check engine LAND ROVER DISCOVERY 2002 Repair Manual
[x] Cancel search | Manufacturer: LAND ROVER, Model Year: 2002, Model line: DISCOVERY, Model: LAND ROVER DISCOVERY 2002Pages: 1672, PDF Size: 46.1 MB
Page 353 of 1672
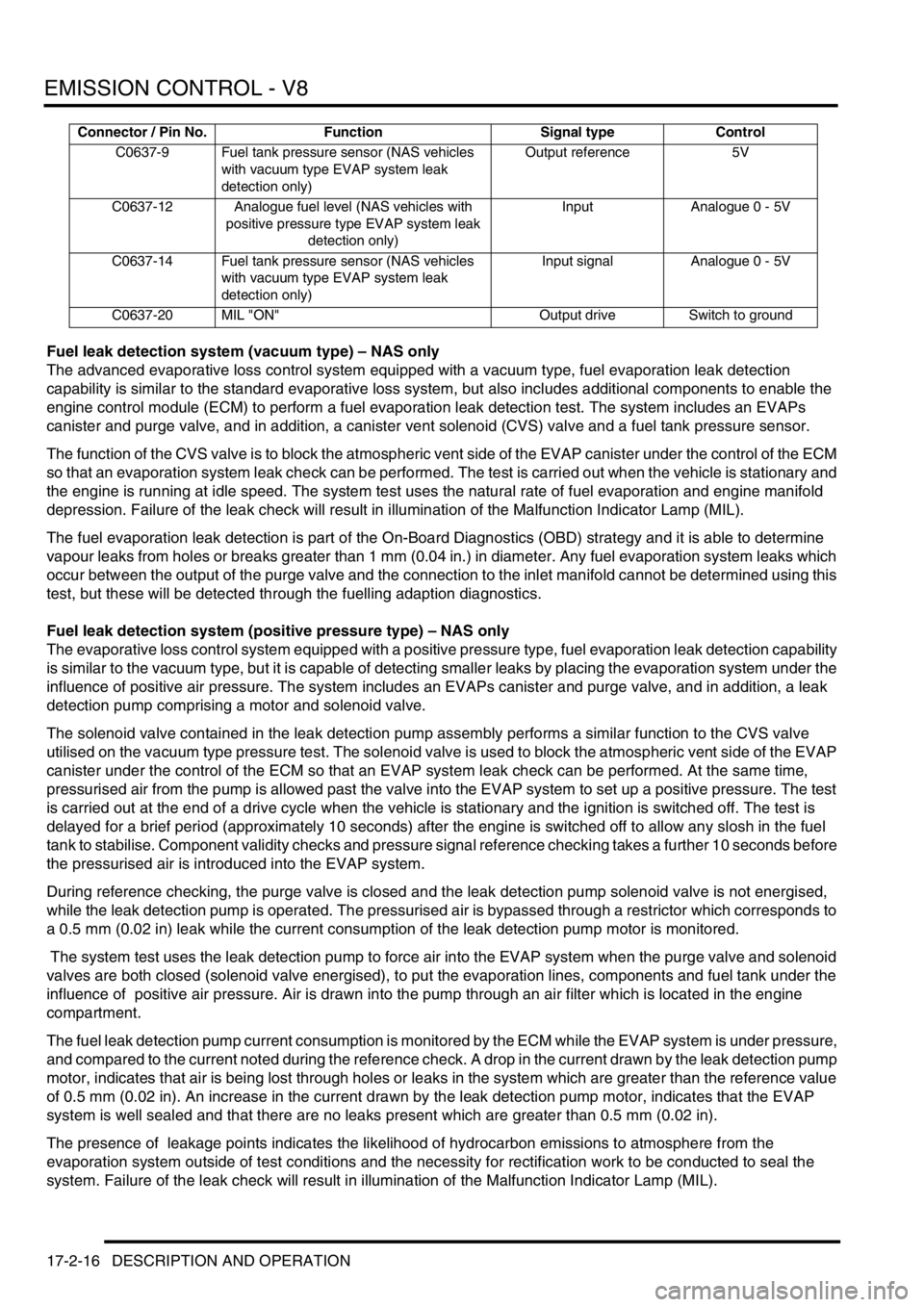
EMISSION CONTROL - V8
17-2-16 DESCRIPTION AND OPERATION
Fuel leak detection system (vacuum type) – NAS only
The advanced evaporative loss control system equipped with a vacuum type, fuel evaporation leak detection
capability is similar to the standard evaporative loss system, but also includes additional components to enable the
engine control module (ECM) to perform a fuel evaporation leak detection test. The system includes an EVAPs
canister and purge valve, and in addition, a canister vent solenoid (CVS) valve and a fuel tank pressure sensor.
The function of the CVS valve is to block the atmospheric vent side of the EVAP canister under the control of the ECM
so that an evaporation system leak check can be performed. The test is carried out when the vehicle is stationary and
the engine is running at idle speed. The system test uses the natural rate of fuel evaporation and engine manifold
depression. Failure of the leak check will result in illumination of the Malfunction Indicator Lamp (MIL).
The fuel evaporation leak detection is part of the On-Board Diagnostics (OBD) strategy and it is able to determine
vapour leaks from holes or breaks greater than 1 mm (0.04 in.) in diameter. Any fuel evaporation system leaks which
occur between the output of the purge valve and the connection to the inlet manifold cannot be determined using this
test, but these will be detected through the fuelling adaption diagnostics.
Fuel leak detection system (positive pressure type) – NAS only
The evaporative loss control system equipped with a positive pressure type, fuel evaporation leak detection capability
is similar to the vacuum type, but it is capable of detecting smaller leaks by placing the evaporation system under the
influence of positive air pressure. The system includes an EVAPs canister and purge valve, and in addition, a leak
detection pump comprising a motor and solenoid valve.
The solenoid valve contained in the leak detection pump assembly performs a similar function to the CVS valve
utilised on the vacuum type pressure test. The solenoid valve is used to block the atmospheric vent side of the EVAP
canister under the control of the ECM so that an EVAP system leak check can be performed. At the same time,
pressurised air from the pump is allowed past the valve into the EVAP system to set up a positive pressure. The test
is carried out at the end of a drive cycle when the vehicle is stationary and the ignition is switched off. The test is
delayed for a brief period (approximately 10 seconds) after the engine is switched off to allow any slosh in the fuel
tank to stabilise. Component validity checks and pressure signal reference checking takes a further 10 seconds before
the pressurised air is introduced into the EVAP system.
During reference checking, the purge valve is closed and the leak detection pump solenoid valve is not energised,
while the leak detection pump is operated. The pressurised air is bypassed through a restrictor which corresponds to
a 0.5 mm (0.02 in) leak while the current consumption of the leak detection pump motor is monitored.
The system test uses the leak detection pump to force air into the EVAP system when the purge valve and solenoid
valves are both closed (solenoid valve energised), to put the evaporation lines, components and fuel tank under the
influence of positive air pressure. Air is drawn into the pump through an air filter which is located in the engine
compartment.
The fuel leak detection pump current consumption is monitored by the ECM while the EVAP system is under pressure,
and compared to the current noted during the reference check. A drop in the current drawn by the leak detection pump
motor, indicates that air is being lost through holes or leaks in the system which are greater than the reference value
of 0.5 mm (0.02 in). An increase in the current drawn by the leak detection pump motor, indicates that the EVAP
system is well sealed and that there are no leaks present which are greater than 0.5 mm (0.02 in).
The presence of leakage points indicates the likelihood of hydrocarbon emissions to atmosphere from the
evaporation system outside of test conditions and the necessity for rectification work to be conducted to seal the
system. Failure of the leak check will result in illumination of the Malfunction Indicator Lamp (MIL).
C0637-9 Fuel tank pressure sensor (NAS vehicles
with vacuum type EVAP system leak
detection only)Output reference 5V
C0637-12 Analogue fuel level (NAS vehicles with
positive pressure type EVAP system leak
detection only)Input Analogue 0 - 5V
C0637-14 Fuel tank pressure sensor (NAS vehicles
with vacuum type EVAP system leak
detection only)Input signal Analogue 0 - 5V
C0637-20 MIL "ON" Output drive Switch to ground Connector / Pin No. Function Signal type Control
Page 358 of 1672
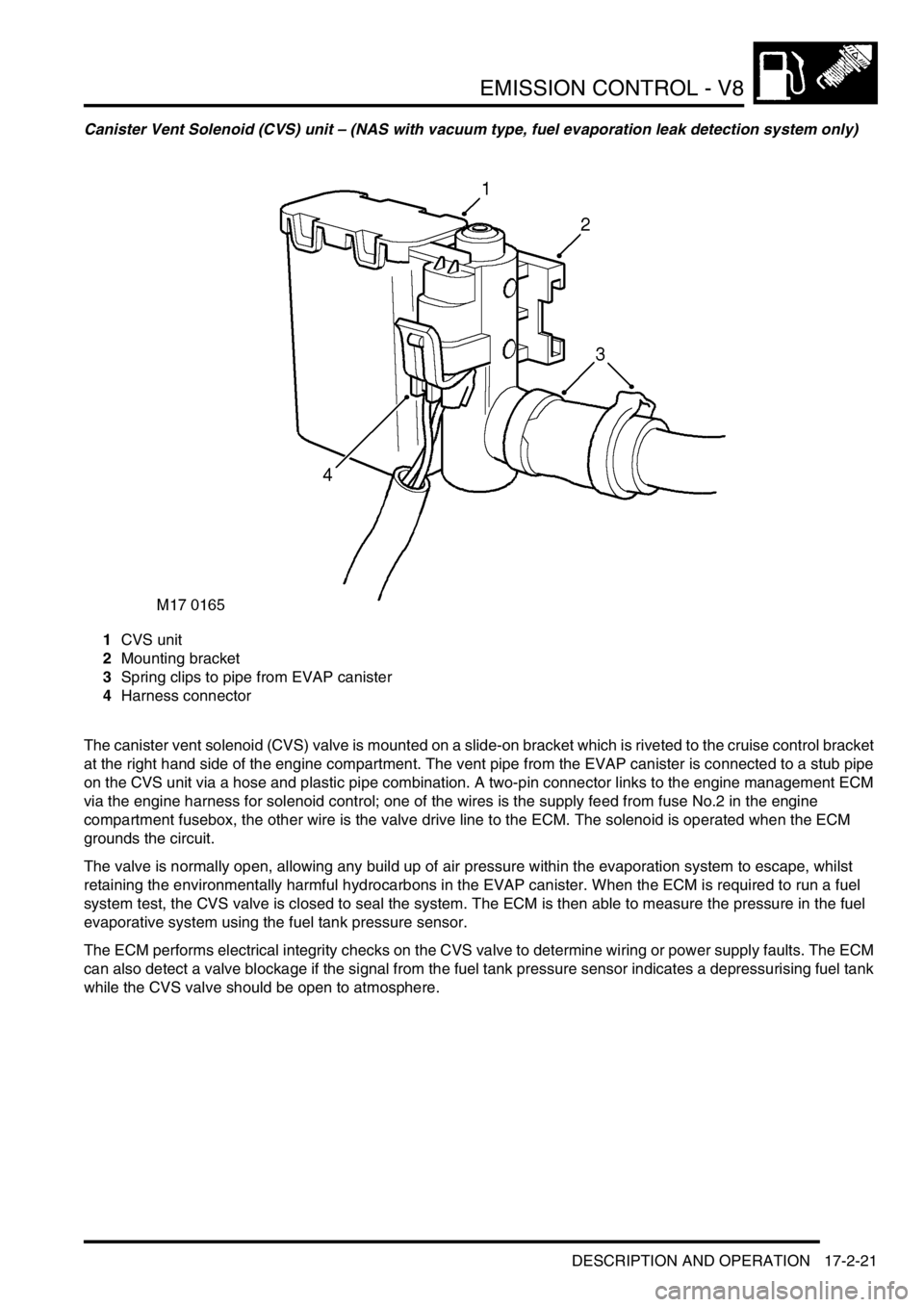
EMISSION CONTROL - V8
DESCRIPTION AND OPERATION 17-2-21
Canister Vent Solenoid (CVS) unit – (NAS with vacuum type, fuel evaporation leak detection system only)
1CVS unit
2Mounting bracket
3Spring clips to pipe from EVAP canister
4Harness connector
The canister vent solenoid (CVS) valve is mounted on a slide-on bracket which is riveted to the cruise control bracket
at the right hand side of the engine compartment. The vent pipe from the EVAP canister is connected to a stub pipe
on the CVS unit via a hose and plastic pipe combination. A two-pin connector links to the engine management ECM
via the engine harness for solenoid control; one of the wires is the supply feed from fuse No.2 in the engine
compartment fusebox, the other wire is the valve drive line to the ECM. The solenoid is operated when the ECM
grounds the circuit.
The valve is normally open, allowing any build up of air pressure within the evaporation system to escape, whilst
retaining the environmentally harmful hydrocarbons in the EVAP canister. When the ECM is required to run a fuel
system test, the CVS valve is closed to seal the system. The ECM is then able to measure the pressure in the fuel
evaporative system using the fuel tank pressure sensor.
The ECM performs electrical integrity checks on the CVS valve to determine wiring or power supply faults. The ECM
can also detect a valve blockage if the signal from the fuel tank pressure sensor indicates a depressurising fuel tank
while the CVS valve should be open to atmosphere.
Page 362 of 1672
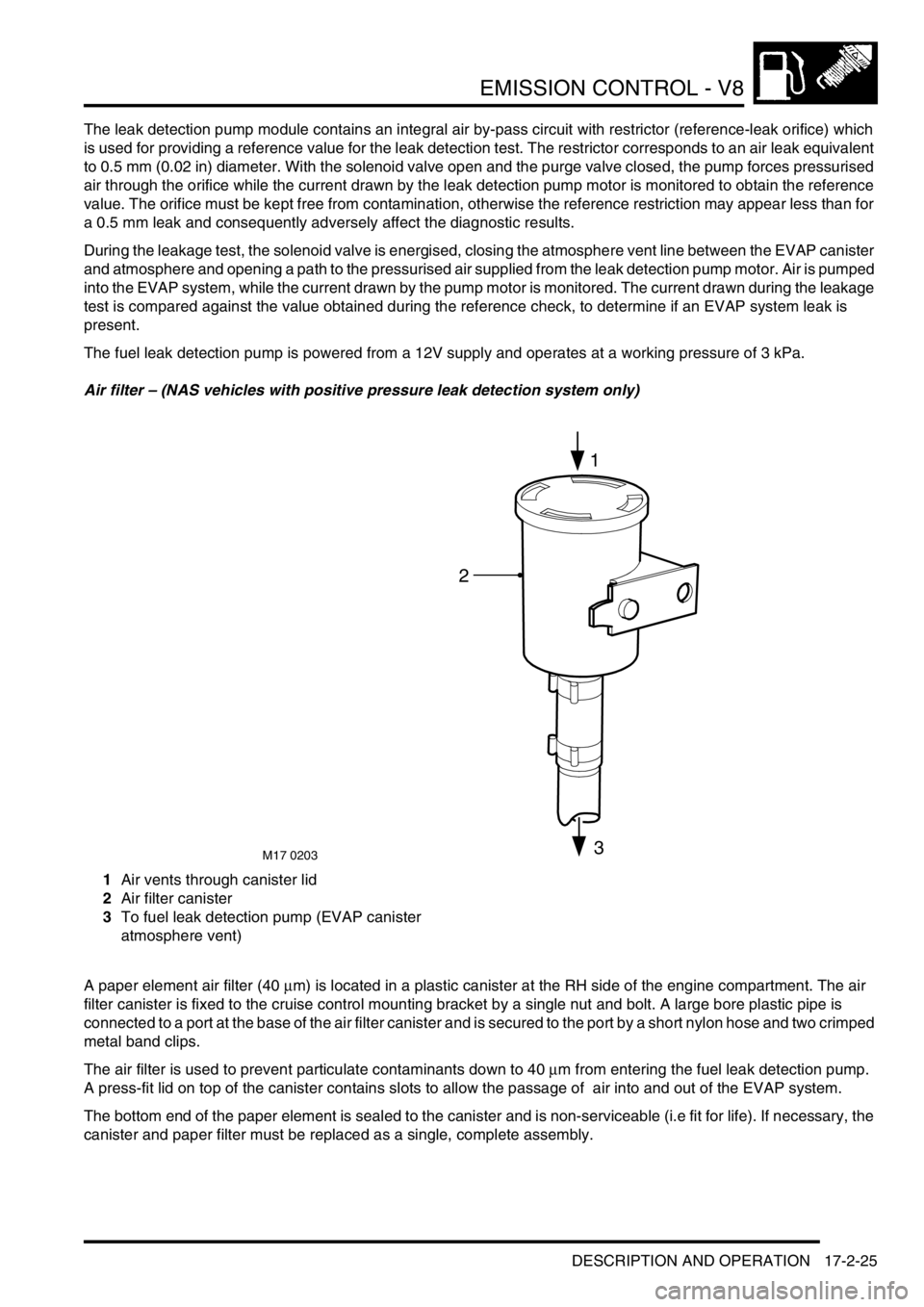
EMISSION CONTROL - V8
DESCRIPTION AND OPERATION 17-2-25
The leak detection pump module contains an integral air by-pass circuit with restrictor (reference-leak orifice) which
is used for providing a reference value for the leak detection test. The restrictor corresponds to an air leak equivalent
to 0.5 mm (0.02 in) diameter. With the solenoid valve open and the purge valve closed, the pump forces pressurised
air through the orifice while the current drawn by the leak detection pump motor is monitored to obtain the reference
value. The orifice must be kept free from contamination, otherwise the reference restriction may appear less than for
a 0.5 mm leak and consequently adversely affect the diagnostic results.
During the leakage test, the solenoid valve is energised, closing the atmosphere vent line between the EVAP canister
and atmosphere and opening a path to the pressurised air supplied from the leak detection pump motor. Air is pumped
into the EVAP system, while the current drawn by the pump motor is monitored. The current drawn during the leakage
test is compared against the value obtained during the reference check, to determine if an EVAP system leak is
present.
The fuel leak detection pump is powered from a 12V supply and operates at a working pressure of 3 kPa.
Air filter – (NAS vehicles with positive pressure leak detection system only)
1Air vents through canister lid
2Air filter canister
3To fuel leak detection pump (EVAP canister
atmosphere vent)
A paper element air filter (40
µm) is located in a plastic canister at the RH side of the engine compartment. The air
filter canister is fixed to the cruise control mounting bracket by a single nut and bolt. A large bore plastic pipe is
connected to a port at the base of the air filter canister and is secured to the port by a short nylon hose and two crimped
metal band clips.
The air filter is used to prevent particulate contaminants down to 40
µm from entering the fuel leak detection pump.
A press-fit lid on top of the canister contains slots to allow the passage of air into and out of the EVAP system.
The bottom end of the paper element is sealed to the canister and is non-serviceable (i.e fit for life). If necessary, the
canister and paper filter must be replaced as a single, complete assembly.
M17 0203
2
1
3
Page 363 of 1672
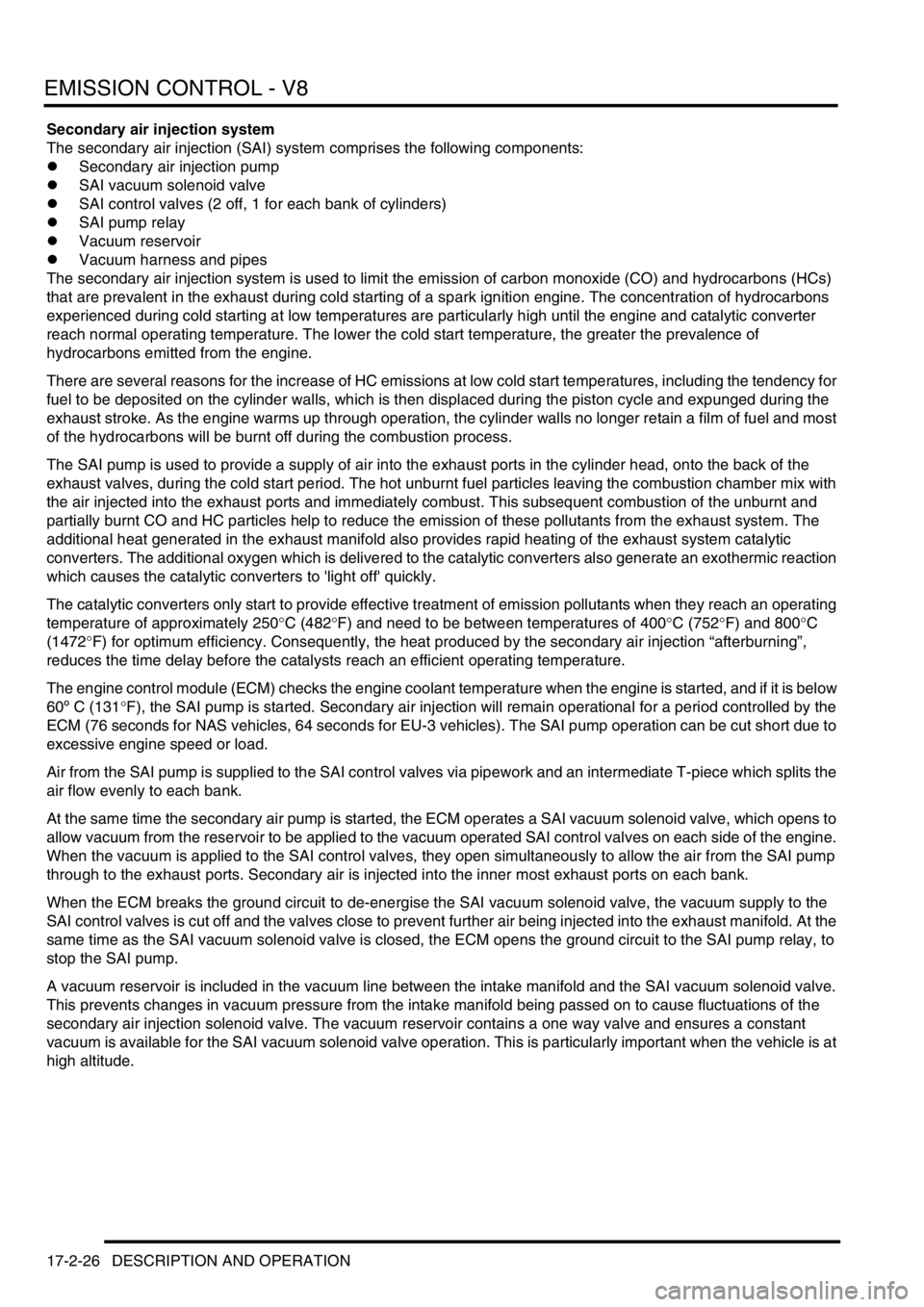
EMISSION CONTROL - V8
17-2-26 DESCRIPTION AND OPERATION
Secondary air injection system
The secondary air injection (SAI) system comprises the following components:
lSecondary air injection pump
lSAI vacuum solenoid valve
lSAI control valves (2 off, 1 for each bank of cylinders)
lSAI pump relay
lVacuum reservoir
lVacuum harness and pipes
The secondary air injection system is used to limit the emission of carbon monoxide (CO) and hydrocarbons (HCs)
that are prevalent in the exhaust during cold starting of a spark ignition engine. The concentration of hydrocarbons
experienced during cold starting at low temperatures are particularly high until the engine and catalytic converter
reach normal operating temperature. The lower the cold start temperature, the greater the prevalence of
hydrocarbons emitted from the engine.
There are several reasons for the increase of HC emissions at low cold start temperatures, including the tendency for
fuel to be deposited on the cylinder walls, which is then displaced during the piston cycle and expunged during the
exhaust stroke. As the engine warms up through operation, the cylinder walls no longer retain a film of fuel and most
of the hydrocarbons will be burnt off during the combustion process.
The SAI pump is used to provide a supply of air into the exhaust ports in the cylinder head, onto the back of the
exhaust valves, during the cold start period. The hot unburnt fuel particles leaving the combustion chamber mix with
the air injected into the exhaust ports and immediately combust. This subsequent combustion of the unburnt and
partially burnt CO and HC particles help to reduce the emission of these pollutants from the exhaust system. The
additional heat generated in the exhaust manifold also provides rapid heating of the exhaust system catalytic
converters. The additional oxygen which is delivered to the catalytic converters also generate an exothermic reaction
which causes the catalytic converters to 'light off' quickly.
The catalytic converters only start to provide effective treatment of emission pollutants when they reach an operating
temperature of approximately 250
°C (482°F) and need to be between temperatures of 400°C (752°F) and 800°C
(1472
°F) for optimum efficiency. Consequently, the heat produced by the secondary air injection “afterburning”,
reduces the time delay before the catalysts reach an efficient operating temperature.
The engine control module (ECM) checks the engine coolant temperature when the engine is started, and if it is below
60º C (131
°F), the SAI pump is started. Secondary air injection will remain operational for a period controlled by the
ECM (76 seconds for NAS vehicles, 64 seconds for EU-3 vehicles). The SAI pump operation can be cut short due to
excessive engine speed or load.
Air from the SAI pump is supplied to the SAI control valves via pipework and an intermediate T-piece which splits the
air flow evenly to each bank.
At the same time the secondary air pump is started, the ECM operates a SAI vacuum solenoid valve, which opens to
allow vacuum from the reservoir to be applied to the vacuum operated SAI control valves on each side of the engine.
When the vacuum is applied to the SAI control valves, they open simultaneously to allow the air from the SAI pump
through to the exhaust ports. Secondary air is injected into the inner most exhaust ports on each bank.
When the ECM breaks the ground circuit to de-energise the SAI vacuum solenoid valve, the vacuum supply to the
SAI control valves is cut off and the valves close to prevent further air being injected into the exhaust manifold. At the
same time as the SAI vacuum solenoid valve is closed, the ECM opens the ground circuit to the SAI pump relay, to
stop the SAI pump.
A vacuum reservoir is included in the vacuum line between the intake manifold and the SAI vacuum solenoid valve.
This prevents changes in vacuum pressure from the intake manifold being passed on to cause fluctuations of the
secondary air injection solenoid valve. The vacuum reservoir contains a one way valve and ensures a constant
vacuum is available for the SAI vacuum solenoid valve operation. This is particularly important when the vehicle is at
high altitude.
Page 371 of 1672
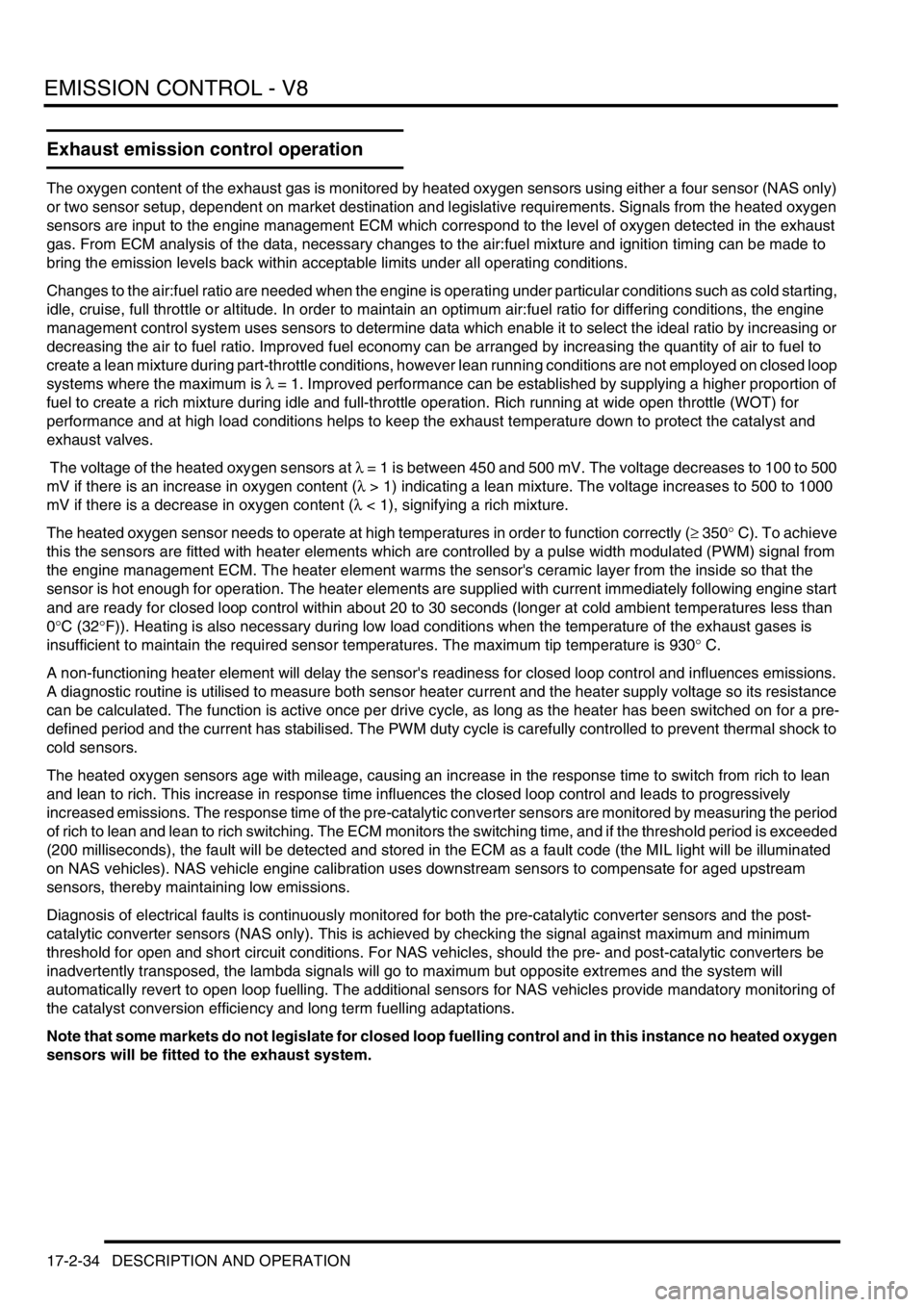
EMISSION CONTROL - V8
17-2-34 DESCRIPTION AND OPERATION
Exhaust emission control operation
The oxygen content of the exhaust gas is monitored by heated oxygen sensors using either a four sensor (NAS only)
or two sensor setup, dependent on market destination and legislative requirements. Signals from the heated oxygen
sensors are input to the engine management ECM which correspond to the level of oxygen detected in the exhaust
gas. From ECM analysis of the data, necessary changes to the air:fuel mixture and ignition timing can be made to
bring the emission levels back within acceptable limits under all operating conditions.
Changes to the air:fuel ratio are needed when the engine is operating under particular conditions such as cold starting,
idle, cruise, full throttle or altitude. In order to maintain an optimum air:fuel ratio for differing conditions, the engine
management control system uses sensors to determine data which enable it to select the ideal ratio by increasing or
decreasing the air to fuel ratio. Improved fuel economy can be arranged by increasing the quantity of air to fuel to
create a lean mixture during part-throttle conditions, however lean running conditions are not employed on closed loop
systems where the maximum is
λ = 1. Improved performance can be established by supplying a higher proportion of
fuel to create a rich mixture during idle and full-throttle operation. Rich running at wide open throttle (WOT) for
performance and at high load conditions helps to keep the exhaust temperature down to protect the catalyst and
exhaust valves.
The voltage of the heated oxygen sensors at
λ = 1 is between 450 and 500 mV. The voltage decreases to 100 to 500
mV if there is an increase in oxygen content (
λ > 1) indicating a lean mixture. The voltage increases to 500 to 1000
mV if there is a decrease in oxygen content (
λ < 1), signifying a rich mixture.
The heated oxygen sensor needs to operate at high temperatures in order to function correctly (
≥ 350° C). To achieve
this the sensors are fitted with heater elements which are controlled by a pulse width modulated (PWM) signal from
the engine management ECM. The heater element warms the sensor's ceramic layer from the inside so that the
sensor is hot enough for operation. The heater elements are supplied with current immediately following engine start
and are ready for closed loop control within about 20 to 30 seconds (longer at cold ambient temperatures less than
0
°C (32°F)). Heating is also necessary during low load conditions when the temperature of the exhaust gases is
insufficient to maintain the required sensor temperatures. The maximum tip temperature is 930
° C.
A non-functioning heater element will delay the sensor's readiness for closed loop control and influences emissions.
A diagnostic routine is utilised to measure both sensor heater current and the heater supply voltage so its resistance
can be calculated. The function is active once per drive cycle, as long as the heater has been switched on for a pre-
defined period and the current has stabilised. The PWM duty cycle is carefully controlled to prevent thermal shock to
cold sensors.
The heated oxygen sensors age with mileage, causing an increase in the response time to switch from rich to lean
and lean to rich. This increase in response time influences the closed loop control and leads to progressively
increased emissions. The response time of the pre-catalytic converter sensors are monitored by measuring the period
of rich to lean and lean to rich switching. The ECM monitors the switching time, and if the threshold period is exceeded
(200 milliseconds), the fault will be detected and stored in the ECM as a fault code (the MIL light will be illuminated
on NAS vehicles). NAS vehicle engine calibration uses downstream sensors to compensate for aged upstream
sensors, thereby maintaining low emissions.
Diagnosis of electrical faults is continuously monitored for both the pre-catalytic converter sensors and the post-
catalytic converter sensors (NAS only). This is achieved by checking the signal against maximum and minimum
threshold for open and short circuit conditions. For NAS vehicles, should the pre- and post-catalytic converters be
inadvertently transposed, the lambda signals will go to maximum but opposite extremes and the system will
automatically revert to open loop fuelling. The additional sensors for NAS vehicles provide mandatory monitoring of
the catalyst conversion efficiency and long term fuelling adaptations.
Note that some markets do not legislate for closed loop fuelling control and in this instance no heated oxygen
sensors will be fitted to the exhaust system.
Page 373 of 1672
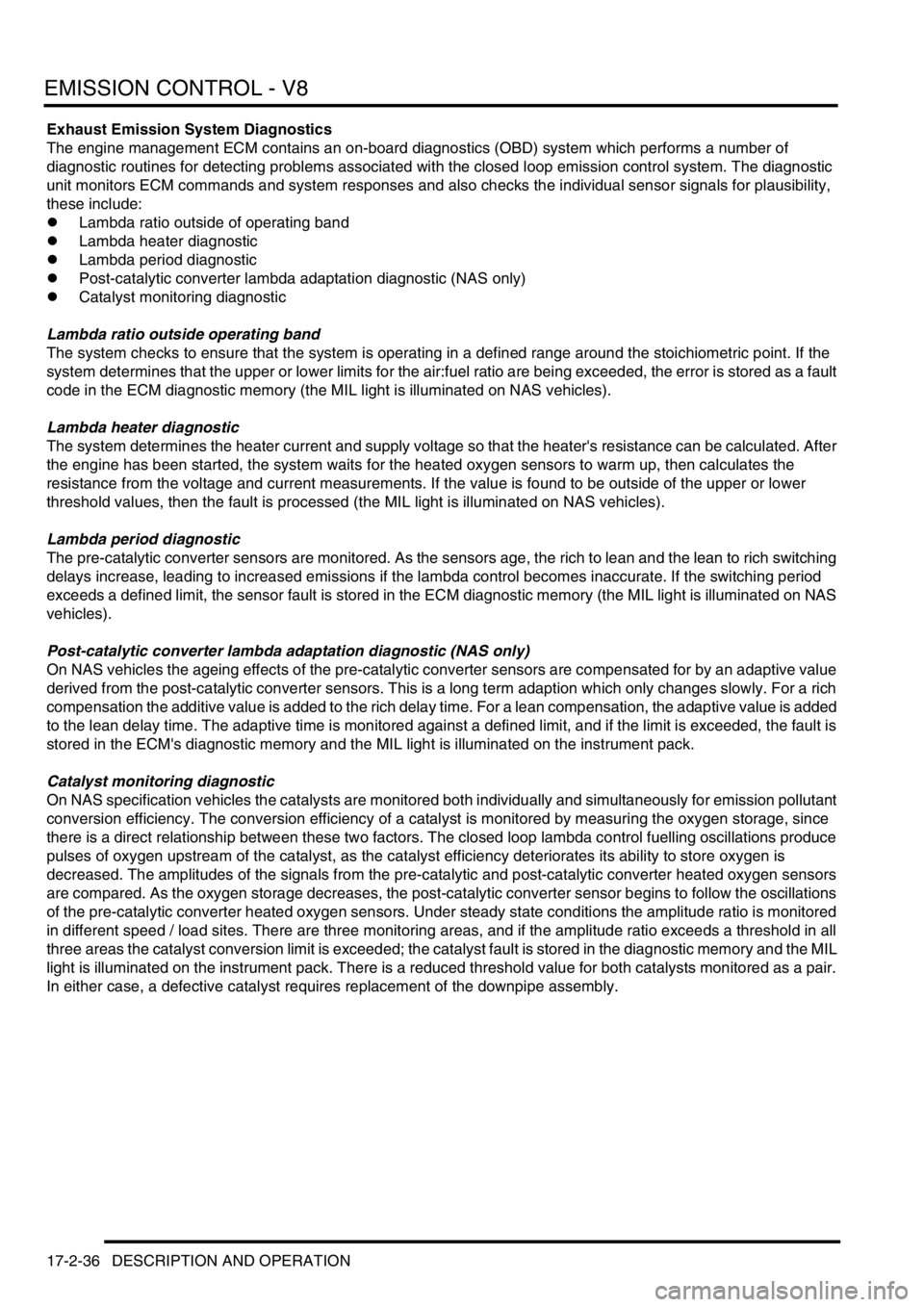
EMISSION CONTROL - V8
17-2-36 DESCRIPTION AND OPERATION
Exhaust Emission System Diagnostics
The engine management ECM contains an on-board diagnostics (OBD) system which performs a number of
diagnostic routines for detecting problems associated with the closed loop emission control system. The diagnostic
unit monitors ECM commands and system responses and also checks the individual sensor signals for plausibility,
these include:
lLambda ratio outside of operating band
lLambda heater diagnostic
lLambda period diagnostic
lPost-catalytic converter lambda adaptation diagnostic (NAS only)
lCatalyst monitoring diagnostic
Lambda ratio outside operating band
The system checks to ensure that the system is operating in a defined range around the stoichiometric point. If the
system determines that the upper or lower limits for the air:fuel ratio are being exceeded, the error is stored as a fault
code in the ECM diagnostic memory (the MIL light is illuminated on NAS vehicles).
Lambda heater diagnostic
The system determines the heater current and supply voltage so that the heater's resistance can be calculated. After
the engine has been started, the system waits for the heated oxygen sensors to warm up, then calculates the
resistance from the voltage and current measurements. If the value is found to be outside of the upper or lower
threshold values, then the fault is processed (the MIL light is illuminated on NAS vehicles).
Lambda period diagnostic
The pre-catalytic converter sensors are monitored. As the sensors age, the rich to lean and the lean to rich switching
delays increase, leading to increased emissions if the lambda control becomes inaccurate. If the switching period
exceeds a defined limit, the sensor fault is stored in the ECM diagnostic memory (the MIL light is illuminated on NAS
vehicles).
Post-catalytic converter lambda adaptation diagnostic (NAS only)
On NAS vehicles the ageing effects of the pre-catalytic converter sensors are compensated for by an adaptive value
derived from the post-catalytic converter sensors. This is a long term adaption which only changes slowly. For a rich
compensation the additive value is added to the rich delay time. For a lean compensation, the adaptive value is added
to the lean delay time. The adaptive time is monitored against a defined limit, and if the limit is exceeded, the fault is
stored in the ECM's diagnostic memory and the MIL light is illuminated on the instrument pack.
Catalyst monitoring diagnostic
On NAS specification vehicles the catalysts are monitored both individually and simultaneously for emission pollutant
conversion efficiency. The conversion efficiency of a catalyst is monitored by measuring the oxygen storage, since
there is a direct relationship between these two factors. The closed loop lambda control fuelling oscillations produce
pulses of oxygen upstream of the catalyst, as the catalyst efficiency deteriorates its ability to store oxygen is
decreased. The amplitudes of the signals from the pre-catalytic and post-catalytic converter heated oxygen sensors
are compared. As the oxygen storage decreases, the post-catalytic converter sensor begins to follow the oscillations
of the pre-catalytic converter heated oxygen sensors. Under steady state conditions the amplitude ratio is monitored
in different speed / load sites. There are three monitoring areas, and if the amplitude ratio exceeds a threshold in all
three areas the catalyst conversion limit is exceeded; the catalyst fault is stored in the diagnostic memory and the MIL
light is illuminated on the instrument pack. There is a reduced threshold value for both catalysts monitored as a pair.
In either case, a defective catalyst requires replacement of the downpipe assembly.
Page 377 of 1672
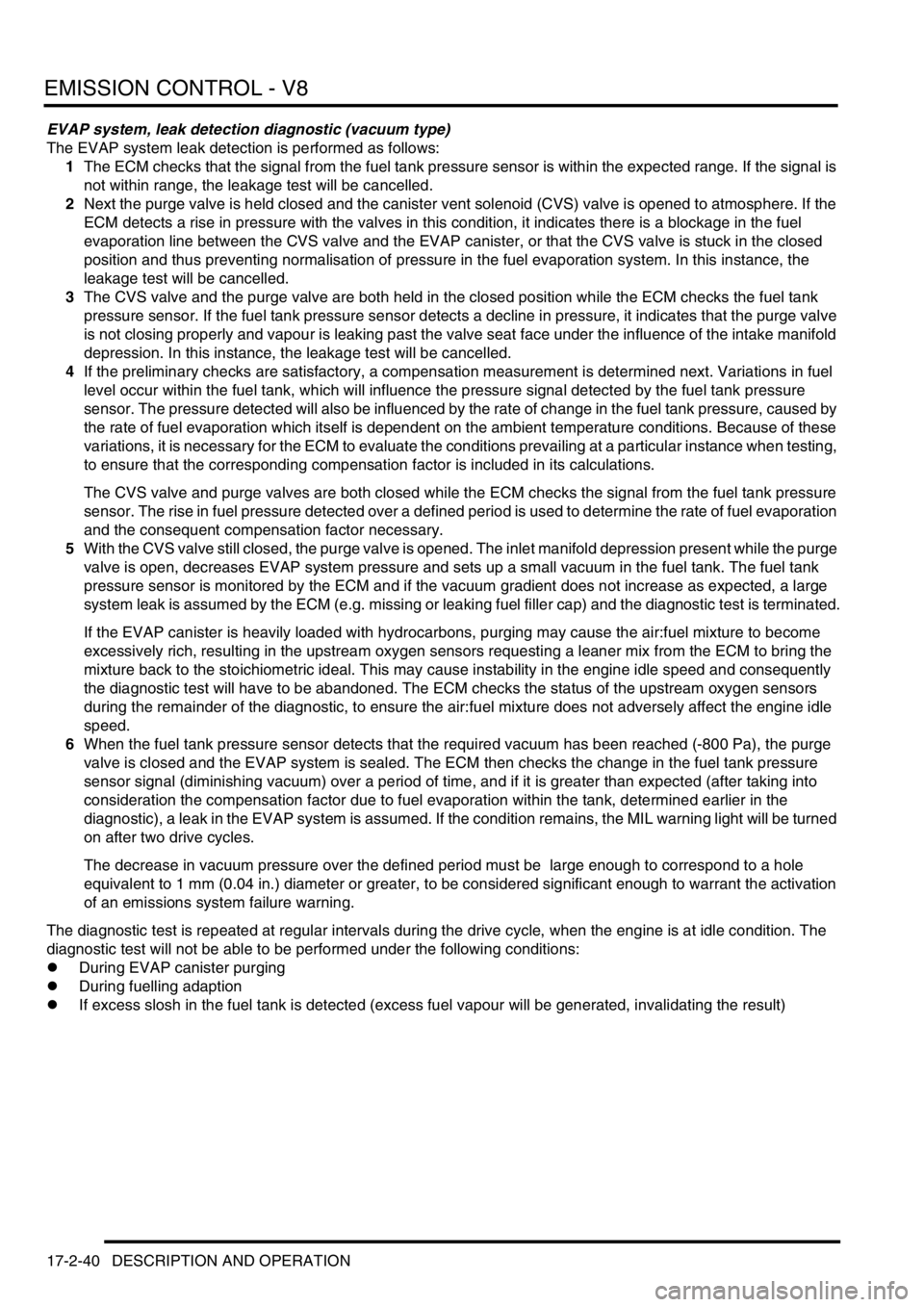
EMISSION CONTROL - V8
17-2-40 DESCRIPTION AND OPERATION
EVAP system, leak detection diagnostic (vacuum type)
The EVAP system leak detection is performed as follows:
1The ECM checks that the signal from the fuel tank pressure sensor is within the expected range. If the signal is
not within range, the leakage test will be cancelled.
2Next the purge valve is held closed and the canister vent solenoid (CVS) valve is opened to atmosphere. If the
ECM detects a rise in pressure with the valves in this condition, it indicates there is a blockage in the fuel
evaporation line between the CVS valve and the EVAP canister, or that the CVS valve is stuck in the closed
position and thus preventing normalisation of pressure in the fuel evaporation system. In this instance, the
leakage test will be cancelled.
3The CVS valve and the purge valve are both held in the closed position while the ECM checks the fuel tank
pressure sensor. If the fuel tank pressure sensor detects a decline in pressure, it indicates that the purge valve
is not closing properly and vapour is leaking past the valve seat face under the influence of the intake manifold
depression. In this instance, the leakage test will be cancelled.
4If the preliminary checks are satisfactory, a compensation measurement is determined next. Variations in fuel
level occur within the fuel tank, which will influence the pressure signal detected by the fuel tank pressure
sensor. The pressure detected will also be influenced by the rate of change in the fuel tank pressure, caused by
the rate of fuel evaporation which itself is dependent on the ambient temperature conditions. Because of these
variations, it is necessary for the ECM to evaluate the conditions prevailing at a particular instance when testing,
to ensure that the corresponding compensation factor is included in its calculations.
The CVS valve and purge valves are both closed while the ECM checks the signal from the fuel tank pressure
sensor. The rise in fuel pressure detected over a defined period is used to determine the rate of fuel evaporation
and the consequent compensation factor necessary.
5With the CVS valve still closed, the purge valve is opened. The inlet manifold depression present while the purge
valve is open, decreases EVAP system pressure and sets up a small vacuum in the fuel tank. The fuel tank
pressure sensor is monitored by the ECM and if the vacuum gradient does not increase as expected, a large
system leak is assumed by the ECM (e.g. missing or leaking fuel filler cap) and the diagnostic test is terminated.
If the EVAP canister is heavily loaded with hydrocarbons, purging may cause the air:fuel mixture to become
excessively rich, resulting in the upstream oxygen sensors requesting a leaner mix from the ECM to bring the
mixture back to the stoichiometric ideal. This may cause instability in the engine idle speed and consequently
the diagnostic test will have to be abandoned. The ECM checks the status of the upstream oxygen sensors
during the remainder of the diagnostic, to ensure the air:fuel mixture does not adversely affect the engine idle
speed.
6When the fuel tank pressure sensor detects that the required vacuum has been reached (-800 Pa), the purge
valve is closed and the EVAP system is sealed. The ECM then checks the change in the fuel tank pressure
sensor signal (diminishing vacuum) over a period of time, and if it is greater than expected (after taking into
consideration the compensation factor due to fuel evaporation within the tank, determined earlier in the
diagnostic), a leak in the EVAP system is assumed. If the condition remains, the MIL warning light will be turned
on after two drive cycles.
The decrease in vacuum pressure over the defined period must be large enough to correspond to a hole
equivalent to 1 mm (0.04 in.) diameter or greater, to be considered significant enough to warrant the activation
of an emissions system failure warning.
The diagnostic test is repeated at regular intervals during the drive cycle, when the engine is at idle condition. The
diagnostic test will not be able to be performed under the following conditions:
lDuring EVAP canister purging
lDuring fuelling adaption
lIf excess slosh in the fuel tank is detected (excess fuel vapour will be generated, invalidating the result)
Page 378 of 1672
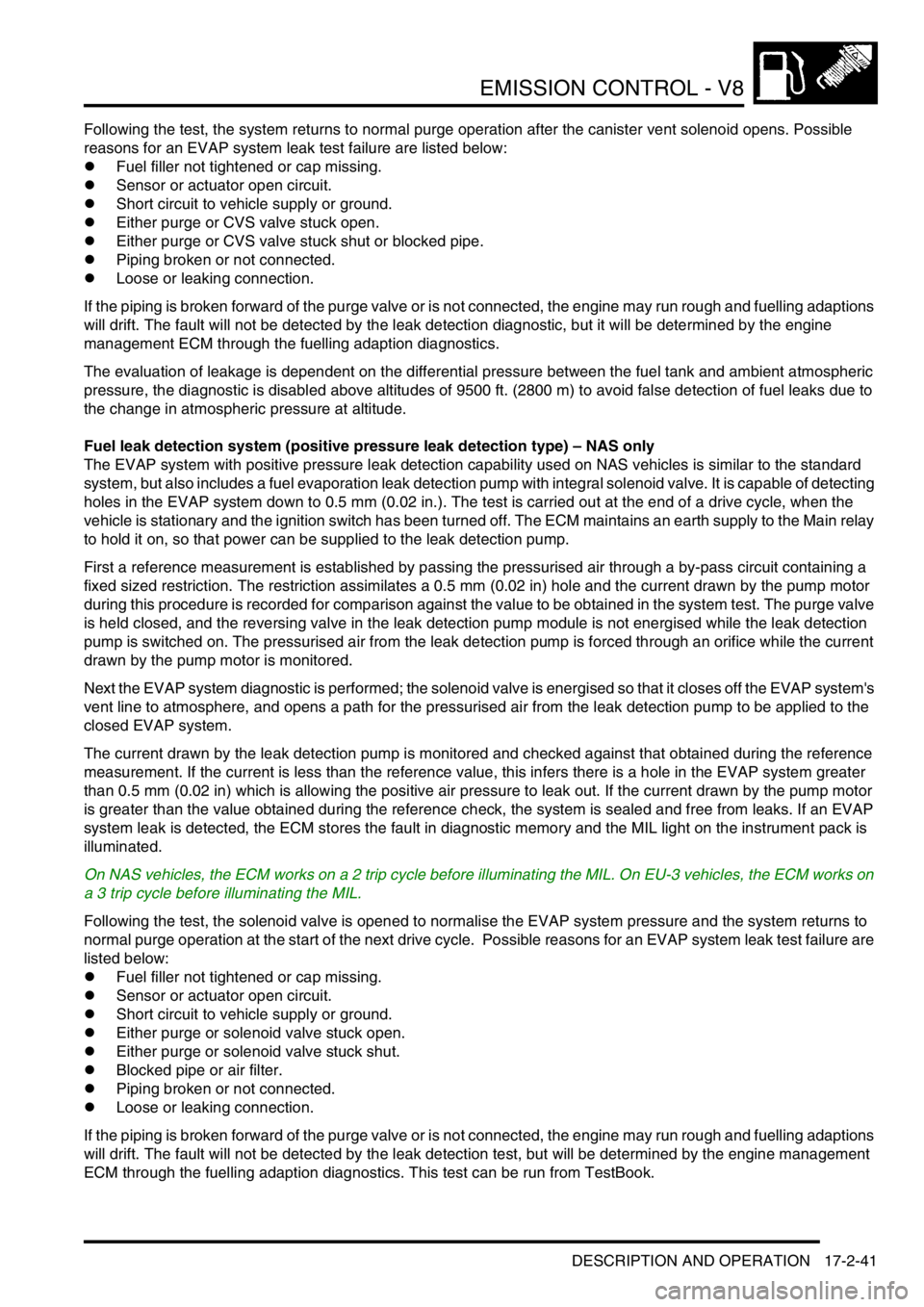
EMISSION CONTROL - V8
DESCRIPTION AND OPERATION 17-2-41
Following the test, the system returns to normal purge operation after the canister vent solenoid opens. Possible
reasons for an EVAP system leak test failure are listed below:
lFuel filler not tightened or cap missing.
lSensor or actuator open circuit.
lShort circuit to vehicle supply or ground.
lEither purge or CVS valve stuck open.
lEither purge or CVS valve stuck shut or blocked pipe.
lPiping broken or not connected.
lLoose or leaking connection.
If the piping is broken forward of the purge valve or is not connected, the engine may run rough and fuelling adaptions
will drift. The fault will not be detected by the leak detection diagnostic, but it will be determined by the engine
management ECM through the fuelling adaption diagnostics.
The evaluation of leakage is dependent on the differential pressure between the fuel tank and ambient atmospheric
pressure, the diagnostic is disabled above altitudes of 9500 ft. (2800 m) to avoid false detection of fuel leaks due to
the change in atmospheric pressure at altitude.
Fuel leak detection system (positive pressure leak detection type) – NAS only
The EVAP system with positive pressure leak detection capability used on NAS vehicles is similar to the standard
system, but also includes a fuel evaporation leak detection pump with integral solenoid valve. It is capable of detecting
holes in the EVAP system down to 0.5 mm (0.02 in.). The test is carried out at the end of a drive cycle, when the
vehicle is stationary and the ignition switch has been turned off. The ECM maintains an earth supply to the Main relay
to hold it on, so that power can be supplied to the leak detection pump.
First a reference measurement is established by passing the pressurised air through a by-pass circuit containing a
fixed sized restriction. The restriction assimilates a 0.5 mm (0.02 in) hole and the current drawn by the pump motor
during this procedure is recorded for comparison against the value to be obtained in the system test. The purge valve
is held closed, and the reversing valve in the leak detection pump module is not energised while the leak detection
pump is switched on. The pressurised air from the leak detection pump is forced through an orifice while the current
drawn by the pump motor is monitored.
Next the EVAP system diagnostic is performed; the solenoid valve is energised so that it closes off the EVAP system's
vent line to atmosphere, and opens a path for the pressurised air from the leak detection pump to be applied to the
closed EVAP system.
The current drawn by the leak detection pump is monitored and checked against that obtained during the reference
measurement. If the current is less than the reference value, this infers there is a hole in the EVAP system greater
than 0.5 mm (0.02 in) which is allowing the positive air pressure to leak out. If the current drawn by the pump motor
is greater than the value obtained during the reference check, the system is sealed and free from leaks. If an EVAP
system leak is detected, the ECM stores the fault in diagnostic memory and the MIL light on the instrument pack is
illuminated.
On NAS vehicles, the ECM works on a 2 trip cycle before illuminating the MIL. On EU-3 vehicles, the ECM works on
a 3 trip cycle before illuminating the MIL.
Following the test, the solenoid valve is opened to normalise the EVAP system pressure and the system returns to
normal purge operation at the start of the next drive cycle. Possible reasons for an EVAP system leak test failure are
listed below:
lFuel filler not tightened or cap missing.
lSensor or actuator open circuit.
lShort circuit to vehicle supply or ground.
lEither purge or solenoid valve stuck open.
lEither purge or solenoid valve stuck shut.
lBlocked pipe or air filter.
lPiping broken or not connected.
lLoose or leaking connection.
If the piping is broken forward of the purge valve or is not connected, the engine may run rough and fuelling adaptions
will drift. The fault will not be detected by the leak detection test, but will be determined by the engine management
ECM through the fuelling adaption diagnostics. This test can be run from TestBook.
Page 379 of 1672
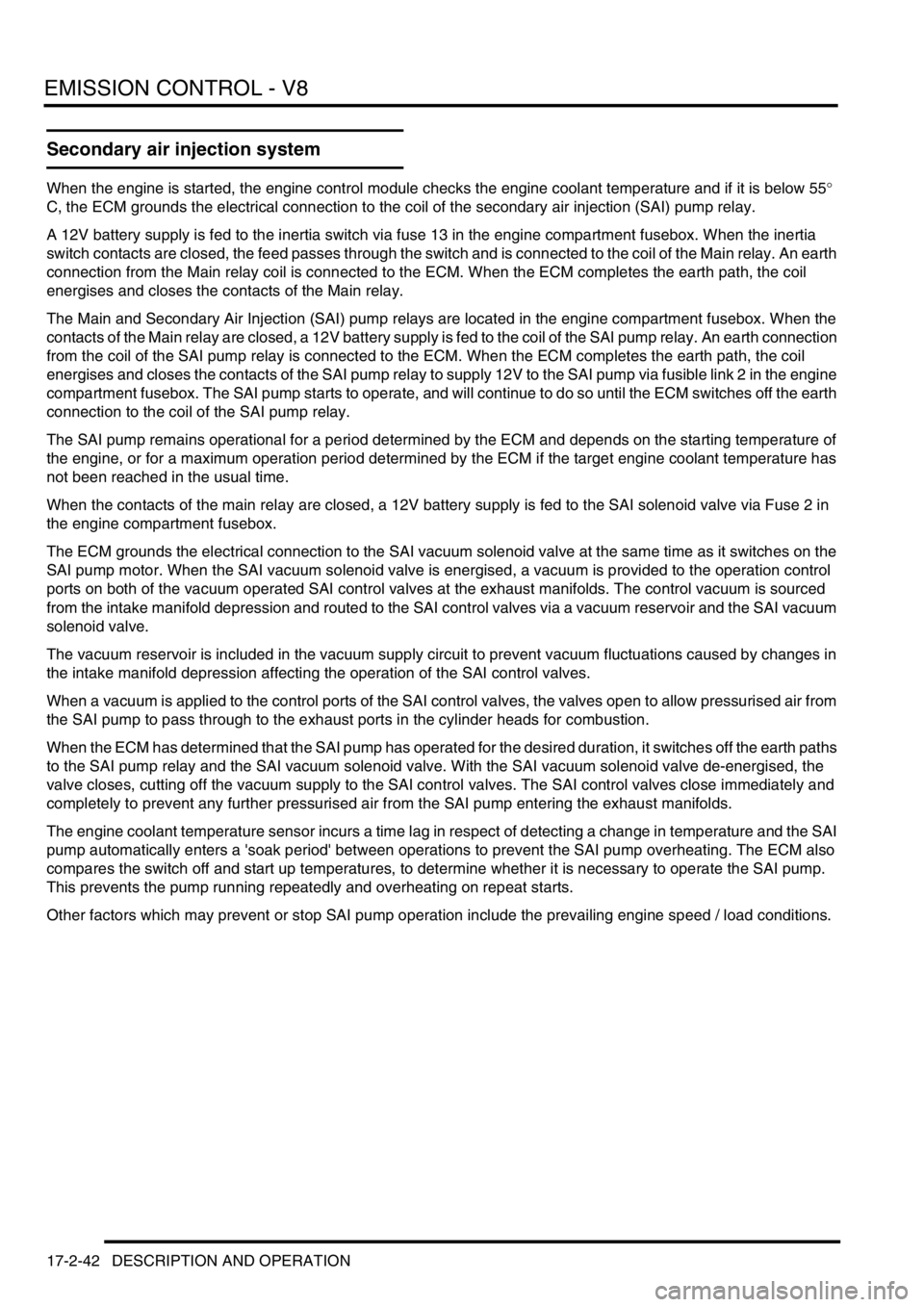
EMISSION CONTROL - V8
17-2-42 DESCRIPTION AND OPERATION
Secondary air injection system
When the engine is started, the engine control module checks the engine coolant temperature and if it is below 55°
C, the ECM grounds the electrical connection to the coil of the secondary air injection (SAI) pump relay.
A 12V battery supply is fed to the inertia switch via fuse 13 in the engine compartment fusebox. When the inertia
switch contacts are closed, the feed passes through the switch and is connected to the coil of the Main relay. An earth
connection from the Main relay coil is connected to the ECM. When the ECM completes the earth path, the coil
energises and closes the contacts of the Main relay.
The Main and Secondary Air Injection (SAI) pump relays are located in the engine compartment fusebox. When the
contacts of the Main relay are closed, a 12V battery supply is fed to the coil of the SAI pump relay. An earth connection
from the coil of the SAI pump relay is connected to the ECM. When the ECM completes the earth path, the coil
energises and closes the contacts of the SAI pump relay to supply 12V to the SAI pump via fusible link 2 in the engine
compartment fusebox. The SAI pump starts to operate, and will continue to do so until the ECM switches off the earth
connection to the coil of the SAI pump relay.
The SAI pump remains operational for a period determined by the ECM and depends on the starting temperature of
the engine, or for a maximum operation period determined by the ECM if the target engine coolant temperature has
not been reached in the usual time.
When the contacts of the main relay are closed, a 12V battery supply is fed to the SAI solenoid valve via Fuse 2 in
the engine compartment fusebox.
The ECM grounds the electrical connection to the SAI vacuum solenoid valve at the same time as it switches on the
SAI pump motor. When the SAI vacuum solenoid valve is energised, a vacuum is provided to the operation control
ports on both of the vacuum operated SAI control valves at the exhaust manifolds. The control vacuum is sourced
from the intake manifold depression and routed to the SAI control valves via a vacuum reservoir and the SAI vacuum
solenoid valve.
The vacuum reservoir is included in the vacuum supply circuit to prevent vacuum fluctuations caused by changes in
the intake manifold depression affecting the operation of the SAI control valves.
When a vacuum is applied to the control ports of the SAI control valves, the valves open to allow pressurised air from
the SAI pump to pass through to the exhaust ports in the cylinder heads for combustion.
When the ECM has determined that the SAI pump has operated for the desired duration, it switches off the earth paths
to the SAI pump relay and the SAI vacuum solenoid valve. With the SAI vacuum solenoid valve de-energised, the
valve closes, cutting off the vacuum supply to the SAI control valves. The SAI control valves close immediately and
completely to prevent any further pressurised air from the SAI pump entering the exhaust manifolds.
The engine coolant temperature sensor incurs a time lag in respect of detecting a change in temperature and the SAI
pump automatically enters a 'soak period' between operations to prevent the SAI pump overheating. The ECM also
compares the switch off and start up temperatures, to determine whether it is necessary to operate the SAI pump.
This prevents the pump running repeatedly and overheating on repeat starts.
Other factors which may prevent or stop SAI pump operation include the prevailing engine speed / load conditions.
Page 412 of 1672
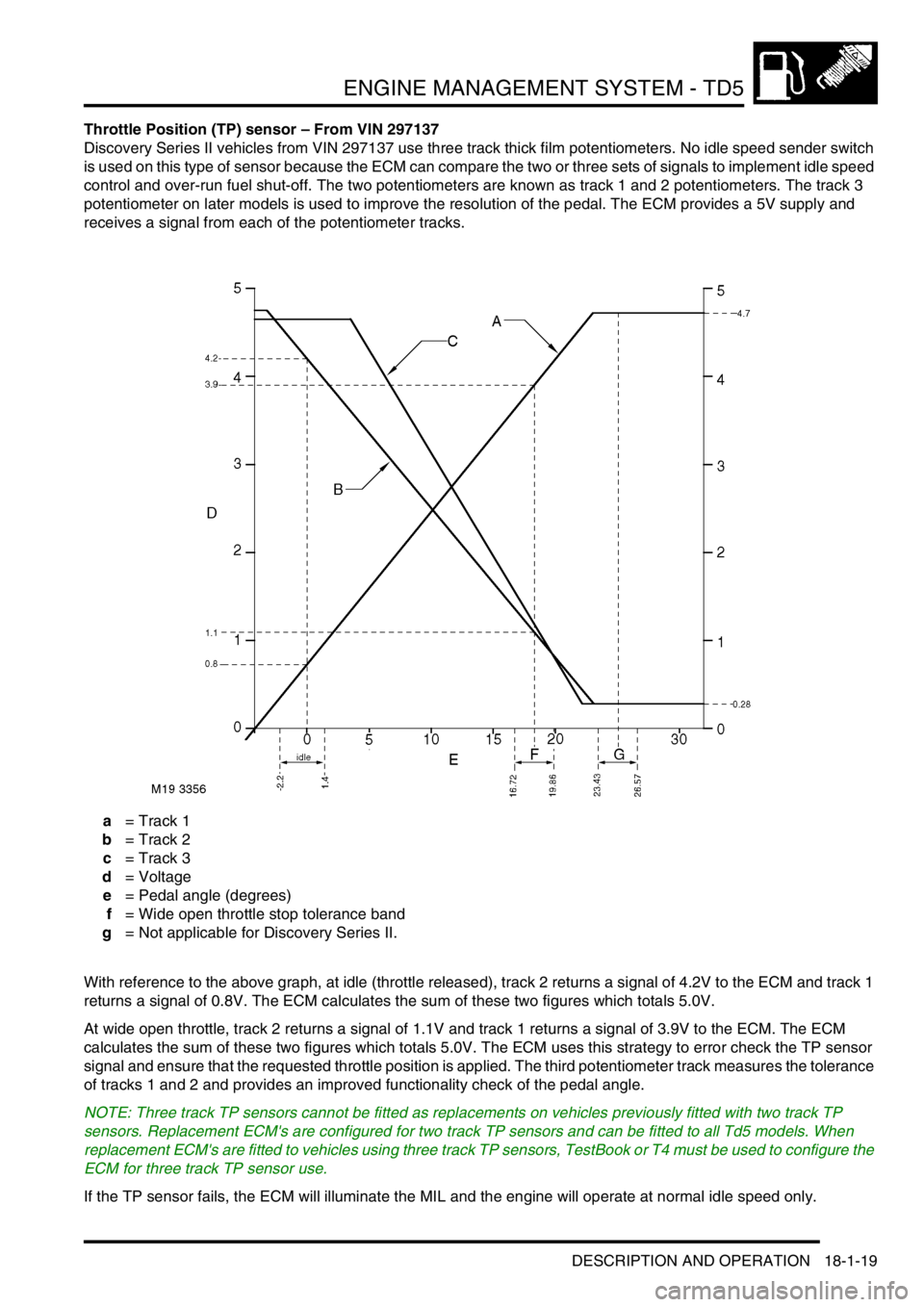
ENGINE MANAGEMENT SYSTEM - TD5
DESCRIPTION AND OPERATION 18-1-19
Throttle Position (TP) sensor – From VIN 297137
Discovery Series II vehicles from VIN 297137 use three track thick film potentiometers. No idle speed sender switch
is used on this type of sensor because the ECM can compare the two or three sets of signals to implement idle speed
control and over-run fuel shut-off. The two potentiometers are known as track 1 and 2 potentiometers. The track 3
potentiometer on later models is used to improve the resolution of the pedal. The ECM provides a 5V supply and
receives a signal from each of the potentiometer tracks.
a = Track 1
b = Track 2
c = Track 3
d = Voltage
e = Pedal angle (degrees)
f = Wide open throttle stop tolerance band
g = Not applicable for Discovery Series II.
With reference to the above graph, at idle (throttle released), track 2 returns a signal of 4.2V to the ECM and track 1
returns a signal of 0.8V. The ECM calculates the sum of these two figures which totals 5.0V.
At wide open throttle, track 2 returns a signal of 1.1V and track 1 returns a signal of 3.9V to the ECM. The ECM
calculates the sum of these two figures which totals 5.0V. The ECM uses this strategy to error check the TP sensor
signal and ensure that the requested throttle position is applied. The third potentiometer track measures the tolerance
of tracks 1 and 2 and provides an improved functionality check of the pedal angle.
NOTE: Three track TP sensors cannot be fitted as replacements on vehicles previously fitted with two track TP
sensors. Replacement ECM's are configured for two track TP sensors and can be fitted to all Td5 models. When
replacement ECM's are fitted to vehicles using three track TP sensors, TestBook or T4 must be used to configure the
ECM for three track TP sensor use.
If the TP sensor fails, the ECM will illuminate the MIL and the engine will operate at normal idle speed only.