DODGE TRUCK 1993 Service Repair Manual
Manufacturer: DODGE, Model Year: 1993, Model line: TRUCK, Model: DODGE TRUCK 1993Pages: 1502, PDF Size: 80.97 MB
Page 111 of 1502
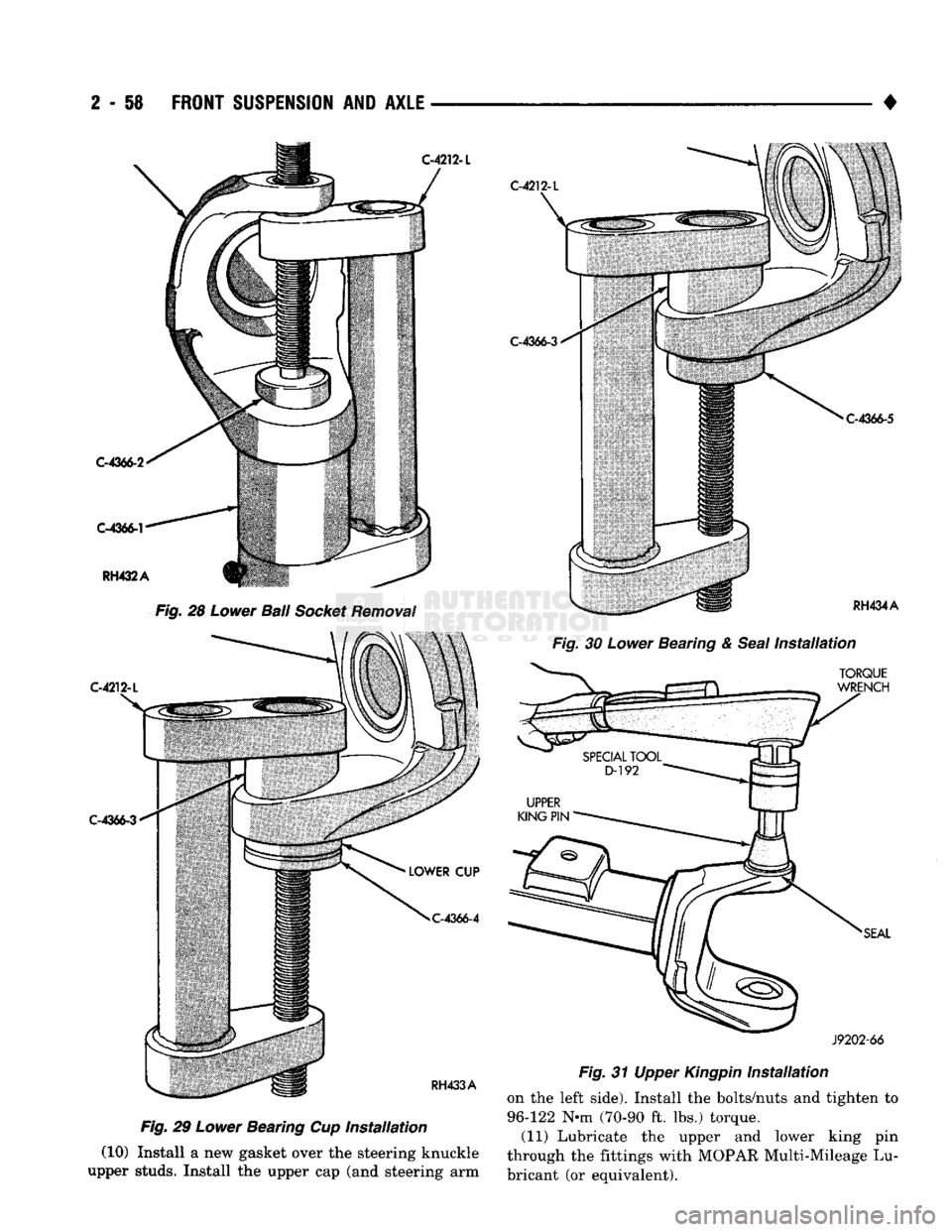
2
- 58
FRONT
SUSPENSION
AND
AXLE
•
C-4366-2
C-4366-1
RH432A
C-4212-L
Fig.
28
Lower
Ball
Socket
Removal
C-4212-L
C-4366-3
C-4366-4
RH433A
Fig.
29
Lower
Bearing Cup Installation
(10) Install a new gasket over the steering knuckle
upper studs. Install the upper cap (and steering arm
C-4212-L
C-4366-3
RH434A
Fig.
30
Lower
Bearing &
Seal
Installation
TORQUE
WRENCH
SEAL
J9202-66
Fig.
31 Upper
Kingpin
Installation
on the left side). Install the bolts/nuts and tighten to
96-122 N*m (70-90 ft. lbs.) torque. (11) Lubricate the upper and lower king pin
through the fittings with MOPAR Multi-Mileage Lu
bricant (or equivalent).
Page 112 of 1502
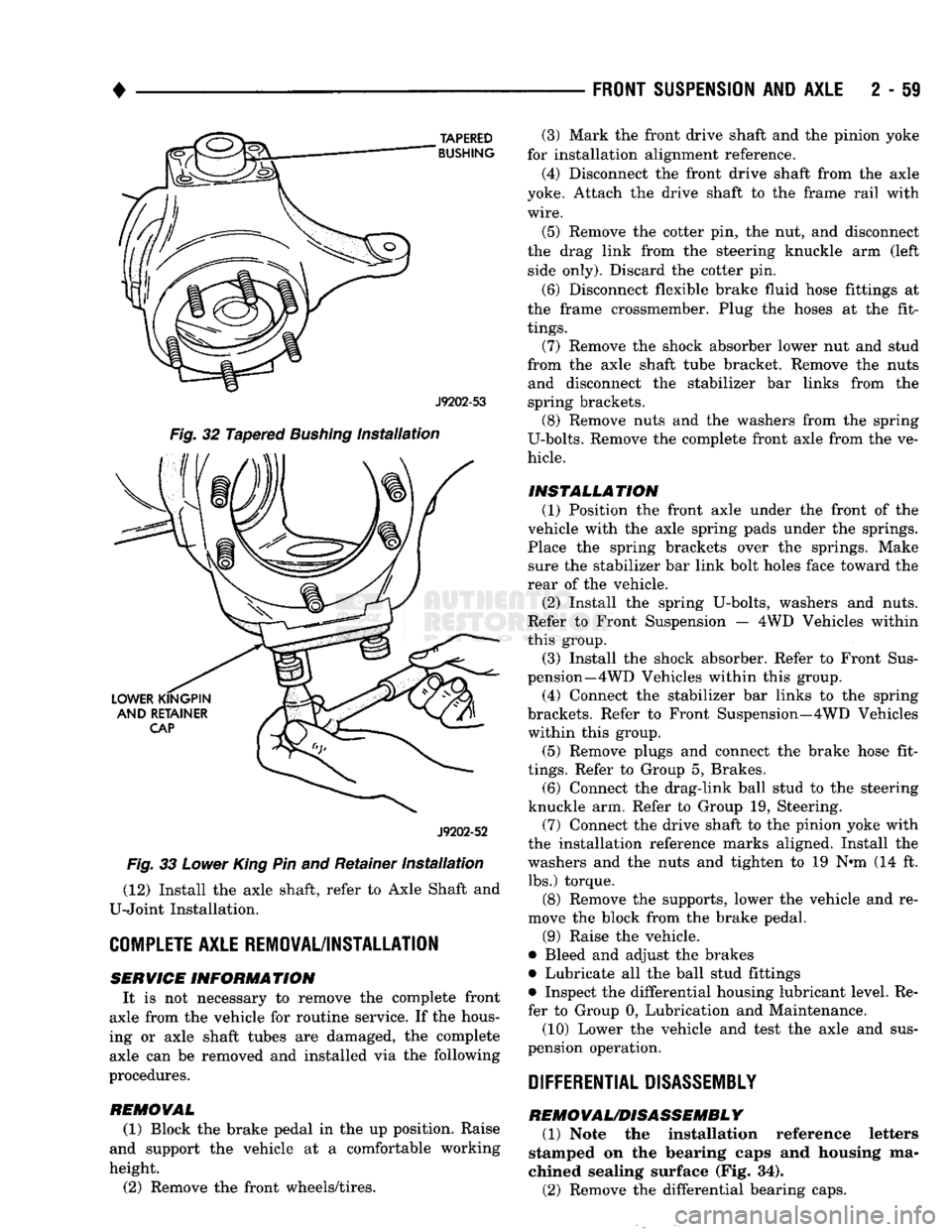
•
TAPERED
BUSHING
J9202-53
Fig.
32 Tapered
Bushing
Installation
J9202-52
Fig.
33
Lower
King
Pin and Retainer
Installation
(12) Install the axle shaft, refer to Axle Shaft and
U-Joint Installation.
COMPLETE
AXLE REMOVAL/INSTALLATION SERVICE
INFORMATION
It is not necessary to remove the complete front
axle from the vehicle for routine service. If the hous
ing or axle shaft tubes are damaged, the complete axle can be removed and installed via the following
procedures.
REMOVAL
(1) Block the brake pedal in the up position. Raise
and support the vehicle at a comfortable working
height.
(2) Remove the front wheels/tires.
FRONT SUSPENSION
AND
AXLE
2 - 59
(3) Mark the front drive shaft and the pinion yoke
for installation alignment reference.
(4) Disconnect the front drive shaft from the axle
yoke. Attach the drive shaft to the frame rail with
wire.
(5) Remove the cotter pin, the nut, and disconnect
the drag link from the steering knuckle arm (left side only). Discard the cotter pin.
(6) Disconnect flexible brake fluid hose fittings at
the frame crossmember. Plug the hoses at the fit
tings.
(7) Remove the shock absorber lower nut and stud
from the axle shaft tube bracket. Remove the nuts and disconnect the stabilizer bar links from the
spring brackets. (8) Remove nuts and the washers from the spring
U-bolts. Remove the complete front axle from the ve
hicle.
INSTALLATION (1) Position the front axle under the front of the
vehicle with the axle spring pads under the springs.
Place the spring brackets over the springs. Make sure the stabilizer bar link bolt holes face toward the
rear of the vehicle.
(2) Install the spring U-bolts, washers and nuts.
Refer to Front Suspension — 4WD Vehicles within
this group. (3) Install the shock absorber. Refer to Front Sus
pension—4 WD Vehicles within this group.
(4) Connect the stabilizer bar links to the spring
brackets. Refer to Front Suspension—4WD Vehicles within this group.
(5) Remove plugs and connect the brake hose fit
tings.
Refer to Group 5, Brakes. (6) Connect the drag-link ball stud to the steering
knuckle arm. Refer to Group 19, Steering. (7) Connect the drive shaft to the pinion yoke with
the installation reference marks aligned. Install the
washers and the nuts and tighten to 19 N-m (14 ft. lbs.) torque.
(8) Remove the supports, lower the vehicle and re
move the block from the brake pedal.
(9) Raise the vehicle.
• Bleed and adjust the brakes
• Lubricate all the ball stud fittings
• Inspect the differential housing lubricant level. Re
fer to Group 0, Lubrication and Maintenance.
(10) Lower the vehicle and test the axle and sus
pension operation.
DIFFERENTIAL DISASSEMBLY
REMOVAL/DISASSEMBLY
(1) Note the installation reference letters
stamped on the bearing caps and housing ma
chined sealing surface (Fig. 34).
(2) Remove the differential bearing caps.
Page 113 of 1502
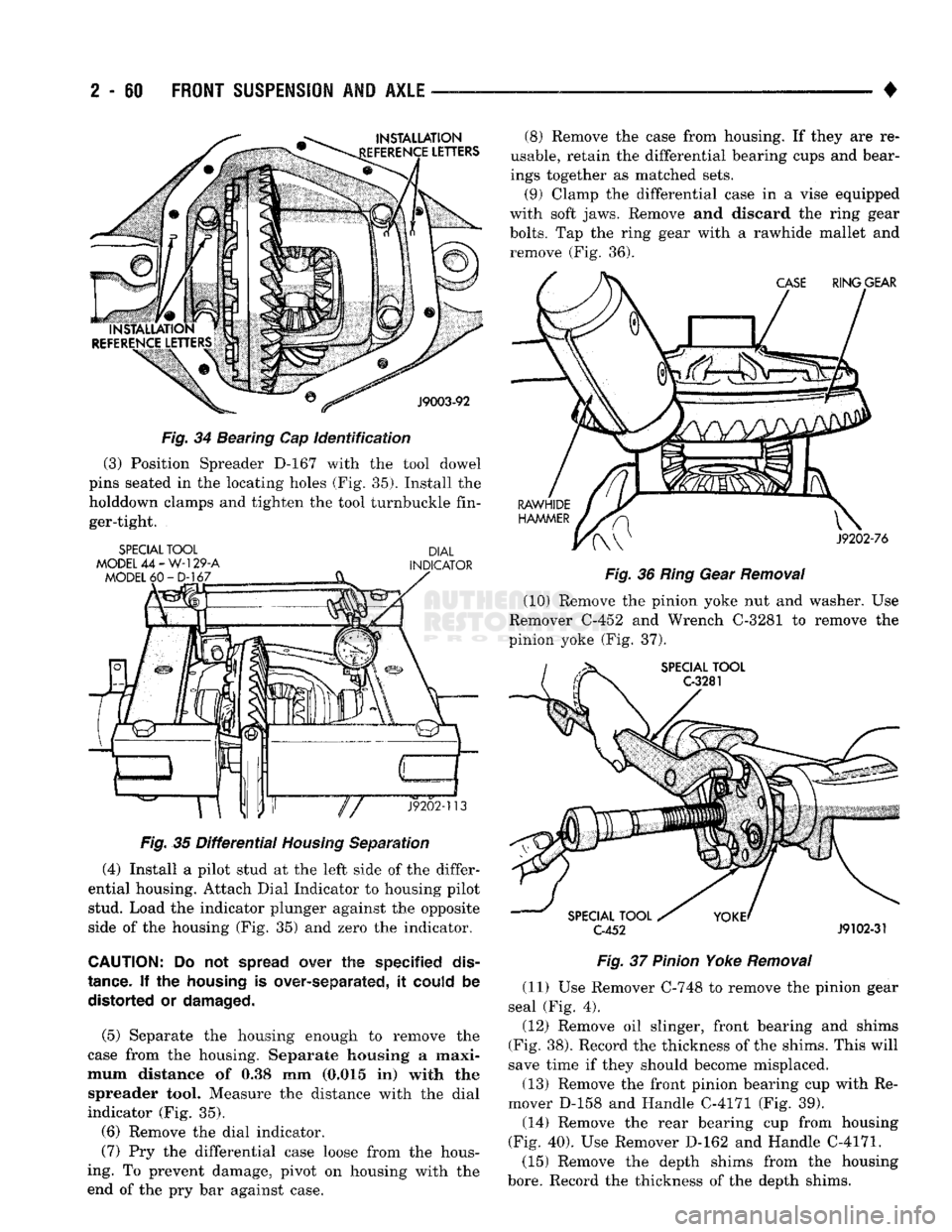
2
- 60
FRONT
SUSPENSION
AND
AXLE
•
Fig.
34 Bearing Cap identification (3) Position Spreader D-167 with the tool dowel
pins seated in the locating holes (Fig. 35). Install the
holddown clamps and tighten the tool turnbuckle fin ger-tight.
SPECIAL
TOOL
DIAL
MODEL
44 -
W-129-A
INDICATOR
Fig.
35
Differential
Housing
Separation (4) Install a pilot stud at the left side of the differ
ential housing. Attach Dial Indicator to housing pilot stud. Load the indicator plunger against the opposite
side of the housing (Fig. 35) and zero the indicator.
CAUTION:
Do not
spread
over the specified
dis
tance.
If the
housing
is over-separated, it
could
be distorted or
damaged.
(5) Separate the housing enough to remove the
case from the housing. Separate housing a maxi
mum distance of 0.38 mm (0.015 in) with the spreader tool. Measure the distance with the dial
indicator (Fig. 35).
(6) Remove the dial indicator.
(7) Pry the differential case loose from the hous
ing. To prevent damage, pivot on housing with the
end of the pry bar against case. (8) Remove the case from housing. If they are re
usable, retain the differential bearing cups and bear
ings together as matched sets. (9) Clamp the differential case in a vise equipped
with soft jaws. Remove and discard the ring gear
bolts.
Tap the ring gear with a rawhide mallet and remove (Fig. 36).
Fig.
36
Ring
Gear
Removal
(10) Remove the pinion yoke nut and washer. Use
Remover C-452 and Wrench C-3281 to remove the
pinion yoke (Fig. 37). C-452
J9102-31
Fig.
37
Pinion
Yoke
Removal
(11) Use Remover C-748 to remove the pinion gear
seal (Fig. 4).
(12) Remove oil slinger, front bearing and shims
(Fig. 38). Record the thickness of the shims. This will
save time if they should become misplaced.
(13) Remove the front pinion bearing cup with Re
mover D-158 and Handle C-4171 (Fig. 39). (14) Remove the rear bearing cup from housing
(Fig. 40). Use Remover D-162 and Handle C-4171.
(15) Remove the depth shims from the housing
bore.
Record the thickness of the depth shims.
Page 114 of 1502
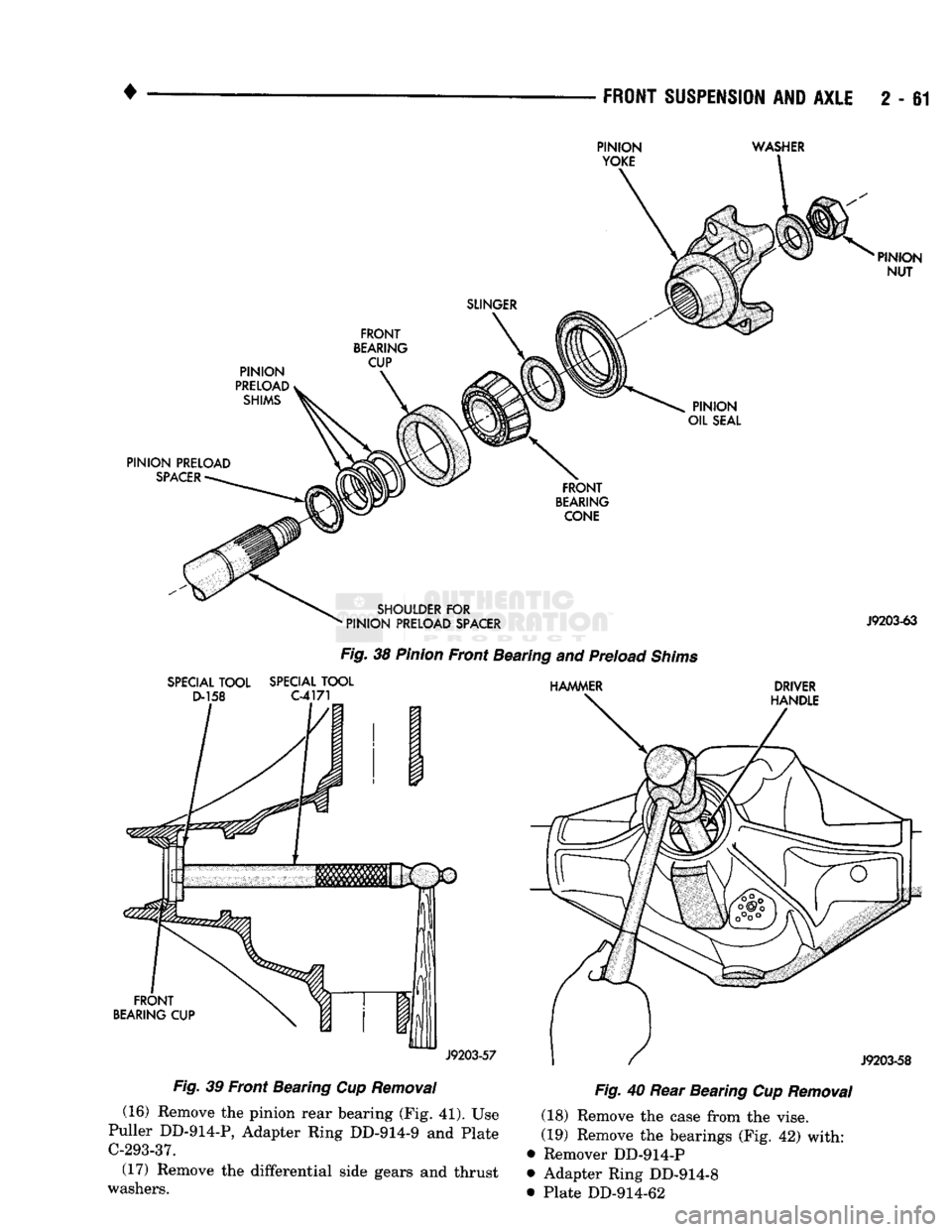
FRONT
SUSPENSION
AND
AXLE
2 - 61
PINION
YOKE
WASHER
SLINGER
PINION
PRELOAD,
SHIMS
FRONT
BEARING
CUP
PINION
NUT
PINION
OIL
SEAL
PINION PRELOAD
SPACER
FRONT
BEARING
CONE
SHOULDER
FOR
•
PINION
PRELOAD
SPACER
J9203-63
SPECIAL
TOOL
SPECIAL
TOOL
D-158
C-4171
Fig.
38
Pinion
Front Bearing and Preload
Shims
HAMMER
DRIVER
HANDLE
FRONT
BEARING
CUP
J9203-57
J9203-58
Fig.
39 Front Bearing Cup
Removal
(16) Remove the pinion rear bearing (Fig. 41). Use
Puller DD-914-P, Adapter Ring DD-914-9 and Plate
C-293-37.
(17) Remove the differential side gears and thrust
washers.
Fig.
40 Rear Bearing Cup
Removal
(18) Remove the case from the vise.
(19) Remove the bearings (Fig. 42) with: Remover DD-914-P
Adapter Ring DD-914-8
Plate DD-914-62
Page 115 of 1502
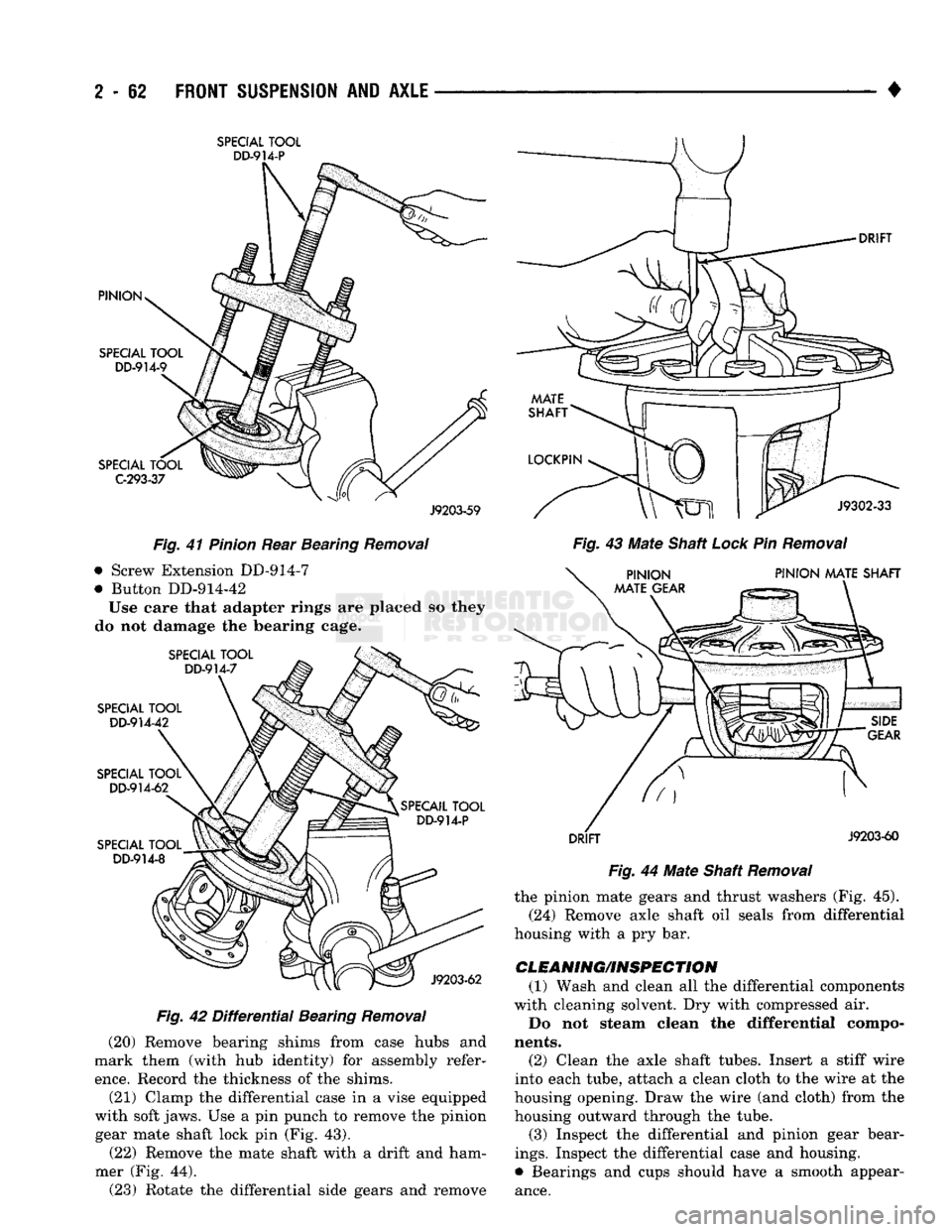
2
- 82
FRONT SUSPENSION
AND
AXLE
•
SPECIAL
TOOL
DD-914-P
J9203-59
Fig.
41
Pinion
Rear Bearing
Removal
• Screw Extension DD-914-7
• Button DD-914-42
Use eare that adapter rings are placed so they
do not damage the bearing cage.
Fig.
42
Differential
Bearing
Removal
(20) Remove bearing shims from case hubs and
mark them (with hub identity) for assembly refer
ence.
Record the thickness of the shims.
(21) Clamp the differential case in a vise equipped
with soft jaws. Use a pin punch to remove the pinion gear mate shaft lock pin (Fig. 43).
(22) Remove the mate shaft with a drift and ham
mer (Fig. 44). (23) Rotate the differential side gears and remove
Fig.
43 Mate Shaft
Lock
Pin
Removal
Fig.
44 Mate Shaft
Removal
the pinion mate gears and thrust washers (Fig. 45).
(24) Remove axle shaft oil seals from differential
housing with a pry bar.
CLEANING/INSPECTION (1) Wash and clean all the differential components
with cleaning solvent. Dry with compressed air.
Do not steam clean the differential compo
nents.
(2) Clean the axle shaft tubes. Insert a stiff wire
into each tube, attach a clean cloth to the wire at the
housing opening. Draw the wire (and cloth) from the housing outward through the tube.
(3) Inspect the differential and pinion gear bear
ings.
Inspect the differential case and housing.
• Bearings and cups should have a smooth appear
ance.
Page 116 of 1502
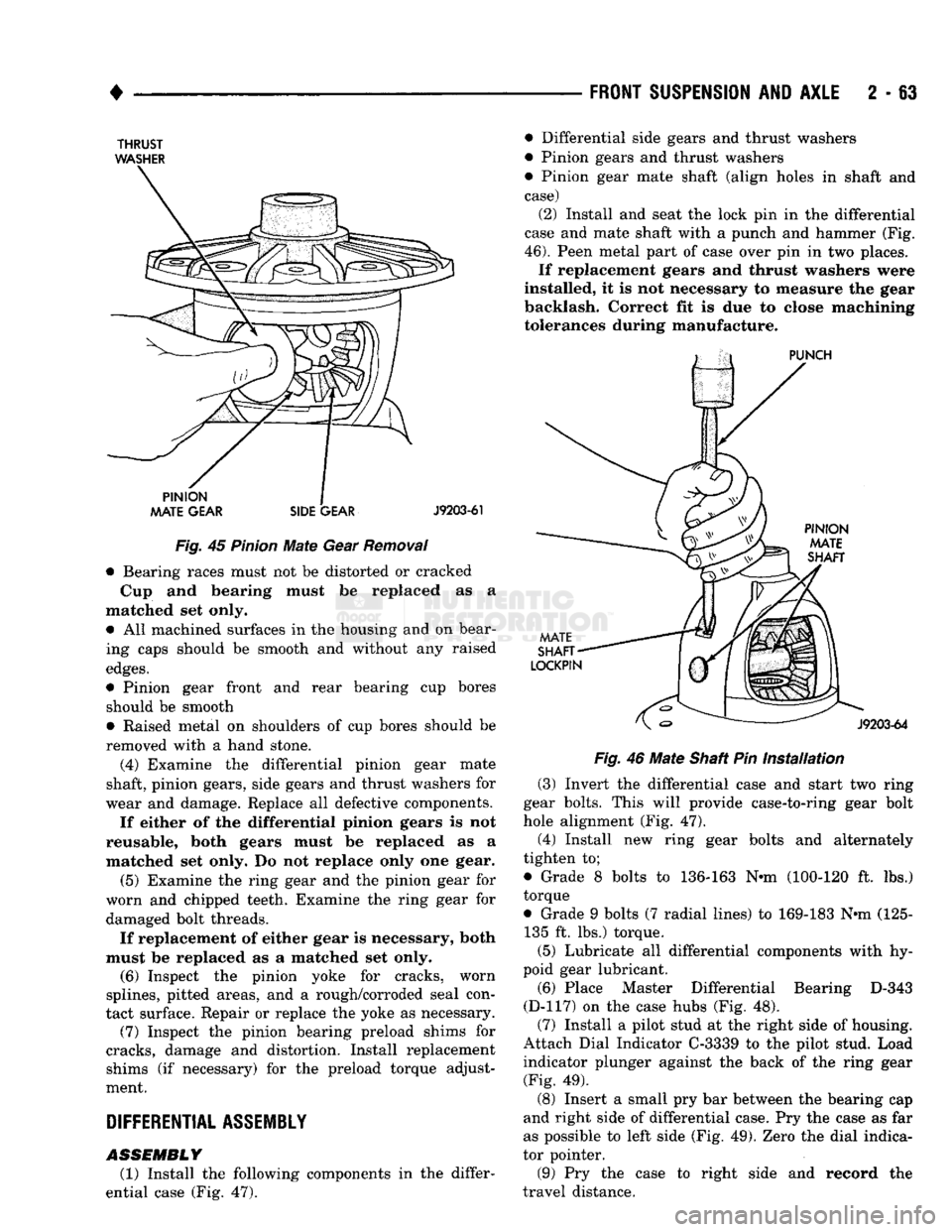
•
FRONT SUSPENSION
AND
AXLE
2 - 63
THRUST
WASHER
Fig.
45
Pinion
Mate
Gear
Removal
• Bearing races must not be distorted or cracked
Cup and bearing must be replaced as a
matched set only. • All machined surfaces in the housing and on bear
ing caps should be smooth and without any raised
edges.
• Pinion gear front and rear bearing cup bores should be smooth
• Raised metal on shoulders of cup bores should be
removed with a hand stone.
(4) Examine the differential pinion gear mate
shaft, pinion gears, side gears and thrust washers for
wear and damage. Replace all defective components.
If either of the differential pinion gears is not
reusable, both gears must be replaced as a
matched set only. Do not replace only one gear.
(5) Examine the ring gear and the pinion gear for
worn and chipped teeth. Examine the ring gear for damaged bolt threads.
If replacement of either gear is necessary, both
must be replaced as a matched set only. (6) Inspect the pinion yoke for cracks, worn
splines, pitted areas, and a rough/corroded seal con
tact surface. Repair or replace the yoke as necessary. (7) Inspect the pinion bearing preload shims for
cracks, damage and distortion. Install replacement shims (if necessary) for the preload torque adjust
ment.
DIFFERENTIAL
ASSEMBLY
ASSEMBLY
(1) Install the following components in the differ
ential case (Fig. 47). • Differential side gears and thrust washers
• Pinion gears and thrust washers
• Pinion gear mate shaft (align holes in shaft and
case) (2) Install and seat the lock pin in the differential
case and mate shaft with a punch and hammer (Fig.
46).
Peen metal part of case over pin in two places. If replacement gears and thrust washers were
installed, it is not necessary to measure the gear
backlash. Correct fit is due to close machining tolerances during manufacture.
Fig.
46
Mate
Shaft Pin
Installation
(3) Invert the differential case and start two ring
gear bolts. This will provide case-to-ring gear bolt
hole alignment (Fig. 47). (4) Install new ring gear bolts and alternately
tighten to;
• Grade 8 bolts to 136-163 N*m (100-120 ft. lbs.)
torque
• Grade 9 bolts (7 radial lines) to 169-183 N*m (125- 135 ft. lbs.) torque.
(5) Lubricate all differential components with hy
poid gear lubricant. (6) Place Master Differential Bearing D-343
(D-117) on the case hubs (Fig. 48). (7) Install a pilot stud at the right side of housing.
Attach Dial Indicator C-3339 to the pilot stud. Load indicator plunger against the back of the ring gear (Fig. 49).
(8) Insert a small pry bar between the bearing cap
and right side of differential case. Pry the case as far
as possible to left side (Fig. 49). Zero the dial indica
tor pointer.
(9) Pry the case to right side and record the
travel distance.
Page 117 of 1502
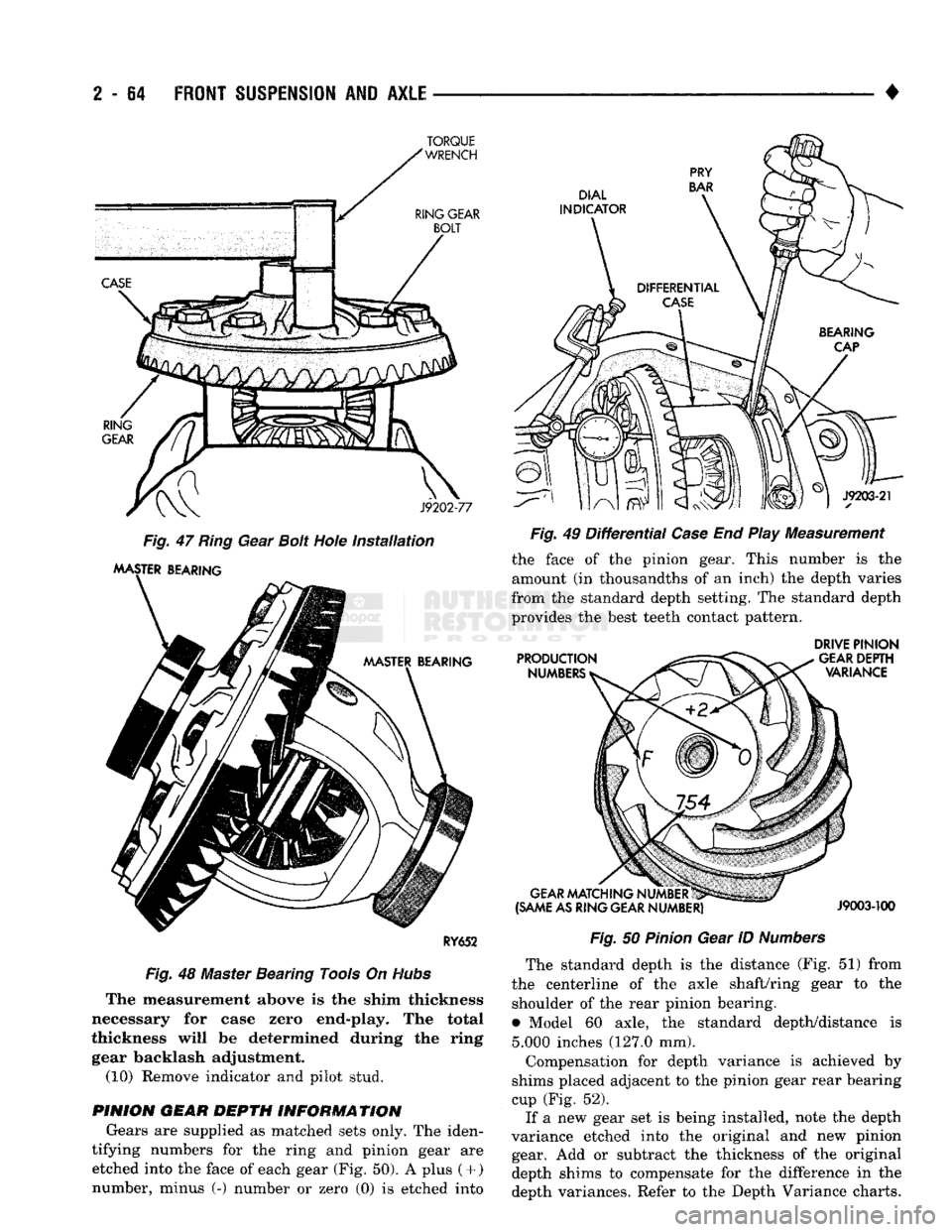
2
- 64
FRONT
SUSPENSION
AND
AXLE
—
Fig.
47 Ring Gear Bolt Hole
installation
MASTER BEARING
RY652
Fig.
48 Master Bearing Tools On
Hubs
The measurement above is the shim thickness
necessary for case zero end-play. The total
thickness will be determined during the ring gear backlash adjustment. (10) Remove indicator and pilot stud.
PINION GEAR DEPTH INFORMATION Gears are supplied as matched sets only. The iden
tifying numbers for the ring and pinion gear are etched into the face of each gear (Fig. 50). A plus
(
+ )
number, minus (-) number or zero (0) is etched into •
Fig.
49
Differential
Case
End Play Measurement the face of the pinion gear. This number is the
amount (in thousandths of an inch) the depth varies
from the standard depth setting. The standard depth
provides the best teeth contact pattern.
DRIVE
PINION
Fig.
50
Pinion
Gear ID
Numbers
The standard depth is the distance (Fig. 51) from
the centerline of the axle shaft/ring gear to the shoulder of the rear pinion bearing.
• Model 60 axle, the standard depth/distance is
5.000
inches (127.0 mm).
Compensation for depth variance is achieved by
shims placed adjacent to the pinion gear rear bearing
cup (Fig. 52). If a new gear set is being installed, note the depth
variance etched into the original and new pinion gear. Add or subtract the thickness of the original
depth shims to compensate for the difference in the
depth variances. Refer to the Depth Variance charts.
TORQUE
Page 118 of 1502
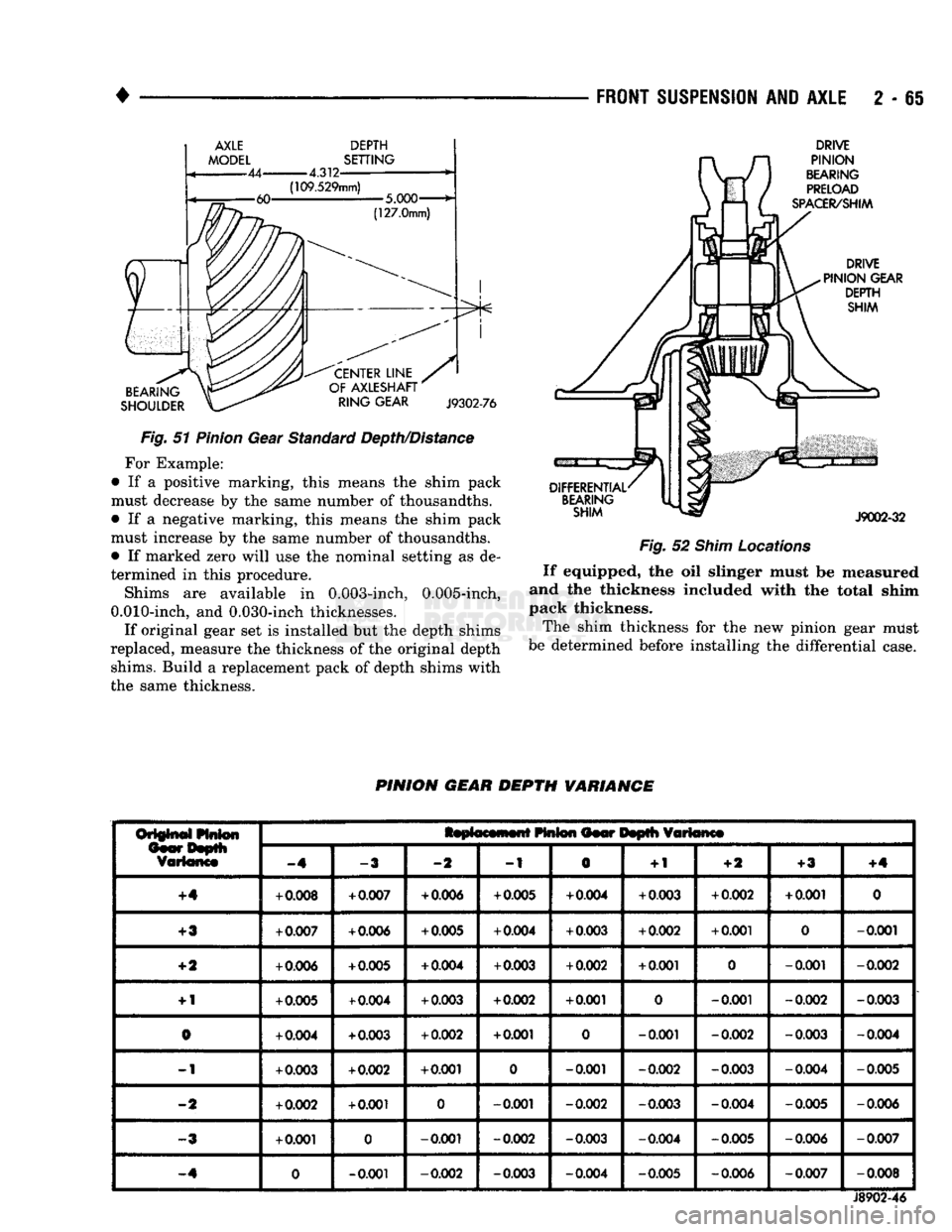
•
FRONT
SUSPENSION
AND
AXLE
2 - 65
AXLE
DEPTH
MODEL
SETTING
Fig. 51 Pinion Gear Standard Depth/Distance For Example:
• If a positive marking, this means the shim pack
must decrease by the same number of thousandths.
• If a negative marking, this means the shim pack
must increase by the same number of thousandths.
• If marked zero will use the nominal setting as de
termined in this procedure.
Shims are available in 0.003-inch, 0.005-inch,
0.010-inch, and 0.030-inch thicknesses.
If original gear set is installed but the depth shims
replaced, measure the thickness of the original depth shims. Build a replacement pack of depth shims with
the same thickness.
DRIVE
Fig. 52 Shim Locations If equipped, the oil slinger must be measured
and the thickness included with the total shim
pack thickness.
The shim thickness for the new pinion gear must
be determined before installing the differential case. PINION GEAR DEPTH VARIANCE
Original Pinion Gear Depth
Variance
Replacement
Pinion
Gear
Depth Variance
Original Pinion
Gear Depth
Variance
-4
-3
-2 -1
0
+
1
-ft
+
3
+4
+
0.008
+
0.007
+
0.006
+
0.005
+
0.004
+
0.003
+
0.002
+
0.001
0
+S
+0.007
+
0.006
+
0.005
+
0.004
+
0.003
+
0.002
+
0.001
0
-0.001
4-1
+
0.006
+
0.005
+
0.004
+
0.003
+
0.002
+
0.001
0
-0.001 -0.002
4-1
+
0.005
+
0.004
+
0.003
+0.002
+
0.001
0
-0.001 -0.002
-0.003
0
+
0.004
+0.003
+
0.002
+
0.001
0
-0.001 -0.002 -0.003
-0.004
-I
+
0.003
+
0.002
+
0.001
0
-0.001
-0.002 -0.003 -0.004
-0.005
-2
+
0.002
+
0.001
0
-0.001 -0.002
-0.003
-0.004
-0.005
-0.006
-3
+
0.001
0
-0.001
-0.002
-0.003
-0.004
-0.005
-0.006
-0.007
-4
0
-0.001 -0.002
-0.003 -0.004
-0.005 -0.006
-0.007
-0.008
J8902-46
Page 119 of 1502
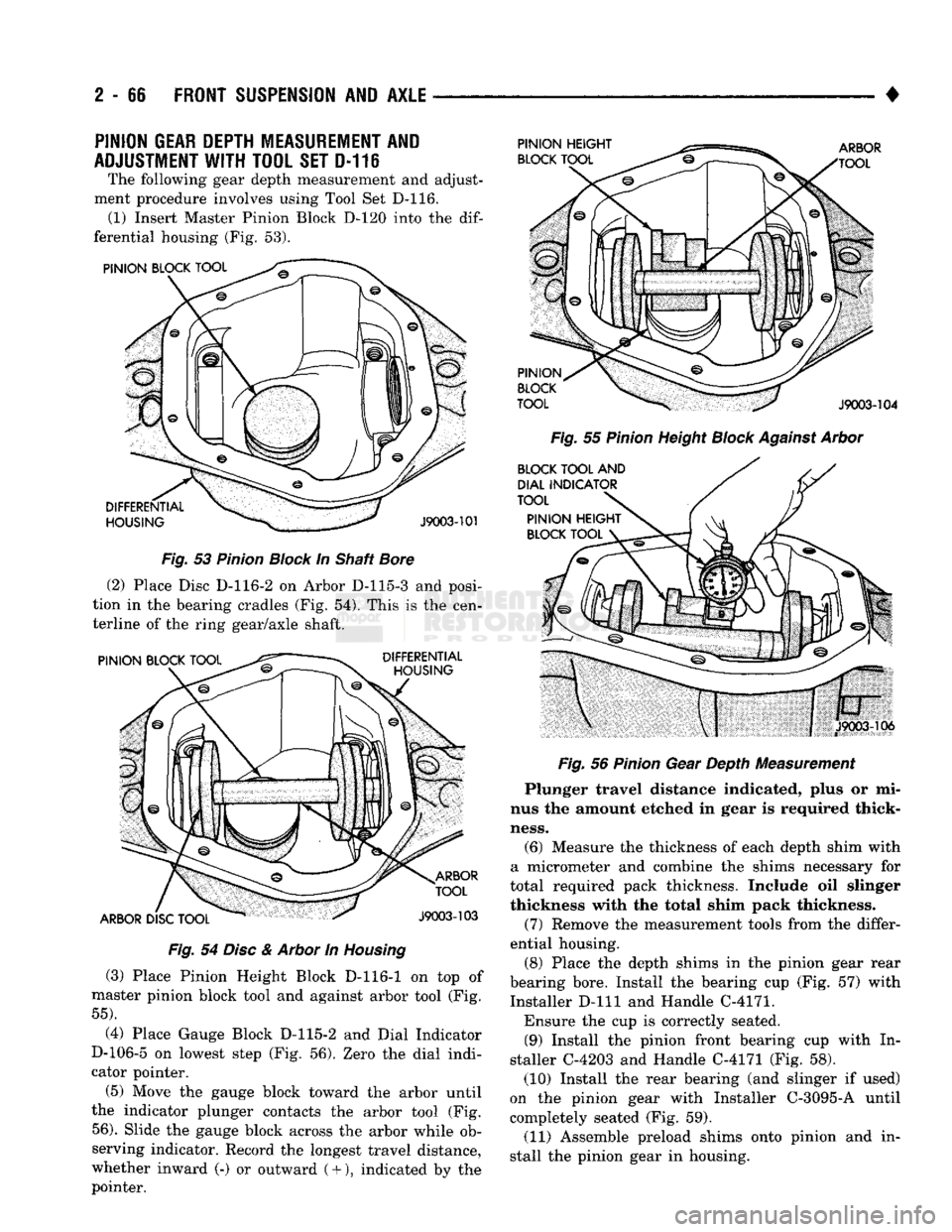
2
- 66
FRONT
SUSPENSION
AND
AXLE
•
PINION
GEAR
DEPTH
MEASUREMENT
AND
ADJUSTMENT
WITH
TOOL
SET
D-116 The following gear depth measurement and adjust
ment procedure involves using Tool Set D-116. (1) Insert Master Pinion Block D-120 into the
dif
ferential housing (Fig. 53).
Fig.
53
Pinion
Block
In Shaft
Bore
(2) Place Disc D-116-2 on Arbor D-115-3 and posi
tion in the bearing cradles (Fig. 54). This is the cen
terline of the ring gear/axle shaft.
Fig.
54
Disc
&
Arbor
In
Housing
(3) Place Pinion Height Block D-116-1 on top of
master pinion block tool and against arbor tool (Fig.
55).
(4) Place Gauge Block D-115-2 and Dial Indicator
D-106-5 on lowest step (Fig. 56). Zero the dial indi
cator pointer.
(5) Move the gauge block toward the arbor until
the indicator plunger contacts the arbor tool (Fig.
56).
Slide the gauge block across the arbor while ob
serving indicator. Record the longest travel distance,
whether inward (-) or outward
(
+ ), indicated by the
pointer.
Fig.
55
Pinion
Height
Block
Against
Arbor
Fig.
56
Pinion
Gear Depth Measurement
Plunger travel distance indicated, plus or mi
nus the amount etched in gear is required thick
ness.
(6) Measure the thickness of each depth shim with
a micrometer and combine the shims necessary for
total required pack thickness. Include oil slinger
thickness with the total shim pack thickness.
(7) Remove the measurement tools from the differ
ential housing.
(8) Place the depth shims in the pinion gear rear
bearing bore. Install the bearing cup (Fig. 57) with
Installer D-lll and Handle C-4171.
Ensure the cup is correctly seated. (9) Install the pinion front bearing cup with In
staller C-4203 and Handle C-4171 (Fig. 58). (10) Install the rear bearing (and slinger if used)
on the pinion gear with Installer C-3095-A until
completely seated (Fig. 59).
(11) Assemble preload shims onto pinion and in
stall the pinion gear in housing.
Page 120 of 1502
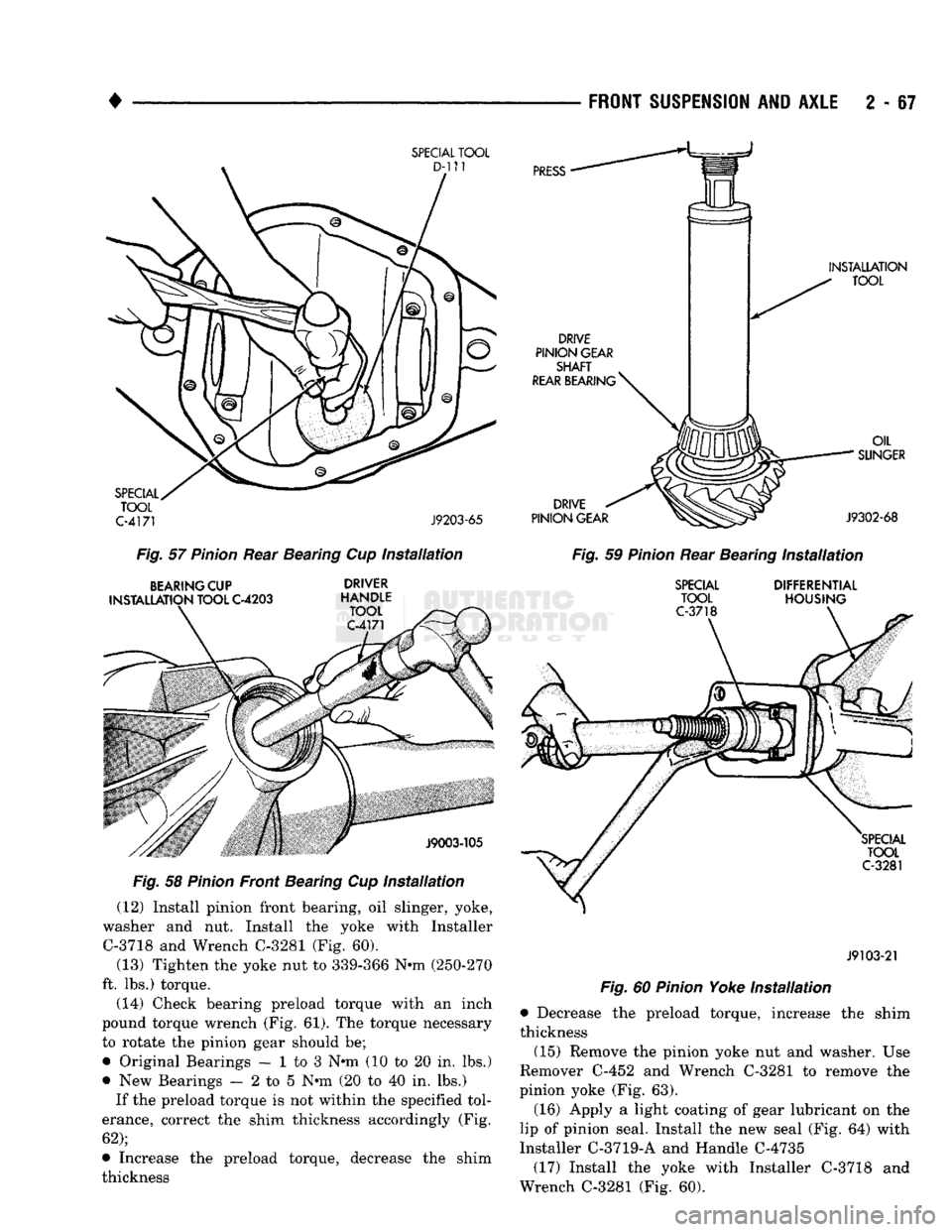
•
FRONT
SUSPENSION
AND
AXLE
2 - 67
SPECIAL
TOOL
D-111
PRESS
DRIVE
PINION GEAR SHAFT
REAR
BEARING' INSTALLATION
TOOL
SPECIAL
TOOL
C-4171
J9203-65
DRIVE
PINION GEAR OIL
SUNGER
J9302-68
Fig.
57
Pinion
Rear Bearing Cup
Installation
Fig.
59
Pinion
Rear Bearing
Installation
BEARING
CUP
INSTALLATION TOOL
C-4203
DRIVER
HANDLE TOOL
C-4171
SPECIAL
TOOL
C-3718
DIFFERENTIAL
HOUSING
SPECIAL
TOOL
C-3281
Fig.
58
Pinion
Front Bearing Cup
Installation
(12) Install pinion front bearing, oil slinger, yoke,
washer and nut. Install the yoke with Installer C-3718 and Wrench C-3281 (Fig. 60).
(13) Tighten the yoke nut to 339-366 N-m (250-270
ft. lbs.) torque. (14) Check bearing preload torque with an inch
pound torque wrench (Fig. 61). The torque necessary
to rotate the pinion gear should be;
• Original Bearings — 1 to 3 N*m (10 to 20 in. lbs.)
• New Bearings — 2 to 5 N-m (20 to 40 in. lbs.) If the preload torque is not within the specified tol
erance, correct the shim thickness accordingly (Fig.
62);
• Increase the preload torque, decrease the shim
thickness
J9103-21
Fig.
60
Pinion
Yoke
Installation
• Decrease the preload torque, increase the shim
thickness (15) Remove the pinion yoke nut and washer. Use
Remover C-452 and Wrench C-3281 to remove the
pinion yoke (Fig. 63).
(16) Apply a light coating of gear lubricant on the
lip of pinion seal. Install the new seal (Fig. 64) with
Installer C-3719-A and Handle C-4735
(17) Install the yoke with Installer C-3718 and
Wrench C-3281 (Fig. 60).