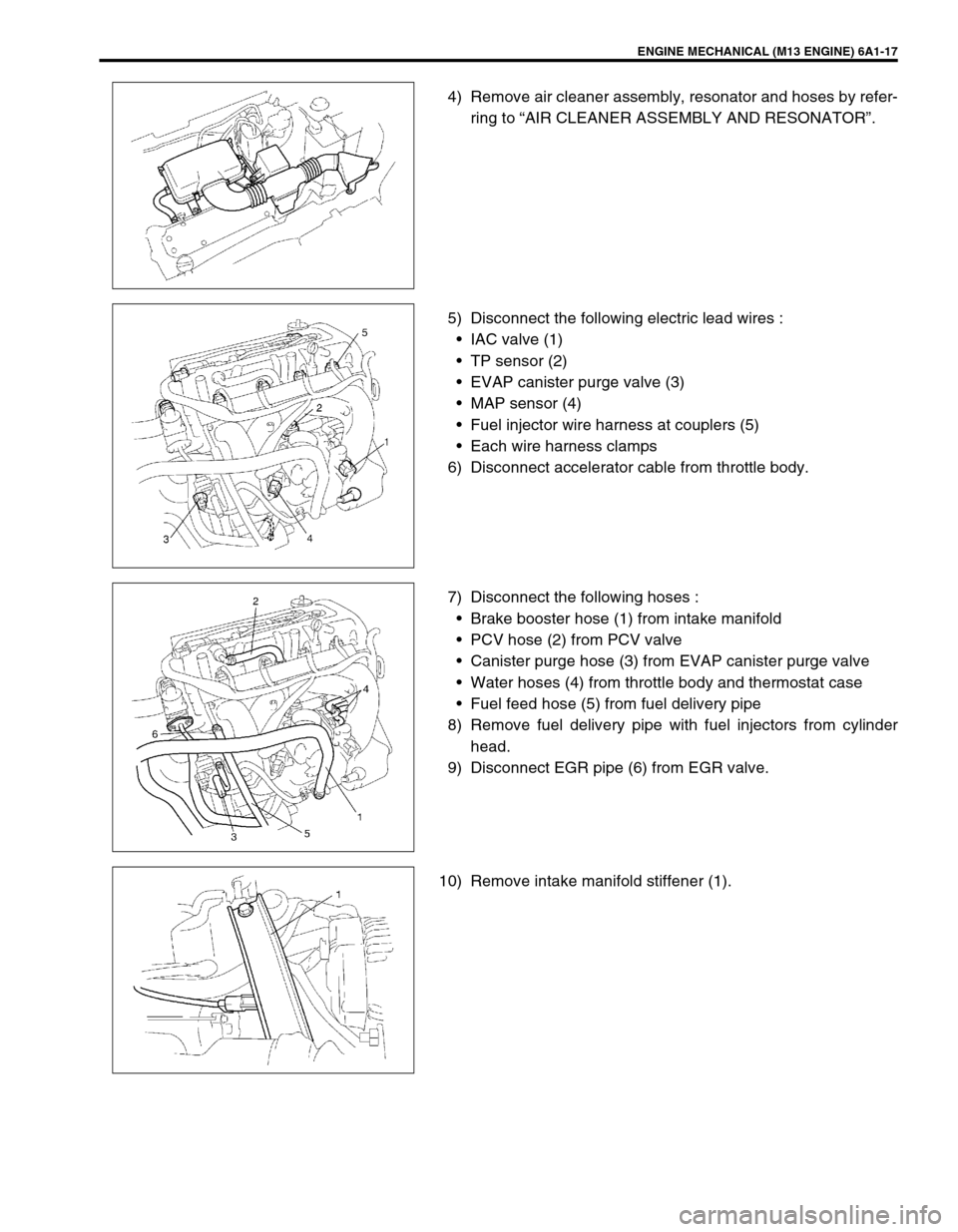
ENGINE MECHANICAL (M13 ENGINE) 6A1-17
4) Remove air cleaner assembly, resonator and hoses by refer-
ring to “AIR CLEANER ASSEMBLY AND RESONATOR”.
5) Disconnect the following electric lead wires :
IAC valve (1)
TP sensor (2)
EVAP canister purge valve (3)
MAP sensor (4)
Fuel injector wire harness at couplers (5)
Each wire harness clamps
6) Disconnect accelerator cable from throttle body.
7) Disconnect the following hoses :
Brake booster hose (1) from intake manifold
PCV hose (2) from PCV valve
Canister purge hose (3) from EVAP canister purge valve
Water hoses (4) from throttle body and thermostat case
Fuel feed hose (5) from fuel delivery pipe
8) Remove fuel delivery pipe with fuel injectors from cylinder
head.
9) Disconnect EGR pipe (6) from EGR valve.
10) Remove intake manifold stiffener (1).
Page 519 of 698
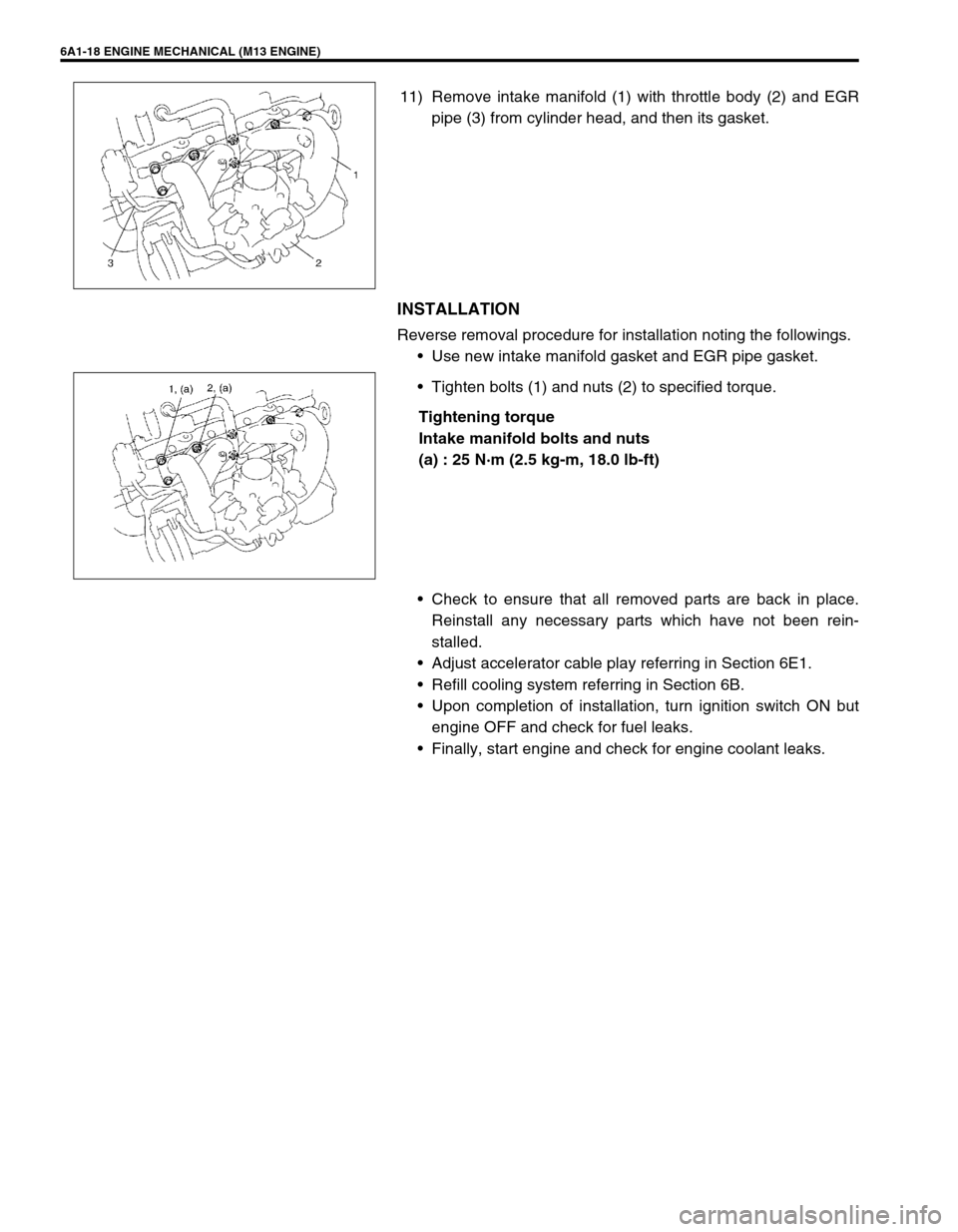
6A1-18 ENGINE MECHANICAL (M13 ENGINE)
11) Remove intake manifold (1) with throttle body (2) and EGR
pipe (3) from cylinder head, and then its gasket.
INSTALLATION
Reverse removal procedure for installation noting the followings.
Use new intake manifold gasket and EGR pipe gasket.
Tighten bolts (1) and nuts (2) to specified torque.
Tightening torque
Intake manifold bolts and nuts
(a) : 25 N·m (2.5 kg-m, 18.0 lb-ft)
Check to ensure that all removed parts are back in place.
Reinstall any necessary parts which have not been rein-
stalled.
Adjust accelerator cable play referring in Section 6E1.
Refill cooling system referring in Section 6B.
Upon completion of installation, turn ignition switch ON but
engine OFF and check for fuel leaks.
Finally, start engine and check for engine coolant leaks.
Page 520 of 698
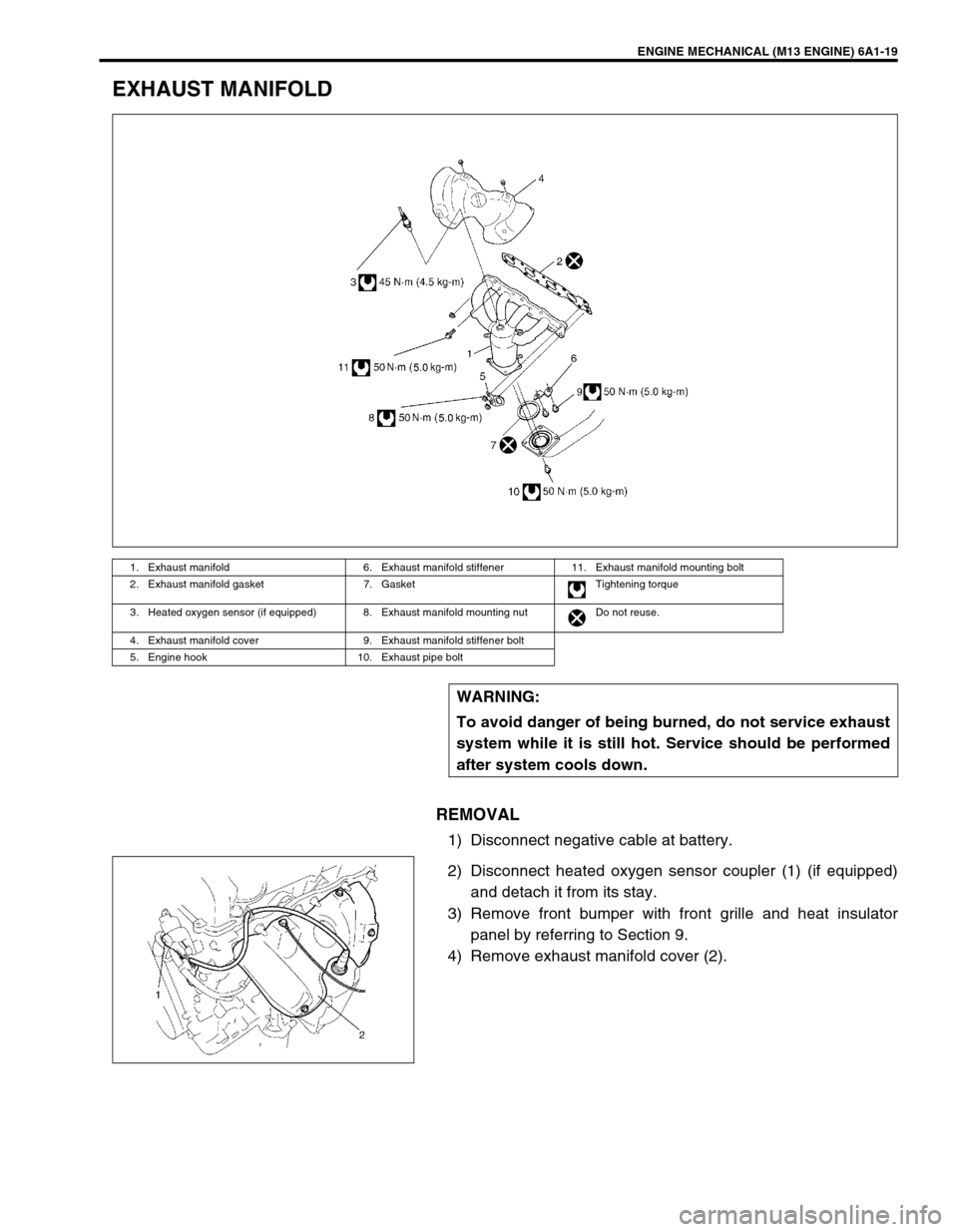
ENGINE MECHANICAL (M13 ENGINE) 6A1-19
EXHAUST MANIFOLD
REMOVAL
1) Disconnect negative cable at battery.
2) Disconnect heated oxygen sensor coupler (1) (if equipped)
and detach it from its stay.
3) Remove front bumper with front grille and heat insulator
panel by referring to Section 9.
4) Remove exhaust manifold cover (2).
1. Exhaust manifold 6. Exhaust manifold stiffener 11. Exhaust manifold mounting bolt
2. Exhaust manifold gasket 7. Gasket Tightening torque
3. Heated oxygen sensor (if equipped) 8. Exhaust manifold mounting nut Do not reuse.
4. Exhaust manifold cover 9. Exhaust manifold stiffener bolt
5. Engine hook 10. Exhaust pipe bolt
WARNING:
To avoid danger of being burned, do not service exhaust
system while it is still hot. Service should be performed
after system cools down.