FORD FESTIVA 1991 Service Manual
Manufacturer: FORD, Model Year: 1991, Model line: FESTIVA, Model: FORD FESTIVA 1991Pages: 454, PDF Size: 9.53 MB
Page 421 of 454
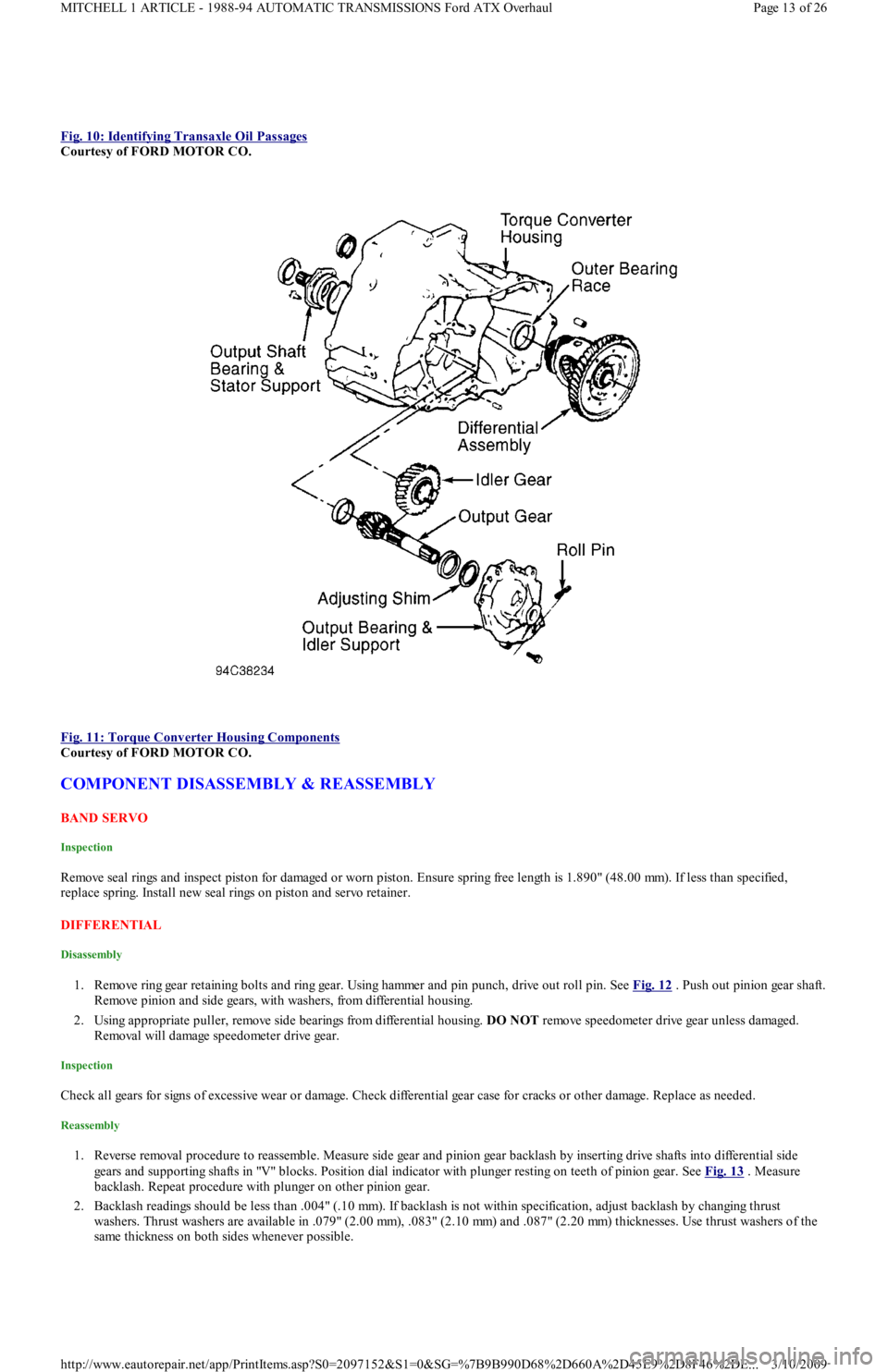
Fig. 10: Identifying Transaxle Oil Passages
Courtesy of FORD MOTOR CO.
Fig. 11: Torque Converter Housing Components
Courtesy of FORD MOTOR CO.
COMPONENT DISASSEMBLY & REASSEMBLY
BAND SERVO
Inspection
Remove seal rings and inspect piston for damaged or worn piston. Ensure spring free length is 1.890" (48.00 mm). If less than specified,
replace spring. Install new seal rings on piston and servo retainer.
DIFFERENTIAL
Disassembly
1. Remove ring gear retaining bolts and ring gear. Using hammer and pin punch, drive out roll pin. See Fig. 12. Push out pinion gear shaft.
Remove pinion and side gears, with washers, from differential housing.
2. Using appropriate puller, remove side bearings from differential housing. DO NOT remove speedometer drive gear unless damaged.
Removal will damage speedometer drive gear.
Inspection
Check all gears for signs of excessive wear or damage. Check differential gear case for cracks or other damage. Replace as needed.
Reassembly
1. Reverse removal procedure to reassemble. Measure side gear and pinion gear backlash by inserting drive shafts into differential side
gears and supporting shafts in "V" blocks. Position dial indicator with plunger resting on teeth of pinion gear. See Fig. 13
. Measure
backlash. Repeat procedure with plunger on other pinion gear.
2. Backlash readings should be less than .004" (.10 mm). If backlash is not within specification, adjust backlash by changing thrust
washers. Thrust washers are available in .079" (2.00 mm), .083" (2.10 mm) and .087" (2.20 mm) thicknesses. Use thrust washers of t h e
same thickness on both sides whenever possible.
Page 13 of 26 MITCHELL 1 ARTICLE - 1988-94 AUTOMATIC TRANSMISSIONS Ford ATX Overhaul
3/10/2009 http://www.eautorepair.net/app/PrintItems.asp?S0=2097152&S1=0&SG=%7B9B990D68%2D660A%2D45E9%2D8F46%2DE
...
Page 422 of 454
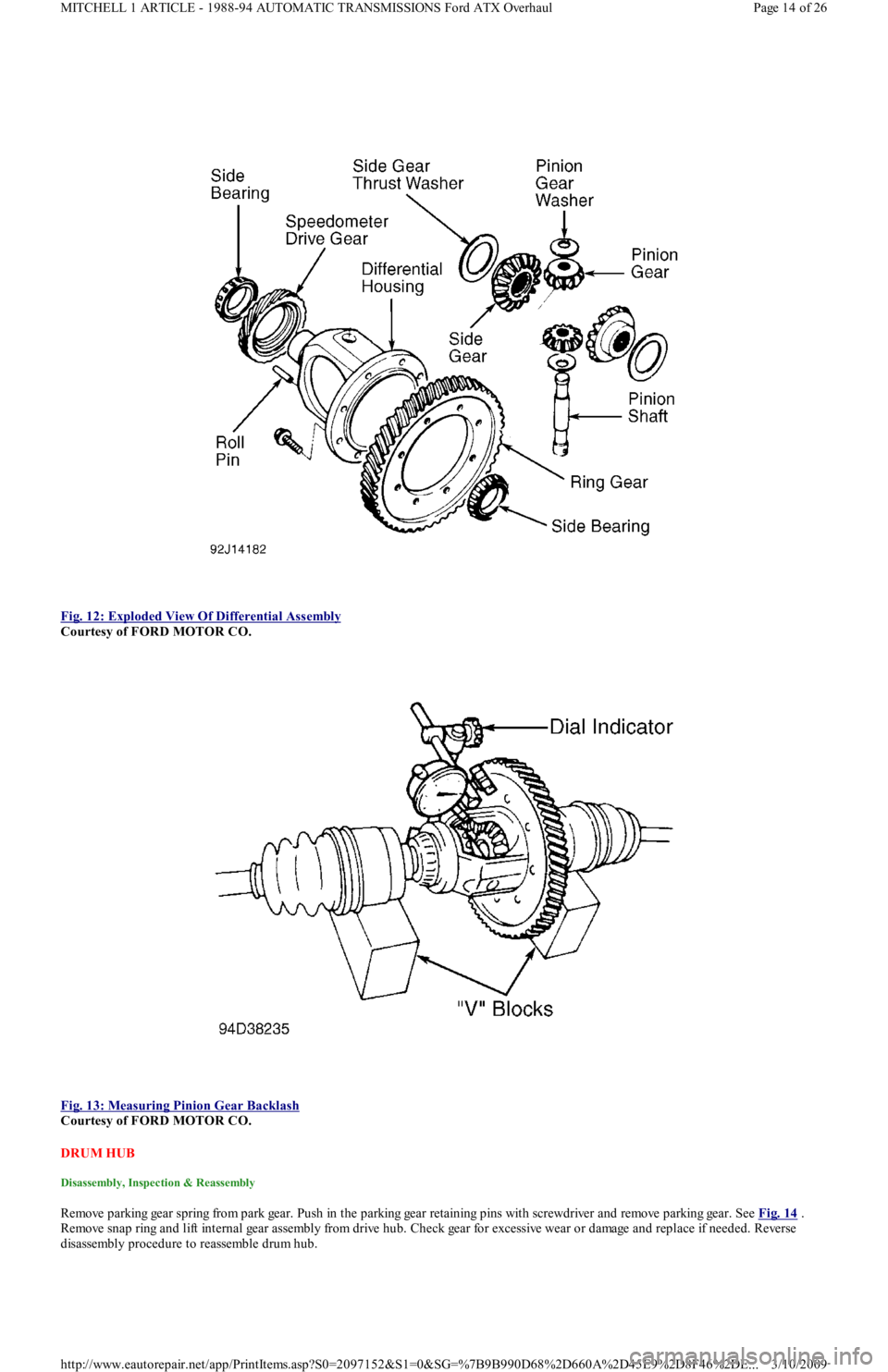
Fig. 12: Exploded View Of Differential Assembly
Courtesy of FORD MOTOR CO.
Fig. 13: Measuring Pinion Gear Backlash
Courtesy of FORD MOTOR CO.
DRUM HUB
Disassembly, Inspection & Reassembly
Remove parking gear spring from park gear. Push in the parking gear retaining pins with screwdriver and remove parking gear. See Fig. 14 .
Remove snap ring and lift internal gear assembly from drive hub. Check gear for excessive wear or damage and replace if needed. Reverse
disassembly procedure to reassemble drum hub.
Page 14 of 26 MITCHELL 1 ARTICLE - 1988-94 AUTOMATIC TRANSMISSIONS Ford ATX Overhaul
3/10/2009 http://www.eautorepair.net/app/PrintItems.asp?S0=2097152&S1=0&SG=%7B9B990D68%2D660A%2D45E9%2D8F46%2DE
...
Page 423 of 454
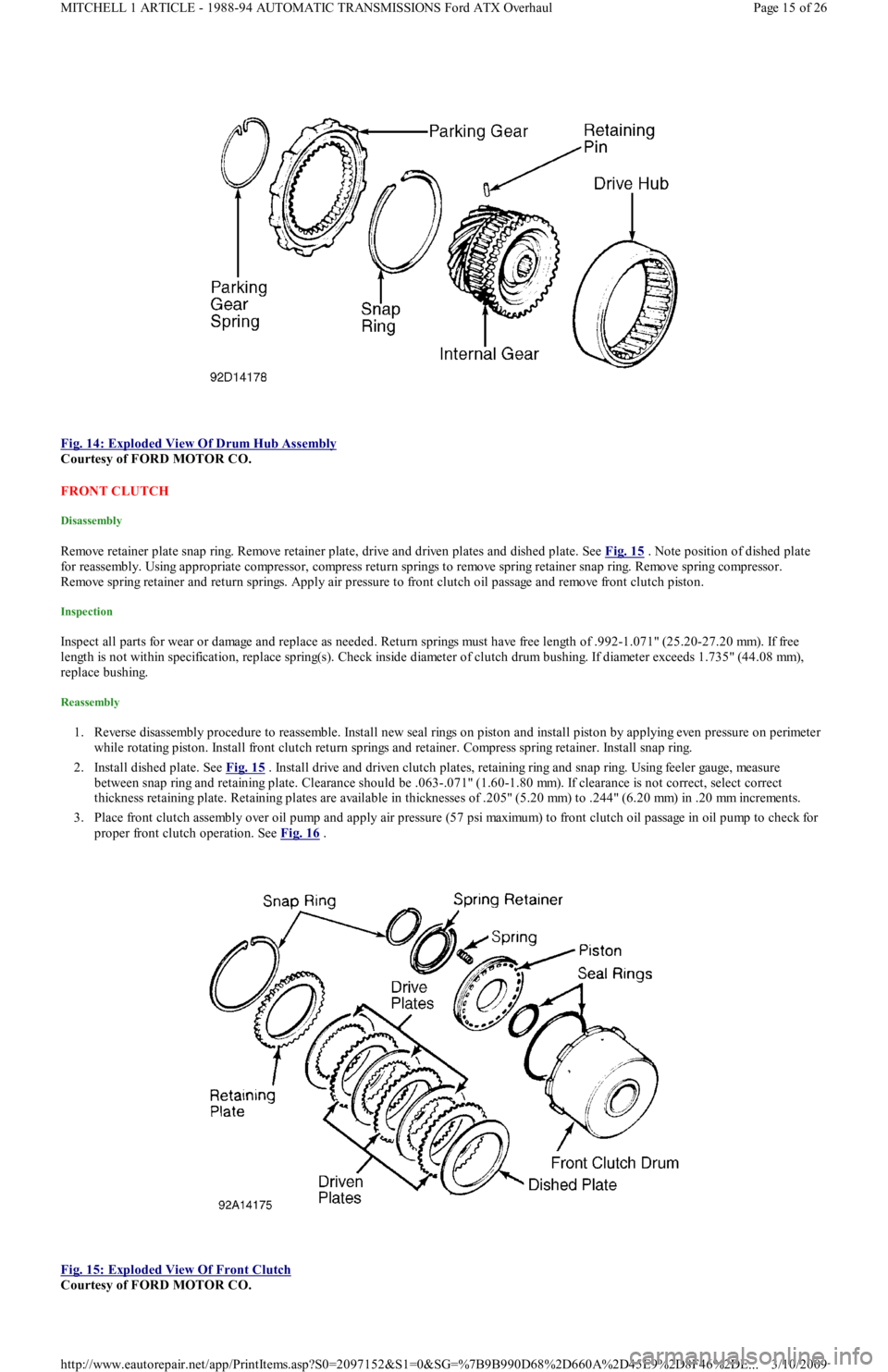
Fig. 14: Exploded View Of Drum Hub Assembly
Courtesy of FORD MOTOR CO.
FRONT CLUTCH
Disassembly
Remove retainer plate snap ring. Remove retainer plate, drive and driven plates and dished plate. See Fig. 15 . Note position of dished plate
for reassembly. Using appropriate compressor, compress return springs to remove spring retainer snap ring. Remove spring compressor.
Remove spring retainer and return springs. Apply air pressure to front clutch oil passage and remove front clutch piston.
Inspection
Inspect all parts for wear or damage and replace as needed. Return springs must have free length of .992-1.071" (25.20-27.20 mm). If free
length is not within specification, replace spring(s). Check inside diameter of clutch drum bushing. If diameter exceeds 1.735" (44.08 mm),
replace bushing.
Reassembly
1. Reverse disassembly procedure to reassemble. Install new seal rings on piston and install piston by applying even pressure on perimeter
while rotating piston. Install front clutch return springs and retainer. Compress spring retainer. Install snap ring.
2. Install dished plate. See Fig. 15
. Install drive and driven clutch plates, retaining ring and snap ring. Using feeler gauge, measure
between snap ring and retaining plate. Clearance should be .063-.071" (1.60-1.80 mm). If clearance is not correct, select correct
thickness retaining plate. Retaining plates are available in thicknesses of .205" (5.20 mm) to .244" (6.20 mm) in .20 mm increments.
3. Place front clutch assembly over oil pump and apply air pressure (57 psi maximum) to front clutch oil passage in oil pump to check for
proper front clutch operation. See Fig. 16
.
Fig. 15: Exploded View Of Front Clutch
Courtesy of FORD MOTOR CO.
Page 15 of 26 MITCHELL 1 ARTICLE - 1988-94 AUTOMATIC TRANSMISSIONS Ford ATX Overhaul
3/10/2009 http://www.eautorepair.net/app/PrintItems.asp?S0=2097152&S1=0&SG=%7B9B990D68%2D660A%2D45E9%2D8F46%2DE
...
Page 424 of 454
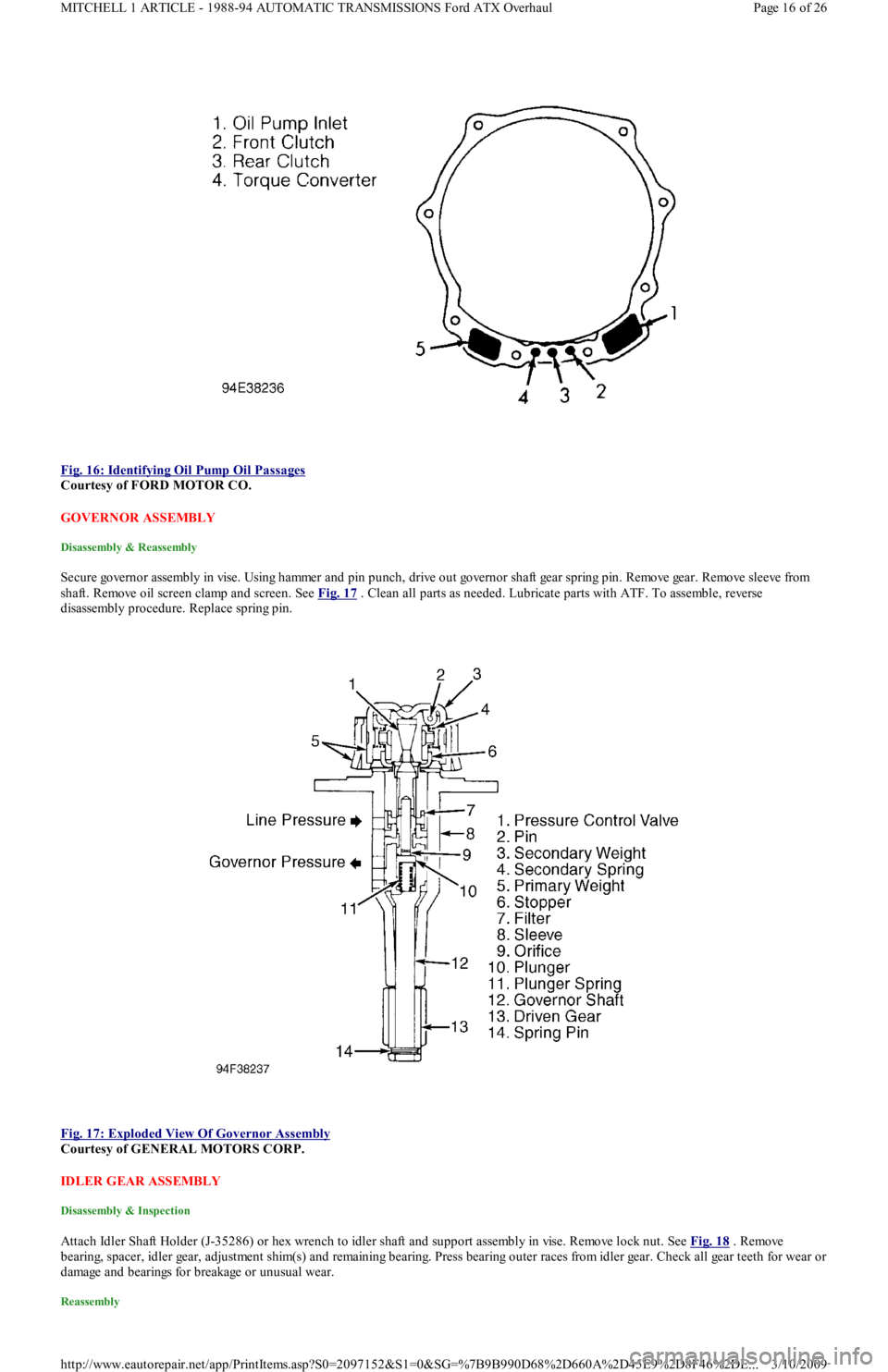
Fig. 16: Identifying Oil Pump Oil Passages
Courtesy of FORD MOTOR CO.
GOVERNOR ASSEMBLY
Disassembly & Reassembly
S e c u r e go ve r n o r a sse mb l y in vise . Usin g h a mme r a n d p in p u n c h , d r ive o u t go ve r n o r sh a ft ge a r sp r in g p in . R e mo ve ge a r . R e mo ve sl eeve from
shaft. Remove oil screen clamp and screen. See Fig. 17
. Clean all parts as needed. Lubricate parts with ATF. To assemble, reverse
disassembly procedure. Replace spring pin.
Fig. 17: Exploded View Of Governor Assembly
Courtesy of GENERAL MOTORS CORP.
IDLER GEAR ASSEMBLY
Disassembly & Inspection
Attach Idler Shaft Holder (J-35286) or hex wrench to idler shaft and support assembly in vise. Remove lock nut. See Fig. 18 . Remove
bearing, spacer, idler gear, adjustment shim(s) and remaining bearing. Press bearing outer races from idler gear. Check all gear teeth for wear or
damage and bearings for breakage or unusual wear.
Reassembly
Page 16 of 26 MITCHELL 1 ARTICLE - 1988-94 AUTOMATIC TRANSMISSIONS Ford ATX Overhaul
3/10/2009 http://www.eautorepair.net/app/PrintItems.asp?S0=2097152&S1=0&SG=%7B9B990D68%2D660A%2D45E9%2D8F46%2DE
...
Page 425 of 454
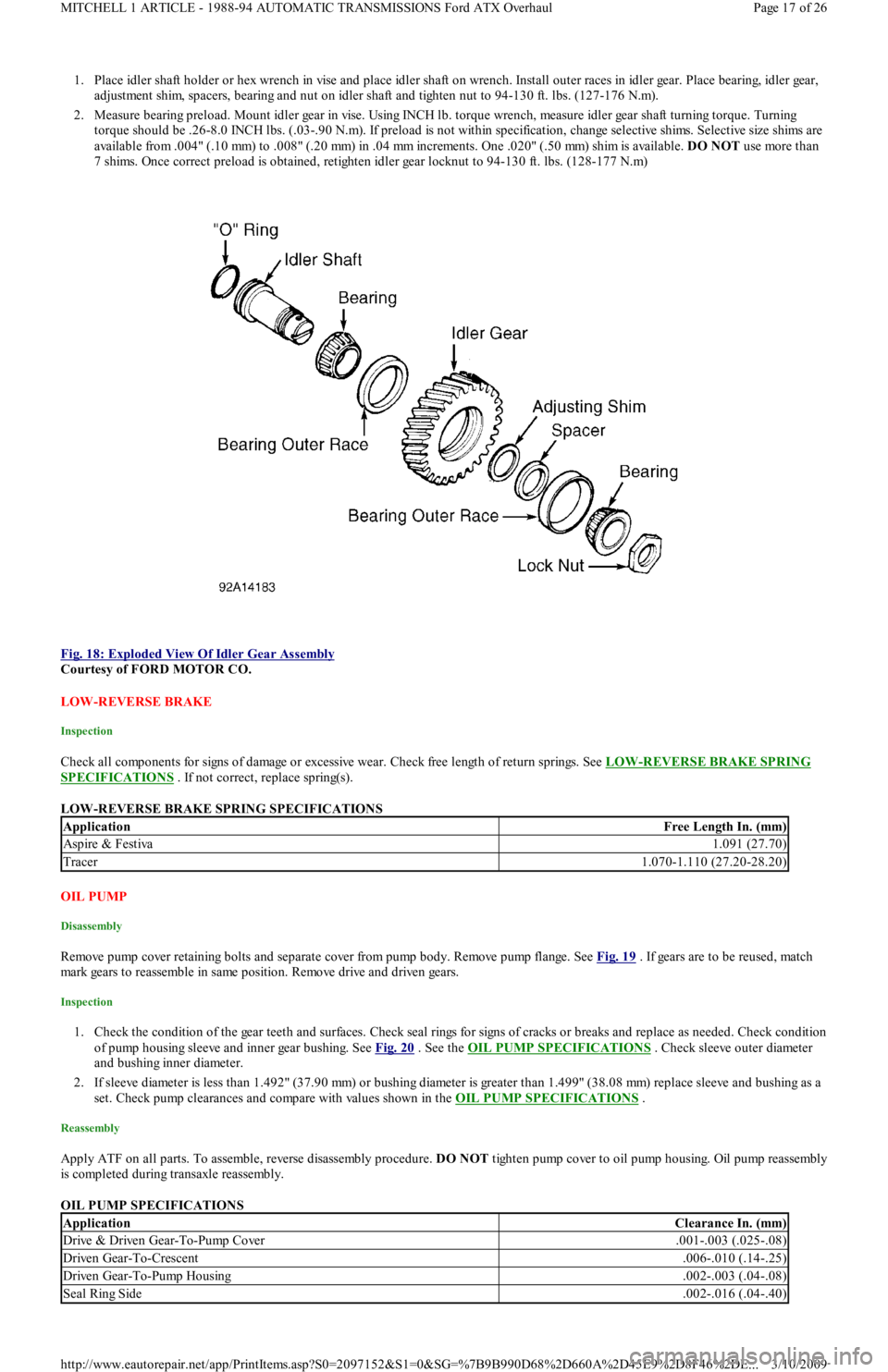
1. Place idler shaft holder or hex wrench in vise and place idler shaft on wrench. Install outer races in idler gear. Place bearing, idler gear,
adjustment shim, spacers, bearing and nut on idler shaft and tighten nut to 94-130 ft. lbs. (127-176 N.m).
2. Measure bearing preload. Mount idler gear in vise. Using INCH lb. torque wrench, measure idler gear shaft turning torque. Turning
torque should be .26-8.0 INCH lbs. (.03-.90 N.m). If preload is not within specification, change selective shims. Selective size shims are
available from .004" (.10 mm) to .008" (.20 mm) in .04 mm increments. One .020" (.50 mm) shim is available. DO NOT use more than
7 shims. Once correct preload is obtained, retighten idler gear locknut to 94-130 ft. lbs. (128-177 N.m)
Fig. 18: Exploded View Of Idler Gear Assembly
Courtesy of FORD MOTOR CO.
LOW-REVERSE BRAKE
Inspection
Check all components for signs of damage or excessive wear. Check free length of return springs. See LOW-REVERSE BRAKE SPRING
SPECIFICATIONS . If not correct, replace spring(s).
LOW-REVERSE BRAKE SPRING SPECIFICATIONS
OIL PUMP
Disassembly
Remove pump cover retaining bolts and separate cover from pump body. Remove pump flange. See Fig. 19 . If gears are to be reused, match
mark gears to reassemble in same position. Remove drive and driven gears.
Inspection
1. Check the condition of the gear teeth and surfaces. Check seal rings for signs of cracks or breaks and replace as needed. Check condition
of pump housing sleeve and inner gear bushing. See Fig. 20
. See the OIL PUMP SPECIFICATIONS . Check sleeve outer diameter
and bushing inner diameter.
2. If sleeve diameter is less than 1.492" (37.90 mm) or bushing diameter is greater than 1.499" (38.08 mm) replace sleeve and bushing as a
set. Check pump clearances and compare with values shown in the OIL PUMP SPECIFICATIONS
.
Reassembly
Apply ATF on all parts. To assemble, reverse disassembly procedure. DO NOTtighten pump cover to oil pump housing. Oil pump reassembly
is completed during transaxle reassembly.
OIL PUMP SPECIFICATIONS
ApplicationFree Length In. (mm)
Aspire & Festiva1.091 (27.70)
Tracer1.070-1.110 (27.20-28.20)
ApplicationClearance In. (mm)
Drive & Driven Gear-To-Pump Cover.001-.003 (.025-.08)
Driven Gear-To-Crescent.006-.010 (.14-.25)
Driven Gear-To-Pump Housing.002-.003 (.04-.08)
Seal Ring Side.002-.016 (.04-.40)
Page 17 of 26 MITCHELL 1 ARTICLE - 1988-94 AUTOMATIC TRANSMISSIONS Ford ATX Overhaul
3/10/2009 http://www.eautorepair.net/app/PrintItems.asp?S0=2097152&S1=0&SG=%7B9B990D68%2D660A%2D45E9%2D8F46%2DE
...
Page 426 of 454
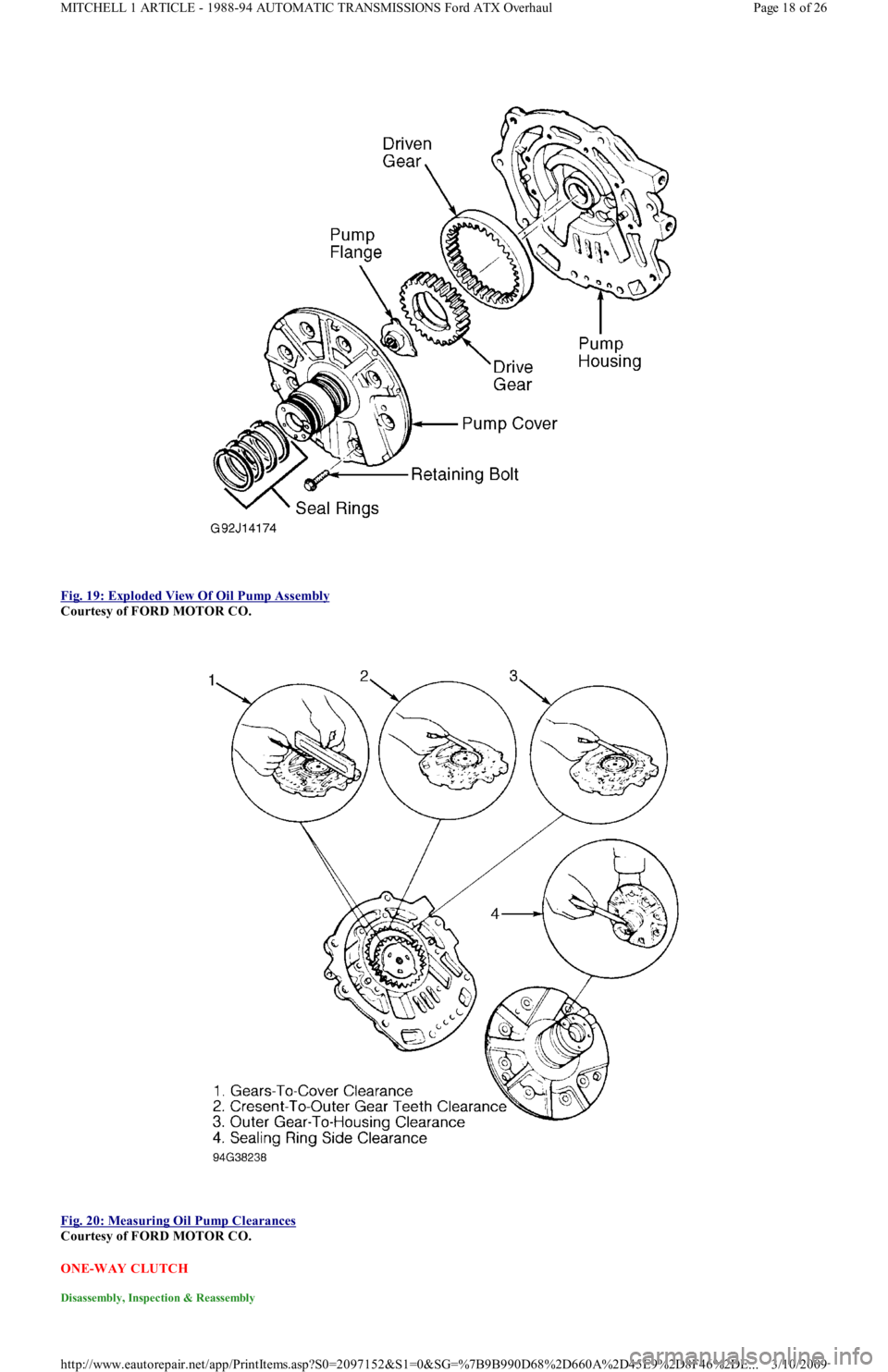
Fig. 19: Exploded View Of Oil Pump Assembly
Courtesy of FORD MOTOR CO.
Fig. 20: Measuring Oil Pump Clearances
Courtesy of FORD MOTOR CO.
ONE-WAY CLUTCH
Disassembly, Inspection & Reassembly
Page 18 of 26 MITCHELL 1 ARTICLE - 1988-94 AUTOMATIC TRANSMISSIONS Ford ATX Overhaul
3/10/2009 http://www.eautorepair.net/app/PrintItems.asp?S0=2097152&S1=0&SG=%7B9B990D68%2D660A%2D45E9%2D8F46%2DE
...
Page 427 of 454
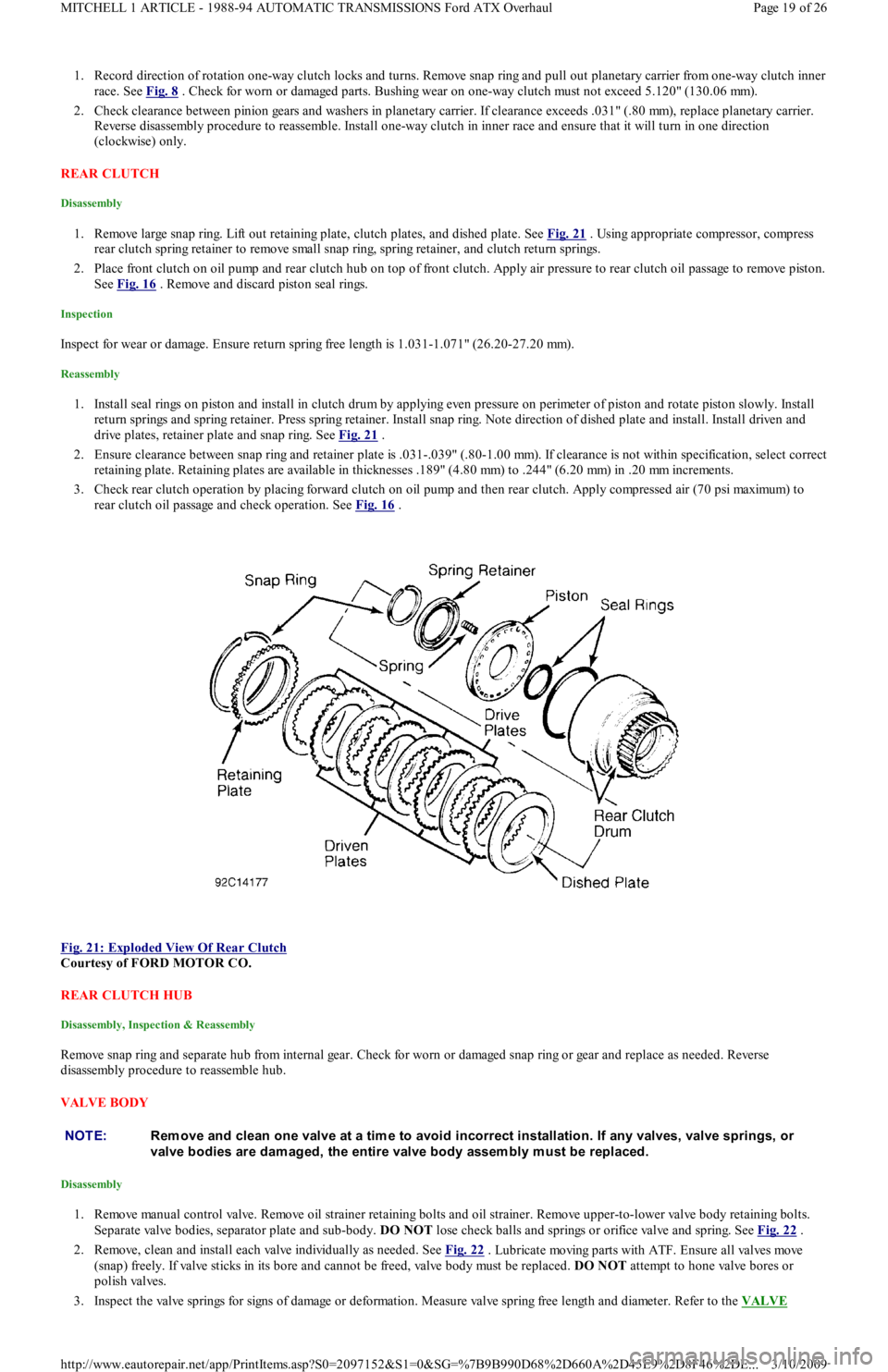
1. Record direction of rotation one-way clutch locks and turns. Remove snap ring and pull out planetary carrier from one-way clutch inner
race. See Fig. 8
. Check for worn or damaged parts. Bushing wear on one-way clutch must not exceed 5.120" (130.06 mm).
2. Check clearance between pinion gears and washers in planetary carrier. If clearance exceeds .031" (.80 mm), replace planetary carrier.
Reverse disassembly procedure to reassemble. Install one-way clutch in inner race and ensure that it will turn in one direction
(clockwise) only.
REAR CLUTCH
Disassembly
1. Remove large snap ring. Lift out retaining plate, clutch plates, and dished plate. See Fig. 21 . Using appropriate compressor, compress
rear clutch spring retainer to remove small snap ring, spring retainer, and clutch return springs.
2. Place front clutch on oil pump and rear clutch hub on top of front clutch. Apply air pressure to rear clutch oil passage to remove piston.
See Fig. 16
. Remove and discard piston seal rings.
Inspection
Inspect for wear or damage. Ensure return spring free length is 1.031-1.071" (26.20-27.20 mm).
Reassembly
1. Install seal rings on piston and install in clutch drum by applying even pressure on perimeter of piston and rotate piston slowly. Install
return springs and spring retainer. Press spring retainer. Install snap ring. Note direction of dished plate and install. Install driven and
drive plates, retainer plate and snap ring. See Fig. 21
.
2. Ensure clearance between snap ring and retainer plate is .031-.039" (.80-1.00 mm). If clearance is not within specification, select correct
retaining plate. Retaining plates are available in thicknesses .189" (4.80 mm) to .244" (6.20 mm) in .20 mm increments.
3. Check rear clutch operation by placing forward clutch on oil pump and then rear clutch. Apply compressed air (70 psi maximum) to
rear clutch oil passage and check operation. See Fig. 16
.
Fig. 21: Exploded View Of Rear Clutch
Courtesy of FORD MOTOR CO.
REAR CLUTCH HUB
Disassembly, Inspection & Reassembly
Remove snap ring and separate hub from internal gear. Check for worn or damaged snap ring or gear and replace as needed. Reverse
disassembly procedure to reassemble hub.
VALVE BODY
Disassembly
1. Remove manual control valve. Remove oil strainer retaining bolts and oil strainer. Remove upper-to-lower valve body retaining bolts.
Separate valve bodies, separator plate and sub-body. DO NOT lose check balls and springs or orifice valve and spring. See Fig. 22
.
2. Remove, clean and install each valve individually as needed. See Fig. 22
. Lubricate moving parts with ATF. Ensure all valves move
(snap) freely. If valve sticks in its bore and cannot be freed, valve body must be replaced. DO NOT attempt to hone valve bores or
polish valves.
3. Inspect the valve springs for signs of damage or deformation. Measure valve spring free length and diameter. Refer to the VALVE
NOTE:Rem ove and clean one valve at a tim e to avoid incorrect installation. If any valves, valve springs, or
valve bodies are dam aged, the entire valve body assem bly m ust be replaced.
Page 19 of 26 MITCHELL 1 ARTICLE - 1988-94 AUTOMATIC TRANSMISSIONS Ford ATX Overhaul
3/10/2009 http://www.eautorepair.net/app/PrintItems.asp?S0=2097152&S1=0&SG=%7B9B990D68%2D660A%2D45E9%2D8F46%2DE
...
Page 428 of 454
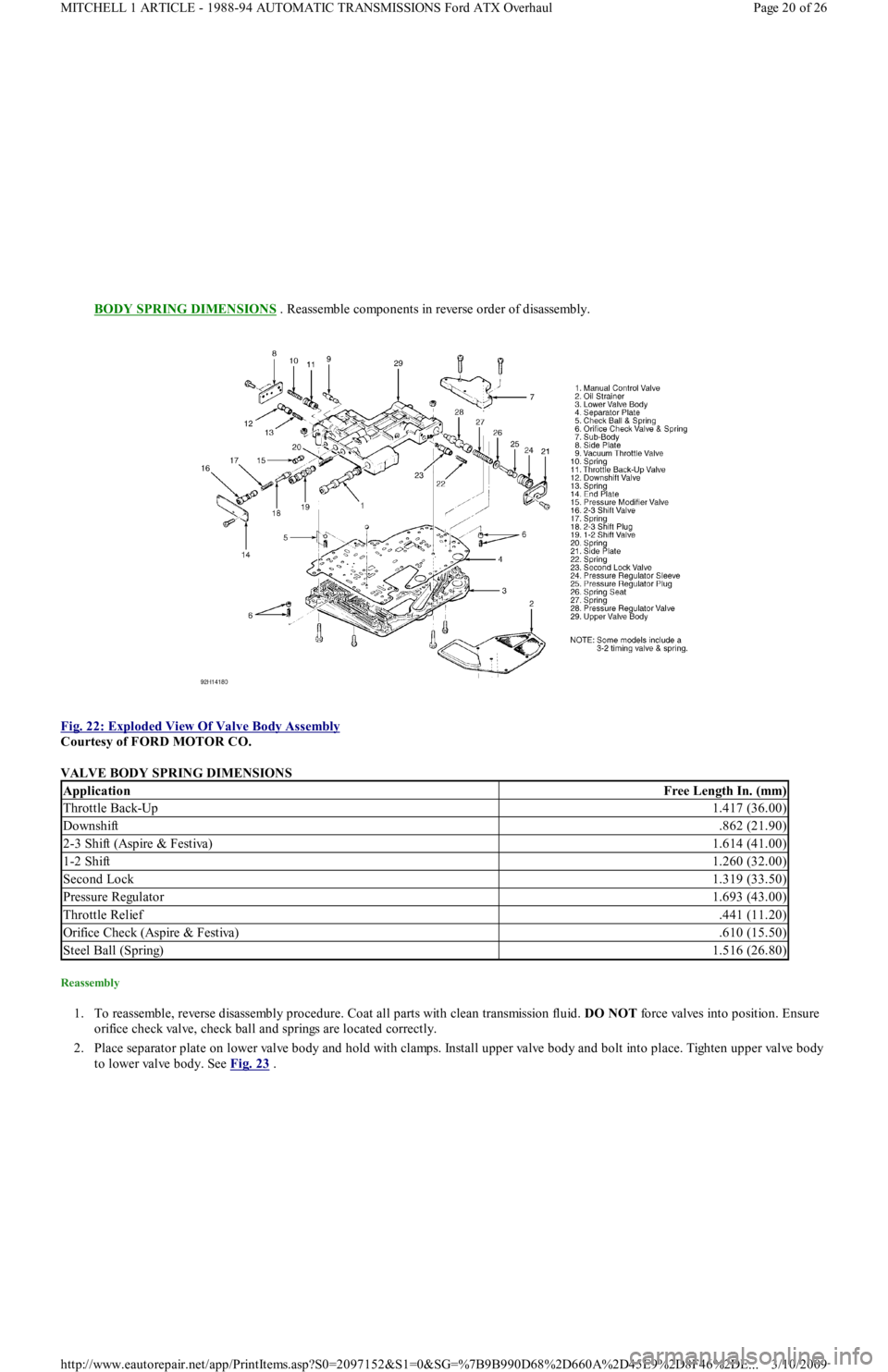
BODY SPRING DIMENSIONS . Reassemble components in reverse order of disassembly.
Fig. 22: Exploded View Of Valve Body Assembly
Courtesy of FORD MOTOR CO.
VALVE BODY SPRING DIMENSIONS
Reassembly
1. To reassemble, reverse disassembly procedure. Coat all parts with clean transmission fluid. DO NOT force valves into position. Ensure
orifice check valve, check ball and springs are located correctly.
2. Place separator plate on lower valve body and hold with clamps. Install upper valve body and bolt into place. Tighten upper valve body
to lower valve body. See Fig. 23
.
ApplicationFree Length In. (mm)
Throttle Back-Up1.417 (36.00)
Downshift.862 (21.90)
2-3 Shift (Aspire & Festiva)1.614 (41.00)
1-2 Shift1.260 (32.00)
Second Lock1.319 (33.50)
Pressure Regulator1.693 (43.00)
Throttle Relief.441 (11.20)
Orifice Check (Aspire & Festiva).610 (15.50)
Steel Ball (Spring)1.516 (26.80)
Page 20 of 26 MITCHELL 1 ARTICLE - 1988-94 AUTOMATIC TRANSMISSIONS Ford ATX Overhaul
3/10/2009 http://www.eautorepair.net/app/PrintItems.asp?S0=2097152&S1=0&SG=%7B9B990D68%2D660A%2D45E9%2D8F46%2DE
...
Page 429 of 454
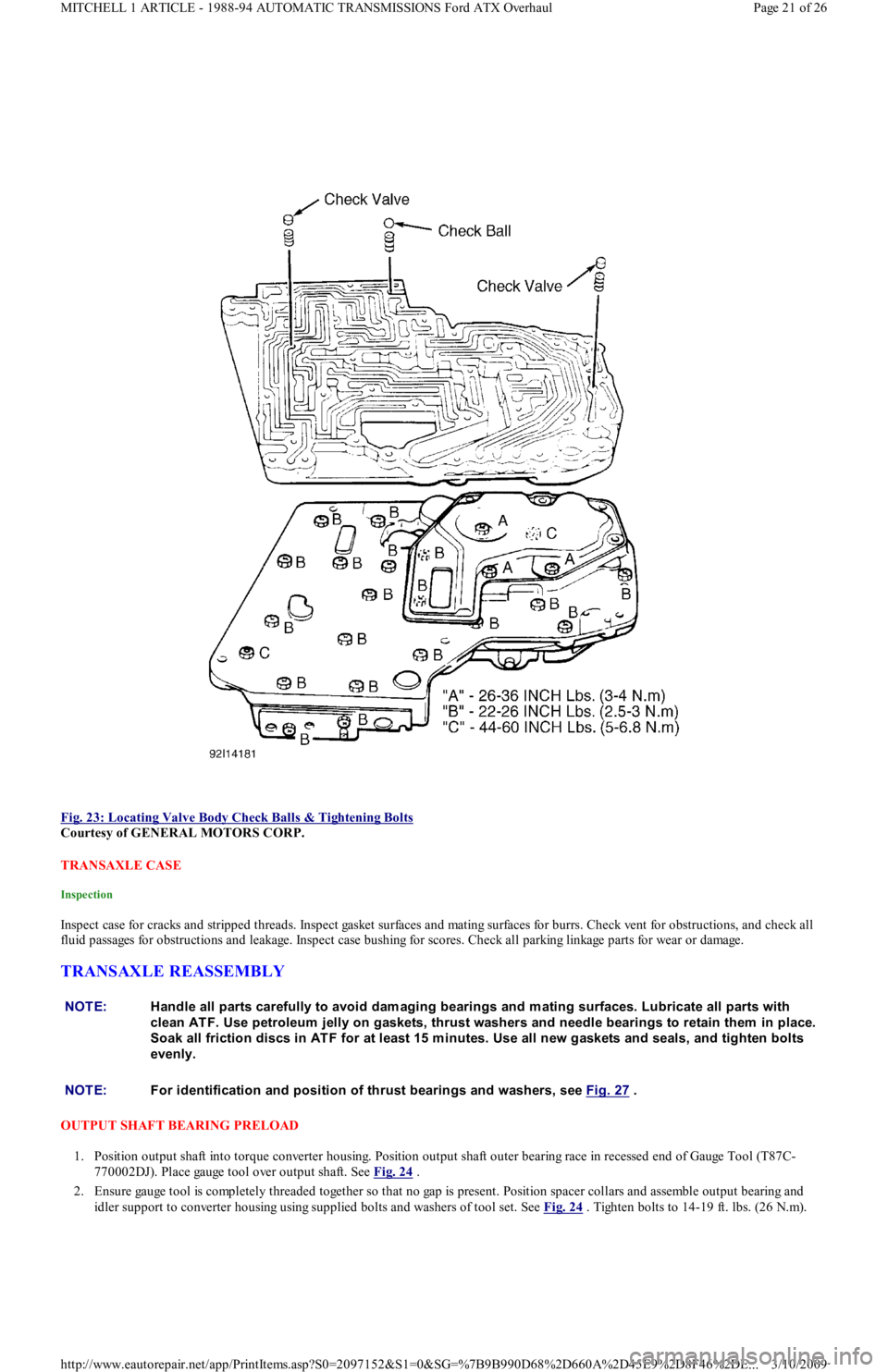
Fig. 23: Locating Valve Body Check Balls & Tightening Bolts
Courtesy of GENERAL MOTORS CORP.
TRANSAXLE CASE
Inspection
Inspect case for cracks and stripped threads. Inspect gasket surfaces and mating surfaces for burrs. Check vent for obstructions, and check all
fluid passages for obstructions and leakage. Inspect case bushing for scores. Check all parking linkage parts for wear or damage.
TRANSAXLE REASSEMBLY
OUTPUT SHAFT BEARING PRELOAD
1. Position output shaft into torque converter housing. Position output shaft outer bearing race in recessed end of Gauge Tool (T87C-
770002DJ). Place gauge tool over output shaft. See Fig. 24
.
2. Ensure gauge tool is completely threaded together so that no gap is present. Position spacer collars and assemble output bearing and
idler support to converter housing using supplied bolts and washers of tool set. See Fig. 24
. Tighten bolts to 14-19 ft. lbs. (26 N.m).
NOTE:Handle all parts carefully to avoid dam aging bearings and m ating surfaces. Lubricate all parts with
clean AT F. Use petroleum jelly on gaskets, thrust washers and needle bearings to retain them in place.
Soak all friction discs in AT F for at least 15 m inutes. Use all new gaskets and seals, and tighten bolts
evenly.
NOTE:For identification and position of thrust bearings and washers, see Fig. 27
.
Page 21 of 26 MITCHELL 1 ARTICLE - 1988-94 AUTOMATIC TRANSMISSIONS Ford ATX Overhaul
3/10/2009 http://www.eautorepair.net/app/PrintItems.asp?S0=2097152&S1=0&SG=%7B9B990D68%2D660A%2D45E9%2D8F46%2DE
...
Page 430 of 454
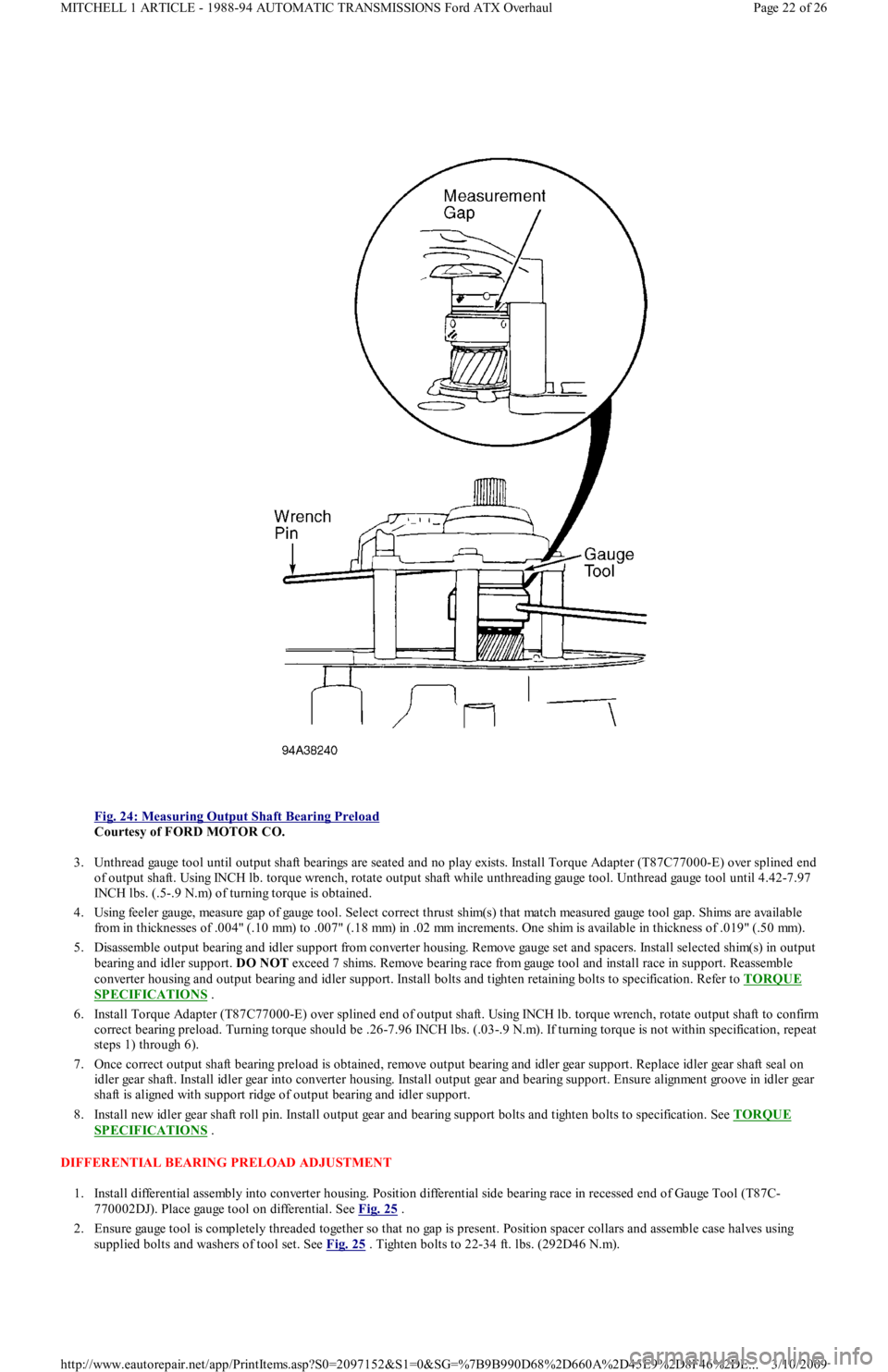
Fig. 24: Measuring Output Shaft Bearing Preload
Courtesy of FORD MOTOR CO.
3. Unthread gauge tool until output shaft bearings are seated and no play exists. Install Torque Adapter (T87C77000-E) over splined end
of output shaft. Using INCH lb. torque wrench, rotate output shaft while unthreading gauge tool. Unthread gauge tool until 4.42-7.97
INCH lbs. (.5-.9 N.m) of turning torque is obtained.
4. Using feeler gauge, measure gap of gauge tool. Select correct thrust shim(s) that match measured gauge tool gap. Shims are available
from in thicknesses of .004" (.10 mm) to .007" (.18 mm) in .02 mm increments. One shim is available in thickness of .019" (.50 mm).
5. Disassemble output bearing and idler support from converter housing. Remove gauge set and spacers. Install selected shim(s) in output
bearing and idler support. DO NOT exceed 7 shims. Remove bearing race from gauge tool and install race in support. Reassemble
converter housing and output bearing and idler support. Install bolts and tighten retaining bolts to specification. Refer to TORQUE
SPECIFICATIONS .
6. Install Torque Adapter (T87C77000-E) over splined end of output shaft. Using INCH lb. torque wrench, rotate output shaft to confirm
correct bearing preload. Turning torque should be .26-7.96 INCH lbs. (.03-.9 N.m). If turning torque is not within specification, repeat
steps 1) through 6).
7. Once correct output shaft bearing preload is obtained, remove output bearing and idler gear support. Replace idler gear shaft seal on
idler gear shaft. Install idler gear into converter housing. Install output gear and bearing support. Ensure alignment groove in idler gear
shaft is aligned with support ridge of output bearing and idler support.
8. Install new idler gear shaft roll pin. Install output gear and bearing support bolts and tighten bolts to specification. See TORQUE
SPECIFICATIONS .
DIFFERENTIAL BEARING PRELOAD ADJUSTMENT
1. Install differential assembly into converter housing. Position differential side bearing race in recessed end of Gauge Tool (T87C-
770002DJ). Place gauge tool on differential. See Fig. 25
.
2. Ensure gauge tool is completely threaded together so that no gap is present. Position spacer collars and assemble case halves using
supplied bolts and washers of tool set. See Fig. 25
. Tighten bolts to 22-34 ft. lbs. (292D46 N.m).
Page 22 of 26 MITCHELL 1 ARTICLE - 1988-94 AUTOMATIC TRANSMISSIONS Ford ATX Overhaul
3/10/2009 http://www.eautorepair.net/app/PrintItems.asp?S0=2097152&S1=0&SG=%7B9B990D68%2D660A%2D45E9%2D8F46%2DE
...