DODGE TRUCK 1993 Service Repair Manual
Manufacturer: DODGE, Model Year: 1993, Model line: TRUCK, Model: DODGE TRUCK 1993Pages: 1502, PDF Size: 80.97 MB
Page 1351 of 1502
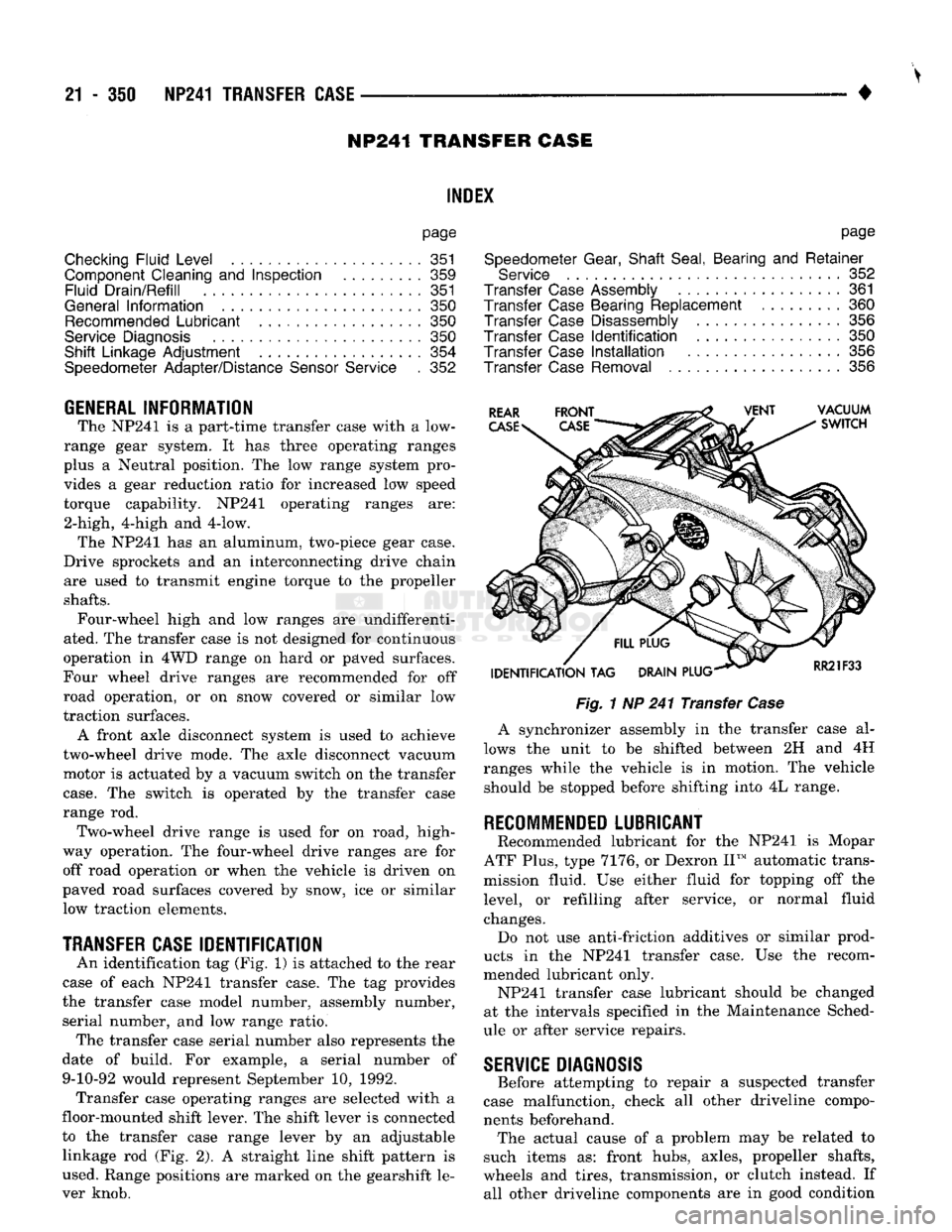
21 - 350 NP241
TRANSFER CASE
• NP241 TRANSFER CASE
INDEl
page
Checking
Fluid
Level
351
Component Cleaning
and
Inspection
359
Fluid
Drain/Refill
351
General
Information
350
Recommended
Lubricant
.................. 350
Service
Diagnosis
....................... 350
Shift
Linkage
Adjustment
354
Speedometer Adapter/Distance
Sensor
Service
. 352
page
Speedometer Gear, Shaft
Seal,
Bearing
and
Retainer
Service
352
Transfer
Case
Assembly
.................. 361
Transfer
Case
Bearing Replacement
......... 360
Transfer
Case
Disassembly
................ 356
Transfer
Case
Identification ................ 350
Transfer
Case
Installation
................. 356
Transfer
Case
Removal
356
GENERAL
INFORMATION
The NP241 is a part-time transfer case with a low-
range gear system. It has three operating ranges
plus a Neutral position. The low range system pro vides a gear reduction ratio for increased low speed
torque capability. NP241 operating ranges are: 2-high, 4-high and 4-low. The NP241 has an aluminum, two-piece gear case.
Drive sprockets and an interconnecting drive chain are used to transmit engine torque to the propeller
shafts.
Four-wheel high and low ranges are undifferenti
ated. The transfer case is not designed for continuous
operation in 4WD range on hard or paved surfaces.
Four wheel drive ranges are recommended for off
road operation, or on snow covered or similar low
traction surfaces. A front axle disconnect system is used to achieve
two-wheel drive mode. The axle disconnect vacuum motor is actuated by a vacuum switch on the transfer
case.
The switch is operated by the transfer case
range rod. Two-wheel drive range is used for on road, high
way operation. The four-wheel drive ranges are for off road operation or when the vehicle is driven on
paved road surfaces covered by snow, ice or similar low traction elements.
TRANSFER CASE
IDENTIFICATION
An identification tag (Fig, 1) is attached to the rear
case of each NP241 transfer case. The tag provides
the transfer case model number, assembly number, serial number, and low range ratio. The transfer case serial number also represents the
date of build. For example, a serial number of 9-10-92 would represent September 10, 1992. Transfer case operating ranges are selected with a
floor-mounted shift lever. The shift lever is connected
to the transfer case range lever by an adjustable linkage rod (Fig. 2). A straight line shift pattern is
used. Range positions are marked on the gearshift le
ver knob.
Fig.
1 NP 241 Transfer
Case
A synchronizer assembly in the transfer case al
lows the unit to be shifted between 2H and 4H
ranges while the vehicle is in motion. The vehicle should be stopped before shifting into 4L range.
RECOMMENDED
LUBRICANT
Recommended lubricant for the NP241 is Mopar
ATF Plus, type 7176, or Dexron II™ automatic trans
mission fluid. Use either fluid for topping off the
level, or refilling after service, or normal fluid
changes. Do not use anti-friction additives or similar prod
ucts in the NP241 transfer case. Use the recom
mended lubricant only. NP241 transfer case lubricant should be changed
at the intervals specified in the Maintenance Sched
ule or after service repairs.
SERVICE
DIAGNOSIS
Before attempting to repair a suspected transfer
case malfunction, check all other driveline compo
nents beforehand. The actual cause of a problem may be related to
such items as: front hubs, axles, propeller shafts,
wheels and tires, transmission, or clutch instead. If all other driveline components are in good condition
Page 1352 of 1502
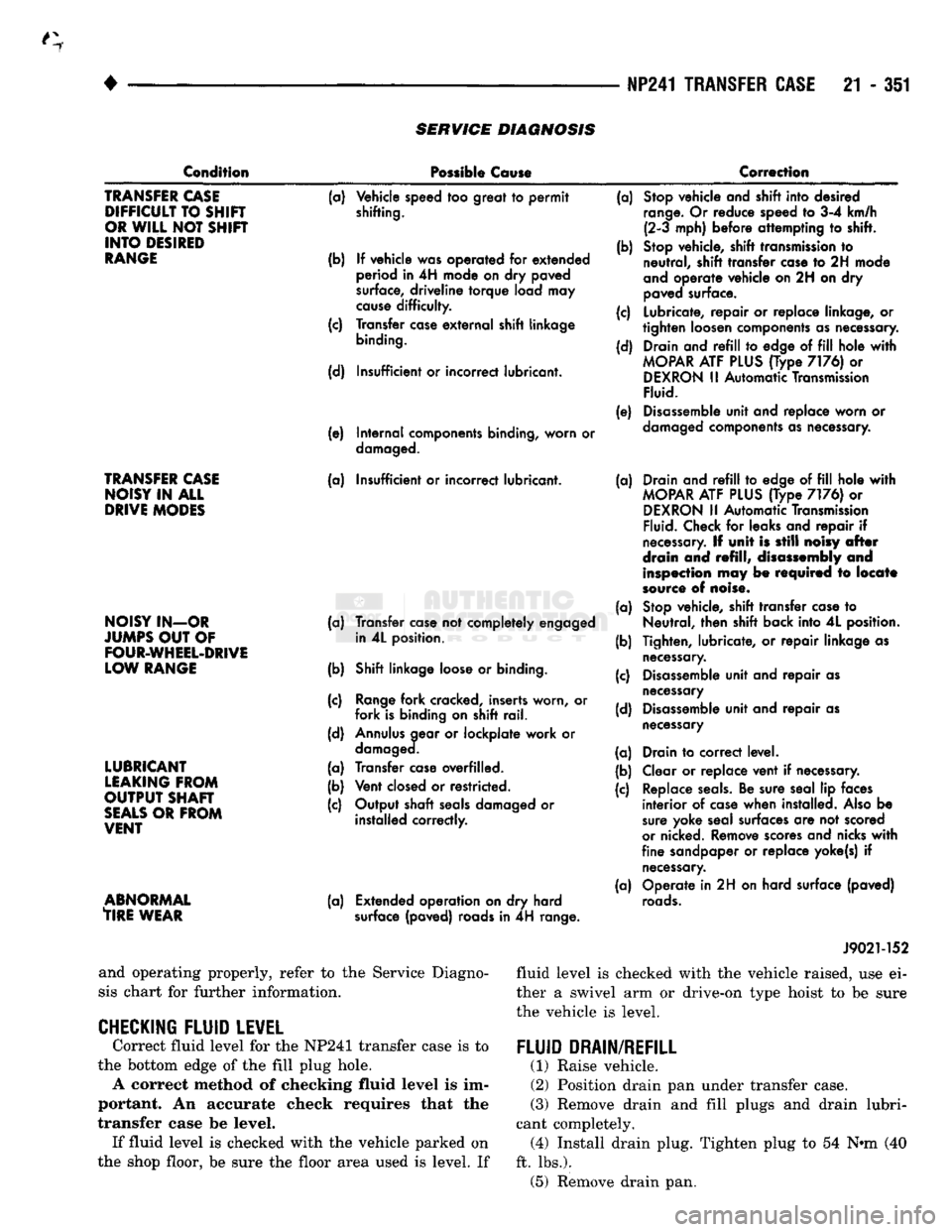
•
NP241 TRANSFER CASE
21 - 351
SERVICE
DIAGNOSIS
Condition
Possible
Cause
Correction
TRANSFER
CASE
DIFFICULT
TO
SHIR
OR
WILL
NOT
SHIFT
INTO
DESIRED
RANGE
TRANSFER
CASE
NOISY
IN ALL
DRIVE
MODES
NOISY
IN-OR
JUMPS
OUT
OF
FOUR-WHEEL-DRIVE
LOW
RANGE
LUBRICANT
LEAKING
FROM
OUTPUT
SHAFT
SEALS
OR
FROM
VENT
ABNORMAL
TIRE
WEAR
(a)
Vehicle speed
too
great
to permit
shifting.
(b)
If
vehicle was operated
for
extended
period
in 4H
mode
on dry
paved
surface,
driveline
torque
load
may
cause
difficulty.
(c) Transfer
case
external
shift linkage
binding.
(d) Insufficient
or
incorrect lubricant.
(e) Internal components binding, worn
or
damaged.
(a) Insufficient
or
incorrect lubricant.
(a) Transfer
case
not
completely engaged in
4L
position.
(b) Shift linkage
loose
or
binding.
(c)
Range
fork cracked, inserts worn,
or
fork is binding
on
shift rail.
(d)
Annulus
gear
or
lockplate work
or
damaged.
(a) Transfer
case
overfilled.
(b) Vent
closed
or
restricted.
(c) Output shaft
seals
damaged
or
installed correctly.
(a) Extended operation
on dry
hard
surface
(paved) roads
in 4H
range. (a)
Stop
vehicle and shift into desired
range.
Or
reduce speed
to 3-4
km/h (2-3 mph) before attempting
to
shift.
(b)
Stop
vehicle, shift
transmission
to
neutral, shift transfer
case
to 2H
mode
and
operate vehicle on
2H on dry
paved
surface.
(c) Lubricate, repair
or
replace linkage,
or
tighten loosen components as necessary.
(d) Drain and
refill to
edge
of fill
hole
with
MOPAR
ATF
PLUS
(Type
7176) or
DEXRON
II
Automatic
Transmission
Fluid.
(e)
Disassemble
unit and replace worn
or
damaged
components
as necessary.
(a) Drain and
refill to
edge
of fill
hole
with
MOPAR
ATF
PLUS
(Type
7176) or
DEXRON
II
Automatic
Transmission
Fluid.
Check
for
leaks and repair
if
necessary.
If
unit
is
still
noisy
after
drain
and
refill,
disassembly
and
inspection
may be
required
to
locate
source
of
noise.
(a)
Stop
vehicle, shift transfer
case
to
Neutral, then shift back into
4L
position.
(b) Tighten, lubricate,
or
repair linkage
as
necessary.
(c)
Disassemble
unit and repair
as
necessary
(d)
Disassemble
unit and repair
as
necessary
(a) Drain
to
correct level.
(b) Clear
or
replace vent
if
necessary.
(c) Replace
seals.
Be sure seal
lip
faces interior
of
case
when installed.
Also
be
sure
yoke seal surfaces
are not
scored
or
nicked. Remove
scores
and nicks
with
fine sandpaper
or
replace yoke(s)
if
necessary.
(a) Operate
in 2H on
hard surface (paved)
roads.
and operating properly, refer to the Service Diagno
sis chart for further information.
CHECKING FLUID LEVEL
Correct fluid level for the NP241 transfer case is to
the bottom edge of the fill plug hole. A correct method of checking fluid level is im
portant. An accurate check requires that the
transfer case be level. If fluid level is checked with the vehicle parked on
the shop floor, be sure the floor area used is level. If J9021-152
fluid level is checked with the vehicle raised, use ei
ther a swivel arm or drive-on type hoist to be sure
the vehicle is level.
FLUID DRAIN/REFILL
(1) Raise vehicle.
(2) Position drain pan under transfer case.
(3)
Remove drain and fill plugs and drain lubri
cant completely. (4) Install drain plug. Tighten plug to 54 N»m (40
ft. lbs.). (5) Remove drain pan.
Page 1353 of 1502
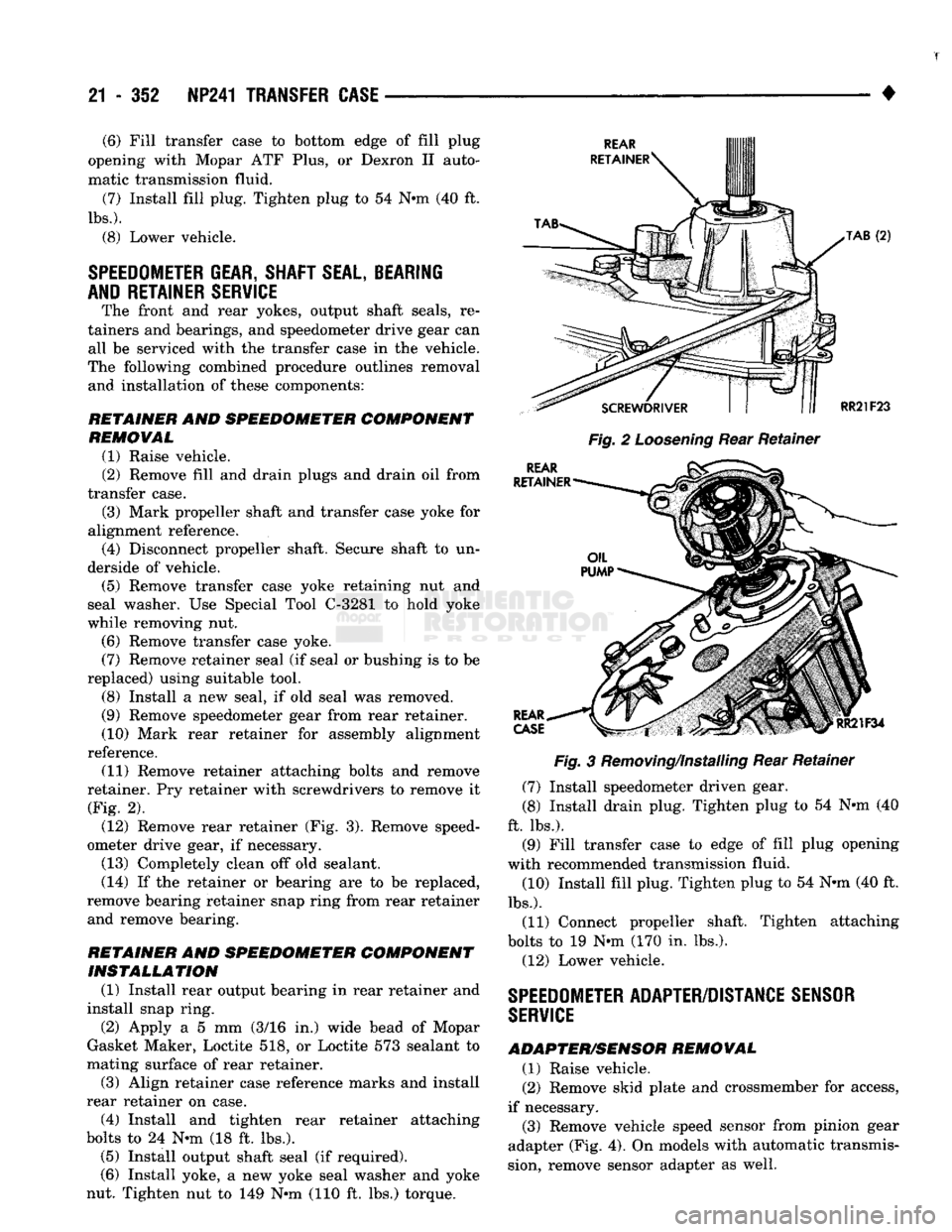
21 - 352 NP241
TRANSFER
CASE
—
•
Fig.
2
Loosening
Rear Retainer
Fig.
3 Removing/Installing Rear Retainer
(7) Install speedometer driven gear.
(8) Install drain plug. Tighten plug to 54 N-m (40
ft. lbs.). (9) Fill transfer case to edge of fill plug opening
with recommended transmission fluid. (10) Install fill plug. Tighten plug to 54 N-m (40 ft.
lbs.).
(11) Connect propeller shaft. Tighten attaching
bolts to 19 N-m (170 in. lbs.).
(12) Lower vehicle.
SPEEDOMETER
ADAPTER/DISTANCE
SENSOR
SERVICE
ADAPTER/SENSOR
REMOVAL
(1) Raise vehicle.
(2) Remove skid plate and crossmember for access,
if necessary. (3) Remove vehicle speed sensor from pinion gear
adapter (Fig. 4). On models with automatic transmis
sion, remove sensor adapter as well.
(6) Fill transfer case to bottom edge of fill plug
opening with Mopar ATF Plus, or Dexron II auto
matic transmission fluid.
(7) Install fill plug. Tighten plug to 54 N«m (40 ft.
lbs.).
(8) Lower vehicle.
SPEEDOMETER
GEAR, SHAFT
SEAL,
BEARING
AND RETAINER SERVICE
The front and rear yokes, output shaft seals, re
tainers and bearings, and speedometer drive gear can all be serviced with the transfer case in the vehicle.
The following combined procedure outlines removal and installation of these components:
RETAINER
AND
SPEEDOMETER COMPONENT REMOVAL
(1) Raise vehicle.
(2) Remove fill and drain plugs and drain oil from
transfer case. (3) Mark propeller shaft and transfer case yoke for
alignment reference. (4) Disconnect propeller shaft. Secure shaft to un
derside of vehicle. (5) Remove transfer case yoke retaining nut and
seal washer. Use Special Tool C-3281 to hold yoke
while removing nut. (6) Remove transfer case yoke. (7) Remove retainer seal (if seal or bushing is to be
replaced) using suitable tool.
(8) Install a new seal, if old seal was removed.
(9) Remove speedometer gear from rear retainer.
(10) Mark rear retainer for assembly alignment
reference. (11) Remove retainer attaching bolts and remove
retainer. Pry retainer with screwdrivers to remove it (Fig. 2). (12) Remove rear retainer (Fig. 3). Remove speed
ometer drive gear, if necessary.
(13) Completely clean off old sealant.
(14) If the retainer or bearing are to be replaced,
remove bearing retainer snap ring from rear retainer
and remove bearing.
RETAINER
AND
SPEEDOMETER COMPONENT INSTALLATION
(1) Install rear output bearing in rear retainer and
install snap ring. (2) Apply a 5 mm (3/16 in.) wide bead of Mopar
Gasket Maker, Loctite 518, or Loctite 573 sealant to
mating surface of rear retainer.
(3) Align retainer case reference marks and install
rear retainer on case. (4) Install and tighten rear retainer attaching
bolts to 24 N«m (18 ft. lbs.). (5) Install output shaft seal (if required).
(6) Install yoke, a new yoke seal washer and yoke
nut. Tighten nut to 149 N-m (110 ft. lbs.) torque.
Page 1354 of 1502
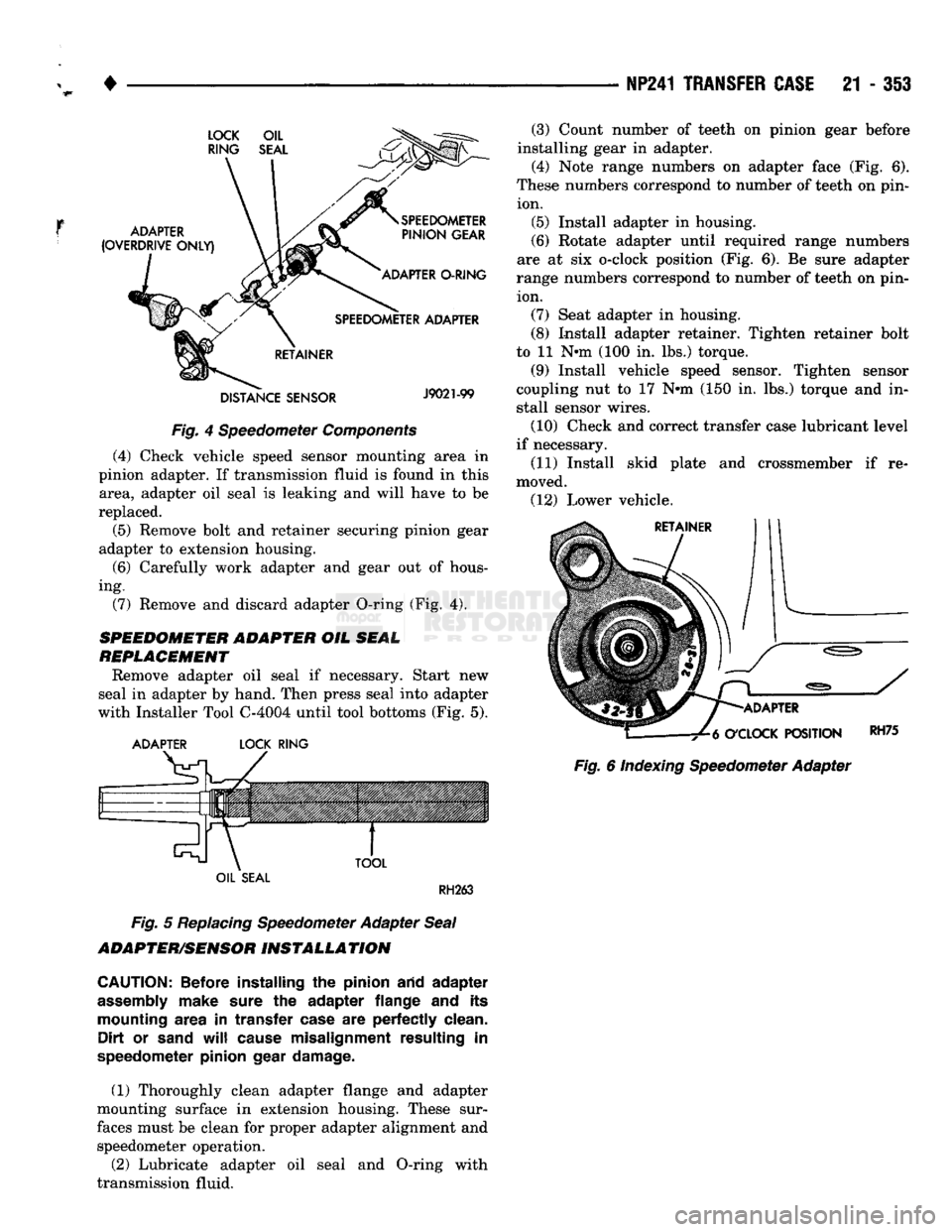
•
NP241 TRANSFER
CASE
21 - 313
LOCK OIL RING SEAL
ADAPTER
(OVERDRIVE
ONLY)
SPEEDOMETER
PINION
GEAR
ADAPTER
O-RING
SPEEDOMETER
ADAPTER
RETAINER
DISTANCE
SENSOR
J9021-99
Fig.
4 Speedometer
Components
(4) Check vehicle speed sensor mounting area in
pinion adapter. If transmission fluid is found in this area, adapter oil seal is leaking and will have to be
replaced.
(5) Remove bolt and retainer securing pinion gear
adapter to extension housing.
(6)
Carefully work adapter and gear out of hous
ing. (7) Remove and discard adapter O-ring (Fig. 4).
SPEEDOMETER ADAPTER
OIL
SEAL
REPLACEMENT
Remove adapter oil seal if necessary. Start new
seal in adapter by hand. Then press seal into adapter
with Installer Tool C-4004 until tool bottoms (Fig. 5).
ADAPTER
LOCK
RING
TOOL
(3) Count number of teeth on pinion gear before
installing gear in adapter.
(4) Note range numbers on adapter face (Fig. 6).
These numbers correspond to number of teeth on pin ion. (5) Install adapter in housing.
(6)
Rotate adapter until required range numbers
are at six o-clock position (Fig. 6). Be sure adapter
range numbers correspond to number of teeth on pin ion. (7) Seat adapter in housing.
(8) Install adapter retainer. Tighten retainer bolt
to 11 N-m (100 in. lbs.) torque.
(9) Install vehicle speed sensor. Tighten sensor
coupling nut to 17 N-m (150 in. lbs.) torque and in
stall sensor wires.
(10) Check and correct transfer case lubricant level
if necessary.
(11) Install skid plate and crossmember if re
moved. (12) Lower vehicle.
ADAPTER
O'CLOCK
POSITION
Fig.
6 Indexing Speedometer Adapter
RH75
OIL
SEAL
RH263
Fig.
5
Replacing
Speedometer Adapter
Seal
ADAPTER/SENSOR
INSTALLATION
CAUTION:
Before installing
the
pinion arid adapter
assembly
make sure
the
adapter flange
and its
mounting area
in
transfer case
are
perfectly clean. Dirt
or
sand
will
cause misalignment resulting
in
speedometer pinion gear damage.
(1) Thoroughly clean adapter flange and adapter
mounting surface in extension housing. These sur
faces must be clean for proper adapter alignment and speedometer operation.
(2) Lubricate adapter oil seal and O-ring with
transmission fluid.
Page 1355 of 1502
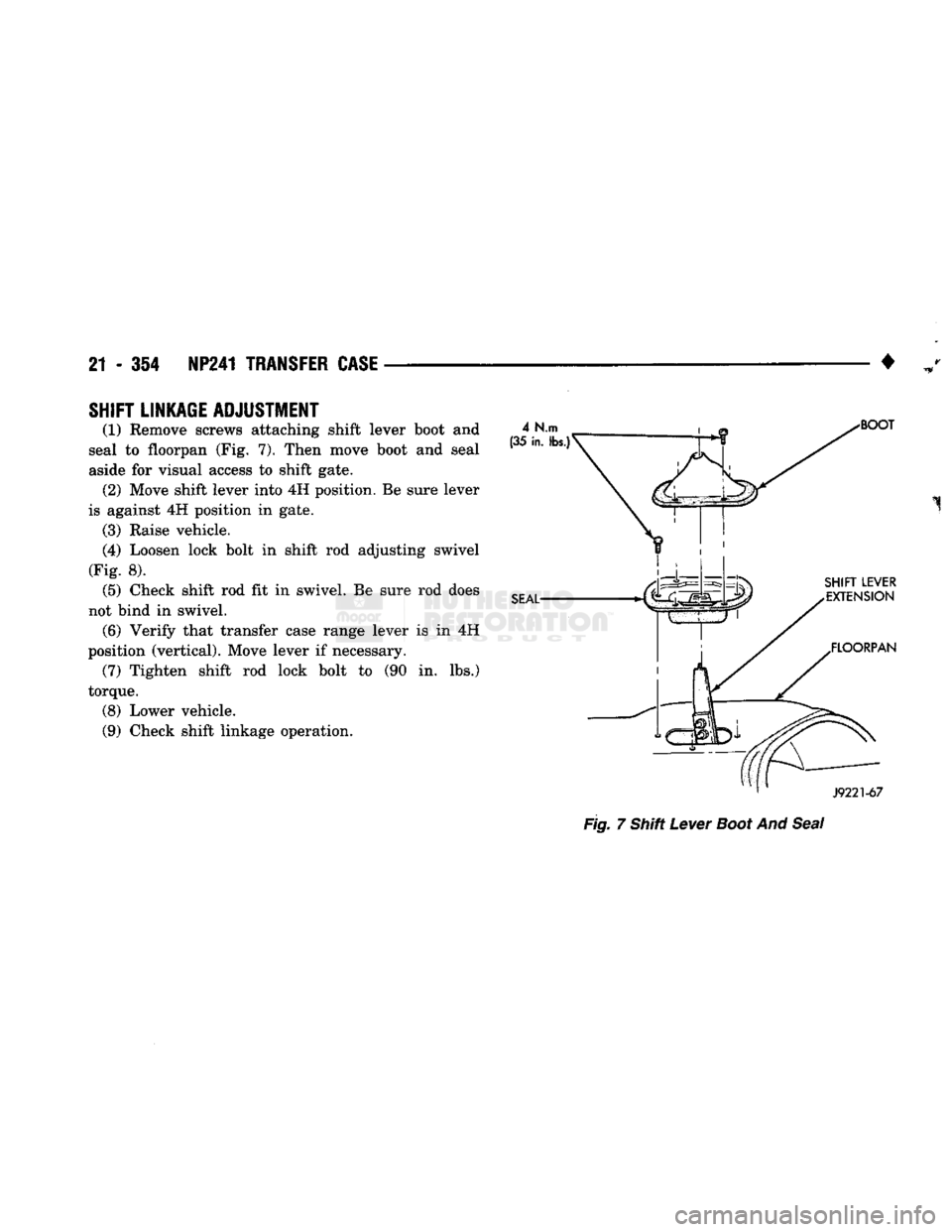
21 - 354 NP241
TRANSFER
CASE
•
SHIFT
LINKAGE
ADJUSTMENT
(1) Remove screws attaching shift lever boot and
seal to floorpan (Fig. 7). Then move boot and seal aside for visual access to shift gate. (2) Move shift lever into 4H position. Be sure lever
is against 4H position in gate. (3) Raise vehicle.
(4) Loosen lock bolt in shift rod adjusting swivel
(Fig. 8). (5) Check shift rod fit in swivel. Be sure rod does
not bind in swivel. (6) Verify that transfer case range lever is in 4H
position (vertical). Move lever if necessary. (7) Tighten shift rod lock bolt to (90 in. lbs.)
torque. (8) Lower vehicle.
(9) Check shift linkage operation.
Fig.
7 Shift
Lever
Boot
And
Seal
Page 1356 of 1502
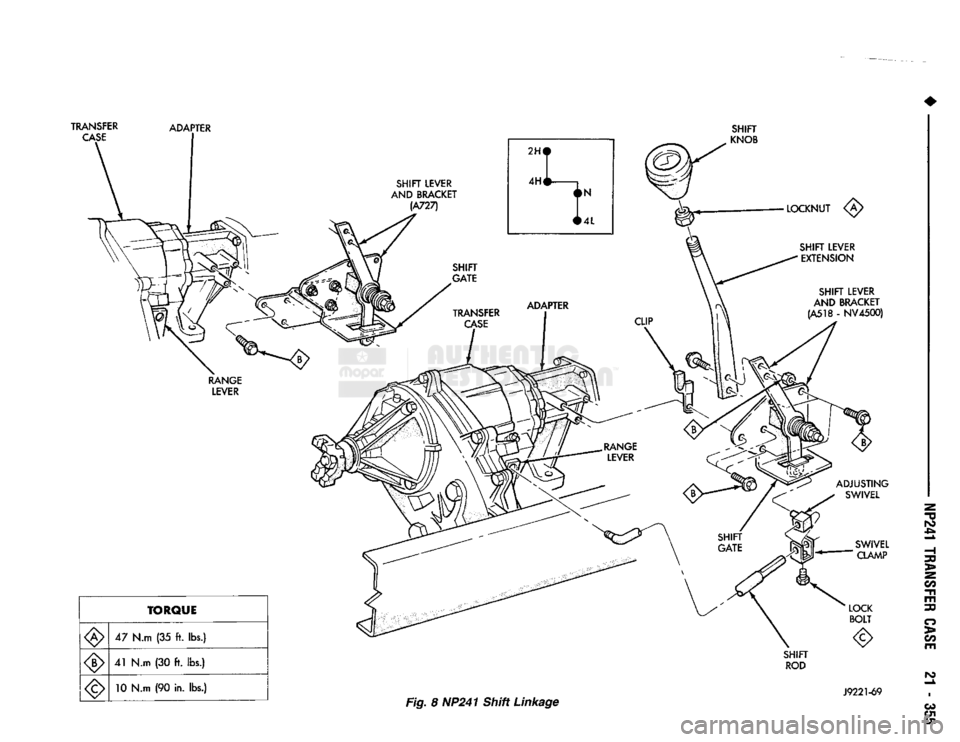
Page 1357 of 1502
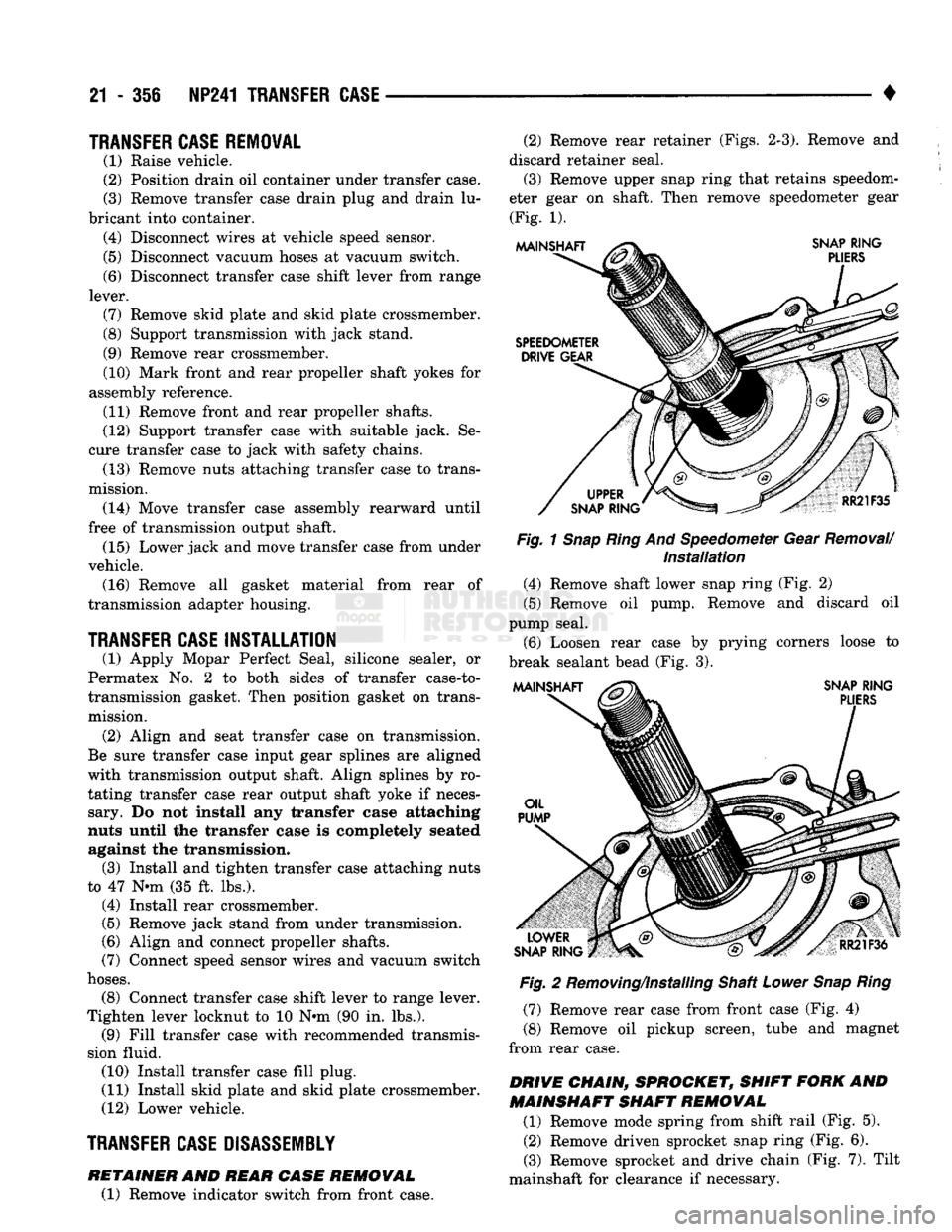
21 - 356 NP241
TRANSFER
CASE
•
TRANSFER
CASE
REMOVAL
(1) Raise vehicle.
(2) Position drain oil container under transfer case.
(3) Remove transfer case drain plug and drain lu
bricant into container. (4) Disconnect wires at vehicle speed sensor.
(5) Disconnect vacuum hoses at vacuum switch.
(6) Disconnect transfer case shift lever from range
lever. (7) Remove skid plate and skid plate crossmember.
(8) Support transmission with jack stand.
(9) Remove rear crossmember.
(10) Mark front and rear propeller shaft yokes for
assembly reference. (11) Remove front and rear propeller shafts.
(12) Support transfer case with suitable jack. Se
cure transfer case to jack with safety chains. (13) Remove nuts attaching transfer case to trans
mission. (14) Move transfer case assembly rearward until
free of transmission output shaft. (15) Lower jack and move transfer case from under
vehicle. (16) Remove all gasket material from rear of
transmission adapter housing.
TRANSFER CASE
INSTALLATION
(1) Apply Mopar Perfect Seal, silicone sealer, or
Permatex No. 2 to both sides of transfer case-to-
transmission gasket. Then position gasket on trans mission.
(2) Align and seat transfer case on transmission.
Be sure transfer case input gear splines are aligned
with transmission output shaft. Align splines by ro
tating transfer case rear output shaft yoke if neces sary. Do not install any transfer case attaching
nuts until the transfer case is completely seated against the transmission.
(3) Install and tighten transfer case attaching nuts
to 47 N*m (35 ft. lbs.). (4) Install rear crossmember.
(5) Remove jack stand from under transmission.
(6) Align and connect propeller shafts.
(7) Connect speed sensor wires and vacuum switch
hoses.
(8) Connect transfer case shift lever to range lever.
Tighten lever locknut to 10 N*m (90 in. lbs.). (9) Fill transfer case with recommended transmis
sion fluid. (10) Install transfer case fill plug.
(11) Install skid plate and skid plate crossmember.
(12) Lower vehicle.
TRANSFER CASE DISASSEMBLY
(2) Remove rear retainer (Figs. 2-3). Remove and
discard retainer seal. (3) Remove upper snap ring that retains speedom
eter gear on shaft. Then remove speedometer gear (Fig. 1).
Fig.
1
Snap Ring
And Speedometer Gear
Removal/
Installation
(4) Remove shaft lower snap ring (Fig. 2)
(5) Remove oil pump. Remove and discard oil
pump seal. (6) Loosen rear case by prying corners loose to
break sealant bead (Fig. 3).
Fig.
2 Removing/Installing Shaft
Lower
Snap Ring
(7) Remove rear case from front case (Fig. 4)
(8) Remove oil pickup screen, tube and magnet
from rear case.
DRIVE CHAIN, SPROCKET, SHIFT FORK
AND
MAINSHAFT SHAFT REMOVAL
(1) Remove mode spring from shift rail (Fig. 5).
(2) Remove driven sprocket snap ring (Fig. 6).
(3) Remove sprocket and drive chain (Fig. 7). Tilt
mainshaft for clearance if necessary.
RETAINER
AND
REAR CASE
REMOVAL
(1) Remove indicator switch from front case.
Page 1358 of 1502
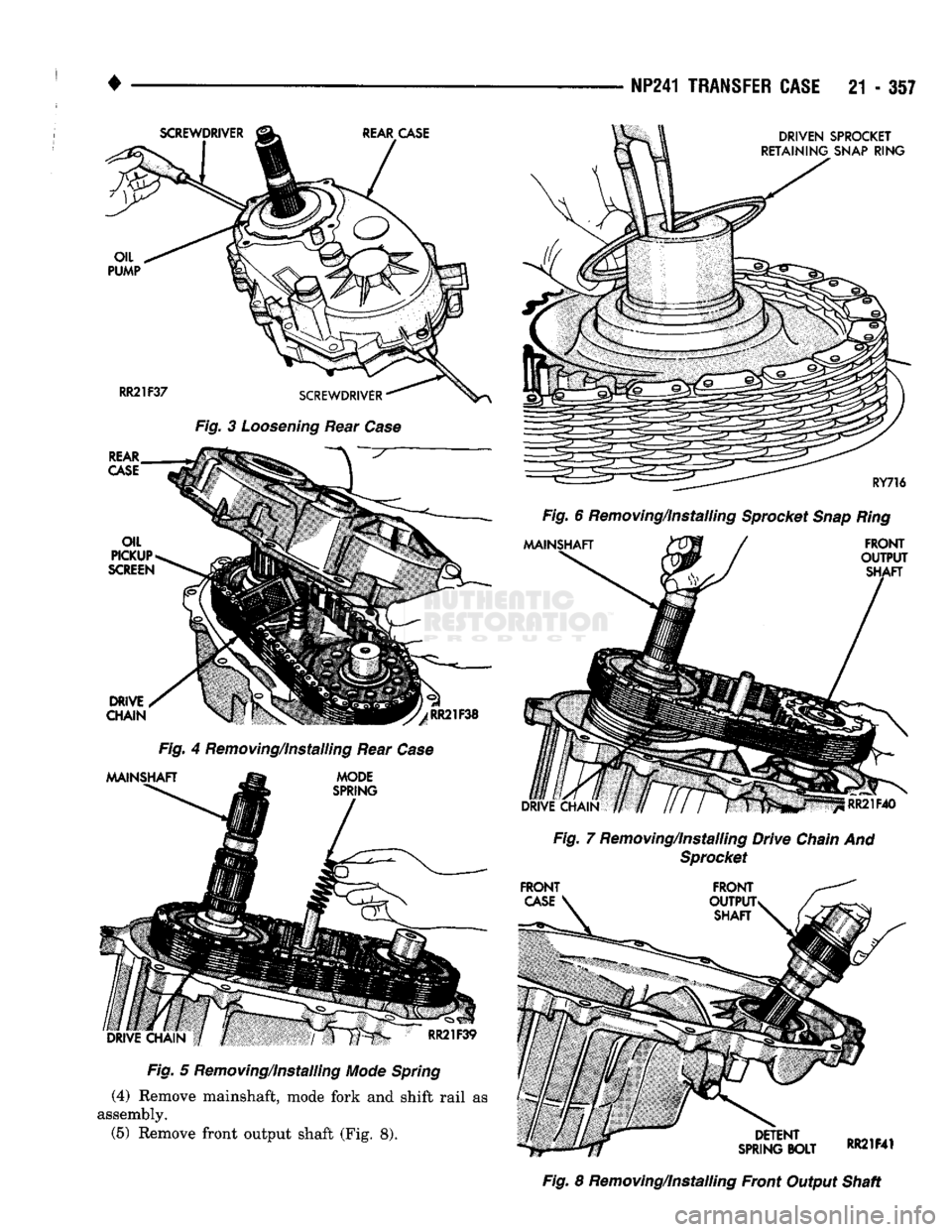
•
Fig. 3 Loosening Rear Case Fig. 5 Removing/Installing Mode Spring
(4)
Remove mainshaft, mode fork and shift rail as
assembly.
(5)
Remove front output shaft (Fig. 8).
NP241
TRANSFER CASE
21 - 3i7
Fig. 8 Removing/Installing Front Output Shaft
Page 1359 of 1502
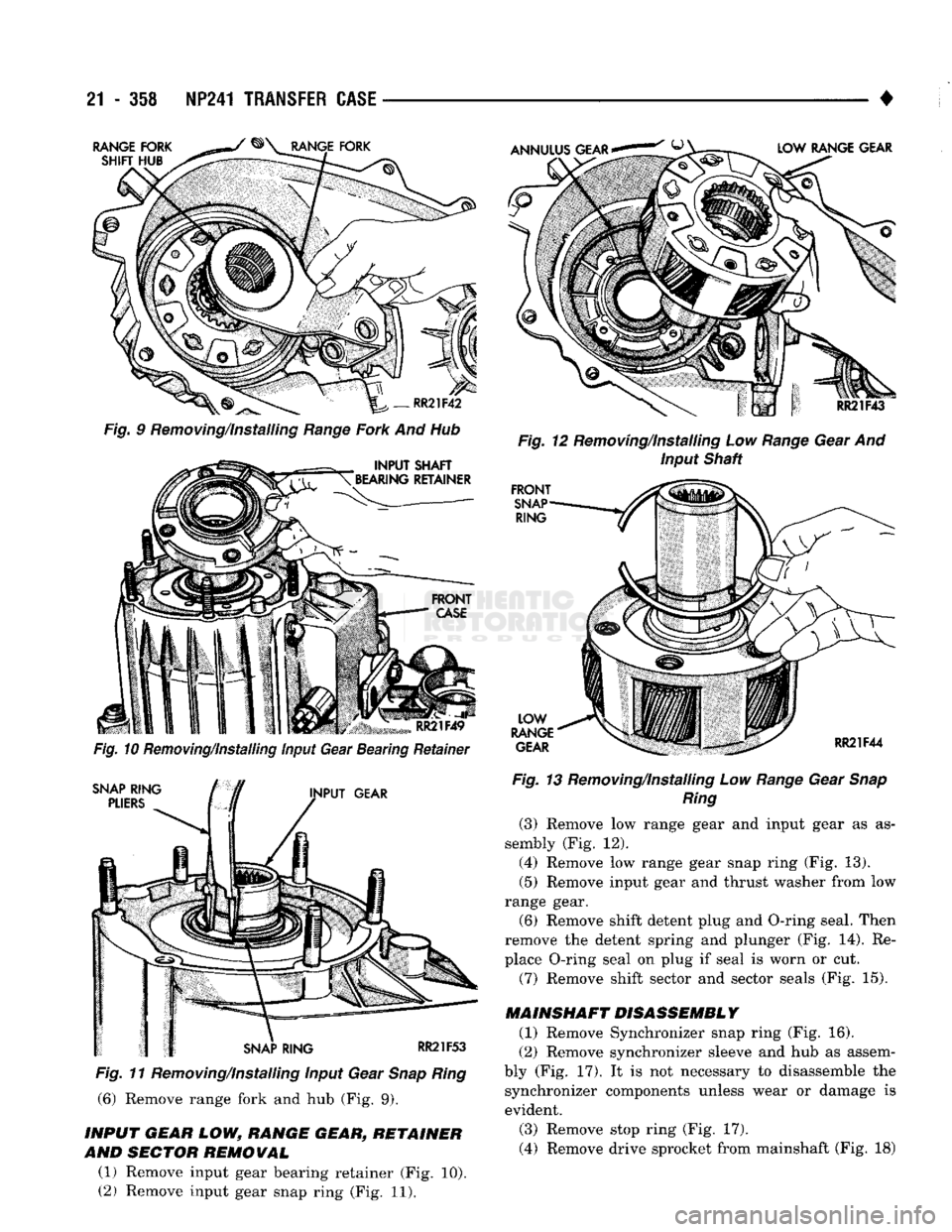
21
- 358
NP241
TRANSFER
CASE
•
RANGE FORK SHIR HUB RANGE FORK
ANNULUS LOW RANGE GEAR
-RR21F42
Fig.
9 Removing/Installing
Range
Fork And Hub
INPUT
SHAFT
^BEARING RETAINER
,
RR21F49
Fig. 10
Removing/Installing
input
Gear
Bearing
Retainer
SNAP RING
/
PLIERS
L
INPUT
GEAR
SNAP RING
RR21F53
Fig.
11 Removing/instaliing Input Gear
Snap
Ring
(6) Remove range fork and hub (Fig. 9).
INPUT GEAR LOW, RANGE GEAR, RETAINER
AND
SECTOR
REMOVAL
(1) Remove input gear bearing retainer (Fig. 10).
(2) Remove input gear snap ring (Fig. 11).
Fig.
12 Removing/Installing Low
Range
Gear And
Input
Shaft
FRONT
SNAP RING
LOW
RANGE GEAR
RR21F44
Fig.
13 Removing/Installing Low
Range
Gear
Snap
Ring
(3) Remove low range gear and input gear as as
sembly (Fig. 12).
(4) Remove low range gear snap ring (Fig. 13).
(5) Remove input gear and thrust washer from low
range gear. (6) Remove shift detent plug and O-ring seal. Then
remove the detent spring and plunger (Fig. 14). Re
place O-ring seal on plug if seal is worn or cut.
(7) Remove shift sector and sector seals (Fig. 15).
MAINSHAFT
DISASSEMBLY
(1) Remove Synchronizer snap ring (Fig. 16).
(2) Remove synchronizer sleeve and hub as assem
bly (Fig. 17). It is not necessary to disassemble the synchronizer components unless wear or damage is
evident.
(3) Remove stop ring (Fig. 17).
(4) Remove drive sprocket from mainshaft (Fig. 18)
Page 1360 of 1502
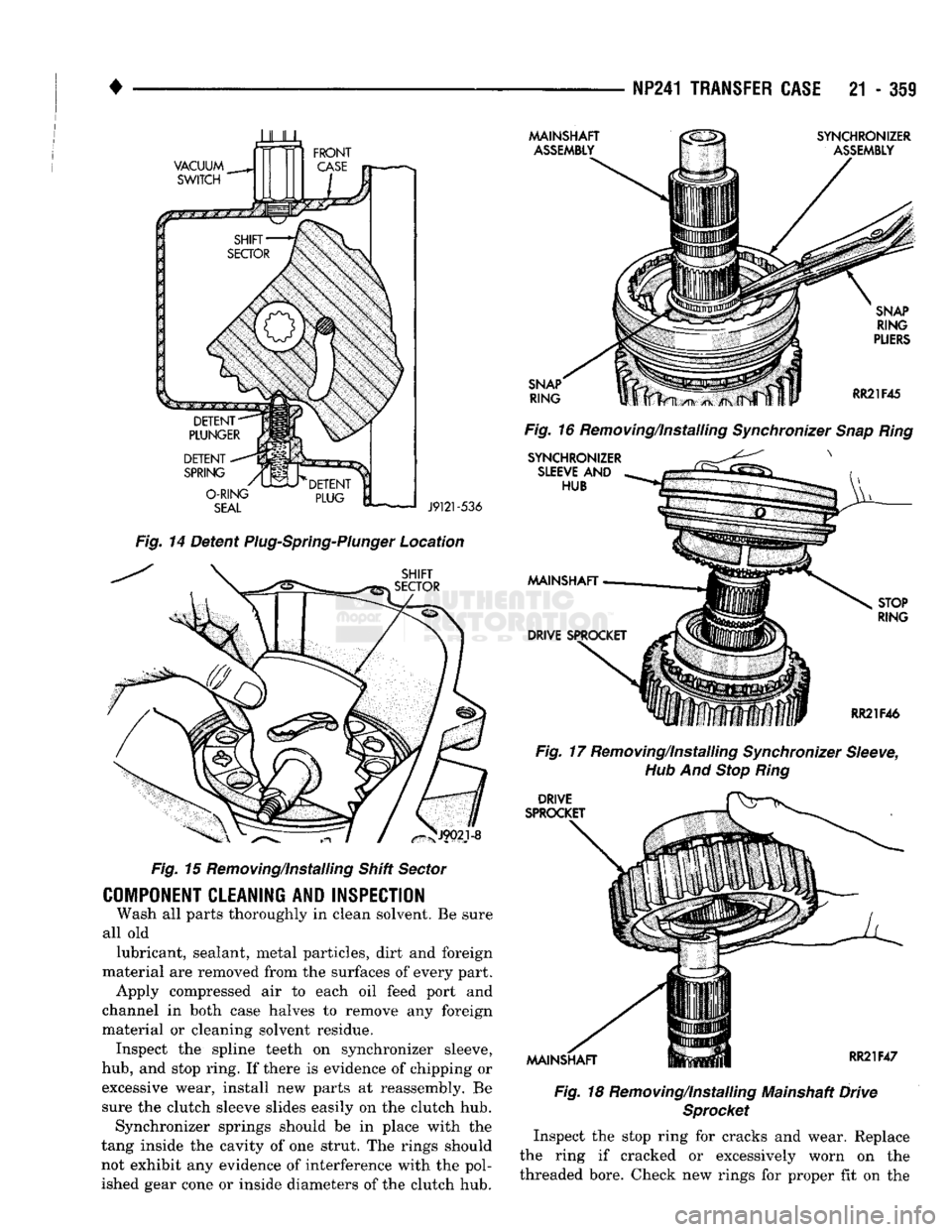
•
NP241
TRANSFER
CASE
21 - 359
JULL
VACUUM
SWITCH
MAINSHAFT
ASSEMBLY
SYNCHRONIZER
ASSEMBLY
DETENT
SPRING
O-RING
SEAL
J9121-536
Fig.
14 Detent
Plug-Spring-Plunger
Location
SHIFT
SECTOR
J9021-8
Fig.
15 Removing/Installing Shift
Sector
COMPONENT CLEANING AND INSPECTION
Wash all parts thoroughly in clean solvent. Be sure
all old lubricant, sealant, metal particles, dirt and foreign
material are removed from the surfaces of every part. Apply compressed air to each oil feed port and
channel in both case halves to remove any foreign
material or cleaning solvent residue. Inspect the spline teeth on synchronizer sleeve,
hub,
and stop ring. If there is evidence of chipping or
excessive wear, install new parts at reassembly. Be sure the clutch sleeve slides easily on the clutch hub. Synchronizer springs should be in place with the
tang inside the cavity of one strut. The rings should
not exhibit any evidence of interference with the pol
ished gear cone or inside diameters of the clutch hub.
SNAP
RING
SNAP
RING
PLIERS
RR21F45 Fig.
16 Removing/Installing
Synchronizer
Snap
Ring
SYNCHRONIZER
SLEEVE
AND
HUB
MAINSHAFT
DRIVE SPROCKET STOP
RING
RR21F46 Fig.
17 Removing/Installing
Synchronizer
Sleeve,
Hub
And
Stop
Ring
DRIVE
SPROCKET
MAINSHAFT
RR21F47
Fig.
18 Removing/Installing Mainshaft Drive
Sprocket
Inspect the stop ring for cracks and wear. Replace
the ring if cracked or excessively worn on the
threaded bore. Check new rings for proper fit on the