service INFINITI QX56 2011 Factory Service Manual
[x] Cancel search | Manufacturer: INFINITI, Model Year: 2011, Model line: QX56, Model: INFINITI QX56 2011Pages: 5598, PDF Size: 94.53 MB
Page 3062 of 5598
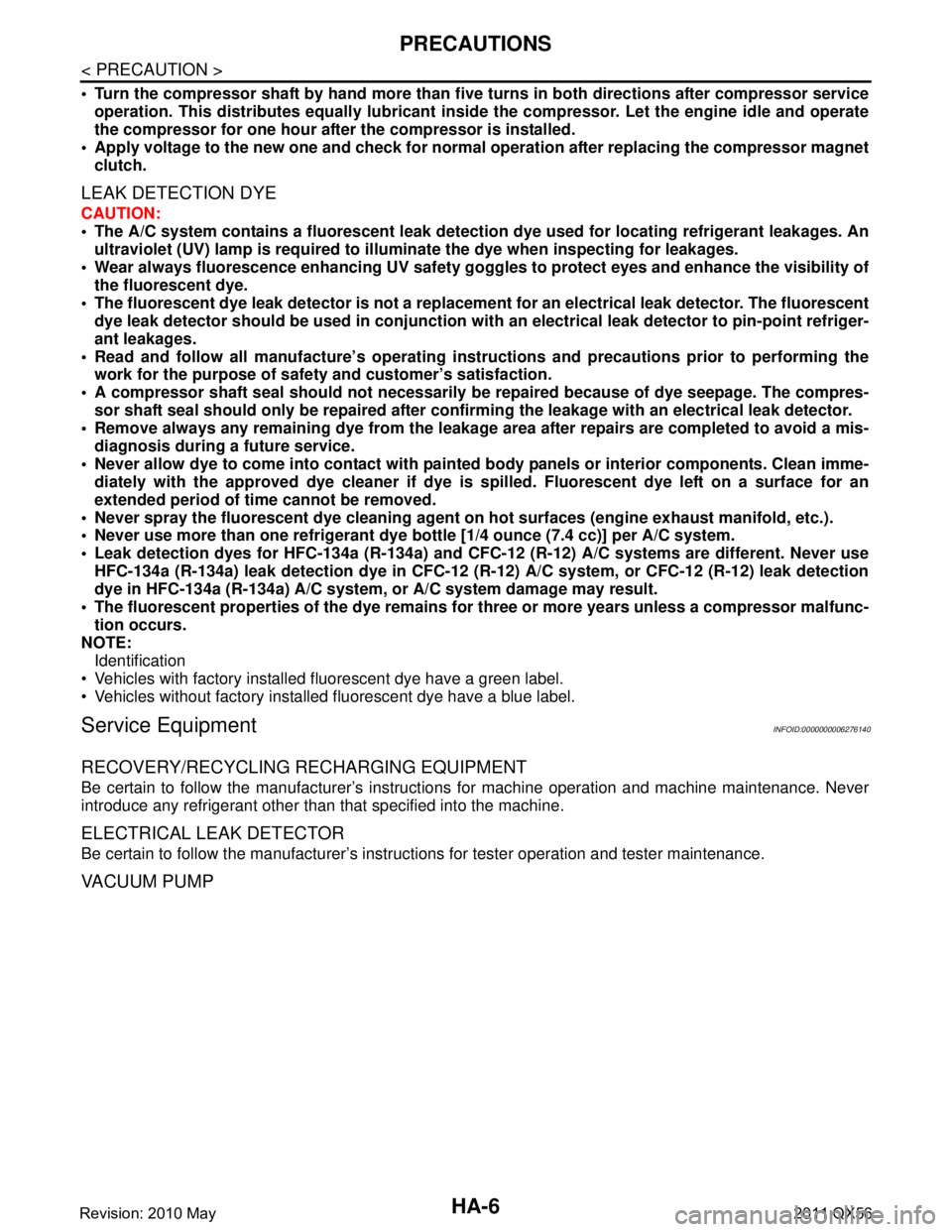
HA-6
< PRECAUTION >
PRECAUTIONS
Turn the compressor shaft by hand more than five turns in both directions after compressor service
operation. This distributes equall y lubricant inside the compressor. Let the engine idle and operate
the compressor for one hour after the compressor is installed.
Apply voltage to the new one and check for norma l operation after replacing the compressor magnet
clutch.
LEAK DETECTION DYE
CAUTION:
The A/C system contains a fluorescent leak detect ion dye used for locating refrigerant leakages. An
ultraviolet (UV) lamp is required to il luminate the dye when inspecting for leakages.
Wear always fluorescence enhancing UV safety goggles to protect eyes and enhance the visibility of
the fluorescent dye.
The fluorescent dye leak detector is not a replacem ent for an electrical leak detector. The fluorescent
dye leak detector should be used in conjunction with an electrical leak detector to pin-point refriger-
ant leakages.
Read and follow all manufacture’ s operating instructions and precau tions prior to performing the
work for the purpose of safet y and customer’s satisfaction.
A compressor shaft seal should not necessarily be repaired because of dye seepage. The compres-
sor shaft seal should only be repaired after conf irming the leakage with an electrical leak detector.
Remove always any remaining dye from the leakage area after repairs are completed to avoid a mis-
diagnosis during a future service.
Never allow dye to come into contact with painted body panels or interior components. Clean imme-
diately with the approved dye cl eaner if dye is spilled. Fluorescent dye left on a surface for an
extended period of time cannot be removed.
Never spray the fluorescent dye cleaning agent on hot surfaces (eng ine exhaust manifold, etc.).
Never use more than one refrigerant dye bottle [1/4 ounce (7.4 cc)] per A/C system.
Leak detection dyes for HFC-134a (R-134a) and CFC- 12 (R-12) A/C systems are different. Never use
HFC-134a (R-134a) leak detection dye in CFC-12 (R- 12) A/C system, or CFC-12 (R-12) leak detection
dye in HFC-134a (R-134a) A/C system, or A/C system damage may result.
The fluorescent properties of the dye remains fo r three or more years unless a compressor malfunc-
tion occurs.
NOTE:
Identification
Vehicles with factory installed fluorescent dye have a green label.
Vehicles without factory installed fluorescent dye have a blue label.
Service EquipmentINFOID:0000000006276140
RECOVERY/RECYCLING RECHARGING EQUIPMENT
Be certain to follow the manufacturer’s instructions for machine operation and machine maintenance. Never
introduce any refrigerant other than that specified into the machine.
ELECTRICAL LEAK DETECTOR
Be certain to follow the manufacturer’s instruct ions for tester operation and tester maintenance.
VACUUM PUMP
Revision: 2010 May2011 QX56
Page 3063 of 5598
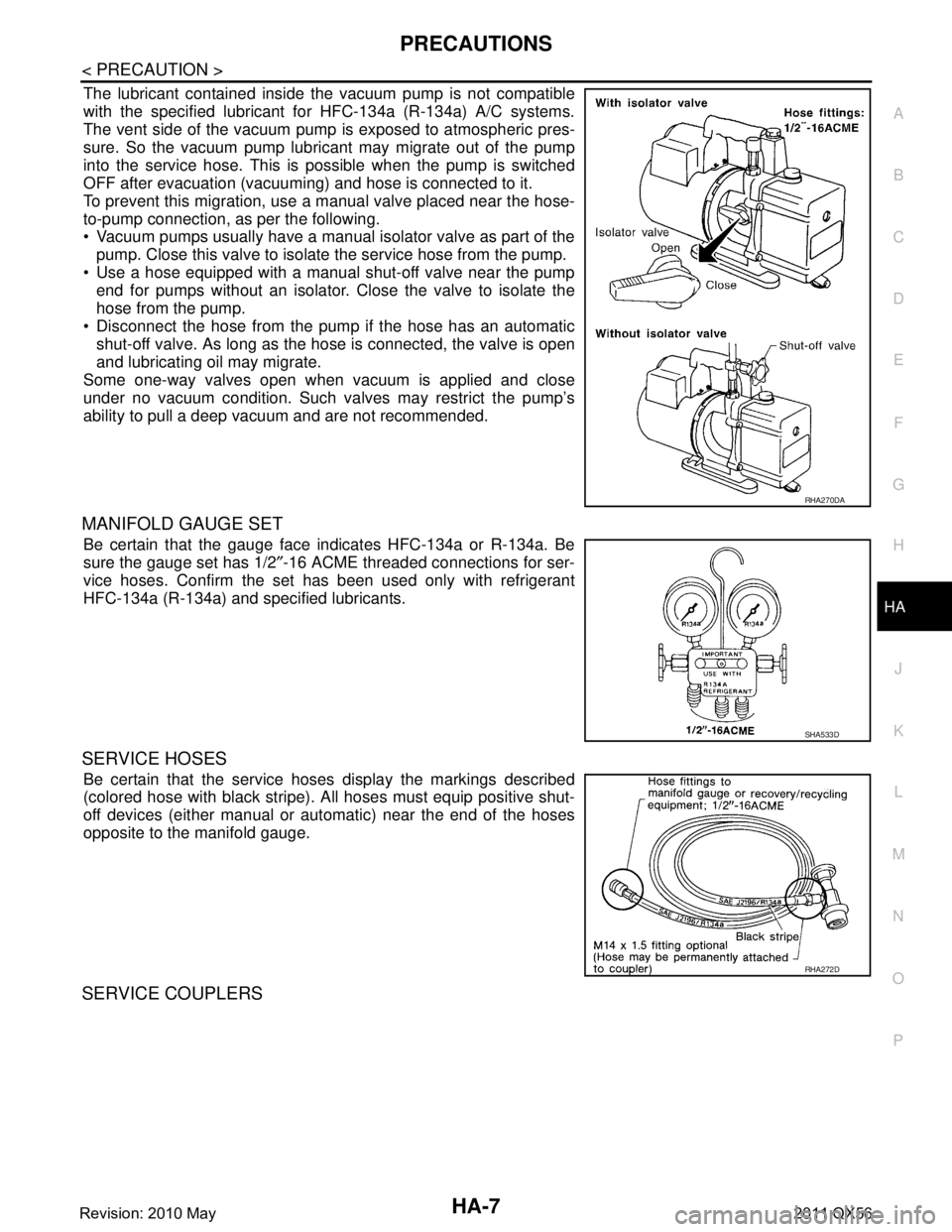
PRECAUTIONSHA-7
< PRECAUTION >
C
DE
F
G H
J
K L
M A
B
HA
N
O P
The lubricant contained inside the vacuum pump is not compatible
with the specified lubricant for HFC-134a (R-134a) A/C systems.
The vent side of the vacuum pump is exposed to atmospheric pres-
sure. So the vacuum pump lubricant may migrate out of the pump
into the service hose. This is possible when the pump is switched
OFF after evacuation (vacuuming) and hose is connected to it.
To prevent this migration, use a manual valve placed near the hose-
to-pump connection, as per the following.
Vacuum pumps usually have a manual isolator valve as part of the
pump. Close this valve to isolate the service hose from the pump.
Use a hose equipped with a manual shut-off valve near the pump end for pumps without an isolator. Close the valve to isolate the
hose from the pump.
Disconnect the hose from the pum p if the hose has an automatic
shut-off valve. As long as the hose is connected, the valve is open
and lubricating oil may migrate.
Some one-way valves open when vacuum is applied and close
under no vacuum condition. Such valves may restrict the pump’s
ability to pull a deep vacuum and are not recommended.
MANIFOLD GAUGE SET
Be certain that the gauge face indicates HFC-134a or R-134a. Be
sure the gauge set has 1/2 ″-16 ACME threaded connections for ser-
vice hoses. Confirm the set has been used only with refrigerant
HFC-134a (R-134a) and specified lubricants.
SERVICE HOSES
Be certain that the service hoses display the markings described
(colored hose with black stripe). A ll hoses must equip positive shut-
off devices (either manual or automatic) near the end of the hoses
opposite to the manifold gauge.
SERVICE COUPLERS
RHA270DA
SHA533D
RHA272D
Revision: 2010 May2011 QX56
Page 3064 of 5598
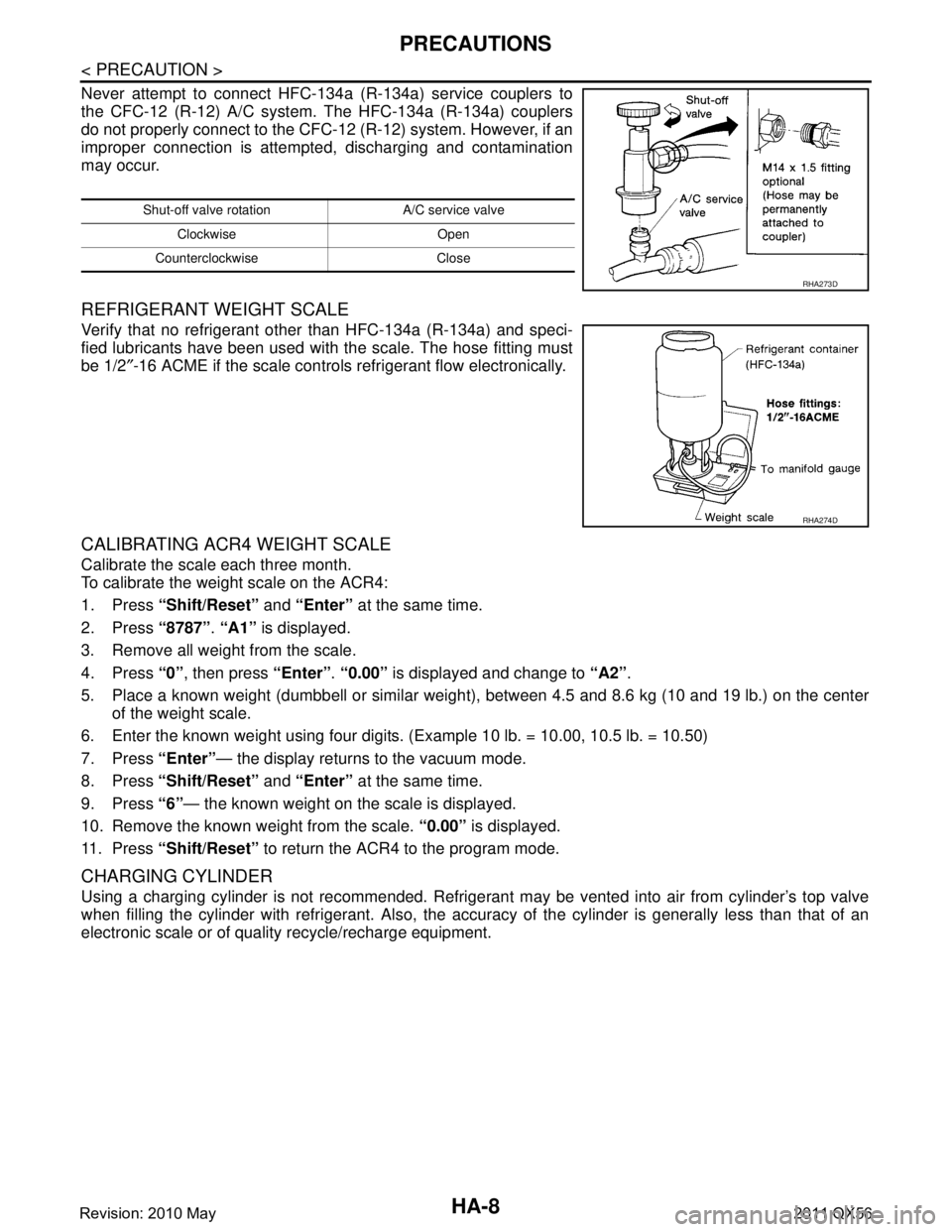
HA-8
< PRECAUTION >
PRECAUTIONS
Never attempt to connect HFC-134a (R-134a) service couplers to
the CFC-12 (R-12) A/C system. The HFC-134a (R-134a) couplers
do not properly connect to the CFC-12 (R-12) system. However, if an
improper connection is attempted, discharging and contamination
may occur.
REFRIGERANT WEIGHT SCALE
Verify that no refrigerant other than HFC-134a (R-134a) and speci-
fied lubricants have been used with the scale. The hose fitting must
be 1/2″-16 ACME if the scale controls refrigerant flow electronically.
CALIBRATING ACR4 WEIGHT SCALE
Calibrate the scale each three month.
To calibrate the weight scale on the ACR4:
1. Press “Shift/Reset” and “Enter” at the same time.
2. Press “8787”. “A1” is displayed.
3. Remove all weight from the scale.
4. Press “0”, then press “Enter”. “0.00” is displayed and change to “A2”.
5. Place a known weight (dumbbell or similar weight ), between 4.5 and 8.6 kg (10 and 19 lb.) on the center
of the weight scale.
6. Enter the known weight using four digi ts. (Example 10 lb. = 10.00, 10.5 lb. = 10.50)
7. Press “Enter”— the display returns to the vacuum mode.
8. Press “Shift/Reset” and “Enter” at the same time.
9. Press “6”— the known weight on the scale is displayed.
10. Remove the known weight from the scale. “0.00” is displayed.
11. Press “Shift/Reset” to return the ACR4 to the program mode.
CHARGING CYLINDER
Using a charging cylinder is not recommended. Refrigerant may be vented into air from cylinder’s top valve
when filling the cylinder with refrigerant. Also, the accu racy of the cylinder is generally less than that of an
electronic scale or of quality recycle/recharge equipment.
Shut-off valve rotati on A/C service valve
Clockwise Open
Counterclockwise Close
RHA273D
RHA274D
Revision: 2010 May2011 QX56
Page 3065 of 5598
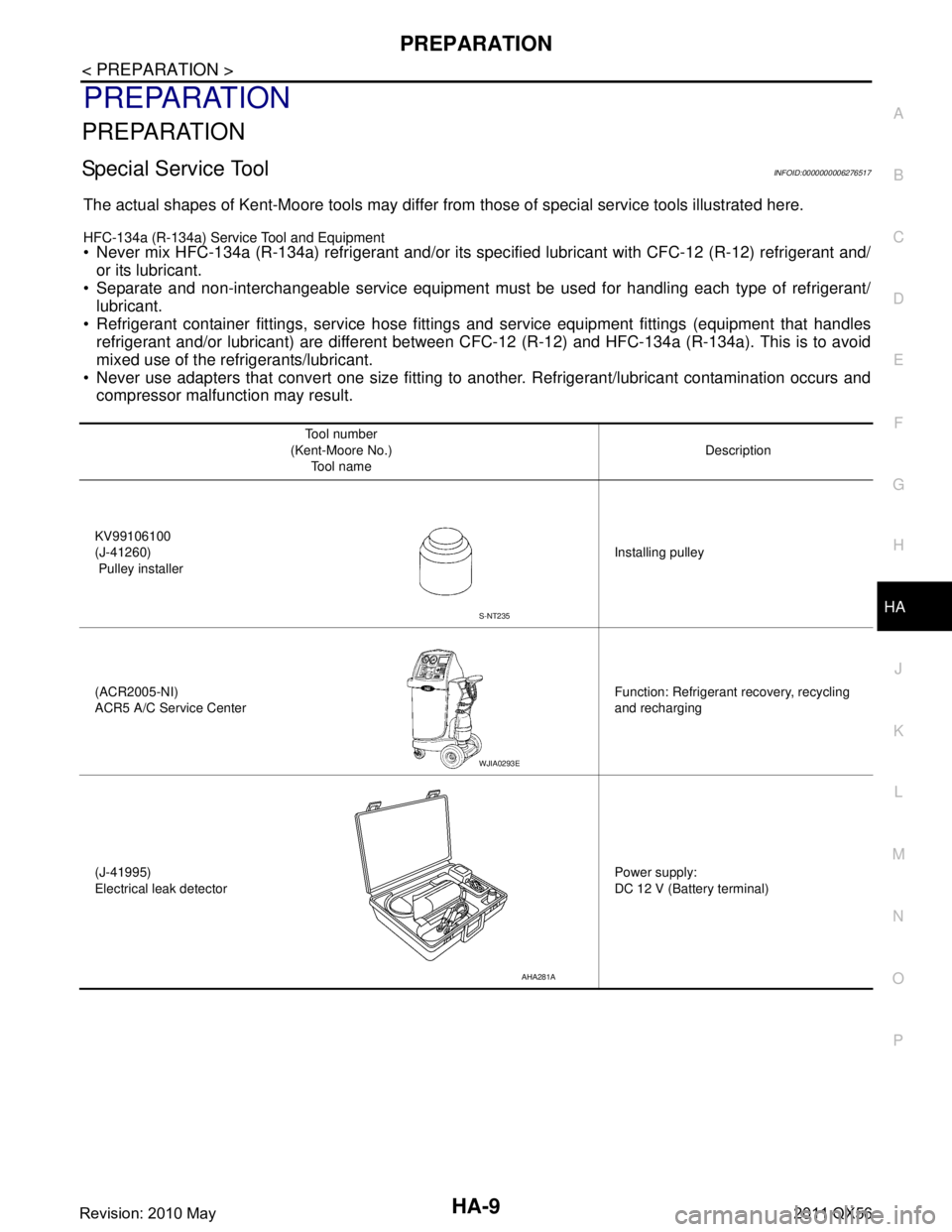
PREPARATIONHA-9
< PREPARATION >
C
DE
F
G H
J
K L
M A
B
HA
N
O P
PREPARATION
PREPARATION
Special Service ToolINFOID:0000000006276517
The actual shapes of Kent-Moore tools may differ fr om those of special service tools illustrated here.
HFC-134a (R-134a) Service Tool and Equipment
Never mix HFC-134a (R-134a) refrigerant and/or its spec ified lubricant with CFC-12 (R-12) refrigerant and/
or its lubricant.
Separate and non-interchangeable service equipment must be used for handling each type of refrigerant/
lubricant.
Refrigerant container fittings, service hose fittings and service equipment fittings (equipment that handles
refrigerant and/or lubricant) are different between CF C-12 (R-12) and HFC-134a (R-134a). This is to avoid
mixed use of the refrigerants/lubricant.
Never use adapters that convert one size fitting to another. Refrigerant/lubricant contamination occurs and
compressor malfunction may result.
Tool number
(Kent-Moore No.) Tool name Description
KV99106100
(J-41260)
Pulley installer Installing pulley
(ACR2005-NI)
ACR5 A/C Se rvice Center Function: Refrigerant recovery, recycling
and recharging
(J-41995)
Electrical leak detector Power supply:
DC 12 V (Battery terminal)
S-NT235
WJIA0293E
AHA281A
Revision: 2010 May2011 QX56
Page 3067 of 5598
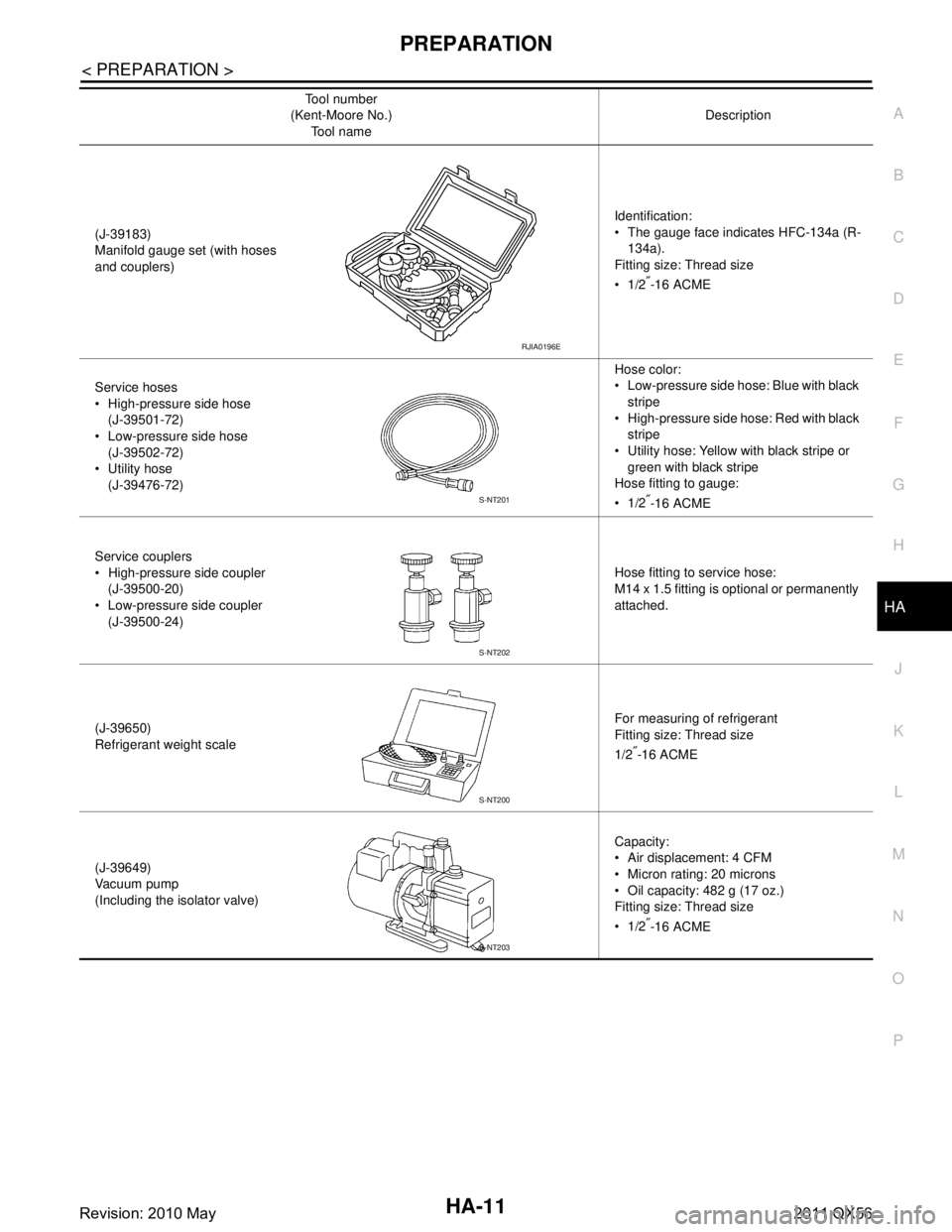
PREPARATIONHA-11
< PREPARATION >
C
DE
F
G H
J
K L
M A
B
HA
N
O P
(J-39183)
Manifold gauge set (with hoses
and couplers) Identification:
The gauge face indicates HFC-134a (R-
134a).
Fitting size: Thread size
1/2
″-16 ACME
Service hoses
High-pressure side hose (J-39501-72)
Low-pressure side hose
(J-39502-72)
Utility hose (J-39476-72) Hose color:
Low-pressure side hose: Blue with black
stripe
High-pressure side hose: Red with black stripe
Utility hose: Yellow with black stripe or
green with black stripe
Hose fitting to gauge:
1/2
″-16 ACME
Service couplers
High-pressure side coupler (J-39500-20)
Low-pressure side coupler (J-39500-24) Hose fitting to service hose:
M14 x 1.5 fitting is optional or permanently
attached.
(J-39650)
Refrigerant weight scale For measuring of refrigerant
Fitting size: Thread size
1/2
″-16 ACME
(J-39649)
Va c u u m p u m p
(Including the isolator valve) Capacity:
Air displacement: 4 CFM
Micron rating: 20 microns
Oil capacity: 482 g (17 oz.)
Fitting size: Thread size
1/2
″-16 ACME
Tool number
(Kent-Moore No.)
Tool name Description
RJIA0196E
S-NT201
S-NT202
S-NT200
S-NT203
Revision: 2010 May2011 QX56
Page 3068 of 5598
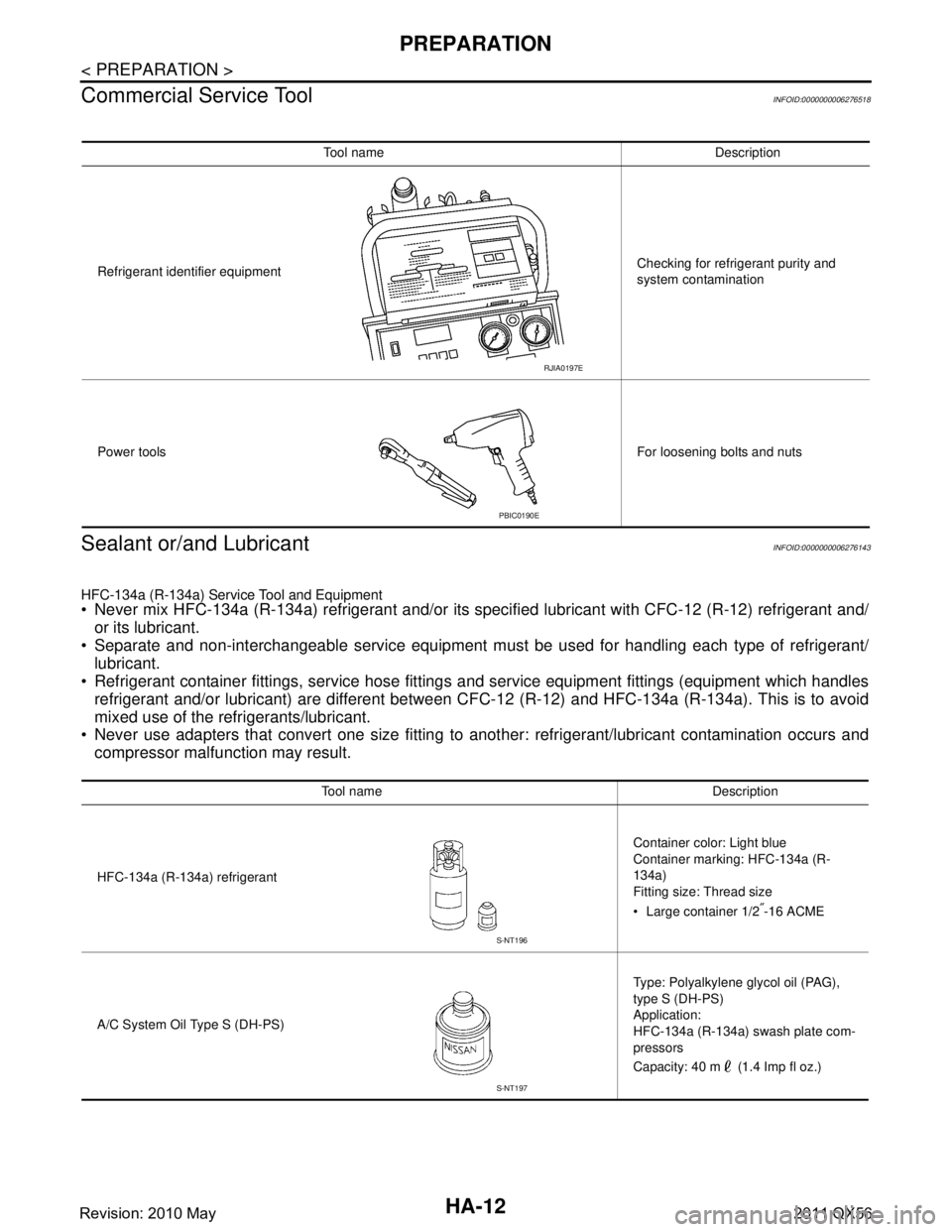
HA-12
< PREPARATION >
PREPARATION
Commercial Service Tool
INFOID:0000000006276518
Sealant or/and LubricantINFOID:0000000006276143
HFC-134a (R-134a) Service Tool and Equipment
Never mix HFC-134a (R-134a) refrigerant and/or its s pecified lubricant with CFC-12 (R-12) refrigerant and/
or its lubricant.
Separate and non-interchangeable service equipment must be used for handling each type of refrigerant/ lubricant.
Refrigerant container fittings, service hose fittings and service equipment fittings (equipment which handles
refrigerant and/or lubricant) are different between CF C-12 (R-12) and HFC-134a (R-134a). This is to avoid
mixed use of the refrigerants/lubricant.
Never use adapters that convert one size fitting to another: refrigerant/lubricant contamination occurs and
compressor malfunction may result.
Tool name Description
Refrigerant identifier equipment Checking for refrigerant purity and
system contamination
Power tools For loosening bolts and nuts
RJIA0197E
PBIC0190E
Tool name Description
HFC-134a (R-134a) refrigerant Container color: Light blue
Container marking: HFC-134a (R-
134a)
Fitting size: Thread size
Large container 1/2
″-16 ACME
A/C System Oil Type S (DH-PS) Type: Polyalkylene glycol oil (PAG),
type S (DH-PS)
Application:
HFC-134a (R-134a) swash plate com-
pressors
Capacity: 40 m (1.4 Imp fl oz.)
S-NT196
S-NT197
Revision: 2010 May2011 QX56
Page 3074 of 5598
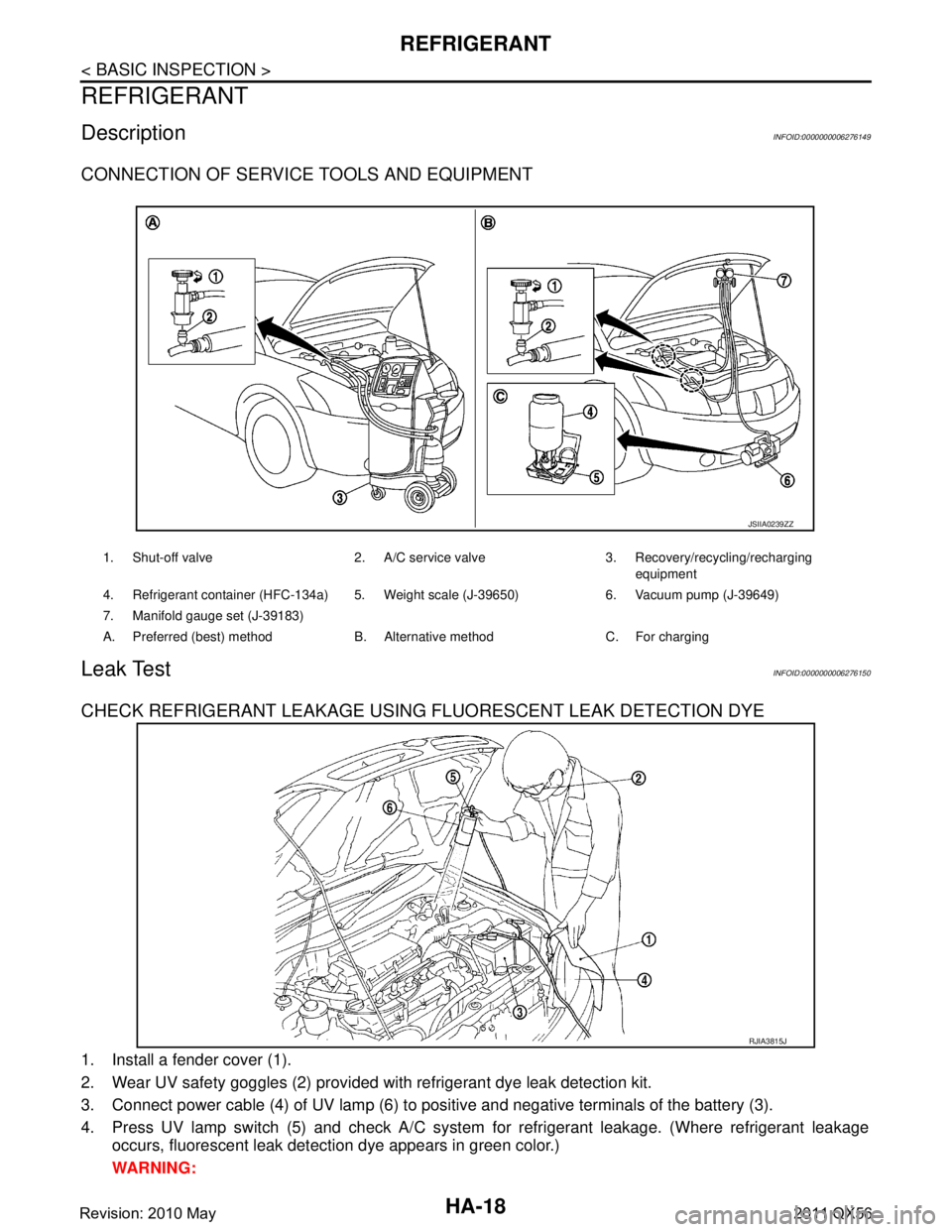
HA-18
< BASIC INSPECTION >
REFRIGERANT
REFRIGERANT
DescriptionINFOID:0000000006276149
CONNECTION OF SERVICE TOOLS AND EQUIPMENT
Leak TestINFOID:0000000006276150
CHECK REFRIGERANT LEAKAGE USING FLUORESCENT LEAK DETECTION DYE
1. Install a fender cover (1).
2. Wear UV safety goggles (2) provided with refrigerant dye leak detection kit.
3. Connect power cable (4) of UV lamp (6) to positive and negative terminals of the battery (3).
4. Press UV lamp switch (5) and check A/C system for refrigerant leakage. (Where refrigerant leakage
occurs, fluorescent leak detec tion dye appears in green color.)
WARNING:
1. Shut-off valve 2. A/C service valve 3. Recovery/recycling/recharging equipment
4. Refrigerant container (HFC-134a) 5. Weight scale (J-39650) 6. Vacuum pump (J-39649)
7. Manifold gauge set (J-39183)
A. Preferred (best) method B. Alternative method C. For charging
JSIIA0239ZZ
RJIA3815J
Revision: 2010 May2011 QX56
Page 3075 of 5598
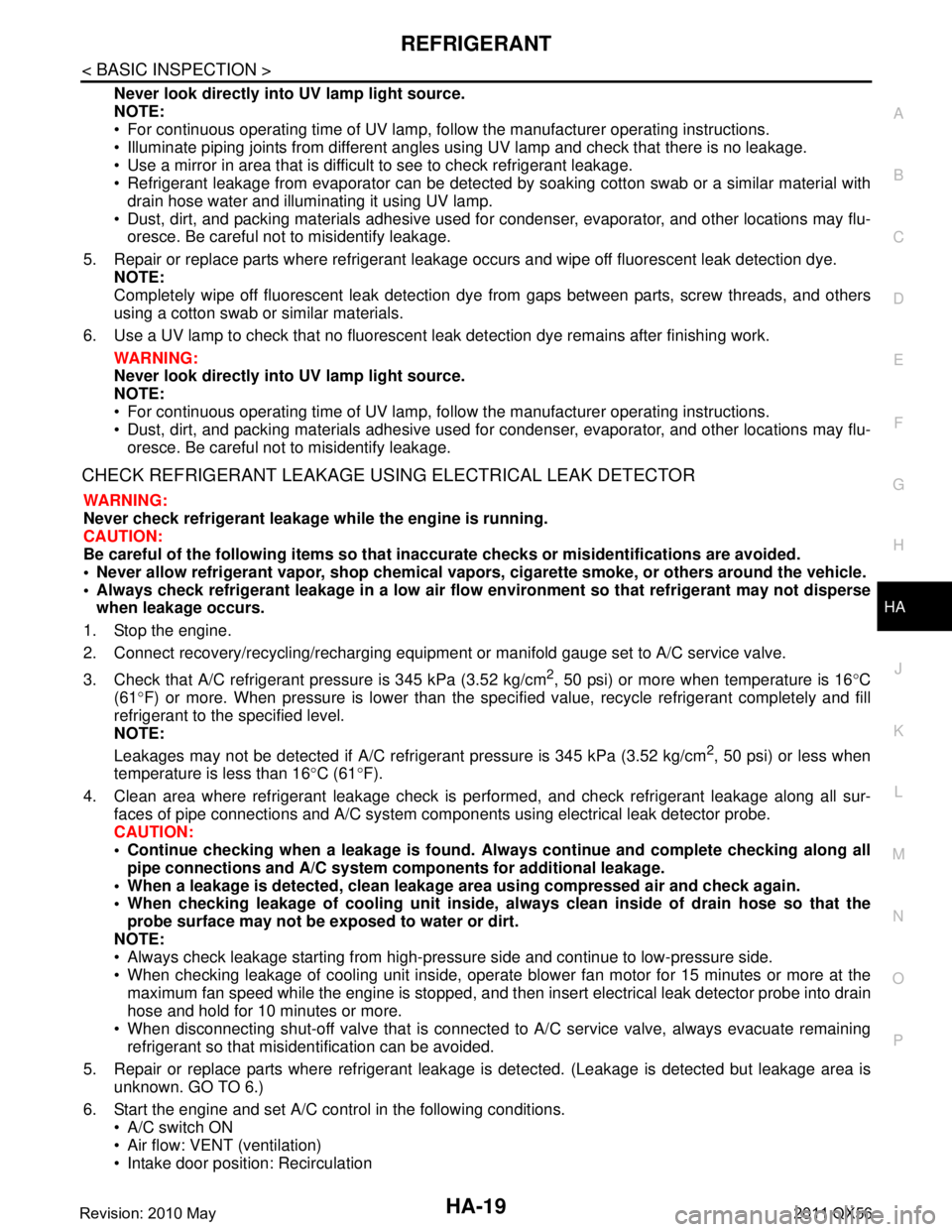
REFRIGERANTHA-19
< BASIC INSPECTION >
C
DE
F
G H
J
K L
M A
B
HA
N
O P
Never look directly into UV lamp light source.
NOTE:
For continuous operating time of UV lamp, fo llow the manufacturer operating instructions.
Illuminate piping joints from different angles us ing UV lamp and check that there is no leakage.
Use a mirror in area that is difficult to see to check refrigerant leakage.
Refrigerant leakage from evaporator can be detected by soaking cotton swab or a similar material with
drain hose water and illuminating it using UV lamp.
Dust, dirt, and packing materials adhesive used for condenser, evaporator, and other locations may flu- oresce. Be careful not to misidentify leakage.
5. Repair or replace parts where refrigerant leak age occurs and wipe off fluorescent leak detection dye.
NOTE:
Completely wipe off fluorescent leak detection dy e from gaps between parts, screw threads, and others
using a cotton swab or similar materials.
6. Use a UV lamp to check that no fluorescent leak detection dye remains after finishing work. WARNING:
Never look directly into UV lamp light source.
NOTE:
For continuous operating time of UV lamp, fo llow the manufacturer operating instructions.
Dust, dirt, and packing materials adhesive used for condenser, evaporator, and other locations may flu-
oresce. Be careful not to misidentify leakage.
CHECK REFRIGERANT LEAKAGE USIN G ELECTRICAL LEAK DETECTOR
WARNING:
Never check refrigerant leakage while the engine is running.
CAUTION:
Be careful of the following items so that in accurate checks or misidentifications are avoided.
Never allow refrigerant vapor, shop chemical vapors, cigarette smoke, or others around the vehicle.
Always check refrigerant leakage in a low air flow environment so that refrigerant may not disperse
when leakage occurs.
1. Stop the engine.
2. Connect recovery/recycling/recharging equipment or manifold gauge set to A/C service valve.
3. Check that A/C refrigerant pressure is 345 kPa (3.52 kg/cm
2, 50 psi) or more when temperature is 16 °C
(61 °F) or more. When pressure is lower than the spec ified value, recycle refrigerant completely and fill
refrigerant to the specified level.
NOTE:
Leakages may not be detected if A/C refri gerant pressure is 345 kPa (3.52 kg/cm
2, 50 psi) or less when
temperature is less than 16 °C (61 °F).
4. Clean area where refrigerant leakage check is per formed, and check refrigerant leakage along all sur-
faces of pipe connections and A/C system com ponents using electrical leak detector probe.
CAUTION:
Continue checking when a leakage is found. Always continue and complete checking along all
pipe connections and A/C system co mponents for additional leakage.
When a leakage is detected, clean leakage area using compressed air and check again.
When checking leakage of cooling unit inside, al ways clean inside of drain hose so that the
probe surface may not be exposed to water or dirt.
NOTE:
Always check leakage starting from high-pressure side and continue to low-pressure side.
When checking leakage of cooling unit inside, operate blower fan motor for 15 minutes or more at the maximum fan speed while the engine is stopped, and then insert electrical leak detector probe into drain
hose and hold for 10 minutes or more.
When disconnecting shut-off valve that is connected to A/C service valve, always evacuate remaining
refrigerant so that misidentification can be avoided.
5. Repair or replace parts where refrigerant leak age is detected. (Leakage is detected but leakage area is
unknown. GO TO 6.)
6. Start the engine and set A/C control in the following conditions. A/C switch ON
Air flow: VENT (ventilation)
Intake door position: Recirculation
Revision: 2010 May2011 QX56
Page 3076 of 5598
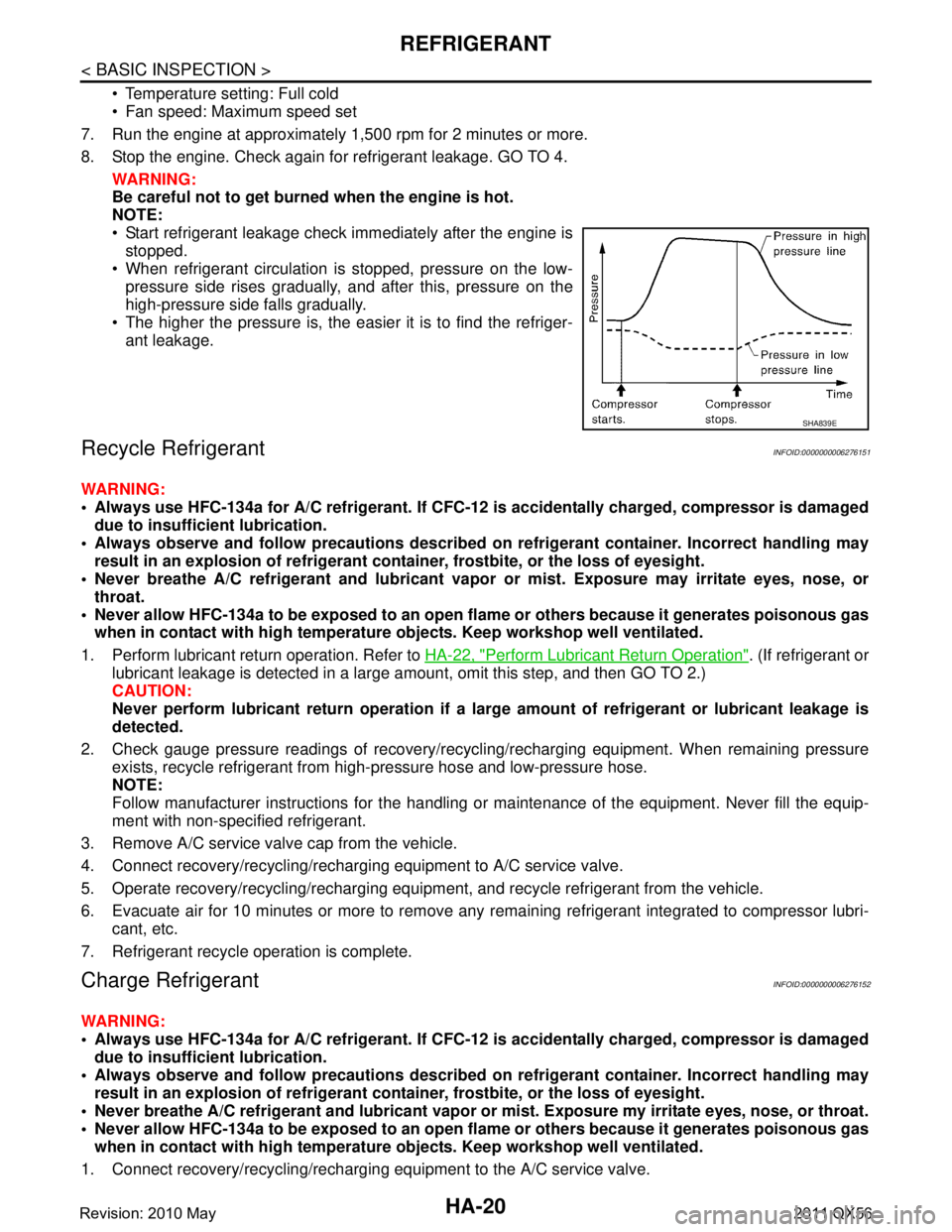
HA-20
< BASIC INSPECTION >
REFRIGERANT
Temperature setting: Full cold
Fan speed: Maximum speed set
7. Run the engine at approximately 1,500 rpm for 2 minutes or more.
8. Stop the engine. Check again for refrigerant leakage. GO TO 4.
WARNING:
Be careful not to get burned when the engine is hot.
NOTE:
Start refrigerant leakage check immediately after the engine is stopped.
When refrigerant circulation is stopped, pressure on the low-
pressure side rises gradually, and after this, pressure on the
high-pressure side falls gradually.
The higher the pressure is, the easier it is to find the refriger-
ant leakage.
Recycle RefrigerantINFOID:0000000006276151
WARNING:
Always use HFC-134a for A/C refrigerant. If CFC-12 is accidentally charged, compressor is damaged
due to insufficient lubrication.
Always observe and follow precaution s described on refrigerant container. Incorrect handling may
result in an explosion of refrigerant co ntainer, frostbite, or the loss of eyesight.
Never breathe A/C refrigerant and lubricant vapor or mist. Exposure may irritate eyes, nose, or
throat.
Never allow HFC-134a to be exposed to an open flam e or others because it generates poisonous gas
when in contact with high temperature ob jects. Keep workshop well ventilated.
1. Perform lubricant return operation. Refer to HA-22, "
Perform Lubricant Return Operation". (If refrigerant or
lubricant leakage is detected in a large am ount, omit this step, and then GO TO 2.)
CAUTION:
Never perform lubricant return op eration if a large amount of refrigerant or lubricant leakage is
detected.
2. Check gauge pressure readings of recovery/recyc ling/recharging equipment. When remaining pressure
exists, recycle refrigerant from high-pressure hose and low-pressure hose.
NOTE:
Follow manufacturer instructions for the handling or maintenance of the equipment. Never fill the equip-
ment with non-specified refrigerant.
3. Remove A/C service valve cap from the vehicle.
4. Connect recovery/recycling/rechargi ng equipment to A/C service valve.
5. Operate recovery/recycling/recharging equipm ent, and recycle refrigerant from the vehicle.
6. Evacuate air for 10 minutes or more to remove any remaining refrigerant integrated to compressor lubri-
cant, etc.
7. Refrigerant recycle operation is complete.
Charge RefrigerantINFOID:0000000006276152
WARNING:
Always use HFC-134a for A/C refrigerant. If CFC-12 is accidentally charged, compressor is damaged
due to insufficient lubrication.
Always observe and follow precaution s described on refrigerant container. Incorrect handling may
result in an explosion of refrigerant co ntainer, frostbite, or the loss of eyesight.
Never breathe A/C refrigerant and lubricant vapor or mist. Exposure my irritate eyes, nose, or throat.
Never allow HFC-134a to be exposed to an open flam e or others because it generates poisonous gas
when in contact with high temperature ob jects. Keep workshop well ventilated.
1. Connect recovery/recycling/recharging equipment to the A/C service valve.
SHA839E
Revision: 2010 May2011 QX56
Page 3077 of 5598
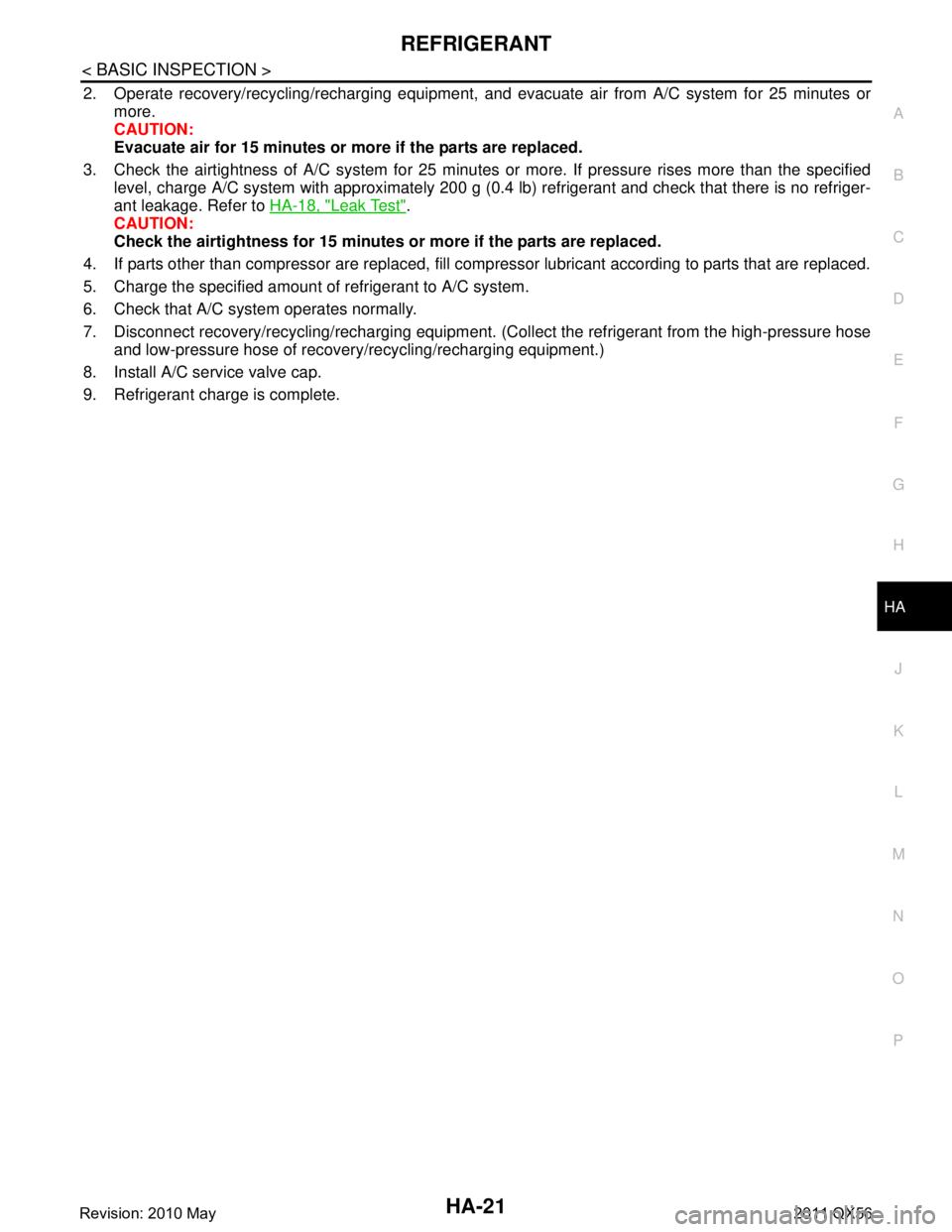
REFRIGERANTHA-21
< BASIC INSPECTION >
C
DE
F
G H
J
K L
M A
B
HA
N
O P
2. Operate recovery/recycling/recharging equipment, and evacuate air from A/C system for 25 minutes or
more.
CAUTION:
Evacuate air for 15 minutes or mo re if the parts are replaced.
3. Check the airtightness of A/C system for 25 minutes or more. If pressure rises more than the specified
level, charge A/C system with approximately 200 g (0.4 lb) refrigerant and check that there is no refriger-
ant leakage. Refer to HA-18, "
Leak Test".
CAUTION:
Check the airtightness for 15 minutes or more if the parts are replaced.
4. If parts other than compressor are replaced, fill comp ressor lubricant according to parts that are replaced.
5. Charge the specified amount of refrigerant to A/C system.
6. Check that A/C system operates normally.
7. Disconnect recovery/recycling/recharging equipment. (Co llect the refrigerant from the high-pressure hose
and low-pressure hose of recove ry/recycling/recharging equipment.)
8. Install A/C service valve cap.
9. Refrigerant charge is complete.
Revision: 2010 May2011 QX56