Connector JAGUAR X308 1998 2.G Workshop Manual
[x] Cancel search | Manufacturer: JAGUAR, Model Year: 1998, Model line: X308, Model: JAGUAR X308 1998 2.GPages: 2490, PDF Size: 69.81 MB
Page 1778 of 2490
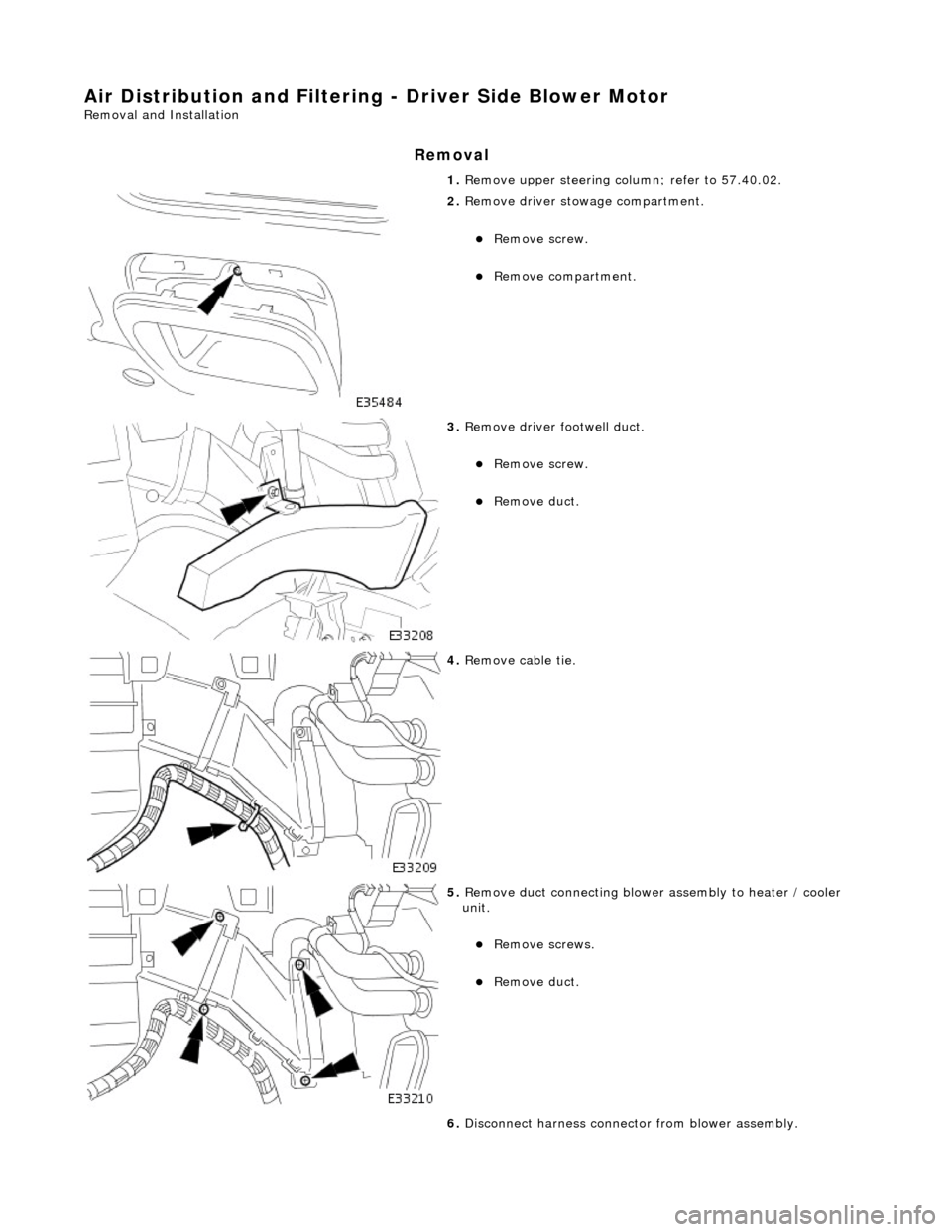
Air Distribution and Filtering - Driver Side Blower Motor
Removal and Installation
Removal
1. Remove upper steering co lumn; refer to 57.40.02.
2. Remove driver stowage compartment.
Remove screw.
Remove compartment.
3. Remove driver footwell duct.
Remove screw.
Remove duct.
4. Remove cable tie.
5. Remove duct connecting blower assembly to heater / cooler
unit.
Remove screws.
Remove duct.
6. Disconnect harness connector from blower assembly.
Page 1779 of 2490
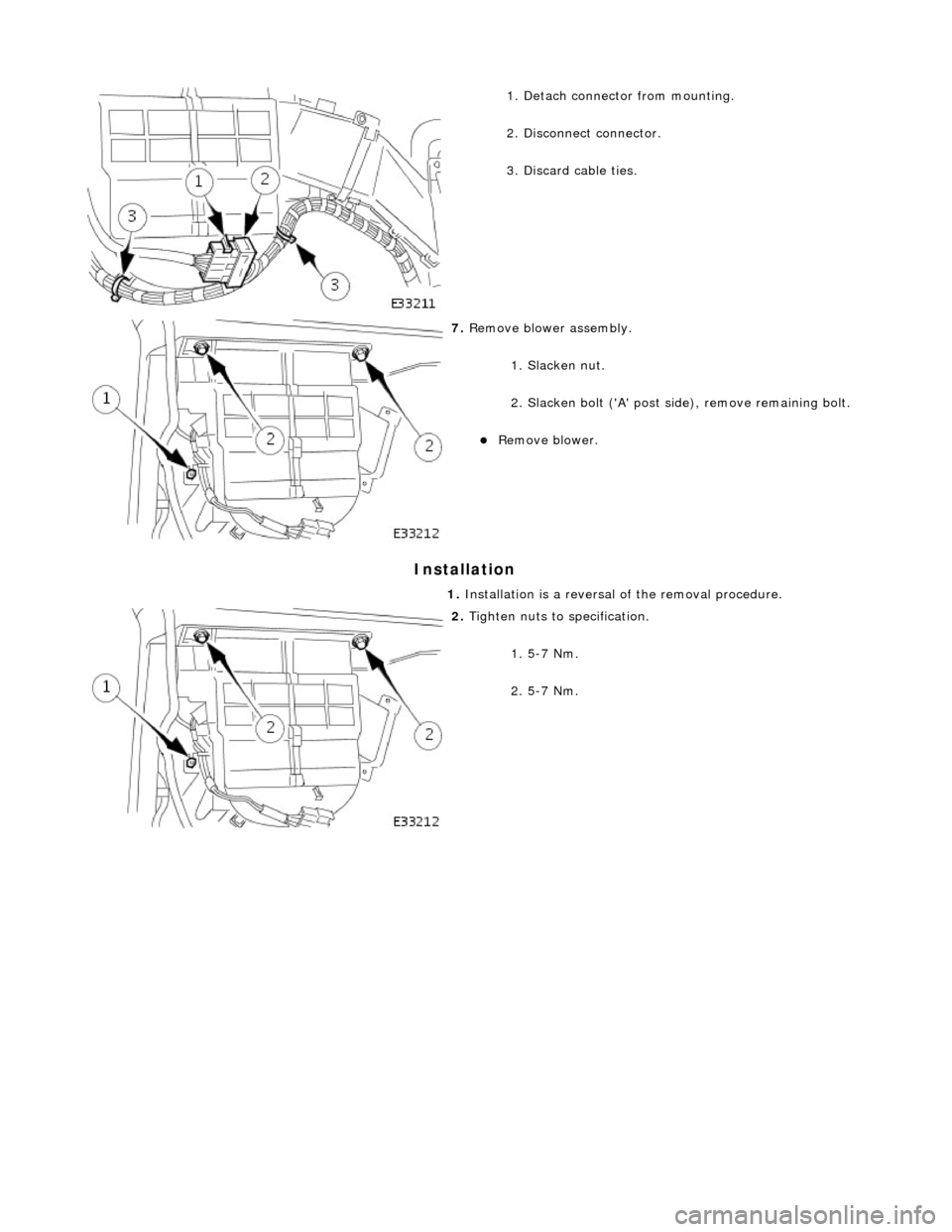
Installation
1. Detach connector from mounting.
2. Disconnect connector.
3. Discard cable ties.
7. Remove blower assembly.
1. Slacken nut.
2. Slacken bolt ('A' post si de), remove remaining bolt.
Remove blower.
1. Installation is a reversal of the removal procedure.
2. Tighten nuts to specification.
1. 5-7 Nm.
2. 5-7 Nm.
Page 1780 of 2490
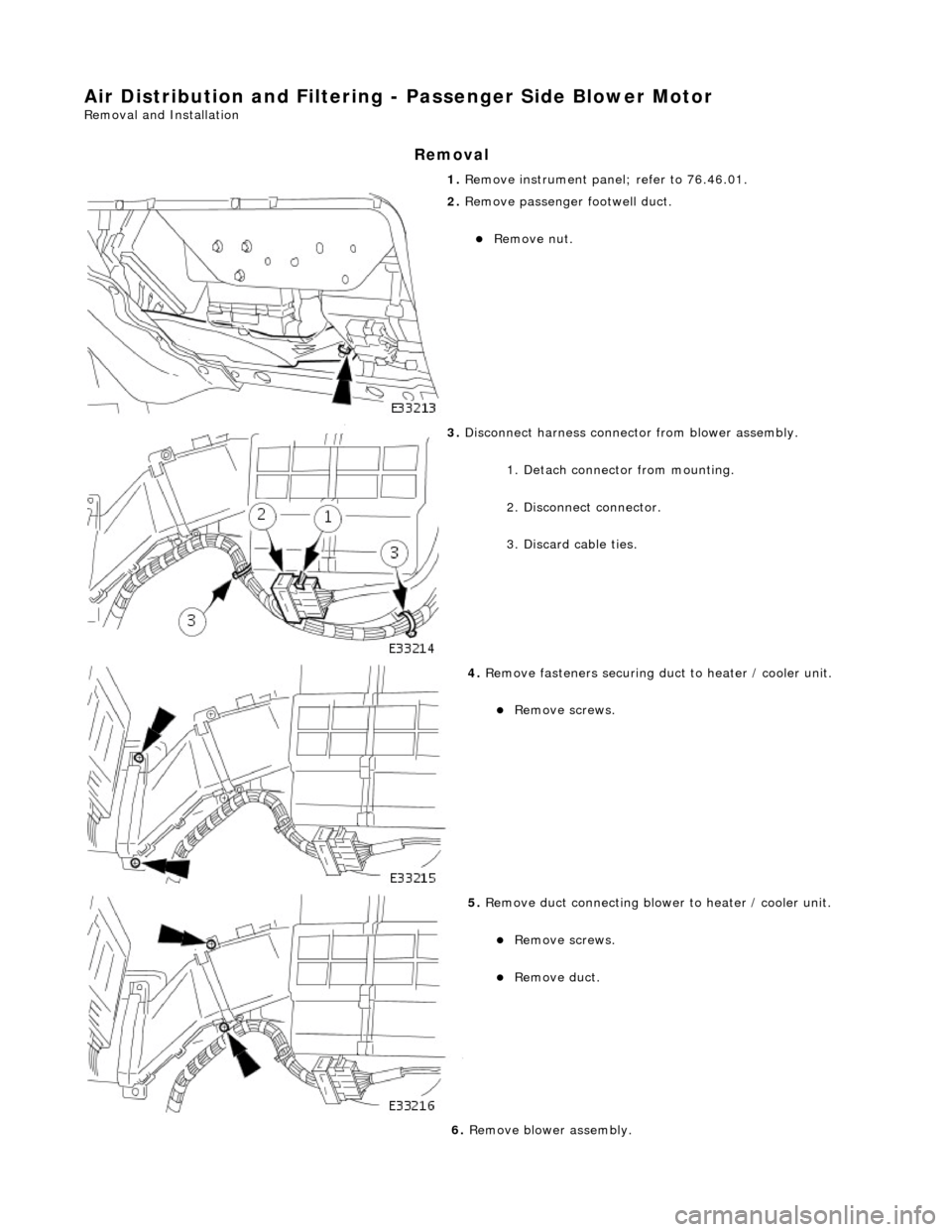
Air Distribution and Filtering - Passenger Side Blower Motor
Removal and Installation
Removal
1. Remove instrument panel; refer to 76.46.01.
2. Remove passenger footwell duct.
Remove nut.
3. Disconnect harness connector from blower assembly.
1. Detach connector from mounting.
2. Disconnect connector.
3. Discard cable ties.
4. Remove fasteners securing duct to heater / cooler unit.
Remove screws.
5. Remove duct connecting blower to heater / cooler unit.
Remove screws.
Remove duct.
6. Remove blower assembly.
Page 1782 of 2490
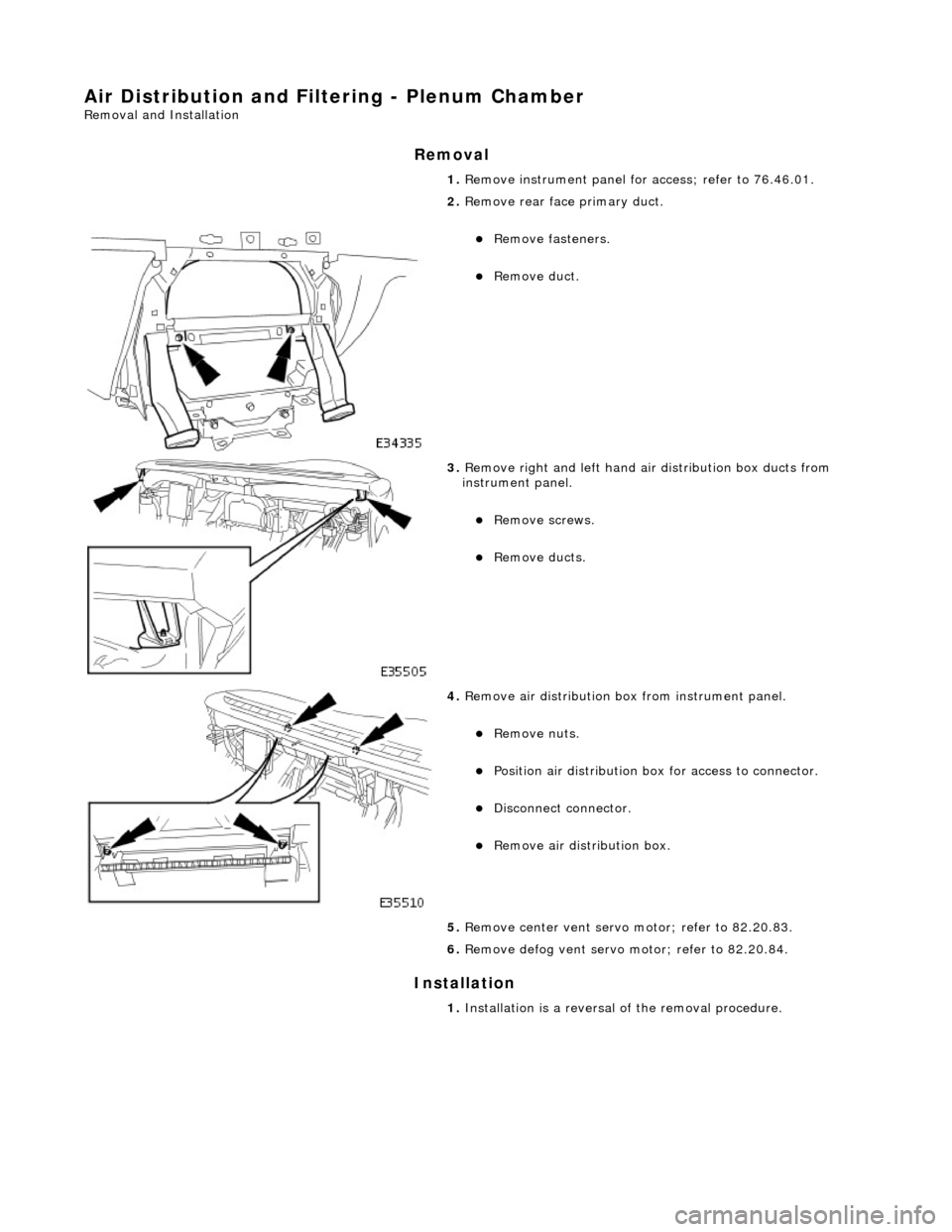
Air Distribution and Filtering - Plenum Chamber
Removal and Installation
Removal
Installation
1.
Remove instrument panel for access; refer to 76.46.01.
2. Remove rear face primary duct.
Remove fasteners.
Remove duct.
3. Remove right and left hand ai r distribution box ducts from
instrument panel.
Remove screws.
Remove ducts.
4. Remove air distribution bo x from instrument panel.
Remove nuts.
Position air distribution box for access to connector.
Disconnect connector.
Remove air distribution box.
5. Remove center vent servo motor; refer to 82.20.83.
6. Remove defog vent servo motor; refer to 82.20.84.
1. Installation is a reversal of the removal procedure.
Page 1784 of 2490
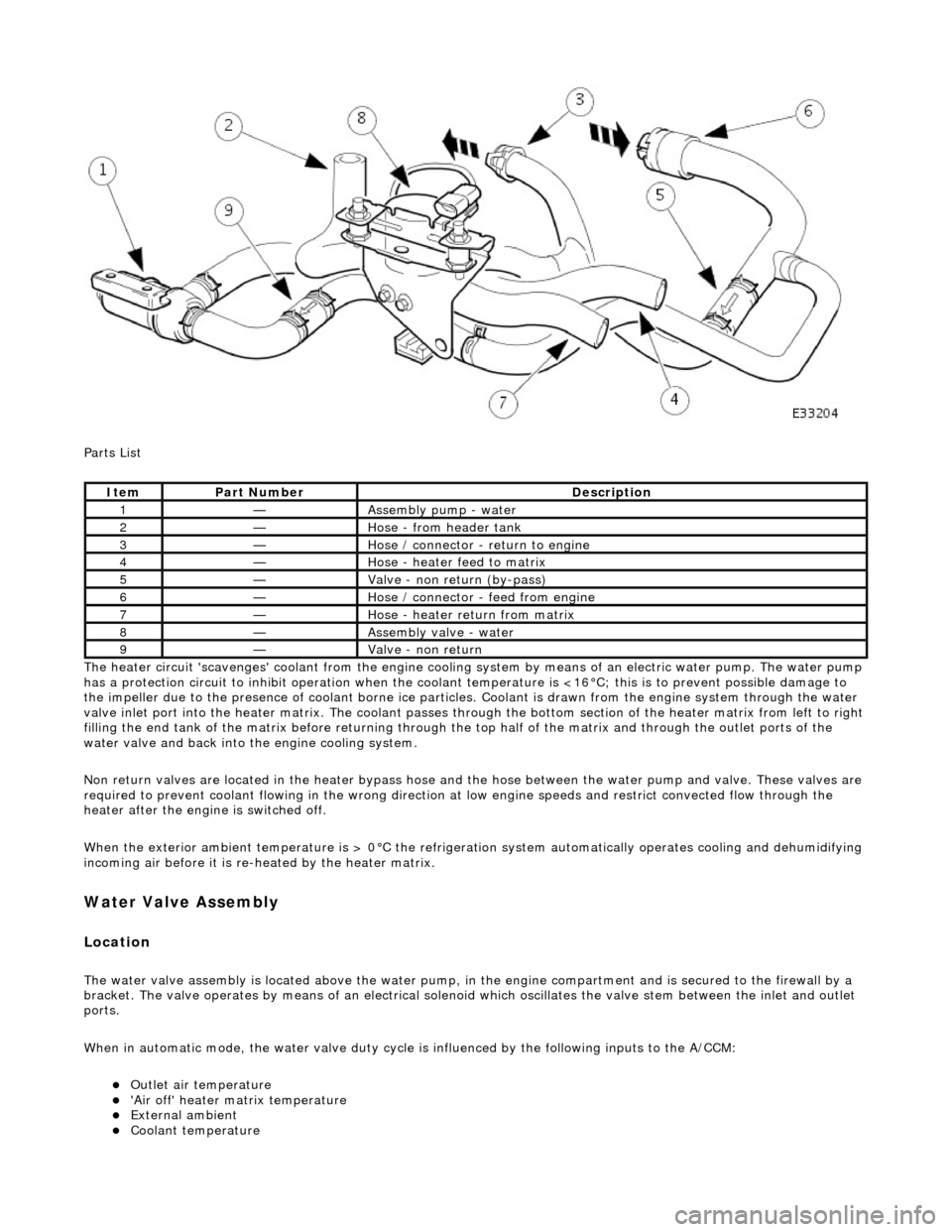
Parts List
The heater circuit 'scavenges' coolant from the engine cooling system by mean s of an electric water pump. The water pump
has a protection circuit to inhibit operation when the coolant temperature is <16°C; this is to prevent possible damage to
the impeller due to the presence of coolant borne ice particles. Coolant is drawn from the en gine system through the water
valve inlet port into the heater matrix. The coolant passes thro ugh the bottom section of the heater matrix from left to right
filling the end tank of the matrix before returning through the top half of the ma trix and through the outlet ports of the
water valve and back into the engine cooling system.
Non return valves are located in the heat er bypass hose and the hose between the water pump and valve. These valves are
required to prevent coolant flowing in th e wrong direction at low engine speeds and restrict convected flow through the
heater after the engine is switched off.
When the exterior ambient temperature is > 0°C the refrigerat ion system automatically operates cooling and dehumidifying
incoming air before it is re -heated by the heater matrix.
Water Valve Assembly
Location
The water valve assembly is located above the water pump, in the engine compartmen t and is secured to the firewall by a
bracket. The valve operates by means of an electrical solenoid which oscillates the valve stem between the inlet and outlet
ports.
When in automatic mode, the water valve duty cycle is influenced by the following inputs to the A/CCM:
Outlet air temperature 'Air off' heater matrix temperature External ambient Coolant temperature
ItemPart NumberDescription
1—Assembly pump - water
2—Hose - from header tank
3—Hose / connector - return to engine
4—Hose - heater feed to matrix
5—Valve - non return (by-pass)
6—Hose / connector - feed from engine
7—Hose - heater return from matrix
8—Assembly valve - water
9—Valve - non return
Page 1785 of 2490
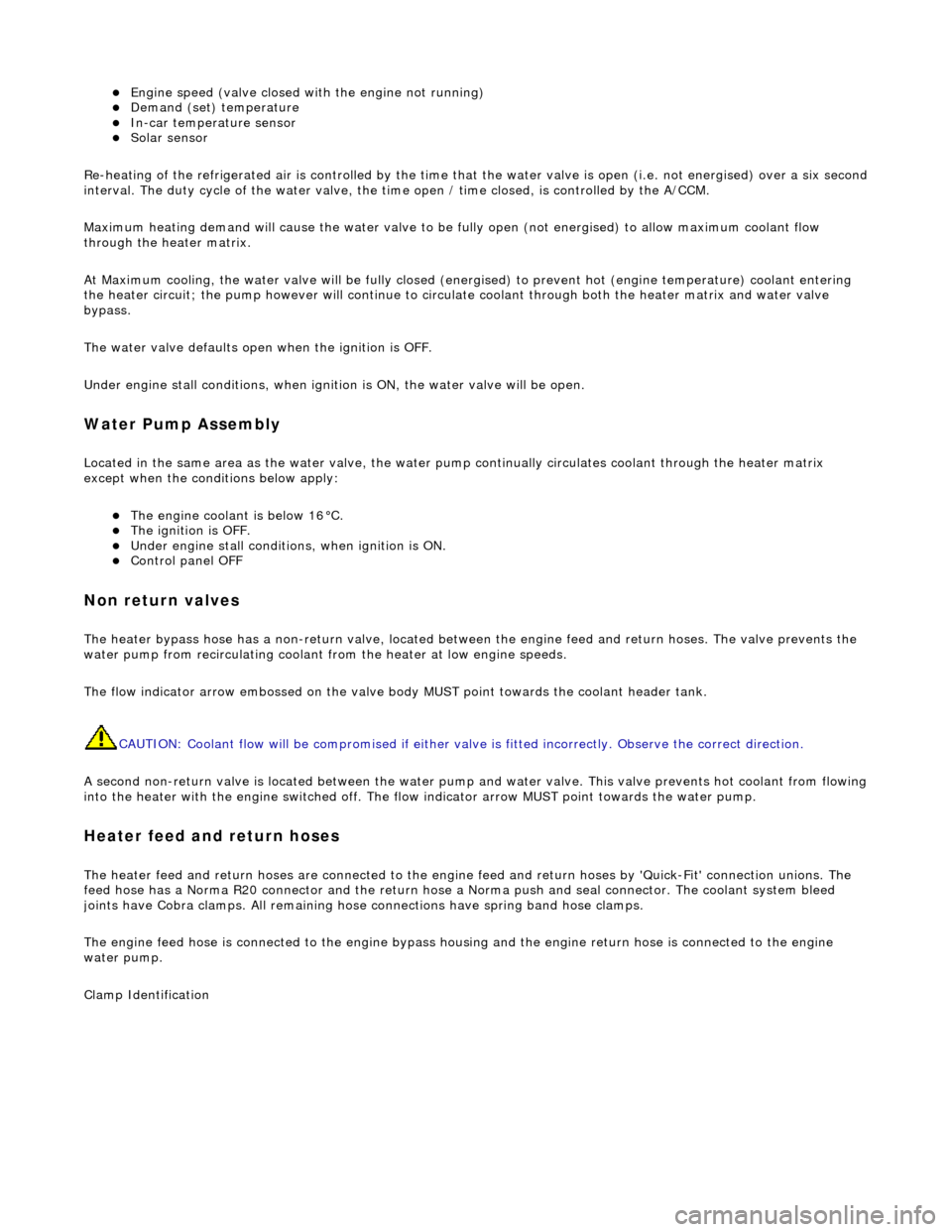
Engine speed (valve closed with the engine not running) Demand (set) temperature In-car temperature sensor Solar sensor
Re-heating of the refrigerated air is contro lled by the time that the water valve is open (i.e. not energised) over a six secon d
interval. The duty cycle of the water valve, the time open / time closed, is controlled by the A/CCM.
Maximum heating demand will cause the water valve to be fu lly open (not energised) to allow maximum coolant flow
through the heater matrix.
At Maximum cooling, the water va lve will be fully closed (energised) to prevent hot (engine temperature) coolant entering
the heater circuit; the pump however will continue to circulate coolant through both the heater matrix and water valve
bypass.
The water valve defaults open when the ignition is OFF.
Under engine stall conditions, when ignition is ON, the water valve will be open.
Water Pump Assembly
Located in the same area as the water valve, the water pump continually circulates coolant through the heater matrix
except when the conditions below apply:
The engine coolant is below 16°C. The ignition is OFF. Under engine stall conditions, when ignition is ON. Control panel OFF
Non return valves
The heater bypass hose has a non-return valve, located between the engine feed and return hoses. The valve prevents the
water pump from recirculating coolant fro m the heater at low engine speeds.
The flow indicator arrow embossed on the valve bo dy MUST point towards the coolant header tank.
CAUTION: Coolant flow will be compromi sed if either valve is fitted incorrectly. Observe the correct direction.
A second non-return valve is located betw een the water pump and water valve. This valve prevents hot coolant from flowing
into the heater with the engine switched off. The flow indicator arrow MUST point towards the water pump.
Heater feed and return hoses
The heater feed and return hoses are connected to the engine feed and return hoses by 'Quick-Fit' connection unions. The
feed hose has a Norma R20 connector and the return hose a Norma push and seal connector. The coolant system bleed
joints have Cobra clamps. All remaining hose connections have spring band hose clamps.
The engine feed hose is connected to the engine bypass hous ing and the engine return hose is connected to the engine
water pump.
Clamp Identification
Page 1787 of 2490
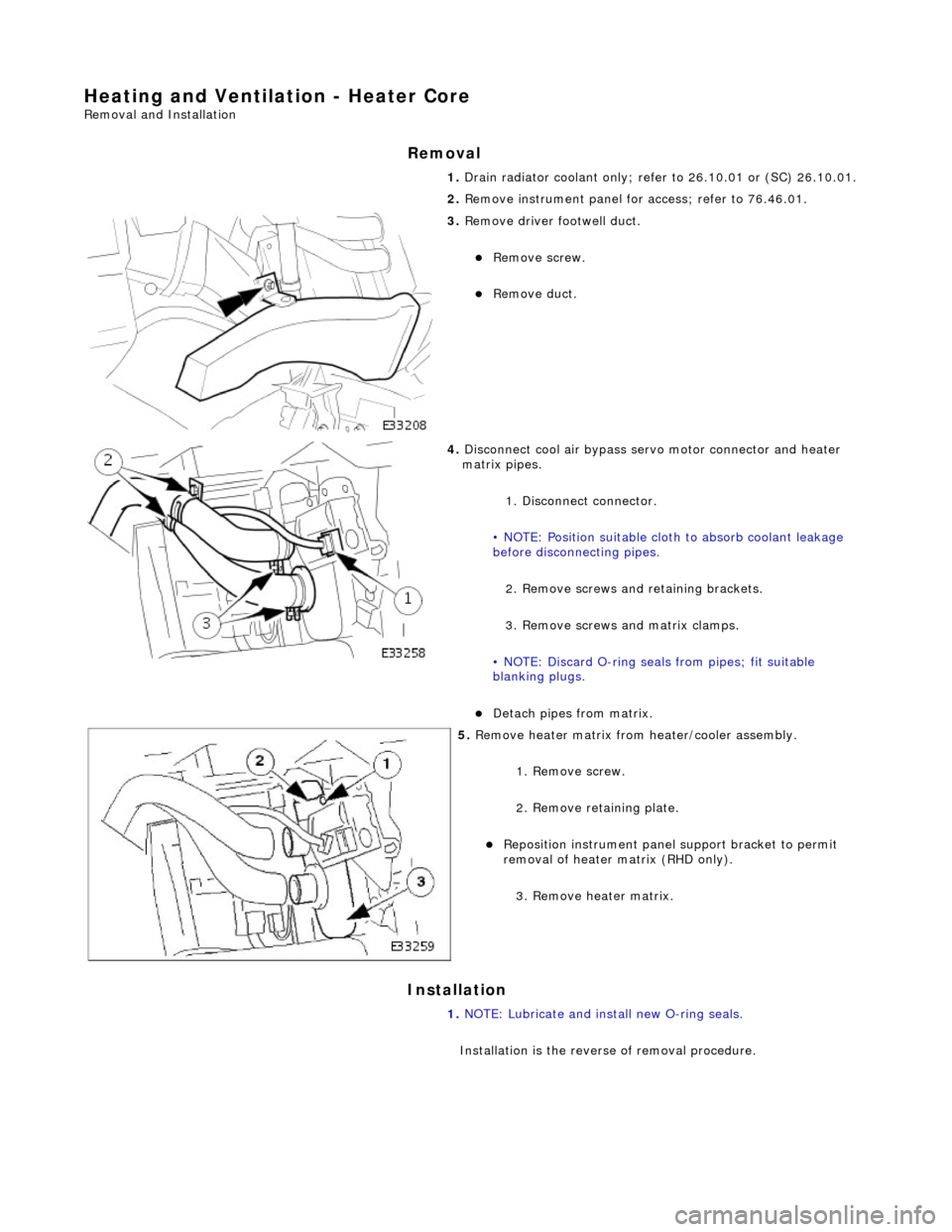
Heating and Ventilation - Heater Core
Removal and Installation
Removal
Installation
1.
Drain radiator coolant only; re fer to 26.10.01 or (SC) 26.10.01.
2. Remove instrument panel for access; refer to 76.46.01.
3. Remove driver footwell duct.
Remove screw.
Remove duct.
4. Disconnect cool air bypass serv o motor connector and heater
matrix pipes.
1. Disconnect connector.
• NOTE: Position suitable clot h to absorb coolant leakage
before disconnecting pipes.
2. Remove screws and retaining brackets.
3. Remove screws and matrix clamps.
• NOTE: Discard O-ring seals from pipes; fit suitable
blanking plugs.
Detach pipes from matrix.
5. Remove heater matrix from heater/cooler assembly.
1. Remove screw.
2. Remove retaining plate.
Reposition instrument panel support bracket to permit
removal of heater matrix (RHD only).
3. Remove heater matrix.
1. NOTE: Lubricate and install new O-ring seals.
Installation is the reverse of removal procedure.
Page 1790 of 2490
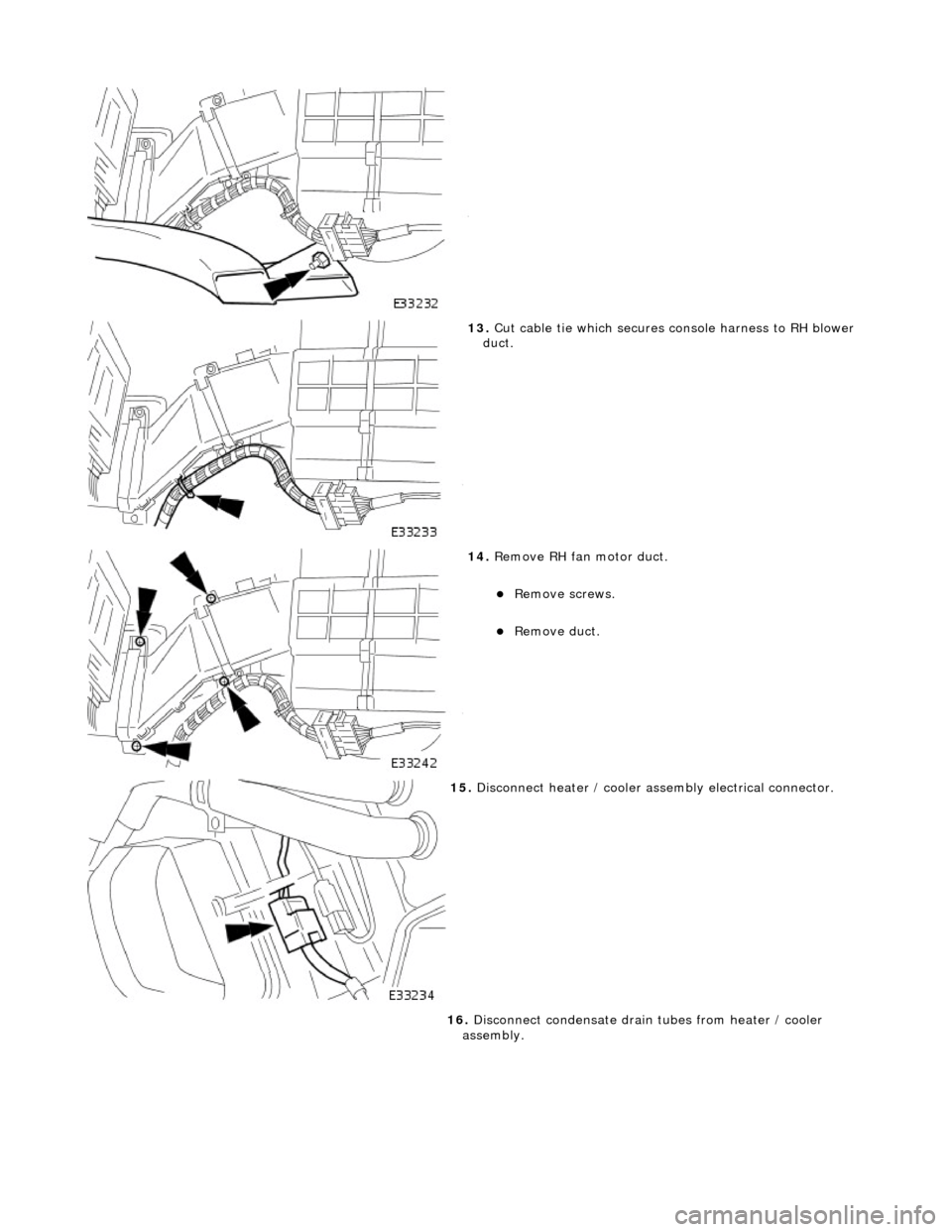
13. Cut cable tie which secures console harness to RH blower
duct.
14. Remove RH fan motor duct.
Remove screws.
Remove duct.
15. Disconnect heater / cooler assembly electrical connector.
16. Disconnect condensate drain tubes from heater / cooler
assembly.
Page 1791 of 2490
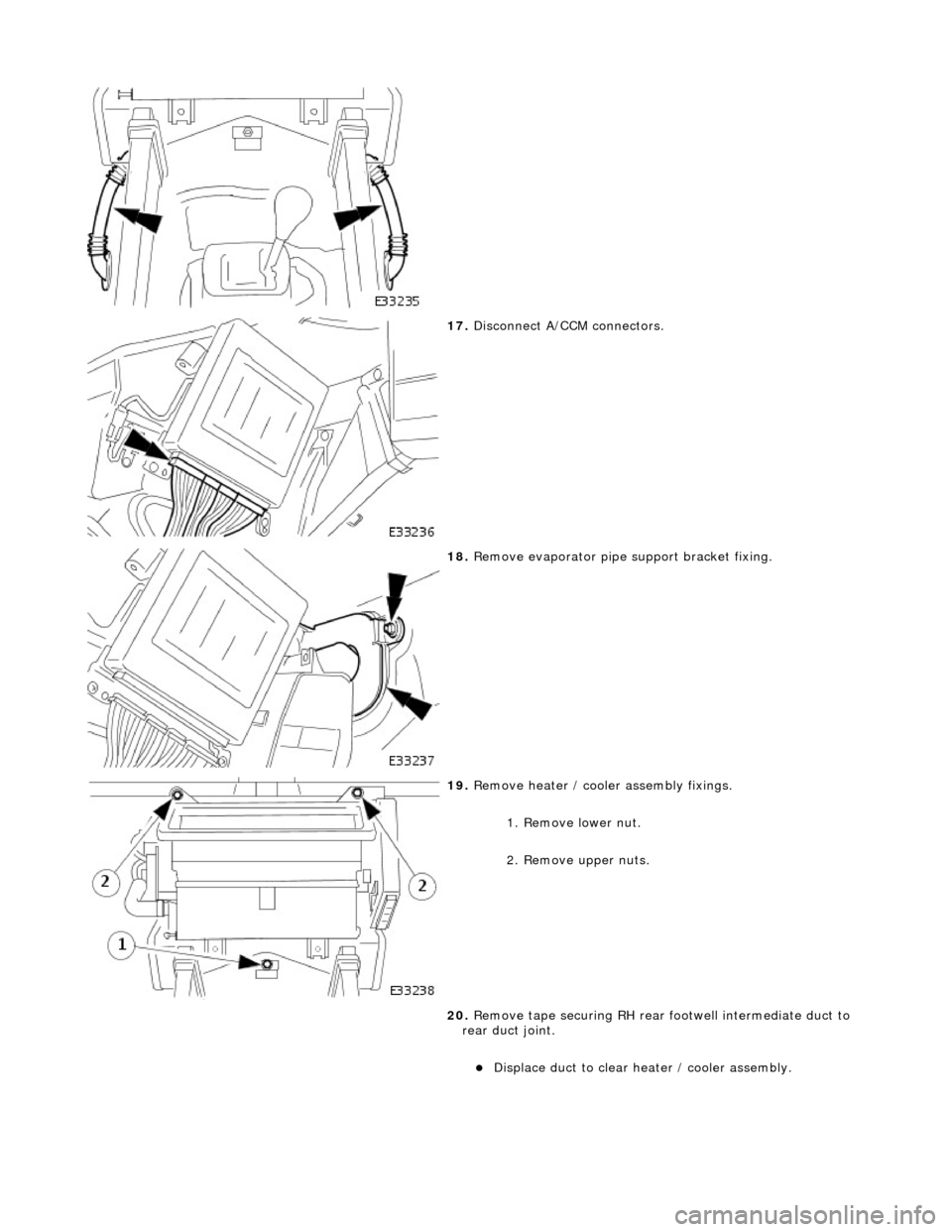
17. Disconnect A/CCM connectors.
18. Remove evaporator pipe support bracket fixing.
19. Remove heater / cooler assembly fixings.
1. Remove lower nut.
2. Remove upper nuts.
20. Remove tape securing RH rear footwell intermediate duct to
rear duct joint.
Displace duct to clear heater / cooler assembly.
Page 1793 of 2490
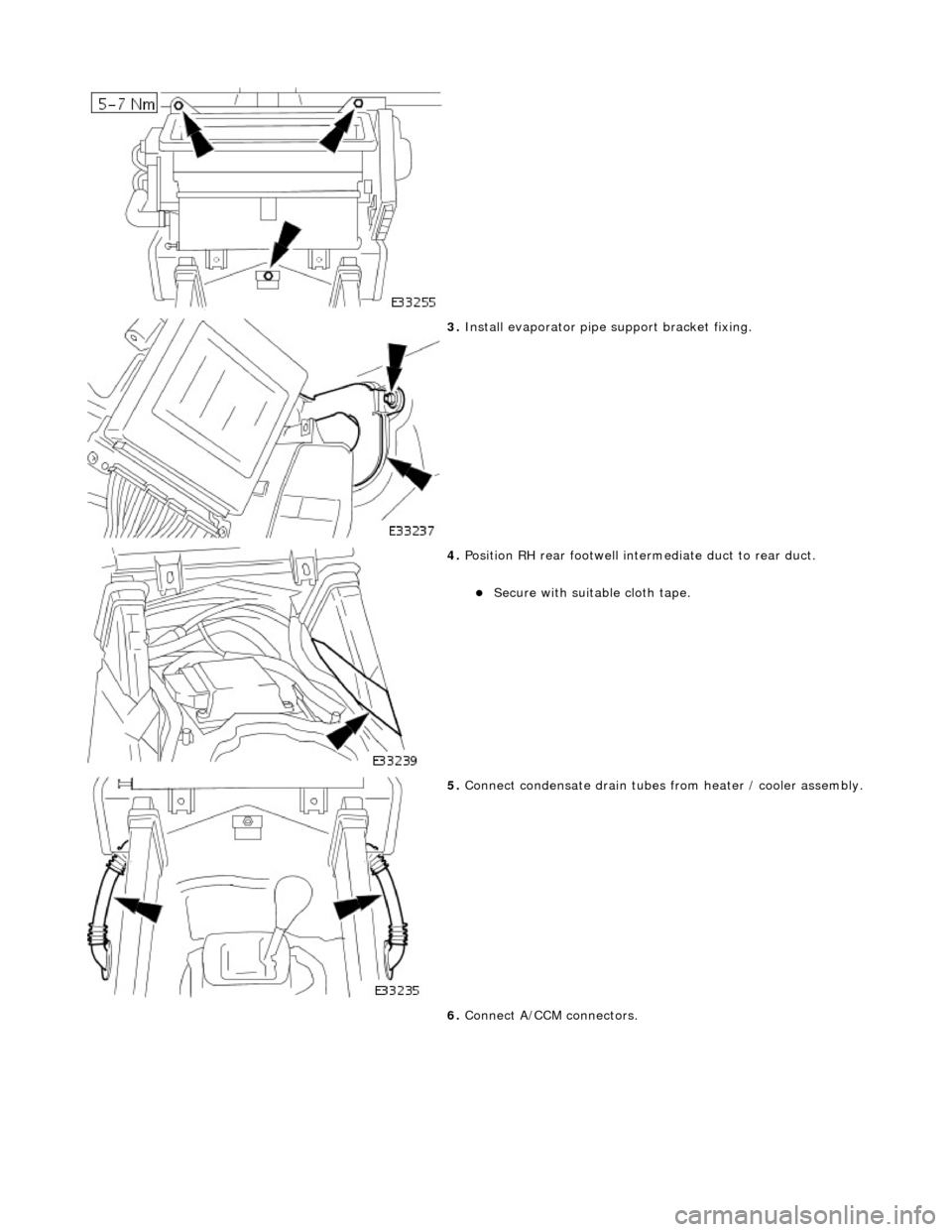
3. Install evaporator pipe support bracket fixing.
4. Position RH rear footwell inte rmediate duct to rear duct.
Secure with suitable cloth tape.
5. Connect condensate drain tubes from heater / cooler assembly.
6. Connect A/CCM connectors.