DODGE RAM 2002 Service Repair Manual
Manufacturer: DODGE, Model Year: 2002, Model line: RAM, Model: DODGE RAM 2002Pages: 2255, PDF Size: 62.07 MB
Page 1901 of 2255
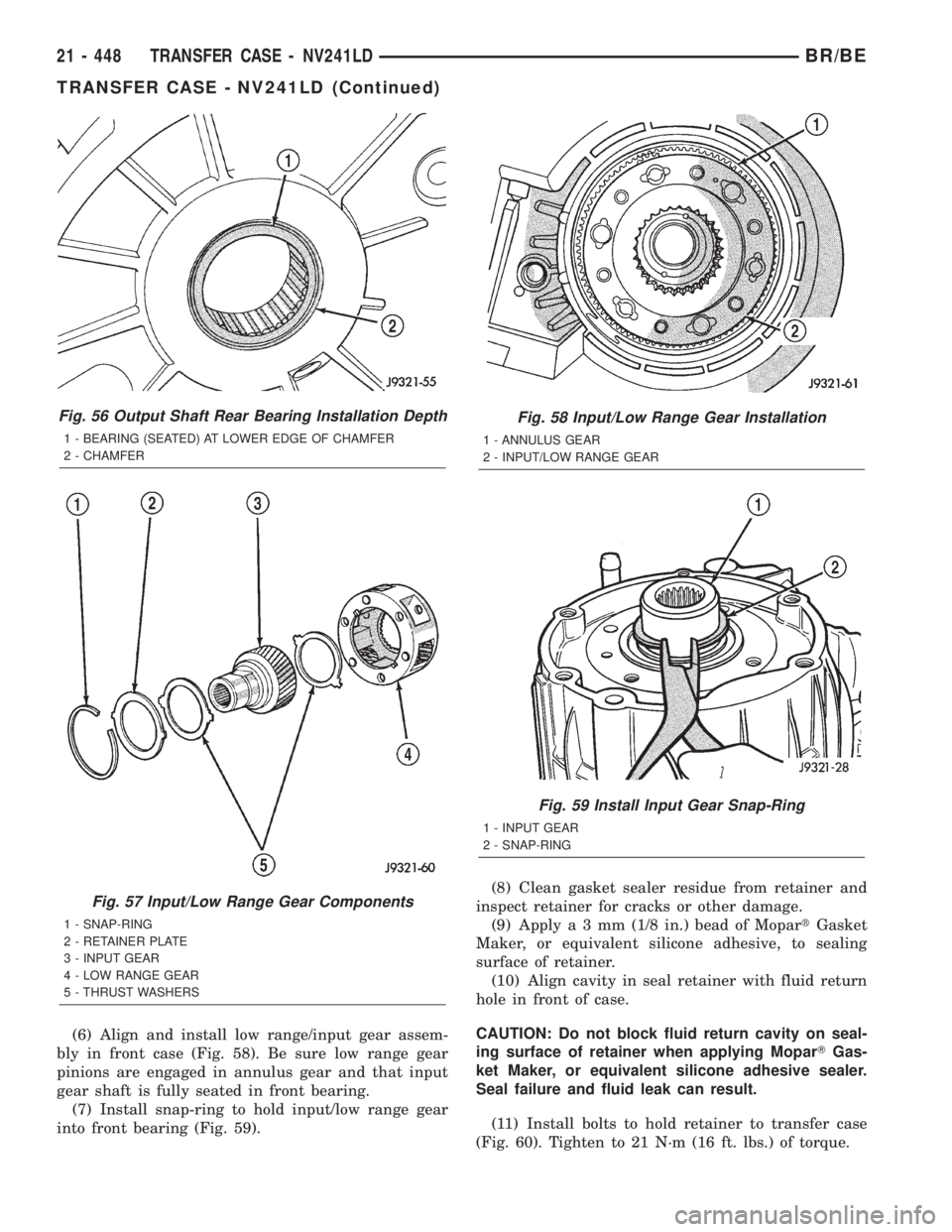
(6) Align and install low range/input gear assem-
bly in front case (Fig. 58). Be sure low range gear
pinions are engaged in annulus gear and that input
gear shaft is fully seated in front bearing.
(7) Install snap-ring to hold input/low range gear
into front bearing (Fig. 59).(8) Clean gasket sealer residue from retainer and
inspect retainer for cracks or other damage.
(9) Applya3mm(1/8 in.) bead of MopartGasket
Maker, or equivalent silicone adhesive, to sealing
surface of retainer.
(10) Align cavity in seal retainer with fluid return
hole in front of case.
CAUTION: Do not block fluid return cavity on seal-
ing surface of retainer when applying MoparTGas-
ket Maker, or equivalent silicone adhesive sealer.
Seal failure and fluid leak can result.
(11) Install bolts to hold retainer to transfer case
(Fig. 60). Tighten to 21 N´m (16 ft. lbs.) of torque.
Fig. 56 Output Shaft Rear Bearing Installation Depth
1 - BEARING (SEATED) AT LOWER EDGE OF CHAMFER
2 - CHAMFER
Fig. 57 Input/Low Range Gear Components
1 - SNAP-RING
2 - RETAINER PLATE
3 - INPUT GEAR
4 - LOW RANGE GEAR
5 - THRUST WASHERS
Fig. 58 Input/Low Range Gear Installation
1 - ANNULUS GEAR
2 - INPUT/LOW RANGE GEAR
Fig. 59 Install Input Gear Snap-Ring
1 - INPUT GEAR
2 - SNAP-RING
21 - 448 TRANSFER CASE - NV241LDBR/BE
TRANSFER CASE - NV241LD (Continued)
Page 1902 of 2255
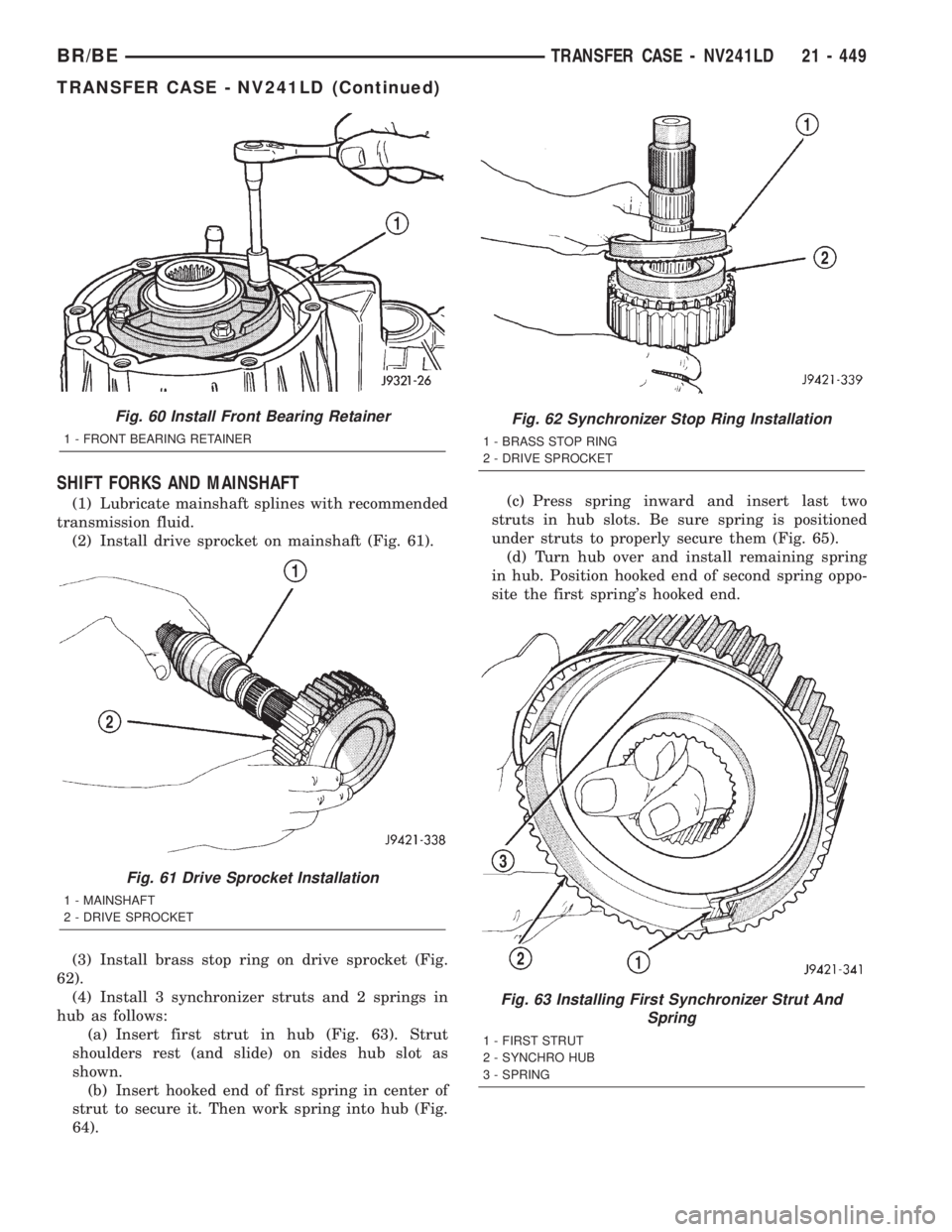
SHIFT FORKS AND MAINSHAFT
(1) Lubricate mainshaft splines with recommended
transmission fluid.
(2) Install drive sprocket on mainshaft (Fig. 61).
(3) Install brass stop ring on drive sprocket (Fig.
62).
(4) Install 3 synchronizer struts and 2 springs in
hub as follows:
(a) Insert first strut in hub (Fig. 63). Strut
shoulders rest (and slide) on sides hub slot as
shown.
(b) Insert hooked end of first spring in center of
strut to secure it. Then work spring into hub (Fig.
64).(c) Press spring inward and insert last two
struts in hub slots. Be sure spring is positioned
under struts to properly secure them (Fig. 65).
(d) Turn hub over and install remaining spring
in hub. Position hooked end of second spring oppo-
site the first spring's hooked end.
Fig. 60 Install Front Bearing Retainer
1 - FRONT BEARING RETAINER
Fig. 61 Drive Sprocket Installation
1 - MAINSHAFT
2 - DRIVE SPROCKET
Fig. 62 Synchronizer Stop Ring Installation
1 - BRASS STOP RING
2 - DRIVE SPROCKET
Fig. 63 Installing First Synchronizer Strut And
Spring
1 - FIRST STRUT
2 - SYNCHRO HUB
3 - SPRING
BR/BETRANSFER CASE - NV241LD 21 - 449
TRANSFER CASE - NV241LD (Continued)
Page 1903 of 2255
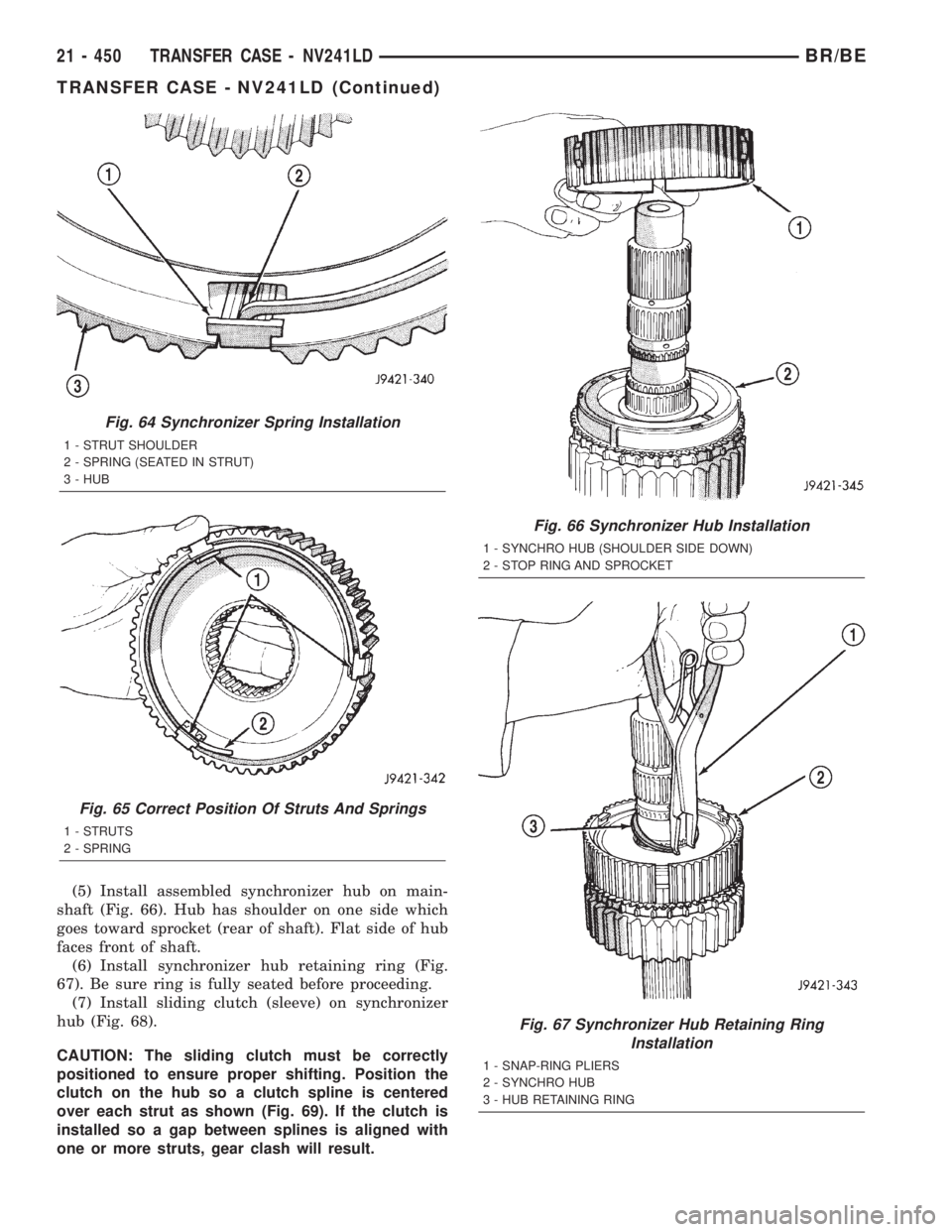
(5) Install assembled synchronizer hub on main-
shaft (Fig. 66). Hub has shoulder on one side which
goes toward sprocket (rear of shaft). Flat side of hub
faces front of shaft.
(6) Install synchronizer hub retaining ring (Fig.
67). Be sure ring is fully seated before proceeding.
(7) Install sliding clutch (sleeve) on synchronizer
hub (Fig. 68).
CAUTION: The sliding clutch must be correctly
positioned to ensure proper shifting. Position the
clutch on the hub so a clutch spline is centered
over each strut as shown (Fig. 69). If the clutch is
installed so a gap between splines is aligned with
one or more struts, gear clash will result.
Fig. 64 Synchronizer Spring Installation
1 - STRUT SHOULDER
2 - SPRING (SEATED IN STRUT)
3 - HUB
Fig. 65 Correct Position Of Struts And Springs
1 - STRUTS
2 - SPRING
Fig. 66 Synchronizer Hub Installation
1 - SYNCHRO HUB (SHOULDER SIDE DOWN)
2 - STOP RING AND SPROCKET
Fig. 67 Synchronizer Hub Retaining Ring
Installation
1 - SNAP-RING PLIERS
2 - SYNCHRO HUB
3 - HUB RETAINING RING
21 - 450 TRANSFER CASE - NV241LDBR/BE
TRANSFER CASE - NV241LD (Continued)
Page 1904 of 2255
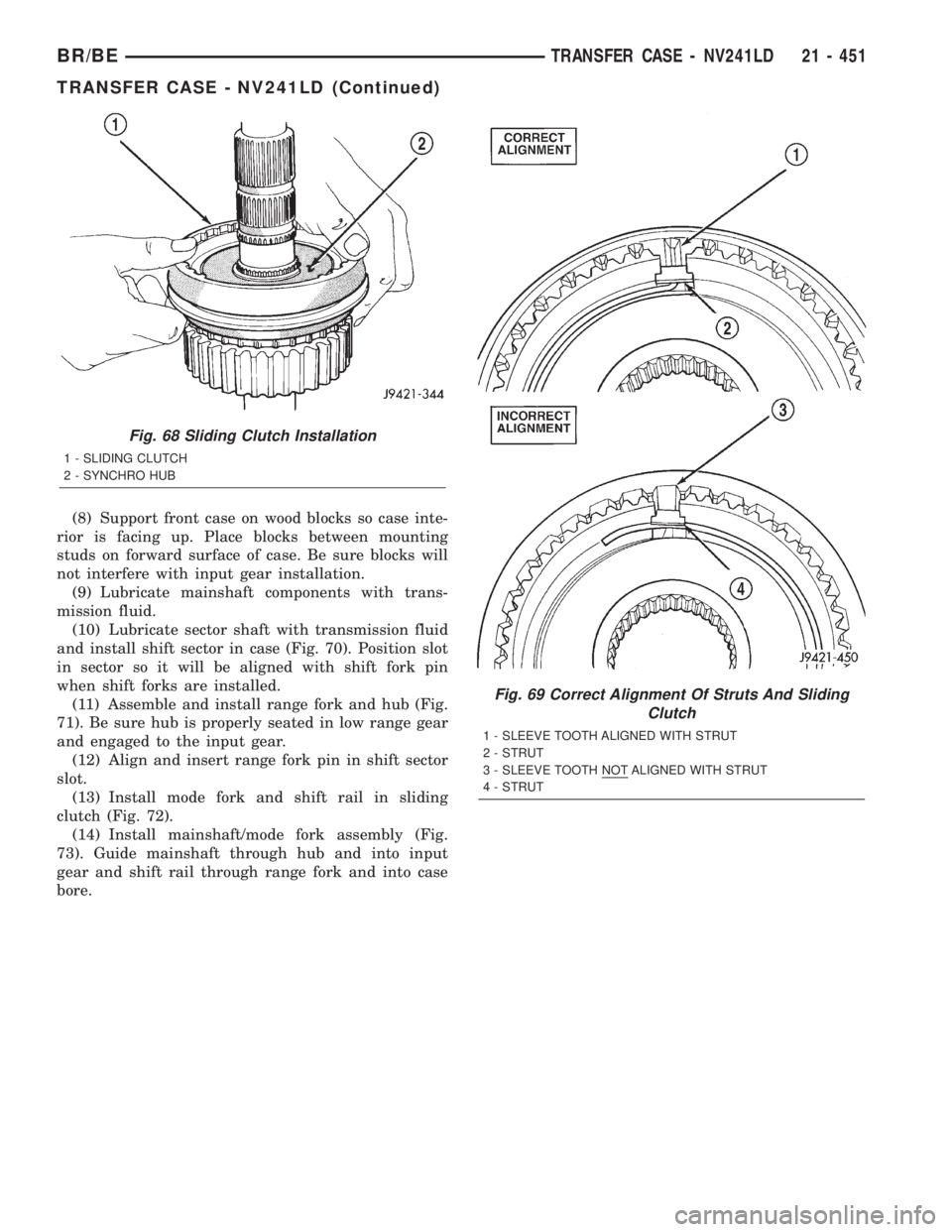
(8) Support front case on wood blocks so case inte-
rior is facing up. Place blocks between mounting
studs on forward surface of case. Be sure blocks will
not interfere with input gear installation.
(9) Lubricate mainshaft components with trans-
mission fluid.
(10) Lubricate sector shaft with transmission fluid
and install shift sector in case (Fig. 70). Position slot
in sector so it will be aligned with shift fork pin
when shift forks are installed.
(11) Assemble and install range fork and hub (Fig.
71). Be sure hub is properly seated in low range gear
and engaged to the input gear.
(12) Align and insert range fork pin in shift sector
slot.
(13) Install mode fork and shift rail in sliding
clutch (Fig. 72).
(14) Install mainshaft/mode fork assembly (Fig.
73). Guide mainshaft through hub and into input
gear and shift rail through range fork and into case
bore.
Fig. 68 Sliding Clutch Installation
1 - SLIDING CLUTCH
2 - SYNCHRO HUB
Fig. 69 Correct Alignment Of Struts And Sliding
Clutch
1 - SLEEVE TOOTH ALIGNED WITH STRUT
2 - STRUT
3 - SLEEVE TOOTH NOT ALIGNED WITH STRUT
4 - STRUT
BR/BETRANSFER CASE - NV241LD 21 - 451
TRANSFER CASE - NV241LD (Continued)
Page 1905 of 2255
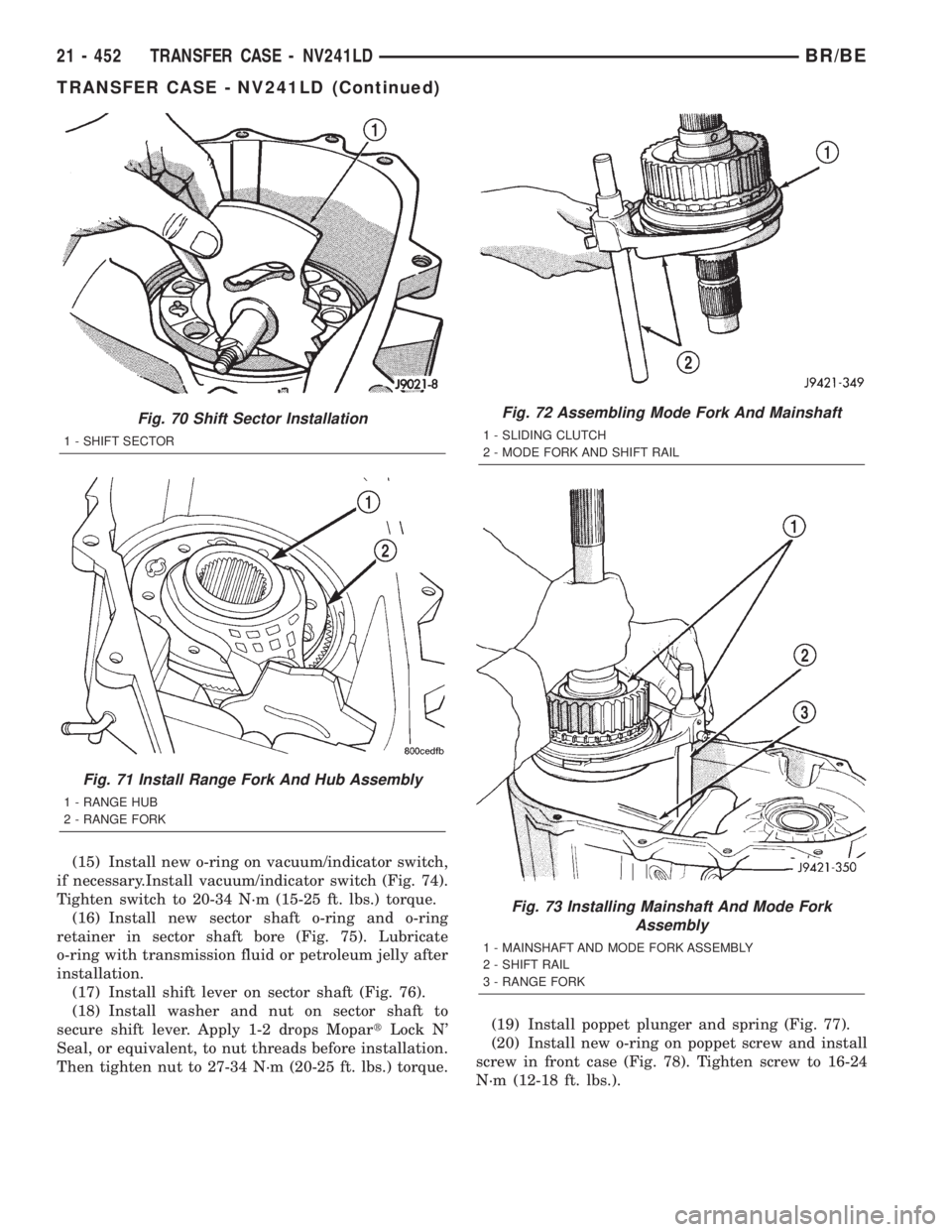
(15) Install new o-ring on vacuum/indicator switch,
if necessary.Install vacuum/indicator switch (Fig. 74).
Tighten switch to 20-34 N´m (15-25 ft. lbs.) torque.
(16) Install new sector shaft o-ring and o-ring
retainer in sector shaft bore (Fig. 75). Lubricate
o-ring with transmission fluid or petroleum jelly after
installation.
(17) Install shift lever on sector shaft (Fig. 76).
(18) Install washer and nut on sector shaft to
secure shift lever. Apply 1-2 drops MopartLock N'
Seal, or equivalent, to nut threads before installation.
Then tighten nut to 27-34 N´m (20-25 ft. lbs.) torque.(19) Install poppet plunger and spring (Fig. 77).
(20) Install new o-ring on poppet screw and install
screw in front case (Fig. 78). Tighten screw to 16-24
N´m (12-18 ft. lbs.).
Fig. 70 Shift Sector Installation
1 - SHIFT SECTOR
Fig. 71 Install Range Fork And Hub Assembly
1 - RANGE HUB
2 - RANGE FORK
Fig. 72 Assembling Mode Fork And Mainshaft
1 - SLIDING CLUTCH
2 - MODE FORK AND SHIFT RAIL
Fig. 73 Installing Mainshaft And Mode Fork
Assembly
1 - MAINSHAFT AND MODE FORK ASSEMBLY
2 - SHIFT RAIL
3 - RANGE FORK
21 - 452 TRANSFER CASE - NV241LDBR/BE
TRANSFER CASE - NV241LD (Continued)
Page 1906 of 2255
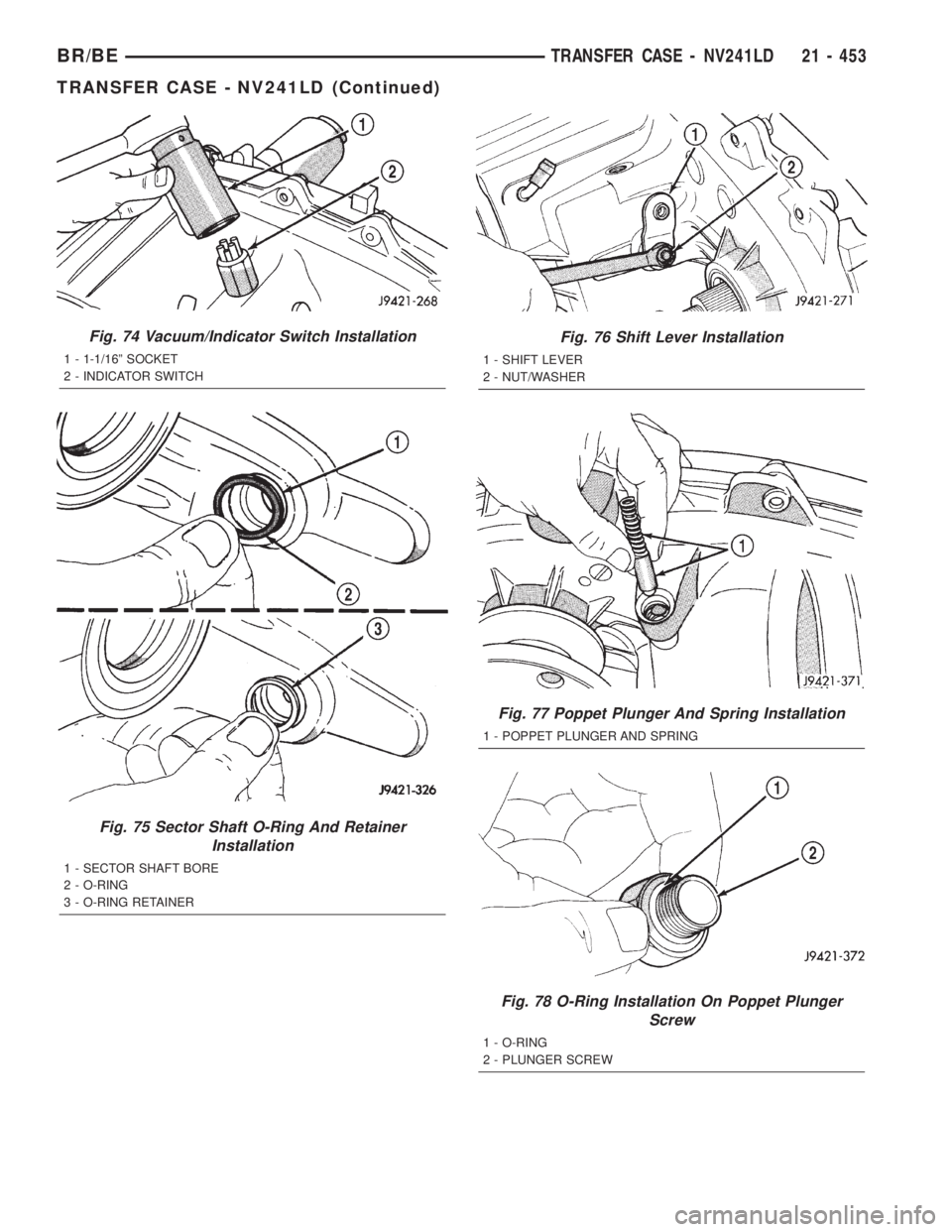
Fig. 74 Vacuum/Indicator Switch Installation
1 - 1-1/16º SOCKET
2 - INDICATOR SWITCH
Fig. 75 Sector Shaft O-Ring And Retainer
Installation
1 - SECTOR SHAFT BORE
2 - O-RING
3 - O-RING RETAINER
Fig. 76 Shift Lever Installation
1 - SHIFT LEVER
2 - NUT/WASHER
Fig. 77 Poppet Plunger And Spring Installation
1 - POPPET PLUNGER AND SPRING
Fig. 78 O-Ring Installation On Poppet Plunger
Screw
1 - O-RING
2 - PLUNGER SCREW
BR/BETRANSFER CASE - NV241LD 21 - 453
TRANSFER CASE - NV241LD (Continued)
Page 1907 of 2255
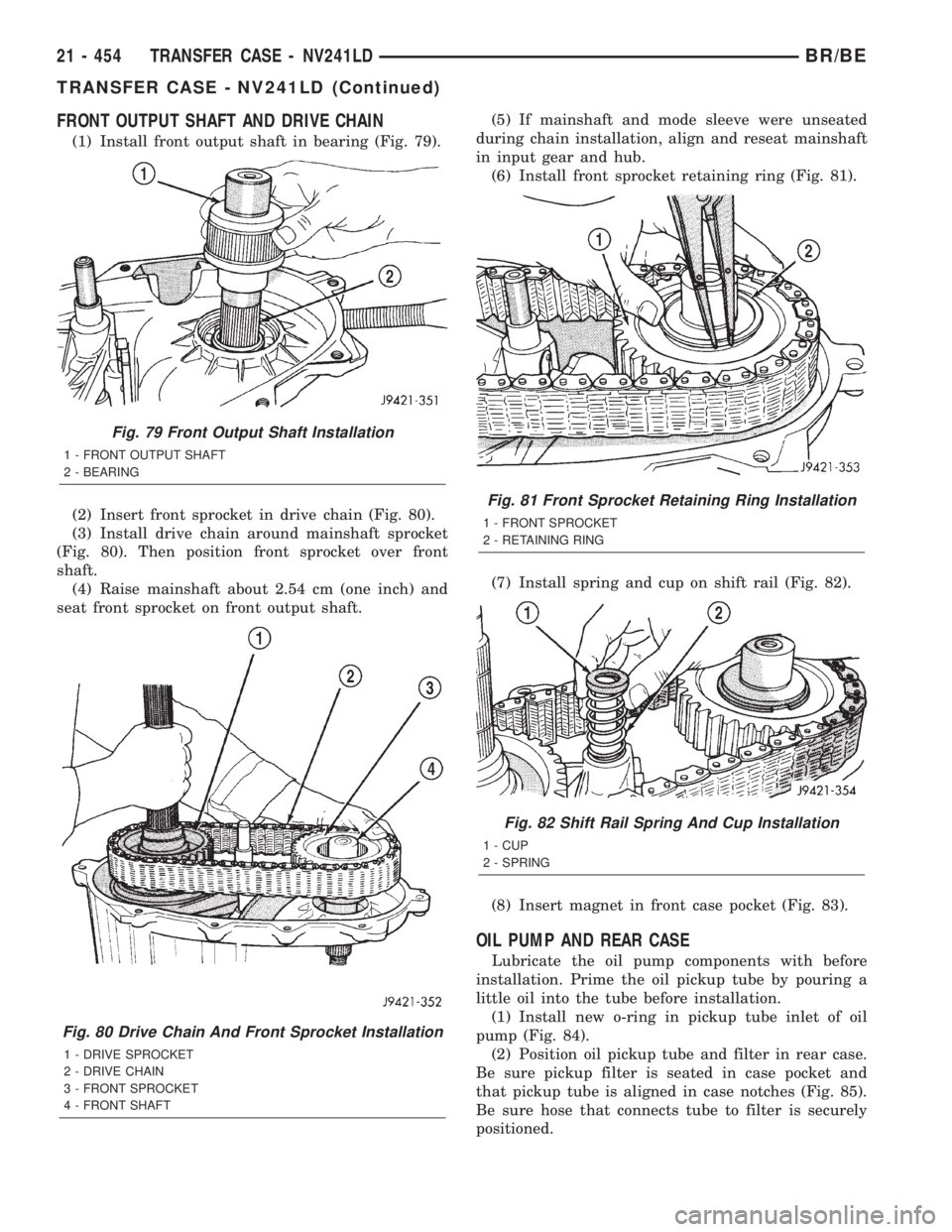
FRONT OUTPUT SHAFT AND DRIVE CHAIN
(1) Install front output shaft in bearing (Fig. 79).
(2) Insert front sprocket in drive chain (Fig. 80).
(3) Install drive chain around mainshaft sprocket
(Fig. 80). Then position front sprocket over front
shaft.
(4) Raise mainshaft about 2.54 cm (one inch) and
seat front sprocket on front output shaft.(5) If mainshaft and mode sleeve were unseated
during chain installation, align and reseat mainshaft
in input gear and hub.
(6) Install front sprocket retaining ring (Fig. 81).
(7) Install spring and cup on shift rail (Fig. 82).
(8) Insert magnet in front case pocket (Fig. 83).
OIL PUMP AND REAR CASE
Lubricate the oil pump components with before
installation. Prime the oil pickup tube by pouring a
little oil into the tube before installation.
(1) Install new o-ring in pickup tube inlet of oil
pump (Fig. 84).
(2) Position oil pickup tube and filter in rear case.
Be sure pickup filter is seated in case pocket and
that pickup tube is aligned in case notches (Fig. 85).
Be sure hose that connects tube to filter is securely
positioned.
Fig. 79 Front Output Shaft Installation
1 - FRONT OUTPUT SHAFT
2 - BEARING
Fig. 80 Drive Chain And Front Sprocket Installation
1 - DRIVE SPROCKET
2 - DRIVE CHAIN
3 - FRONT SPROCKET
4 - FRONT SHAFT
Fig. 81 Front Sprocket Retaining Ring Installation
1 - FRONT SPROCKET
2 - RETAINING RING
Fig. 82 Shift Rail Spring And Cup Installation
1 - CUP
2 - SPRING
21 - 454 TRANSFER CASE - NV241LDBR/BE
TRANSFER CASE - NV241LD (Continued)
Page 1908 of 2255
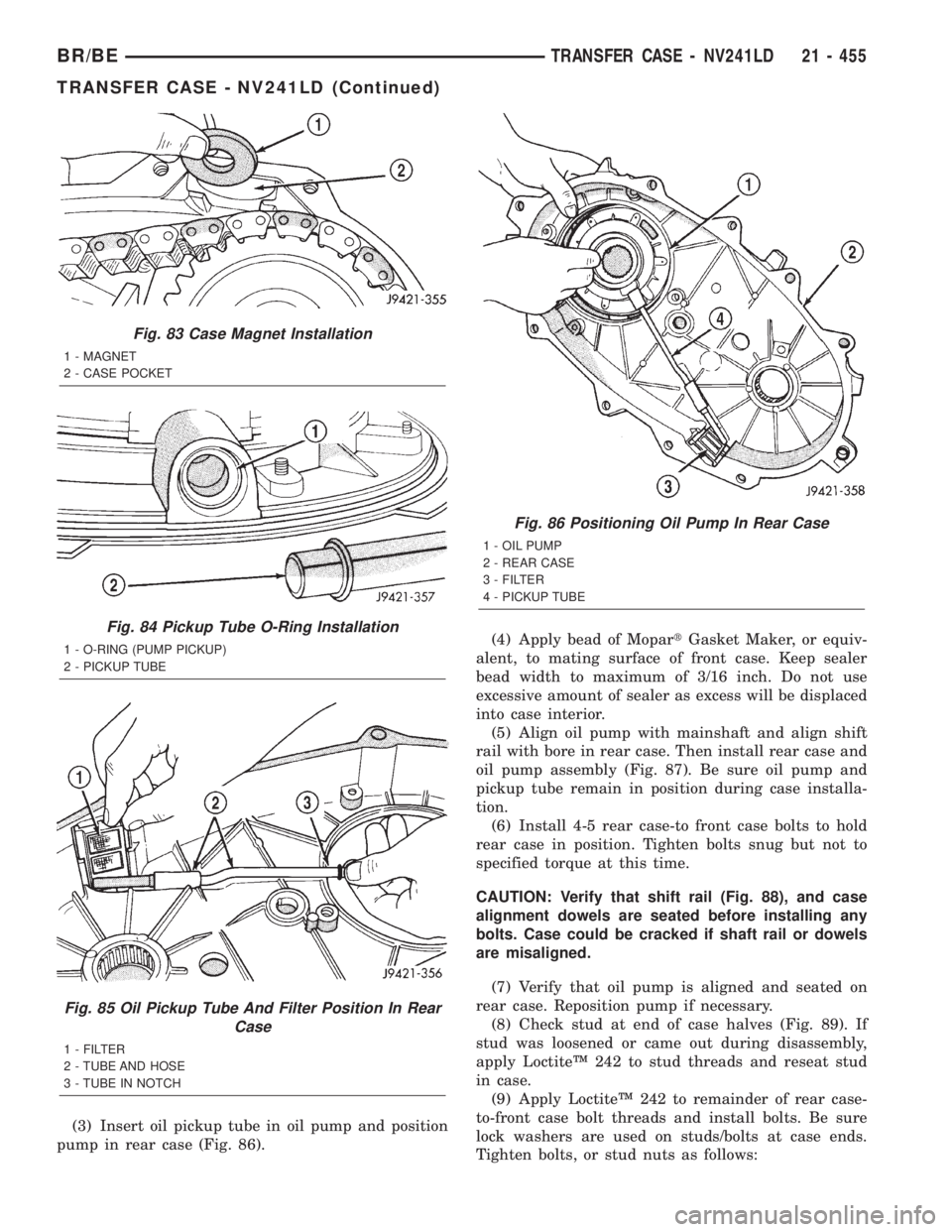
(3) Insert oil pickup tube in oil pump and position
pump in rear case (Fig. 86).(4) Apply bead of MopartGasket Maker, or equiv-
alent, to mating surface of front case. Keep sealer
bead width to maximum of 3/16 inch. Do not use
excessive amount of sealer as excess will be displaced
into case interior.
(5) Align oil pump with mainshaft and align shift
rail with bore in rear case. Then install rear case and
oil pump assembly (Fig. 87). Be sure oil pump and
pickup tube remain in position during case installa-
tion.
(6) Install 4-5 rear case-to front case bolts to hold
rear case in position. Tighten bolts snug but not to
specified torque at this time.
CAUTION: Verify that shift rail (Fig. 88), and case
alignment dowels are seated before installing any
bolts. Case could be cracked if shaft rail or dowels
are misaligned.
(7) Verify that oil pump is aligned and seated on
rear case. Reposition pump if necessary.
(8) Check stud at end of case halves (Fig. 89). If
stud was loosened or came out during disassembly,
apply LoctiteŸ 242 to stud threads and reseat stud
in case.
(9) Apply LoctiteŸ 242 to remainder of rear case-
to-front case bolt threads and install bolts. Be sure
lock washers are used on studs/bolts at case ends.
Tighten bolts, or stud nuts as follows:
Fig. 83 Case Magnet Installation
1 - MAGNET
2 - CASE POCKET
Fig. 84 Pickup Tube O-Ring Installation
1 - O-RING (PUMP PICKUP)
2 - PICKUP TUBE
Fig. 85 Oil Pickup Tube And Filter Position In Rear
Case
1 - FILTER
2 - TUBE AND HOSE
3 - TUBE IN NOTCH
Fig. 86 Positioning Oil Pump In Rear Case
1 - OIL PUMP
2 - REAR CASE
3 - FILTER
4 - PICKUP TUBE
BR/BETRANSFER CASE - NV241LD 21 - 455
TRANSFER CASE - NV241LD (Continued)
Page 1909 of 2255
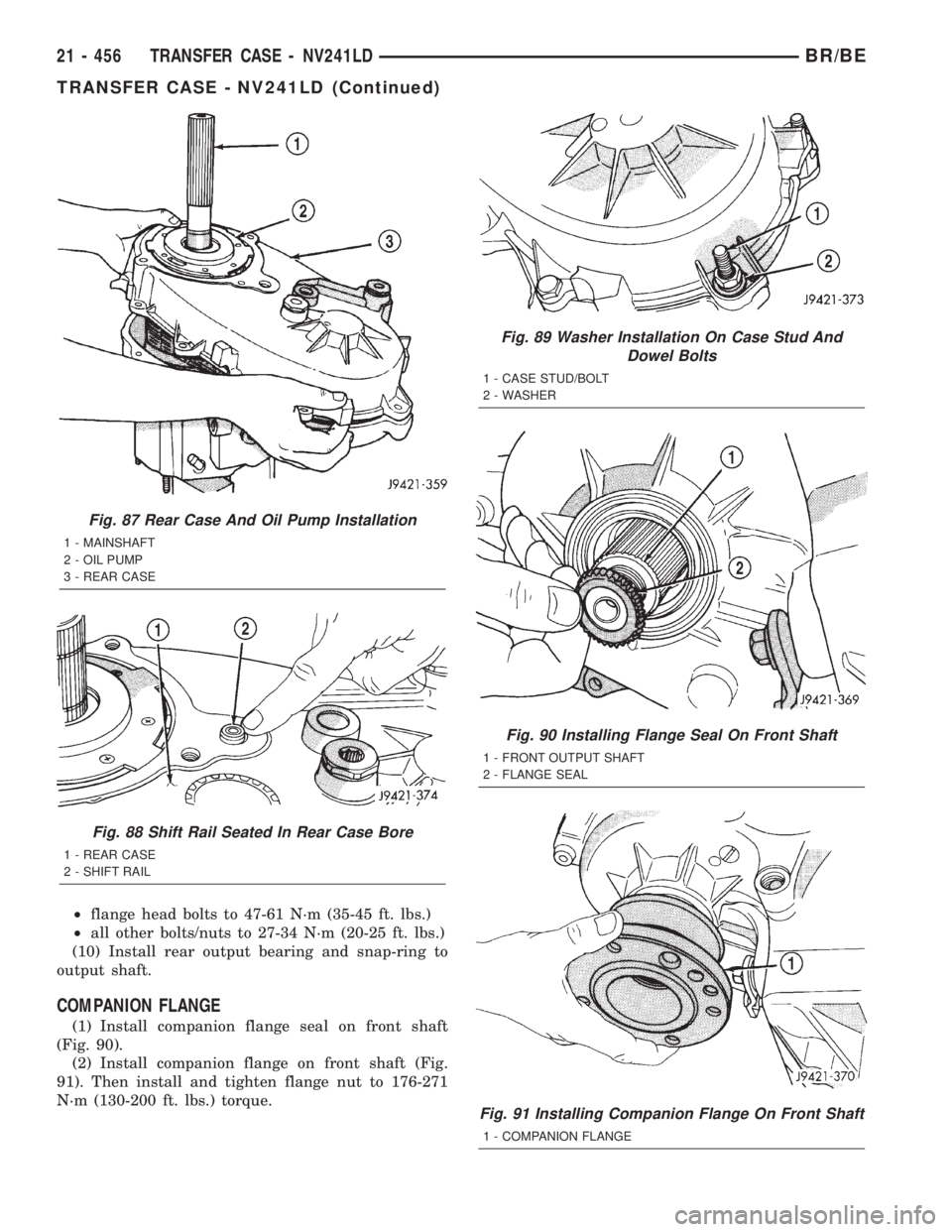
²flange head bolts to 47-61 N´m (35-45 ft. lbs.)
²all other bolts/nuts to 27-34 N´m (20-25 ft. lbs.)
(10) Install rear output bearing and snap-ring to
output shaft.
COMPANION FLANGE
(1) Install companion flange seal on front shaft
(Fig. 90).
(2) Install companion flange on front shaft (Fig.
91). Then install and tighten flange nut to 176-271
N´m (130-200 ft. lbs.) torque.
Fig. 87 Rear Case And Oil Pump Installation
1 - MAINSHAFT
2 - OIL PUMP
3 - REAR CASE
Fig. 88 Shift Rail Seated In Rear Case Bore
1 - REAR CASE
2 - SHIFT RAIL
Fig. 89 Washer Installation On Case Stud And
Dowel Bolts
1 - CASE STUD/BOLT
2 - WASHER
Fig. 90 Installing Flange Seal On Front Shaft
1 - FRONT OUTPUT SHAFT
2 - FLANGE SEAL
Fig. 91 Installing Companion Flange On Front Shaft
1 - COMPANION FLANGE
21 - 456 TRANSFER CASE - NV241LDBR/BE
TRANSFER CASE - NV241LD (Continued)
Page 1910 of 2255
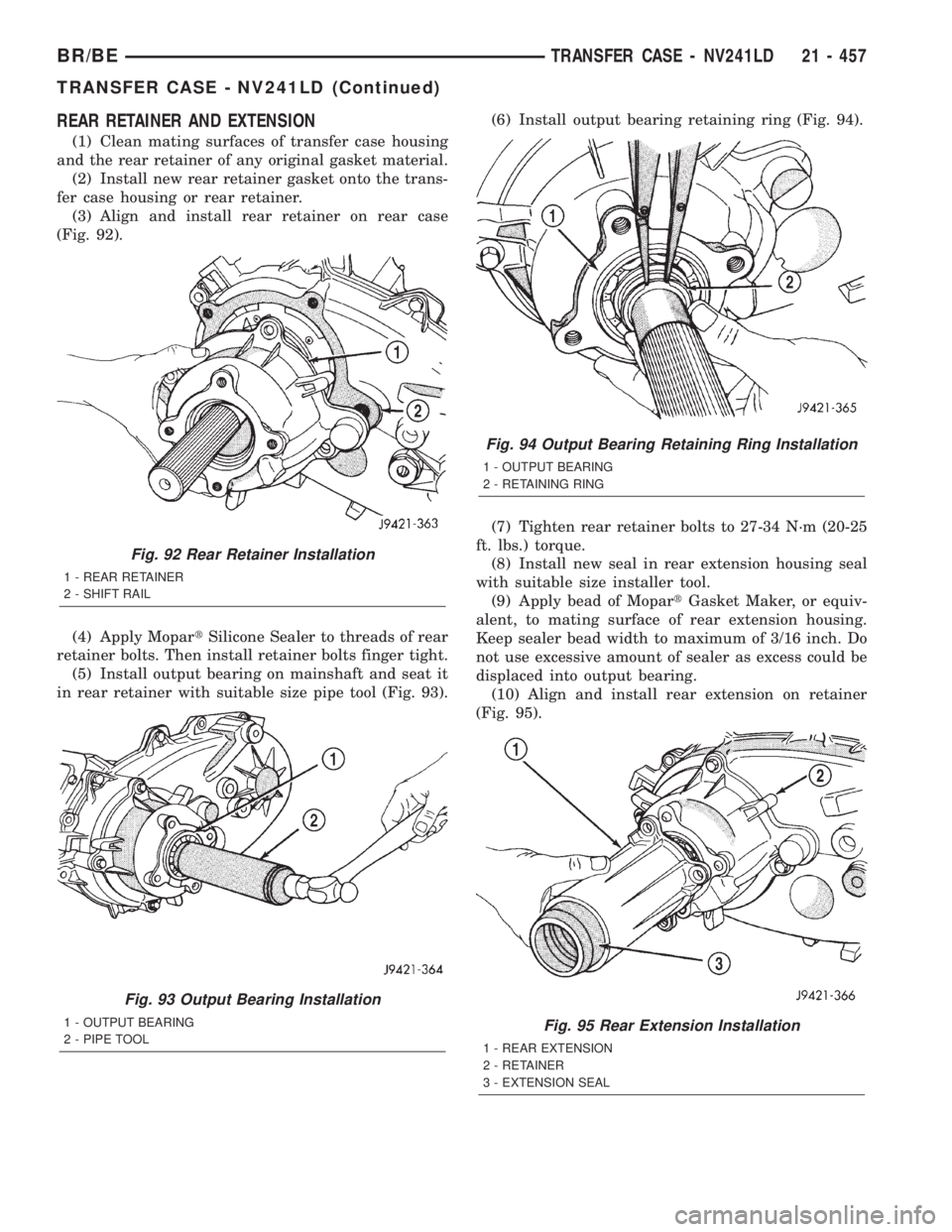
REAR RETAINER AND EXTENSION
(1) Clean mating surfaces of transfer case housing
and the rear retainer of any original gasket material.
(2) Install new rear retainer gasket onto the trans-
fer case housing or rear retainer.
(3) Align and install rear retainer on rear case
(Fig. 92).
(4) Apply MopartSilicone Sealer to threads of rear
retainer bolts. Then install retainer bolts finger tight.
(5) Install output bearing on mainshaft and seat it
in rear retainer with suitable size pipe tool (Fig. 93).(6) Install output bearing retaining ring (Fig. 94).
(7) Tighten rear retainer bolts to 27-34 N´m (20-25
ft. lbs.) torque.
(8) Install new seal in rear extension housing seal
with suitable size installer tool.
(9) Apply bead of MopartGasket Maker, or equiv-
alent, to mating surface of rear extension housing.
Keep sealer bead width to maximum of 3/16 inch. Do
not use excessive amount of sealer as excess could be
displaced into output bearing.
(10) Align and install rear extension on retainer
(Fig. 95).
Fig. 92 Rear Retainer Installation
1 - REAR RETAINER
2 - SHIFT RAIL
Fig. 93 Output Bearing Installation
1 - OUTPUT BEARING
2 - PIPE TOOL
Fig. 94 Output Bearing Retaining Ring Installation
1 - OUTPUT BEARING
2 - RETAINING RING
Fig. 95 Rear Extension Installation
1 - REAR EXTENSION
2 - RETAINER
3 - EXTENSION SEAL
BR/BETRANSFER CASE - NV241LD 21 - 457
TRANSFER CASE - NV241LD (Continued)