DODGE RAM 2002 Service Repair Manual
Manufacturer: DODGE, Model Year: 2002, Model line: RAM, Model: DODGE RAM 2002Pages: 2255, PDF Size: 62.07 MB
Page 1891 of 2255
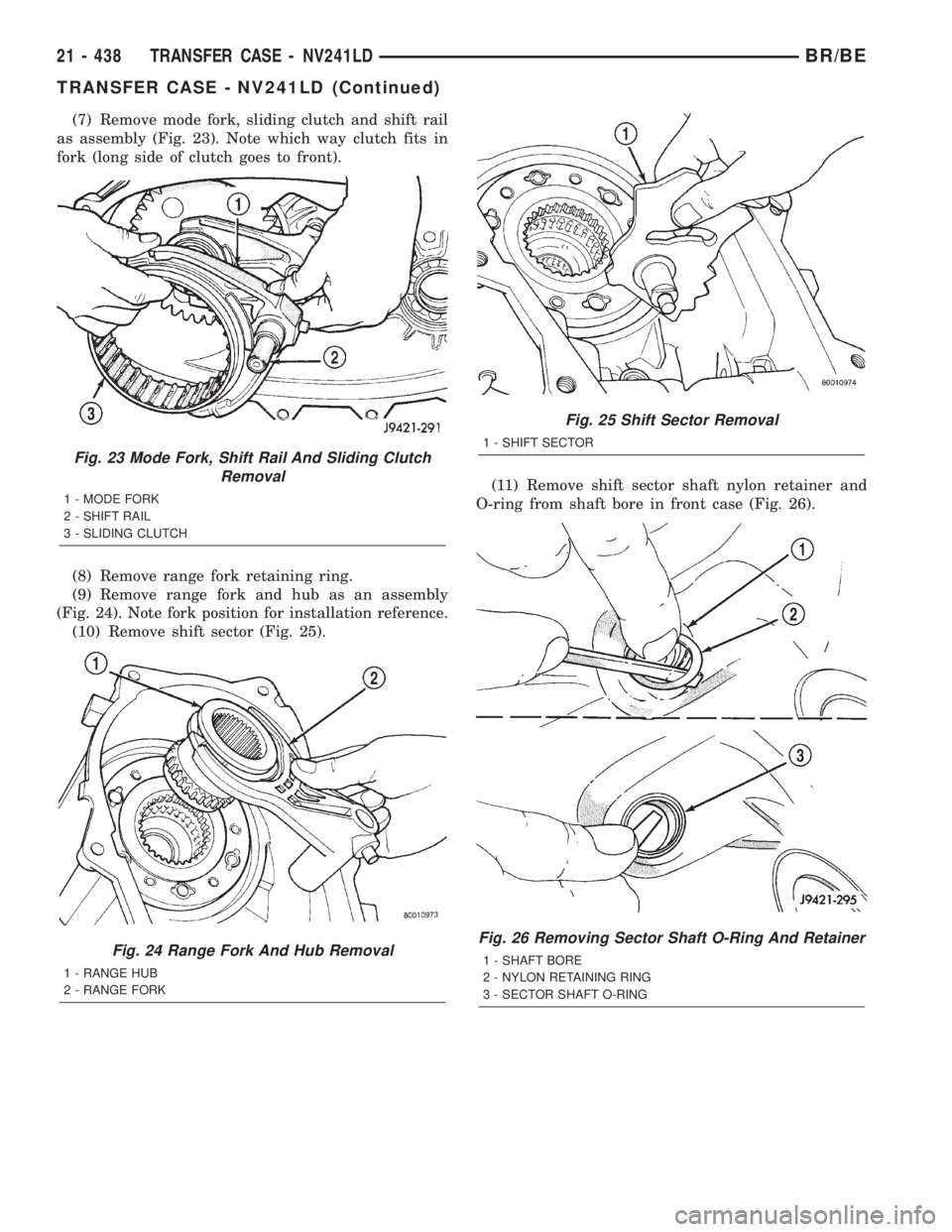
(7) Remove mode fork, sliding clutch and shift rail
as assembly (Fig. 23). Note which way clutch fits in
fork (long side of clutch goes to front).
(8) Remove range fork retaining ring.
(9) Remove range fork and hub as an assembly
(Fig. 24). Note fork position for installation reference.
(10) Remove shift sector (Fig. 25).(11) Remove shift sector shaft nylon retainer and
O-ring from shaft bore in front case (Fig. 26).
Fig. 23 Mode Fork, Shift Rail And Sliding Clutch
Removal
1 - MODE FORK
2 - SHIFT RAIL
3 - SLIDING CLUTCH
Fig. 24 Range Fork And Hub Removal
1 - RANGE HUB
2 - RANGE FORK
Fig. 25 Shift Sector Removal
1 - SHIFT SECTOR
Fig. 26 Removing Sector Shaft O-Ring And Retainer
1 - SHAFT BORE
2 - NYLON RETAINING RING
3 - SECTOR SHAFT O-RING
21 - 438 TRANSFER CASE - NV241LDBR/BE
TRANSFER CASE - NV241LD (Continued)
Page 1892 of 2255
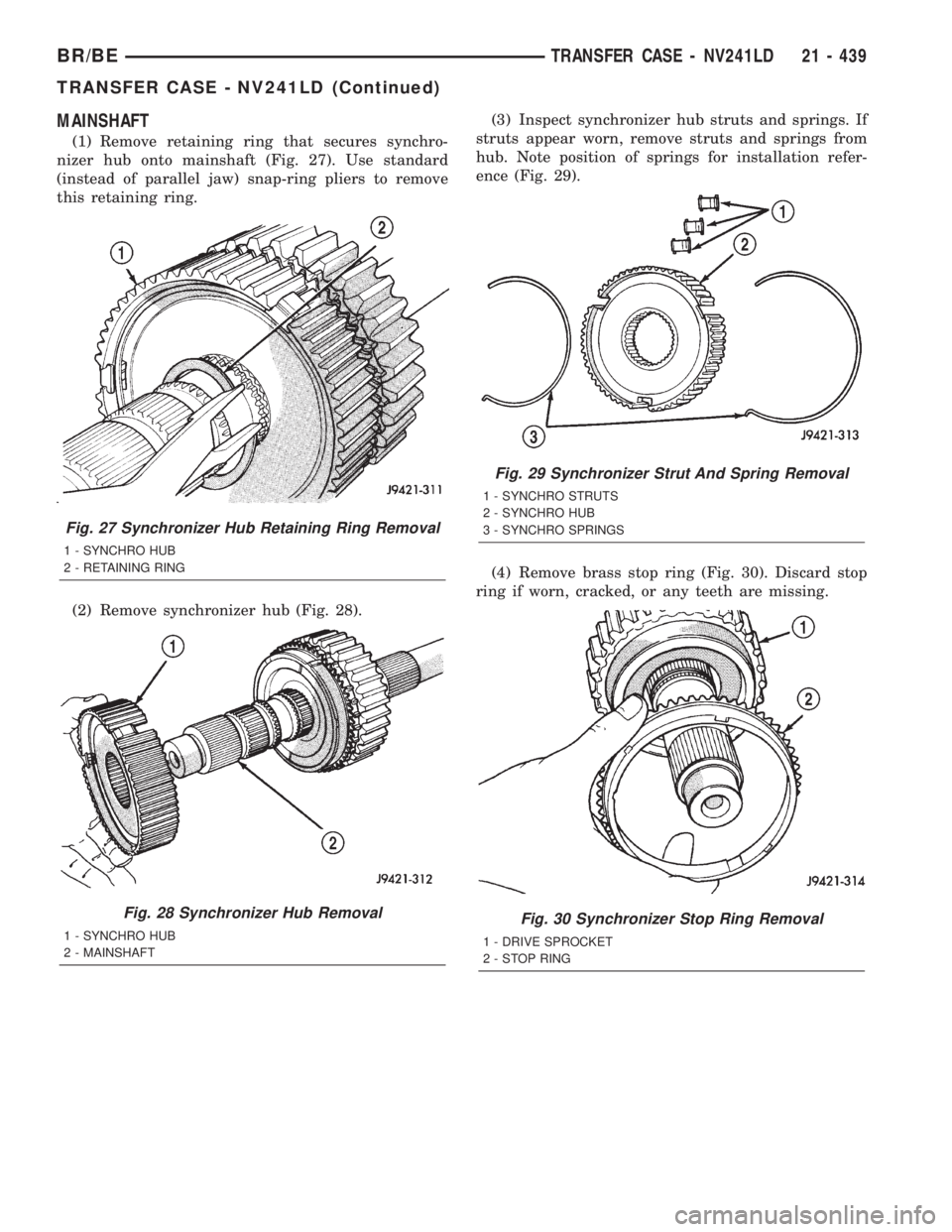
MAINSHAFT
(1) Remove retaining ring that secures synchro-
nizer hub onto mainshaft (Fig. 27). Use standard
(instead of parallel jaw) snap-ring pliers to remove
this retaining ring.
(2) Remove synchronizer hub (Fig. 28).(3) Inspect synchronizer hub struts and springs. If
struts appear worn, remove struts and springs from
hub. Note position of springs for installation refer-
ence (Fig. 29).
(4) Remove brass stop ring (Fig. 30). Discard stop
ring if worn, cracked, or any teeth are missing.
Fig. 27 Synchronizer Hub Retaining Ring Removal
1 - SYNCHRO HUB
2 - RETAINING RING
Fig. 28 Synchronizer Hub Removal
1 - SYNCHRO HUB
2 - MAINSHAFT
Fig. 29 Synchronizer Strut And Spring Removal
1 - SYNCHRO STRUTS
2 - SYNCHRO HUB
3 - SYNCHRO SPRINGS
Fig. 30 Synchronizer Stop Ring Removal
1 - DRIVE SPROCKET
2 - STOP RING
BR/BETRANSFER CASE - NV241LD 21 - 439
TRANSFER CASE - NV241LD (Continued)
Page 1893 of 2255
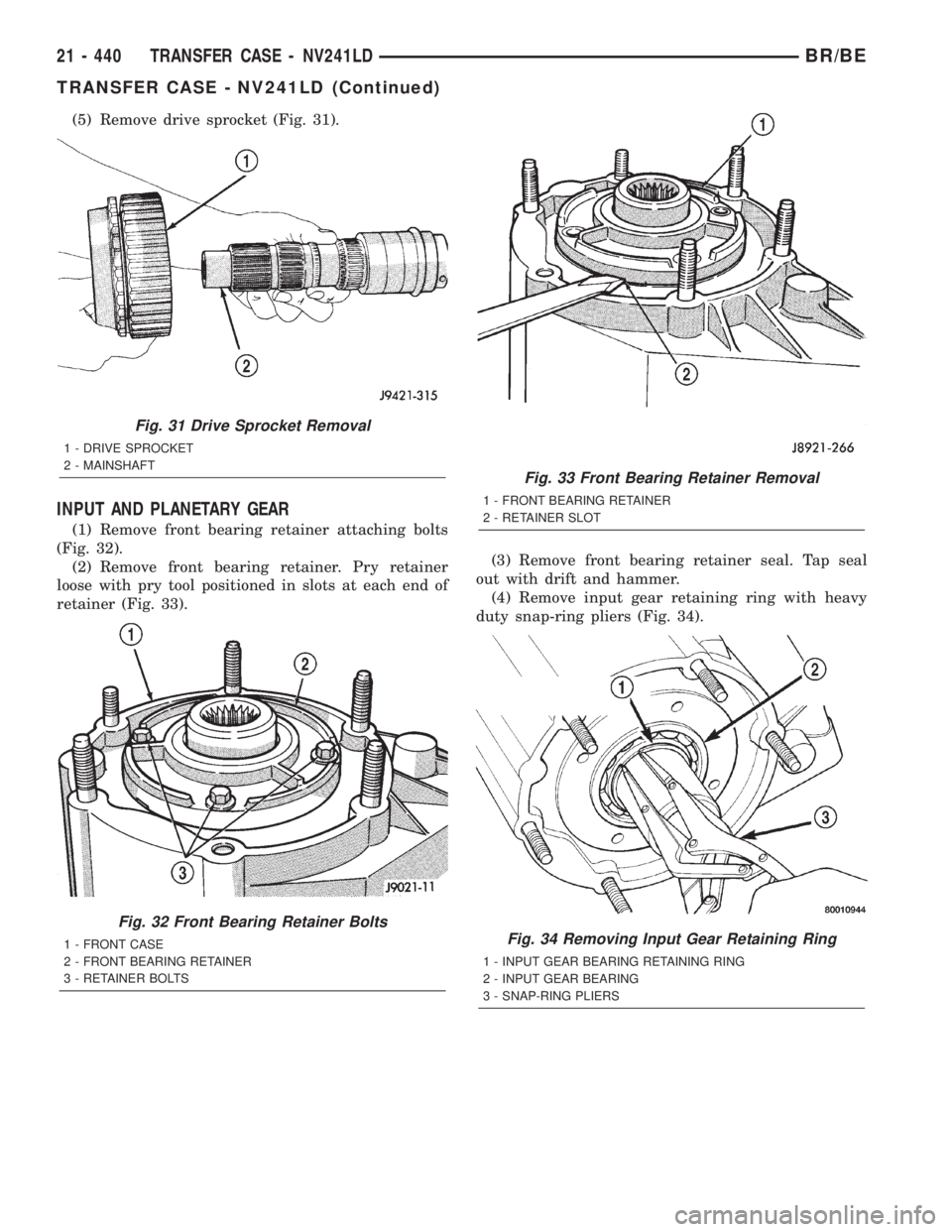
(5) Remove drive sprocket (Fig. 31).
INPUT AND PLANETARY GEAR
(1) Remove front bearing retainer attaching bolts
(Fig. 32).
(2) Remove front bearing retainer. Pry retainer
loose with pry tool positioned in slots at each end of
retainer (Fig. 33).(3) Remove front bearing retainer seal. Tap seal
out with drift and hammer.
(4) Remove input gear retaining ring with heavy
duty snap-ring pliers (Fig. 34).
Fig. 31 Drive Sprocket Removal
1 - DRIVE SPROCKET
2 - MAINSHAFT
Fig. 32 Front Bearing Retainer Bolts
1 - FRONT CASE
2 - FRONT BEARING RETAINER
3 - RETAINER BOLTS
Fig. 33 Front Bearing Retainer Removal
1 - FRONT BEARING RETAINER
2 - RETAINER SLOT
Fig. 34 Removing Input Gear Retaining Ring
1 - INPUT GEAR BEARING RETAINING RING
2 - INPUT GEAR BEARING
3 - SNAP-RING PLIERS
21 - 440 TRANSFER CASE - NV241LDBR/BE
TRANSFER CASE - NV241LD (Continued)
Page 1894 of 2255
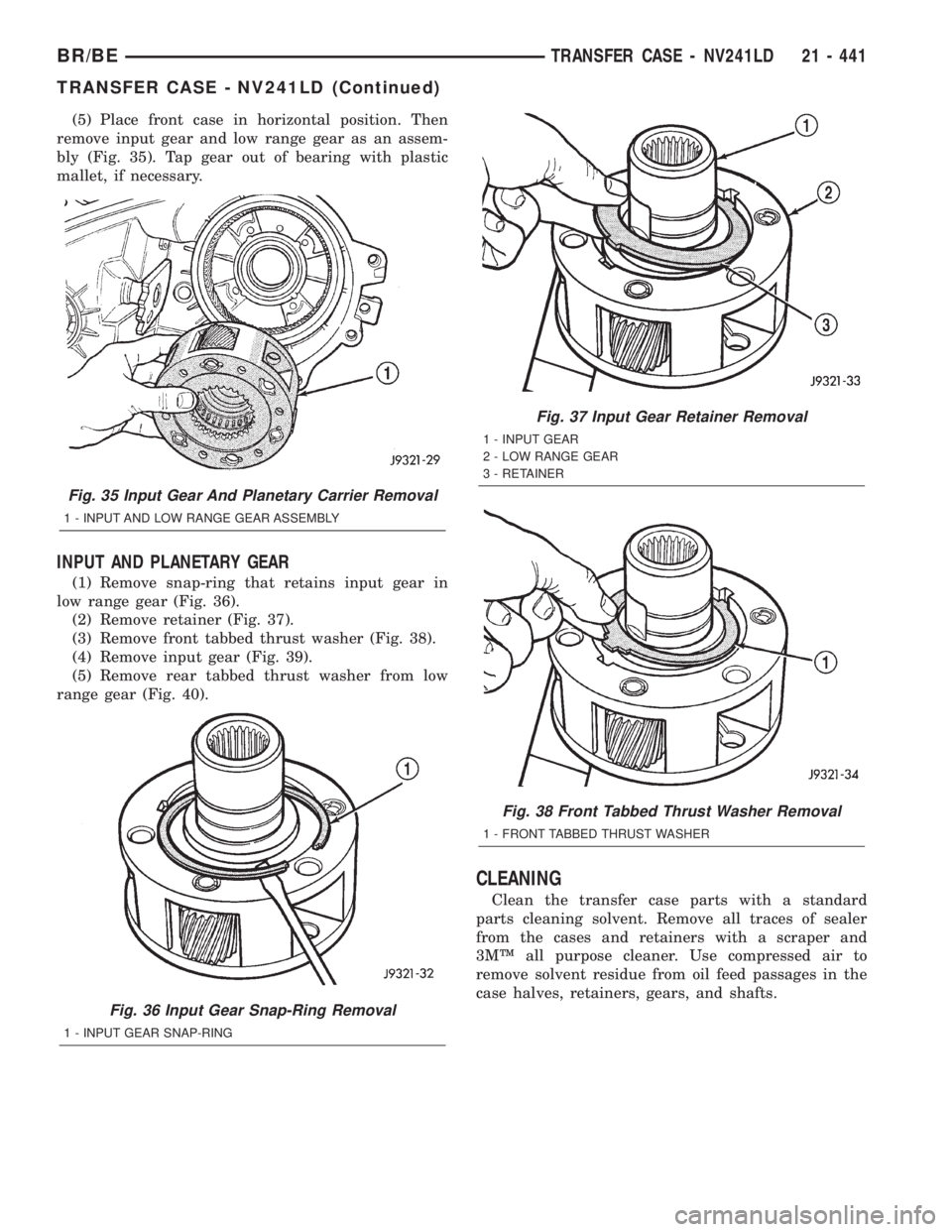
(5) Place front case in horizontal position. Then
remove input gear and low range gear as an assem-
bly (Fig. 35). Tap gear out of bearing with plastic
mallet, if necessary.
INPUT AND PLANETARY GEAR
(1) Remove snap-ring that retains input gear in
low range gear (Fig. 36).
(2) Remove retainer (Fig. 37).
(3) Remove front tabbed thrust washer (Fig. 38).
(4) Remove input gear (Fig. 39).
(5) Remove rear tabbed thrust washer from low
range gear (Fig. 40).
CLEANING
Clean the transfer case parts with a standard
parts cleaning solvent. Remove all traces of sealer
from the cases and retainers with a scraper and
3MŸ all purpose cleaner. Use compressed air to
remove solvent residue from oil feed passages in the
case halves, retainers, gears, and shafts.
Fig. 35 Input Gear And Planetary Carrier Removal
1 - INPUT AND LOW RANGE GEAR ASSEMBLY
Fig. 36 Input Gear Snap-Ring Removal
1 - INPUT GEAR SNAP-RING
Fig. 37 Input Gear Retainer Removal
1 - INPUT GEAR
2 - LOW RANGE GEAR
3 - RETAINER
Fig. 38 Front Tabbed Thrust Washer Removal
1 - FRONT TABBED THRUST WASHER
BR/BETRANSFER CASE - NV241LD 21 - 441
TRANSFER CASE - NV241LD (Continued)
Page 1895 of 2255
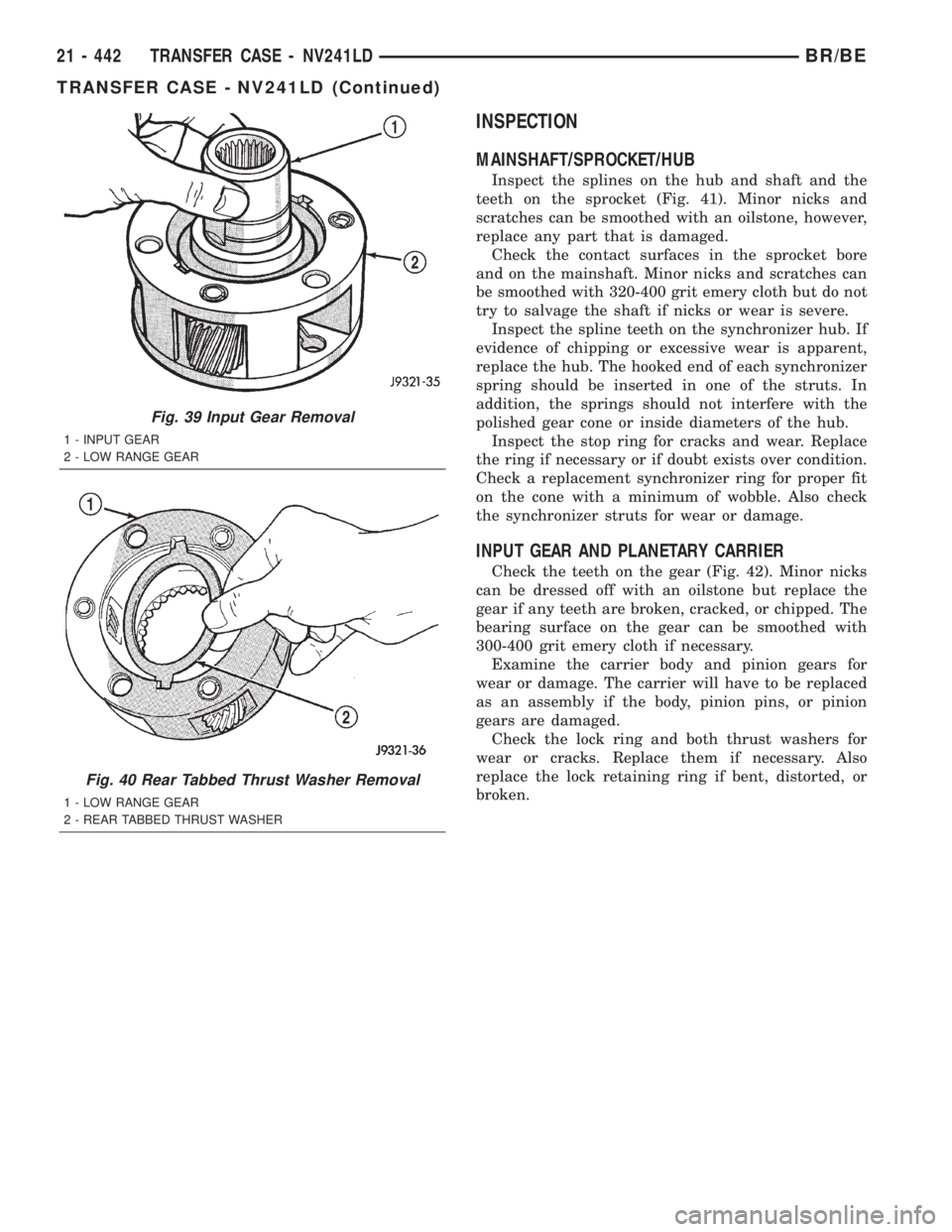
INSPECTION
MAINSHAFT/SPROCKET/HUB
Inspect the splines on the hub and shaft and the
teeth on the sprocket (Fig. 41). Minor nicks and
scratches can be smoothed with an oilstone, however,
replace any part that is damaged.
Check the contact surfaces in the sprocket bore
and on the mainshaft. Minor nicks and scratches can
be smoothed with 320-400 grit emery cloth but do not
try to salvage the shaft if nicks or wear is severe.
Inspect the spline teeth on the synchronizer hub. If
evidence of chipping or excessive wear is apparent,
replace the hub. The hooked end of each synchronizer
spring should be inserted in one of the struts. In
addition, the springs should not interfere with the
polished gear cone or inside diameters of the hub.
Inspect the stop ring for cracks and wear. Replace
the ring if necessary or if doubt exists over condition.
Check a replacement synchronizer ring for proper fit
on the cone with a minimum of wobble. Also check
the synchronizer struts for wear or damage.
INPUT GEAR AND PLANETARY CARRIER
Check the teeth on the gear (Fig. 42). Minor nicks
can be dressed off with an oilstone but replace the
gear if any teeth are broken, cracked, or chipped. The
bearing surface on the gear can be smoothed with
300-400 grit emery cloth if necessary.
Examine the carrier body and pinion gears for
wear or damage. The carrier will have to be replaced
as an assembly if the body, pinion pins, or pinion
gears are damaged.
Check the lock ring and both thrust washers for
wear or cracks. Replace them if necessary. Also
replace the lock retaining ring if bent, distorted, or
broken.
Fig. 39 Input Gear Removal
1 - INPUT GEAR
2 - LOW RANGE GEAR
Fig. 40 Rear Tabbed Thrust Washer Removal
1 - LOW RANGE GEAR
2 - REAR TABBED THRUST WASHER
21 - 442 TRANSFER CASE - NV241LDBR/BE
TRANSFER CASE - NV241LD (Continued)
Page 1896 of 2255
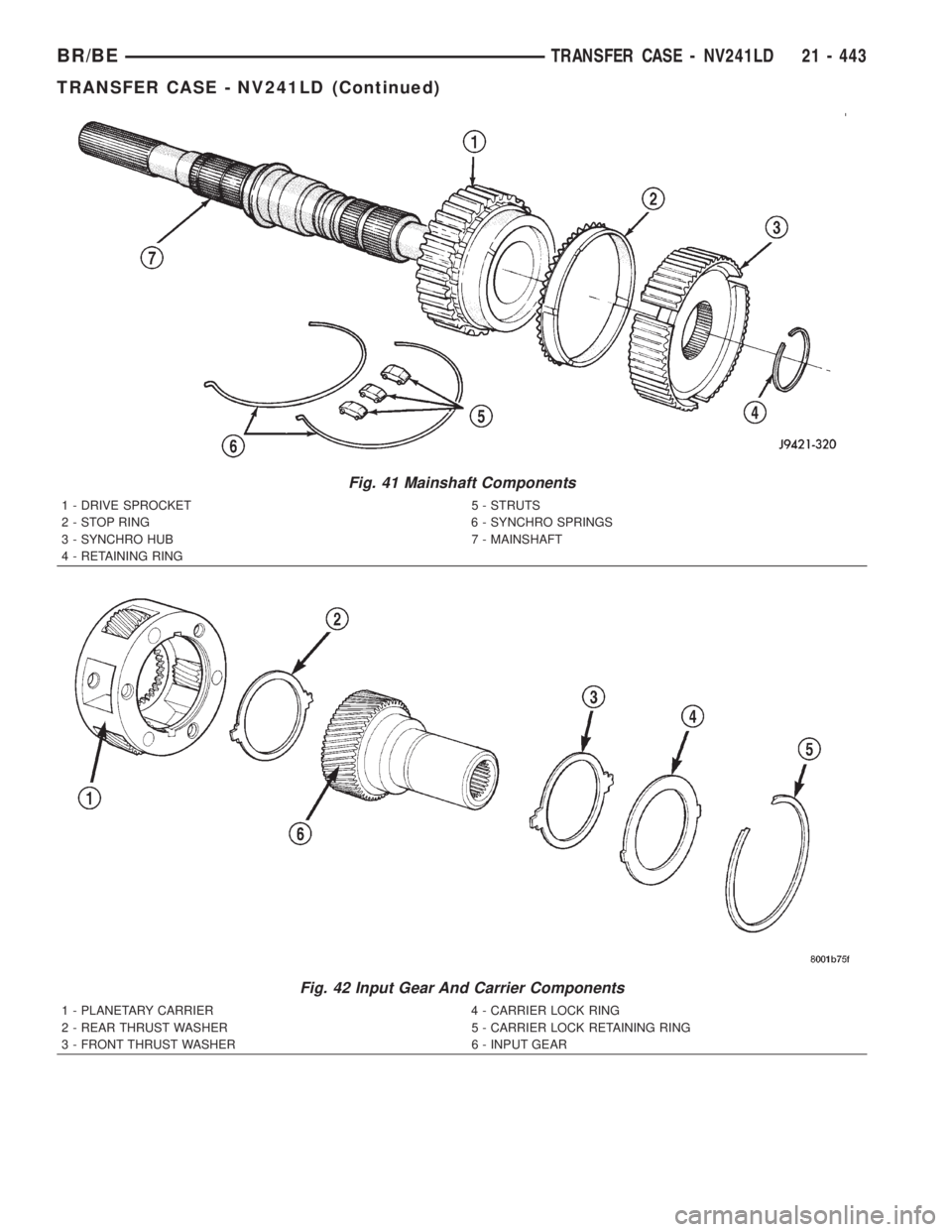
Fig. 41 Mainshaft Components
1 - DRIVE SPROCKET 5 - STRUTS
2 - STOP RING 6 - SYNCHRO SPRINGS
3 - SYNCHRO HUB 7 - MAINSHAFT
4 - RETAINING RING
Fig. 42 Input Gear And Carrier Components
1 - PLANETARY CARRIER 4 - CARRIER LOCK RING
2 - REAR THRUST WASHER 5 - CARRIER LOCK RETAINING RING
3 - FRONT THRUST WASHER 6 - INPUT GEAR
BR/BETRANSFER CASE - NV241LD 21 - 443
TRANSFER CASE - NV241LD (Continued)
Page 1897 of 2255
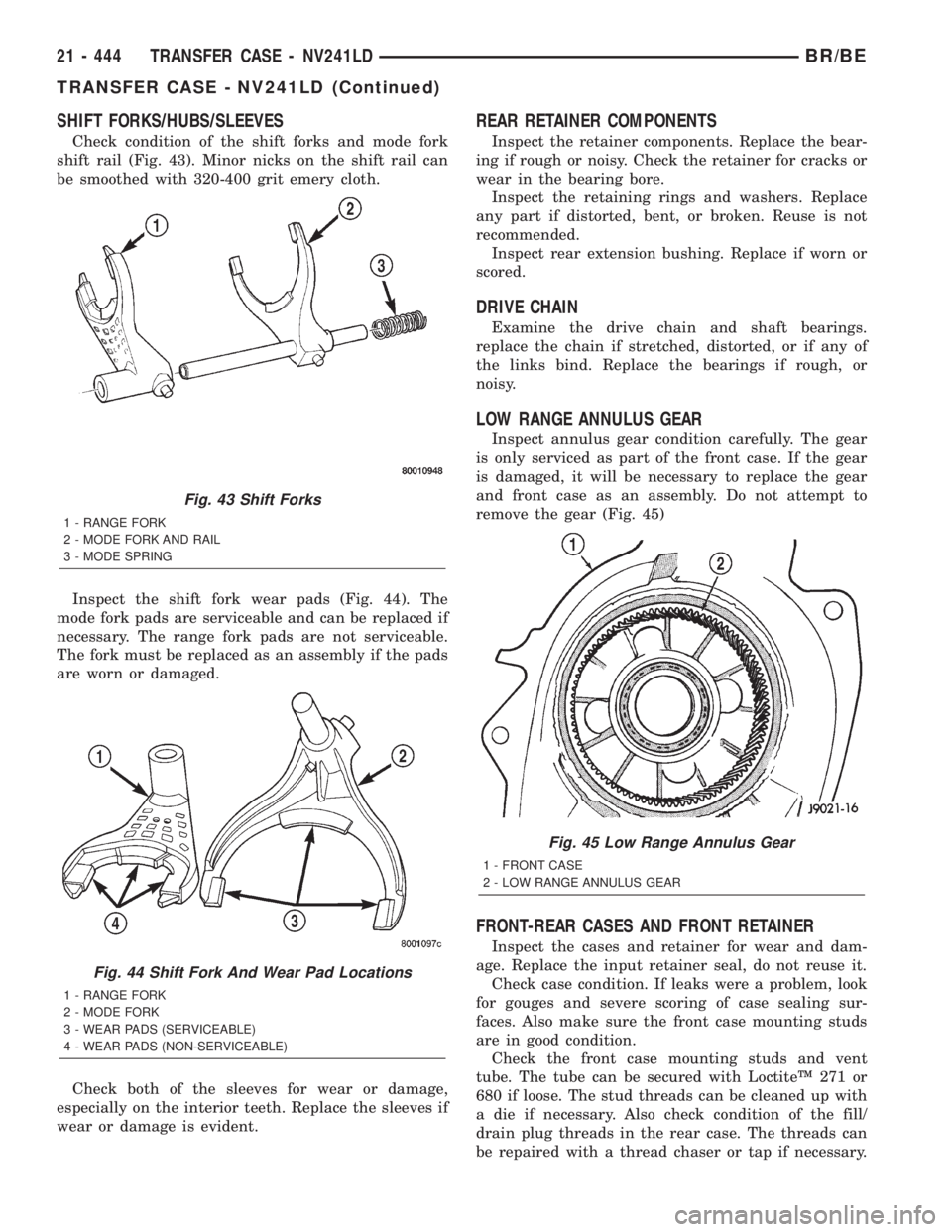
SHIFT FORKS/HUBS/SLEEVES
Check condition of the shift forks and mode fork
shift rail (Fig. 43). Minor nicks on the shift rail can
be smoothed with 320-400 grit emery cloth.
Inspect the shift fork wear pads (Fig. 44). The
mode fork pads are serviceable and can be replaced if
necessary. The range fork pads are not serviceable.
The fork must be replaced as an assembly if the pads
are worn or damaged.
Check both of the sleeves for wear or damage,
especially on the interior teeth. Replace the sleeves if
wear or damage is evident.
REAR RETAINER COMPONENTS
Inspect the retainer components. Replace the bear-
ing if rough or noisy. Check the retainer for cracks or
wear in the bearing bore.
Inspect the retaining rings and washers. Replace
any part if distorted, bent, or broken. Reuse is not
recommended.
Inspect rear extension bushing. Replace if worn or
scored.
DRIVE CHAIN
Examine the drive chain and shaft bearings.
replace the chain if stretched, distorted, or if any of
the links bind. Replace the bearings if rough, or
noisy.
LOW RANGE ANNULUS GEAR
Inspect annulus gear condition carefully. The gear
is only serviced as part of the front case. If the gear
is damaged, it will be necessary to replace the gear
and front case as an assembly. Do not attempt to
remove the gear (Fig. 45)
FRONT-REAR CASES AND FRONT RETAINER
Inspect the cases and retainer for wear and dam-
age. Replace the input retainer seal, do not reuse it.
Check case condition. If leaks were a problem, look
for gouges and severe scoring of case sealing sur-
faces. Also make sure the front case mounting studs
are in good condition.
Check the front case mounting studs and vent
tube. The tube can be secured with LoctiteŸ 271 or
680 if loose. The stud threads can be cleaned up with
a die if necessary. Also check condition of the fill/
drain plug threads in the rear case. The threads can
be repaired with a thread chaser or tap if necessary.
Fig. 43 Shift Forks
1 - RANGE FORK
2 - MODE FORK AND RAIL
3 - MODE SPRING
Fig. 44 Shift Fork And Wear Pad Locations
1 - RANGE FORK
2 - MODE FORK
3 - WEAR PADS (SERVICEABLE)
4 - WEAR PADS (NON-SERVICEABLE)
Fig. 45 Low Range Annulus Gear
1 - FRONT CASE
2 - LOW RANGE ANNULUS GEAR
21 - 444 TRANSFER CASE - NV241LDBR/BE
TRANSFER CASE - NV241LD (Continued)
Page 1898 of 2255
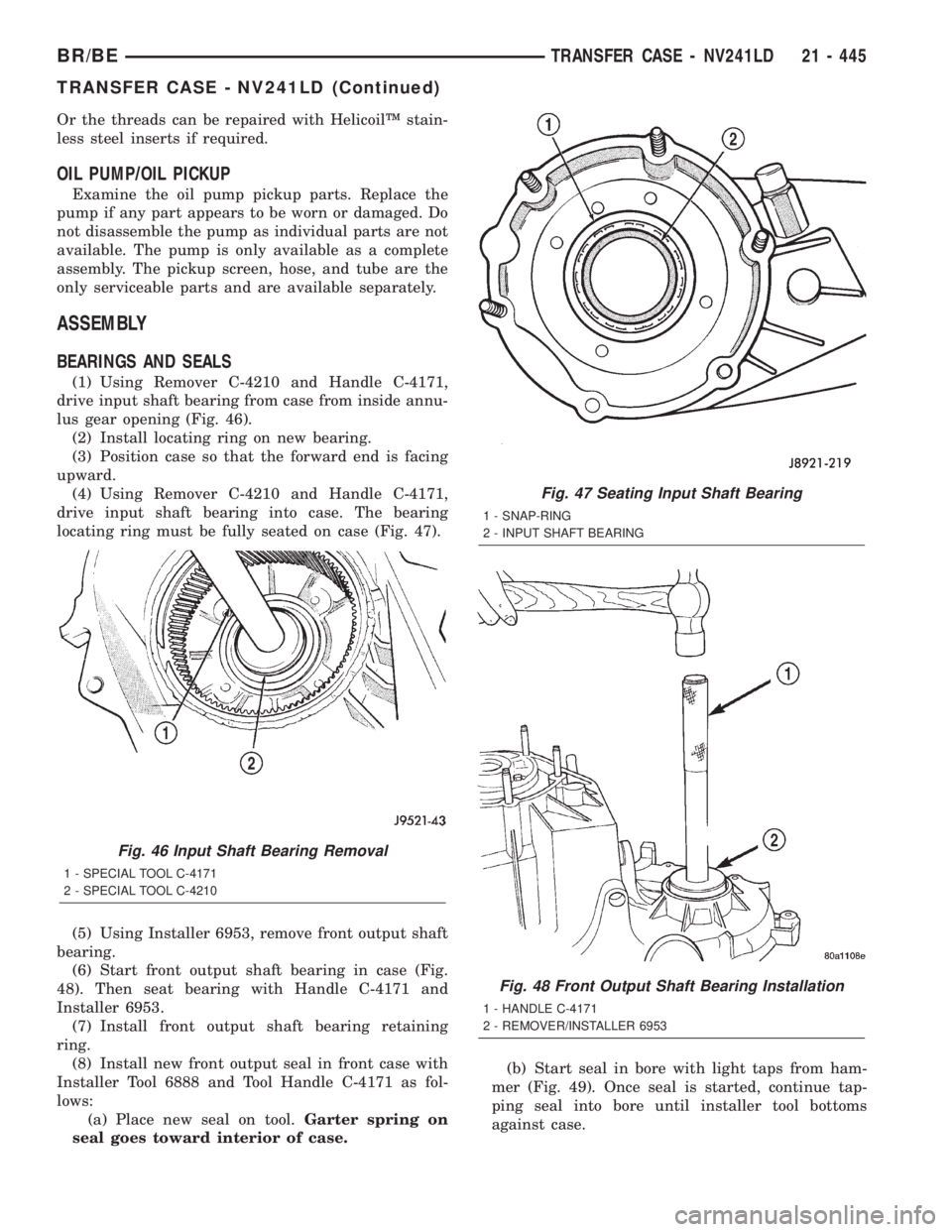
Or the threads can be repaired with HelicoilŸ stain-
less steel inserts if required.
OIL PUMP/OIL PICKUP
Examine the oil pump pickup parts. Replace the
pump if any part appears to be worn or damaged. Do
not disassemble the pump as individual parts are not
available. The pump is only available as a complete
assembly. The pickup screen, hose, and tube are the
only serviceable parts and are available separately.
ASSEMBLY
BEARINGS AND SEALS
(1) Using Remover C-4210 and Handle C-4171,
drive input shaft bearing from case from inside annu-
lus gear opening (Fig. 46).
(2) Install locating ring on new bearing.
(3) Position case so that the forward end is facing
upward.
(4) Using Remover C-4210 and Handle C-4171,
drive input shaft bearing into case. The bearing
locating ring must be fully seated on case (Fig. 47).
(5) Using Installer 6953, remove front output shaft
bearing.
(6) Start front output shaft bearing in case (Fig.
48). Then seat bearing with Handle C-4171 and
Installer 6953.
(7) Install front output shaft bearing retaining
ring.
(8) Install new front output seal in front case with
Installer Tool 6888 and Tool Handle C-4171 as fol-
lows:
(a) Place new seal on tool.Garter spring on
seal goes toward interior of case.(b) Start seal in bore with light taps from ham-
mer (Fig. 49). Once seal is started, continue tap-
ping seal into bore until installer tool bottoms
against case.
Fig. 46 Input Shaft Bearing Removal
1 - SPECIAL TOOL C-4171
2 - SPECIAL TOOL C-4210
Fig. 47 Seating Input Shaft Bearing
1 - SNAP-RING
2 - INPUT SHAFT BEARING
Fig. 48 Front Output Shaft Bearing Installation
1 - HANDLE C-4171
2 - REMOVER/INSTALLER 6953
BR/BETRANSFER CASE - NV241LD 21 - 445
TRANSFER CASE - NV241LD (Continued)
Page 1899 of 2255
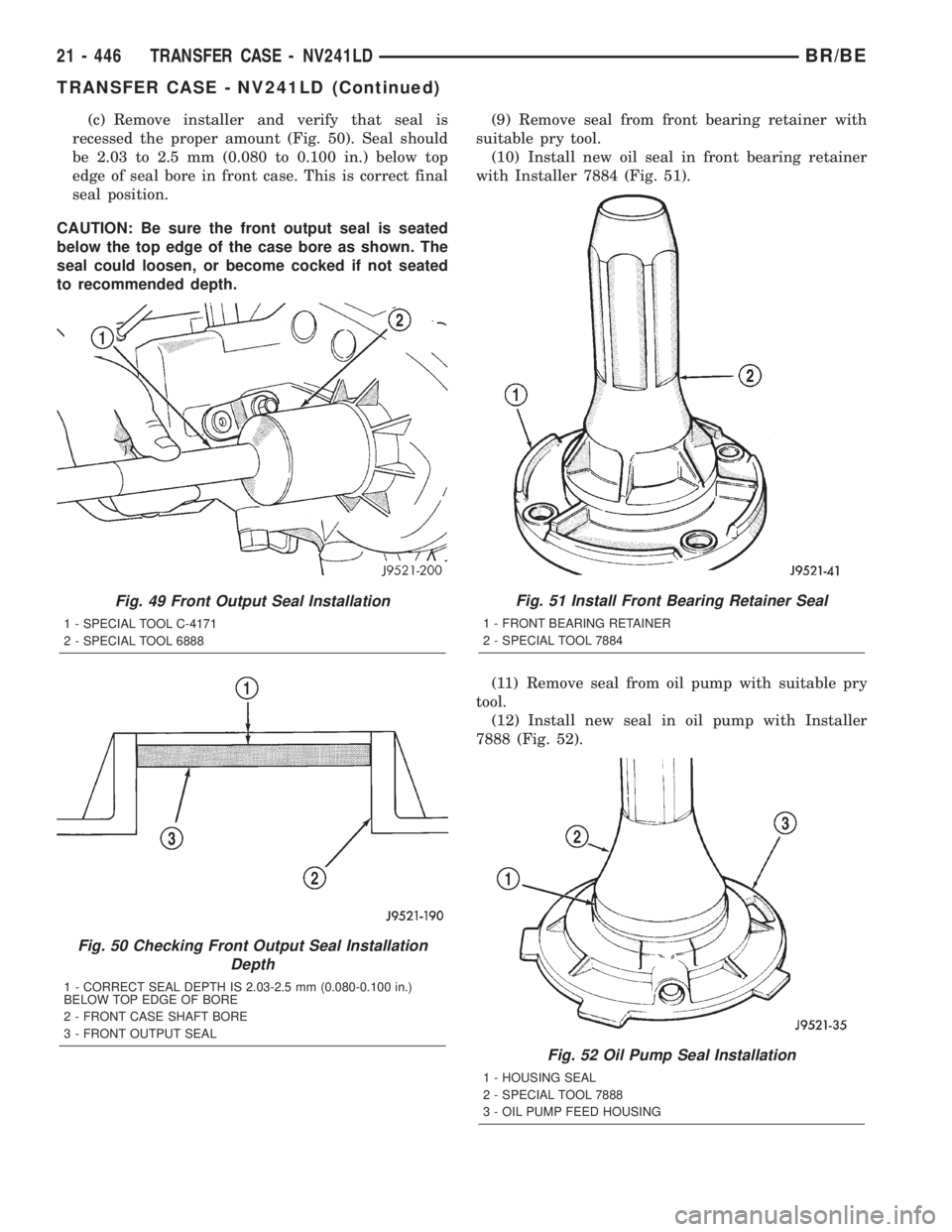
(c) Remove installer and verify that seal is
recessed the proper amount (Fig. 50). Seal should
be 2.03 to 2.5 mm (0.080 to 0.100 in.) below top
edge of seal bore in front case. This is correct final
seal position.
CAUTION: Be sure the front output seal is seated
below the top edge of the case bore as shown. The
seal could loosen, or become cocked if not seated
to recommended depth.(9) Remove seal from front bearing retainer with
suitable pry tool.
(10) Install new oil seal in front bearing retainer
with Installer 7884 (Fig. 51).
(11) Remove seal from oil pump with suitable pry
tool.
(12) Install new seal in oil pump with Installer
7888 (Fig. 52).
Fig. 49 Front Output Seal Installation
1 - SPECIAL TOOL C-4171
2 - SPECIAL TOOL 6888
Fig. 50 Checking Front Output Seal Installation
Depth
1 - CORRECT SEAL DEPTH IS 2.03-2.5 mm (0.080-0.100 in.)
BELOW TOP EDGE OF BORE
2 - FRONT CASE SHAFT BORE
3 - FRONT OUTPUT SEAL
Fig. 51 Install Front Bearing Retainer Seal
1 - FRONT BEARING RETAINER
2 - SPECIAL TOOL 7884
Fig. 52 Oil Pump Seal Installation
1 - HOUSING SEAL
2 - SPECIAL TOOL 7888
3 - OIL PUMP FEED HOUSING
21 - 446 TRANSFER CASE - NV241LDBR/BE
TRANSFER CASE - NV241LD (Continued)
Page 1900 of 2255
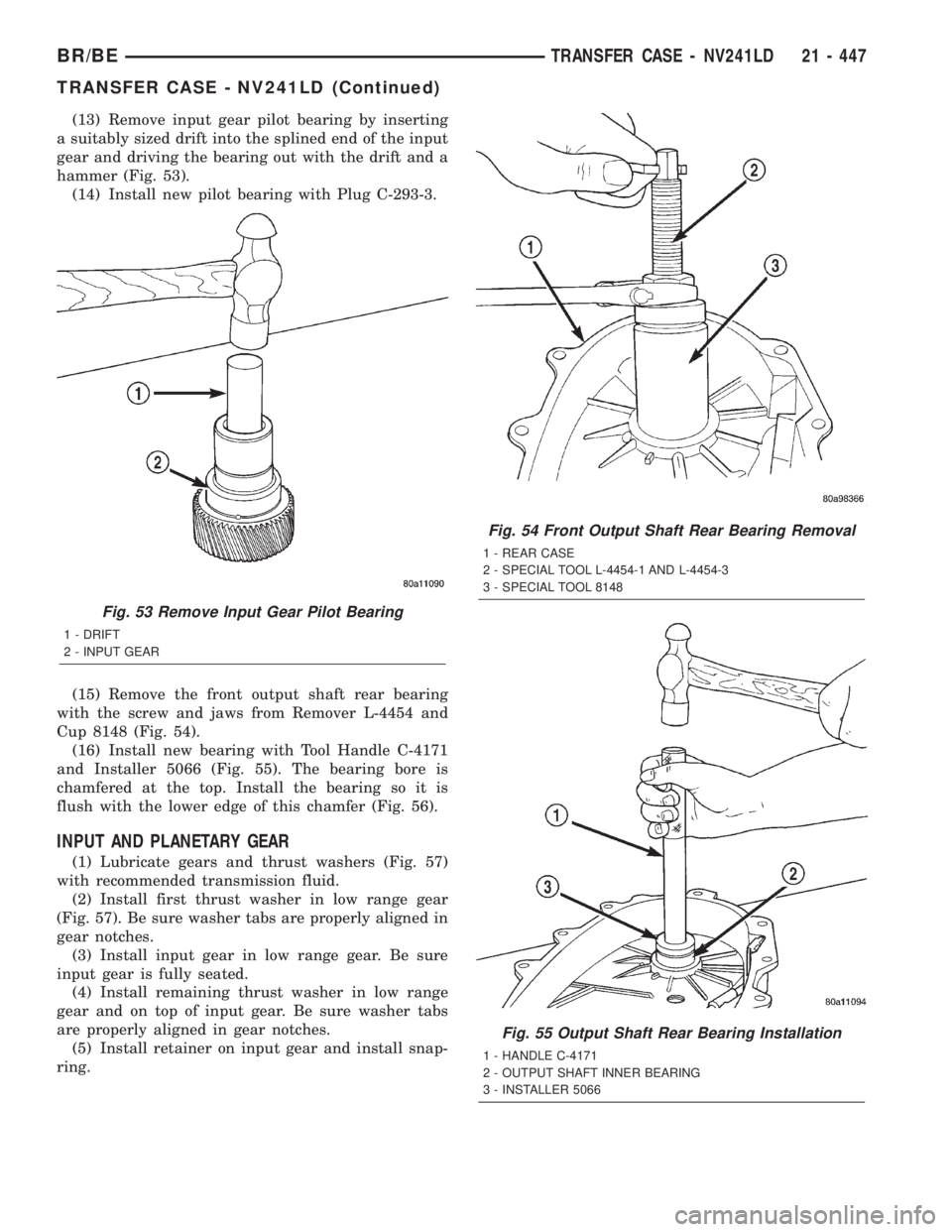
(13) Remove input gear pilot bearing by inserting
a suitably sized drift into the splined end of the input
gear and driving the bearing out with the drift and a
hammer (Fig. 53).
(14) Install new pilot bearing with Plug C-293-3.
(15) Remove the front output shaft rear bearing
with the screw and jaws from Remover L-4454 and
Cup 8148 (Fig. 54).
(16) Install new bearing with Tool Handle C-4171
and Installer 5066 (Fig. 55). The bearing bore is
chamfered at the top. Install the bearing so it is
flush with the lower edge of this chamfer (Fig. 56).
INPUT AND PLANETARY GEAR
(1) Lubricate gears and thrust washers (Fig. 57)
with recommended transmission fluid.
(2) Install first thrust washer in low range gear
(Fig. 57). Be sure washer tabs are properly aligned in
gear notches.
(3) Install input gear in low range gear. Be sure
input gear is fully seated.
(4) Install remaining thrust washer in low range
gear and on top of input gear. Be sure washer tabs
are properly aligned in gear notches.
(5) Install retainer on input gear and install snap-
ring.
Fig. 53 Remove Input Gear Pilot Bearing
1 - DRIFT
2 - INPUT GEAR
Fig. 54 Front Output Shaft Rear Bearing Removal
1 - REAR CASE
2 - SPECIAL TOOL L-4454-1 AND L-4454-3
3 - SPECIAL TOOL 8148
Fig. 55 Output Shaft Rear Bearing Installation
1 - HANDLE C-4171
2 - OUTPUT SHAFT INNER BEARING
3 - INSTALLER 5066
BR/BETRANSFER CASE - NV241LD 21 - 447
TRANSFER CASE - NV241LD (Continued)