clock INFINITI QX56 2011 Factory User Guide
[x] Cancel search | Manufacturer: INFINITI, Model Year: 2011, Model line: QX56, Model: INFINITI QX56 2011Pages: 5598, PDF Size: 94.53 MB
Page 2085 of 5598
![INFINITI QX56 2011 Factory User Guide
DIAGNOSIS SYSTEM (ECM)EC-61
< SYSTEM DESCRIPTION > [VK56VD]
C
D
E
F
G H
I
J
K L
M A
EC
NP
O
ECM blinks MIL for about 10 seconds if all SRT codes are not set.
MALFUNCTION WARNING MODE
Description
In INFINITI QX56 2011 Factory User Guide
DIAGNOSIS SYSTEM (ECM)EC-61
< SYSTEM DESCRIPTION > [VK56VD]
C
D
E
F
G H
I
J
K L
M A
EC
NP
O
ECM blinks MIL for about 10 seconds if all SRT codes are not set.
MALFUNCTION WARNING MODE
Description
In](/img/42/57033/w960_57033-2084.png)
DIAGNOSIS SYSTEM (ECM)EC-61
< SYSTEM DESCRIPTION > [VK56VD]
C
D
E
F
G H
I
J
K L
M A
EC
NP
O
ECM blinks MIL for about 10 seconds if all SRT codes are not set.
MALFUNCTION WARNING MODE
Description
In this function ECM turns on or blinks MIL when it det
ects a malfunction in the emission control system com-
ponents and/or the powertrain control components (which affe ct vehicle emissions) to inform the driver that a
malfunction has been detected.
Operation Procedure
1. Turn ignition switch ON.
2. Check that MIL illuminates. If it remains OFF, check MIL circuit. Refer to EC-515, "
Diagnosis Procedure".
3. Start engine and let it idle. For two trip detection logic diagnoses, ECM turns on MIL when it detects the same malfunction twice in
the two consecutive driving cycles.
For 1st trip detection logic diagnoses, ECM turns on MIL when it detects a malfunction in one driving cycle.
ECM blinks MIL when it detects a malfunction t hat may damage the three way catalyst (misfire).
SELF-DIAGNOSTIC RESULTS MODE
Description
This function allows to indicate DTCs or 1st trip DTCs stored in ECM according to the number of times MIL is
blinking.
How to Set Self-diagnostic Results Mode
NOTE:
It is better to count the time accurately with a clock.
It is impossible to switch the diagnostic mode when an accelerator pedal position sensor circuit has a mal-
function.
After ignition switch is turned off, ECM is a lways released from the “Self-diagnostic results” mode.
1. Confirm that accelerator pedal is fully releas ed, turn ignition switch ON and wait 3 seconds.
2. Repeat the following procedure quickly five times within 5 seconds. Fully depress the accelerator pedal.
Fully release the accelerator pedal.
3. Wait 7 seconds, fully depress the accelerator pedal and keep it depressed for approx. 10 seconds until the
MIL starts blinking.
NOTE:
Do not release the accelerator pedal for 10 seconds if MIL starts blinking during this period. This blinking
is displaying SRT status and is continued for another 10 seconds.
4. Fully release the accelerator pedal. ECM has entered to Self-diagnostic results mode.
JMBIA1515GB
Revision: 2010 May2011 QX56
Page 2172 of 5598
![INFINITI QX56 2011 Factory User Guide
EC-148
< BASIC INSPECTION >[VK56VD]
IDLE AIR VOLUME LEARNING
IDLE AIR VOLUME LEARNING
DescriptionINFOID:0000000006217750
Idle Air Volume Learning is a function of ECM to learn
the idle air volume th INFINITI QX56 2011 Factory User Guide
EC-148
< BASIC INSPECTION >[VK56VD]
IDLE AIR VOLUME LEARNING
IDLE AIR VOLUME LEARNING
DescriptionINFOID:0000000006217750
Idle Air Volume Learning is a function of ECM to learn
the idle air volume th](/img/42/57033/w960_57033-2171.png)
EC-148
< BASIC INSPECTION >[VK56VD]
IDLE AIR VOLUME LEARNING
IDLE AIR VOLUME LEARNING
DescriptionINFOID:0000000006217750
Idle Air Volume Learning is a function of ECM to learn
the idle air volume that keeps engine idle speed within
the specific range. It must be perfo rmed under the following conditions:
Each time the electric throttle control actuator or ECM is replaced.
Idle speed or ignition timing is out of the specification.
Work ProcedureINFOID:0000000006217751
1.PRECONDITIONING
Check that all of the following conditions are satisfied.
Learning will be cancelled if any of the follo wing conditions are missed for even a moment.
Battery voltage: More than 12.9 V (At idle)
Engine coolant temperature: 70 - 105 °C (158 - 221 °F)
Selector lever position: P or N
Electric load switch: OFF
(Air conditioner, headlamp, rear window defogger)
On vehicles equipped with daytime light systems, if the parking brake is applied before the engine is
started the headlamp will not illuminate.
Steering wheel: Neutral (Straight-ahead position)
Vehicle speed: Stopped
Transmission: Warmed-up
- With CONSULT-III: Drive vehicle until “ATF TEMP 2” in “DATA MONITOR” mode of “A/T” system indicates
less than 0.9 V.
- Without CONSULT-III: Drive vehicle for 10 minutes.
Will CONSULT-III be used?
YES >> GO TO 2.
NO >> GO TO 3.
2.PERFORM IDLE AIR VOLUME LEARNING
WITH CONSULT-III
1. Perform Accelerator Pedal Released Position Learning. Refer to EC-146, "
Work Procedure".
2. Perform Throttle Valve Closed Position Learning. EC-147, "
Work Procedure".
3. Start engine and warm it up to normal operating temperature.
4. Select “IDLE AIR VOL LEARN” in “WORK SUPPORT” mode.
5. Touch “START” and wait 20 seconds.
Is
“CMPLT” displayed on CONSULT-III screen?
YES >> GO TO 4.
NO >> GO TO 5.
3.PERFORM IDLE AIR VOLUME LEARNING
WITHOUT CONSULT-III
NOTE:
It is better to count the ti me accurately with a clock.
It is impossible to switch the di agnostic mode when an accelerator pedal position sensor circuit has
a malfunction.
1. Perform Accelerator Pedal Released Position Learning. Refer to EC-146, "
Work Procedure".
2. Perform Throttle Valve Closed Position Learning. EC-147, "
Work Procedure".
3. Start engine and warm it up to normal operating temperature.
4. Turn ignition switch OFF and wait at least 10 seconds.
5. Confirm that accelerator pedal is fully releas ed, turn ignition switch ON and wait 3 seconds.
6. Repeat the following procedure quickly 5 times within 5 seconds.
- Fully depress the accelerator pedal.
- Fully release the accelerator pedal.
7. Wait 7 seconds, fully depress the accelerator pedal for approx. 20 seconds until the MIL stops blinking
and turns ON.
8. Fully release the accelerator pedal within 3 seconds after the MIL turns ON.
Revision: 2010 May2011 QX56
Page 2174 of 5598
![INFINITI QX56 2011 Factory User Guide
EC-150
< BASIC INSPECTION >[VK56VD]
VVEL CONTROL SHAFT POSI
TION SENSOR ADJUSTMENT
VVEL CONTROL SHAFT POSITI ON SENSOR ADJUSTMENT
DescriptionINFOID:0000000006217752
VVEL control shaft position sensor INFINITI QX56 2011 Factory User Guide
EC-150
< BASIC INSPECTION >[VK56VD]
VVEL CONTROL SHAFT POSI
TION SENSOR ADJUSTMENT
VVEL CONTROL SHAFT POSITI ON SENSOR ADJUSTMENT
DescriptionINFOID:0000000006217752
VVEL control shaft position sensor](/img/42/57033/w960_57033-2173.png)
EC-150
< BASIC INSPECTION >[VK56VD]
VVEL CONTROL SHAFT POSI
TION SENSOR ADJUSTMENT
VVEL CONTROL SHAFT POSITI ON SENSOR ADJUSTMENT
DescriptionINFOID:0000000006217752
VVEL control shaft position sensor adjustment is an operat ion to adjust the initial position of the VVEL control
shaft position sensor.
It must be performed each time VVEL ladder assembly is replaced.
CAUTION:
It must be performed only on the replaced bank side.
It must not be performed except when VVEL la dder assembly is replaced. If by any chance the
adjustment is performed, replace VVEL ladder assembly.
Work ProcedureINFOID:0000000006217753
1.START
Will CONSULT-III be used?
Will CONSULT-III be used?
YES >> GO TO 2.
NO >> GO TO 3.
2.PERFORM VVEL CONTROL SHAFT POSITION SENSOR ADJUSTMENT
WITH CONSULT-III
1. Turn ignition switch ON.
2. Select “VVEL POS SEN ADJ PREP” in “WORK SUPPORT” mode with CONSULT-III.
3. Touch “Start” and wait a few seconds.
4. Check that “CMPLT” is displayed on CONSULT-III screen.
5. Select “VVEL POSITION SEN-B1” or “VVEL POSI TION SEN-B2” in “DATA MONITOR” mode with CON-
SULT-III.
6. Loosen the VVEL control shaft position sensor mounting bolts
(1).
7. Turn the VVEL control shaft position sensor (2) clockwise and counterclockwise while monitoring the output voltage of “VVEL
POSITION SEN-B1” or “VVEL POSITION SEN-B2” and adjust
the output voltage to be within the standard value.
8. Tighten the VVEL control shaft position sensor mounting bolts.
9. Reconfirm that the output voltage of “VVEL POSITI ON SEN-B1” or “VVEL POSITION SEN-B2” is within
the standard value.
NOTE:
If it varies from the standard value after the m ounting bolts are tightened, perform steps 6 to 8 again.
10. Turn ignition switch OFF and wait at least 10 seconds.
11. Start engine and warm it up to normal operating temperature.
12. Turn ignition switch OFF and wait at least 10 seconds.
13. Perform idle air volume learning. Refer to EC-148, "
Work Procedure".
>> INSPECTION END
3.PERFORM VVEL CONTROL SHAFT POSITION SENSOR ADJUSTMENT
WITHOUT CONSULT-III
1. Disconnect VVEL control shaft position sensor harness connector.
2. Remove VVEL actuator motor relay.
3. Turn ignition switch ON, wait at least 5 seconds and then turn it OFF. Voltage: 500
± 48 mV
: 7.0 Nm (0.71 kg-m, 62 in-lb)
Voltage: 500 ± 48 mV
JSBIA0533ZZ
Revision: 2010 May2011 QX56
Page 2175 of 5598
![INFINITI QX56 2011 Factory User Guide
VVEL CONTROL SHAFT POSITION SENSOR ADJUSTMENT
EC-151
< BASIC INSPECTION > [VK56VD]
C
D
E
F
G H
I
J
K L
M A
EC
NP
O
4. Reconnect all harness connectors disconnected.
5. Install VVEL actuator motor rel INFINITI QX56 2011 Factory User Guide
VVEL CONTROL SHAFT POSITION SENSOR ADJUSTMENT
EC-151
< BASIC INSPECTION > [VK56VD]
C
D
E
F
G H
I
J
K L
M A
EC
NP
O
4. Reconnect all harness connectors disconnected.
5. Install VVEL actuator motor rel](/img/42/57033/w960_57033-2174.png)
VVEL CONTROL SHAFT POSITION SENSOR ADJUSTMENT
EC-151
< BASIC INSPECTION > [VK56VD]
C
D
E
F
G H
I
J
K L
M A
EC
NP
O
4. Reconnect all harness connectors disconnected.
5. Install VVEL actuator motor relay.
6. Turn ignition switch ON and wait at least 5 seconds.
7. Loosen the VVEL control shaft position sensor mounting bolts
(1).
8. Turn the VVEL control shaft position sensor (2) clockwise and
counterclockwise while monitoring the output voltage between
the VVEL control module terminals with a tester and adjust the
output voltage to be within the standard value.
9. Tighten the VVEL control shaft position sensor mounting bolts.
10. Reconfirm that the output voltage of VVEL contro l shaft position sensor is within the standard value.
NOTE:
If it varies from the standard value after the m ounting bolts are tightened, perform steps 7 to 9 again.
11. Turn ignition switch OFF and wait at least 10 seconds.
12. Start engine and warm it up to normal operating temperature.
13. Turn ignition switch OFF and wait at least 10 seconds.
14. Perform Idle Air Volume Learning. Refer to EC-148, "
Work Procedure".
>> INSPECTION END
JSBIA0533ZZ
VVEL control module Voltage
Bank Connector +–
Terminal Terminal
1 F56 36
500 ± 48 mV
254
: 7.0 Nm (0.71 kg-m, 62 in-lb)
VVEL control module
Voltage
Bank Connector +–
Terminal Terminal
1 F56 3 6
500 ± 48 mV
254
Revision: 2010 May2011 QX56
Page 2372 of 5598
![INFINITI QX56 2011 Factory User Guide
EC-348
< DTC/CIRCUIT DIAGNOSIS >[VK56VD]
P0456 EVAP CONTROL SYSTEM
2.CHECK FUEL FILLER CAP INSTALLATION
Check that the cap is tightened proper ly by rotating the cap clockwise.
Is the inspection resu INFINITI QX56 2011 Factory User Guide
EC-348
< DTC/CIRCUIT DIAGNOSIS >[VK56VD]
P0456 EVAP CONTROL SYSTEM
2.CHECK FUEL FILLER CAP INSTALLATION
Check that the cap is tightened proper ly by rotating the cap clockwise.
Is the inspection resu](/img/42/57033/w960_57033-2371.png)
EC-348
< DTC/CIRCUIT DIAGNOSIS >[VK56VD]
P0456 EVAP CONTROL SYSTEM
2.CHECK FUEL FILLER CAP INSTALLATION
Check that the cap is tightened proper ly by rotating the cap clockwise.
Is the inspection result normal?
YES >> GO TO 3.
NO >> Open fuel filler cap, then clean cap and fuel filler neck threads using air blower. Then retighten until reteaching sound is heard.
3.CHECK FUEL FILLER CAP FUNCTION
Check for air releasing sound while opening the fuel filler cap.
Is the inspection result normal?
YES >> GO TO 5.
NO >> GO TO 4.
4.CHECK FUEL TANK VACUUM RELIEF VALVE
Refer to EC-350, "
Component Inspection (Fuel Filler Cap)".
Is the inspection result normal?
YES >> GO TO 5.
NO >> Replace fuel filler cap with a genuine one.
5.CHECK FOR EVAP LEAK
Refer to FL-12, "
Inspection".
Is there any leak in EVAP line?
YES >> Repair or replace.
NO >> GO TO 6.
6.CHECK EVAP CANISTER VENT CONTROL VALVE
Check the following.
EVAP canister vent control valve is installed properly. Refer to FL-10, "
Exploded View".
EVAP canister vent control valve. Refer to EC-327, "
Component Inspection (EVAP Cani ster Vent Control Valve)".
Is the inspection result normal?
YES >> GO TO 7.
NO >> Repair or replace EVAP canister vent control valve and O-ring. Refer to FL-10, "
Exploded View".
7.CHECK IF EVAP CANISTER SATURATED WITH WATER
1. Remove EVAP canister (1) with EVAP canister vent control valve (2) and EVAP control system pressure sensor attached.
2. Check if water will drain from the EVAP canister.
Does water drain from EVAP canister?
YES >> GO TO 8.
NO-1 >> With CONSULT-III: GO TO 10.
NO-2 >> Without CONSULT-III: GO TO 11.
8.CHECK EVAP CANISTER
Weigh the EVAP canister assembly with the EVAP canister vent control valve and EVAP control system pres-
sure sensor attached. Refer to FL-10, "
Exploded View".
The weight should be less than 2.5 kg (5.5 lb).
Is the inspection result normal?
YES-1 >> With CONSULT-III: GO TO 10.
YES-2 >> Without CONSULT-III: GO TO 11.
NO >> GO TO 9.
JSBIA0692ZZ
Revision: 2010 May2011 QX56
Page 2575 of 5598
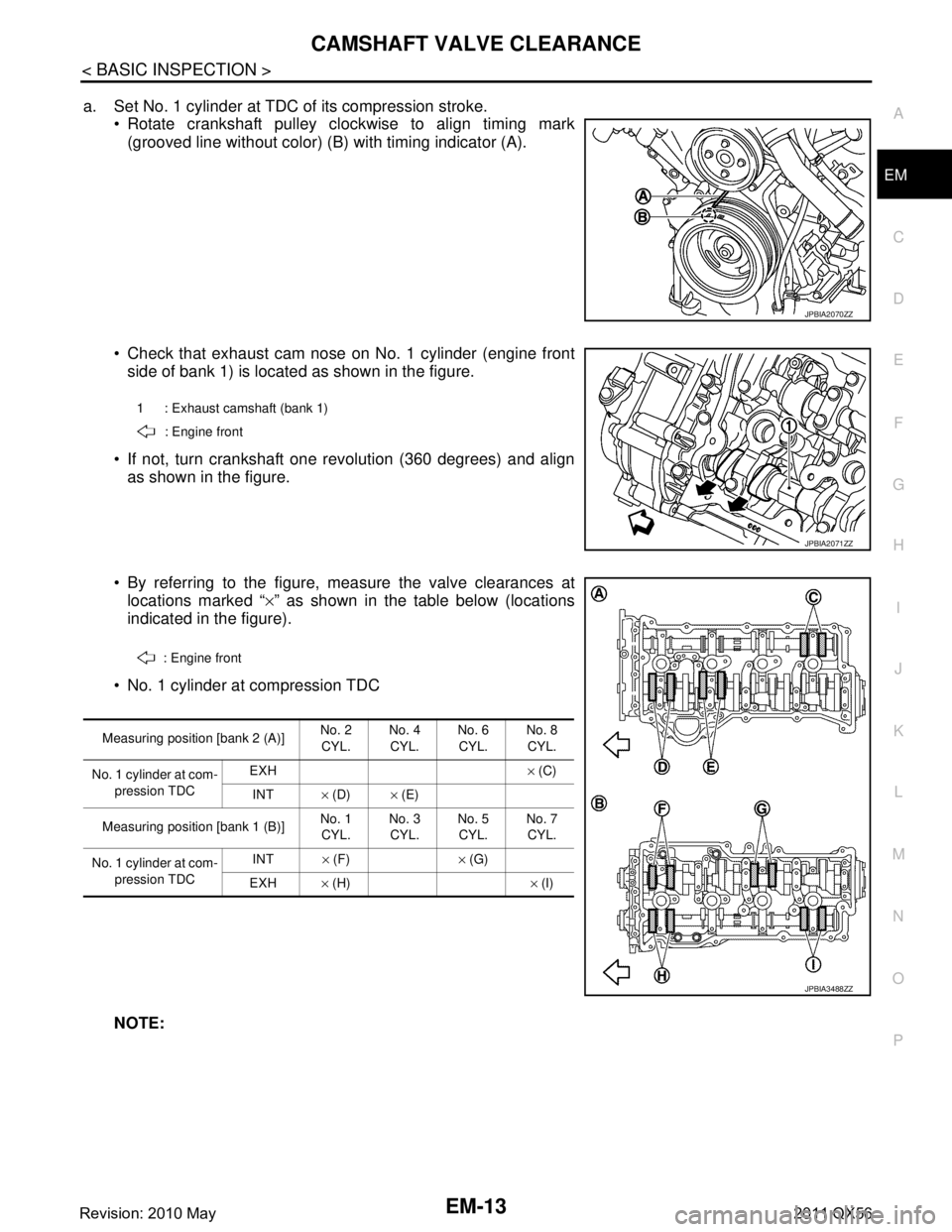
CAMSHAFT VALVE CLEARANCEEM-13
< BASIC INSPECTION >
C
DE
F
G H
I
J
K L
M A
EM
NP
O
a. Set No. 1 cylinder at TDC of its compression stroke.
Rotate crankshaft pulley clockwise to align timing mark
(grooved line without color) (B) with timing indicator (A).
Check that exhaust cam nose on No. 1 cylinder (engine front side of bank 1) is located as shown in the figure.
If not, turn crankshaft one revolution (360 degrees) and align as shown in the figure.
By referring to the figure, measure the valve clearances at locations marked “ ×” as shown in the table below (locations
indicated in the figure).
No. 1 cylinder at compression TDC
NOTE:
JPBIA2070ZZ
1 : Exhaust camshaft (bank 1) : Engine front
JPBIA2071ZZ
: Engine front
Measuring position [bank 2 (A)] No. 2
CYL. No. 4
CYL. No. 6
CYL. No. 8
CYL.
No. 1 cylinder at com- pression TDC EXH
× (C)
INT × (D) × (E)
Measuring position [bank 1 (B)] No. 1
CYL. No. 3
CYL. No. 5
CYL. No. 7
CYL.
No. 1 cylinder at com- pression TDC INT
× (F) × (G)
EXH × (H) × (I)
JPBIA3488ZZ
Revision: 2010 May2011 QX56
Page 2576 of 5598
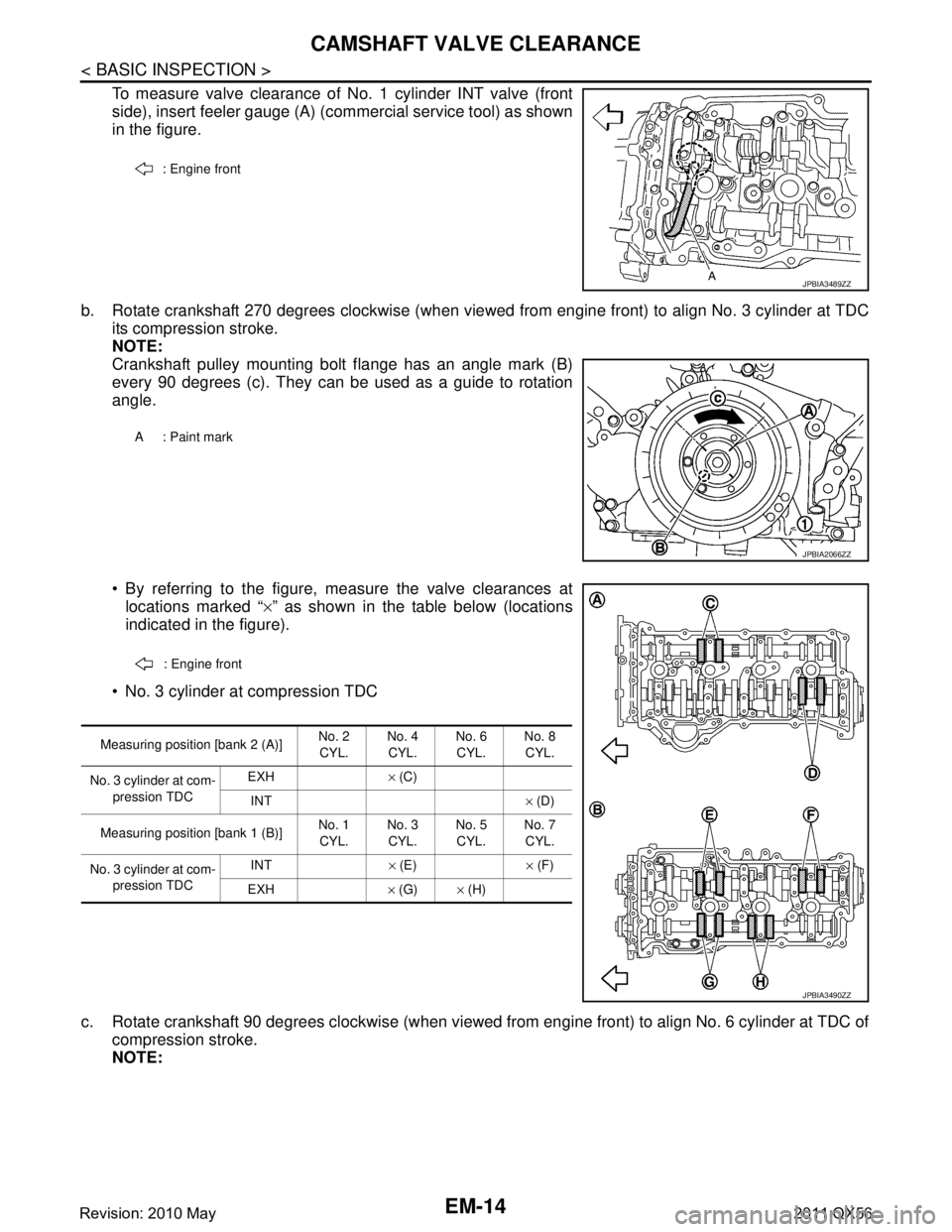
EM-14
< BASIC INSPECTION >
CAMSHAFT VALVE CLEARANCE
To measure valve clearance of No. 1 cylinder INT valve (front
side), insert feeler gauge (A) (commercial service tool) as shown
in the figure.
b. Rotate crankshaft 270 degrees clockwise (when viewed from engine front) to align No. 3 cylinder at TDC its compression stroke.
NOTE:
Crankshaft pulley mounting bolt flange has an angle mark (B)
every 90 degrees (c). They can be used as a guide to rotation
angle.
By referring to the figure, measure the valve clearances atlocations marked “ ×” as shown in the table below (locations
indicated in the figure).
No. 3 cylinder at compression TDC
c. Rotate crankshaft 90 degrees clockwise (when viewed from engine front) to align No. 6 cylinder at TDC of compression stroke.
NOTE:
: Engine front
JPBIA3489ZZ
A : Paint mark
JPBIA2066ZZ
: Engine front
Measuring position [bank 2 (A)] No. 2
CYL. No. 4
CYL. No. 6
CYL. No. 8
CYL.
No. 3 cylinder at com- pression TDC EXH
× (C)
INT × (D)
Measuring position [bank 1 (B)] No. 1
CYL. No. 3
CYL. No. 5
CYL. No. 7
CYL.
No. 3 cylinder at com- pression TDC INT
× (E) × (F)
EXH × (G) × (H)
JPBIA3490ZZ
Revision: 2010 May2011 QX56
Page 2583 of 5598
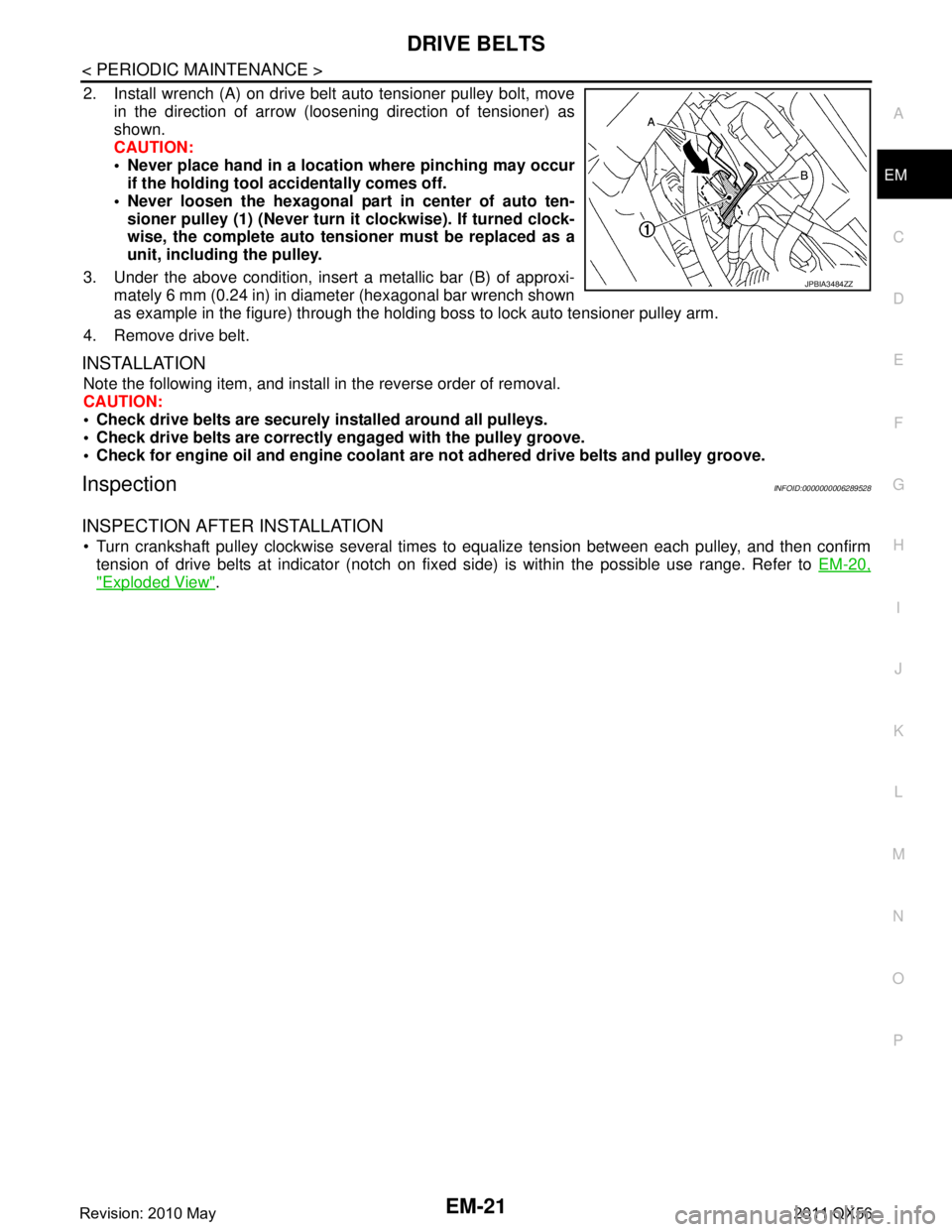
DRIVE BELTSEM-21
< PERIODIC MAINTENANCE >
C
DE
F
G H
I
J
K L
M A
EM
NP
O
2. Install wrench (A) on drive belt auto tensioner pulley bolt, move
in the direction of arrow (loosening direction of tensioner) as
shown.
CAUTION:
Never place hand in a location where pinching may occurif the holding tool accidentally comes off.
Never loosen the hexagonal part in center of auto ten- sioner pulley (1) (Never turn it clockwise). If turned clock-
wise, the complete auto tensioner must be replaced as a
unit, including the pulley.
3. Under the above condition, insert a metallic bar (B) of approxi- mately 6 mm (0.24 in) in diameter (hexagonal bar wrench shown
as example in the figure) through the holding boss to lock auto tensioner pulley arm.
4. Remove drive belt.
INSTALLATION
Note the following item, and install in the reverse order of removal.
CAUTION:
Check drive belts are securely installed around all pulleys.
Check drive belts are correctly engaged with the pulley groove.
Check for engine oil and engine coolant ar e not adhered drive belts and pulley groove.
InspectionINFOID:0000000006289528
INSPECTION AFTER INSTALLATION
Turn crankshaft pulley clockwise several times to equalize tension between each pulley, and then confirm
tension of drive belts at indicator (notch on fixed side) is within the possible use range. Refer to EM-20,
"Exploded View".
JPBIA3484ZZ
Revision: 2010 May2011 QX56
Page 2588 of 5598
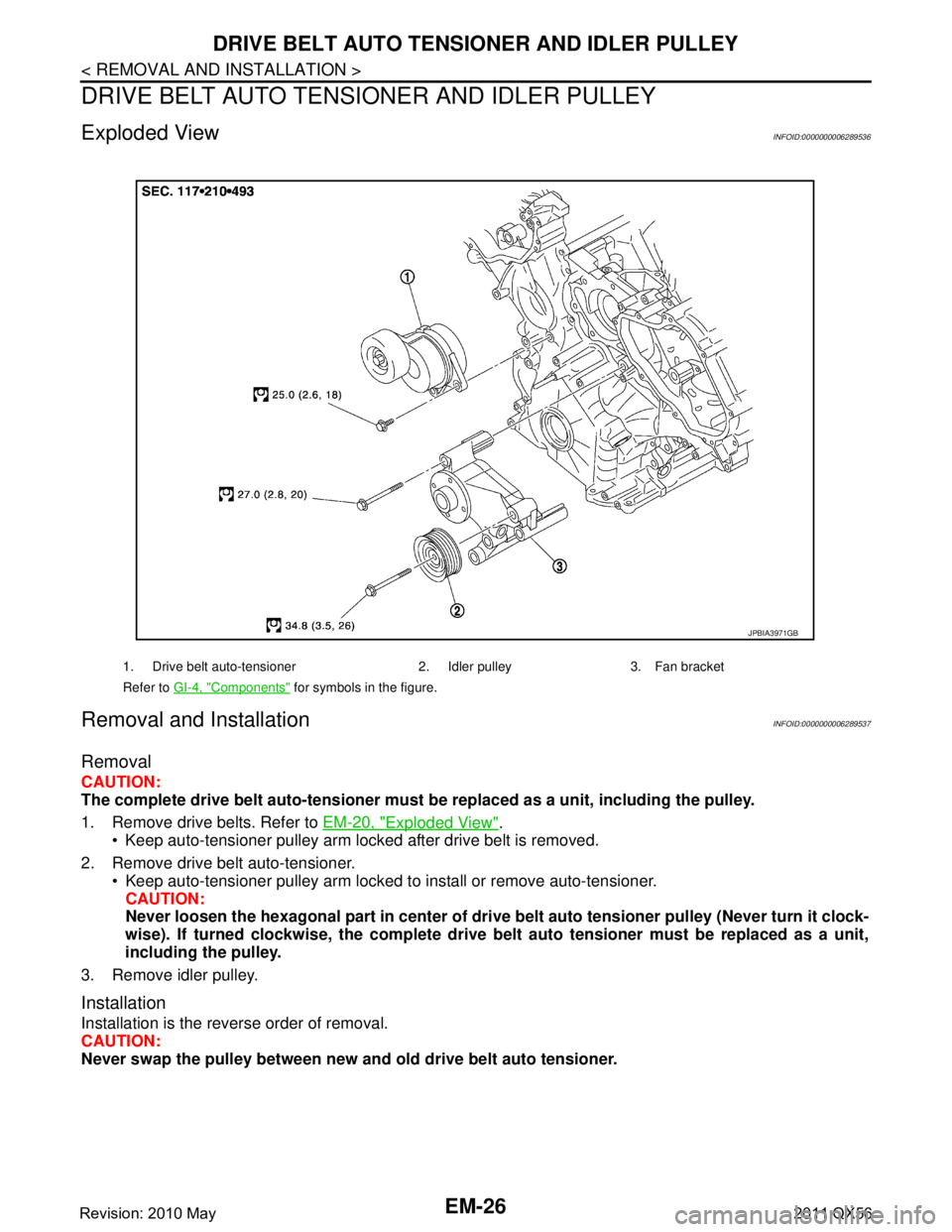
EM-26
< REMOVAL AND INSTALLATION >
DRIVE BELT AUTO TENSIONER AND IDLER PULLEY
DRIVE BELT AUTO TENSI ONER AND IDLER PULLEY
Exploded ViewINFOID:0000000006289536
Removal and InstallationINFOID:0000000006289537
Removal
CAUTION:
The complete drive belt auto-tensioner must be replaced as a unit, including the pulley.
1. Remove drive belts. Refer to EM-20, "
Exploded View".
Keep auto-tensioner pulley arm locked after drive belt is removed.
2. Remove drive belt auto-tensioner. Keep auto-tensioner pulley arm locked to install or remove auto-tensioner.CAUTION:
Never loosen the hexagonal part in center of dri ve belt auto tensioner pulley (Never turn it clock-
wise). If turned clockwise, the complete drive belt auto tensioner must be replaced as a unit,
including the pulley.
3. Remove idler pulley.
Installation
Installation is the reverse order of removal.
CAUTION:
Never swap the pulley between new an d old drive belt auto tensioner.
1. Drive belt auto-tensioner 2. Idler pulley 3. Fan bracket
Refer to GI-4, "
Components" for symbols in the figure.
JPBIA3971GB
Revision: 2010 May2011 QX56
Page 2612 of 5598
![INFINITI QX56 2011 Factory User Guide
EM-50
< REMOVAL AND INSTALLATION >
FUEL INJECTOR AND FUEL TUBE
c. Press down body portion (A) of injector remover [SST:KV10119600 (—)] until it contacts cylinder head.
d. Tighten injector remover INFINITI QX56 2011 Factory User Guide
EM-50
< REMOVAL AND INSTALLATION >
FUEL INJECTOR AND FUEL TUBE
c. Press down body portion (A) of injector remover [SST:KV10119600 (—)] until it contacts cylinder head.
d. Tighten injector remover](/img/42/57033/w960_57033-2611.png)
EM-50
< REMOVAL AND INSTALLATION >
FUEL INJECTOR AND FUEL TUBE
c. Press down body portion (A) of injector remover [SST:KV10119600 (—)] until it contacts cylinder head.
d. Tighten injector remover [SST: KV10119600 (—)] clockwise and remove injector from cylinder head.
e. Cut Teflon seal (1) while pinching it. Be careful not to damage injector.
f. Remove insulator from mounting ho le of fuel injector of cylinder
head.
INSTALLATION
1. Install seal ring to fuel injector as per the following: CAUTION:
Handle seal ring with bare hands. Never wear gloves.
Never apply engine oil to seal ring.
Never clean seal ring with solvent.
JPBIA3747ZZ
JPBIA3748ZZ
JSBIA0346ZZ
Revision: 2010 May2011 QX56