air condition ASTON MARTIN V8 VANTAGE 2010 User Guide
[x] Cancel search | Manufacturer: ASTON MARTIN, Model Year: 2010, Model line: V8 VANTAGE, Model: ASTON MARTIN V8 VANTAGE 2010Pages: 947, PDF Size: 43.21 MB
Page 265 of 947
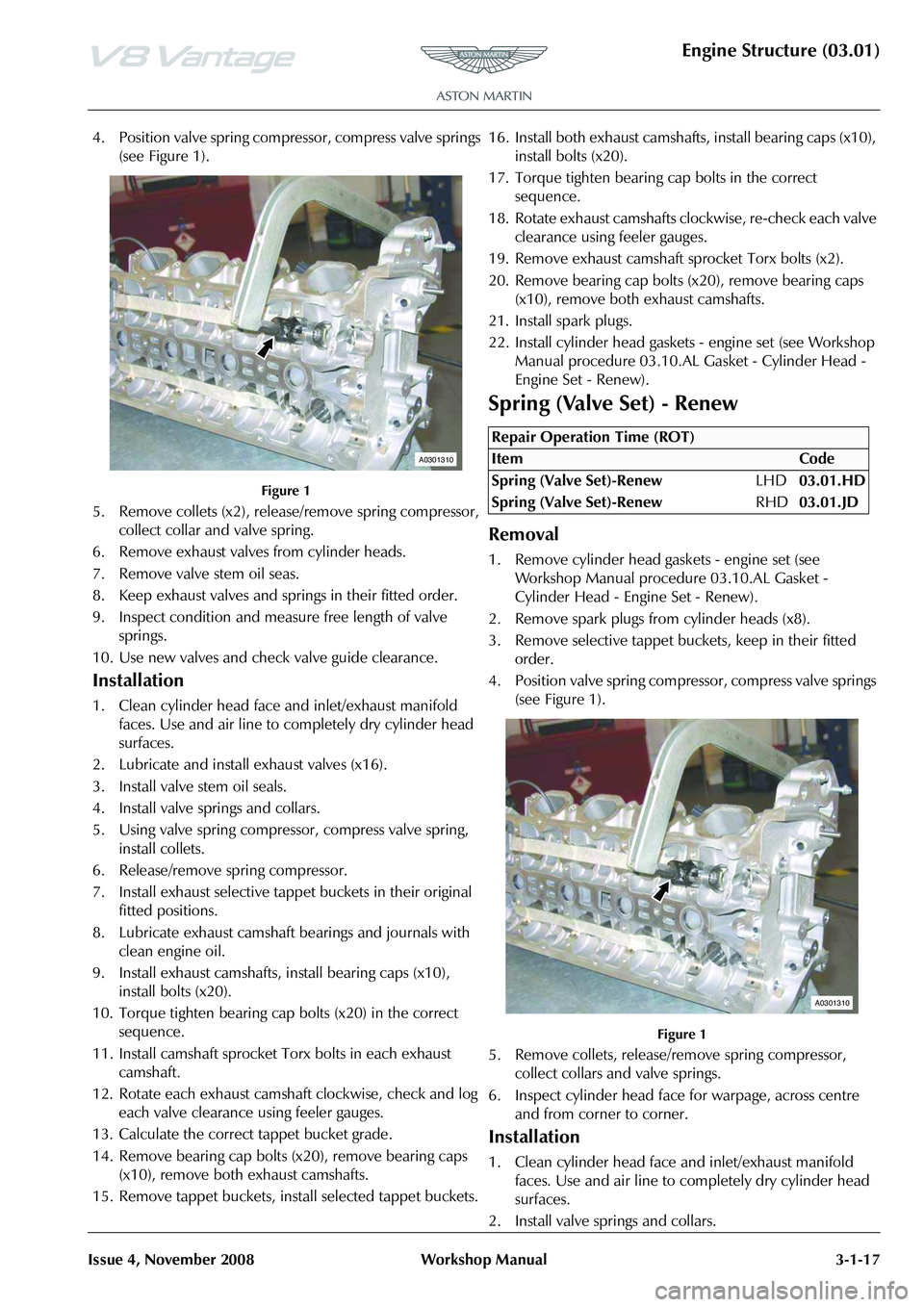
Engine Structure (03.01)
Issue 4, November 2008Workshop Manual 3-1-17
4. Position valve spring compressor, compress valve springs
(see Figure 1).
Figure 1
5. Remove collets (x2), release/remove spring compressor, collect collar and valve spring.
6. Remove exhaust valves from cylinder heads.
7. Remove valve stem oil seas.
8. Keep exhaust valves and springs in their fitted order.
9. Inspect condition and measure free length of valve springs.
10. Use new valves and check valve guide clearance.
Installation
1. Clean cylinder head face and inlet/exhaust manifold faces. Use and air line to completely dry cylinder head
surfaces.
2. Lubricate and install exhaust valves (x16).
3. Install valve stem oil seals.
4. Install valve springs and collars.
5. Using valve spring compressor, compress valve spring, install collets.
6. Release/remove spring compressor.
7. Install exhaust selective tappet buckets in their original fitted positions.
8. Lubricate exhaust camshaft be arings and journals with
clean engine oil.
9. Install exhaust camshafts, install bearing caps (x10), install bolts (x20).
10. Torque tighten bearing cap bolts (x20) in the correct
sequence.
11. Install camshaft sprocket Torx bolts in each exhaust camshaft.
12. Rotate each exhaust camshaf t clockwise, check and log
each valve clearance using feeler gauges.
13. Calculate the correct tappet bucket grade.
14. Remove bearing cap bolts (x20), remove bearing caps
(x10), remove both exhaust camshafts.
15. Remove tappet buckets, install selected tappet buckets. 16. Install both exhaust camshaft
s, install bearing caps (x10),
install bolts (x20).
17. Torque tighten bearing cap bolts in the correct sequence.
18. Rotate exhaust camshafts clockwise, re-check each valve clearance using feeler gauges.
19. Remove exhaust camshaft sprocket Torx bolts (x2).
20. Remove bearing cap bolts (x20), remove bearing caps (x10), remove both exhaust camshafts.
21. Install spark plugs.
22. Install cylinder head gaskets - engine set (see Workshop Manual procedure 03.10.AL Gasket - Cylinder Head -
Engine Set - Renew).
Spring (Valve Set) - Renew
Removal
1. Remove cylinder head gaskets - engine set (see Workshop Manual procedure 03.10.AL Gasket -
Cylinder Head - Engine Set - Renew).
2. Remove spark plugs from cylinder heads (x8).
3. Remove selective tappet buckets, keep in their fitted order.
4. Position valve spring compressor, compress valve springs (see Figure 1).
Figure 1
5. Remove collets, release/remove spring compressor, collect collars and valve springs.
6. Inspect cylinder head face for warpage, across centre and from corner to corner.
Installation
1. Clean cylinder head face and inlet/exhaust manifold faces. Use and air line to completely dry cylinder head
surfaces.
2. Install valve springs and collars.
A0301310
Repair Operation Time (ROT)
A0301310
Page 300 of 947
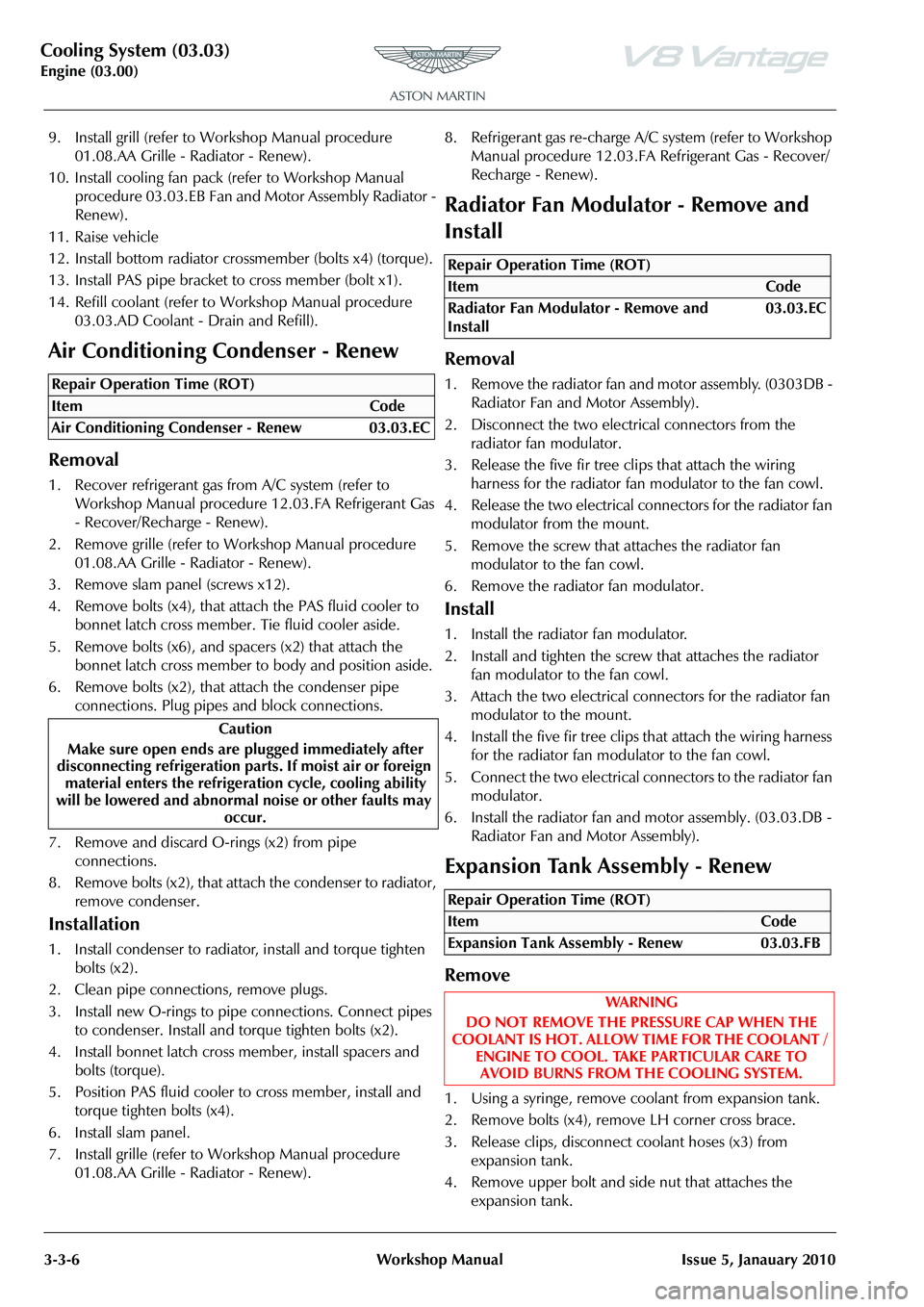
Cooling System (03.03)
Engine (03.00)3-3-6 Workshop Manual Issue 5, Janauary 2010
9. Install grill (refer to Workshop Manual procedure 01.08.AA Grille - Radiator - Renew).
10. Install cooling fan pack (refer to Workshop Manual procedure 03.03.EB Fan and Motor Assembly Radiator -
Renew).
11. Raise vehicle
12. Install bottom radiator cros smember (bolts x4) (torque).
13. Install PAS pipe bracket to cross member (bolt x1).
14. Refill coolant (refer to Workshop Manual procedure 03.03.AD Coolant - Drain and Refill).
Air Conditioning Condenser - Renew
Removal
1. Recover refrigerant gas fr om A/C system (refer to
Workshop Manual procedure 12.03.FA Refrigerant Gas
- Recover/Recharge - Renew).
2. Remove grille (refer to Workshop Manual procedure 01.08.AA Grille - Radiator - Renew).
3. Remove slam panel (screws x12).
4. Remove bolts (x4), that attach the PAS fluid cooler to bonnet latch cross member. Tie fluid cooler aside.
5. Remove bolts (x6), and spacers (x2) that attach the bonnet latch cross member to body and position aside.
6. Remove bolts (x2), that attach the condenser pipe connections. Plug pipes and block connections.
7. Remove and discard O-rings (x2) from pipe connections.
8. Remove bolts (x2), that attach the condenser to radiator, remove condenser.
Installation
1. Install condenser to radiator, install and torque tighten bolts (x2).
2. Clean pipe connections, remove plugs.
3. Install new O-rings to pipe connections. Connect pipes
to condenser. Install and torque tighten bolts (x2).
4. Install bonnet latch cross member, install spacers and bolts (torque).
5. Position PAS fluid cooler to cross member, install and torque tighten bolts (x4).
6. Install slam panel.
7. Install grille (refer to Workshop Manual procedure 01.08.AA Grille - Radiator - Renew). 8. Refrigerant gas re-charge A/C system (refer to Workshop
Manual procedure 12.03.FA Refrigerant Gas - Recover/
Recharge - Renew).
Radiator Fan Modulator - Remove and
Install
Removal
1. Remove the radiator fan and motor assembly. (0303DB - Radiator Fan and Motor Assembly).
2. Disconnect the two electrical connectors from the radiator fan modulator.
3. Release the five fir tree cl ips that attach the wiring
harness for the radiator fan modulator to the fan cowl.
4. Release the two electrical connectors for the radiator fan modulator from the mount.
5. Remove the screw that attaches the radiator fan modulator to the fan cowl.
6. Remove the radiator fan modulator.
Install
1. Install the radiator fan modulator.
2. Install and tighten the screw that attaches the radiator fan modulator to the fan cowl.
3. Attach the two electrical connectors for the radiator fan modulator to the mount.
4. Install the five fir tree clips that attach the wiring harness for the radiator fan modulator to the fan cowl.
5. Connect the two electrical connectors to the radiator fan modulator.
6. Install the radiator fan and motor assembly. (03.03.DB - Radiator Fan and Motor Assembly).
Expansion Tank Assembly - Renew
Remove
1. Using a syringe, remove coolant from expansion tank.
2. Remove bolts (x4), remove LH corner cross brace.
3. Release clips, disconnect coolant hoses (x3) from expansion tank.
4. Remove upper bolt and side nut that attaches the expansion tank.
Repair Operation Time (ROT)
Repair Operation Time (ROT)
ItemCode
Radiator Fan Modulator - Remove and
Install 03.03.EC
Repair Operation Time (ROT)
ItemCode
Expansion Tank Assembly - Renew 03.03.FB
WAR NI NG
DO NOT REMOVE THE PRESSURE CAP WHEN THE
COOLANT IS HOT. ALLOW TIME FOR THE COOLANT /
ENGINE TO COOL. TAKE PARTICULAR CARE TO AVOID BURNS FROM THE COOLING SYSTEM.
Page 360 of 947
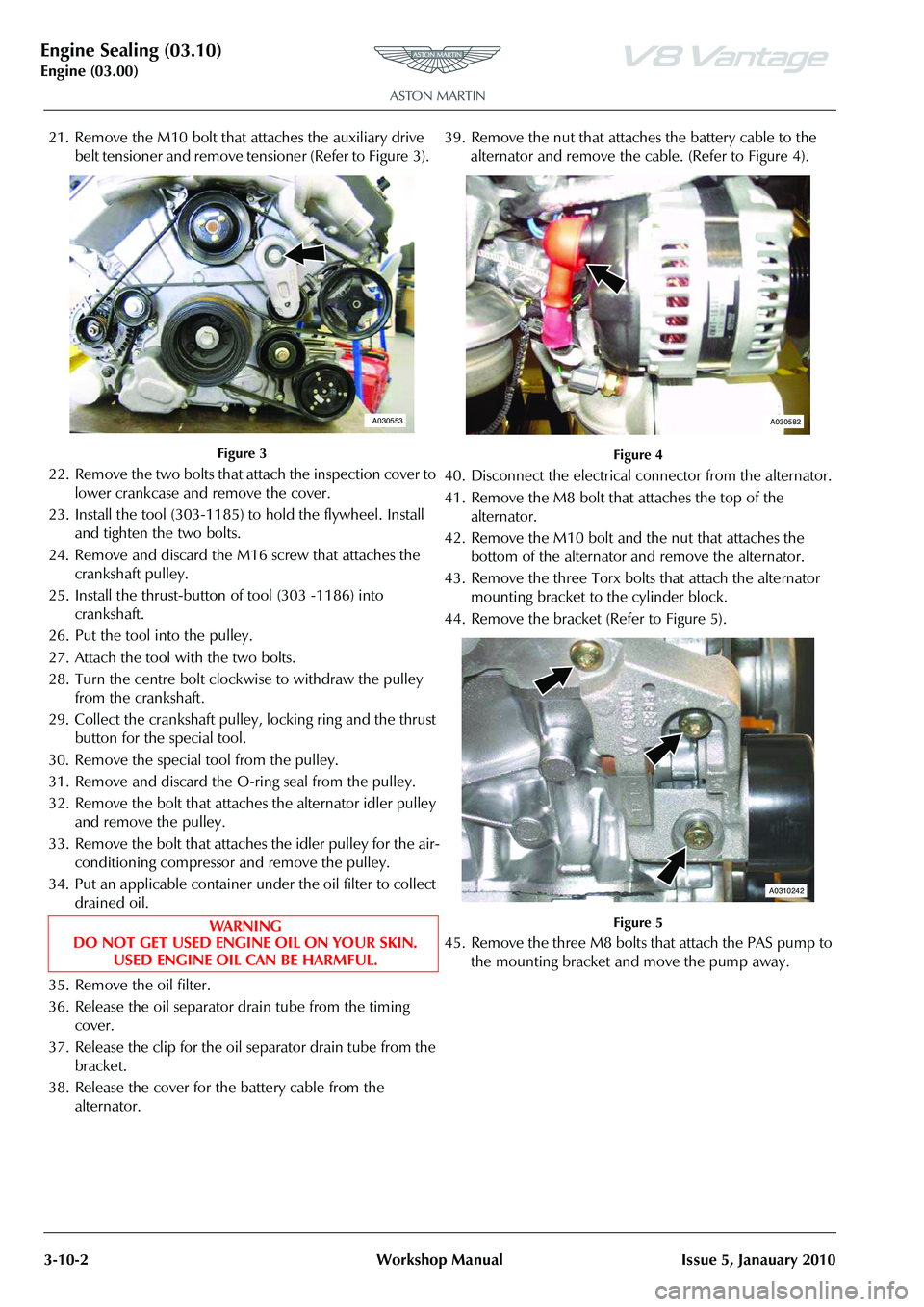
Engine Sealing (03.10)
Engine (03.00)3-10-2 Workshop Manual Issue 5, Janauary 2010
21. Remove the M10 bolt that attaches the auxiliary drive belt tensioner and remove tensioner (Refer to Figure 3).
Figure 3
22. Remove the two bolts that attach the inspection cover to lower crankcase and remove the cover.
23. Install the tool (303-1185) to hold the flywheel. Install and tighten the two bolts.
24. Remove and discard the M16 screw that attaches the crankshaft pulley.
25. Install the thrust-button of tool (303 -1186) into crankshaft.
26. Put the tool into the pulley.
27. Attach the tool with the two bolts.
28. Turn the centre bolt clockwise to withdraw the pulley from the crankshaft.
29. Collect the crankshaft pulley, locking ring and the thrust button for the special tool.
30. Remove the special tool from the pulley.
31. Remove and discard the O-ring seal from the pulley.
32. Remove the bolt that attaches the alternator idler pulley and remove the pulley.
33. Remove the bolt that attaches the idler pulley for the air- conditioning compressor and remove the pulley.
34. Put an applicable container under the oil filter to collect drained oil.
35. Remove the oil filter.
36. Release the oil separator drain tube from the timing cover.
37. Release the clip for the oil separator drain tube from the bracket.
38. Release the cover for the battery cable from the alternator. 39. Remove the nut that attaches the battery cable to the
alternator and remove the cable. (Refer to Figure 4).
Figure 4
40. Disconnect the electrical connector from the alternator.
41. Remove the M8 bolt that attaches the top of the alternator.
42. Remove the M10 bolt and the nut that attaches the bottom of the alternator and remove the alternator.
43. Remove the three Torx bolts that attach the alternator mounting bracket to the cylinder block.
44. Remove the bracket (Refer to Figure 5).
Figure 5
45. Remove the three M8 bolts that attach the PAS pump to the mounting bracket and move the pump away.
WAR NI NG
DO NOT GET USED ENGINE OIL ON YOUR SKIN.
USED ENGINE OIL CAN BE HARMFUL.
A030553A030582
A0310242
Page 361 of 947
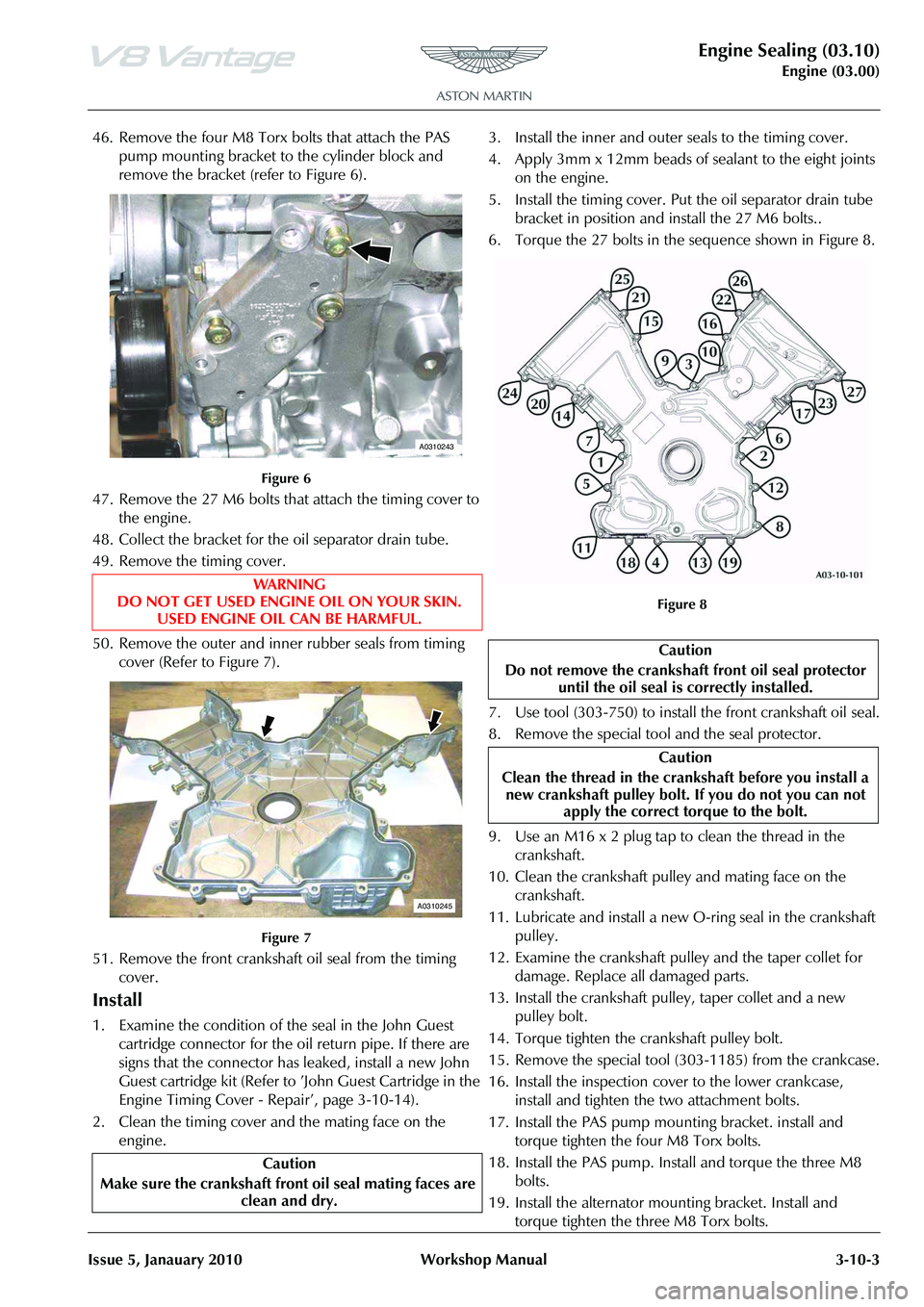
Engine Sealing (03.10)
Engine (03.00)
Issue 5, Janauary 2010 Workshop Manual 3-10-3
46. Remove the four M8 Torx bolts that attach the PAS pump mounting bracket to the cylinder block and
remove the bracket (refer to Figure 6).
Figure 6
47. Remove the 27 M6 bolts that attach the timing cover to the engine.
48. Collect the bracket for the oil separator drain tube.
49. Remove the timing cover.
50. Remove the outer and inner rubber seals from timing cover (Refer to Figure 7).
Figure 7
51. Remove the front crankshaft oil seal from the timing
cover.
Install
1. Examine the condition of the seal in the John Guest cartridge connector for the oil return pipe. If there are
signs that the connector has leaked, install a new John
Guest cartridge kit (Refer to ’John Guest Cartridge in the
Engine Timing Cover - Repair’, page 3-10-14).
2. Clean the timing cover and the mating face on the engine. 3. Install the inner and outer seals to the timing cover.
4. Apply 3mm x 12mm beads of sealant to the eight joints
on the engine.
5. Install the timing cover. Put the oil separator drain tube bracket in position and install the 27 M6 bolts..
6. Torque the 27 bolts in the sequence shown in Figure 8.
Figure 8
7. Use tool (303-750) to install the front crankshaft oil seal.
8. Remove the special tool and the seal protector.
9. Use an M16 x 2 plug tap to clean the thread in the crankshaft.
10. Clean the crankshaft pulley and mating face on the crankshaft.
11. Lubricate and install a new O-ring seal in the crankshaft pulley.
12. Examine the crankshaft pulley and the taper collet for damage. Replace all damaged parts.
13. Install the crankshaft pulley, taper collet and a new pulley bolt.
14. Torque tighten the crankshaft pulley bolt.
15. Remove the special tool (303-1185) from the crankcase.
16. Install the inspection cover to the lower crankcase, install and tighten the two attachment bolts.
17. Install the PAS pump mounting bracket. install and torque tighten the four M8 Torx bolts.
18. Install the PAS pump. Install and torque the three M8 bolts.
19. Install the alternator mounting bracket. Install and torque tighten the three M8 Torx bolts.
WA R N I N G
DO NOT GET USED ENGINE OIL ON YOUR SKIN.
USED ENGINE OIL CAN BE HARMFUL.
Caution
Make sure the cranks haft front oil seal mating faces are
clean and dry.
A0310243
A0310245
Caution
Do not remove the crankshaft front oil seal protector
until the oil seal is correctly installed.
Caution
Clean the thread in the cran kshaft before you install a
new crankshaft pulley bolt. If you do not you can not apply the correct torque to the bolt.
Page 362 of 947
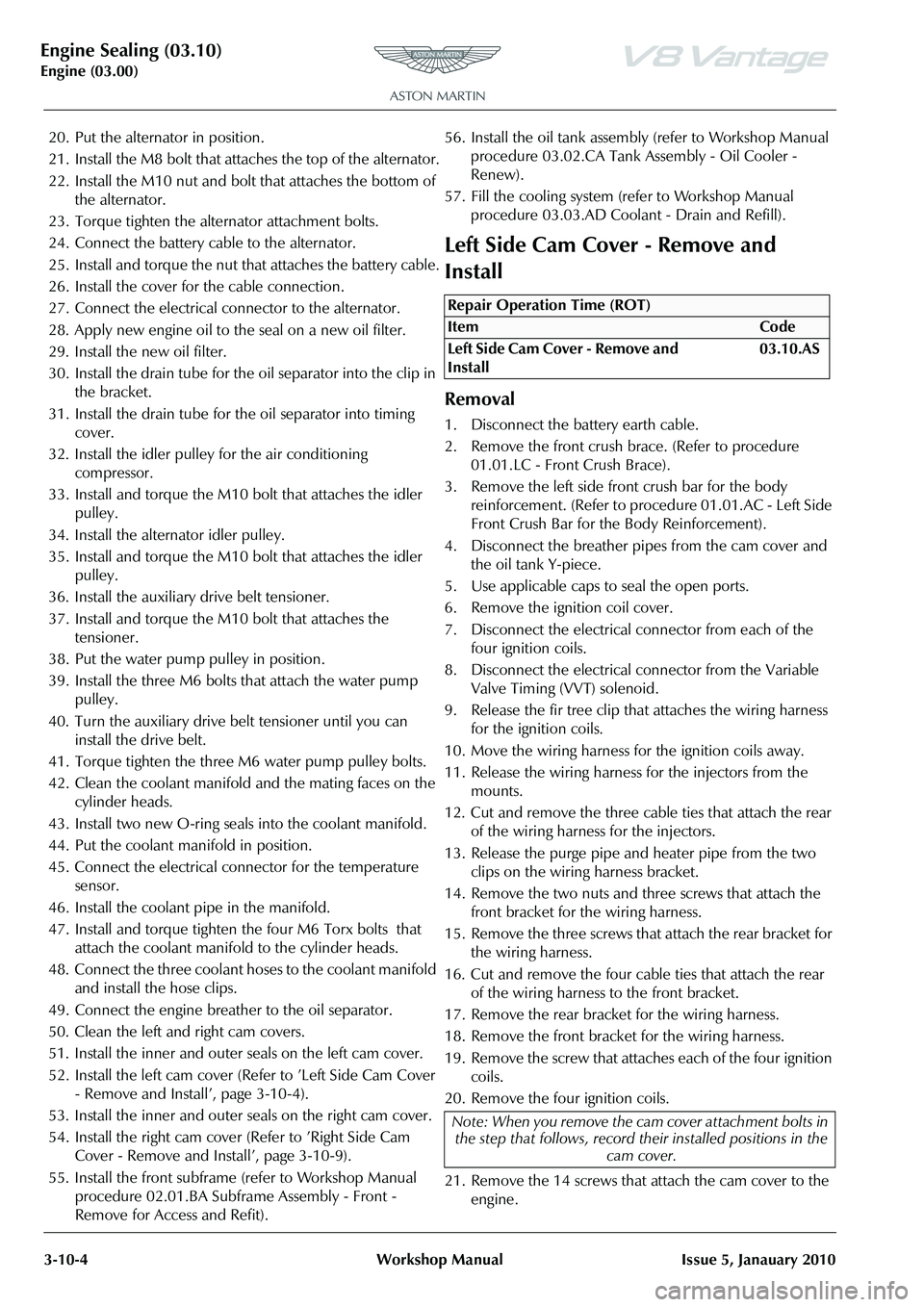
Engine Sealing (03.10)
Engine (03.00)3-10-4 Workshop Manual Issue 5, Janauary 2010
20. Put the alternator in position.
21. Install the M8 bolt that attaches the top of the alternator.
22. Install the M10 nut and bolt that attaches the bottom of the alternator.
23. Torque tighten the alternator attachment bolts.
24. Connect the battery cable to the alternator.
25. Install and torque the nut that attaches the battery cable.
26. Install the cover for the cable connection.
27. Connect the electrical connector to the alternator.
28. Apply new engine oil to the seal on a new oil filter.
29. Install the new oil filter.
30. Install the drain tube for the oil separator into the clip in the bracket.
31. Install the drain tube for the oil separator into timing cover.
32. Install the idler pulley for the air conditioning compressor.
33. Install and torque the M10 bolt that attaches the idler pulley.
34. Install the alternator idler pulley.
35. Install and torque the M10 bolt that attaches the idler pulley.
36. Install the auxiliary drive belt tensioner.
37. Install and torque the M10 bolt that attaches the tensioner.
38. Put the water pump pulley in position.
39. Install the three M6 bolts that attach the water pump pulley.
40. Turn the auxiliary drive be lt tensioner until you can
install the drive belt.
41. Torque tighten the three M6 water pump pulley bolts.
42. Clean the coolant manifold and the mating faces on the cylinder heads.
43. Install two new O-ring seals into the coolant manifold.
44. Put the coolant manifold in position.
45. Connect the electrical connector for the temperature sensor.
46. Install the coolant pipe in the manifold.
47. Install and torque tighten the four M6 Torx bolts that attach the coolant manifold to the cylinder heads.
48. Connect the three coolant hoses to the coolant manifold and install the hose clips.
49. Connect the engine breather to the oil separator.
50. Clean the left and right cam covers.
51. Install the inner and outer seals on the left cam cover.
52. Install the left cam cover (Refer to ’Left Side Cam Cover - Remove and Install’, page 3-10-4).
53. Install the inner and outer seals on the right cam cover.
54. Install the right cam cover (Refer to ’Right Side Cam Cover - Remove and Install’, page 3-10-9).
55. Install the front subframe (refer to Workshop Manual procedure 02.01.BA Subframe Assembly - Front -
Remove for Access and Refit). 56. Install the oil tank assembly
(refer to Workshop Manual
procedure 03.02.CA Tank Assembly - Oil Cooler -
Renew).
57. Fill the cooling system (refer to Workshop Manual procedure 03.03.AD Coolant - Drain and Refill).
Left Side Cam Cover - Remove and
Install
Removal
1. Disconnect the battery earth cable.
2. Remove the front crush brace. (Refer to procedure 01.01.LC - Front Crush Brace).
3. Remove the left side front crush bar for the body reinforcement. (Refer to procedure 01.01.AC - Left Side
Front Crush Bar for the Body Reinforcement).
4. Disconnect the breather pi pes from the cam cover and
the oil tank Y-piece.
5. Use applicable caps to seal the open ports.
6. Remove the ignition coil cover.
7. Disconnect the electrical connector from each of the four ignition coils.
8. Disconnect the electrical connector from the Variable
Valve Timing (VVT) solenoid.
9. Release the fir tree clip that attaches the wiring harness for the ignition coils.
10. Move the wiring harness for the ignition coils away.
11. Release the wiring harness for the injectors from the mounts.
12. Cut and remove the three cable ties that attach the rear of the wiring harness for the injectors.
13. Release the purge pipe an d heater pipe from the two
clips on the wiring harness bracket.
14. Remove the two nuts and three screws that attach the front bracket for the wiring harness.
15. Remove the three screws that attach the rear bracket for the wiring harness.
16. Cut and remove the four cable ties that attach the rear
of the wiring harness to the front bracket.
17. Remove the rear bracket for the wiring harness.
18. Remove the front bracket for the wiring harness.
19. Remove the screw that attaches each of the four ignition coils.
20. Remove the four ignition coils.
21. Remove the 14 screws that attach the cam cover to the
engine.
Repair Operation Time (ROT)
ItemCode
Left Side Cam Cover - Remove and
Install 03.10.AS
Note: When you remo ve the cam cover attachment bolts in
the step that follows , record their installed positions in the
cam cover.
Page 455 of 947
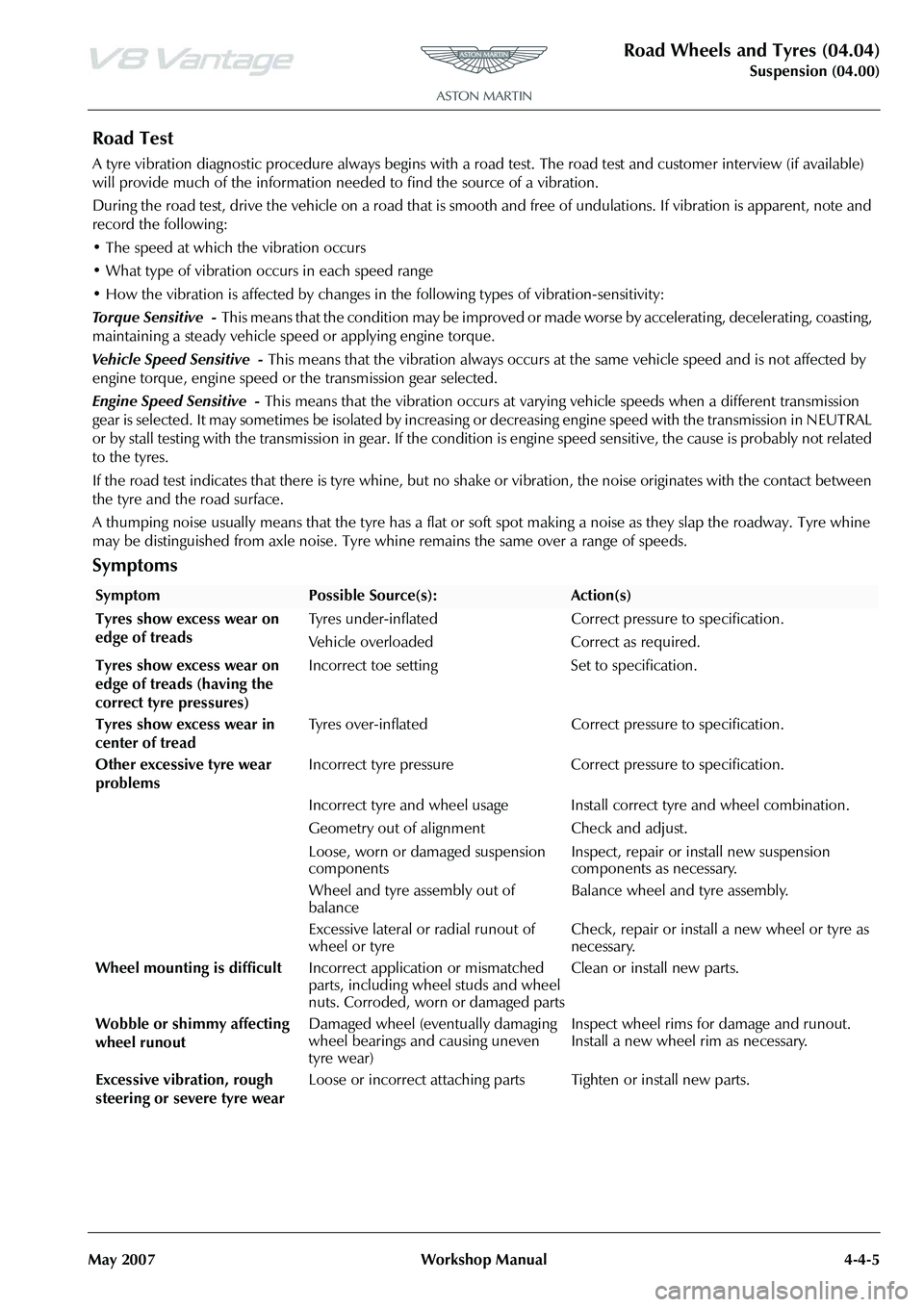
Road Wheels and Tyres (04.04)
Suspension (04.00)
May 2007 Workshop Manual 4-4-5
Road Test
A tyre vibration diagnostic proc edure always begins with a road test. The road test and customer interview (if available)
will provide much of the information neede d to find the source of a vibration.
During the road test, drive the vehicle on a road that is smoot h and free of undulations. If vibration is apparent, note and
record the following:
• The speed at which the vibration occurs
• What type of vibration occurs in each speed range
• How the vibration is affected by changes in the following types of vibration-sensitivity:
Torque Sensitive - This means that the condition may be improved or made worse by accelerating, decelerating, coasting,
maintaining a steady vehicle speed or applying engine torque.
Vehicle Speed Sensitive - This means that the vibration always occurs at the same vehicle speed and is not affected by
engine torque, engine speed or the transmission gear selected.
Engine Speed Sensitive - This means that the vibration occurs at varyin g vehicle speeds when a different transmission
gear is selected. It may sometimes be isolated by increasing or decreasing engine speed with the transmission in NEUTRAL
or by stall testing with the transmission in gear. If the condition is engine speed sensitive, the cause is probably not relate d
to the tyres.
If the road test indicates that there is tyre whine, but no sh ake or vibration, the noise originates with the contact between
the tyre and the road surface.
A thumping noise usually means that the tyre has a flat or soft spot making a noise as they slap the roadway. Tyre whine
may be distinguished from axle noise. Tyre whine remains the same over a range of speeds.
Symptoms
SymptomPossible Source(s):Action(s)
Tyres show excess wear on
edge of treads Tyres under-inflated Correct pressure to specification.
Vehicle overloaded Correct as required.
Tyres show excess wear on
edge of treads (having the
correct tyre pressures) Incorrect toe setting Set to specification.
Tyres show excess wear in
center of tread Tyres over-inflated Correct pressure to specification.
Other excessive tyre wear
problems Incorrect tyre pressure Correct pressure to specification.
Incorrect tyre and wheel usage Install correct tyre and wheel combination.
Geometry out of alignm
ent Check and adjust.
Loose, worn or damaged suspension
components Inspect, repair or install new suspension
components as necessary.
Wheel and tyre assembly out of
balance Balance wheel and tyre assembly.
Excessive lateral or radial runout of
wheel or tyre Check, repair or install a new wheel or tyre as
necessary.
Wheel mounting is difficult Incorrect application or mismatched
parts, including wheel studs and wheel
nuts. Corroded, worn or damaged parts Clean or install new parts.
Wobble or shimmy affecting
wheel runout Damaged wheel (eventually damaging
wheel bearings and causing uneven
tyre wear) Inspect wheel rims for damage and runout.
Install a new wheel rim as necessary.
Excessive vibration, rough
steering or severe tyre wear Loose or incorrect attaching parts Tighten or install new parts.
Page 457 of 947
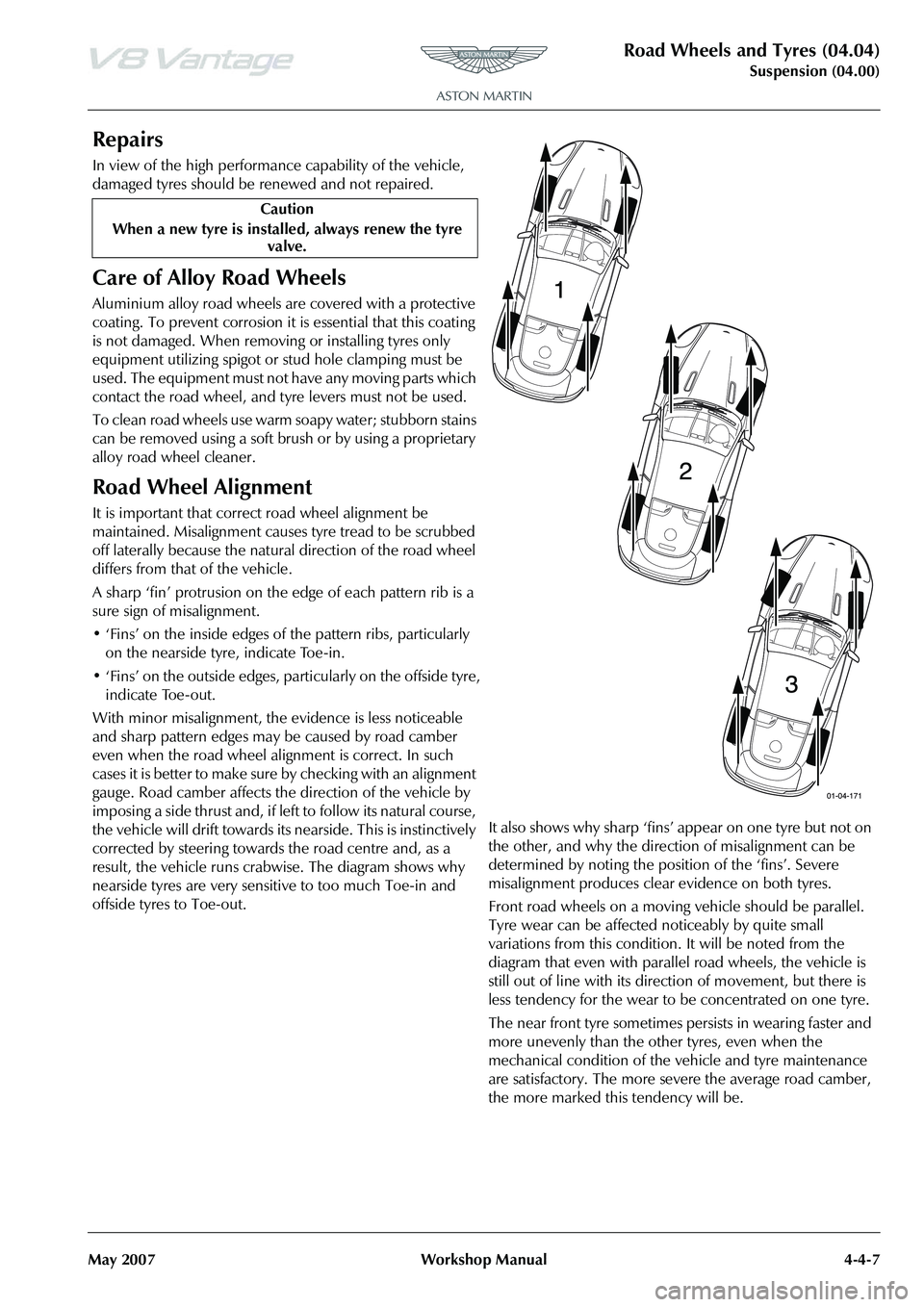
Road Wheels and Tyres (04.04)
Suspension (04.00)
May 2007 Workshop Manual 4-4-7
Repairs
In view of the high performance capability of the vehicle,
damaged tyres should be renewed and not repaired.
Care of Alloy Road Wheels
Aluminium alloy road wheels are covered with a protective
coating. To prevent corrosion it is essential that this coating
is not damaged. When removing or installing tyres only
equipment utilizing spigot or stud hole clamping must be
used. The equipment must not have any moving parts which
contact the road wheel, and ty re levers must not be used.
To clean road wheels use warm soapy water; stubborn stains
can be removed using a soft brush or by using a proprietary
alloy road wheel cleaner.
Road Wheel Alignment
It is important that correct road wheel alignment be
maintained. Misalignment causes tyre tread to be scrubbed
off laterally because the natural direction of the road wheel
differs from that of the vehicle.
A sharp ‘fin’ protrusion on the edge of each pattern rib is a
sure sign of misalignment.
• ‘Fins’ on the inside edges of the pattern ribs, particularly on the nearside tyre, indicate Toe-in.
• ‘Fins’ on the outside edges, particularly on the offside tyre, indicate Toe-out.
With minor misalignment, the ev idence is less noticeable
and sharp pattern edges may be caused by road camber
even when the road wheel alignment is correct. In such
c a s e s i t i s b e t t e r t o m a k e s u r e b y c h e c k i n g w i t h a n a l i g n m e n t
gauge. Road camber affects the direction of the vehicle by
imposing a side thrus t and , if le ft to follow its natural cou rs e,
the vehicle will drift towards its nearside. This is instinctively
corrected by steering towards the road centre and, as a
result, the vehicle runs crab wise. The diagram shows why
nearside tyres are very sensitive to too much Toe-in and
offside tyres to Toe-out. It also shows why sharp ‘fins’ appear on one tyre but not on
the other, and why the direction of misalignment can be
determined by noting the position of the ‘fins’. Severe
misalignment produces clea
r evidence on both tyres.
Front road wheels on a moving vehicle should be parallel.
Tyre wear can be affected noticeably by quite small
variations from this condition. It will be noted from the
diagram that even with parallel road wheels, the vehicle is
still out of line with its dire ction of movement, but there is
less tendency for the wear to be concentrated on one tyre.
The near front tyre sometimes persists in wearing faster and
more unevenly than the other tyres, even when the
mechanical condition of the vehicle and tyre maintenance
are satisfactory. The more severe the average road camber,
the more marked this tendency will be.
Caution
When a new tyre is installe d, always renew the tyre
valve.
Page 485 of 947
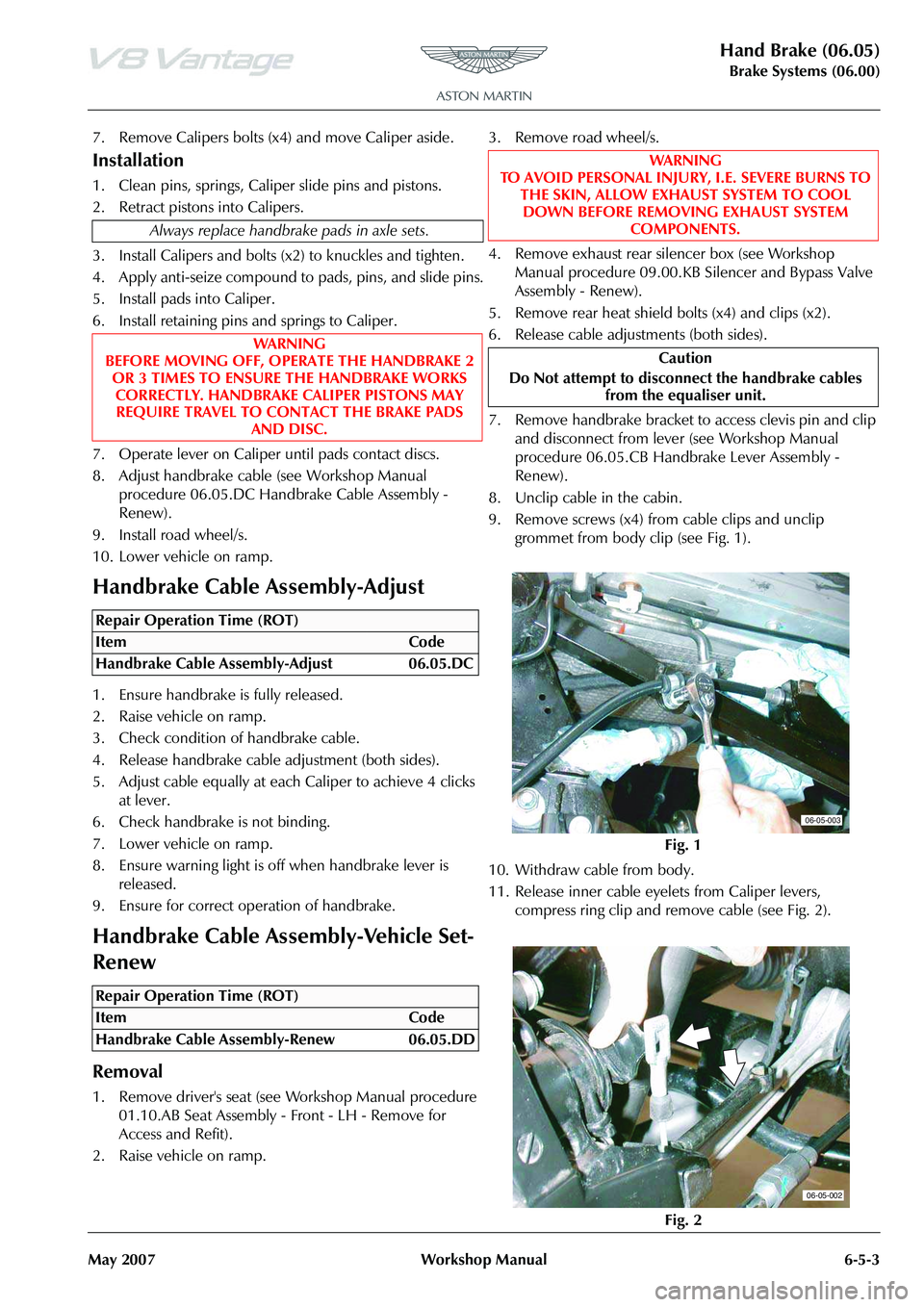
Hand Brake (06.05)
Brake Systems (06.00)
May 2007 Workshop Manual 6-5-3
7. Remove Calipers bolts (x 4) and move Caliper aside.
Installation
1. Clean pins, springs, Caliper slide pins and pistons.
2. Retract pistons into Calipers.
3. Install Calipers and bolts (x2) to knuckles and tighten.
4. Apply anti-seize compound to pads, pins, and slide pins.
5. Install pads into Caliper.
6. Install retaining pins and springs to Caliper.
7. Operate lever on Caliper until pads contact discs.
8. Adjust handbrake cable (see Workshop Manual
procedure 06.05.DC Handbrake Cable Assembly -
Renew).
9. Install road wheel/s.
10. Lower vehicle on ramp.
Handbrake Cable Assembly-Adjust
1. Ensure handbrake is fully released.
2. Raise vehicle on ramp.
3. Check condition of handbrake cable.
4. Release handbrake cable adjustment (both sides).
5. Adjust cable equally at each Caliper to achieve 4 clicks at lever.
6. Check handbrake is not binding.
7. Lower vehicle on ramp.
8. Ensure warning light is off when handbrake lever is released.
9. Ensure for correct operation of handbrake.
Handbrake Cable Assembly-Vehicle Set-
Renew
Removal
1. Remove driver's seat (see Workshop Manual procedure
01.10.AB Seat Assembly - Front - LH - Remove for
Access and Refit).
2. Raise vehicle on ramp. 3. Remove road wheel/s.
4. Remove exhaust rear sile
ncer box (see Workshop
Manual procedure 09.00.KB Silencer and Bypass Valve
Assembly - Renew).
5. Remove rear heat shield bolts (x4) and clips (x2).
6. Release cable adjustments (both sides).
7. Remove handbrake bracket to access clevis pin and clip and disconnect from lever (see Workshop Manual
procedure 06.05.CB Handbrake Lever Assembly -
Renew).
8. Unclip cable in the cabin.
9. Remove screws (x4) from cable clips and unclip grommet from body clip (see Fig. 1).
10. Withdraw cable from body.
11. Release inner cable eyelets from Caliper levers, compress ring clip and remove cable (see Fig. 2).
Always replace handbrake pads in axle sets.
WA R N I N G
BEFORE MOVING OFF, OPERATE THE HANDBRAKE 2 OR 3 TIMES TO ENSURE THE HANDBRAKE WORKS
CORRECTLY. HANDBRAKE CALIPER PISTONS MAY REQUIRE TRAVEL TO CONTACT THE BRAKE PADS AND DISC.
Repair Operation Time (ROT)
Repair Operation Time (ROT)
WA R N I N G
TO AVOID PERSONAL INJURY, I.E. SEVERE BURNS TO
THE SKIN, ALLOW EXHAUST SYSTEM TO COOL DOWN BEFORE REMOVING EXHAUST SYSTEM COMPONENTS.
Caution
Do Not attempt to disconne ct the handbrake cables
from the equaliser unit.
Fig. 1
Fig. 2
06-05-003
06-05-002
Page 568 of 947
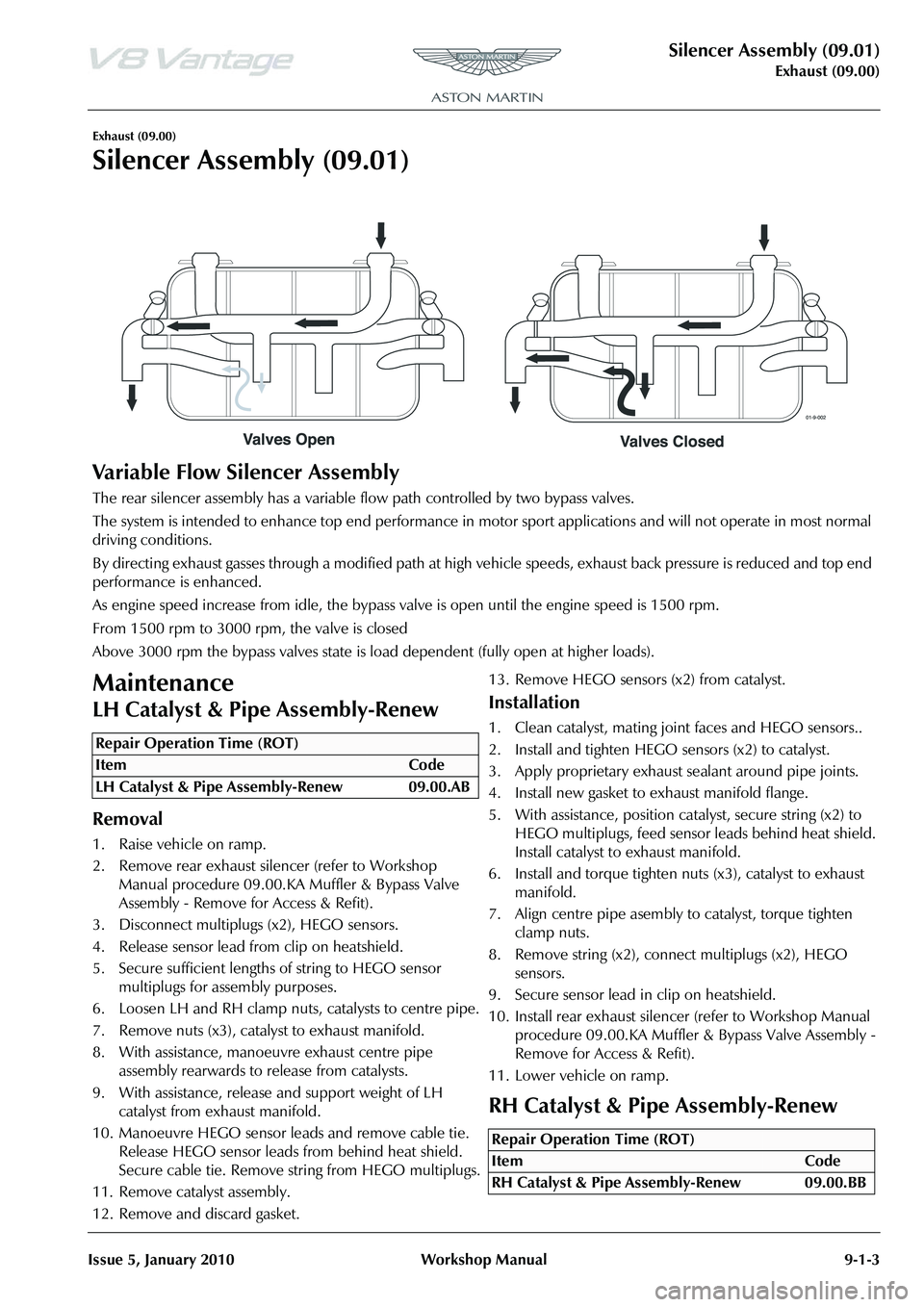
Silencer Assembly (09.01)
Exhaust (09.00)
Issue 5, January 2010 Workshop Manual 9-1-3
Exhaust (09.00)
Silencer Assembly (09.01)
Variable Flow Silencer Assembly
The rear silencer assembly has a variable fl ow path controlled by two bypass valves.
The system is intended to enhance top end performance in mo tor sport applications and will not operate in most normal
driving conditions.
By directing exhaust gasses through a modified path at high vehicle speeds, exhaust back pressure is reduced and top end
performance is enhanced.
As engine speed increase from idle, the bypass valve is open until the engine speed is 1500 rpm.
From 1500 rpm to 3000 rpm, the valve is closed
Above 3000 rpm the bypass valves state is load dependent (fully open at higher loads).
Maintenance
LH Catalyst & Pipe Assembly-Renew
Removal
1. Raise vehicle on ramp.
2. Remove rear exhaust silencer (refer to Workshop Manual procedure 09.00.KA Muffler & Bypass Valve
Assembly - Remove for Access & Refit).
3. Disconnect multiplugs (x2), HEGO sensors.
4. Release sensor lead from clip on heatshield.
5. Secure sufficient lengths of string to HEGO sensor multiplugs for assembly purposes.
6. Loosen LH and RH clamp nuts , catalysts to centre pipe.
7. Remove nuts (x3), catalyst to exhaust manifold.
8. With assistance, manoeuvre exhaust centre pipe assembly rearwards to release from catalysts.
9. With assistance, release and support weight of LH catalyst from exhaust manifold.
10. Manoeuvre HEGO sensor le ads and remove cable tie.
Release HEGO sensor leads from behind heat shield.
Secure cable tie. Remove string from HEGO multiplugs.
11. Remove catalyst assembly.
12. Remove and discard gasket. 13. Remove HEGO sensor
s (x2) from catalyst.
Installation
1. Clean catalyst, mating joint faces and HEGO sensors..
2. Install and tighten HEGO sensors (x2) to catalyst.
3. Apply proprietary exhaust se alant around pipe joints.
4. Install new gasket to exhaust manifold flange.
5. With assistance, position cata lyst, secure string (x2) to
HEGO multiplugs, feed sensor leads behind heat shield.
Install catalyst to exhaust manifold.
6. Install and torque tighten nuts (x3), catalyst to exhaust manifold.
7. Align centre pipe asembly to catalyst, torque tighten
clamp nuts.
8. Remove string (x2), conne ct multiplugs (x2), HEGO
sensors.
9. Secure sensor lead in clip on heatshield.
10. Install rear exhaust silencer (refer to Workshop Manual procedure 09.00.KA Muffler & Bypass Valve Assembly -
Remove for Access & Refit).
11. Lower vehicle on ramp.
RH Catalyst & Pipe Assembly-Renew
Repair Operation Time (ROT)
Repair Operation Time (ROT)
Page 585 of 947
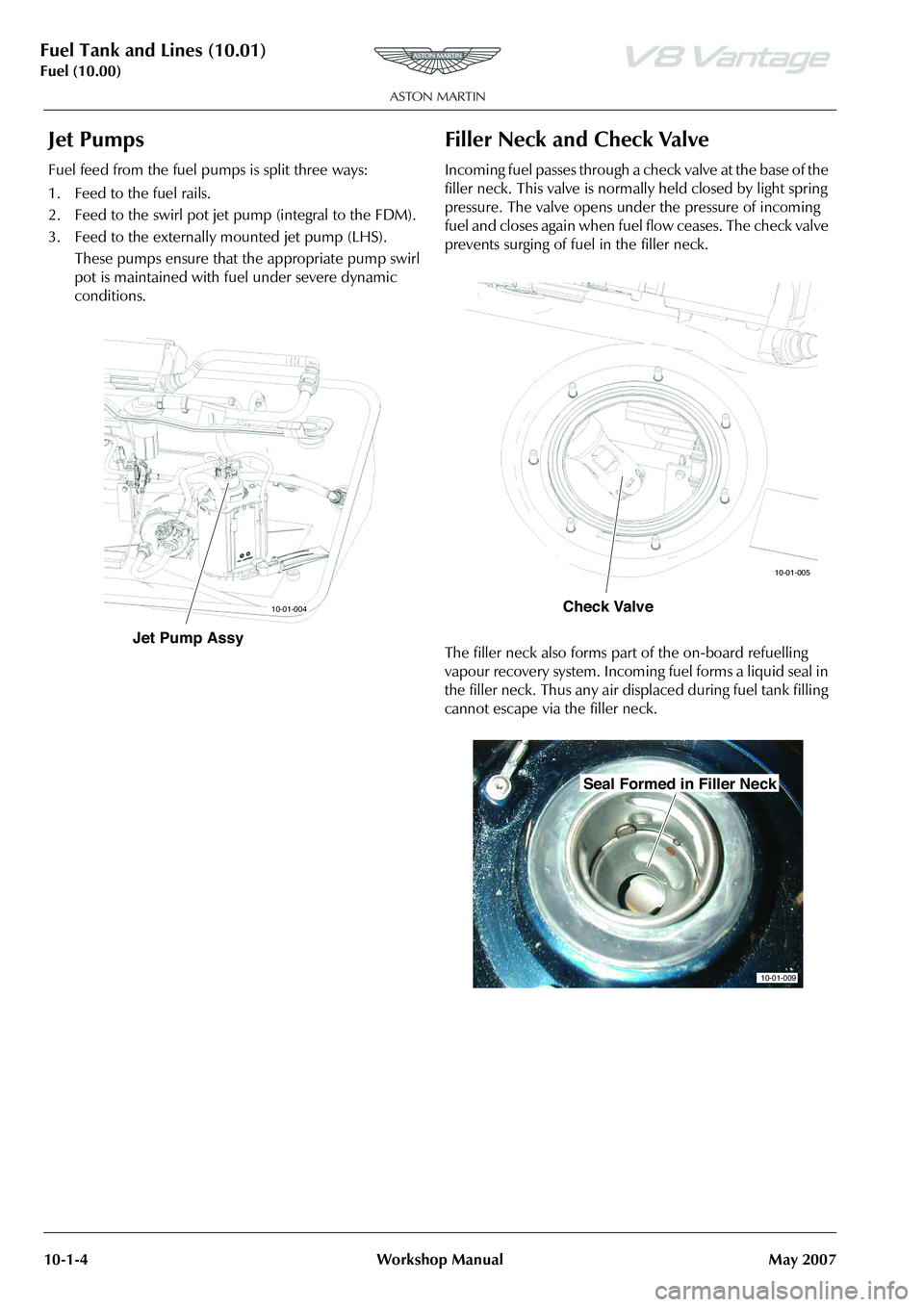
Fuel Tank and Lines (10.01)
Fuel (10.00)10-1-4 Workshop Manual May 2007
Jet Pumps
Fuel feed from the fuel pumps is split three ways:
1. Feed to the fuel rails.
2. Feed to the swirl pot jet pump (integral to the FDM).
3. Feed to the externally mounted jet pump (LHS). These pumps ensure that the appropriate pump swirl
pot is maintained with fuel under severe dynamic
conditions.
Filler Neck and Check Valve
Incoming fuel passes through a check valve at the base of the
filler neck. This valve is normally held closed by light spring
pressure. The valve opens under the pressure of incoming
fuel and closes again when fuel flow ceases. The check valve
prevents surging of fuel in the filler neck.
The filler neck also forms part of the on-board refuelling
vapour recovery system. Incoming fuel forms a liquid seal in
the filler neck. Thus any air displaced during fuel tank filling
cannot escape via the filler neck.
- H W 3 X P S $ V V \
&