engine HONDA CIVIC 2002 7.G Repair Manual
[x] Cancel search | Manufacturer: HONDA, Model Year: 2002, Model line: CIVIC, Model: HONDA CIVIC 2002 7.GPages: 1139, PDF Size: 28.19 MB
Page 150 of 1139
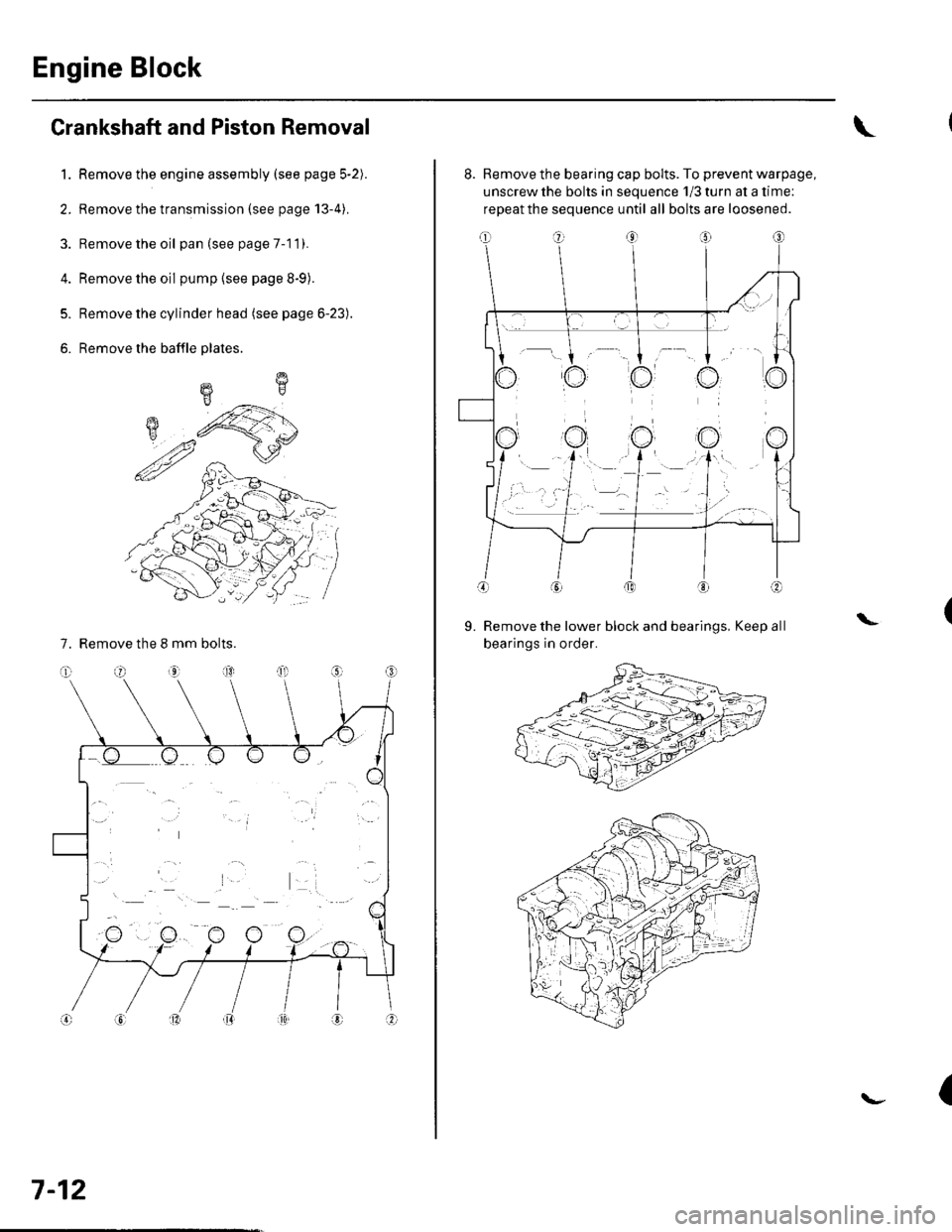
Engine Block
Crankshaft and Piston Removal
1. Remove the engine assembly (see page 5-2).
2. Remove the transmission (see page 13-4).
3. Remove the oil pan (see page 7-1 1).
4. Remove the oil pump {see page 8-9).
5. Remove the cylinder head (see page 6-23).
6. Remove the baffle plates.
7. Remove the 8 mm bolts.
E
7-12
8. Remove the bearing cap bolts. To prevent warpage,
unscrew the bolts in sequence 1/3 turn at a time:
repeat the sequence until all bolts are loosened.
Remove the lower block and bearings, Keep all
bearings in order.
\L
(
Page 151 of 1139
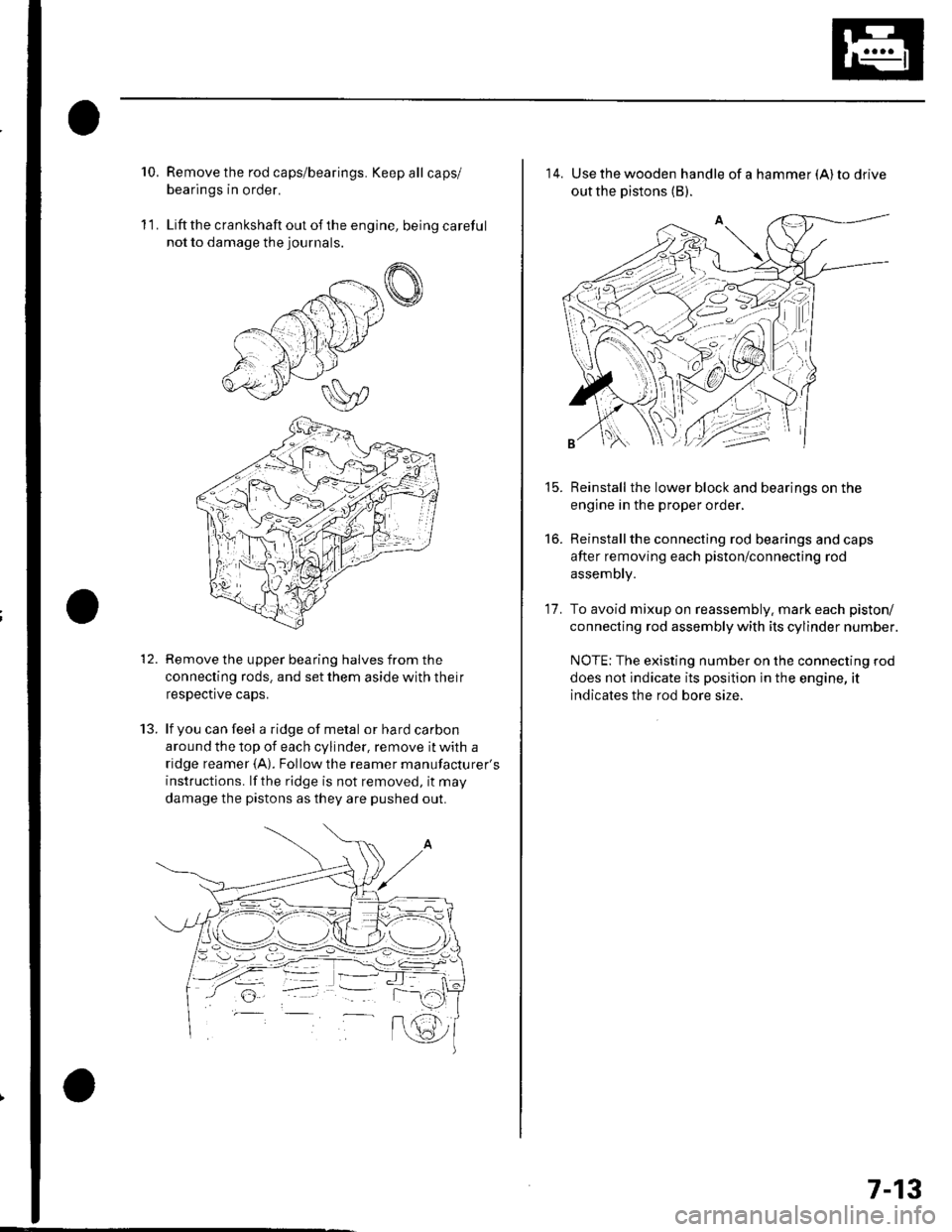
10.Remove the rod caps/bearings. Keep all caps/
bearings in order.
Liftthe crankshaft out ofthe engine, being careful
not to damage the journals.
Remove the upper bearing halves from the
connecting rods. and set them aside with their
respective caps.
lf you can feel a ridge of metal or hard carbon
around the top of each cylinder, remove it with a
ridge reamer {A). Followthe reamer manufacturer's
instructions. lf the ridge is not removed, it may
damage the pistons as they are pushed out.
11.
t.J.
14. Use the wooden handle of a hammer (A) to drive
out the pistons (B).
Reinstall the lower block and bearings on the
engine in the proper order,
Reinstallthe connecting rod bearings and caps
after removing each piston/connecting rod
assembly.
To avoid mixup on reassembly. mark each piston/
connecting rod assembly with its cylinder number.
NOTE: The existing number on the connecting rod
does not indicate its position in the engine, it
indicates the rod bore size.
15.
to.
17.
7-13
Page 152 of 1139
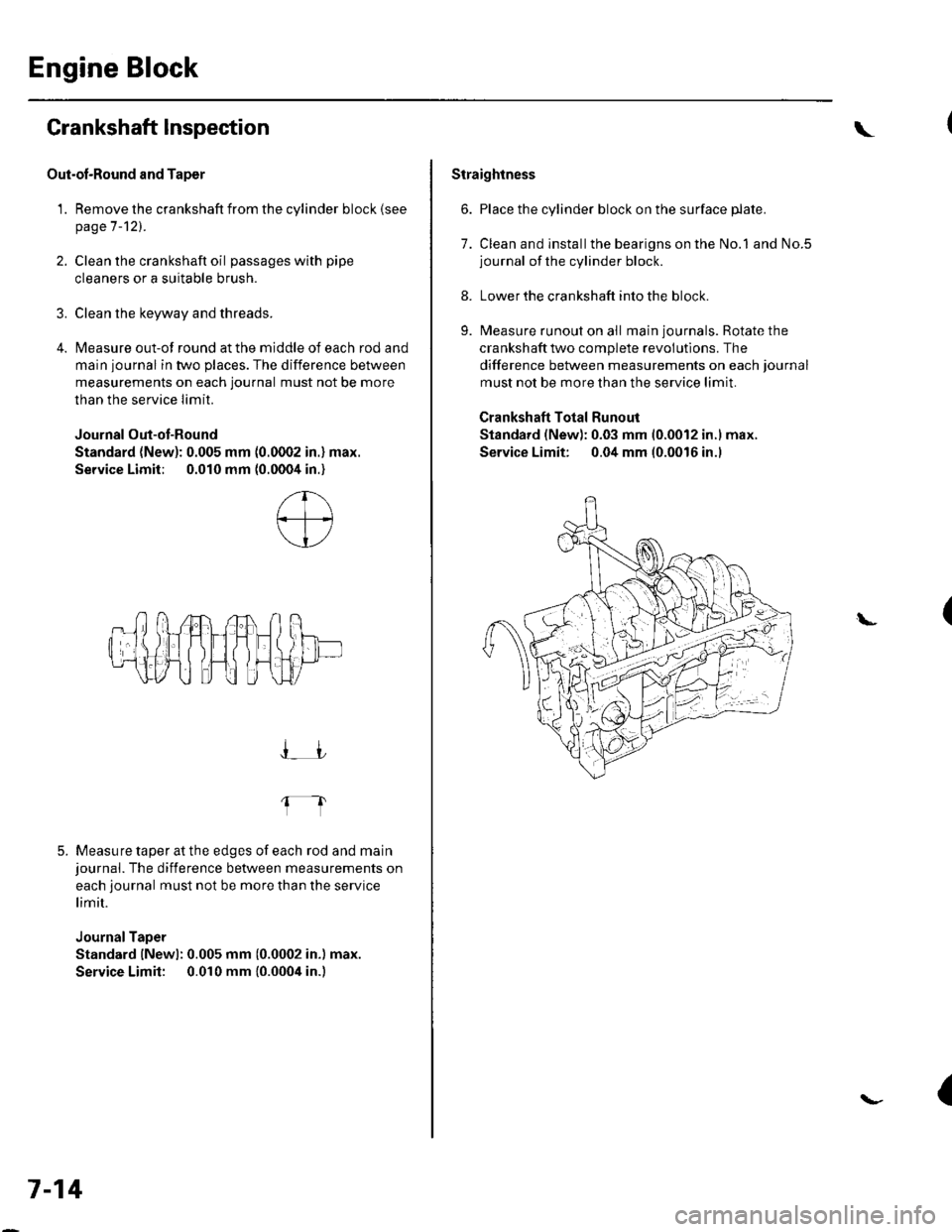
Engine Block
Crankshaft lnspection
Out-ol-Round and Taper
1. Remove the crankshaft from the cylinder block (see
page 7-121.
2. Clean the crankshaft oil passages with pipe
cleaners or a suitable brush.
3. Clean the keyway and threads.
4. Measure out-of round at the middle of each rod and
main journal in two places. The difference between
measurements on each journal must not be more
than the service Iimit.
Journal Out-ot-Round
Standard (New): 0.005 mm (0.0002 in.) max.
Service Limit; 0.010 mm (0.0004 in.)
5. Measure taper at the edges of each rod and mainjournal. The difference between measurements on
each journal must not be more than the service
limit.
JournalTaper
Standard lNewl: 0.005 mm (0.0002 in.) max.
Service Limit: 0.010 mm {0.0004 in.)
I_JJ
fl
7-14
\
Straightness
6. Place the cylinder block on the surface plate.
7. Clean and installthe bearigns on the No.1 and No.5journal of the cylinder block.
8. Lower the crankshaft into the block.
9. Measure runout on all main journals. Rotate the
crankshaft two complete revolutlons. The
difference between measurements on each journal
must not be more than the service limit.
Crankshaft Total Runout
Standard (New): 0.03 mm 10.0012 in.l max.
Service Limit: 0.04 mm (0.0016 in.l
(L
{
Page 154 of 1139
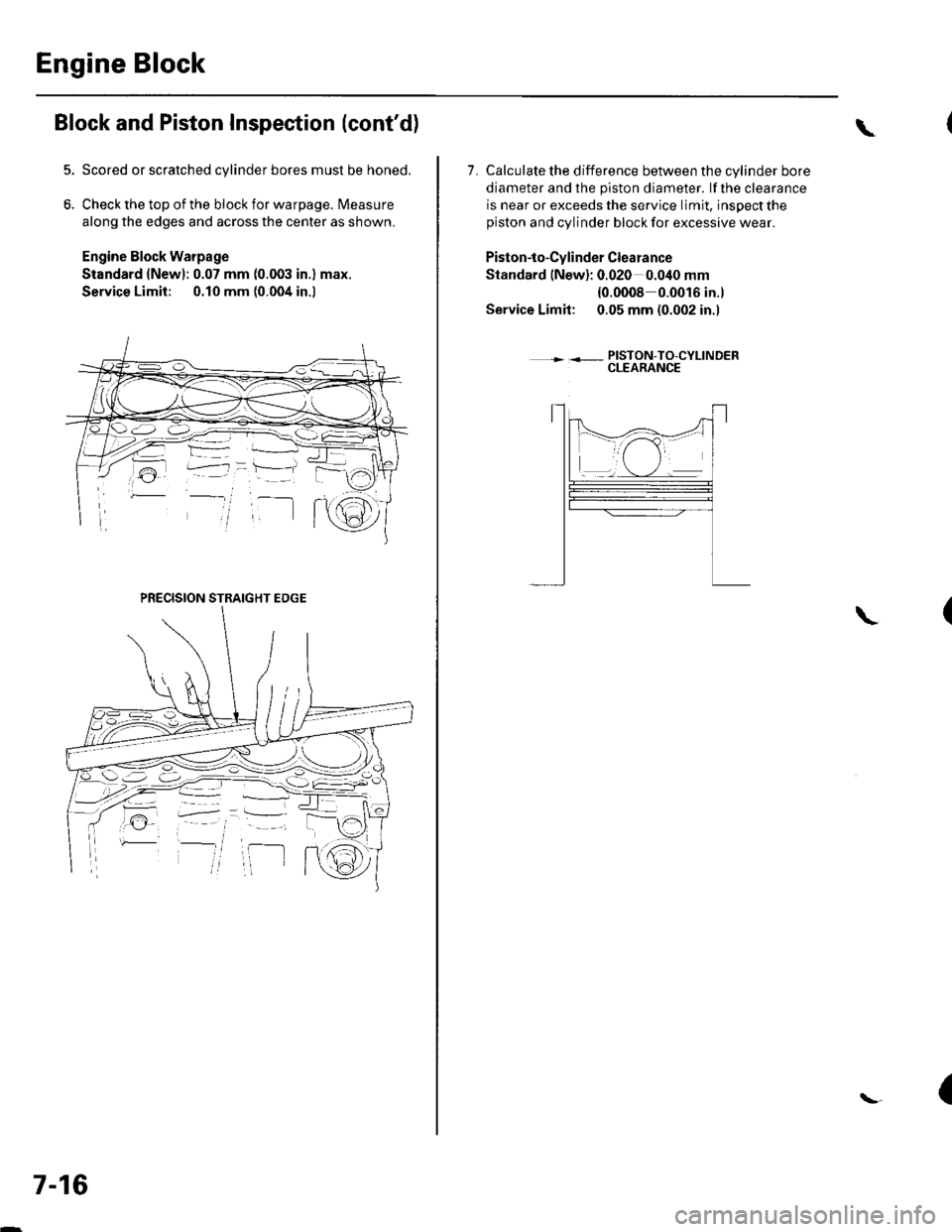
Engine Block
Block and Piston Inspection (cont'd)
Scored or scratched cylinder bores must be honed.
Check the top of the block for warpage. Measure
along the edges and across the center as shown.
Engine Block Warpage
Standard lNew): 0.07 mm (0.003 in.) max.
Service Limit: 0.10 mm (0.004 in.l
PRECISION STRAIGHT EDGE
7-16
\
7. Calculate the difference between the cylinder bore
diameter and the plston diameter. lf the clearance
is near or exceeds the service limit, inspect thepiston and cvlinder block for excessive wear.
Piston-to-Cylinder Clearance
Standard lNew): 0.020 0.040 mm
{0.0008 0.0016 in.)
Service Limit: 0.05 mm (0.002 in.l
++ PISTON-TO-CYLINDERCLEARANCE
\
(
Page 155 of 1139
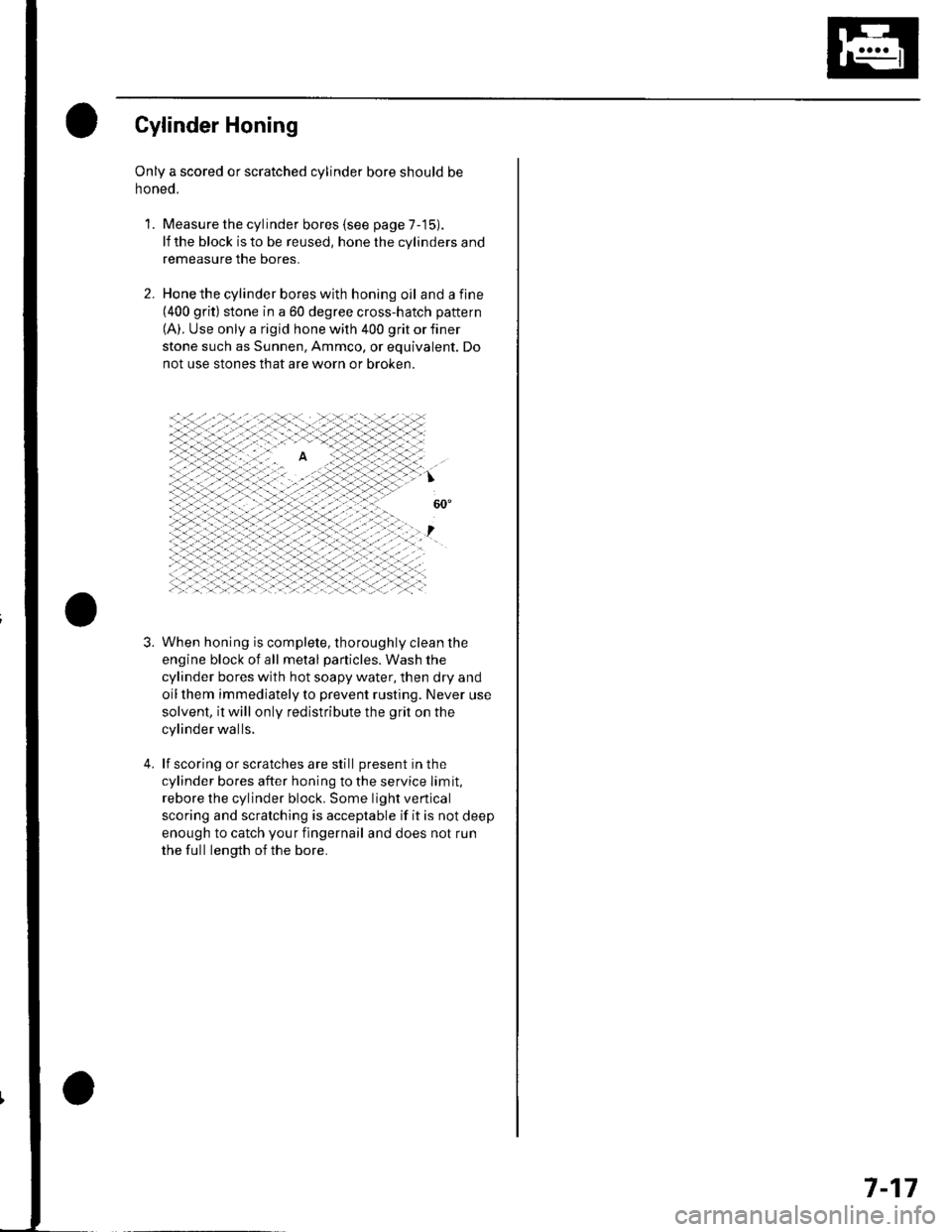
Cylinder Honing
Only a scored or scratched cylinder bore should be
noneo.
Measure the cylinder bores {see page 7-15).
lf the block is to be reused, hone the cylinders and
remeasure the bores.
Hone the cylinder bores with honing oil and a fine(400 grit) stone in a 60 degree cross-hatch pattern
(A). Use only a rigid hone with 400 grit or finer
stone such as Sunnen, Ammco, or equivalent. Do
not use stones that are worn or broken.
When honing is complete, thoroughly clean the
engine block of all metal particles. Wash the
cylinder bores with hot soapy water, then dry and
oil them immediately to prevent rusting. Never use
solvent, it will only redistribute the grit on the
cylinder walls.
lf scoring or scratches are still present in the
cylinder bores after honing to the service limit,
rebore the cylinder block. Some light vertical
scoring and scratching is acceptable if it is not deep
enough to catch your fingernail and does not run
the full length of the bore.
'L
3.
7-17
Page 156 of 1139
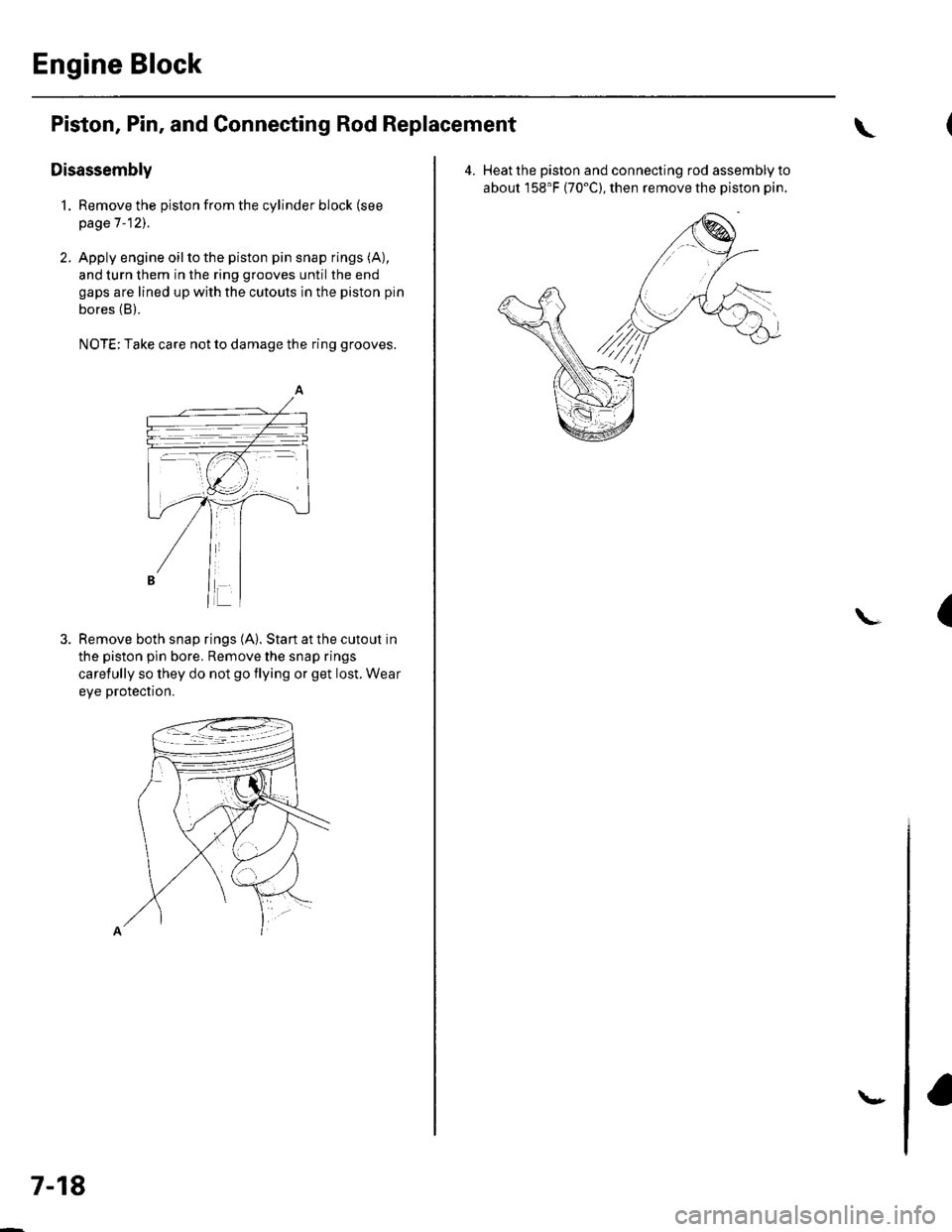
Engine Block
Piston, Pin, and Connecting Rod Replacement
Disassembly
1. Remove the piston from the cylinder block (see
page 7 -12).
2. Apply engine oilto the piston pin snap rings (A),
and turn them in the ring grooves until the end
gaps are lined up with the cutouts in the piston pin
bores (B).
NOTE; Take care not to damage the ring grooves.
Remove both snap rings (A). Start at the cutout in
the piston pin bore. Remove the snap rings
carefully so they do not go flying or get lost. Wear
eve protection.
7-18
\"
4.Heat the piston and connecting rod assembly to
about 158'F (70"C), then remove the piston pin.
(\
Page 158 of 1139
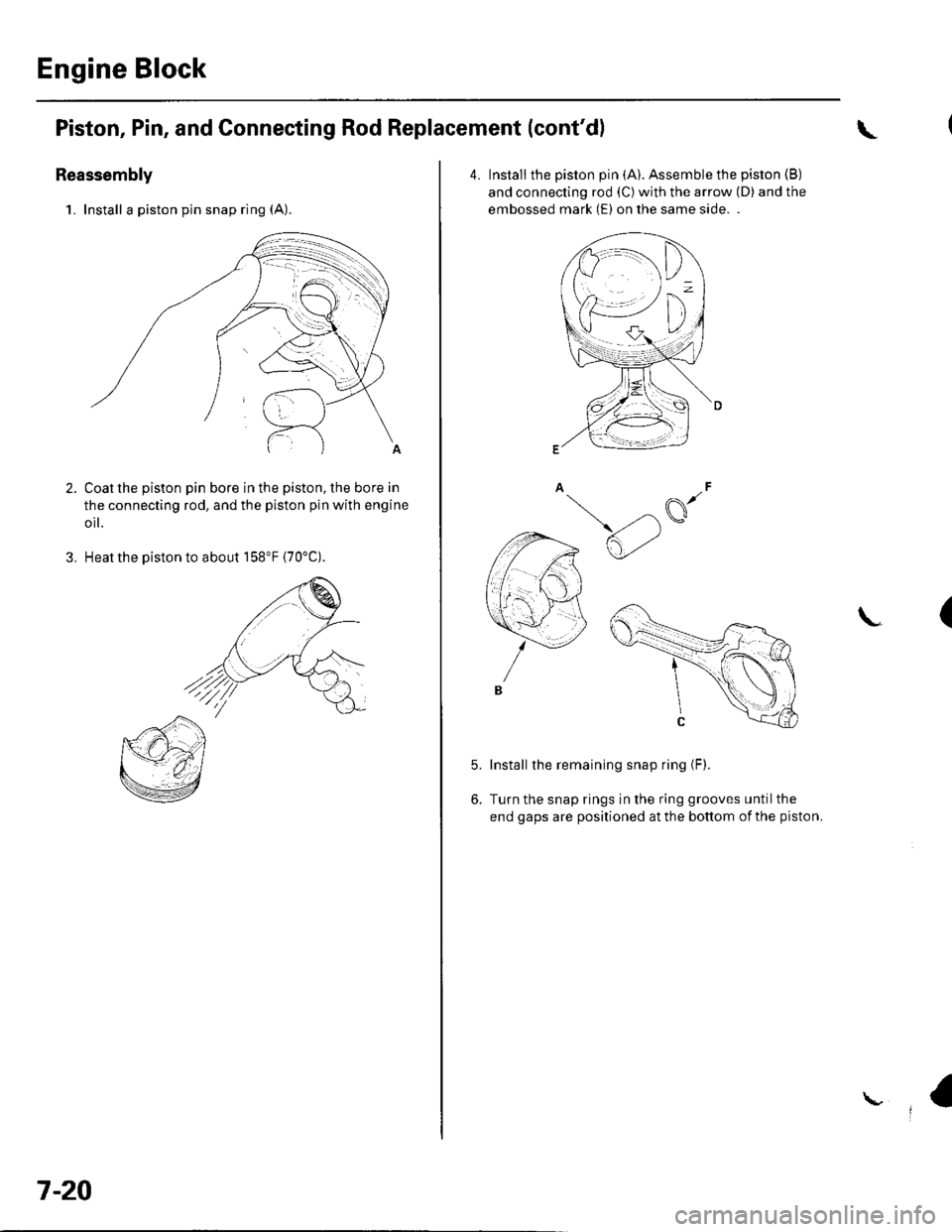
Engine Block
Piston, Pin, and Connecting Rod Replacement (cont'd)
Reassembly
1. Install a piston pin snap ring (A).
Coat the piston pin bore in the piston, the bore in
the connecting rod, and the piston pin with engine
oil.
Heat the piston to about 158"F (70'C).3.
7 -20
\
4. Install the piston pin (A). Assemble the piston (B)
and connecting rod (C) with the arrow (D) and the
embossed mark (E) on the same side. -
Install the remaining snap ring (F).
Turn the snap rings in the ring grooves untilthe
end gaps are positioned at the bottom of the piston.
(
5.
6.
I
Page 159 of 1139
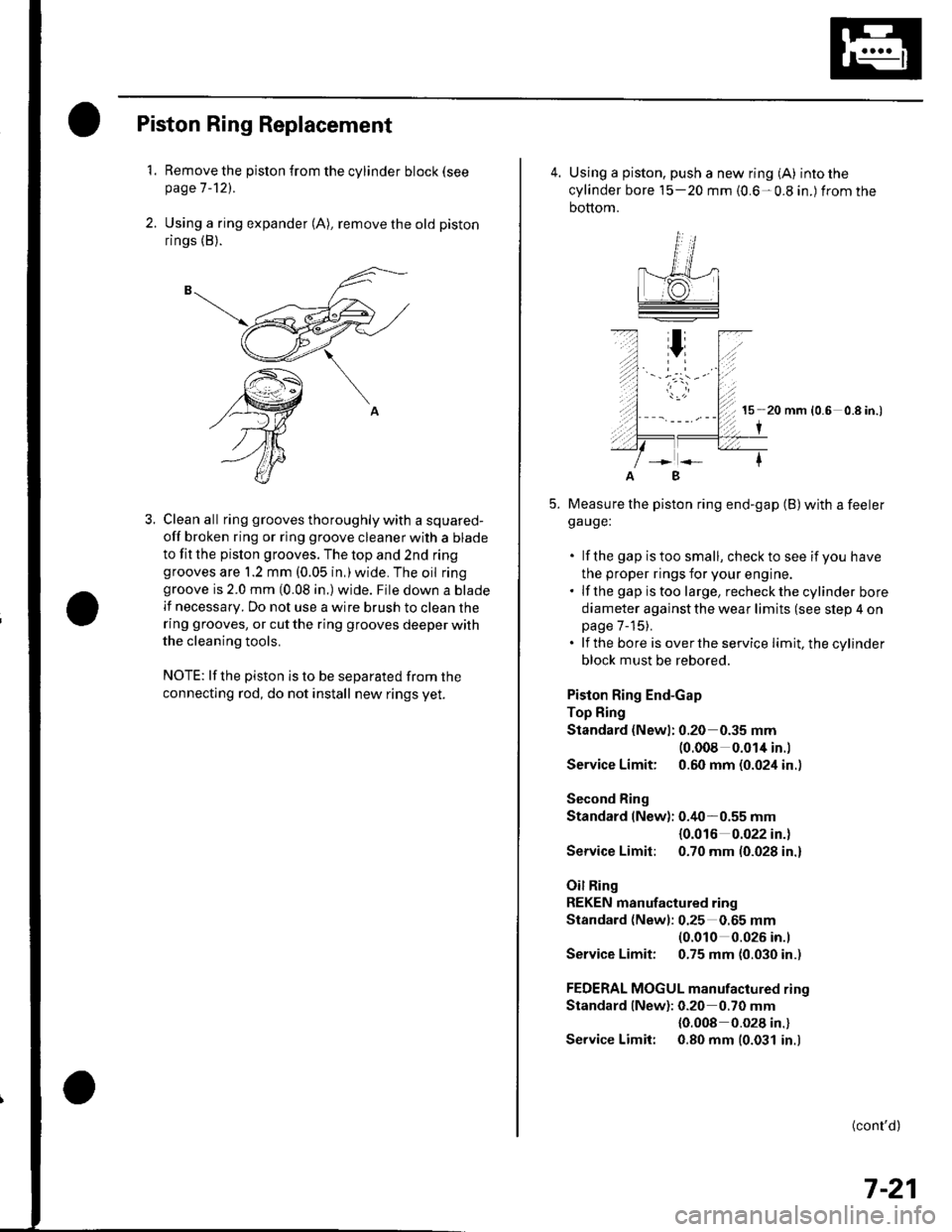
Piston Ring Replacement
1. Remove the piston {rom the cylinder block (see
page 7 -121.
2. Using a ring expander (A), remove the old piston
rings (B).
3. Clean all ring grooves thoroughly with a squared-
off broken ring or ring groove cleaner with a blade
to fit the pislon grooves. The top and 2nd ringgrooves are 1.2 mm (0.05 in,)wide. The oil ringgroove is 2.0 mm (0.08 in.) wide. File down a blade
lf necessary. Do not use a wire brush to clean the
ring grooves, or cut the ring grooves deeper with
the cleaning tools.
NOTE: lf the piston is to be separated from the
connecting rod, do not install new rings yet.
4. Using a piston, push a new ring (A) into the
cylinder bore 15-20 mm {0.6-0.8 in.) from the
bottom.
15 20 mm (0.6 0.8 in.)
I
Measure the piston ring end-gap (B) with a feelerga uge:
. lf the gap istoo small, checkto see if you have
the proper rings for your engine.. lf the gap istoo large, recheckthecylinder bore
diameter against the wear limits (see slep 4 onpage 7-15).. lf the bore is overthe service limit, the cylinder
block must be rebored.
Piston Ring End-Gap
Top Fing
Standard (Newl: 0.20 0.35 mm(0.008 0.014 in.l
Service Limit: 0.60 mm (0.024 in..
Second Ring
Standard (New): 0.40-0.55 mm
{0.016 0.022 in.)
Service Limit: 0.70 mm (0.028 in.)
Oil Ring
REKEN manufactured ring
Standard (Newl: 0.25 0.65 mm(0.010 0.026 in.l
Service Limit: 0.75 mm (0.030 in.)
FEDERAL MOGUL manufactured rino
Standard lNew): 0.20 0.70 mm
{0.008 0.028 in.}
Service Limit: 0.80 mm (0.031 in.)
B
(cont'd)
7-21
Page 160 of 1139
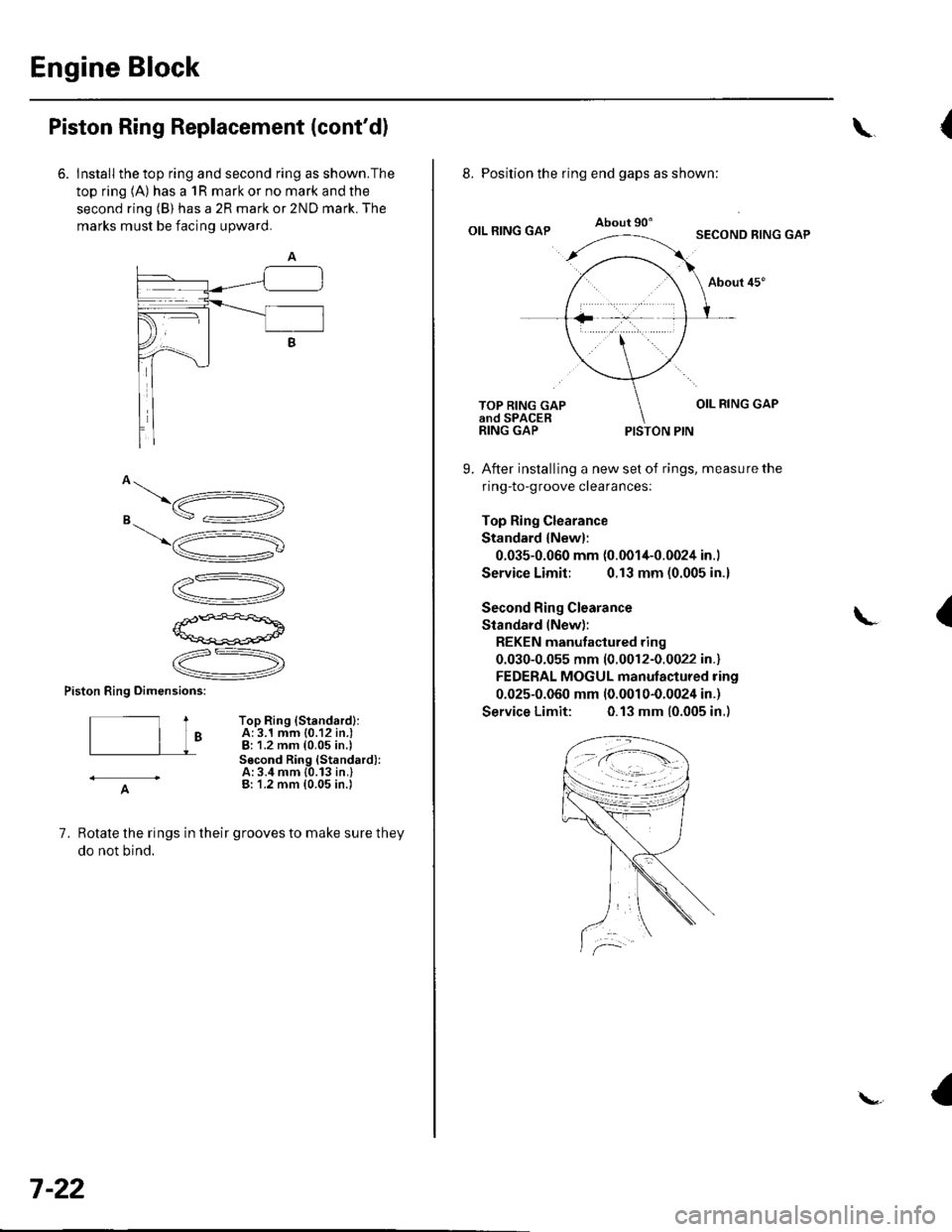
Engine Block
Piston Ring Replacement (cont'd)
6. Install the top ring and second ring as shown.The
top ring (A) has a 1R mark or no mark and the
second ring (B) has a 2R mark or 2ND mark. The
marks must be facing upward.
o\,"16.
s =:-=2
\5
V"
12-)V
P'ffi+a\aq*-pogd
.ZR,
V
Piston Ring oimensions:
t ToP Ring {Standardl:| | o A: 3.1 mm {0.12 in.l
| | J - B:1.2 mm {0.05 in.)Socond Ring {Standard):A:3.4 mm {0.13 in.}- A- B:'1.2 mm (0.05 in.i
7, Rotate the rings in their grooves to make sure they
do not bind.
7-22
\{
8. Position the ring end gaps as shown:
OIL RING GAPAbout 90'SECOND RING GAP
About 45"
OIL RING GAPTOP RING GAPand SPACERRING GAPPISTON PIN
9. After installing a new set of rings, measure the
ring-to-groove clearances:
Top Ring Clearance
Standard {New}:
0.035-0.060 mm {0.0014-0.0024 in.)
Service Limit: 0.13 mm (0.005 in.)
Second Ring Clearance
Standard lNew):
REKEN manutactured ring
0.030-0.055 mm (0.0012-0.0022 in.)
FEDERAL MOGUL manulactured ring
0.025-0.060 mm (0.001 0-0.0024 in.)
Service Limit: 0.13 mm (0.005 in.)
{
Page 161 of 1139
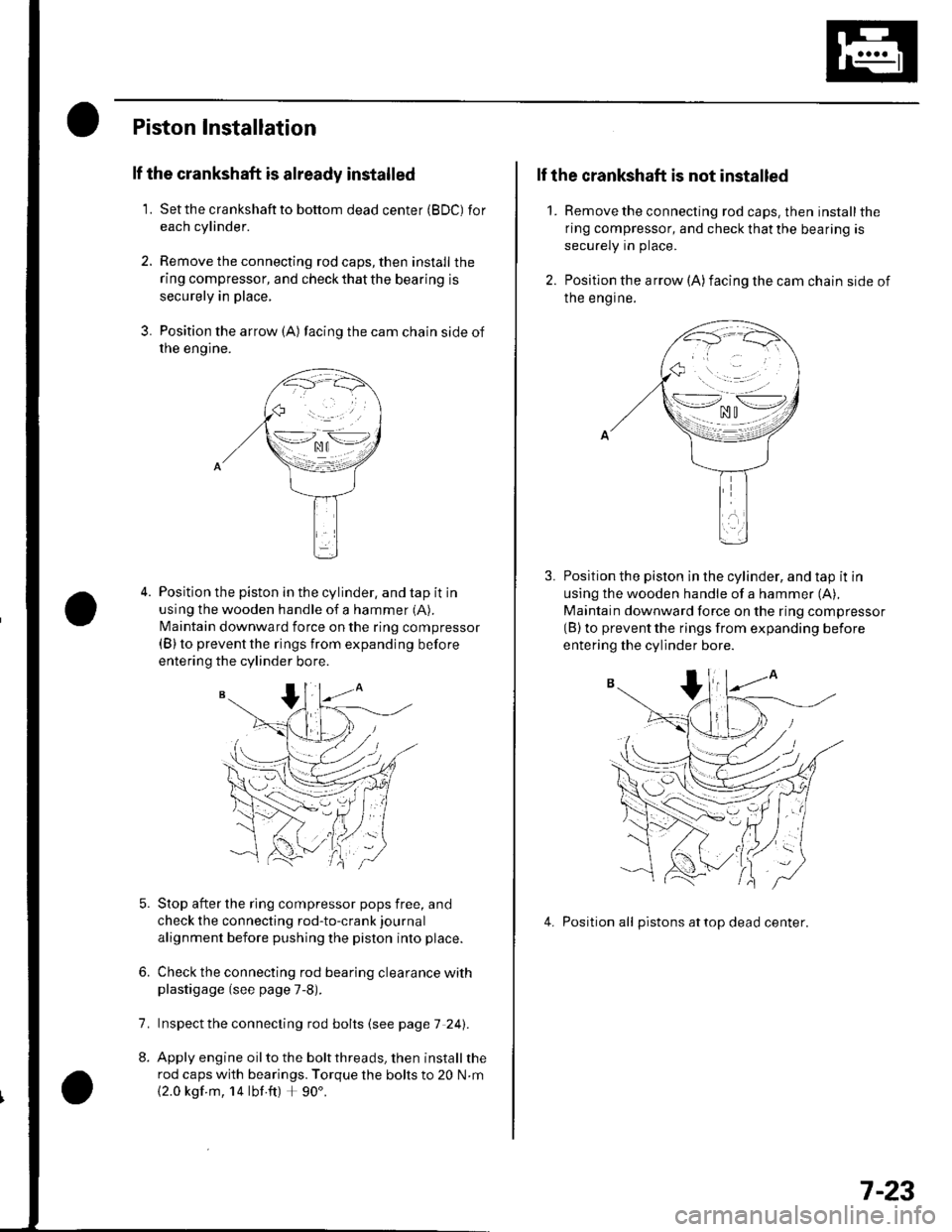
Piston Installation
lf the crankshaft is already installed
1. Setthe crankshaftto bottom dead center (BDC) for
each cylinder.
2. Remove the connecting rod caps, then install the
ring compressor, and check that the bearing is
securely in place,
3. Position the arrow {A) facing the cam chain side of
rne engtne.
Position the piston in the cylinder, and tap it in
using the wooden handle of a hammer (A).
N4aintain downward force on the ring compressor(B) to prevent the rings from expanding before
entering the cylinder bore.
Stop after the ring compressor pops free, and
check the connecting rod-to-crank journal
alignment before pushing the piston into place.
Check the connecting rod bearing clearance withplastigage (see page 7-8).
lnspect the connecting rod bolts (see page 7 241.
Apply engine oil to the bolt threads, then install the
rod caps with bearings. Torque the bolts to 20 N.m
{2.0 kgf m, 14 lbf ft) + 90'.
6.
7.
2.
1.
lf the crankshaft is not installed
Remove the connecting rod caps. then install the
ring compressor, and check that the bearing is
securely in place.
Position the arrow (A)facing the cam chain side of
Ine engrne.
Position the piston in the cylinder, and tap it in
using the wooden handle of a hammer (A),
Maintain downward force on the ring compressor(B) to prevent the rings from expanding before
entering the cylinder bore.
4. Position all pistons attop dead center.
\--lno n\-.--l. ^u t
>-*/zi
.,.'_\pf{
wr
(( 'V,/ :
7-23