set clock INFINITI QX56 2007 Factory Service Manual
[x] Cancel search | Manufacturer: INFINITI, Model Year: 2007, Model line: QX56, Model: INFINITI QX56 2007Pages: 3061, PDF Size: 64.56 MB
Page 29 of 3061
![INFINITI QX56 2007 Factory Service Manual ACS-16
< SERVICE INFORMATION >[ICC]
LASER BEAM AIMING ADJUSTMENT
8. After the CONSULT-II displays “ADJUST THE VERTICAL OF
LASER BEAM AIMING” turn the vertical adjusting screw until
“U/D CORRECT INFINITI QX56 2007 Factory Service Manual ACS-16
< SERVICE INFORMATION >[ICC]
LASER BEAM AIMING ADJUSTMENT
8. After the CONSULT-II displays “ADJUST THE VERTICAL OF
LASER BEAM AIMING” turn the vertical adjusting screw until
“U/D CORRECT](/img/42/57029/w960_57029-28.png)
ACS-16
< SERVICE INFORMATION >[ICC]
LASER BEAM AIMING ADJUSTMENT
8. After the CONSULT-II displays “ADJUST THE VERTICAL OF
LASER BEAM AIMING” turn the vertical adjusting screw until
“U/D CORRECT” value is set in the range of ±4.
CAUTION:
Turn the screw slowly. The value on the CONSULT-II is
slower than the actual movement of the ICC sensor. Wait 2
seconds between each adjustment. Also, during adjust-
ment work, do not block the ICC sensor lens with your hand
or body. In that case, there are times when aiming cannot
be conducted correctly.
NOTE:
Turning the screw clockwise raises the ICC sensor and counter-
clockwise lowers the ICC sensor.
9. When “U/D CORRECT” value indicates ±4, confirm that the value remains within ±4 for at least 2 seconds
while nothing is touching the ICC sensor.
When “COMPLETED THE VERTICAL AIMING OF LASER
BEAM” appears on screen, touch “END”.
CAUTION:
Be sure that the margin of “U/D CORRECT” is within ±4
when the ICC sensor unit is untouched.
10. Confirm that “ADJUSTING AUTOMATIC HORIZONTAL LASER
BEAM AIMING” is on screen and wait while the horizontal
adjustment is made automatically. (maximum: 10 seconds).
SKIA1221E
WKIA1869E
WKIA2676E
SKIA1224E
Page 294 of 3061
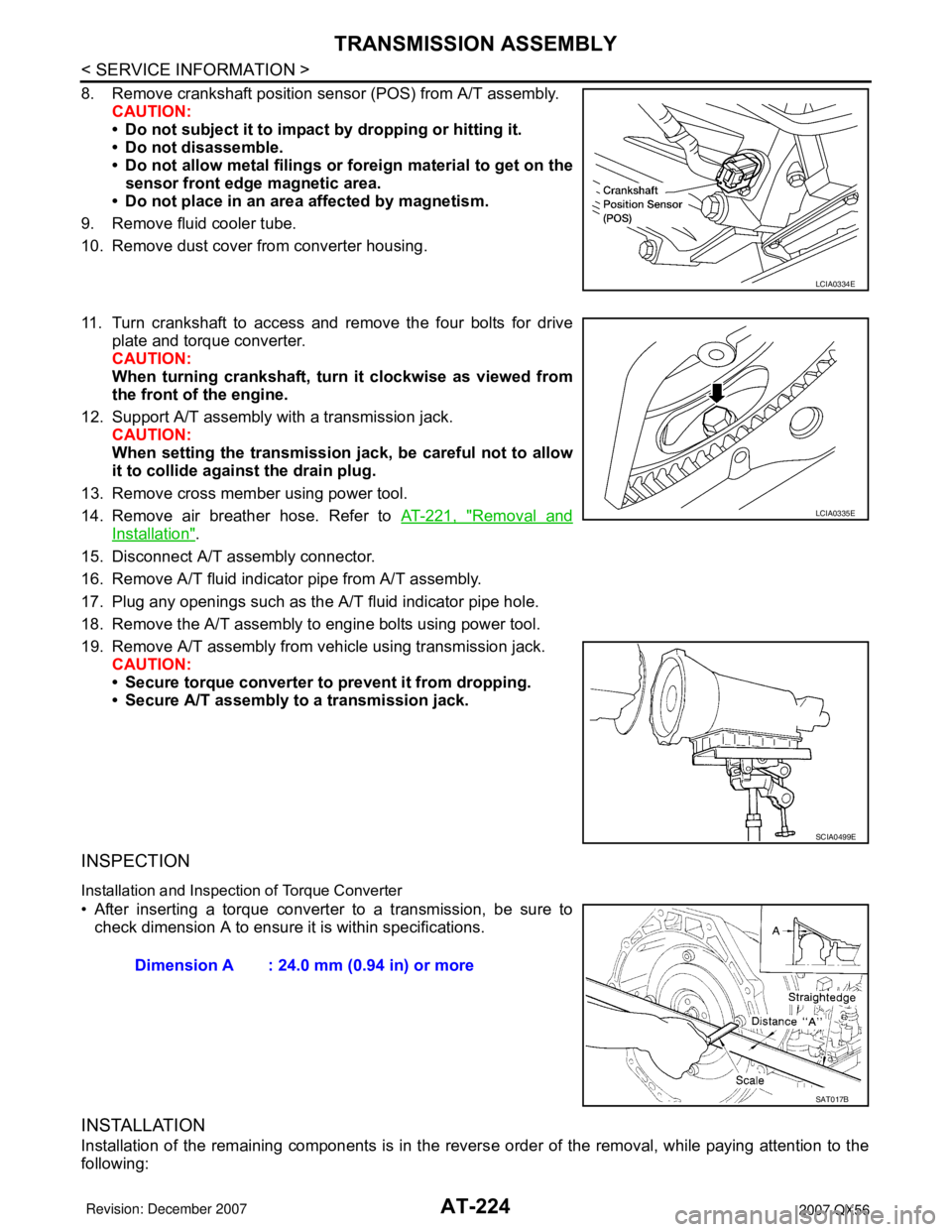
AT-224
< SERVICE INFORMATION >
TRANSMISSION ASSEMBLY
8. Remove crankshaft position sensor (POS) from A/T assembly.
CAUTION:
• Do not subject it to impact by dropping or hitting it.
• Do not disassemble.
• Do not allow metal filings or foreign material to get on the
sensor front edge magnetic area.
• Do not place in an area affected by magnetism.
9. Remove fluid cooler tube.
10. Remove dust cover from converter housing.
11. Turn crankshaft to access and remove the four bolts for drive
plate and torque converter.
CAUTION:
When turning crankshaft, turn it clockwise as viewed from
the front of the engine.
12. Support A/T assembly with a transmission jack.
CAUTION:
When setting the transmission jack, be careful not to allow
it to collide against the drain plug.
13. Remove cross member using power tool.
14. Remove air breather hose. Refer to AT-221, "
Removal and
Installation".
15. Disconnect A/T assembly connector.
16. Remove A/T fluid indicator pipe from A/T assembly.
17. Plug any openings such as the A/T fluid indicator pipe hole.
18. Remove the A/T assembly to engine bolts using power tool.
19. Remove A/T assembly from vehicle using transmission jack.
CAUTION:
• Secure torque converter to prevent it from dropping.
• Secure A/T assembly to a transmission jack.
INSPECTION
Installation and Inspection of Torque Converter
• After inserting a torque converter to a transmission, be sure to
check dimension A to ensure it is within specifications.
INSTALLATION
Installation of the remaining components is in the reverse order of the removal, while paying attention to the
following:
LCIA0334E
LCIA0335E
SCIA0499E
Dimension A : 24.0 mm (0.94 in) or more
SAT017B
Page 296 of 3061
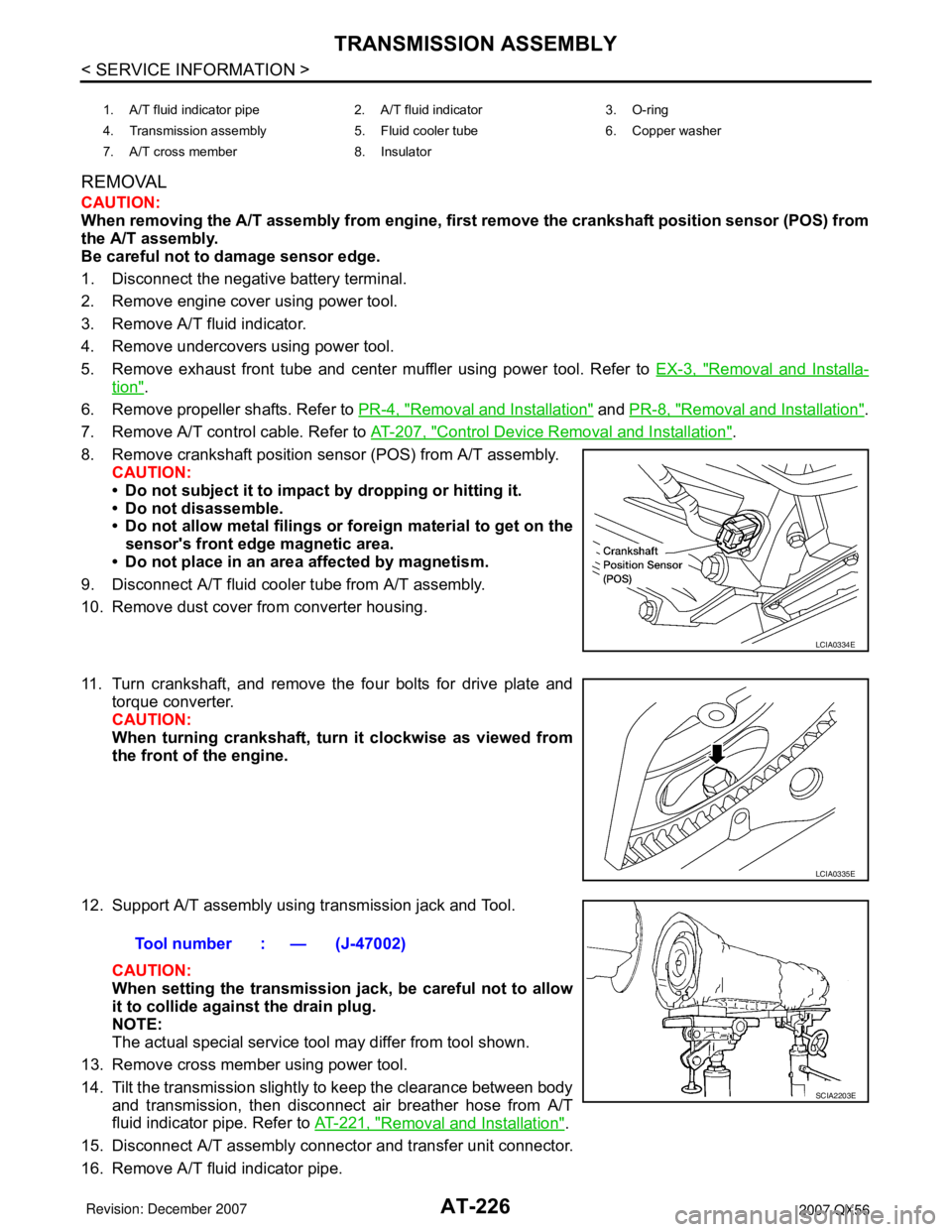
AT-226
< SERVICE INFORMATION >
TRANSMISSION ASSEMBLY
REMOVAL
CAUTION:
When removing the A/T assembly from engine, first remove the crankshaft position sensor (POS) from
the A/T assembly.
Be careful not to damage sensor edge.
1. Disconnect the negative battery terminal.
2. Remove engine cover using power tool.
3. Remove A/T fluid indicator.
4. Remove undercovers using power tool.
5. Remove exhaust front tube and center muffler using power tool. Refer to EX-3, "
Removal and Installa-
tion".
6. Remove propeller shafts. Refer to PR-4, "
Removal and Installation" and PR-8, "Removal and Installation".
7. Remove A/T control cable. Refer to AT-207, "
Control Device Removal and Installation".
8. Remove crankshaft position sensor (POS) from A/T assembly.
CAUTION:
• Do not subject it to impact by dropping or hitting it.
• Do not disassemble.
• Do not allow metal filings or foreign material to get on the
sensor's front edge magnetic area.
• Do not place in an area affected by magnetism.
9. Disconnect A/T fluid cooler tube from A/T assembly.
10. Remove dust cover from converter housing.
11. Turn crankshaft, and remove the four bolts for drive plate and
torque converter.
CAUTION:
When turning crankshaft, turn it clockwise as viewed from
the front of the engine.
12. Support A/T assembly using transmission jack and Tool.
CAUTION:
When setting the transmission jack, be careful not to allow
it to collide against the drain plug.
NOTE:
The actual special service tool may differ from tool shown.
13. Remove cross member using power tool.
14. Tilt the transmission slightly to keep the clearance between body
and transmission, then disconnect air breather hose from A/T
fluid indicator pipe. Refer to AT-221, "
Removal and Installation".
15. Disconnect A/T assembly connector and transfer unit connector.
16. Remove A/T fluid indicator pipe.
1. A/T fluid indicator pipe 2. A/T fluid indicator 3. O-ring
4. Transmission assembly 5. Fluid cooler tube 6. Copper washer
7. A/T cross member 8. Insulator
LCIA0334E
LCIA0335E
Tool number : — (J-47002)
SCIA2203E
Page 418 of 3061
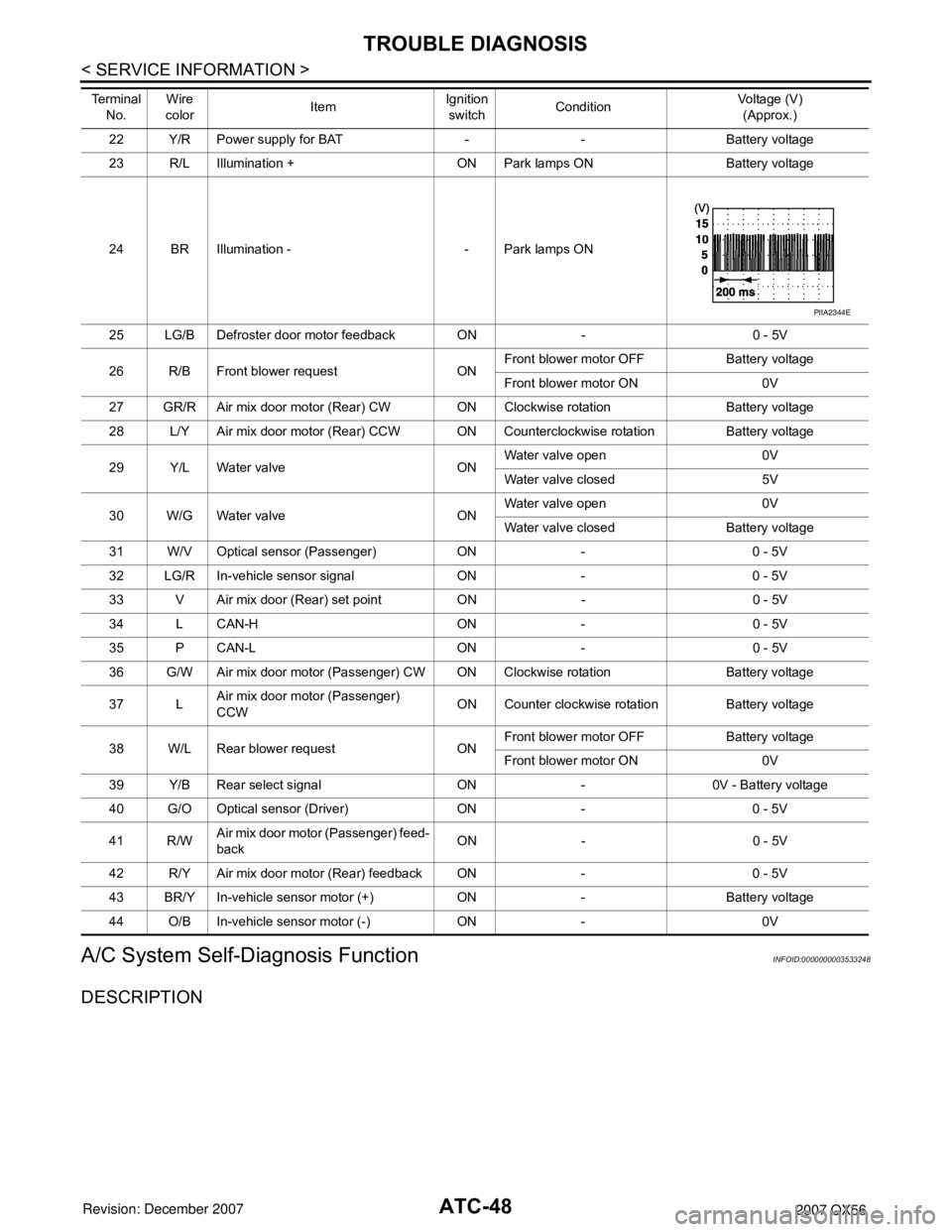
ATC-48
< SERVICE INFORMATION >
TROUBLE DIAGNOSIS
A/C System Self-Diagnosis Function
INFOID:0000000003533248
DESCRIPTION
22 Y/R Power supply for BAT - - Battery voltage
23 R/L Illumination + ON Park lamps ON Battery voltage
24 BR Illumination - - Park lamps ON
25 LG/B Defroster door motor feedback ON - 0 - 5V
26 R/B Front blower request ON Front blower motor OFF Battery voltage
Front blower motor ON 0V
27 GR/R Air mix door motor (Rear) CW ON Clockwise rotation Battery voltage
28 L/Y Air mix door motor (Rear) CCW ON Coun terclockwise rotation Battery voltage
29 Y/L Water valve ON Water valve open 0V
Water valve closed 5V
30 W/G Water valve ON Water valve open 0V
Water valve closed Battery voltage
31 W/V Optical sensor (Passenger) ON - 0 - 5V
32 LG/R In-vehicle sensor signal ON - 0 - 5V
33 V Air mix door (Rear) set point ON - 0 - 5V
34 L CAN-H ON - 0 - 5V
35 P CAN-L ON - 0 - 5V
36 G/W Air mix door motor (Passenger) CW ON Clockwise rotation Battery voltage
37 L Air mix door motor (Passenger)
CCW ON Counter clockwise rotation Battery voltage
38 W/L Rear blower request ON Front blower motor OFF Battery voltage
Front blower motor ON 0V
39 Y/B Rear select signal ON - 0V - Battery voltage
40 G/O Optical sensor (Driver) ON - 0 - 5V
41 R/W Air mix door motor (Passenger) feed-
back ON - 0 - 5V
42 R/Y Air mix door motor (Rear) feedback ON - 0 - 5V
43 BR/Y In-vehicle sensor motor (+) ON - Battery voltage
44 O/B In-vehicle sensor motor (-) ON - 0V
Te r m i n a l
No. Wire
color ItemIgnition
switch Condition Voltage (V)
(Approx.)
PIIA2344E
Page 420 of 3061
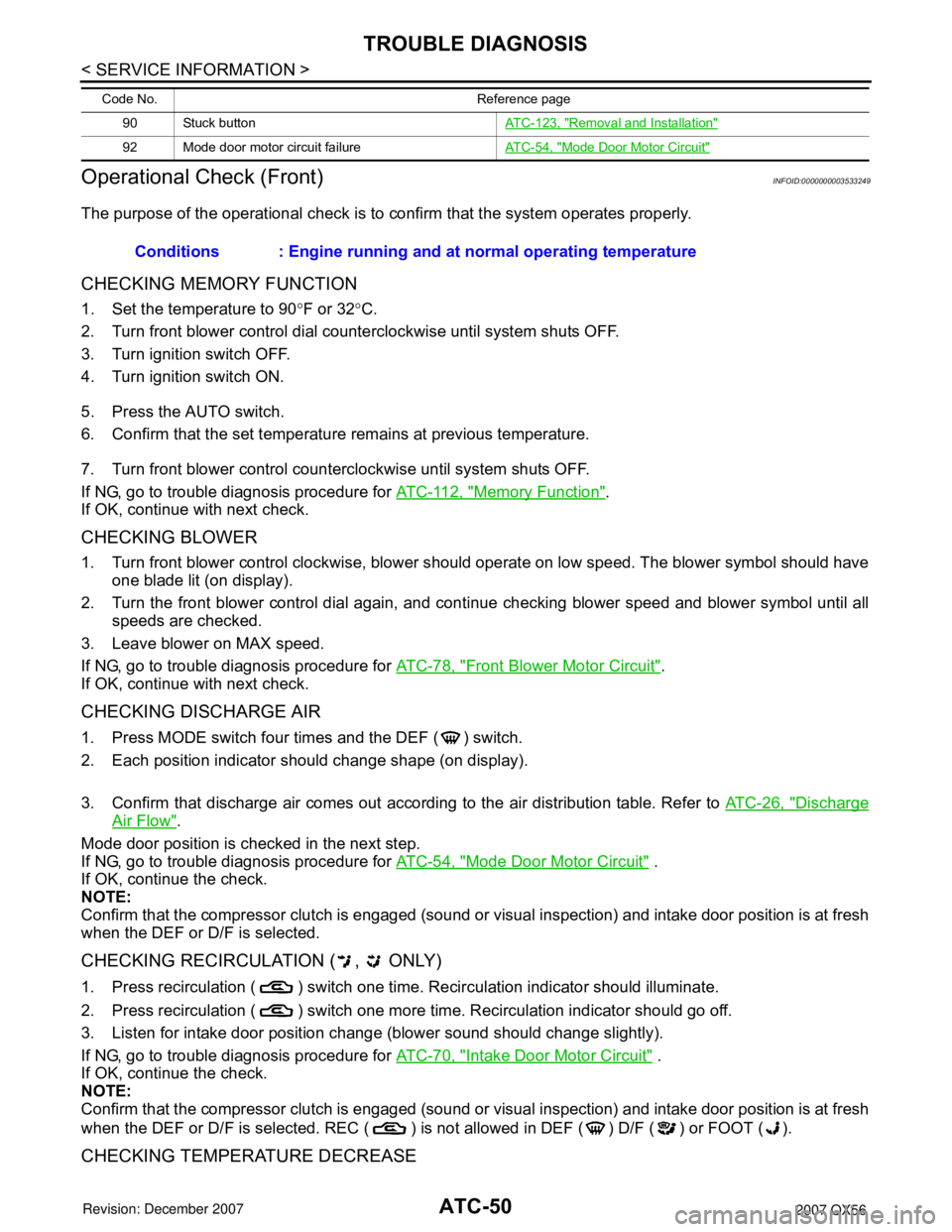
ATC-50
< SERVICE INFORMATION >
TROUBLE DIAGNOSIS
Operational Check (Front)
INFOID:0000000003533249
The purpose of the operational check is to confirm that the system operates properly.
CHECKING MEMORY FUNCTION
1. Set the temperature to 90 °F or 32 °C.
2. Turn front blower control dial counterclockwise until system shuts OFF.
3. Turn ignition switch OFF.
4. Turn ignition switch ON.
5. Press the AUTO switch.
6. Confirm that the set temperature remains at previous temperature.
7. Turn front blower control counterclockwise until system shuts OFF.
If NG, go to trouble diagnosis procedure for ATC-112, "
Memory Function".
If OK, continue with next check.
CHECKING BLOWER
1. Turn front blower control clockwise, blower s hould operate on low speed. The blower symbol should have
one blade lit (on display).
2. Turn the front blower control dial again, and c ontinue checking blower speed and blower symbol until all
speeds are checked.
3. Leave blower on MAX speed.
If NG, go to trouble diagnosis procedure for ATC-78, "
Front Blower Motor Circuit".
If OK, continue with next check.
CHECKING DISCHARGE AIR
1. Press MODE switch four times and the DEF ( ) switch.
2. Each position indicator should change shape (on display).
3. Confirm that discharge air comes out according to the air distribution table. Refer to ATC-26, "
Discharge
Air Flow".
Mode door position is checked in the next step.
If NG, go to trouble diagnosis procedure for ATC-54, "
Mode Door Motor Circuit" .
If OK, continue the check.
NOTE:
Confirm that the compressor clutch is engaged (sound or vis ual inspection) and intake door position is at fresh
when the DEF or D/F is selected.
CHECKING RECIRCULATION ( , ONLY)
1. Press recirculation ( ) switch one time. Recirculation indicator should illuminate.
2. Press recirculation ( ) switch one more time. Recirculation indicator should go off.
3. Listen for intake door position change (blower sound should change slightly).
If NG, go to trouble diagnosis procedure for ATC-70, "
Intake Door Motor Circuit" .
If OK, continue the check.
NOTE:
Confirm that the compressor clutch is engaged (sound or vis ual inspection) and intake door position is at fresh
when the DEF or D/F is selected. REC ( ) is not allowed in DEF ( ) D/F ( ) or FOOT ( ).
CHECKING TEMPERATURE DECREASE
90 Stuck button ATC-123, "Removal and Installation"
92 Mode door motor circuit failureAT C - 5 4 , "Mode Door Motor Circuit"
Code No. Reference page
Conditions : Engine running and at normal operating temperature
Page 421 of 3061
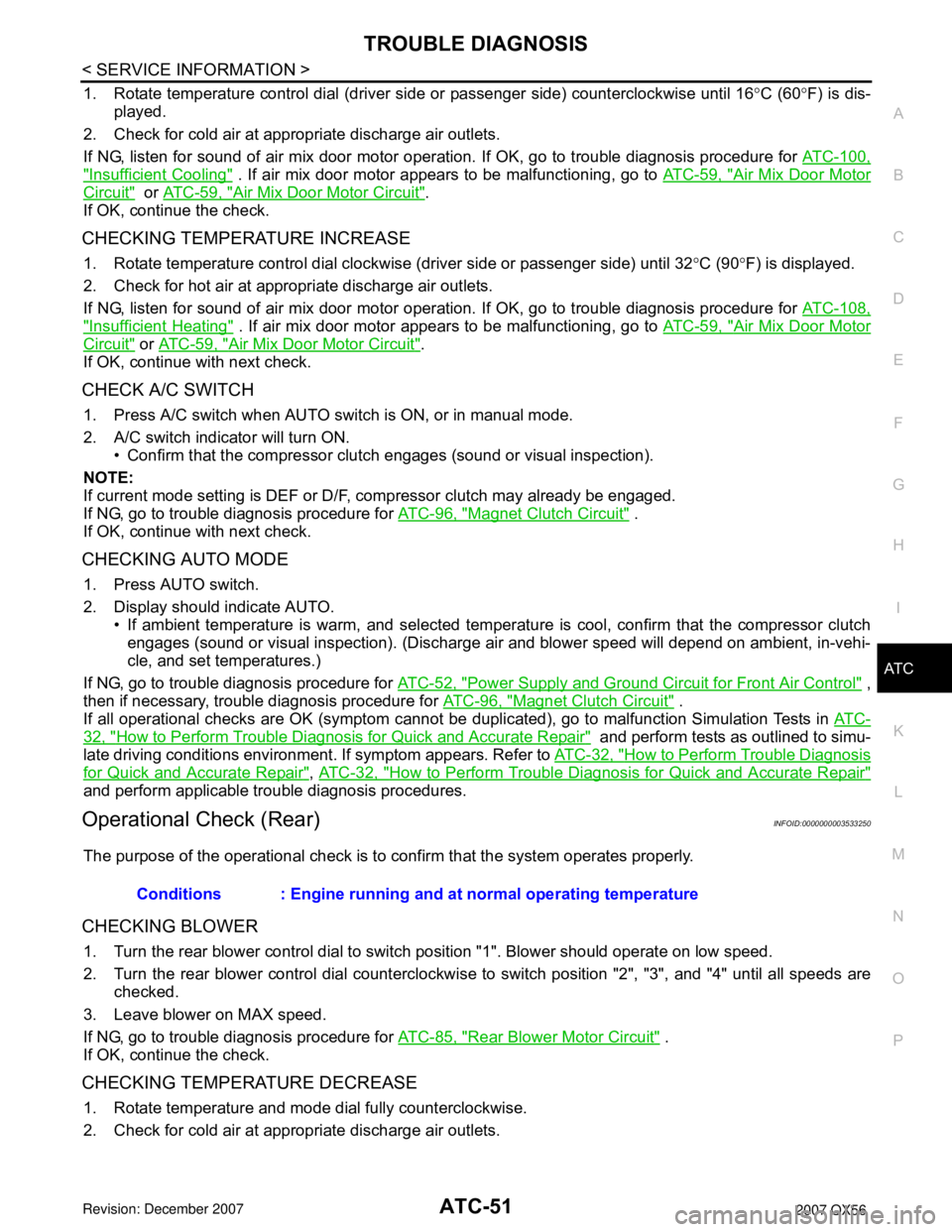
TROUBLE DIAGNOSISATC-51
< SERVICE INFORMATION >
C
DE
F
G H
I
K L
M A
B
AT C
N
O P
1. Rotate temperature control dial (driver si de or passenger side) counterclockwise until 16 °C (60 °F) is dis-
played.
2. Check for cold air at appropriate discharge air outlets.
If NG, listen for sound of air mix door motor operat ion. If OK, go to trouble diagnosis procedure for ATC-100,
"Insufficient Cooling" . If air mix door motor appears to be malfunctioning, go to ATC-59, "Air Mix Door Motor
Circuit" or ATC-59, "Air Mix Door Motor Circuit".
If OK, continue the check.
CHECKING TEMPERATURE INCREASE
1. Rotate temperature control dial clockw ise (driver side or passenger side) until 32°C (90 °F) is displayed.
2. Check for hot air at appropriate discharge air outlets.
If NG, listen for sound of air mix door motor operat ion. If OK, go to trouble diagnosis procedure for ATC-108,
"Insufficient Heating" . If air mix door motor appears to be malfunctioning, go to ATC-59, "Air Mix Door Motor
Circuit" or ATC-59, "Air Mix Door Motor Circuit".
If OK, continue with next check.
CHECK A/C SWITCH
1. Press A/C switch when AUTO switch is ON, or in manual mode.
2. A/C switch indicator will turn ON.
• Confirm that the compressor clutch engages (sound or visual inspection).
NOTE:
If current mode setting is DEF or D/F, compressor clutch may already be engaged.
If NG, go to trouble diagnosis procedure for ATC-96, "
Magnet Clutch Circuit" .
If OK, continue with next check.
CHECKING AUTO MODE
1. Press AUTO switch.
2. Display should indicate AUTO.
• If ambient temperature is warm, and selected temperat ure is cool, confirm that the compressor clutch
engages (sound or visual inspection). (Discharge air and blower speed will depend on ambient, in-vehi-
cle, and set temperatures.)
If NG, go to trouble diagnosis procedure for ATC-52, "
Power Supply and Ground Circuit for Front Air Control" ,
then if necessary, trouble diagnosis procedure for ATC-96, "
Magnet Clutch Circuit" .
If all operational checks are OK (symptom cannot be duplicated), go to malfunction Simulation Tests in AT C -
32, "How to Perform Trouble Diagnosis for Quick and Accurate Repair" and perform tests as outlined to simu-
late driving conditions environment . If symptom appears. Refer to ATC-32, "
How to Perform Trouble Diagnosis
for Quick and Accurate Repair", ATC-32, "How to Perform Trouble Diagnosis for Quick and Accurate Repair"
and perform applicable trouble diagnosis procedures.
Operational Check (Rear)INFOID:0000000003533250
The purpose of the operational check is to confirm that the system operates properly.
CHECKING BLOWER
1. Turn the rear blower control dial to swit ch position "1". Blower should operate on low speed.
2. Turn the rear blower control dial counterclockwis e to switch position "2", "3", and "4" until all speeds are
checked.
3. Leave blower on MAX speed.
If NG, go to trouble diagnosis procedure for ATC-85, "
Rear Blower Motor Circuit" .
If OK, continue the check.
CHECKING TEMPERATURE DECREASE
1. Rotate temperature and mode dial fully counterclockwise.
2. Check for cold air at appropriate discharge air outlets. Conditions : Engine running and at normal operating temperature
Page 422 of 3061
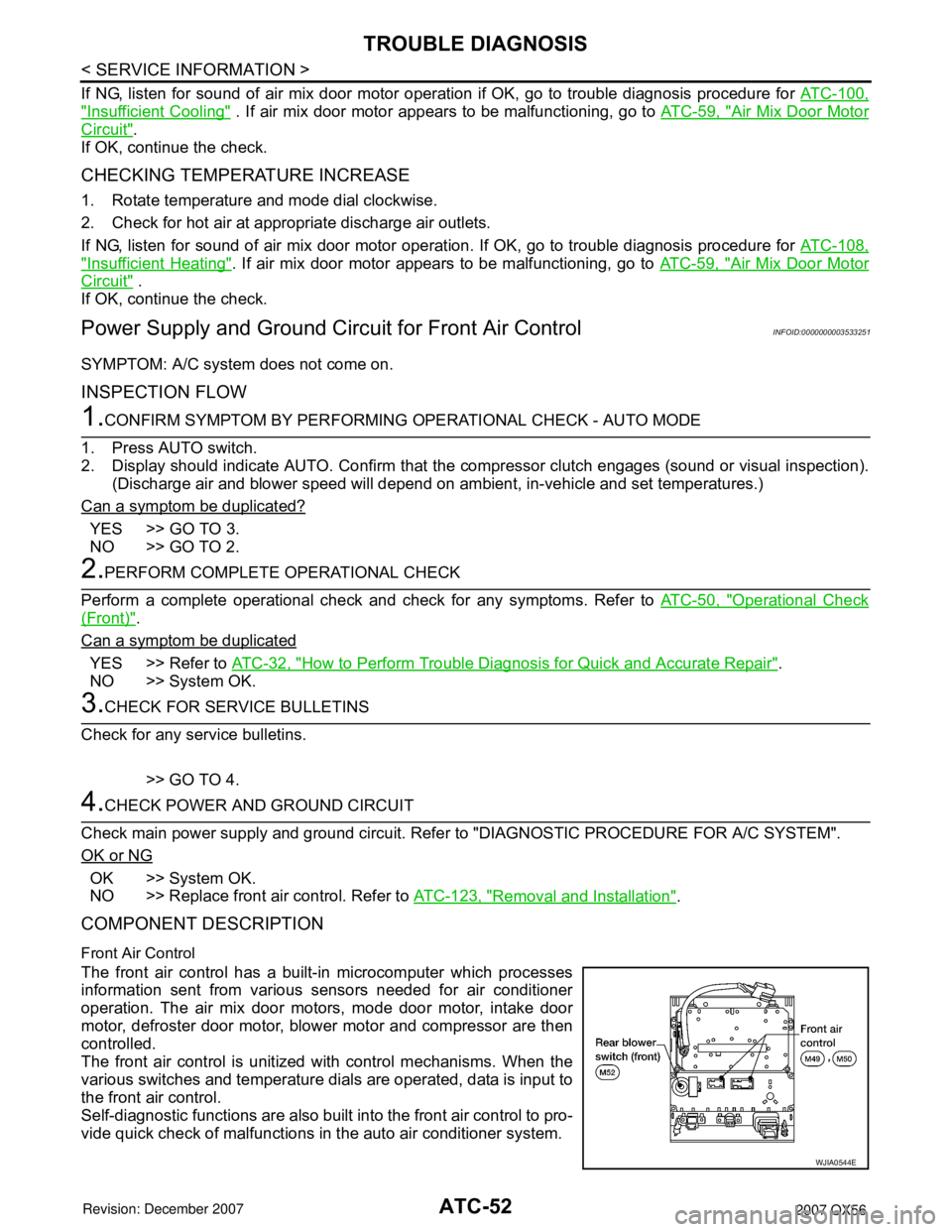
ATC-52
< SERVICE INFORMATION >
TROUBLE DIAGNOSIS
If NG, listen for sound of air mix door motor operation if OK, go to trouble diagnosis procedure for ATC-100,
"Insufficient Cooling" . If air mix door motor appears to be malfunctioning, go to ATC-59, "Air Mix Door Motor
Circuit".
If OK, continue the check.
CHECKING TEMPERATURE INCREASE
1. Rotate temperature and mode dial clockwise.
2. Check for hot air at appropriate discharge air outlets.
If NG, listen for sound of air mix door motor operat ion. If OK, go to trouble diagnosis procedure for ATC-108,
"Insufficient Heating". If air mix door motor appears to be malfunctioning, go to ATC-59, "Air Mix Door Motor
Circuit" .
If OK, continue the check.
Power Supply and Ground Circu it for Front Air ControlINFOID:0000000003533251
SYMPTOM: A/C system does not come on.
INSPECTION FLOW
1.CONFIRM SYMPTOM BY PERFORMING OPERATIONAL CHECK - AUTO MODE
1. Press AUTO switch.
2. Display should indicate AUTO. Confirm that the compressor clutch engages (sound or visual inspection).
(Discharge air and blower speed will depend on am bient, in-vehicle and set temperatures.)
Can a symptom be duplicated?
YES >> GO TO 3.
NO >> GO TO 2.
2.PERFORM COMPLETE OPERATIONAL CHECK
Perform a complete operational check and check for any symptoms. Refer to ATC-50, "
Operational Check
(Front)".
Can a symptom be duplicated
YES >> Refer to ATC-32, "How to Perform Trouble Diagnosis for Quick and Accurate Repair".
NO >> System OK.
3.CHECK FOR SERVICE BULLETINS
Check for any service bulletins.
>> GO TO 4.
4.CHECK POWER AND GROUND CIRCUIT
Check main power supply and ground circuit. Refe r to "DIAGNOSTIC PROCEDURE FOR A/C SYSTEM".
OK or NG
OK >> System OK.
NO >> Replace front air control. Refer to ATC-123, "
Removal and Installation".
COMPONENT DESCRIPTION
Front Air Control
The front air control has a built-in microcomputer which processes
information sent from various sensors needed for air conditioner
operation. The air mix door motors, mode door motor, intake door
motor, defroster door motor, blower motor and compressor are then
controlled.
The front air control is unitized with control mechanisms. When the
various switches and temperature dials are operated, data is input to
the front air control.
Self-diagnostic functions are also built into the front air control to pro-
vide quick check of malfunctions in the auto air conditioner system.
WJIA0544E
Page 455 of 3061
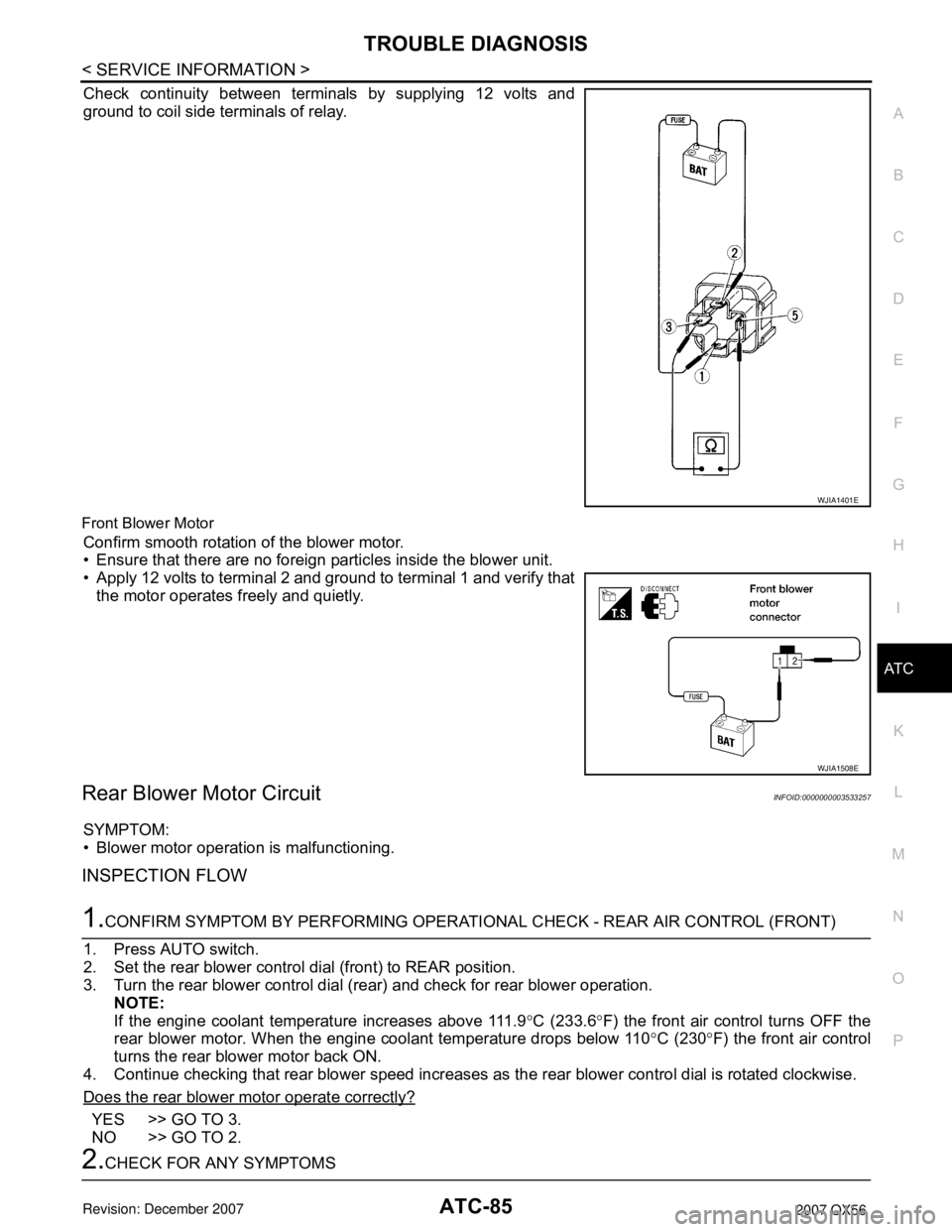
TROUBLE DIAGNOSISATC-85
< SERVICE INFORMATION >
C
DE
F
G H
I
K L
M A
B
AT C
N
O P
Check continuity between terminals by supplying 12 volts and
ground to coil side terminals of relay.
Front Blower Motor
Confirm smooth rotation of the blower motor.
• Ensure that there are no foreign particles inside the blower unit.
• Apply 12 volts to terminal 2 and ground to terminal 1 and verify that the motor operates freely and quietly.
Rear Blower Motor CircuitINFOID:0000000003533257
SYMPTOM:
• Blower motor operation is malfunctioning.
INSPECTION FLOW
1.CONFIRM SYMPTOM BY PERFORMING OPERATIO NAL CHECK - REAR AIR CONTROL (FRONT)
1. Press AUTO switch.
2. Set the rear blower control dial (front) to REAR position.
3. Turn the rear blower control dial (rear) and check for rear blower operation. NOTE:
If the engine coolant temperature increases above 111.9 °C (233.6 °F) the front air control turns OFF the
rear blower motor. When the engine coolant temperature drops below 110 °C (230 °F) the front air control
turns the rear blower motor back ON.
4. Continue checking that rear blower speed increases as the rear blower control dial is rotated clockwise.
Does the rear blower motor operate correctly?
YES >> GO TO 3.
NO >> GO TO 2.
2.CHECK FOR ANY SYMPTOMS
WJIA1401E
WJIA1508E
Page 457 of 3061
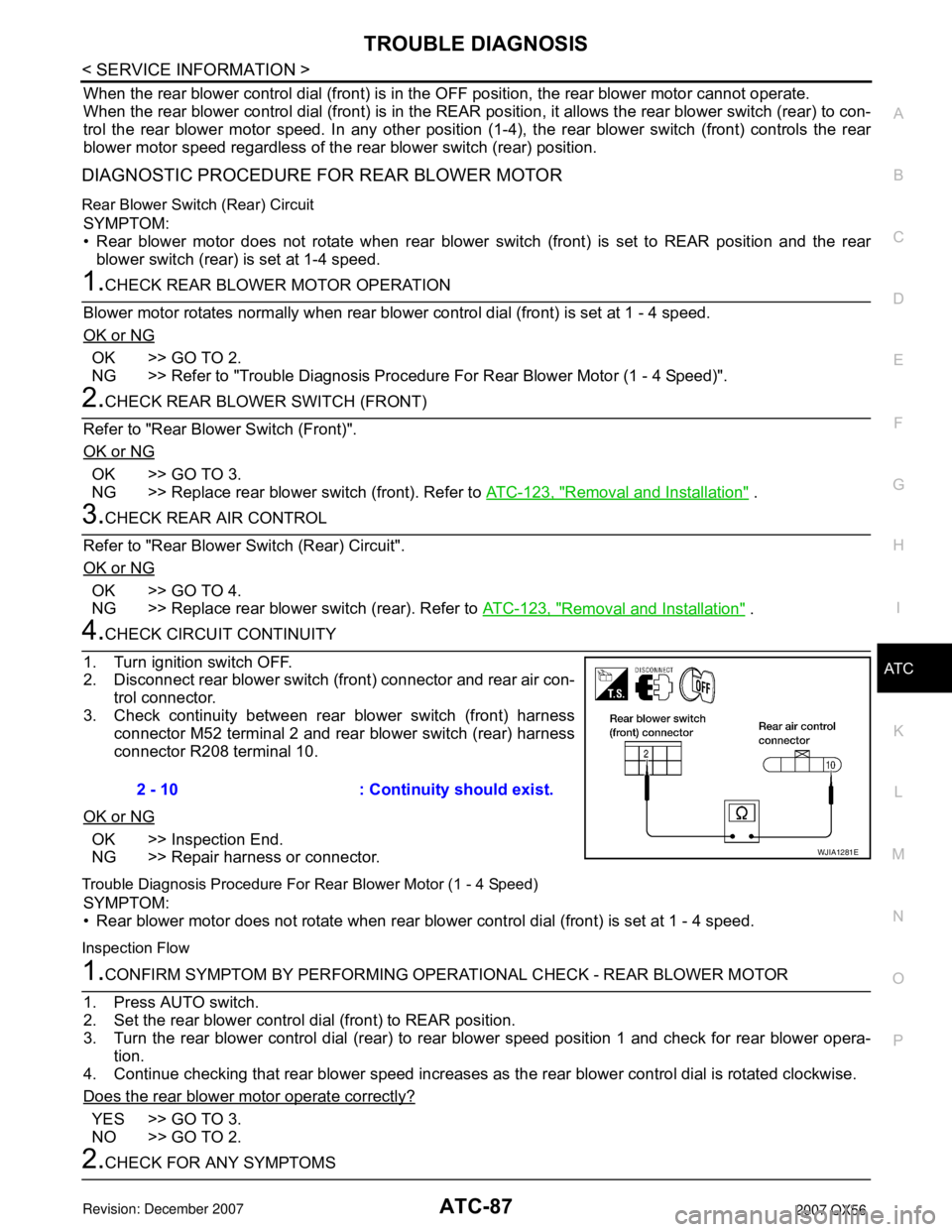
TROUBLE DIAGNOSISATC-87
< SERVICE INFORMATION >
C
DE
F
G H
I
K L
M A
B
AT C
N
O P
When the rear blower control dial (front) is in t he OFF position, the rear blower motor cannot operate.
When the rear blower control dial (front) is in the REAR position, it allows the rear blower switch (rear) to con-
trol the rear blower motor speed. In any other position (1 -4), the rear blower switch (front) controls the rear
blower motor speed regardless of the rear blower switch (rear) position.
DIAGNOSTIC PROCEDURE FOR REAR BLOWER MOTOR
Rear Blower Switch (Rear) Circuit
SYMPTOM:
• Rear blower motor does not rotate when rear blower switch (front) is set to REAR position and the rear
blower switch (rear) is set at 1-4 speed.
1.CHECK REAR BLOWER MOTOR OPERATION
Blower motor rotates normally when rear blower control dial (front) is set at 1 - 4 speed.
OK or NG
OK >> GO TO 2.
NG >> Refer to "Trouble Diagnosis Procedure For Rear Blower Motor (1 - 4 Speed)".
2.CHECK REAR BLOWER SWITCH (FRONT)
Refer to "Rear Blower Switch (Front)".
OK or NG
OK >> GO TO 3.
NG >> Replace rear blower switch (front). Refer to ATC-123, "
Removal and Installation" .
3.CHECK REAR AIR CONTROL
Refer to "Rear Blower Switch (Rear) Circuit".
OK or NG
OK >> GO TO 4.
NG >> Replace rear blower switch (rear). Refer to ATC-123, "
Removal and Installation" .
4.CHECK CIRCUIT CONTINUITY
1. Turn ignition switch OFF.
2. Disconnect rear blower switch (front) connector and rear air con-
trol connector.
3. Check continuity between rear blower switch (front) harness connector M52 terminal 2 and rear blower switch (rear) harness
connector R208 terminal 10.
OK or NG
OK >> Inspection End.
NG >> Repair harness or connector.
Trouble Diagnosis Procedure For Rear Blower Motor (1 - 4 Speed)
SYMPTOM:
• Rear blower motor does not rotate when rear blower control dial (front) is set at 1 - 4 speed.
Inspection Flow
1.CONFIRM SYMPTOM BY PERFORMING OPERAT IONAL CHECK - REAR BLOWER MOTOR
1. Press AUTO switch.
2. Set the rear blower control dial (front) to REAR position.
3. Turn the rear blower control dial (rear) to rear blower speed position 1 and check for rear blower opera- tion.
4. Continue checking that rear blower speed increases as the rear blower control dial is rotated clockwise.
Does the rear blower motor operate correctly?
YES >> GO TO 3.
NO >> GO TO 2.
2.CHECK FOR ANY SYMPTOMS 2 - 10 : Continuity should exist.
WJIA1281E
Page 1147 of 3061

EC-64
< SERVICE INFORMATION >
ON BOARD DIAGNOSTIC (OBD) SYSTEM
When any SRT codes are not set, MIL may flash without DTC. For the details, refer to EC-49, "Emission-
related Diagnostic Information".
HOW TO SWITCH DIAGNOSTIC TEST MODE
NOTE:
•It is better to count the time accurately with a clock.
•It is impossible to switch the diagnostic mode when an accelerator pedal position sensor circuit has
a malfunction.
•Always ECM returns to Diagnostic Test Mode I after ignition switch is turned OFF.
How to Set Diagnostic Test Mode II (Self-diagnostic Results)
1. Confirm that accelerator pedal is fully released, turn ignition switch ON and wait 3 seconds.
2. Repeat the following procedure quickly five times within 5 seconds.
a. Fully depress the accelerator pedal.
b. Fully release the accelerator pedal.
3. Wait 7 seconds, fully depress the accelerator pedal and keep it for approx. 10 seconds until the MIL starts
blinking.
NOTE:
Do not release the accelerator pedal for 10 seconds if MIL may start blinking on the halfway of this
10 seconds. This blinking is displaying SRT status and is continued for another 10 seconds. For
the details, refer to EC-49, "
Emission-related Diagnostic Information".
4. Fully release the accelerator pedal.
ECM has entered to Diagnostic Test Mode II (Self-diagnostic results).
NOTE:
Wait until the same DTC (or 1st trip DTC) appears to confirm all DTCs certainly.
How to Erase Diagnostic Test Mode II (Self-diagnostic Results)
1. Set ECM in Diagnostic Test Mode II (Self-diagnostic results). Refer to "How to Set Diagnostic Test Mode II
(Self-diagnostic Results)".
2. Fully depress the accelerator pedal and keep it for more than 10 seconds.
The emission-related diagnostic information has been erased from the backup memory in the ECM.
3. Fully release the accelerator pedal, and confirm the DTC 0000 is displayed.
DIAGNOSTIC TEST MODE I — BULB CHECK
In this mode, the MIL on the instrument panel should stay ON. If it remains OFF, check the bulb. Refer to DI-26
or see EC-643.
DIAGNOSTIC TEST MODE I — MALFUNCTION WARNING
This DTC number is clarified in Diagnostic Test Mode II (SELF-DIAGNOSTIC RESULTS)
DIAGNOSTIC TEST MODE II — SELF-DIAGNOSTIC RESULTS
In this mode, the DTC and 1st trip DTC are indicated by the number of blinks of the MIL as shown below.
The DTC and 1st trip DTC are displayed at the same time. If the MIL does not illuminate in diagnostic test
mode I (Malfunction warning), all displayed items are 1st trip DTCs. If only one code is displayed when the MIL
illuminates in diagnostic test mode II (SELF-DIAGNOSTIC RESULTS), it is a DTC; if two or more codes are
PBIB0092E
MIL Condition
ON When the malfunction is detected.
OFF No malfunction.