TOYOTA AVENSIS 2005 Service Repair Manual
Manufacturer: TOYOTA, Model Year: 2005, Model line: AVENSIS, Model: TOYOTA AVENSIS 2005Pages: 5135, PDF Size: 95.28 MB
Page 4901 of 5135
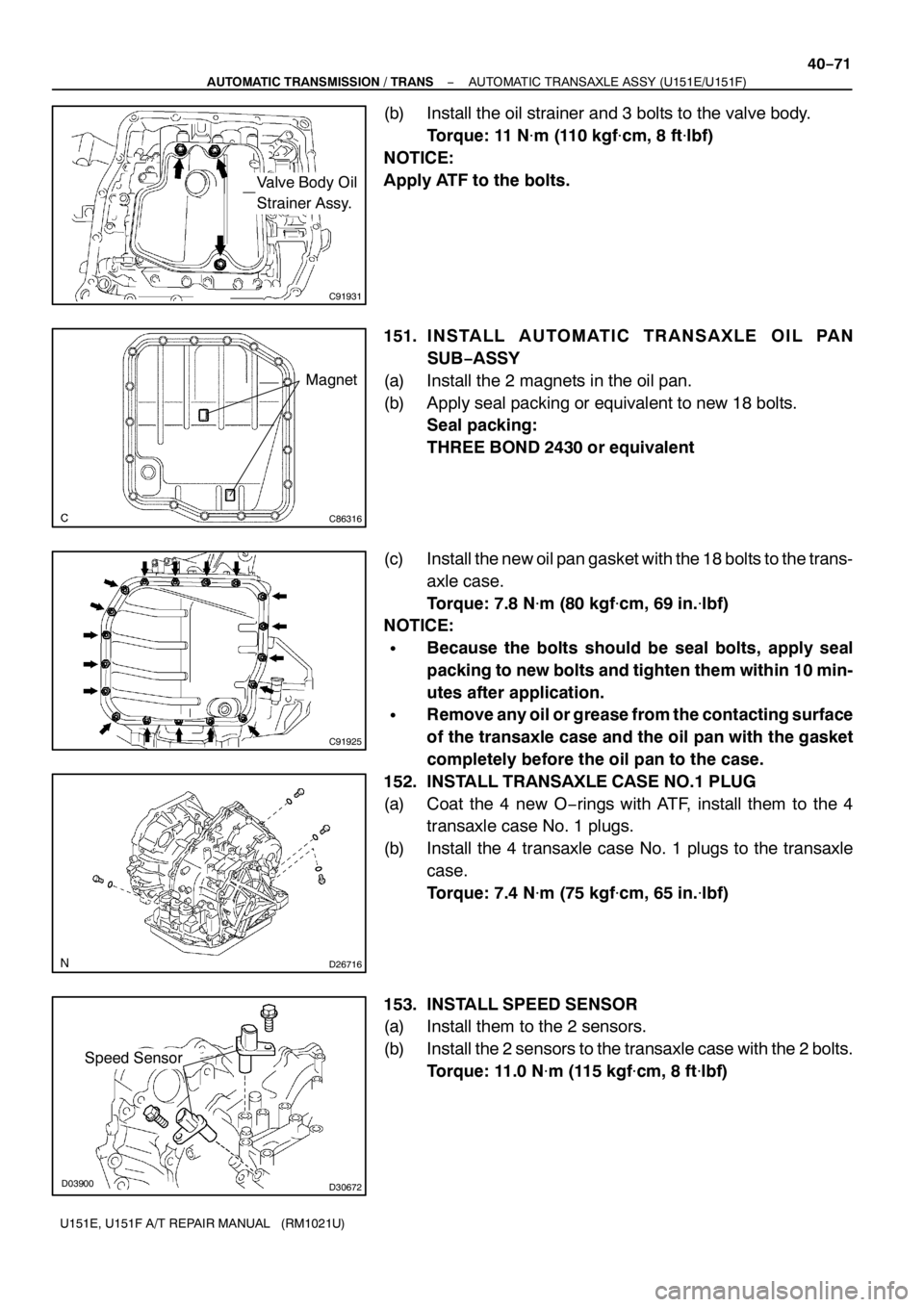
C91931
Valve Body Oil
Strainer Assy.
C86316
Magnet
C91925
D26716
D03900D30672
Speed Sensor
− AUTOMATIC TRANSMISSION / TRANSAUTOMATIC TRANSAXLE ASSY (U151E/U151F)
40−71
U151E, U151F A/T REPAIR MANUAL (RM1021U)
(b) Install the oil strainer and 3 bolts to the valve body.
Torque:11Nm(110 kgfcm, 8 ftlbf)
NOTICE:
Apply ATF to the bolts.
151. INSTALL AUTOMATIC TRANSAXLE OIL PAN
SUB−ASSY
(a) Install the 2 magnets in the oil pan.
(b) Apply seal packing or equivalent to new 18 bolts.
Seal packing:
THREE BOND 2430 or equivalent
(c) Install the new oil pan gasket with the 18 bolts to the trans-
axle case.
Torque: 7.8 Nm (80 kgfcm, 69 in.lbf)
NOTICE:
SBecause the bolts should be seal bolts, apply seal
packing to new bolts and tighten them within10 min-
utes after application.
SRemove any oil or grease from the contacting surface
of the transaxle case and the oil pan with the gasket
completely before the oil pan to the case.
152. INSTALL TRANSAXLE CASE NO.1PLUG
(a) Coat the 4 new O−rings with ATF, install them to the 4
transaxle case No. 1 plugs.
(b) Install the 4 transaxle case No. 1 plugs to the transaxle
case.
Torque: 7.4 Nm (75 kgfcm, 65 in.lbf)
153. INSTALL SPEED SENSOR
(a) Install them to the 2 sensors.
(b) Install the 2 sensors to the transaxle case with the 2 bolts.
Torque:11.0 Nm(115 kgfcm, 8 ftlbf)
Page 4902 of 5135
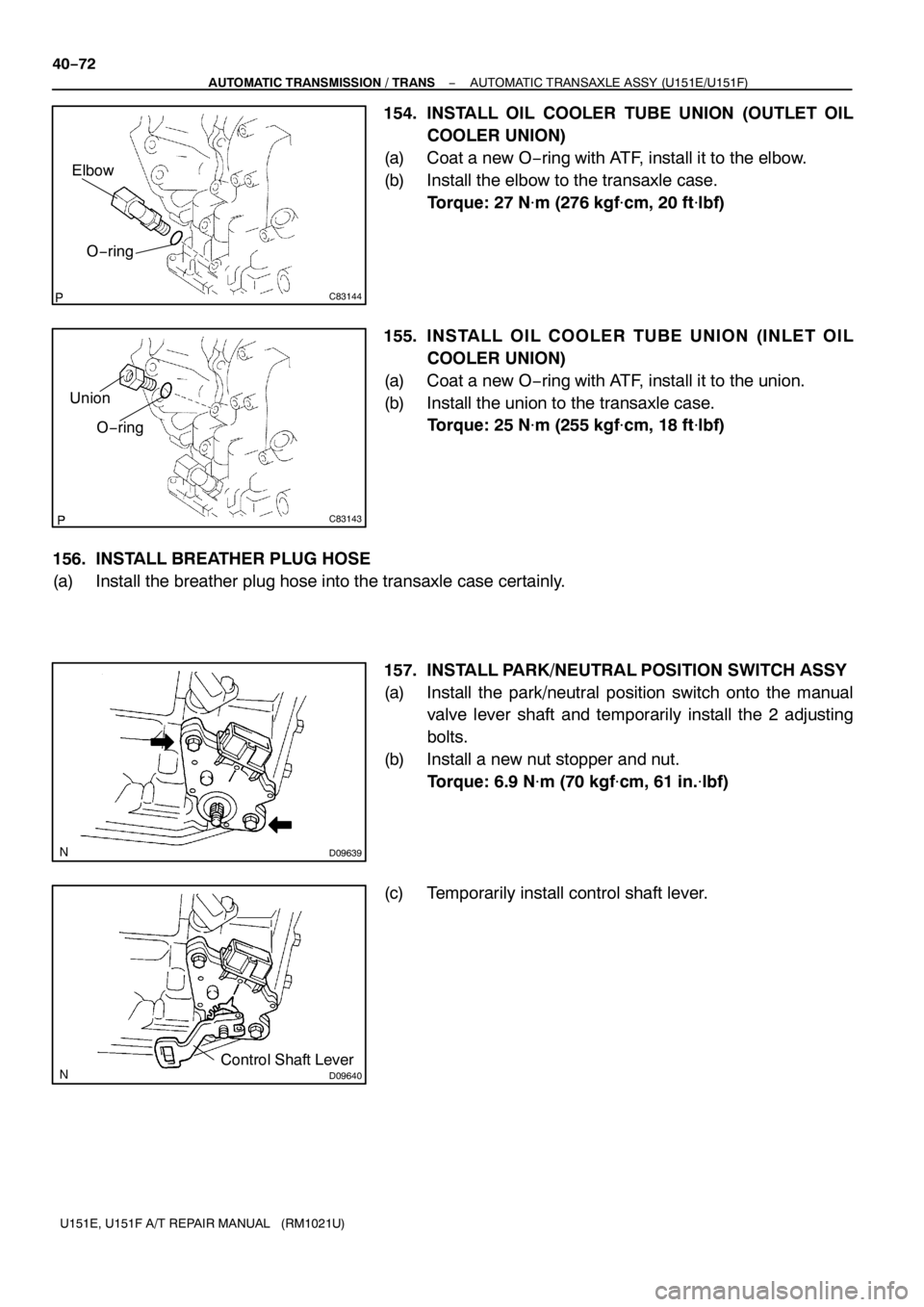
C83144
Elbow
O−ring
C83143
Union
O−ring
D09639
D09640Control Shaft Lever
40−72
− AUTOMATIC TRANSMISSION / TRANSAUTOMATIC TRANSAXLE ASSY (U151E/U151F)
U151E, U151F A/T REPAIR MANUAL (RM1021U)
154. INSTALL OIL COOLER TUBE UNION (OUTLET OIL
COOLER UNION)
(a) Coat a new O−ring with ATF, install it to the elbow.
(b) Install the elbow to the transaxle case.
Torque: 27 Nm (276 kgfcm, 20 ftlbf)
155. INSTALL OIL COOLER TUBE UNION (INLET OIL
COOLER UNION)
(a) Coat a new O−ring with ATF, install it to the union.
(b) Install the union to the transaxle case.
Torque: 25 Nm (255 kgfcm,18ftlbf)
156. INSTALL BREATHER PLUG HOSE
(a) Install the breather plug hose into the transaxle case certainly.
157. INSTALL PARK/NEUTRAL POSITION SWITCH ASSY
(a) Install the park/neutral position switch onto the manual
valve lever shaft and temporarily install the 2 adjusting
bolts.
(b) Install a new nut stopper and nut.
Torque: 6.9 Nm (70 kgfcm, 61in.lbf)
(c) Temporarily install control shaft lever.
Page 4903 of 5135
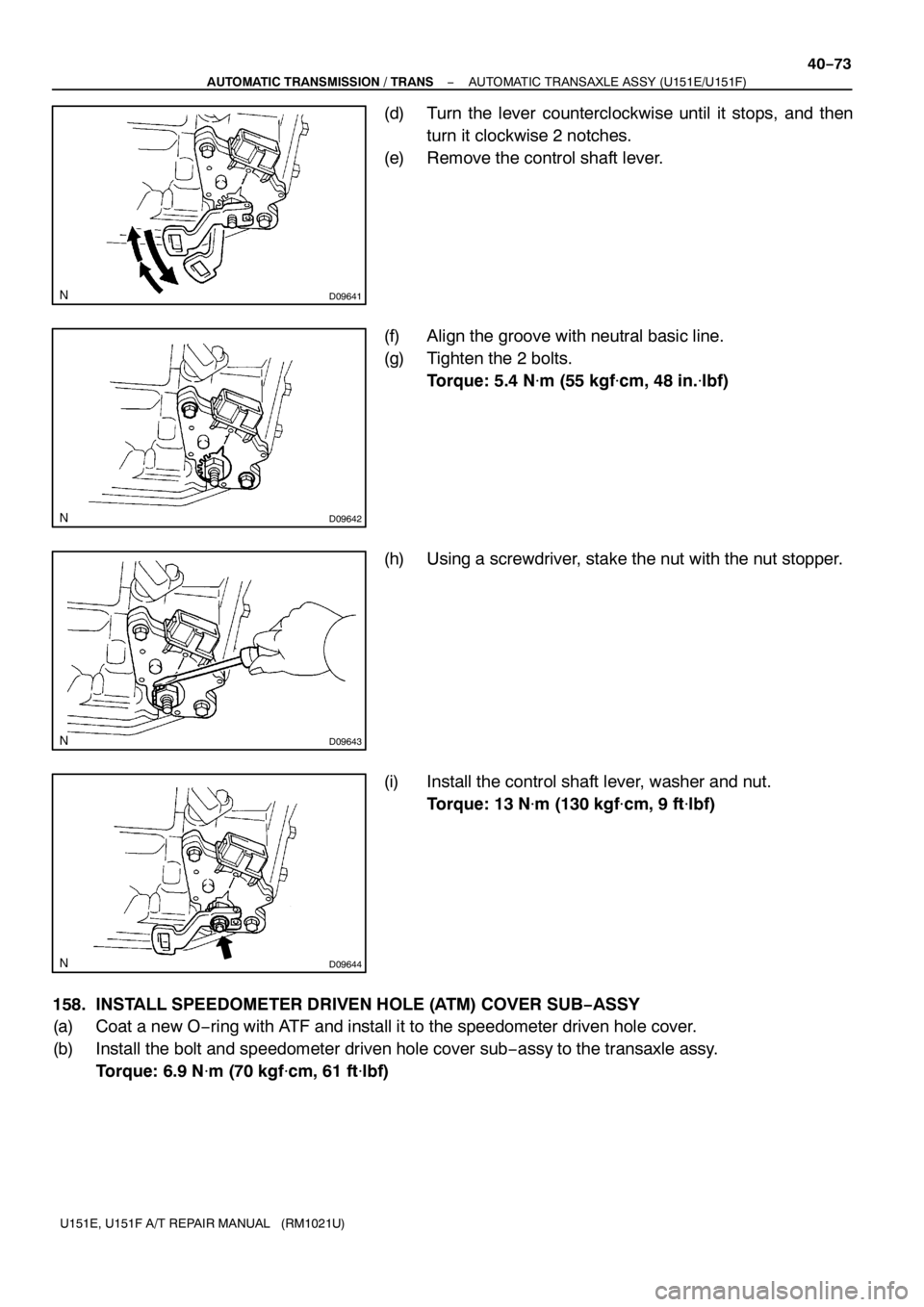
D09641
D09642
D09643
D09644
− AUTOMATIC TRANSMISSION / TRANSAUTOMATIC TRANSAXLE ASSY (U151E/U151F)
40−73
U151E, U151F A/T REPAIR MANUAL (RM1021U)
(d) Turn the lever counterclockwise until it stops, and then
turn it clockwise 2 notches.
(e) Remove the control shaft lever.
(f) Align the groove with neutral basic line.
(g) Tighten the 2 bolts.
Torque: 5.4 Nm (55 kgfcm, 48 in.lbf)
(h) Using a screwdriver, stake the nut with the nut stopper.
(i) Install the control shaft lever, washer and nut.
Torque:13Nm(130 kgfcm, 9 ftlbf)
158. INSTALL SPEEDOMETER DRIVEN HOLE (ATM) COVER SUB−ASSY
(a) Coat a new O−ring with ATF and install it to the speedometer driven hole cover.
(b) Install the bolt and speedometer driven hole cover sub−assy to the transaxle assy.
Torque: 6.9 Nm (70 kgfcm, 61ftlbf)
Page 4904 of 5135
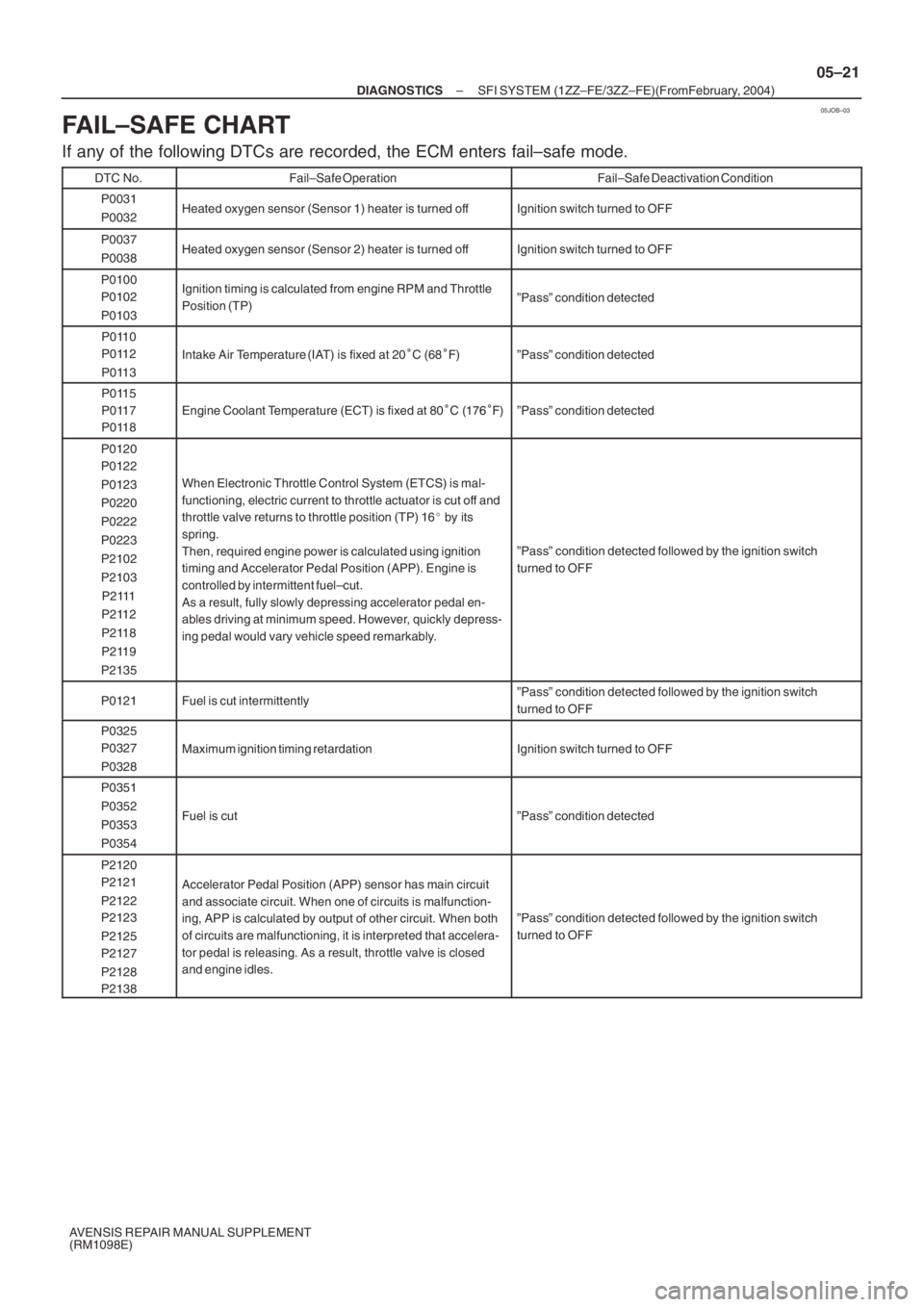
05JOB–03
– DIAGNOSTICSSFI SYSTEM (1ZZ–FE/3ZZ–FE)(From February, 2004)
05–21
AVENSIS REPAIR MANUAL SUPPLEMENT
(RM1098E)
FAIL–SAFE CHART
If any of the following DTCs are recorded, the ECM enters fail–safe mode.
DTC No.Fail–Safe OperationFail–Safe Deactivation Condition
P0031
P0032Heated oxygen sensor (Sensor 1) heater is turned offIgnition switch turned to OFF
P0037
P0038Heated oxygen sensor (Sensor 2) heater is turned offIgnition switch turned to OFF
P0100
P0102
P0103Ignition timing is calculated from engine RPM and Throttle
Position (TP)”Pass” condition detected
P0110
P0112
P0113
Intake Air Temperature (IAT) is fixed at 20C (68F)”Pass” condition detected
P0115
P0117
P0118
Engine Coolant Temperature (ECT) is fixed at 80 ”Pass” condition detected
P0120
P0122
P0123
P0220
P0222
P0223
P2102
P2103
P2111
P2112
P2118
P2119
P2135
When Electronic Throttle Control System (ETCS) is mal-
functioning, electric current to throttle actuator is cut off and
throttle valve returns to throttle position (TP) 16 by its
spring.
Then, required engine power is calculated using ignition
timing and Accelerator Pedal Position (APP). Engine is
controlled by intermittent fuel–cut.
As a result, fully slowly depressing accelerator pedal en-
ables driving at minimum speed. However, quickly depress-
ing pedal would vary vehicle speed remarkably.
”Pass” condition detected followed by the ignition switch
turned to OFF
P0121Fuel is cut intermittently”Pass” condition detected followed by the ignition switch
turned to OFF
P0325
P0327
P0328
Maximum ignition timing retardationIgnition switch turned to OFF
P0351
P0352
P0353
P0354
Fuel is cut”Pass” condition detected
P2120
P2121
P2122
P2123
P2125
P2127
P2128
P2138
Accelerator Pedal Position (APP) sensor has main circuit
and associate circuit. When one of circuits is malfunction-
ing, APP is calculated by output of other circuit. When both
of circuits are malfunctioning, it is interpreted that accelera-
tor pedal is releasing. As a result, throttle valve is closed
and engine idles.
”Pass” condition detected followed by the ignition switch
turned to OFF
Page 4905 of 5135
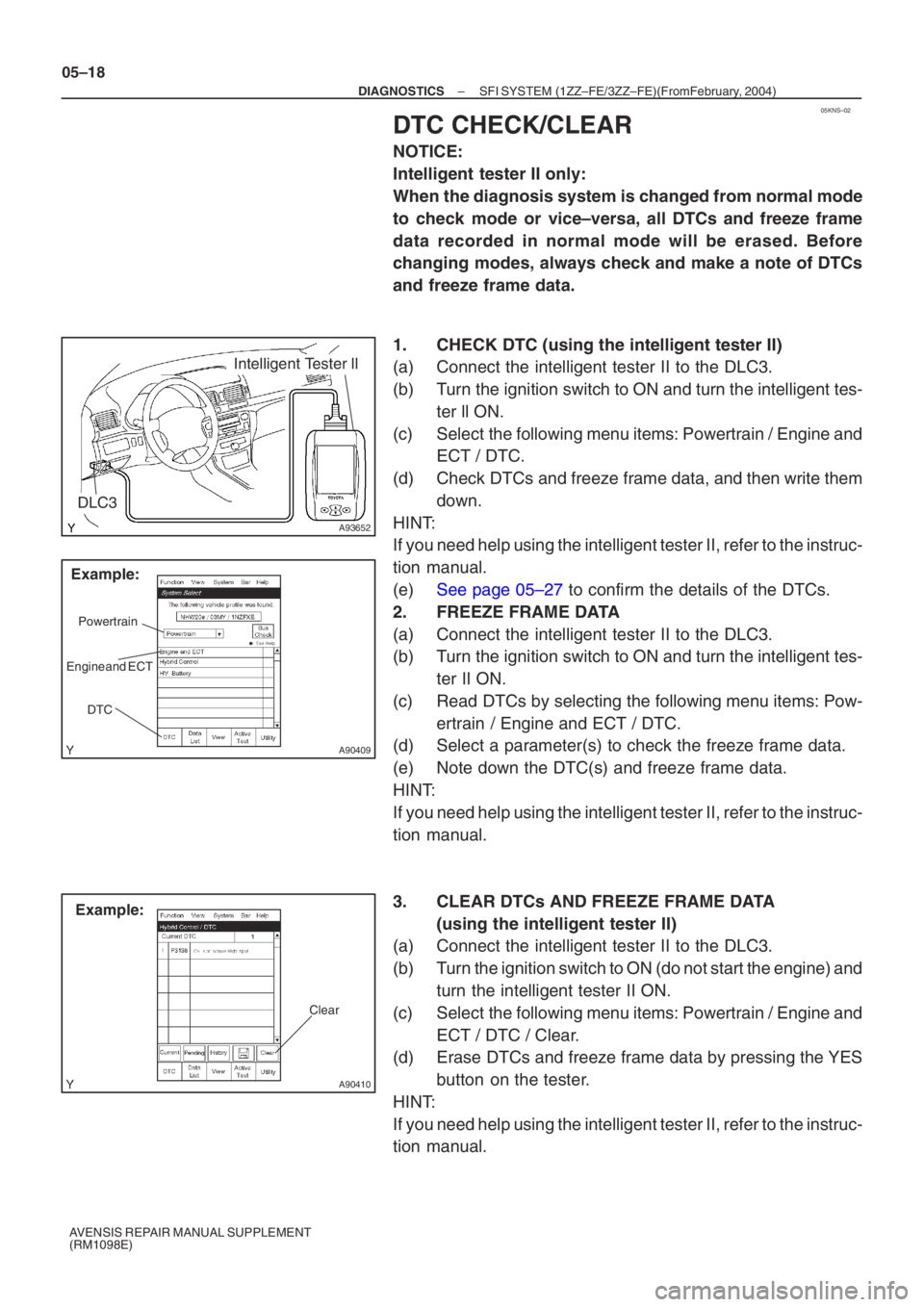
05KNS–02
A93652
DLC3
Intelligent Tester ll
A90409
Powertrain
Engine and ECT DTC
Example:
A90410
Clear
Example:
05–18
–
DIAGNOSTICS SFI SYSTEM (1ZZ–FE/3ZZ–FE)(From February, 2004)
AVENSIS REPAIR MANUAL SUPPLEMENT
(RM1098E)
DTC CHECK/CLEAR
NOTICE:
Intelligent tester II only:
When the diagnosis system is changed from normal mode
to check mode or vice–versa, all DTCs and freeze frame
data recorded in normal mode will be er ased. Before
changing modes, always check and make a note of DTCs
and freeze frame data.
1. CHECK DTC (using the intelligent tester II)
(a) Connect the intelligent tester II to the DLC3.
(b) Turn the ignition switch to ON and turn the intelligent tes-
ter ll ON.
(c) Select the following menu items: Powertrain / Engine and ECT / DTC.
(d) Check DTCs and freeze frame data, and then write them down.
HINT:
If you need help using the intelligent tester II, refer to the instruc-
tion manual.
(e) See page 05–27 to confirm the details of the DTCs.
2. FREEZE FRAME DATA
(a) Connect the intelligent tester II to the DLC3.
(b) Turn the ignition switch to ON and turn the intelligent tes- ter II ON.
(c) Read DTCs by selecting the following menu items: Pow- ertrain / Engine and ECT / DTC.
(d) Select a parameter(s) to check the freeze frame data.
(e) Note down the DTC(s) and freeze frame data.
HINT:
If you need help using the intelligent tester II, refer to the instruc-
tion manual.
3. CLEAR DTCs AND FREEZE FRAME DATA
(using the intelligent tester II)
(a) Connect the intelligent tester II to the DLC3.
(b) Turn the ignition switch to ON (do not start the engine) and
turn the intelligent tester II ON.
(c) Select the following menu items: Powertrain / Engine and ECT / DTC / Clear.
(d) Erase DTCs and freeze frame data by pressing the YES
button on the tester.
HINT:
If you need help using the intelligent tester II, refer to the instruc-
tion manual.
Page 4906 of 5135
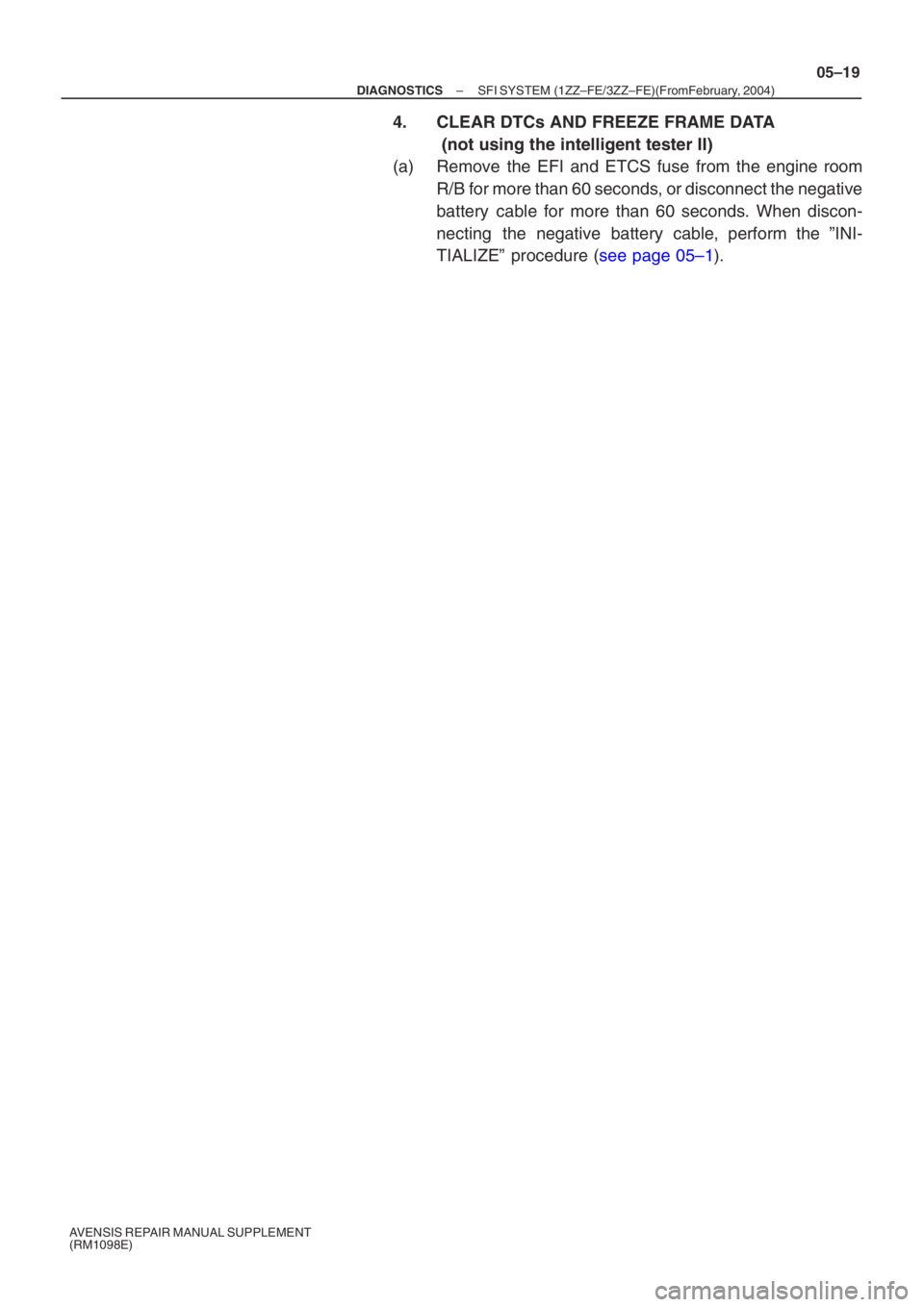
–
DIAGNOSTICS SFI SYSTEM (1ZZ–FE/3ZZ–FE)(From February, 2004)
05–19
AVENSIS REPAIR MANUAL SUPPLEMENT
(RM1098E)
4. CLEAR DTCs AND FREEZE FRAME DATA
(not using the intelligent tester II)
(a) Remove the EFI and ETCS fuse from the engine room
R/B for more than 60 seconds, or disconnect the negative
battery cable for more than 60 seconds. When discon-
necting the negative battery cable, perform the ”INI-
TIALIZE” procedure ( see page 05–1 ).
Page 4907 of 5135
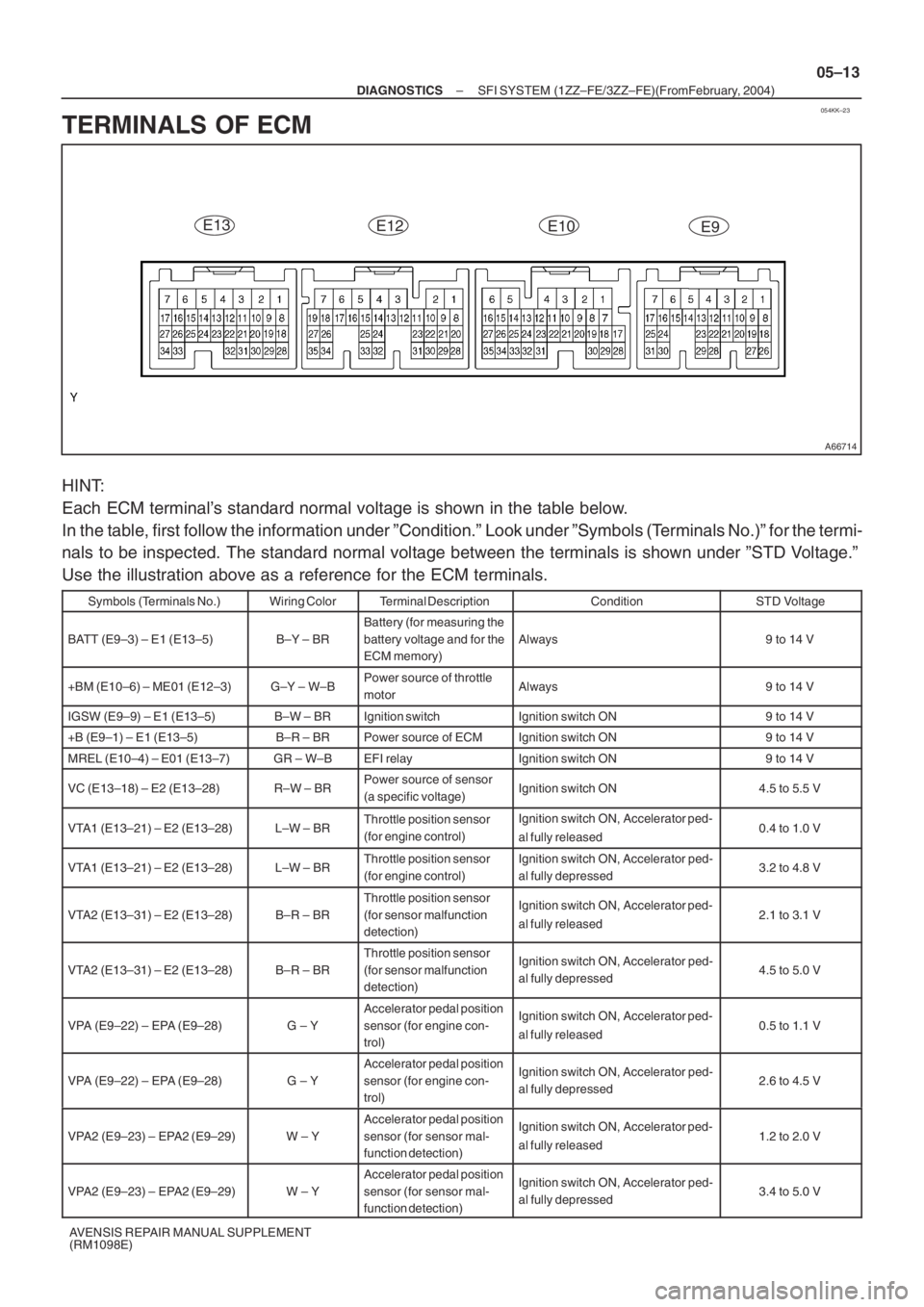
054KK–23
A66714
E13
E12
E10
E9
– DIAGNOSTICSSFI SYSTEM (1ZZ–FE/3ZZ–FE)(From February, 2004)
05–13
AVENSIS REPAIR MANUAL SUPPLEMENT
(RM1098E)
TERMINALS OF ECM
HINT:
Each ECM terminal’s standard normal voltage is shown in the table below.
In the table, first follow the information under ”Condition.” Look under ”Symbols (Terminals No.)” for the termi-
nals to be inspected. The standard normal voltage between the terminals is shown under ”STD Voltage.”
Use the illustration above as a reference for the ECM terminals.
Symbols (Terminals No.)Wiring ColorTerminal DescriptionConditionSTD Voltage
BATT (E9–3) – E1 (E13–5)B–Y – BR
Battery (for measuring the
battery voltage and for the
ECM memory)
Always9 to 14 V
+BM (E10–6) – ME01 (E12–3)G–Y – W–BPower source of throttle
motorAlways9 to 14 V
IGSW (E9–9) – E1 (E13–5)B–W – BRIgnition switchIgnition switch ON9 to 14 V
+B (E9–1) – E1 (E13–5)B–R – BRPower source of ECMIgnition switch ON9 to 14 V
MREL (E10–4) – E01 (E13–7)GR – W–BEFI relayIgnition switch ON9 to 14 V
VC (E13–18) – E2 (E13–28)R–W – BRPower source of sensor
(a specific voltage)Ignition switch ON4.5 to 5.5 V
VTA1 (E13–21) – E2 (E13–28)L–W – BRThrottle position sensor
(for engine control)Ignition switch ON, Accelerator ped-
al fully released0.4 to 1.0 V
VTA1 (E13–21) – E2 (E13–28)L–W – BRThrottle position sensor
(for engine control)Ignition switch ON, Accelerator ped-
al fully depressed3.2 to 4.8 V
VTA2 (E13–31) – E2 (E13–28)B–R – BR
Throttle position sensor
(for sensor malfunction
detection)Ignition switch ON, Accelerator ped-
al fully released2.1 to 3.1 V
VTA2 (E13–31) – E2 (E13–28)B–R – BR
Throttle position sensor
(for sensor malfunction
detection)Ignition switch ON, Accelerator ped-
al fully depressed4.5 to 5.0 V
VPA (E9–22) – EPA (E9–28)G – Y
Accelerator pedal position
sensor (for engine con-
trol)Ignition switch ON, Accelerator ped-
al fully released0.5 to 1.1 V
VPA (E9–22) – EPA (E9–28)G – Y
Accelerator pedal position
sensor (for engine con-
trol)Ignition switch ON, Accelerator ped-
al fully depressed2.6 to 4.5 V
VPA2 (E9–23) – EPA2 (E9–29)W – Y
Accelerator pedal position
sensor (for sensor mal-
function detection)Ignition switch ON, Accelerator ped-
al fully released1.2 to 2.0 V
VPA2 (E9–23) – EPA2 (E9–29)W – Y
Accelerator pedal position
sensor (for sensor mal-
function detection)Ignition switch ON, Accelerator ped-
al fully depressed3.4 to 5.0 V
Page 4908 of 5135
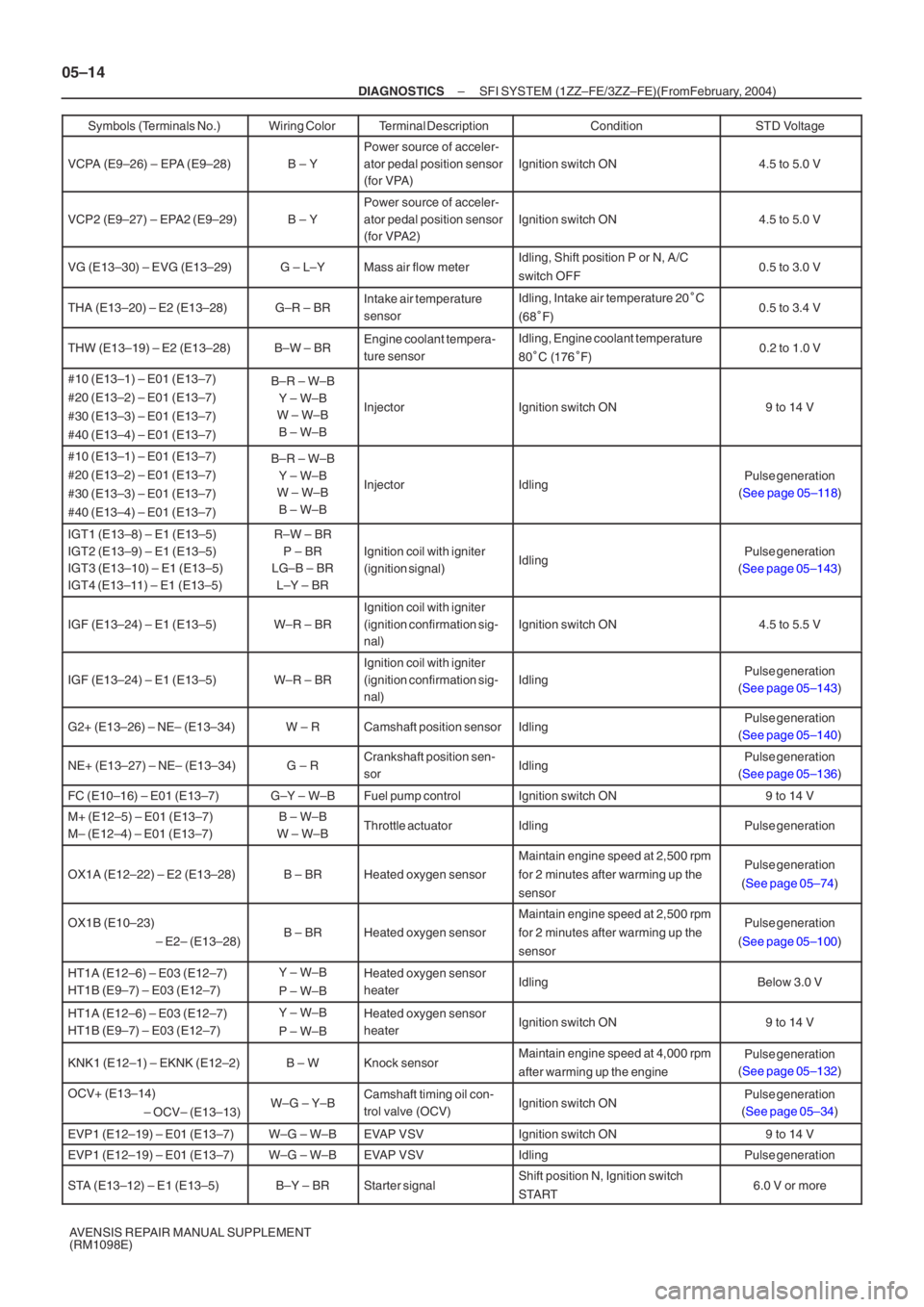
05–14
–
DIAGNOSTICS SFI SYSTEM (1ZZ–FE/3ZZ–FE)(From February, 2004)
AVENSIS REPAIR MANUAL SUPPLEMENT
(RM1098E) Symbols (Terminals No.)
STD Voltage
Condition
Terminal Description
Wiring Color
VCPA (E9–26) – EPA (E9–28)B – Y
Power source of acceler-
ator pedal position sensor
(for VPA)
Ignition switch ON4.5 to 5.0 V
VCP2 (E9–27) – EPA2 (E9–29)B – Y
Power source of acceler-
ator pedal position sensor
(for VPA2)
Ignition switch ON4.5 to 5.0 V
VG (E13–30) – EVG (E13–29)G – L–YMass air flow meterIdling, Shift position P or N, A/C
switch OFF0.5 to 3.0 V
THA (E13–20) – E2 (E13–28)G–R – BRIntake air temperature
sensorIdling, Intake air temperature 20 C
(68 F)0.5 to 3.4 V
THW (E13–19) – E2 (E13–28)B–W – BREngine coolant tempera-
ture sensorIdling, Engine coolant temperature
80 \b0.2 to 1.0 V
#10 (E13–1) – E01 (E13–7)
#20 (E13–2) – E01 (E13–7)
#30 (E13–3) – E01 (E13–7)
#40 (E13–4) – E01 (E13–7)B–R – W–B
Y – W–B
W – W–B
B – W–B
InjectorIgnition switch ON9 to 14 V
#10 (E13–1) – E01 (E13–7)
#20 (E13–2) – E01 (E13–7)
#30 (E13–3) – E01 (E13–7)
#40 (E13–4) – E01 (E13–7)B–R – W–B Y – W–B
W – W–B
B – W–B
InjectorIdlingPulse generation
( See page 05– 118 )
IGT1 (E13–8) – E1 (E13–5)
IGT2 (E13–9) – E1 (E13–5)
IGT3 (E13–10) – E1 (E13–5)
IGT4 (E13–11) – E1 (E13–5)R–W – BR
P – BR
LG–B – BR
L–Y – BR
Ignition coil with igniter
(ignition signal)IdlingPulse generation
( See page 05–143 )
IGF (E13–24) – E1 (E13–5)W–R – BR
Ignition coil with igniter
(ignition confirmation sig-
nal)
Ignition switch ON4.5 to 5.5 V
IGF (E13–24) – E1 (E13–5)W–R – BR
Ignition coil with igniter
(ignition confirmation sig-
nal)
IdlingPulse generation
( See page 05–143 )
G2+ (E13–26) – NE– (E13–34)W – RCamshaft position sensorIdlingPulse generation
( See page 05–140 )
NE+ (E13–27) – NE– (E13–34)G – RCrankshaft position sen-
sorIdlingPulse generation
( See page 05–136 )
FC (E10–16) – E01 (E13–7)G–Y – W–BFuel pump controlIgnition switch ON9 to 14 V
M+ (E12–5) – E01 (E13–7)
M– (E12–4) – E01 (E13–7)B – W–B
W – W–BThrottle actuatorIdlingPulse generation
OX1A (E12–22) – E2 (E13–28)B – BRHeated oxygen sensor
Maintain engine speed at 2,500 rpm
for 2 minutes after warming up the
sensorPulse generation
( See page 05–74 )
OX1B (E10–23)
– E2– (E13–28)B – BRHeated oxygen sensor
Maintain engine speed at 2,500 rpm
for 2 minutes after warming up the
sensorPulse generation
( See page 05–100 )
HT1A (E12–6) – E03 (E12–7)
HT1B (E9–7) – E03 (E12–7)Y – W–B
P – W–BHeated oxygen sensor
heaterIdlingBelow 3.0 V
HT1A (E12–6) – E03 (E12–7)
HT1B (E9–7) – E03 (E12–7)Y – W–B
P – W–BHeated oxygen sensor
heaterIgnition switch ON9 to 14 V
KNK1 (E12–1) – EKNK (E12–2)B – WKnock sensorMaintain engine speed at 4,000 rpm
after warming up the enginePulse generation
( See page 05–132 )
OCV+ (E13–14)
– OCV– (E13–13)W–G – Y–BCamshaft timing oil con-
trol valve (OCV)Ignition switch ONPulse generation
( See page 05–34 )
EVP1 (E12–19) – E01 (E13–7)W–G – W–BEVAP VSVIgnition switch ON9 to 14 V
EVP1 (E12–19) – E01 (E13–7)W–G – W–BEVAP VSVIdlingPulse generation
STA (E13–12) – E1 (E13–5)B–Y – BRStarter signalShift position N, Ignition switch
START6.0 V or more
Page 4909 of 5135
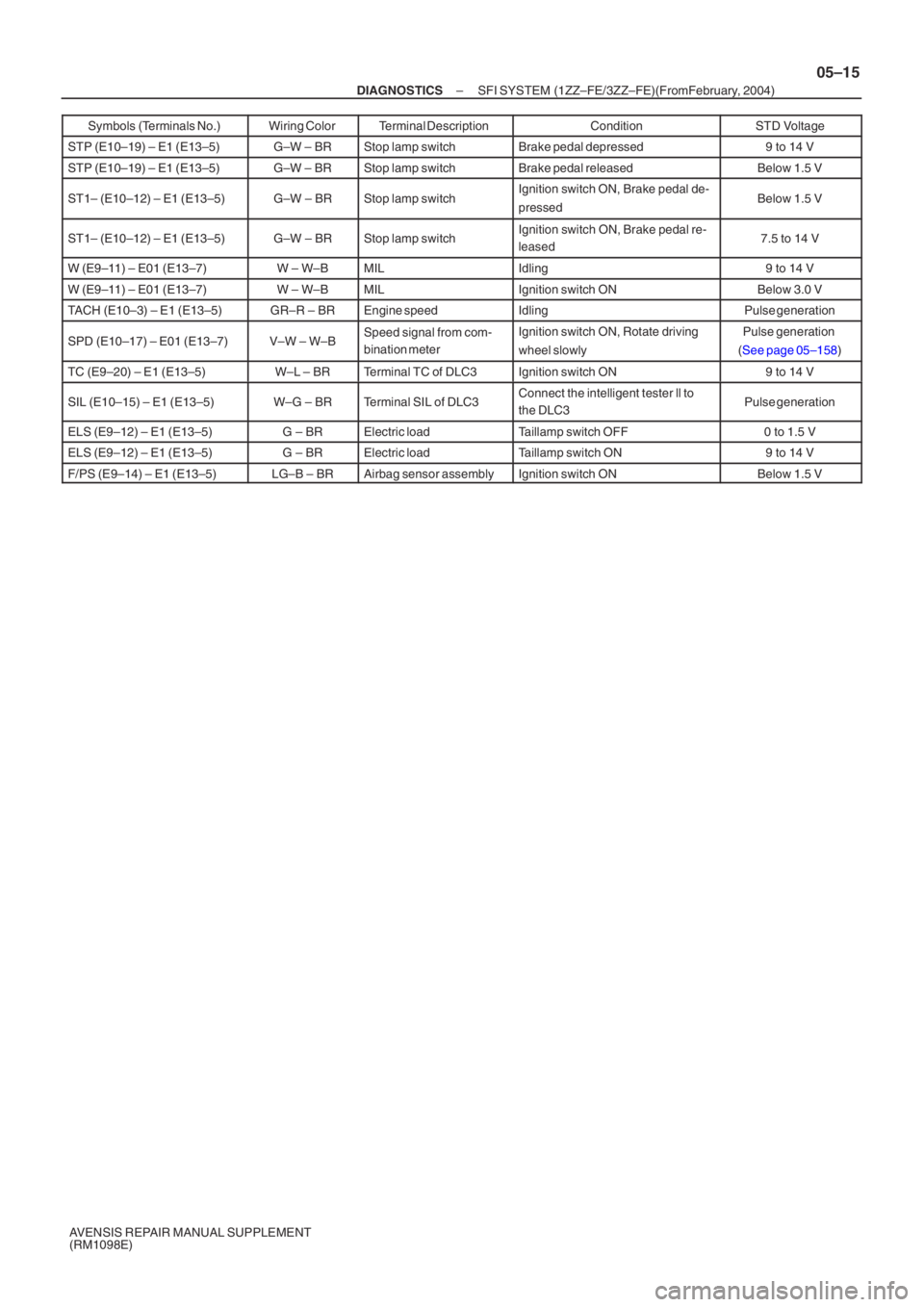
–
DIAGNOSTICS SFI SYSTEM (1ZZ–FE/3ZZ–FE)(From February, 2004)
05–15
AVENSIS REPAIR MANUAL SUPPLEMENT
(RM1098E)Symbols (Terminals No.)
STD Voltage
Condition
Terminal Description
Wiring Color
STP (E10–19) – E1 (E13–5)G–W – BRStop lamp switchBrake pedal depressed9 to 14 V
STP (E10–19) – E1 (E13–5)G–W – BRStop lamp switchBrake pedal releasedBelow 1.5 V
ST1– (E10–12) – E1 (E13–5)G–W – BRStop lamp switchIgnition switch ON, Brake pedal de-
pressedBelow 1.5 V
ST1– (E10–12) – E1 (E13–5)G–W – BRStop lamp switchIgnition switch ON, Brake pedal re-
leased7.5 to 14 V
W (E9–11) – E01 (E13–7)W – W–BMILIdling9 to 14 V
W (E9–11) – E01 (E13–7)W – W–BMILIgnition switch ONBelow 3.0 V
TACH (E10–3) – E1 (E13–5)GR–R – BREngine speedIdlingPulse generation
SPD (E10–17) – E01 (E13–7)V–W – W–BSpeed signal from com-
bination meterIgnition switch ON, Rotate driving
wheel slowlyPulse generation
( See page 05–158 )
TC (E9–20) – E1 (E13–5)W–L – BRTerminal TC of DLC3Ignition switch ON9 to 14 V
SIL (E10–15) – E1 (E13–5)W–G – BRTerminal SIL of DLC3Connect the intelligent tester ll to
the DLC3Pulse generation
ELS (E9–12) – E1 (E13–5)G – BRElectric loadTaillamp switch OFF0 to 1.5 V
ELS (E9–12) – E1 (E13–5)G – BRElectric loadTaillamp switch ON9 to 14 V
F/PS (E9–14) – E1 (E13–5)LG–B – BRAirbag sensor assemblyIgnition switch ONBelow 1.5 V
Page 4910 of 5135
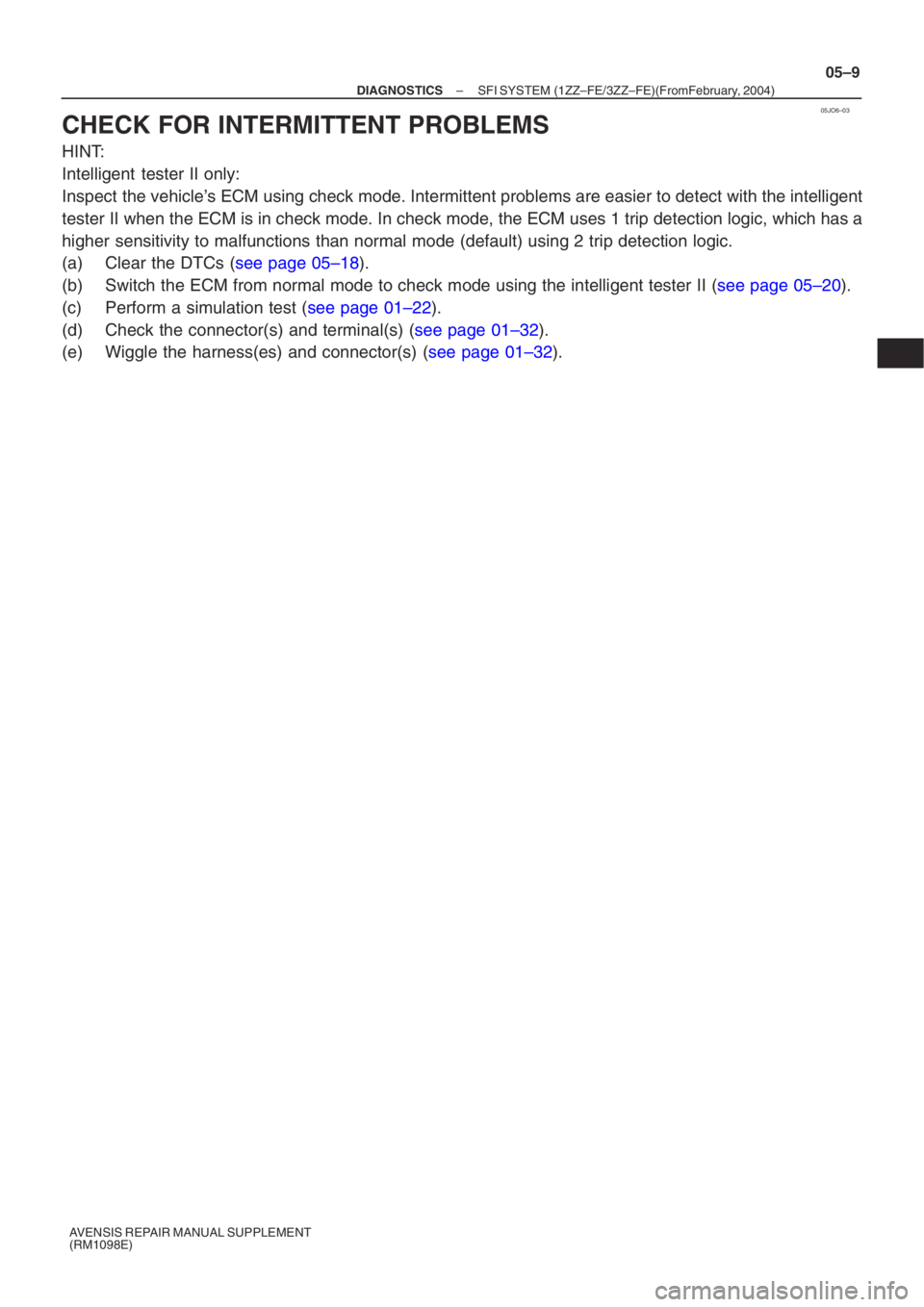
05JO6–03
–
DIAGNOSTICS SFI SYSTEM (1ZZ–FE/3ZZ–FE)(From February, 2004)
05–9
AVENSIS REPAIR MANUAL SUPPLEMENT
(RM1098E)
CHECK FOR INTERMITTENT PROBLEMS
HINT:
Intelligent tester II only:
Inspect the vehicle’s ECM using check mode. Intermittent problems are easier to detect with \
the intelligent
tester II when the ECM is in check mode. In check mode, the ECM uses 1 t\
rip detection logic, which has a
higher sensitivity to malfunctions than normal mode (default) using 2 trip d\
etection logic.
(a) Clear the DTCs ( see page 05–18).
(b) Switch the ECM from normal mode to check mode using the intelligent test\
er II ( see page 05–20).
(c) Perform a simulation test ( see page 01–22).
(d) Check the connector(s) and terminal(s) ( see page 01–32).
(e) Wiggle the harness(es) and connector(s) ( see page 01–32).