sensor INFINITI QX56 2011 Factory Service Manual
[x] Cancel search | Manufacturer: INFINITI, Model Year: 2011, Model line: QX56, Model: INFINITI QX56 2011Pages: 5598, PDF Size: 94.53 MB
Page 7 of 5598
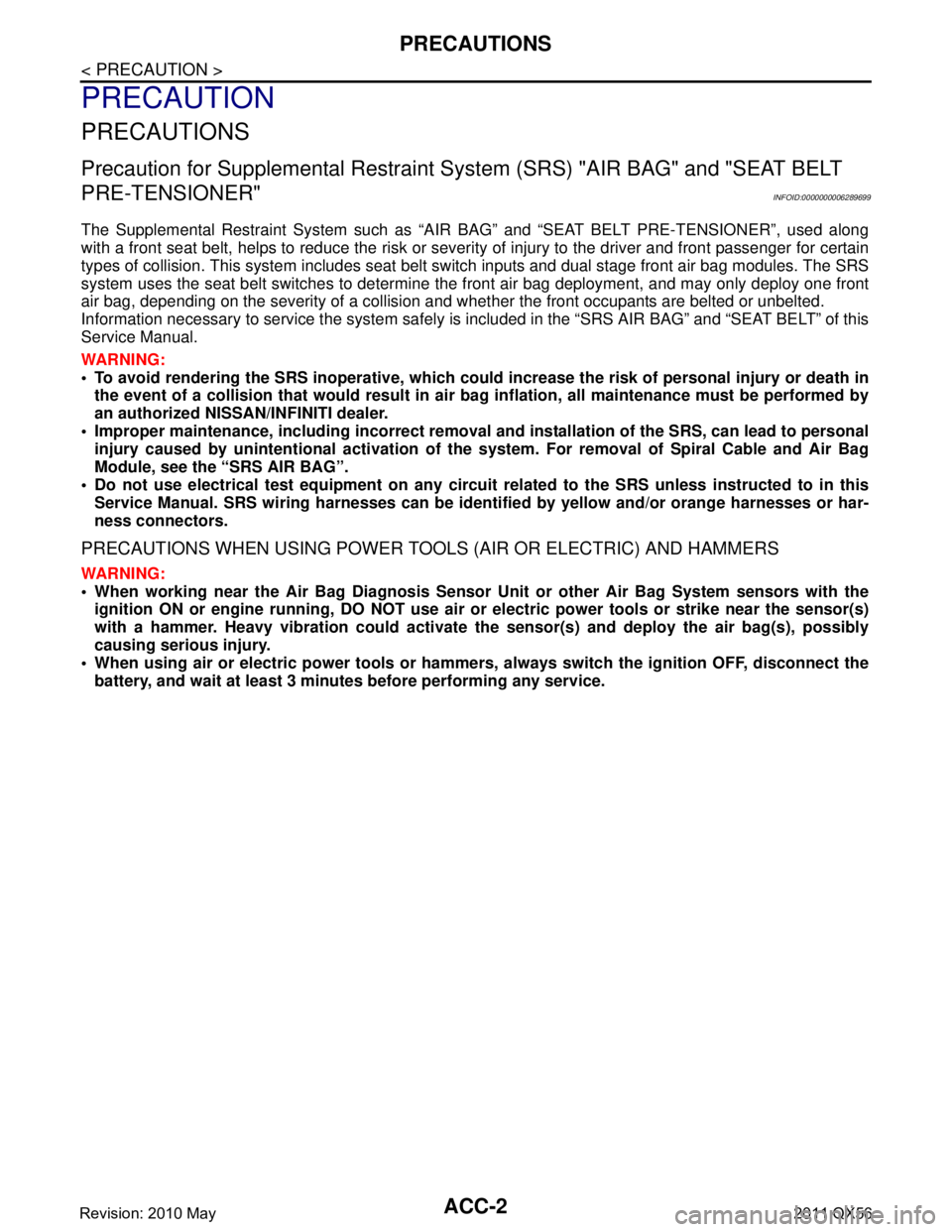
ACC-2
< PRECAUTION >
PRECAUTIONS
PRECAUTION
PRECAUTIONS
Precaution for Supplemental Restraint System (SRS) "AIR BAG" and "SEAT BELT
PRE-TENSIONER"
INFOID:0000000006289699
The Supplemental Restraint System such as “A IR BAG” and “SEAT BELT PRE-TENSIONER”, used along
with a front seat belt, helps to reduce the risk or severi ty of injury to the driver and front passenger for certain
types of collision. This system includes seat belt switch inputs and dual stage front air bag modules. The SRS
system uses the seat belt switches to determine the front air bag deployment, and may only deploy one front
air bag, depending on the severity of a collision and w hether the front occupants are belted or unbelted.
Information necessary to service the system safely is included in the “SRS AIR BAG” and “SEAT BELT” of this
Service Manual.
WARNING:
• To avoid rendering the SRS inopera tive, which could increase the risk of personal injury or death in
the event of a collision that would result in air bag inflation, all maintenance must be performed by
an authorized NISS AN/INFINITI dealer.
Improper maintenance, including in correct removal and installation of the SRS, can lead to personal
injury caused by unintent ional activation of the system. For re moval of Spiral Cable and Air Bag
Module, see the “SRS AIR BAG”.
Do not use electrical test equipmen t on any circuit related to the SRS unless instructed to in this
Service Manual. SRS wiring harnesses can be identi fied by yellow and/or orange harnesses or har-
ness connectors.
PRECAUTIONS WHEN USING POWER TOOLS (AIR OR ELECTRIC) AND HAMMERS
WARNING:
When working near the Air Bag Diagnosis Sensor Unit or other Air Bag System sensors with the ignition ON or engine running, DO NOT use air or electric power tools or strike near the sensor(s)
with a hammer. Heavy vibration could activate the sensor(s) and deploy the air bag(s), possibly
causing serious injury.
When using air or electric power tools or hammers , always switch the ignition OFF, disconnect the
battery, and wait at least 3 minu tes before performing any service.
Revision: 2010 May2011 QX56
Page 8 of 5598
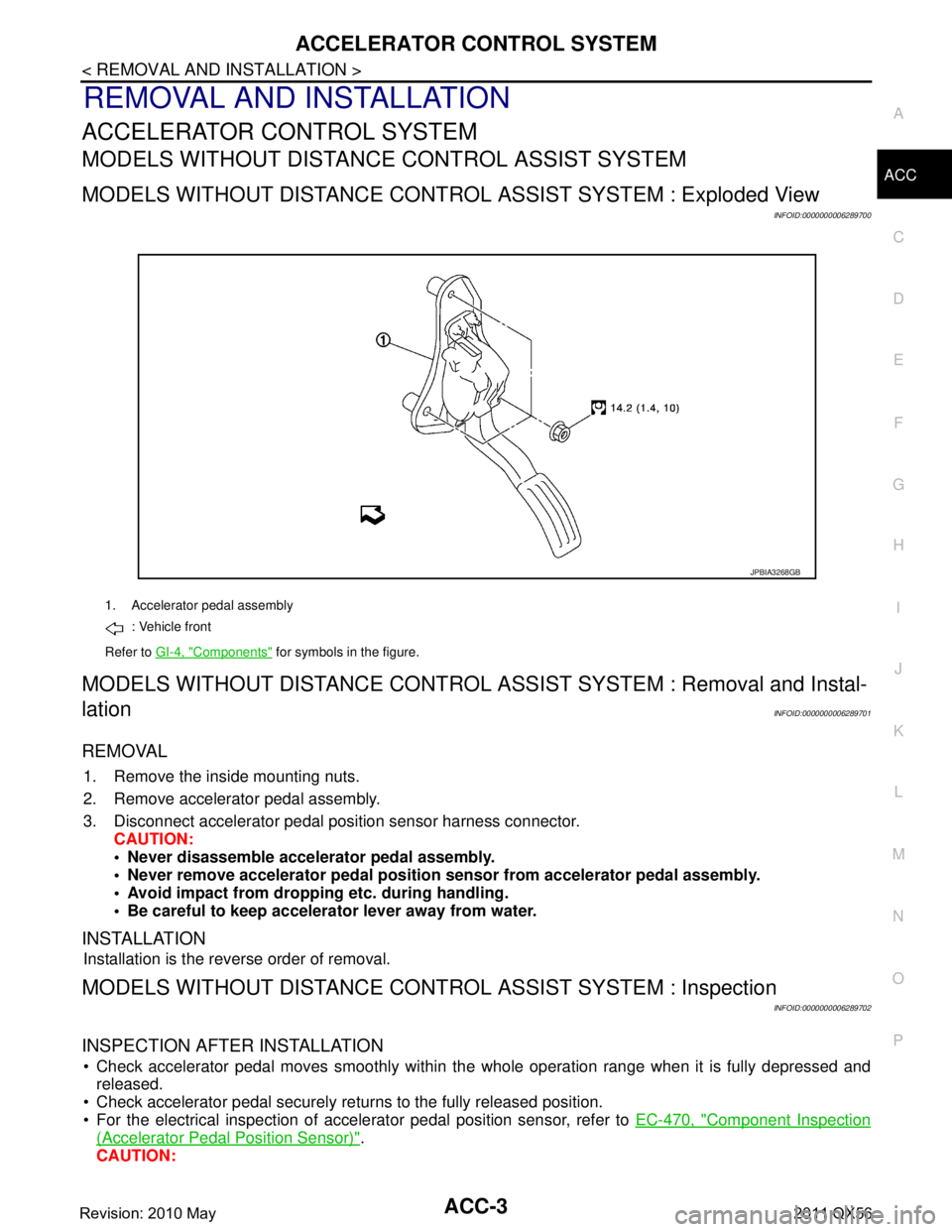
ACCELERATOR CONTROL SYSTEMACC-3
< REMOVAL AND INSTALLATION >
C
DE
F
G H
I
J
K L
M A
ACC
NP
O
REMOVAL AND INSTALLATION
ACCELERATOR CONTROL SYSTEM
MODELS WITHOUT DISTANCE
CONTROL ASSIST SYSTEM
MODELS WITHOUT DISTANCE CONTRO L ASSIST SYSTEM : Exploded View
INFOID:0000000006289700
MODELS WITHOUT DISTANCE CONTROL ASS IST SYSTEM : Removal and Instal-
lation
INFOID:0000000006289701
REMOVAL
1. Remove the inside mounting nuts.
2. Remove accelerator pedal assembly.
3. Disconnect accelerator pedal position sensor harness connector. CAUTION:
Never disassemble accelerator pedal assembly.
Never remove accelerator pedal position sensor from accelerator pedal assembly.
Avoid impact from dropping etc. during handling.
Be careful to keep accelerator lever away from water.
INSTALLATION
Installation is the reverse order of removal.
MODELS WITHOUT DISTANCE CONT ROL ASSIST SYSTEM : Inspection
INFOID:0000000006289702
INSPECTION AFTER INSTALLATION
Check accelerator pedal moves smoothly within the whole operation range when it is fully depressed and
released.
Check accelerator pedal securely returns to the fully released position.
For the electrical inspection of accelerator pedal position sensor, refer to EC-470, "
Component Inspection
(Accelerator Pedal Position Sensor)".
CAUTION:
1. Accelerator pedal assembly
: Vehicle front
Refer to GI-4, "
Components" for symbols in the figure.
JPBIA3268GB
Revision: 2010 May2011 QX56
Page 9 of 5598
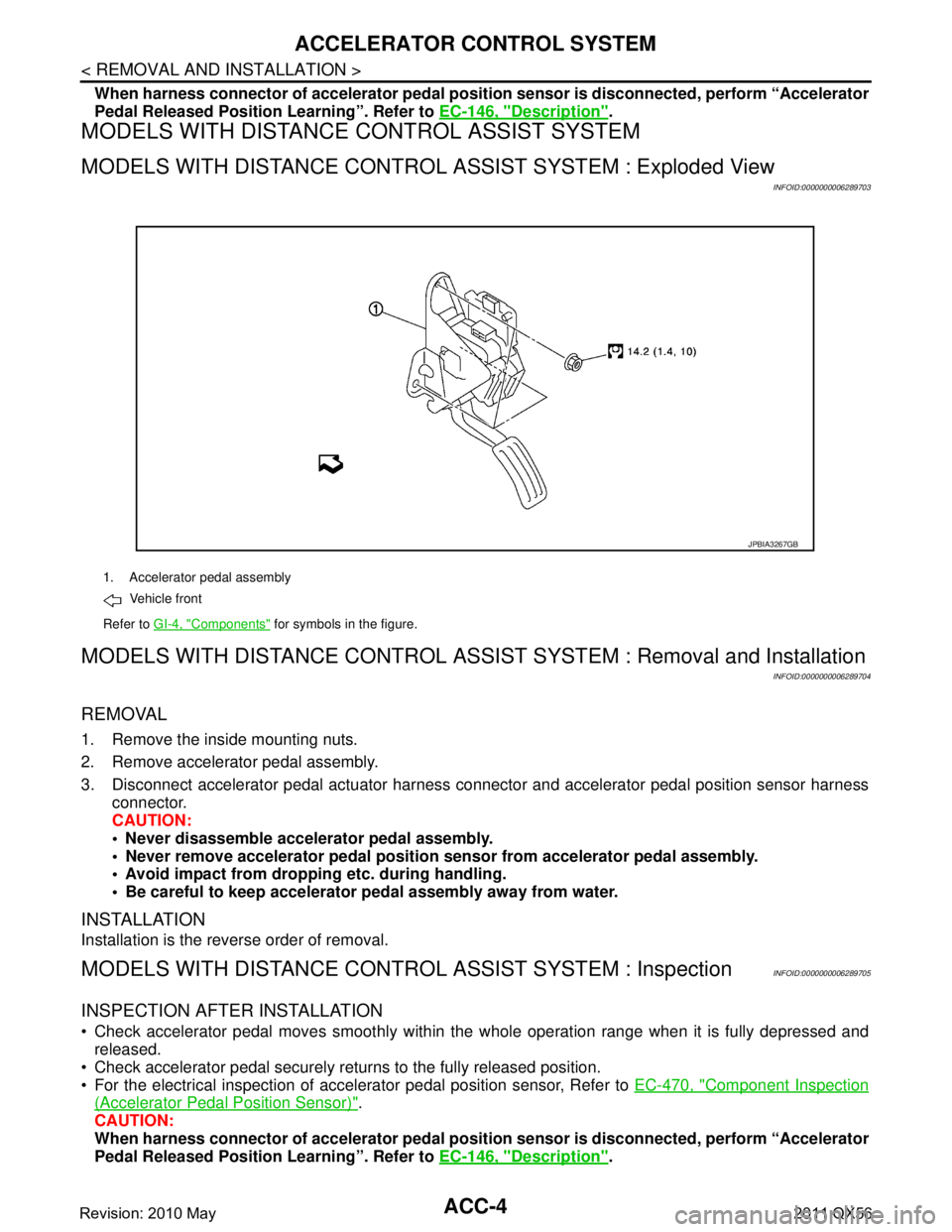
ACC-4
< REMOVAL AND INSTALLATION >
ACCELERATOR CONTROL SYSTEM
When harness connector of accelerator pedal position sensor is disconnected, perform “Accelerator
Pedal Released Position Learning”. Refer to EC-146, "
Description".
MODELS WITH DISTANCE CONTROL ASSIST SYSTEM
MODELS WITH DISTANCE CONTRO L ASSIST SYSTEM : Exploded View
INFOID:0000000006289703
MODELS WITH DISTANCE CONTROL ASSI ST SYSTEM : Removal and Installation
INFOID:0000000006289704
REMOVAL
1. Remove the inside mounting nuts.
2. Remove accelerator pedal assembly.
3. Disconnect accelerator pedal actuator harness connec tor and accelerator pedal position sensor harness
connector.
CAUTION:
Never disassemble accelerator pedal assembly.
Never remove accelerator pedal position sensor from accelerator pedal assembly.
Avoid impact from dropping etc. during handling.
Be careful to keep accelerator pedal assembly away from water.
INSTALLATION
Installation is the reverse order of removal.
MODELS WITH DISTANCE CONTRO L ASSIST SYSTEM : InspectionINFOID:0000000006289705
INSPECTION AFTER INSTALLATION
Check accelerator pedal moves smoothly within the whole operation range when it is fully depressed and
released.
Check accelerator pedal securely returns to the fully released position.
For the electrical inspection of acce lerator pedal position sensor, Refer to EC-470, "
Component Inspection
(Accelerator Pedal Position Sensor)".
CAUTION:
When harness connector of accelerator pedal posi tion sensor is disconnected, perform “Accelerator
Pedal Released Position Learning”. Refer to EC-146, "
Description".
1. Accelerator pedal assembly
Vehicle front
Refer to GI-4, "
Components" for symbols in the figure.
JPBIA3267GB
Revision: 2010 May2011 QX56
Page 12 of 5598
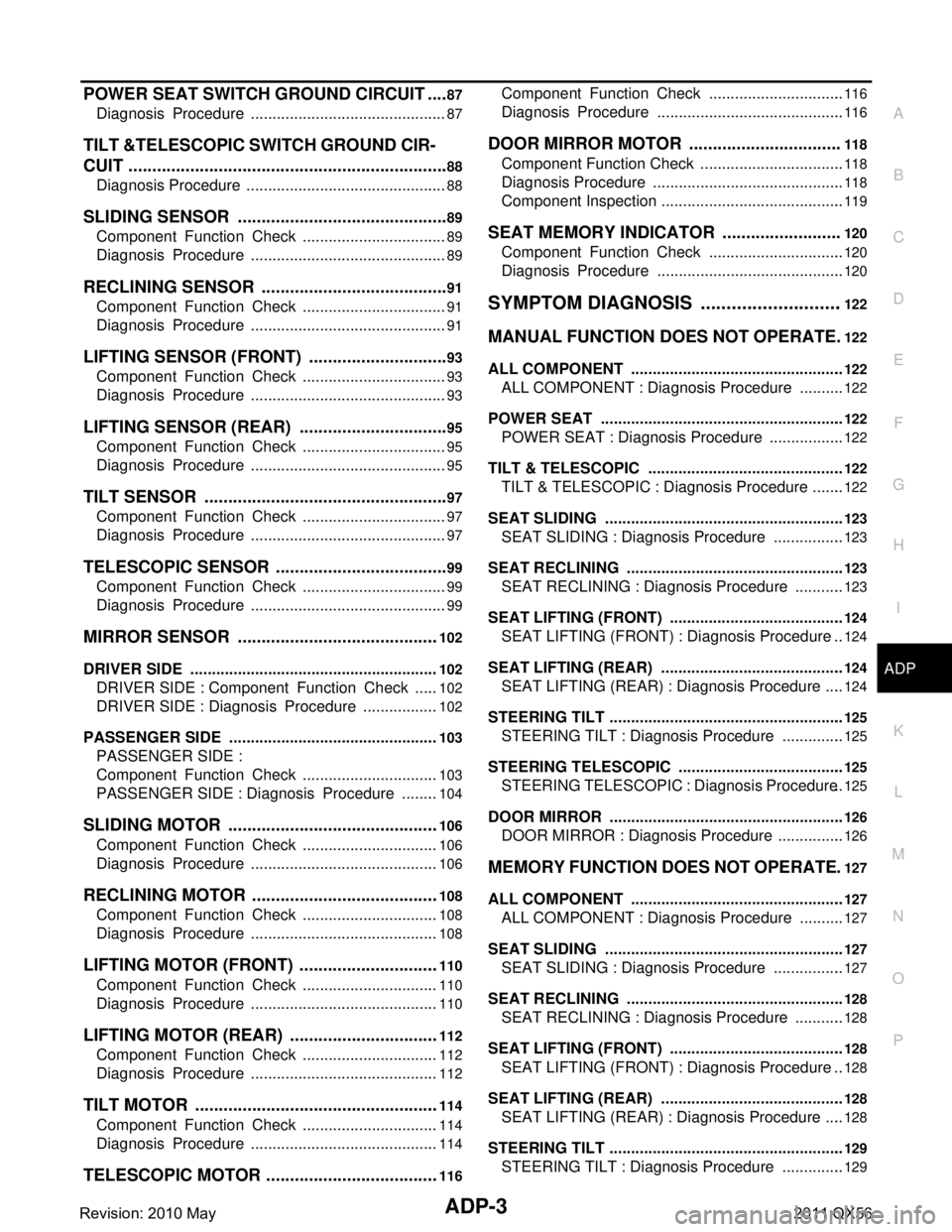
ADP-3
C
DE
F
G H
I
K L
M A
B
ADP
N
O P
POWER SEAT SWITCH GROUND CIRCUIT ....87
Diagnosis Procedure .......................................... ....87
TILT &TELESCOPIC SWITCH GROUND CIR-
CUIT ....................................................................
88
Diagnosis Procedure ........................................... ....88
SLIDING SENSOR .............................................89
Component Function Check .............................. ....89
Diagnosis Procedure ..............................................89
RECLINING SENSOR ........................................91
Component Function Check .............................. ....91
Diagnosis Procedure ..............................................91
LIFTING SENSOR (FRONT) ..............................93
Component Function Check .............................. ....93
Diagnosis Procedure ..............................................93
LIFTING SENSOR (REAR) ................................95
Component Function Check .............................. ....95
Diagnosis Procedure ..............................................95
TILT SENSOR ....................................................97
Component Function Check .............................. ....97
Diagnosis Procedure ..............................................97
TELESCOPIC SENSOR .....................................99
Component Function Check .............................. ....99
Diagnosis Procedure ..............................................99
MIRROR SENSOR ...........................................102
DRIVER SIDE ........................................................ ..102
DRIVER SIDE : Component Function Check ......102
DRIVER SIDE : Diagnosis Procedure ..................102
PASSENGER SIDE .................................................103
PASSENGER SIDE :
Component Function Check .............................. ..
103
PASSENGER SIDE : Diagnosis Procedure .........104
SLIDING MOTOR .............................................106
Component Function Check .............................. ..106
Diagnosis Procedure ............................................106
RECLINING MOTOR ........................................108
Component Function Check .............................. ..108
Diagnosis Procedure ............................................108
LIFTING MOTOR (FRONT) ..............................110
Component Function Check .............................. ..110
Diagnosis Procedure ............................................110
LIFTING MOTOR (REAR) ................................112
Component Function Check .............................. ..112
Diagnosis Procedure ............................................112
TILT MOTOR ....................................................114
Component Function Check .............................. ..114
Diagnosis Procedure ............................................114
TELESCOPIC MOTOR .....................................116
Component Function Check .............................. ..116
Diagnosis Procedure ............................................116
DOOR MIRROR MOTOR ................................118
Component Function Check ..................................118
Diagnosis Procedure .............................................118
Component Inspection ...........................................119
SEAT MEMORY INDICATOR .........................120
Component Function Check ................................120
Diagnosis Procedure ............................................120
SYMPTOM DIAGNOSIS ............................122
MANUAL FUNCTION DOES NOT OPERATE .122
ALL COMPONENT ................................................ ..122
ALL COMPONENT : Diagnosis Procedure ...........122
POWER SEAT ....................................................... ..122
POWER SEAT : Diagnosis Procedure ..................122
TILT & TELESCOPIC ............................................ ..122
TILT & TELESCOPIC : Diagnosis Procedure ........122
SEAT SLIDING ...................................................... ..123
SEAT SLIDING : Diagnosis Procedure .................123
SEAT RECLINING ................................................. ..123
SEAT RECLINING : Diagnosis Procedure ............123
SEAT LIFTING (FRONT) ....................................... ..124
SEAT LIFTING (FRONT) : Diagnosis Procedure ..124
SEAT LIFTING (REAR) ...........................................124
SEAT LIFTING (REAR) : Diagnosis Procedure .....124
STEERING TILT ..................................................... ..125
STEERING TILT : Diagnosis Procedure ...............125
STEERING TELESCOPIC ..................................... ..125
STEERING TELESCOPIC : Diagnosis Procedure ..125
DOOR MIRROR ..................................................... ..126
DOOR MIRROR : Diagnosis Procedure ................126
MEMORY FUNCTION DOES NOT OPERATE .127
ALL COMPONENT ................................................ ..127
ALL COMPONENT : Diagnosis Procedure ...........127
SEAT SLIDING ...................................................... ..127
SEAT SLIDING : Diagnosis Procedure .................127
SEAT RECLINING ................................................. ..128
SEAT RECLINING : Diagnosis Procedure ............128
SEAT LIFTING (FRONT) ....................................... ..128
SEAT LIFTING (FRONT) : Diagnosis Procedure ..128
SEAT LIFTING (REAR) ...........................................128
SEAT LIFTING (REAR) : Diagnosis Procedure .....128
STEERING TILT ..................................................... ..129
STEERING TILT : Diagnosis Procedure ...............129
Revision: 2010 May2011 QX56
Page 14 of 5598
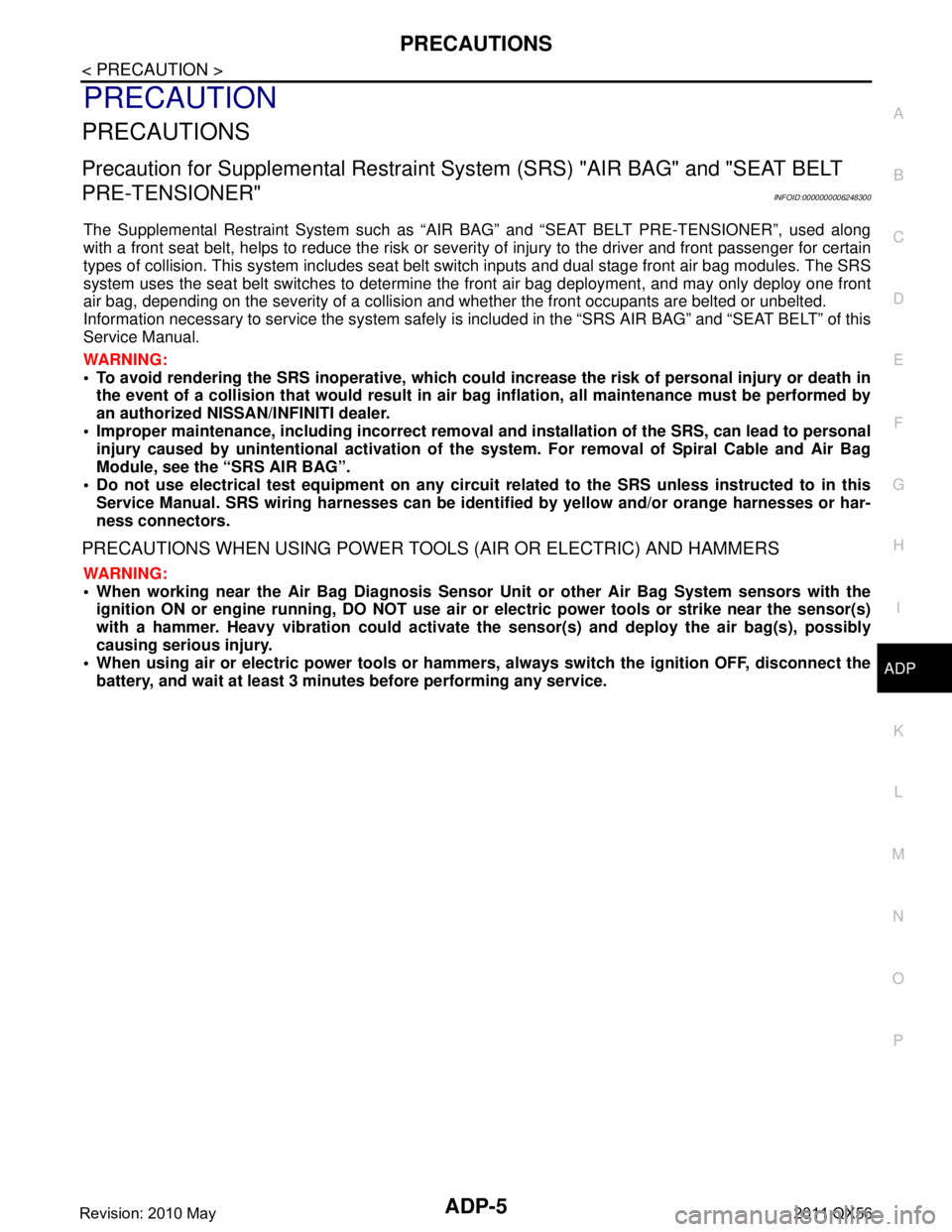
PRECAUTIONSADP-5
< PRECAUTION >
C
DE
F
G H
I
K L
M A
B
ADP
N
O P
PRECAUTION
PRECAUTIONS
Precaution for Supplemental Restraint System (SRS) "AIR BAG" and "SEAT BELT
PRE-TENSIONER"
INFOID:0000000006248300
The Supplemental Restraint System such as “A IR BAG” and “SEAT BELT PRE-TENSIONER”, used along
with a front seat belt, helps to reduce the risk or severi ty of injury to the driver and front passenger for certain
types of collision. This system includes seat belt switch inputs and dual stage front air bag modules. The SRS
system uses the seat belt switches to determine the front air bag deployment, and may only deploy one front
air bag, depending on the severity of a collision and whether the front occupants are belted or unbelted.
Information necessary to service the system safely is included in the “SRS AIR BAG” and “SEAT BELT” of this
Service Manual.
WARNING:
• To avoid rendering the SRS inoper ative, which could increase the risk of personal injury or death in
the event of a collision that would result in air ba g inflation, all maintenance must be performed by
an authorized NISSAN/INFINITI dealer.
Improper maintenance, including in correct removal and installation of the SRS, can lead to personal
injury caused by unintentional act ivation of the system. For removal of Spiral Cable and Air Bag
Module, see the “SRS AIR BAG”.
Do not use electrical test equipm ent on any circuit related to the SRS unless instructed to in this
Service Manual. SRS wiring harnesses can be identi fied by yellow and/or orange harnesses or har-
ness connectors.
PRECAUTIONS WHEN USING POWER TOOLS (AIR OR ELECTRIC) AND HAMMERS
WARNING:
When working near the Air Bag Diagnosis Sensor Unit or other Air Bag System sensors with the
ignition ON or engine running, DO NOT use air or electric power tools or strike near the sensor(s)
with a hammer. Heavy vibration could activate the sensor(s) and deploy the air bag(s), possibly
causing serious injury.
When using air or electric power tools or hammers , always switch the ignition OFF, disconnect the
battery, and wait at least 3 minutes before performing any service.
Revision: 2010 May2011 QX56
Page 18 of 5598
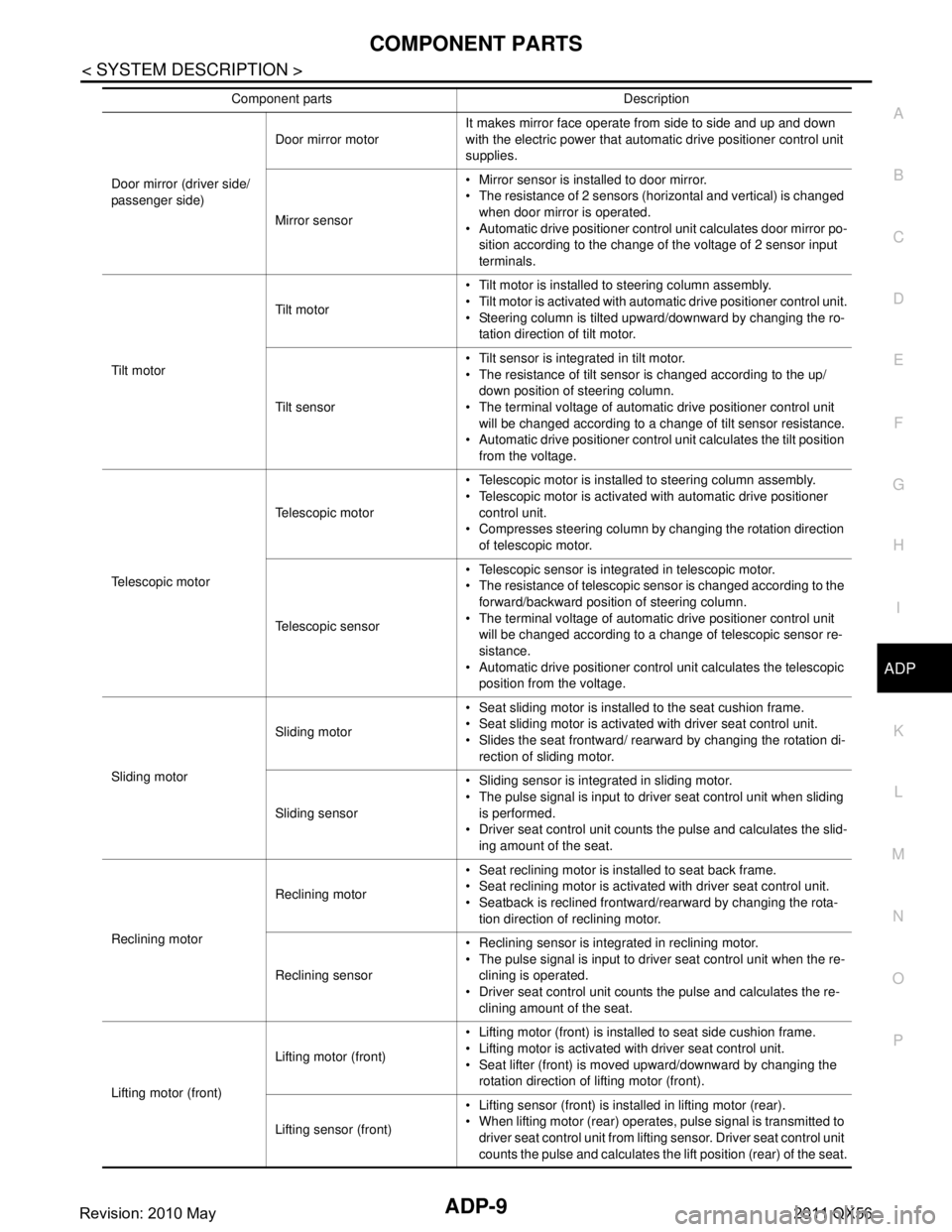
COMPONENT PARTSADP-9
< SYSTEM DESCRIPTION >
C
DE
F
G H
I
K L
M A
B
ADP
N
O P
Door mirror (driver side/
passenger side) Door mirror motor
It makes mirror face operate from side to side and up and down
with the electric power that automatic drive positioner control unit
supplies.
Mirror sensor Mirror sensor is inst
alled to door mirror.
The resistance of 2 sensors (horizontal and vertical) is changed when door mirror is operated.
Automatic drive positioner control unit calculates door mirror po- sition according to the change of the voltage of 2 sensor input
terminals.
Tilt motor Tilt motor
Tilt motor is installed to steering column assembly.
Tilt motor is activated with automatic drive positioner control unit.
Steering column is tilted upward/downward by changing the ro-
tation direction of tilt motor.
Tilt sensor Tilt sensor is integrated in tilt motor.
The resistance of tilt sensor is changed according to the up/
down position of steering column.
The terminal voltage of automatic drive positioner control unit
will be changed according to a change of tilt sensor resistance.
Automatic drive positioner control unit calculates the tilt position from the voltage.
Telescopic motor Te l e s c o p i c m o t o r
Telescopic motor is installed to steering column assembly.
Telescopic motor is activated with automatic drive positioner
control unit.
Compresses steering column by changing the rotation direction
of telescopic motor.
Telescopic sensor Telescopic sensor is integrated in telescopic motor.
The resistance of telescopic sensor is changed according to the
forward/backward position of steering column.
The terminal voltage of automatic drive positioner control unit will be changed according to a change of telescopic sensor re-
sistance.
Automatic drive positioner control unit calculates the telescopic position from the voltage.
Sliding motor Sliding motor
Seat sliding motor is installed to the seat cushion frame.
Seat sliding motor is activated with driver seat control unit.
Slides the seat frontward/ rearward by changing the rotation di-
rection of sliding motor.
Sliding sensor Sliding sensor is integrated in sliding motor.
The pulse signal is input to driver seat control unit when sliding
is performed.
Driver seat control unit counts the pulse and calculates the slid- ing amount of the seat.
Reclining motor Reclining motor
Seat reclining motor is installed to seat back frame.
Seat reclining motor is activated with driver seat control unit.
Seatback is reclined frontward/rearward by changing the rota-
tion direction of reclining motor.
Reclining sensor Reclining sensor is integrated in reclining motor.
The pulse signal is input to driver seat control unit when the re-
clining is operated.
Driver seat control unit counts the pulse and calculates the re- clining amount of the seat.
Lifting motor (front) Lifting motor (front)
Lifting motor (front) is installed to seat side cushion frame.
Lifting motor is activated with driver seat control unit.
Seat lifter (front) is moved upward/downward by changing the
rotation direction of lifting motor (front).
Lifting sensor (front) Lifting sensor (front) is inst
alled in lifting motor (rear).
When lifting motor (rear) operates, pulse signal is transmitted to driver seat control unit from lifting sensor. Driver seat control unit
counts the pulse and calculates the lift position (rear) of the seat.
Component parts Description
Revision: 2010 May2011 QX56
Page 19 of 5598
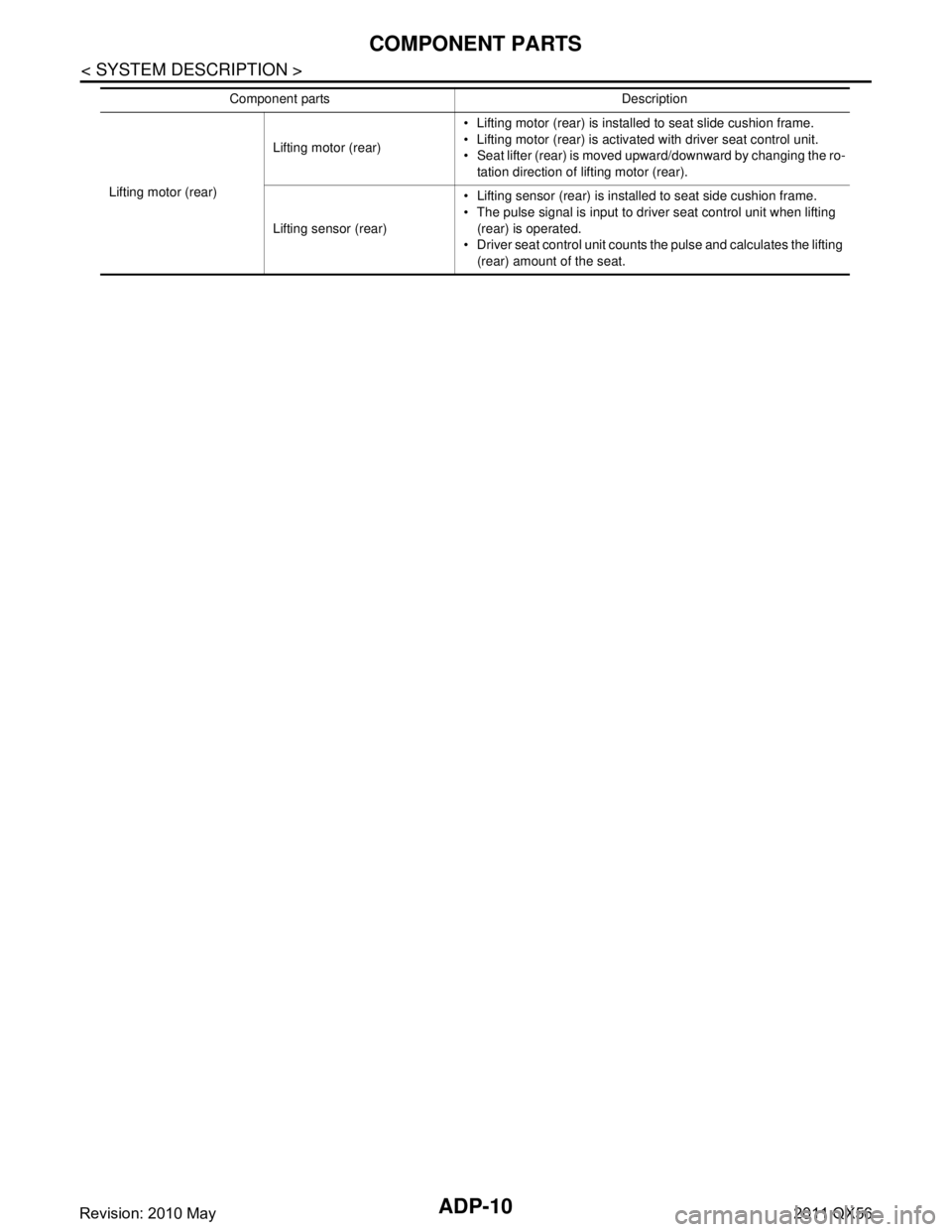
ADP-10
< SYSTEM DESCRIPTION >
COMPONENT PARTS
Lifting motor (rear)Lifting motor (rear)
Lifting motor (rear) is installed to seat slide cushion frame.
Lifting motor (rear) is activated with driver seat control unit.
Seat lifter (rear) is moved upward/downward by changing the ro-
tation direction of lifting motor (rear).
Lifting sensor (rear) Lifting sensor (rear) is installed to seat side cushion frame.
The pulse signal is input to driver seat control unit when lifting
(rear) is operated.
Driver seat control unit counts the pulse and calculates the lifting (rear) amount of the seat.
Component parts Description
Revision: 2010 May2011 QX56
Page 25 of 5598
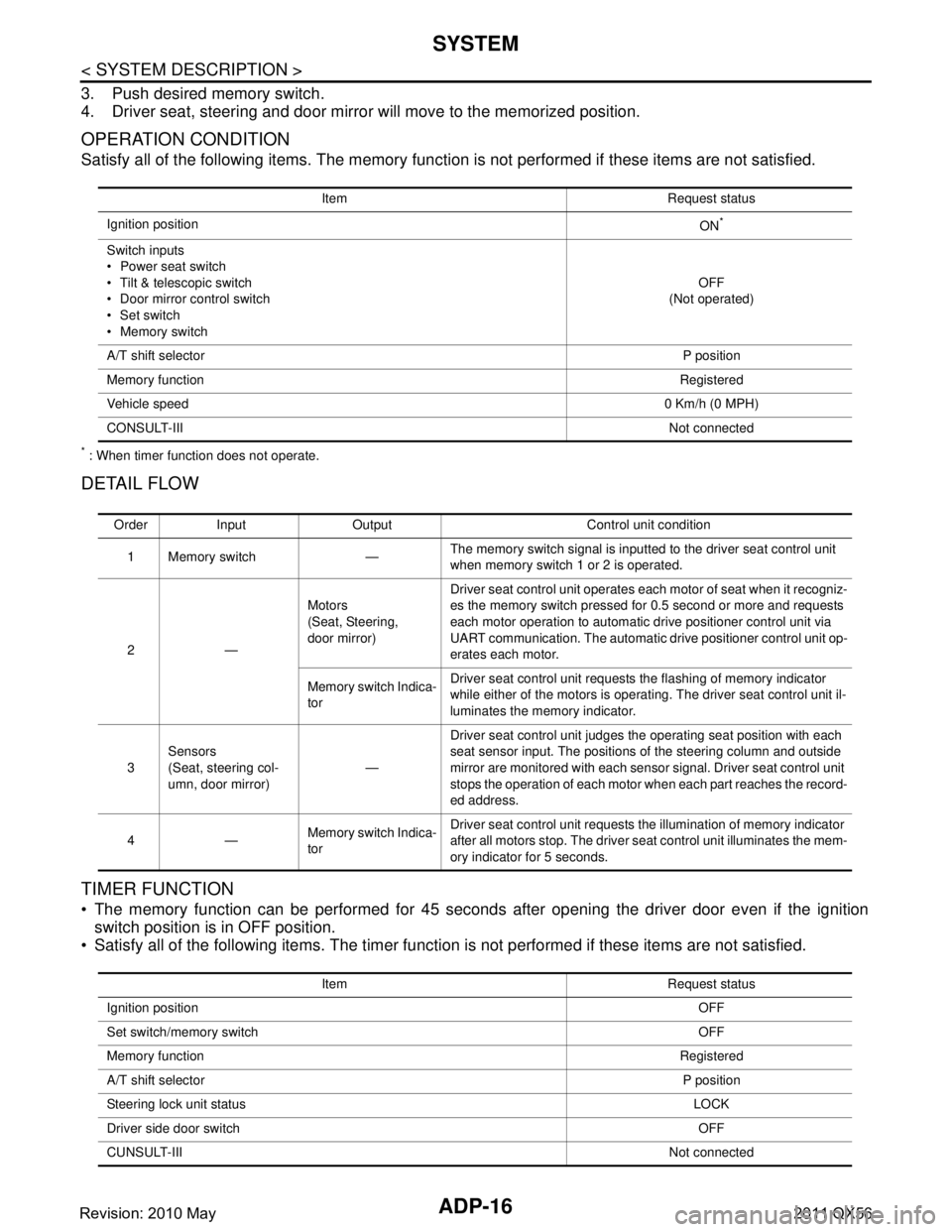
ADP-16
< SYSTEM DESCRIPTION >
SYSTEM
3. Push desired memory switch.
4. Driver seat, steering and door mirror will move to the memorized position.
OPERATION CONDITION
Satisfy all of the following items. The memory function is not performed if these items are not satisfied.
* : When timer function does not operate.
DETAIL FLOW
TIMER FUNCTION
The memory function can be performed for 45 seconds after opening the driver door even if the ignition
switch position is in OFF position.
Satisfy all of the following items. The timer functi on is not performed if these items are not satisfied.
Item Request status
Ignition position ON
*
Switch inputs
Power seat switch
Tilt & telescopic switch
Door mirror control switch
Set switch
Memory switchOFF
(Not operated)
A/T shift selector P position
Memory function Registered
Vehicle speed 0 Km/h (0 MPH)
CONSULT-III Not connected
Order Input Output Control unit condition
1 Memory switch — The memory switch signal is inputted to the driver seat control unit
when memory switch 1 or 2 is operated.
2— Motors
(Seat, Steering,
door mirror)Driver seat control unit operates each motor of seat when it recogniz-
es the memory switch pressed for 0.5 second or more and requests
each motor operation to automatic drive positioner control unit via
UART communication. The automatic drive positioner control unit op-
erates each motor.
Memory switch Indica-
tor Driver seat control unit requests the flashing of memory indicator
while either of the motors is operating. The driver seat control unit il-
luminates the memory indicator.
3 Sensors
(Seat, steering col-
umn, door mirror) —Driver seat control unit judges the operating seat position with each
seat sensor input. The positions of the steering column and outside
mirror are monitored with each sensor signal. Driver seat control unit
stops the operation of each motor when each part reaches the record-
ed address.
4— Memory switch Indica-
torDriver seat control unit requests the illumination of memory indicator
after all motors stop. The driver seat control unit illuminates the mem-
ory indicator for 5 seconds.
Item Request status
Ignition position OFF
Set switch/memory switch OFF
Memory function Registered
A/T shift selector P position
Steering lock unit status LOCK
Driver side door switch OFF
CUNSULT-III Not connected
Revision: 2010 May2011 QX56
Page 27 of 5598
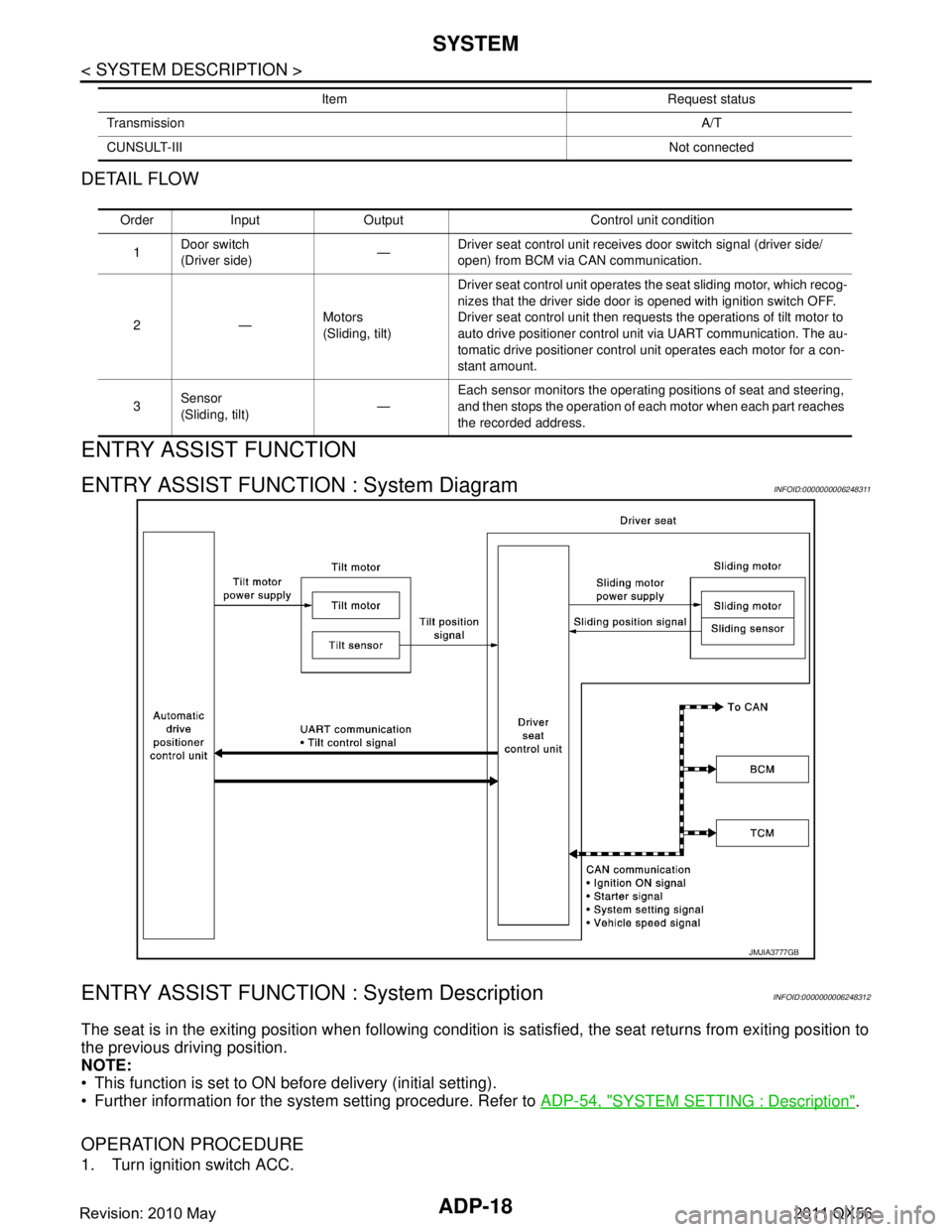
ADP-18
< SYSTEM DESCRIPTION >
SYSTEM
DETAIL FLOW
ENTRY ASSIST FUNCTION
ENTRY ASSIST FUNCTION : System DiagramINFOID:0000000006248311
ENTRY ASSIST FUNCTION : System DescriptionINFOID:0000000006248312
The seat is in the exiting position when following condition is satisfied, the seat returns from exiting position to
the previous driving position.
NOTE:
This function is set to ON before delivery (initial setting).
Further information for the system setting procedure. Refer to ADP-54, "
SYSTEM SETTING : Description".
OPERATION PROCEDURE
1. Turn ignition switch ACC.
Transmission A/T
CUNSULT-III Not connected
Item Request status
Order Input Output Control unit condition
1 Door switch
(Driver side)
—Driver seat control unit receives door switch signal (driver side/
open) from BCM via CAN communication.
2— Motors
(Sliding, tilt)Driver seat control unit operates the seat sliding motor, which recog-
nizes that the driver side door is opened with ignition switch OFF.
Driver seat control unit then requests the operations of tilt motor to
auto drive positioner control unit via UART communication. The au-
tomatic drive positioner control unit operates each motor for a con-
stant amount.
3 Sensor
(Sliding, tilt) —Each sensor monitors the operating positions of seat and steering,
and then stops the operation of each motor when each part reaches
the recorded address.
JMJIA3777GB
Revision: 2010 May2011 QX56
Page 28 of 5598
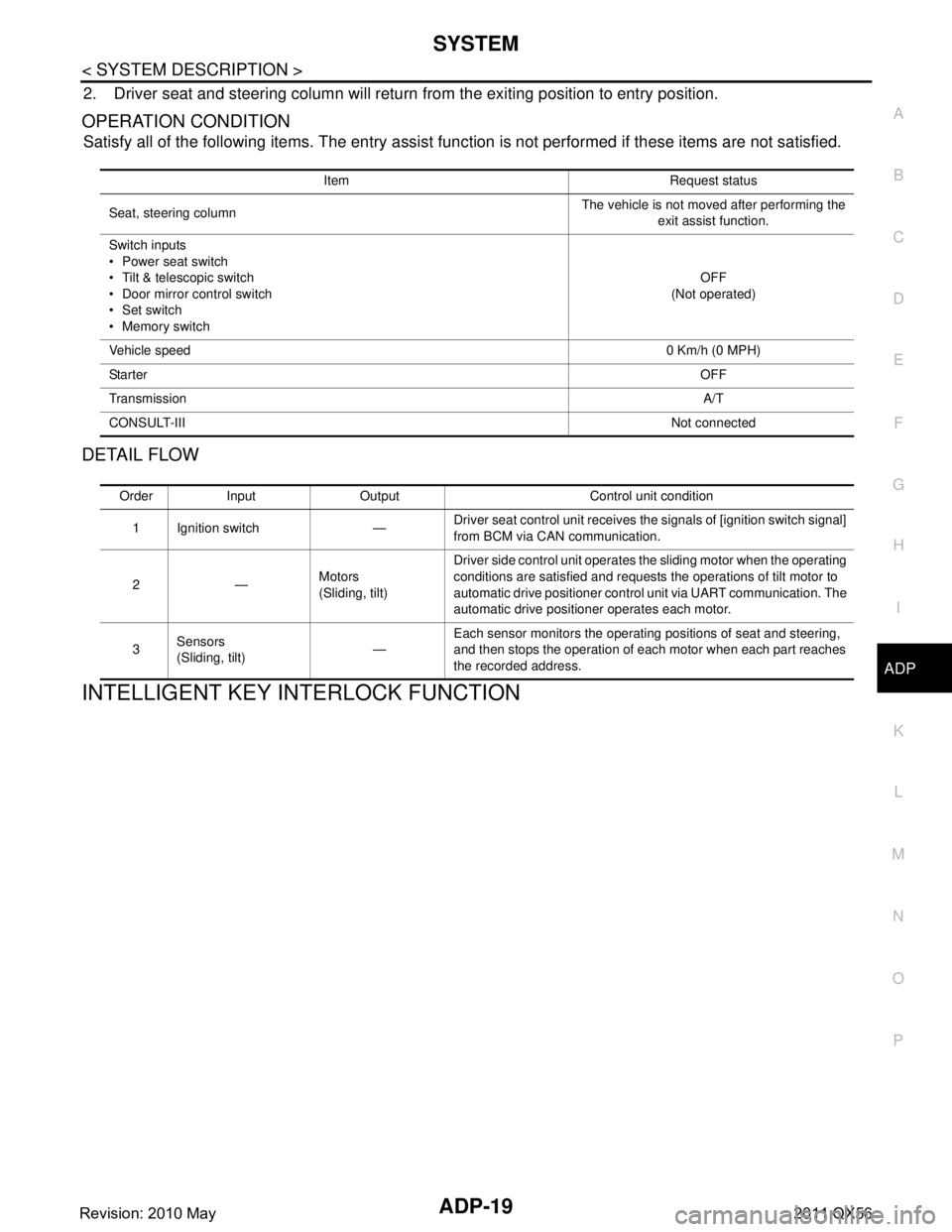
SYSTEMADP-19
< SYSTEM DESCRIPTION >
C
DE
F
G H
I
K L
M A
B
ADP
N
O P
2. Driver seat and steering column will return from the exiting position to entry position.
OPERATION CONDITION
Satisfy all of the following items. The entry assist f unction is not performed if these items are not satisfied.
DETAIL FLOW
INTELLIGENT KEY INTERLOCK FUNCTION
Item Request status
Seat, steering column The vehicle is not moved after performing the
exit assist function.
Switch inputs
Power seat switch
Tilt & telescopic switch
Door mirror control switch
Set switch
Memory switch OFF
(Not operated)
Vehicle speed 0 Km/h (0 MPH)
Sta rte r OFF
Transmission A/T
CONSULT-III Not connected
Order Input Output Control unit condition
1 Ignition switch — Driver seat control unit receives the signals of [ignition switch signal]
from BCM via CAN communication.
2— Motors
(Sliding, tilt)Driver side control unit operates the sliding motor when the operating
conditions are satisfied and requests the operations of tilt motor to
automatic drive positioner control unit via UART communication. The
automatic drive positioner operates each motor.
3 Sensors
(Sliding, tilt) —Each sensor monitors the operating positions of seat and steering,
and then stops the operation of each motor when each part reaches
the recorded address.
Revision: 2010 May2011 QX56