MAZDA 626 1987 Workshop Manual
Manufacturer: MAZDA, Model Year: 1987,
Model line: 626,
Model: MAZDA 626 1987
Pages: 1865, PDF Size: 94.35 MB
MAZDA 626 1987 Workshop Manual
626 1987
MAZDA
MAZDA
https://www.carmanualsonline.info/img/28/57059/w960_57059-0.png
MAZDA 626 1987 Workshop Manual
Trending: brake sensor, load capacity, jacking, maintenance, roof, fuel cap release, trunk release
Page 621 of 1865
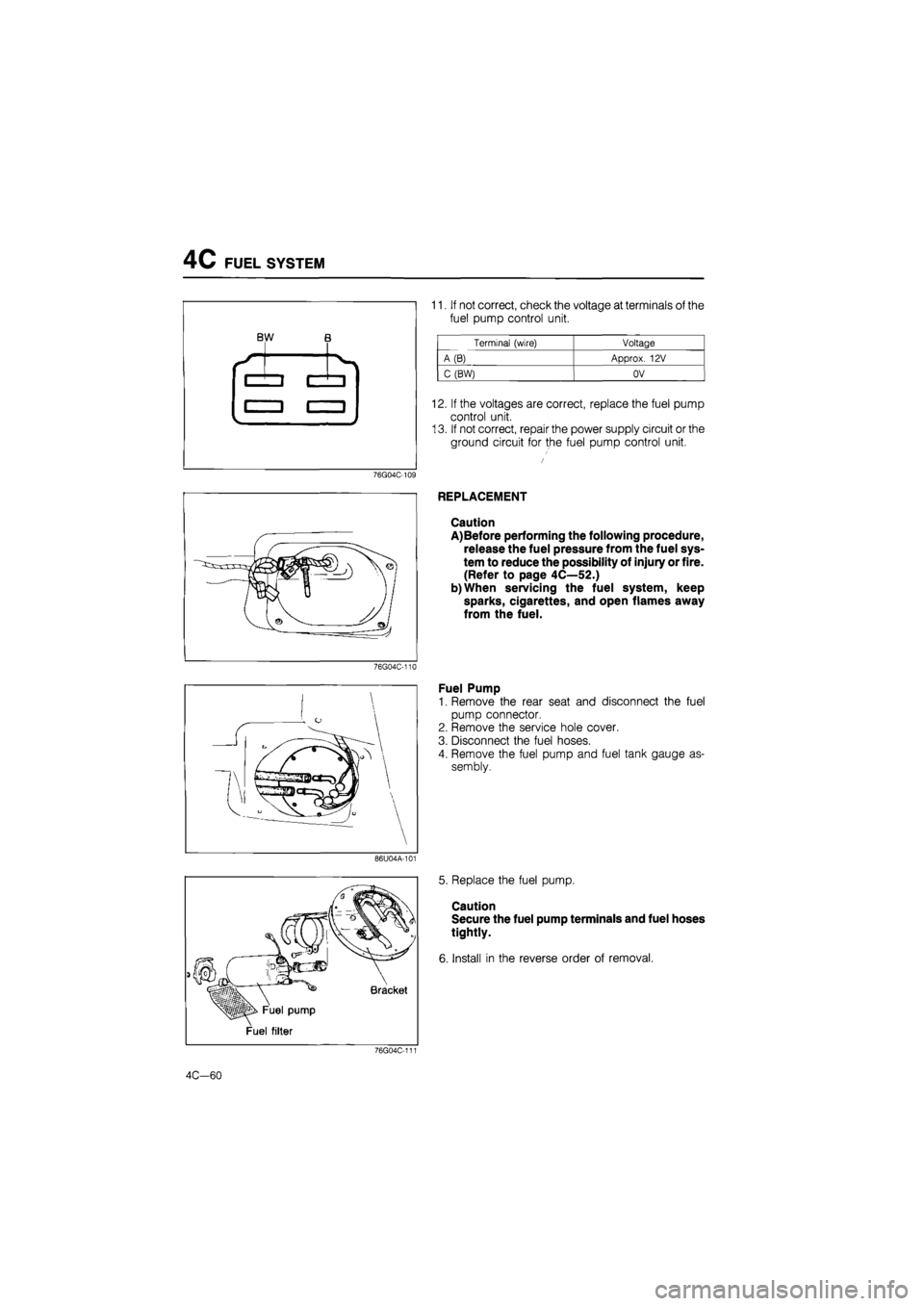
4C FUEL SYSTEM
BW B
11. If not correct, check the voltage at terminals of the
fuel pump control unit.
76G04C-109
76G04C-110
86U04A-101
Fuel pump
Fuel filter
Bracket
76G04C-111
Terminal (wire) Voltage
A(B) Approx. 12V
C (BW) OV
12. If the voltages are correct, replace the fuel pump
control unit.
13. If not correct, repair the power supply circuit or the
ground circuit for the fuel pump control unit.
REPLACEMENT
Caution
A)Before performing the following procedure,
release the fuel pressure from the fuel sys-
tem to reduce the possibility of injury or fire.
(Refer to page 4C—52.)
b)When servicing the fuel system, keep
sparks, cigarettes, and open flames away
from the fuel.
Fuel Pump
1. Remove the rear seat and disconnect the fuel
pump connector.
2. Remove the service hole cover.
3. Disconnect the fuel hoses.
4. Remove the fuel pump and fuel tank gauge as-
sembly.
5. Replace the fuel pump.
Caution
Secure the fuel pump terminals and fuel hoses
tightly.
6. Install in the reverse order of removal.
4C—60
Page 622 of 1865
FUEL SYSTEM 4C
76G04C-112
86U04B-083
76G04C-113
Transfer Pump
1. Remove the fuel tank. (Refer to page 4C—65.)
2. Disconnect the fuel hoses from the transfer pump.
3. Remove the transfer pump.
4. Install in the reverse order of removal.
Injector
1. Remove the engine hanger.
2. Remove the wiring harness bracket.
3. Disconnect the PCV valve and hose from the dy-
namic chamber.
76G04C-114
4C-61
Page 623 of 1865
4C FUEL SYSTEM
4. Disconnect the main fuel hose from the delivery
pipe assembly.
5. Disconnect the fuel return hose from the fuel re-
turn pipe.
6. Remove fuel return pipe mounting bolt.
76G04C-115
7. Remove the delivery pipe assembly mounting bolts
and insulators.
76G04C-116
Remove the grommets, injectors, and insulators.
Install in the reverse order of removal, referring to
the installation note.
Tightening torque:
Delivery pipe, dynamic chamber, and en-
gine hanger
19—25 N m (1.9—2.6 m-kg, 14—19 ft-lb)
76G04C-117
O-ring Injector / Correct
v L
Grommet Delivery pipe
Wrong
/
Dc^Li Wrong
Installation note
Injector
1. Use new O-rings.
2. Apply a small amount of engine oil to the O-rings
when installing.
86U04A-108
4C-62
Page 624 of 1865
FUEL SYSTEM 4C
3. Install the injectors and the injector insulators.
86U04A-109
O-ring
Grommet
Injector
Insulator
Bolt
,J| Delivery
XM P'pe
\1 \>_ - ( ^ ,r- Insulator
Insulator
Install the insulators between the intake manifold and
the delivery pipe.
76G04C-118
Delivery Pipe
1. Remove the injectors. (Refer to page 4C—61.)
2. Separate the fuel return pipe from the delivery pipe
assembly.
76G04C-119
3. Replace the delivery pipe.
4. Install in the reverse order of removal, referring to
the installation note.
Tightening torque:
Fuel return pipe 8—11 N-m
(0.8—1.1 m-kg, 69—95 in-lb)
76G04C-120
4C-63
Page 625 of 1865
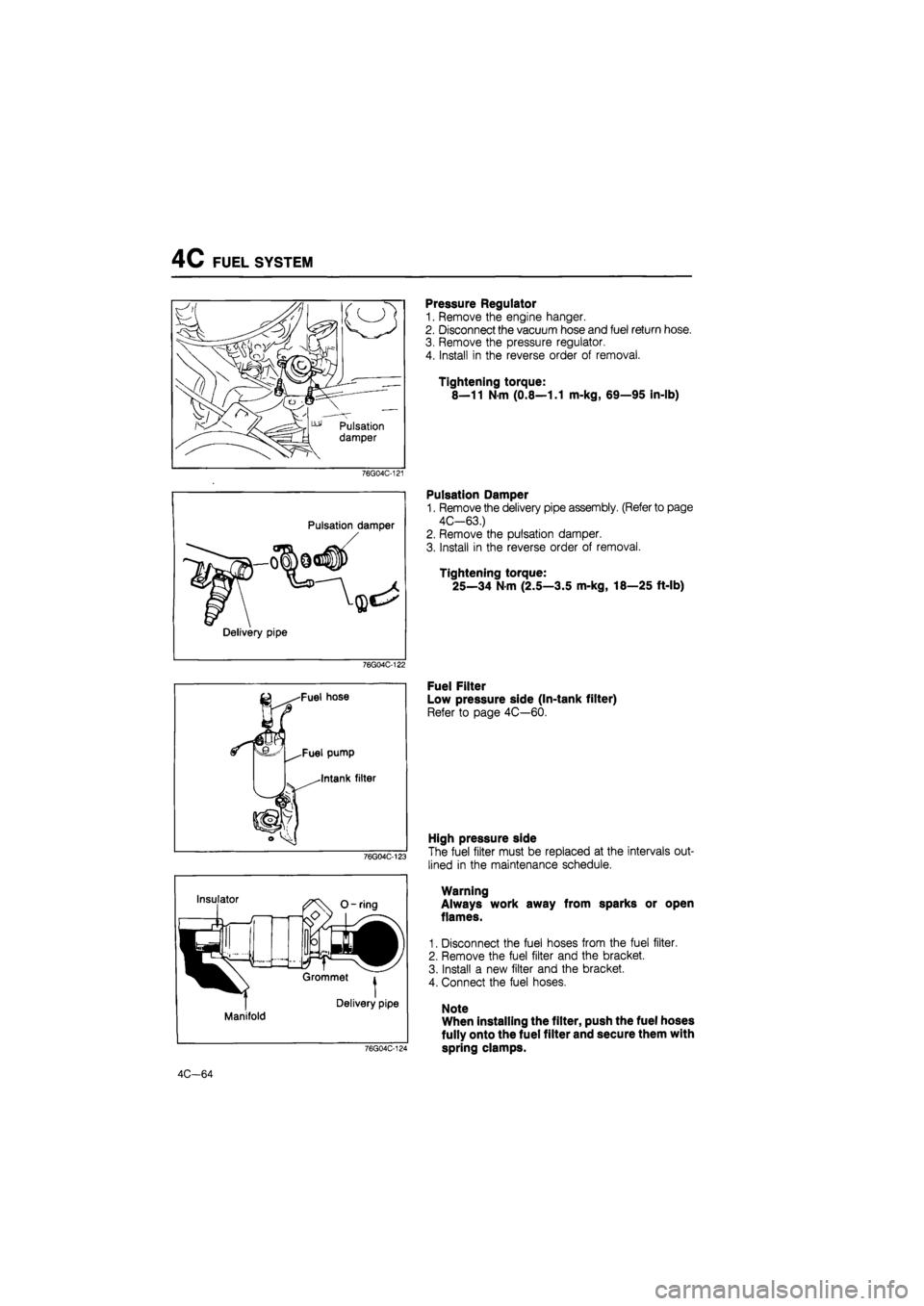
4C FUEL SYSTEM
^ Pulsation
damper
76G04C-121
Pulsation damper
—
Delivery pipe
76G04C-122
Fuel hose
,Fuel pump
-Intank filter
76G04C-123
Insulator
f f r—
/ 0 DM
•
II r
O - ring
Grommet
Manifold
Delivery pipe
Pressure Regulator
1. Remove the engine hanger.
2. Disconnect the vacuum hose and fuel return hose.
3. Remove the pressure regulator.
4. Install in the reverse order of removal.
Tightening torque:
8—11 Nm (0.8—1.1 m-kg, 69—95 in-lb)
Pulsation Damper
1. Remove the delivery pipe assembly. (Refer to page
4C-63.)
2. Remove the pulsation damper.
3. Install in the reverse order of removal.
Tightening torque:
25—34 N m (2.5—3.5 m-kg, 18—25 ft-lb)
Fuel Filter
Low pressure side (In-tank filter)
Refer to page 4C—60.
76G04C-124
High pressure side
The fuel filter must be replaced at the intervals out-
lined in the maintenance schedule.
Warning
Always work away from sparks or open
flames.
1. Disconnect the fuel hoses from the fuel filter.
2. Remove the fuel filter and the bracket.
3. Install a new filter and the bracket.
4. Connect the fuel hoses.
Note
When installing the filter, push the fuel hoses
fully onto the fuel filter and secure them with
spring clamps.
4C-64
Page 626 of 1865
FUEL SYSTEM 4C
FUEL TANK
Removal
Caution
a) Before performing the following procedure, release the fuel pressure from the fuel sys-
tem to reduce the possibility of injury or fire. (Refer to page 4C—52.)
b)When removing the fuel tank, keep sparks, cigarettes, and open flames away from the
fuel tank.
Remove in the sequence shown in the figure.
76G04C-125
Note
Drain the fuel from the fuel tank before removing the tank.
1. Remove fuel filler cap.
2. Fuel pump connectors
3. Fuel hoses
4. Steering angle transfer shaft (4-wheel
steering)
(Refer to section 10)
5. Cross member (4-wheel steering)
6. Evaporative hoses
7. Fuel filler hose
8. Breather hose
9. Parking cable bracket
10. Fuel tank strap
11. Fuel tank
4C-65
Page 627 of 1865
4C FUEL SYSTEM
Inspection
1. Check the fuel tank for cracks and corrosion.
2. If any defect is found, repair or replace the tank.
Warning
Before repairing, clean the fuel tank thorough-
ly with steam to remove all explosive fuel and
fumes.
Installation
Install in the reverse order of removal, referring to the installation note.
Torque Specifications
4C-66
76G04C-126
Page 628 of 1865
FUEL SYSTEM 4C
Installation note
Hoses
1. Push the ends of the main fuel hose, fuel return
hose, and evaporation hoses onto the fuel tank fit-
tings at least 25 mm (1.0 in).
2. Push the fuel filler hose onto the fuel tank pipe and
filler pipe at least 35 mm (1.4 in).
Steering angle transfer shaft
(4-wheel steering)
Refer to section 10
4C—67
Page 629 of 1865
4C PRC SYSTEM
PRESSURE REGULATOR CONTROL
(PRC)
SYSTEM
Distributor (Ne signal)
I Fuel
(To fuel tank)
76G04C-128
To prevent percolation of the fuel during idle after the engine is restarted, vacuum is cut to the pres-
sure regulator, increasing the fuel pressure.
Specified time: Approx. 120 sec.
Operating condition: Coolant temperature — above 70°C (158°F)
Intake air temperature — above 30°C (86°F)....Unleaded fuel
above 50°C (122°F)....Leaded fuel
4C-68
Page 630 of 1865
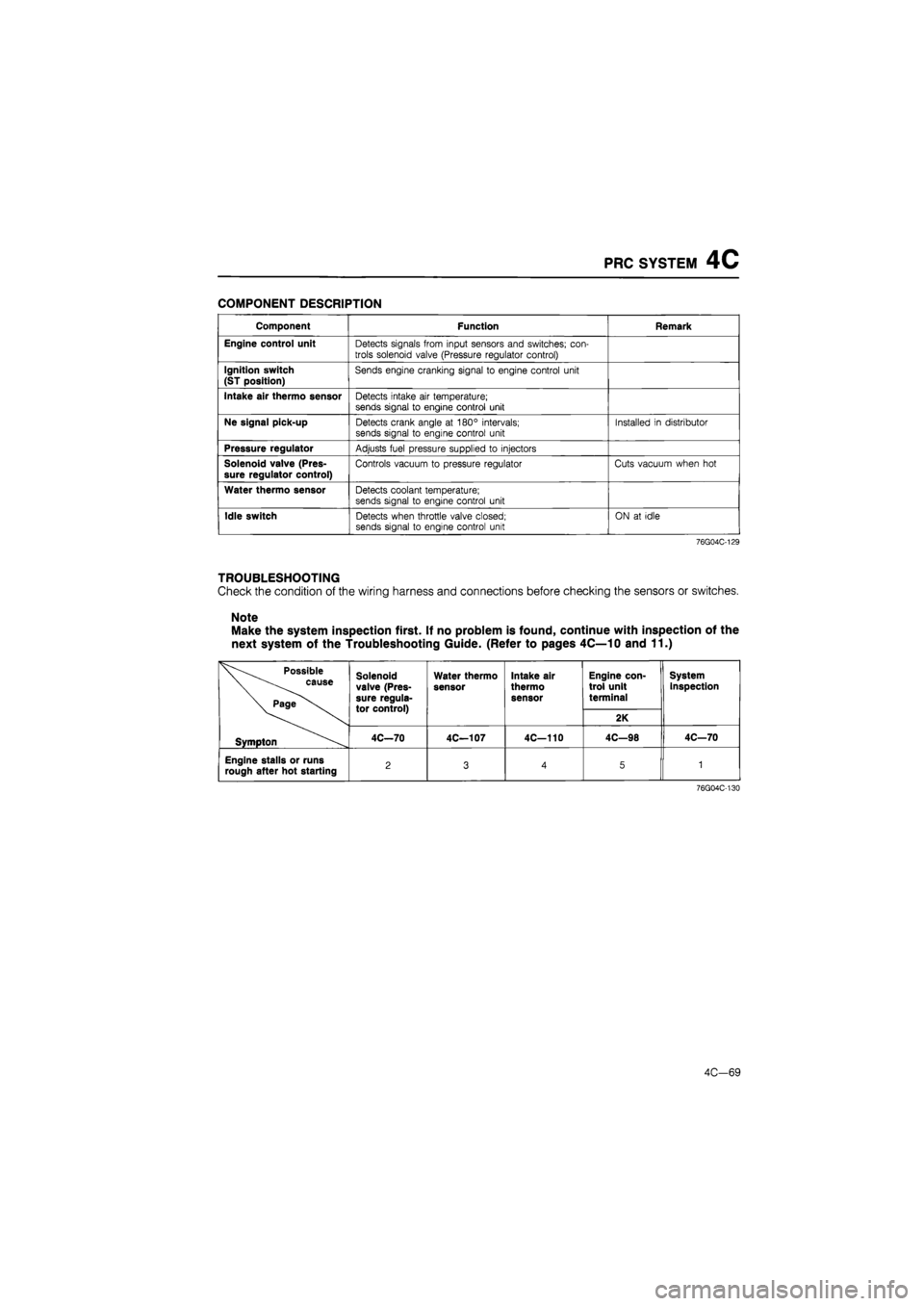
PRC SYSTEM 4C
COMPONENT DESCRIPTION
Component Function Remark
Engine control unit Detects signals from input sensors and switches; con-trols solenoid valve (Pressure regulator control)
Ignition switch
(ST position)
Sends engine cranking signal to engine control unit
Intake air thermo sensor Detects intake air temperature; sends signal to engine control unit
Ne signal pick-up Detects crank angle at 180° intervals; sends signal to engine control unit Installed in distributor
Pressure regulator Adjusts fuel pressure supplied to injectors
Solenoid valve (Pres-
sure regulator control)
Controls vacuum to pressure regulator Cuts vacuum when hot
Water thermo sensor Detects coolant temperature; sends signal to engine control unit
Idle switch Detects when throttle valve closed; sends signal to engine control unit ON at idle
76G04C-129
TROUBLESHOOTING
Check the condition of the wiring harness and connections before checking the sensors or switches.
Note
Make the system inspection first. If no problem is found, continue with inspection of the
next system of the Troubleshooting Guide. (Refer to pages 4C—10 and 11.)
Possible
\ cause
\ Page
Solenoid valve (Pres-sure regula-tor control)
Water thermo
sensor
Intake air
thermo
sensor
Engine con-trol unit terminal
System inspection Solenoid valve (Pres-sure regula-tor control) 2K
Symplon 4C—70 4C—107 4C-110 4C—98 4C—70
Engine stalls or runs rough after hot starting 2 3 4 5 1
76G04C-130
4C-69
Trending: check engine, fuel cap release, transmission, air filter, transmission oil, belt, overheating