DATSUN 210 1979 User Guide
Manufacturer: DATSUN, Model Year: 1979, Model line: 210, Model: DATSUN 210 1979Pages: 548, PDF Size: 28.66 MB
Page 11 of 548
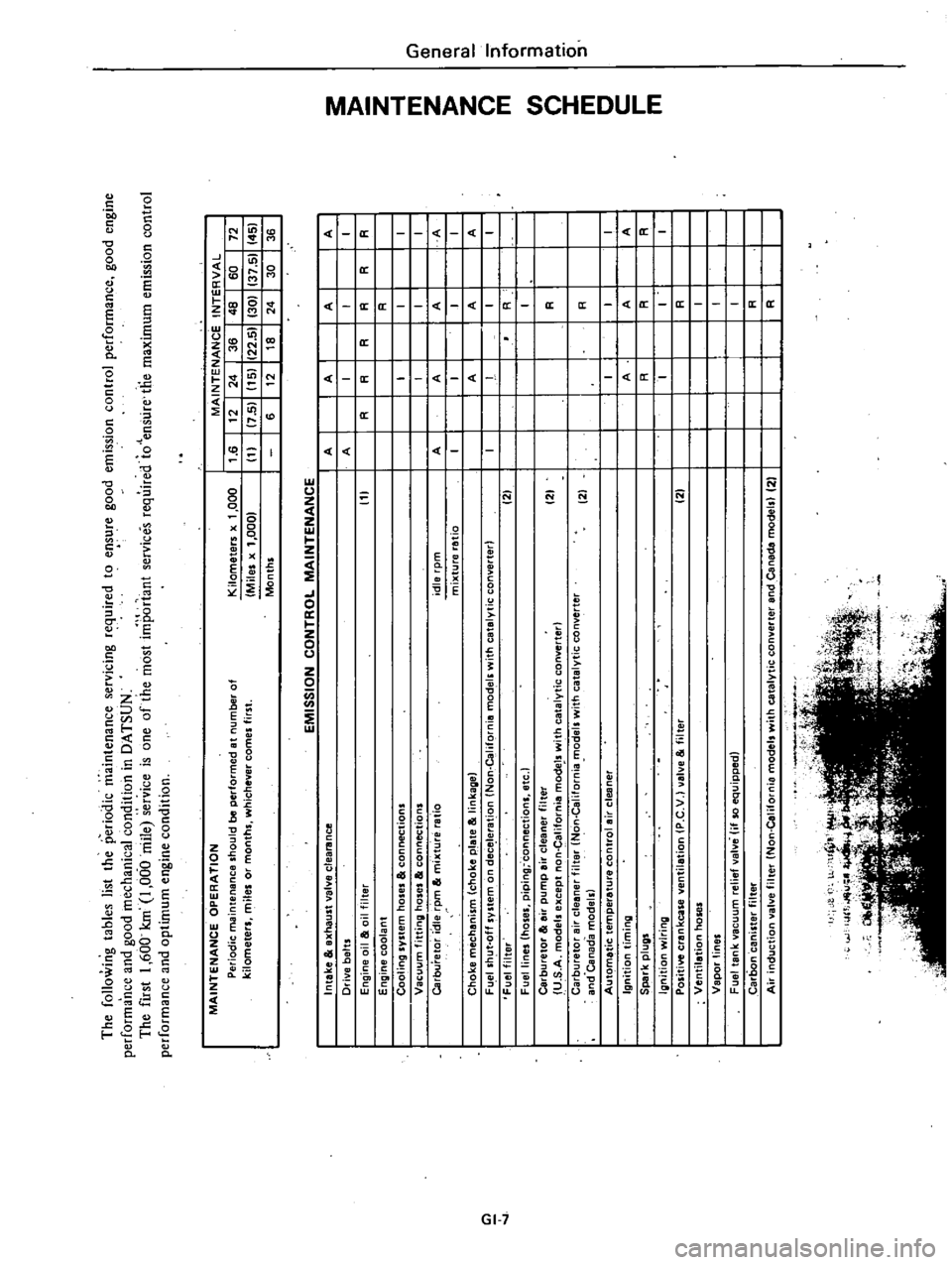
I
I
w
I
w
ID
P
u
f
t
600
rlI
000
mile
ser
ce
one
0
e
lUe
US
1
d
l
erfol1
ance
and
ol
tirrlUlll
engine
con
Itlon
1
Ip
lE
P
CE
OPEl
P
lI0
hId
formed
at
numbef
ot
periodic
roll
tero
l
OU
k
l
lllele
Ie
0
onlhO
h
chOVe
co
e
1000
efS
j
es
l
Month
1
6
P
1
1E
P
CE
lEI
VP
L
1
2
24
36
48
60
72
7
5
15
2
2
5
301
37
5
45
6
1
2
18
24
30
36
G
l
1
Ip
lE
A
CE
OPEl
P
lI0
periodic
roll
ten
should
be
l
i
ometert
TIlles
ot
onth
Month
EMISSION
CONll
O
MMN1ENJl
NCE
P
P
P
P
I
ota
l
e
8t
exhaust
a
NEt
c
ear1lf
C
P
l
l
l
l
On
belU
11
l
l
I
EnQltltl
0
11
0
filter
I
engine
COO
Brot
I
Coo
n
v
te
hO
conne
on
P
P
P
laC
1
lrn
titt1ng
hOleS
8l
eof
ect
Ql1
P
IdlG
rpm
I
ca
elo
dIe
p
t
M
I
I
fl
1
turu
ra
IO
P
P
P
ChO
0
h8
chOke
pl
ink
1
1
de
th
ca
IV
e
conv
I
I
t
f
NOf
call
QP
2
I
f
1
h
t
olt
v
t
on
dec
0
iF
vel
filter
f
net
hO
p
p
nO
eonn
t
on
tc
2
l
p
cl
ner
It
ca
bU
tO
P
ode
h
e
ra
V
e
conv
rto
V
S
P
d
caP
cal
O
n
2
l
0
cI
n
tnte
on
C
M
n
od
rh
c
ralV
e
con
t8
carburetor
a
f
and
CB
3da
ff
lodels
P
P
p
o
e
p
r
control
o
n
P
f
l
I
grtltlOfl
tll1U
Spal
plIJQ
l
nltIOfl
Iflng
2
po
cr
nkca
i
ion
P
C
v
8
1
Vtoti
tlOll
r10lCS
e
pol
ln
l
F
nk
c
liel
v
iI
SO
pped
l
1
Calilorn
odO
h
ca
V
p
nd
c
on
e
I
t
on
It
i
J
r
a
g
q
c
C
l
l
l
5
o
3
Q
o
o
l
Page 12 of 548
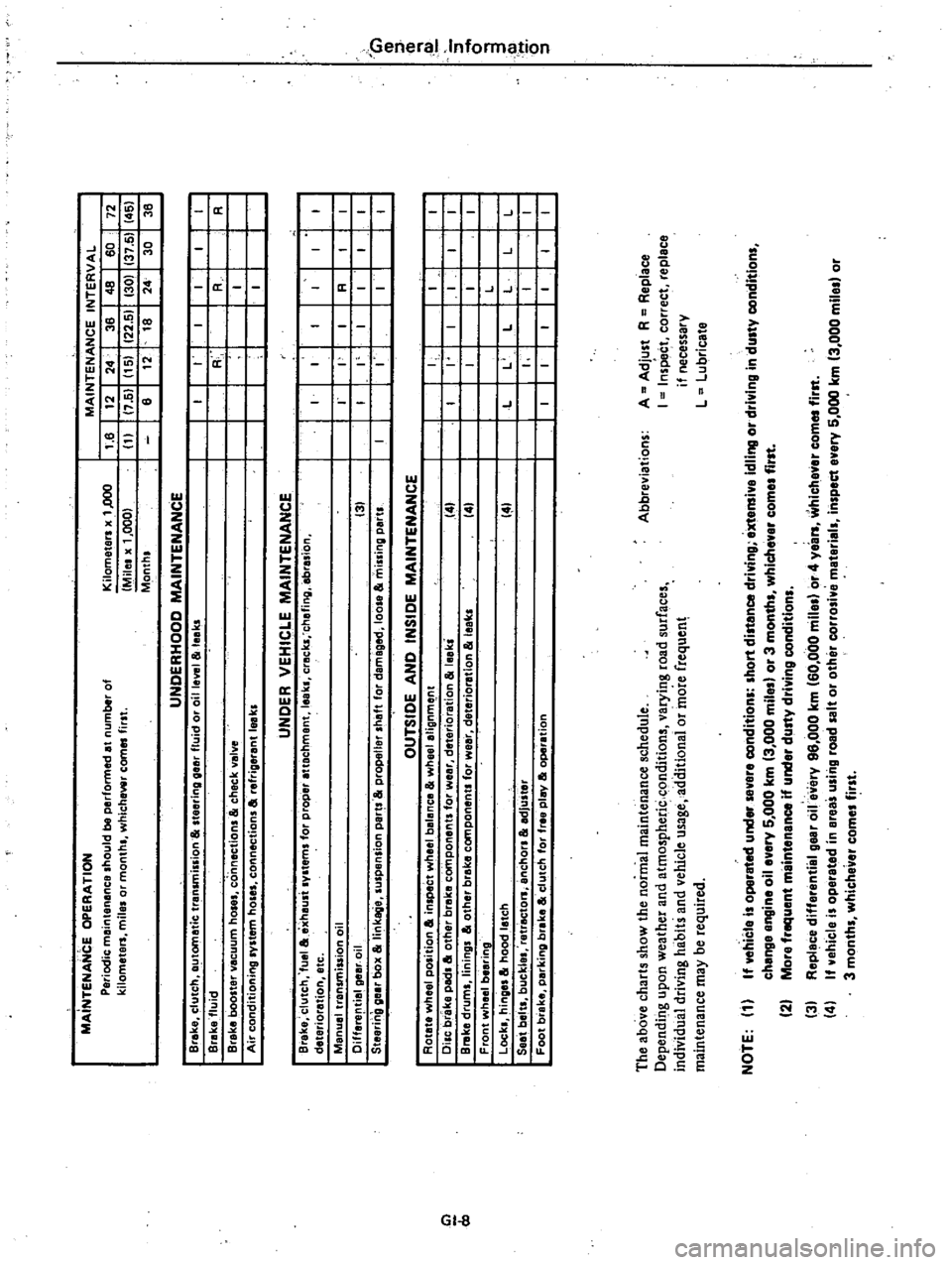
MAiNTENANCE
OPERATION
Periodic
maintenance
should
be
performed
at
number
of
kilometers
mila
or
month
whichewr
comes
first
Kilometers
1
000
Mile
x
1
000
M
3nthl
MAINTENANCE
INTERVAL
1
6
I
12
I
24
I
36
I
48
I
60
72
111
117
611
11511122
511
30
1137
5
45
I
6
I
12
r
16
I
24
I
30
36
UNDERHOOD
MAINTENANCE
Gl
The
above
charts
show
the
normal
maintenance
schedule
Dependir
tg
upon
weather
and
atmospheric
conditions
varying
road
surfaces
individual
driving
habits
and
vehicle
usage
additionai
or
more
frequen
maintenance
may
be
required
Abbreviations
A
Adjust
R
Replace
I
Inspe
t
correct
replace
if
necessary
L
Lubricate
NOTE
1
If
vehicle
i
operated
under
evere
conditions
hort
distance
driving
extensive
idling
or
driving
in
du
ty
condition
change
angine
oil
every
5
000
km
3
000
mile
or
3
month
whlchevar
come
first
2
More
frequent
maintenance
if
under
dusty
driving
condition
3
Replace
differential
gear
oile
ery
96
000
km
60
000
mila
or
4
years
whichaver
com
first
4
If
vehicle
i
operated
in
ereas
u
ing
road
alt
or
other
corro
ive
material
inspect
evary
5
000
km
3
000
mile
or
3
months
whichever
comes
first
Page 13 of 548
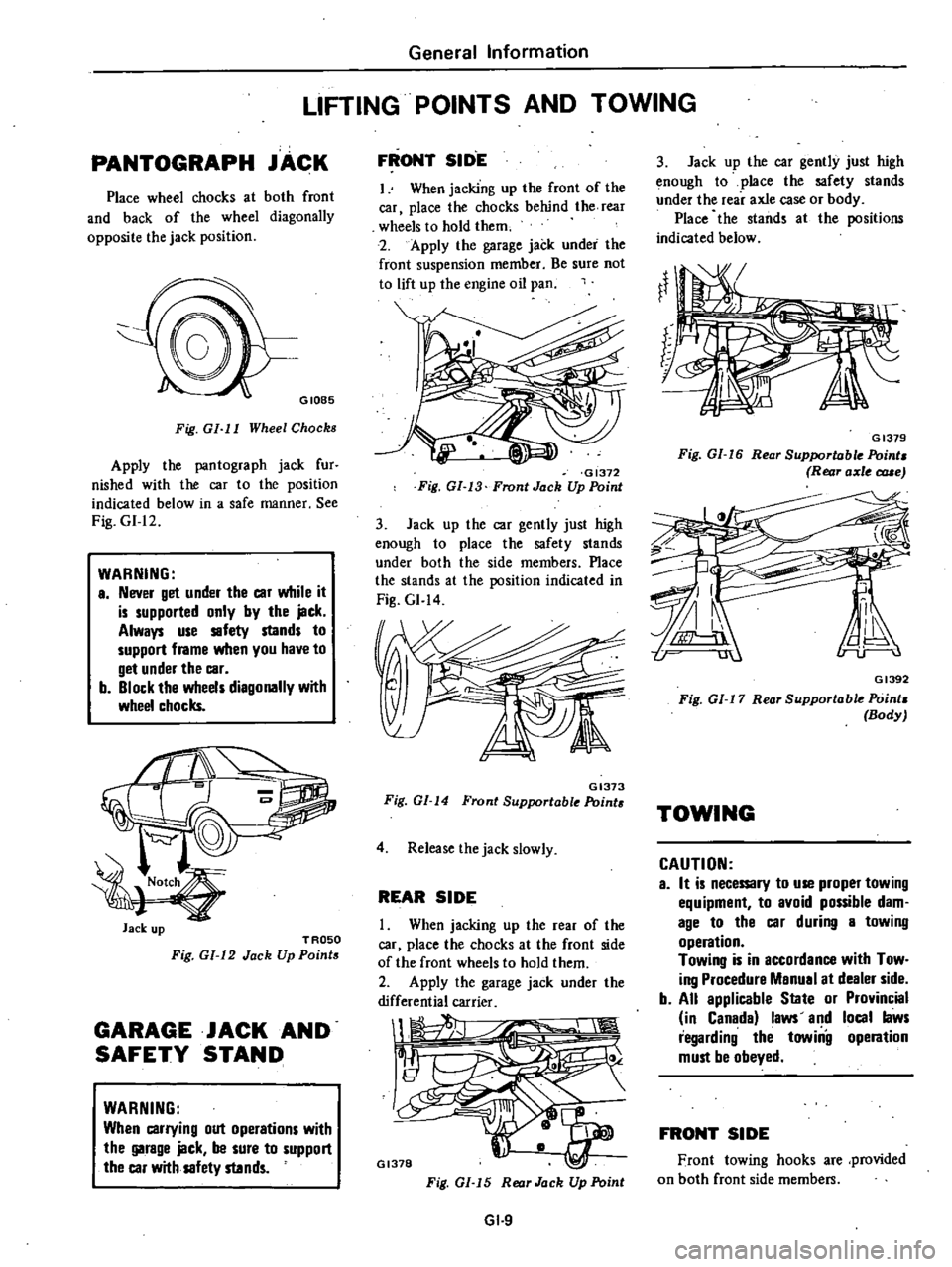
General
Information
LIFTING
POINTS
AND
TOWING
PANTOGRAPH
JACK
Place
wheel
chocks
at
both
front
and
back
of
the
wheel
diagonally
opposite
the
jack
position
GIOB5
Fig
GI
I
I
Wheel
Chocks
Apply
the
pantograph
jack
fur
nished
with
the
car
to
the
position
indicated
below
in
a
safe
manner
See
Fig
GI
12
WARNING
a
Never
get
under
the
car
while
it
is
supported
only
by
the
jack
Always
use
safety
stands
to
support
frame
when
you
have
to
get
under
the
car
b
Block
the
wheels
diagonally
with
wheel
chocks
Jack
up
TROSO
Fig
GI
12
Jack
Up
Points
GARAGE
JACK
AND
SAFETY
STAND
WARNING
When
carrying
out
operations
with
the
garage
jack
be
sure
to
support
the
car
with
safety
stands
FRONT
SID
E
I
When
jacking
up
the
front
of
the
car
place
the
chocks
behind
the
rear
wheels
to
hold
them
2
Apply
the
garage
jack
under
the
front
suspension
member
Be
sure
not
to
lift
up
the
engine
oil
pan
GI372
Fig
GI
13
Front
Jack
Up
Point
3
Jack
up
the
car
gently
just
high
enough
to
place
the
safety
stands
under
both
the
side
members
Place
the
stands
at
the
position
indicated
in
Fig
GI
14
GI373
Fig
GI
14
Front
Supportable
Point
4
Release
the
jack
slowly
REAR
SIDE
When
jacking
up
the
rear
of
the
car
place
the
chocks
at
the
front
side
of
the
front
wheels
to
hold
them
2
Apply
the
garage
jack
under
the
differential
carrier
1
1
Il
GI378
Fig
GI
15
Rear
Jack
Up
Point
GI
9
3
Jack
up
the
car
gently
just
high
enough
to
place
the
safety
stands
under
the
rear
axle
case
or
body
Place
the
stands
at
the
positions
indicated
below
GI379
Fig
GI
16
Rear
Supportable
Point
Rear
axle
c
rue
GI392
Fig
01
17
Rear
Supportable
Point
Body
TOWING
CAUTION
a
It
is
necemry
to
use
proper
towing
equipment
to
avoid
possible
dam
age
to
the
car
during
a
towing
operation
Towing
is
in
accordance
with
Tow
ing
Procedure
Manual
at
dealer
side
b
All
applicable
State
or
Provincial
in
Canada
laws
and
local
laws
regarding
the
towiilg
operation
must
be
obeyed
FRONT
SIDE
Front
towing
hooks
are
provided
on
both
front
side
members
Page 14 of 548
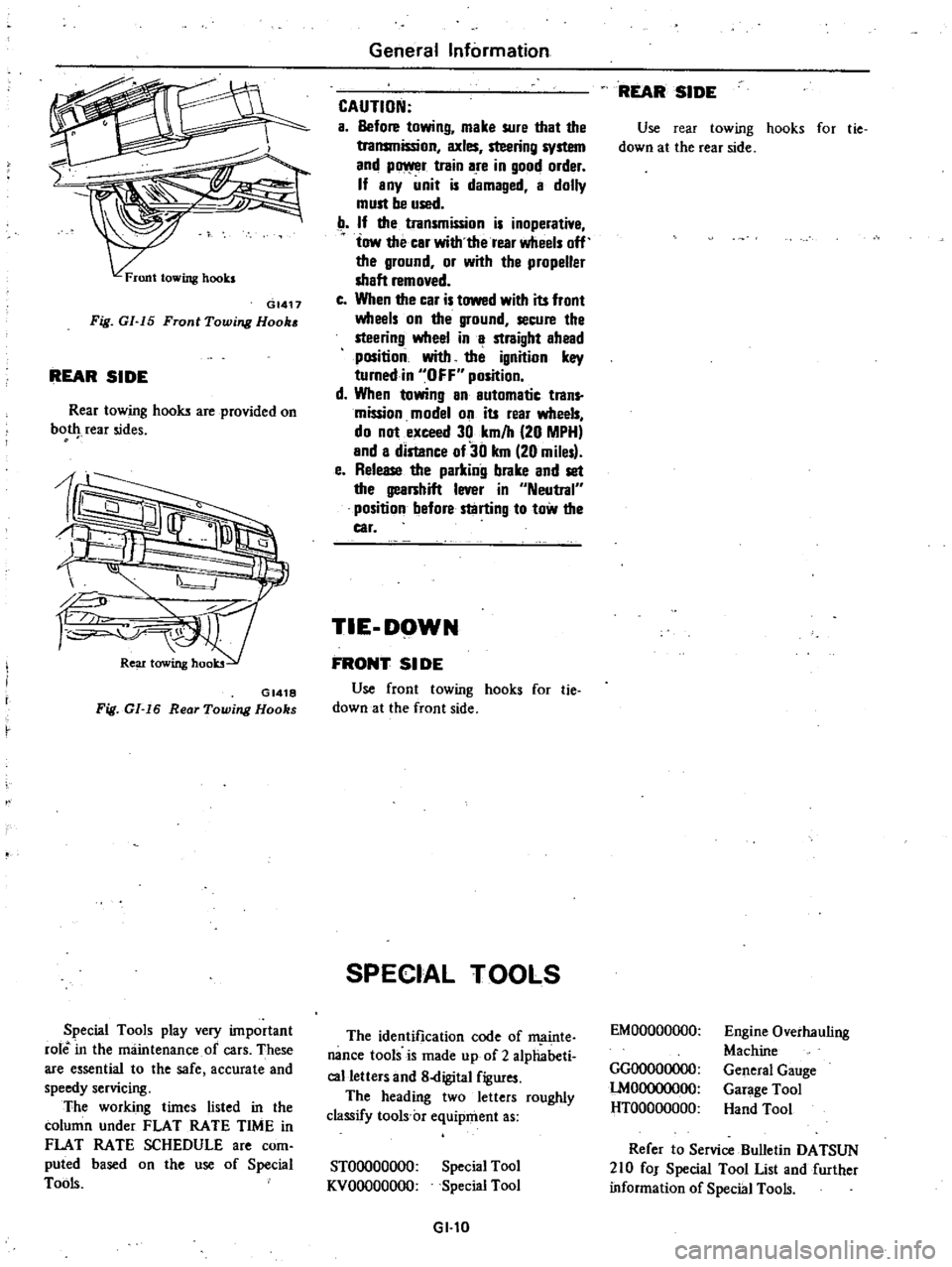
GI417
Fig
GI
15
Front
Towing
Hook
REAR
SIDE
Rear
towing
hooks
are
provided
on
bot
rear
sides
GI418
Fig
GI
16
Rear
Towing
Hooks
Special
Tools
play
very
important
role
in
the
maintenance
of
cars
These
are
essential
to
the
safe
accurate
and
speedy
servicing
The
working
times
listed
in
the
column
under
FLAT
RATE
TIME
in
FLAT
RATE
SCHEDULE
are
com
puted
based
on
the
use
of
Special
Tools
General
Information
CAUTION
a
Before
towing
make
sure
that
the
transmission
axles
steering
system
and
p
r
train
are
in
good
order
If
any
unit
is
damaged
a
dolly
must
be
used
If
the
transmission
is
inoperative
tow
the
car
with
the
rear
wheels
off
the
ground
or
with
the
propeller
shaft
removed
c
When
the
car
is
towed
with
its
front
wheels
on
the
ground
secure
the
steering
wheel
in
a
straight
ahead
position
with
the
ignition
key
turnedin
OFF
position
d
When
towing
an
automatic
trans
mission
model
on
its
rear
wheels
do
not
exceed
30
km
h
20
MPH
and
a
distance
of30
km
20
miles
e
Release
the
parking
brake
and
set
the
gearshift
lever
in
Neutral
position
before
starting
to
tow
the
car
TIE
DOWN
FRONT
51
DE
Use
front
towing
hooks
for
tie
down
at
the
front
side
SPECIAL
TOOLS
The
identification
code
of
ffi
linte
nance
tools
is
made
up
of
2
alphabeti
calletters
and
8
digital
figures
The
heading
two
letters
roughly
classify
tools
c
equipment
as
STOOOOOOOO
KVOOOOOOOO
Special
Tool
Special
Tool
GI
l0
REAR
SIDE
Use
rear
towing
hooks
for
tie
down
at
the
rear
side
EMOOOOOOOO
GGOOOOOOOO
lMOOOOOOOO
HTOOOOOOOO
Engine
Overhauling
Machine
General
Gauge
Garage
Tool
Hand
Tool
Refer
to
Service
Bulletin
DATSUN
210
fOJ
Special
Tool
List
and
further
information
of
Special
Tools
Page 15 of 548
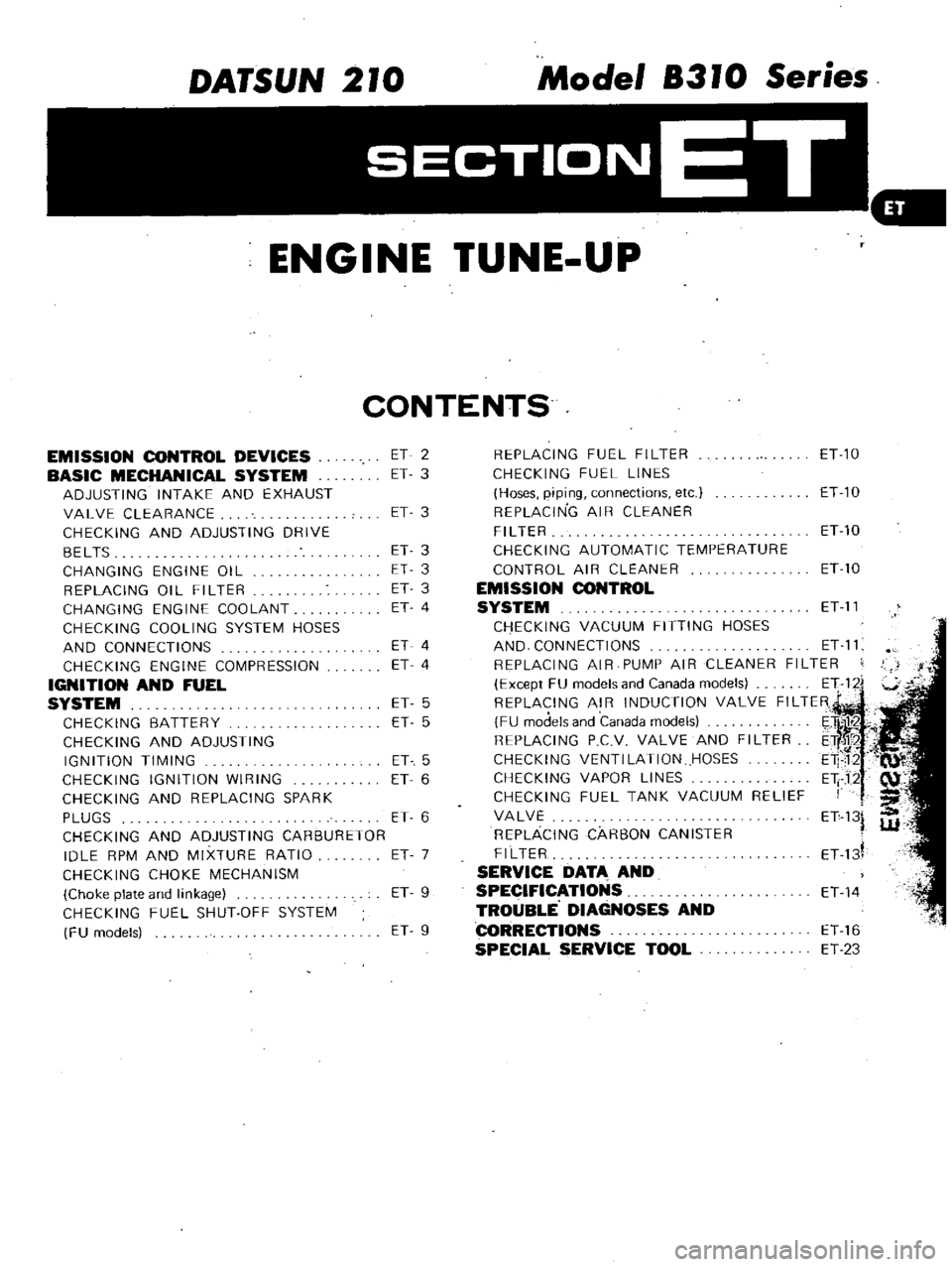
DATSUN
210
Model
8310
Series
SECTIONET
ET
ENGINE
TUNE
UP
CONTENTS
EMISSION
CONTROL
DEVICES
BASIC
MECHANICAL
SYSTEM
ADJUSTING
INTAKE
AND
EXHAUST
VALVE
CLEARANCE
CHECKING
AND
ADJUSTING
DRIVE
BELTS
CHANGING
ENGINE
OIL
REPLACING
01
L
FI
L
TER
CHANGING
ENGINE
COOLANT
CHECKING
COOLING
SYSTEM
HOSES
AND
CONNECTIONS
CHECKING
ENGINE
COMPRESSION
IGNITION
AND
FUEL
SYSTEM
CHECKING
BATTERY
CHECKING
AND
ADJUSTING
IGNITION
TIMING
CHECKING
IGNITION
WIRING
CHECKING
AND
REPLACING
SPARK
PLUGS
CHECKING
AND
ADJUSTING
CARBURETOR
IDLE
RPM
AND
MIXTURE
RATIO
CHECKING
CHOKE
MECHANISM
Choke
plate
and
linkage
CHECKING
FUEL
SHUT
OFF
SYSTEM
FU
models
ET
2
ET
3
ET
3
ET
3
ET
3
ET
3
ET
4
ET
4
ET
4
ET
5
ET
5
ET
5
ET
6
ET
6
ET
7
ET
9
ET
9
REPLACING
FUEL
FILTER
ET
10
CHECKING
FUEL
LINES
Hoses
piping
connections
etc
ET
10
REPLACING
AIR
CLEANER
FILTER
ETlO
CHECKING
AUTOMATIC
TEMPERATURE
CONTROL
AIR
CLEANER
ET
10
EMISSION
CONTROL
SYSTEM
ET
11
CHECKING
VACUUM
FITTING
HOSES
AND
CONNECTIONS
ET
11
REPLACING
AIR
PUMP
AIR
CLEANER
FILTER
Except
FU
models
and
Canada
models
E
1122i
REPLACING
AIR
INDUCTION
VALVE
FILTER
FU
models
and
Canada
models
E
tlil1r2
C
REPLACING
PCV
VALVE
AND
FILTER
ETf
CHECKING
VENTI
LATION
HOSES
E1P12
CHECKING
VAPOR
LINES
Eli
J2
CHECKING
FUEL
TANK
VACUUM
RELIEF
I
f
III
VALVE
ET
13
REPLACING
CARBON
CANISTER
W
FILTER
ET
d
SERVICE
DATA
AND
SPECIFICATIONS
ET
14
TROUBLE
DIAGNOSES
AND
CORRECTIONS
ET
16
SPECIAL
SERVICE
TOOL
ET
23
Page 16 of 548
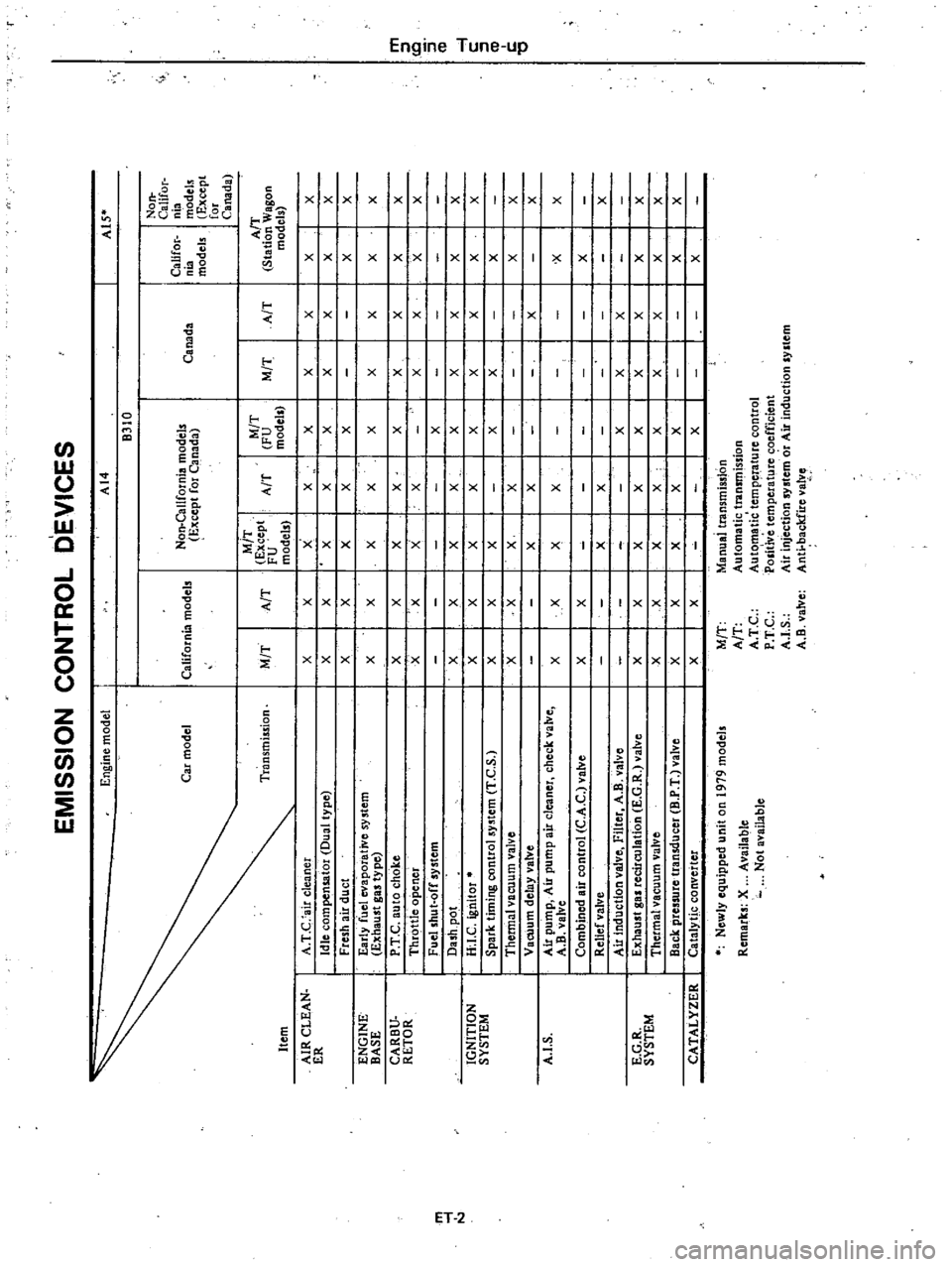
f
EMISSION
CONTROL
DEVICES
En
ine
model
I
AI4
I
A1S
B310
Non
CaliCor
Non
California
models
Califor
nia
Car
model
California
models
E
cept
for
C
nada
Canada
nia
modeb
models
Except
for
Canada
M
T
M
T
A
T
Ti
ansmiuion
M
T
A
T
Except
A
T
FU
M
T
A
T
Station
Wagon
FU
models
models
models
AIR
CLEAN
I
A
T
C
air
cleaner
I
X
I
X
X
I
X
I
X
I
X
I
X
I
X
X
ER
Idle
compensator
Dual
type
X
I
X
X
I
X
I
X
I
X
I
X
I
X
X
Fresh
air
duct
X
I
X
X
I
X
I
X
I
I
I
X
X
ENGINE
I
Early
fuel
evaporative
system
X
I
X
X
xl
X
I
X
I
X
I
X
X
BASE
Exhaust
gas
type
CARBV
I
P
T
C
auto
choke
X
I
X
X
X
I
X
I
X
I
X
I
X
X
m
RETOR
I
l
Thr
ttle
opener
X
X
X
X
I
I
X
I
X
I
X
X
Q
I
Fuel
shut
off
system
I
X
I
I
I
3
m
ll
i
Dash
po
t
X
X
X
X
I
X
I
X
I
X
I
X
X
N
l
IGNITION
I
H
I
C
ignitor
X
X
X
X
I
X
I
X
I
X
I
X
X
c
SYSTEM
Spark
timing
contra
system
T
e
S
X
X
X
I
I
I
I
l
X
X
I
X
ll
Thermal
vacuum
valve
X
X
X
I
X
I
I
I
I
X
X
c
Vacuum
delay
valve
X
I
X
I
I
I
X
I
0
X
A
I
S
I
Air
pump
Air
pump
air
cleaner
check
valve
I
X
X
I
X
I
X
I
I
I
I
x
X
A
B
valve
Combined
air
control
C
A
C
valve
I
X
X
I
I
I
I
I
I
X
Relief
valve
I
I
X
I
X
I
I
I
I
X
Air
induction
valve
Filter
A
B
valve
I
I
I
I
X
I
X
I
X
E
G
R
I
Exhaust
gas
recirculation
E
G
R
valve
I
X
I
X
I
X
I
X
I
X
I
X
I
X
I
X
X
SYSTEM
Thetmalvacuum
valve
I
X
I
X
I
X
I
X
I
X
I
X
I
X
I
X
X
Back
pressure
transducer
B
P
T
valve
I
X
I
X
I
X
I
X
I
X
I
I
I
X
X
CATALYZER
I
CatalytJc
converter
I
X
I
X
I
I
I
X
I
I
I
X
Newly
equipped
unit
on
1979
models
M
T
Manual
transmission
Remarks
X
Available
A
T
Automatic
transmission
Not
available
A
T
C
Aute
matic
tempeJ
ature
control
P
T
C
POlitive
temperature
coefficient
A
I
S
Air
injection
system
or
Air
induction
system
A
B
valve
Anti
backfire
valve
Page 17 of 548
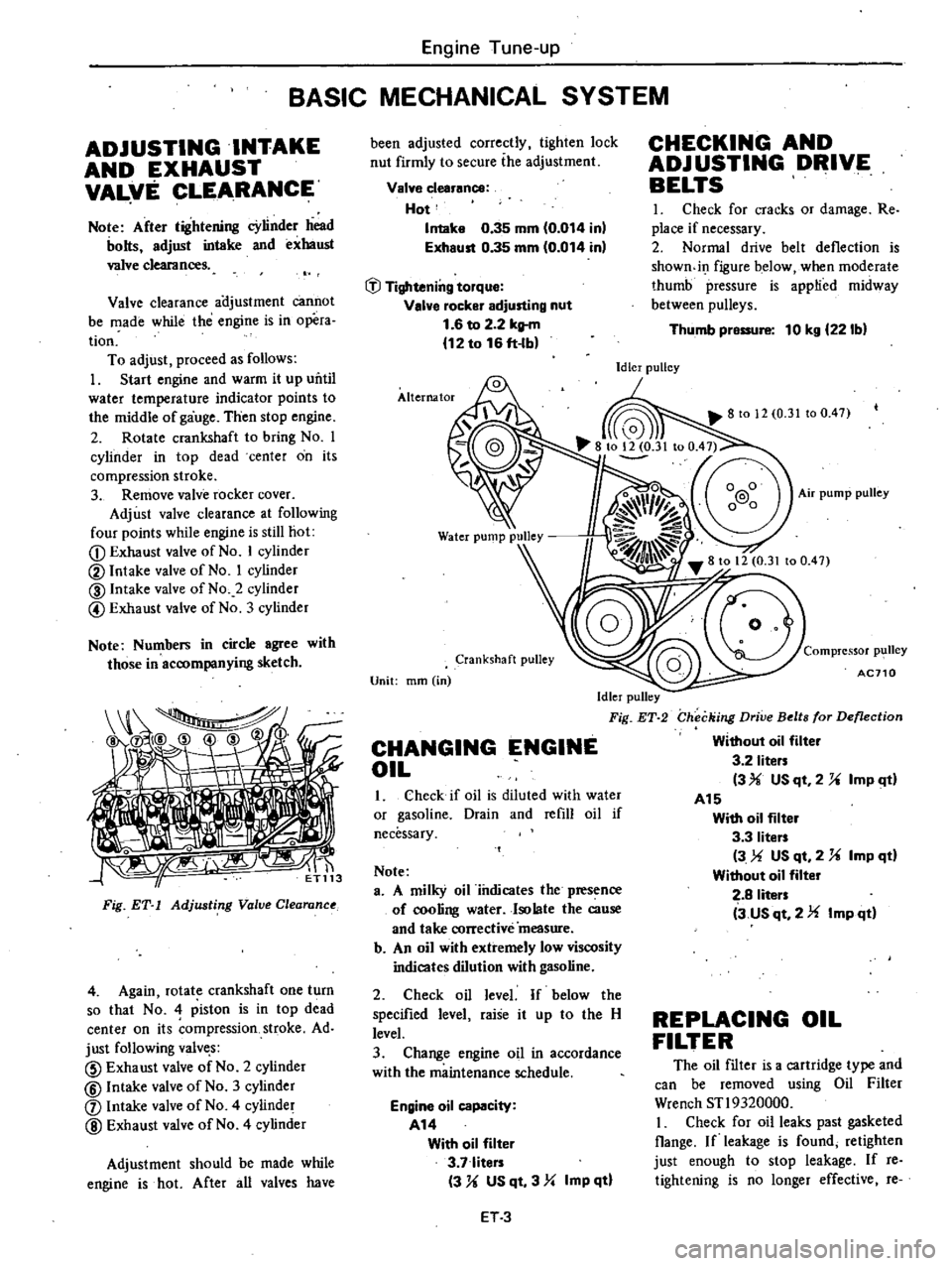
Engine
Tune
up
BASIC
MECHANICAL
SYSTEM
ADJUSTING
INTAKE
AND
EXHAUST
VAL
fE
CLEARANCE
Note
After
tightening
cYlinder
head
bolts
adjust
intake
and
exhaust
valve
clearances
Valve
clearance
ai
ljustment
cannot
be
made
while
the
engine
is
in
opera
tion
To
adjust
proceed
as
follows
I
Start
engine
and
warm
it
up
uritil
water
temperature
indicator
points
to
the
middle
of
gauge
Then
stop
engine
2
Rotate
crankshaft
to
bring
No
I
cylinder
in
top
dead
center
on
its
compression
stroke
3
Remove
valve
rocker
cover
Adjust
valve
clearance
at
following
four
points
while
engine
is
still
hot
CD
Exhaust
valve
of
No
I
cylinder
@
Intake
valve
of
No
I
cylinder
@
Intake
valve
of
No
2
cylinder
@
Exhaust
valve
of
No
3
cylinder
Note
Numbers
in
circle
agree
with
those
in
accompanying
sketch
tiri
Fig
ET
1
Adjusting
Value
Clearanu
4
Again
rotate
crankshaft
one
turn
so
that
No
4
piston
is
in
top
dead
center
on
its
ompression
stroke
Ad
just
following
valve
s
CID
Exhaust
valve
of
No
2
cylinder
@
Intake
valve
of
No
3
cylinder
j
Intake
valve
of
No
4
cylinder
@
Exhaust
valve
of
No
4
cylinder
Adjustment
should
be
made
while
engine
is
hot
After
all
valves
have
been
adjusted
correctly
tighten
lock
nut
firmly
to
secure
ihe
adjustment
Valve
clearance
Hot
Intake
0
35
mm
0
014
inl
Exhaust
0
35
mm
0
014
in
tJl
Tightening
torque
Valve
rocker
adjusting
nut
1
6
to
2
2
kltm
12
to
16
ft
lb
Alternator
Crankshaft
pulley
Unit
mm
in
Idler
pulley
Fig
ET
2
CHANGING
ENGINE
OIL
1
Check
if
oil
is
diluted
with
water
or
gasoline
Drain
and
refill
oil
if
necessary
Note
a
A
milky
oil
iiulicates
the
presence
of
cooling
water
Isolate
the
cause
and
take
corrective
measure
b
An
oil
with
extremely
low
viscosity
indicates
dilution
with
gasoline
2
Check
oil
level
If
below
the
specified
level
raise
it
up
to
the
H
level
3
Change
engine
oil
in
accordance
with
the
maintenance
schedule
Engine
oil
capacity
A14
With
oil
filter
3
7
liters
3
U
US
qt
3
Yo
Imp
qtl
ET3
CHECKING
AND
ADJUSTING
DRIVE
BELTS
I
Check
for
cracks
or
damage
Re
place
if
necessary
2
Normal
drive
belt
deflection
is
showndI
figure
below
when
moderate
thumb
pressure
is
applied
midway
between
pulleys
Thumb
pressure
10
kg
221bl
Idler
pulley
Compressor
p1
111ey
AC710
Checking
Drive
Belts
for
Deflection
Without
oil
filter
3
2
liters
3
USqt
2
U
ImP
ltl
A15
With
oil
filter
3
3
liters
3
US
qt
2
U
Imp
qd
Without
oil
filter
2
8
liters
3
us
qt
2
Imp
qd
REPLACING
OIL
FILTER
The
oil
filter
is
a
cartridge
type
and
can
be
removed
using
Oil
Filter
Wrench
STl9320000
I
Check
for
oil
leaks
past
gasketed
Oange
If
leakage
is
found
retighten
just
enough
to
stop
leakage
If
reo
tightening
is
no
longer
effective
re
Page 18 of 548
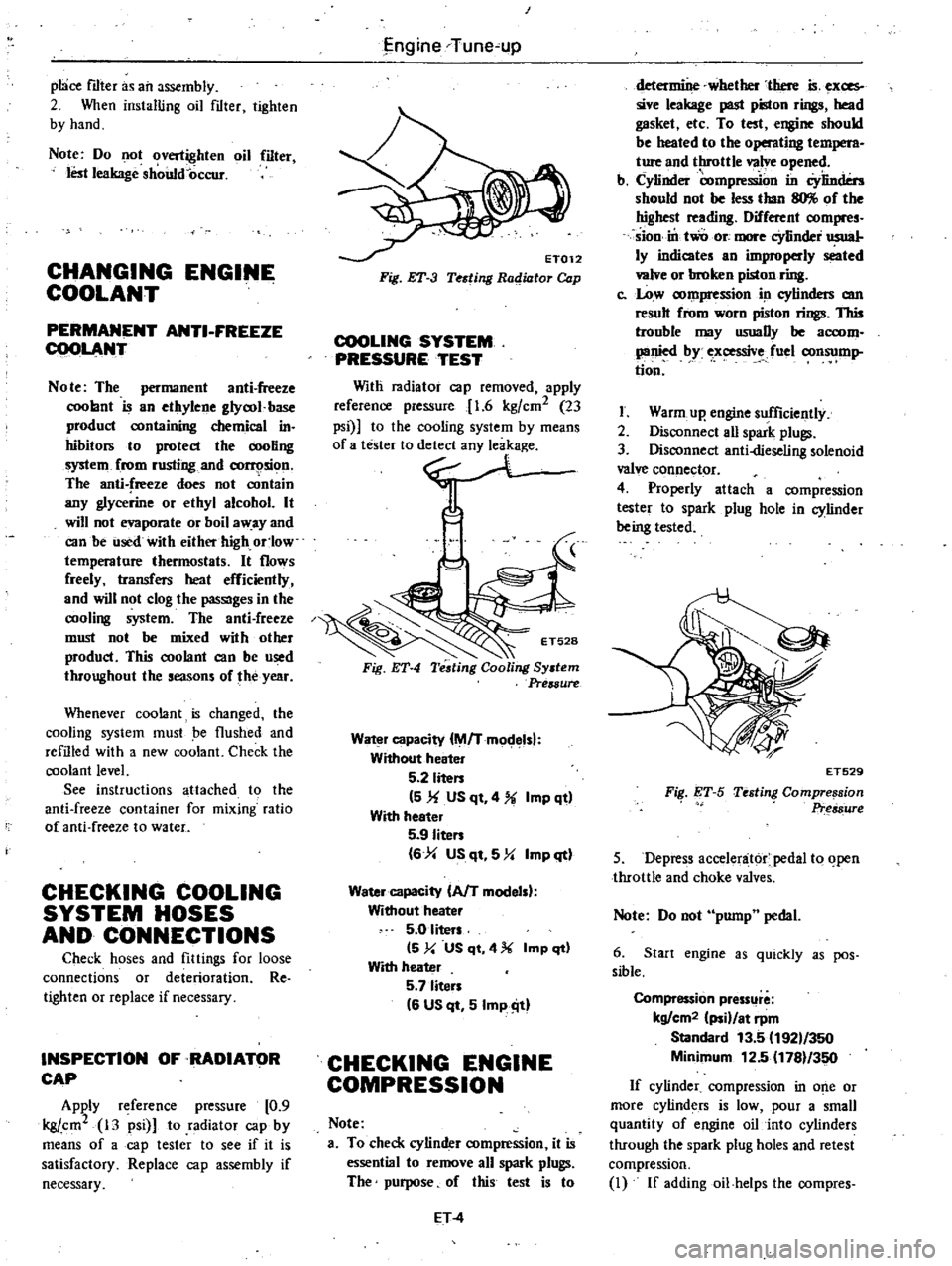
pl
ice
mter
as
an
assembly
2
When
installing
oil
mter
tighten
by
hand
Note
Do
not
overtighten
oil
filter
lest
leakage
shoUld
occur
CHANGING
ENGINE
COOLANT
PERMANENT
ANTI
FREEZE
COOLANT
Note
The
permanent
anti
freeze
coolant
is
an
ethylene
glya
l
base
product
containing
chemical
in
hibitors
to
protect
the
cooling
system
from
rusting
and
corrosion
The
anti
freeze
does
not
cOntain
any
glycerine
or
ethyl
alcohol
It
will
not
evaporate
or
boil
a
ay
and
can
be
ilsed
with
either
high
or
low
temperature
thermostats
It
flows
freely
transfers
heat
efficiently
and
will
not
clog
the
passages
in
the
cooling
system
The
anti
freeze
must
not
be
mixed
with
other
product
This
coolant
can
be
used
throughout
the
seasons
of
the
year
Whenever
coolant
is
changed
the
cooling
system
must
be
flushed
and
refilled
with
a
new
coolant
Check
the
coolant
level
See
instructions
attached
to
the
anti
freeze
container
for
mixing
ratio
of
anti
freeze
to
water
CHECKING
COOLING
SYSTEM
HOSES
AND
CONNECTIONS
Check
hoses
and
fittings
for
loose
connections
or
deterioration
Re
tighten
or
replace
if
necessary
INSPECTION
OF
RADIATOR
CAP
Apply
reference
pressure
0
9
kgj
cm2
13
psi
to
radiator
cap
by
means
of
a
cap
tester
to
see
if
it
is
satisfactory
Replace
cap
assembly
if
necessary
I
j
ngine
Tune
up
ET012
Fig
ET
3
Testing
Radiator
Cap
COOLING
SYSTEM
PRESSURE
TEST
Witli
radiator
cap
removed
apply
reference
pressure
1
6
kgfcm2
23
psi
to
the
cooling
system
by
means
0
no
Fig
ET
4
Water
capacity
M
Tmodelsl
Without
heater
5
2
liten
5
1f
US
qt
4
Imp
qt
With
heeter
5
9
Iiten
6
4
US
qt
5
Y
Imp
qt
Water
capacity
AfT
modelsl
Without
heater
5
0
liters
5
y
US
qt
4
Imp
qt
With
heater
5
7
liten
6
US
qt
5
Imp
ill
CHECKING
ENGINE
COMPRESSION
Note
a
To
check
cylinder
compression
it
is
essential
to
remove
all
spark
plugs
The
purpose
of
this
test
is
to
ET
4
determine
whether
there
is
exces
sive
leakage
past
piston
rings
head
gasket
etc
To
test
engine
should
be
heated
to
the
operating
t
M
ture
and
throttle
valve
opened
b
Cylinder
compre
on
in
Cylinders
should
not
be
less
than
llO
of
the
highest
reading
Different
compres
sion
in
two
ore
more
cYlinder
usual
ly
indicates
an
improperly
seated
valve
or
broken
piston
ring
c
Low
compression
in
cylinders
am
result
from
worn
piston
rings
This
trouble
may
usuaDy
be
accom
panied
by
ex
ssive
fuel
consump
tion
I
Warm
up
engine
sufficiently
2
Disconnect
aU
spark
plugs
3
Disconnect
anti
dieseling
solenoid
valve
connector
4
Properly
attach
a
compression
tester
to
spark
plug
hole
in
cylinder
being
tested
FiI
ET
S
ET529
Testing
Compre
sion
Pr
s8ure
5
Depress
accelenit6r
pedal
to
open
throttle
and
choke
valves
Note
Do
not
pump
pedal
6
Start
engine
as
quickly
as
pos
sible
Compression
pressllre
kg
cm2
ii
at
rpm
Standard
13
5
192
350
Minimum
12
5
1781
350
If
cylinder
compression
in
o
e
or
more
cylinders
is
low
pour
a
small
quantity
of
engine
oil
into
cylinders
through
the
spark
plug
holes
and
retest
compression
I
If
addingoil
helps
the
compres
Page 19 of 548
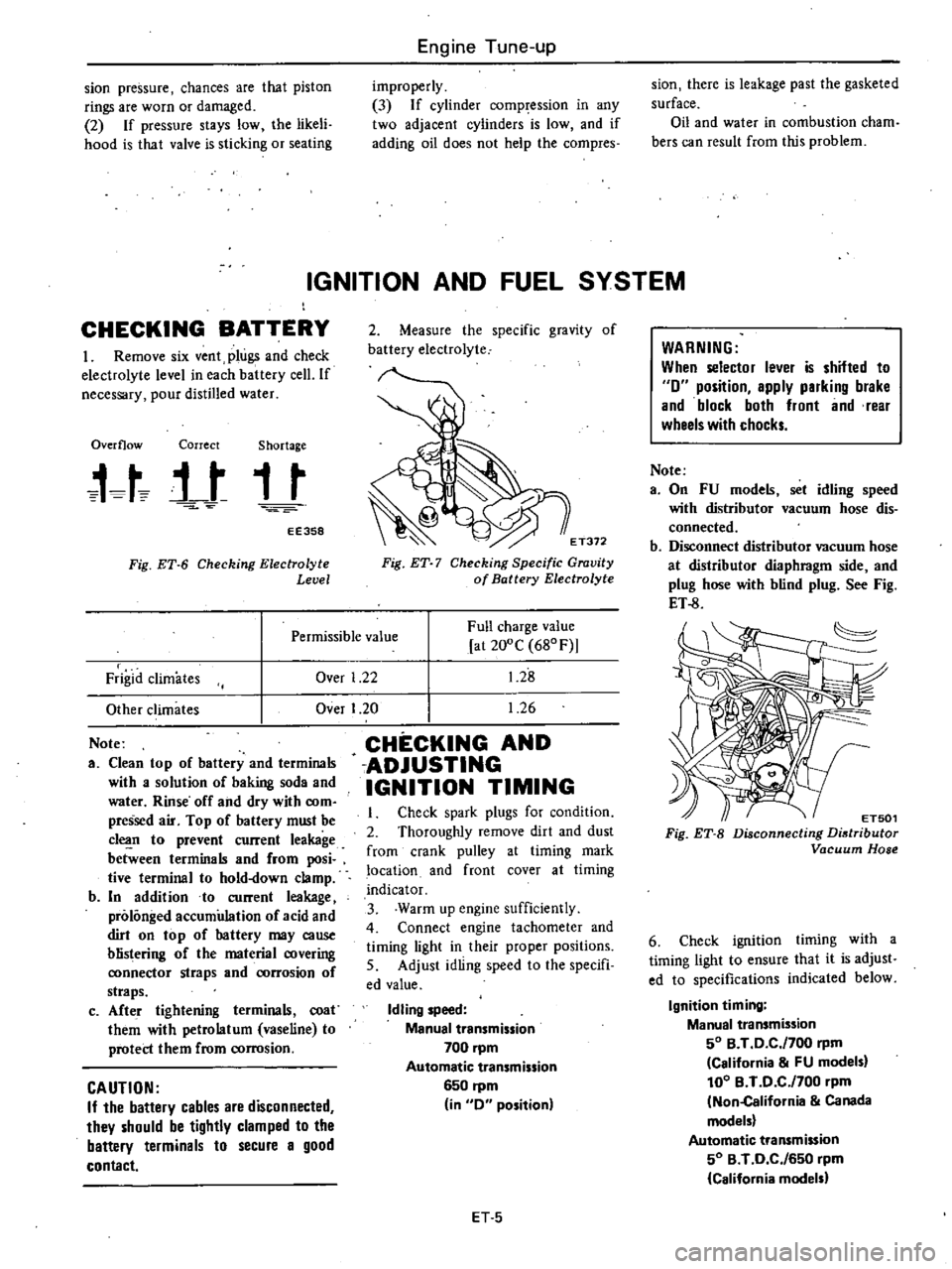
sion
pressure
chances
are
that
piston
rings
are
worn
or
damaged
2
If
pressure
stays
low
the
likeli
hood
is
that
valve
is
sticking
or
seating
Engine
Tune
up
improperly
3
If
cylinder
compression
in
any
two
adjacent
cylinders
is
low
and
if
adding
oil
does
not
help
the
compres
sion
there
is
leakage
past
the
gasketed
surface
Oil
and
water
in
combustion
cham
bers
can
result
from
this
problem
IGNITION
AND
FUEL
SYSTEM
CHECKING
BATTERY
I
Remove
six
vent
plugs
and
check
electrolyte
level
in
each
battery
cell
If
necessary
pour
distilled
water
Overflow
Correct
Shortage
t
t
j
t
t
t
EE358
Fig
ET
6
Checking
Electrolyte
Level
2
Measure
the
specific
gravity
of
battery
electrolyte
E
T372
Fig
ET
7
Checking
Specific
Gravity
of
Battery
Electrolyte
Over
1
22
Full
charge
value
at
200C
680F
1
28
1
26
Permissible
value
Frigid
climates
Other
climates
Note
a
Clean
top
of
battery
and
terminals
with
a
solution
of
baking
soda
and
water
Rinse
off
and
dry
with
com
pressed
air
Top
of
battery
must
be
c1
n
to
prevent
current
leakage
between
terminals
and
from
posi
tive
terminal
to
hold
down
clamp
b
In
addition
to
current
leakage
prolonged
accumulation
of
acid
and
dirt
on
top
of
hattery
may
cause
blistering
of
the
material
covering
ronnector
straps
and
rorrosion
of
straps
c
Afte
r
tightening
terminals
coat
them
with
petrolatum
vaseline
to
protect
them
from
corrosion
CAUTION
If
the
battery
cables
are
disconnected
they
should
be
tightly
clamped
to
the
battery
terminals
to
secure
a
good
contact
Over
I
20
CHECKING
AND
ADJUSTING
IGNITION
TIMING
Check
spark
plugs
for
condition
2
Thoroughly
remove
dirt
and
dust
from
crank
pulley
at
timing
mark
location
and
front
cover
at
timing
indicator
3
Warm
up
engine
sufficiently
4
Connect
engine
tachometer
and
timing
light
in
their
proper
positions
5
Adjust
idling
speed
to
the
specifi
ed
value
Idling
speed
Manual
transmission
700
pm
Automatic
transmission
6S0
rpm
in
0
position
ET
S
WARNING
When
selector
lever
is
shifted
to
0
position
apply
parking
brake
and
block
both
front
and
rear
wheels
with
chocks
Note
a
On
FU
models
set
idling
speed
with
distributor
vacuum
hose
dis
connected
b
Disconnect
distributor
vacuum
hose
at
distributor
diaphragm
side
and
plug
hose
with
blind
plug
See
Fig
ET
8
ET501
Fig
ET
B
Disconnecting
Distributor
Vacuum
Hose
6
Check
ignition
timing
with
a
timing
light
to
ensure
that
it
is
adjust
ed
to
specifications
indicated
below
Ignition
timing
Manual
transmission
SO
B
T
0
C
f700
rpm
California
FU
models
100
B
T
0
C
f700
pm
Non
California
Canada
models
Automatic
transmission
SO
B
T
0
C
f6S0
rpm
California
models
Page 20 of 548
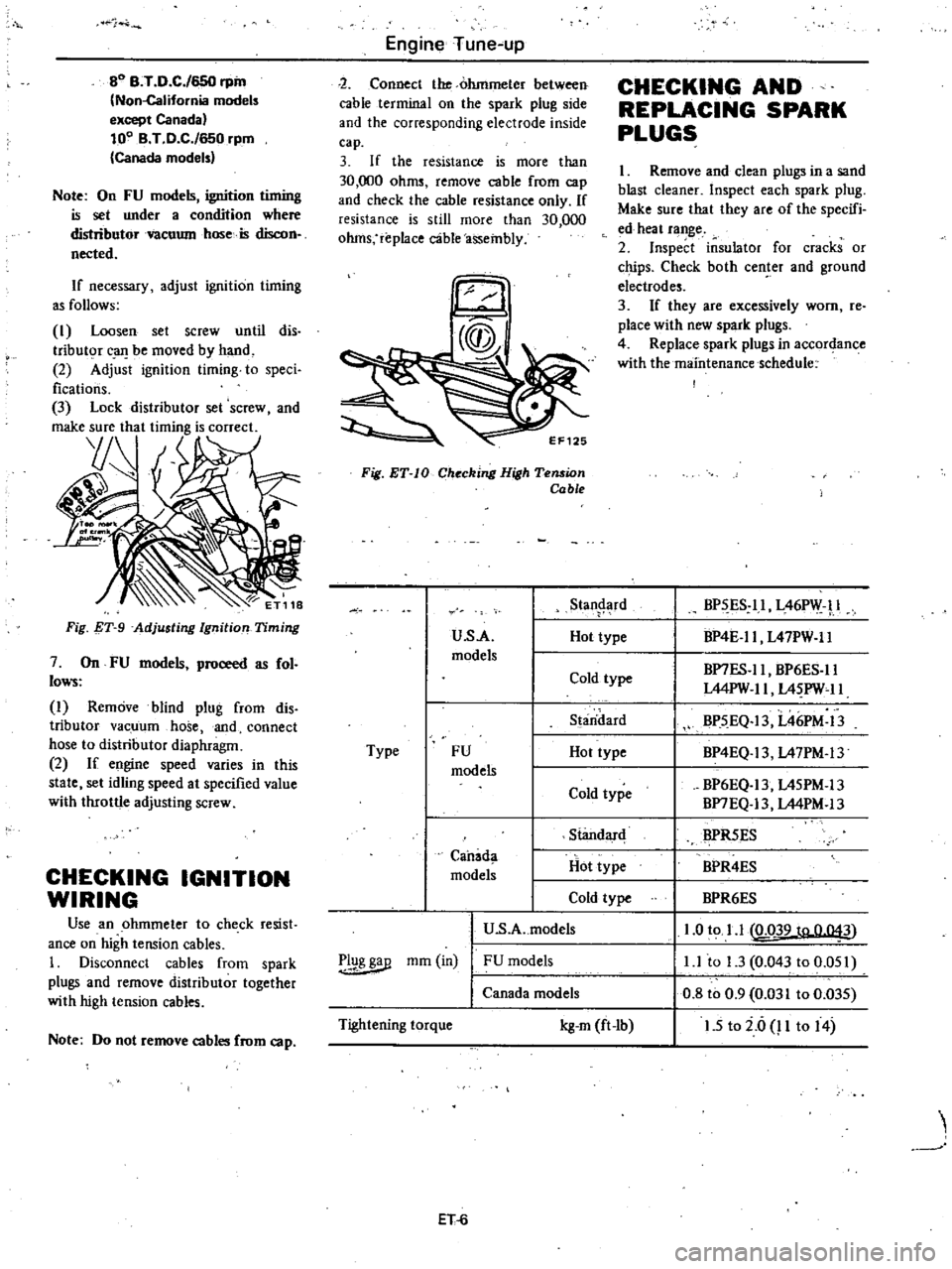
SO
B
T
D
C
l650
rpm
Non
California
models
except
Canada
100
B
T
D
C
650
rpm
Canada
models
Note
On
FU
models
ignition
timing
is
set
under
a
condition
where
distributor
vacuum
hose
is
discon
nected
If
necessary
adjust
ignition
timing
as
follows
I
Loosen
set
screw
until
dis
tributor
c
uJ
be
moved
by
hand
2
Adjust
ignition
timing
to
speci
fications
3
Lock
distributor
set
screw
and
make
sure
that
timing
is
correct
YJ
Fig
T
9
Adjusting
Ignition
Timing
7
On
FU
models
proceed
as
fol
lows
I
Remove
blind
plug
from
dis
tributor
vacuum
hose
and
connect
hose
to
distributor
diaphragm
2
If
engine
speed
varies
in
this
state
set
idling
speed
at
specified
value
with
throttle
adjusting
screw
CHECKING
IGNITION
WIRING
Use
an
ohmmeter
to
check
resist
ance
on
high
tension
cables
1
Disconnect
cables
from
spark
plugs
and
remove
distributor
together
with
high
tension
cables
Note
Do
not
remove
cables
from
cap
Engine
Tune
up
2
Connect
the
ohmmeter
between
cable
terminal
on
the
spark
plug
side
and
the
corresponding
electrode
inside
cap
3
If
the
resistance
is
more
than
30
000
ohms
remove
cable
from
cap
and
check
the
cable
resistance
only
If
resistance
is
still
more
than
30
000
ohms
replace
c3ble
assembly
Fig
ET
IO
Checking
High
Tension
Cable
u
s
A
models
Type
FU
models
Standard
Hot
type
Cold
type
U
S
A
models
Canada
models
r
1g
mm
in
FU
models
Canada
models
Tightening
torque
kg
m
ft
lb
ET
6
Stan
rd
Hot
type
Cold
type
S
aridard
Hot
type
Cold
type
CHECKING
AND
REPLACING
SPARK
PLUGS
I
Remove
and
clean
plugs
in
a
sand
blast
cleaner
Inspect
each
spark
plug
Make
sure
that
they
are
of
the
specifi
ed
heat
range
2
Inspect
insulator
for
cracks
or
chips
Check
both
center
and
ground
electrodes
3
If
they
are
excessively
worn
re
place
with
new
spark
plugs
4
Replace
spark
plugs
in
accordance
with
the
maintenance
schedule
BP
ES
ll
L46PW
l
BP4E
ll
L47PW
ll
BP7ES
ll
BP6ES
ll
L44PW
II
L4
PW
11
BP5
EQ
13
L46PM
13
BP4EQ
13
L47PM
13
BP6EQ
13
L45PM
13
BP7EQ
13
L44PM
13
BPR5ES
BPR4ES
BPR6ES
1
0
to
1
1
LQ39
to
0
043
l
l
to
1
3
0
043
to
0
051
0
8
to
0
9
0
031
to
0
035
1
5
to
i
6
P
to
14