sensor SUZUKI SX4 2006 1.G Service Workshop Manual
[x] Cancel search | Manufacturer: SUZUKI, Model Year: 2006, Model line: SX4, Model: SUZUKI SX4 2006 1.GPages: 1556, PDF Size: 37.31 MB
Page 807 of 1556
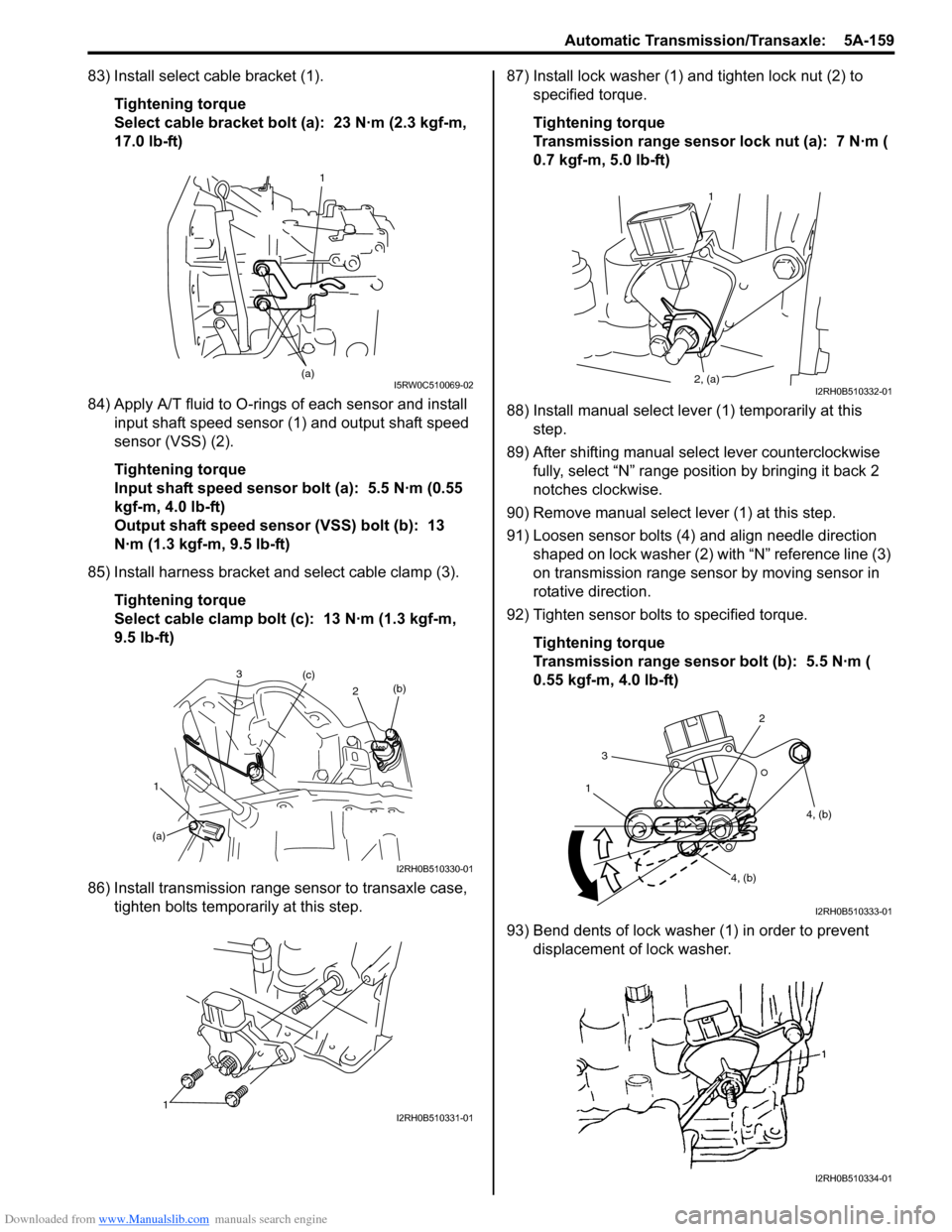
Downloaded from www.Manualslib.com manuals search engine Automatic Transmission/Transaxle: 5A-159
83) Install select cable bracket (1).
Tightening torque
Select cable bracket bolt (a): 23 N·m (2.3 kgf-m,
17.0 lb-ft)
84) Apply A/T fluid to O-rings of each sensor and install
input shaft speed sensor (1) and output shaft speed
sensor (VSS) (2).
Tightening torque
Input shaft speed sensor bolt (a): 5.5 N·m (0.55
kgf-m, 4.0 lb-ft)
Output shaft speed sensor (VSS) bolt (b): 13
N·m (1.3 kgf-m, 9.5 lb-ft)
85) Install harness bracket and select cable clamp (3).
Tightening torque
Select cable clamp bolt (c): 13 N·m (1.3 kgf-m,
9.5 lb-ft)
86) Install transmission range sensor to transaxle case,
tighten bolts temporarily at this step.87) Install lock washer (1) and tighten lock nut (2) to
specified torque.
Tightening torque
Transmission range sensor lock nut (a): 7 N·m (
0.7 kgf-m, 5.0 lb-ft)
88) Install manual select lever (1) temporarily at this
step.
89) After shifting manual select lever counterclockwise
fully, select “N” range position by bringing it back 2
notches clockwise.
90) Remove manual select lever (1) at this step.
91) Loosen sensor bolts (4) and align needle direction
shaped on lock washer (2) with “N” reference line (3)
on transmission range sensor by moving sensor in
rotative direction.
92) Tighten sensor bolts to specified torque.
Tightening torque
Transmission range sensor bolt (b): 5.5 N·m (
0.55 kgf-m, 4.0 lb-ft)
93) Bend dents of lock washer (1) in order to prevent
displacement of lock washer.
1
(a)I5RW0C510069-02
(a)13
(c)
2(b)
I2RH0B510330-01
1I2RH0B510331-01
1
2, (a)
I2RH0B510332-01
132
4, (b)
4, (b)
I2RH0B510333-01
I2RH0B510334-01
Page 809 of 1556
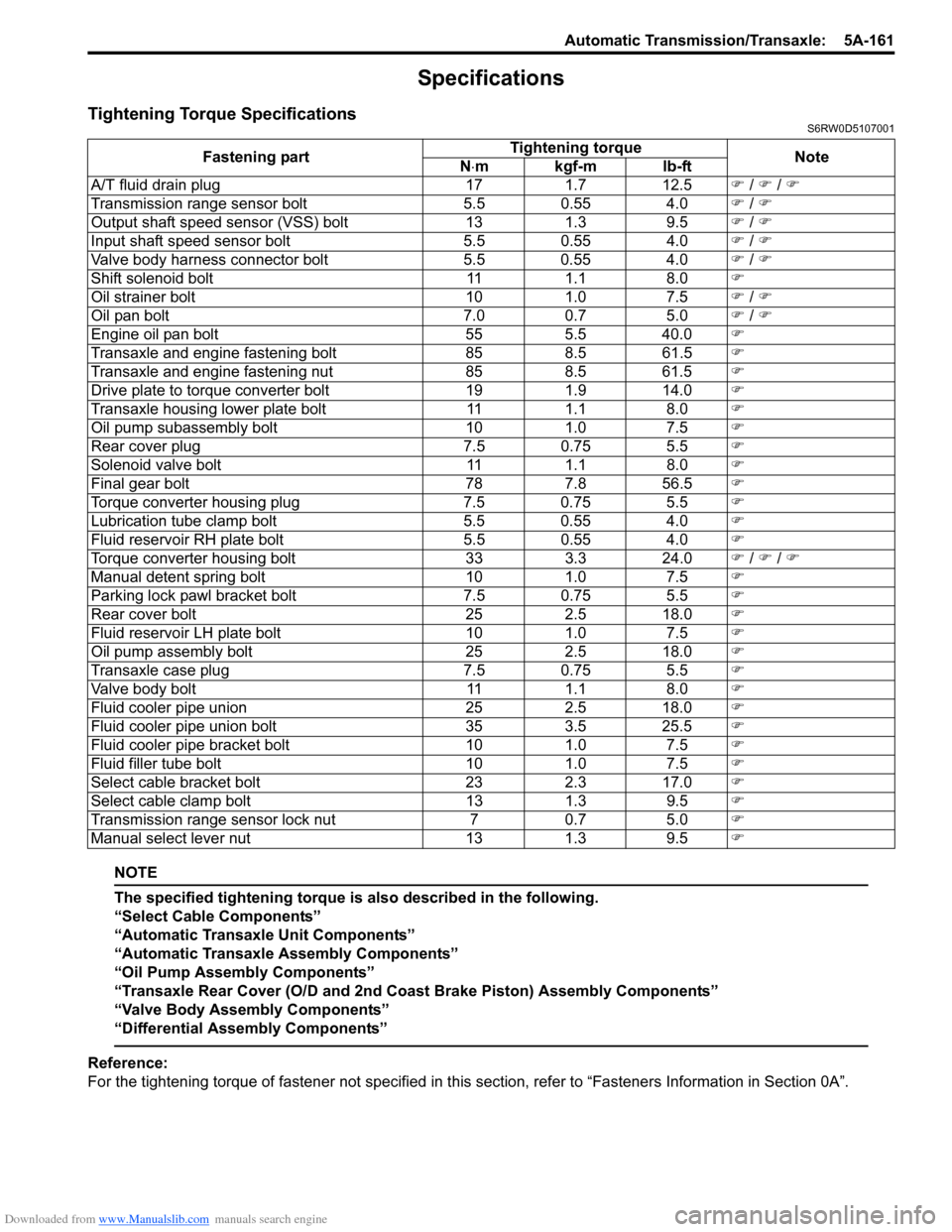
Downloaded from www.Manualslib.com manuals search engine Automatic Transmission/Transaxle: 5A-161
Specifications
Tightening Torque SpecificationsS6RW0D5107001
NOTE
The specified tightening torque is also described in the following.
“Select Cable Components”
“Automatic Transaxle Unit Components”
“Automatic Transaxle Assembly Components”
“Oil Pump Assembly Components”
“Transaxle Rear Cover (O/D and 2nd Coast Brake Piston) Assembly Components”
“Valve Body Assembly Components”
“Differential Assembly Components”
Reference:
For the tightening torque of fastener not specified in this section, refer to “Fasteners Information in Section 0A”. Fastening partTightening torque
Note
N⋅mkgf-mlb-ft
A/T fluid drain plug 17 1.7 12.5 ) / ) / )
Transmission range sensor bolt 5.5 0.55 4.0 ) / )
Output shaft speed sensor (VSS) bolt 13 1.3 9.5 ) / )
Input shaft speed sensor bolt 5.5 0.55 4.0 ) / )
Valve body harness connector bolt 5.5 0.55 4.0 ) / )
Shift solenoid bolt 11 1.1 8.0 )
Oil strainer bolt 10 1.0 7.5 ) / )
Oil pan bolt 7.0 0.7 5.0 ) / )
Engine oil pan bolt 55 5.5 40.0 )
Transaxle and engine fastening bolt 85 8.5 61.5 )
Transaxle and engine fastening nut 85 8.5 61.5 )
Drive plate to torque converter bolt 19 1.9 14.0 )
Transaxle housing lower plate bolt 11 1.1 8.0 )
Oil pump subassembly bolt 10 1.0 7.5 )
Rear cover plug 7.5 0.75 5.5 )
Solenoid valve bolt 11 1.1 8.0 )
Final gear bolt 78 7.8 56.5 )
Torque converter housing plug 7.5 0.75 5.5 )
Lubrication tube clamp bolt 5.5 0.55 4.0 )
Fluid reservoir RH plate bolt 5.5 0.55 4.0 )
Torque converter housing bolt 33 3.3 24.0 ) / ) / )
Manual detent spring bolt 10 1.0 7.5 )
Parking lock pawl bracket bolt 7.5 0.75 5.5 )
Rear cover bolt 25 2.5 18.0 )
Fluid reservoir LH plate bolt 10 1.0 7.5 )
Oil pump assembly bolt 25 2.5 18.0 )
Transaxle case plug 7.5 0.75 5.5 )
Valve body bolt 11 1.1 8.0 )
Fluid cooler pipe union 25 2.5 18.0 )
Fluid cooler pipe union bolt 35 3.5 25.5 )
Fluid cooler pipe bracket bolt 10 1.0 7.5 )
Fluid filler tube bolt 10 1.0 7.5 )
Select cable bracket bolt 23 2.3 17.0 )
Select cable clamp bolt 13 1.3 9.5 )
Transmission range sensor lock nut 7 0.7 5.0 )
Manual select lever nut 13 1.3 9.5 )
Page 865 of 1556

Downloaded from www.Manualslib.com manuals search engine Table of Contents 6- i
6
Section 6
CONTENTS
Steering
Precautions ................................................. 6-1
Precautions............................................................. 6-1
Precautions on Steering........................................ 6-1
Steering General Diagnosis.................... 6A-1
Precautions........................................................... 6A-1
Precautions for Steering Diagnosis ..................... 6A-1
Diagnostic Information and Procedures ............ 6A-1
Steering Symptom Diagnosis .............................. 6A-1
Steering System Inspection ................................ 6A-2
Steering Wheel and Column................... 6B-1
Precautions........................................................... 6B-1
Service Precautions of Steering Wheel and
Column.............................................................. 6B-1
General Description ............................................. 6B-1
Steering Wheel and Column Construction .......... 6B-1
Diagnostic Information and Procedures ............ 6B-2
Checking Steering Column for Accident
Damage ............................................................ 6B-2
Repair Instructions .............................................. 6B-3
Steering Wheel and Column Construction .......... 6B-3
Steering Wheel Removal and Installation ........... 6B-4
Contact Coil Cable Assembly Removal and
Installation ......................................................... 6B-5
Centering Contact Coil Cable Assembly ............. 6B-6
Contact Coil Cable Assembly Inspection ............ 6B-6
Steering Column Removal and Installation ......... 6B-6
Steering Column Inspection ................................ 6B-8
Ignition Switch Cylinder Assembly Removal
and Installation (Non- Keyless Start Model)...... 6B-8
Steering Lock Assembly (Ignition Switch)
Removal and Installation................................... 6B-9
Steering Lower Shaft Removal and
Installation ....................................................... 6B-10
Specifications..................................................... 6B-11
Tightening Torque Specifications ...................... 6B-11
Special Tools and Equipment ........................... 6B-11
Special Tool ...................................................... 6B-11
Power Assisted Steering System........... 6C-1
Precautions........................................................... 6C-1
P/S System Note ................................................. 6C-1
Precautions in Diagnosing Troubles ................... 6C-1General Description .............................................6C-2
P/S System Description ......................................6C-2
EPS Diagnosis General Description ...................6C-3
On-Board Diagnostic System Description ...........6C-3
Schematic and Routing Diagram ........................6C-4
EPS System Wiring Circuit Diagram ...................6C-4
Diagnostic Information and Procedures ............6C-5
EPS System Check .............................................6C-5
“EPS” Warning Light Check ................................6C-8
DTC Check..........................................................6C-8
DTC Clearance ...................................................6C-9
DTC Table ...........................................................6C-9
Visual Inspection ...............................................6C-11
Scan Tool Data .................................................6C-12
P/S System Symptom Diagnosis ......................6C-13
DLC and Its Communication Check (No
communication to P/S Control Module)...........6C-14
“EPS” Warning Light Does Not Come ON with
Ignition Switch Turned ON before Engine
Starts ...............................................................6C-16
“EPS” Warning Light Remains ON Steady
after Engine Starts ..........................................6C-18
DTC C1111 / C1113 / C1115: Torque Sensor
Circuit Failure ..................................................6C-19
DTC C1116: Steering Torque Sensor Power
Supply Circuit ..................................................6C-21
DTC C1121 / C1123 / C1124: Vehicle Speed
Signal Circuit Failure .......................................6C-22
DTC C1122: Engine Speed Signal....................6C-24
DTC C1141 / C1142 / C1143 / C1145: Motor
Circuit Failure ..................................................6C-26
DTC C1153: P/S Control Module Power
Supply Circuit ..................................................6C-27
DTC C1155: P/S Control Module Internal
Failure .............................................................6C-28
P/S Control Module Power Supply and
Ground Circuit Check ......................................6C-29
Inspection of P/S Control Module and Its
Circuits ............................................................6C-30
Steering Wheel Play Check ..............................6C-34
Steering Force Check .......................................6C-34
Repair Instructions ............................................6C-35
Steering Gear Case Assembly Components ....6C-35
Tie-Rod End Boot On-Vehicle Inspection .........6C-36
Tie-Rod End Removal and Installation..............6C-36
Page 866 of 1556
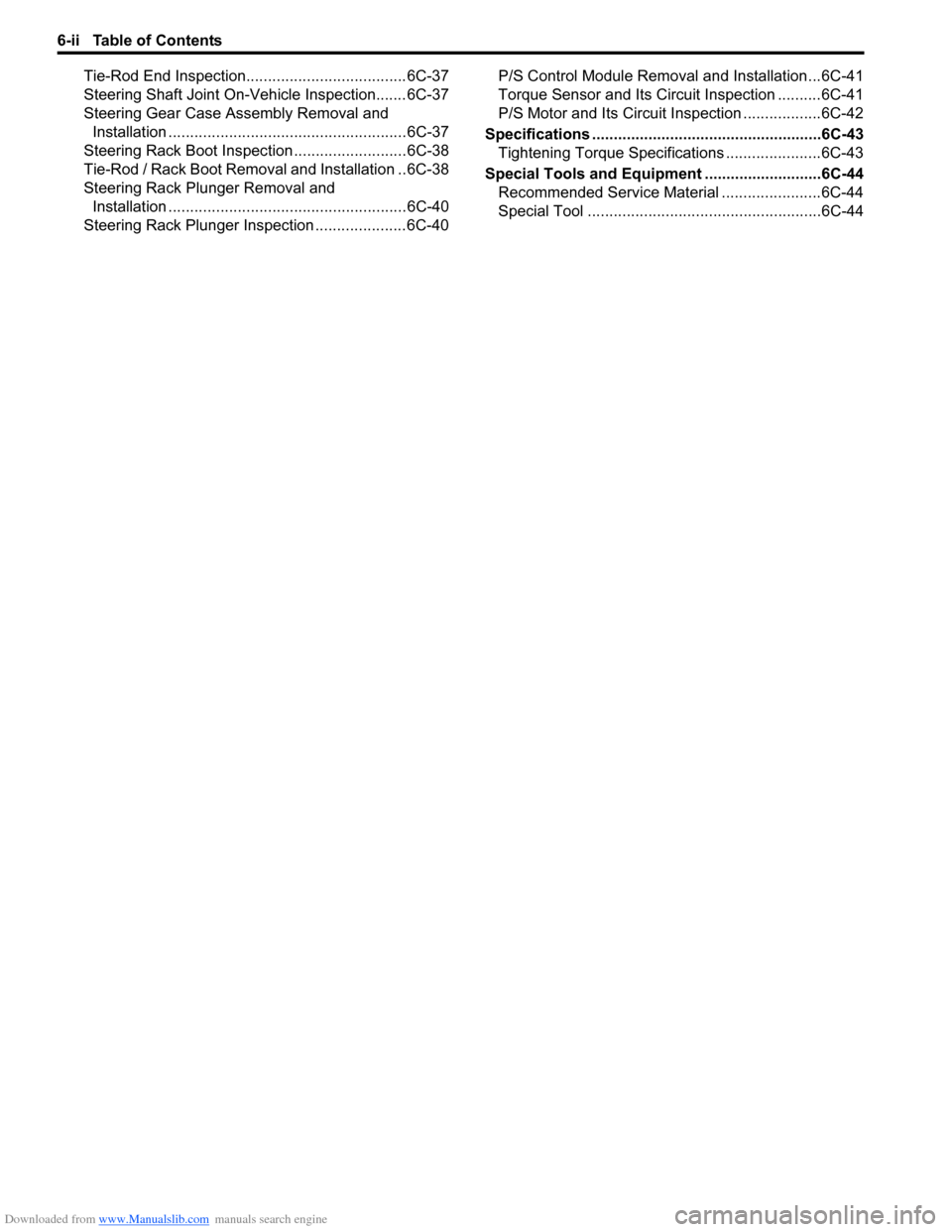
Downloaded from www.Manualslib.com manuals search engine 6-ii Table of Contents
Tie-Rod End Inspection.....................................6C-37
Steering Shaft Joint On-Vehicle Inspection.......6C-37
Steering Gear Case Assembly Removal and
Installation .......................................................6C-37
Steering Rack Boot Inspection ..........................6C-38
Tie-Rod / Rack Boot Removal and Installation ..6C-38
Steering Rack Plunger Removal and
Installation .......................................................6C-40
Steering Rack Plunger Inspection .....................6C-40P/S Control Module Removal and Installation...6C-41
Torque Sensor and Its Circuit Inspection ..........6C-41
P/S Motor and Its Circuit Inspection ..................6C-42
Specifications .....................................................6C-43
Tightening Torque Specifications ......................6C-43
Special Tools and Equipment ...........................6C-44
Recommended Service Material .......................6C-44
Special Tool ......................................................6C-44
Page 882 of 1556
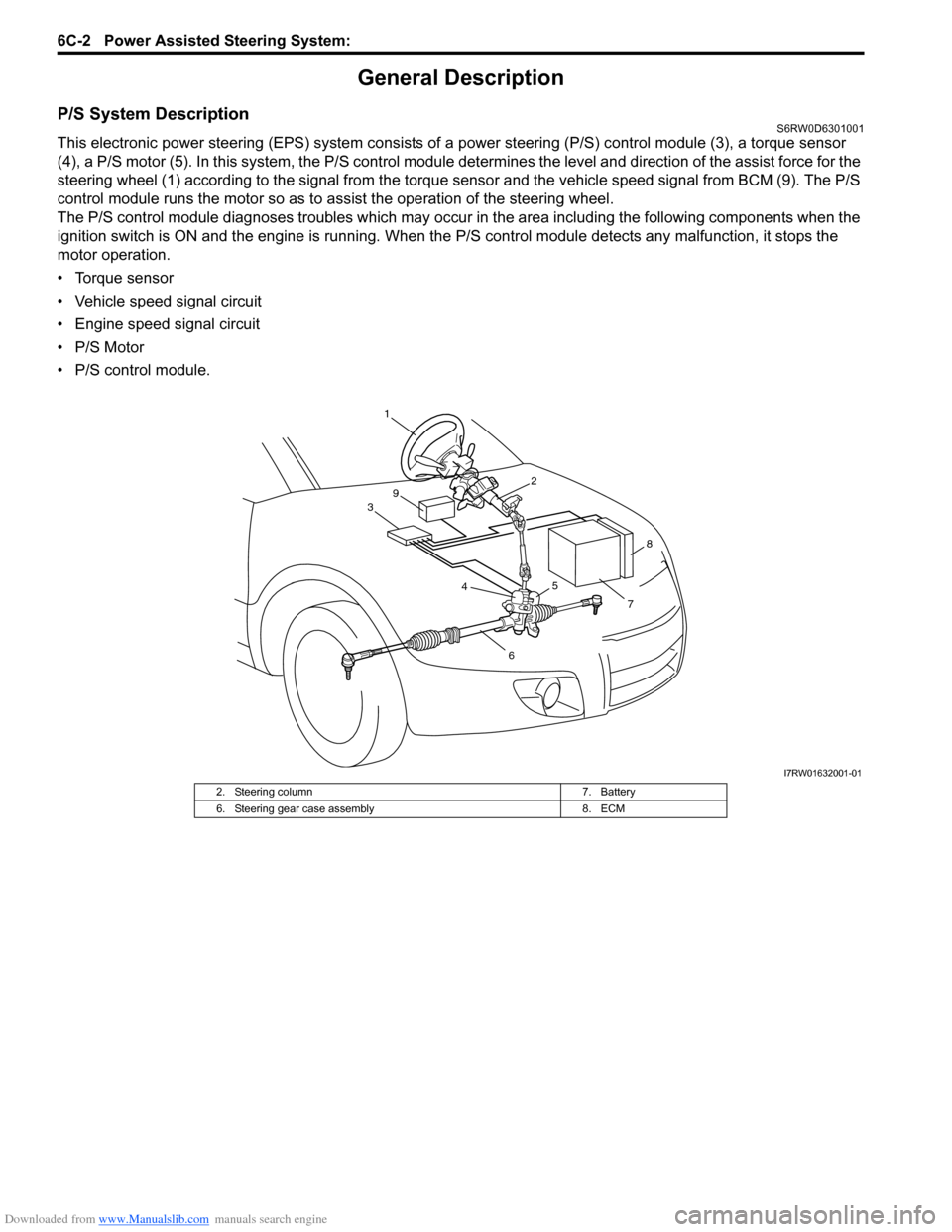
Downloaded from www.Manualslib.com manuals search engine 6C-2 Power Assisted Steering System:
General Description
P/S System DescriptionS6RW0D6301001
This electronic power steering (EPS) system consists of a power steering (P/S) control module (3), a torque sensor
(4), a P/S motor (5). In this system, the P/S control module determines the level and direction of the assist force for the
steering wheel (1) according to the signal from the torque sensor and the vehicle speed signal from BCM (9). The P/S
control module runs the motor so as to assist the operation of the steering wheel.
The P/S control module diagnoses troubles which may occur in the area including the following components when the
ignition switch is ON and the engine is running. When the P/S control module detects any malfunction, it stops the
motor operation.
• Torque sensor
• Vehicle speed signal circuit
• Engine speed signal circuit
• P/S Motor
• P/S control module.
1
32
4
6
7
5
8
9
I7RW01632001-01
2. Steering column 7. Battery
6. Steering gear case assembly 8. ECM
Page 884 of 1556
![SUZUKI SX4 2006 1.G Service Workshop Manual Downloaded from www.Manualslib.com manuals search engine 6C-4 Power Assisted Steering System:
Schematic and Routing Diagram
EPS System Wiring Circuit DiagramS6RW0D6302001
[A]
123
45
3 21
4
567
8
9 11 SUZUKI SX4 2006 1.G Service Workshop Manual Downloaded from www.Manualslib.com manuals search engine 6C-4 Power Assisted Steering System:
Schematic and Routing Diagram
EPS System Wiring Circuit DiagramS6RW0D6302001
[A]
123
45
3 21
4
567
8
9 11](/img/20/7612/w960_7612-883.png)
Downloaded from www.Manualslib.com manuals search engine 6C-4 Power Assisted Steering System:
Schematic and Routing Diagram
EPS System Wiring Circuit DiagramS6RW0D6302001
[A]
123
45
3 21
4
567
8
9 11
10 12 13
141516
17 18 19201
2
[B]
1
2
[C] [D]
10 9 8 7654 3 21
16 15 14 13 12 11
26 25 24 2322 21 20 19 18 17
32 31 30 29 28 27
[F][E]
12
BRN RED/
BLU GRY LT GRN/
BLK
BLK
RED
WHT GRN
BLK
E11-1
E11-5
E11-14
E11-12
[J]:E01-44E01-4
[J]:E01-27E01-26
E12-1
E12-2
E11-10E11-8
E11-9
E11-19
E13-1 GRN
GRY
GRN
WHT
G241-25G241-31
RED/BLK
11
12
1314 3 18
20
21
7 19
4 12
22
12V
E13-2BLK
9V
REDE11-20
12V
12V
E61-2
E61-1
610
55
5V
8
E11-115V
PPL
E11-4
9
23
+BB
BLU/
WHTE04-9
1524YELE11-18E31-5
E31-2
E31-39V
3V
E31-4
E31-1IG11617
C07-25
[H]
[G]
G04-15
[I]:G04-22
25L313-3
[I]
I6RW0D630001-01
[A]: P/S control module connector No.1 “E11” (viewed from harness side) 3. Junction block assembly 15. BCM
[B]: P/S control module connector No.2 “E13” (viewed from harness side) 4. Main fuse 16. Output shaft speed sensor
[C]: P/S control module connector No.3 “E12” (viewed from harness side) 5. Front (left/right) wheel speed sensor 17. TCM
[D]: Combination meter connector “G241” (viewed from harness side) 6. ABS control module 18. Individual circuit fuse box No.1
[E]: Torque sensor connector “E31” (viewed from harness side) 7. Combination meter 19. “IGN” fuse
[F]: Motor connector “E61” (viewed from harness side) 8. “EPS” warning light 20. “P/S” fuse
[G]: M/T model 9. Data link connector (DLC) 21. “IG1 SIG” fuse
[H]: A/T model 10. ECM 22. “MTR” fuse
[I]: Junction block without BCM model (Taiwan model) 11. P/S control module 23. To ABS control module
[J]: M15A engine with 4A/T equipped with slip control model (Hong Kong
model)12. P/S motor 24. To HVAC control module
1. Main fuse box 13. Shield 25. To SDM
2. Ignition switch 14. Torque sensor (built into steering gear case)
Page 885 of 1556
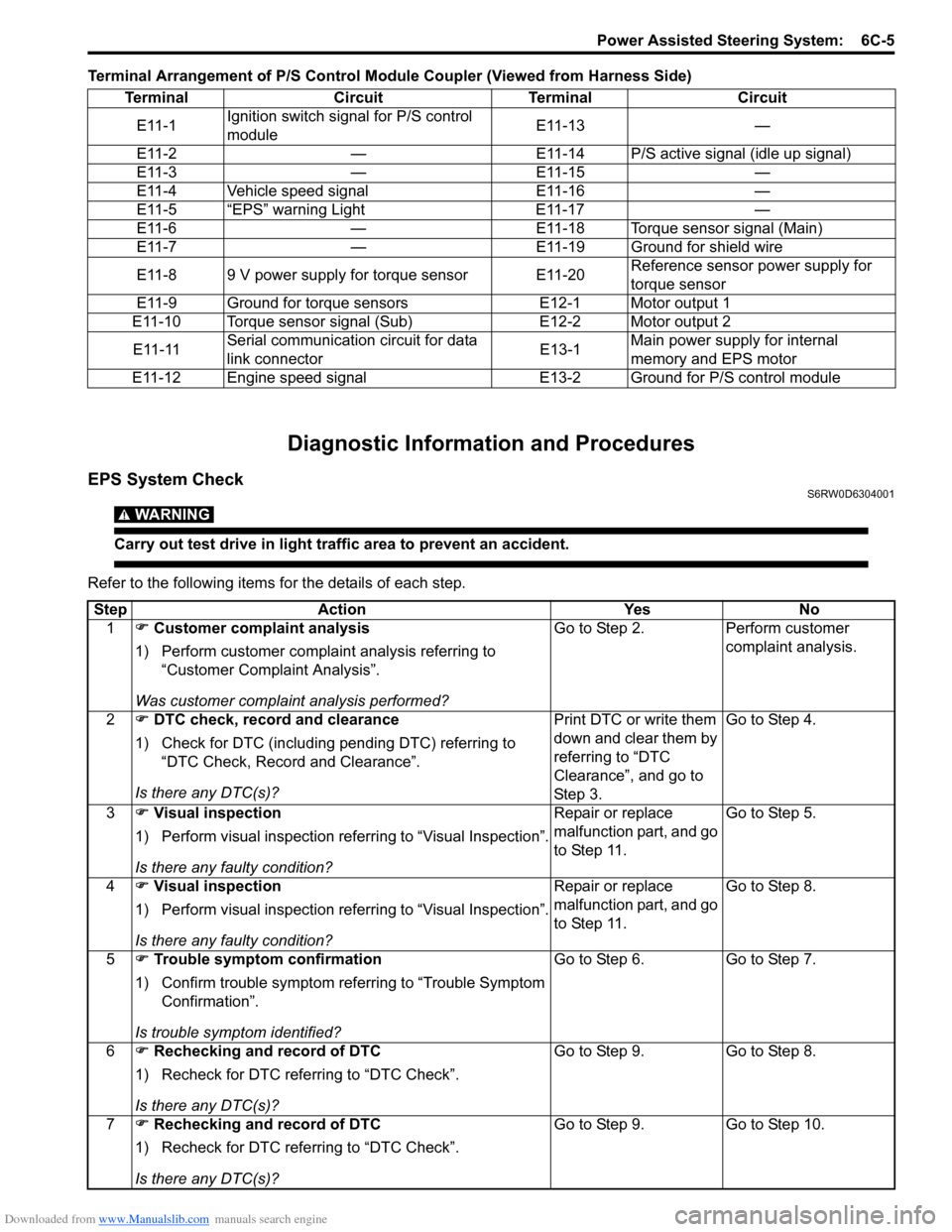
Downloaded from www.Manualslib.com manuals search engine Power Assisted Steering System: 6C-5
Terminal Arrangement of P/S Control Module Coupler (Viewed from Harness Side)
Diagnostic Information and Procedures
EPS System CheckS6RW0D6304001
WARNING!
Carry out test drive in light traffic area to prevent an accident.
Refer to the following items for the details of each step.Terminal Circuit Terminal Circuit
E11-1Ignition switch signal for P/S control
moduleE11-13 —
E11-2 — E11-14 P/S active signal (idle up signal)
E11-3 — E11-15 —
E11-4 Vehicle speed signal E11-16 —
E11-5 “EPS” warning Light E11-17 —
E11-6 — E11-18 Torque sensor signal (Main)
E11-7 — E11-19 Ground for shield wire
E11-8 9 V power supply for torque sensor E11-20Reference sensor power supply for
torque sensor
E11-9 Ground for torque sensors E12-1 Motor output 1
E11-10 Torque sensor signal (Sub) E12-2 Motor output 2
E11-11Serial communication circuit for data
link connectorE13-1Main power supply for internal
memory and EPS motor
E11-12 Engine speed signal E13-2 Ground for P/S control module
Step Action Yes No
1 ) Customer complaint analysis
1) Perform customer complaint analysis referring to
“Customer Complaint Analysis”.
Was customer complaint analysis performed?Go to Step 2. Perform customer
complaint analysis.
2 ) DTC check, record and clearance
1) Check for DTC (including pending DTC) referring to
“DTC Check, Record and Clearance”.
Is there any DTC(s)?Print DTC or write them
down and clear them by
referring to “DTC
Clearance”, and go to
St ep 3 .Go to Step 4.
3 ) Visual inspection
1) Perform visual inspection referring to “Visual Inspection”.
Is there any faulty condition?Repair or replace
malfunction part, and go
to Step 11.Go to Step 5.
4 ) Visual inspection
1) Perform visual inspection referring to “Visual Inspection”.
Is there any faulty condition?Repair or replace
malfunction part, and go
to Step 11.Go to Step 8.
5 ) Trouble symptom confirmation
1) Confirm trouble symptom referring to “Trouble Symptom
Confirmation”.
Is trouble symptom identified?Go to Step 6. Go to Step 7.
6 ) Rechecking and record of DTC
1) Recheck for DTC referring to “DTC Check”.
Is there any DTC(s)?Go to Step 9. Go to Step 8.
7 ) Rechecking and record of DTC
1) Recheck for DTC referring to “DTC Check”.
Is there any DTC(s)?Go to Step 9. Go to Step 10.
Page 888 of 1556
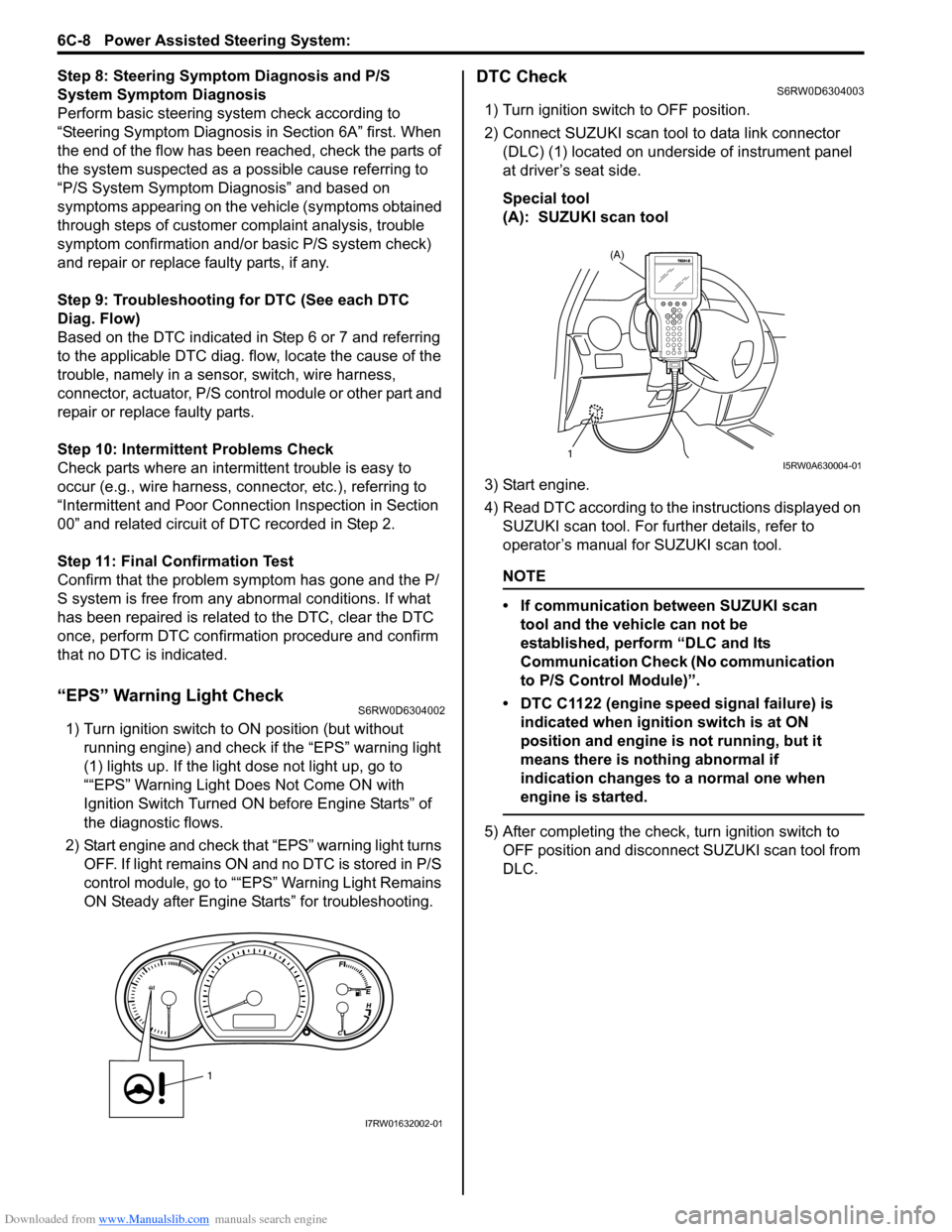
Downloaded from www.Manualslib.com manuals search engine 6C-8 Power Assisted Steering System:
Step 8: Steering Symptom Diagnosis and P/S
System Symptom Diagnosis
Perform basic steering system check according to
“Steering Symptom Diagnosis in Section 6A” first. When
the end of the flow has been reached, check the parts of
the system suspected as a possible cause referring to
“P/S System Symptom Diagnosis” and based on
symptoms appearing on the vehicle (symptoms obtained
through steps of customer complaint analysis, trouble
symptom confirmation and/or basic P/S system check)
and repair or replace faulty parts, if any.
Step 9: Troubleshooting for DTC (See each DTC
Diag. Flow)
Based on the DTC indicated in Step 6 or 7 and referring
to the applicable DTC diag. flow, locate the cause of the
trouble, namely in a sensor, switch, wire harness,
connector, actuator, P/S control module or other part and
repair or replace faulty parts.
Step 10: Intermittent Problems Check
Check parts where an intermittent trouble is easy to
occur (e.g., wire harness, connector, etc.), referring to
“Intermittent and Poor Connection Inspection in Section
00” and related circuit of DTC recorded in Step 2.
Step 11: Final Confirmation Test
Confirm that the problem symptom has gone and the P/
S system is free from any abnormal conditions. If what
has been repaired is related to the DTC, clear the DTC
once, perform DTC confirmation procedure and confirm
that no DTC is indicated.
“EPS” Warning Light CheckS6RW0D6304002
1) Turn ignition switch to ON position (but without
running engine) and check if the “EPS” warning light
(1) lights up. If the light dose not light up, go to
““EPS” Warning Light Does Not Come ON with
Ignition Switch Turned ON before Engine Starts” of
the diagnostic flows.
2) Start engine and check that “EPS” warning light turns
OFF. If light remains ON and no DTC is stored in P/S
control module, go to ““EPS” Warning Light Remains
ON Steady after Engine Starts” for troubleshooting.
DTC CheckS6RW0D6304003
1) Turn ignition switch to OFF position.
2) Connect SUZUKI scan tool to data link connector
(DLC) (1) located on underside of instrument panel
at driver’s seat side.
Special tool
(A): SUZUKI scan tool
3) Start engine.
4) Read DTC according to the instructions displayed on
SUZUKI scan tool. For further details, refer to
operator’s manual for SUZUKI scan tool.
NOTE
• If communication between SUZUKI scan
tool and the vehicle can not be
established, perform “DLC and Its
Communication Check (No communication
to P/S Control Module)”.
• DTC C1122 (engine speed signal failure) is
indicated when ignition switch is at ON
position and engine is not running, but it
means there is nothing abnormal if
indication changes to a normal one when
engine is started.
5) After completing the check, turn ignition switch to
OFF position and disconnect SUZUKI scan tool from
DLC.
1
I7RW01632002-01
(A)
1I5RW0A630004-01
Page 889 of 1556
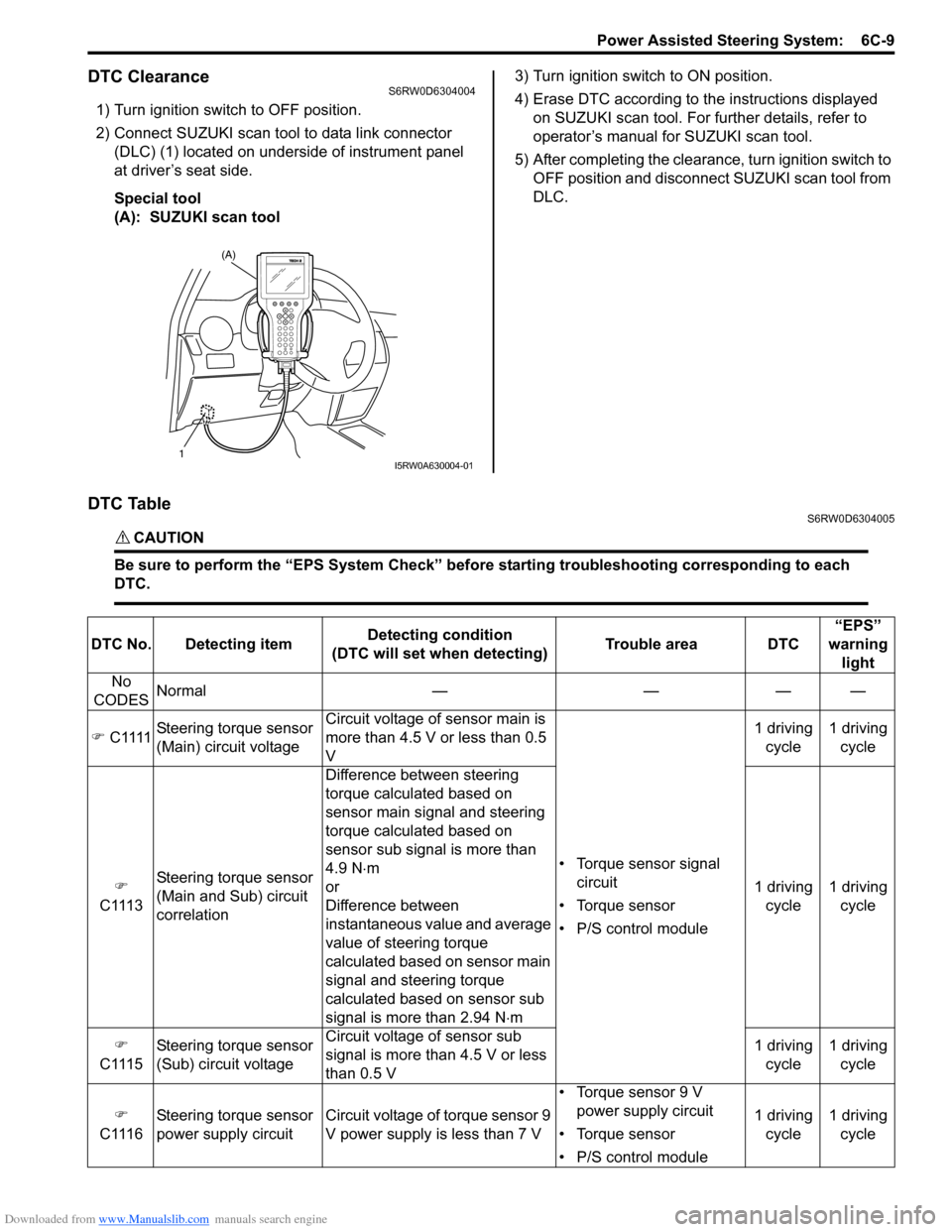
Downloaded from www.Manualslib.com manuals search engine Power Assisted Steering System: 6C-9
DTC ClearanceS6RW0D6304004
1) Turn ignition switch to OFF position.
2) Connect SUZUKI scan tool to data link connector
(DLC) (1) located on underside of instrument panel
at driver’s seat side.
Special tool
(A): SUZUKI scan tool3) Turn ignition switch to ON position.
4) Erase DTC according to the instructions displayed
on SUZUKI scan tool. For further details, refer to
operator’s manual for SUZUKI scan tool.
5) After completing the clearance, turn ignition switch to
OFF position and disconnect SUZUKI scan tool from
DLC.
DTC TableS6RW0D6304005
CAUTION!
Be sure to perform the “EPS System Check” before starting troubleshooting corresponding to each
DTC.
(A)
1I5RW0A630004-01
DTC No. Detecting itemDetecting condition
(DTC will set when detecting)Trouble area DTC“EPS”
warning
light
No
CODESNormal — — — —
) C1111Steering torque sensor
(Main) circuit voltageCircuit voltage of sensor main is
more than 4.5 V or less than 0.5
V
• Torque sensor signal
circuit
• Torque sensor
• P/S control module1 driving
cycle1 driving
cycle
)
C1113Steering torque sensor
(Main and Sub) circuit
correlationDifference between steering
torque calculated based on
sensor main signal and steering
torque calculated based on
sensor sub signal is more than
4.9 N⋅m
or
Difference between
instantaneous value and average
value of steering torque
calculated based on sensor main
signal and steering torque
calculated based on sensor sub
signal is more than 2.94 N⋅m1 driving
cycle1 driving
cycle
)
C1115Steering torque sensor
(Sub) circuit voltageCircuit voltage of sensor sub
signal is more than 4.5 V or less
than 0.5 V1 driving
cycle1 driving
cycle
)
C1116Steering torque sensor
power supply circuit Circuit voltage of torque sensor 9
V power supply is less than 7 V• Torque sensor 9 V
power supply circuit
• Torque sensor
• P/S control module1 driving
cycle1 driving
cycle