CHEVROLET PLYMOUTH ACCLAIM 1993 Service Manual
Manufacturer: CHEVROLET, Model Year: 1993, Model line: PLYMOUTH ACCLAIM, Model: CHEVROLET PLYMOUTH ACCLAIM 1993Pages: 2438, PDF Size: 74.98 MB
Page 2041 of 2438
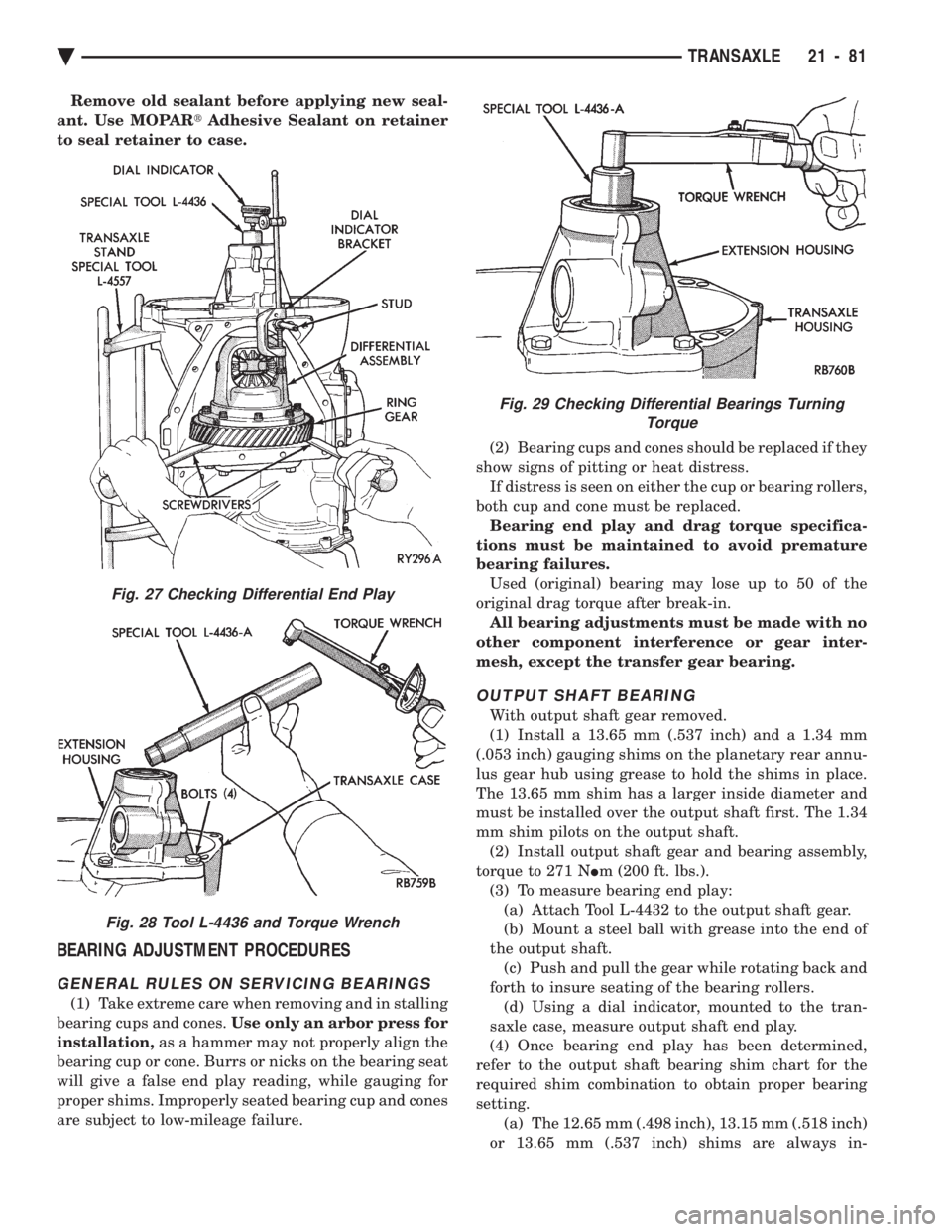
Remove old sealant before applying new seal-
ant. Use MOPAR tAdhesive Sealant on retainer
to seal retainer to case.
BEARING ADJUSTMENT PROCEDURES
GENERAL RULES ON SERVICING BEARINGS
(1) Take extreme care when removing and in stalling
bearing cups and cones. Use only an arbor press for
installation, as a hammer may not properly align the
bearing cup or cone. Burrs or nicks on the bearing seat
will give a false end play reading, while gauging for
proper shims. Improperly seated bearing cup and cones
are subject to low-mileage failure. (2) Bearing cups and cones should be replaced if they
show signs of pitting or heat distress. If distress is seen on either the cup or bearing rollers,
both cup and cone must be replaced. Bearing end play and drag torque specifica-
tions must be maintained to avoid premature
bearing failures. Used (original) bearing may lose up to 50 of the
original drag torque after break-in. All bearing adjustments must be made with no
other component interference or gear inter-
mesh, except the transfer gear bearing.
OUTPUT SHAFT BEARING
With output shaft gear removed.
(1) Install a 13.65 mm (.537 inch) and a 1.34 mm
(.053 inch) gauging shims on the planetary rear annu-
lus gear hub using grease to hold the shims in place.
The 13.65 mm shim has a larger inside diameter and
must be installed over the output shaft first. The 1.34
mm shim pilots on the output shaft. (2) Install output shaft gear and bearing assembly,
torque to 271 N Im (200 ft. lbs.).
(3) To measure bearing end play: (a) Attach Tool L-4432 to the output shaft gear.
(b) Mount a steel ball with grease into the end of
the output shaft. (c) Push and pull the gear while rotating back and
forth to insure seating of the bearing rollers. (d) Using a dial indicator, mounted to the tran-
saxle case, measure output shaft end play.
(4) Once bearing end play has been determined,
refer to the output shaft bearing shim chart for the
required shim combination to obtain proper bearing
setting. (a) The 12.65 mm (.498 inch), 13.15 mm (.518 inch)
or 13.65 mm (.537 inch) shims are always in-
Fig. 27 Checking Differential End Play
Fig. 28 Tool L-4436 and Torque Wrench
Fig. 29 Checking Differential Bearings Turning Torque
Ä TRANSAXLE 21 - 81
Page 2042 of 2438
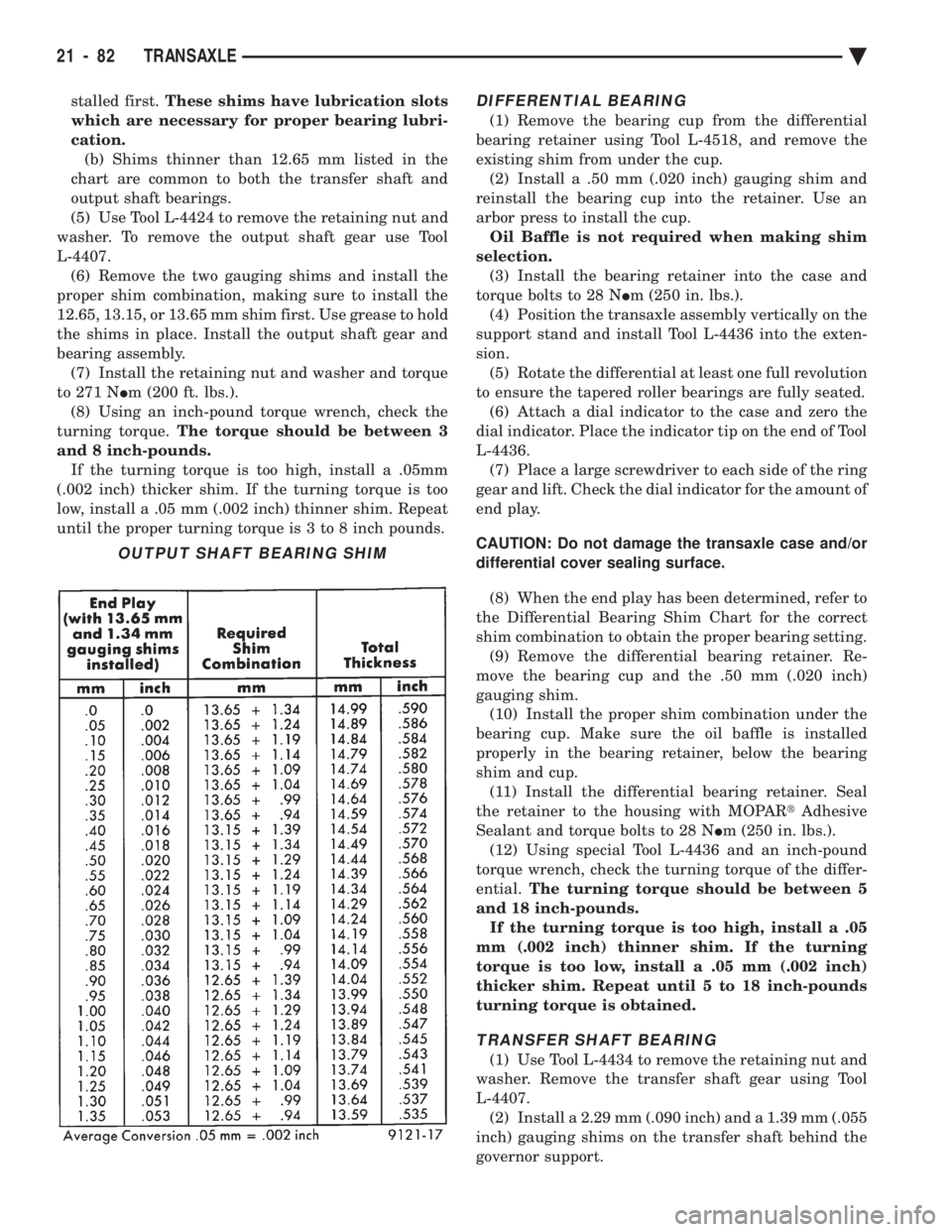
stalled first. These shims have lubrication slots
which are necessary for proper bearing lubri-
cation. (b) Shims thinner than 12.65 mm listed in the
chart are common to both the transfer shaft and
output shaft bearings.
(5) Use Tool L-4424 to remove the retaining nut and
washer. To remove the output shaft gear use Tool
L-4407. (6) Remove the two gauging shims and install the
proper shim combination, making sure to install the
12.65, 13.15, or 13.65 mm shim first. Use grease to hold
the shims in place. Install the output shaft gear and
bearing assembly. (7) Install the retaining nut and washer and torque
to 271 N Im (200 ft. lbs.).
(8) Using an inch-pound torque wrench, check the
turning torque. The torque should be between 3
and 8 inch-pounds. If the turning torque is too high, install a .05mm
(.002 inch) thicker shim. If the turning torque is too
low, install a .05 mm (.002 inch) thinner shim. Repeat
until the proper turning torque is 3 to 8 inch pounds.DIFFERENTIAL BEARING
(1) Remove the bearing cup from the differential
bearing retainer using Tool L-4518, and remove the
existing shim from under the cup. (2) Install a .50 mm (.020 inch) gauging shim and
reinstall the bearing cup into the retainer. Use an
arbor press to install the cup. Oil Baffle is not required when making shim
selection. (3) Install the bearing retainer into the case and
torque bolts to 28 N Im (250 in. lbs.).
(4) Position the transaxle assembly vertically on the
support stand and install Tool L-4436 into the exten-
sion. (5) Rotate the differential at least one full revolution
to ensure the tapered roller bearings are fully seated. (6) Attach a dial indicator to the case and zero the
dial indicator. Place the indicator tip on the end of Tool
L-4436. (7) Place a large screwdriver to each side of the ring
gear and lift. Check the dial indicator for the amount of
end play.
CAUTION: Do not damage the transaxle case and/or
differential cover sealing surface.
(8) When the end play has been determined, refer to
the Differential Bearing Shim Chart for the correct
shim combination to obtain the proper bearing setting. (9) Remove the differential bearing retainer. Re-
move the bearing cup and the .50 mm (.020 inch)
gauging shim. (10) Install the proper shim combination under the
bearing cup. Make sure the oil baffle is installed
properly in the bearing retainer, below the bearing
shim and cup. (11) Install the differential bearing retainer. Seal
the retainer to the housing with MOPAR tAdhesive
Sealant and torque bolts to 28 N Im (250 in. lbs.).
(12) Using special Tool L-4436 and an inch-pound
torque wrench, check the turning torque of the differ-
ential. The turning torque should be between 5
and 18 inch-pounds. If the turning torque is too high, install a .05
mm (.002 inch) thinner shim. If the turning
torque is too low, install a .05 mm (.002 inch)
thicker shim. Repeat until 5 to 18 inch-pounds
turning torque is obtained.
TRANSFER SHAFT BEARING
(1) Use Tool L-4434 to remove the retaining nut and
washer. Remove the transfer shaft gear using Tool
L-4407. (2) Install a 2.29 mm (.090 inch) and a 1.39 mm (.055
inch) gauging shims on the transfer shaft behind the
governor support.
OUTPUT SHAFT BEARING SHIM
21 - 82 TRANSAXLE Ä
Page 2043 of 2438
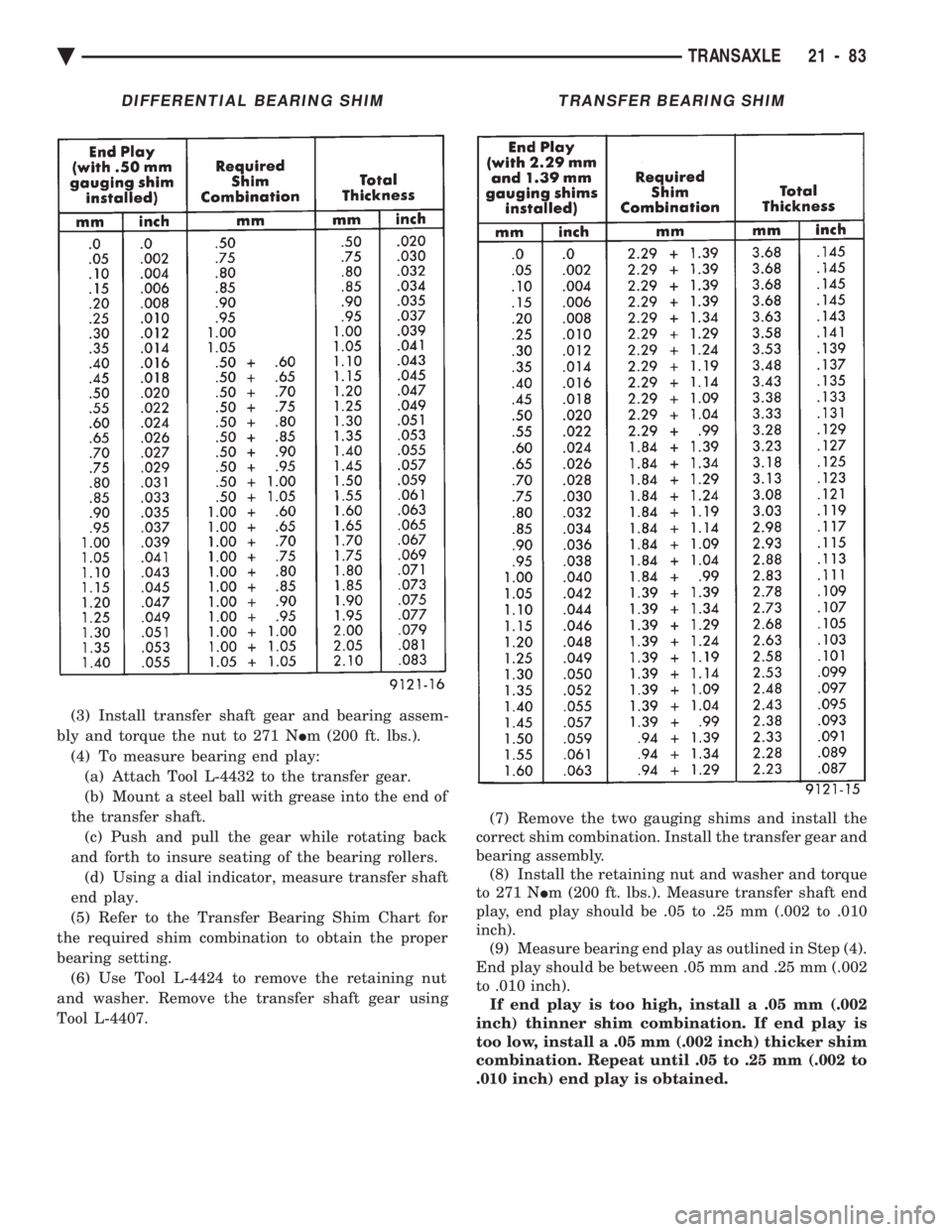
(3) Install transfer shaft gear and bearing assem-
bly and torque the nut to 271 N Im (200 ft. lbs.).
(4) To measure bearing end play: (a) Attach Tool L-4432 to the transfer gear.
(b) Mount a steel ball with grease into the end of
the transfer shaft. (c) Push and pull the gear while rotating back
and forth to insure seating of the bearing rollers. (d) Using a dial indicator, measure transfer shaft
end play.
(5) Refer to the Transfer Bearing Shim Chart for
the required shim combination to obtain the proper
bearing setting. (6) Use Tool L-4424 to remove the retaining nut
and washer. Remove the transfer shaft gear using
Tool L-4407. (7) Remove the two gauging shims and install the
correct shim combination. Install the transfer gear and
bearing assembly. (8) Install the retaining nut and washer and torque
to 271 N Im (200 ft. lbs.). Measure transfer shaft end
play, end play should be .05 to .25 mm (.002 to .010
inch). (9) Measure bearing end play as outlined in Step (4).
End play should be between .05 mm and .25 mm (.002
to .010 inch). If end play is too high, install a .05 mm (.002
inch) thinner shim combination. If end play is
too low, install a .05 mm (.002 inch) thicker shim
combination. Repeat until .05 to .25 mm (.002 to
.010 inch) end play is obtained.
DIFFERENTIAL BEARING SHIMTRANSFER BEARING SHIM
Ä TRANSAXLE 21 - 83
Page 2044 of 2438
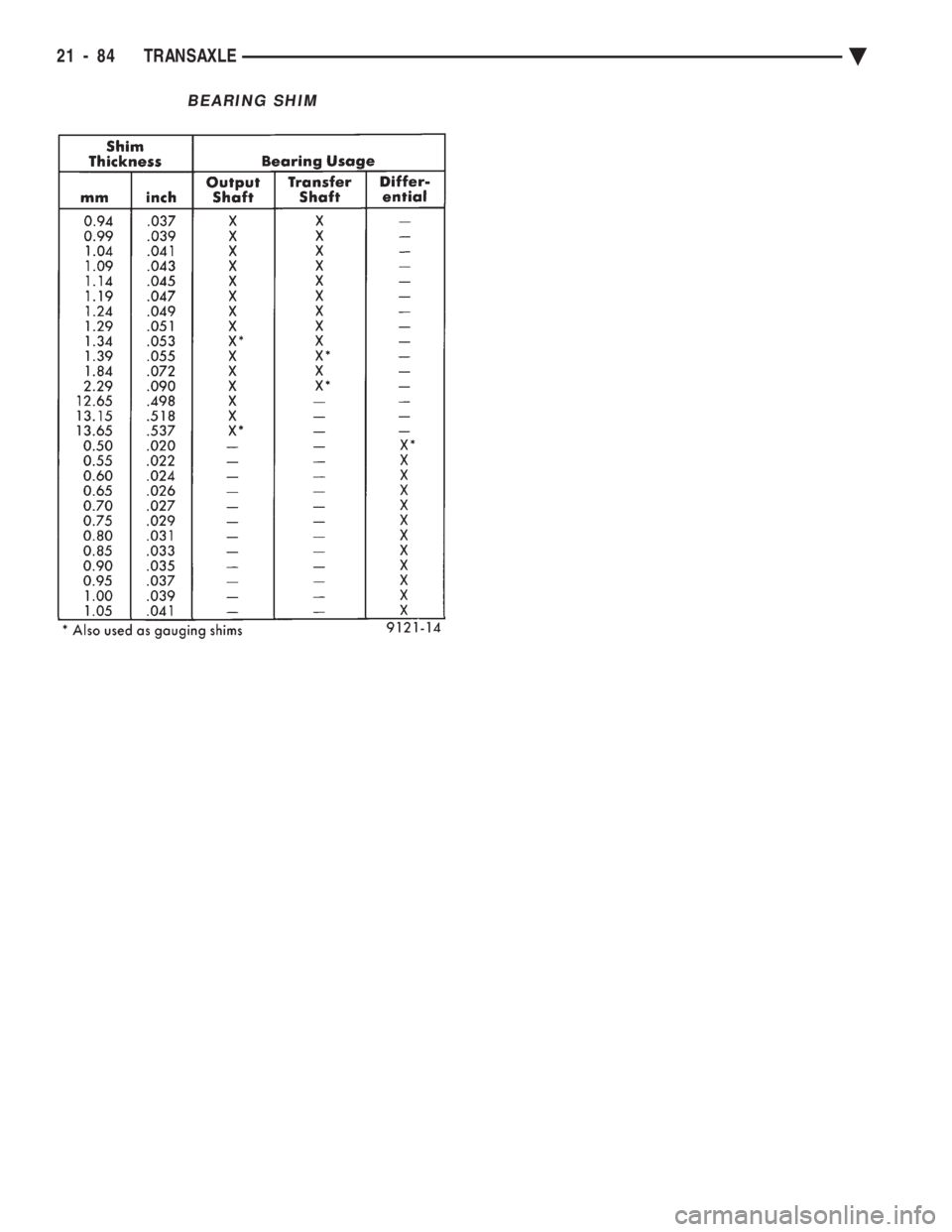
BEARING SHIM
21 - 84 TRANSAXLE Ä
Page 2045 of 2438
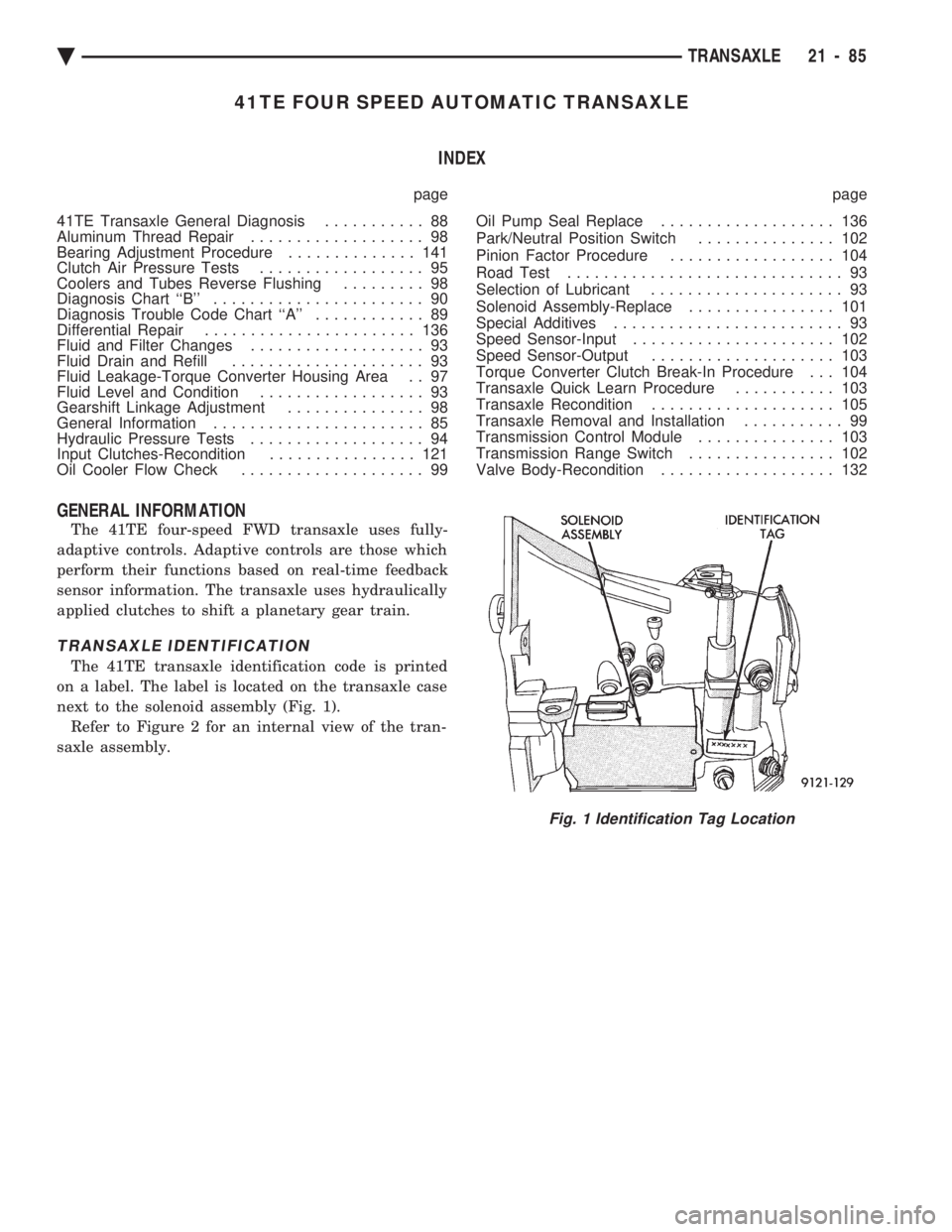
41TE FOUR SPEED AUTOMATIC TRANSAXLE INDEX
page page
41TE Transaxle General Diagnosis ........... 88
Aluminum Thread Repair ................... 98
Bearing Adjustment Procedure .............. 141
Clutch Air Pressure Tests .................. 95
Coolers and Tubes Reverse Flushing ......... 98
Diagnosis Chart ``B'' ....................... 90
Diagnosis Trouble Code Chart ``A'' ............ 89
Differential Repair ....................... 136
Fluid and Filter Changes ................... 93
Fluid Drain and Refill ..................... 93
Fluid Leakage-Torque Converter Housing Area . . 97
Fluid Level and Condition .................. 93
Gearshift Linkage Adjustment ............... 98
General Information ....................... 85
Hydraulic Pressure Tests ................... 94
Input Clutches-Recondition ................ 121
Oil Cooler Flow Check .................... 99 Oil Pump Seal Replace
................... 136
Park/Neutral Position Switch ............... 102
Pinion Factor Procedure .................. 104
Road Test .............................. 93
Selection of Lubricant ..................... 93
Solenoid Assembly-Replace ................ 101
Special Additives ......................... 93
Speed Sensor-Input ...................... 102
Speed Sensor-Output .................... 103
Torque Converter Clutch Break-In Procedure . . . 104
Transaxle Quick Learn Procedure ........... 103
Transaxle Recondition .................... 105
Transaxle Removal and Installation ........... 99
Transmission Control Module ............... 103
Transmission Range Switch ................ 102
Valve Body-Recondition ................... 132
GENERAL INFORMATION
The 41TE four-speed FWD transaxle uses fully-
adaptive controls. Adaptive controls are those which
perform their functions based on real-time feedback
sensor information. The transaxle uses hydraulically
applied clutches to shift a planetary gear train.
TRANSAXLE IDENTIFICATION
The 41TE transaxle identification code is printed
on a label. The label is located on the transaxle case
next to the solenoid assembly (Fig. 1). Refer to Figure 2 for an internal view of the tran-
saxle assembly.
Fig. 1 Identification Tag Location
Ä TRANSAXLE 21 - 85
Page 2046 of 2438
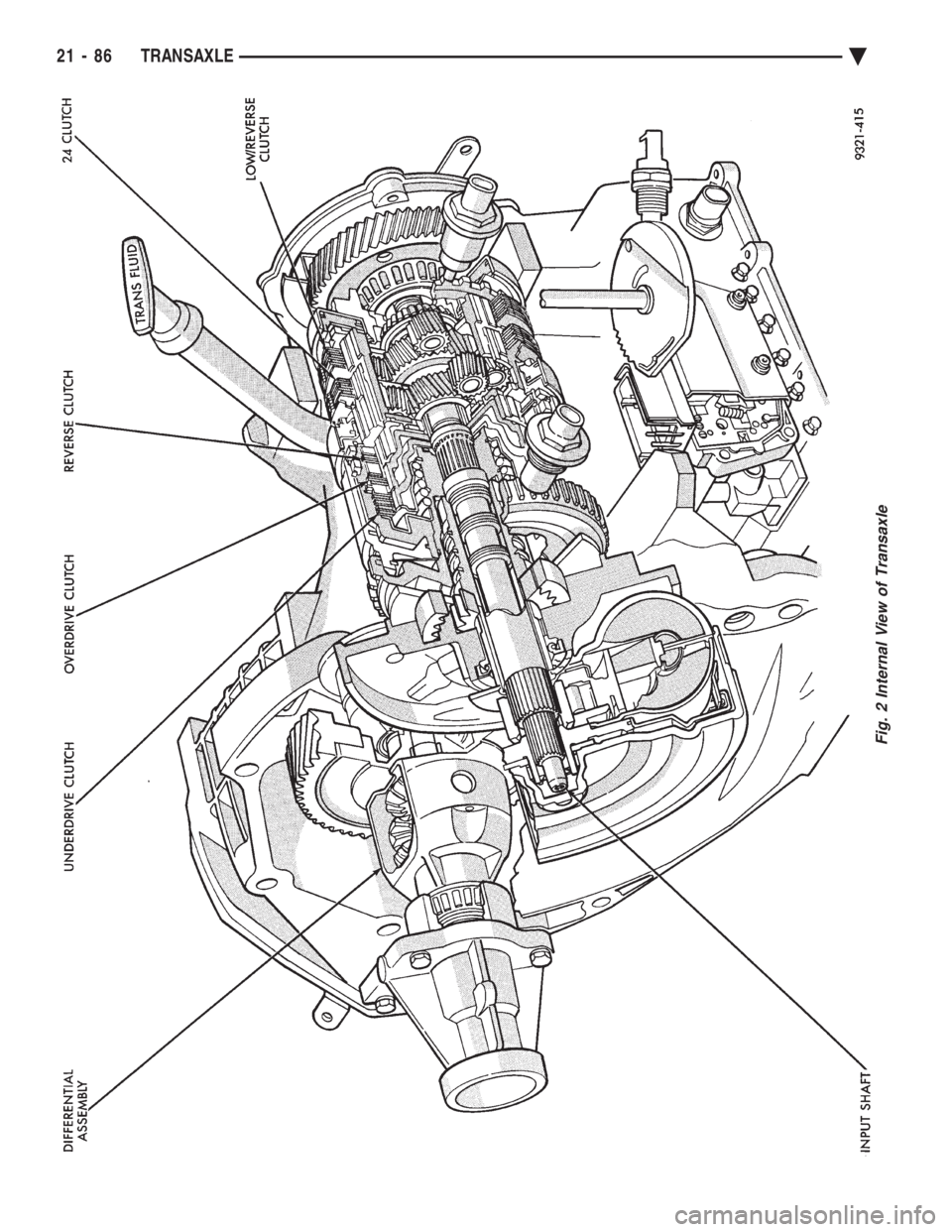
Fig. 2 Internal View of Transaxle
21 - 86 TRANSAXLE Ä
Page 2047 of 2438
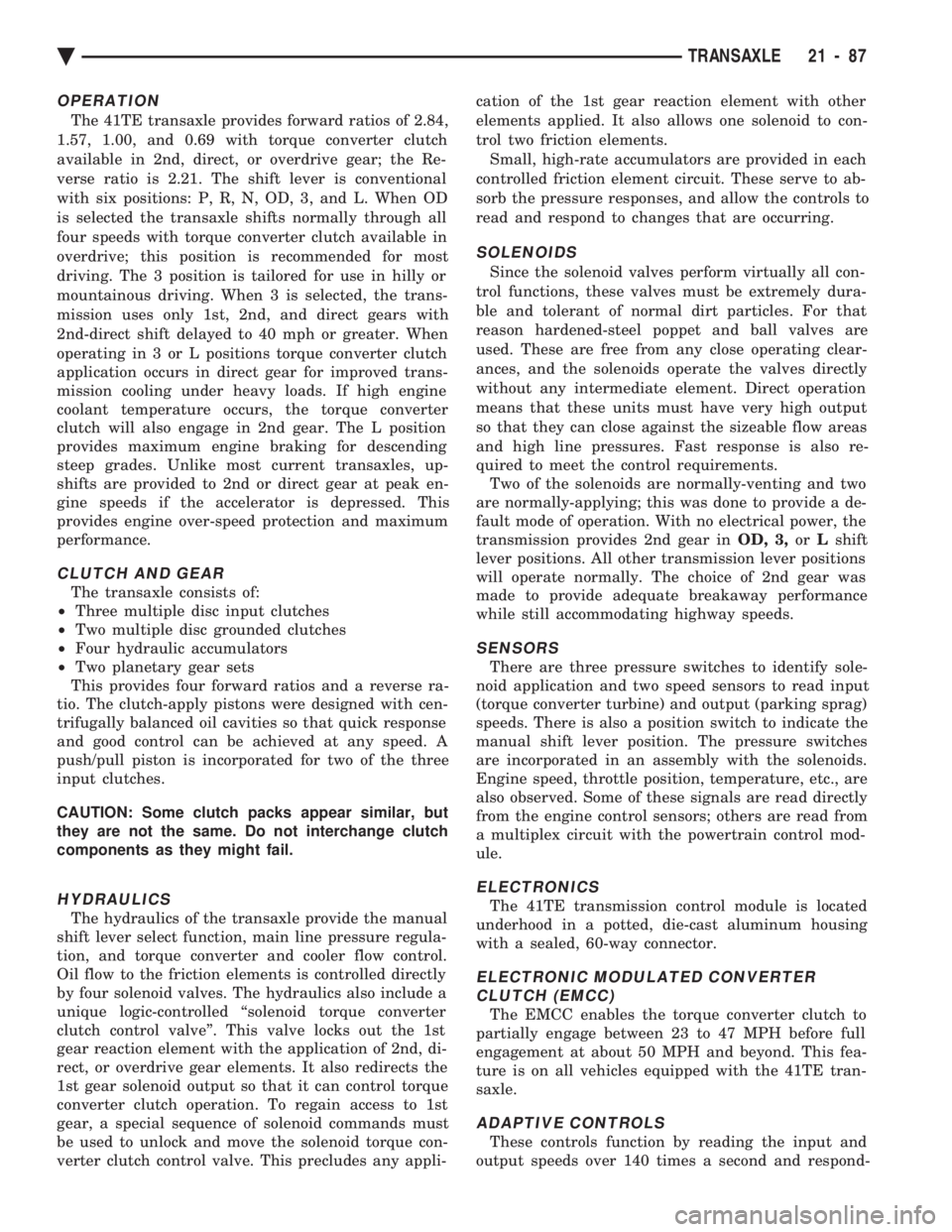
OPERATION
The 41TE transaxle provides forward ratios of 2.84,
1.57, 1.00, and 0.69 with torque converter clutch
available in 2nd, direct, or overdrive gear; the Re-
verse ratio is 2.21. The shift lever is conventional
with six positions: P, R, N, OD, 3, and L. When OD
is selected the transaxle shifts normally through all
four speeds with torque converter clutch available in
overdrive; this position is recommended for most
driving. The 3 position is tailored for use in hilly or
mountainous driving. When 3 is selected, the trans-
mission uses only 1st, 2nd, and direct gears with
2nd-direct shift delayed to 40 mph or greater. When
operating in 3 or L positions torque converter clutch
application occurs in direct gear for improved trans-
mission cooling under heavy loads. If high engine
coolant temperature occurs, the torque converter
clutch will also engage in 2nd gear. The L position
provides maximum engine braking for descending
steep grades. Unlike most current transaxles, up-
shifts are provided to 2nd or direct gear at peak en-
gine speeds if the accelerator is depressed. This
provides engine over-speed protection and maximum
performance.
CLUTCH AND GEAR
The transaxle consists of:
² Three multiple disc input clutches
² Two multiple disc grounded clutches
² Four hydraulic accumulators
² Two planetary gear sets
This provides four forward ratios and a reverse ra-
tio. The clutch-apply pistons were designed with cen-
trifugally balanced oil cavities so that quick response
and good control can be achieved at any speed. A
push/pull piston is incorporated for two of the three
input clutches.
CAUTION: Some clutch packs appear similar, but
they are not the same. Do not interchange clutch
components as they might fail.
HYDRAULICS
The hydraulics of the transaxle provide the manual
shift lever select function, main line pressure regula-
tion, and torque converter and cooler flow control.
Oil flow to the friction elements is controlled directly
by four solenoid valves. The hydraulics also include a
unique logic-controlled ``solenoid torque converter
clutch control valve''. This valve locks out the 1st
gear reaction element with the application of 2nd, di-
rect, or overdrive gear elements. It also redirects the
1st gear solenoid output so that it can control torque
converter clutch operation. To regain access to 1st
gear, a special sequence of solenoid commands must
be used to unlock and move the solenoid torque con-
verter clutch control valve. This precludes any appli- cation of the 1st gear reaction element with other
elements applied. It also allows one solenoid to con-
trol two friction elements.
Small, high-rate accumulators are provided in each
controlled friction element circuit. These serve to ab-
sorb the pressure responses, and allow the controls to
read and respond to changes that are occurring.
SOLENOIDS
Since the solenoid valves perform virtually all con-
trol functions, these valves must be extremely dura-
ble and tolerant of normal dirt particles. For that
reason hardened-steel poppet and ball valves are
used. These are free from any close operating clear-
ances, and the solenoids operate the valves directly
without any intermediate element. Direct operation
means that these units must have very high output
so that they can close against the sizeable flow areas
and high line pressures. Fast response is also re-
quired to meet the control requirements. Two of the solenoids are normally-venting and two
are normally-applying; this was done to provide a de-
fault mode of operation. With no electrical power, the
transmission provides 2nd gear in OD, 3,orLshift
lever positions. All other transmission lever positions
will operate normally. The choice of 2nd gear was
made to provide adequate breakaway performance
while still accommodating highway speeds.
SENSORS
There are three pressure switches to identify sole-
noid application and two speed sensors to read input
(torque converter turbine) and output (parking sprag)
speeds. There is also a position switch to indicate the
manual shift lever position. The pressure switches
are incorporated in an assembly with the solenoids.
Engine speed, throttle position, temperature, etc., are
also observed. Some of these signals are read directly
from the engine control sensors; others are read from
a multiplex circuit with the powertrain control mod-
ule.
ELECTRONICS
The 41TE transmission control module is located
underhood in a potted, die-cast aluminum housing
with a sealed, 60-way connector.
ELECTRONIC MODULATED CONVERTER CLUTCH (EMCC)
The EMCC enables the torque converter clutch to
partially engage between 23 to 47 MPH before full
engagement at about 50 MPH and beyond. This fea-
ture is on all vehicles equipped with the 41TE tran-
saxle.
ADAPTIVE CONTROLS
These controls function by reading the input and
output speeds over 140 times a second and respond-
Ä TRANSAXLE 21 - 87
Page 2048 of 2438
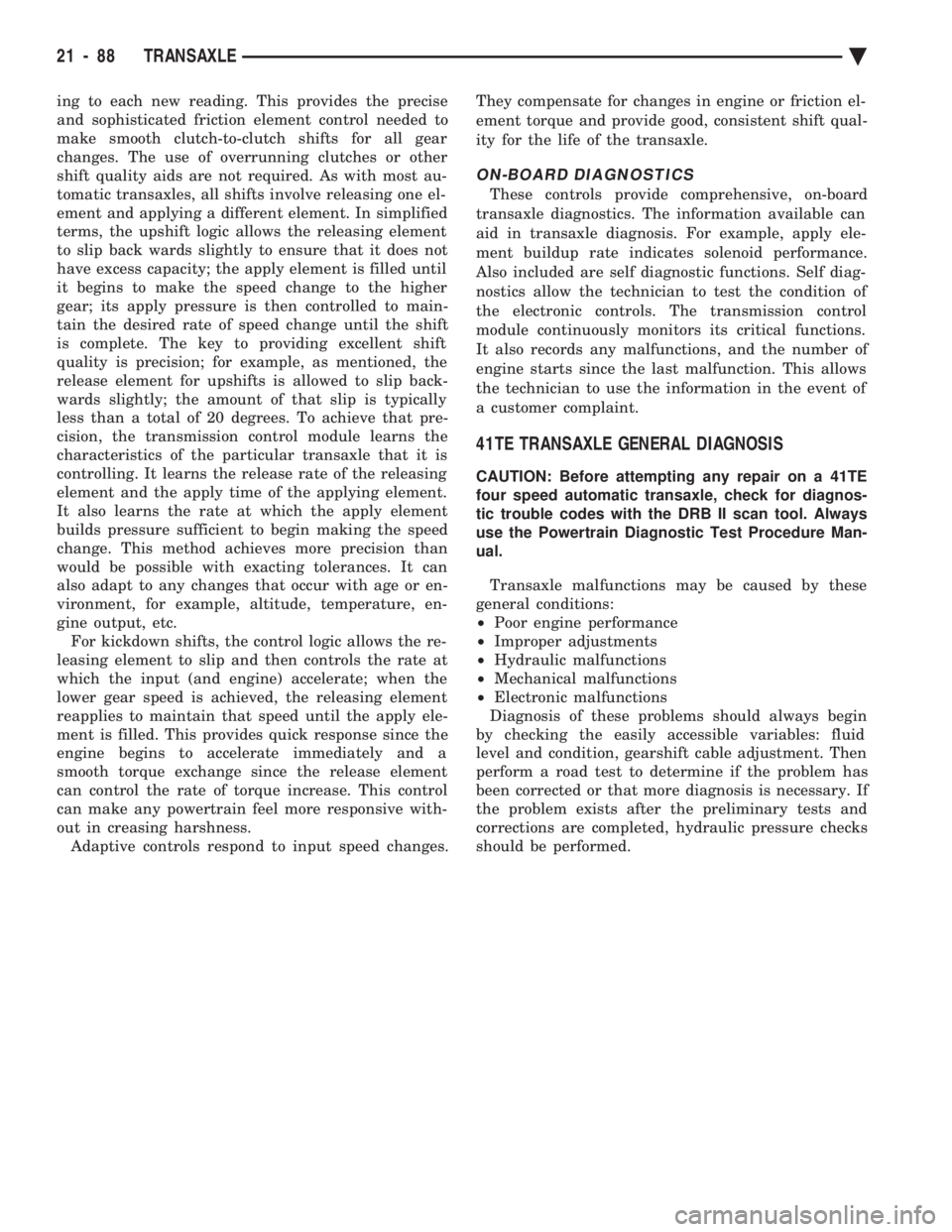
ing to each new reading. This provides the precise
and sophisticated friction element control needed to
make smooth clutch-to-clutch shifts for all gear
changes. The use of overrunning clutches or other
shift quality aids are not required. As with most au-
tomatic transaxles, all shifts involve releasing one el-
ement and applying a different element. In simplified
terms, the upshift logic allows the releasing element
to slip back wards slightly to ensure that it does not
have excess capacity; the apply element is filled until
it begins to make the speed change to the higher
gear; its apply pressure is then controlled to main-
tain the desired rate of speed change until the shift
is complete. The key to providing excellent shift
quality is precision; for example, as mentioned, the
release element for upshifts is allowed to slip back-
wards slightly; the amount of that slip is typically
less than a total of 20 degrees. To achieve that pre-
cision, the transmission control module learns the
characteristics of the particular transaxle that it is
controlling. It learns the release rate of the releasing
element and the apply time of the applying element.
It also learns the rate at which the apply element
builds pressure sufficient to begin making the speed
change. This method achieves more precision than
would be possible with exacting tolerances. It can
also adapt to any changes that occur with age or en-
vironment, for example, altitude, temperature, en-
gine output, etc. For kickdown shifts, the control logic allows the re-
leasing element to slip and then controls the rate at
which the input (and engine) accelerate; when the
lower gear speed is achieved, the releasing element
reapplies to maintain that speed until the apply ele-
ment is filled. This provides quick response since the
engine begins to accelerate immediately and a
smooth torque exchange since the release element
can control the rate of torque increase. This control
can make any powertrain feel more responsive with-
out in creasing harshness. Adaptive controls respond to input speed changes. They compensate for changes in engine or friction el-
ement torque and provide good, consistent shift qual-
ity for the life of the transaxle.
ON-BOARD DIAGNOSTICS
These controls provide comprehensive, on-board
transaxle diagnostics. The information available can
aid in transaxle diagnosis. For example, apply ele-
ment buildup rate indicates solenoid performance.
Also included are self diagnostic functions. Self diag-
nostics allow the technician to test the condition of
the electronic controls. The transmission control
module continuously monitors its critical functions.
It also records any malfunctions, and the number of
engine starts since the last malfunction. This allows
the technician to use the information in the event of
a customer complaint.
41TE TRANSAXLE GENERAL DIAGNOSIS
CAUTION: Before attempting any repair on a 41TE
four speed automatic transaxle, check for diagnos-
tic trouble codes with the DRB II scan tool. Always
use the Powertrain Diagnostic Test Procedure Man-
ual.
Transaxle malfunctions may be caused by these
general conditions:
² Poor engine performance
² Improper adjustments
² Hydraulic malfunctions
² Mechanical malfunctions
² Electronic malfunctions
Diagnosis of these problems should always begin
by checking the easily accessible variables: fluid
level and condition, gearshift cable adjustment. Then
perform a road test to determine if the problem has
been corrected or that more diagnosis is necessary. If
the problem exists after the preliminary tests and
corrections are completed, hydraulic pressure checks
should be performed.
21 - 88 TRANSAXLE Ä
Page 2049 of 2438
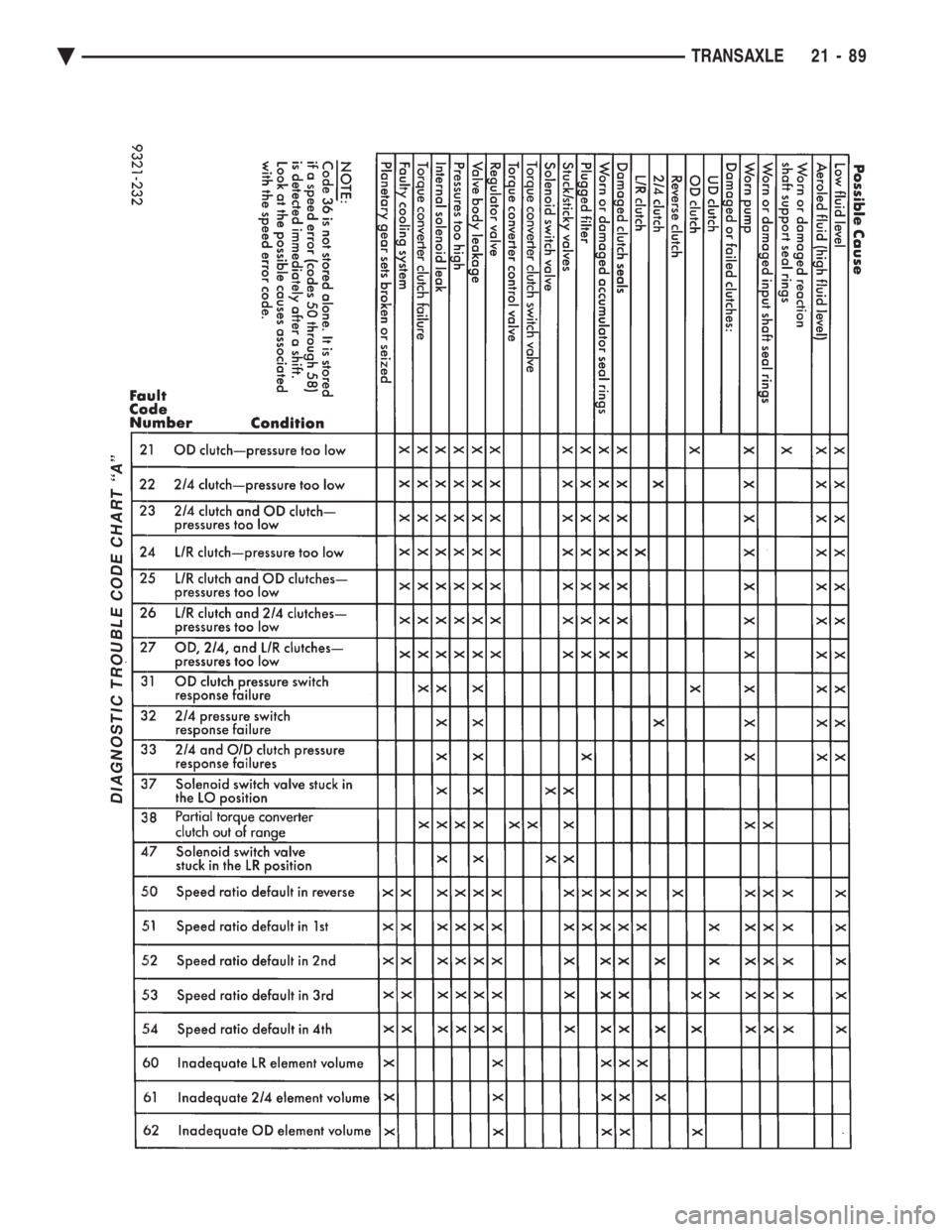
DIAGNOSTIC TROUBLE CODE CHART ``A''
Ä TRANSAXLE 21 - 89
Page 2050 of 2438
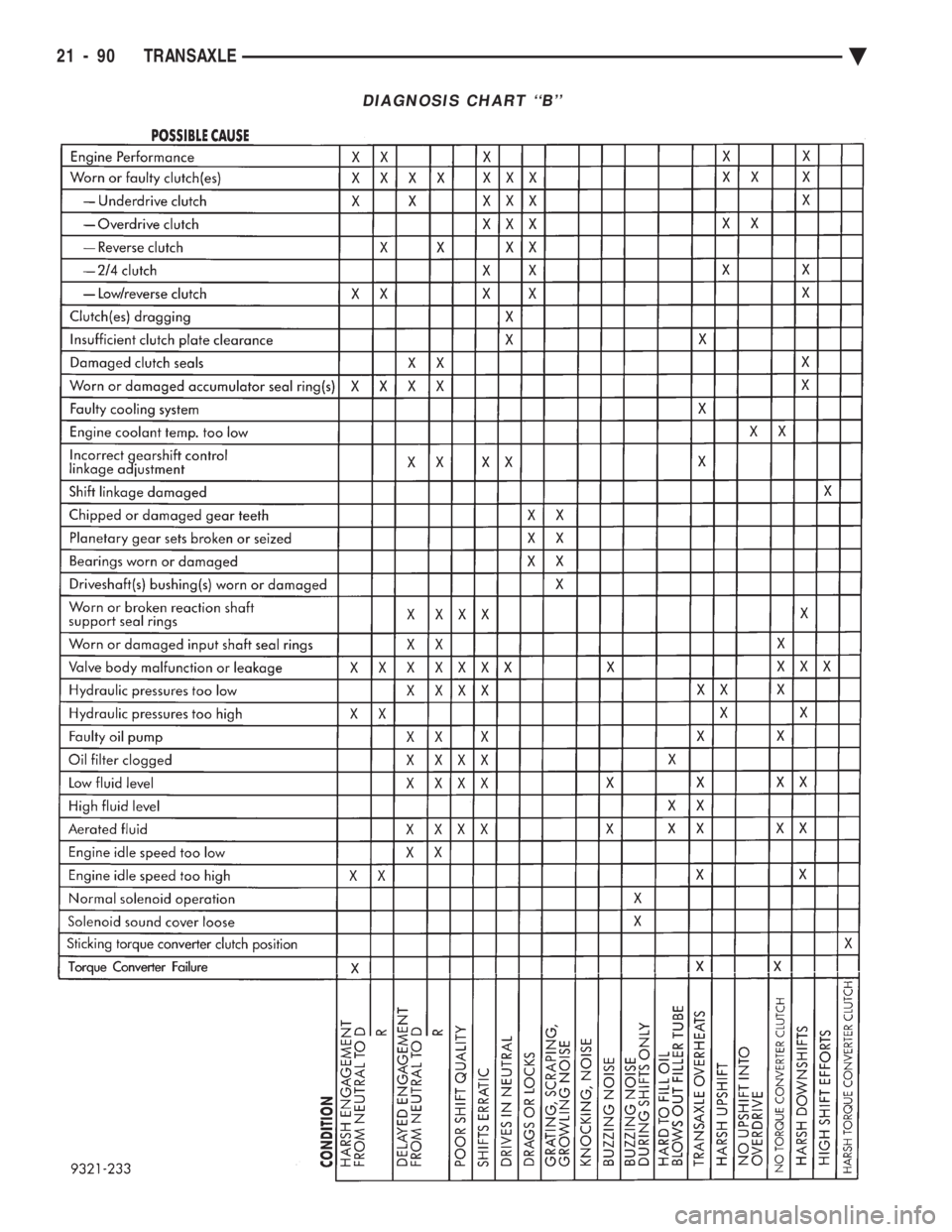
DIAGNOSIS CHART ``B''
21 - 90 TRANSAXLE Ä