tow CHEVROLET CAMARO 1967 1.G Chassis Service Manual
[x] Cancel search | Manufacturer: CHEVROLET, Model Year: 1967, Model line: CAMARO, Model: CHEVROLET CAMARO 1967 1.GPages: 659, PDF Size: 114.24 MB
Page 253 of 659
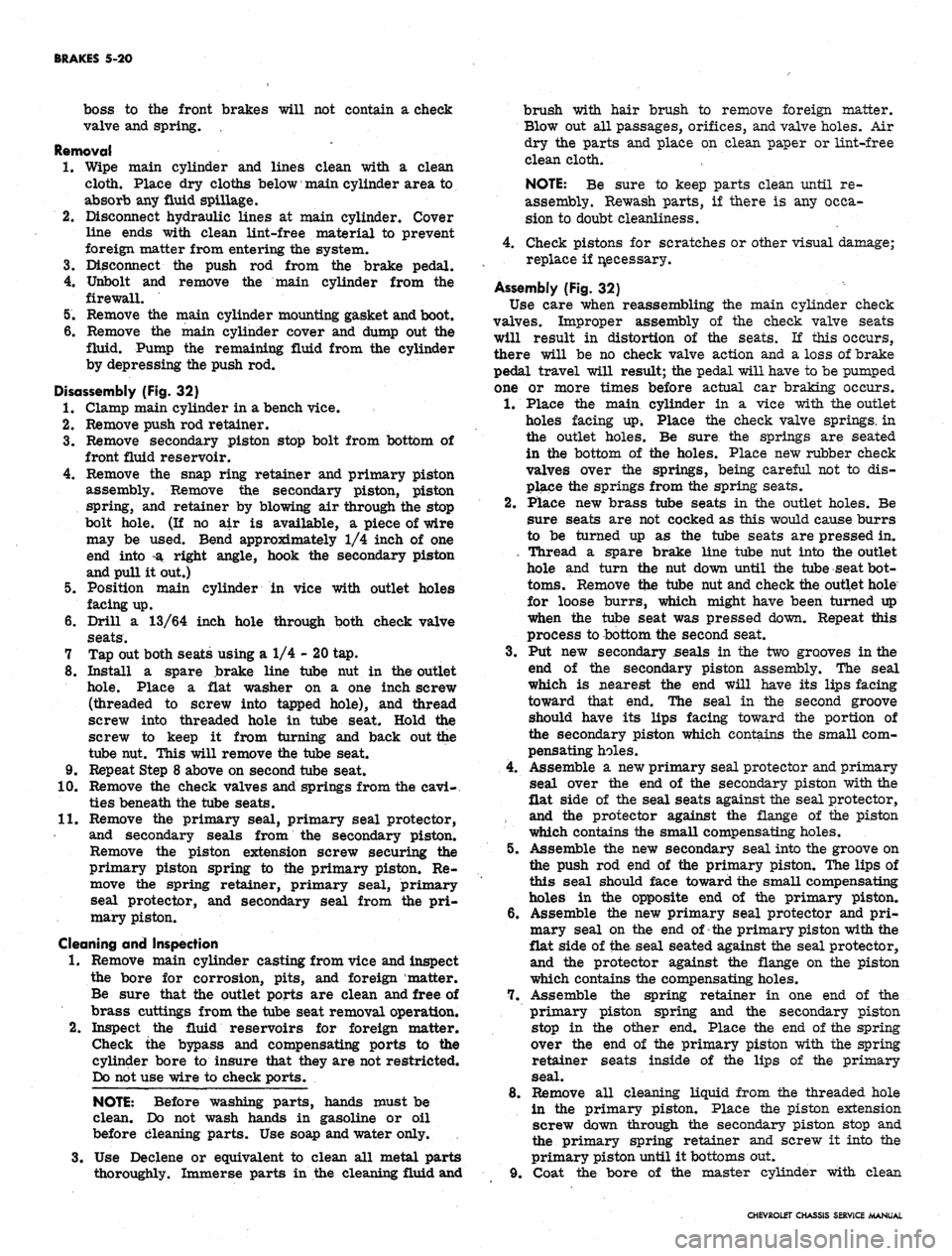
BRAKES 5-20
boss to the front brakes will not contain a check
valve and spring. .
Removal
1.
Wipe main cylinder and lines clean with a clean
cloth. Place dry cloths below main cylinder area to
absorb any fluid spillage.
2.
Disconnect hydraulic lines at main cylinder. Cover
line ends with clean lint-free material to prevent
foreign matter from entering the system.
3.
Disconnect the push rod from the brake pedal.
4.
Unbolt and remove the main cylinder from the
firewall.
5.
Remove the main cylinder mounting gasket and boot.
6. Remove the main cylinder cover and dump out the
fluid. Pump the remaining fluid from the cylinder
by depressing the push rod.
Disassembly (Fig. 32)
1.
Clamp main cylinder in a bench vice.
2.
Remove push rod retainer.
3.
Remove secondary piston stop bolt from bottom of
front fluid reservoir.
4.
Remove the snap ring retainer and primary piston
assembly. Remove the secondary piston, piston
spring, and retainer by blowing air through the stop
bolt hole. (If no air is available, a piece of wire
may be used. Bend approximately 1/4 inch of one
end into -a right angle, hook the secondary piston
and pull it out.)
5.
Position main cylinder in vice with outlet holes
facing up.
6. Drill a 13/64 inch hole through both check valve
seats.
7 Tap out both seats using a 1/4 - 20 tap.
8. Install a spare brake line tube nut in the outlet
hole.
Place a flat washer on a one inch screw
(threaded to screw into tapped hole), and thread
screw into threaded hole in tube seat. Hold the
screw to keep it from turning and back out the
tube nut. This will remove the tube seat.
9. Repeat Step 8 above on second tube seat.
10.
Remove the check valves and springs from the cavi-
ties beneath the tube seats.
11.
Remove the primary seal, primary seal protector,
and secondary seals from the secondary piston.
Remove the piston extension screw securing the
primary piston spring to the primary piston. Re-
move the spring retainer, primary seal, primary
seal protector, and secondary seal from the pri-
mary piston.
Cleaning and Inspection
1.
Remove main cylinder casting from vice and inspect
the bore for corrosion, pits, and foreign matter.
Be sure that the outlet ports are clean and free of
brass cuttings from the tube seat removal operation.
2.
Inspect the fluid reservoirs for foreign matter.
Check the bypass and compensating ports to the
cylinder bore to insure that they are not restricted.
Do not use wire to check ports.
NOTE: Before washing parts, hands must be
clean. Do not wash hands in gasoline or oil
before cleaning parts. Use soap and water only.
3.
Use Declene or equivalent to clean all metal parts
thoroughly. Immerse parts in the cleaning fluid and
brush with hair brush to remove foreign matter.
Blow out all passages, orifices, and valve holes. Air
dry the parts and place on clean paper or lint-free
clean cloth.
NOTE: Be sure to keep parts clean until re-
assembly. Rewash parts, if there is any occa-
sion to doubt cleanliness.
4.
Check pistons for scratches or other visual damage;
replace if necessary.
Assembly (Fig. 32)
Use care when reassembling the main cylinder check
valves. Improper assembly of the check valve seats
will result in distortion of the seats. If this occurs,
there will be no check valve action and a loss of brake
pedal travel will result; the pedal will have to be pumped
one or more times before actual car braking occurs.
1.
Place the main cylinder in a vice with the outlet
holes facing up. Place the check valve springs, in
the outlet holes. Be sure the springs are seated
in the bottom of the holes. Place new rubber check
valves over the springs, being careful not to dis-
place the springs from the spring seats.
2.
Place new brass tube seats in the outlet holes. Be
sure seats are not cocked as this would cause burrs
to be turned up as the tube seats are pressed in.
. Thread a spare brake line tube nut into the outlet
hole and turn the nut down until the tube seat bot-
toms.
Remove the tube nut and check the outlet hole
for loose burrs, which might have been turned up
when the tube seat was pressed down. Repeat this
process to bottom the second seat.
3.
Put new secondary seals in the two grooves in the
end of the secondary piston assembly. The seal
which is nearest the end will have its lips facing
toward that end. The seal in the second groove
should have its lips facing toward the portion of
the secondary piston which contains the small com-
pensating holes.
4.
Assemble a new primary seal protector and primary
seal over the end of the secondary piston with the
flat side of the seal seats against the seal protector,
and the protector against the flange of the piston
which contains the small compensating holes.
5.
Assemble the new secondary seal into the groove on
the push rod end of the primary piston. The lips of
this seal should face toward the small compensating
holes in the opposite end of the primary piston.
6. Assemble the new primary seal protector and pri-
mary seal on the end of-the primary piston with the
flat side of the. seal seated against the seal protector,
and the protector against the flange on the piston
which contains the compensating holes.
7.
Assemble the spring retainer in one end of the
primary piston spring and the secondary piston
stop in the other end. Place the end of the spring
over the end of the primary piston with the spring
retainer seats inside of the lips of the primary
seal.
8. Remove all cleaning liquid from the threaded hole
in the primary piston. Place the piston extension
screw down through the secondary piston stop and
the primary spring retainer and screw it into the
primary piston until it bottoms out.
9. Coat the bore of the master cylinder with clean
CHEVROLET CHASSIS SERVICE MANUAL
Page 254 of 659
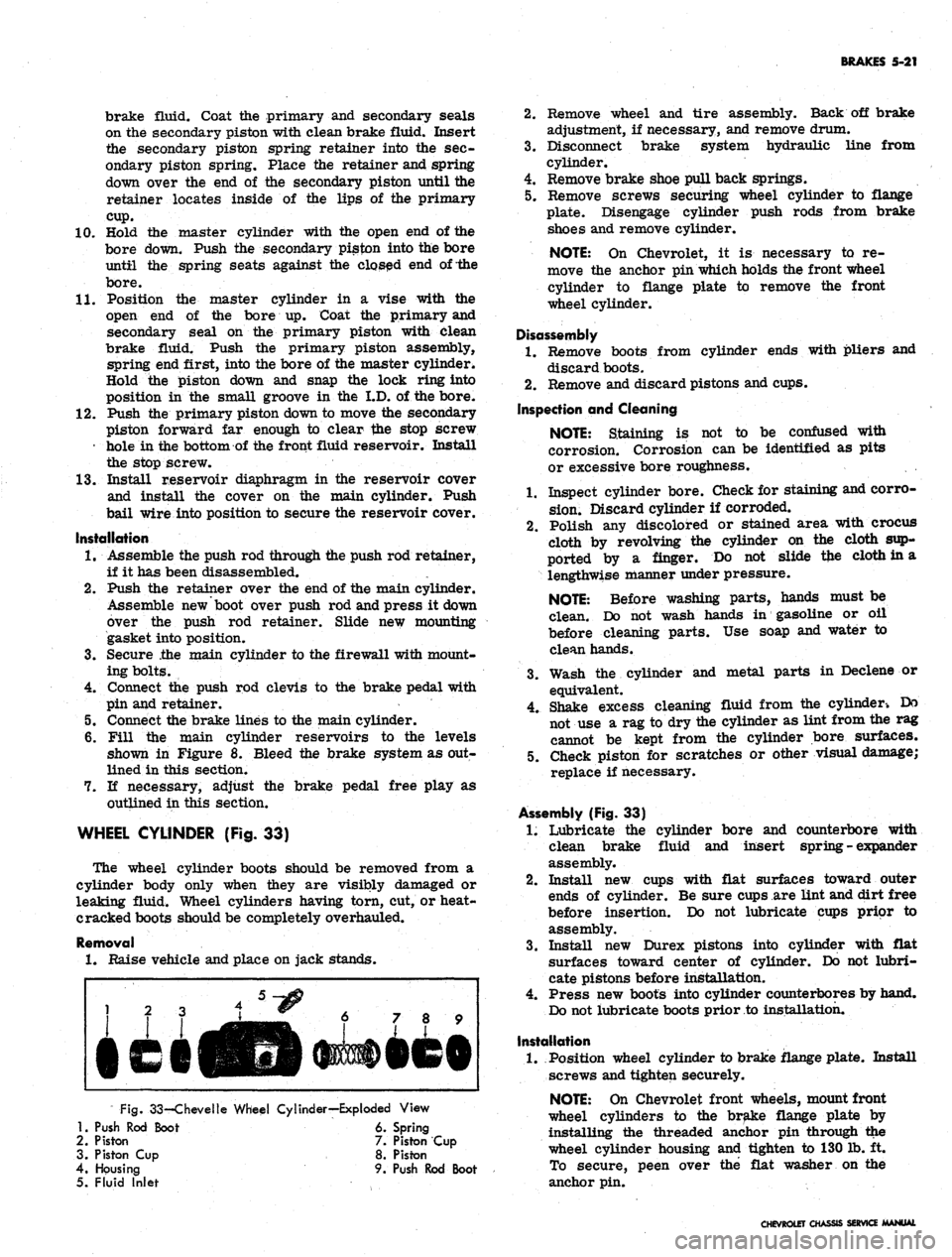
BRAKES 5-21
brake fluid. Coat the primary and secondary seals
on the secondary piston with clean brake fluid. Insert
the secondary piston spring retainer into the sec-
ondary piston spring. Place the retainer and spring
down over the end of the secondary piston until the
retainer locates inside of the lips of the primary
cup.
10.
Hold the master cylinder with the open end of the
bore down. Push the secondary piston into the bore
until the spring seats against the closed end of the
bore.
11.
Position the master cylinder in a vise with the
open end of the bore up. Coat the primary and
secondary seal on the primary piston with clean
brake fluid. Push the primary piston assembly,
spring end first, into the bore of the master cylinder*
Hold the piston down and snap the lock ring into
position in the small groove in the I.D. of the bore.
12.
Push the primary piston down to move the secondary
piston forward far enough to clear the stop screw
hole in the bottom of the front fluid reservoir. Install
the stop screw.
13.
Install reservoir diaphragm in the reservoir cover
and install the cover on the main cylinder. Push
bail wire into position to secure the reservoir cover.
Installation
1.
Assemble the push rod through the push rod retainer,
if it has been disassembled.
2.
Push the retainer over the end of the main cylinder.
Assemble new boot over push rod and press it down
over the push rod retainer. Slide new mounting
gasket into position.
3.
Secure .the main cylinder to the firewall with mount-
ing bolts.
4.
Connect the push rod clevis to the brake pedal with
pin and retainer.
5. Connect the brake lines to the main cylinder.
6. Fill the main cylinder reservoirs to the levels
shown in Figure 8. Bleed the brake system as out-
lined in this section.
7. K necessary, adjust the brake pedal free play as
outlined in this section.
WHEEL CYLINDER (Fig. 33)
The wheel cylinder boots should be removed from a
cylinder body only when they are visibly damaged or
leaking fluid. Wheel cylinders having torn, cut, or heat-
cracked boots should be completely overhauled.
Removal
1.
Raise vehicle and place on jack stands.
Fig.
33-Chevelle Wheel Cylinder—Exploded View
1.
Push Rod Boot 6. Spring
2.
Piston 7. Piston Cup
3. Piston Cup 8. Piston
4.
Housing 9. Push Rod Boot
5. Fluid Inlet
2.
Remove wheel and tire assembly. Back off brake
adjustment, if necessary, and remove drum.
3.
Disconnect brake system hydraulic line from
cylinder.
4.
Remove brake shoe pull back springs.
5. Remove screws securing wheel cylinder to flange
plate. Disengage cylinder push rods from brake
shoes and remove cylinder.
NOTE:
On Chevrolet, it is necessary to re-
move the anchor pin which holds the front wheel
cylinder to flange plate to remove the front
wheel cylinder.
Disassembly
1.
Remove boots from cylinder ends with pliers and
discard boots.
2.
Remove and discard pistons and cups.
Inspection and Cleaning
NOTE:
Staining is not to be confused with
corrosion. Corrosion can be identified as pits
or excessive bore roughness.
1.
Inspect cylinder bore. Check for staining and corro-
sion.
Discard cylinder if corroded.
2.
Polish any discolored or stained area with crocus
cloth by revolving the cylinder on the cloth sup-
ported by a finger. Do not slide tfce cloth in a
lengthwise manner under pressure.
NOTE:
Before washing parts, hands must be
clean. Do not wash hands in gasoline or oil
before cleaning parts. Use soap and water to
clean hands.
3.
Wash the cylinder and metal parts in Declene or
equivalent.
4.
Shake excess cleaning fluid from the cylinder-. Do
not use a rag to dry the cylinder as lint from the rag
cannot be kept from the cylinder bore surfaces.
5. Check piston for scratches or other visual damage;
replace if necessary.
Assembly (Fig. 33)
1.
Lubricate the cylinder bore and counterbore with
clean brake fluid and insert spring - expander
assembly.
2.
Install new cups with flat surfaces toward outer
ends of cylinder. Be sure cups are lint and dirt free
before insertion. Do not lubricate cups prior to
assembly.
3.
Install new Durex pistons into cylinder with flat
surfaces toward center of cylinder. Do not lubri-
cate pistons before installation.
4.
Press new boots into cylinder counterbores by hand.
Do not lubricate boots prior to installation.
Installation
1.
Position wheel cylinder to brake flange plate. Install
screws and tighten securely.
NOTE:
On Chevrolet front wheels, mount front
wheel cylinders to the brake flange plate by
installing the threaded anchor pin through the
wheel cylinder housing and tighten to 130 lb. ft.
To secure, peen over the flat washer on the
anchor pin.
CHEVROLET CHASSIS SERVICE MANUAL
Page 261 of 659
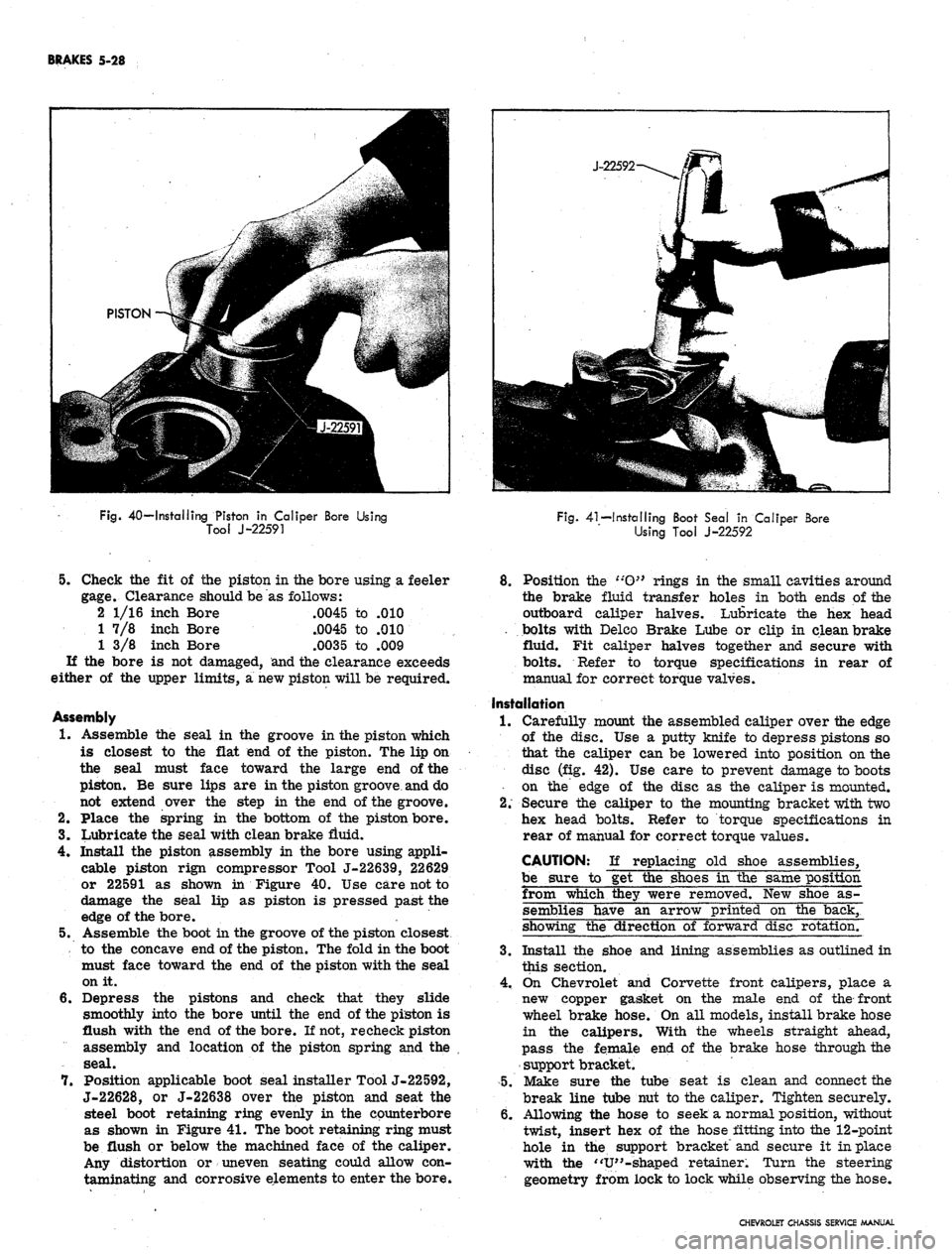
BRAKES 5-28
Fig.
40—Installing Piston in Caliper Bore Using
Tool J-22591
Fig.
41—Installing Boot Seal in Caliper Bore
Using Tool J-22592
5.
Check the fit of the piston in the bore using a feeler
gage.
Clearance should be as follows:
2 1/16 inch Bore .0045 to .010
1 7/8 inch Bore .0045 to .010
1 3/8 inch Bore .0035 to .009
If the bore is not damaged, and the clearance exceeds
either of the upper limits, a new piston will be required.
Assembly
1.
Assemble the seal in the groove in the piston which
is closest to the flat end of the piston. The lip on
the seal must face toward the large end of the
piston. Be sure lips are in the piston groove and do
not extend over the step in the end of the groove.
2.
Place the spring in the bottom of the piston bore.
3.
Lubricate the seal with dean brake fluid.
4.
Install the piston assembly in the bore using appli-
cable piston rign compressor Tool J-22639, 22629
or 22591 as shown in Figure 40. Use care not to
damage the seal lip as piston is pressed past the
edge of the bore. .
5.
Assemble the boot in the groove of the piston closest
to the concave end of the piston. The fold in the boot
must face toward the end of the piston with the seal
on it.
6. Depress the pistons and check that they slide
smoothly into the bore until the end of the piston is
flush with the end of the bore. If not, re check piston
assembly and location of the piston spring and the
seal.
7.
Position applicable boot seal installer Tool J-22592,
J-22628, or J-22638 over the piston and seat the
steel boot retaining ring evenly in the counterbore
as shown in Figure 41. The boot retaining ring must
be flush or below the machined face of the caliper.
Any distortion or uneven seating could allow con-
taminating and corrosive elements to enter the bore.
8. Position the t:O}> rings in the small cavities around
the brake fluid transfer holes in both ends of the
outboard caliper halves. Lubricate the hex head
. bolts with Delco Brake Lube or clip in clean brake
fluid. Fit caliper halves together and secure with
bolts.
Refer to torque specifications in rear of
manual for correct torque valves.
Installation
1.
Carefully mount the assembled caliper over the edge
of the disc. Use a putty knife to depress pistons so
that the caliper can be lowered into position on the
disc (fig. 42). Use care to prevent damage to boots
• on the edge of the disc as the caliper is mounted.
2.
Secure the caliper to the mounting bracket with two
hex head bolts. Refer to torque specifications in
rear of manual for correct torque values.
CAUTION: If replacing old shoe assemblies,
be sure to get the shoes in the same position
from which they were removed. New shoe as-
semblies have an arrow printed on the back,
showing the direction of forward disc rotation.
3.
Install the shoe and lining assemblies as outlined in
this section.
4.
On Chevrolet and Corvette front calipers, place a
new copper gasket on the male end of the front
wheel brake hose. On all models, install brake hose
in the calipers. With the wheels straight ahead,
pass the female end of the brake hose through the
support bracket.
5.
Make sure the tube seat is clean and connect the
break line tube nut to the caliper. Tighten securely.
6. Allowing the hose to seek a normal position, without
twist, insert hex of the hose fitting into the 12-point
hole in the support bracket and secure it in place
with the "V"-shaped retainer. Turn the steering
geometry from lock to lock while observing the hose.
CHEVROLET CHASSIS SERVICE MANUAL
Page 269 of 659
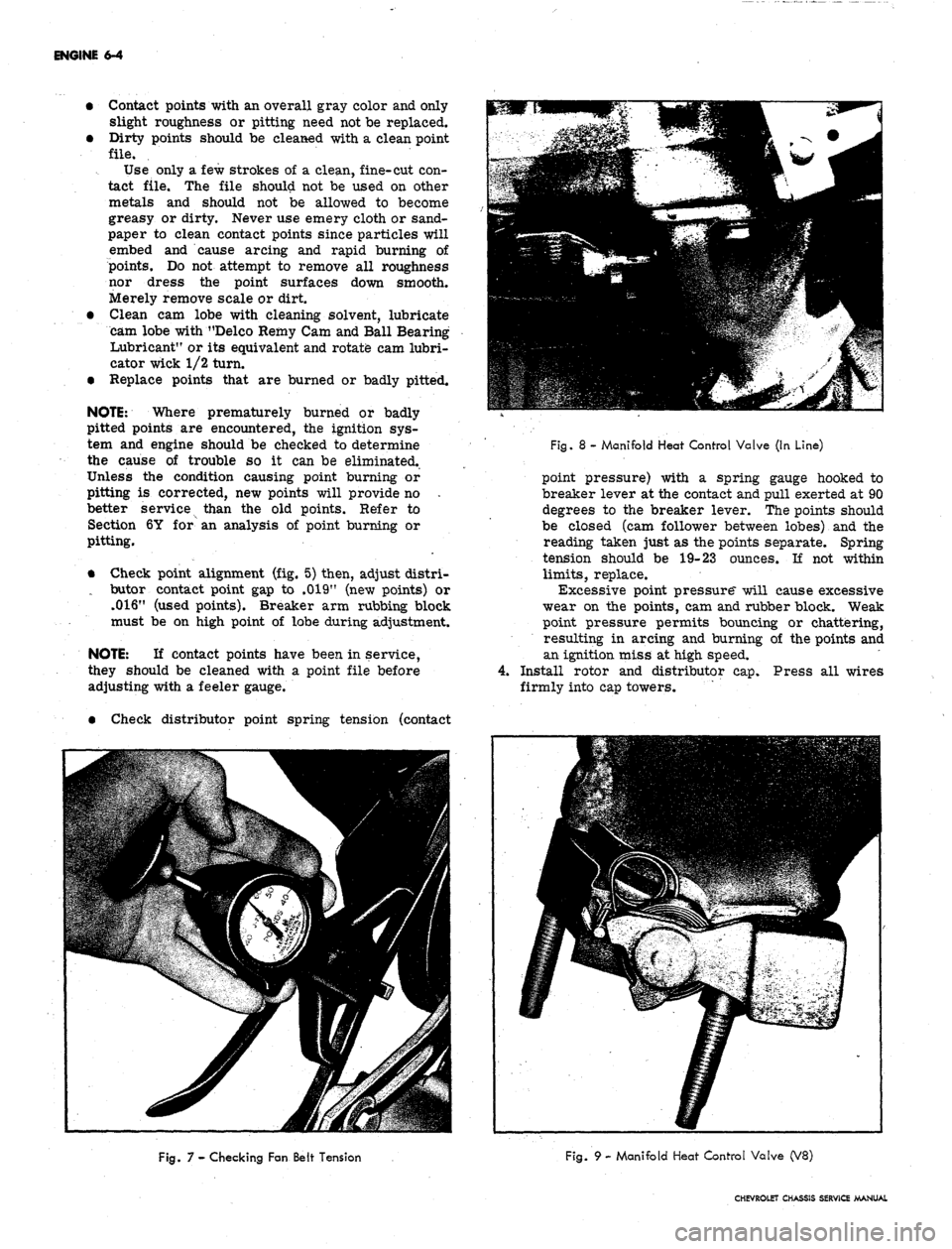
ENGINE 6-4
• Contact points with an overall gray color and only
slight roughness or pitting need not be replaced.
• Dirty points should be cleaned with a clean point
file.
Use only a few strokes of a clean, fine-cut con-
tact file. The file should not be used on other
metals and should not be allowed to become
greasy or dirty. Never use emery cloth or sand-
paper to clean contact points since particles will
embed and cause arcing and rapid burning of
points. Do not attempt to remove all roughness
nor dress the point surfaces down smooth.
Merely remove scale or dirt.
• Clean cam lobe with cleaning solvent, lubricate
cam lobe with "Delco Remy Cam and Ball Bearing
Lubricant" or its equivalent and rotate cam lubri-
cator wick 1/2 turn.
• Replace points that are burned or badly pitted.
NOTE: Where prematurely burned or badly
pitted points are encountered, the ignition sys-
tem and engine should be checked to determine
the cause of trouble so it can be eliminated.
Unless the condition causing point burning or
pitting is corrected, new points will provide no .
better service than the old points. Refer to
Section 6Y for an analysis of point burning or
pitting.
• Check point alignment (fig. 5) then, adjust distri-
. butor contact point gap to .019" (new points) or
.016"
(used points). Breaker arm rubbing block
must be on high point of lobe during adjustment.
NOTE: If contact points have been in service,
they should be cleaned with a point file before
adjusting with a feeler gauge.
• Check distributor point spring tension (contact
Fig. 8 - Manifold Heat Control Valve (In Line)
point pressure) with a spring gauge hooked to
breaker lever at the contact and pull exerted at 90
degrees to the breaker lever. The points should
be closed (cam follower between lobes) and the
reading taken just as the points separate. Spring
tension should be 19-23 ounces. If not within
limits,
replace.
Excessive point pressure" will cause excessive
wear on the points, cam and rubber block. Weak
point pressure permits bouncing or chattering,
resulting in arcing and burning of the points and
an ignition miss at high speed.
4.
Install rotor and distributor cap. Press all wires
firmly into cap towers.
Fig. 7 - Checking Fan Belt Tension
Fig. 9 - Manifold Heat Control Valve (V8)
CHEVROLET CHASSIS SERVICE MANUAL
Page 275 of 659
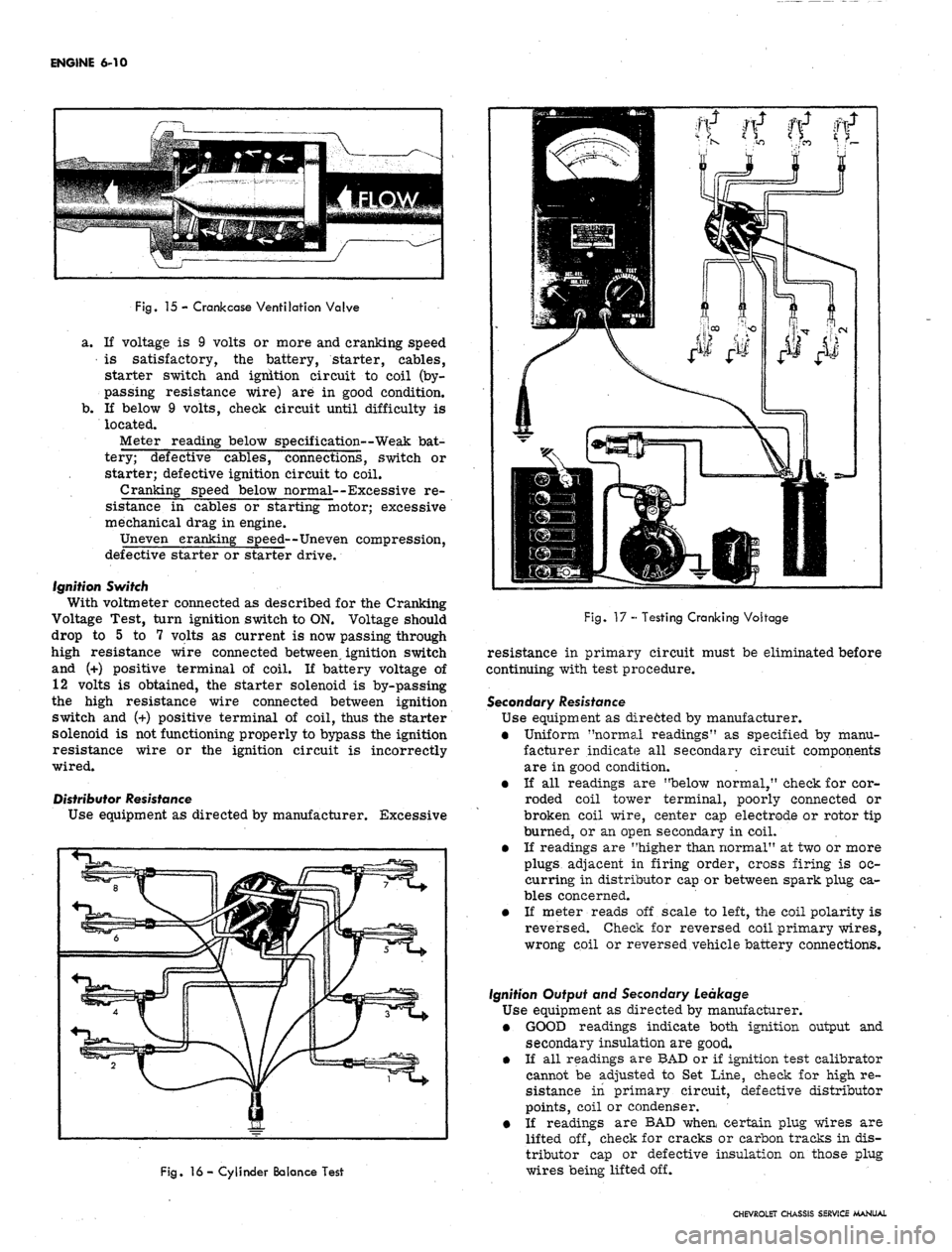
ENGINE 6-10
Fig.
15 - Crank case Ventilation Valve
a. If voltage is 9 volts or more and cranking speed
is satisfactory, the battery, starter, cables,
starter switch and ignition circuit to coil (by-
passing resistance wire) are in good condition.
b.
If below 9 volts, check circuit until difficulty is
located.
Meter reading below specification—Weak bat-
tery; defective cables, connections, switch or
starter; defective ignition circuit to coil.
Cranking speed below normal--Excessive re-
sistance in cables or starting motor; excessive
mechanical drag in engine.
Uneven cranking speed—Uneven compression,
defective starter or starter drive.
Ignition Switch
With voltmeter connected as described for the Cranking
Voltage Test, turn ignition switch to ON. Voltage should
drop to 5 to 7 volts as current is now passing through
high resistance wire connected between ignition switch
and (+) positive terminal of coil. If battery voltage of
12 volts is obtained, the starter solenoid is by-passing
the high resistance wire connected between ignition
switch and (+) positive terminal of coil, thus the starter
solenoid is not functioning properly to bypass the ignition
resistance wire or the ignition circuit is incorrectly
wired.
Distributor Resistance
Use equipment as directed by manufacturer.
Excessive
(t n ti ft
Fig.
16 - Cylinder Balance Test
Fig.
17 - Testing Cranking Voltage
resistance in primary circuit must be eliminated before
continuing with test procedure.
Secondary Resistance
Use equipment as dire6ted by manufacturer.
• Uniform "normal readings" as specified by manu-
facturer indicate all secondary circuit components
are in good condition.
• If all readings are "below normal," check for cor-
roded coil tower terminal, poorly connected or
broken coil wire, center cap electrode or rotor tip
burned, or an open secondary in coil.
• If readings are "higher than normal" at two or more
plugs adjacent in firing order, cross firing is oc-
curring in distributor cap or between spark plug ca-
bles concerned.
• If meter reads off scale to left, the coil polarity is
reversed. Check for reversed coil primary wires,
wrong coil or reversed vehicle battery connections.
Ignition Output and Secondary Leakage
Use equipment as directed by manufacturer.
• GOOD readings indicate both ignition output and
secondary insulation are good.
• If all readings are BAD or if ignition test calibrator
cannot be adjusted to Set Line, check for high re-
sistance in primary circuit, defective distributor
points, coil or condenser.
e If readings are BAD when certain plug wires are
lifted off, check for cracks or carbon tracks in dis-
tributor cap or defective insulation on those plug
wires being lifted off.
CHEVROLET CHASSIS SERVICE MANUAL
Page 284 of 659
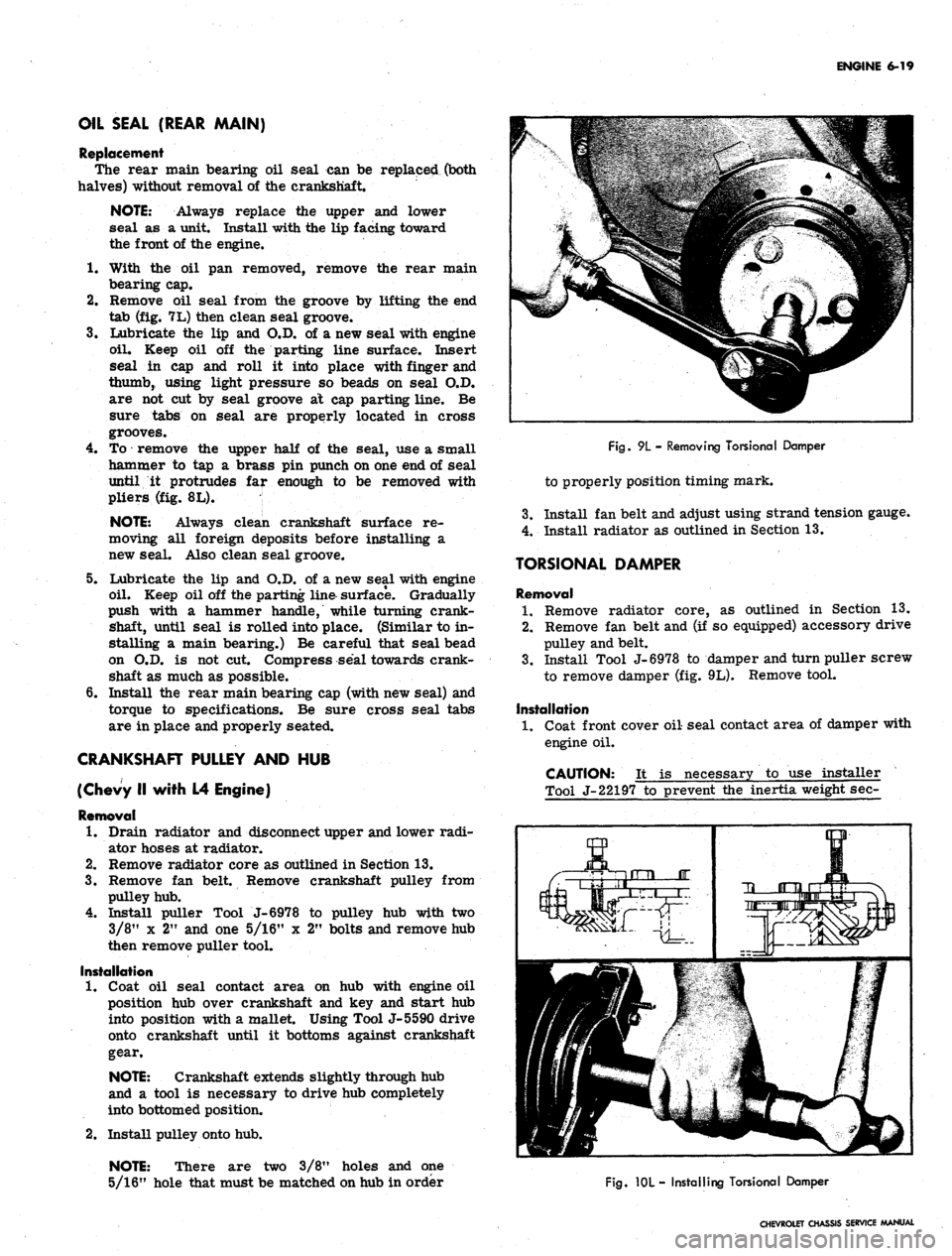
ENGINE 6-19
OIL SEAL (REAR MAIN)
Replacement
The rear main bearing oil seal can be replaced (both
halves) without removal of the crankshaft.
NOTE:
Always replace the upper and lower
seal as a unit. Install with the lip facing toward
the front of the engine.
1.
With the oil pan removed, remove the rear main
bearing cap.
2.
Remove oil seal from the groove by lifting the end
tab (fig. 7L) then clean seal groove.
3.
Lubricate the lip and O.D. of a new seal with engine
oil. Keep oil off the parting line surface. Insert
seal in cap and roll it into place with finger and
thumb,
using light pressure so beads on seal O.D.
are not cut by seal groove at cap parting line. Be
sure tabs on seal are properly located in cross
grooves.
4.
To remove the upper half of the seal, use a small
hammer to tap a brass pin punch on one end of seal
until it protrudes far enough to be removed with
pliers (fig. 8L).
NOTE:
Always clean crankshaft surface re-
moving all foreign deposits before installing a
new seal. Also clean seal groove.
5. Lubricate the lip and O.D. of a new seal with engine
oil. Keep oil off the parting line surface. Gradually
push with a hammer handle, while turning crank-
shaft, until seal is rolled into place. (Similar to in-
stalling a main bearing.) Be careful that seal bead
on O.D. is not cut. Compress seal towards crank-
shaft as much as possible.
6. Install the rear main bearing cap (with new seal) and
torque to specifications. Be sure cross seal tabs
are in place and properly seated.
CRANKSHAFT PULLEY AND HUB
(Chevy II with L4 Engine)
Removal
1.
Drain radiator and disconnect upper and lower radi-
ator hoses at radiator.
2.
Remove radiator core as outlined in Section 13.
3.
Remove fan belt. Remove crankshaft pulley from
pulley hub.
4.
Install puller Tool J-6978 to pulley hub with two
3/8"
x 2" and one 5/16" x 2" bolts and remove hub
then remove puller tool.
Installation
1.
Coat oil seal contact area on hub with engine oil
position hub over crankshaft and key and start hub
into position with a mallet. Using Tool J-5590 drive
onto crankshaft until it bottoms against crankshaft
gear.
NOTE:
Crankshaft extends slightly through hub
and a tool is necessary to drive hub completely
into bottomed position.
2.
Install pulley onto hub.
NOTE:
There are two 3/8" holes and one
5/16" hole that must be matched on hub in order
Fig.
9L - Removing Torsional Damper
to properly position timing mark.
3.
Install fan belt and adjust using strand tension gauge.
4.
Install radiator as outlined in Section 13.
TORSIONAL DAMPER
Removal
1.
Remove radiator core, as outlined in Section 13.
2.
Remove fan belt and (if so equipped) accessory drive
pulley and belt.
3.
Install Tool J-6978 to damper and turn puller screw
to remove damper (fig. 9L). Remove tool.
Installation
1.
Coat front cover oil seal contact area of damper with
engine oil.
CAUTION: It is necessary to use installer
Tool J-22197 to prevent the inertia weight sec-
Fig.
10L - Installing Torsional Damper
CHEVROLET CHASSIS SERVICE MANUAL
Page 285 of 659
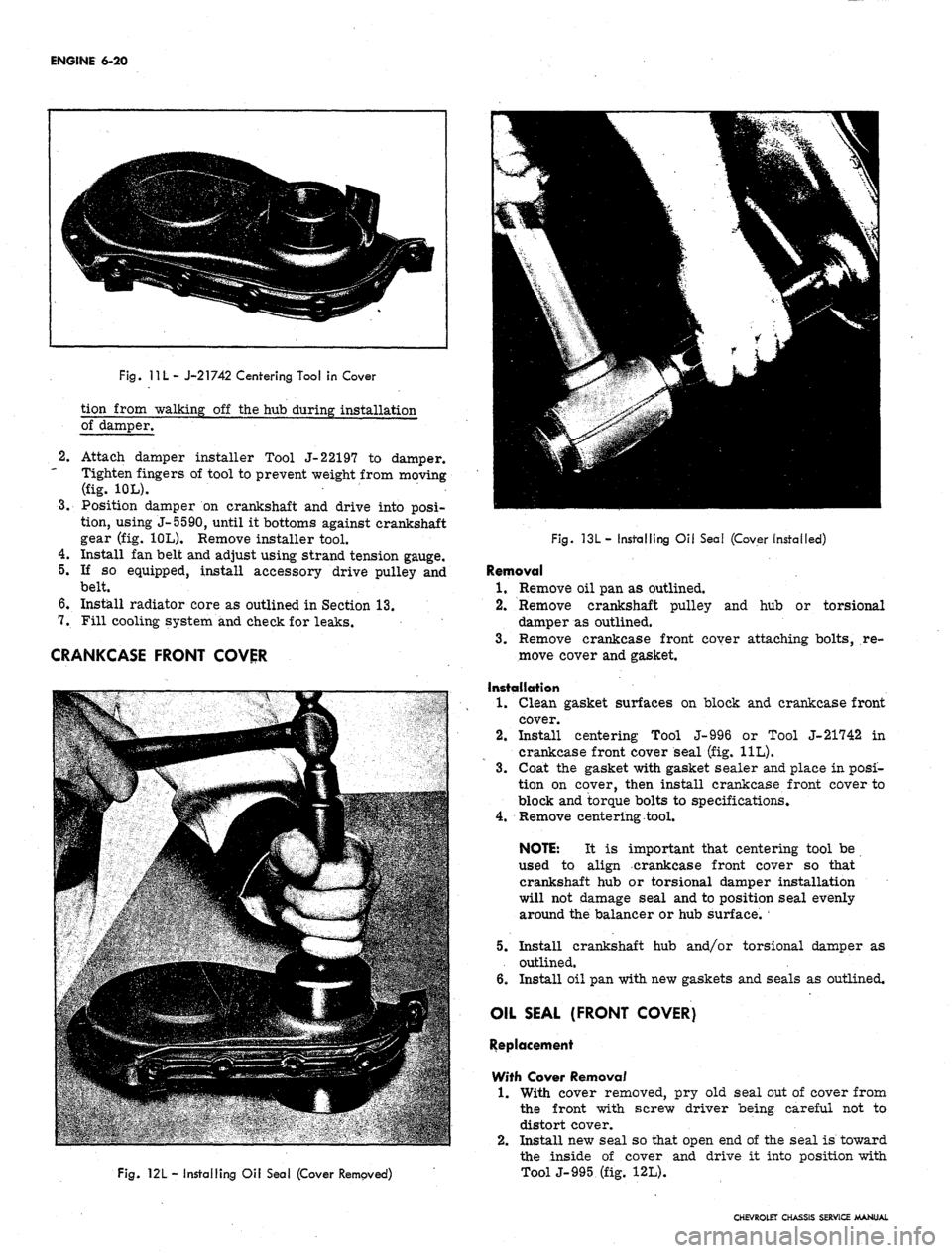
ENGINE 6-20
Fig.
11 L
- J-21742 Centering Tool in Cover
tion from walking off the hub during installation
of damper.
2.
3.
Attach damper installer Tool J-22197 to damper.
Tighten fingers of tool to prevent weight from moving
(fig. 10L).
Position damper on crankshaft and drive into posi-
tion, using J-5590, until it bottoms against crankshaft
gear (fig. 10L). Remove installer tool.
4.
Install fan belt and adjust using strand tension gauge.
5.
If so equipped, install accessory drive pulley and
belt.
6. Install radiator core as outlined in Section 13.
7.
Fill cooling system and check for leaks.
CRANKCASE FRONT COVER
Fig.
121
- Installing Oil Seal (Cover Removed)
Fig. 13L- Installing Oil Seal (Cover installed)
Removal
1.
Remove oil pan as outlined.
2.
Remove crankshaft pulley and hub or torsional
damper as outlined.
3.
Remove crankcase front coyer attaching bolts, re-
move cover and gasket.
Installation
1.
Clean gasket surfaces on block and crankcase front
cover.
2.
Install centering Tool J-996 or Tool J-21742 in
crankcase front cover seal (fig. 11L).
3.
Coat the gasket with gasket sealer and place in posi-
tion on cover, then install crankcase front cover to
block and torque bolts to specifications.
4.
Remove centering tool.
NOTE: It is important that centering tool be
used to align crankcase front cover so that
crankshaft hub or torsional damper installation
will not damage seal and to position seal evenly
around the balancer or hub surface.
5.
Install crankshaft hub and/or torsional damper as
outlined.
6. Install oil pan with new gaskets and seals as outlined.
OIL SEAL (FRONT COVER)
Replacement
With Cover Removal
1.
With cover removed, pry old seal out of cover from
the front with screw driver being careful not to
distort cover.
2.
Install new seal so that open end of the seal is toward
the inside of cover and drive it into position with
ToolJ-995 (fig. 12L).
CHEVROLET CHASSIS SERVICE MANUAL
Page 286 of 659
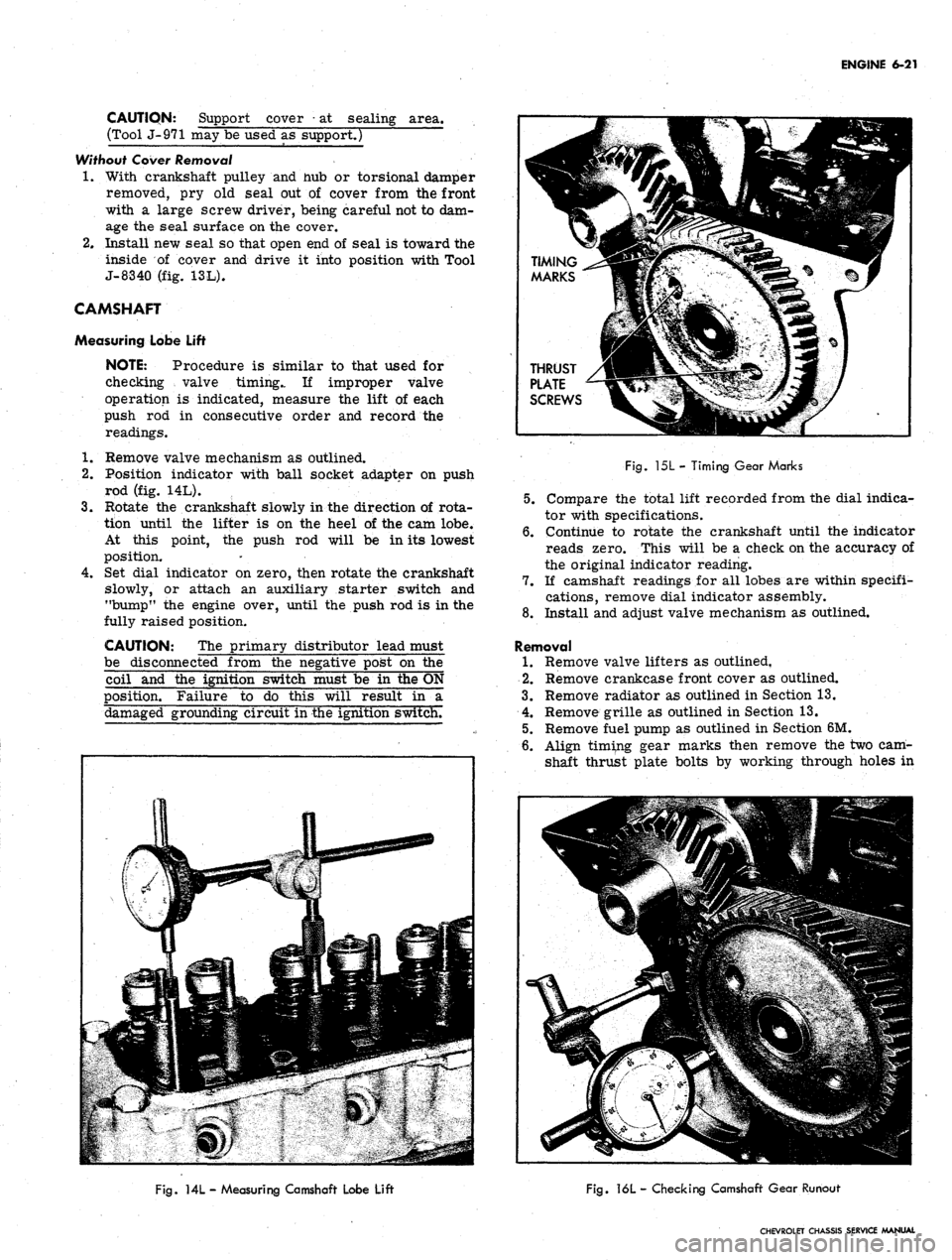
ENGINE 6-21
CAUTION: Support cover
•
at sealing area.
(Tool J-971 may be used as support.)
Without Cover
Removal
1.
With crankshaft pulley and nub or torsional damper
removed, pry old seal out of cover from the front
with a large screw driver, being careful not to dam-
age the seal surface on the cover.
2.
Install new seal so that open end of seal is toward the
inside of cover and drive it into position with Tool
J-8340 (fig. 13L).
CAMSHAFT
Measuring Lobe Lift
NOTE: Procedure is similar to that used for
checking valve timing.. If improper valve
operation is indicated, measure the lift of each
push rod in consecutive order and record the
readings.
1.
Remove valve mechanism as outlined.
2.
Position indicator with ball socket adapter on push
rod (fig. 14L).
3.
Rotate the crankshaft slowly in the direction of rota-
tion until the lifter is on the heel of the cam lobe.
At this point, the push rod will be in its lowest
position.
4.
Set dial indicator on zero, then rotate the crankshaft
slowly, or attach an auxiliary starter switch and
"bump" the engine over, until the push rod is in the
fully raised position.
CAUTION: The primary distributor lead must
be disconnected from the negative post on the
coil and the ignition switch must be in the ON
position. Failure to do this will result in a
damaged grounding circuit in the ignition switch.
Fig.
15L - Timing Gear Marks
5.
Compare the total lift recorded from the dial indica-
tor with specifications.
6. Continue to rotate the crankshaft until the indicator
reads zero. This will be a check on the accuracy of
the original indicator reading.
7.
If camshaft readings for all lobes are within specifi-
cations, remove dial indicator assembly.
8. Install and adjust valve mechanism as outlined.
Removal
1.
Remove valve lifters as outlined,
2.
Remove crankcase front cover as outlined.
3.
Remove radiator as outlined in Section 13.
4.
Remove grille as outlined in Section 13.
5.
Remove fuel pump as outlined in Section 6M.
6. Align timing gear marks then remove the two cam-
shaft thrust plate bolts by working through holes in
Fig.
ML - Measuring Camshaft Lobe Lift
Fig.
16L - Checking Camshaft Gear Runout
CHEVROLET CHASSIS SERVICE MANUAL
Page 288 of 659
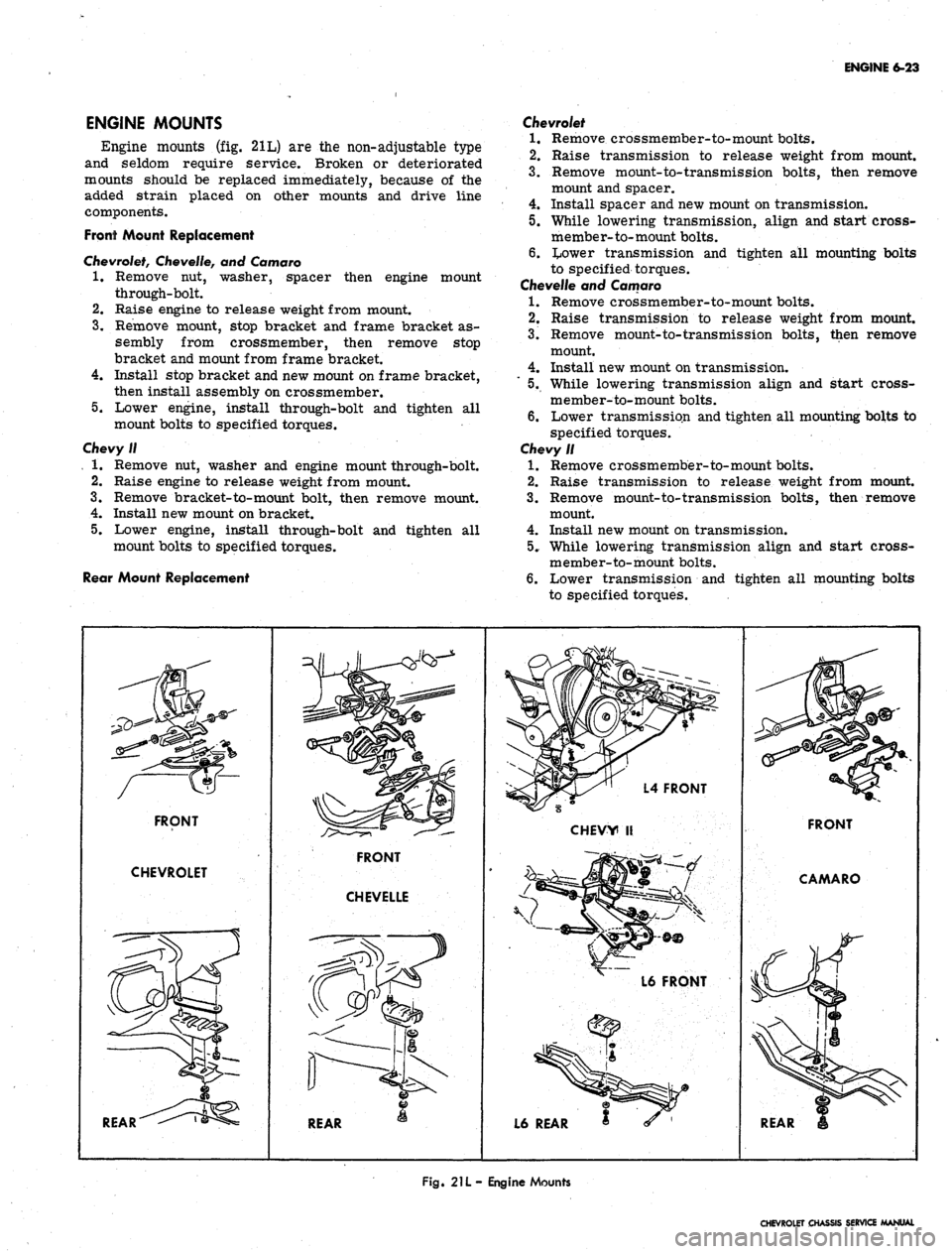
ENGINE 6-23
ENGINE MOUNTS
Engine mounts (fig. 21L) are the non-adjustable type
and seldom require service. Broken or deteriorated
mounts should be replaced immediately, because of the
added strain placed on other mounts and drive line
components.
Front Mount Replacement
Chevrolet,
Chevelle, and Comoro
1.
Remove nut, washer, spacer then engine mount
through-bolt.
2.
Raise engine to release weight from mount.
3.
Remove mount, stop bracket and frame bracket as-
sembly from crossmember, then remove stop
bracket and mount from frame bracket.
4.
Install stop bracket and new mount on frame bracket,
then install assembly on crossmember.
5.
Lower engine, install through-bolt and tighten all
mount bolts to specified torques.
Chevy II
, 1. Remove nut, washer and engine mount through-bolt.
2.
Raise engine to release weight from mount.
3.
Remove bracket-to-mount bolt, then remove mount.
4.
Install new mount on bracket.
5.
Lower engine, install through-bolt and tighten all
mount bolts to specified torques.
Rear Mount Replacement
Chevrolet
1.
Remove crossmember-to-mount bolts.
2.
Raise transmission to release weight from mount.
3.
Remove mount-to-trans mission bolts, then remove
mount and spacer.
4.
Install spacer and new mount on transmission.
5.
While lowering transmission, align and start cross-
member-to-mount bolts.
6. tower transmission and tighten all mounting bolts
to specified torques.
Chevelle and Camaro
1.
Remove crossmember-to-mount bolts.
2.
Raise transmission to release weight from mount.
3.
Remove mount-to-transmission bolts, then remove
mount.
4.
Install new mount on transmission.
5.
While lowering transmission align and start cross-
member-to-mount bolts.
6. Lower transmission and tighten all mounting bolts to
specified torques.
Chevy II
1.
Remove crossmember-to-mount bolts.
2.
Raise transmission to release weight from mount.
3.
Remove mount-to-transmission bolts, then remove
mount.
4.
Install new mount on transmission.
5.
While lowering transmission align and start cross-
member-to-mount bolts.
6. Lower transmission and tighten all mounting bolts
to specified torques.
FRONT
CHEVROLET
REAR
REAR
L4 FRONT
CHEVY II
L6 FRONT
L6 REAR
FRONT
CAMARO
REAR
Fig.
21L- Engine Mounts
CHEVROLET CHASSIS SERVICE MANUAL
Page 297 of 659
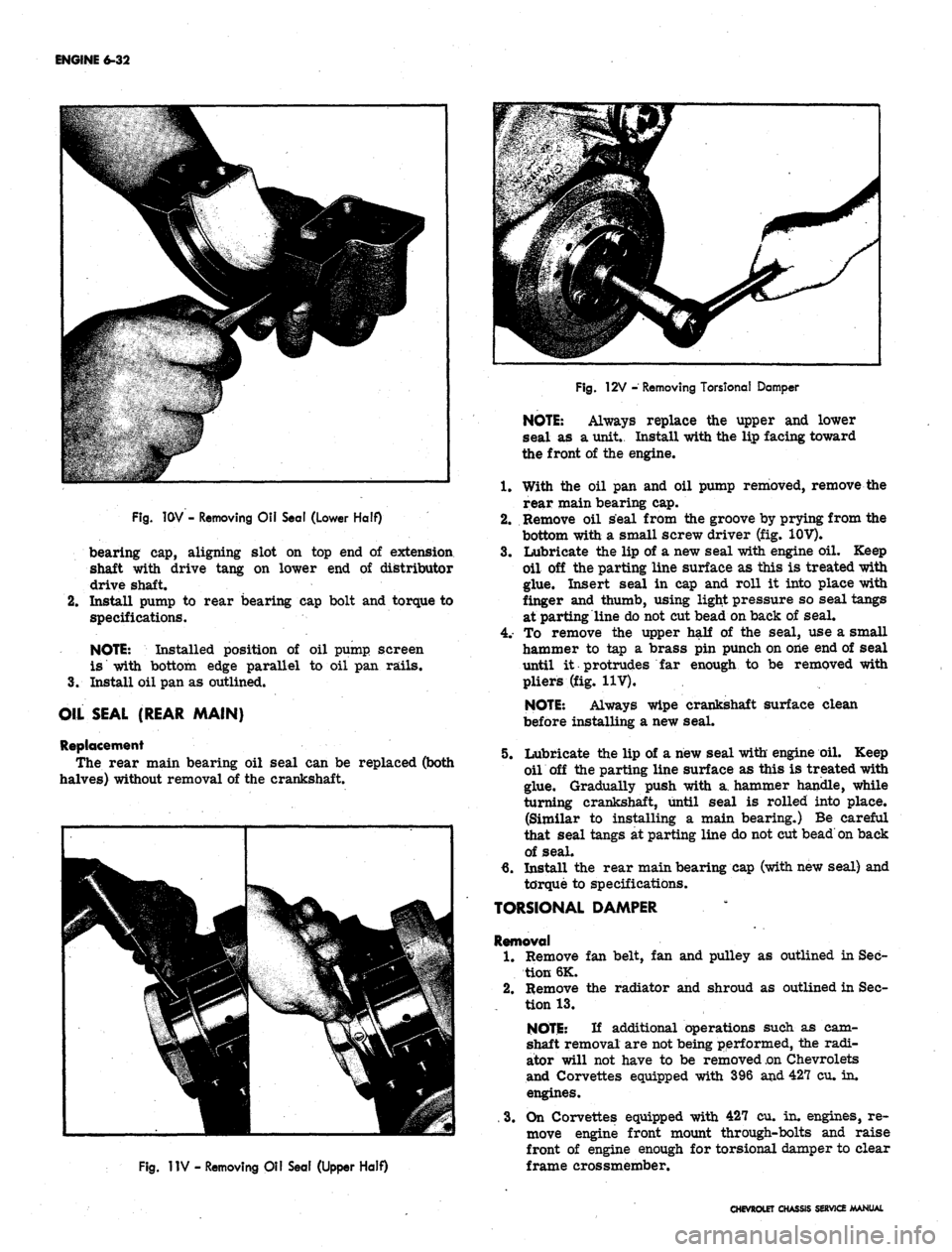
ENGINE 6-32
Fig.
1GV - Removing Oil Seal (Lower Half)
bearing cap, aligning slot on top end of extension
shaft with drive tang on lower end of distributor
drive shaft.
2.
Install pump to rear bearing cap bolt and torque to
specifications.
NOTE:
Installed position of oil pump, screen
is with bottom edge parallel to oil pan rails.
3.
Install oil pan as outlined.
OIL SEAL (REAR MAIN)
Replacement
The rear main bearing oil seal can be replaced (both
halves) without removal of the crankshaft.
Fig.
12V - Removing Torstonal Damper
NOTE:
Always replace the upper and lower
seal as a unit.. Install with the lip facing toward
the front of the engine.
With the oil pan and oil pump removed, remove the
rear main bearing cap.
Remove oil seal from the groove by prying from the
bottom with a small screw driver (fig. 10V).
Lubricate the lip of a new seal with engine oil. Keep
oil off the parting line surface as this is treated with
glue. Insert seal in cap and roll it into place with
finger and thumb, using light pressure so seal tangs
at parting line do not cut bead on back of seal.
To remove the upper half of the seal, use a small
hammer to tap a brass pin punch on one end of seal
until it protrudes far enough to be removed with
pliers (fig. 11V).
NOTE:
Always wipe crankshaft surface clean
before installing a new seal.
1.
2.
3.
5.
Fig.
1IV - Removing Oil Seal (Upper Half)
Lubricate the lip of a new seal with engine oil. Keep
oil off the parting line surface as this is treated with
glue. Gradually push with a. hammer handle, while
turning crankshaft, until seal is rolled into place.
(Similar to installing a main bearing.) Be careful
that seal tangs at parting line do not cut bead on back
of seal.
6. Install the rear main bearing cap (with new seal) and
torque to specifications.
TORSIONAL DAMPER
Removal
1.
Remove fan belt, fan and pulley as outlined in Sec-
tion 6K.
2.
Remove the radiator and shroud as outlined in Sec-
tion 13.
NOTE:
If additional operations such as cam-
shaft removal are not being performed, the radi-
ator will not have to be removed
.on
Chevrolets
and Corvettes equipped with 396 and 427 cu. in.
engines.
. 3. On Corvettes equipped with 427 cu. in. engines, re-
move engine front mount through-bolts and raise
front of engine enough for torsional damper to clear
frame crossmember.
CHEVROLET CHASSIS SERVICE MANUAL