torque MITSUBISHI ECLIPSE 1991 Service Manual
[x] Cancel search | Manufacturer: MITSUBISHI, Model Year: 1991, Model line: ECLIPSE, Model: MITSUBISHI ECLIPSE 1991Pages: 1216, PDF Size: 67.42 MB
Page 914 of 1216
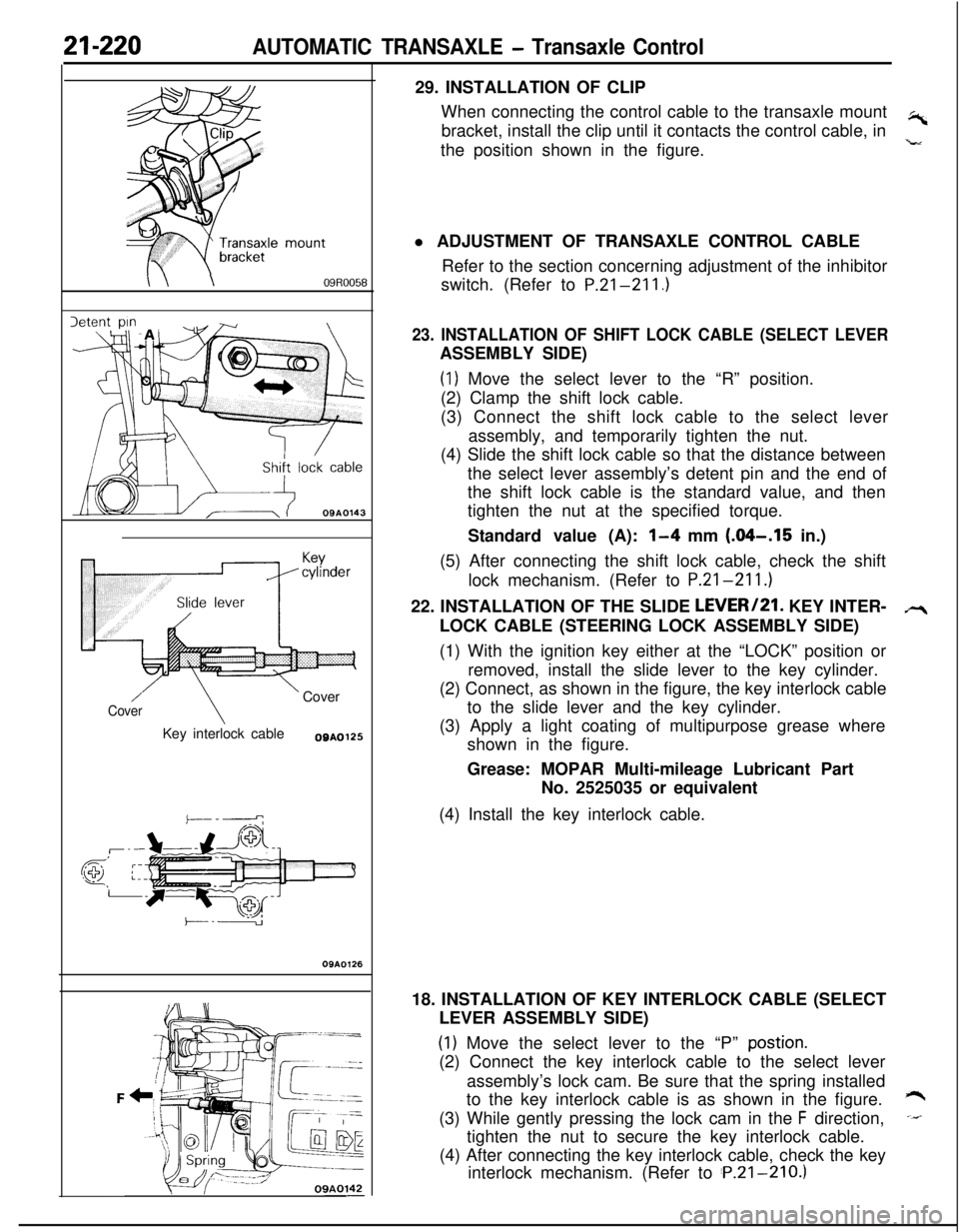
AUTOMATIC TRANSAXLE - Transaxle Control
:lemotJnt
\\ \09R0058
09AO143
/’
\
’ CoverCoverKey interlock cableOSA0125
OSAO12629. INSTALLATION OF CLIP
When connecting the control cable to the transaxle mount
,-bracket, install the clip until it contacts the control cable, in
the position shown in the figure.
,”l ADJUSTMENT OF TRANSAXLE CONTROL CABLE
Refer to the section concerning adjustment of the inhibitor
switch. (Refer to P.21-211.)
23. INSTALLATION OF SHIFT LOCK CABLE (SELECT LEVERASSEMBLY SIDE)
(1) Move the select lever to the “R” position.
(2) Clamp the shift lock cable.
(3) Connect the shift lock cable to the select lever
assembly, and temporarily tighten the nut.
(4) Slide the shift lock cable so that the distance between
the select lever assembly’s detent pin and the end of
the shift lock cable is the standard value, and then
tighten the nut at the specified torque.
Standard value (A):
l-4 mm (.04-.I5 in.)
(5) After connecting the shift lock cable, check the shift
lock mechanism. (Refer to P.21-211.)
22. INSTALLATION OF THE SLIDE LEVERI21. KEY INTER-
LOCK CABLE (STEERING LOCK ASSEMBLY SIDE)
(1) With the ignition key either at the “LOCK” position or
removed, install the slide lever to the key cylinder.
(2) Connect, as shown in the figure, the key interlock cable
to the slide lever and the key cylinder.
(3) Apply a light coating of multipurpose grease where
shown in the figure.
Grease: MOPAR Multi-mileage Lubricant Part
No. 2525035 or equivalent
(4) Install the key interlock cable.
18. INSTALLATION OF KEY INTERLOCK CABLE (SELECT
LEVER ASSEMBLY SIDE)
(1) Move the select lever to the “P” postion.(2) Connect the key interlock cable to the select lever
assembly’s lock cam. Be sure that the spring installed
to the key interlock cable is as shown in the figure.
*(3) While gently pressing the lock cam in the
F direction,-tighten the nut to secure the key interlock cable.
(4) After connecting the key interlock cable, check the key
interlock mechanism. (Refer to ‘P.21-210.)
Page 921 of 1216
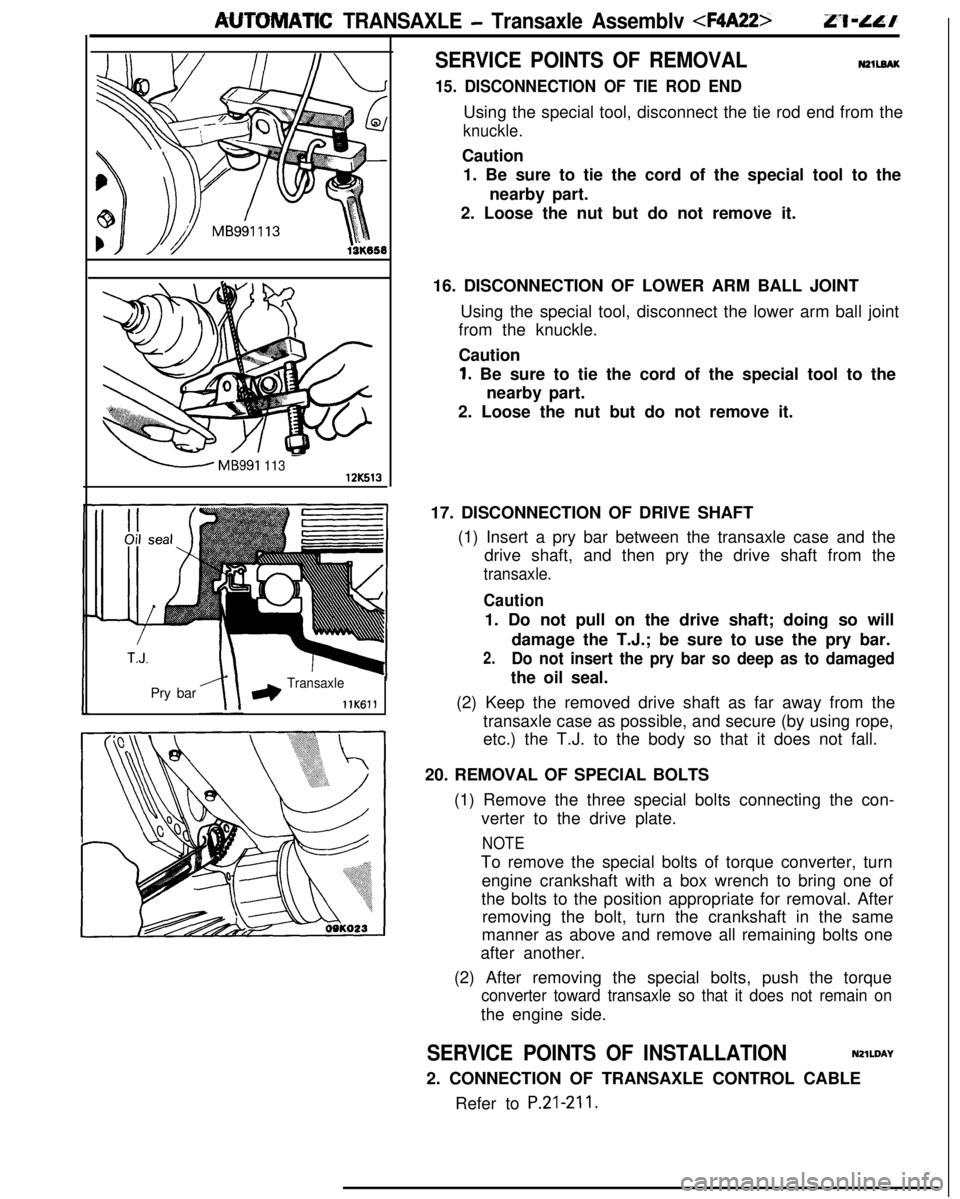
AUTOMATIC TRANSAXLE - Transaxle Assemblv
-MB991 11312K513Pry bar
*Transaxle
llK611
SERVICE POINTS OF REMOVALN2llEAK
15. DISCONNECTION OF TIE ROD ENDUsing the special tool, disconnect the tie rod end from the
knuckle.Caution
1. Be sure to tie the cord of the special tool to the
nearby part.
2. Loose the nut but do not remove it.
16. DISCONNECTION OF LOWER ARM BALL JOINT
Using the special tool, disconnect the lower arm ball joint
from the knuckle.
Caution
1. Be sure to tie the cord of the special tool to the
nearby part.
2. Loose the nut but do not remove it.
17. DISCONNECTION OF DRIVE SHAFT
(1) Insert a pry bar between the transaxle case and the
drive shaft, and then pry the drive shaft from the
transaxle.
Caution1. Do not pull on the drive shaft; doing so will
damage the T.J.; be sure to use the pry bar.
2.Do not insert the pry bar so deep as to damagedthe oil seal.
(2) Keep the removed drive shaft as far away from the
transaxle case as possible, and secure (by using rope,
etc.) the T.J. to the body so that it does not fall.
20. REMOVAL OF SPECIAL BOLTS
(1) Remove the three special bolts connecting the con-
verter to the drive plate.
NOTETo remove the special bolts of torque converter, turn
engine crankshaft with a box wrench to bring one of
the bolts to the position appropriate for removal. After
removing the bolt, turn the crankshaft in the same
manner as above and remove all remaining bolts one
after another.
(2) After removing the special bolts, push the torque
converter toward transaxle so that it does not remain onthe engine side.
SERVICE POINTS OF INSTALLATIONN2lWAY
2. CONNECTION OF TRANSAXLE CONTROL CABLE
Refer to
P.21-211.
Page 922 of 1216
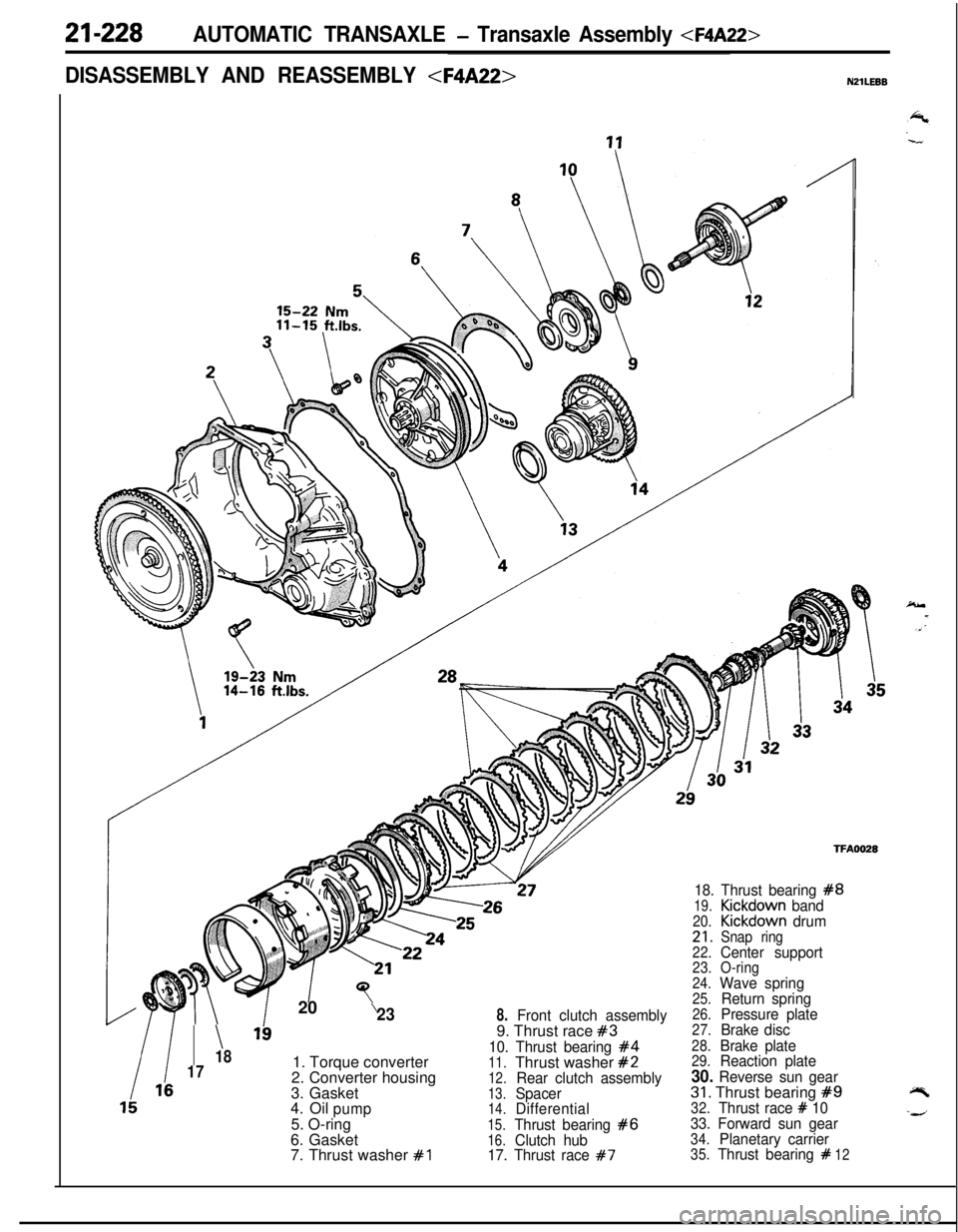
21-228AUTOMATIC TRANSAXLE - Transaxle Assembly
DISASSEMBLY AND REASSEMBLY
\18
1720
\231. Torque converter
2. Converter housing
3. Gasket
4. Oil
pump5. O-ring
6. Gasket
7. Thrust washer
#l
8.Front clutch assembly9. Thrust race #3
10. Thrust bearing #411.Thrust washer #212.Rear clutch assembly13.Spacer14.Differential
15.Thrust bearing #616.Clutch hub
17. Thrust race #7
18. Thrust bearing #819.Kickdown band20.Kickdown drum21.Snap ring
22.Center support23.O-ring
24.Wave spring25.Return spring26.Pressure plate27.Brake disc
28.Brake plate29.Reaction plate
30. Reverse sun gear31. Thrust bearing #932.Thrust race # 10
33. Forward sun gear
34.Planetary carrier35.Thrust bearing #12
Page 924 of 1216
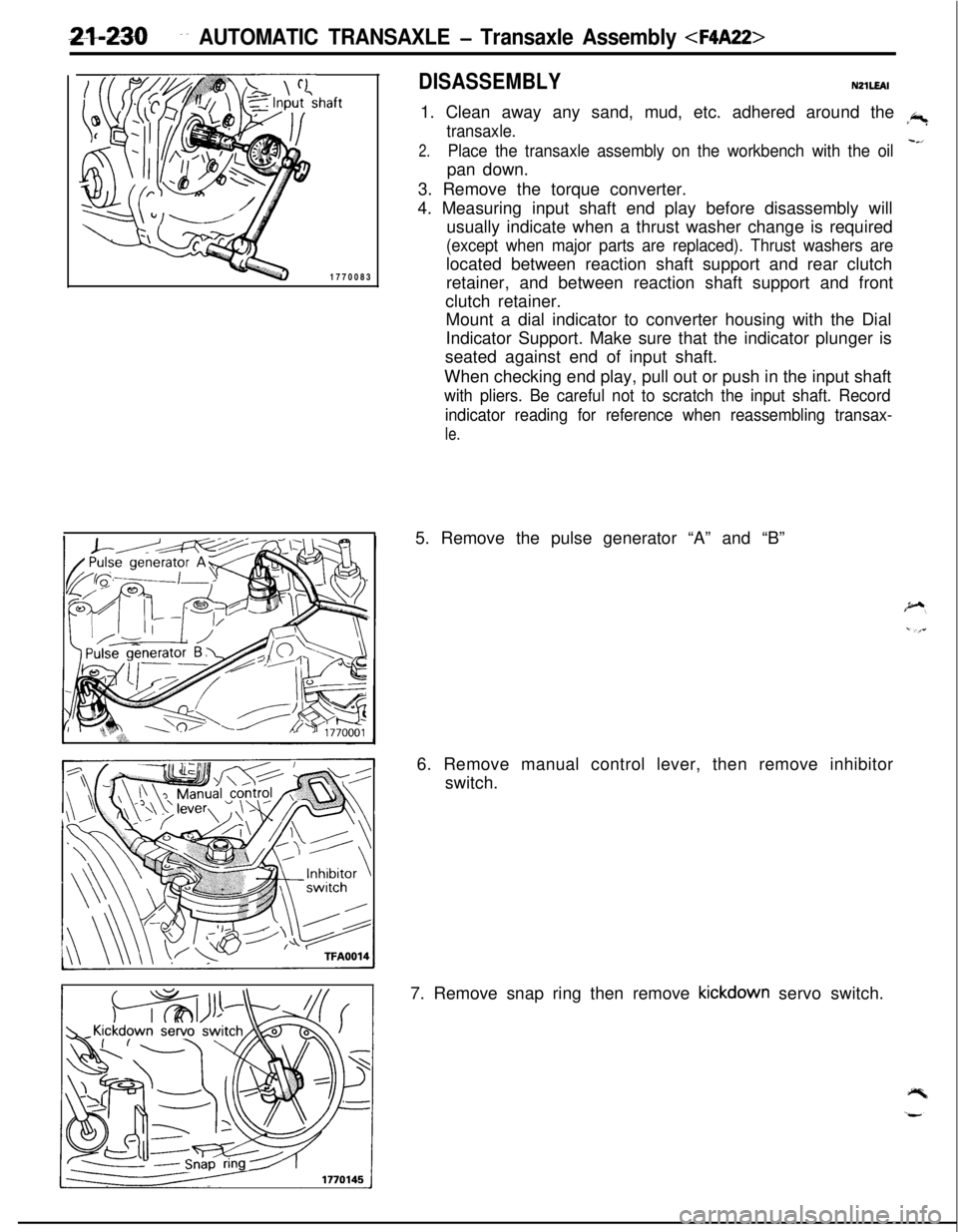
-2.rt-2-30~~ AUTOMATIC TRANSAXLE - Transaxle Assembly
;haft1770083
DISASSEMBLYNZlLEAl1. Clean away any sand, mud, etc. adhered around the
.+
transaxle..
2.
Place the transaxle assembly on the workbench with the oil--’
pan down.
3. Remove the torque converter.
4. Measuring input shaft end play before disassembly will
usually indicate when a thrust washer change is required
(except when major parts are replaced). Thrust washers arelocated between reaction shaft support and rear clutch
retainer, and between reaction shaft support and front
clutch retainer.
Mount a dial indicator to converter housing with the Dial
Indicator Support. Make sure that the indicator plunger is
seated against end of input shaft.
When checking end play, pull out or push in the input shaft
with pliers. Be careful not to scratch the input shaft. Record
indicator reading for reference when reassembling transax-
le.5. Remove the pulse generator “A” and “B”
6. Remove manual control lever, then remove inhibitor
switch.
7. Remove snap ring then remove
kickdown servo switch.
Page 938 of 1216
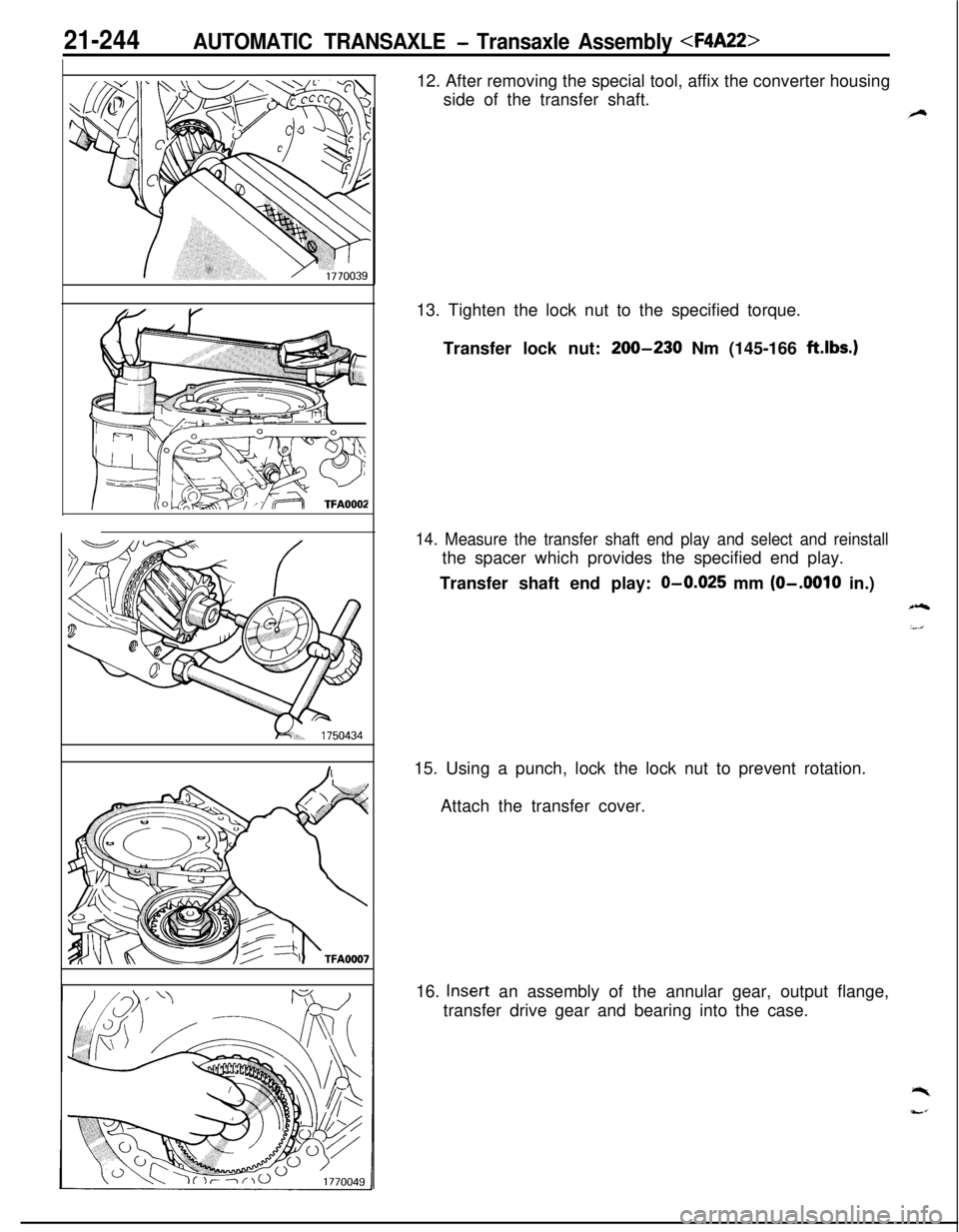
21-244AUTOMATIC TRANSAXLE - Transaxle Assembly
side of the transfer shaft.
P-13. Tighten the lock nut to the specified torque.
Transfer lock nut:
200-230 Nm (145-166 ft.lbs.)
14. Measure the transfer shaft end play and select and reinstallthe spacer which provides the specified end play.
Transfer shaft end play: O-0.025 mm (O-.0010 in.)
e15. Using a punch, lock the lock nut to prevent rotation.
Attach the transfer cover.
16.
Insert an assembly of the annular gear, output flange,
transfer drive gear and bearing into the case.
Page 939 of 1216
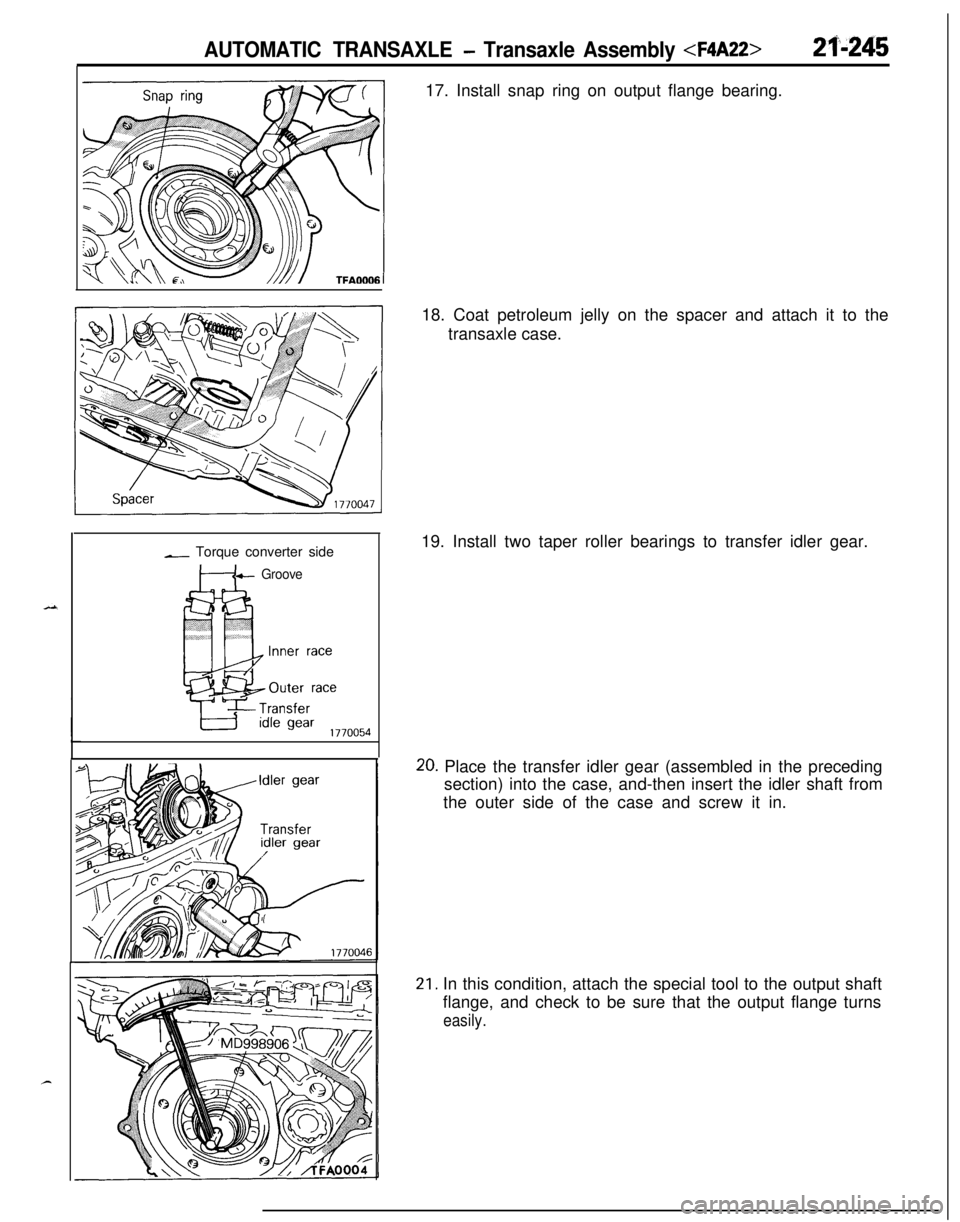
AUTOMATIC TRANSAXLE - Transaxle Assembly
_ Torque converter side
H Groove17. Install snap ring on output flange bearing.
18. Coat petroleum jelly on the spacer and attach it to the
transaxle case.
19. Install two taper roller bearings to transfer idler gear.
20. Place the transfer idler gear (assembled in the preceding
section) into the case, and-then insert the idler shaft from
the outer side of the case and screw it in.
21. In this condition, attach the special tool to the output shaft
flange, and check to be sure that the output flange turns
easily.
Page 940 of 1216
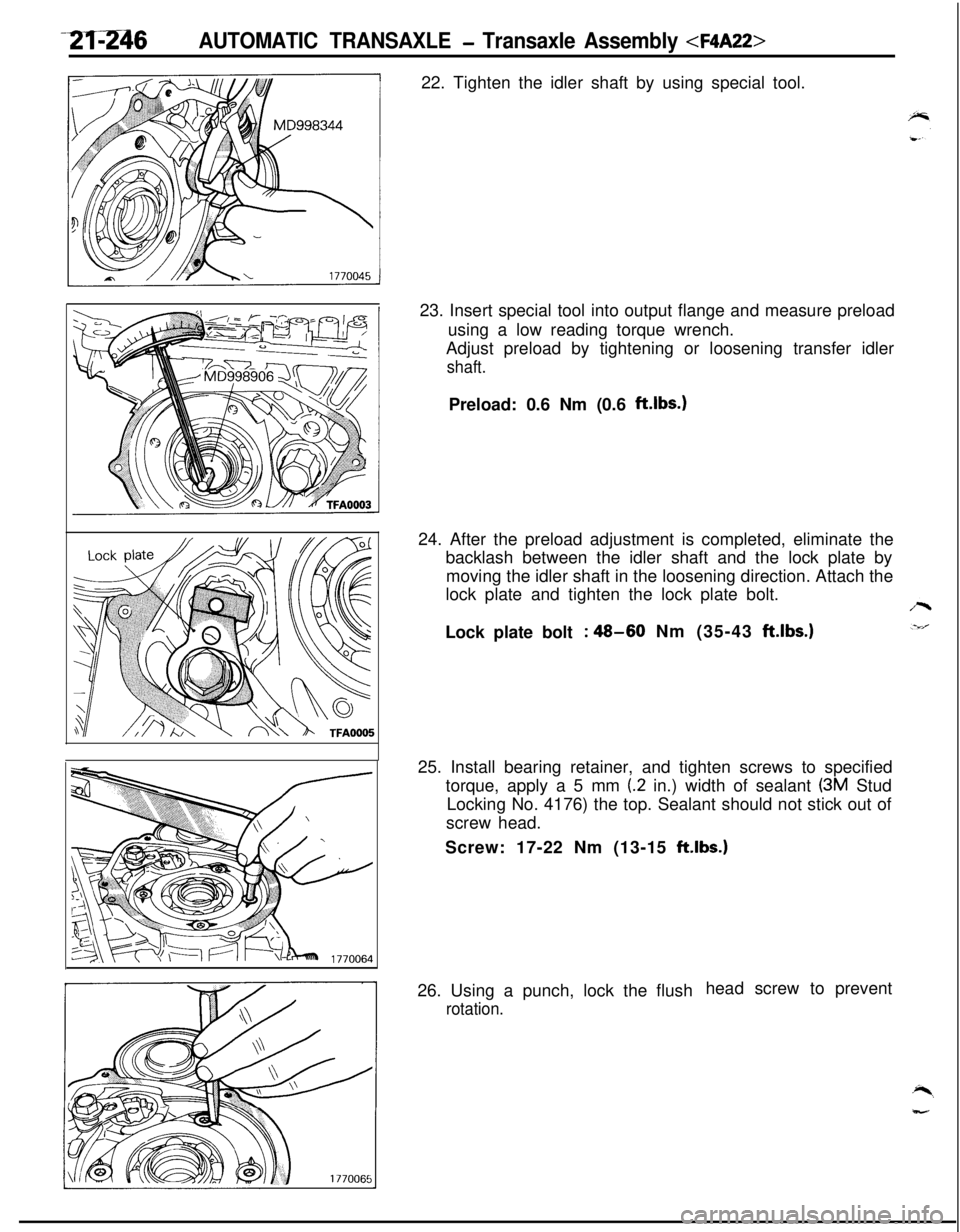
-T1;;z2)6AUTOMATIC TRANSAXLE - Transaxle Assembly
23. Insert special tool into output flange and measure preload
using a low reading torque wrench.
Adjust preload by tightening or loosening transfer idler
shaft.Preload: 0.6 Nm (0.6
ft.lbs.)24. After the preload adjustment is completed, eliminate the
backlash between the idler shaft and the lock plate by
moving the idler shaft in the loosening direction. Attach the
lock plate and tighten the lock plate bolt.
Lock plate bolt
: 48-60 Nm (35-43 ft.lbs.)25. Install bearing retainer, and tighten screws to specified
torque, apply a 5 mm
(.2 in.) width of sealant (3M Stud
Locking No. 4176) the top. Sealant should not stick out of
screw head.
Screw: 17-22 Nm (13-15
ft.lbs.)head screw to prevent
26. Using a punch, lock the flush
rotation.
Page 952 of 1216
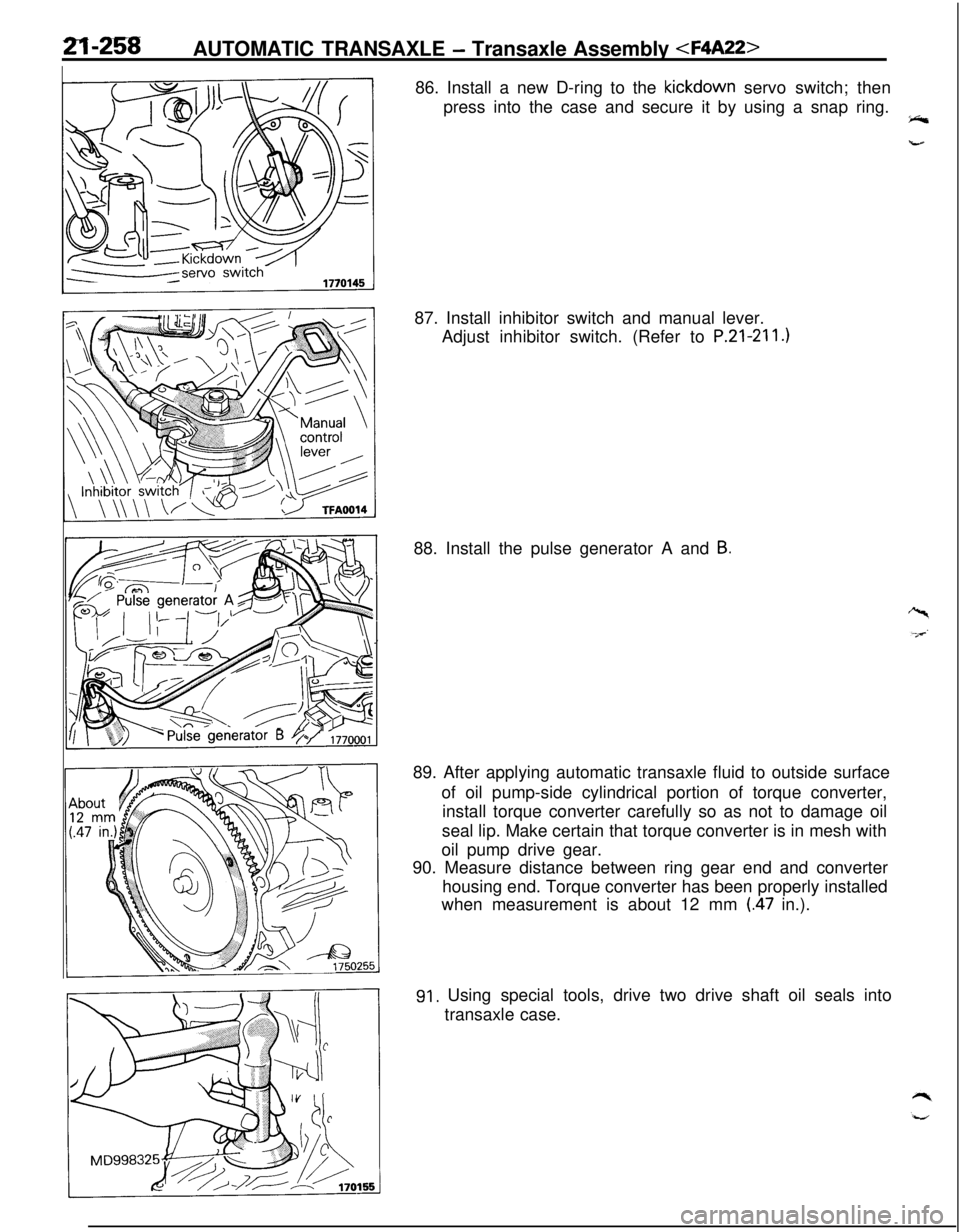
AUTOMATIC TRANSAXLE - Transaxle Assembly
press into the case and secure it by using a snap ring.
87. Install inhibitor switch and manual lever.
Adjust inhibitor switch. (Refer to
P.21-211.)88. Install the pulse generator A and
B.89. After applying automatic transaxle fluid to outside surface
of oil pump-side cylindrical portion of torque converter,
install torque converter carefully so as not to damage oil
seal lip. Make certain that torque converter is in mesh with
oil pump drive gear.
90. Measure distance between ring gear end and converter
housing end. Torque converter has been properly installed
when measurement is about 12 mm
(.47 in.).
91. Using special tools, drive two drive shaft oil seals into
transaxle case.
Page 960 of 1216
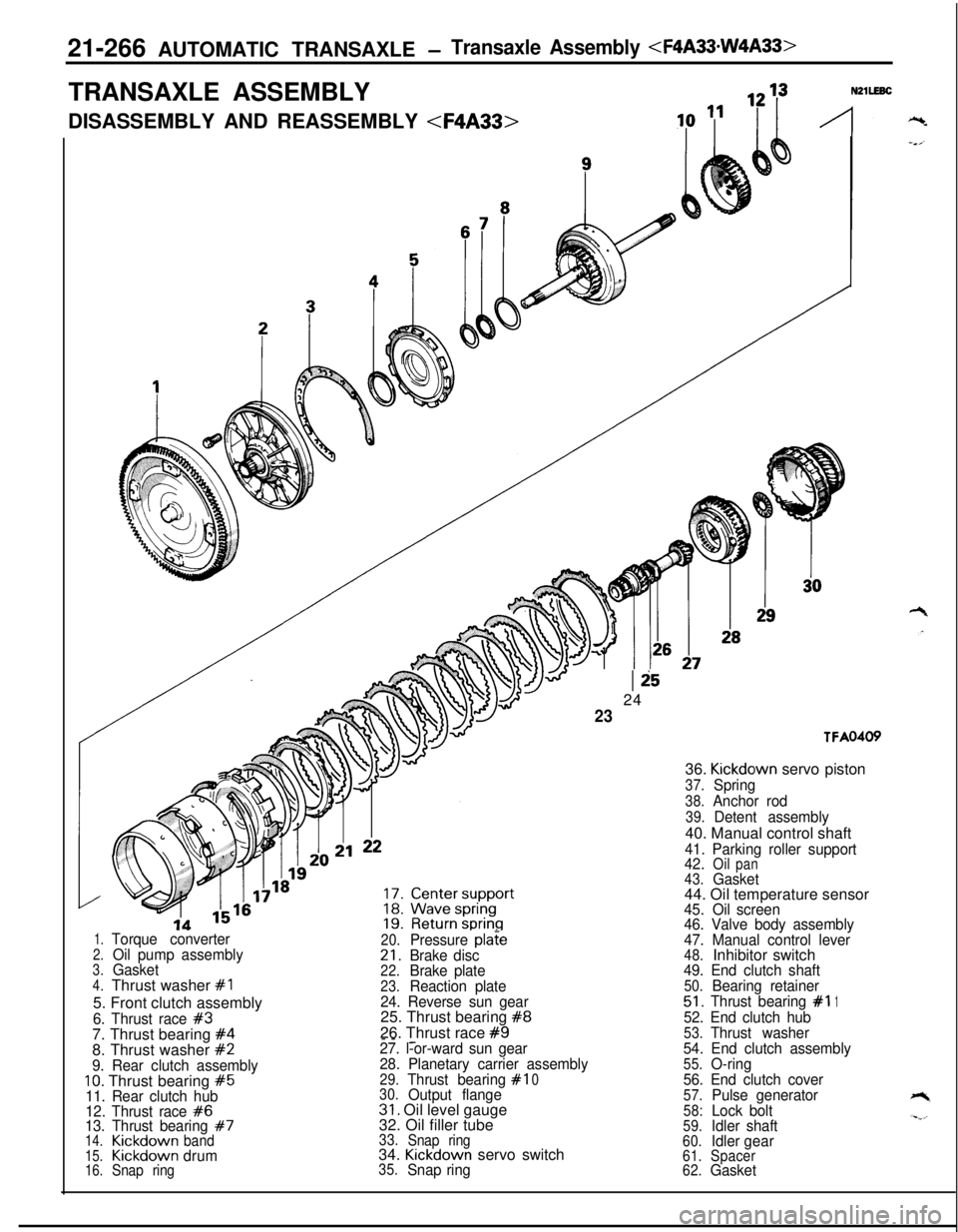
21-266 AUTOMATIC TRANSAXLE -Transaxle Assembly
DISASSEMBLY AND REASSEMBLY
20.Pressure pla?e21.Brake disc22.Brake plate23.Reaction plate
24. Reverse sun gear25. Thrust bearing
#826. Thrust race
#9---
1.Torque converter2.Oil pump assembly3.Gasket4.Thrust washer #I5. Front clutch assembly
6. Thrust race #37. Thrust bearing #48. Thrust washer #227. l-or-ward sun gear
9. Rear clutch assembly28. Planetary carrier assembly
10. Thrust bearing #529.Thrust bearing#I0
11. Rear clutch hub30.Output flange
12. Thrust race
#631. Oil level gauge
13. Thrust bearing #732. Oil filler tube14.Kickdownband33.
Snap ring15.Kickdowndrum34. Kickdown servo switch16.Snap ring35.Snap ring
Ii524
23
TFA0405’36.
Kickdown servo piston
37.Spring
38.Anchor rod
39.Detent assembly40. Manual control shaft
41. Parking roller support
42.Oilpan43.Gasket44. Oil temperature sensor
45.Oil screen
46. Valve body assembly
47. Manual control lever
48.Inhibitor switch49. End clutch shaft50.Bearing retainer51.Thrust bearing #I152. End clutch hub53.Thrust washer
54. End clutch assembly
55.O-ring
56. End clutch cover
57.Pulse generator58:Lock bolt59.Idler shaft60.Idlergear61.Spacer
62.Gasket
Page 962 of 1216
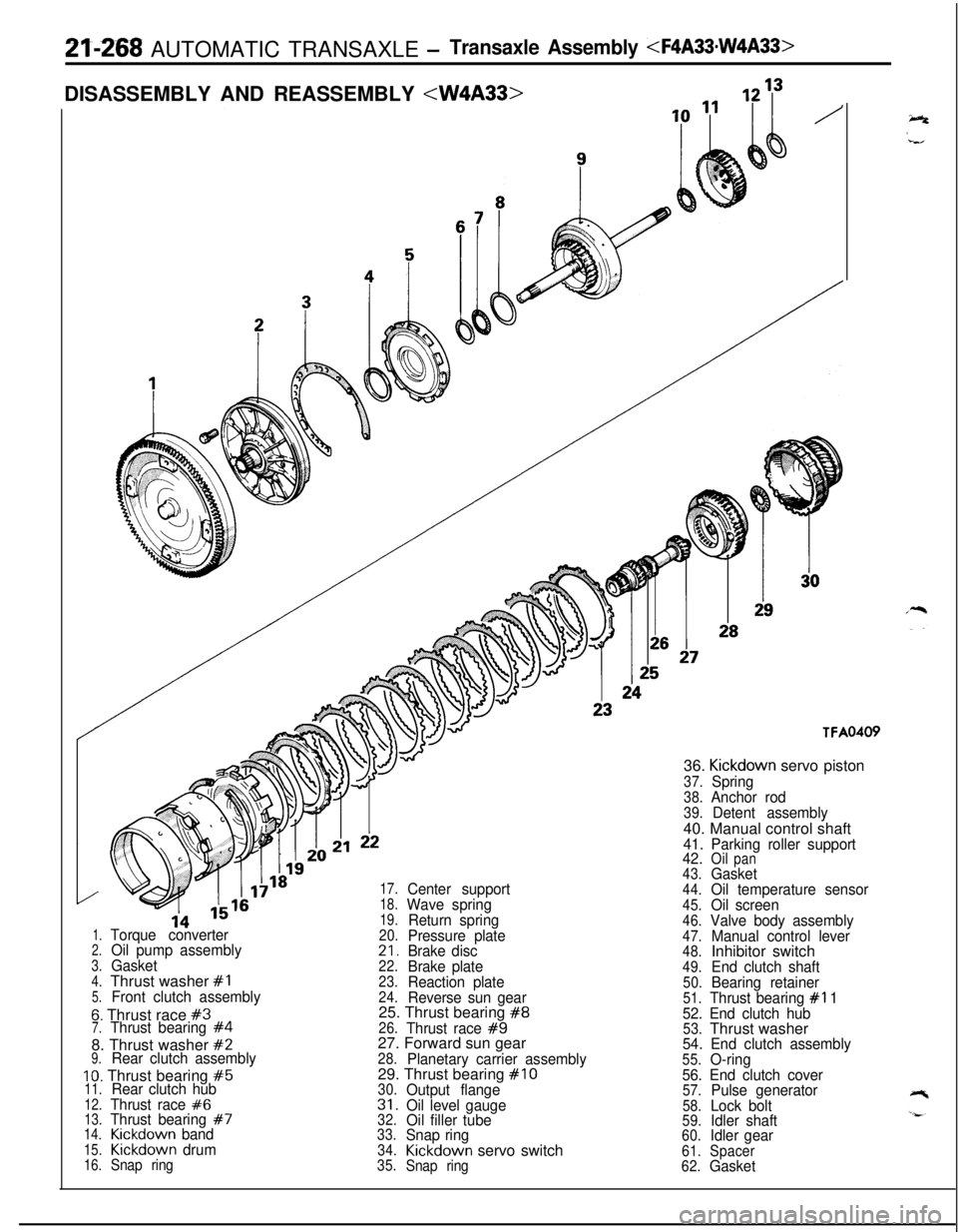
21-268 AUTOMATIC TRANSAXLE -Transaxle Assembly
TFA0409
1.Torque converter2.Oil pump assembly3.Gasket4.Thrust washer #I5.Front clutch assembly
6. Thrust race #37.Thrust bearing #48. Thrust washer
#29.Rear clutch assembly
10. Thrust bearing #511.Rear clutch hub12.Thrust race #613.Thrust bearing #714.Kickdown band15.Kickdown drum16.Snap ring
17.Center support18.Wave spring19.Return spring20.Pressure plate21.Brake disc22.Brake plate23.Reaction plate24.Reverse sun gear25. Thrust bearing #826.Thrust race #927. Forward sun gear
28.Planetary carrier assembly29. Thrust bearing #IO30.Output flange31.Oil level gauge32.Oil filler tube33.Snap ring34.Kickdown servo switch35.
Snap ring36.
Kickdown servo piston
37.Spring38.Anchor rod39.Detent assembly40. Manual control shaft
41. Parking roller support
42.Oilpan43.Gasket44.Oil temperature sensor45.Oil screen46.Valve body assembly47.Manual control lever48.Inhibitor switch49.End clutch shaft50.Bearing retainer51.Thrust bearing #I 1
52. End clutch hub
53.Thrust washer54. End clutch assembly55.O-ring
56. End clutch cover
57.Pulse generator58.Lock bolt59.Idler shaft60.Idler gear61.Spacer
62.Gasket