tow CHEVROLET CAMARO 1967 1.G Chassis Repair Manual
[x] Cancel search | Manufacturer: CHEVROLET, Model Year: 1967, Model line: CAMARO, Model: CHEVROLET CAMARO 1967 1.GPages: 659, PDF Size: 114.24 MB
Page 299 of 659
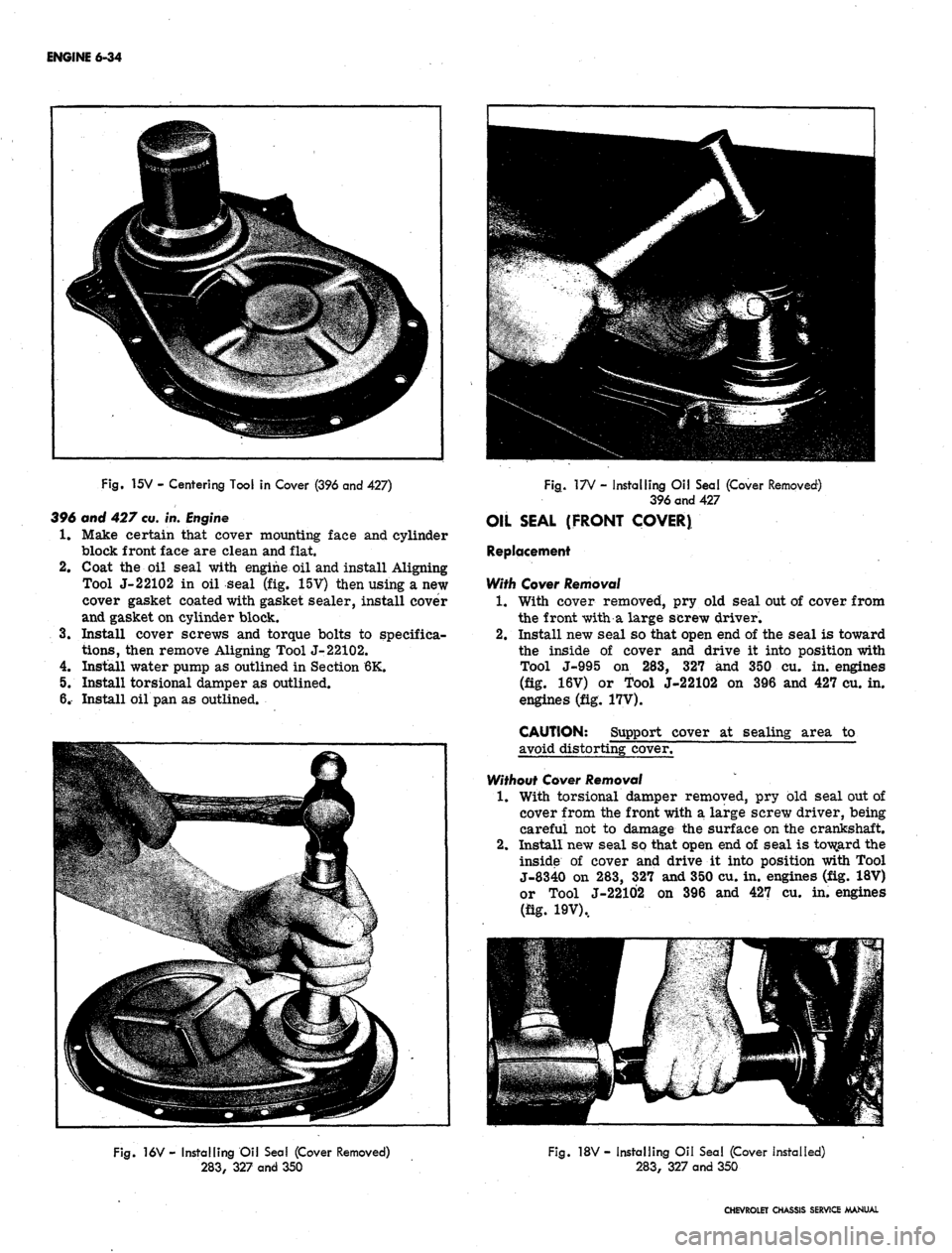
ENGINE 6-34
Fig.
15V - Centering Tool in Cover (396 and 427)
396 and 427
cu.
in.
Engine
1.
Make certain that cover mounting face and cylinder
block front face are clean and flat.
2.
Coat the oil seal with engine oil and install Aligning
Tool J-22102 in oil seal (fig. 15V) then using a new
cover gasket coated with gasket sealer, install cover
and gasket on cylinder block.
3.
Install cover screws and torque bolts to specifica-
tions,
then remove Aligning Tool J-22102.
4.
Install water pump as outlined in Section 6K.
5. Install torsional damper as outlined.
6. Install oil pan as outlined.
Fig.
17V - Installing Oil Seal (Cover Removed)
396 and 427
OIL SEAL (FRONT COVER)
Replacement
With Cover
Removal
1.
With cover removed, pry old seal out of cover from
the front with a large screw driver.
2.
Install new seal so that open end of the seal is toward
the inside of cover and drive it into position with
Tool J-995 on 283, 327 and 350 cu. in. engines
(fig. 16V) or Tool J-22102 on 396 and 427 cu. in.
engines (fig. 17V).
CAUTION: Support cover at sealing area to
avoid distorting cover.
Without Cover
Removal
1.
With torsional damper removed, pry old seal out of
cover from the front with a large screw driver, being
careful not to damage the surface on the crankshaft.
2.
Install new seal so that open end of seal is toward the
inside of cover and drive it into position with Tool
J-8340 on 283, 327 and 350 cu. in. engines (fig. 18V)
or Tool J-22102 on 396 and 427 cu. in. engines
(fig. 19V),
Fig.
16V - Installing Oil Seal (Cover Removed)
283,
327 and 350
Fig.
18V- Installing Oil Sea! (Cover Installed)
283,
327 and 350
CHEVROLET CHASSIS SERVICE MANUAL
Page 317 of 659
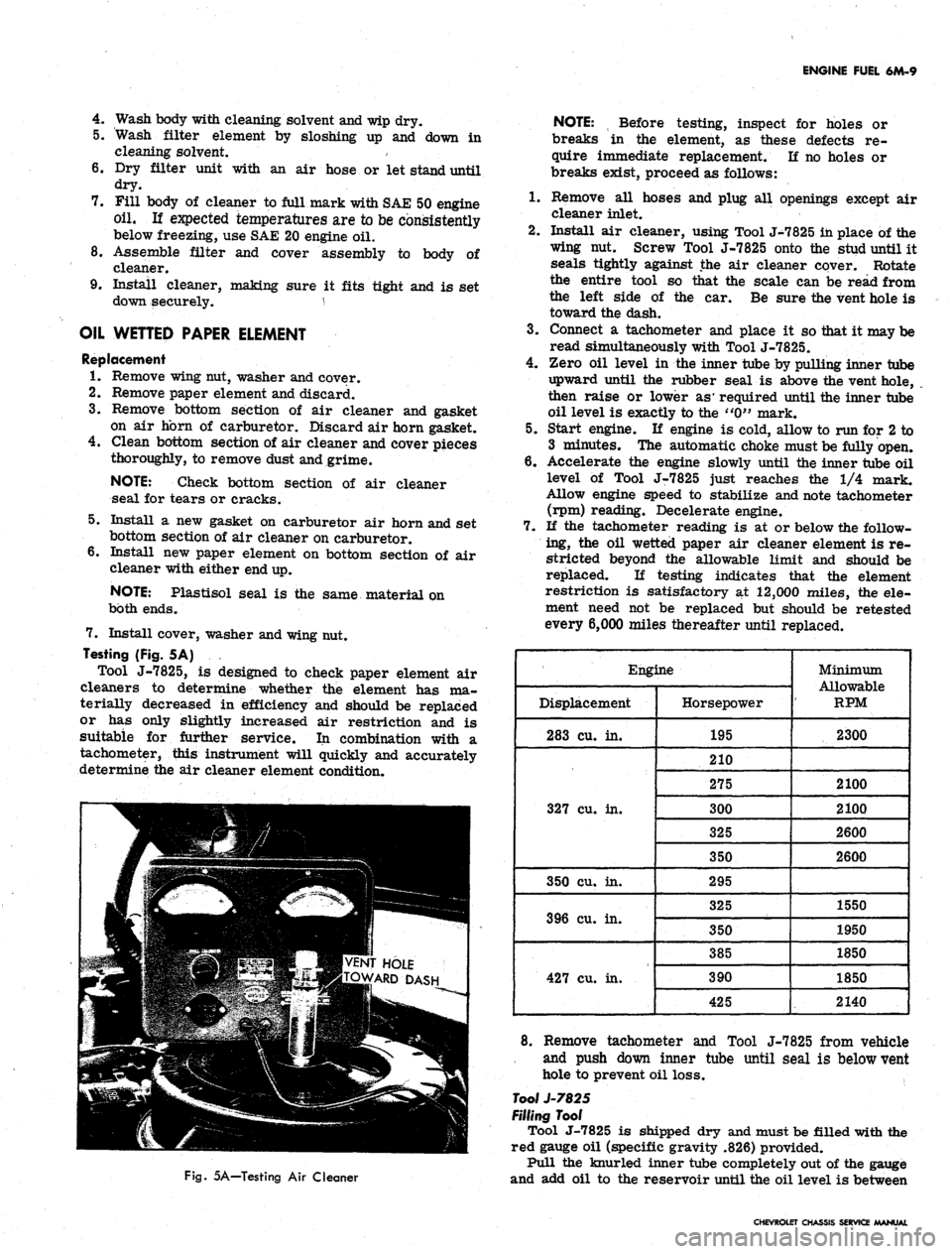
ENGINE FUEL 6M-9
4.
Wash body with cleaning solvent and wip dry.
5. Wash filter element by sloshing up and down in
cleaning solvent.
6. Dry filter unit with an air hose or let stand until
dry.
7. Fill body of cleaner to full mark with SAE 50 engine
oil. If expected temperatures are to be consistently
below freezing, use SAE 20 engine oil.
8. Assemble filter and cover assembly to body of
cleaner.
9. Install cleaner, making sure it fits tight and is set
down securely. \
OIL
WETTED
PAPER
ELEMENT
Replacement
1.
Remove wing nut, washer and cover.
2.
Remove paper element and discard.
3.
Remove bottom section of air cleaner and gasket
on air horn of carburetor. Discard air horn gasket.
4.
Clean bottom section of air cleaner and cover pieces
thoroughly, to remove dust and grime.
NOTE:
Check bottom section of air cleaner
seal for tears or cracks.
5. Install a new gasket on carburetor air horn and set
bottom section of air cleaner on carburetor.
6. Install new paper element on bottom section of air
cleaner with either end up.
NOTE:
Plastisol seal is the same material on
both ends.
7. Install cover, washer and wing nut.
Testing (Fig. 5A)
Tool J-7825, is designed to check paper element air
cleaners to determine whether the element has ma-
terially decreased in efficiency arid should be replaced
or has only slightly increased air restriction and is
suitable for further service. In combination with a
tachometer, this instrument will quickly and accurately
determine the air cleaner element condition.
VENT HOLE
TOWARD DASH
NOTE:
t Before testing, inspect for holes or
breaks in the element, as these defects re-
quire immediate replacement. If no holes or
breaks exist, proceed as follows:
1.
Remove all hoses and plug all openings except air
cleaner inlet.
2.
Install air cleaner, using Tool J-7825 in place of the
wing nut. Screw Tool J-7825 onto the stud until it
seals tightly against the air cleaner cover. Rotate
the entire tool so that the scale can be read from
the left side of the car. Be sure the vent hole is
toward the dash.
3.
Connect a tachometer and place it so that it may be
read simultaneously with Tool J-7825.
4.
Zero oil level in the inner tube by pulling inner tube
upward until the rubber seal is above the vent hole,
then raise or lower as' required until the inner tube
oil level is exactly to the "0" mark.
5. Start engine. If engine is cold, allow to run for 2 to
3 minutes. The automatic choke must be fully open.
6. Accelerate the engine slowly until the inner tube oil
level of Tool J-7825 just reaches the 1/4 mark.
Allow engine speed to stabilize and note tachometer
(rpm) reading. Decelerate engine.
7. If the tachometer reading is at or below the follow-
ing, the oil wetted paper air cleaner element is re-
stricted beyond the allowable limit and should be
replaced. If testing indicates that the element
restriction is satisfactory at 12,000 miles, the ele-
ment need not be replaced but should be retested
every 6,000 miles thereafter until replaced.
Engine
Displacement
283 cu.
in.
327 cu.
in.
350 cu. in.
396 cu.
in.
427 cu.
in.
Horsepower
195
210
275
300
325
350
295
325
350
385
390
425
Minimum
Allowable
RPM
2300
2100
210Q
2600
2600
1550
1950
1850
1850
2140
Fig.
5A—Testing Air Cleaner
8. Remove tachometer and Tool J-7825 from vehicle
and push down inner tube until seal is below vent
hole to prevent oil loss.
Tool J-7825
FiHing
Tool
Tool J-7825 is shipped dry and must be filled with the
red gauge oil (specific gravity .826) provided.
Pull the knurled inner tube completely out of the gauge
and add oil to the reservoir until the oil level is between
CHEVROLET CHASSIS SERVICE /MANUAL
Page 323 of 659
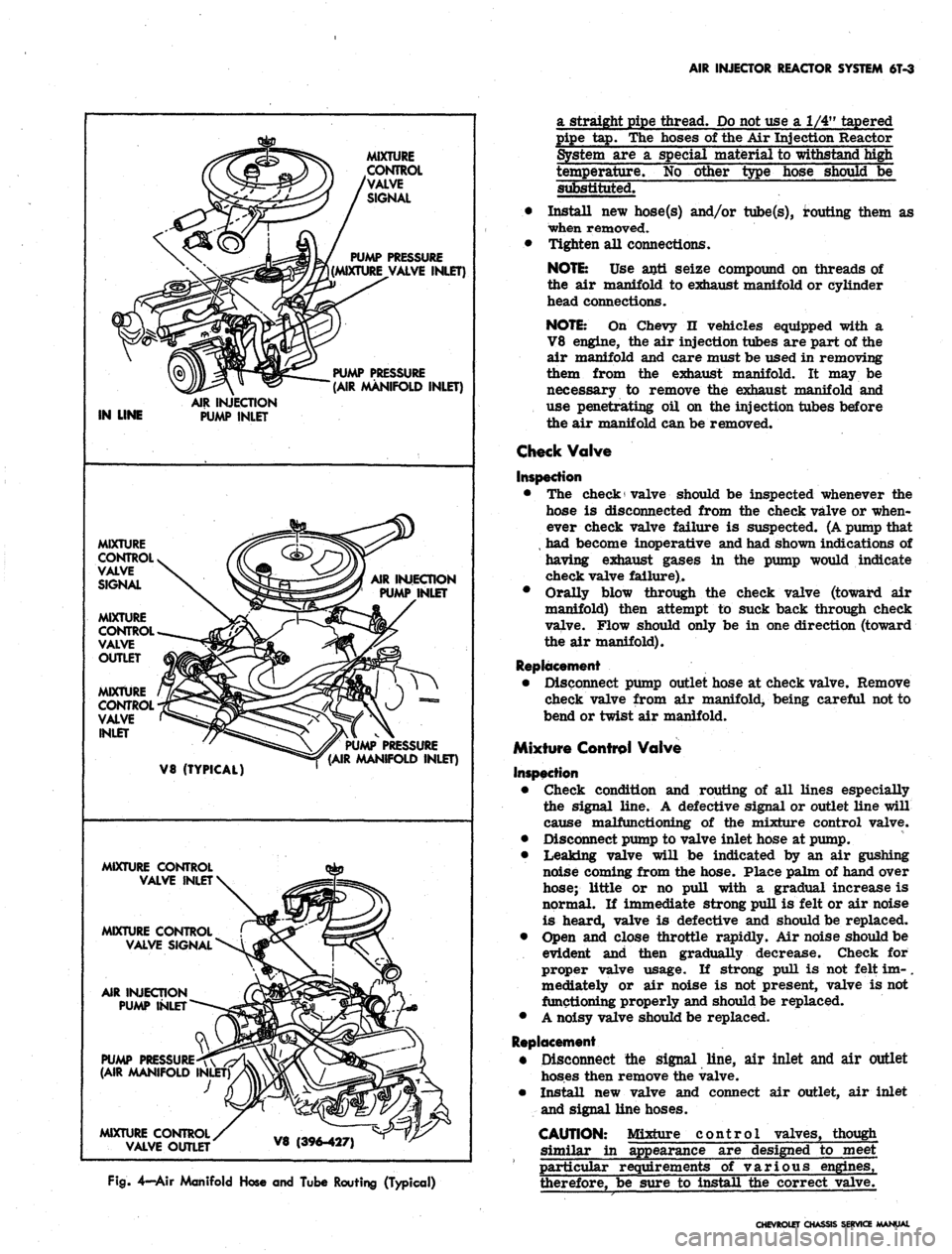
AIR INJECTOR REACTOR SYSTEM
6T-3
MIXTURE
CONTROL
VALVE
SIGNAL
PUMP PRESSURE
(MIXTURE VALVE INLET)
PUMP PRESSURE
(AIR MANIFOLD INLET)
IN LINE
AIR INJECTION
PUMP INLET
MIXTURE
CONTROL
VALVE
SIGNAL
MIXTURE
CONTROL
VALVE
OUTLET
MIXTURE
CONTROL
VALVE
INLET
AIR INJECTION
PUMP INLET
V8 (TYPICAL)
PUMP PRESSURE
(AIR MANIFOLD INLET)
MIXTURE CONTROL
VALVE INLET
MIXTURE CONTROL
VALVE SIGNAL
AIR INJECTION
PUMP INLET
PUMP PRESSURE^
(AIR MANIFOLD
J
MIXTURE CONTROL
VALVE OUTLET
V8 (396-427)
Fig.
4—Air Manifold Hose and Tube Routing (Typical)
a straight pipe thread.
Do
not use
a 1/4"
tapered
pipe
tap. The
hoses
of
the
Air
Injection Reactor
System
are a
special material
to
withstand high
temperature.
No
other type hose should
be
substituted.
• Install
new
hose(s) and/or tube(s), routing them
as
when removed.
• Tighten
all
connections.
NOTE:
Use
anti seize compound
on
threads
of
the
air
manifold
to
exhaust manifold
or
cylinder
head connections.
NOTE:
On
Chevy
n
vehicles equipped with
a
V8 engine,
the air
injection tubes
are
part
of the
air manifold
and
care must
be
used
in
removing
them from
the
exhaust manifold.
It may be
necessary
to
remove
the
exhaust manifold
and
use penetrating
oil on the
injection tubes before
the
air
manifold can
be
removed.
Check Valve
Inspection
•
The
check valve should
be
inspected whenever
the
hose
is
disconnected from
the
check valve
or
when-
ever check valve failure
is
suspected. (A pump that
,
had
become inoperative and had shown indications
of
having exhaust gases
in the
pump would indicate
check valve failure)..
• Orally blow through
the
check valve (toward
air
manifold) then attempt
to
suck back through check
valve. Flow should only
be in one
direction (toward
the
air
manifold).
Replacement
• Disconnect pump outlet hose
at
check valve. Remove
check valve from
air
manifold, being careful not
to
bend
or
twist
air
manifold.
Mixture Control Valve
Inspection
• Check condition
and
routing
of all
lines especially
the signal line.
A
defective signal
or
outlet line will
cause malfunctioning
of the
mixture control valve.
• Disconnect pump
to
valve inlet hose
at
pump.
• Leaking valve will
be
indicated
by an air
gushing
noise coming from
the
hose. Place palm
of
hand over
hose; little
or no
pull with
a
gradual increase
is
normal.
If
immediate strong pull
is
felt
or air
noise
is heard, valve
is
defective
and
should
be
replaced.
• Open
and
close throttle rapidly.
Air
noise should
be
evident
and
then gradually decrease. Check
for
proper valve usage.
If
strong pull
is not
felt
im-.
mediately
or air
noise
is not
present, valve
is not
functioning properly and should be replaced.
•
A
noisy valve should be replaced.
Replacement
• Disconnect
the
signal line,
air
inlet
and air
outlet
hoses then remove
the
valve.
• Install
new
valve
and
connect
air
outlet,
air
inlet
and signal line hoses.
CAUTION: Mixture control valves, though
similar
in
appearance
are
designed
to
meet
particular requirements
of
various engines,
therefore,
be
sure
to
install
the
correct valve.
CHEVROLET CHASSIS SERVICE MANUAL
Page 335 of 659
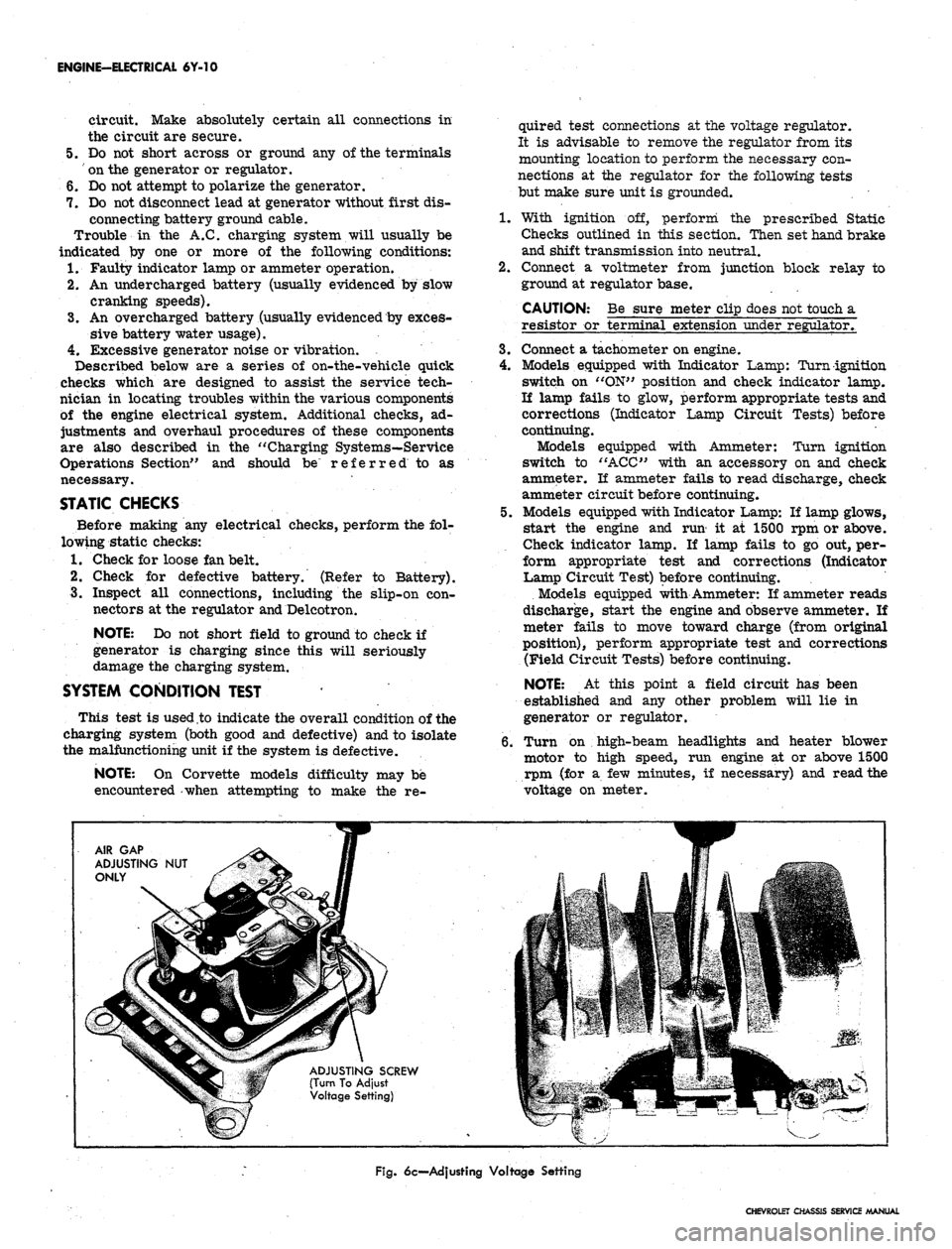
ENGINE-ELECTRICAL 6Y-10
circuit. Make absolutely certain all connections in
the circuit are secure.
5.
Do not short across or ground any of the terminals
on the generator or regulator.
6. Do not attempt to polarize the generator.
7.
Do not disconnect lead at generator without first dis-
connecting battery ground cable.
Trouble in the A.C. charging system will usually be
indicated by one or more of the following conditions:
1.
Faulty indicator lamp or ammeter operation.
2.
An undercharged battery (usually evidenced by slow
cranking speeds).
3.
An overcharged battery (usually evidenced by exces-
sive battery water usage).
4.
Excessive generator noise or vibration.
Described below are a series of on-the-vehicle quick
checks which are designed to assist the service tech-
nician in locating troubles within the various components
of the engine electrical system. Additional checks, ad-
justments and overhaul procedures of these components
are also described in the "Charging Systems—Service
Operations Section" and should be referred to as
necessary.
STATIC CHECKS
Before making any electrical checks, perform the fol-
lowing static checks:
1.
Check for loose fan belt.
2.
Check for defective battery. (Refer to Battery).
3.
Inspect all connections, including the slip-on con-
nectors at the regulator and Delcotron.
NOTE: Do not short field to ground to check if
generator is charging since this will seriously
damage the charging system.
SYSTEM CONDITION TEST
This test is used .to indicate the overall condition of the
charging system (both good and defective) and to isolate
the malfunctioning unit if the system is defective.
NOTE: On Corvette models difficulty may be
encountered -when attempting to make the re-
quired test connections at the voltage regulator.
It is advisable to remove the regulator from its
mounting location to perform the necessary con-
nections at the regulator for the following tests
but make sure unit is grounded.
1.
With ignition off, perform the prescribed Static
Checks outlined in this section. Then set hand brake
and shift transmission
into
neutral.
2.
Connect a voltmeter from junction block relay to
ground at regulator base.
CAUTION: Be sure meter clip does not touch a
resistor or terminal extension under regulator,
3.
Connect a tachometer on engine.
4.
Models equipped with Indicator Lamp: Turn ignition
switch on "ON" position and check indicator lamp.
If lamp fails to glow, perform appropriate tests and
corrections (Indicator Lamp Circuit Tests) before
continuing.
Models equipped with Ammeter: Turn ignition
switch to "ACC" with an accessory on and check
ammeter. If ammeter fails to read discharge, check
ammeter circuit before continuing.
5.
Models equipped with Indicator Lamp: If lamp glows,
start the engine and run' it at 1500 rpm or above.
Check indicator lamp. If lamp fails to go out, per-
form appropriate test and corrections (Indicator
Lamp Circuit Test) before continuing.
Models equipped with Ammeter: If ammeter reads
discharge, start the engine and observe ammeter. If
meter fails to move toward charge (from original
position), perform appropriate test and corrections
(Field Circuit Tests) before continuing.
NOTE: At this point a field circuit has been
established and any other problem will lie in
generator or regulator.
6. Turn on high-beam headlights and heater blower
motor to high speed, run engine at or above 1500
rpm (for a few minutes, if necessary) and read the
voltage on meter.
AIR GAP
ADJUSTING NUT
ONLY
ADJUSTING SCREW
(Turn To Adjust
Voltage Setting)
Fig.
6c—Adjusting Voltage Setting
CHEVROLET CHASSIS SERVICE MANUAL
Page 344 of 659
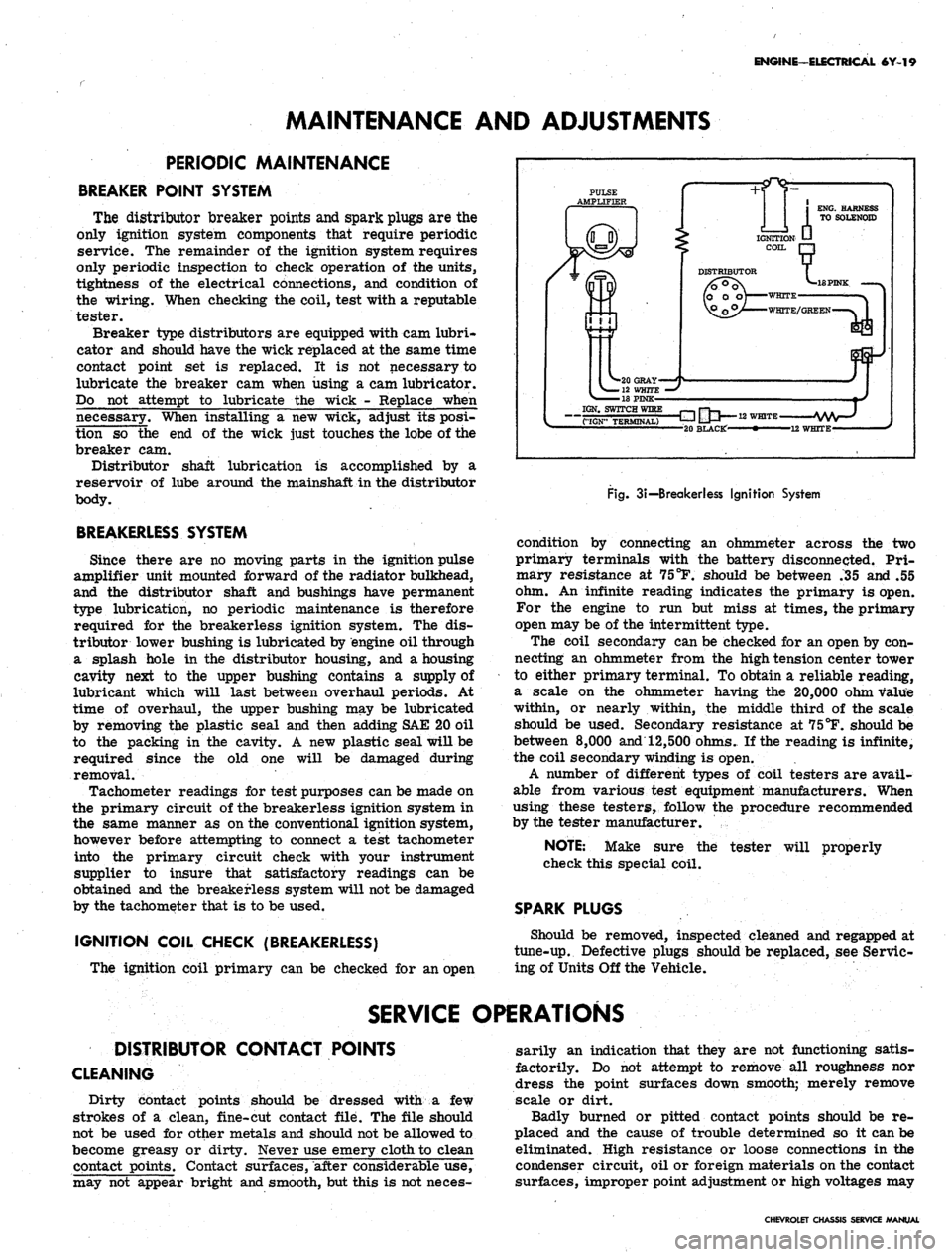
MAINTENANCE AND ADJUSTMENTS
ENGINE-ELECTRICAL 6Y-19
PERIODIC MAINTENANCE
BREAKER POINT SYSTEM
The distributor breaker points and spark plugs are the
only ignition system components that require periodic
service. The remainder of the ignition system requires
only periodic inspection to check operation of the units,
tightness of the electrical connections, and condition of
the wiring. When checking the coil, test with a reputable
tester.
Breaker type distributors are equipped with cam lubri-
cator and should have the wick replaced at the same time
contact point set is replaced. It is not necessary to
lubricate the breaker cam when using a cam lubricator.
Do not attempt to lubricate the wick - Replace when
necessary. When installing a new wick, adjust its posi-
tion so the end of the wick just touches the lobe of the
breaker cam.
Distributor shaft lubrication is accomplished by a
reservoir of lube around the mainshaft in the distributor
body.
BREAKERLESS SYSTEM
Since there are no moving parts in the ignition pulse
amplifier unit mounted forward of the radiator bulkhead,
and the distributor shaft and bushings have permanent
type lubrication, no periodic maintenance is therefore
required for the breakerless ignition system. The dis-
tributor lower bushing is lubricated by engine oil through
a splash hole in the distributor housing, and a housing
cavity next to the upper bushing contains a supply of
lubricant which will last between overhaul periods. At
time of overhaul, the upper bushing may be lubricated
by removing the plastic seal and then adding SAE 20 oil
to the packing in the cavity. A new plastic seal will be
required since the old one will be damaged during
removal.
Tachometer readings for test purposes can be made on
the primary circuit of the breakerless ignition system in
the same manner as on the conventional ignition system,
however before attempting to connect a test tachometer
into the primary circuit check with your instrument
supplier to insure that satisfactory readings can be
obtained and the breakerless system will not be damaged
by the tachometer that is to be used,
IGNITION COIL CHECK (BREAKERLESS)
The ignition coil primary can be checked for an open
PULSE
AMPLIFIER
IGN. SWITCH WIRE
"("IGN" TERMINAL)
-E3 IJU
12
WHITE-
-20 BLACKf' • 12 WHITE-
Fig.
3i—
Breakerless Ignition System
condition by connecting an ohmmeter across the two
primary terminals with the battery disconnected. Pri-
mary resistance at 75
°F.
should be between .35 and .55
ohm. An infinite reading indicates the primary is open.
For the engine to run but miss at times, the primary
open may be of the intermittent type.
The coil secondary can be checked for an open by con-
necting an ohmmeter from the high tension center tower
to either primary terminal. To obtain a reliable reading,
a scale on the ohmmeter having the 20,000 ohm value
within, or nearly within, the middle third of the scale
should be used. Secondary resistance at 75°F. should be
between
8,000
and 12,500 ohms. If the reading is infinite,
the coil secondary winding is open.
A number of different types of coil testers are avail-
able from various test equipment manufacturers. When
using these testers, follow the procedure recommended
by the tester manufacturer.
tester will properly
NOTE:
Make sure the
check this special coil.
SPARK PLUGS
Should be removed, inspected cleaned and regapped at
tune-up. Defective plugs should be replaced, see Servic-
ing of Units Off the Vehicle.
SERVICE OPERATIONS
DISTRIBUTOR CONTACT POINTS
CLEANING
Dirty contact points should be dressed with a few
strokes of a clean, fine-cut contact file. The file should
not be used for other metals and should not be allowed to
become greasy or dirty. Never use emery cloth to clean
contact points. Contact surfaces, after considerable use,
may not appear bright and smooth, but this is not neces-
sarily an indication that they are not functioning satis-
factorily. Do not attempt to remove all roughness nor
dress the point surfaces down smooth; merely remove
scale or dirt.
Badly burned or pitted contact points should be re-
placed and the cause of trouble determined so it can be
eliminated. High resistance or loose connections in the
condenser circuit, oil or foreign materials on the contact
surfaces, improper point adjustment or high voltages may
CHEVROLET CHASSIS SERVICE MANUAL
Page 348 of 659
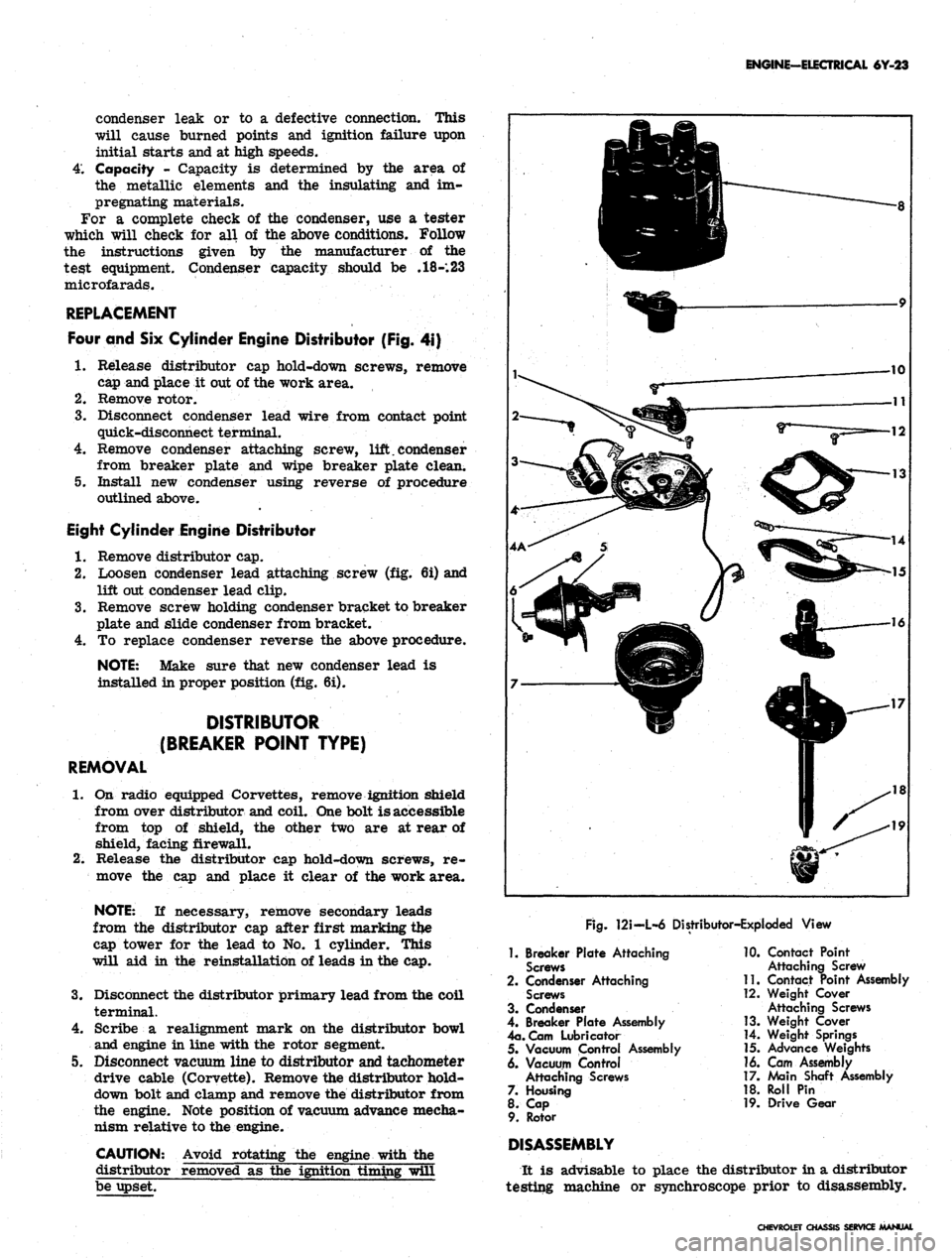
ENGINE-ELECTRICAL 6Y-23
condenser leak or to a defective connection. This
will cause burned points and ignition failure upon
initial starts and at high speeds.
4.
Capacity - Capacity is determined by the area of
the metallic elements and the insulating and im-
pregnating materials.
For a complete check of the condenser, use a tester
which will check for all of the above conditions. Follow
the instructions given by the manufacturer of the
test equipment. Condenser capacity should be
.18-:
23
microfarads.
REPLACEMENT
Four and Six Cylinder Engine Distributor (Fig. 4i)
1.
Release distributor cap hold-down screws, remove
cap and place it out of the work area.
2.
Remove rotor.
3.
Disconnect condenser lead wire from contact point
quick-disconnect terminal.
4.
Remove condenser attaching screw, lift.condenser
from breaker plate and wipe breaker plate clean.
5. Install new condenser using reverse of procedure
outlined above.
Eight Cylinder Engine Distributor
1.
Remove distributor cap.
2.
Loosen condenser lead attaching screw (fig. 6i) and
lift out condenser lead clip.
3.
Remove screw holding condenser bracket to breaker
plate and slide condenser from bracket.
4.
To replace condenser reverse the above procedure.
NOTE:
Make sure that new condenser lead is
installed in proper position (fig. 6i).
DISTRIBUTOR
(BREAKER POINT TYPE)
REMOVAL
1.
On radio equipped Corvettes, remove ignition shield
from over distributor and coil. One bolt is accessible
from top of shield, the other two are at rear of
shield, facing firewall.
2.
Release the distributor cap hold-down screws, re-
move the cap and place it clear of the work area.
NOTE:
If necessary, remove secondary leads
from the distributor cap after first marking the
cap tower for the lead to No. 1 cylinder. This
will aid in the reinstallation of leads in the cap.
3.
Disconnect the distributor primary lead from the coil
terminal.
4.
Scribe a realignment mark on the distributor bowl
and engine in line with the rotor segment.
5. Disconnect vacuum line to distributor and tachometer
drive cable (Corvette). Remove the distributor hold-
down bolt and elamp and remove the distributor from
the engine. Note position of vacuum advance mecha-
nism relative to the engine.
CAUTION: Avoid rotating the engine with the
distributor removed as the ignition timing will
be upset.
Rg.
121-L-6 Distributor-Exploded View
1.
Breaker Plate Attaching
Screws
2.
Condenser Attaching
Screws
3. Condenser
4.
Breaker Plate Assembly
4a.
Cam Lubricator
5. Vacuum Control Assembly
6. Vacuum Control
Attaching Screws
7. Housing
8. Cap
9. Rotor
DISASSEMBLY
10.
Contact Point
Attaching Screw
11.
Contact Point Assembly
12.
Weight Cover
Attaching Screws
13.
Weight Cover
14.
Weight Springs
15.
Advance Weights
16. Cam Assembly
17.
Main Shaft Assembly
18.
Roll Pin
19.
Drive Gear
It is advisable to place the distributor in a distributor
testing machine or synchroscope prior to disassembly.
CHEVROLET CU
SERVICE MANUAL
Page 349 of 659
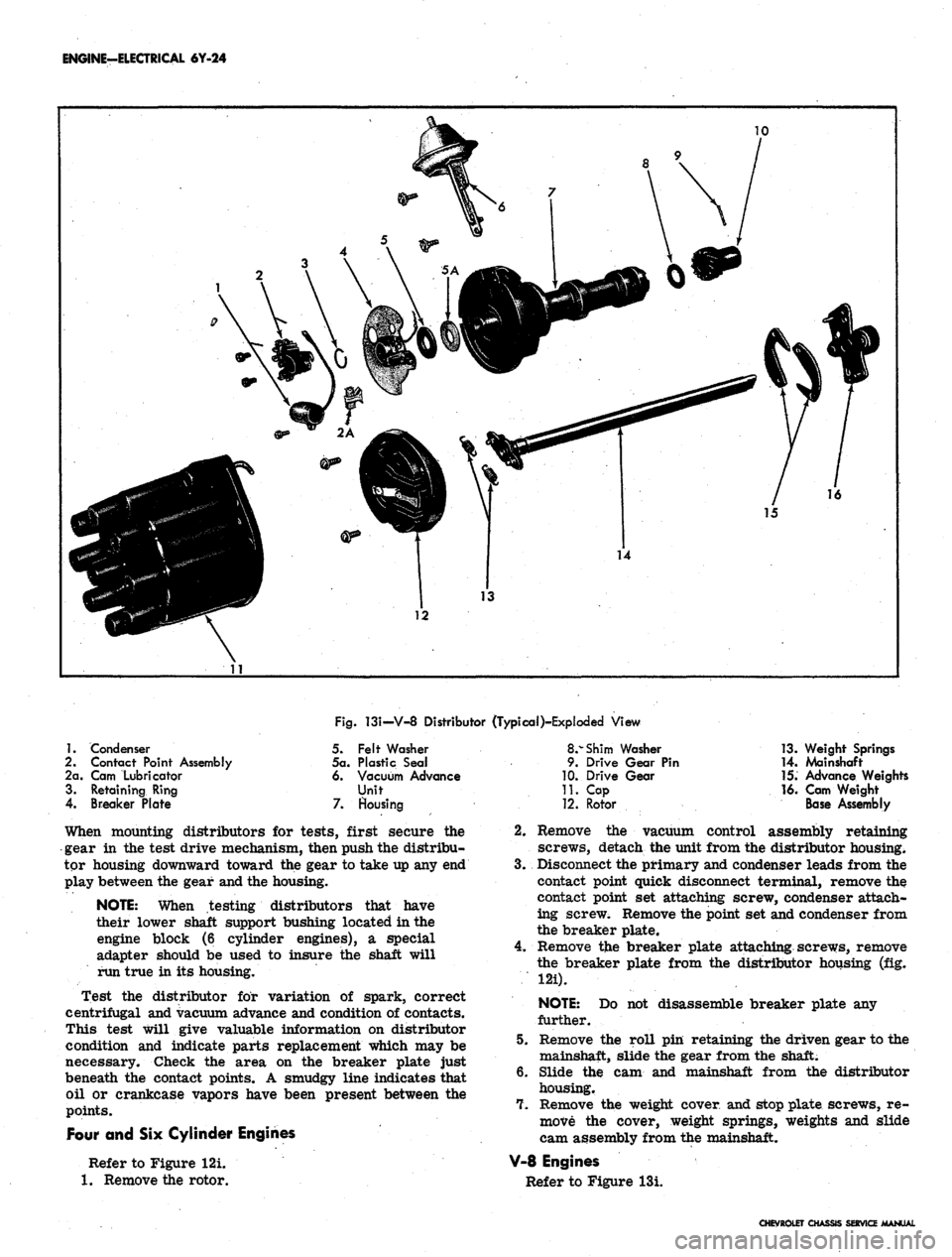
ENGINE-ELECTRICAL 6Y-24
Fig.
13I-V-8 Distributor (Typical)-Exploded View
1.
2.
2a.
3.
4.
Condenser
Contact Point Assembly
Cam Lubricator
Retaining Ring
Breaker Plate
5.
5a.
6.
7.
Felt Washer
Plastic Seal
Vacuum Advance
Unit
Housing
8.^
Shim
Washer
9. Drive Gear Pin
10.
Drive Gear
11.
Cap
12.
Rotor
13.
Weight Springs
14.
Mainshaft
15.
Advance Weights
16.
Cam Weight
Base Assembly
When mounting distributors for tests, first secure the
gear in the test drive mechanism, then push the distribu-
tor housing downward toward the gear to take up any end
play between the gear and the housing.
NOTE:
When testing distributors that have
their lower shaft support bushing located in the
engine block (6 cylinder engines), a special
adapter should be used to insure the shaft will
run true in its housing.
Test the distributor for variation of spark, correct
centrifugal and vacuum advance and condition of contacts.
This test will give valuable information on distributor
condition and indicate parts replacement which may be
necessary. Check the area on the breaker plate just
beneath the contact points. A smudgy line indicates that
oil or crankcase vapors have been present between the
points.
Four and Six Cylinder Engines
Refer to Figure 12i.
1.
Remove the rotor.
2.
3.
Remove the vacuum control assembly retaining
screws, detach the unit from the distributor housing.
Disconnect the primary and condenser leads from the
contact point quick disconnect terminal, remove the
contact point set attaching screw, condenser attach-
ing screw. Remove the point set and condenser from
the breaker plate.
Remove the breaker plate attaching screws, remove
the breaker plate from the distributor housing (fig.
NOTE:
Do not disassemble breaker plate any
further.
5. Remove the roll pin retaining the driven gear to the
mainshaft, slide the gear from the shaft.
6. Slide the cam and mainshaft from the distributor
housing.
7. Remove the weight cover, and stop plate screws, re-
move the cover, weight springs, weights and slide
cam assembly from the mainshaft.
V-8 Engines
Refer to Figure 13i.
CHEVROLET CHASStS SERVICE MANUAL
Page 352 of 659
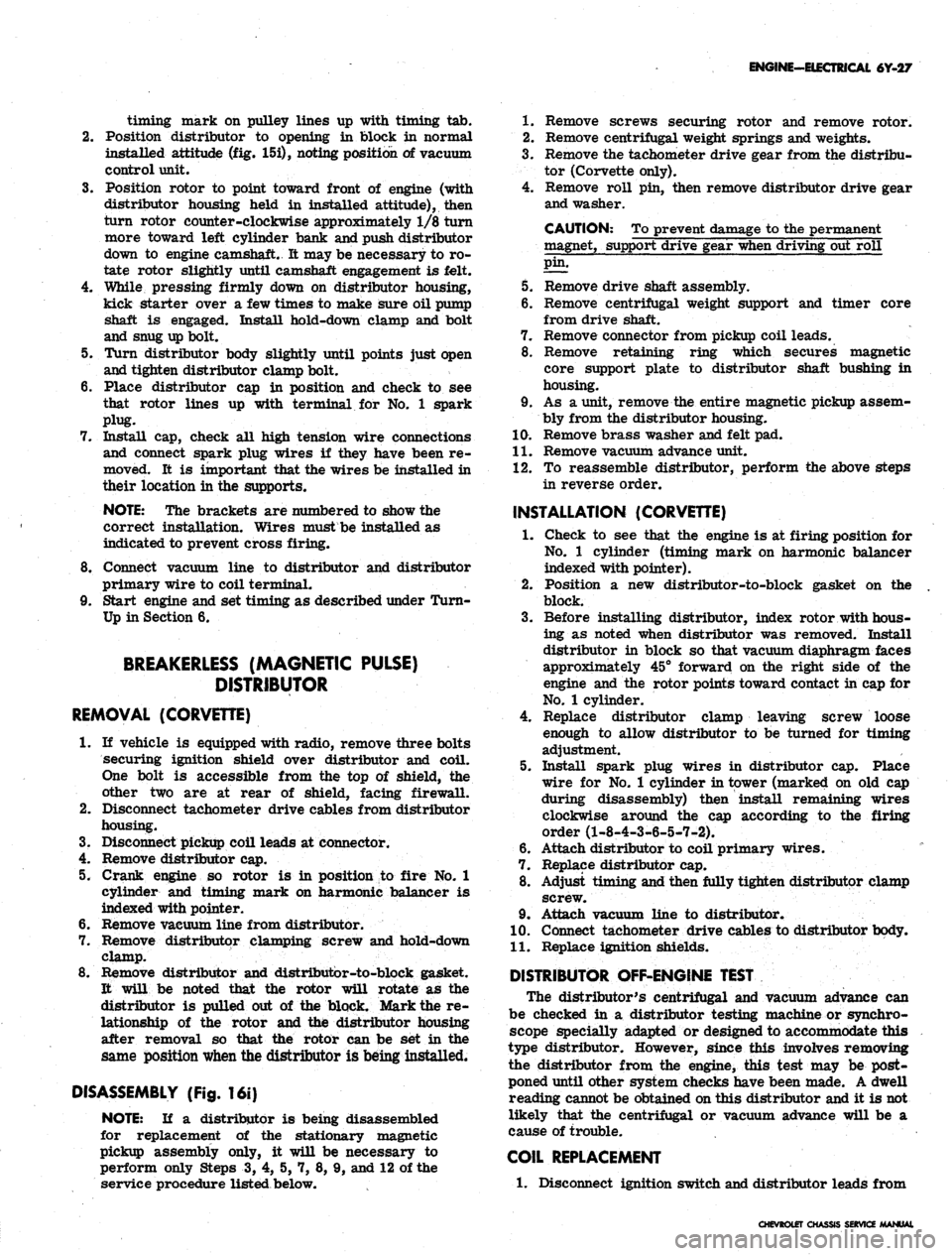
ENGINE-ELECTRICAL 6Y-27
timing mark on pulley lines up with timing tab.
2.
Position distributor to opening in block in normal
installed attitude (fig. 15i), noting position of vacuum
control unit.
3.
Position rotor to point toward front of engine (with
distributor housing held in installed attitude), then
turn rotor counter-clockwise approximately 1/8 turn
more toward left cylinder bank and push distributor
down to engine camshaft. It may be necessary to ro-
tate rotor slightly until camshaft engagement is felt.
4.
While pressing firmly down on distributor housing,
kick starter over a few times to make sure oil pump
shaft is engaged. Install hold-down clamp and bolt
and snug up bolt.
5. Turn distributor body slightly until points just open
and tighten distributor clamp bolt.
6. Place distributor cap in position and check to see
that rotor lines up with terminal for No. 1 spark
plug.
7. Install cap, check all high tension wire connections
and connect spark plug wires if they have been re-
moved. It is important that the wires be installed in
their location in the supports.
NOTE:
The brackets are numbered to show the
correct installation. Wires must be installed as
indicated to prevent cross firing.
8. Connect vacuum line to distributor and distributor
primary wire to coil terminal.
9. Start engine and set timing as described under Turn-
Up in Section 6.
BREAKERLESS (MAGNETIC PULSE)
DISTRIBUTOR
REMOVAL (CORVETTE)
1.
If vehicle is equipped with radio, remove three bolts
securing ignition shield over distributor and coil.
One bolt is accessible from the top of shield, the
other two are at rear of shield, facing firewall.
2.
Disconnect tachometer drive cables from distributor
housing.
3.
Disconnect pickup coil leads at connector.
4.
Remove distributor cap.
5. Crank engine so rotor is in position to fire No. 1
cylinder and timing mark on harmonic balancer is
indexed with pointer.
6. Remove vacuum line from distributor.
7. Remove distributor clamping screw and hold-down
clamp.
8. Remove distributor and distributor-to-block gasket.
It will be noted that the rotor will rotate as the
distributor is pulled out of the block. Mark the re-
lationship of the rotor and the distributor housing
after removal so that the rotor can be set in the
same position when the distributor is being installed.
DISASSEMBLY (Fig. 16i)
NOTE:
If a distributor is being disassembled
for replacement of the stationary magnetic
pickup assembly only, it will be necessary to
perform only Steps 3, 4, 5, 7, 8, 9, and 12 of the
service procedure listed below.
1.
Remove screws securing rotor and remove rotor.
2.
Remove centrifugal weight springs and weights.
3.
Remove the tachometer drive gear from the distribu-
tor (Corvette only).
4.
Remove roll pin, then remove distributor drive gear
and washer.
CAUTION: To prevent
magnet, support drive gear
;e to the permanent
?n
driving out roll
pin.
5. Remove drive shaft assembly.
6. Remove centrifugal weight support and timer core
from drive shaft.
7. Remove connector from pickup coil leads.
8. Remove retaining ring which secures magnetic
core support plate to distributor shaft bushing in
housing.
9. As a unit, remove the entire magnetic pickup assem-
bly from the distributor housing.
10.
Remove brass washer and felt pad.
11.
Remove vacuum advance unit.
12.
To reassemble distributor, perform the above steps
in reverse order.
INSTALLATION (CORVETTE)
1.
Check to see that the engine is at firing position for
No.
1 cylinder (timing mark on harmonic balancer
indexed with pointer).
2.
Position a new distributor-to-block gasket on the
block.
3.
Before installing distributor, index rotor with hous-
ing as noted when distributor was removed. Install
distributor in block so that vacuum diaphragm faces
approximately 45° forward on the right side of the
engine and the rotor points toward contact in cap for
No.
1 cylinder.
4.
Replace distributor clamp leaving screw loose
enough to allow distributor to be turned for timing
adjustment.
5. Install spark plug wires in distributor cap. Place
wire for No. 1 cylinder in tower (marked on old cap
during disassembly) then install remaining wires
clockwise around the cap according to the firing
order (1-8-4-3-6-5-7-2).
6. Attach distributor to coil primary wires.
7. Replace distributor cap.
8. Adjust timing and then fully tighten distributor clamp
screw.
9. Attach vacuum line to distributor.
10.
Connect tachometer drive cables to distributor body.
11.
Replace ignition shields.
DISTRIBUTOR OFF-ENGINE TEST
The distributor's centrifugal and vacuum advance can
be checked in a distributor testing machine or synchro-
scope specially adapted or designed to accommodate this
type distributor. However, since this involves removing
the distributor from the engine, this test may be post-
poned until other system checks have been made. A dwell
reading cannot be obtained on this distributor and it is not
likely that the centrifugal or vacuum advance will be a
cause of trouble.
COIL REPLACEMENT
1.
Disconnect ignition switch and distributor leads from
CHEVROLET CHASSIS SERVICE MANUAL
Page 361 of 659
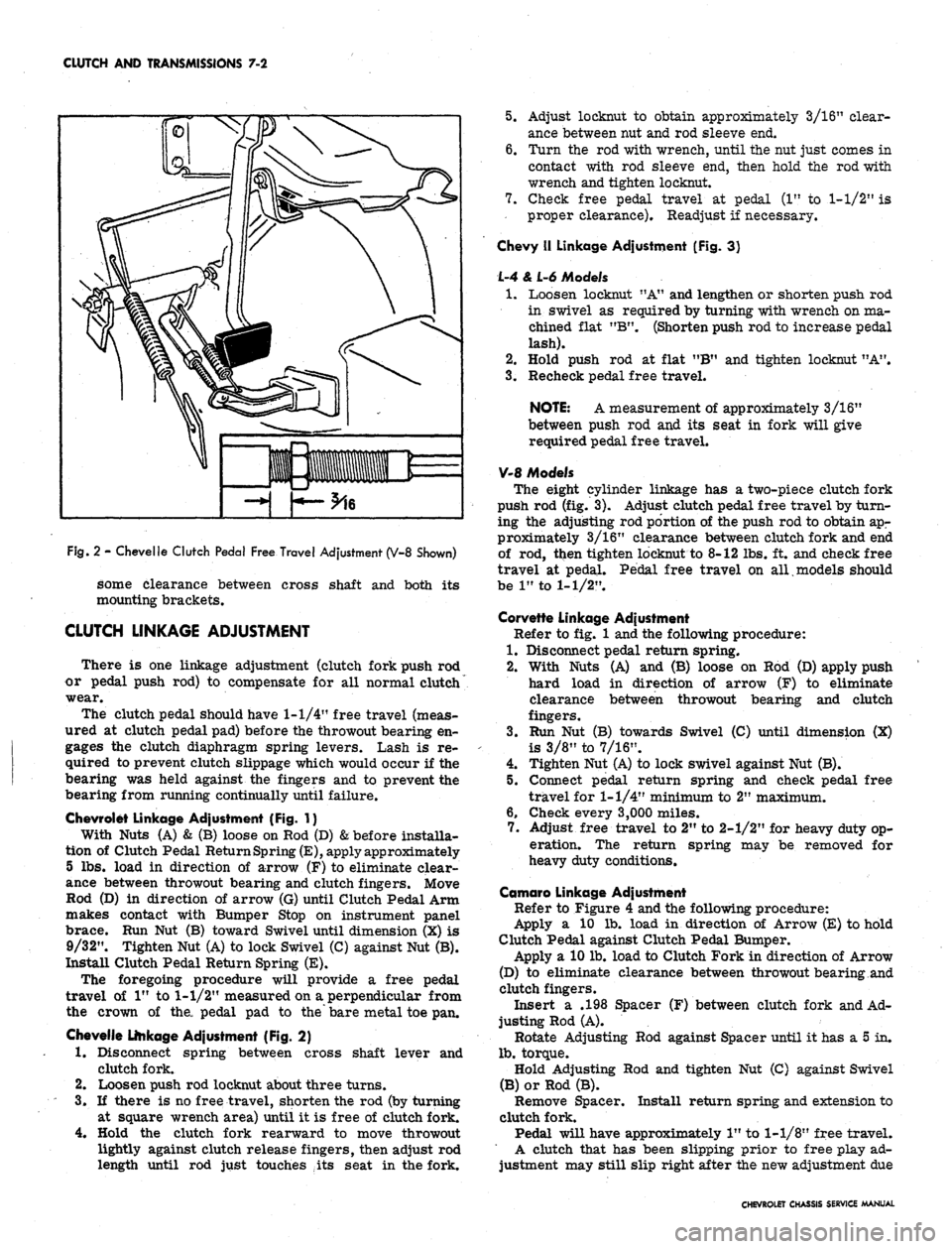
CLUTCH AND TRANSMISSIONS 7-2
Fig.
2 - Chevelle Clutch Pedal Free Travel Adjustment (V-8 Shown)
some clearance between cross shaft and both its
mounting brackets.
CLUTCH LINKAGE ADJUSTMENT
There is one linkage adjustment (clutch fork push rod
or pedal push rod) to compensate for all normal clutch
wear.
The clutch pedal should have
1-1/4"
free travel (meas-
ured at clutch pedal pad) before the throwout bearing en-
gages the clutch diaphragm spring levers. Lash is re-
quired to prevent clutch slippage which would occur if the
bearing was held against the fingers and to prevent the
bearing from running continually until failure.
Chevrolet Linkage Adjustment (Fig. 1}
With Nuts (A) & (B) loose on Rod (D)
&
before installa-
tion of Clutch Pedal Return Spring
(E),
apply approximately
5 lbs. load in direction of arrow (F) to eliminate clear-
ance between throwout bearing and clutch fingers. Move
Rod (D) in direction of arrow (G) until Clutch Pedal Arm
makes contact with Bumper Stop on instrument panel
brace. Run Nut (B) toward Swivel until dimension (X) is
9/32". Tighten Nut (A) to lock Swivel (C) against Nut (B).
Install Clutch Pedal Return Spring (E).
The foregoing procedure will provide a free pedal
travel of 1" to
1-1/2"
measured on a perpendicular from
the crown of the, pedal pad to the bare metal toe pan.
Chevelle Linkage Adjustment (Fig. 2)
1.
Disconnect spring between cross shaft lever and
clutch fork.
2.
Loosen push rod locknut about three turns.
3.
If there is no free travel, shorten the rod (by turning
at square wrench area) until it is free of clutch fork.
4.
Hold the clutch fork rearward to move throwout
lightly against clutch release fingers, then adjust rod
length until rod just touches ,its seat in the fork.
5.
Adjust locknut to obtain approximately 3/16" clear-
ance between nut and rod sleeve end.
6. Turn the rod with wrench, until the nut just comes in
contact with rod sleeve end, then hold the rod with
wrench and tighten locknut.
7.
Check free pedal travel at pedal (1" to
1-1/2"
is
proper clearance). Readjust if necessary.
Chevy II Linkage Adjustment (Fig. 3}
L-4 & L-6 Models
1.
Loosen locknut "A" and lengthen or shorten push rod
in swivel as required by turning with wrench on ma-
chined flat "B". (Shorten push rod to increase pedal
lash).
2.
Hold push rod at flat "B" and tighten locknut "A".
3.
Recheck pedal free travel.
NOTE: A measurement of approximately 3/16"
between push rod and its seat in fork will give
required pedal free travel.
V-8 Models
The eight cylinder linkage has a two-piece clutch fork
push rod (fig. 3). Adjust clutch pedal free travel by turn-
ing the adjusting rod portion of the push rod to obtain apr
proximately 3/16" clearance between clutch fork and end
of rod, ttien tighten locknut to 8-12 lbs. ft. and check free
travel at pedal. Pedal free travel on all models should
be 1" to
1-1/2".
Corvette Linkage Adjustment
Refer to fig. 1 and the following procedure:
1.
Disconnect pedal return spring.
2.
With Nuts (A) and (B) loose on Rod (D) apply push
hard load in direction of arrow (F) to eliminate
clearance between throwout bearing and clutch
fingers.
3.
Run Nut (B) towards Swivel (C) until dimension (X)
is 3/8" to 7/16".
4.
Tighten Nut (A) to lock swivel against Nut (B).
5.
Connect pedal return spring and check pedal free
travel for
1-1/4"
minimum to 2" maximum.
6. Check every 3,000 miles.
7.
Adjust free travel to 2" to 2-1/2" for heavy duty op-
eration. The return spring may be removed for
heavy duty conditions.
Camaro Linkage Adjustment
Refer to Figure 4 and the following procedure:
Apply a 10 lb. load in direction of Arrow (E) to hold
Clutch Pedal against Clutch Pedal Bumper.
Apply a 10 lb. load to Clutch Fork in direction of Arrow
(D) to eliminate clearance between throwout bearing and
clutch fingers.
Insert a .198 Spacer (F) between clutch fork and Ad-
justing Rod (A).
Rotate Adjusting Rod against Spacer until it has a 5 in.
lb.
torque.
Hold Adjusting Rod and tighten Nut (C) against Swivel
(B) or Rod (B).
Remove Spacer. Install return spring and extension to
clutch fork.
Pedal will have approximately 1" to
1-1/8"
free travel.
A clutch that has been slipping prior to free play ad-
justment may still slip right after the new adjustment due
CHEVROLET CHASSIS SERVICE MANUAL
Page 366 of 659
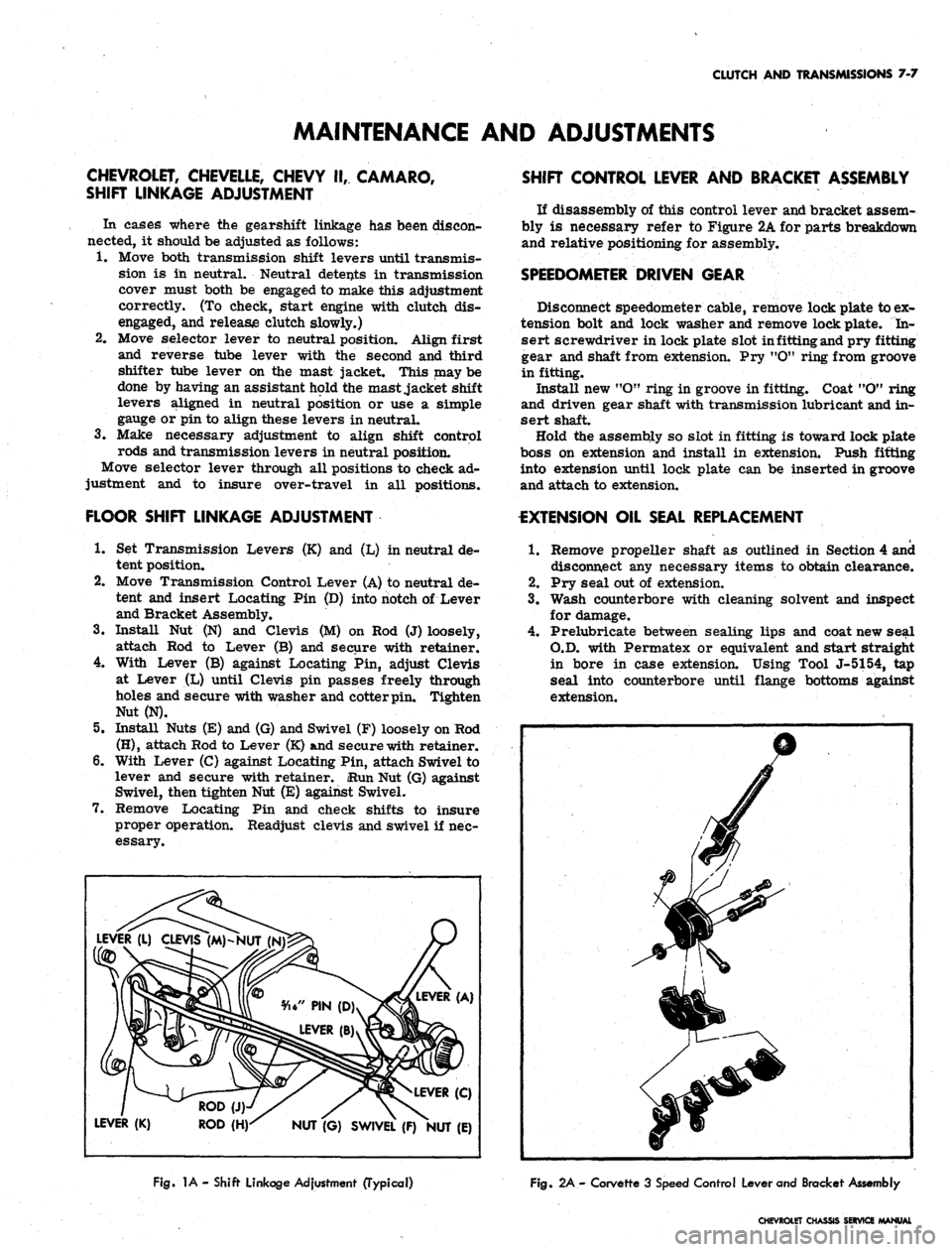
CLUTCH AND TRANSMISSIONS 7-7
MAINTENANCE AND ADJUSTMENTS
CHEVROLET, CHEVELLE, CHEVY II, CAMARO,
SHIFT LINKAGE ADJUSTMENT
In cases where the gearshift linkage has been discon-
nected, it should be adjusted as follows:
1.
Move both transmission shift levers until transmis-
sion is in neutral. Neutral detents in transmission
cover must both be engaged to make this adjustment
correctly. (To check, start engine with clutch dis-
engaged, and release clutch slowly.)
2.
Move selector lever to neutral position. Align first
and reverse tube lever with the second and third
shifter tube lever on the mast jacket. This may be
done by having an assistant hold the mast .jacket shift
levers aligned in neutral position or use a simple
gauge or pin to align these levers in neutral.
3.
Make necessary adjustment to align shift control
rods and transmission levers in neutral position.
Move selector lever through all positions to check ad-
justment and to insure over-travel in all positions.
FLOOR SHIFT LINKAGE ADJUSTMENT
1.
Set Transmission Levers (K) and (L) in neutral de-
tent position.
2.
Move Transmission Control Lever (A) to neutral de-
tent and insert Locating Pin (D) into notch of Lever
and Bracket Assembly.
3.
Install Nut (N) and Clevis (M) on Rod (J) loosely,
attach Rod to Lever (B) and secure with retainer.
4.
With Lever (B) against Locating Pin, adjust Clevis
at Lever (L) until Clevis pin passes freely through
holes and secure with washer and cotter pin. Tighten
Nut (N).
5.
Install Nuts (E) and (G) and Swivel (F) loosely on Rod
(H),
attach Rod to Lever (K) and secure with retainer.
6. With Lever (C) against Locating Pin, attach Swivel to
lever and secure with retainer. iRun Nut (G) against
Swivel, then tighten Nut (E) against Swivel.
7.
Remove Locating Pin and check shifts to insure
proper operation. Readjust clevis and swivel if nec-
essary.
LEVER (A)
LEVER (L) CLEVIS (M)-NUT (N
LEVER (C)
ROD(J).
" - -
LEVER (K) ROD (H)^ NUT '(G) SWIVEL (F) ^NUT (E)
SHIFT CONTROL LEVER AND BRACKET ASSEMBLY
If disassembly of this control lever and bracket assem-
bly is necessary refer to Figure 2A for parts breakdown
and relative positioning for assembly.
SPEEDOMETER DRIVEN GEAR
Disconnect speedometer cable, remove lock plate to ex-
tension bolt and lock washer and remove lock plate. In-
sert screwdriver in lock plate slot in fitting and pry fitting
gear and shaft from extension. Pry "O" ring from groove
in fitting.
Install new "OM ring in groove in fitting. Coat "O" ring
and driven gear shaft with transmission lubricant and in-
sert shaft.
Hold the assembly so slot in fitting is toward lock plate
boss on extension and install in extension. Push fitting
into extension until lock plate can be inserted in groove
and attach to extension.
EXTENSION OIL SEAL REPLACEMENT
.1.
Remove propeller shaft as outlined in Section 4 and
disconnect any necessary items to obtain clearance.
2.
Pry seal out of extension.
3.
Wash counterbore with cleaning solvent and inspect
for damage.
4.
Prelubricate between sealing lips and coat new seal
O.D. with Permatex or equivalent and start straight
in bore in case extension. Using Tool J-5154, tap
seal into counterbore until flange bottoms against
extension.
Fig.
1A- Shift Linkage Adjustment (Typical)
Fig.
2A - Corvette 3 Speed Control Lever and Bracket Assembly
CHEVROLET CHASSIS SERVICE MANUAL