CHRYSLER VOYAGER 1996 Owner's Guide
Manufacturer: CHRYSLER, Model Year: 1996, Model line: VOYAGER, Model: CHRYSLER VOYAGER 1996Pages: 1938, PDF Size: 55.84 MB
Page 31 of 1938
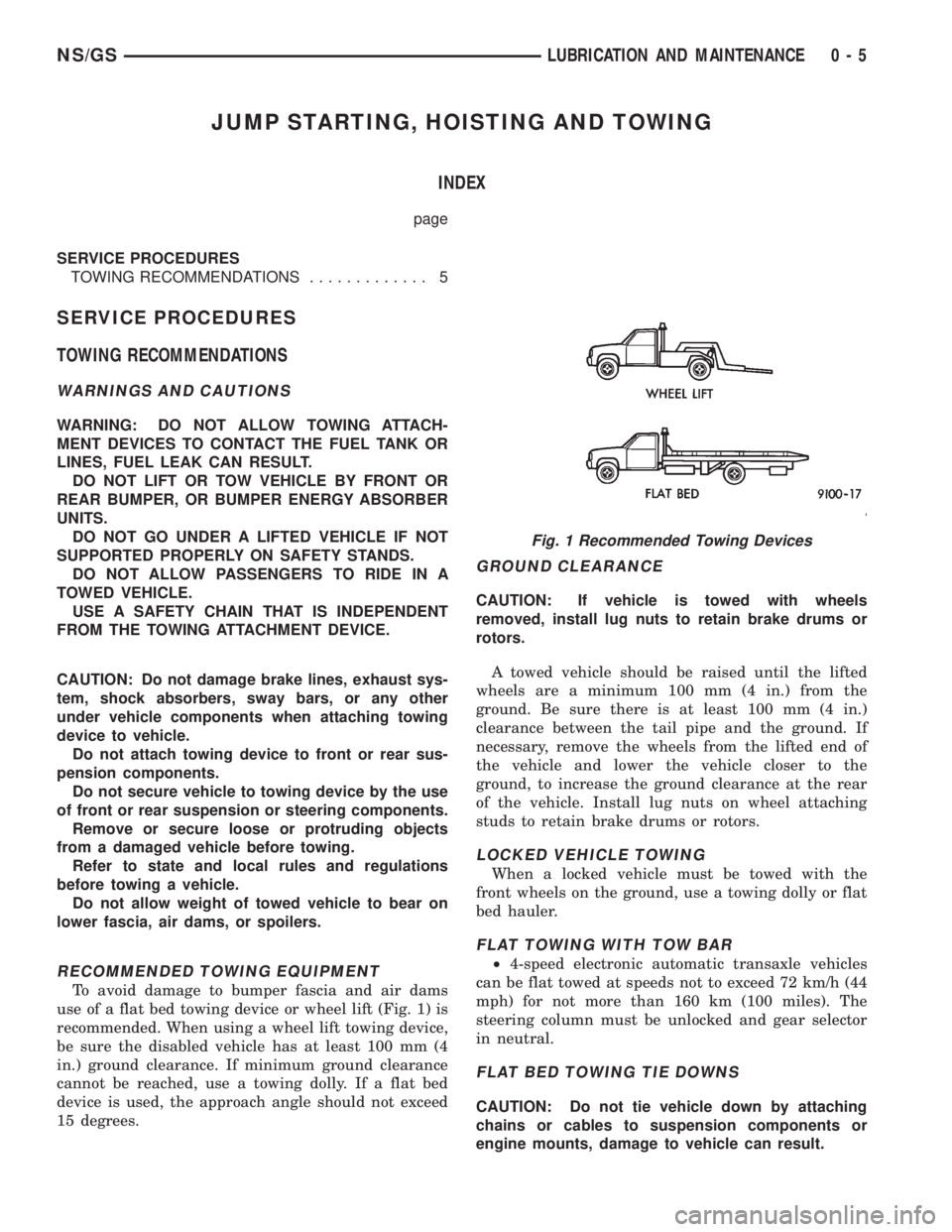
JUMP STARTING, HOISTING AND TOWING
INDEX
page
SERVICE PROCEDURES
TOWING RECOMMENDATIONS............. 5
SERVICE PROCEDURES
TOWING RECOMMENDATIONS
WARNINGS AND CAUTIONS
WARNING: DO NOT ALLOW TOWING ATTACH-
MENT DEVICES TO CONTACT THE FUEL TANK OR
LINES, FUEL LEAK CAN RESULT.
DO NOT LIFT OR TOW VEHICLE BY FRONT OR
REAR BUMPER, OR BUMPER ENERGY ABSORBER
UNITS.
DO NOT GO UNDER A LIFTED VEHICLE IF NOT
SUPPORTED PROPERLY ON SAFETY STANDS.
DO NOT ALLOW PASSENGERS TO RIDE IN A
TOWED VEHICLE.
USE A SAFETY CHAIN THAT IS INDEPENDENT
FROM THE TOWING ATTACHMENT DEVICE.
CAUTION: Do not damage brake lines, exhaust sys-
tem, shock absorbers, sway bars, or any other
under vehicle components when attaching towing
device to vehicle.
Do not attach towing device to front or rear sus-
pension components.
Do not secure vehicle to towing device by the use
of front or rear suspension or steering components.
Remove or secure loose or protruding objects
from a damaged vehicle before towing.
Refer to state and local rules and regulations
before towing a vehicle.
Do not allow weight of towed vehicle to bear on
lower fascia, air dams, or spoilers.
RECOMMENDED TOWING EQUIPMENT
To avoid damage to bumper fascia and air dams
use of a flat bed towing device or wheel lift (Fig. 1) is
recommended. When using a wheel lift towing device,
be sure the disabled vehicle has at least 100 mm (4
in.) ground clearance. If minimum ground clearance
cannot be reached, use a towing dolly. If a flat bed
device is used, the approach angle should not exceed
15 degrees.
GROUND CLEARANCE
CAUTION: If vehicle is towed with wheels
removed, install lug nuts to retain brake drums or
rotors.
A towed vehicle should be raised until the lifted
wheels are a minimum 100 mm (4 in.) from the
ground. Be sure there is at least 100 mm (4 in.)
clearance between the tail pipe and the ground. If
necessary, remove the wheels from the lifted end of
the vehicle and lower the vehicle closer to the
ground, to increase the ground clearance at the rear
of the vehicle. Install lug nuts on wheel attaching
studs to retain brake drums or rotors.
LOCKED VEHICLE TOWING
When a locked vehicle must be towed with the
front wheels on the ground, use a towing dolly or flat
bed hauler.
FLAT TOWING WITH TOW BAR
²4-speed electronic automatic transaxle vehicles
can be flat towed at speeds not to exceed 72 km/h (44
mph) for not more than 160 km (100 miles). The
steering column must be unlocked and gear selector
in neutral.
FLAT BED TOWING TIE DOWNS
CAUTION: Do not tie vehicle down by attaching
chains or cables to suspension components or
engine mounts, damage to vehicle can result.
Fig. 1 Recommended Towing Devices
NS/GSLUBRICATION AND MAINTENANCE 0 - 5
Page 32 of 1938
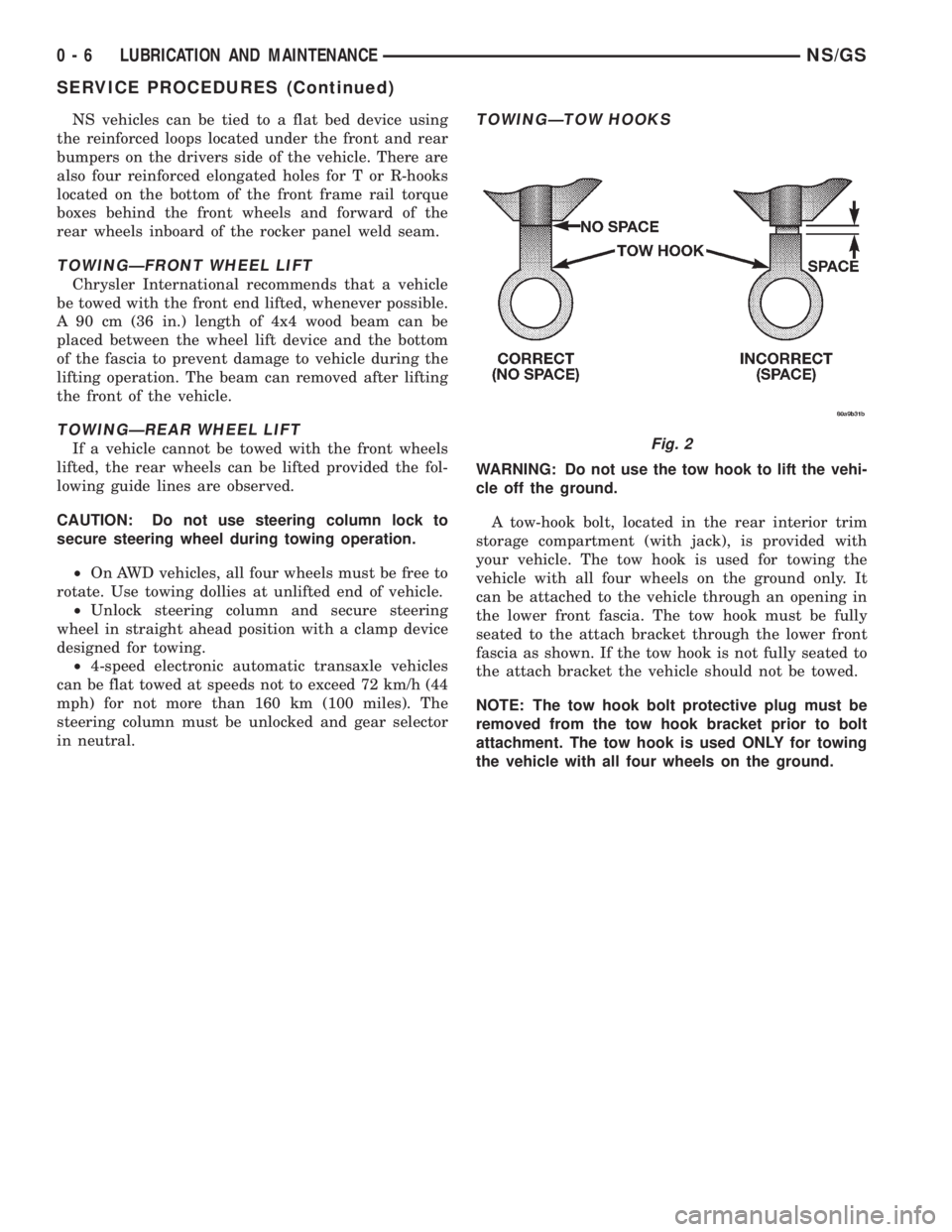
NS vehicles can be tied to a flat bed device using
the reinforced loops located under the front and rear
bumpers on the drivers side of the vehicle. There are
also four reinforced elongated holes for T or R-hooks
located on the bottom of the front frame rail torque
boxes behind the front wheels and forward of the
rear wheels inboard of the rocker panel weld seam.
TOWINGÐFRONT WHEEL LIFT
Chrysler International recommends that a vehicle
be towed with the front end lifted, whenever possible.
A 90 cm (36 in.) length of 4x4 wood beam can be
placed between the wheel lift device and the bottom
of the fascia to prevent damage to vehicle during the
lifting operation. The beam can removed after lifting
the front of the vehicle.
TOWINGÐREAR WHEEL LIFT
If a vehicle cannot be towed with the front wheels
lifted, the rear wheels can be lifted provided the fol-
lowing guide lines are observed.
CAUTION: Do not use steering column lock to
secure steering wheel during towing operation.
²On AWD vehicles, all four wheels must be free to
rotate. Use towing dollies at unlifted end of vehicle.
²Unlock steering column and secure steering
wheel in straight ahead position with a clamp device
designed for towing.
²4-speed electronic automatic transaxle vehicles
can be flat towed at speeds not to exceed 72 km/h (44
mph) for not more than 160 km (100 miles). The
steering column must be unlocked and gear selector
in neutral.
TOWINGÐTOW HOOKS
WARNING: Do not use the tow hook to lift the vehi-
cle off the ground.
A tow-hook bolt, located in the rear interior trim
storage compartment (with jack), is provided with
your vehicle. The tow hook is used for towing the
vehicle with all four wheels on the ground only. It
can be attached to the vehicle through an opening in
the lower front fascia. The tow hook must be fully
seated to the attach bracket through the lower front
fascia as shown. If the tow hook is not fully seated to
the attach bracket the vehicle should not be towed.
NOTE: The tow hook bolt protective plug must be
removed from the tow hook bracket prior to bolt
attachment. The tow hook is used ONLY for towing
the vehicle with all four wheels on the ground.
Fig. 2
0 - 6 LUBRICATION AND MAINTENANCENS/GS
SERVICE PROCEDURES (Continued)
Page 33 of 1938
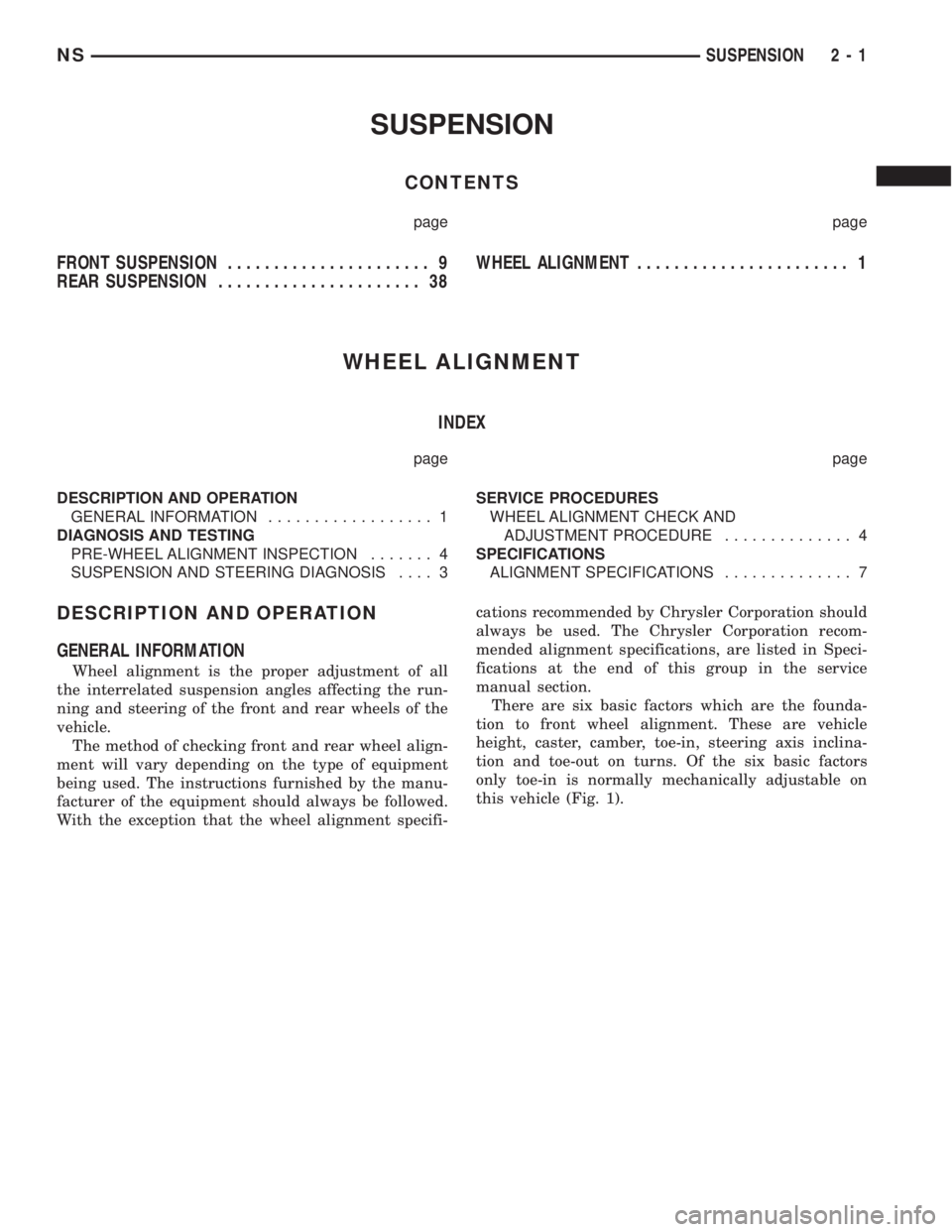
SUSPENSION
CONTENTS
page page
FRONT SUSPENSION...................... 9
REAR SUSPENSION...................... 38WHEEL ALIGNMENT....................... 1
WHEEL ALIGNMENT
INDEX
page page
DESCRIPTION AND OPERATION
GENERAL INFORMATION.................. 1
DIAGNOSIS AND TESTING
PRE-WHEEL ALIGNMENT INSPECTION....... 4
SUSPENSION AND STEERING DIAGNOSIS.... 3SERVICE PROCEDURES
WHEEL ALIGNMENT CHECK AND
ADJUSTMENT PROCEDURE.............. 4
SPECIFICATIONS
ALIGNMENT SPECIFICATIONS.............. 7
DESCRIPTION AND OPERATION
GENERAL INFORMATION
Wheel alignment is the proper adjustment of all
the interrelated suspension angles affecting the run-
ning and steering of the front and rear wheels of the
vehicle.
The method of checking front and rear wheel align-
ment will vary depending on the type of equipment
being used. The instructions furnished by the manu-
facturer of the equipment should always be followed.
With the exception that the wheel alignment specifi-cations recommended by Chrysler Corporation should
always be used. The Chrysler Corporation recom-
mended alignment specifications, are listed in Speci-
fications at the end of this group in the service
manual section.
There are six basic factors which are the founda-
tion to front wheel alignment. These are vehicle
height, caster, camber, toe-in, steering axis inclina-
tion and toe-out on turns. Of the six basic factors
only toe-in is normally mechanically adjustable on
this vehicle (Fig. 1).
NSSUSPENSION 2 - 1
Page 34 of 1938
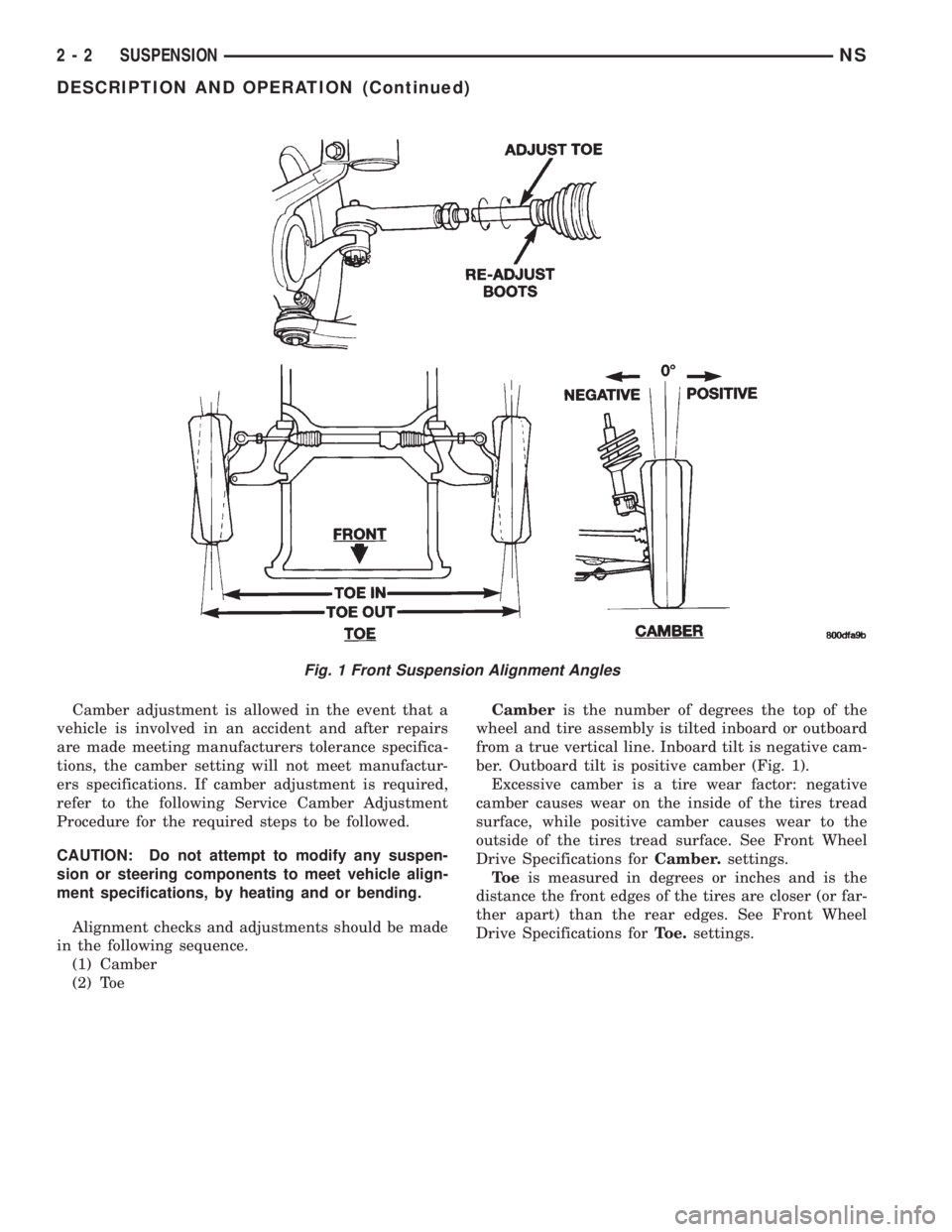
Camber adjustment is allowed in the event that a
vehicle is involved in an accident and after repairs
are made meeting manufacturers tolerance specifica-
tions, the camber setting will not meet manufactur-
ers specifications. If camber adjustment is required,
refer to the following Service Camber Adjustment
Procedure for the required steps to be followed.
CAUTION: Do not attempt to modify any suspen-
sion or steering components to meet vehicle align-
ment specifications, by heating and or bending.
Alignment checks and adjustments should be made
in the following sequence.
(1) Camber
(2) ToeCamberis the number of degrees the top of the
wheel and tire assembly is tilted inboard or outboard
from a true vertical line. Inboard tilt is negative cam-
ber. Outboard tilt is positive camber (Fig. 1).
Excessive camber is a tire wear factor: negative
camber causes wear on the inside of the tires tread
surface, while positive camber causes wear to the
outside of the tires tread surface. See Front Wheel
Drive Specifications forCamber.settings.
To eis measured in degrees or inches and is the
distance the front edges of the tires are closer (or far-
ther apart) than the rear edges. See Front Wheel
Drive Specifications forToe.settings.
Fig. 1 Front Suspension Alignment Angles
2 - 2 SUSPENSIONNS
DESCRIPTION AND OPERATION (Continued)
Page 35 of 1938
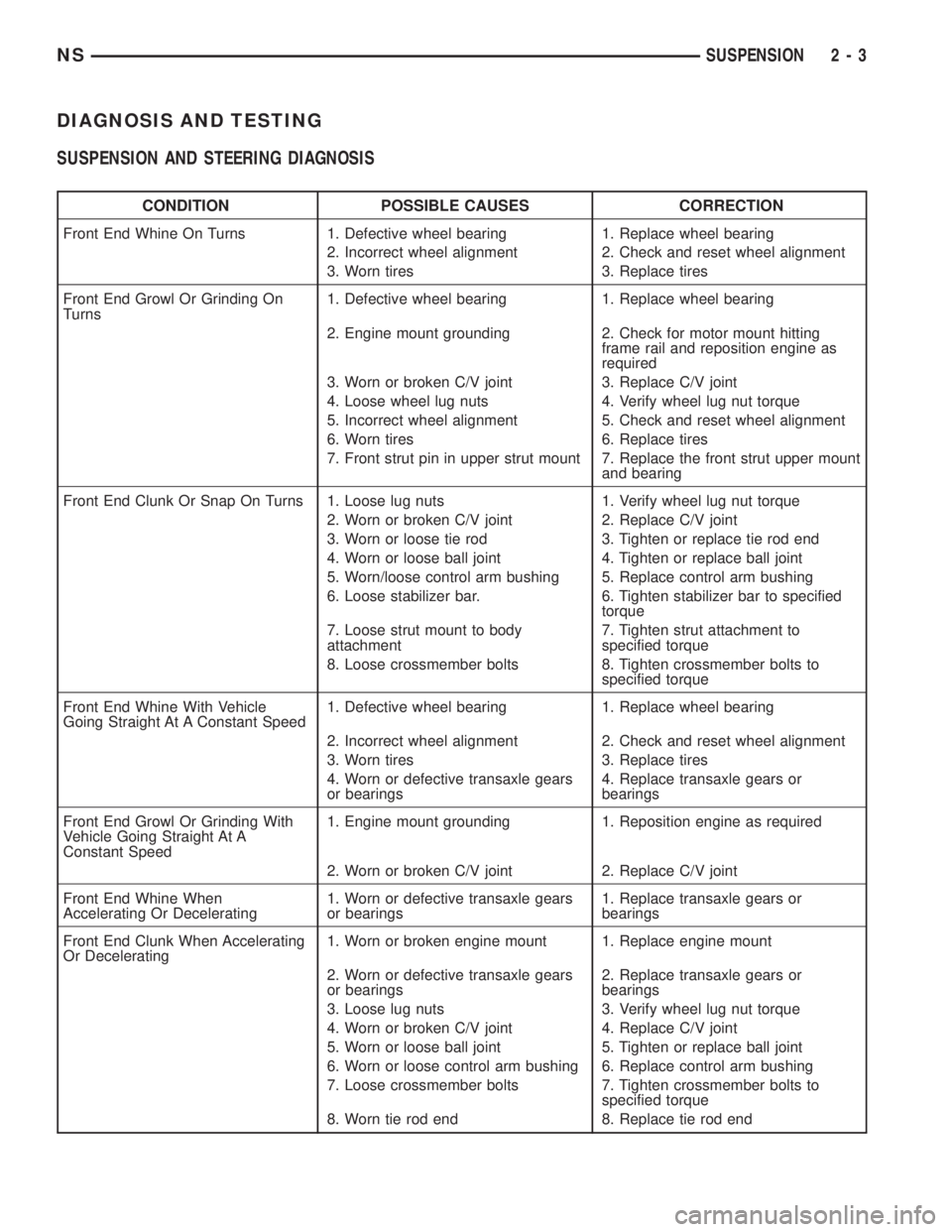
DIAGNOSIS AND TESTING
SUSPENSION AND STEERING DIAGNOSIS
CONDITION POSSIBLE CAUSES CORRECTION
Front End Whine On Turns 1. Defective wheel bearing 1. Replace wheel bearing
2. Incorrect wheel alignment 2. Check and reset wheel alignment
3. Worn tires 3. Replace tires
Front End Growl Or Grinding On
Turns1. Defective wheel bearing 1. Replace wheel bearing
2. Engine mount grounding 2. Check for motor mount hitting
frame rail and reposition engine as
required
3. Worn or broken C/V joint 3. Replace C/V joint
4. Loose wheel lug nuts 4. Verify wheel lug nut torque
5. Incorrect wheel alignment 5. Check and reset wheel alignment
6. Worn tires 6. Replace tires
7. Front strut pin in upper strut mount 7. Replace the front strut upper mount
and bearing
Front End Clunk Or Snap On Turns 1. Loose lug nuts 1. Verify wheel lug nut torque
2. Worn or broken C/V joint 2. Replace C/V joint
3. Worn or loose tie rod 3. Tighten or replace tie rod end
4. Worn or loose ball joint 4. Tighten or replace ball joint
5. Worn/loose control arm bushing 5. Replace control arm bushing
6. Loose stabilizer bar. 6. Tighten stabilizer bar to specified
torque
7. Loose strut mount to body
attachment7. Tighten strut attachment to
specified torque
8. Loose crossmember bolts 8. Tighten crossmember bolts to
specified torque
Front End Whine With Vehicle
Going Straight At A Constant Speed1. Defective wheel bearing 1. Replace wheel bearing
2. Incorrect wheel alignment 2. Check and reset wheel alignment
3. Worn tires 3. Replace tires
4. Worn or defective transaxle gears
or bearings4. Replace transaxle gears or
bearings
Front End Growl Or Grinding With
Vehicle Going Straight At A
Constant Speed1. Engine mount grounding 1. Reposition engine as required
2. Worn or broken C/V joint 2. Replace C/V joint
Front End Whine When
Accelerating Or Decelerating1. Worn or defective transaxle gears
or bearings1. Replace transaxle gears or
bearings
Front End Clunk When Accelerating
Or Decelerating1. Worn or broken engine mount 1. Replace engine mount
2. Worn or defective transaxle gears
or bearings2. Replace transaxle gears or
bearings
3. Loose lug nuts 3. Verify wheel lug nut torque
4. Worn or broken C/V joint 4. Replace C/V joint
5. Worn or loose ball joint 5. Tighten or replace ball joint
6. Worn or loose control arm bushing 6. Replace control arm bushing
7. Loose crossmember bolts 7. Tighten crossmember bolts to
specified torque
8. Worn tie rod end 8. Replace tie rod end
NSSUSPENSION 2 - 3
Page 36 of 1938

CONDITION POSSIBLE CAUSES CORRECTION
Road Wander 1. Incorrect tire pressure 1. Inflate tires to recommended
pressure
2. Incorrect front or rear wheel toe 2. Check and reset wheel toe
3. Worn wheel bearings 3. Replace wheel bearing
4. Worn control arm bushings 4. Replace control arm bushing
5. Excessive friction in steering gear 5. Replace steering gear
6. Excessive friction in steering shaft
coupling6. Replace steering coupler
7. Excessive friction in strut upper
bearing7. Replace strut bearing
Lateral Pull 1. Unequal tire pressure 1. Inflate all tires to recommended
pressure
2. Radial tire lead 2. Perform lead correction procedure
3. Incorrect front wheel camber 3. Check and reset front wheel
camber
4. Power steering gear imbalance 4. Replace power steering gear
5. Wheel braking 5. Correct braking condition causing
lateral pull
Excessive Steering Free Play 1. Incorrect Steering Gear Adjustment 1. Adjust Or Replace Steering Gear
2. Worn or loose tie rod ends 2. Replace or tighten tie rod ends
3. Loose steering gear mounting bolts 3. Tighten steering gear bolts to
specified torque
4. Loose or worn steering shaft
coupler4. Replace steering shaft coupler
Excessive Steering Effort 1. Low tire pressure 1. Inflate all tires to recommended
pressure
2. Lack of lubricant in steering gear 2. Replace steering gear
3. Low power steering fluid level 3. Fill power steering fluid reservoir to
correct level
4. Loose power steering pump drive
belt4. Correctly adjust power steering
pump drive belt
5. Lack of lubricant in ball joints 5. Lubricate or replace ball joints
6. Steering gear malfunction 6. Replace steering gear
7. Lack of lubricant in steering
coupler7. Replace steering coupler
PRE-WHEEL ALIGNMENT INSPECTION
Before any attempt is made to change or correct
the wheel alignment factors. The following part
inspection and the necessary corrections should be
made to those parts which influence the steering of
the vehicle.
(1) Check and inflate all tires to recommended
pressure. All tires should be the same size and in
good condition and have approximately the same
wear. Note the type of tread wear which will aid in
diagnosing, see Wheels and Tires, Group 22.
(2) Check front wheel and tire assembly for radial
runout.
(3) Inspect lower ball joints and all steering link-
age for looseness.
(4) Check for broken or sagged front and rear
springs.(5) Check vehicle ride height to verify it is within
specifications.
(6) AlignmentMUSTonly be checked after the
vehicle has the following areas inspected and or
adjusted. Recommended tire pressures, full tank of
fuel, no passenger or luggage compartment load and
is on a level floor or a properly calibrated alignment
rack.
SERVICE PROCEDURES
WHEEL ALIGNMENT CHECK AND ADJUSTMENT
PROCEDURE
CASTER AND CAMBER
Front suspension Caster and Camber settings on
this vehicle are determined at the time the vehicle is
designed. This is done by determining the precise
2 - 4 SUSPENSIONNS
DIAGNOSIS AND TESTING (Continued)
Page 37 of 1938
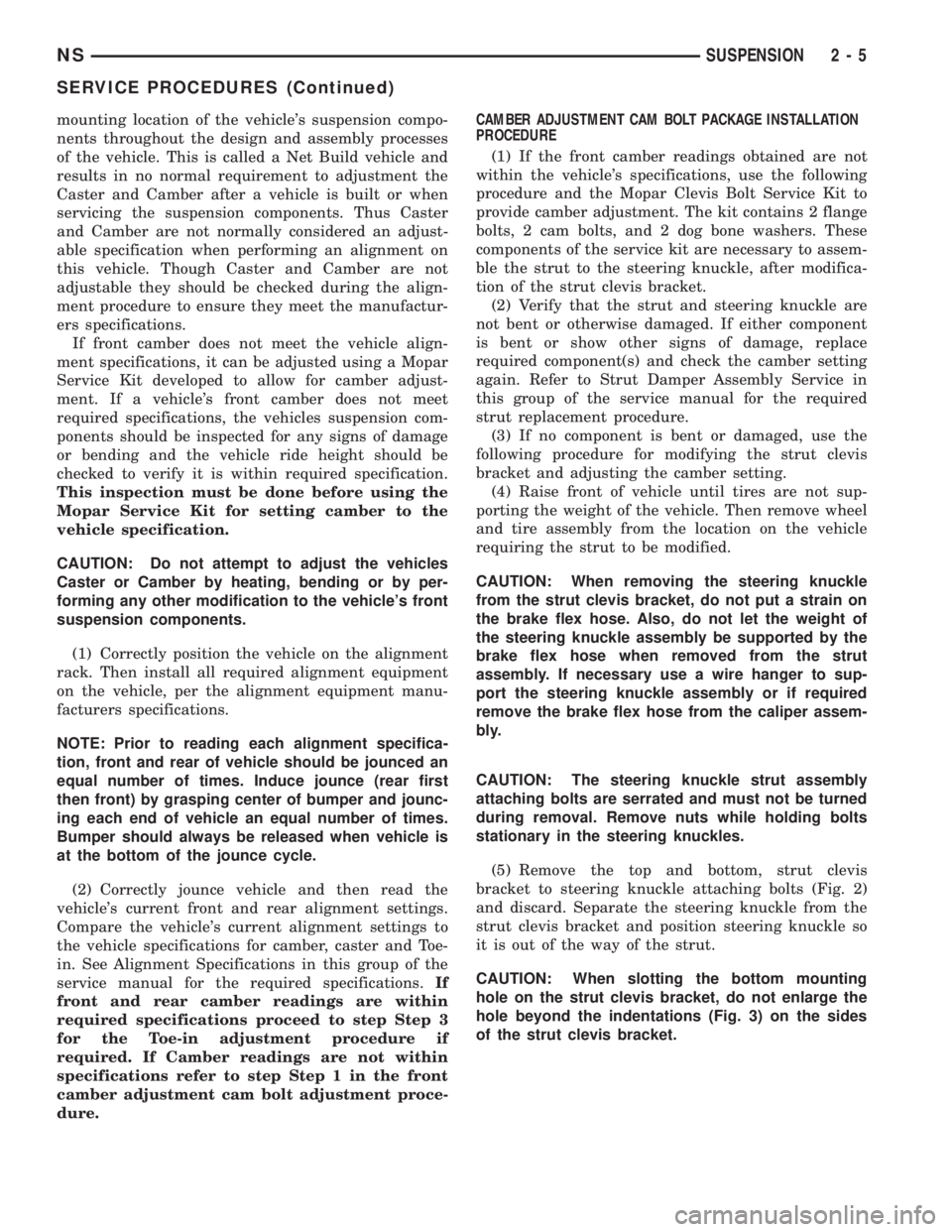
mounting location of the vehicle's suspension compo-
nents throughout the design and assembly processes
of the vehicle. This is called a Net Build vehicle and
results in no normal requirement to adjustment the
Caster and Camber after a vehicle is built or when
servicing the suspension components. Thus Caster
and Camber are not normally considered an adjust-
able specification when performing an alignment on
this vehicle. Though Caster and Camber are not
adjustable they should be checked during the align-
ment procedure to ensure they meet the manufactur-
ers specifications.
If front camber does not meet the vehicle align-
ment specifications, it can be adjusted using a Mopar
Service Kit developed to allow for camber adjust-
ment. If a vehicle's front camber does not meet
required specifications, the vehicles suspension com-
ponents should be inspected for any signs of damage
or bending and the vehicle ride height should be
checked to verify it is within required specification.
This inspection must be done before using the
Mopar Service Kit for setting camber to the
vehicle specification.
CAUTION: Do not attempt to adjust the vehicles
Caster or Camber by heating, bending or by per-
forming any other modification to the vehicle's front
suspension components.
(1) Correctly position the vehicle on the alignment
rack. Then install all required alignment equipment
on the vehicle, per the alignment equipment manu-
facturers specifications.
NOTE: Prior to reading each alignment specifica-
tion, front and rear of vehicle should be jounced an
equal number of times. Induce jounce (rear first
then front) by grasping center of bumper and jounc-
ing each end of vehicle an equal number of times.
Bumper should always be released when vehicle is
at the bottom of the jounce cycle.
(2) Correctly jounce vehicle and then read the
vehicle's current front and rear alignment settings.
Compare the vehicle's current alignment settings to
the vehicle specifications for camber, caster and Toe-
in. See Alignment Specifications in this group of the
service manual for the required specifications.If
front and rear camber readings are within
required specifications proceed to step Step 3
for the Toe-in adjustment procedure if
required. If Camber readings are not within
specifications refer to step Step 1 in the front
camber adjustment cam bolt adjustment proce-
dure.CAMBER ADJUSTMENT CAM BOLT PACKAGE INSTALLATION
PROCEDURE
(1) If the front camber readings obtained are not
within the vehicle's specifications, use the following
procedure and the Mopar Clevis Bolt Service Kit to
provide camber adjustment. The kit contains 2 flange
bolts, 2 cam bolts, and 2 dog bone washers. These
components of the service kit are necessary to assem-
ble the strut to the steering knuckle, after modifica-
tion of the strut clevis bracket.
(2) Verify that the strut and steering knuckle are
not bent or otherwise damaged. If either component
is bent or show other signs of damage, replace
required component(s) and check the camber setting
again. Refer to Strut Damper Assembly Service in
this group of the service manual for the required
strut replacement procedure.
(3) If no component is bent or damaged, use the
following procedure for modifying the strut clevis
bracket and adjusting the camber setting.
(4) Raise front of vehicle until tires are not sup-
porting the weight of the vehicle. Then remove wheel
and tire assembly from the location on the vehicle
requiring the strut to be modified.
CAUTION: When removing the steering knuckle
from the strut clevis bracket, do not put a strain on
the brake flex hose. Also, do not let the weight of
the steering knuckle assembly be supported by the
brake flex hose when removed from the strut
assembly. If necessary use a wire hanger to sup-
port the steering knuckle assembly or if required
remove the brake flex hose from the caliper assem-
bly.
CAUTION: The steering knuckle strut assembly
attaching bolts are serrated and must not be turned
during removal. Remove nuts while holding bolts
stationary in the steering knuckles.
(5) Remove the top and bottom, strut clevis
bracket to steering knuckle attaching bolts (Fig. 2)
and discard. Separate the steering knuckle from the
strut clevis bracket and position steering knuckle so
it is out of the way of the strut.
CAUTION: When slotting the bottom mounting
hole on the strut clevis bracket, do not enlarge the
hole beyond the indentations (Fig. 3) on the sides
of the strut clevis bracket.
NSSUSPENSION 2 - 5
SERVICE PROCEDURES (Continued)
Page 38 of 1938
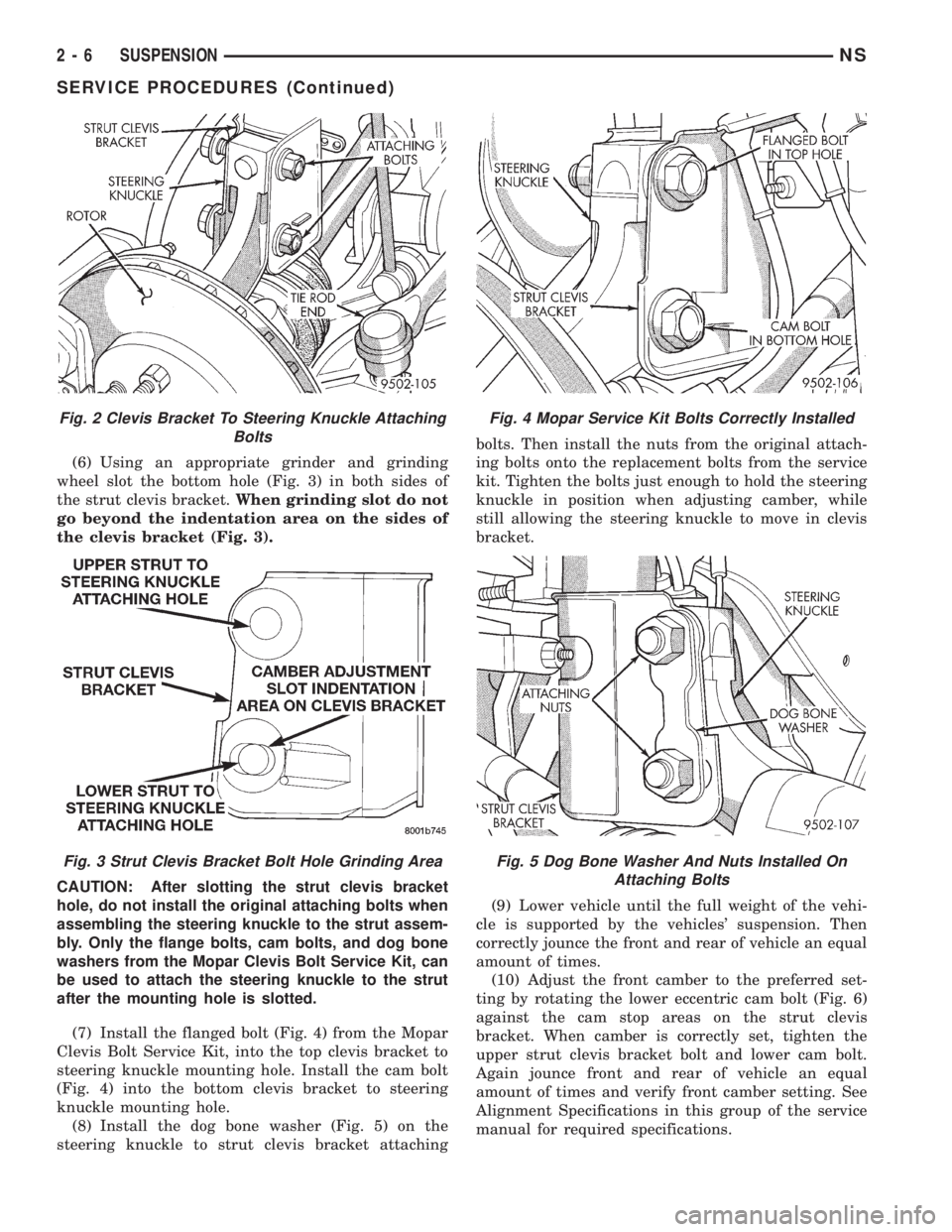
(6) Using an appropriate grinder and grinding
wheel slot the bottom hole (Fig. 3) in both sides of
the strut clevis bracket.When grinding slot do not
go beyond the indentation area on the sides of
the clevis bracket (Fig. 3).
CAUTION: After slotting the strut clevis bracket
hole, do not install the original attaching bolts when
assembling the steering knuckle to the strut assem-
bly. Only the flange bolts, cam bolts, and dog bone
washers from the Mopar Clevis Bolt Service Kit, can
be used to attach the steering knuckle to the strut
after the mounting hole is slotted.
(7) Install the flanged bolt (Fig. 4) from the Mopar
Clevis Bolt Service Kit, into the top clevis bracket to
steering knuckle mounting hole. Install the cam bolt
(Fig. 4) into the bottom clevis bracket to steering
knuckle mounting hole.
(8) Install the dog bone washer (Fig. 5) on the
steering knuckle to strut clevis bracket attachingbolts. Then install the nuts from the original attach-
ing bolts onto the replacement bolts from the service
kit. Tighten the bolts just enough to hold the steering
knuckle in position when adjusting camber, while
still allowing the steering knuckle to move in clevis
bracket.
(9) Lower vehicle until the full weight of the vehi-
cle is supported by the vehicles' suspension. Then
correctly jounce the front and rear of vehicle an equal
amount of times.
(10) Adjust the front camber to the preferred set-
ting by rotating the lower eccentric cam bolt (Fig. 6)
against the cam stop areas on the strut clevis
bracket. When camber is correctly set, tighten the
upper strut clevis bracket bolt and lower cam bolt.
Again jounce front and rear of vehicle an equal
amount of times and verify front camber setting. See
Alignment Specifications in this group of the service
manual for required specifications.
Fig. 2 Clevis Bracket To Steering Knuckle Attaching
Bolts
Fig. 3 Strut Clevis Bracket Bolt Hole Grinding Area
Fig. 4 Mopar Service Kit Bolts Correctly Installed
Fig. 5 Dog Bone Washer And Nuts Installed On
Attaching Bolts
2 - 6 SUSPENSIONNS
SERVICE PROCEDURES (Continued)
Page 39 of 1938
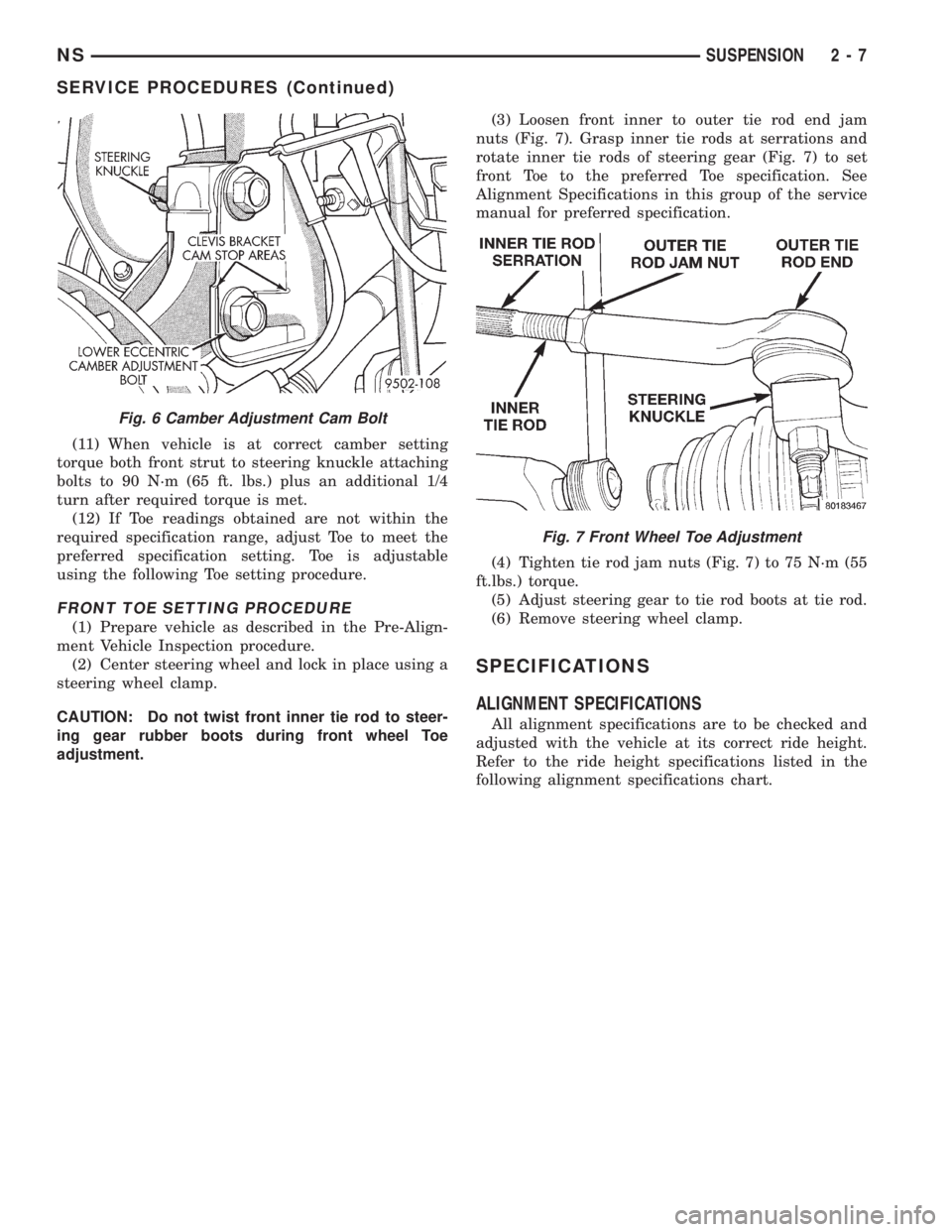
(11) When vehicle is at correct camber setting
torque both front strut to steering knuckle attaching
bolts to 90 N´m (65 ft. lbs.) plus an additional 1/4
turn after required torque is met.
(12) If Toe readings obtained are not within the
required specification range, adjust Toe to meet the
preferred specification setting. Toe is adjustable
using the following Toe setting procedure.
FRONT TOE SETTING PROCEDURE
(1) Prepare vehicle as described in the Pre-Align-
ment Vehicle Inspection procedure.
(2) Center steering wheel and lock in place using a
steering wheel clamp.
CAUTION: Do not twist front inner tie rod to steer-
ing gear rubber boots during front wheel Toe
adjustment.(3) Loosen front inner to outer tie rod end jam
nuts (Fig. 7). Grasp inner tie rods at serrations and
rotate inner tie rods of steering gear (Fig. 7) to set
front Toe to the preferred Toe specification. See
Alignment Specifications in this group of the service
manual for preferred specification.
(4) Tighten tie rod jam nuts (Fig. 7) to 75 N´m (55
ft.lbs.) torque.
(5) Adjust steering gear to tie rod boots at tie rod.
(6) Remove steering wheel clamp.
SPECIFICATIONS
ALIGNMENT SPECIFICATIONS
All alignment specifications are to be checked and
adjusted with the vehicle at its correct ride height.
Refer to the ride height specifications listed in the
following alignment specifications chart.
Fig. 6 Camber Adjustment Cam Bolt
Fig. 7 Front Wheel Toe Adjustment
NSSUSPENSION 2 - 7
SERVICE PROCEDURES (Continued)
Page 40 of 1938
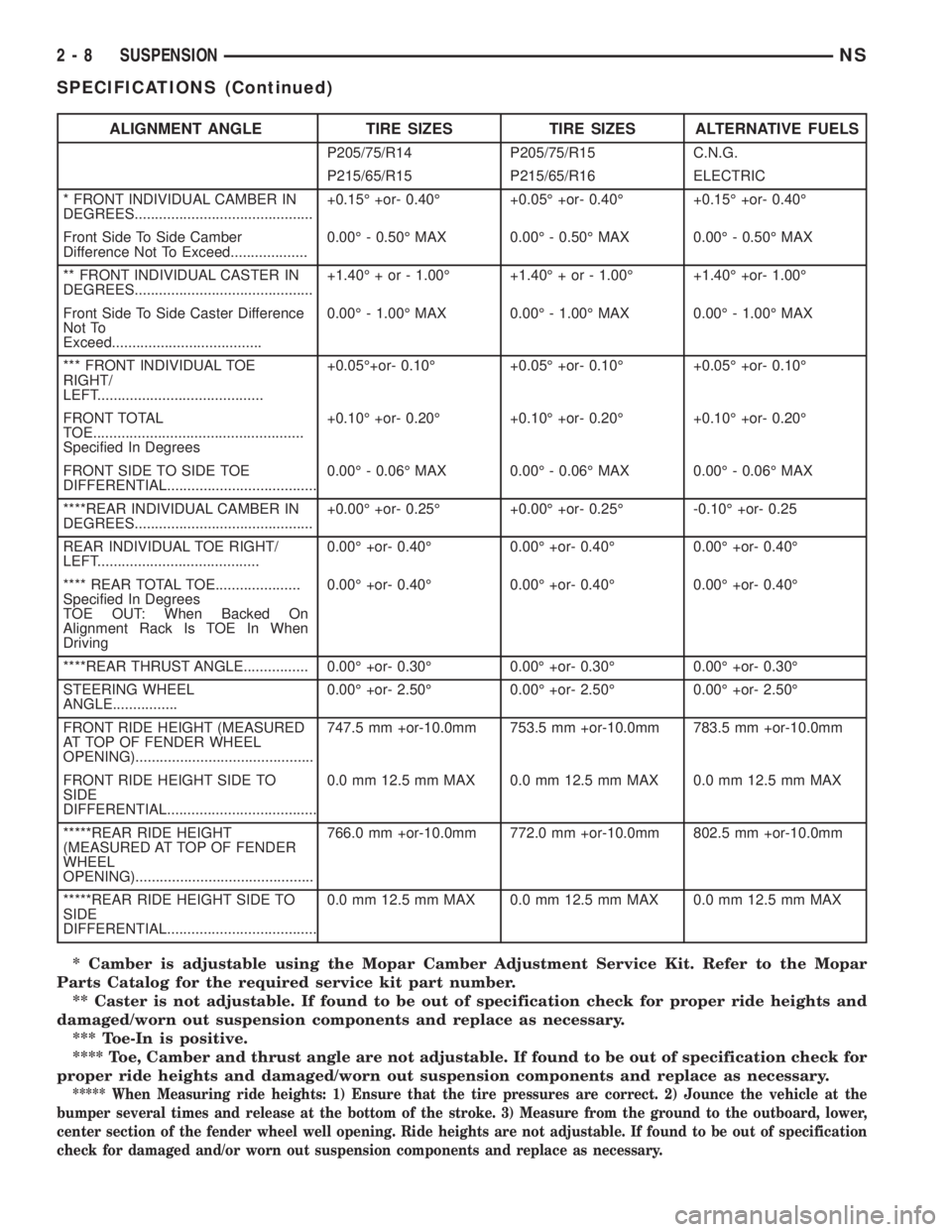
* Camber is adjustable using the Mopar Camber Adjustment Service Kit. Refer to the Mopar
Parts Catalog for the required service kit part number.
** Caster is not adjustable. If found to be out of specification check for proper ride heights and
damaged/worn out suspension components and replace as necessary.
*** Toe-In is positive.
**** Toe, Camber and thrust angle are not adjustable. If found to be out of specification check for
proper ride heights and damaged/worn out suspension components and replace as necessary.
***** When Measuring ride heights: 1) Ensure that the tire pressures are correct. 2) Jounce the vehicle at the
bumper several times and release at the bottom of the stroke. 3) Measure from the ground to the outboard, lower,
center section of the fender wheel well opening. Ride heights are not adjustable. If found to be out of specification
check for damaged and/or worn out suspension components and replace as necessary.
ALIGNMENT ANGLE TIRE SIZES TIRE SIZES ALTERNATIVE FUELS
P205/75/R14 P205/75/R15 C.N.G.
P215/65/R15 P215/65/R16 ELECTRIC
* FRONT INDIVIDUAL CAMBER IN
DEGREES............................................+0.15É +or- 0.40É +0.05É +or- 0.40É +0.15É +or- 0.40É
Front Side To Side Camber
Difference Not To Exceed...................0.00É - 0.50É MAX 0.00É - 0.50É MAX 0.00É - 0.50É MAX
** FRONT INDIVIDUAL CASTER IN
DEGREES............................................+1.40É + or - 1.00É +1.40É + or - 1.00É +1.40É +or- 1.00É
Front Side To Side Caster Difference
Not To
Exceed.....................................0.00É - 1.00É MAX 0.00É - 1.00É MAX 0.00É - 1.00É MAX
*** FRONT INDIVIDUAL TOE
RIGHT/
LEFT.........................................+0.05É+or- 0.10É +0.05É +or- 0.10É +0.05É +or- 0.10É
FRONT TOTAL
TOE....................................................
Specified In Degrees+0.10É +or- 0.20É +0.10É +or- 0.20É +0.10É +or- 0.20É
FRONT SIDE TO SIDE TOE
DIFFERENTIAL.....................................0.00É - 0.06É MAX 0.00É - 0.06É MAX 0.00É - 0.06É MAX
****REAR INDIVIDUAL CAMBER IN
DEGREES............................................+0.00É +or- 0.25É +0.00É +or- 0.25É -0.10É +or- 0.25
REAR INDIVIDUAL TOE RIGHT/
LEFT........................................0.00É +or- 0.40É 0.00É +or- 0.40É 0.00É +or- 0.40É
**** REAR TOTAL TOE.....................
Specified In Degrees
TOE OUT: When Backed On
Alignment Rack Is TOE In When
Driving0.00É +or- 0.40É 0.00É +or- 0.40É 0.00É +or- 0.40É
****REAR THRUST ANGLE................ 0.00É +or- 0.30É 0.00É +or- 0.30É 0.00É +or- 0.30É
STEERING WHEEL
ANGLE................0.00É +or- 2.50É 0.00É +or- 2.50É 0.00É +or- 2.50É
FRONT RIDE HEIGHT (MEASURED
AT TOP OF FENDER WHEEL
OPENING)............................................747.5 mm +or-10.0mm 753.5 mm +or-10.0mm 783.5 mm +or-10.0mm
FRONT RIDE HEIGHT SIDE TO
SIDE
DIFFERENTIAL.....................................0.0 mm 12.5 mm MAX 0.0 mm 12.5 mm MAX 0.0 mm 12.5 mm MAX
*****REAR RIDE HEIGHT
(MEASURED AT TOP OF FENDER
WHEEL
OPENING)............................................766.0 mm +or-10.0mm 772.0 mm +or-10.0mm 802.5 mm +or-10.0mm
*****REAR RIDE HEIGHT SIDE TO
SIDE
DIFFERENTIAL.....................................0.0 mm 12.5 mm MAX 0.0 mm 12.5 mm MAX 0.0 mm 12.5 mm MAX
2 - 8 SUSPENSIONNS
SPECIFICATIONS (Continued)