FIAT TEMPRA 1988 Service And Manual PDF
Manufacturer: FIAT, Model Year: 1988, Model line: TEMPRA, Model: FIAT TEMPRA 1988Pages: 171, PDF Size: 18.05 MB
Page 71 of 171
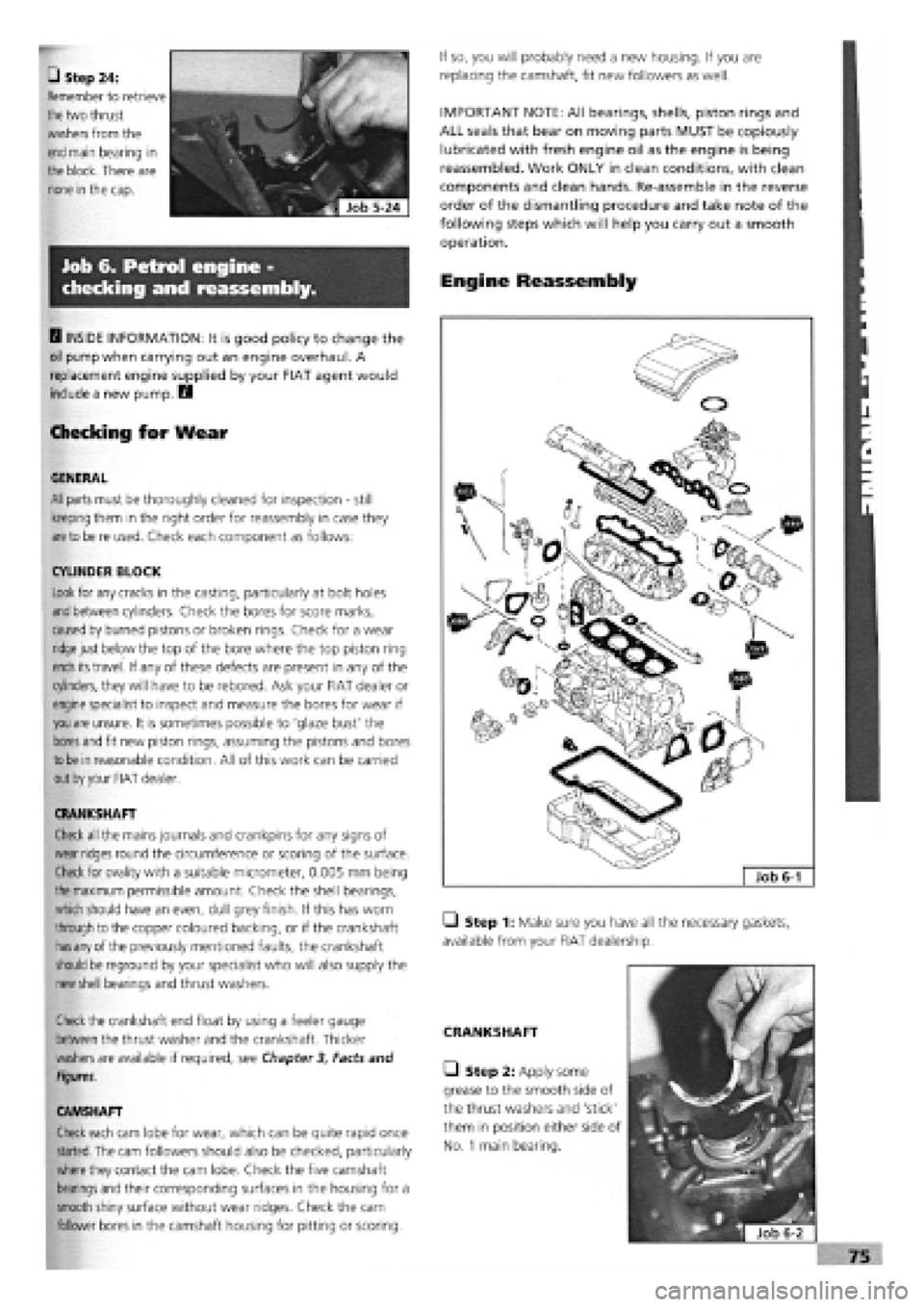
• Step 24:
Remember to retrieve
the
two thrust
washers from the
end
main bearing in
the block. There are
none in the cap.
If so, you will probably need a new housing. If you are
replacing the camshaft, fit new followers as well.
IMPORTANT NOTE: All bearings, shells, piston rings and
ALL seals that bear on moving parts MUST be copiously
lubricated with fresh engine oil as the engine is being
reassembled. Work ONLY in clean conditions, with clean
components and clean hands. Re-assemble in the reverse
order of the dismantling procedure and take note of the
following steps which will help you carry out a smooth
operation.
Engine Reassembly lob 6. Petrol engine -
checking and reassembly.
Q INSIDE INFORMATION: It is good policy to change the
oil pump when carrying out an engine overhaul. A
replacement engine supplied by your FIAT agent would
include a new pump. D
Checking for Wear
GENERAL
All parts must be thoroughly cleaned for inspection
-
still
keeping them in the right order for reassembly in case they
are to
be re used. Check each component as follows:
CYLINDER BLOCK
Look
for any cracks in the casting, particularly at bolt holes
and
between cylinders. Check the bores for score marks,
caused by burned pistons or broken rings. Check for a wear
ridge just
below the top of the bore where the top piston ring
ends its
travel. If any of these defects are present in any of the
cylinders, they will have to be rebored. Ask your FIAT dealer or
engine
specialist to inspect and measure the bores for wear if
you
are unsure. It is sometimes possible to 'glaze bust' the
bores and
fit new piston rings, assuming the pistons and bores
to be in
reasonable condition. All of this work can be carried
out by
your FIAT dealer.
CRANKSHAFT
Check
all
the mains journals and crankpins for any signs of
wear ridges round the circumference or scoring of the surface.
Check
for ovality with a suitable micrometer, 0.005 mm being
the maximum
permissible amount. Check the shell bearings,
which
should have an even, dull grey finish. If this has worn
through
to the copper coloured backing, or if the crankshaft
has any
of the previously mentioned faults, the crankshaft
should
be reground by your specialist who will also supply the
new shell
bearings and thrust washers.
Check
the crankshaft end float by using a feeler gauge
between the thrust washer and the crankshaft. Thicker
washers
are available if required, see Chapter
3,
Facts and
Figures.
CAMSHAFT
Check each cam lobe for wear, which can be quite rapid once
started. The cam followers should also be checked, particularly
where
they contact the cam lobe. Check the five camshaft
bearings
and their corresponding surfaces in the housing for a
smooth
shiny surface without wear ridges. Check the cam
follower bores in the camshaft housing for pitting or scoring.
Job 6-1
Q Step 1: Make sure you have all the necessary gaskets,
available from your FIAT dealership.
CRANKSHAFT
• Step 2: Apply some
grease to the smooth side of
the thrust washers and 'stick'
them in position either side of
No. 1 main bearing.
Page 72 of 171
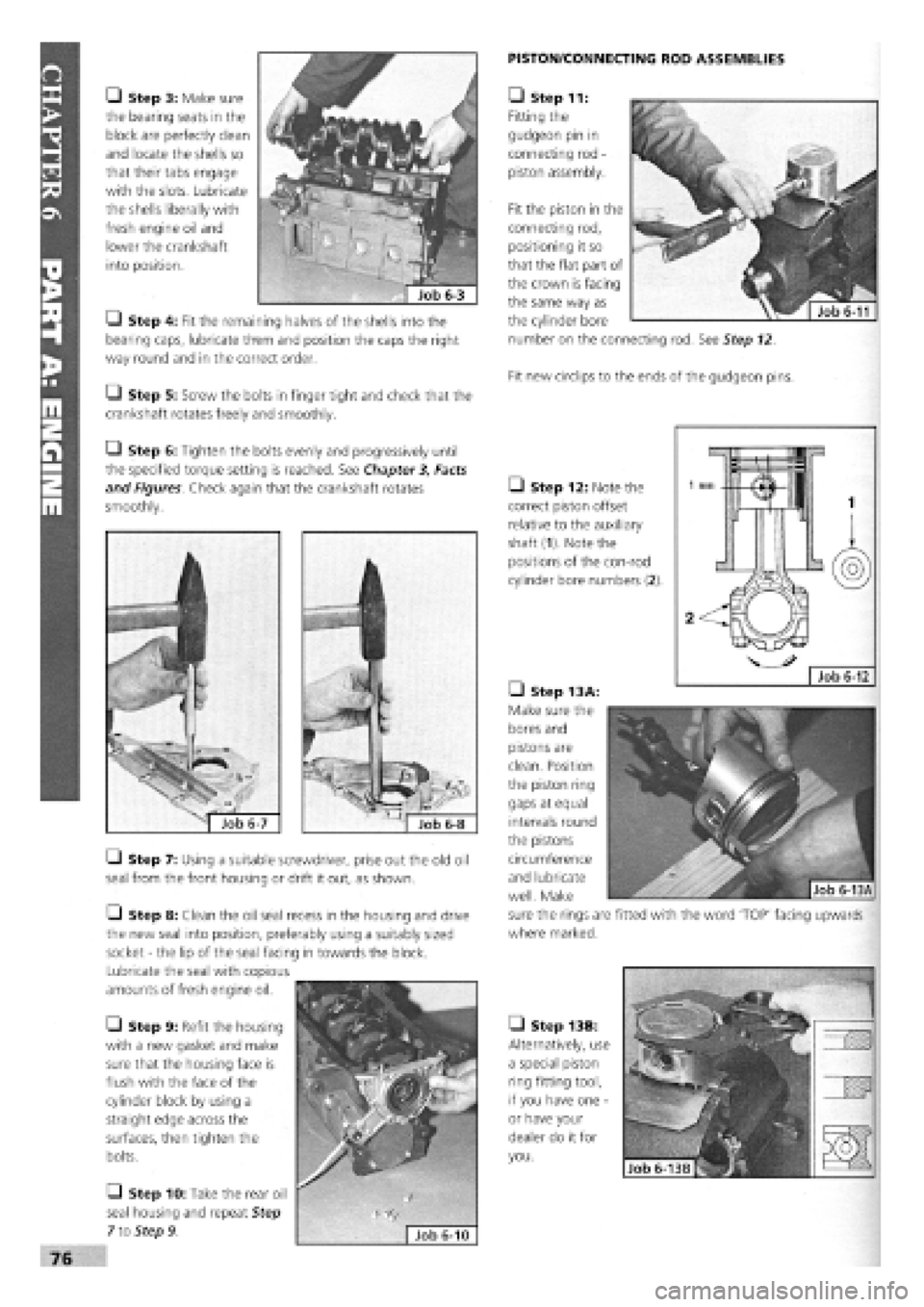
• Step 7: Using a suitable screwdriver, prise out the old oil
seal from the front housing or drift it out, as shown.
PISTON/CONNECTING ROD ASSEMBLIES
• Step 11:
Fitting the
gudgeon pin in
connecting rod -
piston assembly.
Fit new circlips to the ends of the gudgeon pins.
• Step 12: Note the
correct piston offset
relative to the auxiliary
shaft (1). Note the
positions of the con-rod
cylinder bore numbers (2).
Q Step 5: Screw the bolts in finger tight and check that the
crankshaft rotates freely and smoothly.
Q Step 6: Tighten the bolts evenly and progressively until
the specified torque setting is reached. See Chapter
3,
Facts
and Figures. Check again that the crankshaft rotates
smoothly.
• Step 3: Make sure
the bearing seats in the
block are perfectly clean
and locate the shells so
that their tabs engage
with the slots. Lubricate
the shells liberally with
fresh engine oil and
lower the crankshaft
into position.
• Step 4: Fit the remaining halves of the shells into the
bearing caps, lubricate threm and position the caps the right
way round and in the correct order.
Fit the piston in the
connecting rod,
positioning it so
that the flat part of
the crown is facing
the same way as
the cylinder bore
number on the connecting rod. See Step 12.
Job
6-12
• Step 13 A:
Make sure the
bores and
pistons are
clean. Position
the piston ring
gaps at equal
intervals round
the pistons
circumference
and lubricate
well. Make
sure the rings are fitted with the word 'TOP' facing upwards
where marked.
1
• Step 9: Refit the housing
with a new gasket and make
sure that the housing face is
flush with the face of the
cylinder block by using a
straight edge across the
surfaces, then tighten the
bolts.
• Step 10: Take the rear oil
seal housing and repeat Step
7 to Step 9
Q Step 8: Clean the oil seal recess in the housing and drive
the new seal into position, preferably using a suitably sized
socket
-
the lip of the seal facing in towards the block.
Lubricate the seal with copious
amounts of fresh engine oil.
• Step 13B:
Alternatively, use
a special piston
ring fitting tool,
if you have one
-
or have your
dealer do it for
you.
Page 73 of 171
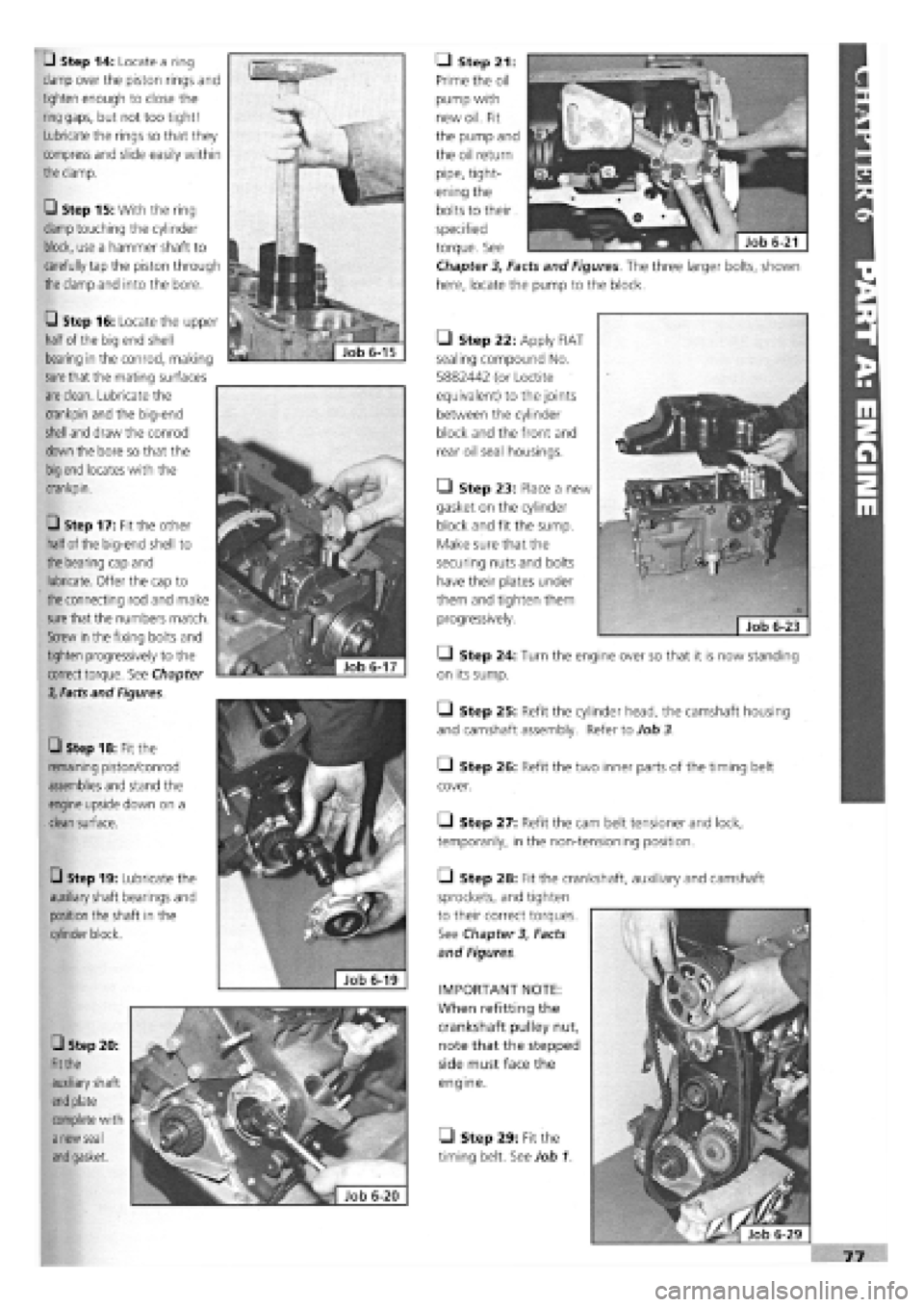
G Step 14: Locate a ring
clamp over the piston rings and
tighten enough to close the
ring
gaps, but not too tight!
Lubricate the rings so that they
compress and slide easily within
the
clamp.
• Step 15: With the ring
clamp
touching the cylinder
block, use a hammer shaft to
carefully tap the piston through
the
clamp and into the bore.
Q Step 27: Refit the cam belt tensioner and lock,
temporarily, in the non-tensioning position.
IMPORTANT NOTE:
When refitting the
crankshaft pulley nut,
note that the stepped
side must face the
engine.
• Step 29: Fit the
timing belt. See Job 1.
• Step 17: Fit the other
half of the big-end shell to
the
bearing cap and
lubricate. Offer the cap to
the
connecting rod and make
sure
that the numbers match.
Screw
in
the fixing bolts and
tighten progressively to the
correct torque. See Chapter
3, Facts
and Figures.
• Step 18: Fit the
remaining piston/conrod
assemblies and stand the
engine upside down on a
clean
surface.
• Step 19: Lubricate the
auxiliary shaft bearings and
position the shaft in the
cylinder block.
• Step 20:
Fit the
auxiliary shaft
end
plate
complete
with
a
new seal
and
gasket.
G Step 16: Locate the upper
half of the big end shell
bearing in the conrod, making
sure
that the mating surfaces
are clean.
Lubricate the
crankpin and the big-end
shell
and draw the conrod
down the bore so that the
big end
locates with the
crankpin.
• Step 21:
Prime the oil
pump with
new oil. Fit
the pump and
the oil return
pipe, tight-
ening the
bolts to their
specified
torque. See
Chapter
3,
Facts and Figures. The three larger bolts, shown
here, locate the pump to the block.
• Step 24: Turn the engine over so that it is now standing
on its sump.
• Step 25: Refit the cylinder head, the camshaft housing
and camshaft assembly. Refer to Job 3.
Q Step 26: Refit the two inner parts of the timing belt
cover.
• Step 23: Place a new
gasket on the cylinder
block and fit the sump.
Make sure that the
securing nuts and bolts
have their plates under
them and tighten them
progressively.
• Step 22: Apply FIAT
sealing compound No.
5882442 (or Loctite
equivalent) to the joints
between the cylinder
block and the front and
rear oil seal housings.
• Step 28: Fit the crankshaft, auxiliary and camshaft
sprockets, and tighten
to their correct torques.
See Chapter
3,
Facts
and Figures.
Page 74 of 171

• Step 30: Fit
the crankshaft
pulley and
tighten. See
Chapter 3,
Facts and
Figures.
• Step 31: Fit the
water pump and
distribution pipe.
• Step 32A: Refit the
flywheel. Do not unbolt the
TDC sensor (1) from the oil seal
housing at its mounting plate
bolts
(2)
unless it is essential to
do so.
• Step 32B: If
the sensor
mounting plate has
to be disturbed, you
will need the FIAT
special tool illus-
trated here (inset) in
order to reposition it
correctly. Position
the timing mark on
the crankshaft
pulley with the zero
degrees mark on the outer timing belt cover (and double
check that the timing mark on the flywheel
-
rubber bung
removed
-
is aligned at zero degrees).
With the bracket fitted to the oil seal housing, fit the FIAT
special tool onto the bracket in place of the sensor with a slot
in the tool fitting exactly over the TDC pin on the flywheel.
When everything is lined up, position the bracket accurately
and tighten the bolts. Remove the tool and refit the sensor.
IMPORTANT NOTE: During assembly, a shear-bolt will
have been fitted to prevent accidental movement of the
bracket. If you need to undo it, you will need to drill it
out and you should replace it with a new one obtained
from your FIAT dealership.
• Step 33: Refit the clutch. See PARTB: TRANSMISSION,
Job 4.
Q Step 34: Refit the fuel pump and pushrod using new
gaskets on both sides of the spacer block, 0.3 mm thick
between the spacer and the engine and 0.7 mm between the
spacer and the pump. See PART F: FUEL AND EXHAUST for
information on setting the pump position.
• Step 35:
Lubricate the sealing
ring and screw on a
new oil filter.
• Step 36:
Before refitting the
distributor, (see
PART D: IGNITION)
refit, if necessary,
the oil pump drive
gear.
• Step 37: Refit
all remaining
auxiliary compo-
nents (including the
oil vapour recovery
device, shown here),
using new gaskets
as necessary and
referring to
Chapter
3,
Facts
and Figures for the
torque settings.
Q Step 38: Reconnect the engine to the transmission. See
Job 11.
Q Step 39: Refit the complete unit to the car. See Job
9.
• Step 40: fl INSIDE INFORMATION! Before fitting the
spark plugs and with a fully charged battery, turn the
engine on the starter until the oil warning light goes
out. This primes the lubrication system and gives more
immediate oil pressure on initial start up after overhaul-
a critical time in the life of an engine. B
• Step 41: Fit the spark plugs and start the engine
-
this
might take a few seconds more than normal on the initial start
up.
• Step 42: Allow the engine to warm up on fast idle
until
it
reaches working temperature and then slow it down to its
normal speed (if adjustable
-
see PART F: FUEL AND
EXHAUST)
Page 75 of 171
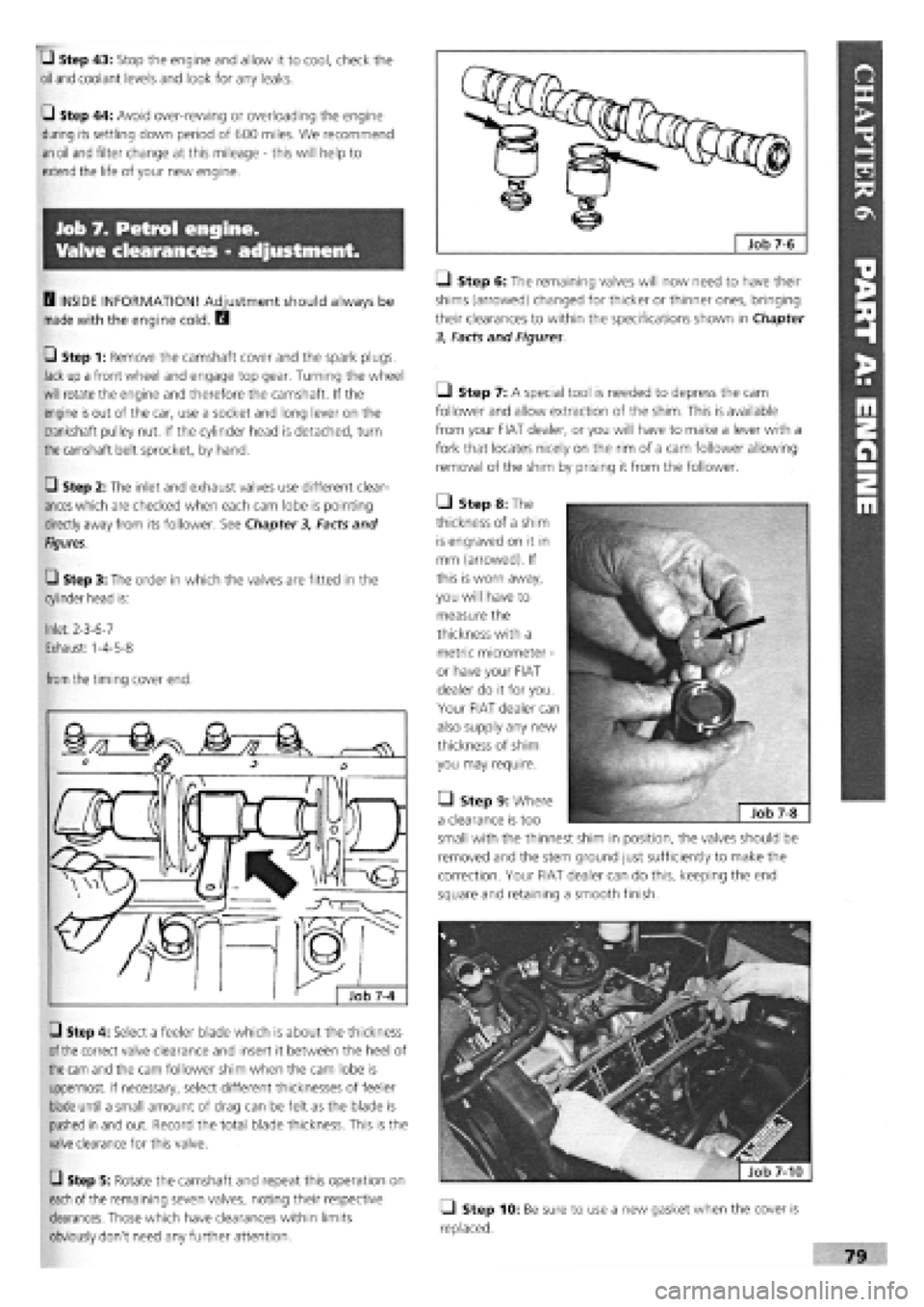
G Step 43: Stop the engine and allow it to cool, check the
oil
and coolant levels and look for any leaks.
G Step 44: Avoid over-rewing or overloading the engine
during its settling down period of 600 miles. We recommend
an oil
and filter change at this mileage
-
this will help to
extend the life of your new engine.
Job 7. Petrol engine.
Valve clearances - adjustment.
0 INSIDE INFORMATION! Adjustment should always be
made with the engine cold. B
G Step 1: Remove the camshaft cover and the spark plugs.
Jack up a front wheel and engage top gear. Turning the wheel
will rotate the engine and therefore the camshaft. If the
engine
is
out of the car, use a socket and long lever on the
crankshaft pulley nut. If the cylinder head is detached, turn
the
camshaft belt sprocket, by hand.
G Step 2: The inlet and exhaust valves use different clear-
ances
which are checked when each cam lobe is pointing
directly away from its follower. See Chapter
3,
Facts and
Figures.
G Step 3: The order in which the valves are fitted in the
cylinder head is:
Inlet: 2-3-6-7
Exhaust: 1-4-5-8
from
the timing cover end.
G Step 4: Select a feeler blade which is about the thickness
of the
correct valve clearance and insert it between the heel of
the cam
and the cam follower shim when the cam lobe is
uppermost. If necessary, select different thicknesses of feeler
blade until a small amount of drag can be felt as the blade is
pushed in and out. Record the total blade thickness. This is the
valve clearance for this valve.
G Step 5: Rotate the camshaft and repeat this operation on
each
of the remaining seven valves, noting their respective
clearances. Those which have clearances within limits
obviously don't need any further attention.
Q Step 6: The remaining valves will now need to have their
shims (arrowed) changed for thicker or thinner ones, bringing
their clearances to within the specifications shown in Chapter
3, Facts and Figures
Ll Step 7: A special tool is needed to depress the cam
follower and allow extraction of the shim. This is available
from your FIAT dealer, or you will have to make a lever with a
fork that locates nicely on the rim of a cam follower allowing
removal of the shim by prising it from the follower.
• Step 8: The
thickness of a shim
is engraved on it in
mm (arrowed). If
this is worn away,
you will have to
measure the
thickness with a
metric micrometer
-
or have your FIAT
dealer do it for you.
Your FIAT dealer can
also supply any new
thickness of shim
you may require.
• Step 9: Where
a clearance is too
small with the thinnest shim in position, the valves should be
removed and the stem ground just sufficiently to make the
correction. Your FIAT dealer can do this, keeping the end
square and retaining a smooth finish.
fjfefe^ | Job 7-10
Q Step 10: Be sure to use a new gasket when the cover is
replaced.
Page 76 of 171
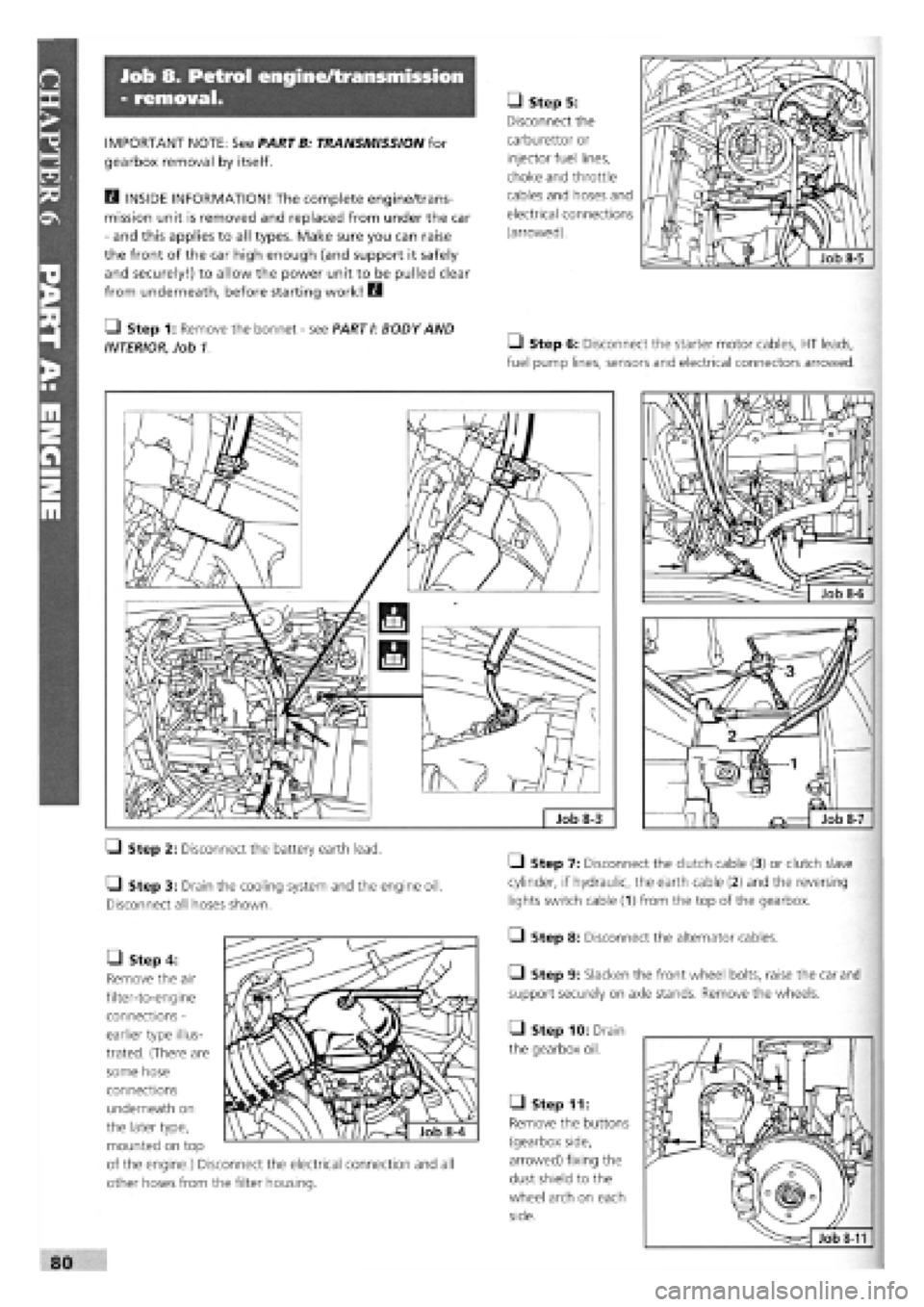
Job 8. Petrol engine/transmission
- removal.
IMPORTANT NOTE: See PARTB: TRANSMISSION for
gearbox removal by itself.
H INSIDE INFORMATION! The complete engine/trans-
mission unit is removed and replaced from under the car
- and this applies to all types. Make sure you can raise
the front of the car high enough (and support it safely
and securely!) to allow the power unit to be pulled clear
from underneath, before starting work! 13
• Step 1: Remove the bonnet
-
see PARTI: BODY AND
INTERIOR, Job 1.
• Step 5:
Disconnect the
carburettor or
injector fuel lines,
choke and throttle
cables and hoses and
electrical connections
(arrowed).
Q Step 6: Disconnect the starter motor cables, HT leads,
fuel pump lines, sensors and electrical connectors arrowed.
Job
8-7
• Step 2: Disconnect the battery earth lead.
• Step 3: Drain the cooling system and the engine oil.
Disconnect all hoses shown.
• Step 7: Disconnect the clutch cable (3) or clutch slave
cylinder, if hydraulic, the earth cable (2) and the reversing
lights switch cable
(1)
from the top of the gearbox.
• Step 8: Disconnect the alternator cables.
Q Step 9: Slacken the front wheel bolts, raise the car and
support securely on axle stands. Remove the wheels.
• Step 10: Drain
the gearbox oil.
• Step 4:
Remove the air
filter-to-engine
connections
-
earlier type illus-
trated. (There are
some hose
connections
underneath on
the later type,
mounted on top
of the engine.) Disconnect the electrical connection and all
other hoses from the filter housing.
• Step 11:
Remove the buttons
(gearbox side,
arrowed) fixing the
dust shield to the
wheel arch on each
side.
Page 77 of 171
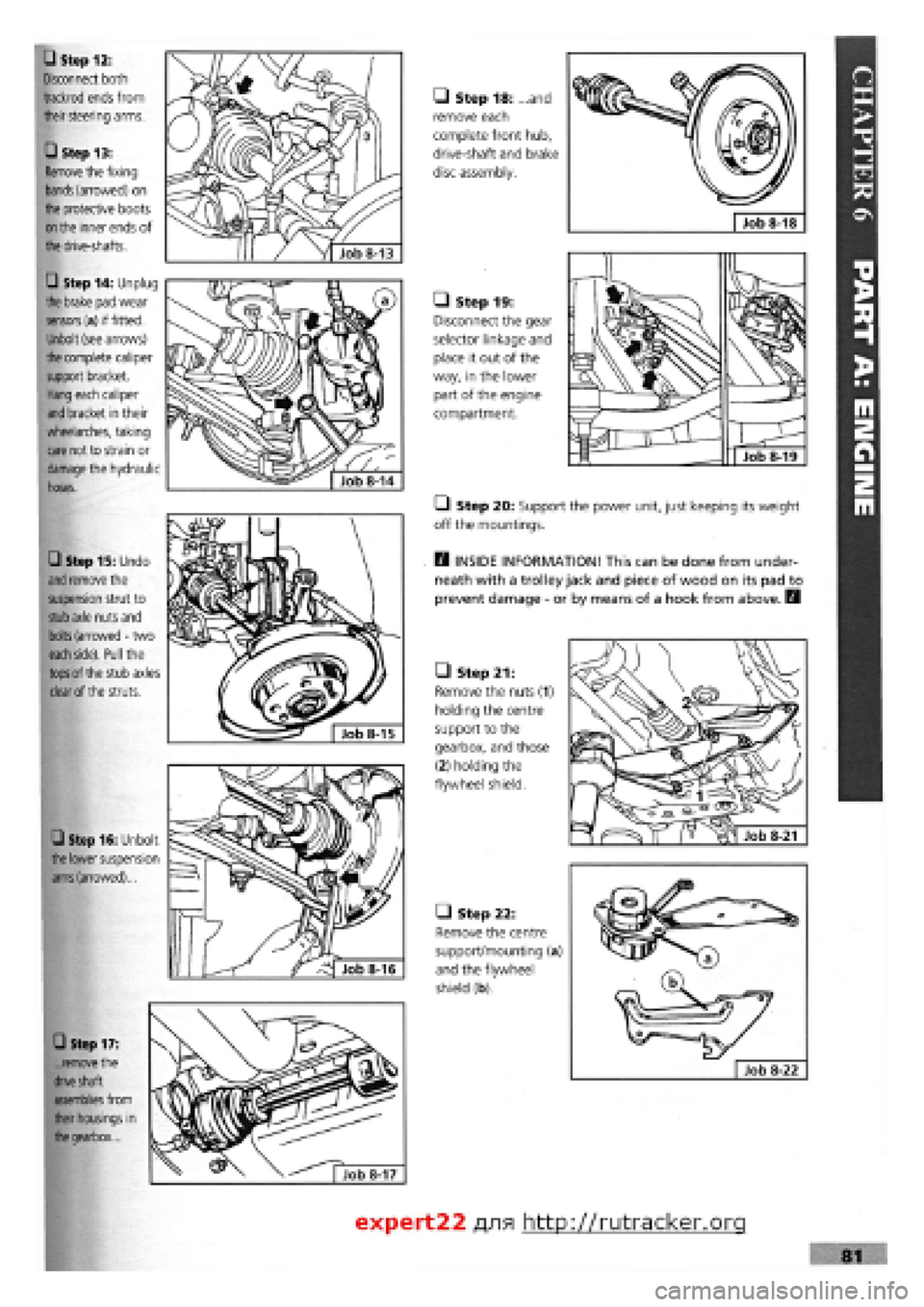
• Step 16: Unbolt
the
lower suspension
arms
(arrowed)...
• Step 17:
...remove
the
drive
shaft
assemblies
from
their housings in
the
gearbox...
• Step 15: Undo
and
remove the
suspension strut to
stub axle
nuts and
bolts
(arrowed
-
two
each side).
Pull the
tops
of the stub axles
clear
of the struts.
• Step 12:
Disconnect both
trackrod ends from
their
steering arms.
• Step 13:
Remove
the fixing
bands
(arrowed) on
the
protective boots
on the
inner ends of
the
drive-shafts.
• Step 14: Unplug
the brake
pad wear
sensors
(a) if fitted.
Unbolt (see arrows)
the
complete caliper
support bracket.
Hang
each caliper
and
bracket in their
wheelarches, taking
care
not to strain or
damage
the hydraulic
hoses.
• Step 21:
Remove the nuts (1)
holding the centre
support to the
gearbox, and those
(2) holding the
flywheel shield.
• Step 22:
Remove the centre
support/mounting (a)
and the flywheel
shield (b).
• Step 18: and
remove each
complete front hub,
drive-shaft and brake
disc assembly.
Job 8-18
Q Step 20: Support the power unit, just keeping its weight
off the mountings.
E3 INSIDE INFORMATION! This can be done from under-
neath with a trolley jack and piece of wood on its pad to
prevent damage
-
or by means of a hook from above. B
• Step 19:
Disconnect the gear
selector linkage and
place it out of the
way, in the lower
part of the engine
compartment.
Job 8-19
Job 8-13
expert22 fl/ia http://rutracker.org
I
Page 78 of 171
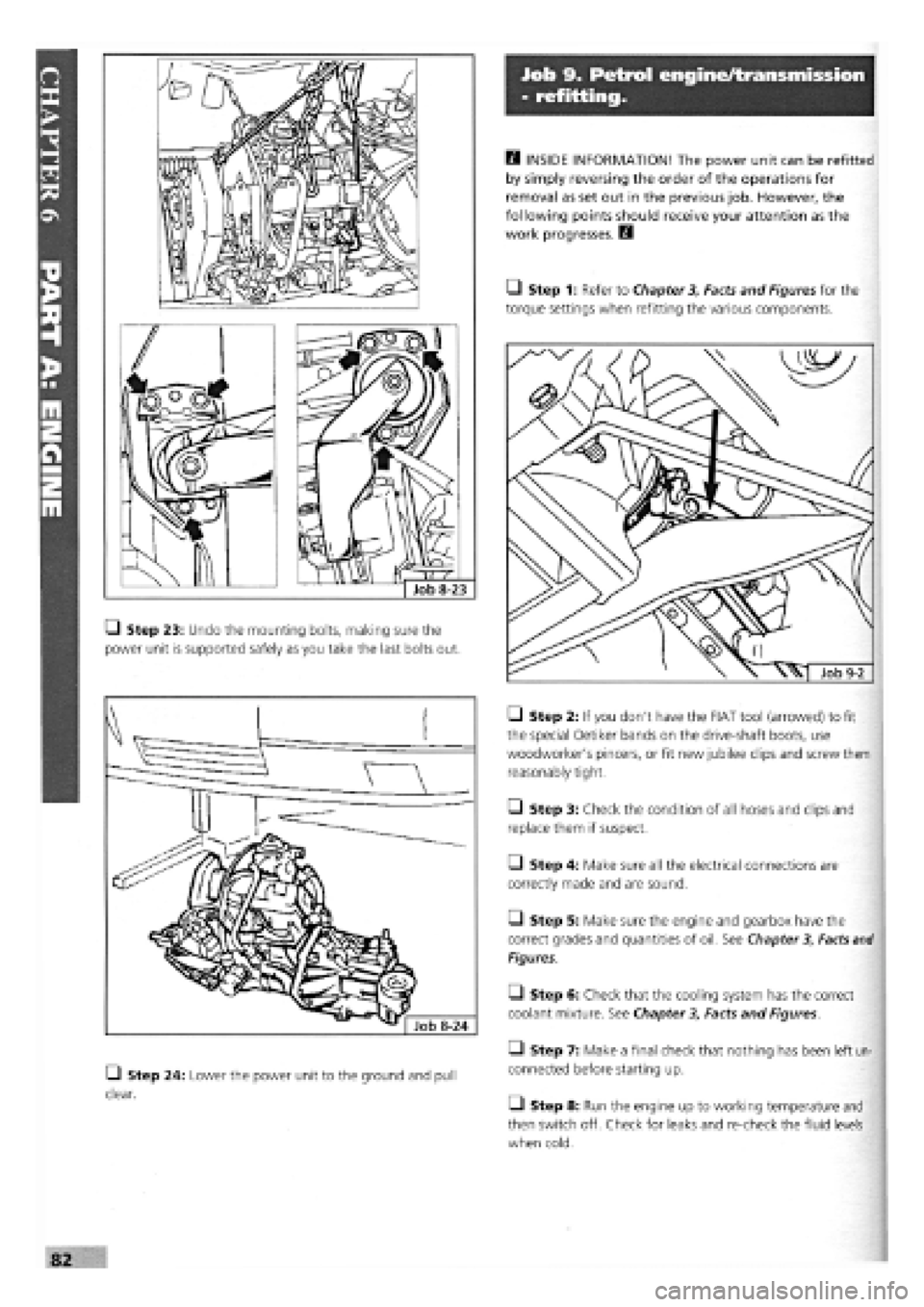
Q Step 23: Undo the mounting bolts, making sure the
power unit is supported safely as you take the last bolts out.
• Step 24: Lower the power unit to the ground and pull
clear.
Job 9. Petrol engine/transmission
- refitting.
Q INSIDE INFORMATION! The power unit can be refitted
by simply reversing the order of the operations for
removal as set out in the previous job. However, the
following points should receive your attention as the
work progresses. H
• Step 1: Refer to Chapter
3,
Facts and Figures for the
torque settings when refitting the various components.
• Step 2: If you don't have the FIAT too! (arrowed) to fit
the special Oetiker bands on the drive-shaft boots, use
woodworker's pincers, or fit new jubilee clips and screw them
reasonably tight.
• Step 3: Check the condition of all hoses and clips and
replace them if suspect.
• Step 4: Make sure all the electrical connections are
correctly made and are sound.
Q Step 5: Make sure the engine and gearbox have the
correct grades and quantities of oil. See Chapter
3,
Facts
and
Figures.
Q Step 6: Check that the cooling system has the correct
coolant mixture. See Chapter
3,
Facts and Figures.
• Step 7: Make a final check that nothing has been left un-
connected before starting up.
• Step 8: Run the engine up to working temperature and
then switch off. Check for leaks and re-check the fluid levels
when cold.
Page 79 of 171
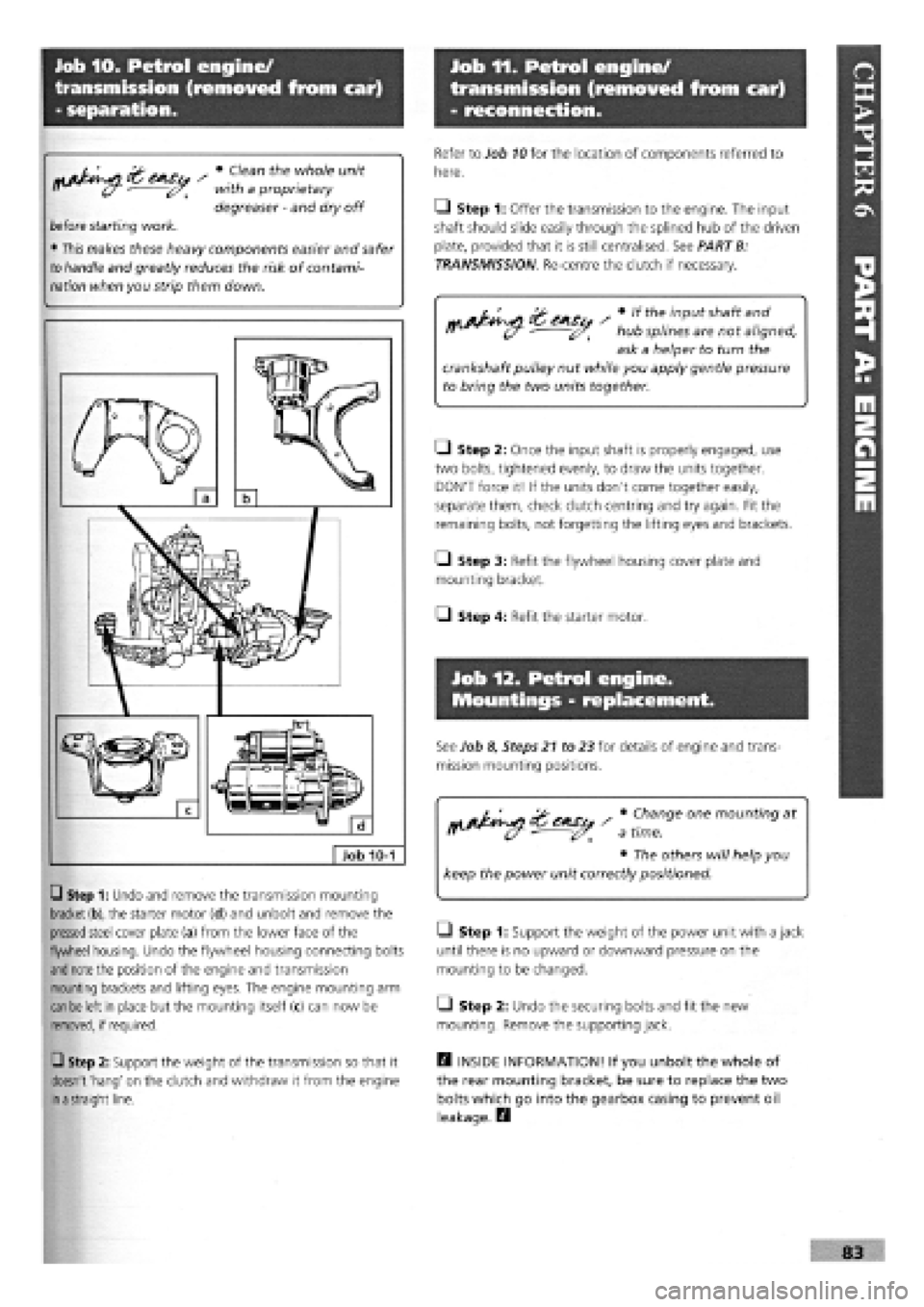
Job 10. Petrol engine/
transmission (removed from car)
- separation.
Job 11. Petrol engine/
transmission (removed from car)
- reconnection.
• Clean the whole unit
with a proprietary
degreaser
-
and dry off
before
starting work.
•
This
makes these heavy components easier and safer
to
handle
and greatly reduces the risk of contami-
nation
when you strip them down.
Job 10-1
Q Step 1: Undo and remove the transmission mounting
bracket (b),
the starter motor (d) and unbolt and remove the
pressed
steel cover plate (a) from the lower face of the
flywheel housing. Undo the flywheel housing connecting bolts
and note
the position of the engine and transmission
mounting brackets and lifting eyes. The engine mounting arm
can be
left in place but the mounting itself (c) can now be
removed, if required.
Q Step 2: Support the weight of the transmission so that it
doesn't 'hang' on the clutch and withdraw it from the engine
in a
straight line.
Refer to Job
10
for the location of components referred to
here.
• Step 1: Offer the transmission to the engine. The input
shaft should slide easily through the splined hub of the driven
plate, provided that it is still centralised. See PART B:
TRANSMISSION Re-centre the clutch if necessary.
r ' «the input shaft and
- hub splines are not aligned,
ask a helper to turn the
crankshaft pulley nut while you apply gentle pressure
to bring the two units together.
• Step 2: Once the input shaft is properly engaged, use
two bolts, tightened evenly, to draw the units together.
DON'T force it! If the units don't come together easily,
separate them, check clutch centring and try again. Fit the
remaining bolts, not forgetting the lifting eyes and brackets.
• Step 3: Refit the flywheel housing cover plate and
mounting bracket.
Q Step 4: Refit the starter motor.
Job 12. Petrol engine.
Mountings - replacement.
See Job 8, Steps 21 to 23 for details of engine and trans-
mission mounting positions.
Change one mounting at
time.
• The others will help you
keep the power unit correctly positioned.
• Step 1: Support the weight of the power unit with a jack
until there is no upward or downward pressure on the
mounting to be changed.
Q Step 2: Undo the securing bolts and fit the new
mounting. Remove the supporting jack.
H INSIDE INFORMATION! If you unbolt the whole of
the rear mounting bracket, be sure to replace the two
bolts which go into the gearbox casing to prevent oil
leakage. D
Page 80 of 171
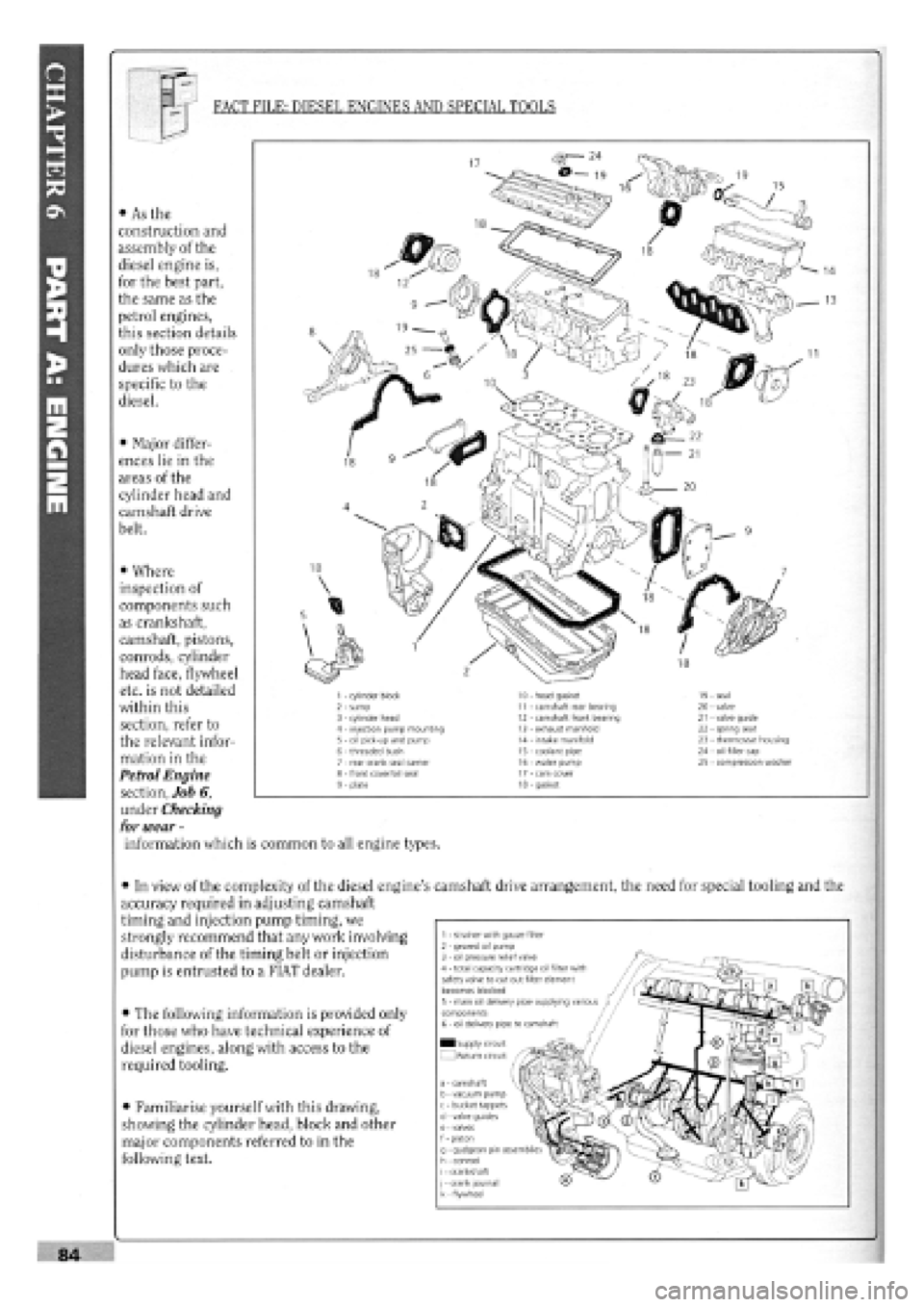
FACT FILE: DIESEL ENGINES AND SPECIAL TOOLS
• As the
construction and
assembly of the
diesel engine is,
for the best part,
the same as the
petrol engines,
this section details
only those proce-
dures which are
specific to the
diesel.
• Major differ-
ences lie in the
areas of the
cylinder head and
camshaft drive
belt.
• Where
inspection of
components such
as crankshaft,
camshaft, pistons,
conrods, cylinder
head face, flywheel
etc. is not detailed
within this
section, refer to
the relevant infor-
mation in the
Petrol Engine
section, Job 6,
under Checking
for wear -
information which is common to all engine types.
• In view of the complexity of the diesel engine's camshaft drive arrangement, the need for special tooling and the
accuracy required in adjusting camshaft
timing and injection pump timing, we
strongly recommend that any work involving
disturbance of the timing belt or injection
pump is entrusted to a FIAT dealer.
• The following information is provided only
for those who have technical experience of
diesel engines, along with access to the
required tooling.
• Familiarise yourself with this drawing,
showing the cylinder head, block and other
major components referred to in the
following text.
1
-
cylinder block 2
-
sump 3
-
cylinder head 4
-
injection pump mounting 5
-
oil pick-up and pump 6
-
threaded bush 7
-
rear crank seal carrier 8
-
front cover/oil seal 9
-
plate
10
-
head gasket 11
-
camshaft rear bearing 12
-
camshaft front bearing 13
-
exhaust manifold 14
-
intake manifold 15
-
coolant pipe 16
-
water pump 17
-
cam cover 18
-
gasket
19-seal 20
-
valve 21
-
valve guide 22
-
spring seat 23
-
thermostat housing 24
-
oil filler cap 25
-
compression washer
1
-
strainer with gauze filter 2
-
geared oil pump 3
-
oil pressure relief valve 4
-
total capacity cartridge oil filter with safety valve to cut out filter element becomes blocked 5
-
main oil delivery pipe supplying various / components 6
-
oil delivery pipe to camshaft
IHSupply circuit I
I Return
circuit
a
-
camshaft b
-
vacuum pump c
-
bucket tappets d
-
valve guides e
-
valves f
-
piston g
-
gudgeon pin assemblie; h
-
conrod i
-
crankshaft j
-
crank journal k
-
flywheel