ignition MAZDA MX-5 1994 Manual Online
[x] Cancel search | Manufacturer: MAZDA, Model Year: 1994, Model line: MX-5, Model: MAZDA MX-5 1994Pages: 1708, PDF Size: 82.34 MB
Page 232 of 1708
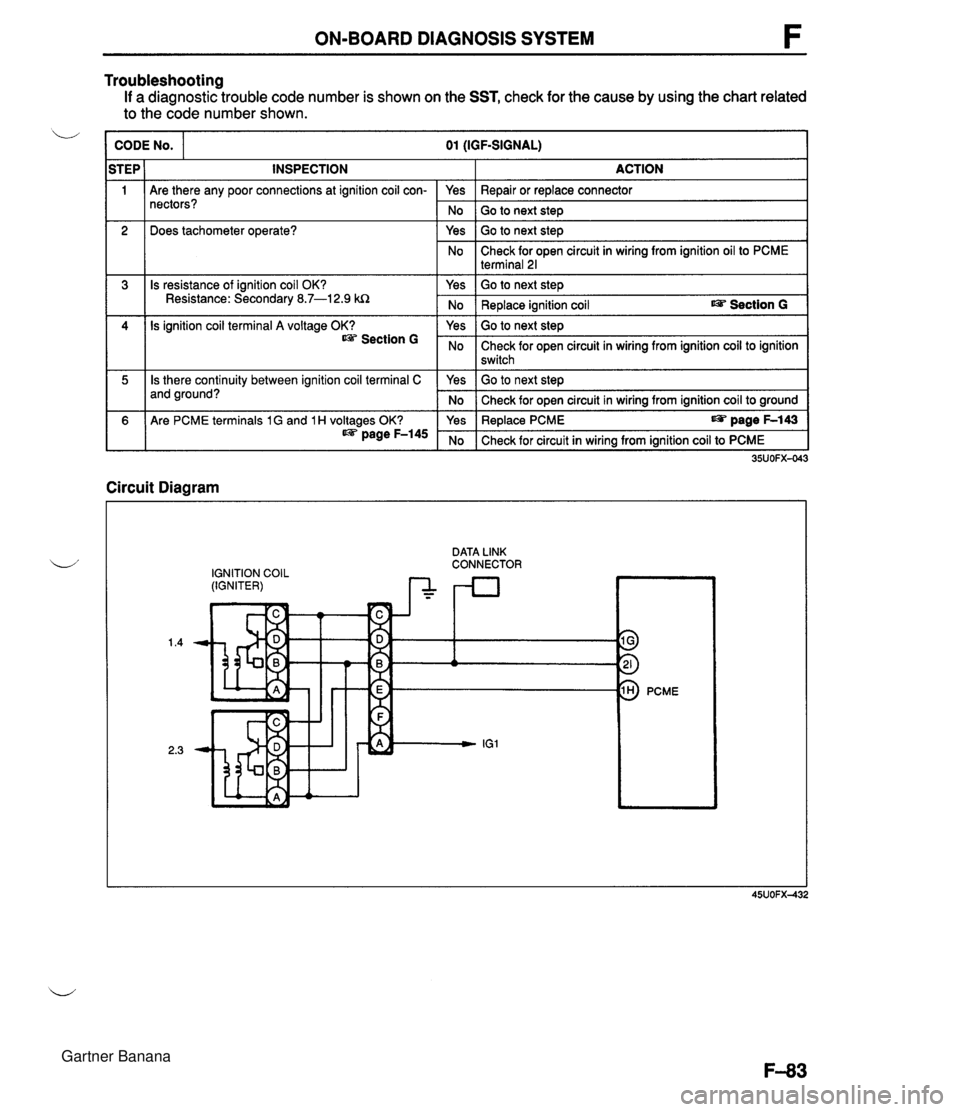
ON-BOARD DIAGNOSIS SYSTEM Troubleshooting If a diagnostic trouble code number is shown on the SST, check for the cause by using the chart related to the code number shown. CODE NO. 01 (IGF-SIGNAL) 1 Are there any poor connections at ignition coil con- nectors? 2 STEP 1 INSPECTION Does tachometer operate? 3 = 1 Is there continuity between ignition coil terminal C and ground? ACTION Is resistance of ignition coil OK? Resistance: Secondary 8.7-1 2.9 kQ 4 1 Are PCME terminals 1 G and 1 H voltages OK? @s page F-145 Is ignition coil terminal A voltage OK? Section G Circuit Diagram IGNITION COIL (IGNITER) Yes 1 Repair or replace connector I No Yes Go to next step Go to next step No Yes Check for open circuit in wiring from ignition oil to PCME terminal 21 Go to next step No Yes Yes I Replace PCME page F-143 I Replace ignition coil rn Section G Go to next step No Yes No - - No I Check for circuit in wiring from ignition coil to PCME I 35UOFX-043 Check for open circuit in wiring from ignition coil to ignition switch Go to next step Check for open circuit in wiring from ignition coil to ground DATA LINK - . . . . . - . . CONNECTOR 9 3 PCME Gartner Banana
Page 234 of 1708
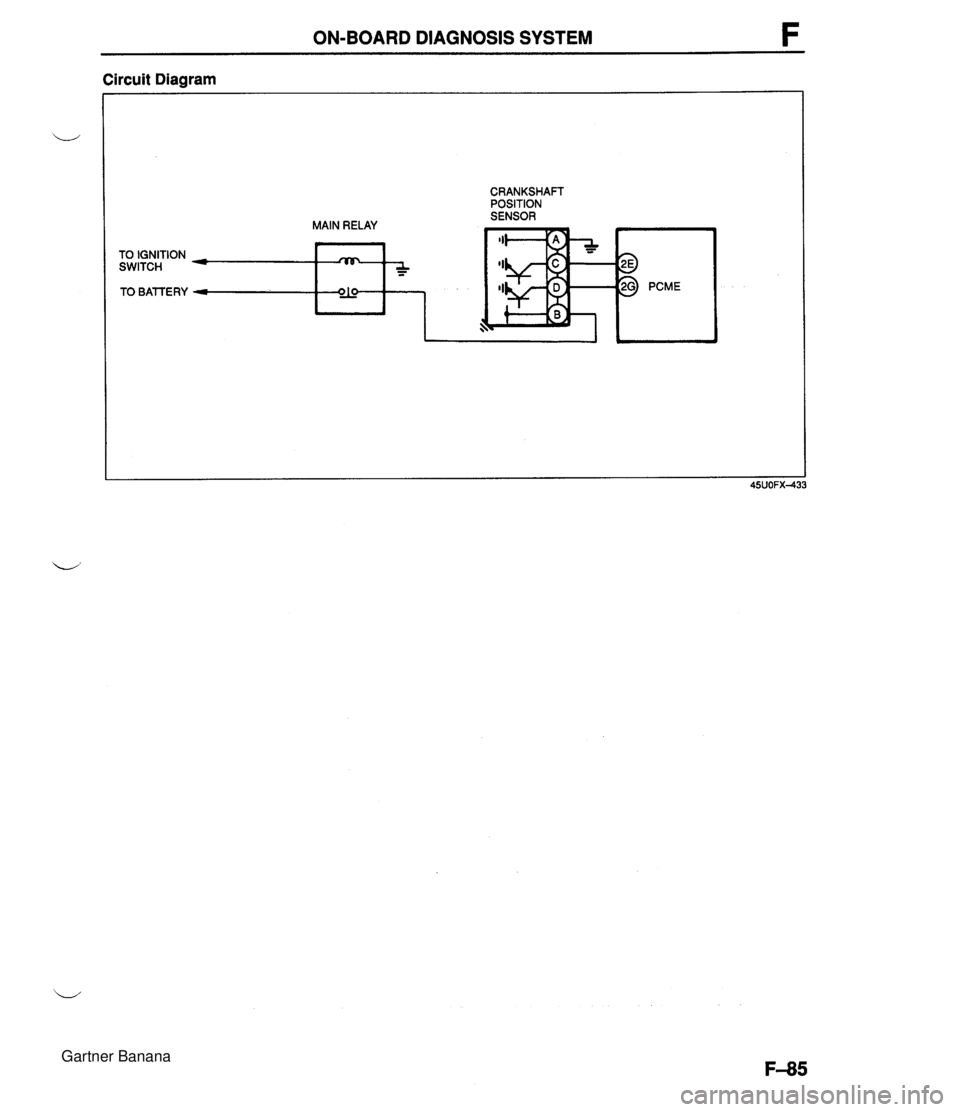
ON-BOARD DIAGNOSIS SYSTEM F Circuit Diagram TO IGNITION SWITCH TO BATTERY MAIN RELAY :AF*, CRANKSHAFT POSITION SENSOR Gartner Banana
Page 240 of 1708
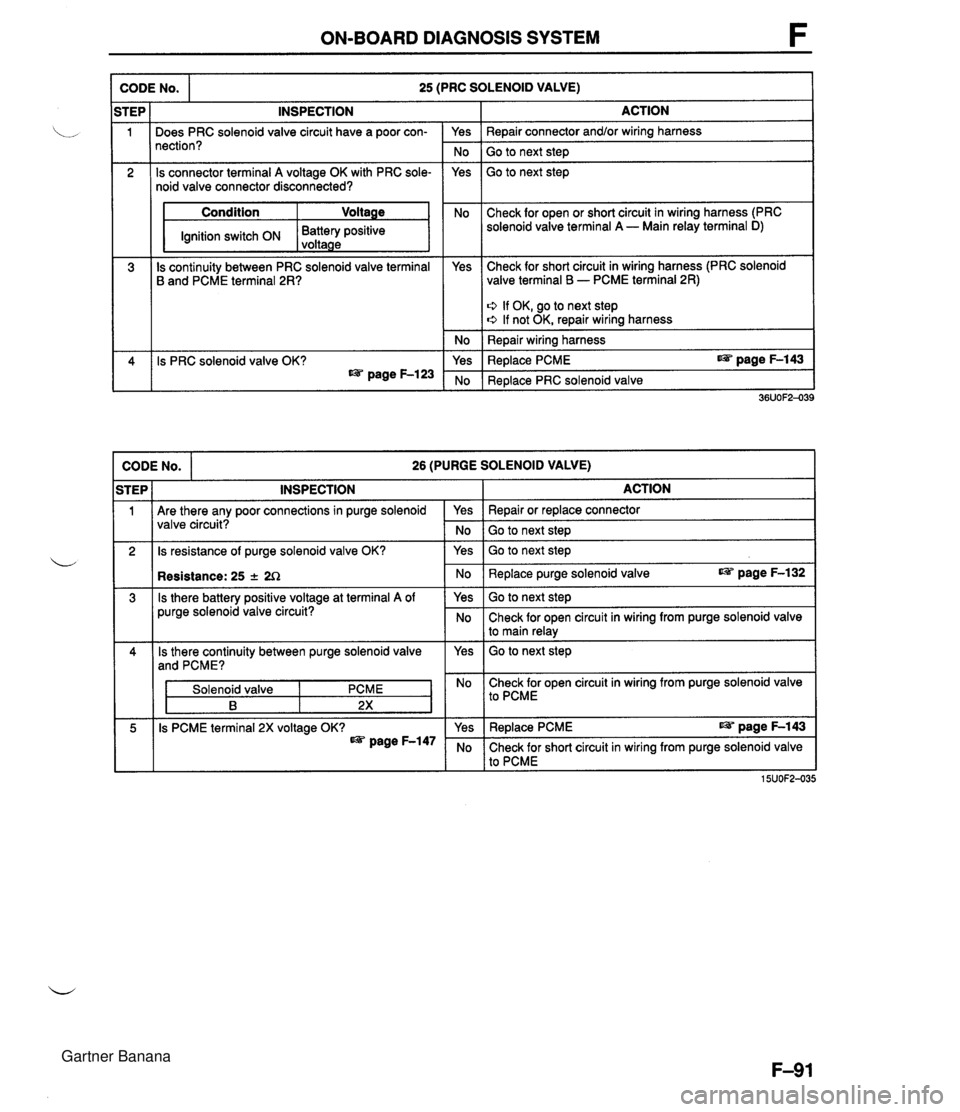
ON-BOARD DIAGNOSIS SYSTEM CODE No. 25 (PRC SOLENOID VALVE) I Condition Ignition switch ON ACTION Repair connector and/or wiring harness Go to next step Go to next step STEP 1 2 Check for open or short circuit in wiring harness (PRC Battery positive solenoid valve terminal A - Main relay terminal D) voltaae 3 CODE No. 26 (PURGE SOLENOID VALVE) iTEP I INSPECTION I ACTION 4 ' I Are there any poor connections in purge solenoid valve circuit? INSPECTION I . - I Is continuity between PRC solenoid valve terminal B and PCME terminal 2R? I 2 Is resistance of purge solenoid valve OK? Does PRC solenoid valve circuit have a poor con- nection? Is connector terminal A voltage OK with PRC sole- noid valve connector disconnected? 36UOF2-039 Is PRC solenoid valve OK? as page F-123 Is there battery positive voltage at terminal A of purge solenoid valve circuit? Yes No Yes Yes Solenoid valve Check for short circuit in wiring harness (PRC solenoid valve terminal B - PCME terminal 2R) No Yes ' No 5 Is PCME terminal 2X voltage OK? page F-147 Q If OK, go to next step e If not OK, repair wiring harness Repair wiring harness Replace PCME page F-143 Replace PRC solenoid valve Yes Repair or replace connector No Go to next step Yes Go to next step No Replace purge solenoid valve page F-132 Yes Go to next step No Check for open circuit in wiring from purge solenoid valve I to main relay I No Check for open circuit in wiring from purge solenoid valve I to PcME I Yes I Replace PCME page F-143 No Check for short circuit in wiring from purge solenoid valve to PCME 15UOF2-035 Gartner Banana
Page 242 of 1708
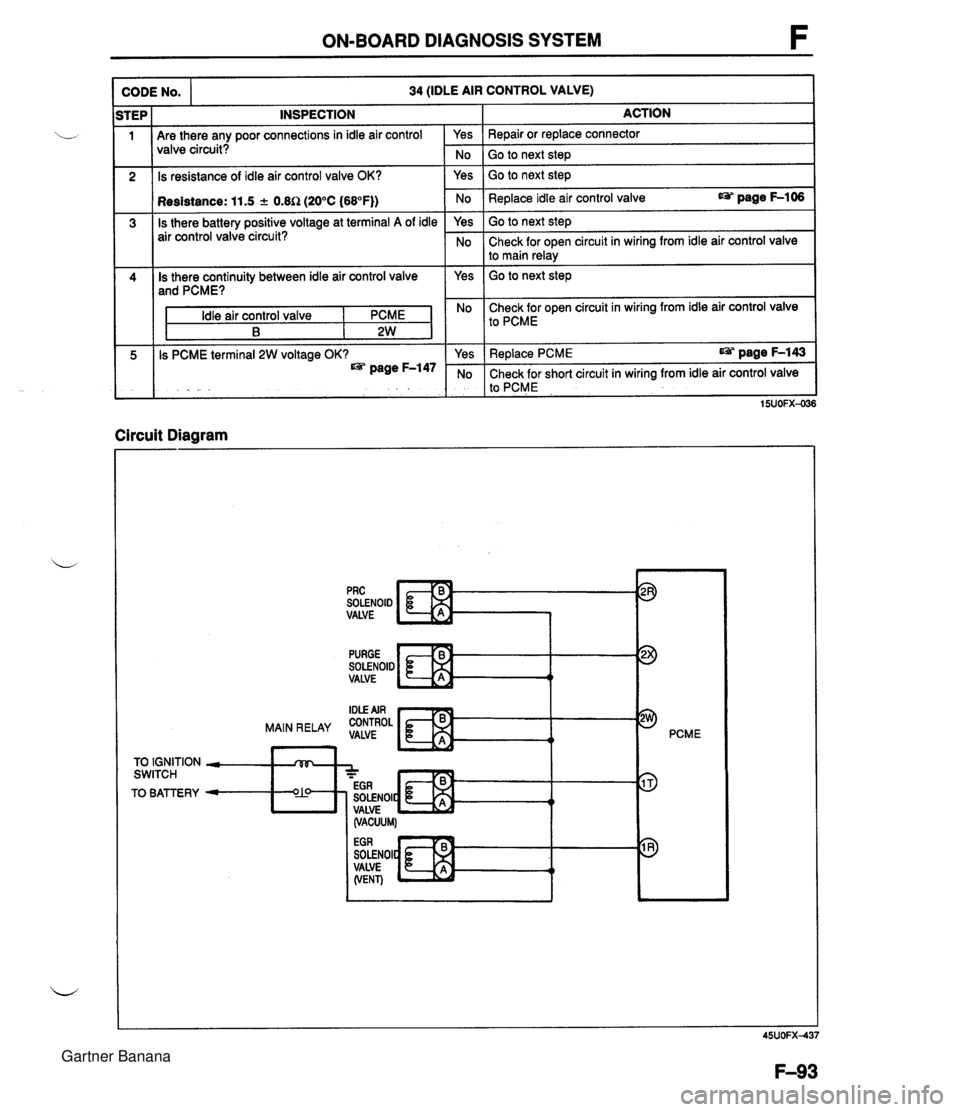
ON-BOARD DIAGNOSIS SYSTEM INSPECTION Are there any poor connections in idle air control valve circuit? CODE NO. Is resistance of idle air control valve OK? 34 (IDLE AIR CONTROL VALVE) 1 Resistance: 11.5 + 0.8R (20°C (68°F)) Is there battery positive voltage at terminal A of idle air control valve circuit? Is there continuity between idle air control valve and PCME? Idle air control valve I PCME B 2W Is PCME terminal 2W voltage OK? page F-147 Circuit Diagram No 1 Go to next ste~ I Yes ACTION Repair or replace connector Yes No Yes Go to next step I I Go to next step Replace idle air control valve page F-106 Yes No No Check for open circuit in wiring from idle air control valve I to PCME Go to next step Check for open circuit in wiring from idle air control valve to main relay SOLENOID VALVE pRc c Yes No PURGE SOLENOID VALVE Replace PCME page F-143 Check for short circuit in wiring from idle air control valve to PCME t PCME 15UOFX-036 TO IGNITION - rVF, SWITCH A - - EGR TO BATTERY - O?! SOLENOIC t 4 I, VALVE (VACUUM) SOLENOI VALVE (VENT) Gartner Banana
Page 243 of 1708
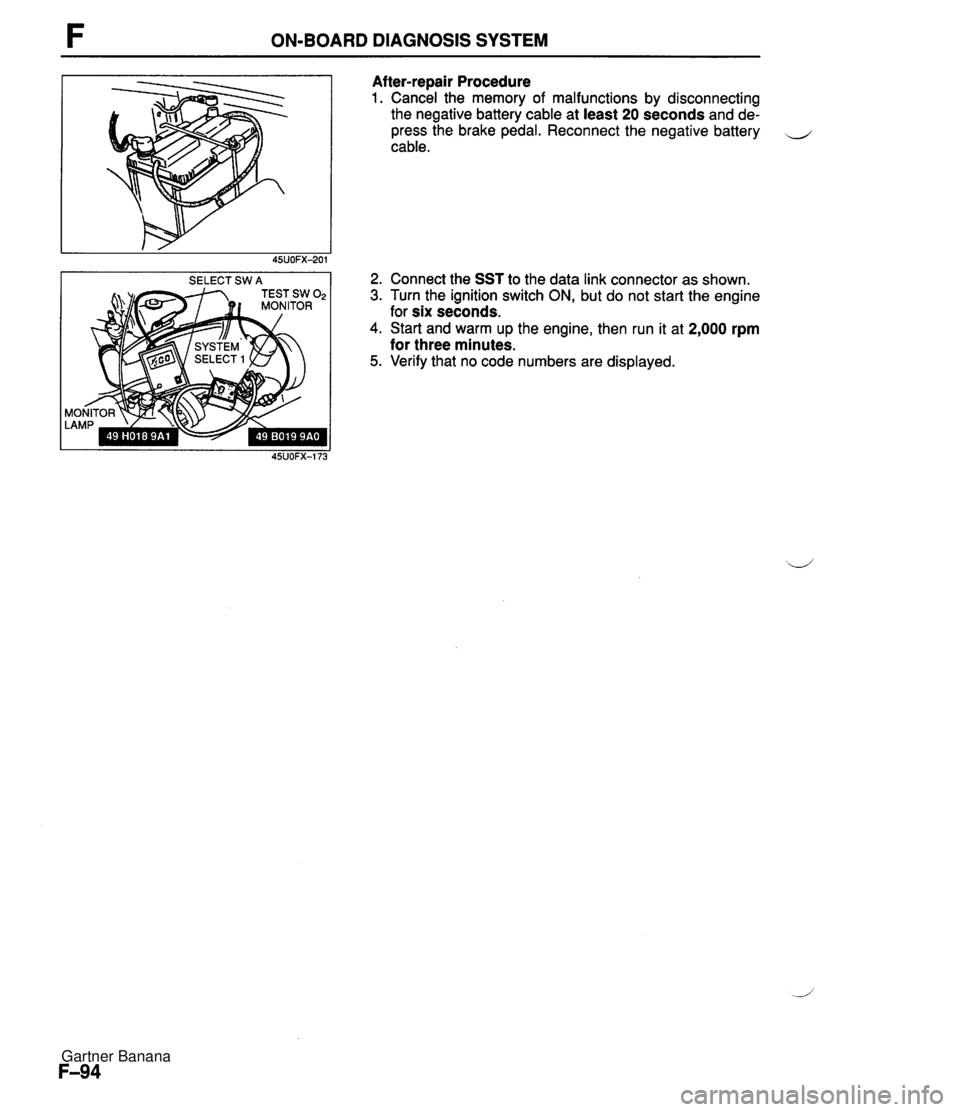
ON-BOARD DIAGNOSIS SYSTEM SELECT SW A Af ter-repair Procedure 1. Cancel the memory of malfunctions by disconnecting the negative battery cable at least 20 seconds and de- press the brake pedal. Reconnect the negative battery cable. 2. Connect the SST to the data link connector as shown. 3. Turn the ignition switch ON, but do not start the engine for six seconds. 4. Start and warm up the engine, then run it at 2,000 rpm for three minutes. 5. Verify that no code numbers are displayed. Gartner Banana
Page 244 of 1708
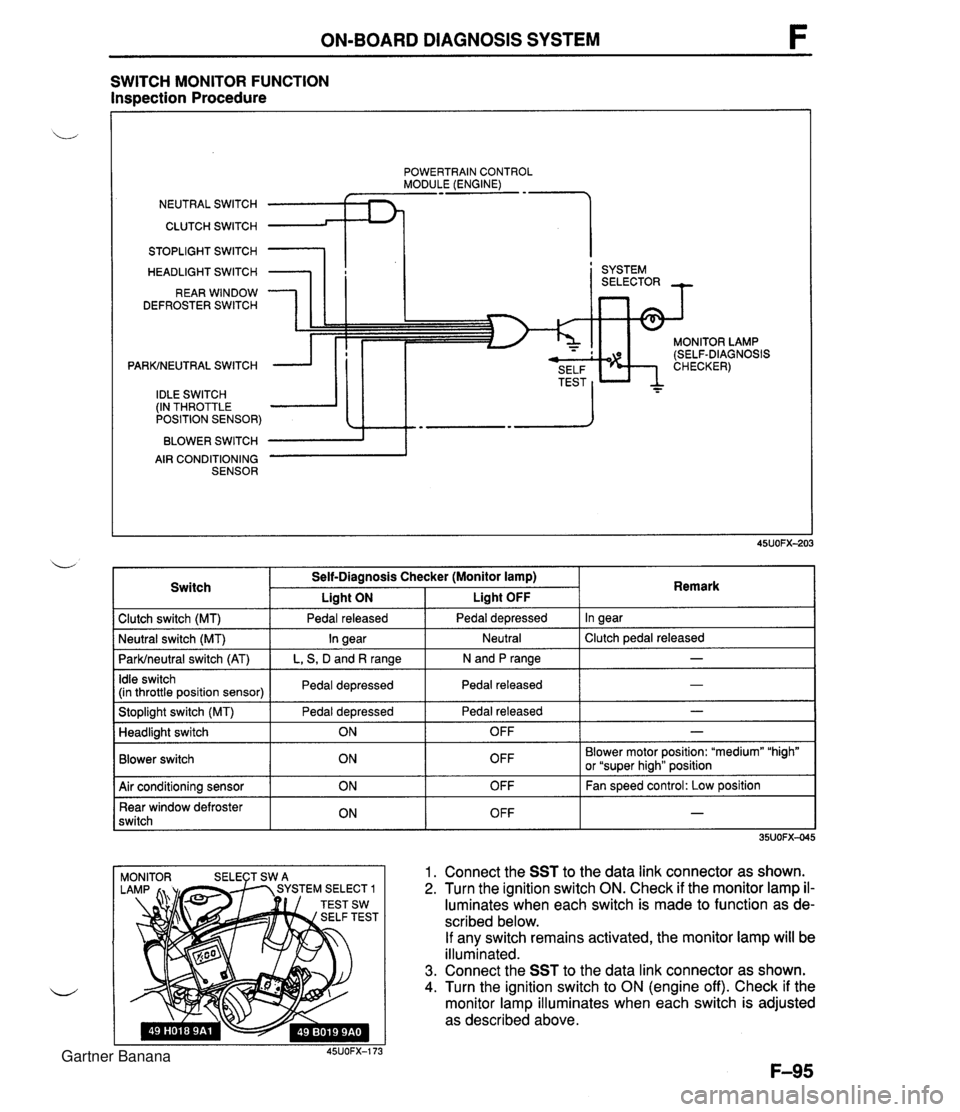
ON-BOARD DIAGNOSIS SYSTEM SWITCH MONITOR FUNCTION Inspection Procedure POWERTRAIN CONTROL MODULE (ENGINE) NEUTRAL SWITCH CLUTCH SWITCH 1 STOPLIGHT SWITCH HEADLIGHT SWITCH REAR WINDOW DEFROSTER SWITCH PARKINEUTRAL SWITCH IDLE SWITCH (IN THROTTLE POSITION SENSOR) BLOWER SWITCH AIR CONDITIONING SENSOR I ' SYSTEM MONITOR LAMP (SELF-DIAGNOSIS 1 Clutch switch (MT) 1 Pedal released I Pedal depressed I In gear I Switch Self-Diagnosis Checker (Monitor lamp) I Liaht ON Liaht OFF . . I I I - I Idle switch (in throttle position sensor) I Pedal depressed I Pedal released 1 Remark ParWneutral switch (AT) I L, S, D and R range I N and P range I I I Stoplight switch (MT) Pedal depressed I Pedal released - I Neutral I Clutch pedal released Neutral switch (MT) - In gear I I Blower switch Headlight switch OFF Blower motor position: "medium" "high" or "super hiah" position I I ON 1. Connect the SST to the data link connector as shown. 2. Turn the ignition switch ON. Check if the monitor lamp il- luminates when each switch is made to function as de- scribed below. If any switch remains activated, the monitor lamp will be illuminated. 3. Connect the SST to the data link connector as shown. 4. Turn the ignition switch to ON (engine off). Check if the monitor lamp illuminates when each switch is adjusted as described above. 45UOFX-173 OFF 1 Air conditioning sensor Rear window defroster switch - ON ON OFF OFF Fan speed control: Low position - Gartner Banana
Page 247 of 1708
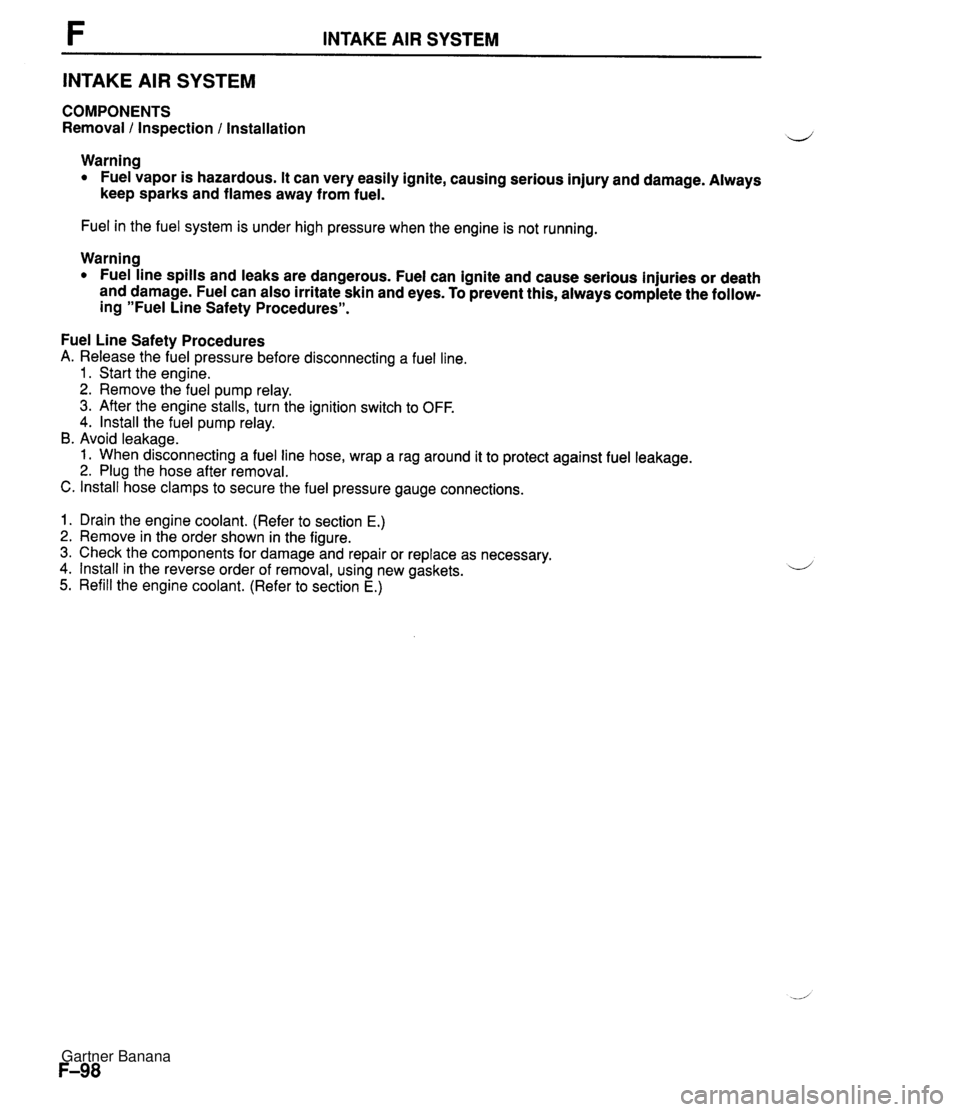
INTAKE AIR SYSTEM INTAKE AIR SYSTEM COMPONENTS Removal 1 Inspection l Installation Warning Fuel vapor is hazardous. It can very easily ignite, causing serious injury and damage. Always keep sparks and flames away from fuel. Fuel in the fuel system is under high pressure when the engine is not running. Warning Fuel line spills and leaks are dangerous. Fuel can ignite and cause serious injuries or death and damage. Fuel can also irritate skin and eyes. To prevent this, always complete the follow- ing "Fuel Line Safety Procedures". Fuel Line Safety Procedures A. Release the fuel pressure before disconnecting a fuel line. 1. Start the engine. 2. Remove the fuel pump relay. 3. After the engine stalls, turn the ignition switch to OFF. 4. lnstall the fuel pump relay. B. Avoid leakage. 1. When disconnecting a fuel line hose, wrap a rag around it to protect against fuel leakage. 2. Plug the hose after removal. C. lnstall hose clamps to secure the fuel pressure gauge connections. 1. Drain the engine coolant. (Refer to section E.) 2. Remove in the order shown in the figure. 3. Check the components for damage and repair or replace as necessary. 4. lnstall in the reverse order of removal, using new gaskets. 5. Refill the engine coolant. (Refer to section E.) Gartner Banana
Page 257 of 1708
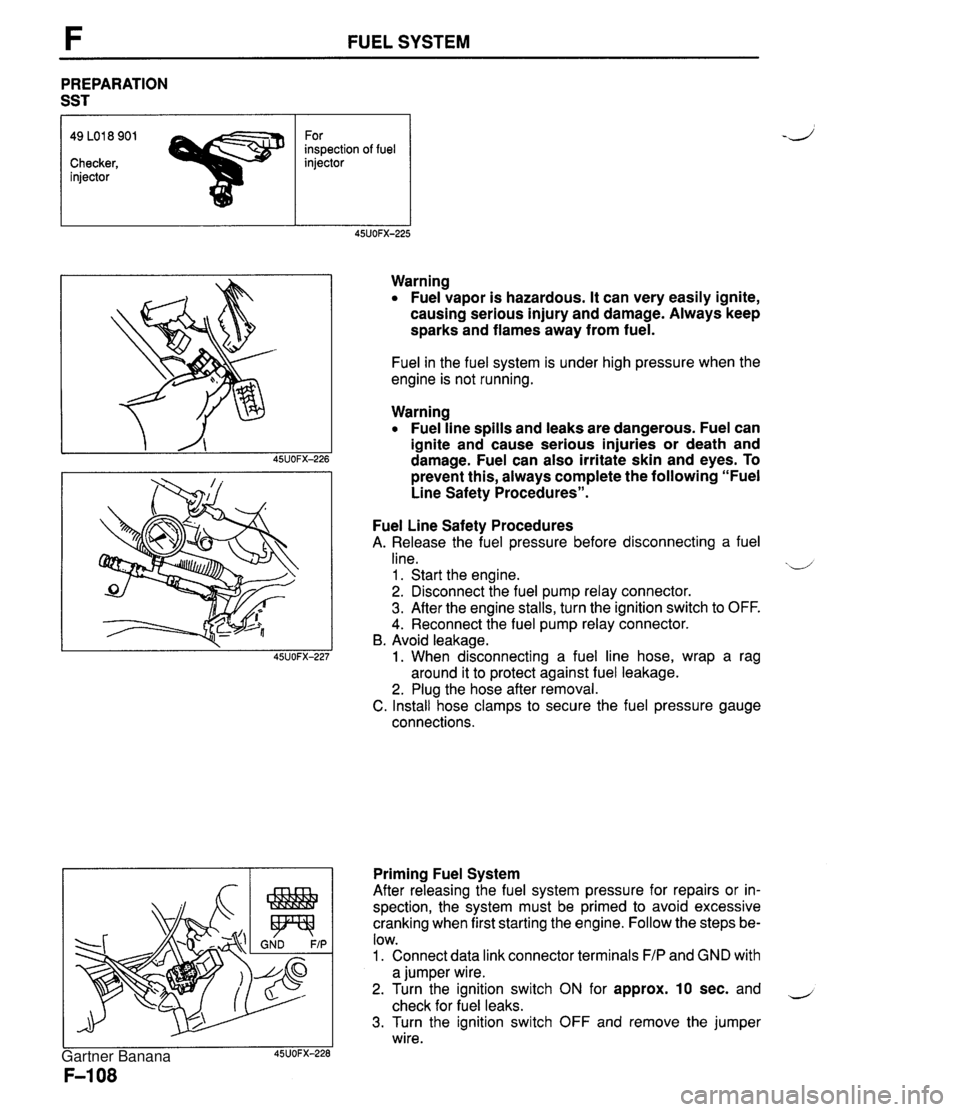
FUEL SYSTEM PREPARATION SST 49 LO1 8 901 For inspection of fuel Checker, injector injector Warning Fuel vapor is hazardous. It can very easily ignite, causing serious injury and damage. Always keep sparks and flames away from fuel. Fuel in the fuel system is under high pressure when the engine is not running. Warning Fuel line spills and leaks are dangerous. Fuel can ignite and cause serious injuries or death and damage. Fuel can also irritate skin and eyes. To prevent this, always complete the following "Fuel Line Safety Procedures". Fuel Line Safety Procedures A. Release the fuel pressure before disconnecting a fuel line. xd 1 . Start the engine. 2. Disconnect the fuel pump relay connector. 3. After the engine stalls, turn the ignition switch to OFF. 4. Reconnect the fuel pump relay connector. B. Avoid leakage. 1. When disconnecting a fuel line hose, wrap a rag around it to protect against fuel leakage. 2. Plug the hose after removal. C. Install hose clamps to secure the fuel pressure gauge connections. Priming Fuel System After releasing the fuel system pressure for repairs or in- spection, the system must be primed to avoid excessive cranking when first starting the engine. Follow the steps be- low. 1. Connect data link connector terminals F/P and GND with a jumper wire. 2. Turn the ignition switch ON for approx. 10 sec. and - check for fuel leaks. 3. Turn the ignition switch OFF and remove the jumper wire. Gartner Banana
Page 258 of 1708
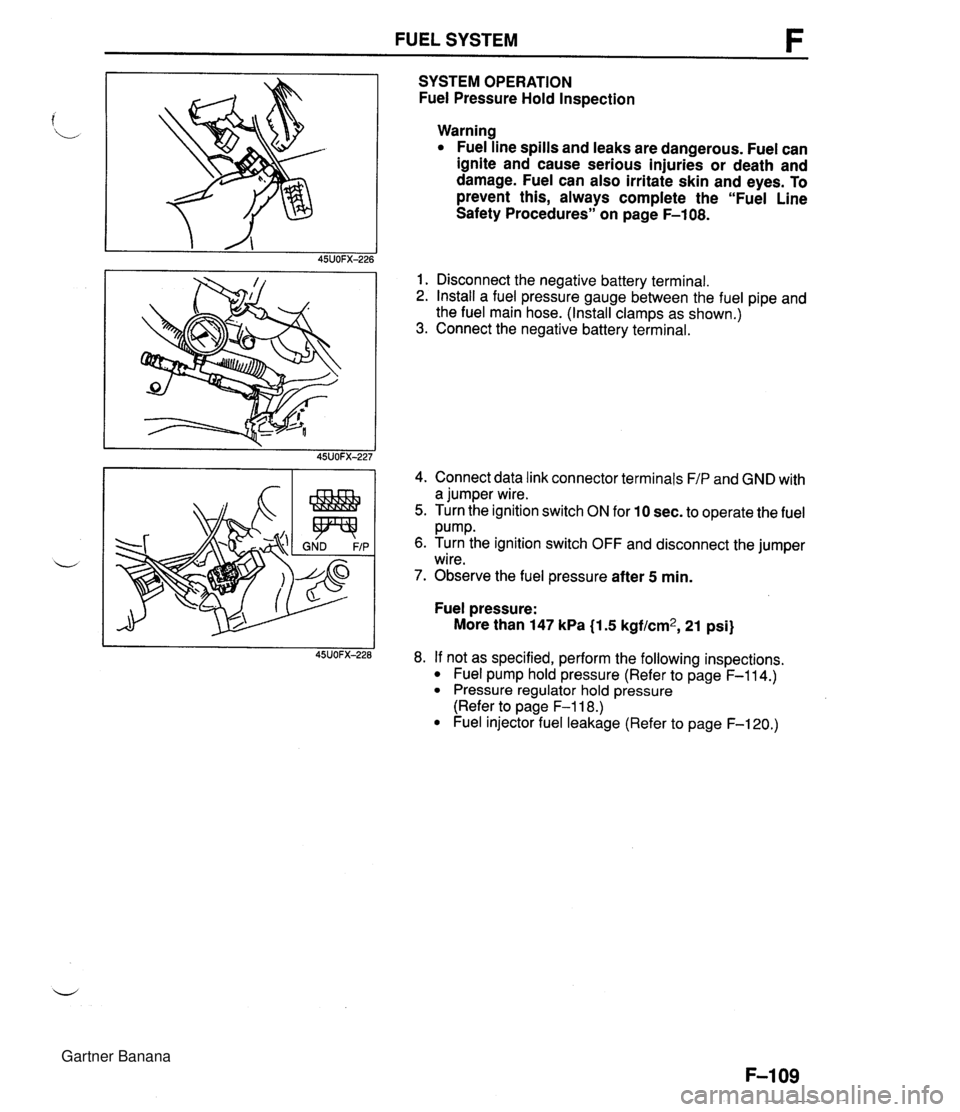
FUEL SYSTEM SYSTEM OPERATION Fuel Pressure Hold Inspection Warning Fuel line spills and leaks are dangerous. Fuel can ignite and cause serious injuries or death and damage. Fuel can also irritate skin and eyes. To prevent this, always complete the "Fuel Line Safety Procedures" on page F-108. 1. Disconnect the negative battery terminal. 2. Install a fuel pressure gauge between the fuel pipe and the fuel main hose. (Install clamps as shown.) 3. Connect the negative battery terminal. 4. Connect data link connector terminals F/P and GND with a jumper wire. 5. Turn the ignition switch ON for 10 sec. to operate the fuel Pump. 6. Turn the ignition switch OFF and disconnect the jumper wire. 7. Observe the fuel pressure after 5 min. Fuel pressure: More than 147 kPa (1.5 kgf/cm2, 21 psi) 8. If not as specified, perform the following inspections. Fuel pump hold pressure (Refer to page F-114.) Pressure regulator hold pressure (Refer to page F-118.) Fuel injector fuel leakage (Refer to page F-120.) Gartner Banana
Page 259 of 1708
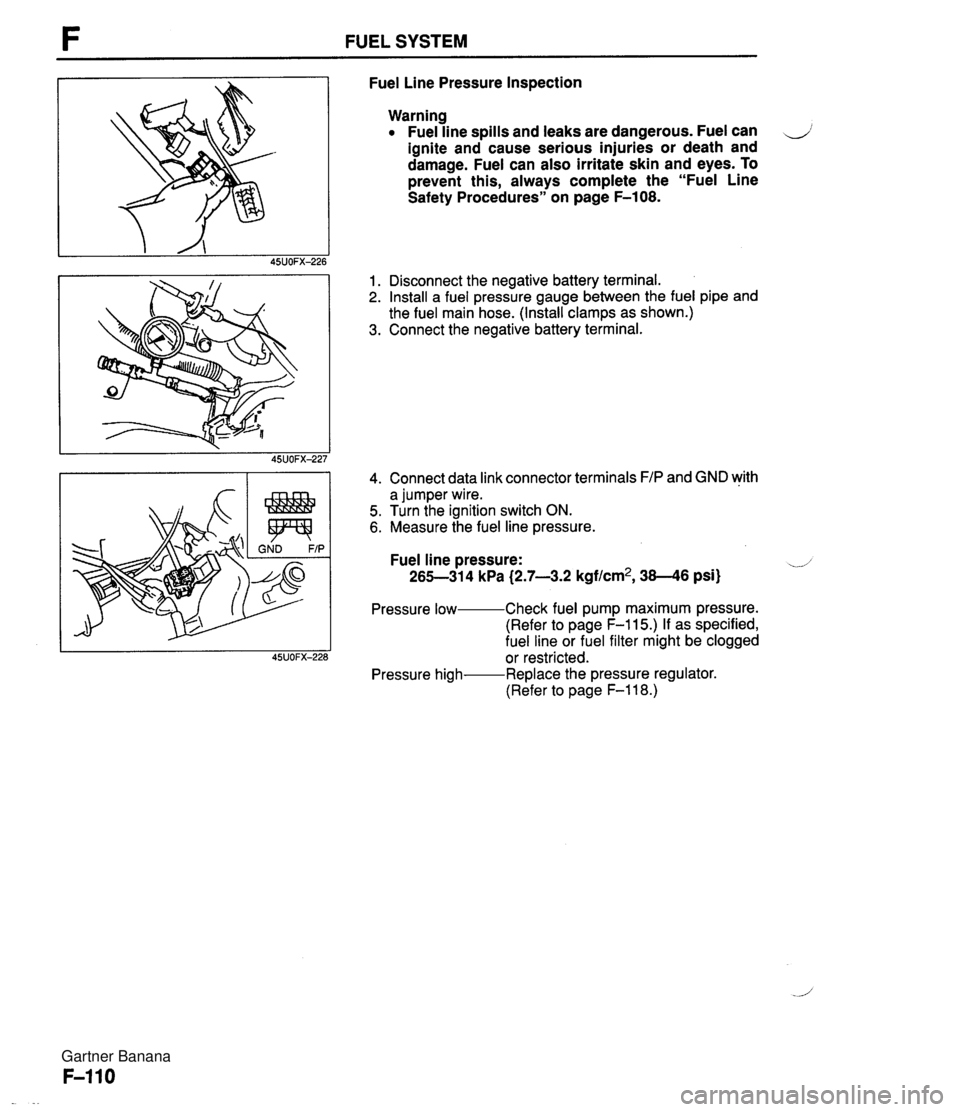
FUEL SYSTEM Fuel Line Pressure Inspection Warning Fuel line spills and leaks are dangerous. Fuel can ignite and cause serious injuries or death and damage. Fuel can also irritate skin and eyes. To prevent this, always complete the "Fuel Line Safety Procedures" on page F-108. 1. Disconnect the negative battery terminal. 2. Install a fuel pressure gauge between the fuel pipe and the fuel main hose. (Install clamps as shown.) 3. Connect the negative battery terminal. 4. Connect data link connector terminals F/P and GND with a jumper wire. 5. Turn the ignition switch ON. 6. Measure the fuel line pressure. Fuel line pressure: 265-31 4 kPa {2.7-3.2 kgf/cm2, 38-46 psi) Pressure low- Check fuel pump maximum pressure. (Refer to page F-115.) If as specified, fuel line or fuel filter might be clogged or restricted. Pressure high- Replace the pressure regulator. (Refer to page F-118.) Gartner Banana