torque MITSUBISHI ECLIPSE 1991 Owner's Manual
[x] Cancel search | Manufacturer: MITSUBISHI, Model Year: 1991, Model line: ECLIPSE, Model: MITSUBISHI ECLIPSE 1991Pages: 1216, PDF Size: 67.42 MB
Page 123 of 1216
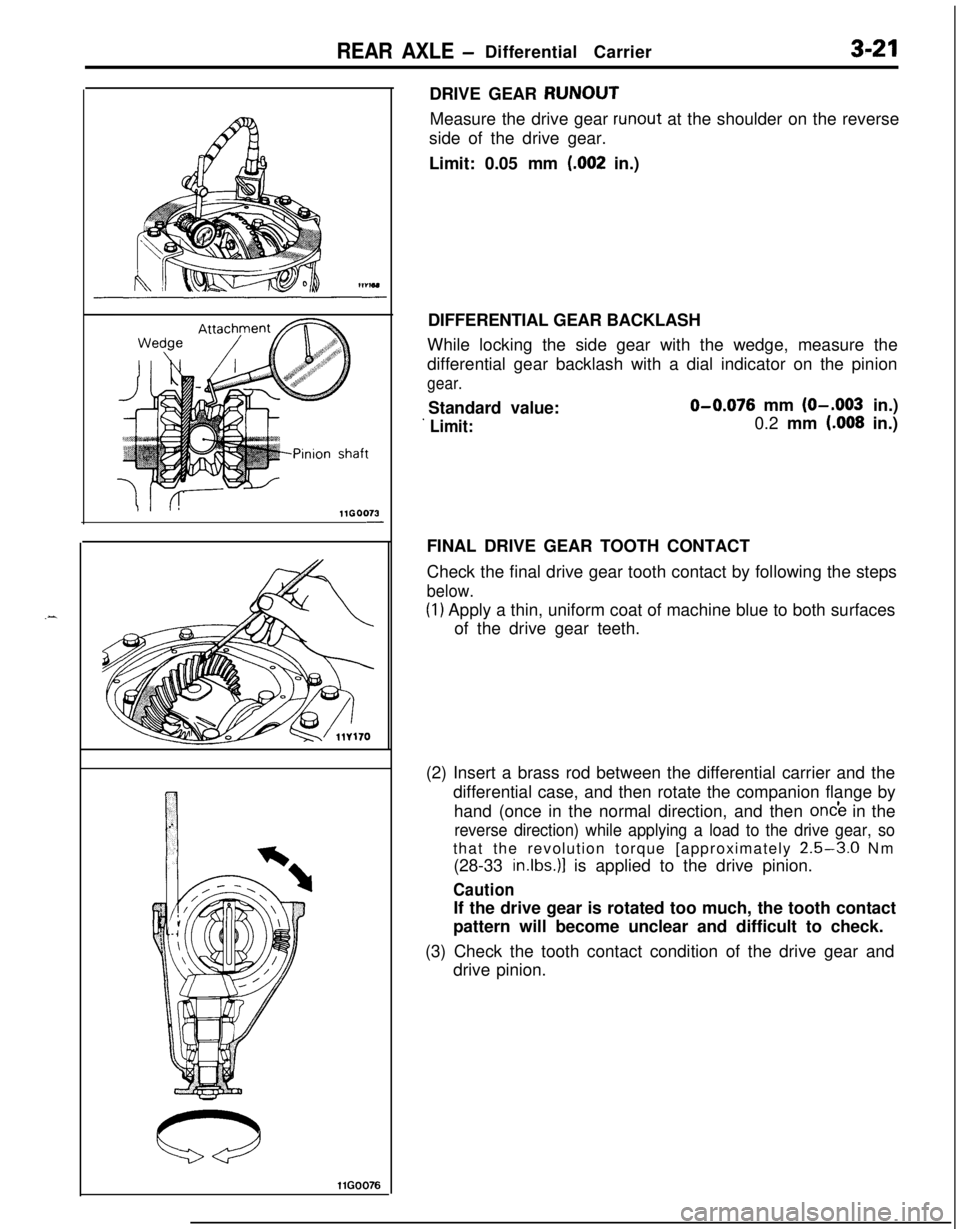
REAR AXLE -Differential Carrier3-21
.-11GOO73
-
llG0076DRIVE GEAR RUNOUT
Measure the drive gear
runout at the shoulder on the reverse
side of the drive gear.
Limit: 0.05 mm
(.002 in.)
DIFFERENTIAL GEAR BACKLASH
While locking the side gear with the wedge, measure the
differential gear backlash with a dial indicator on the pinion
gear.Standard value:O-0.076 mm (O-.003 in.)
’ Limit:0.2 mm (.008 in.)
FINAL DRIVE GEAR TOOTH CONTACT
Check the final drive gear tooth contact by following the steps
below.
(1) Apply a thin, uniform coat of machine blue to both surfaces
of the drive gear teeth.
(2) Insert a brass rod between the differential carrier and the
differential case, and then rotate the companion flange by
hand (once in the normal direction, and then
on& in the
reverse direction) while applying a load to the drive gear, sothat the revolution torque [approximately
2.5-3.0 Nm
(28-33
in.lbs.)] is applied to the drive pinion.
CautionIf the drive gear is rotated too much, the tooth contact
pattern will become unclear and difficult to check.
(3) Check the tooth contact condition of the drive gear and
drive pinion.
Page 128 of 1216
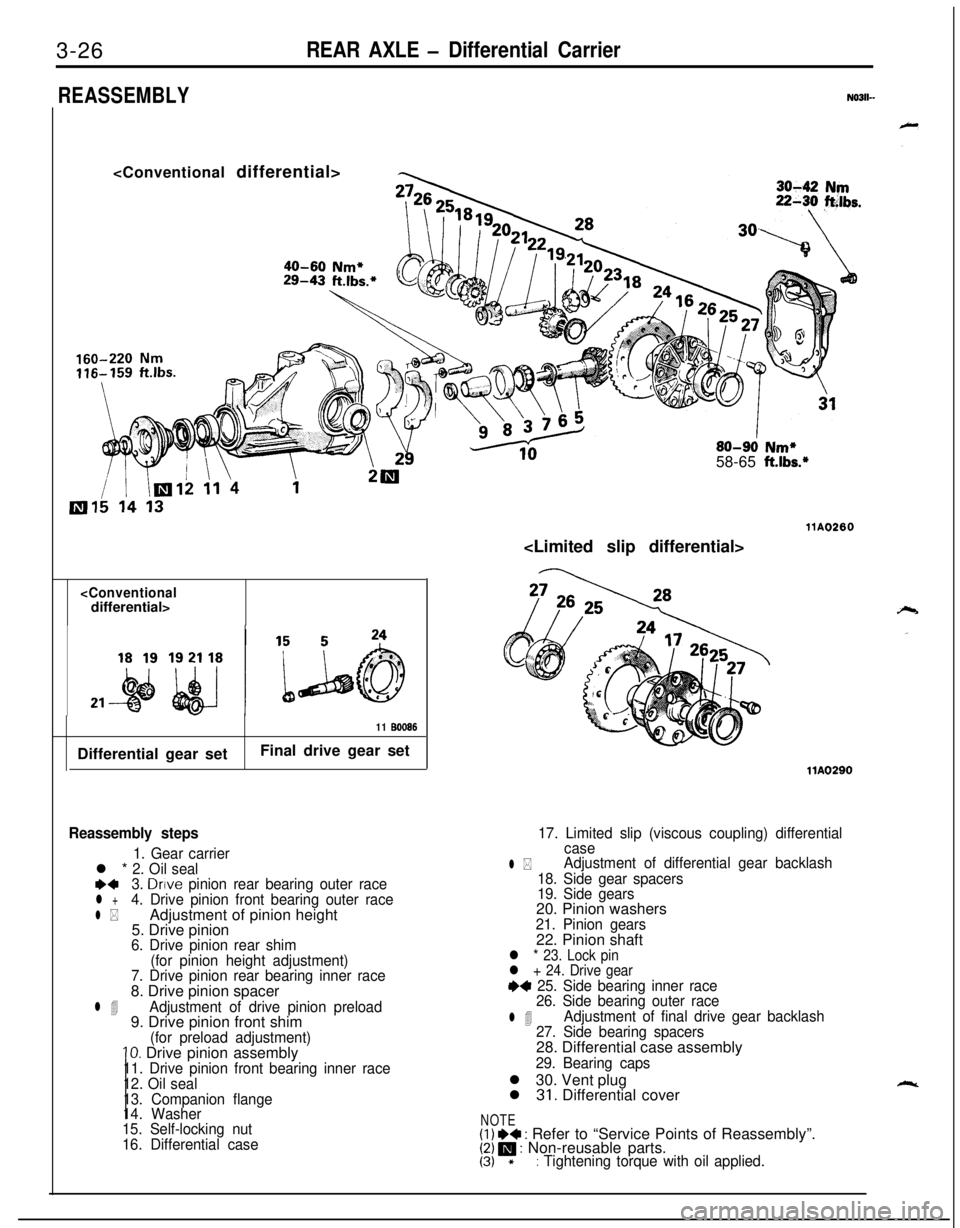
3-26REAR AXLE - Differential Carrier
REASSEMBLYN0311-
Nm*B-43 ft.lbs.*
80-90 Nm*58-65 ft.lbs.*
11 BOO86Differential gear setFinal drive gear set
Reassembly steps
1. Gear carrierl * 2. Oil seale+3. Drive pinion rear bearing outer racel +4. Drive pinion front bearing outer race
l *Adjustment of pinion height
5. Drive pinion
6. Drive pinion rear shim
(for pinion height adjustment)
7. Drive pinion rear bearing inner race8. Drive pinion spacer
l 4Adjustment of drive pinion preload9. Drive pinion front shim
(for preload adjustment)10. Drive pinion assembly11. Drive pinion front bearing inner race
12. Oil seal
13. Companion flange
14. Washer
15. Self-locking nut
16. Differential case
17. Limited slip (viscous coupling) differential
case
l *Adjustment of differential gear backlash
18. Side gear spacers
19. Side gears20. Pinion washers
21. Pinion gears22. Pinion shaft
l * 23. Lock pin
l + 24. Drive gear
+4 25. Side bearing inner race
26. Side bearing outer race
l 4Adjustment of final drive gear backlash
27. Side bearing spacers28. Differential case assembly
29. Bearing capsl 30. Vent plug
l
31. Differential cover
NOTE(I) I)+ : Refer to “Service Points of Reassembly”.[Z!/ m : Non-reusable parts.*: Tightening torque with oil applied.
Page 129 of 1216
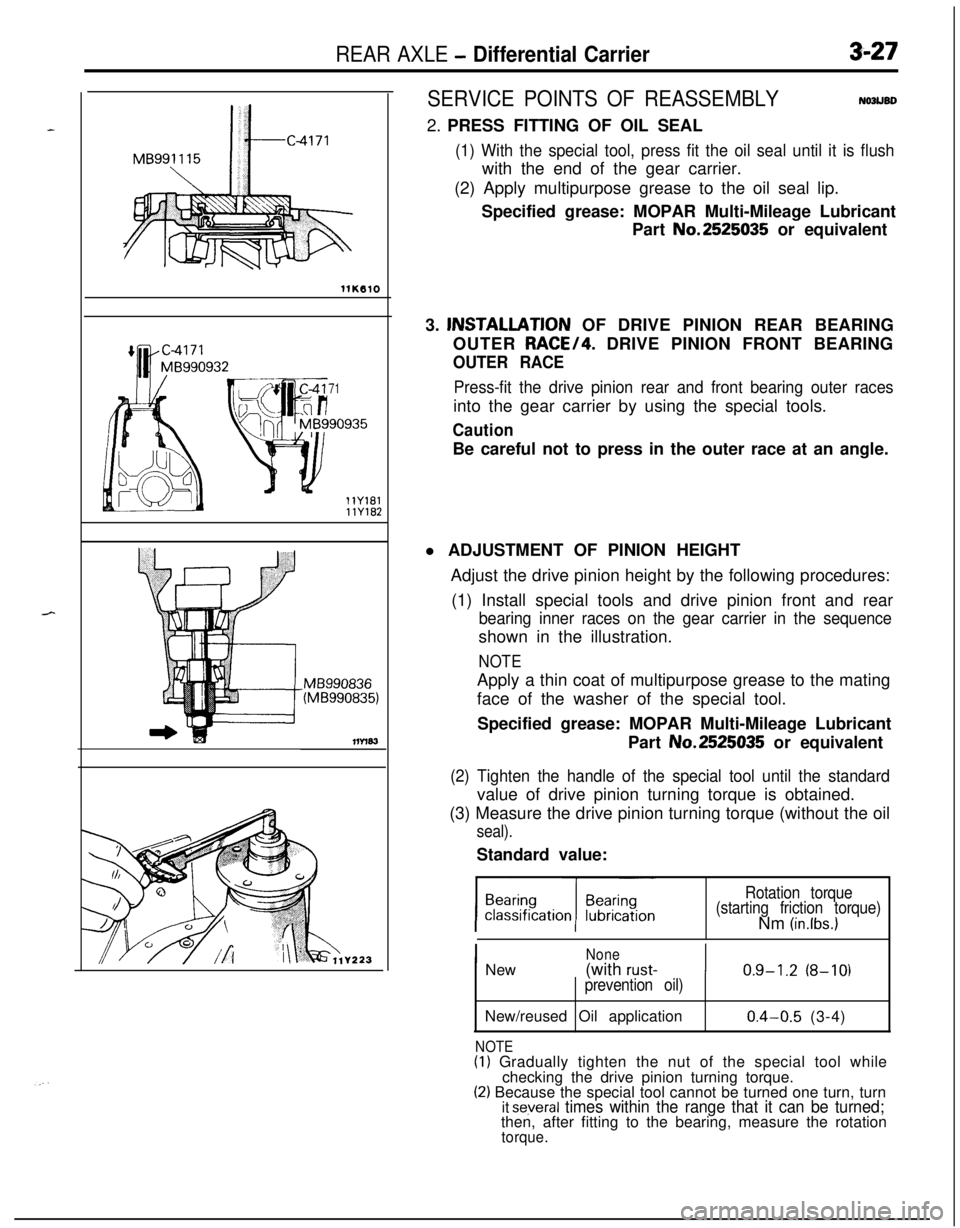
REAR AXLE - Differential Carrier3-27
llK010
71
llY181llY182
.MB990836(MB990835)
llrm3
V223
SERVICE POINTS OF REASSEMBLYNOJUBD2. PRESS FITTING OF OIL SEAL
(1) With the special tool, press fit the oil seal until it is flushwith the end of the gear carrier.
(2) Apply multipurpose grease to the oil seal lip.
Specified grease: MOPAR Multi-Mileage Lubricant
Part No.2525035 or equivalent
3. lNSTALLATlON OF DRIVE PINION REAR BEARING
OUTER RACE/4. DRIVE PINION FRONT BEARING
OUTER RACE
Press-fit the drive pinion rear and front bearing outer racesinto the gear carrier by using the special tools.
CautionBe careful not to press in the outer race at an angle.
l ADJUSTMENT OF PINION HEIGHT
Adjust the drive pinion height by the following procedures:
(1) Install special tools and drive pinion front and rear
bearing inner races on the gear carrier in the sequenceshown in the illustration.
NOTEApply a thin coat of multipurpose grease to the mating
face of the washer of the special tool.
Specified grease: MOPAR Multi-Mileage Lubricant
Part No.2525035 or equivalent
(2) Tighten the handle of the special tool until the standardvalue of drive pinion turning torque is obtained.
(3) Measure the drive pinion turning torque (without the oil
seal).Standard value:
Rotation torque
(starting friction torque)Nm
(in.lbs.)
I
NoneNew(with rust-I0.9-1.2 (8-10)prevention oil)New/reused Oil application
NOTE
0.4-0.5 (3-4)(I) Gradually tighten the nut of the special tool while
checking the drive pinion turning torque.
(2) Because the special tool cannot be turned one turn, turnit several times within the range that it can be turned;then, after fitting to the bearing, measure the rotation
torque.
Page 130 of 1216
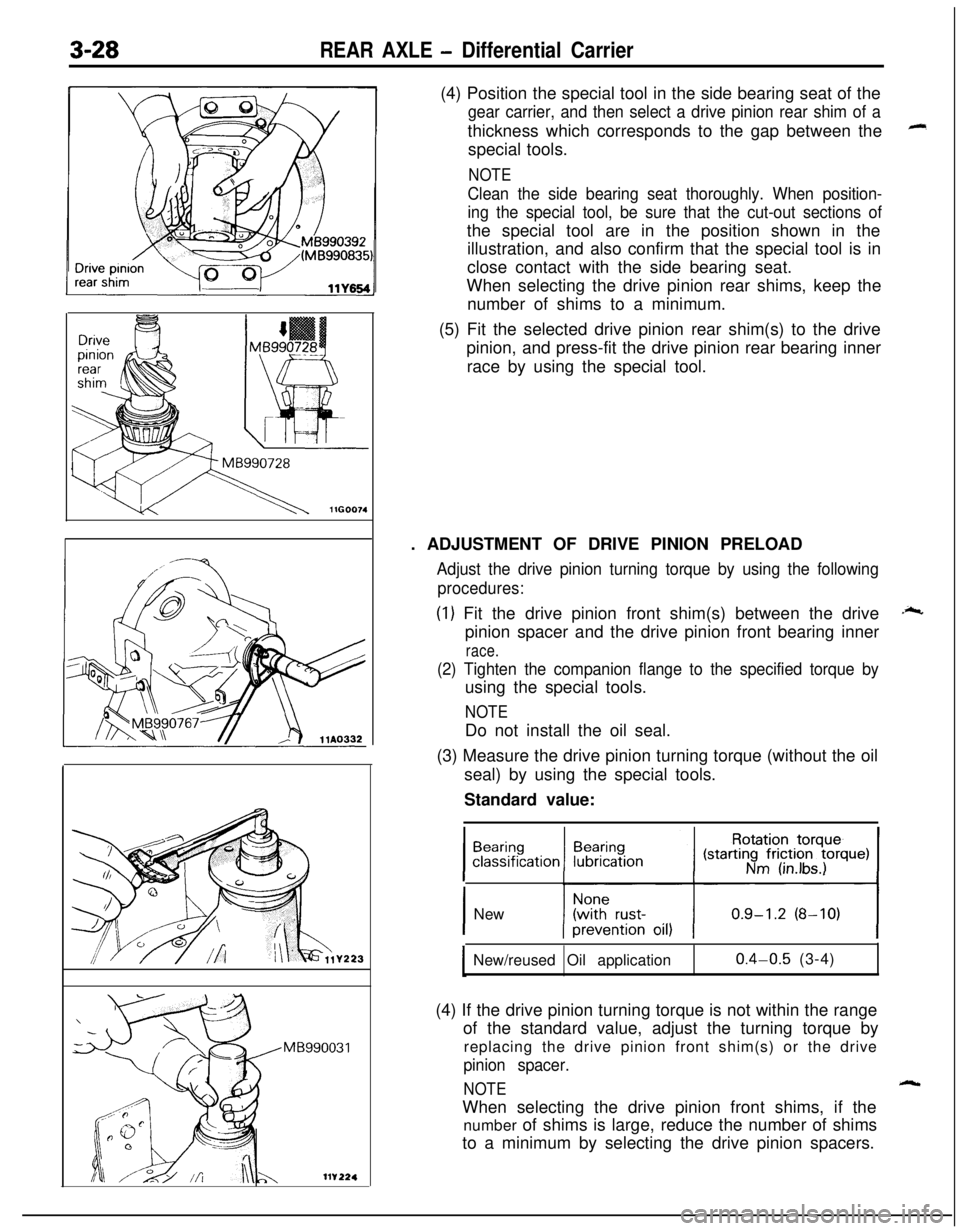
3-28REAR AXLE - Differential Carrier
Y223
MB990031(4) Position the special tool in the side bearing seat of the
gear carrier, and then select a drive pinion rear shim of athickness which corresponds to the gap between the
special tools.
NOTE
Clean the side bearing seat thoroughly. When position-
ing the special tool, be sure that the cut-out sections ofthe special tool are in the position shown in the
illustration, and also confirm that the special tool is in
close contact with the side bearing seat.
When selecting the drive pinion rear shims, keep the
number of shims to a minimum.
(5) Fit the selected drive pinion rear shim(s) to the drive
pinion, and press-fit the drive pinion rear bearing inner
race by using the special tool.
. ADJUSTMENT OF DRIVE PINION PRELOAD
Adjust the drive pinion turning torque by using the following
procedures:
(1) Fit the drive pinion front shim(s) between the drive
pinion spacer and the drive pinion front bearing inner
race.
(2) Tighten the companion flange to the specified torque byusing the special tools.
NOTEDo not install the oil seal.
(3) Measure the drive pinion turning torque (without the oil
seal) by using the special tools.
Standard value:
21
.;c
1 New
New/reused Oil application
0.4-0.5 (3-4)
(4) If the drive pinion turning torque is not within the range
of the standard value, adjust the turning torque by
replacing the drive pinion front shim(s) or the drive
pinion spacer.
NOTEWhen selecting the drive pinion front shims, if the
number of shims is large, reduce the number of shims
to a minimum by selecting the drive pinion spacers.
Page 131 of 1216
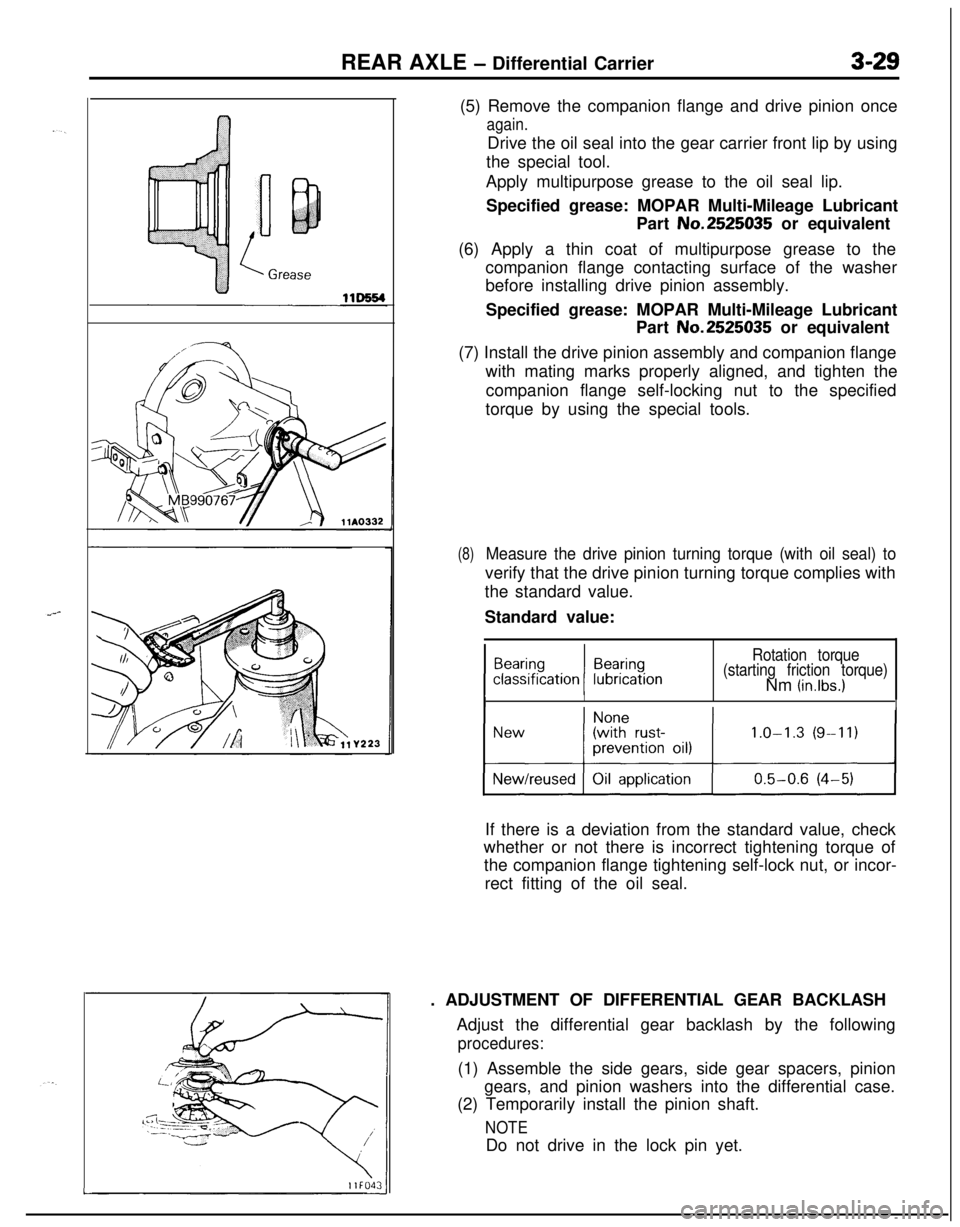
REAR AXLE - Differential Carrier3-29
Y223(5) Remove the companion flange and drive pinion once
again.Drive the oil seal into the gear carrier front lip by using
the special tool.
Apply multipurpose grease to the oil seal lip.
Specified grease: MOPAR Multi-Mileage Lubricant
Part No.2525035 or equivalent
(6) Apply a thin coat of multipurpose grease to the
companion flange contacting surface of the washer
before installing drive pinion assembly.
Specified grease: MOPAR Multi-Mileage Lubricant
Part No.2525035 or equivalent
(7) Install the drive pinion assembly and companion flange
with mating marks properly aligned, and tighten the
companion flange self-locking nut to the specified
torque by using the special tools.
(8)Measure the drive pinion turning torque (with oil seal) toverify that the drive pinion turning torque complies with
the standard value.
Standard value:
Rotation torque
(starting friction torque)Nm
(in.lbs.)
IIIIIf there is a deviation from the standard value, check
whether or not there is incorrect tightening torque of
the companion flange tightening self-lock nut, or incor-
rect fitting of the oil seal.
. ADJUSTMENT OF DIFFERENTIAL GEAR BACKLASH
Adjust the differential gear backlash by the following
procedures:(1) Assemble the side gears, side gear spacers, pinion
gears, and pinion washers into the differential case.
(2) Temporarily install the pinion shaft.
NOTEDo not drive in the lock pin yet.
L-
Page 132 of 1216
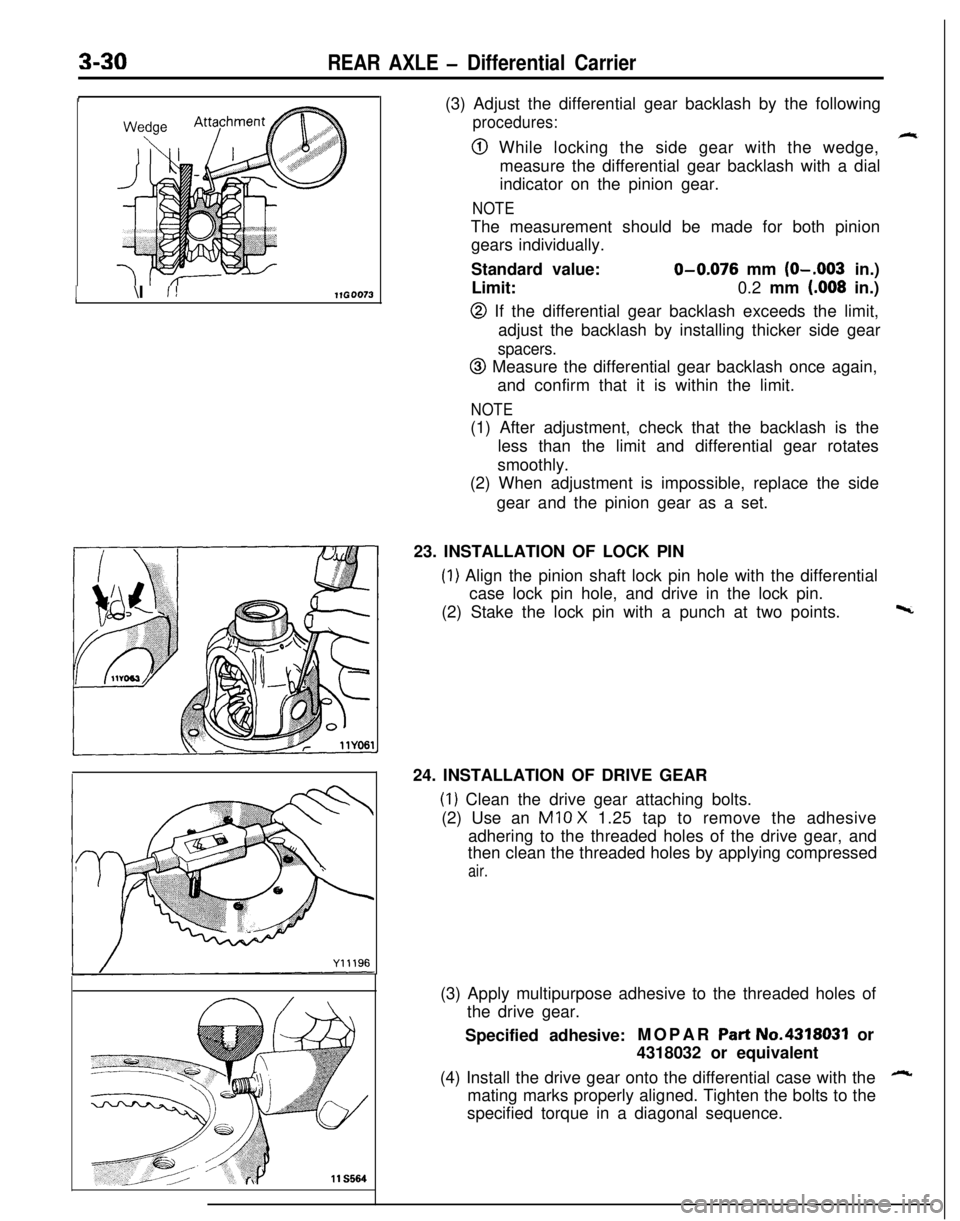
REAR AXLE - Differential Carrier
I\I I!llGOO73I
11 S564(3) Adjust the differential gear backlash by the following
procedures:
@ While locking the side gear with the wedge,
measure the differential gear backlash with a dial
indicator on the pinion gear.
NOTEThe measurement should be made for both pinion
gears individually.
Standard value:
O-0.076 mm (O-.003 in.)
Limit:0.2 mm
(.008 in.)
@ If the differential gear backlash exceeds the limit,
adjust the backlash by installing thicker side gear
spacers.
@ Measure the differential gear backlash once again,
and confirm that it is within the limit.
NOTE(1) After adjustment, check that the backlash is the
less than the limit and differential gear rotates
smoothly.
(2) When adjustment is impossible, replace the side
gear and the pinion gear as a set.
23. INSTALLATION OF LOCK PIN
(1) Align the pinion shaft lock pin hole with the differential
case lock pin hole, and drive in the lock pin.
(2) Stake the lock pin with a punch at two points.
w24. INSTALLATION OF DRIVE GEAR
(1) Clean the drive gear attaching bolts.
(2) Use an
Ml0 X 1.25 tap to remove the adhesive
adhering to the threaded holes of the drive gear, and
then clean the threaded holes by applying compressed
air.(3) Apply multipurpose adhesive to the threaded holes of
the drive gear.
Specified adhesive:MOPAR
Part No.4318031 or
4318032 or equivalent
(4) Install the drive gear onto the differential case with the
Amating marks properly aligned. Tighten the bolts to the
specified torque in a diagonal sequence.
Page 141 of 1216
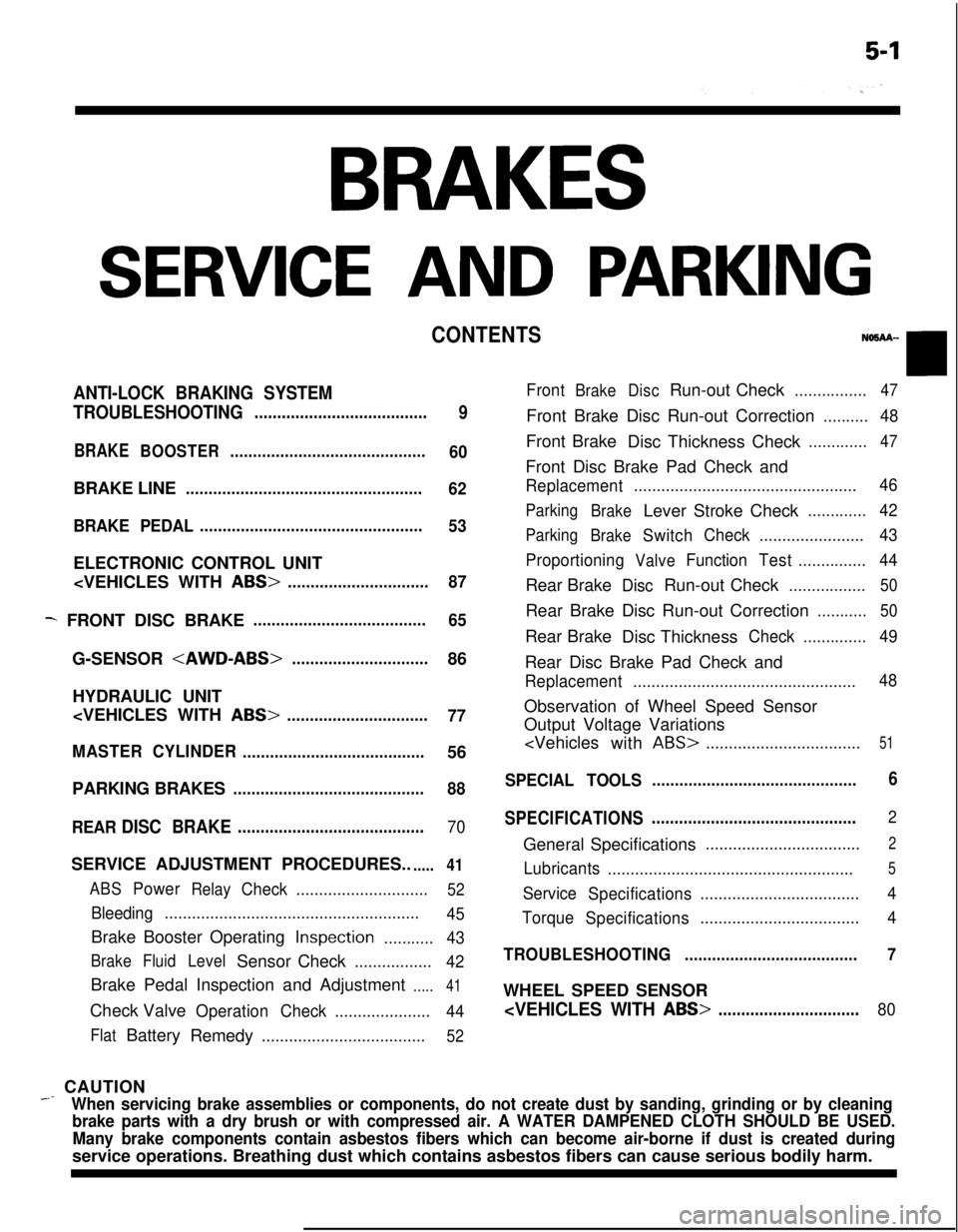
BRAKES
SERVICE AND PARKING
CONTENTS
ANTI-LOCK BRAKING SYSTEM
TROUBLESHOOTING
......................................
9
BRAKEBOOSTER...........................................
60BRAKE LINE
....................................................
62
BRAKE PEDAL.................................................
53ELECTRONIC CONTROL UNIT
- FRONT DISC BRAKE......................................
65G-SENSOR
HYDRAULIC UNIT
77
MASTERCYLINDER
........................................56
PARKING BRAKES
..........................................88
REAR
DISC BRAKE.........................................70SERVICE ADJUSTMENT PROCEDURES..
.....41
ABSPowerRelayCheck.............................52
Bleeding........................................................
45Brake Booster Operating
Inspection...........43
BrakeFluidLevelSensor Check.................
42Brake Pedal Inspection and Adjustment
.....41Check Valve
OperationCheck.....................
44
FlatBattery
Remedy....................................52
FrontBrakeDiscRun-out Check................47Front Brake Disc Run-out Correction
..........48Front Brake
Disc Thickness Check
.............47Front Disc Brake Pad Check and
Replacement.................................................46
Parking
BrakeLever Stroke Check.............42
Parking
BrakeSwitchCheck.......................43
Proportioning
ValveFunctionTest...............44Rear Brake
DiscRun-out Check.................50Rear Brake Disc Run-out Correction
...........50Rear Brake
Disc Thickness
Check..............49Rear Disc Brake Pad Check and
Replacement.................................................48Observation of Wheel Speed Sensor
Output Voltage Variations
ABS>..................................51
SPECIAL TOOLS.............................................6
SPECIFICATIONS.............................................
2General Specifications
..................................2
Lubricants
......................................................5
Service
Specifications...................................4
Torque
Specifications...................................4
TROUBLESHOOTING......................................7WHEEL SPEED SENSOR
_ CAUTION
When servicing brake assemblies or components, do not create dust by sanding, grinding or by cleaning
brake parts with a dry brush or with compressed air. A WATER DAMPENED CLOTH SHOULD BE USED.
Many brake components contain asbestos fibers which can become air-borne if dust is created duringservice operations. Breathing dust which contains asbestos fibers can cause serious bodily harm.
Page 144 of 1216
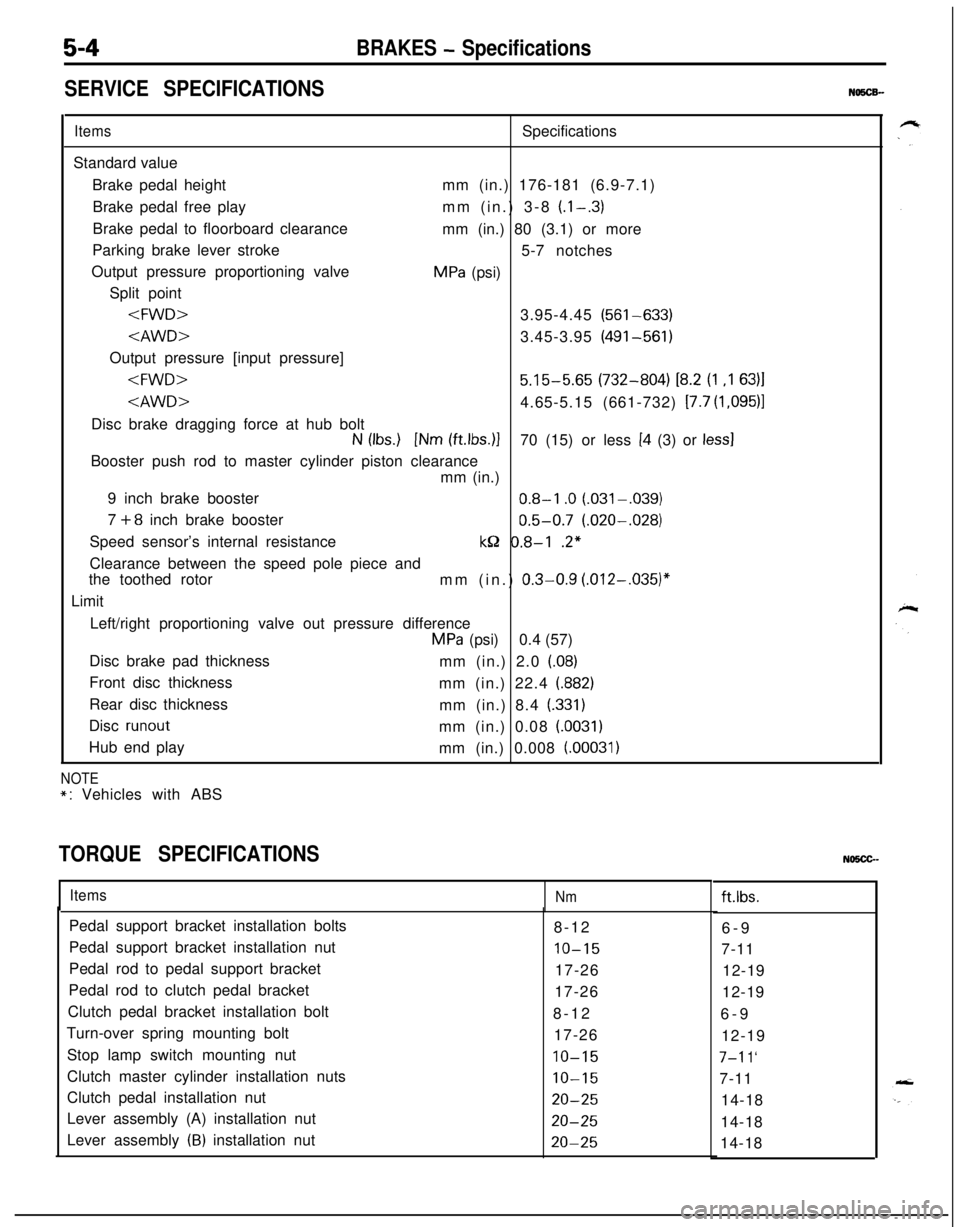
5-4BRAKES - Specifications
SERVICE SPECIFICATIONS
NO5CB-
ItemsSpecifications
Standard value
Brake pedal heightmm (in.) 176-181 (6.9-7.1)
Brake pedal free playmm (in.) 3-8
(l-.3)Brake pedal to floorboard clearance
mm (in.) 80 (3.1) or more
Parking brake lever stroke
5-7 notches
Output pressure proportioning valve
MPa (psi)
Split point
Output pressure [input pressure]
N (Ibs.) [Nm (ftlbs.)]70 (15) or less [4 (3) or less1Booster push rod to master cylinder piston clearance
mm (in.)
9 inch brake booster
0.8-l .O (.031-,039)
7
+8 inch brake booster0.5-0.7 (.020-.028)
Speed sensor’s internal resistance
kQ 0.8-l .2*
Clearance between the speed pole piece and
the toothed rotor
mm (in.)
0.3-0.9 (.012-,035)”Limit
Left/right proportioning valve out pressure difference
MPa (psi)0.4 (57)
Disc brake pad thickness
mm (in.) 2.0 (08)
Front disc thickness
mm (in.) 22.4 (882)
Rear disc thickness
mm (in.) 8.4
(.331)Disc
runoutmm (in.) 0.08 (.0031)Hub end play
mm (in.) 0.008
(.00031)
NOTE
*: Vehicles with ABS
TORQUE SPECIFICATIONS
ItemsNmft.lbs.
Pedal support bracket installation bolts
8-12
6-9
Pedal support bracket installation nut
IO-157-11
Pedal rod to pedal support bracket
17-26
12-19
Pedal rod to clutch pedal bracket
17-26
12-19
Clutch pedal bracket installation bolt
8-12
6-9
Turn-over spring mounting bolt
17-26
12-19
Stop lamp switch mounting nut
IO-157-l 1‘Clutch master cylinder installation nuts
10-157-11
Clutch pedal installation nut
20-2514-18
Lever assembly (A) installation nut
20-2514-18
Lever assembly
(B) installation nut20-2514-18
Page 186 of 1216
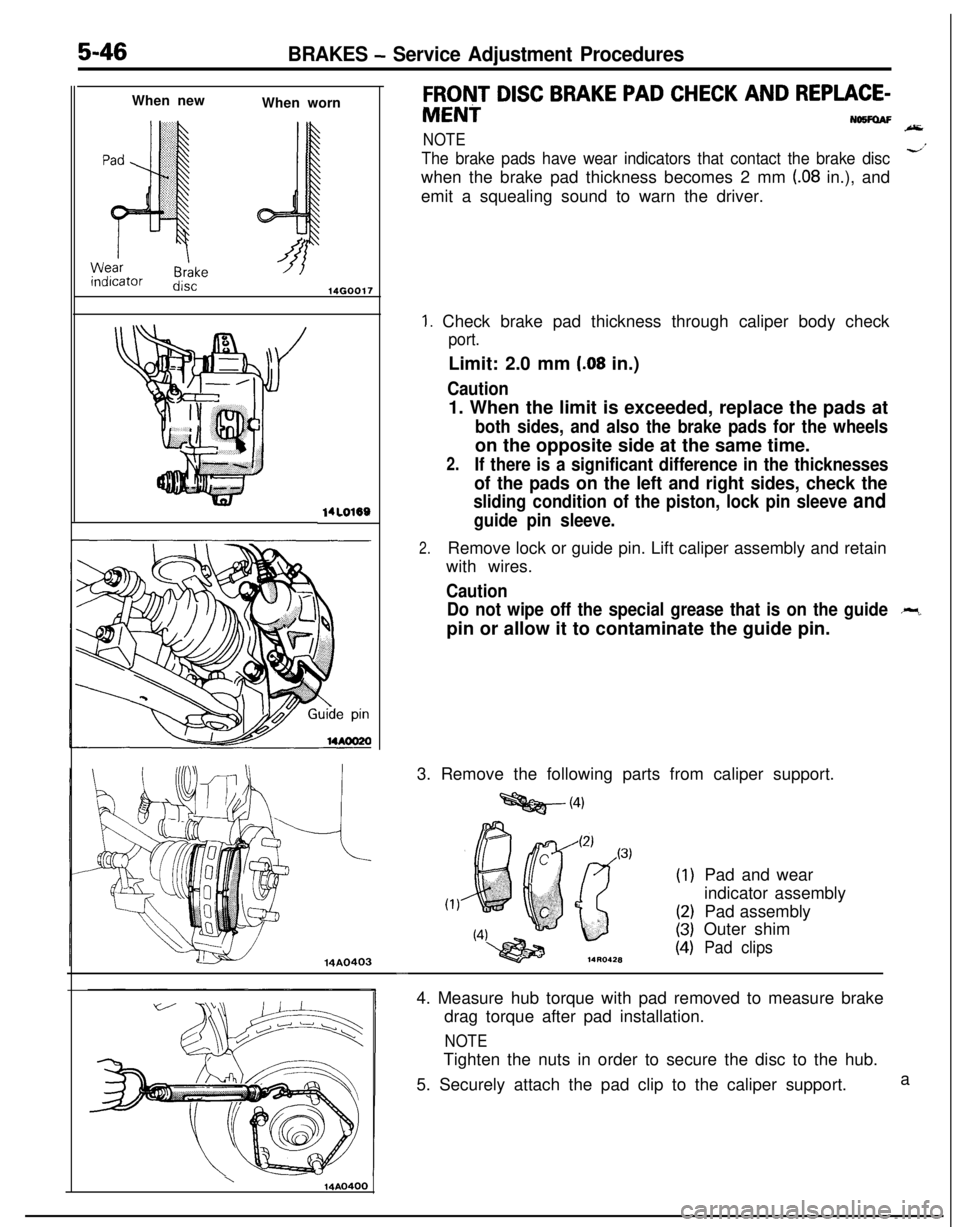
5-46BRAKES - Service Adjustment ProceduresWhen new
When worn
14G0017
14LO169
14A0403
\14AO400
FRONT DISC BRAKE PAD CHECK AND REPLACE-
MENiNWFOAF
NOTE
The brake pads have wear indicators that contact the brake discd’when the brake pad thickness becomes 2 mm
(.08 in.), and
emit a squealing sound to warn the driver.
1. Check brake pad thickness through caliper body check
port.Limit: 2.0 mm
(.08 in.)
Caution1. When the limit is exceeded, replace the pads at
both sides, and also the brake pads for the wheelson the opposite side at the same time.
2.If there is a significant difference in the thicknesses
of the pads on the left and right sides, check the
sliding condition of the piston, lock pin sleeve and
guide pin sleeve.
2.Remove lock or guide pin. Lift caliper assembly and retain
with wires.
Caution
Do not wipe off the special grease that is on the guide
-pin or allow it to contaminate the guide pin.
3. Remove the following parts from caliper support.
=Qg@-(4)
(1)
(2)
(3)
(4)Pad and wear
indicator assembly
Pad assembly
Outer shimPad clips
-4. Measure hub torque with pad removed to measure brake
drag torque after pad installation.
NOTETighten the nuts in order to secure the disc to the hub.
5. Securely attach the pad clip to the caliper support.a
Page 187 of 1216
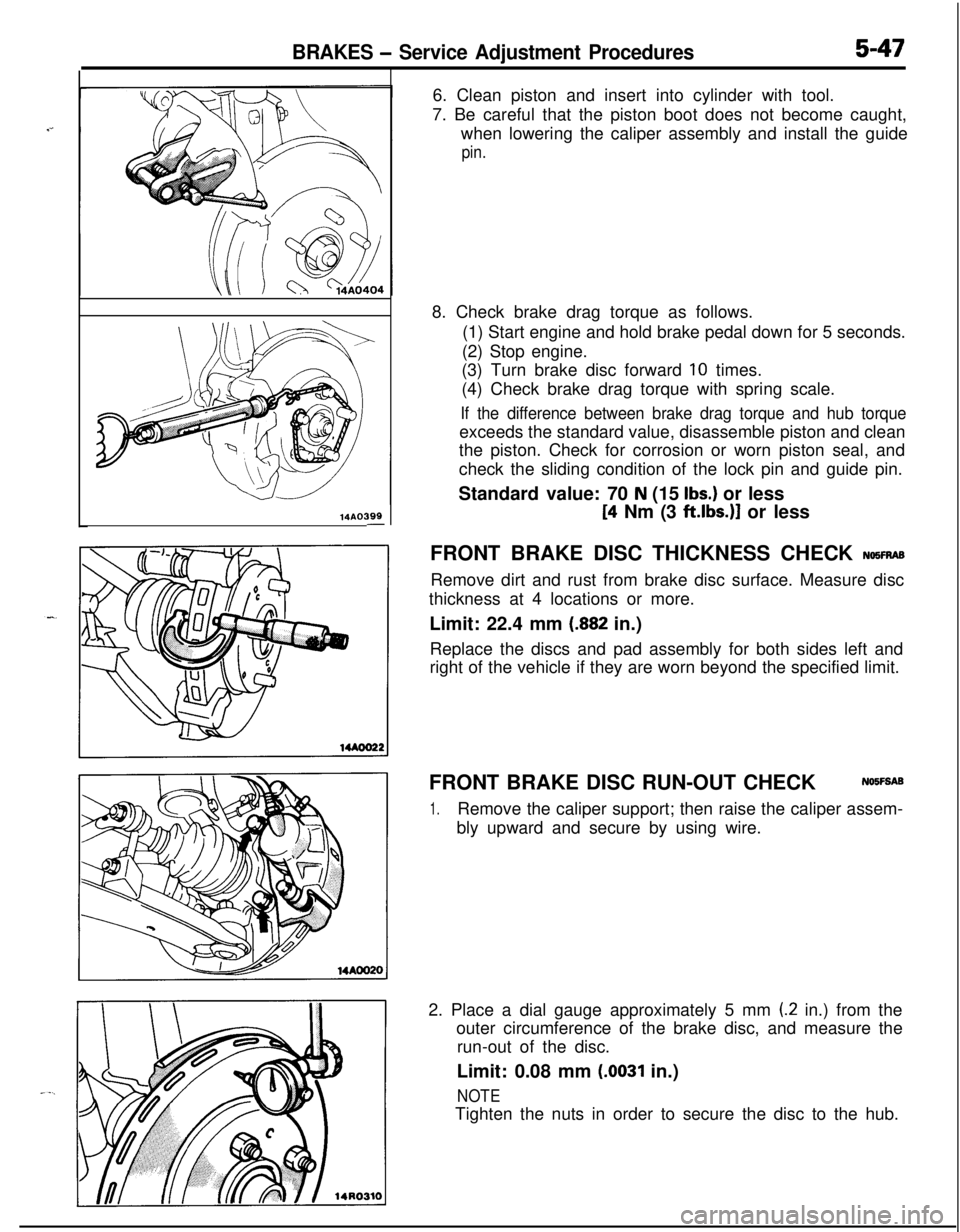
BRAKES - Service Adjustment Procedures5-47
14AO399-6. Clean piston and insert into cylinder with tool.
7. Be careful that the piston boot does not become caught,
when lowering the caliper assembly and install the guide
pin.8. Check brake drag torque as follows.
(1) Start engine and hold brake pedal down for 5 seconds.
(2) Stop engine.
(3) Turn brake disc forward
10 times.
(4) Check brake drag torque with spring scale.
If the difference between brake drag torque and hub torqueexceeds the standard value, disassemble piston and clean
the piston. Check for corrosion or worn piston seal, and
check the sliding condition of the lock pin and guide pin.
Standard value: 70
N (15 Ibs.) or less
[4 Nm (3 ftlbs.)] or less
FRONT BRAKE DISC THICKNESS CHECK
NQ5FRASRemove dirt and rust from brake disc surface. Measure disc
thickness at 4 locations or more.
Limit: 22.4 mm
(.882 in.)
Replace the discs and pad assembly for both sides left and
right of the vehicle if they are worn beyond the specified limit.
FRONT BRAKE DISC RUN-OUT CHECKNOIFSAB
1.Remove the caliper support; then raise the caliper assem-
bly upward and secure by using wire.
2. Place a dial gauge approximately 5 mm
(2 in.) from the
outer circumference of the brake disc, and measure the
run-out of the disc.
Limit: 0.08 mm
(.0031 in.)
NOTETighten the nuts in order to secure the disc to the hub.