FIAT TEMPRA 1988 Service And Workshop Manual
Manufacturer: FIAT, Model Year: 1988, Model line: TEMPRA, Model: FIAT TEMPRA 1988Pages: 171, PDF Size: 18.05 MB
Page 51 of 171
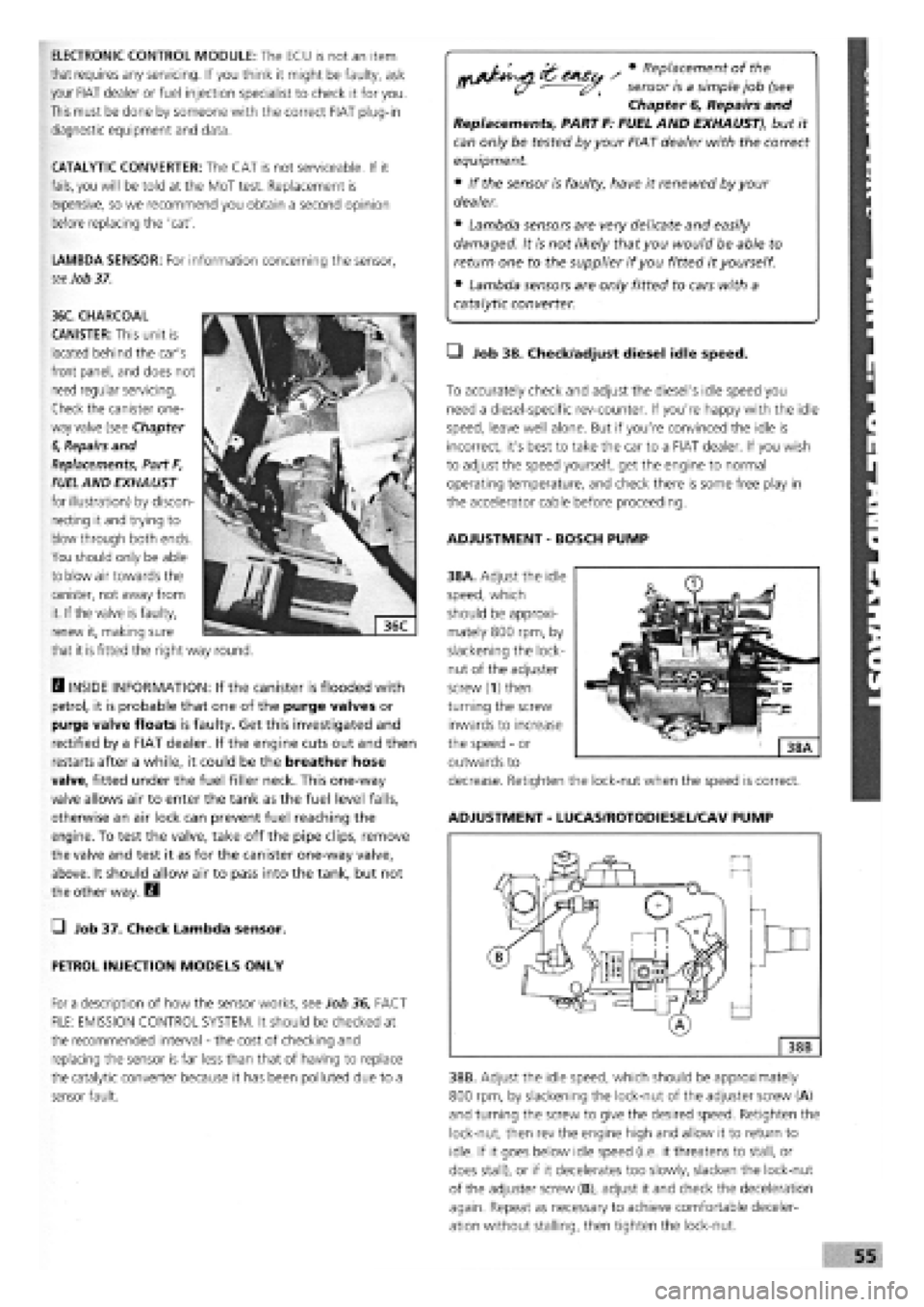
ELECTRONIC CONTROL MODULE: The ECU is not an item
that requires any servicing. If you think it might be faulty, ask
your FIAT dealer or fuel injection specialist to check it for you.
This must be done by someone with the correct FIAT plug-in
diagnostic equipment and data.
CATALYTIC CONVERTER: The CAT is not serviceable. If it
fails, you will be told at the MoT test. Replacement is
expensive, so we recommend you obtain a second opinion
before replacing the 'cat'.
LAMBDA SENSOR: For information concerning the sensor,
see
Job
37.
I' sensor is a simple job (see
Chapter 6, Repairs and
Replacements, PART F: FUEL AND EXHAUST), but it
can only be tested by your FIAT dealer with the correct
equipment
• If the sensor is faulty, have it renewed by your
dealer.
• Lambda sensors are very delicate and easily
damaged. It is not likely that you would be able to
return one to the supplier if you fitted it yourself.
• Lambda sensors are only fitted to cars with a
catalytic converter.
• Job 38. Check/adjust diesel idle speed.
To accurately check and adjust the diesel's idle speed you
need a diesel-specific rev-counter. If you're happy with the idle
speed, leave well alone. But if you're convinced the idle is
incorrect, it's best to take the car to a FIAT dealer. If you wish
to adjust the speed yourself, get the engine to normal
operating temperature, and check there is some free play in
the accelerator cable before proceeding.
ADJUSTMENT
-
BOSCH PUMP
D INSIDE INFORMATION: If the canister is flooded with
petrol, it is probable that one of the purge valves or
purge valve floats is faulty. Get this investigated and
rectified by a FIAT dealer. If the engine cuts out and then
restarts after a while, it could be the breather hose
valve, fitted under the fuel filler neck. This one-way
valve allows air to enter the tank as the fuel level falls,
otherwise an air lock can prevent fuel reaching the
engine. To test the valve, take off the pipe clips, remove
the valve and test it as for the canister one-way valve,
above. It should allow air to pass into the tank, but not
the other way. H
Q Job 37. Check Lambda sensor.
PETROL INJECTION MODELS ONLY
For
a
description of how the sensor works, see Job 36, FACT
FILE: EMISSION CONTROL SYSTEM. It should be checked at
the recommended interval
-
the cost of checking and
replacing the sensor is far less than that of having to replace
the catalytic converter because it has been polluted due to a
sensor fault.
38A. Adjust the idle
speed, which
should be approxi-
mately 800 rpm, by
slackening the lock-
nut of the adjuster
screw (1) then
turning the screw
inwards to increase
the speed
-
or
outwards to
decrease. Retighten the lock-nut when the speed is correct.
ADJUSTMENT
-
LUCAS/ROTODIESEL/CAV PUMP
38B. Adjust the idle speed, which should be approximately
800 rpm, by slackening the lock-nut of the adjuster screw (A)
and turning the screw to give the desired speed. Retighten the
lock-nut, then rev the engine high and allow it to return to
idle. If it goes below idle speed (i.e. it threatens to stall, or
does stall), or if it decelerates too slowly, slacken the lock-nut
of the adjuster screw (B), adjust it and check the deceleration
again. Repeat as necessary to achieve comfortable deceler-
ation without stalling, then tighten the lock-nut.
36C. CHARCOAL
CANISTER: This unit is
located behind the car's
front panel, and does not
need regular servicing.
Check the canister one-
way valve (see Chapter
6,
Repairs and
Replacements, Part F,
FUEL
AND EXHAUST
for illustration) by discon-
necting it and trying to
blow through both ends.
You should only be able
to blow air towards the
canister, not away from
it. If the valve is faulty,
renew it, making sure
that it
is
fitted the right way round.
Page 52 of 171
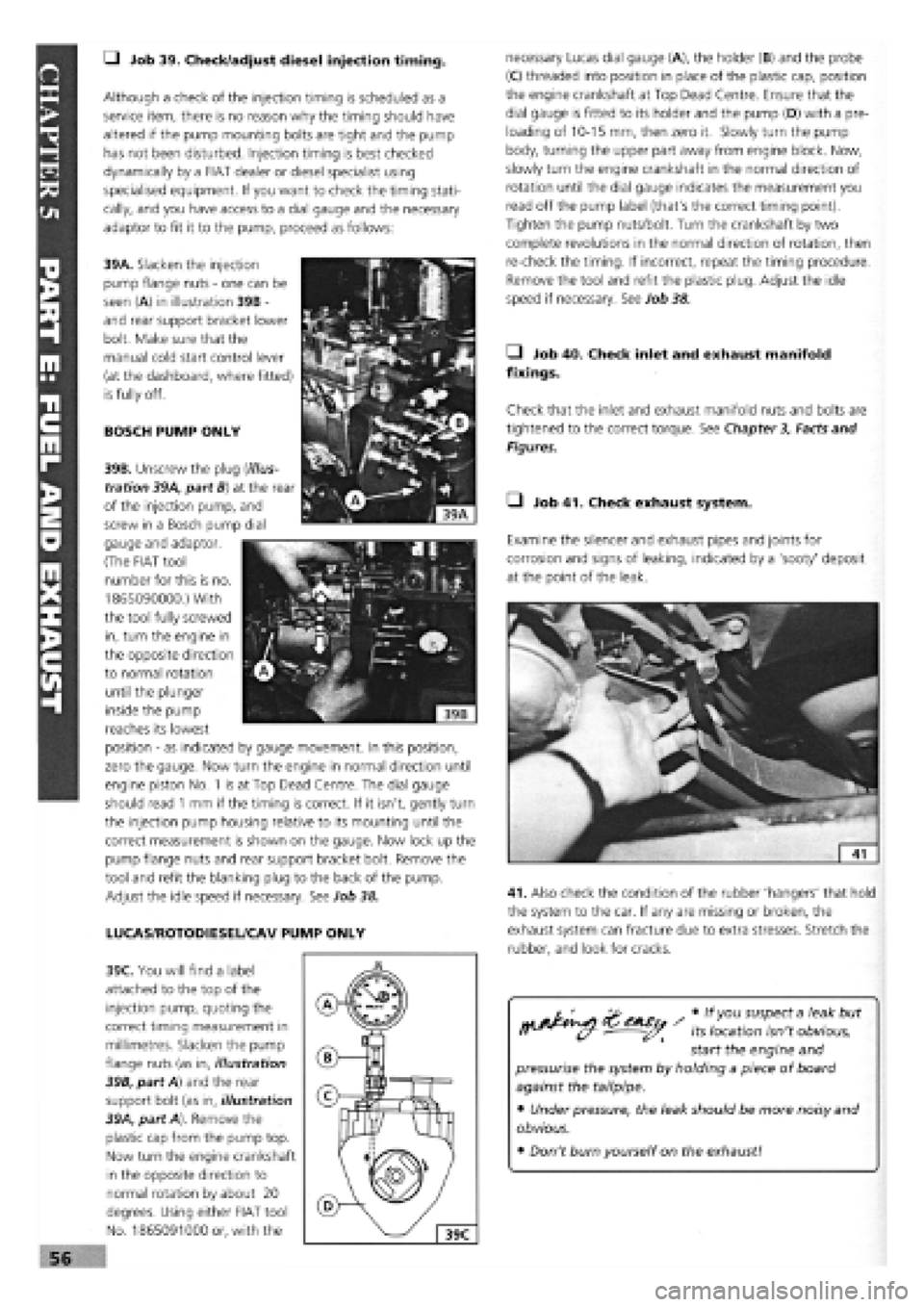
• Job 39. Check/adjust diesel injection timing.
Although a check of the injection timing is scheduled as a
service item, there is no reason why the timing should have
altered if the pump mounting bolts are tight and the pump
has not been disturbed. Injection timing is best checked
dynamically by a FIAT dealer or diesel specialist using
specialised equipment. If you want to check the timing stati-
cally, and you have access to a dial gauge and the necessary
adaptor to fit it to the pump, proceed as follows:
39A. Slacken the injection
pump flange nuts
-
one can be
seen (A) in illustration 39B -
and rear support bracket lower
bolt. Make sure that the
manual cold start control lever
(at the dashboard, where fitted)
is fully off.
BOSCH PUMP ONLY
necessary Lucas dial gauge (A), the holder (B) and the probe
(C) threaded into position in place of the plastic cap, position
the engine crankshaft at Top Dead Centre. Ensure that the
dial gauge is fitted to its holder and the pump (D) with a pre-
loading of 10-15 mm, then zero it. Slowly turn the pump
body, turning the upper part away from engine block. Now,
slowly turn the engine crankshaft in the normal direction of
rotation until the dial gauge indicates the measurement you
read off the pump label (that's the correct timing point).
Tighten the pump nuts/bolt. Turn the crankshaft by two
complete revolutions in the normal direction of rotation, then
re-check the timing. If incorrect, repeat the timing procedure.
Remove the tool and refit the plastic plug. Adjust the idle
speed if necessary. See Job 38.
• Job 40. Check inlet and exhaust manifold
fixings.
Check that the inlet and exhaust manifold nuts and bolts are
tightened to the correct torque. See Chapter
3,
Facts and
Figures.
• Job 41. Check exhaust system.
Examine the silencer and exhaust pipes and joints for
corrosion and signs of leaking, indicated by a 'sooty' deposit
at the point of the leak.
41. Also check the condition of the rubber 'hangers' that hold
the system to the car. If any are missing or broken, the
exhaust system can fracture due to extra stresses. Stretch the
rubber, and look for cracks.
39B. Unscrew the plug (illus-
tration 39A, part B) at the rear
of the injection pump, and
screw in a Bosch pump dial
gauge and adaptor.
(The FIAT tool
number for this is no.
1865090000.) With
the tool fully screwed
in, turn the engine in
the opposite direction
to normal rotation
until the plunger
inside the pump
reaches its lowest
position
-
as indicated by gauge movement. In this position,
zero the gauge. Now turn the engine in normal direction until
engine piston No. 1 is at Top Dead Centre. The dial gauge
should read
1
mm if the timing is correct. If it isn't, gently turn
the injection pump housing relative to its mounting until the
correct measurement is shown on the gauge. Now lock up the
pump flange nuts and rear support bracket bolt. Remove the
tool and refit the blanking plug to the back of the pump.
Adjust the idle speed if necessary. See Job 38.
LUCAS/ROTODIESEL/CAV PUMP ONLY
39C. You will find a label
attached to the top of the
injection pump, quoting the
correct timing measurement in
millimetres. Slacken the pump
flange nuts (as in, illustration
39B, part A) and the rear
support bolt (as in, illustration
39A, part A). Remove the
plastic cap from the pump top.
Now turn the engine crankshaft
in the opposite direction to
normal rotation by about 20
degrees. Using either FIAT tool
No. 1865091000 or, with the
cos / * susPect a but
fl^^^Cf- ^^ its location isn't obvious,
start the engine and
pressurise the system by holding a piece of board
against the tailpipe.
• Under pressure, the leak should be more noisy and
obvious.
• Don't burn yourself on the exhaust!
Page 53 of 171
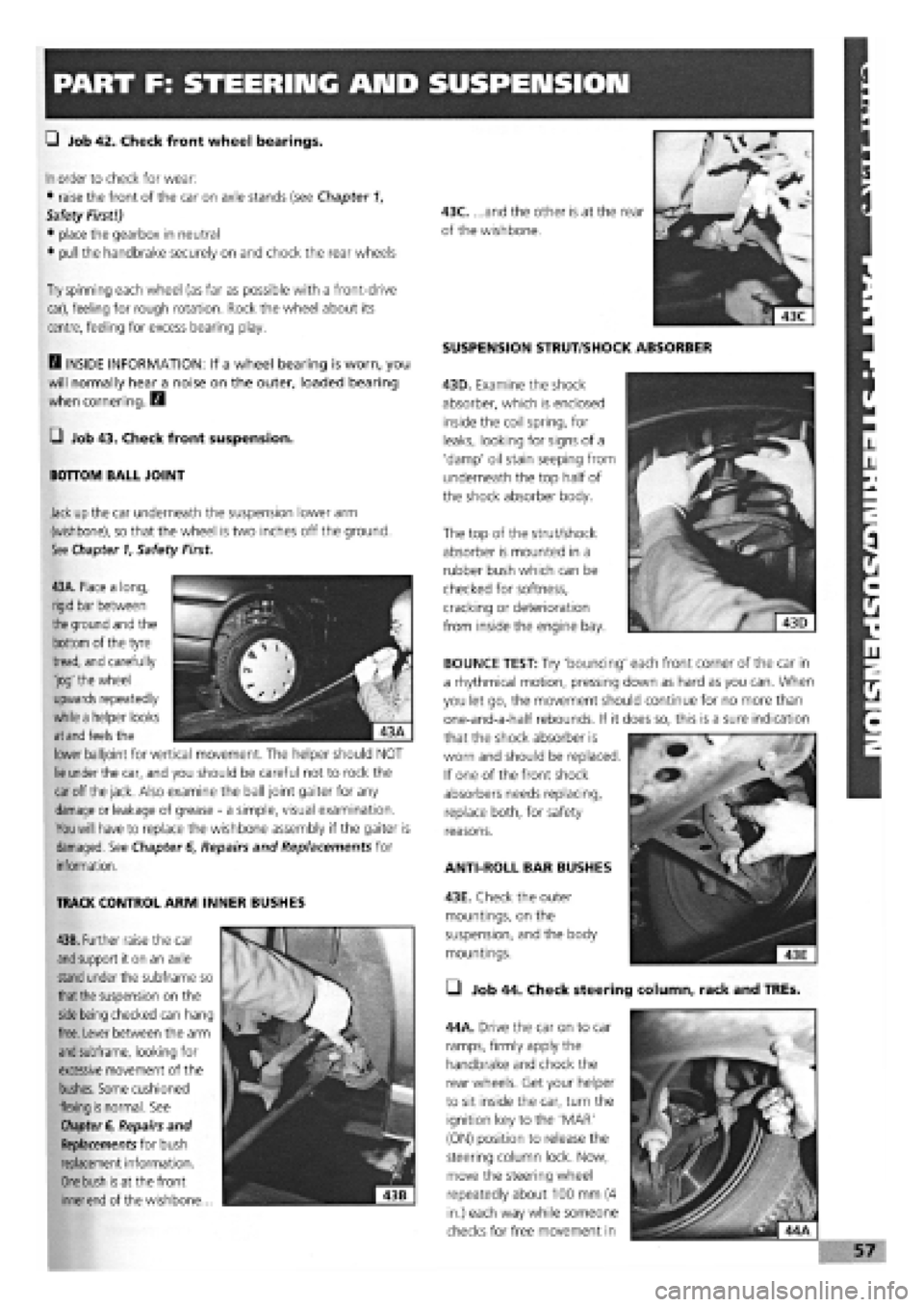
PART F: STEERING AMD SUSPENSION
G Job 42. Check front wheel bearings.
In
order to check for wear:
• raise the front of the car on axle stands (see Chapter 1,
Safety First!)
• place the gearbox in neutral
• pull the handbrake securely on and chock the rear wheels
Try
spinning each wheel (as far as possible with a front-drive
car), feeling for rough rotation. Rock the wheel about its
centre, feeling for excess bearing play.
D INSIDE INFORMATION: If a wheel bearing is worn, you
will normally hear a noise on the outer, loaded bearing
when cornering. D
G Job 43. Check front suspension.
BOTTOM BALL JOINT
Jack
up
the car underneath the suspension lower arm
(wishbone), so that the wheel is two inches off the ground.
See Chapter
1,
Safety First.
SUSPENSION STRUT/SHOCK ABSORBER
43D. Examine the shock
absorber, which is enclosed
inside the coil spring, for
leaks, looking for signs of a
'damp' oil stain seeping from
underneath the top half of
the shock absorber body.
The top of the strut/shock
absorber is mounted in a
rubber bush which can be
checked for softness,
cracking or deterioration
from inside the engine bay.
43A. Place a long,
rigid bar between
the
ground and the
bottom of the tyre
tread, and carefully
'jog' the wheel
upwards repeatedly
while a helper looks
at and
feels the
lower balljoint for vertical movement. The helper should NOT
lie
under the car, and you should be careful not to rock the
car
off
the jack.
Also examine the ball joint gaiter for any
damage
or leakage of grease
-
a simple, visual examination.
You will
have to replace the wishbone assembly if the gaiter is
damaged. See Chapter
6,
Repairs and Replacements for
information.
TRACK CONTROL ARM INNER BUSHES
43B. Further raise the car
and
support it on an axle
stand
under the subframe so
that the
suspension on the
side being
checked can hang
free. Lever between the arm
and
subframe, looking for
excessive movement of the
bushes. Some cushioned
flexing
is
normal. See
Chapter
6, Repairs and
Replacements for bush
replacement information.
One bush is
at the front
inner end
of the wishbone...
ANTI-ROLL BAR BUSHES
43E. Check the outer
mountings, on the
suspension, and the body
mountings.
• Job 44. Check steering column, rack and TREs.
44A. Drive the car on to car
ramps, firmly apply the
handbrake and chock the
rear wheels. Get your helper
to sit inside the car, turn the
ignition key to the 'MAR'
(ON) position to release the
steering column lock. Now,
move the steering wheel
repeatedly about 100 mm (4
in.) each way while someone
checks for free movement in
BOUNCE TEST: Try 'bouncing' each front corner of the car in
a rhythmical motion, pressing down as hard as you can. When
you let go, the movement should continue for no more than
one-and-a-half rebounds. If it does so, this is a sure indication
that the shock absorber is
worn and should be replaced.
If one of the front shock
absorbers needs replacing,
replace both, for safety
reasons.
Page 54 of 171
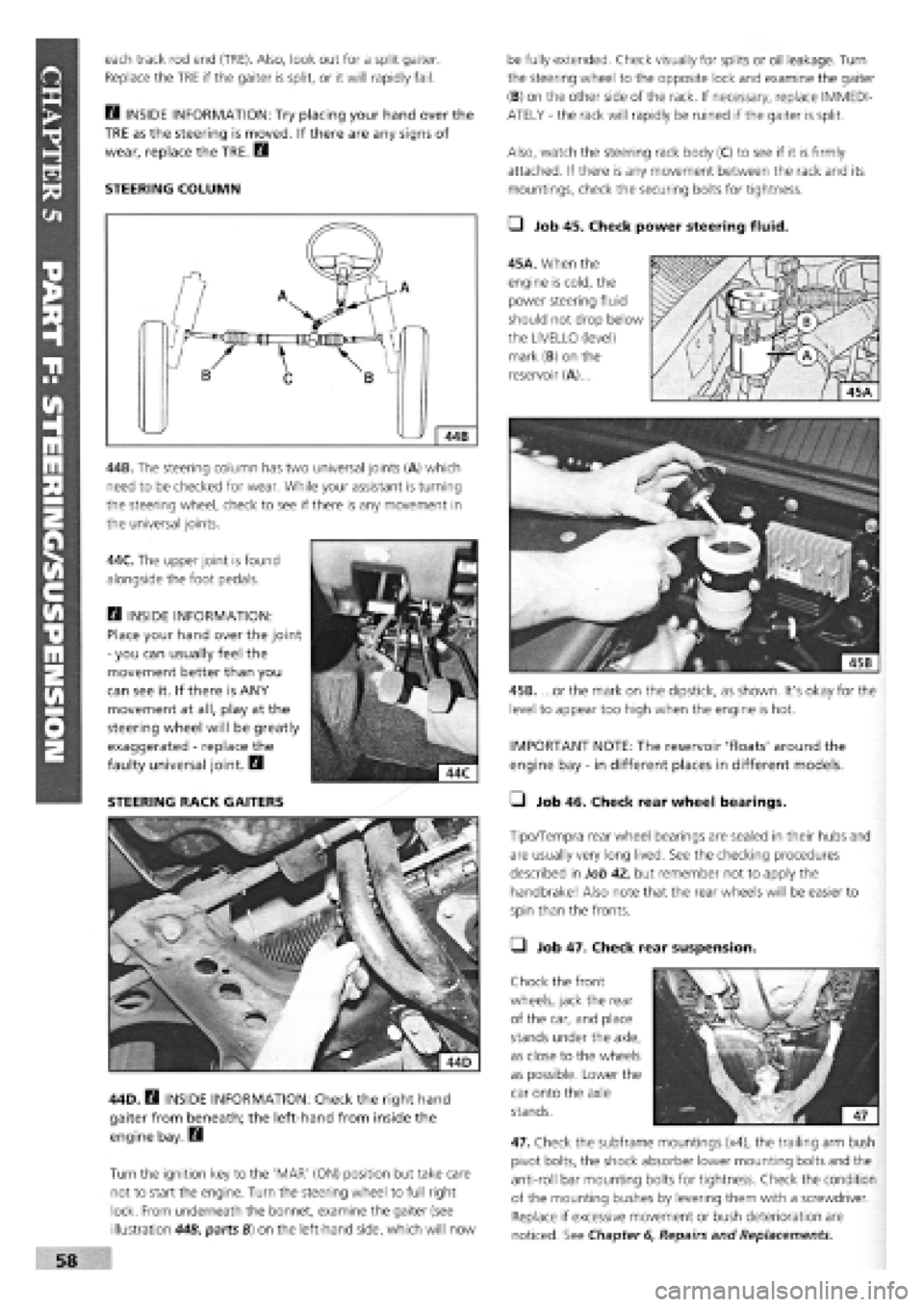
each track rod end (TRE). Also, look out for a split gaiter.
Replace the TRE if the gaiter is split, or it will rapidly fail.
E3 INSIDE INFORMATION: Try placing your hand over the
TRE as the steering is moved. If there are any signs of
wear, replace the TRE. Q
STEERING COLUMN
44B. The steering column has two universal joints (A) which
need to be checked for wear. While your assistant is turning
the steering wheel, check to see if there is any movement in
the universal joints.
44C. The upper joint is found
alongside the foot pedals.
Q INSIDE INFORMATION:
Place your hand over the joint
-
you can usually feel the
movement better than you
can see it. If there is ANY
movement at all, play at the
steering wheel will be greatly
exaggerated
-
replace the
faulty universal joint. B
STEERING RACK GAITERS
44D. B INSIDE INFORMATION: Check the right hand
gaiter from beneath; the left-hand from inside the
engine bay. Q
Turn the ignition key to the 'MAR' (ON) position but take care
not to start the engine. Turn the steering wheel to full right
lock. From underneath the bonnet, examine the gaiter (see
illustration 44B, parts B) on the left-hand side, which will now
be fully extended. Check visually for splits or oil leakage. Turn
the steering wheel to the opposite lock and examine the gaiter
(B) on the other side of the rack. If necessary, replace IMMEDI-
ATELY
-
the rack will rapidly be ruined if the gaiter is split.
Also, watch the steering rack body (C) to see if it is firmly
attached. If there is any movement between the rack and its
mountings, check the securing bolts for tightness.
• Job 45. Check power steering fluid.
45A. When the
engine is cold, the
power steering fluid
should not drop below
the LIVELLO (level)
mark (B) on the
reservoir (A)...
45B. ...or the mark on the dipstick, as shown. It's okay for the
level to appear too high when the engine is hot.
IMPORTANT NOTE: The reservoir 'floats' around the
engine bay
-
in different places in different models.
• Job 46. Check rear wheel bearings.
Tipo/Tempra rear wheel bearings are sealed in their hubs and
are usually very long lived. See the checking procedures
described in Job 42, but remember not to apply the
handbrake! Also note that the rear wheels will be easier to
spin than the fronts.
• Job 47. Check rear suspension.
Chock the front
wheels, jack the rear
of the car, and place
stands under the axle,
as close to the wheels
as possible. Lower the
car onto the axle
stands.
47. Check the subframe mountings (x4), the trailing arm bush
pivot bolts, the shock absorber lower mounting bolts and the
anti-roll bar mounting bolts for tightness. Check the condition
of the mounting bushes by levering them with a screwdriver.
Replace if excessive movement or bush deterioration are
noticed. See Chapter
6,
Repairs and Replacements.
Page 55 of 171
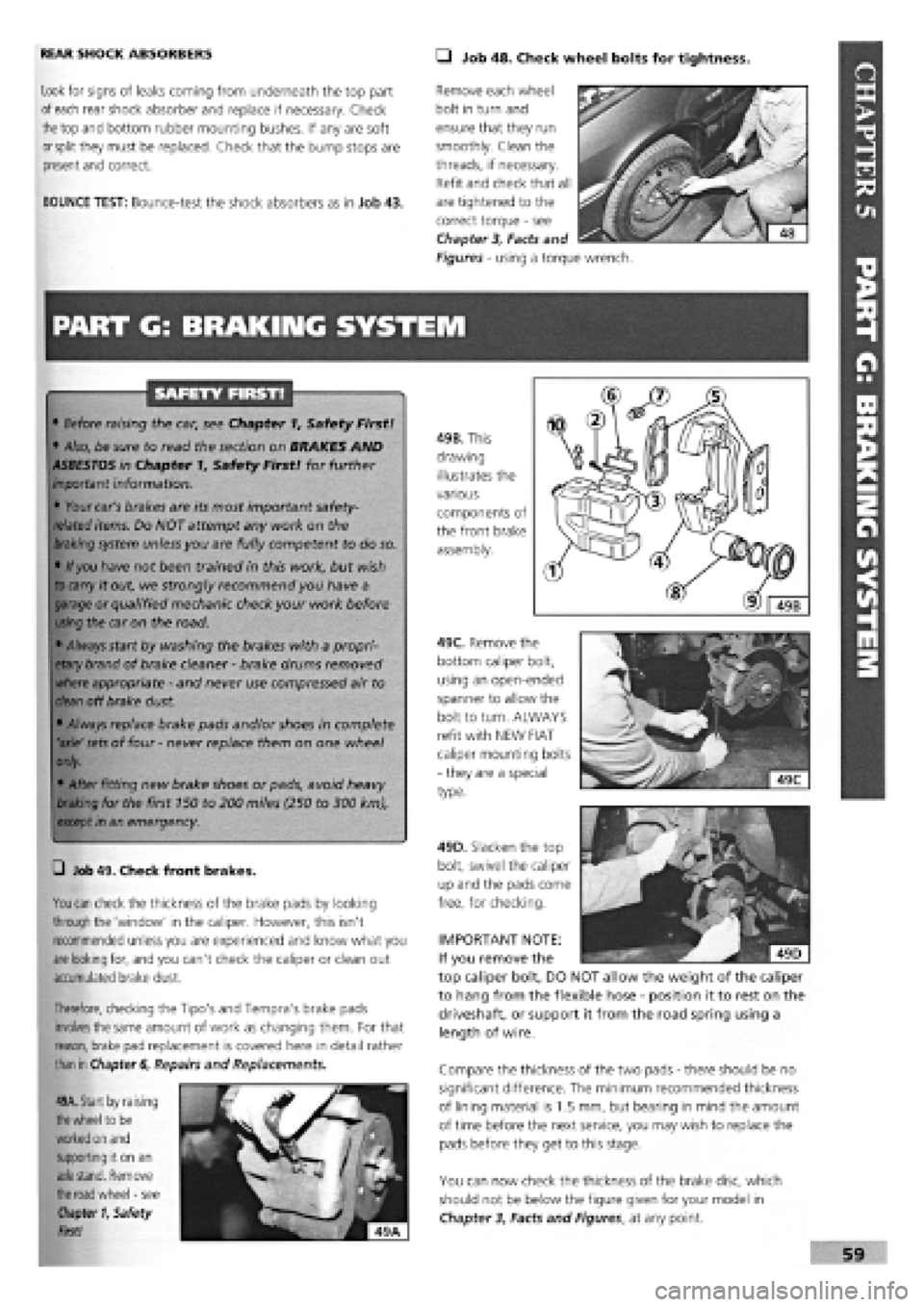
REAR SHOCK ABSORBERS • Job 48. Check wheel bolts for tightness.
Look for signs of leaks coming from underneath the top part
of
each
rear shock absorber and replace if necessary. Check
the
top and bottom rubber mounting bushes. If any are soft
or
split they must be replaced. Check that the bump stops are
present and correct.
BOUNCE TEST: Bounce-test the shock absorbers as in Job 43.
PART G: BRAKING SYSTEM
SAFETY FIRST!
• Job 49. Check front brakes.
You can
check the thickness of the brake pads by looking
through
the 'window' in the caliper. However, this isn't
recommended
unless you are experienced and know what you
are looking for,
and you can't check the caliper or clean out
accumulated
brake dust.
• Before raising the car, see Chapter 1, Safety First!
•
Also,
be sure to read the section on BRAKES AND
ASBESTOS in Chapter 1, Safety First! for further
important
information.
•
Your car's
brakes are its most important
safety-
related items.
Do NOT attempt any work on the
braking system unless
you are fully competent to do so.
• If you have not been trained in this work, but wish
to
carry
it out, we strongly recommend you have a
garage
or qualified mechanic check your work before
using
the car on the road.
•
Always
start by washing the brakes with a propri-
etary
brand of brake cleaner
-
brake drums removed
where
appropriate
-
and never use compressed air to
clean
off
brake
dust.
•
Always
replace brake pads and/or shoes in complete
'axle' sets
of four
-
never replace them on one wheel
only.
• After fitting new brake shoes or pads, avoid heavy
braking
for the first
150
to 200 miles (250 to 300 km),
except
in
an emergency.
49B. This
drawing
illustrates the
various
components of
the front brake
assembly.
49C. Remove the
bottom caliper bolt,
using an open-ended
spanner to allow the
bolt to turn. ALWAYS
refit with NEW FIAT
caliper mounting bolts
-
they are a special
type.
Therefore,
checking the Tipo's and Tempra's brake pads
involves
the same amount of work as changing them. For that
reason, brake
pad replacement is covered here in detail rather
than in
Chapter
6,
Repairs and Replacements.
49A. Start by raising
the
wheel to
be
worked on and
supporting it on
an
axle stand. Remove
the road wheel
-
see
Chapter
1, Safety
First!
Compare the thickness of the two pads
-
there should be no
significant difference. The minimum recommended thickness
of lining material is 1.5 mm, but bearing in mind the amount
of time before the next service, you may wish to replace the
pads before they get to this stage.
You can now check the thickness of the brake disc, which
should not be below the figure given for your model in
Chapter
3,
Facts and Figures, at any point.
Remove each wheel
bolt in turn and
ensure that they run
smoothly. Clean the
threads, if necessary.
Refit and check that all
are tightened to the
correct torque
-
see
Chapter
3,
Facts and
Figures
-
using a torque wrench.
49D. Slacken the top
bolt, swivel the caliper
up and the pads come
free, for checking.
IMPORTANT NOTE:
If you remove the
top caliper bolt, DO NOT allow the weight of the caliper
to hang from the flexible hose
-
position it to rest on the
driveshaft, or support it from the road spring using a
length of wire.
Page 56 of 171
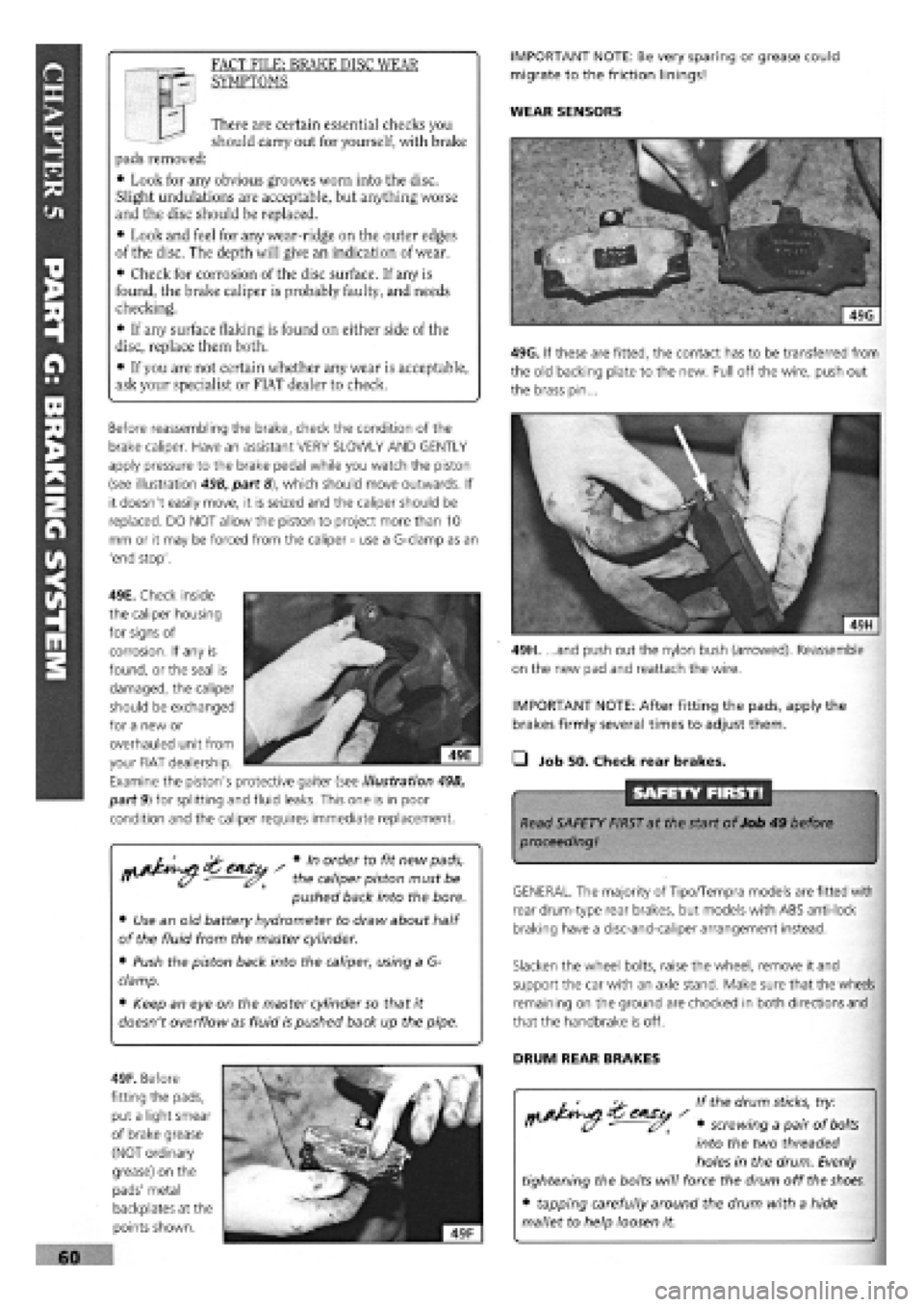
49H. ...and push out the nylon bush (arrowed). Reassemble
on the new pad and reattach the wire.
IMPORTANT NOTE: After fitting the pads, apply the
brakes firmly several times to adjust them.
• Job 50. Check rear brakes.
SAFETY FIRST!
Read SAFETY FIRST at the start of Job 49 before
proceeding!
GENERAL. The majority of Tipo/Tempra models are fitted with
rear drum-type rear brakes, but models with ABS anti-lock
braking have a disc-and-caliper arrangement instead.
Slacken the wheel bolts, raise the wheel, remove it and
support the car with an axle stand. Make sure that the wheels
remaining on the ground are chocked in both directions and
that the handbrake is off.
DRUM REAR BRAKES
If the drum
sticks,
try:
• screwing a pair of
bolts
into the two threaded
holes in the drum. Evenly
tightening the bolts will force the drum off the
shoes.
• tapping carefully around the drum with a hide
mallet to help loosen it.
s Vn order to fit new pads,
r> - the caliper piston must be
pushed back into the bore.
• Use an old battery hydrometer to draw about half
of the fluid from the master cylinder.
• Push the piston back into the caliper, using a G-
clamp.
• Keep an eye on the master cylinder so that it
doesn't overflow as fluid is pushed back up the pipe.
IMPORTANT NOTE: Be very sparing or grease could
migrate to the friction linings!
WEAR SENSORS I I There are certain essential checks you
should carry out for yourself, with brake
pads removed:
• Look for any obvious grooves worn into the disc.
Slight undulations are acceptable, but anything worse
and the disc should be replaced.
• Look and feel for any wear-ridge on the outer edges
of the disc. The depth will give an indication of wear.
• Check for corrosion of the disc surface. If any is
found, the brake caliper is probably faulty, and needs
checking.
• If any surface flaking is found on either side of the
disc, replace them both.
• If you are not certain whether any wear is acceptable,
ask your specialist or FIAT dealer to check.
FACT FILE: BRAKE DISC WEAR
SYMPTOMS
Before reassembling the brake, check the condition of the
brake caliper. Have an assistant VERY SLOWLY AND GENTLY
apply pressure to the brake pedal while you watch the piston
(see illustration 49B, part
8),
which should move outwards. If
it doesn't easily move, it is seized and the caliper should be
replaced. DO NOT allow the piston to project more than 10
mm or it may be forced from the caliper
-
use a G-clamp as an
'end stop'.
49F. Before
fitting the pads,
put a light smear
of brake grease
(NOT ordinary
grease) on the
pads' metal
backplates at the
points shown.
49G. If these are fitted, the contact has to be transferred from
the old backing plate to the new. Pull off the wire, push out
the brass pin...
49E. Check inside
the caliper housing
for signs of
corrosion. If any is
found, or the seal is
damaged, the caliper
should be exchanged
for a new or
overhauled unit from
your FIAT dealership.
Examine the piston's protective gaiter (see illustration 49B,
part 9) for splitting and fluid leaks. This one is in poor
condition and the caliper requires immediate replacement.
Page 57 of 171
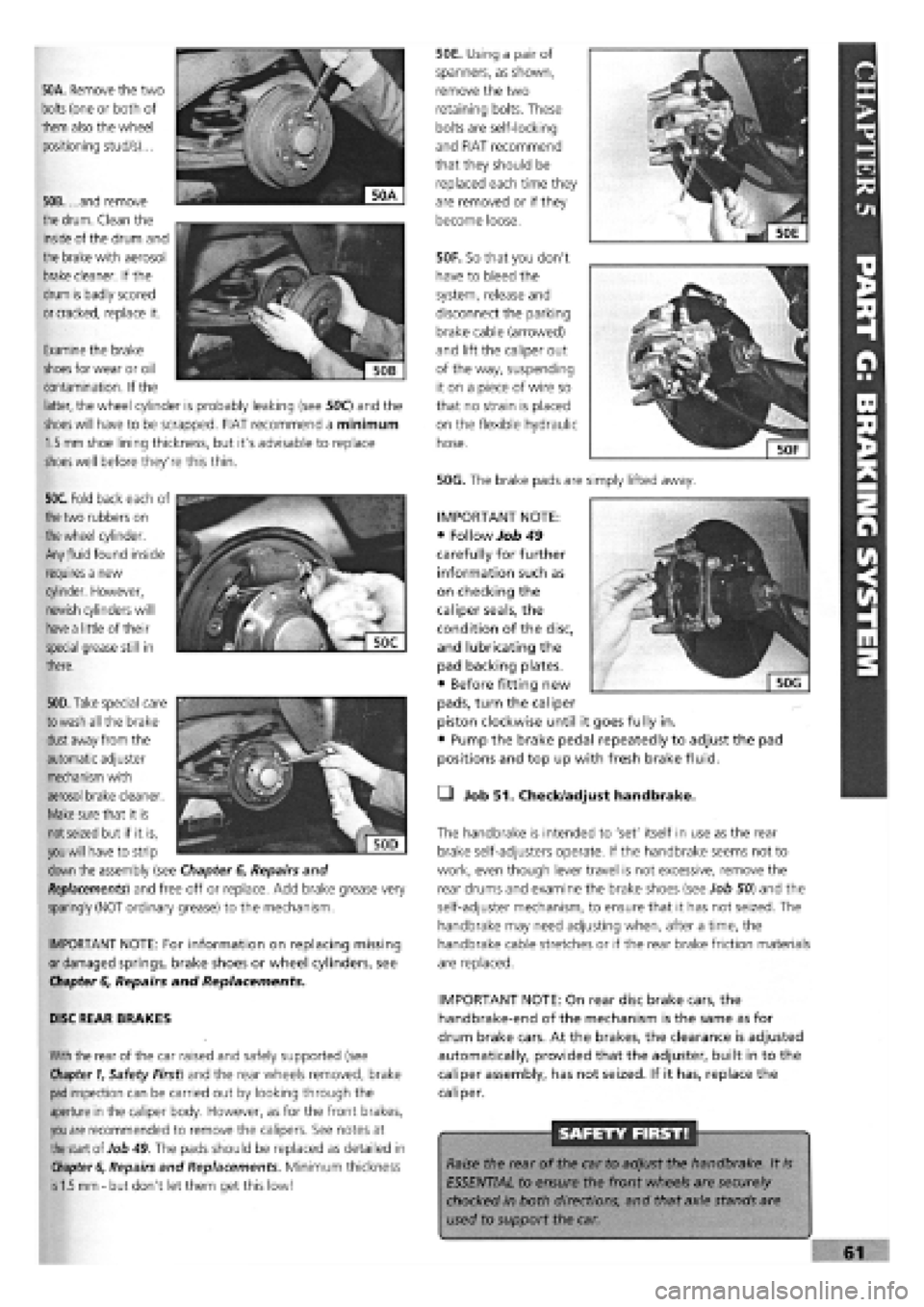
50A. Remove the two
bolts
(one or both of
them also the wheel
positioning stud/s)...
50B. ...and remove
the
drum.
Clean the
inside of the drum and
the brake with aerosol
brake
cleaner. If the
drum is badly scored
or cracked,
replace it.
50F. So that you don't
have to bleed the
system, release and
disconnect the parking
brake cable (arrowed)
and lift the caliper out
of the way, suspending
it on a piece of wire so
that no strain is placed
on the flexible hydraulic
hose.
50G. The brake pads are simply lifted away.
50E. Using a pair of
spanners, as shown,
remove the two
retaining bolts. These
bolts are self-locking
and FIAT recommend
that they should be
replaced each time they
are removed or if they
become loose.
Examine the brake
shoes
for wear or oil
contamination. If the
latter, the wheel cylinder is probably leaking (see 50C) and the
shoes will
have to be scrapped. FIAT recommend a minimum
1.5 mm
shoe lining thickness, but it's advisable to replace
shoes
well before they're this thin.
50C. Fold back each of
the
two rubbers on
the wheel
cylinder.
Any
fluid
found inside
requires a new
cylinder. However,
newish cylinders will
have a
little of their
special grease still in
there.
. """
€
Sjjj
KV,1
| 50D|
50D. Take
special care
to wash
all the brake
dust
away from the
automatic adjuster
mechanism with
aerosol brake cleaner.
Make
sure that it is
not seized
but if it is,
you will
have to strip
down
the assembly (see Chapter
6,
Repairs and
Replacements)
and free off or replace. Add brake grease very
sparingly (NOT ordinary grease) to the mechanism.
IMPORTANT NOTE: For information on replacing missing
or damaged springs, brake shoes or wheel cylinders, see
Chapter
6,
Repairs and Replacements.
DISC REAR BRAKES
With
the rear of the car raised and safely supported (see
Chapter 1,
Safety First) and the rear wheels removed, brake
pad
inspection can be carried out by looking through the
aperture in the caliper body. However, as for the front brakes,
you are
recommended to remove the calipers. See notes at
the
start of Job
49.
The pads should be replaced as detailed in
Chapter 6,
Repairs and Replacements. Minimum thickness
is 1.5 mm -
but don't let them get this low!
• Job 51. Check/adjust handbrake.
The handbrake is intended to 'set' itself in use as the rear
brake self-adjusters operate. If the handbrake seems not to
work, even though lever travel is not excessive, remove the
rear drums and examine the brake shoes (see Job 50) and the
self-adjuster mechanism, to ensure that it has not seized. The
handbrake may need adjusting when, after a time, the
handbrake cable stretches or if the rear brake friction materials
are replaced.
IMPORTANT NOTE: On rear disc brake cars, the
handbrake-end of the mechanism is the same as for
drum brake cars. At the brakes, the clearance is adjusted
automatically, provided that the adjuster, built in to the
caliper assembly, has not seized. If it has, replace the
caliper.
SAFETY FIRST!
Raise the rear of the car to adjust the handbrake. It
is
ESSENTIAL to ensure the front wheels are securely
chocked in both directions, and that axle stands are
used to support the car.
IMPORTANT NOTE:
• Follow Job 49
carefully for further
information such as
on checking the
caliper seals, the
condition of the disc,
and lubricating the
pad backing plates.
• Before fitting new
pads, turn the caliper
piston clockwise until it goes fully in.
• Pump the brake pedal repeatedly to adjust the pad
positions and top up with fresh brake fluid.
Page 58 of 171
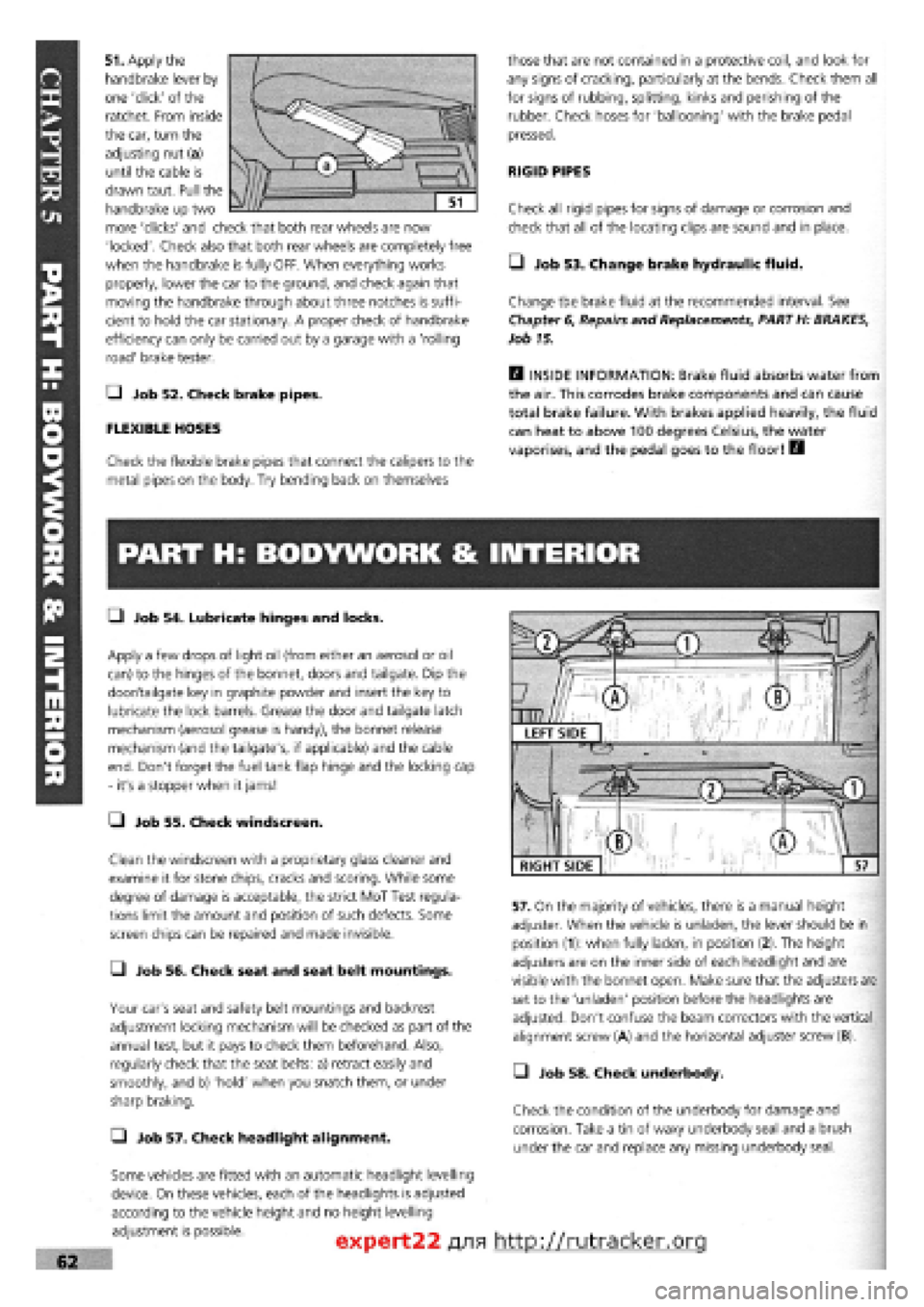
51. Apply the
handbrake lever by
one 'click' of the
ratchet. From inside
the car, turn the
adjusting nut (a)
until the cable is
drawn taut. Pull the
handbrake up two
more 'clicks' and check that both rear wheels are now
'locked'. Check also that both rear wheels are completely free
when the handbrake is fully OFF. When everything works
properly, lower the car to the ground, and check again that
moving the handbrake through about three notches is suffi-
cient to hold the car stationary. A proper check of handbrake
efficiency can only be carried out by a garage with a 'rolling
road' brake tester.
Q Job 52. Check brake pipes.
FLEXIBLE HOSES
Check the flexible brake pipes that connect the calipers to the
metal pipes on the body. Try bending back on themselves
those that are not contained in a protective coil, and look for
any signs of cracking, particularly at the bends. Check them all
for signs of rubbing, splitting, kinks and perishing of the
rubber. Check hoses for 'ballooning' with the brake pedal
pressed.
RIGID PIPES
Check all rigid pipes for signs of damage or corrosion and
check that all of the locating clips are sound and in place.
• Job 53. Change brake hydraulic fluid.
Change the brake fluid at the recommended interval. See
Chapter
6,
Repairs and Replacements, PART H: BRAKES,
Job 15.
H INSIDE INFORMATION: Brake fluid absorbs water from
the air. This corrodes brake components and can cause
total brake failure. With brakes applied heavily, the fluid
can heat to above 100 degrees Celsius, the water
vaporises, and the pedal goes to the floor! B
PART H: BODYWORK & INTERIOR
• Job 54. Lubricate hinges and locks.
Apply a few drops of light oil (from either an aerosol or oil
can) to the hinges of the bonnet, doors and tailgate. Dip the
door/tailgate key in graphite powder and insert the key to
lubricate the lock barrels. Grease the door and tailgate latch
mechanism (aerosol grease is handy), the bonnet release
mechanism (and the tailgate's, if applicable) and the cable
end. Don't forget the fuel tank flap hinge and the locking cap
- it's a stopper when it jams!
• Job 55. Check windscreen.
Clean the windscreen with a proprietary glass cleaner and
examine it for stone chips, cracks and scoring. While some
degree of damage is acceptable, the strict MoT Test regula-
tions limit the amount and position of such defects. Some
screen chips can be repaired and made invisible.
• Job 56. Check seat and seat belt mountings.
Your car's seat and safety belt mountings and backrest
adjustment locking mechanism will be checked as part of the
annual test, but it pays to check them beforehand. Also,
regularly check that the seat belts: a) retract easily and
smoothly, and b) 'hold' when you snatch them, or under
sharp braking.
Q Job 57. Check headlight alignment.
Some vehicles are fitted with an automatic headlight levelling
device. On these vehicles, each of the headlights is adjusted
according to the vehicle height and no height levelling
adjustment is possible.
57. On the majority of vehicles, there is a manual height
adjuster. When the vehicle is unladen, the lever should be in
position (1): when fully laden, in position (2). The height
adjusters are on the inner side of each headlight and are
visible with the bonnet open. Make sure that the adjusters are
set to the 'unladen' position before the headlights are
adjusted. Don't confuse the beam correctors with the vertical
alignment screw (A) and the horizontal adjuster screw (B).
• Job 58. Check underbody.
Check the condition of the underbody for damage and
corrosion. Take a tin of waxy underbody seal and a brush
under the car and replace any missing underbody seal.
expert22 fl/ia http://rutracker.org
RIGHT SIDE
Page 59 of 171
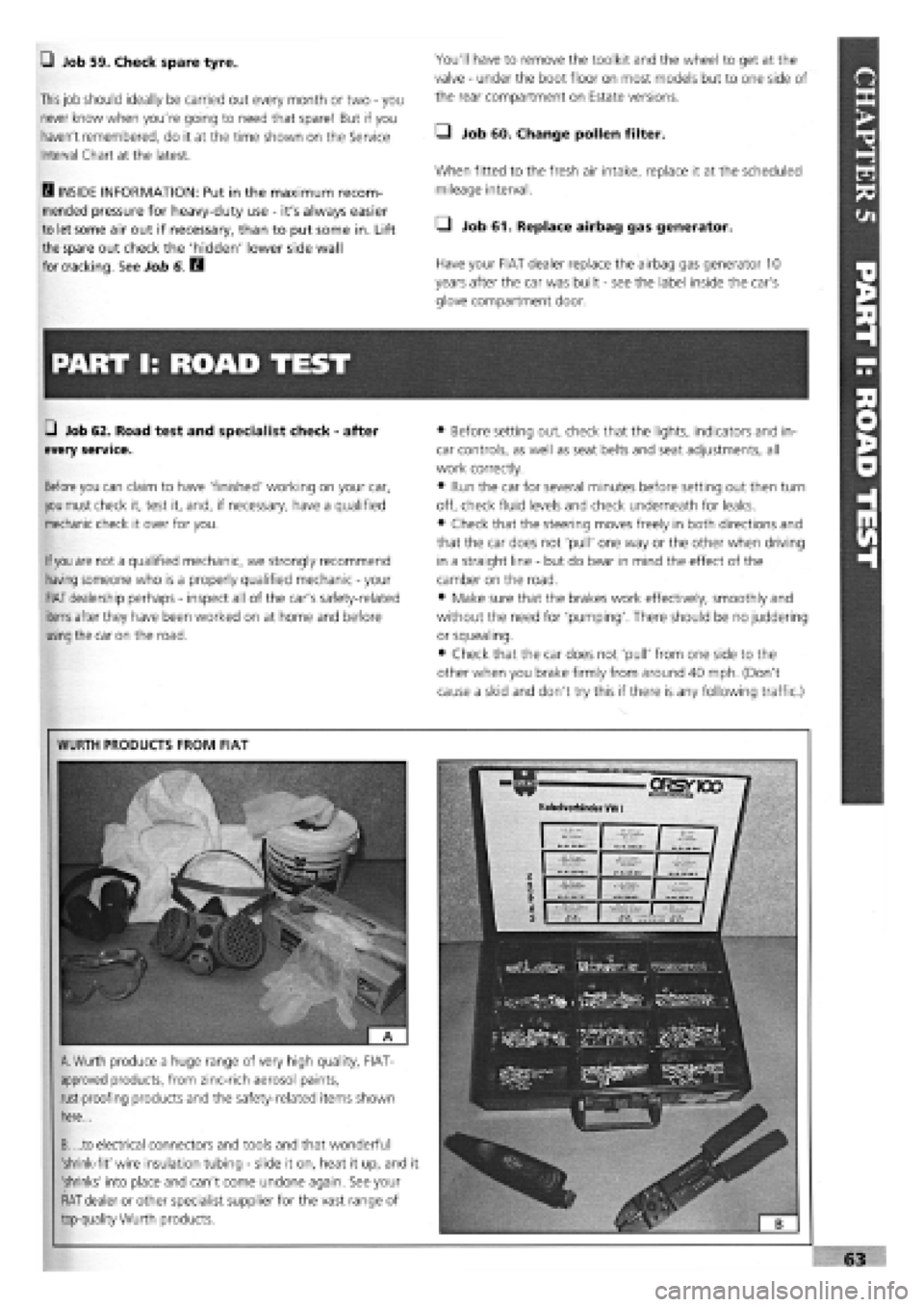
—1 Job 59. Check spare tyre.
This
job should ideally be carried out every month or two
-
you
never know when you're going to need that spare! But if you
haven't remembered, do it at the time shown on the Service
Interval Chart at the latest.
Q INSIDE INFORMATION: Put in the maximum recom-
mended pressure for heavy-duty use
-
it's always easier
to let some air out if necessary, than to put some in. Lift
the spare out check the 'hidden' lower side wall
for cracking. See Job 6. E9
PART I: ROAD TEST
Q Job 62. Road test and specialist check
-
after
every service.
Before you can claim to have 'finished' working on your car,
you must check it, test it, and, if necessary, have a qualified
mechanic check it over for you.
If you
are not a qualified mechanic, we strongly recommend
having someone who is a properly qualified mechanic
-
your
FIAT dealership perhaps
-
inspect all of the car's safety-related
items
after they have been worked on at home and before
using
the car on the road.
You'll have to remove the toolkit and the wheel to get at the
valve
-
under the boot floor on most models but to one side of
the rear compartment on Estate versions.
• Job 60. Change pollen filter.
When fitted to the fresh air intake, replace it at the scheduled
mileage interval.
• Job 61. Replace airbag gas generator.
Have your FIAT dealer replace the airbag gas generator 10
years after the car was built
-
see the label inside the car's
glove compartment door.
• Before setting out, check that the lights, indicators and in-
car controls, as well as seat belts and seat adjustments, all
work correctly.
• Run the car for several minutes before setting out then turn
off, check fluid levels and check underneath for leaks.
• Check that the steering moves freely in both directions and
that the car does not 'pull' one way or the other when driving
in a straight line
-
but do bear in mind the effect of the
camber on the road.
• Make sure that the brakes work effectively, smoothly and
without the need for 'pumping'. There should be no juddering
or squealing.
• Check that the car does not 'pull' from one side to the
other when you brake firmly from around 40 mph. (Don't
cause a skid and don't try this if there is any following traffic.)
"V,
WURTH PRODUCTS FROM FIAT
A.
Wurth produce a huge range of very high quality, FIAT-
approved products, from zinc-rich aerosol paints,
rust-proofing products and the safety-related items shown
here...
B. ...to electrical connectors and tools and that wonderful
'shrink-fit' wire insulation tubing
-
slide it on, heat it up, and it
'shrinks' into place and can't come undone again. See your
FIAT dealer or other specialist supplier for the vast range of
top-quality Wurth products.
Page 60 of 171
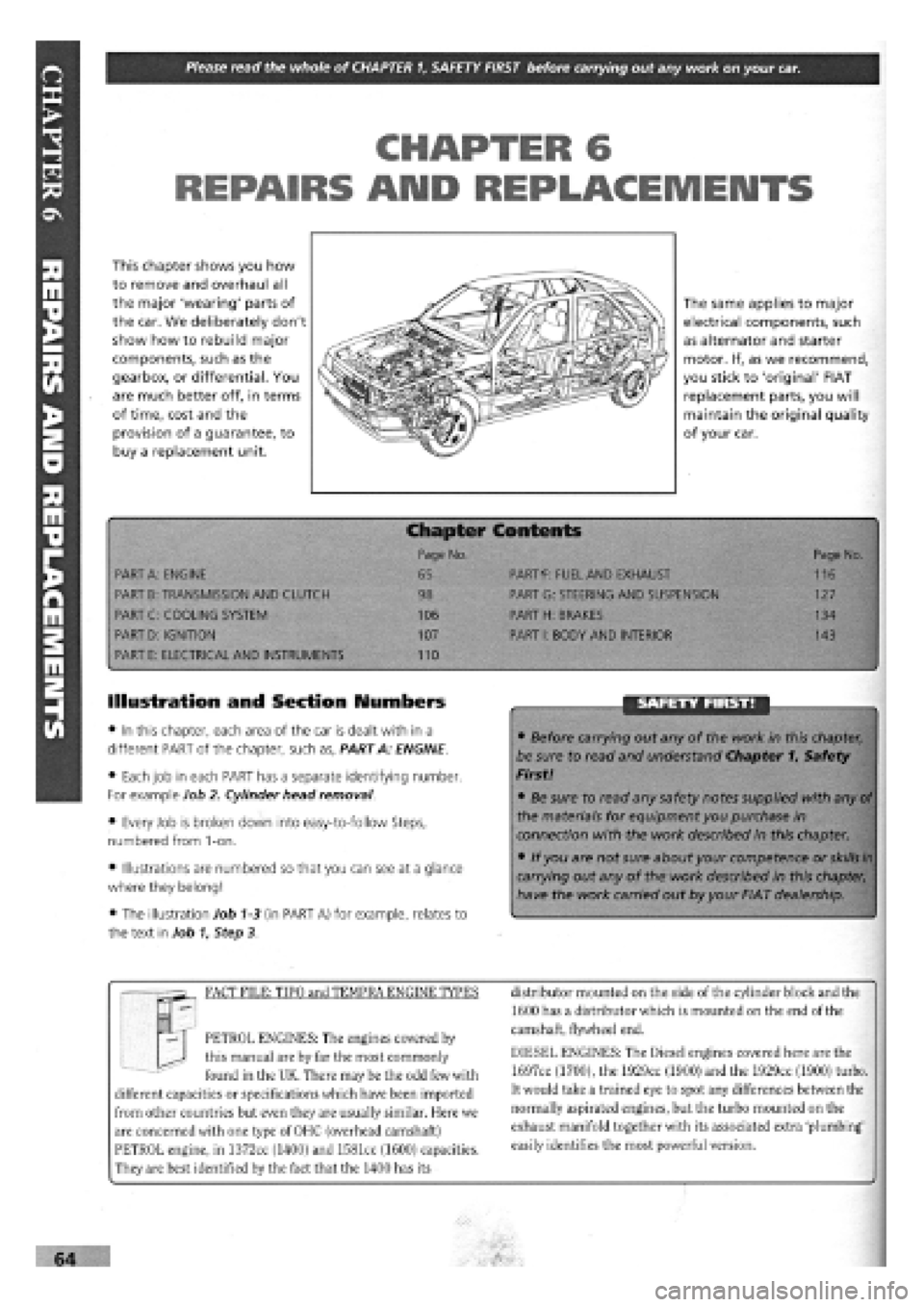
Please read the whole of CHAPTER
1,
SAFETY FIRST before carrying out any work on your car.
CHAPTER 6
REPAIRS AND REPLACEMENTS
This chapter shows you how
to remove and overhaul all
the major 'wearing' parts of
the car. We deliberately don't
show how to rebuild major
components, such as the
gearbox, or differential. You
are much better off, in terms
of time, cost and the
provision of a guarantee, to
buy a replacement unit.
The same applies to major
electrical components, such
as alternator and starter
motor. If, as we recommend,
you stick to 'original' FIAT
replacement parts, you will
maintain the original quality
of your car.
PART A: ENGINE
PART B: TRANSMISSION AND CLUTCH
PART C: COOLING SYSTEM
PART D: IGNITION
PART E: ELECTRICAL AND INSTRUMENTS
:er Contents
PARTf: FUEL AND EXHAUST
PART G: STEERING AND SUSPENSION
PART H: BRAKES
PART I: BODY AND INTERIOR
110
Page No.
116
127
134
143
Illustration and Section Numbers
• In this chapter, each area of the car is dealt with in a
different PART of the chapter, such as, PART A: ENGINE.
• Each job in each PART has a separate identifying number.
For example Job 2. Cylinder head removal.
• Every Job is broken down into easy-to-follow Steps,
numbered from 1-on.
• Illustrations are numbered so that you can see at a glance
where they belong!
• The illustration Job
1-3
(in PART A) for example, relates to
the text in Job 1, Step 3.
SAFETY FIRST!
• Before carrying out any of the work in this chapter,
be sure to read and understand Chapter 1, Safety
First!
• Be sure to read any safety notes supplied with any
of
the materials for equipment you purchase in
connection with the work described in this chapter.
• If you are not sure about your competence or
skills in
carrying out any of the work described in this chapter,
have the work carried out by your FIAT dealership.
FACT FILE: TIPO and TEMPRA ENGINE TYPES
PETROL ENGINES: The engines covered by
this manual are by far the most commonly
found in the UK. There may be the odd few with
different capacities or specifications which have been imported
from other countries but even they are usually similar. Here we
are concerned with one type of OHC (overhead camshaft)
PETROL engine, in 1372cc (1400) and 1581cc (1600) capacities.
They are best identified by the fact that the 1400 has its
distributor mounted on the side of the cylinder block and the
1600 has a distributor which is mounted on the end of the
camshaft, flywheel end.
DIESEL ENGINES: The Diesel engines covered here are the
1697cc (1700), the 1929cc (1900) and the 1929cc (1900) turbo.
It would take a trained eye to spot any differences between the
normally aspirated engines, but the turbo mounted on the
exhaust manifold together with its associated extra 'plumbing'
easily identifies the most powerful version.