DODGE TRUCK 1993 Service Repair Manual
Manufacturer: DODGE, Model Year: 1993, Model line: TRUCK, Model: DODGE TRUCK 1993Pages: 1502, PDF Size: 80.97 MB
Page 131 of 1502
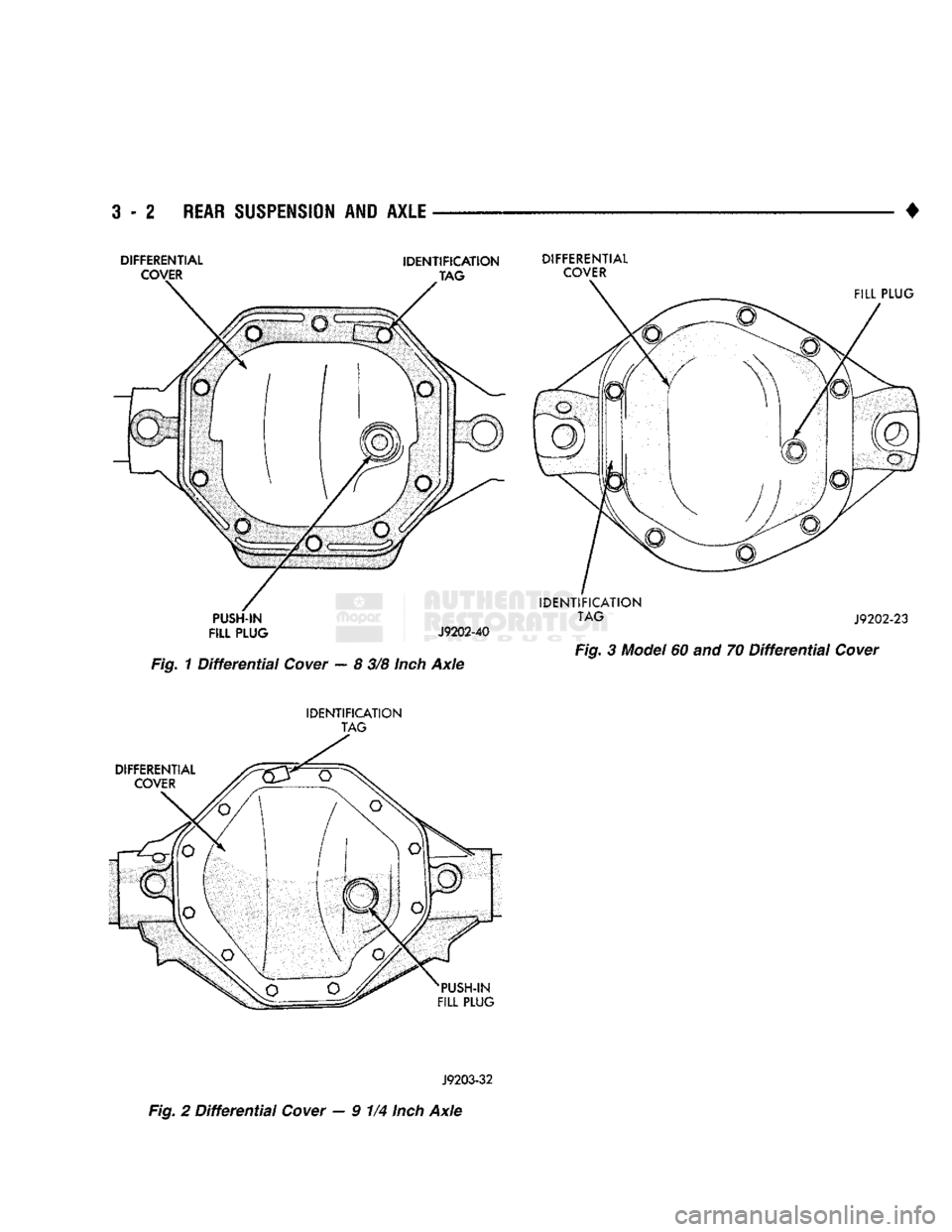
3 - 2
REAR SUSPENSION
AND
AXLE
•
DIFFERENTIAL
IDENTIFICATION
DIFFERENTIAL
FILL
PLUG
J9202-40
Fig. 3 Model 60 and 70 Differential Cover Fig. 1 Differential Cover — 8 3/8
Inch
Axle
IDENTIFICATION
TAG
J9203-32
Fig. 2 Differential Cover — 9 1/4
Inch
Axle
Page 132 of 1502
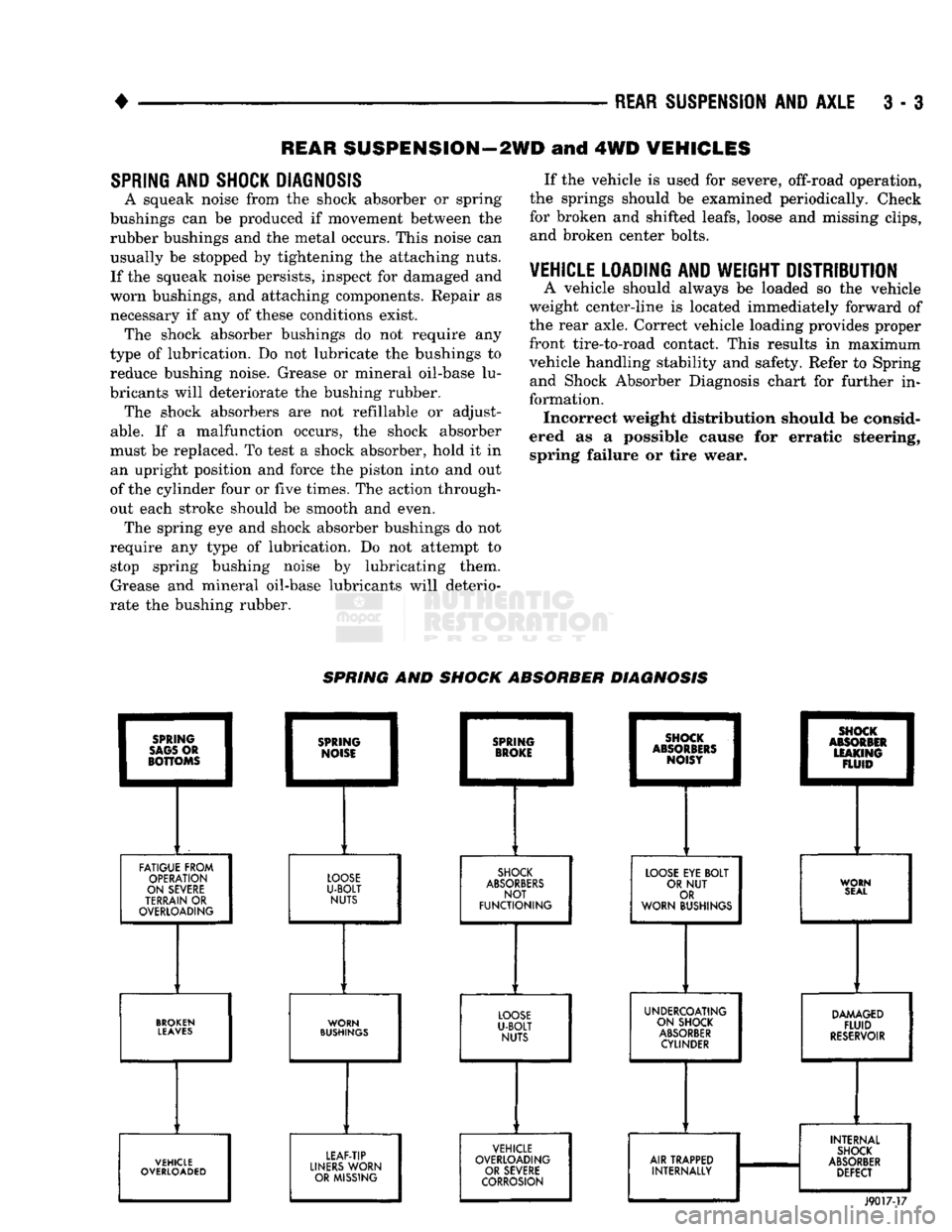
•
REAR
SUSPENSION
AND
AXLE
3 - 3
REAR SUSPENSION—2WD
and 4WD
VEHICLES
SPRING
AND
SHOCK DIAGNOSIS
A squeak noise from the shock absorber or spring
bushings can be produced if movement between the
rubber bushings and the metal occurs. This noise can usually be stopped by tightening the attaching nuts.
If the squeak noise persists, inspect for damaged and
worn bushings, and attaching components. Repair as
necessary if any of these conditions exist. The shock absorber bushings do not require any
type of lubrication. Do not lubricate the bushings to reduce bushing noise. Grease or mineral oil-base lu
bricants will deteriorate the bushing rubber. The shock absorbers are not reflllable or adjust
able.
If a malfunction occurs, the shock absorber
must be replaced. To test a shock absorber, hold it in an upright position and force the piston into and out
of the cylinder four or five times. The action through
out each stroke should be smooth and even. The spring eye and shock absorber bushings do not
require any type of lubrication. Do not attempt to stop spring bushing noise by lubricating them.
Grease and mineral oil-base lubricants will deterio
rate the bushing rubber. If the vehicle is used for severe, off-road operation,
the springs should be examined periodically. Check for broken and shifted leafs, loose and missing clips, and broken center bolts.
VEHICLE LOADING
AND
WEIGHT DISTRIBUTION
A vehicle should always be loaded so the vehicle
weight center-line is located immediately forward of
the rear axle. Correct vehicle loading provides proper
front tire-to-road contact. This results in maximum
vehicle handling stability and safety. Refer to Spring and Shock Absorber Diagnosis chart for further in
formation. Incorrect weight distribution should be consid
ered as a possible cause for erratic steering, spring failure or tire wear. SPRING AND SHOCK ABSORBER DIAGNOSIS
FATIGUE FROM
OPERATION
ON SEVERE
TERRAIN
OR
OVERLOADING
LOOSE
U-BOLT
NUTS
SHOCK
ABSORBERS
NOT
FUNCTIONING
LOOSE
EYE
BOLT
OR
NUT
OR
WORN BUSHINGS WORN
SEAL
BROKEN
LEAVES
WORN
BUSHINGS
UNDERCOATING
ON SHOCK
ABSORBER
CYLINDER
DAMAGED
FLUID
RESERVOIR
VEHICLE
OVERLOADED LEAF-TIP
LINERS
WORN OR MISSING VEHICLE
OVERLOADING OR SEVERE
CORROSION
AIR TRAPPED
INTERNALLY INTERNAL
SHOCK
ABSORBER
DEFECT
J9017-17
Page 133 of 1502
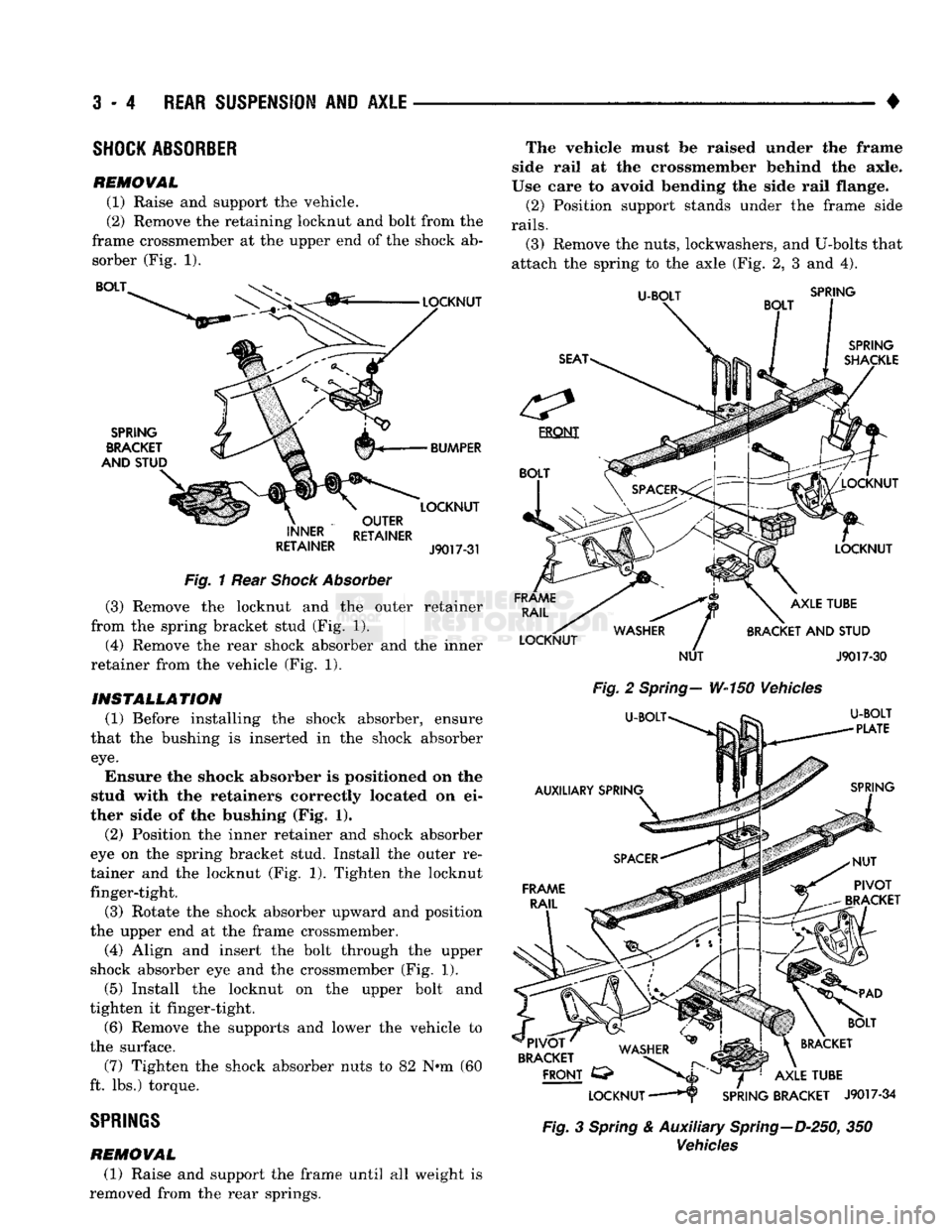
3
- 4
REAR SUSPENSION
AND
AXLE
•
SHOCK
ABSORBER
REMOVAL (1) Raise and support the vehicle.
(2) Remove the retaining locknut and bolt from the
frame crossmember at the upper end of the shock ab sorber (Fig. 1). BOLT
SPRING
BRACKET
AND STUD LOCKNUT
BUMPER LOCKNUT
OUTER
INNER RETAINER
RETAINER
J90T7-31
Fig.
1 Rear
Shock
Absorber
(3) Remove the locknut and the outer retainer
from the spring bracket stud (Fig. 1).
(4) Remove the rear shock absorber and the inner
retainer from the vehicle (Fig. 1).
INSTALLATION (1) Before installing the shock absorber, ensure
that the bushing is inserted in the shock absorber
eye.
Ensure the shock absorber is positioned on the
stud with the retainers correctly located on ei
ther side of the bushing (Fig. 1).
(2) Position the inner retainer and shock absorber
eye on the spring bracket stud. Install the outer re
tainer and the locknut (Fig. 1). Tighten the locknut finger-tight.
(3) Rotate the shock absorber upward and position
the upper end at the frame crossmember.
(4) Align and insert the bolt through the upper
shock absorber eye and the crossmember (Fig. 1).
(5) Install the locknut on the upper bolt and
tighten it finger-tight.
(6) Remove the supports and lower the vehicle to
the surface. (7) Tighten the shock absorber nuts to 82 N*m (60
ft. lbs.) torque.
SPRINGS
REMOVAL (1) Raise and support the frame until all weight is
removed from the rear springs. The vehicle must be raised under the frame
side rail at the crossmember behind the axle.
Use care to avoid bending the side rail flange.
(2) Position support stands under the frame side
rails.
(3) Remove the nuts, lockwashers, and U-bolts that
attach the spring to the axle (Fig. 2, 3 and 4).
U-BOLT
SPRING
SPRING
SHACKLE
FRAME
RAIL
LOCKNUT LOCKNUT
LOCKNUT AXLE TUBE
BRACKET
AND
STUD
NUT
J9017-3Q
Fig.
2
Spring—
W-150 Vehicles
U-BOLT^
U-BOLT
~ '
PLATE
IB*
AUXILIARY SPRING
SPRING
FRAME
RAIL
PIVOT
BRACKET
^ . , _
BOLT
'PIVOT'
WA^HFP
^
in^gJ
\
BRACKET
BRACKET WASHER
^
FRONT
C3>
>>JL
^ T^1
AXLE TUBE
LOCKNUT
——Hr
SPRING BRACKET
J9017-34
Fig.
3
Spring
& Auxiliary
Spring—D-250,
350
Vehicles
Page 134 of 1502
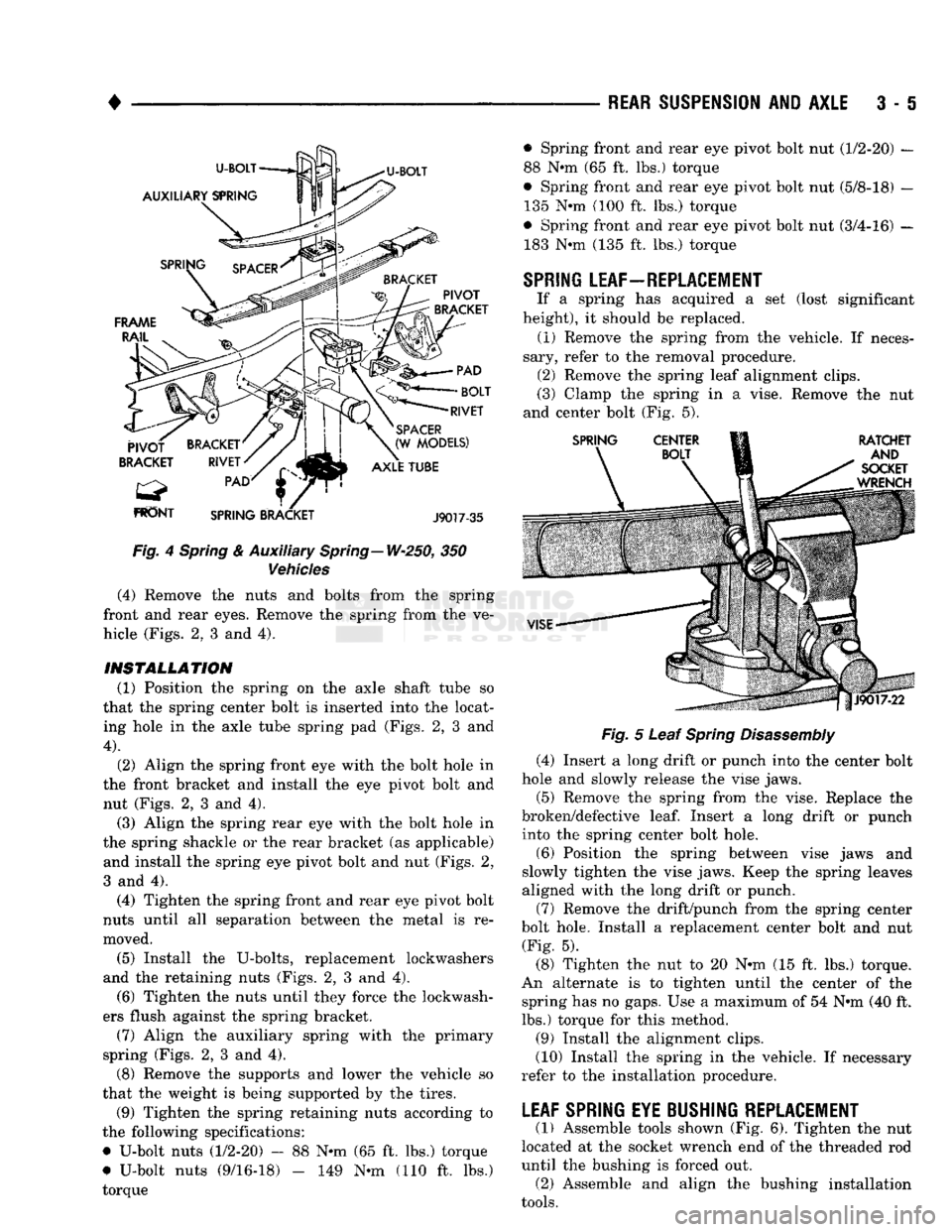
•
Fig.
4
Spring
& Auxiliary Spring—W-250, 350
Vehicles
(4) Remove the nuts and bolts from the spring
front and rear eyes. Remove the spring from the ve
hicle (Figs. 2, 3 and 4).
INSTALLATION (1) Position the spring on the axle shaft tube so
that the spring center bolt is inserted into the locat ing hole in the axle tube spring pad (Figs. 2, 3 and
4).
(2) Align the spring front eye with the bolt hole in
the front bracket and install the eye pivot bolt and nut (Figs. 2, 3 and 4). (3) Align the spring rear eye with the bolt hole in
the spring shackle or the rear bracket (as applicable) and install the spring eye pivot bolt and nut (Figs. 2,
3 and 4).
(4) Tighten the spring front and rear eye pivot bolt
nuts until all separation between the metal is re
moved.
(5) Install the U-bolts, replacement lockwashers
and the retaining nuts (Figs. 2, 3 and 4). (6) Tighten the nuts until they force the lockwash
ers flush against the spring bracket. (7) Align the auxiliary spring with the primary
spring (Figs. 2, 3 and 4).
(8) Remove the supports and lower the vehicle so
that the weight is being supported by the tires.
(9) Tighten the spring retaining nuts according to
the following specifications:
• U-bolt nuts (1/2-20) - 88 N*m (65 ft. lbs.) torque
# U-bolt nuts (9/16-18) - 149 N-m (110 ft. lbs.)
torque —
REAR SUSPENSION
AND
AXLE
3 • 5
Fig.
5 Leaf
Spring
Disassembly
(4) Insert a long drift or punch into the center bolt
hole and slowly release the vise jaws.
(5) Remove the spring from the vise. Replace the
broken/defective
leaf.
Insert a long drift or punch into the spring center bolt hole.
(6) Position the spring between vise jaws and
slowly tighten the vise jaws. Keep the spring leaves
aligned with the long drift or punch.
(7) Remove the drift/punch from the spring center
bolt hole. Install a replacement center bolt and nut (Fig. 5).
(8) Tighten the nut to 20 N-m (15 ft. lbs.) torque.
An alternate is to tighten until the center of the spring has no gaps. Use a maximum of 54 N*m (40 ft.
lbs.) torque for this method.
(9) Install the alignment clips.
(10) Install the spring in the vehicle. If necessary
refer to the installation procedure.
LEAF SPRING EYE BUSHING REPLACEMENT
(1) Assemble tools shown (Fig. 6). Tighten the nut
located at the socket wrench end of the threaded rod
until the bushing is forced out. (2) Assemble and align the bushing installation
tools.
• Spring front and rear eye pivot bolt nut (1/2-20) —
88 N«m (65 ft. lbs.) torque
© Spring front and rear eye pivot bolt nut (5/8-18) — 135 N»m (100 ft. lbs.) torque
• Spring front and rear eye pivot bolt nut (3/4-16) — 183 N-m (135 ft. lbs.) torque
SPRING
LEAF—REPLACEMENT
If a spring has acquired a set (lost significant
height), it should be replaced. (1) Remove the spring from the vehicle. If neces
sary, refer to the removal procedure. (2) Remove the spring leaf alignment clips.
(3) Clamp the spring in a vise. Remove the nut
and center bolt (Fig. 5).
Page 135 of 1502
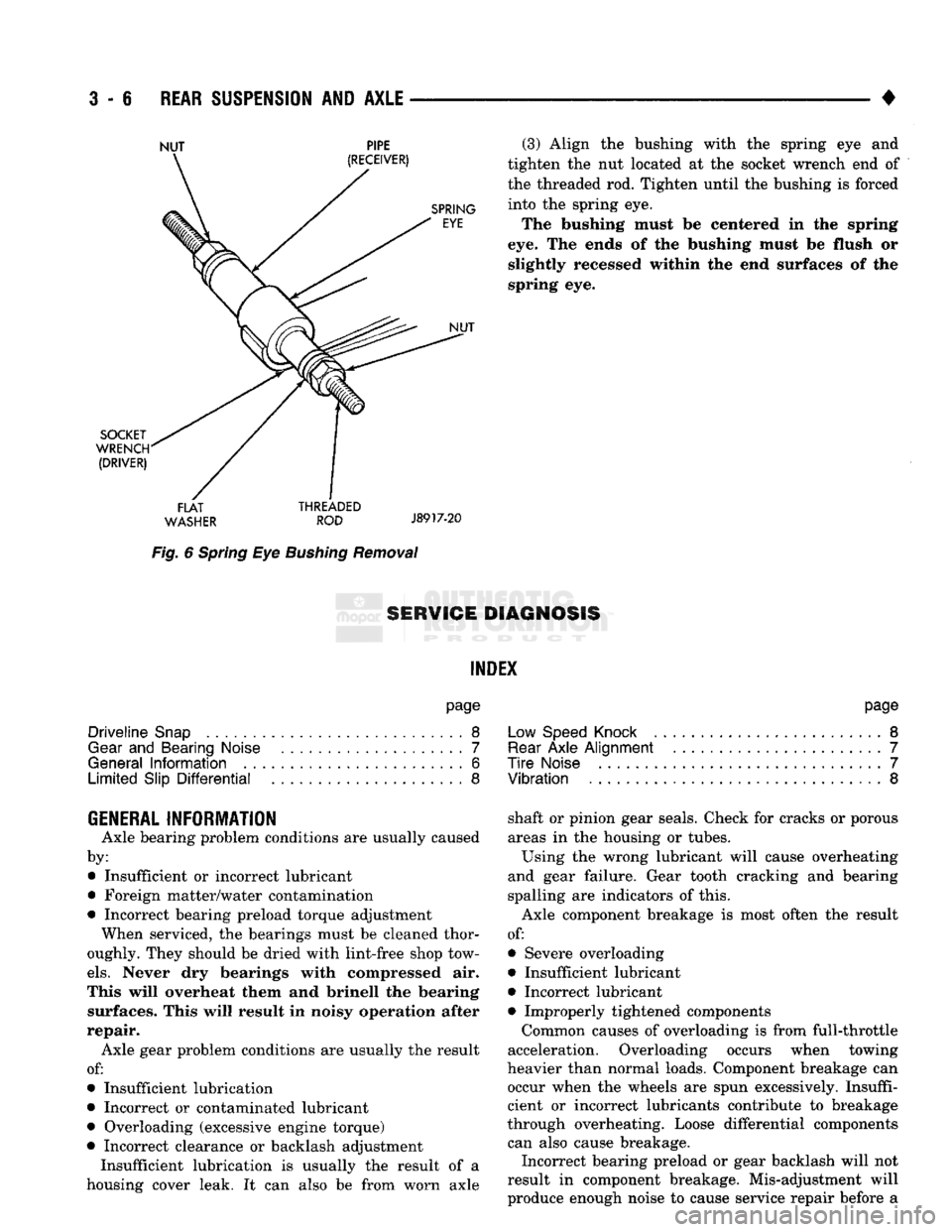
3
- 6
REAR SUSPENSION
AND
AXLE
•
NUT PIPE
SOCKET
WRENCH
(DRIVER)
FLAT
THREADED
WASHER
ROD
J8917-20
Fig.
6
Spring
Eye
Bushing
Removal
(3) Align
the
bushing with
the
spring
eye and
tighten
the nut
located
at the
socket wrench
end of
the threaded
rod.
Tighten until
the
bushing
is
forced into
the
spring
eye.
The bushing must
be
centered
in the
spring
eye.
The
ends
of the
bushing must
be
flush
or
slightly recessed within
the end
surfaces
of the
spring
eye.
8ERW1GE DIAGNOSIS
INDEX
page
Driveline
Snap
8
Gear
and
Bearing Noise
7
General
Information
6
Limited
Slip
Differential
8
page
Low Speed Knock
.........................
8
Rear
Axle
Alignment
.......................
7
Tire
Noise
7
Vibration
8
GENERAL INFORMATION
Axle bearing problem conditions
are
usually caused
by: • Insufficient
or
incorrect lubricant
• Foreign matter/water contamination
• Incorrect bearing preload torque adjustment When serviced,
the
bearings must
be
cleaned thor
oughly. They should
be
dried with lint-free shop tow
els.
Never
dry
bearings with compressed
air.
This will overheat them
and
brinell
the
bearing surfaces. This will result
in
noisy operation after
repair. Axle gear problem conditions
are
usually
the
result
of:
• Insufficient lubrication
• Incorrect
or
contaminated lubricant
• Overloading (excessive engine torque)
• Incorrect clearance
or
backlash adjustment Insufficient lubrication
is
usually
the
result
of a
housing cover leak.
It can
also
be
from worn axle shaft
or
pinion gear seals. Check
for
cracks
or
porous
areas
in the
housing
or
tubes.
Using
the
wrong lubricant will cause overheating
and gear failure. Gear tooth cracking
and
bearing
spalling
are
indicators
of
this.
Axle component breakage
is
most often
the
result
of:
• Severe overloading
• Insufficient lubricant
• Incorrect lubricant • Improperly tightened components
Common causes
of
overloading
is
from full-throttle
acceleration. Overloading occurs when towing
heavier than normal loads. Component breakage
can
occur when
the
wheels
are
spun excessively. Insuffi
cient
or
incorrect lubricants contribute
to
breakage
through overheating. Loose differential components can also cause breakage. Incorrect bearing preload
or
gear backlash will
not
result
in
component breakage. Mis-adjustment will
produce enough noise
to
cause service repair before
a
Page 136 of 1502
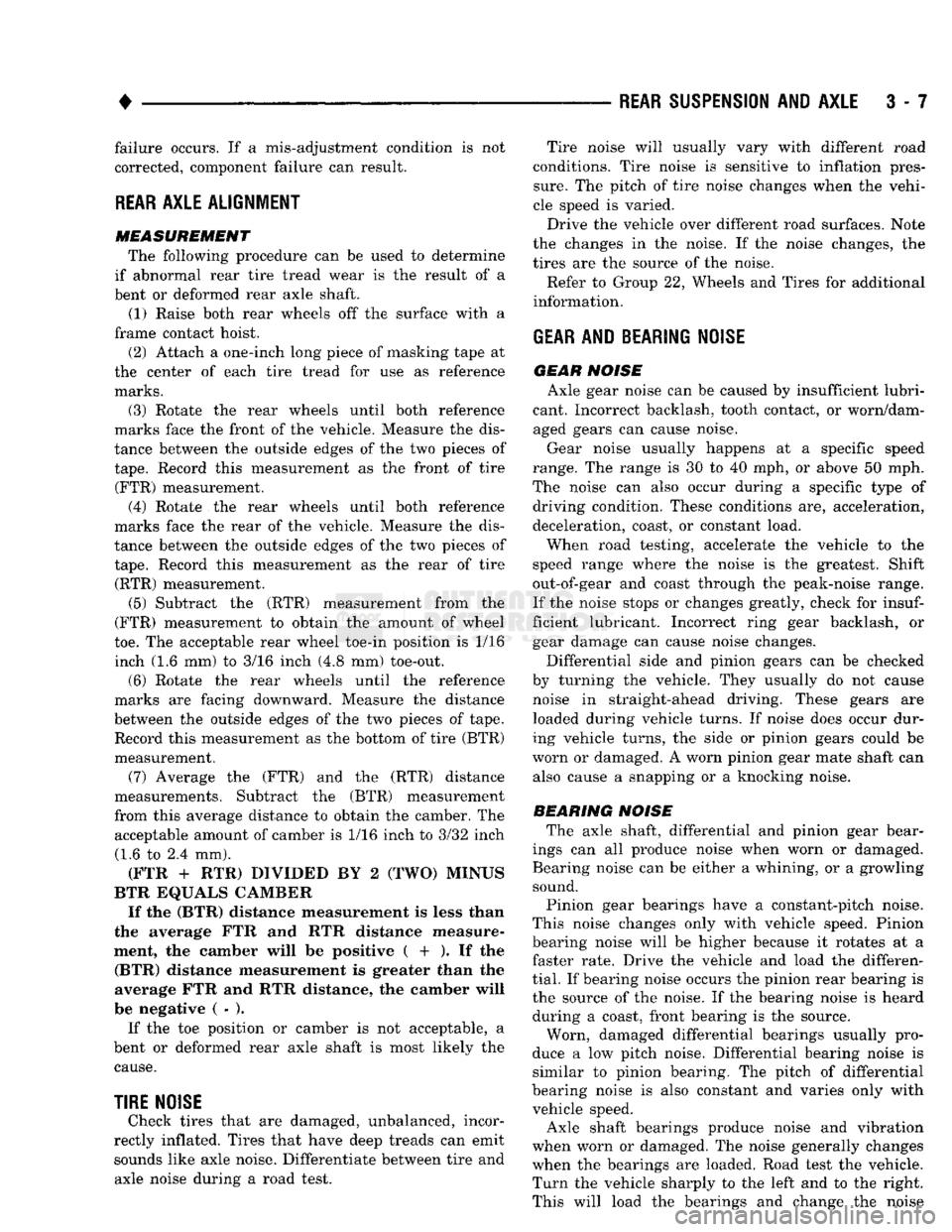
•
RfAR SUSPENSION
AND
AXLE
3 - 7 failure occurs. If a mis-adjustment condition is not
corrected, component failure can result.
REAR
AXLE ALIGNMENT
MEASUREMENT The following procedure can be used to determine
if abnormal rear tire tread wear is the result of a
bent or deformed rear axle shaft.
(1) Raise both rear wheels off the surface with a
frame contact hoist. (2) Attach a one-inch long piece of masking tape at
the center of each tire tread for use as reference marks.
(3) Rotate the rear wheels until both reference
marks face the front of the vehicle. Measure the dis
tance between the outside edges of the two pieces of
tape.
Record this measurement as the front of tire (FTR) measurement.
(4) Rotate the rear wheels until both reference
marks face the rear of the vehicle. Measure the dis
tance between the outside edges of the two pieces of
tape.
Record this measurement as the rear of tire (RTR) measurement.
(5) Subtract the (RTR) measurement from the
(FTR) measurement to obtain the amount of wheel
toe.
The acceptable rear wheel toe-in position is 1/16 inch (1.6 mm) to 3/16 inch (4.8 mm) toe-out.
(6) Rotate the rear wheels until the reference
marks are facing downward. Measure the distance
between the outside edges of the two pieces of tape. Record this measurement as the bottom of tire (BTR)
measurement.
(7) Average the (FTR) and the (RTR) distance
measurements. Subtract the (BTR) measurement
from this average distance to obtain the camber. The acceptable amount of camber is 1/16 inch to 3/32 inch
(1.6 to 2.4 mm).
(FTR + RTR) DIVIDED BY 2 (TWO) MINUS
BTR EQUALS CAMBER
If the (BTR) distance measurement is less than
the average FTR and RTR distance measure
ment, the camber will be positive ( + ). If the (BTR) distance measurement is greater than the average FTR and RTR distance, the camber will
be negative ( - ).
If the toe position or camber is not acceptable, a
bent or deformed rear axle shaft is most likely the cause.
TIRE
NOISE
Check tires that are damaged, unbalanced, incor
rectly inflated. Tires that have deep treads can emit sounds like axle noise. Differentiate between tire and
axle noise during a road test. Tire noise will usually vary with different road
conditions. Tire noise is sensitive to inflation pres
sure.
The pitch of tire noise changes when the vehi
cle speed is varied.
Drive the vehicle over different road surfaces. Note
the changes in the noise. If the noise changes, the
tires are the source of the noise.
Refer to Group 22, Wheels and Tires for additional
information.
GEAR
AND BEARING NOISE
GEAR
NOISE
Axle gear noise can be caused by insufficient lubri
cant. Incorrect backlash, tooth contact, or worn/dam aged gears can cause noise.
Gear noise usually happens at a specific speed
range. The range is 30 to 40 mph, or above 50 mph.
The noise can also occur during a specific type of driving condition. These conditions are, acceleration,
deceleration, coast, or constant load.
When road testing, accelerate the vehicle to the
speed range where the noise is the greatest. Shift
out-of-gear and coast through the peak-noise range.
If the noise stops or changes greatly, check for
insuf
ficient lubricant. Incorrect ring gear backlash, or gear damage can cause noise changes.
Differential side and pinion gears can be checked
by turning the vehicle. They usually do not cause noise in straight-ahead driving. These gears are
loaded during vehicle turns. If noise does occur dur
ing vehicle turns, the side or pinion gears could be
worn or damaged. A worn pinion gear mate shaft can also cause a snapping or a knocking noise.
BEARING NOISE
The axle shaft, differential and pinion gear bear
ings can all produce noise when worn or damaged.
Bearing noise can be either a whining, or a growling sound.
Pinion gear bearings have a constant-pitch noise.
This noise changes only with vehicle speed. Pinion
bearing noise will be higher because it rotates at a faster rate. Drive the vehicle and load the differen
tial.
If bearing noise occurs the pinion rear bearing is the source of the noise. If the bearing noise is heard during a coast, front bearing is the source.
Worn, damaged differential bearings usually pro
duce a low pitch noise. Differential bearing noise is
similar to pinion bearing. The pitch of differential
bearing noise is also constant and varies only with vehicle speed.
Axle shaft bearings produce noise and vibration
when worn or damaged. The noise generally changes
when the bearings are loaded. Road test the vehicle. Turn the vehicle sharply to the left and to the right.
This will load the bearings and change the noise
Page 137 of 1502
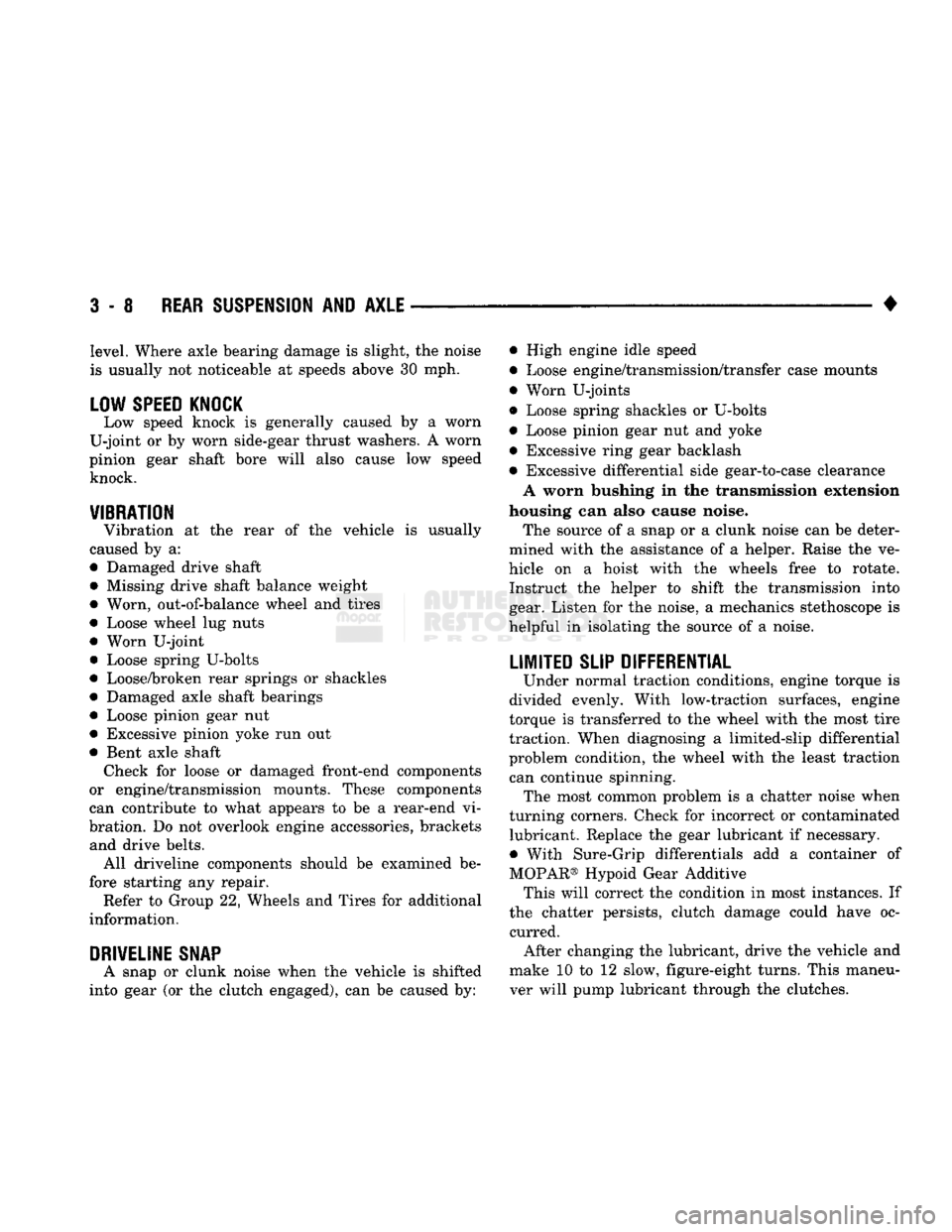
3
- 8
REAR SUSPENSION
AND
AXLE
• level. Where axle bearing damage is slight, the noise
is usually not noticeable at speeds above 30 mph.
LOW SPEED KNOCK
Low speed knock is generally caused by a worn
U-joint or by worn side-gear thrust washers. A worn
pinion gear shaft bore will also cause low speed knock.
VIBRATION
Vibration at the rear of the vehicle is usually
caused by a:
• Damaged drive shaft
• Missing drive shaft balance weight
• Worn, out-of-balance wheel and tires
• Loose wheel lug nuts
• Worn U-joint • Loose spring U-bolts
• Loose/broken rear springs or shackles
• Damaged axle shaft bearings
• Loose pinion gear nut
• Excessive pinion yoke run out
• Bent axle shaft Check for loose or damaged front-end components
or engine/transmission mounts. These components
can contribute to what appears to be a rear-end vi
bration. Do not overlook engine accessories, brackets and drive belts. All driveline components should be examined be
fore starting any repair. Refer to Group 22, Wheels and Tires for additional
information.
DRIVELINE SNAP
A snap or clunk noise when the vehicle is shifted
into gear (or the clutch engaged), can be caused by: • High engine idle speed
• Loose engine/transmission/transfer case mounts
9
Worn U-joints
• Loose spring shackles or U-bolts
• Loose pinion gear nut and yoke
• Excessive ring gear backlash
• Excessive differential side gear-to-case clearance A worn bushing in the transmission extension
housing can also cause noise. The source of a snap or a clunk noise can be deter
mined with the assistance of a helper. Raise the ve
hicle on a hoist with the wheels free to rotate. Instruct the helper to shift the transmission into gear. Listen for the noise, a mechanics stethoscope is
helpful in isolating the source of a noise.
LIMITED
SLIP DIFFERENTIAL
Under normal traction conditions, engine torque is
divided evenly. With low-traction surfaces, engine
torque is transferred to the wheel with the most tire
traction. When diagnosing a limited-slip differential
problem condition, the wheel with the least traction can continue spinning. The most common problem is a chatter noise when
turning corners. Check for incorrect or contaminated lubricant. Replace the gear lubricant if necessary.
• With Sure-Grip differentials add a container of
MOPAR® Hypoid Gear Additive This will correct the condition in most instances. If
the chatter persists, clutch damage could have oc curred. After changing the lubricant, drive the vehicle and
make 10 to 12 slow, figure-eight turns. This maneu
ver will pump lubricant through the clutches.
Page 138 of 1502
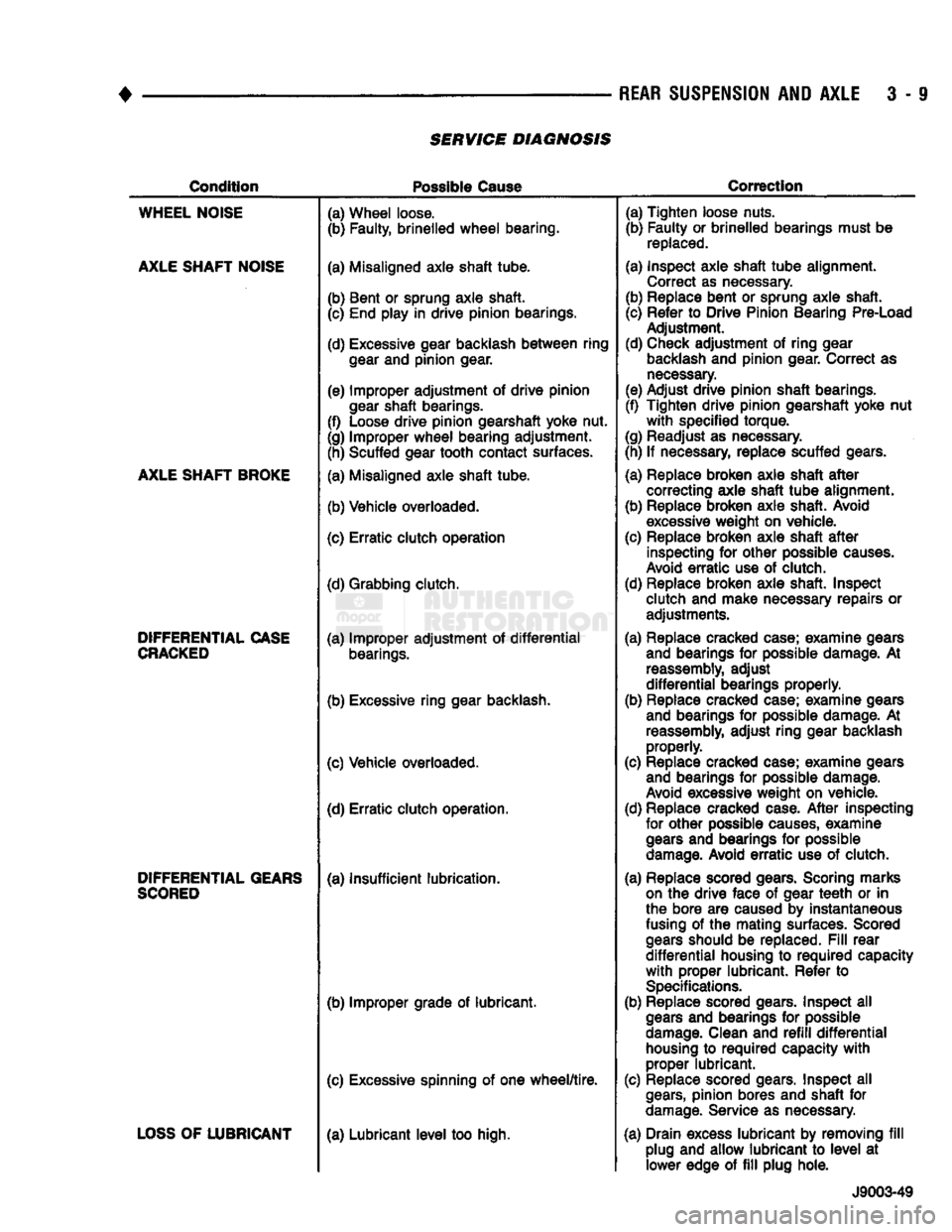
REAR
SUSPENSION
AND
AXLE
3 - 9
SERVICE DIAGNOSIS
Condition
Possible
Cause
Correction
WHEEL
NOISE
AXLE
SHAFT
NOISE
AXLE
SHAFT
BROKE
DIFFERENTIAL
CASE
CRACKED
DIFFERENTIAL
GEARS
SCORED
LOSS
OF
LUBRICANT
(a) Wheel loose.
(b) Faulty, brinelled
wheel
bearing.
(a) Misaligned axle shaft tube.
(b) Bent or sprung axle shaft. (c) End play in drive pinion bearings.
(d) Excessive gear backlash
between
ring
gear
and pinion gear.
(e) Improper adjustment of drive pinion
gear
shaft bearings.
(f) Loose drive pinion gearshaft yoke nut.
(g) Improper
wheel
bearing adjustment. (h) Scuffed gear tooth contact surfaces.
(a) Misaligned axle shaft tube.
(b) Vehicle overloaded.
(c) Erratic clutch operation
(d) Grabbing clutch.
(a) Improper adjustment of
differential
bearings.
(b) Excessive ring gear backlash.
(c) Vehicle overloaded. (d) Erratic clutch operation.
(a) Insufficient lubrication.
(b) Improper grade of lubricant.
(c) Excessive spinning of one
wheel/tire.
(a) Lubricant
level
too high. (a) Tighten loose nuts.
(b) Faulty or brinelled bearings must be
replaced.
(a) Inspect axle shaft
tube
alignment. Correct as necessary.
(b) Replace bent or sprung axle shaft.
(c) Refer to Drive Pinion Bearing Pre-Load Adjustment.
(d) Check adjustment of ring gear
backlash
and pinion gear. Correct as
necessary.
(e) Adjust drive pinion shaft bearings.
(f) Tighten drive pinion gearshaft yoke nut
with
specified torque.
(g) Readjust as necessary.
(h) If necessary, replace scuffed gears.
(a) Replace broken axle shaft
after
correcting axle shaft
tube
alignment.
(b) Replace broken axle shaft. Avoid
excessive
weight on vehicle.
(c) Replace broken axle shaft
after
inspecting for other possible
causes.
Avoid
erratic
use of clutch.
(d) Replace broken axle shaft. Inspect clutch and make necessary repairs or adjustments.
(a) Replace cracked case; examine gears and bearings for possible damage. At
reassembly,
adjust
differential
bearings properly.
(b) Replace cracked case; examine gears and bearings for possible damage. At
reassembly,
adjust ring gear backlash properly.
(c) Replace cracked case; examine gears and bearings for possible damage.
Avoid
excessive weight on vehicle.
(d) Replace cracked case.
After
inspecting for other possible
causes,
examine
gears
and bearings for possible
damage.
Avoid
erratic
use of clutch.
(a) Replace scored gears. Scoring marks
on
the drive face of gear
teeth
or in
the bore are caused by instantaneous
fusing
of the mating surfaces. Scored
gears
should be replaced.
Fill
rear
differential
housing to
required
capacity
with
proper lubricant. Refer to
Specifications.
(b) Replace scored gears. Inspect all
gears
and bearings for possible
damage.
Clean and
refill
differential
housing
to
required
capacity
with
proper lubricant.
(c) Replace scored gears. Inspect all
gears,
pinion bores and shaft for
damage.
Service as necessary.
(a) Drain excess lubricant by removing
fill
plug and allow lubricant to
level
at lower edge of
fill
plug hole.
J9003-49
Page 139 of 1502
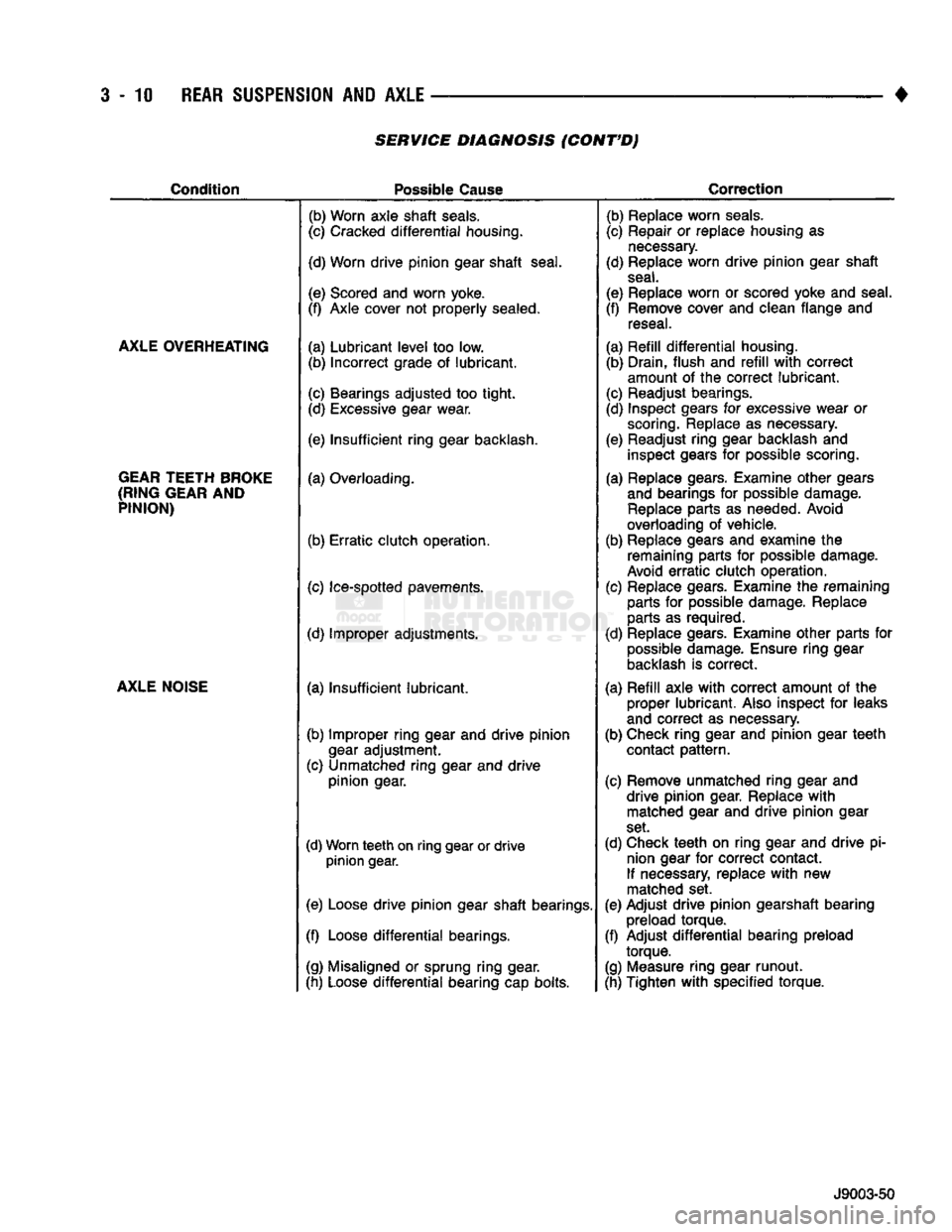
3-10
REAR SUSPENSION
AND
AXLE
SERVICE DIAGNOSIS (CONT'D)
Condition
Possible
Cause
Correction
AXLE OVERHEATING
GEAR TEETH BROKE
(RING GEAR
AND
PINION)
AXLE NOISE
(b) Worn axle
shaft
seals.
(c) Cracked
differential
housing.
(d) Worn
drive
pinion
gear
shaft
seal.
(e) Scored and worn yoke.
(f) Axle cover not
properly
sealed.
(a)
Lubricant
level
too low. (b)
Incorrect
grade of
lubricant.
(c) Bearings
adjusted
too
tight.
(d) Excessive gear wear.
(e)
Insufficient
ring
gear backlash,
(a) Overloading.
(b)
Erratic
clutch
operation.
(c) Ice-spotted pavements.
(d) Improper adjustments.
(a)
Insufficient
lubricant.
(b) Improper
ring
gear and
drive
pinion
gear
adjustment.
(c) Unmatched
ring
gear and
drive
pinion
gear.
(d) Worn
teeth
on
ring
gear or
drive
pinion
gear.
(e) Loose
drive
pinion
gear
shaft
bearings.
(f) Loose
differential
bearings.
(g) Misaligned or sprung
ring
gear.
(h) Loose
differential
bearing cap bolts. (b) Replace worn
seals.
(c) Repair or replace housing as
necessary.
(d) Replace worn
drive
pinion
gear
shaft
seal.
(e) Replace worn or scored yoke and seal.
(f) Remove cover and clean flange and reseal.
(a)
Refill
differential
housing. (b) Drain,
flush
and
refill
with
correct
amount of the
correct
lubricant.
(c) Readjust bearings.
(d) Inspect gears for excessive wear or scoring. Replace as necessary.
(e) Readjust
ring
gear backlash and inspect gears for possible scoring.
(a) Replace gears. Examine
other
gears and bearings for possible damage. Replace parts as needed. Avoid
overloading of vehicle.
(b) Replace gears and examine the remaining parts for possible damage.
Avoid
erratic
clutch
operation.
(c) Replace gears. Examine the remaining parts for possible damage. Replace
parts as required.
(d) Replace gears. Examine
other
parts for possible damage. Ensure
ring
gear
backlash is
correct.
(a)
Refill
axle
with
correct
amount of the proper
lubricant.
Also inspect for leaks
and
correct
as necessary.
(b) Check
ring
gear and
pinion
gear
teeth
contact
pattern.
(c) Remove unmatched
ring
gear and
drive
pinion
gear. Replace
with
matched gear and
drive
pinion
gear
set.
(d) Check
teeth
on
ring
gear and
drive
pi nion gear for
correct
contact.
If necessary, replace
with
new
matched set.
(e) Adjust
drive
pinion
gearshaft bearing preload
torque.
(f) Adjust
differential
bearing preload
torque.
(g) Measure
ring
gear
runout.
(h) Tighten
with
specified
torque.
J9003-50
Page 140 of 1502
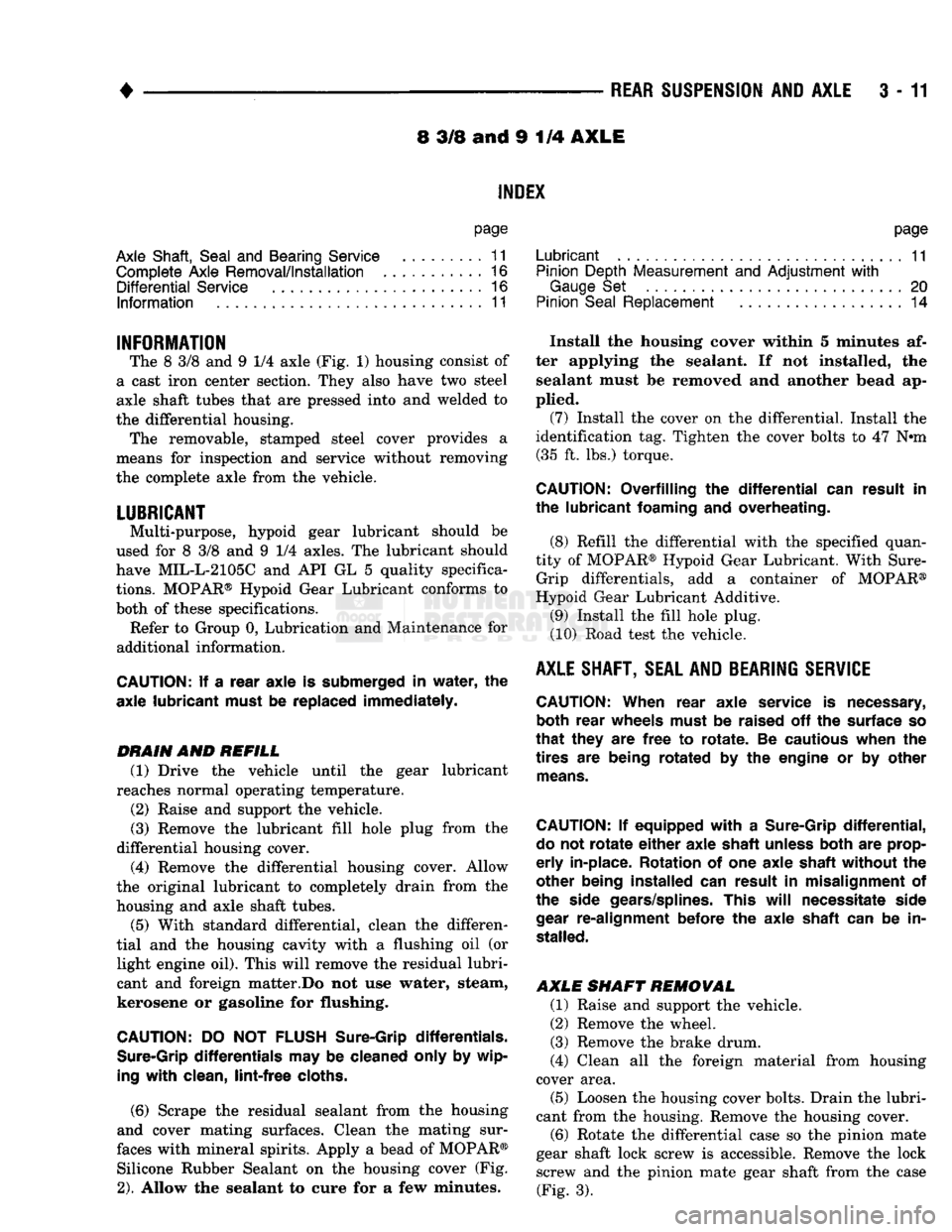
•
REAR
SUSPENSION
AND
AXLE
3 - 11 8 3/8 and 9 1/4
AXLE
INDEX
page
Axle Shaft, Seal
and
Bearing Service
......... 11
Complete Axle Removal/Installation
16
Differential
Service
16
Information
11
INFORMATION
The 8 3/8 and 9 1/4 axle (Fig. 1) housing consist of
a cast iron center section. They also have two steel
axle shaft tubes that are pressed into and welded to
the differential housing. The removable, stamped steel cover provides a
means for inspection and service without removing
the complete axle from the vehicle.
LUBRICANT
Multi-purpose, hypoid gear lubricant should be
used for 8 3/8 and 9 1/4 axles. The lubricant should
have MIL-L-2105C and API GL 5 quality specifica
tions.
MOPAR® Hypoid Gear Lubricant conforms to
both of these specifications.
Refer to Group 0, Lubrication and Maintenance for
additional information.
CAUTION:
If a
rear axle
is
submerged
in
water,
the
axle lubricant must
be
replaced immediately.
DRAIN
AND
REFILL
(1) Drive the vehicle until the gear lubricant
reaches normal operating temperature.
(2) Raise and support the vehicle.
(3) Remove the lubricant fill hole plug from the
differential housing cover.
(4) Remove the differential housing cover. Allow
the original lubricant to completely drain from the
housing and axle shaft tubes. (5) With standard differential, clean the differen
tial and the housing cavity with a flushing oil (or light engine oil). This will remove the residual lubri
cant and foreign matter.Do not use water, steam,
kerosene or gasoline for flushing.
CAUTION:
DO NOT
FLUSH
Sure-Grip differentials.
Sure-Grip
differentials
may be
cleaned only
by
wip
ing
with
clean,
lint-free
cloths.
(6)
Scrape the residual sealant from the housing
and cover mating surfaces. Clean the mating sur
faces with mineral spirits. Apply a bead of MOPAR® Silicone Rubber Sealant on the housing cover (Fig.
2).
Allow the sealant to cure for a few minutes.
page
Lubricant
11
Pinion Depth Measurement
and
Adjustment
with
Gauge
Set 20
Pinion
Seal
Replacement
14
Install the housing cover within 5 minutes af
ter applying the sealant. If not installed, the sealant must be removed and another bead ap
plied. (7) Install the cover on the differential. Install the
identification tag. Tighten the cover bolts to 47 N#m (35 ft. lbs.) torque.
CAUTION:
Overfilling
the
differential
can
result
in
the lubricant foaming
and
overheating.
(8) Refill the differential with the specified quan
tity of MOPAR® Hypoid Gear Lubricant. With Sure- Grip differentials, add a container of MOPAR®
Hypoid Gear Lubricant Additive.
(9) Install the fill hole plug.
(10) Road test the vehicle.
AXLE
SHAFT, SEAL AND BEARING
SERVICE
CAUTION:
When rear axle service
is
necessary, both rear wheels must
be
raised
off the
surface
so
that
they
are
free
to
rotate.
Be
cautious when
the
tires
are
being rotated
by the
engine
or by
other
means.
CAUTION:
If
equipped
with
a
Sure-Grip
differential,
do
not
rotate
either
axle shaft unless both
are
prop
erly
in-place. Rotation
of one
axle shaft without
the
other being installed
can
result
in
misalignment
of
the side gears/splines. This
will
necessitate side
gear
re-alignment before
the
axle shaft
can be in
stalled.
AXLE SHAFT REMOVAL
(1) Raise and support the vehicle.
(2) Remove the wheel.
(3) Remove the brake drum.
(4) Clean all the foreign material from housing
cover area.
(5) Loosen the housing cover bolts. Drain the lubri
cant from the housing. Remove the housing cover.
(6)
Rotate the differential case so the pinion mate
gear shaft lock screw is accessible. Remove the lock screw and the pinion mate gear shaft from the case (Fig. 3).