tow CHEVROLET CAMARO 1967 1.G Chassis Repair Manual
[x] Cancel search | Manufacturer: CHEVROLET, Model Year: 1967, Model line: CAMARO, Model: CHEVROLET CAMARO 1967 1.GPages: 659, PDF Size: 114.24 MB
Page 369 of 659
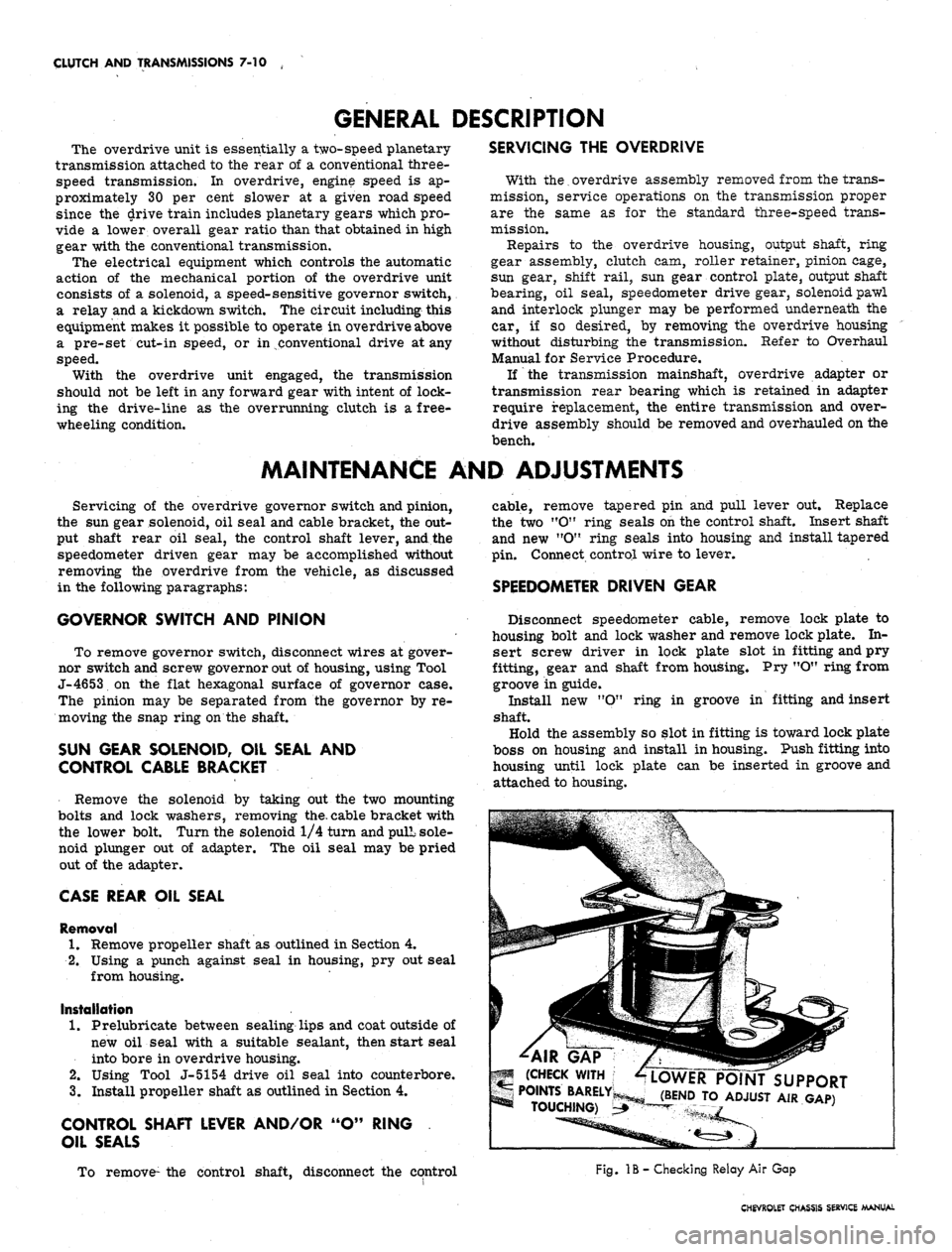
CLUTCH AND TRANSMISSIONS 7-10 ,
GENERAL DESCRIPTION
The overdrive unit is essentially a two-speed planetary-
transmission attached to the rear of a conventional three-
speed transmission. In overdrive, engine speed is ap-
proximately 30 per cent slower at a given road speed
since the drive train includes planetary gears which pro-
vide a lower overall gear ratio than that obtained in high
gear with the conventional transmission.
The electrical equipment which controls the automatic
action of the mechanical portion of the overdrive unit
consists of a solenoid, a speed-sensitive governor switch,
a relay and a kickdown switch. The circuit including this
equipment makes it possible to operate in overdrive above
a pre-set cut-in speed, or in .conventional drive at any
speed.
With the overdrive unit engaged, the transmission
should not be left in any forward gear with intent of lock-
ing the drive-line as the overrunning clutch is a free-
wheeling condition.
SERVICING THE OVERDRIVE
With the,overdrive assembly removed from the trans-
mission, service operations on the transmission proper
are the same as for the standard three-speed trans-
mission.
Repairs to the overdrive housing, output shaft, ring
gear assembly, clutch cam, roller retainer, pinion cage,
sun gear, shift rail, sun gear control plate, output shaft
bearing, oil seal, speedometer drive gear, solenoid pawl
and interlock plunger may be performed underneath the
car, if so desired, by removing the overdrive housing
without disturbing the transmission. Refer to Overhaul
Manual for Service Procedure.
If the transmission mainshaft, overdrive adapter or
transmission rear bearing which is retained in adapter
require replacement, the entire transmission and over-
drive assembly should be removed and overhauled on the
bench.
MAINTENANCE AND ADJUSTMENTS
Servicing of the overdrive governor switch and pinion,
the sun gear solenoid, oil seal and cable bracket, the out-
put shaft rear oil seal, the control shaft lever, and the
speedometer driven gear may be accomplished without
removing the overdrive from the vehicle, as discussed
in the following paragraphs:
GOVERNOR SWITCH AND PINION
To remove governor switch, disconnect wires at gover-
nor switch and screw governor
out
of housing, using Tool
J-4653 on the flat hexagonal surface of governor case.
The pinion may be separated from the governor by re-
moving the snap ring on the shaft.
SUN GEAR SOLENOID, OIL SEAL AND
CONTROL CABLE BRACKET
Remove the solenoid by taking out the two mounting
bolts and lock washers, removing
the.
cable bracket with
the lower bolt. Turn the solenoid 1/4 turn and
pull,
sole-
noid plunger out of adapter. The oil seal may be pried
out of the adapter.
CASE REAR OIL SEAL
Removal
1.
Remove propeller shaft as outlined in Section 4.
2.
Using a punch against seal in housing, pry out seal
from housing.
Installation
1.
Prelubricate between sealing lips and coat outside of
new oil seal with a suitable sealant, then start seal
into bore in overdrive housing.
2.
Using Tool J-5154 drive oil seal into counterbore.
3.
Install propeller shaft as outlined in Section 4.
CONTROL SHAFT LEVER AND/OR "O" RING
OIL SEALS
To remove- the control shaft, disconnect the cpntrol
cable, remove tapered pin and pull lever out. Replace
the two "0" ring seals on the control shaft. Insert shaft
and new "O" ring seals into housing and install tapered
pin. Connect control wire to lever.
SPEEDOMETER DRIVEN GEAR
Disconnect speedometer cable, remove lock plate to
housing bolt and lock washer and remove lock plate. In-
sert screw driver in lock plate slot in fitting and pry
fitting, gear and shaft from housing. Pry "O" ring from
groove in guide.
Install new "O" ring in groove in fitting and insert
shaft.
Hold the assembly so slot in fitting is toward lock plate
boss on housing and install in housing. Push fitting into
housing until lock plate can be inserted in groove and
attached to housing.
L
dl
ZAIR GAP
km (CHECK WITH
M*= POINTS BARELY
'A
AoWER
|^
POINT
0 ADJUST
=^ i
SUPPORT
Fig. IB - Checking Relay Air Gap
CHEVROLET CHASSIS SERVICE MANUAL
Page 374 of 659

CLUTCH AND TRANSMISSIONS 7-15
LOCATING
GAGE B
N
Fig.
1C - Warner T-16 3-Speed Lever and Linkage Adjustment (Camaro and Corvette)
Clearance should be .002 to .008. Interlock sleeves
are available in four sizes to give the proper
clearance.
6. Install outer shifter levers to shafts with lock wash-
ers and nuts. Tighten securely. v
7.
Instill shifting forks to shift levers (1st and re-
verse fork "hump" towards bottom).
Installation
1.
Install new side cover gasket to transmission case,
install cover and secure with lock washers and cap
screws.
NOTE: The two rear side cover to case at-
taching bolts have a special oil sealing spline
and must be used at these two "through" hole
locations.
2.
Connect control rod and cross shaft to control
levers.
1.
Side Cover
2.
Poppet
3. 1st and Reverse Shifter
Lever and Shaft
4.
Poppet Spring
5. 1st and Reverse Shifter
Fork
6. Interlock Pin
7. 2nd and 3rd Shifting
Fork
8. Interlock Sleeve
9. 2nd and 3rd Shifter
Lever and Shaft
10.
"O11 Ring Seal
Fig.
2C - Side Cover Assembly - Layout
CHEVROLET CHASSIS SERVICE MANUAl
Page 378 of 659
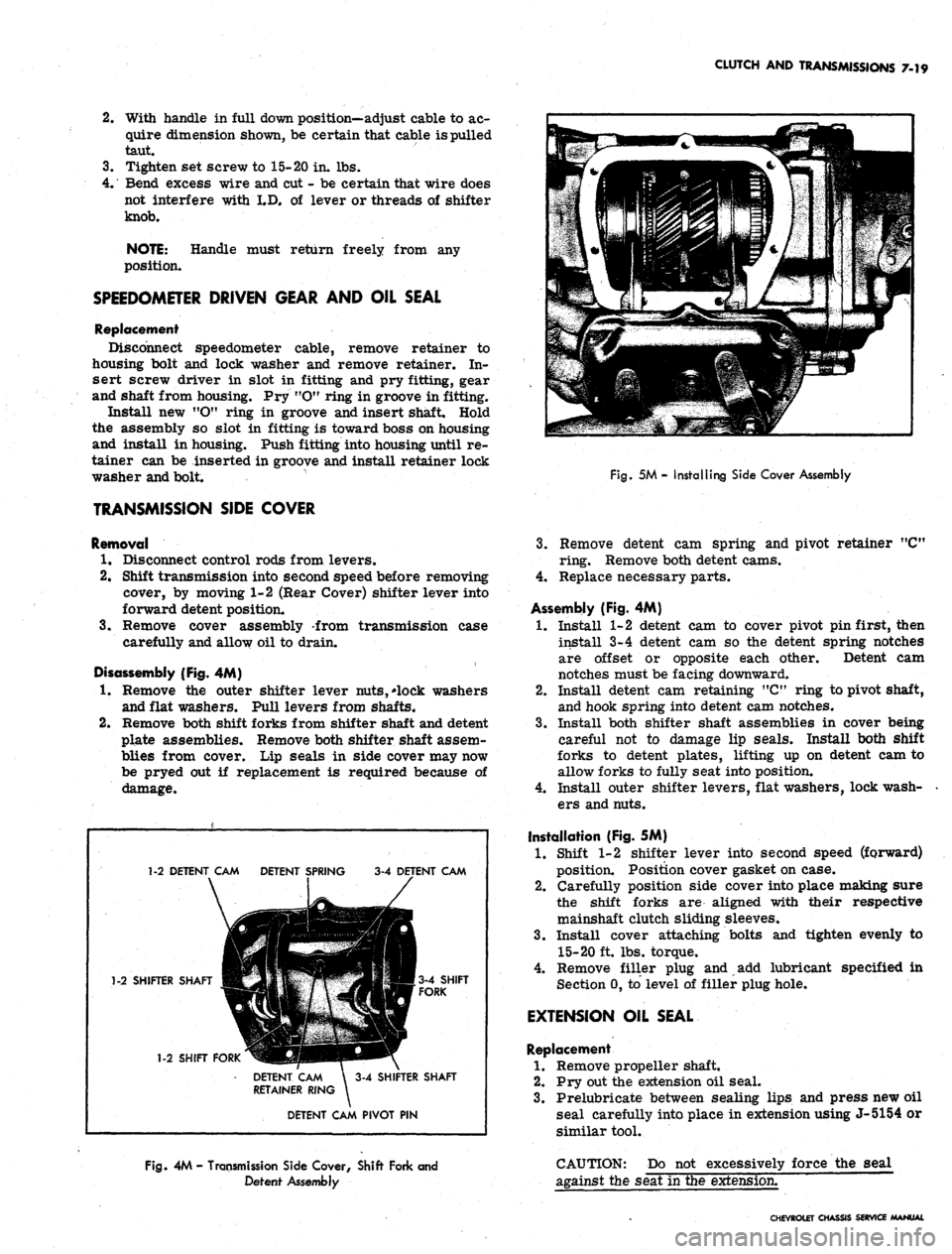
CLUTCH AND TRANSMISSIONS 7-19
2.
With handle in full down position—adjust cable to ac-
quire dimension shown, be certain that cable is pulled
taut.
3.
Tighten set screw to 15-20 in. lbs.
4.
Bend excess wire and cut - be certain that wire does
not interfere with I.D. of lever or threads of shifter
knob.
NOTE: Handle must return freely from any
position.
SPEEDOMETER DRIVEN GEAR AND OIL SEAL
Replacement
Disconnect speedometer cable, remove retainer to
housing bolt and lock washer and remove retainer. In-
sert screw driver in slot in fitting and pry fitting, gear
and shaft from housing. Pry "O" ring in groove in fitting.
Install new "O" ring in groove and insert shaft Hold
the assembly so slot in fitting is toward boss on housing
and install in housing. Push fitting into housing until re-
tainer can be inserted in groove and install retainer lock
washer and bolt.
Fig.
5M - Installing Side Cover Assembly
TRANSMISSION SIDE COVER
Removal
1.
Disconnect control rods from levers.
2.
Shift transmission into second speed before removing
cover, by moving 1-2 (Rear Cover) shifter lever into
forward detent position.
3.
Remove cover assembly -from transmission case
carefully and allow oil to drain.
Disassembly (Fig. 4M)
1.
Remove the outer shifter lever nuts,*lock washers
and flat washers. Pull levers from shafts.
2.
Remove both shift forks from shifter shaft and detent
plate assemblies. Remove both shifter shaft assem-
blies from cover. Lip seals in side cover may now
be pryed out if replacement is required because of
damage.
1-2 DETENT CAM DETENT SPRING
3-4 DETENT CAM
1-2 SHIFTER SHAFT
1-2 SHIFT FORK
3-4 SHIFT
FORK
DETENT CAM \ 3-4 SHIFTER SHAFT
RETAINER RING
DETENT CAM PIVOT PIN
3.
Remove detent cam spring and pivot retainer "C"
ring. Remove both detent cams.
4.
Replace necessary parts.
Assembly (Fig. 4M)
1.
Install 1-2 detent cam to cover pivot pin first, then
install 3-4 detent cam so the detent spring notches
are offset or opposite each other. Detent cam
notches must be facing downward.
2.
Install detent cam retaining "C" ring to pivot shaft,
and hook spring into detent cam notches.
3.
Install both shifter shaft assemblies in cover being
careful not to damage lip seals. Install both shift
forks to detent plates, lifting up on detent cam to
allow forks to fully seat into position.
4.
Install outer shifter levers, flat washers, lock wash-
ers and nuts.
Installation (Fig. 5M)
1.
Shift 1-2 shifter lever into second speed (forward)
position. Position cover gasket on case.
2.
Carefully position side cover into place making sure
the shift forks are aligned with their respective
mainshaft clutch sliding sleeves.
3.
Install cover attaching bolts and tighten evenly to
15-20 ft. lbs. torque.
4.
Remove filler plug and add lubricant specified in
Section 0, to level of filler plug hole.
EXTENSION OIL SEAL
Replacement
1.
Remove propeller shaft.
2.
Pry out the extension oil seal.
3.
Prelubricate between sealing lips and press new oil
seal carefully into place in extension using J-5154 or
similar tool.
Fig.
4M - Transmission Side Cover/ Shift Fork and
Detent Assembly
CAUTION: Do not excessively force the seal
against the seat in the extension.
CHEVROLET CHASSIS SERVICE MANUAL
Page 383 of 659
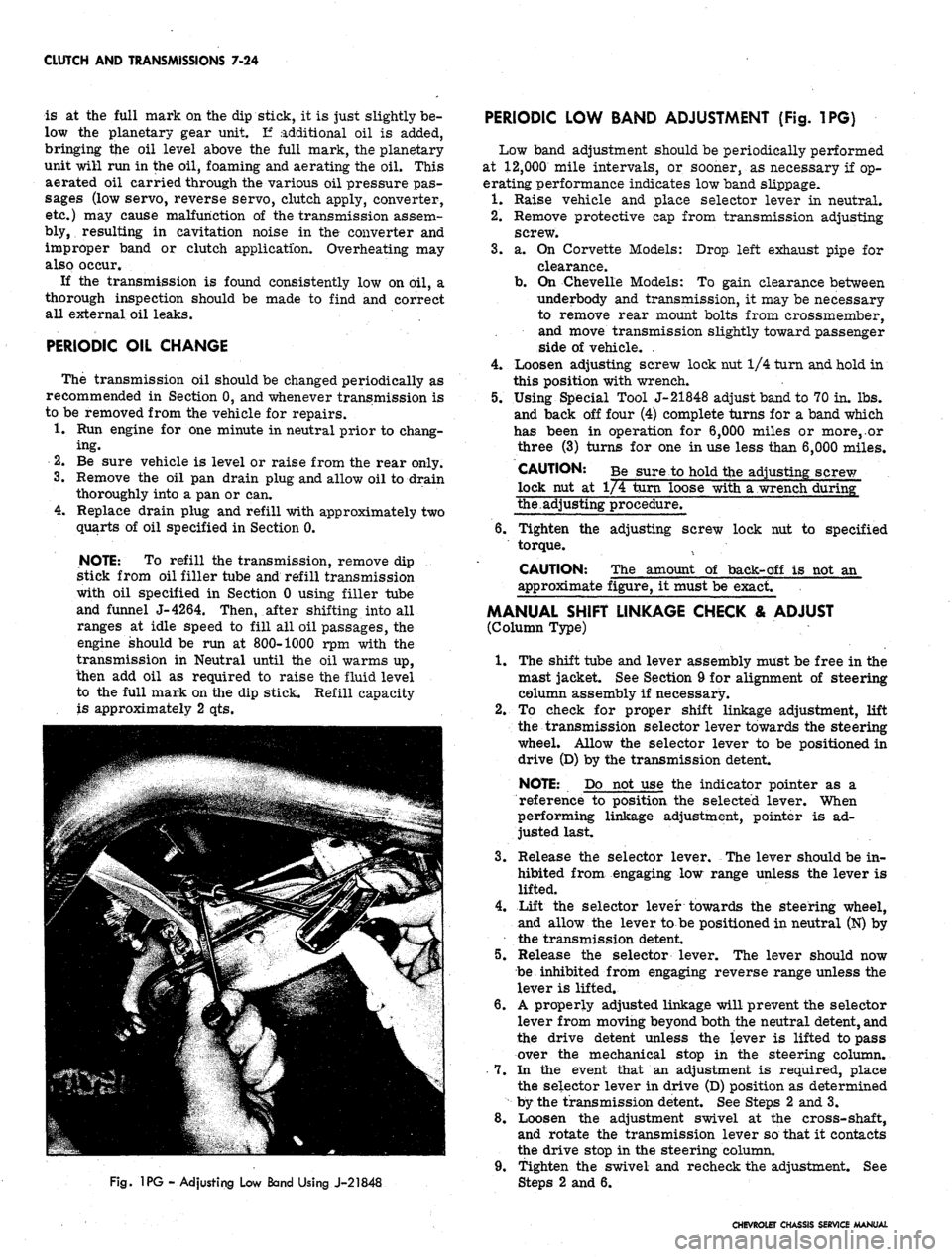
CLUTCH AND TRANSMISSIONS 7-24
is at the full mark on the dip stick, it is just slightly be-
low the planetary gear unit. If additional oil is added,
bringing the oil level above the full mark, the planetary
unit will run in the oil, foaming and aerating the oil. This
aerated oil carried through the various oil pressure pas-
sages (low servo, reverse servo, clutch apply, converter,
etc.) may cause malfunction of the transmission assem-
bly, resulting in cavitation noise in the converter and
improper band or clutch application. Overheating may
also occur.
If the transmission is found consistently low on oil, a
thorough inspection should be made to find and correct
all external oil leaks.
PERIODIC OIL CHANGE
The transmission oil should be changed periodically as
recommended in Section 0, and whenever transmission is
to be removed from the vehicle for repairs.
1.
Run engine for one minute in neutral prior to chang-
ing.
2.
Be sure vehicle is level or raise from the rear only.
3.
Remove the oil pan drain plug and allow oil to drain
thoroughly into a pan or can.
Replace drain plug and refill with approximately two
quarts of oil specified in Section 0.
NOTE: To refill the transmission, remove dip
stick from oil filler tube and refill transmission
with oil specified in Section 0 using filler tube
and funnel J-4264. Then, after shifting into all
ranges at idle speed to fill all oil passages, the
engine should be run at 800-1000 rpm with the
transmission in Neutral until the oil warms up,
then add oil as required to raise the fluid level
to the full mark on the dip stick. Refill capacity
is approximately 2 qts.
4.
Fig.
1PG - Adjusting Low Band Using J-21848
PERIODIC LOW BAND ADJUSTMENT (Fig. 1PG)
Low band adjustment should be periodically performed
at 12,000 mile intervals, or sooner, as necessary if op-
erating performance indicates low band slippage.
1.
Raise vehicle and place selector lever in neutral.
2.
Remove protective cap from transmission adjusting
screw.
3.
a. On Corvette Models: Drop left exhaust pipe for
clearance.
b.
On Chevelle Models: To gain clearance between
underbody and transmission, it may be necessary
to remove rear mount bolts from crossmember,
and move transmission slightly toward passenger
side of vehicle. .
4.
Loosen adjusting screw lock nut 1/4 turn and hold in
this position with wrench.
5.
Using Special Tool J-21848 adjust band to 70 in. lbs.
and back off four (4) complete turns for a band which
has been in operation for 6,000 miles or more,.or
three (3) turns for one in use less than 6,000 miles.
CAUTION: Be sure to hold the adjusting screw
lock nut at 1/4 turn loose with a wrench during"
the.adjusting procedure.
6. Tighten the adjusting screw lock nut to specified
torque.
CAUTION: The amount of back-off is not an
approximate figure, it must be exact.
MANUAL SHIFT LINKAGE CHECK & ADJUST
(Column Type)
1.
The shift tube and lever assembly must be free in the
mast jacket. See Section 9 for alignment of steering
column assembly if necessary.
2.
To check for proper shift linkage adjustment, lift
the transmission selector lever towards the steering
wheel. Allow the selector lever to be positioned in
drive (D) by the transmission detent.
NOTE: Do not use the indicator pointer as a
reference to position the selected lever. When
performing linkage adjustment, pointer is ad-
justed last.
3.
Release the selector lever. The lever should be in-
hibited from engaging low range unless the lever is
lifted.
4.
Lift the selector lever towards the steering wheel,
and allow the lever to be positioned in neutral (N) by
the transmission detent.
5.
Release the selector lever. The lever should now
be inhibited from engaging reverse range unless the
lever is lifted.
6. A properly adjusted linkage will prevent the selector
lever from moving beyond both the neutral detent, and
the drive detent unless the lever is lifted to pass
over the mechanical stop in the steering column.
7.
In the event that an adjustment is required, place
the selector lever in drive (D) position as determined
by the transmission detent. See Steps 2 and 3.
8. Loosen the adjustment swivel at the cross-shaft,
and rotate the transmission lever so that it contacts
the drive stop in the steering column.
9. Tighten the swivel and recheck the adjustment. See
2 and 6.
CHEVROLET CHASSIS SERVICE MANUAL
Page 392 of 659
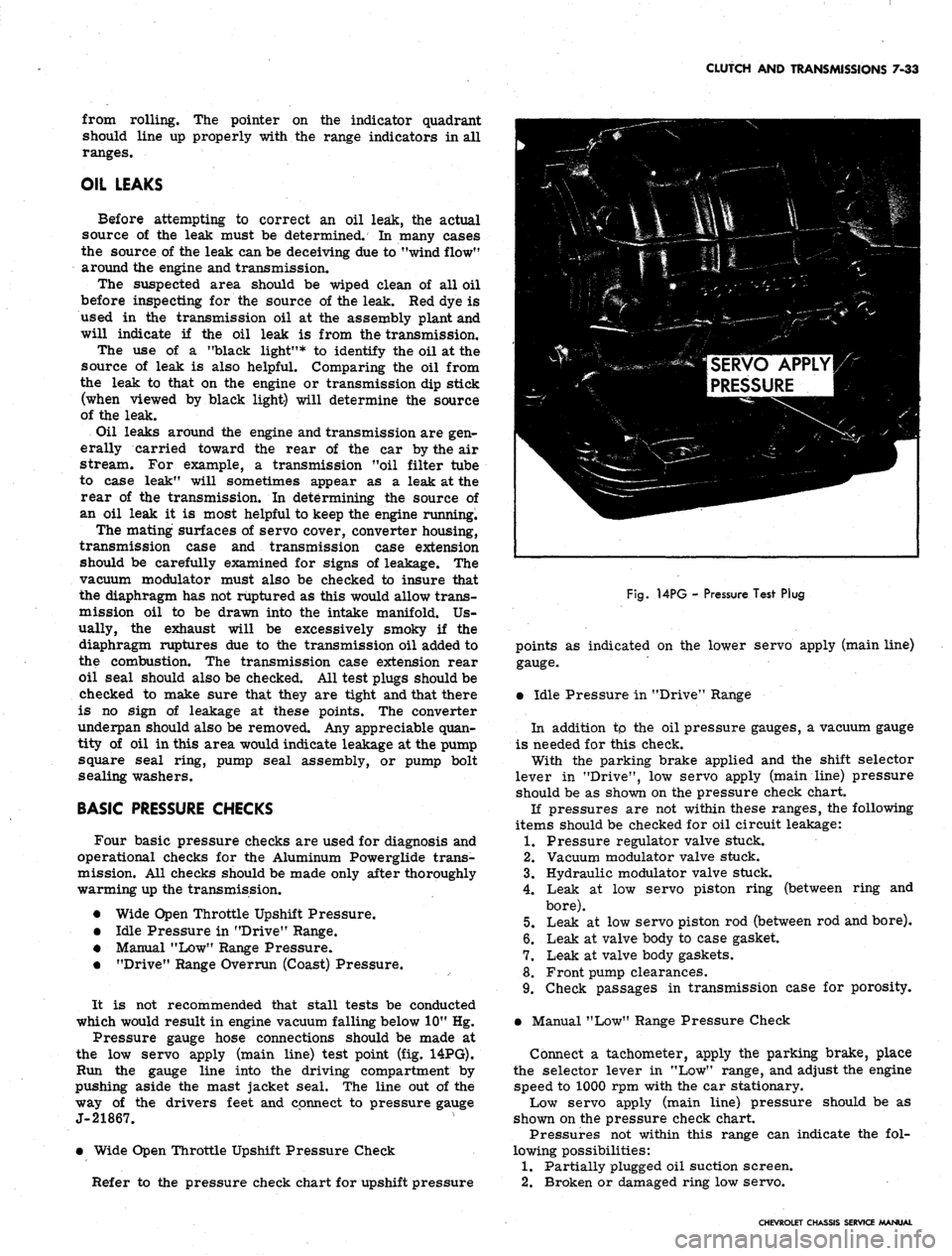
CLUTCH AND TRANSMISSIONS 7-33
from rolling. The pointer on the indicator quadrant
should line up properly with the range indicators in all
ranges.
OIL LEAKS
Before attempting to correct an oil leak, the actual
source of the leak must be determined. In many cases
the source of the leak can be deceiving due to "wind flow1 f
around the engine and transmission.
The suspected area should be wiped clean of all oil
before inspecting for the source of the leak. Red dye is
used in the transmission oil at the assembly plant and
will indicate if the oil leak is from the transmission.
The use of a "black light"* to identify the oil at the
source of leak is also helpful. Comparing the oil from
the leak to that on the engine or transmission dip stick
(when viewed by black light) will determine the source
of the leak.
Oil leaks around the engine and transmission are gen-
erally carried toward the rear of the car by the air
stream. For example, a transmission "oil filter tube
to case leak" will sometimes appear as a leak at the
rear of the transmission. In determining the source of
an oil leak it is most helpful to keep the engine running.
The mating surfaces of servo cover, converter housing,
transmission case and transmission case extension
should be carefully examined for signs of leakage. The
vacuum modulator must also be checked to insure that
the diaphragm has not ruptured as this would allow trans-
mission oil to be drawn into the intake manifold. Us-
ually, the exhaust will be excessively smoky if the
diaphragm ruptures due to the transmission oil added to
the combustion. The transmission case extension rear
oil seal should also be checked. All test plugs should be
checked to make sure that they are tight and that there
is no sign of leakage at these points. The converter
underpan should also be removed. Any appreciable quan-
tity of oil in this area would indicate leakage at the pump
square seal ring, pump seal assembly, or pump bolt
sealing washers.
BASIC PRESSURE CHECKS
Four basic pressure checks are used for diagnosis and
operational checks for the Aluminum Powerglide trans-
mission. All checks should be made only after thoroughly
warming up the transmission.
• Wide Open Throttle Upshift Pressure.
• Idle Pressure in "Drive" Range.
• Manual "Low" Range Pressure.
• "Drive" Range Overrun (Coast) Pressure.
It is not recommended that stall tests be conducted
which would result in engine vacuum falling below 10" Hg.
Pressure gauge hose connections should be made at
the low servo apply (main line) test point (fig. 14PG).
Run the gauge line into the driving compartment by
pushing aside the mast jacket seal. The line out of the
way of the drivers feet and connect to pressure gauge
J-21867.
• Wide Open Throttle Upshift Pressure Check
Refer to the pressure check chart for upshift pressure
SERVO APPLY
PRESSURE
Fig.
14PG - Pressure Test Plug
points as indicated on the lower servo apply (main line)
gauge.
• Idle Pressure in "Drive" Range
In addition tp the oil pressure gauges, a vacuum gauge
is needed for this check.
With the parking brake applied and the shift selector
lever in "Drive", low servo apply (main line) pressure
should be as shown on the pressure check chart.
If pressures are not within these ranges, the following
items should be checked for oil circuit leakage:
1.
Pressure regulator valve stuck.
2.
Vacuum modulator valve stuck.
3.
Hydraulic modulator valve stuck.
4.
Leak at low servo piston ring (between ring and
bore).
5.
Leak at low servo piston rod (between rod and bore).
6. Leak at valve body to case gasket.
7.
Leak at valve body gaskets.
8. Front pump clearances.
9. Check passages in transmission case for porosity.
• Manual "Low" Range Pressure Check
Connect a tachometer, apply the parking brake, place
the selector lever in "Low" range, and adjust the engine
speed to 1000 rpm with the car stationary.
Low servo apply (main line) pressure should be as
shown on the pressure check chart.
Pressures not within this range can indicate the fol-
lowing possibilities:
1.
Partially plugged oil suction screen.
2.
Broken or damaged ring low servo.
CHEVROLET CHASSIS SERVICE MANUAL
Page 396 of 659
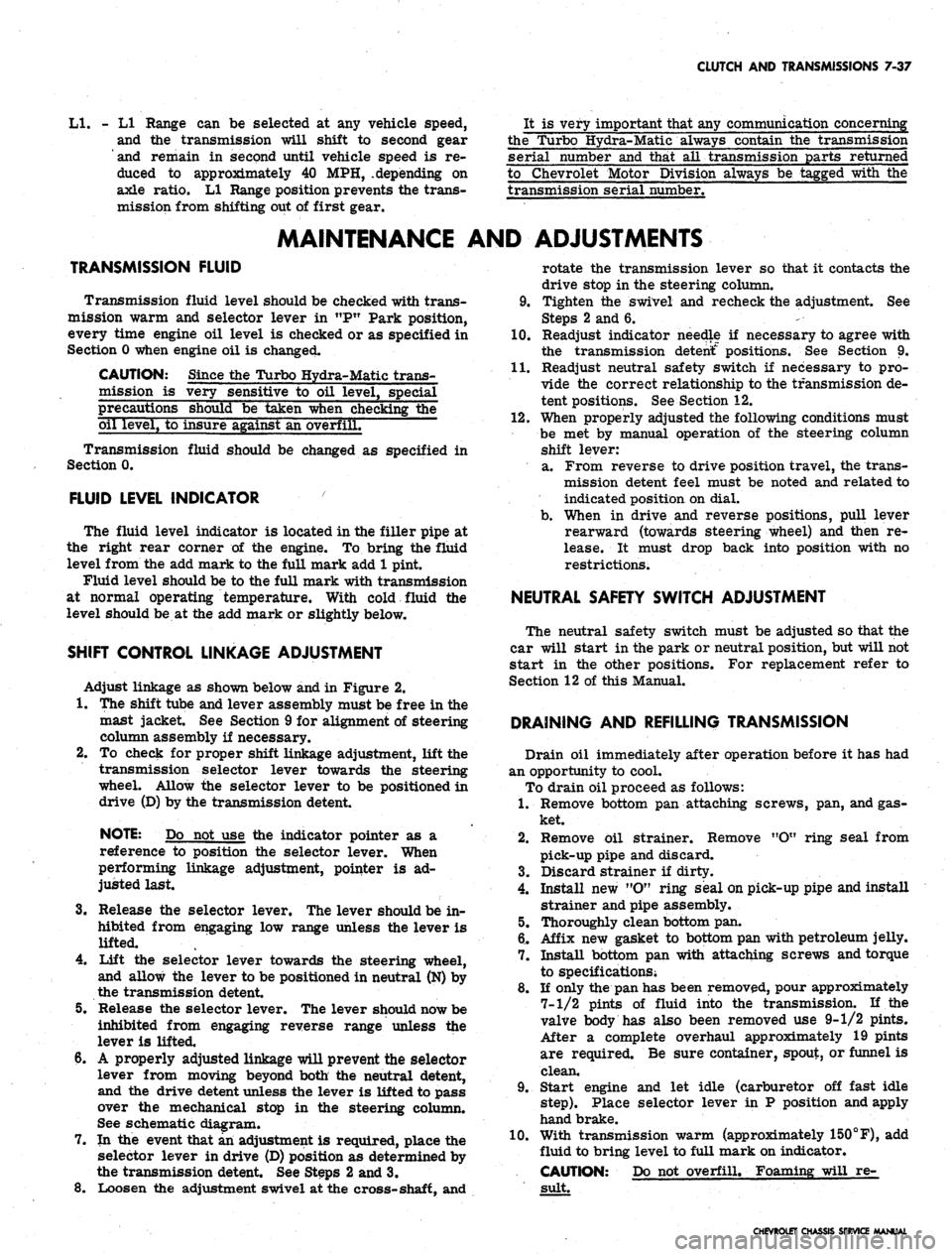
CLUTCH AND TRANSMISSIONS 7-37
LI.
- LI Range can be selected at any vehicle speed,
and the transmission will shift to second gear
and remain in second until vehicle speed is re-
duced to approximately 40 MPH, .depending on
axle ratio. LI Range position prevents the trans-
mission from shifting out of first gear.
It is very important that any communication concerning
the Turbo Hydra-Matic always contain the transmission
serial number and that all transmission parts returned
to Chevrolet Motor Division always be tagged with the
transmission serial number.
MAINTENANCE AND ADJUSTMENTS
TRANSMISSION FLUID
Transmission fluid level should be checked with trans-
mission warm and selector lever in "P" Park position,
every time engine oil level is checked or as specified in
Section 0 when engine oil is changed.
CAUTION: Since the Turbo Hydra-Matic trans-
mission is very sensitive to oil level, special
precautions should be taken when checking the
oil level, to insure against an overfifE
Transmission fluid should be changed as specified in
Section 0.
FLUID LEVEL INDICATOR
The fluid level indicator is located in the filler pipe at
the right rear corner of the engine. To bring the fluid
level from the add mark to the full mark add 1 pint.
Fluid level should be to the full mark with transmission
at normal operating temperature. With cold fluid the
level should be at the add mark or slightly below.
SHIFT CONTROL LINKAGE ADJUSTMENT
Adjust linkage as shown below and in Figure 2.
1.
The shift tube and lever assembly must be free in the
mast jacket See Section 9 for alignment of steering
column assembly if necessary.
2.
To check for proper shift linkage adjustment, lift the
transmission selector lever towards the steering
wheel. Allow the selector lever to be positioned in
drive (D) by the transmission detent.
NOTE: Do not use the indicator pointer as a
reference to position the selector lever. When
performing linkage adjustment, pointer is ad-
justed last.
3.
Release the selector lever. The lever should be in-
hibited from engaging low range unless the lever is
lifted.
4.
Lift the selector lever towards the steering wheel,
and allow the lever to be positioned in neutral (N) by
the transmission detent.
5.
Release the selector lever. The lever should now be
inhibited from engaging reverse range unless the
lever is lifted.
6. A properly adjusted linkage will prevent the selector
lever from moving beyond both the neutral detent,
and the drive detent unless the lever is lifted to pass
over the mechanical stop in the steering column.
See schematic diagram.
7.
In the event that an adjustment is required, place the
selector lever in drive (D) position as determined by
the transmission detent. See Steps 2 and 3.
8. Loosen the adjustment swivel at the cross-shaft, and
rotate the transmission lever so that it contacts the
drive stop in the steering column.
9. Tighten the swivel and recheck the adjustment. See
Steps 2 and 6. -
l(h Readjust indicator needle if necessary to agree with
the transmission detent" positions. See Section 9.
11.
Readjust neutral safety switch if necessary to pro-
vide the correct relationship to the transmission de-
tent positions. See Section 12.
12.
When properly adjusted the following conditions must
be met by manual operation of the steering column
shift lever:
a. From reverse to drive position travel, the trans-
mission detent feel must be noted and related to
indicated position on dial.
b.
When in drive and reverse positions, pull lever
rearward (towards steering wheel) and then re-
lease. It must drop back into position with no
restrictions.
NEUTRAL SAFETY SWITCH ADJUSTMENT
The neutral safety switch must be adjusted so that the
car will start in the park or neutral position, but will not
start in the other positions. For replacement refer to
Section 12 of this Manual.
DRAINING AND REFILLING TRANSMISSION
Drain oil immediately after operation before it has had
an opportunity to cool.
To drain oil proceed as follows:
1.
Remove bottom pan attaching screws, pan, and gas-
ket.
2.
Remove oil strainer. Remove "O" ring seal from
pick-up pipe and discard.
3.
Discard strainer if dirty.
4.
Install new "O" ring seal on pick-up pipe and install
strainer and pipe assembly.
5.
Thoroughly clean bottom pan.
6.. Affix new gasket to bottom pan with petroleum jelly.
7.
Install bottom pan with attaching screws and torque
to specifications;
8. If only the pan has been removed, pour approximately
7-1/2 pints of fluid into the transmission. If the
valve body has also been removed use 9-1/2 pints.
After a complete overhaul approximately 19 pints
are required. Be sure container, spout, or funnel is
clean.
9. Start engine and let idle (carburetor off fast idle
step).
Place selector lever in P position and apply
hand brake.
10.
With transmission warm (approximately 150°F), add
fluid to bring level to full mark on indicator.
CAUTION: Do not overfill. Foaming will re-
sult.
CHEVROLET CHASSIS SERVICE MANUAL
Page 400 of 659
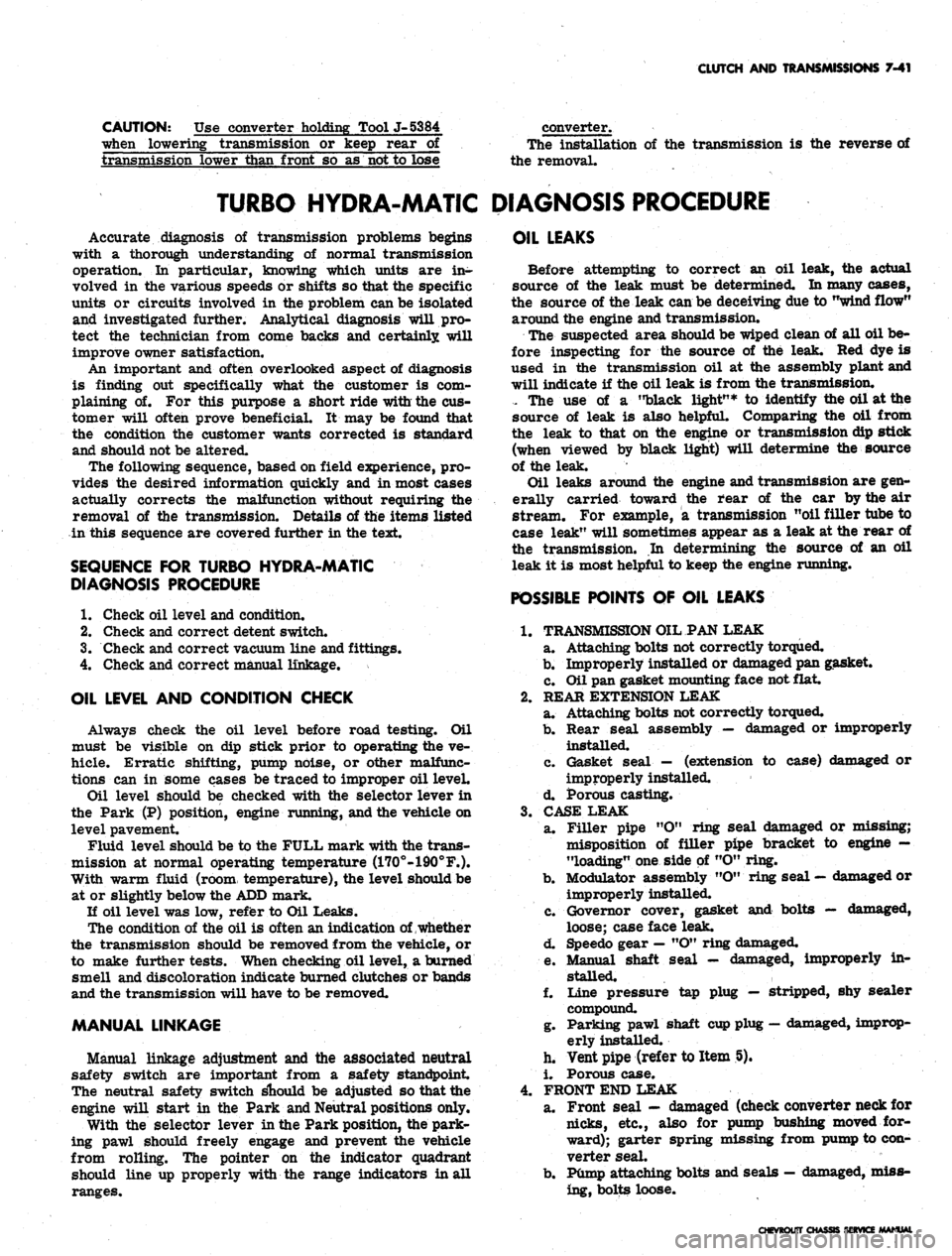
CLUTCH AND TRANSMISSIONS 7-41
CAUTION: Use converter holding ToolJ-5384
when lowering transmission or keep rear of
transmission lower than front so as not to lose
converter.
The installation of the transmission is the reverse of
the removal.
TURBO HYDRA-MATIC DIAGNOSIS PROCEDURE
Accurate diagnosis of transmission problems begins
with a thorough understanding of normal transmission
operation. In particular, knowing which units are in-
volved in the various speeds or shifts so that the specific
units or circuits involved in the problem can be isolated
and investigated further. Analytical diagnosis will pro-
tect the technician from come backs and certainly will
improve owner satisfaction.
An important and often overlooked aspect of diagnosis
is finding out specifically what the customer is com-
plaining of. For this purpose a short ride with the cus-
tomer will often prove beneficial. It may be found that
the condition the customer wants corrected is standard
and should not be altered.
The following sequence, based on field experience, pro-
vides the desired information quickly and in most cases
actually corrects the malfunction without requiring the
removal of the transmission. Details of the items listed
in this sequence are covered further in the text.
SEQUENCE FOR TURBO HYDRA-MATIC
DIAGNOSIS PROCEDURE
1.
Check oil level and condition.
2.
Check and correct detent switch.
3.
Check and correct vacuum line and fittings.
4.
Check and correct manual linkage.
OIL LEVEL AND CONDITION CHECK
Always check the oil level before road testing. Oil
must be visible on dip stick prior to operating the ve-
hicle. Erratic shifting, pump noise, or other malfunc-
tions can in some cases be traced to improper oil level.
Oil level should be checked with the selector lever in
the Park (P) position, engine running, and the vehicle on
level pavement.
Fluid level should be to the FULL mark with the trans-
mission at normal operating temperature (170°-190°
F.).
With warm fluid (room temperature), the level should be
at or slightly below the ADD mark.
If oil level was low, refer to Oil Leaks.
The condition of the oil is often an indication of whether
the transmission should be removed from the vehicle, or
to make further tests. When checking oil level, a burned
smell and discoloration indicate burned clutches or bands
and the transmission will have to be removed.
MANUAL LINKAGE
Manual linkage adjustment and the associated neutral
safety switch are important from a safety standpoint
The neutral safety switch should be adjusted so that the
engine will start in the Park and Neutral positions only.
With the selector lever in the Park position, the park-
ing pawl should freely engage and prevent the vehicle
from rolling. The pointer on the indicator quadrant
should line up properly with the range indicators in all
ranges.
OIL LEAKS
Before attempting to correct an oil leak, the actual
source of the leak must be determined. In many cases,
the source of the leak can be deceiving due to "wind flow"
around the engine and transmission.
The suspected area should be wiped clean of all oil be-
fore inspecting for the source of the leak. Red dye is
used in the transmission oil at the assembly plant and
will indicate if the oil leak is from the transmission.
. The use of a "black light"* to identify the oil at the
source of leak is also helpful. Comparing the oil from
the leak to that on the engine or transmission dip stick
(when viewed by black light) will determine the source
of the leak.
Oil leaks around the engine and transmission are gen-
erally carried toward the rear of the car by the air
stream. For example, a transmission "oil filler tube to
case leak" will sometimes appear as a leak at the rear of
the transmission. In determining the source of an oil
leak it is most helpful to keep the engine running.
POSSIBLE POINTS OF OIL LEAKS
• 1. TRANSMISSION OIL PAN LEAK
a. Attaching bolts not correctly torqued.
b.
Improperly installed or damaged pan gasket.
c. Oil pan gasket mounting face not flat.
2.
REAR EXTENSION LEAK
a. Attaching bolts not correctly torqued.
b.
Rear seal assembly — damaged or improperly
installed.
c. Gasket seal — (extension to case) damaged or
improperly installed.
d. Porous casting.
3.
CASE LEAK
a. Filler pipe "O" ring seal damaged or missing;
misposition of filler pipe bracket to engine —
"loading" one side of
"O"
ring.
b.
Modulator assembly "O" ring seal
—
damaged or
improperly installed.
c. Governor cover, gasket and bolts — damaged,
loose; case face leak.
d. Speedo gear
—
"O" ring damaged.
e. Manual shaft seal — damaged, improperly in-
stalled.
f. line pressure tap plug — stripped, shy sealer
compound.
g. Parking pawl shaft cup plug
—
damaged, improp-
erly installed.
h. Vent pipe (refer to Item 5).
i. Porous case.
4.
FRONT END LEAK
a. Front seal - damaged (check converter neck for
nicks,
etc., also for pump bushing moved for-
ward);
garter spring missing from pump to con-
verter seaL
b.
Pump attaching bolts and seals
—
damaged, miss-
ing, bolts loose.
CHEVROLET a
SERVICE
Page 408 of 659
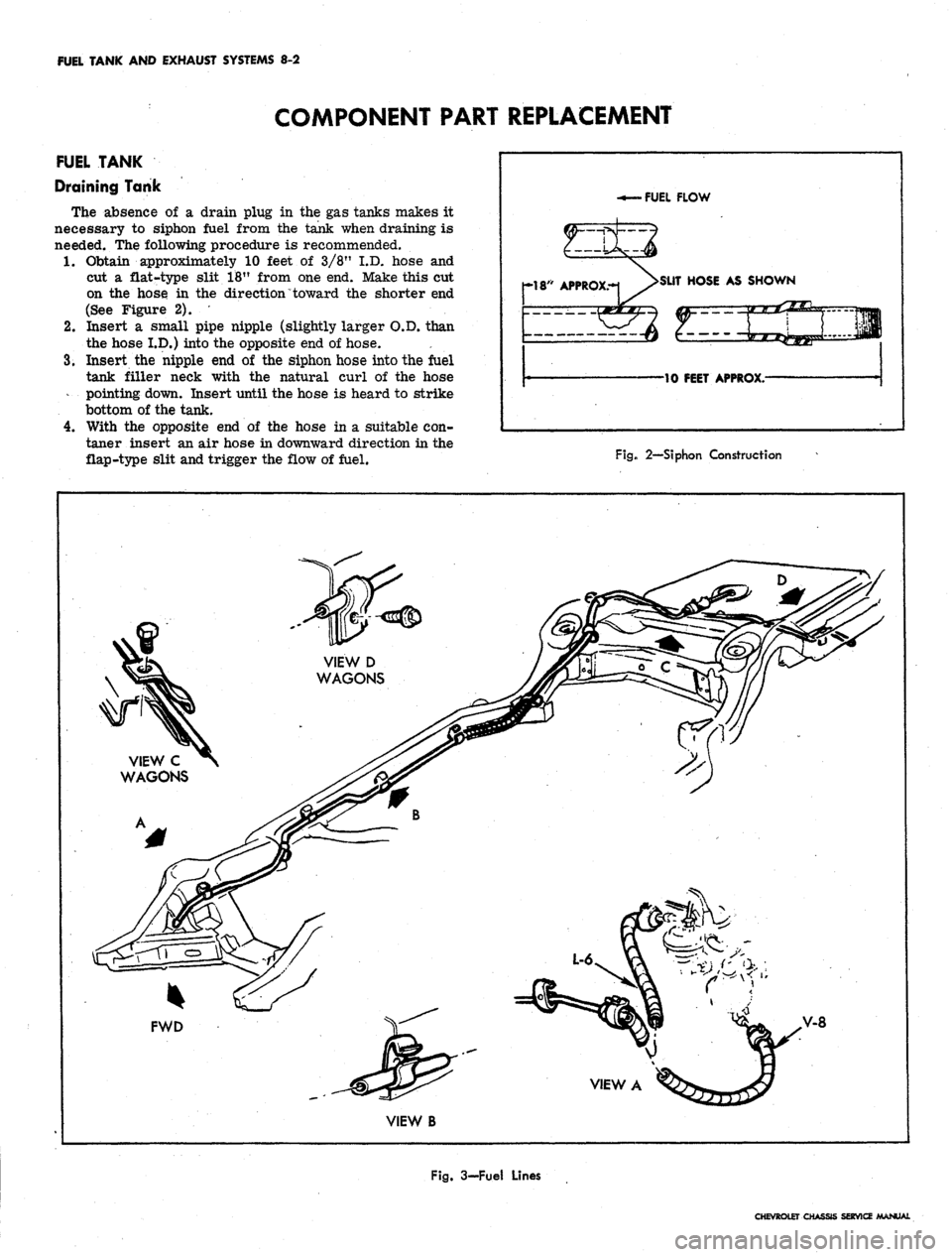
FUEL TANK AND EXHAUST SYSTEMS 8-2
COMPONENT PART REPLACEMENT
FUEL TANK
Draining Tank
The absence of a drain plug in the gas tanks makes it
necessary to siphon fuel from the tank when draining is
needed. The following procedure is recommended.
1.
Obtain approximately 10 feet of 3/8" I.D. hose and
cut a flat-type slit 18" from one end. Make this cut
on the hose in the direction "toward the shorter end
(See Figure 2).
2.
Insert a small pipe nipple (slightly larger O.D. than
the hose I.D.) into the opposite end of hose.
3.
Insert the nipple end of the siphon hose into the fuel
tank filler neck with the natural curl of the hose
pointing down. Insert until the hose is heard to strike
bottom of the tank.
4.
With the opposite end of the hose in a suitable con-
taner insert an air hose in downward direction in the
flap-type slit and trigger the flow of fuel.
FUEL FLOW
-If*
APPROX.-1 >SUT «<>«
AS SHOWN
10 FEET APPROX.-
Fig. 2—Siphon Construction
FWD
V-8
VIEW B
Fig. 3-Fuel Lines
CHEVROLET CHASSIS SERVICE MANUAL
Page 425 of 659
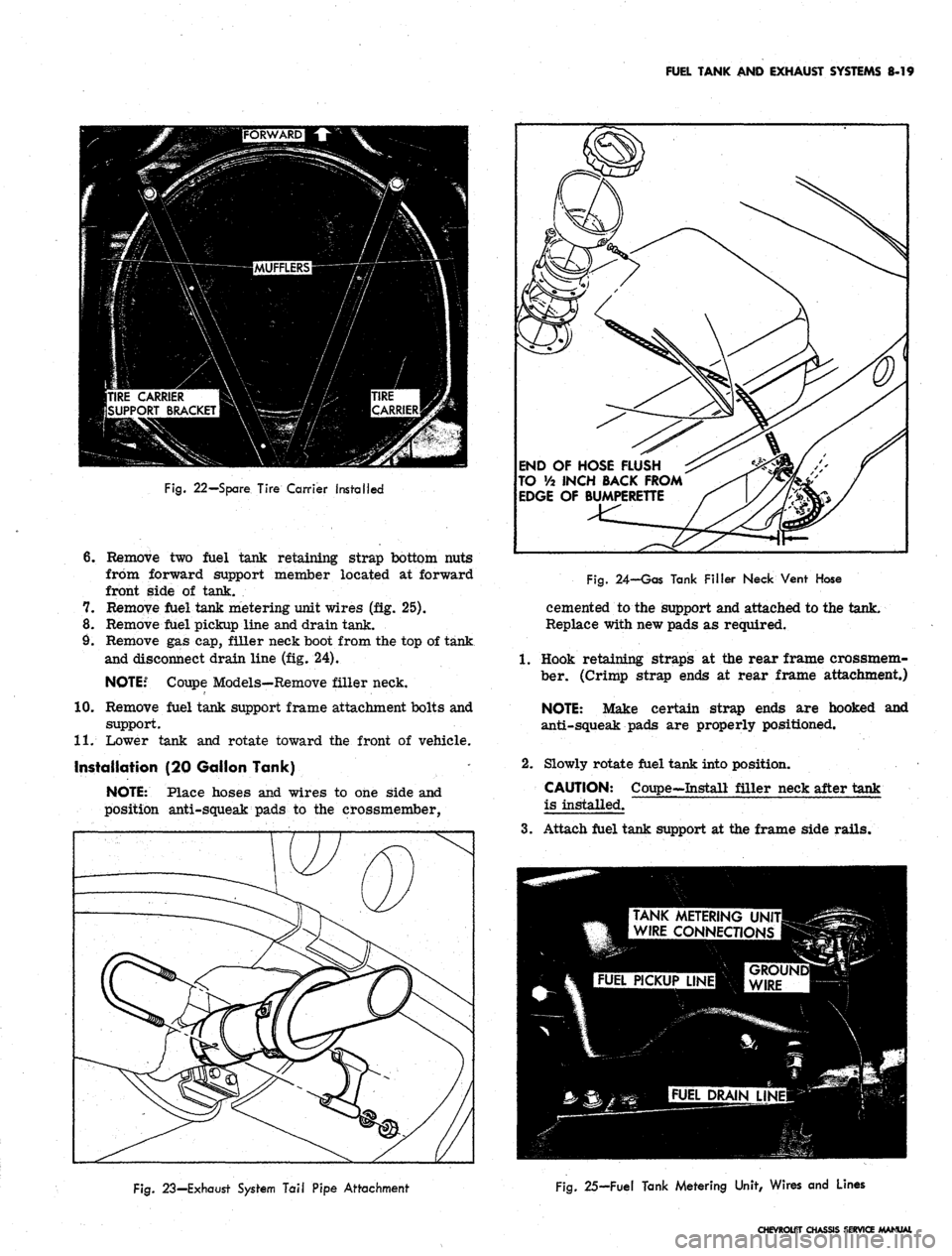
FUEL TANK AND EXHAUST SYSTEMS 8-19
Fig.
22—Spare Tire Carrier Installed
6. Remove two fuel tank retaining strap bottom nuts
from forward support member located at forward
front side of tank.
7. Remove fuel tank metering unit wires (fig. 25).
8. Remove fuel pickup line and drain tank.
9. Remove gas cap, filler neck boot from the top of tank
and disconnect drain line (fig. 24).
NOTE:6
Coupe Models—Remove filler neck.
10.
Remove fuel tank support frame attachment bolts and
support.
11.
Lower tank and rotate toward the front of vehicle.
Installation (20 Gallon Tank)
NOTE:
Place hoses and wires to one side and
position anti-squeak pads to the crossmember,
END OF HOSE FLUSH
TO Va INCH BACK FROM
EDGE OF BUMPERETTE
Fig.
24-Gas Tank Filler Neck Vent Hose
cemented to the support and attached to the tank.
Replace with new pads as required.
1.
Hook retaining straps at the rear frame crossmem-
ber. (Crimp strap ends at rear frame attachment.)
NOTE:
Make certain strap ends are hooked and
anti-squeak pads are properly positioned.
2.
Slowly rotate fuel tank into position.
CAUTION: Coupe-Install filler neck after tank
is installed.
3.
Attach fuel tank support at the frame side rails.
TANK METERING UNI
WIRE CONNECTIONS
Fig.
23—Exhaust System Tail Pipe Attachment
Fig.
25—Fuel Tank Metering Unit, Wires and Lines
CHEVROLET CHASSIS SERVICE MANUAL
Page 431 of 659
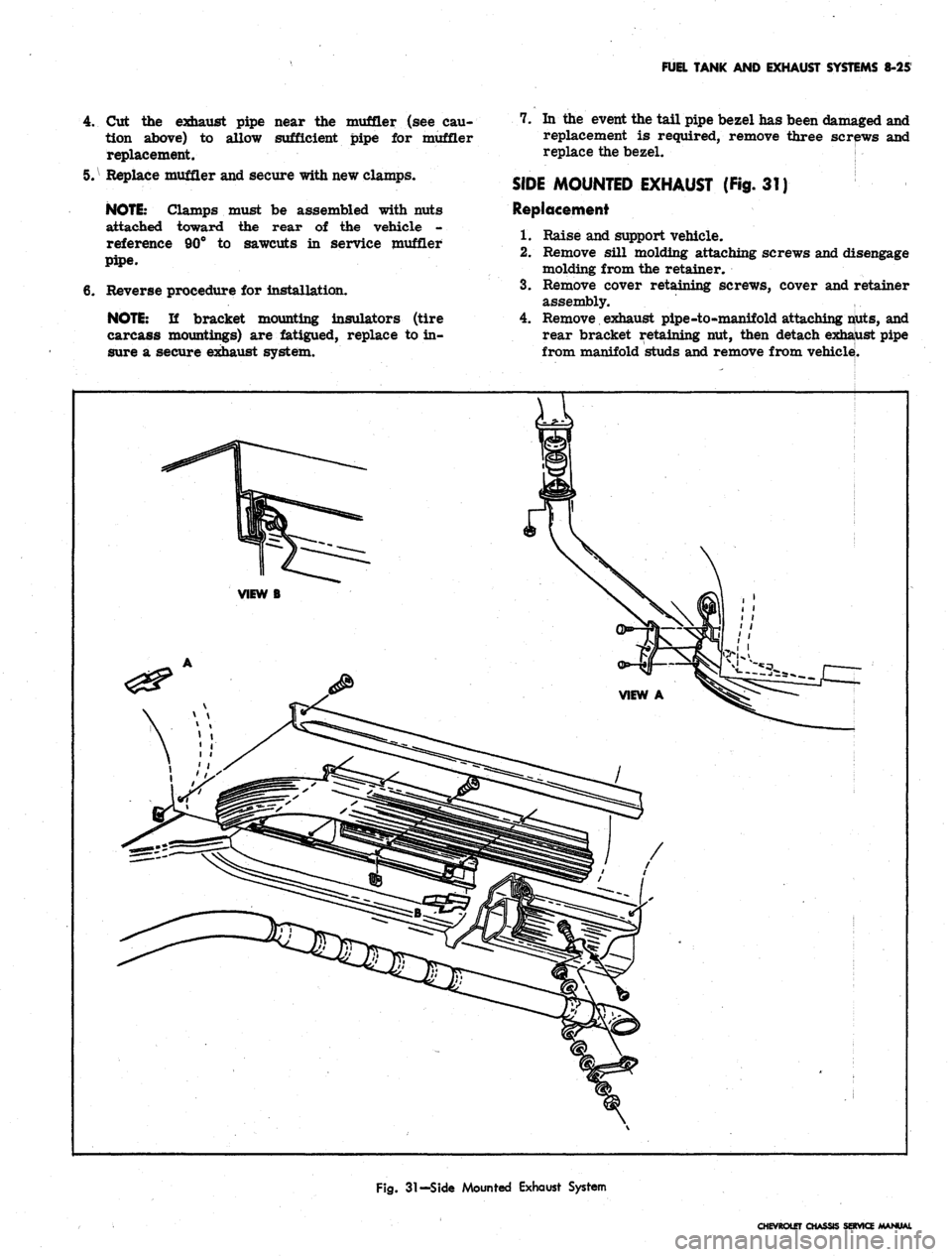
FUEL TANK AND EXHAUST SYSTEMS 8-25
4.
Cut the exhaust pipe near the muffler (see cau-
tion above) to allow sufficient pipe for muffler
replacement.
5.
^
Replace muffler and secure with new clamps.
NOTE:
Clamps must be assembled with nuts
attached toward the rear of the vehicle -
reference 90° to sawcuts in service muffler
pipe.
6. Reverse procedure for installation.
NOTE:
If bracket mounting insulators (tire
carcass mountings) are fatigued, replace to in-
sure a secure exhaust system.
7. In the event the tail pipe bezel has been damaged and
replacement is required, remove three screws and
replace the bezel. i
SIDE MOUNTED EXHAUST (Fig. 31)
Replacement
1.
Raise and support vehicle.
2.
Remove sill molding attaching screws and disengage
molding from the retainer.
3.
Remove cover retaining screws, cover and retainer
assembly.
4.
Remove exhaust pipe-to-manifold attaching nuts, and
rear bracket retaining nut, then detach exhaust pipe
from manifold studs and remove from vehicle.
Fig.
31—Side Mounted Exhaust System
CHEVROLET
CHASSIS SEKVK