MAZDA 6 2002 Workshop Manual Suplement
Manufacturer: MAZDA, Model Year: 2002, Model line: 6, Model: MAZDA 6 2002Pages: 909, PDF Size: 17.16 MB
Page 201 of 909
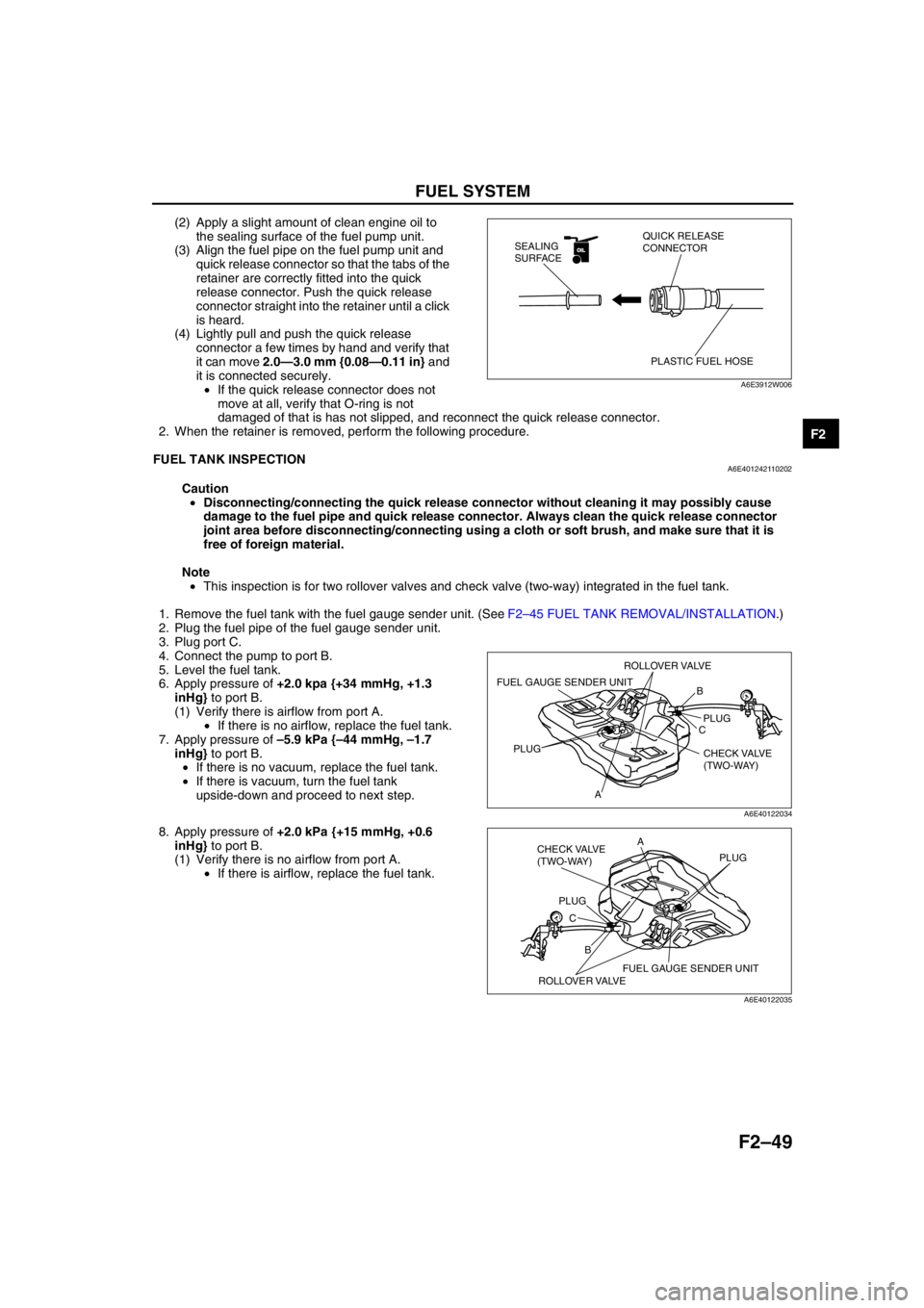
FUEL SYSTEM
F2–49
F2
(2) Apply a slight amount of clean engine oil to
the sealing surface of the fuel pump unit.
(3) Align the fuel pipe on the fuel pump unit and
quick release connector so that the tabs of the
retainer are correctly fitted into the quick
release connector. Push the quick release
connector straight into the retainer until a click
is heard.
(4) Lightly pull and push the quick release
connector a few times by hand and verify that
it can move 2.0—3.0 mm {0.08—0.11 in} and
it is connected securely.
•If the quick release connector does not
move at all, verify that O-ring is not
damaged of that is has not slipped, and reconnect the quick release connector.
2. When the retainer is removed, perform the following procedure.
End Of Sie
FUEL TANK INSPECTIONA6E401242110202
Caution
•Disconnecting/connecting the quick release connector without cleaning it may possibly cause
damage to the fuel pipe and quick release connector. Always clean the quick release connector
joint area before disconnecting/connecting using a cloth or soft brush, and make sure that it is
free of foreign material.
Note
•This inspection is for two rollover valves and check valve (two-way) integrated in the fuel tank.
1. Remove the fuel tank with the fuel gauge sender unit. (See F2–45 FUEL TANK REMOVAL/INSTALLATION.)
2. Plug the fuel pipe of the fuel gauge sender unit.
3. Plug port C.
4. Connect the pump to port B.
5. Level the fuel tank.
6. Apply pressure of +2.0 kpa {+34 mmHg, +1.3
inHg} to port B.
(1) Verify there is airflow from port A.
•If there is no airflow, replace the fuel tank.
7. Apply pressure of –5.9 kPa {–44 mmHg, –1.7
inHg} to port B.
•If there is no vacuum, replace the fuel tank.
•If there is vacuum, turn the fuel tank
upside-down and proceed to next step.
8. Apply pressure of +2.0 kPa {+15 mmHg, +0.6
inHg} to port B.
(1) Verify there is no airflow from port A.
•If there is airflow, replace the fuel tank.
End Of Sie
OILOIL
PLASTIC FUEL HOSE QUICK RELEASE
CONNECTOR SEALING
SURFACE
A6E3912W006
B
C
APLUG
PLUG
CHECK VALVE
(TWO-WAY)
FUEL GAUGE SENDER UNIT
ROLLOVER VALVE
A6E40122034
B CA
PLUGPLUG
CHECK VALVE
(TWO-WAY)
FUEL GAUGE SENDER UNIT
ROLLOVER VALVE
A6E40122035
Page 202 of 909
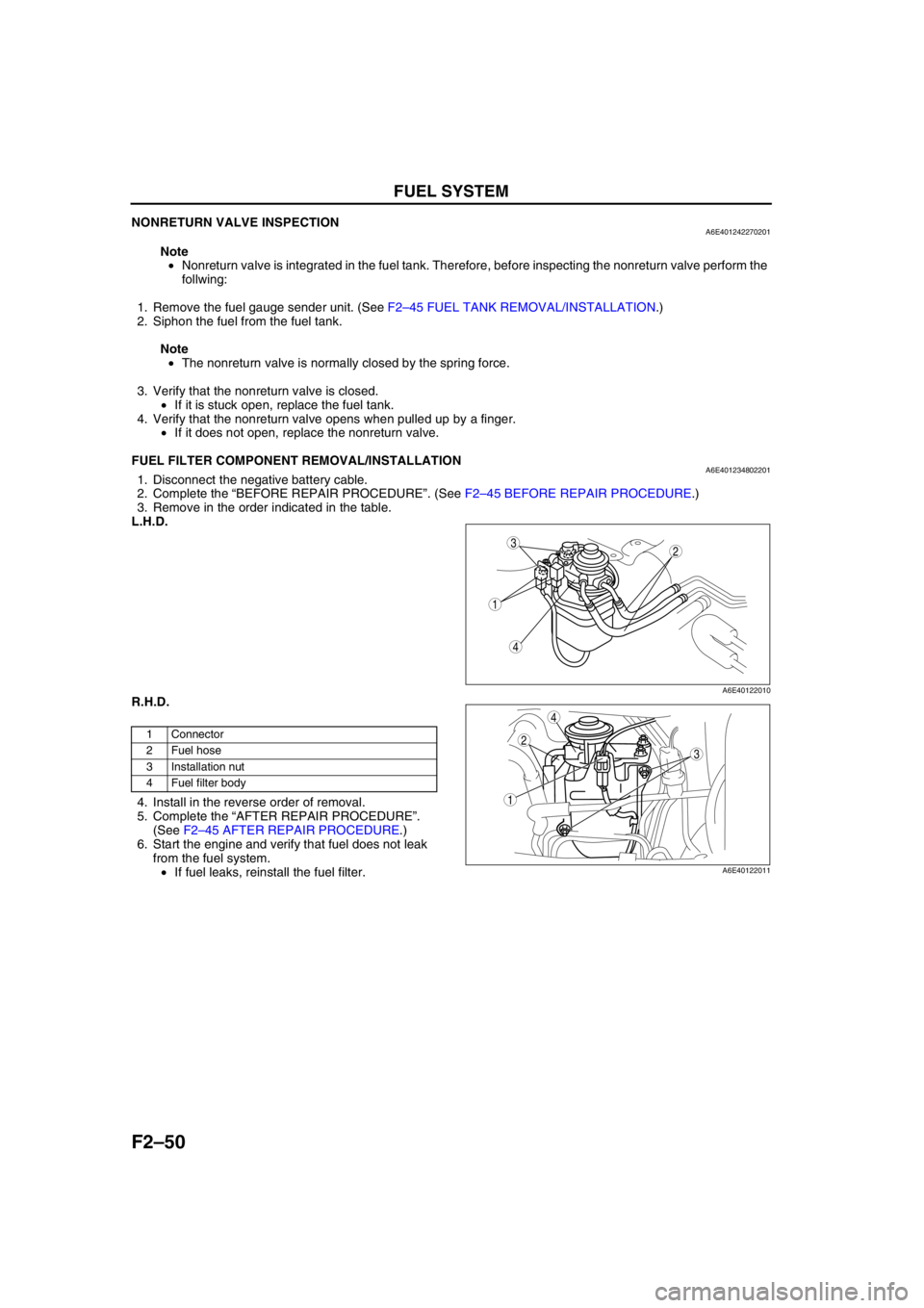
F2–50
FUEL SYSTEM
NONRETURN VALVE INSPECTIONA6E401242270201
Note
•Nonreturn valve is integrated in the fuel tank. Therefore, before inspecting the nonreturn valve perform the
follwing:
1. Remove the fuel gauge sender unit. (See F2–45 FUEL TANK REMOVAL/INSTALLATION.)
2. Siphon the fuel from the fuel tank.
Note
•The nonreturn valve is normally closed by the spring force.
3. Verify that the nonreturn valve is closed.
•If it is stuck open, replace the fuel tank.
4. Verify that the nonreturn valve opens when pulled up by a finger.
•If it does not open, replace the nonreturn valve.
End Of Sie
FUEL FILTER COMPONENT REMOVAL/INSTALLATIONA6E4012348022011. Disconnect the negative battery cable.
2. Complete the “BEFORE REPAIR PROCEDURE”. (See F2–45 BEFORE REPAIR PROCEDURE.)
3. Remove in the order indicated in the table.
L.H.D.
R.H.D.
.
4. Install in the reverse order of removal.
5. Complete the “AFTER REPAIR PROCEDURE”.
(See F2–45 AFTER REPAIR PROCEDURE.)
6. Start the engine and verify that fuel does not leak
from the fuel system.
•If fuel leaks, reinstall the fuel filter.
End Of Sie
1
4
23
A6E40122010
1 Connector
2Fuel hose
3 Installation nut
4 Fuel filter body
4
1
2
3
A6E40122011
Page 203 of 909
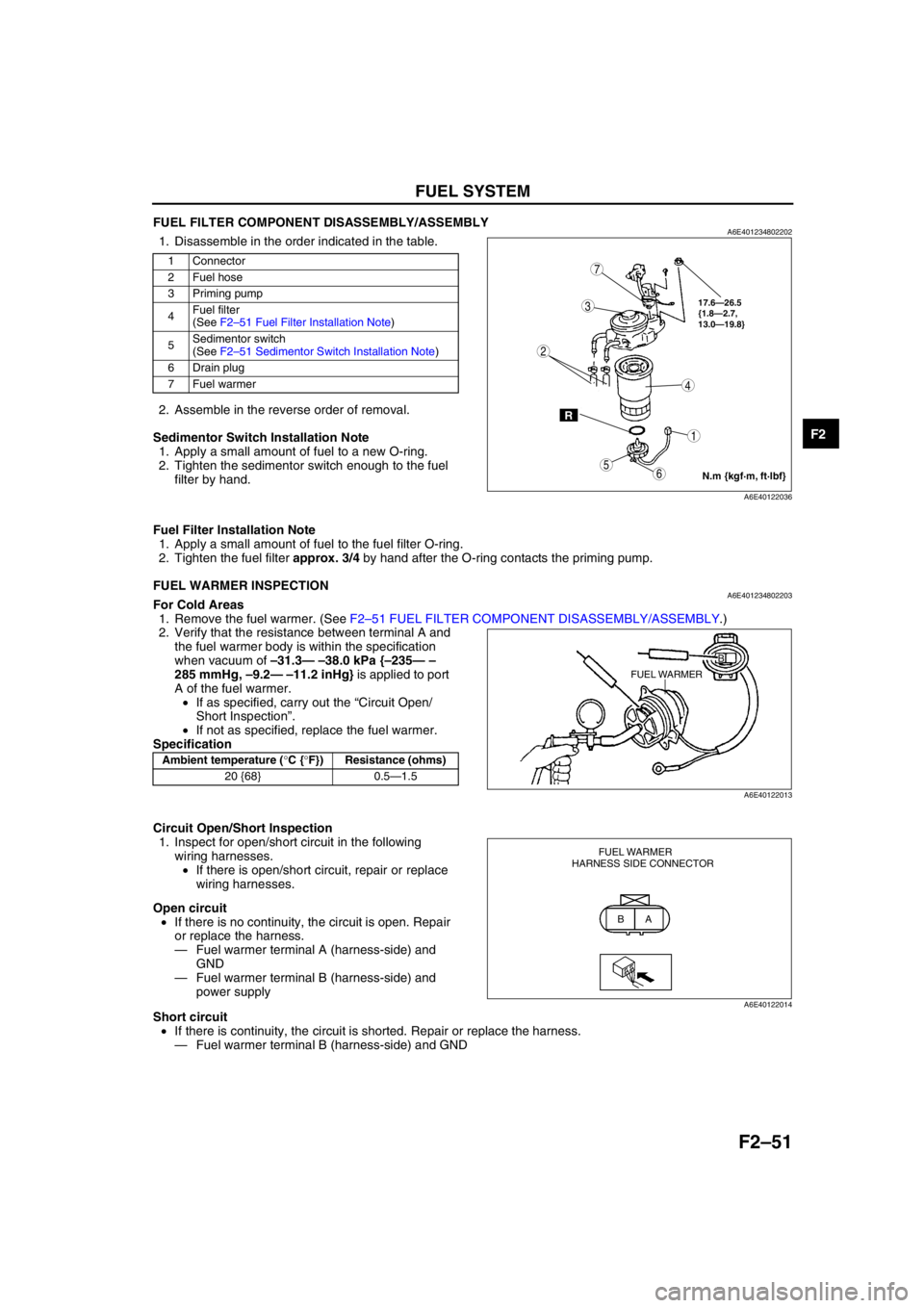
FUEL SYSTEM
F2–51
F2
FUEL FILTER COMPONENT DISASSEMBLY/ASSEMBLYA6E4012348022021. Disassemble in the order indicated in the table..
2. Assemble in the reverse order of removal.
Sedimentor Switch Installation Note
1. Apply a small amount of fuel to a new O-ring.
2. Tighten the sedimentor switch enough to the fuel
filter by hand.
Fuel Filter Installation Note
1. Apply a small amount of fuel to the fuel filter O-ring.
2. Tighten the fuel filter approx. 3/4 by hand after the O-ring contacts the priming pump.
End Of Sie
FUEL WARMER INSPECTIONA6E401234802203For Cold Areas
1. Remove the fuel warmer. (See F2–51 FUEL FILTER COMPONENT DISASSEMBLY/ASSEMBLY.)
2. Verify that the resistance between terminal A and
the fuel warmer body is within the specification
when vacuum of –31.3— –38.0 kPa {–235— –
285 mmHg, –9.2— –11.2 inHg} is applied to port
A of the fuel warmer.
•If as specified, carry out the “Circuit Open/
Short Inspection”.
•If not as specified, replace the fuel warmer.
Specification
Circuit Open/Short Inspection
1. Inspect for open/short circuit in the following
wiring harnesses.
•If there is open/short circuit, repair or replace
wiring harnesses.
Open circuit
•If there is no continuity, the circuit is open. Repair
or replace the harness.
—Fuel warmer terminal A (harness-side) and
GND
—Fuel warmer terminal B (harness-side) and
power supply
Short circuit
•If there is continuity, the circuit is shorted. Repair or replace the harness.
—Fuel warmer terminal B (harness-side) and GND
End Of Sie
1 Connector
2 Fuel hose
3 Priming pump
4Fuel filter
(See F2–51 Fuel Filter Installation Note)
5Sedimentor switch
(See F2–51 Sedimentor Switch Installation Note)
6 Drain plug
7 Fuel warmer
R
17.6—26.5
{1.8—2.7,
13.0—19.8}
7
5
4
3
6
1
2
N.m {kgf·m, ft·lbf}
A6E40122036
Ambient temperature (°C {°F}) Resistance (ohms)
20 {68} 0.5—1.5
FUEL WARMER
B
A6E40122013
A B FUEL WARMER
HARNESS SIDE CONNECTOR
A6E40122014
Page 204 of 909
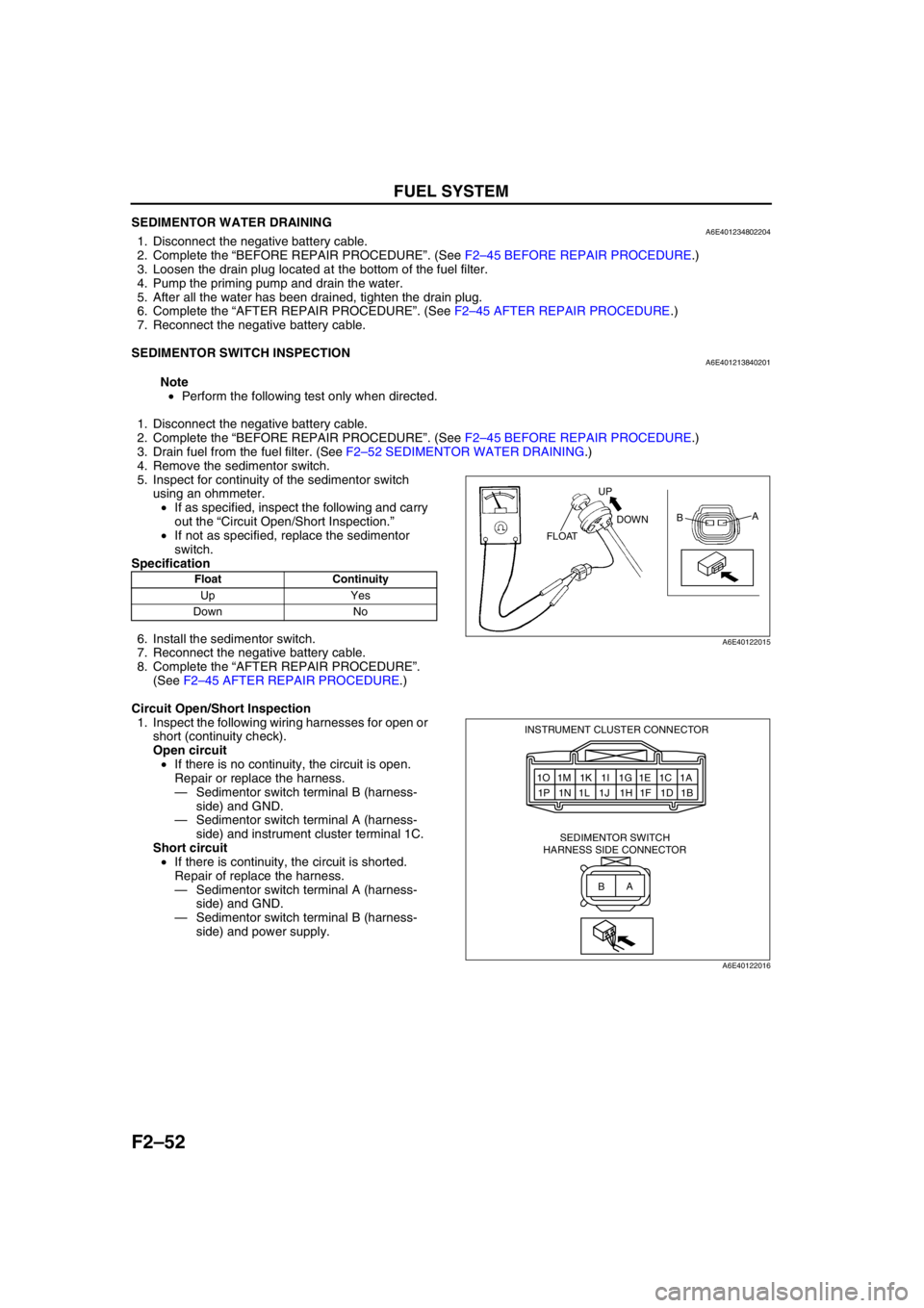
F2–52
FUEL SYSTEM
SEDIMENTOR WATER DRAININGA6E4012348022041. Disconnect the negative battery cable.
2. Complete the “BEFORE REPAIR PROCEDURE”. (See F2–45 BEFORE REPAIR PROCEDURE.)
3. Loosen the drain plug located at the bottom of the fuel filter.
4. Pump the priming pump and drain the water.
5. After all the water has been drained, tighten the drain plug.
6. Complete the “AFTER REPAIR PROCEDURE”. (See F2–45 AFTER REPAIR PROCEDURE.)
7. Reconnect the negative battery cable.
End Of Sie
SEDIMENTOR SWITCH INSPECTIONA6E401213840201
Note
•Perform the following test only when directed.
1. Disconnect the negative battery cable.
2. Complete the “BEFORE REPAIR PROCEDURE”. (See F2–45 BEFORE REPAIR PROCEDURE.)
3. Drain fuel from the fuel filter. (See F2–52 SEDIMENTOR WATER DRAINING.)
4. Remove the sedimentor switch.
5. Inspect for continuity of the sedimentor switch
using an ohmmeter.
•If as specified, inspect the following and carry
out the “Circuit Open/Short Inspection.”
•If not as specified, replace the sedimentor
switch.
Specification
6. Install the sedimentor switch.
7. Reconnect the negative battery cable.
8. Complete the “AFTER REPAIR PROCEDURE”.
(See F2–45 AFTER REPAIR PROCEDURE.)
Circuit Open/Short Inspection
1. Inspect the following wiring harnesses for open or
short (continuity check).
Open circuit
•If there is no continuity, the circuit is open.
Repair or replace the harness.
—Sedimentor switch terminal B (harness-
side) and GND.
—Sedimentor switch terminal A (harness-
side) and instrument cluster terminal 1C.
Short circuit
•If there is continuity, the circuit is shorted.
Repair of replace the harness.
—Sedimentor switch terminal A (harness-
side) and GND.
—Sedimentor switch terminal B (harness-
side) and power supply.
End Of Sie
Float Continuity
Up Yes
Down No
UP
DOWN
FLOATA
B
A6E40122015
1O 1M 1K 1I 1G 1E 1C 1A
1P 1N 1L 1J 1H 1F 1D 1B INSTRUMENT CLUSTER CONNECTOR
SEDIMENTOR SWITCH
HARNESS SIDE CONNECTOR
A
B
A6E40122016
Page 205 of 909
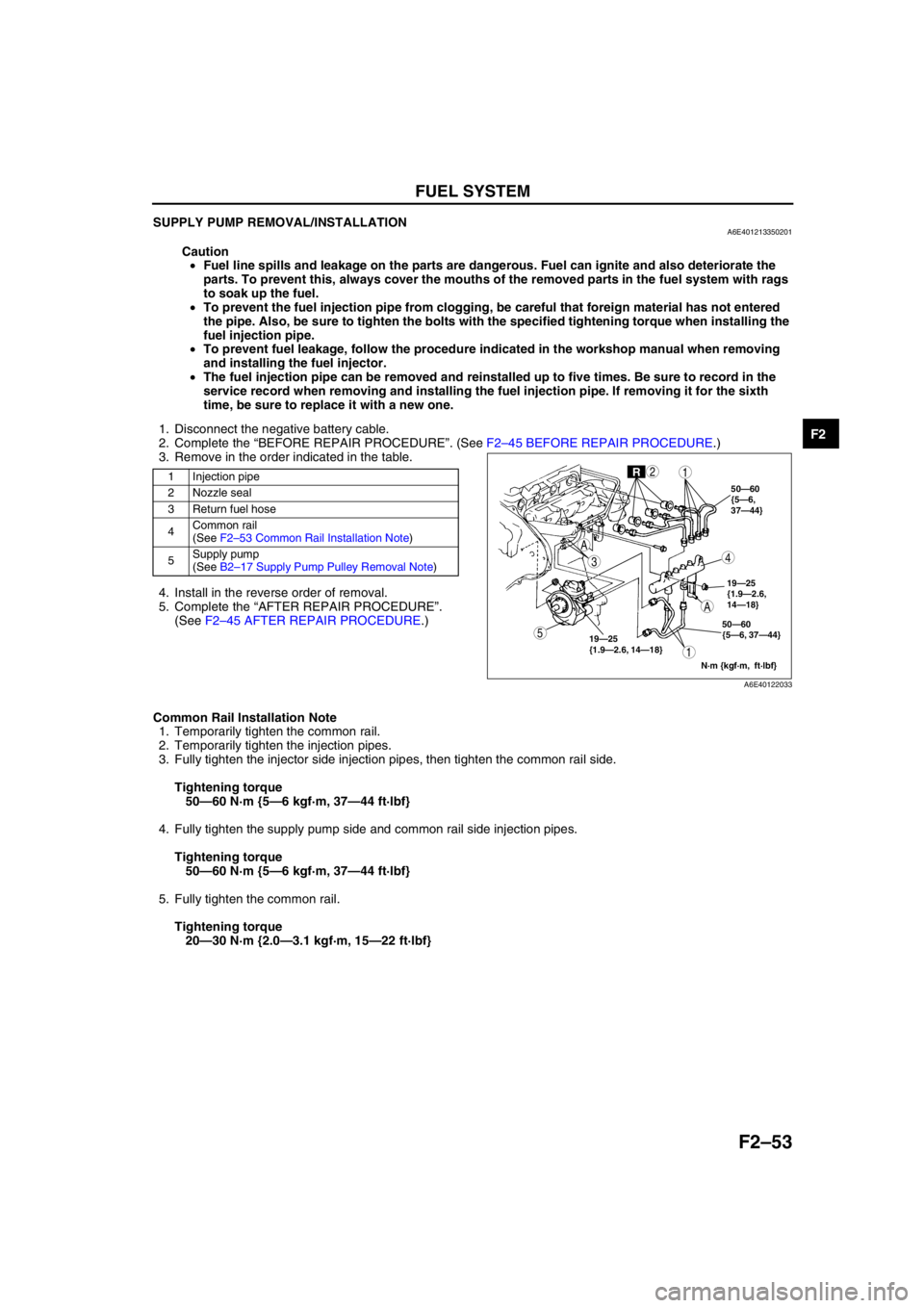
FUEL SYSTEM
F2–53
F2
SUPPLY PUMP REMOVAL/INSTALLATIONA6E401213350201
Caution
•Fuel line spills and leakage on the parts are dangerous. Fuel can ignite and also deteriorate the
parts. To prevent this, always cover the mouths of the removed parts in the fuel system with rags
to soak up the fuel.
•To prevent the fuel injection pipe from clogging, be careful that foreign material has not entered
the pipe. Also, be sure to tighten the bolts with the specified tightening torque when installing the
fuel injection pipe.
•To prevent fuel leakage, follow the procedure indicated in the workshop manual when removing
and installing the fuel injector.
•The fuel injection pipe can be removed and reinstalled up to five times. Be sure to record in the
service record when removing and installing the fuel injection pipe. If removing it for the sixth
time, be sure to replace it with a new one.
1. Disconnect the negative battery cable.
2. Complete the “BEFORE REPAIR PROCEDURE”. (See F2–45 BEFORE REPAIR PROCEDURE.)
3. Remove in the order indicated in the table.
.
4. Install in the reverse order of removal.
5. Complete the “AFTER REPAIR PROCEDURE”.
(See F2–45 AFTER REPAIR PROCEDURE.)
Common Rail Installation Note
1. Temporarily tighten the common rail.
2. Temporarily tighten the injection pipes.
3. Fully tighten the injector side injection pipes, then tighten the common rail side.
Tightening torque
50—60 N·m {5—6 kgf·m, 37—44 ft·lbf}
4. Fully tighten the supply pump side and common rail side injection pipes.
Tightening torque
50—60 N·m {5—6 kgf·m, 37—44 ft·lbf}
5. Fully tighten the common rail.
Tightening torque
20—30 N·m {2.0—3.1 kgf·m, 15—22 ft·lbf}
End Of Sie
1 Injection pipe
2 Nozzle seal
3 Return fuel hose
4Common rail
(See F2–53 Common Rail Installation Note)
5Supply pump
(See B2–17 Supply Pump Pulley Removal Note)
19—25
{1.9—2.6, 14—18}19—25
{1.9—2.6,
14—18} 50—60
{5—6,
37—44}
50—60
{5—6, 37—44}
N·m {kgf·m, ft·lbf}
A
R
A
5
43
12
1
A6E40122033
Page 206 of 909
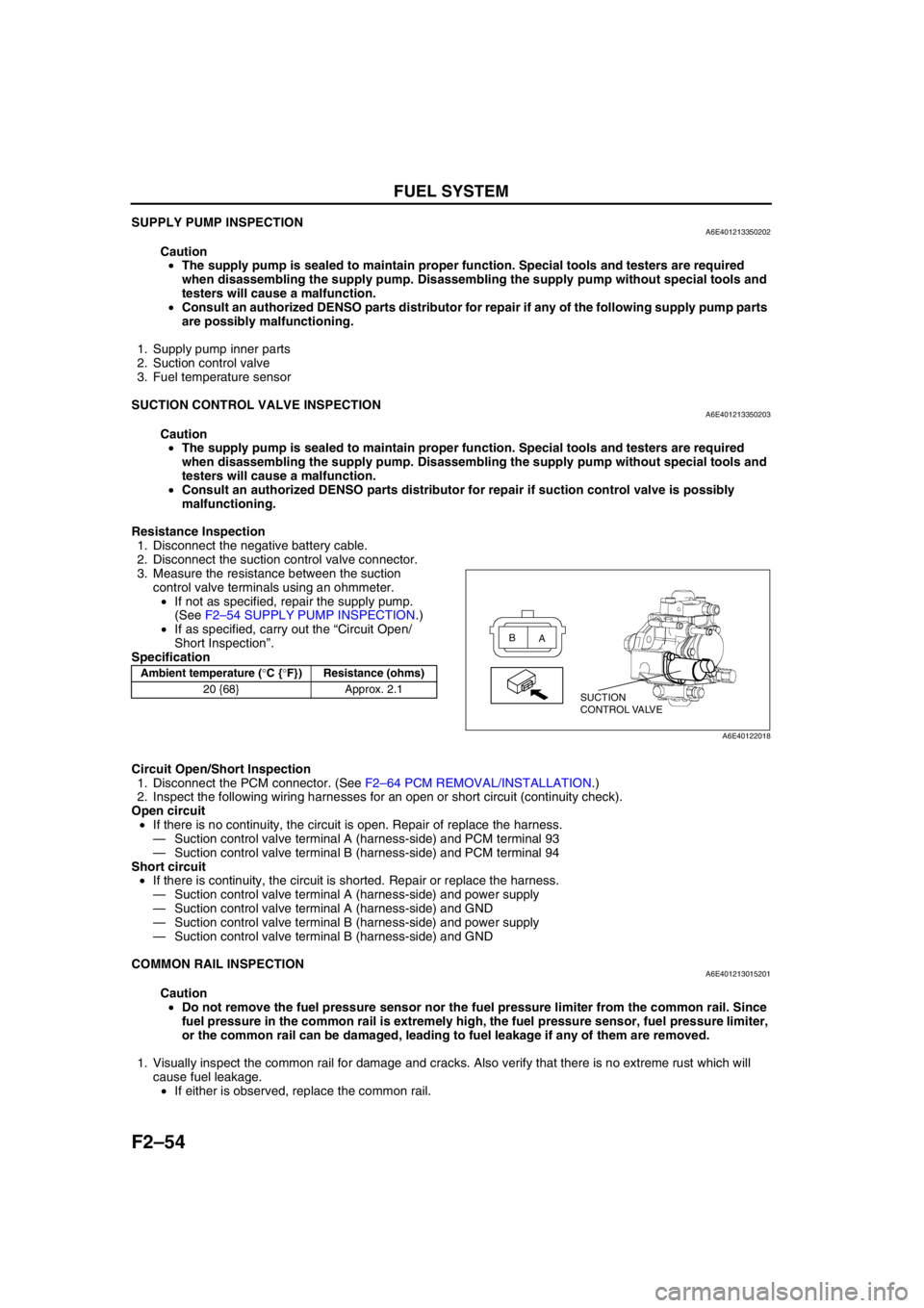
F2–54
FUEL SYSTEM
SUPPLY PUMP INSPECTIONA6E401213350202
Caution
•The supply pump is sealed to maintain proper function. Special tools and testers are required
when disassembling the supply pump. Disassembling the supply pump without special tools and
testers will cause a malfunction.
•Consult an authorized DENSO parts distributor for repair if any of the following supply pump parts
are possibly malfunctioning.
1. Supply pump inner parts
2. Suction control valve
3. Fuel temperature sensor
End Of Sie
SUCTION CONTROL VALVE INSPECTIONA6E401213350203
Caution
•The supply pump is sealed to maintain proper function. Special tools and testers are required
when disassembling the supply pump. Disassembling the supply pump without special tools and
testers will cause a malfunction.
•Consult an authorized DENSO parts distributor for repair if suction control valve is possibly
malfunctioning.
Resistance Inspection
1. Disconnect the negative battery cable.
2. Disconnect the suction control valve connector.
3. Measure the resistance between the suction
control valve terminals using an ohmmeter.
•If not as specified, repair the supply pump.
(See F2–54 SUPPLY PUMP INSPECTION.)
•If as specified, carry out the “Circuit Open/
Short Inspection”.
Specification
Circuit Open/Short Inspection
1. Disconnect the PCM connector. (See F2–64 PCM REMOVAL/INSTALLATION.)
2. Inspect the following wiring harnesses for an open or short circuit (continuity check).
Open circuit
•If there is no continuity, the circuit is open. Repair of replace the harness.
—Suction control valve terminal A (harness-side) and PCM terminal 93
—Suction control valve terminal B (harness-side) and PCM terminal 94
Short circuit
•If there is continuity, the circuit is shorted. Repair or replace the harness.
—Suction control valve terminal A (harness-side) and power supply
—Suction control valve terminal A (harness-side) and GND
—Suction control valve terminal B (harness-side) and power supply
—Suction control valve terminal B (harness-side) and GND
End Of Sie
COMMON RAIL INSPECTIONA6E401213015201
Caution
•Do not remove the fuel pressure sensor nor the fuel pressure limiter from the common rail. Since
fuel pressure in the common rail is extremely high, the fuel pressure sensor, fuel pressure limiter,
or the common rail can be damaged, leading to fuel leakage if any of them are removed.
1. Visually inspect the common rail for damage and cracks. Also verify that there is no extreme rust which will
cause fuel leakage.
•If either is observed, replace the common rail.
End Of Sie
Ambient temperature (°C {°F}) Resistance (ohms)
20 {68} Approx. 2.1
SUCTION
CONTROL VALVE A B
A6E40122018
Page 207 of 909
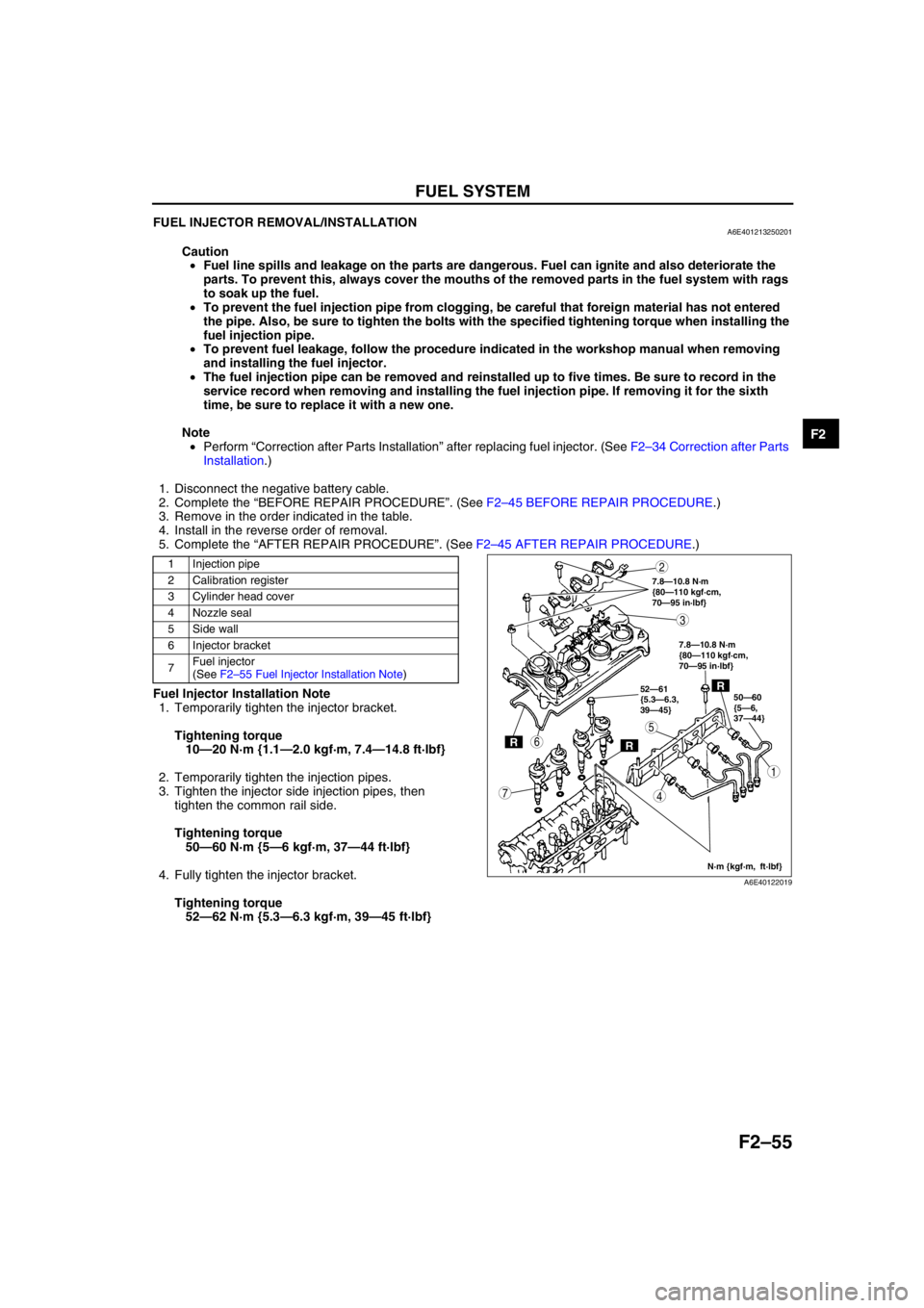
FUEL SYSTEM
F2–55
F2
FUEL INJECTOR REMOVAL/INSTALLATIONA6E401213250201
Caution
•Fuel line spills and leakage on the parts are dangerous. Fuel can ignite and also deteriorate the
parts. To prevent this, always cover the mouths of the removed parts in the fuel system with rags
to soak up the fuel.
•To prevent the fuel injection pipe from clogging, be careful that foreign material has not entered
the pipe. Also, be sure to tighten the bolts with the specified tightening torque when installing the
fuel injection pipe.
•To prevent fuel leakage, follow the procedure indicated in the workshop manual when removing
and installing the fuel injector.
•The fuel injection pipe can be removed and reinstalled up to five times. Be sure to record in the
service record when removing and installing the fuel injection pipe. If removing it for the sixth
time, be sure to replace it with a new one.
Note
•Perform “Correction after Parts Installation” after replacing fuel injector. (See F2–34 Correction after Parts
Installation.)
1. Disconnect the negative battery cable.
2. Complete the “BEFORE REPAIR PROCEDURE”. (See F2–45 BEFORE REPAIR PROCEDURE.)
3. Remove in the order indicated in the table.
4. Install in the reverse order of removal.
5. Complete the “AFTER REPAIR PROCEDURE”. (See F2–45 AFTER REPAIR PROCEDURE.)
.
Fuel Injector Installation Note
1. Temporarily tighten the injector bracket.
Tightening torque
10—20 N·m {1.1—2.0 kgf·m, 7.4—14.8 ft·lbf}
2. Temporarily tighten the injection pipes.
3. Tighten the injector side injection pipes, then
tighten the common rail side.
Tightening torque
50—60 N·m {5—6 kgf·m, 37—44 ft·lbf}
4. Fully tighten the injector bracket.
Tightening torque
52—62 N·m {5.3—6.3 kgf·m, 39—45 ft·lbf}
1 Injection pipe
2 Calibration register
3 Cylinder head cover
4 Nozzle seal
5Side wall
6 Injector bracket
7Fuel injector
(See F2–55 Fuel Injector Installation Note)
RR
R50—60
{5—6,
37—44} 52—61
{5.3—6.3,
39—45}
N·m {kgf·m, ft·lbf} 7.8—10.8 N·m
{80—110 kgf·cm,
70—95 in·lbf}
7.8—10.8 N·m
{80—110 kgf·cm,
70—95 in·lbf}
5
4
3
1
2
7
6
A6E40122019
Page 208 of 909
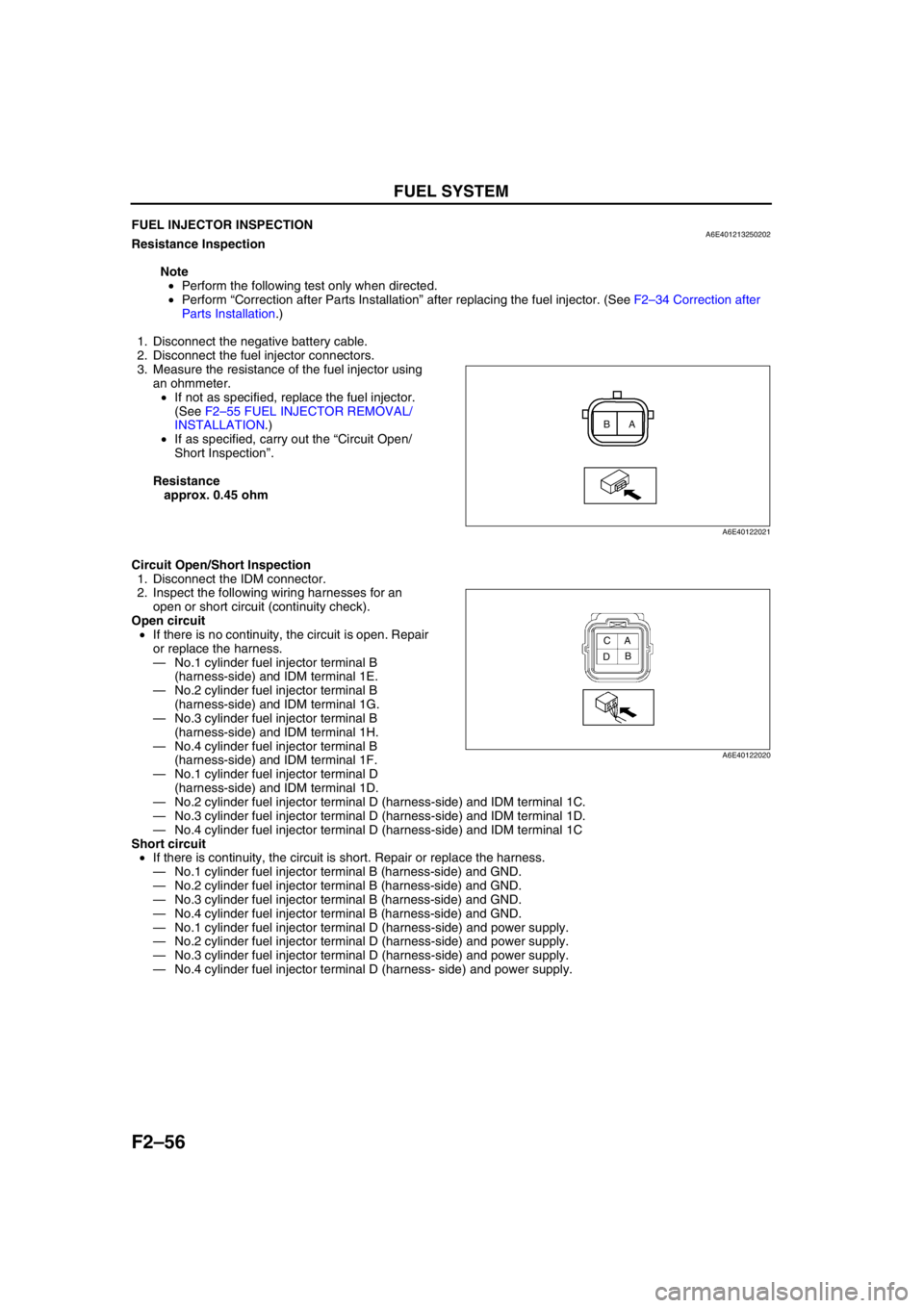
F2–56
FUEL SYSTEM
End Of SieFUEL INJECTOR INSPECTIONA6E401213250202Resistance Inspection
Note
•Perform the following test only when directed.
•Perform “Correction after Parts Installation” after replacing the fuel injector. (See F2–34 Correction after
Parts Installation.)
1. Disconnect the negative battery cable.
2. Disconnect the fuel injector connectors.
3. Measure the resistance of the fuel injector using
an ohmmeter.
•If not as specified, replace the fuel injector.
(See F2–55 FUEL INJECTOR REMOVAL/
INSTALLATION.)
•If as specified, carry out the “Circuit Open/
Short Inspection”.
Resistance
approx. 0.45 ohm
Circuit Open/Short Inspection
1. Disconnect the IDM connector.
2. Inspect the following wiring harnesses for an
open or short circuit (continuity check).
Open circuit
•If there is no continuity, the circuit is open. Repair
or replace the harness.
—No.1 cylinder fuel injector terminal B
(harness-side) and IDM terminal 1E.
—No.2 cylinder fuel injector terminal B
(harness-side) and IDM terminal 1G.
—No.3 cylinder fuel injector terminal B
(harness-side) and IDM terminal 1H.
—No.4 cylinder fuel injector terminal B
(harness-side) and IDM terminal 1F.
—No.1 cylinder fuel injector terminal D
(harness-side) and IDM terminal 1D.
—No.2 cylinder fuel injector terminal D (harness-side) and IDM terminal 1C.
—No.3 cylinder fuel injector terminal D (harness-side) and IDM terminal 1D.
—No.4 cylinder fuel injector terminal D (harness-side) and IDM terminal 1C
Short circuit
•If there is continuity, the circuit is short. Repair or replace the harness.
—No.1 cylinder fuel injector terminal B (harness-side) and GND.
—No.2 cylinder fuel injector terminal B (harness-side) and GND.
—No.3 cylinder fuel injector terminal B (harness-side) and GND.
—No.4 cylinder fuel injector terminal B (harness-side) and GND.
—No.1 cylinder fuel injector terminal D (harness-side) and power supply.
—No.2 cylinder fuel injector terminal D (harness-side) and power supply.
—No.3 cylinder fuel injector terminal D (harness-side) and power supply.
—No.4 cylinder fuel injector terminal D (harness- side) and power supply.
End Of Sie
A B
A6E40122021
A
B C
D
A6E40122020
Page 209 of 909

EXHAUST SYSTEM
F2–57
F2
EXHAUST SYSTEM INSPECTIONA6E4014400002031. Start the engine and inspect each exhaust system component for exhaust gas leakage.
•If leakage is found, repair or replace as necessary.
End Of Sie
EXHAUST SYSTEM REMOVAL/INSTALLATIONA6E401440000204
Warning
•When the engine and exhaust system are hot, they can cause severe burns or injury. Turn off the
engine and wait until they are cool before removing the exhaust system.
1. Disconnect the negative battery cable.
2. Remove in the order indicated in the table.
3. Install in the reverse order of removal.
.
EXHAUST SYSTEM
13
B
B
A
A
N·m {kgf·m, ft·lbf} 7.9—10.7 N
·m
{80—110 kgf·cm,
70—94 in·lbf}
7.9—10.7 N
·m
{80—110 kgf·cm,
70—94 in·lbf}
38—51
{3.9—5.2,
29—37} 7.9—10.7 N·m
{80—110 kgf·cm,
70—94 in·lbf}
38—51
{3.9—5.2,
29—37} 38—51
{3.9—5.2,
29—37} 21.6—26.5
{2.2—2.7,
16.0—19.5} 8.9—12.7 N
·m
{90—130 kgf·cm,
79—112 in·lbf}
8.9—12.7 N·m
{90—130 kgf·cm,
79—112 in·lbf}
43—60
{4.3—6.1, 31—44} 40.3—54.7
{4.11—5.57,
29.8—40.3}
43—60
{4.3—6.1, 31—44}9.1—14.3 N·m
{93—145 kgf·cm,
81—126 in·lbf} 11.8—17.6
{1.2—1.7, 8.7—12.9} 15.7—23.5
{1.6—2.3, 11.6—17.3}
7.9—10.7 N·m
{80—110 kgf·cm,
70—94 in·lbf}
38.2—46.1
{3.9—4.7, 28—34}
R
R
RR
R
R
R
R
RR
R
R
R
9
8
7
5
4
310
11
12
6
1
2
14
R
R
A6E40142006
1 Main silencer
2 Middle pipe
3 Oxidation catalytic converter
4 Front pipe5 Warm up oxidation catalytic converter
(See F2–58 Warm Up Oxidation Catalytic Converter
Removal Note)
6 Turbocharger insulator No. 1
7 Turbocharger insulator No. 2
Page 210 of 909
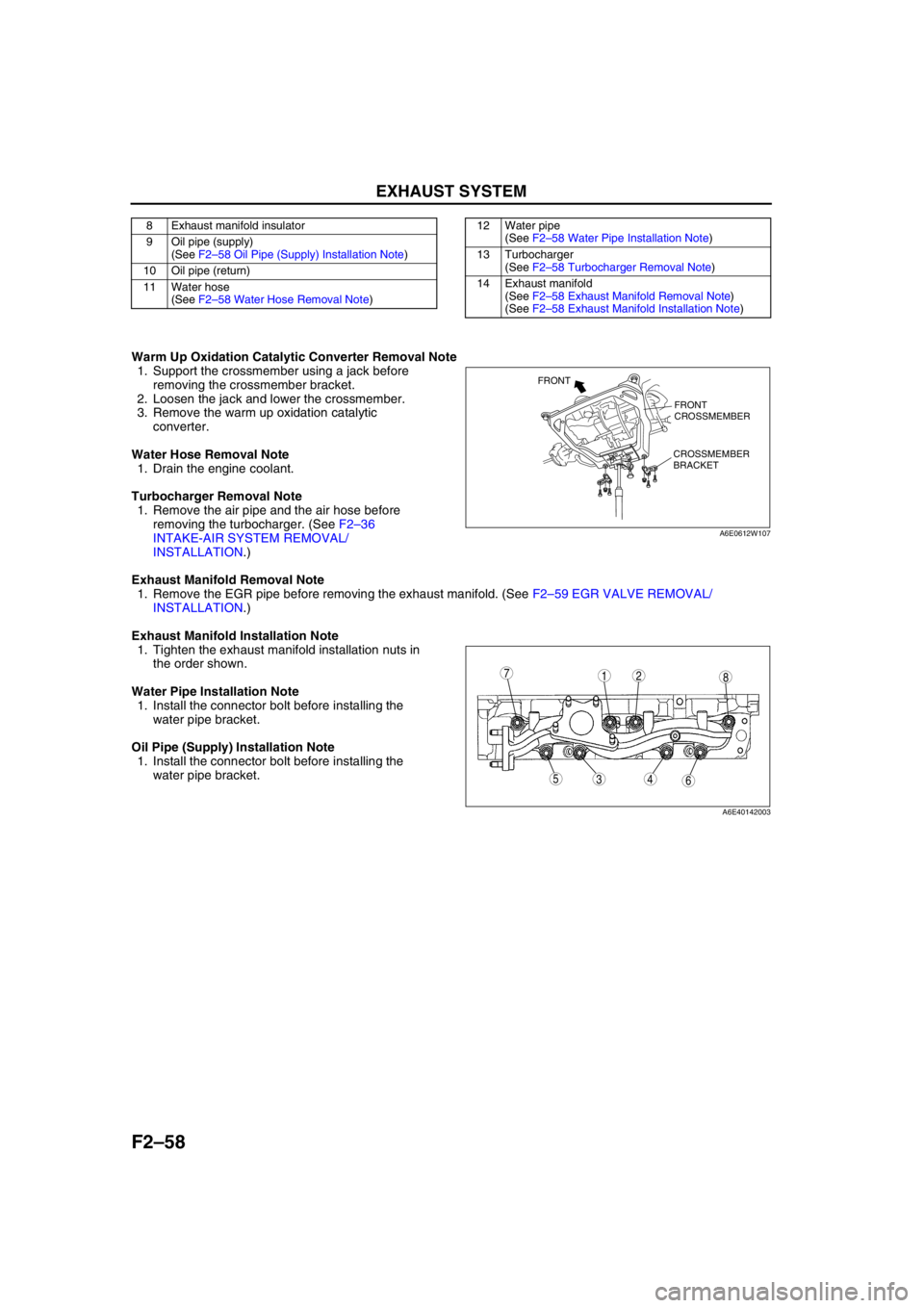
F2–58
EXHAUST SYSTEM
Warm Up Oxidation Catalytic Converter Removal Note
1. Support the crossmember using a jack before
removing the crossmember bracket.
2. Loosen the jack and lower the crossmember.
3. Remove the warm up oxidation catalytic
converter.
Water Hose Removal Note
1. Drain the engine coolant.
Turbocharger Removal Note
1. Remove the air pipe and the air hose before
removing the turbocharger. (See F2–36
INTAKE-AIR SYSTEM REMOVAL/
INSTALLATION.)
Exhaust Manifold Removal Note
1. Remove the EGR pipe before removing the exhaust manifold. (See F2–59 EGR VALVE REMOVAL/
INSTALLATION.)
Exhaust Manifold Installation Note
1. Tighten the exhaust manifold installation nuts in
the order shown.
Water Pipe Installation Note
1. Install the connector bolt before installing the
water pipe bracket.
Oil Pipe (Supply) Installation Note
1. Install the connector bolt before installing the
water pipe bracket.
End Of Sie
8 Exhaust manifold insulator
9 Oil pipe (supply)
(See F2–58 Oil Pipe (Supply) Installation Note)
10 Oil pipe (return)
11 Water hose
(See F2–58 Water Hose Removal Note)12 Water pipe
(See F2–58 Water Pipe Installation Note)
13 Turbocharger
(See F2–58 Turbocharger Removal Note)
14 Exhaust manifold
(See F2–58 Exhaust Manifold Removal Note)
(See F2–58 Exhaust Manifold Installation Note)
FRONT
CROSSMEMBER
CROSSMEMBER
BRACKET FRONT
A6E0612W107
87
5436
12
A6E40142003