sensor MITSUBISHI LANCER EVOLUTION 2007 Service Service Manual
[x] Cancel search | Manufacturer: MITSUBISHI, Model Year: 2007, Model line: LANCER EVOLUTION, Model: MITSUBISHI LANCER EVOLUTION 2007Pages: 1449, PDF Size: 56.82 MB
Page 397 of 1449
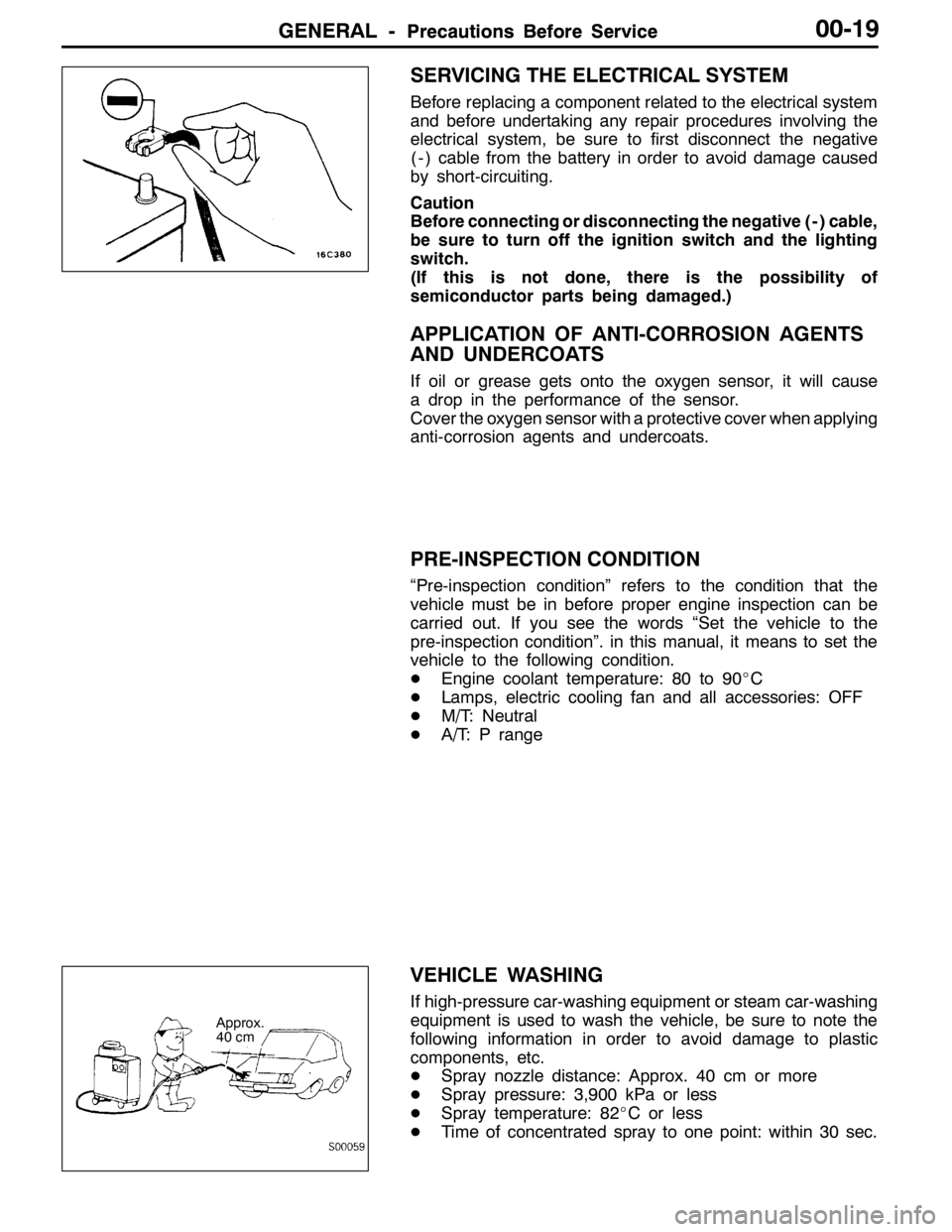
GENERAL -Precautions Before ServiceGENERAL -Precautions Before Service00-19
SERVICING THE ELECTRICAL SYSTEM
Before replacing a component related to the electrical system
and before undertaking any repair procedures involving the
electrical system, be sure to first disconnect the negative
( - ) cable from the battery in order to avoid damage caused
by short-circuiting.
Caution
Before connecting or disconnecting the negative ( - ) cable,
be sure to turn off the ignition switch and the lighting
switch.
(If this is not done, there is the possibility of
semiconductor parts being damaged.)
APPLICATION OF ANTI-CORROSION AGENTS
AND UNDERCOATS
If oil or grease gets onto the oxygen sensor, it will cause
a drop in the performance of the sensor.
Cover the oxygen sensor with a protective cover when applying
anti-corrosion agents and undercoats.
PRE-INSPECTION CONDITION
“Pre-inspection condition” refers to the condition that the
vehicle must be in before proper engine inspection can be
carried out. If you see the words “Set the vehicle to the
pre-inspection condition”. in this manual, it means to set the
vehicle to the following condition.
DEngine coolant temperature: 80 to 90_C
DLamps, electric cooling fan and all accessories: OFF
DM/T: Neutral
DA/T: P range
VEHICLE WASHING
If high-pressure car-washing equipment or steam car-washing
equipment is used to wash the vehicle, be sure to note the
following information in order to avoid damage to plastic
components, etc.
DSpray nozzle distance: Approx. 40 cm or more
DSpray pressure: 3,900 kPa or less
DSpray temperature: 82_C or less
DTime of concentrated spray to one point: within 30 sec.
Approx.
40 cm
Page 399 of 1449
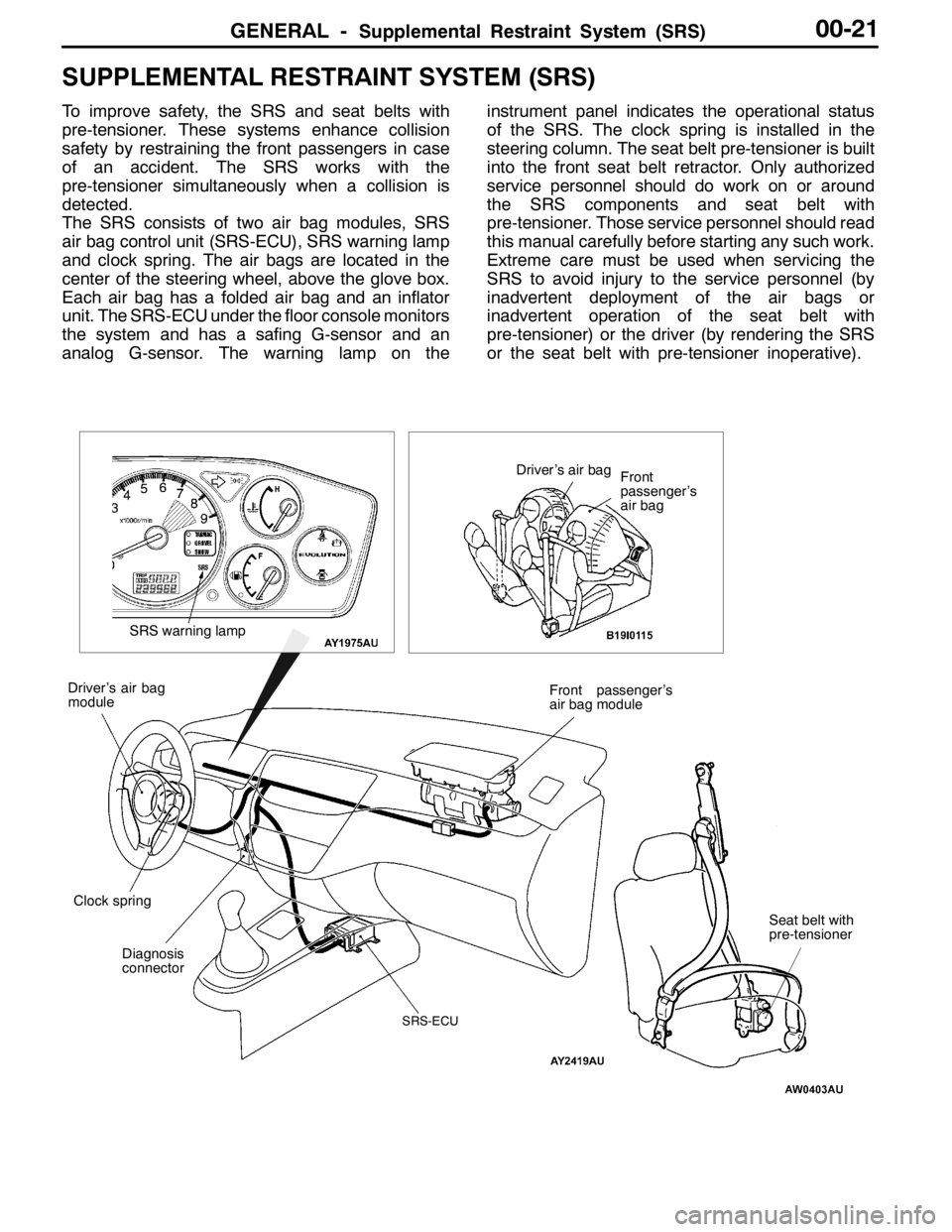
GENERAL -Supplemental Restraint System (SRS)00-21
SUPPLEMENTAL RESTRAINT SYSTEM (SRS)
To improve safety, the SRS and seat belts with
pre-tensioner. These systems enhance collision
safety by restraining the front passengers in case
of an accident. The SRS works with the
pre-tensioner simultaneously when a collision is
detected.
The SRS consists of two air bag modules, SRS
air bag control unit (SRS-ECU), SRS warning lamp
and clock spring. The air bags are located in the
center of the steering wheel, above the glove box.
Each air bag has a folded air bag and an inflator
unit. The SRS-ECU under the floor console monitors
the system and has a safing G-sensor and an
analog G-sensor. The warning lamp on theinstrument panel indicates the operational status
of the SRS. The clock spring is installed in the
steering column. The seat belt pre-tensioner is built
into the front seat belt retractor. Only authorized
service personnel should do work on or around
the SRS components and seat belt with
pre-tensioner. Those service personnel should read
this manual carefully before starting any such work.
Extreme care must be used when servicing the
SRS to avoid injury to the service personnel (by
inadvertent deployment of the air bags or
inadvertent operation of the seat belt with
pre-tensioner) or the driver (by rendering the SRS
or the seat belt with pre-tensioner inoperative).
Diagnosis
connectorFront passenger’s
air bag module
Clock spring Driver’s air bag
module
SRS-ECU
SRS warning lamp
Driver’s air bag
Front
passenger’s
air bag
Seat belt with
pre-tensioner
Page 410 of 1449
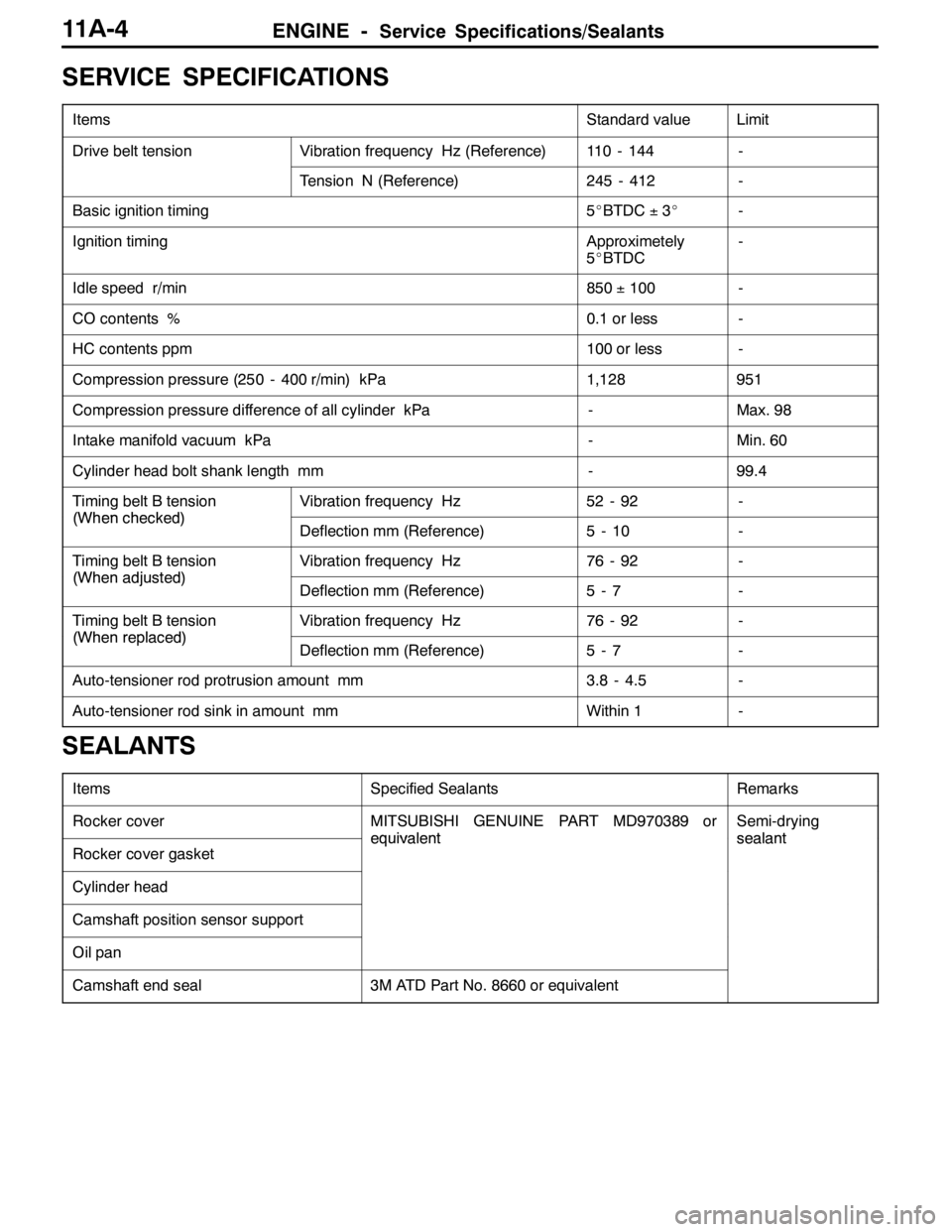
ENGINE -Service Specifications/Sealants11A-4
SERVICE SPECIFICATIONS
ItemsStandard valueLimit
Drive belt tensionVibration frequency Hz (Reference)110 - 144-
Tension N (Reference)245 - 412-
Basic ignition timing5_BTDC±3_-
Ignition timingApproximetely
5_BTDC-
Idle speed r/min850±100-
CO contents %0.1 or less-
HC contents ppm100 or less-
Compression pressure (250 - 400 r/min) kPa1,128951
Compression pressure difference of all cylinder kPa-Max. 98
Intake manifold vacuum kPa-Min. 60
Cylinder head bolt shank length mm-99.4
Timing belt B tension
(Whenchecked)
Vibration frequency Hz52 - 92-
(When checked)Deflection mm (Reference)5-10-
Timing belt B tension
(Whenadjusted)
Vibration frequency Hz76 - 92-
(When adjusted)Deflection mm (Reference)5-7-
Timing belt B tension
(Whenreplaced)
Vibration frequency Hz76 - 92-
(When replaced)Deflection mm (Reference)5-7-
Auto-tensioner rod protrusion amount mm3.8 - 4.5-
Auto-tensioner rod sink in amount mmWithin 1-
SEALANTS
ItemsSpecified SealantsRemarks
Rocker coverMITSUBISHI GENUINE PART MD970389 or
equivalent
Semi-drying
sealant
Rocker cover gasket
equivalentsealant
Cylinder head
Camshaft position sensor support
Oil pan
Camshaft end seal3M ATD Part No. 8660 or equivalent
Page 416 of 1449
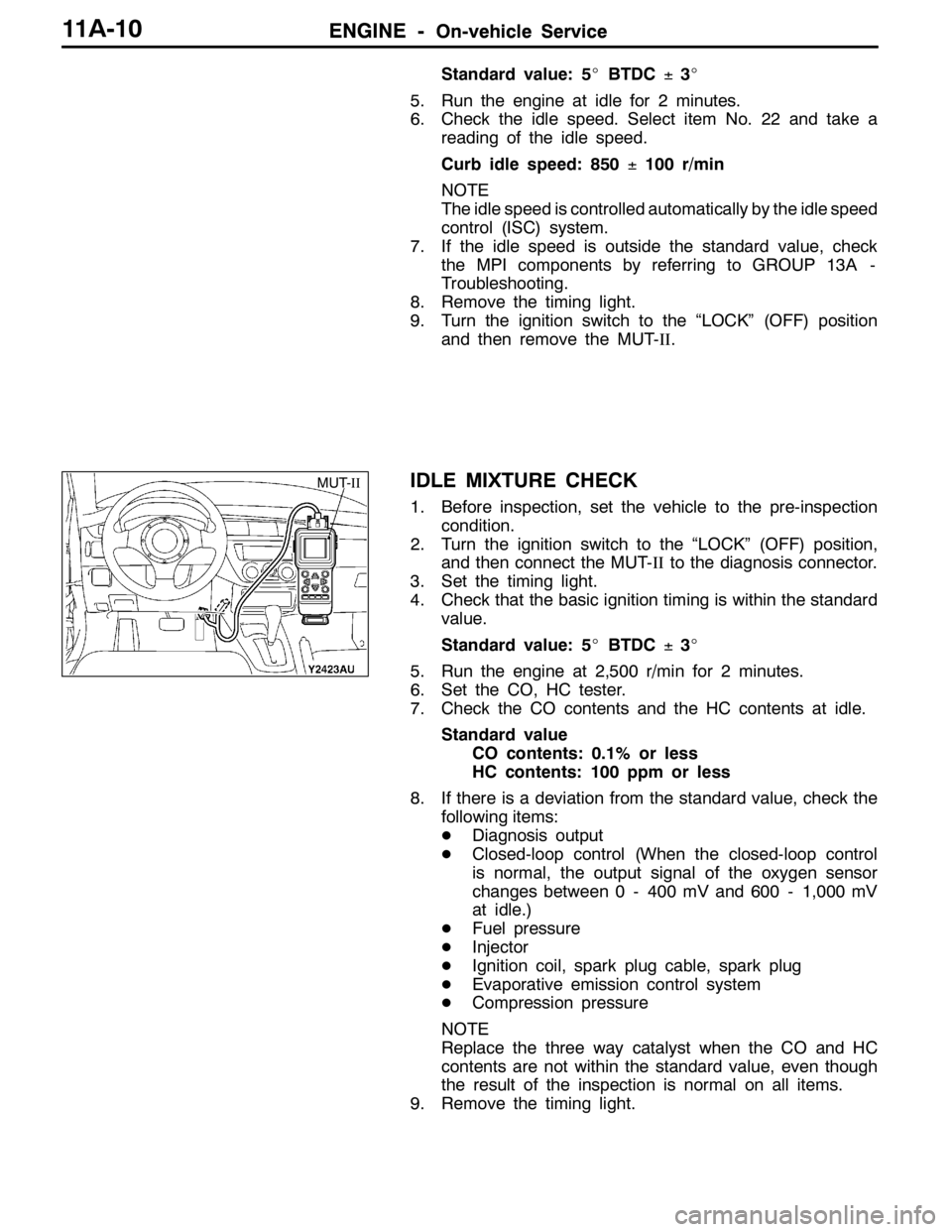
ENGINE -On-vehicle ServiceENGINE -On-vehicle Service11A-10
Standard value: 5_BTDC±3_
5. Run the engine at idle for 2 minutes.
6. Check the idle speed. Select item No. 22 and take a
reading of the idle speed.
Curb idle speed: 850±100 r/min
NOTE
The idle speed is controlled automatically by the idle speed
control (ISC) system.
7. If the idle speed is outside the standard value, check
the MPI components by referring to GROUP 13A -
Troubleshooting.
8. Remove the timing light.
9. Turn the ignition switch to the “LOCK” (OFF) position
and then remove the MUT-II.
IDLE MIXTURE CHECK
1. Before inspection, set the vehicle to the pre-inspection
condition.
2. Turn the ignition switch to the “LOCK” (OFF) position,
and then connect the MUT-IIto the diagnosis connector.
3. Set the timing light.
4. Check that the basic ignition timing is within the standard
value.
Standard value: 5_BTDC±3_
5. Run the engine at 2,500 r/min for 2 minutes.
6. Set the CO, HC tester.
7. Check the CO contents and the HC contents at idle.
Standard value
CO contents: 0.1% or less
HC contents: 100 ppm or less
8. If there is a deviation from the standard value, check the
following items:
DDiagnosis output
DClosed-loop control (When the closed-loop control
is normal, the output signal of the oxygen sensor
changes between 0 - 400 mV and 600 - 1,000 mV
at idle.)
DFuel pressure
DInjector
DIgnition coil, spark plug cable, spark plug
DEvaporative emission control system
DCompression pressure
NOTE
Replace the three way catalyst when the CO and HC
contents are not within the standard value, even though
the result of the inspection is normal on all items.
9. Remove the timing light.
MUT-II
Page 417 of 1449
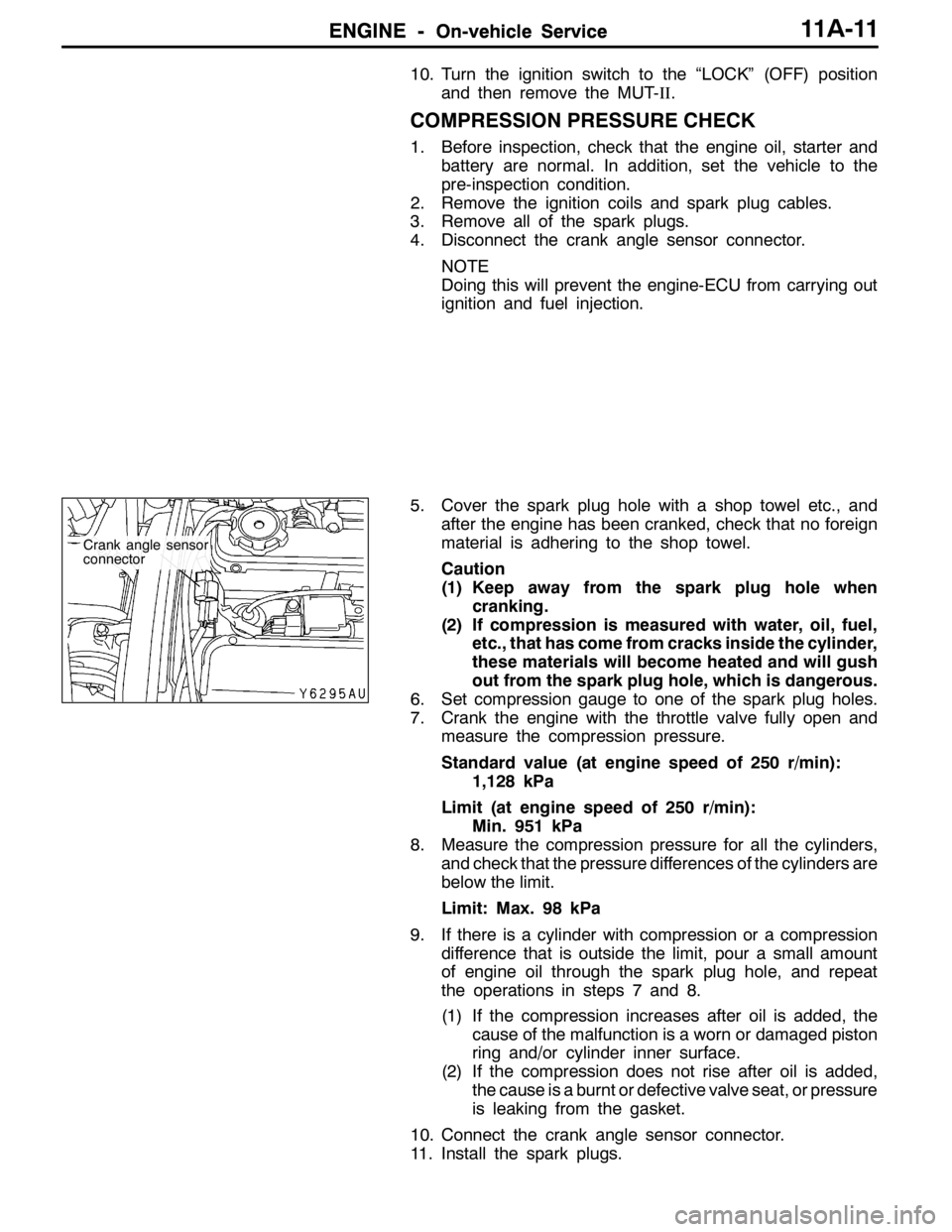
ENGINE -On-vehicle ServiceENGINE -On-vehicle ServiceENGINE -On-vehicle Service11A-11
10. Turn the ignition switch to the “LOCK” (OFF) position
and then remove the MUT-II.
COMPRESSION PRESSURE CHECK
1. Before inspection, check that the engine oil, starter and
battery are normal. In addition, set the vehicle to the
pre-inspection condition.
2. Remove the ignition coils and spark plug cables.
3. Remove all of the spark plugs.
4. Disconnect the crank angle sensor connector.
NOTE
Doing this will prevent the engine-ECU from carrying out
ignition and fuel injection.
5. Cover the spark plug hole with a shop towel etc., and
after the engine has been cranked, check that no foreign
material is adhering to the shop towel.
Caution
(1) Keep away from the spark plug hole when
cranking.
(2) If compression is measured with water, oil, fuel,
etc., that has come from cracks inside the cylinder,
these materials will become heated and will gush
out from the spark plug hole, which is dangerous.
6. Set compression gauge to one of the spark plug holes.
7. Crank the engine with the throttle valve fully open and
measure the compression pressure.
Standard value (at engine speed of 250 r/min):
1,128 kPa
Limit (at engine speed of 250 r/min):
Min. 951 kPa
8. Measure the compression pressure for all the cylinders,
and check that the pressure differences of the cylinders are
below the limit.
Limit: Max. 98 kPa
9. If there is a cylinder with compression or a compression
difference that is outside the limit, pour a small amount
of engine oil through the spark plug hole, and repeat
the operations in steps 7 and 8.
(1) If the compression increases after oil is added, the
cause of the malfunction is a worn or damaged piston
ring and/or cylinder inner surface.
(2) If the compression does not rise after oil is added,
the cause is a burnt or defective valve seat, or pressure
is leaking from the gasket.
10. Connect the crank angle sensor connector.
11. Install the spark plugs.
Crank angle sensor
connector
Page 418 of 1449
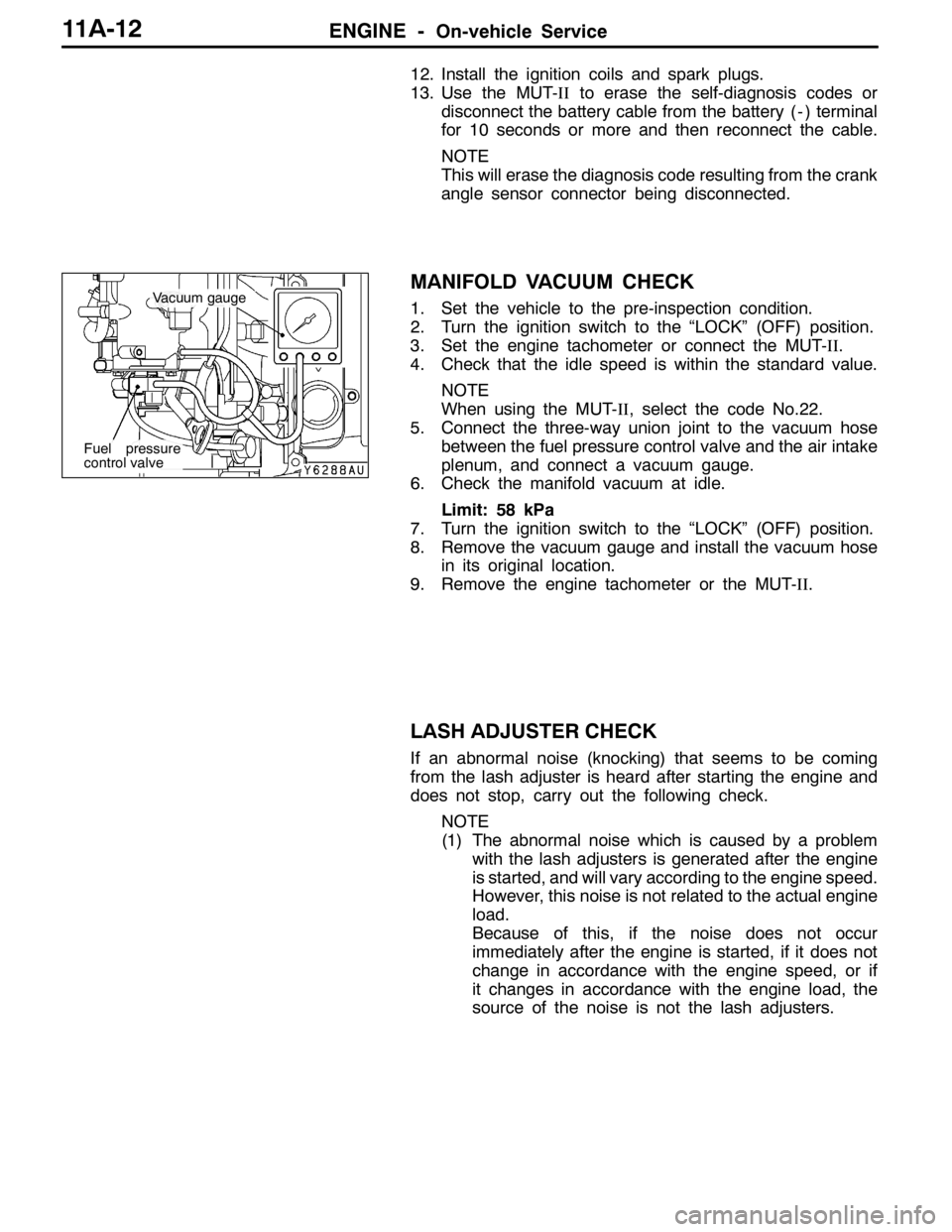
ENGINE -On-vehicle Service11A-12
12. Install the ignition coils and spark plugs.
13. Use the MUT-IIto erase the self-diagnosis codes or
disconnect the battery cable from the battery ( - ) terminal
for 10 seconds or more and then reconnect the cable.
NOTE
This will erase the diagnosis code resulting from the crank
angle sensor connector being disconnected.
MANIFOLD VACUUM CHECK
1. Set the vehicle to the pre-inspection condition.
2. Turn the ignition switch to the “LOCK” (OFF) position.
3. Set the engine tachometer or connect the MUT-II.
4. Check that the idle speed is within the standard value.
NOTE
When using the MUT-II, select the code No.22.
5. Connect the three-way union joint to the vacuum hose
between the fuel pressure control valve and the air intake
plenum, and connect a vacuum gauge.
6. Check the manifold vacuum at idle.
Limit: 58 kPa
7. Turn the ignition switch to the “LOCK” (OFF) position.
8. Remove the vacuum gauge and install the vacuum hose
in its original location.
9. Remove the engine tachometer or the MUT-II.
LASH ADJUSTER CHECK
If an abnormal noise (knocking) that seems to be coming
from the lash adjuster is heard after starting the engine and
does not stop, carry out the following check.
NOTE
(1) The abnormal noise which is caused by a problem
with the lash adjusters is generated after the engine
is started, and will vary according to the engine speed.
However, this noise is not related to the actual engine
load.
Because of this, if the noise does not occur
immediately after the engine is started, if it does not
change in accordance with the engine speed, or if
it changes in accordance with the engine load, the
source of the noise is not the lash adjusters.
Vacuum gauge
Fuel pressure
control valve
Page 423 of 1449
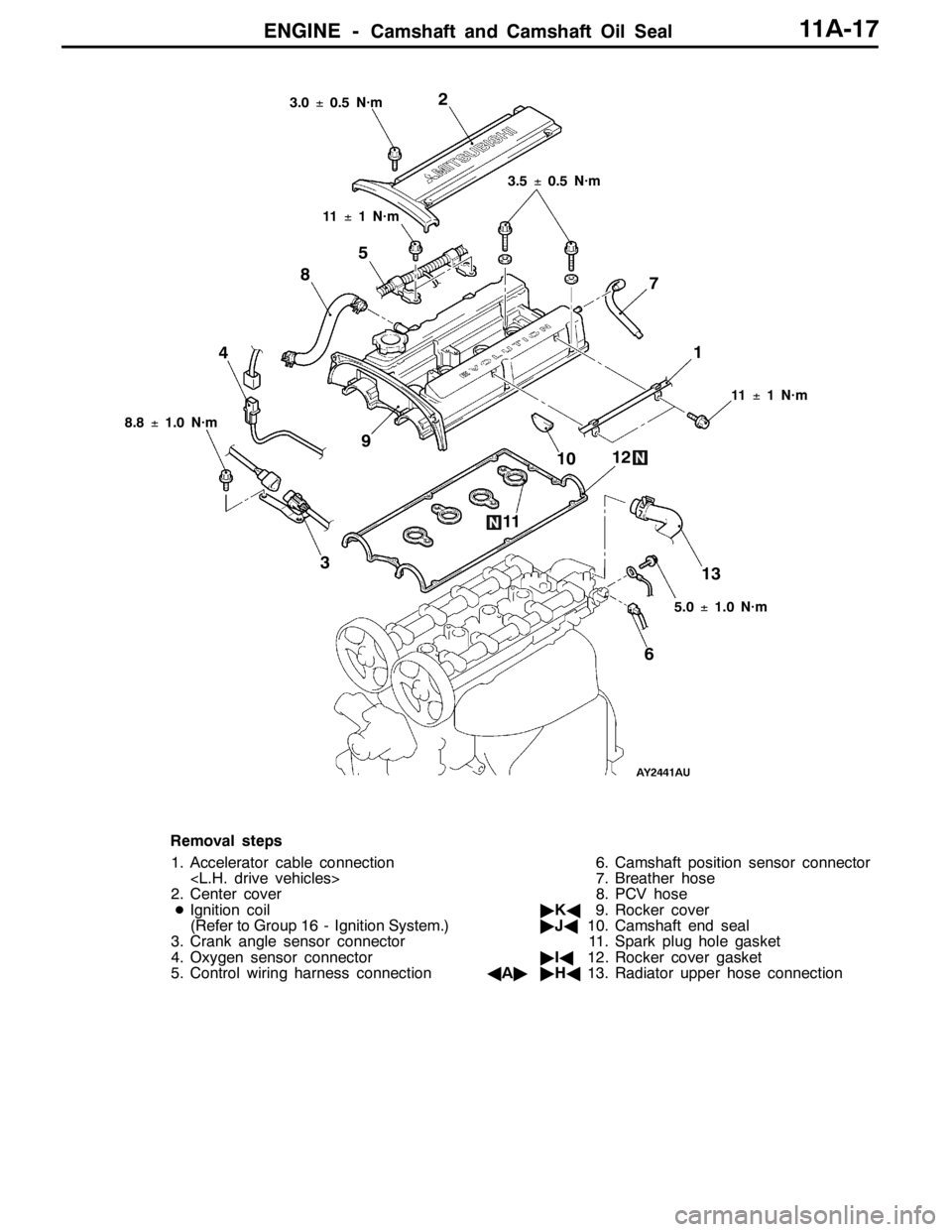
ENGINE -Camshaft and Camshaft Oil Seal11A-17
2
3 45
67 8
9
1012
11
11±1 N·m
8.8±1.0 N·m3.5±0.5 N·m
5.0±1.0 N·m
13
3.0±0.5 N·m
1
11±1 N·m
Removal steps
1. Accelerator cable connection
2. Center cover
DIgnition coil
(Refer to Group 16 - Ignition System.)
3. Crank angle sensor connector
4. Oxygen sensor connector
5. Control wiring harness connection6. Camshaft position sensor connector
7. Breather hose
8. PCV hose
"KA9. Rocker cover
"JA10. Camshaft end seal
11. Spark plug hole gasket
"IA12. Rocker cover gasket
AA""HA13. Radiator upper hose connection
Page 424 of 1449
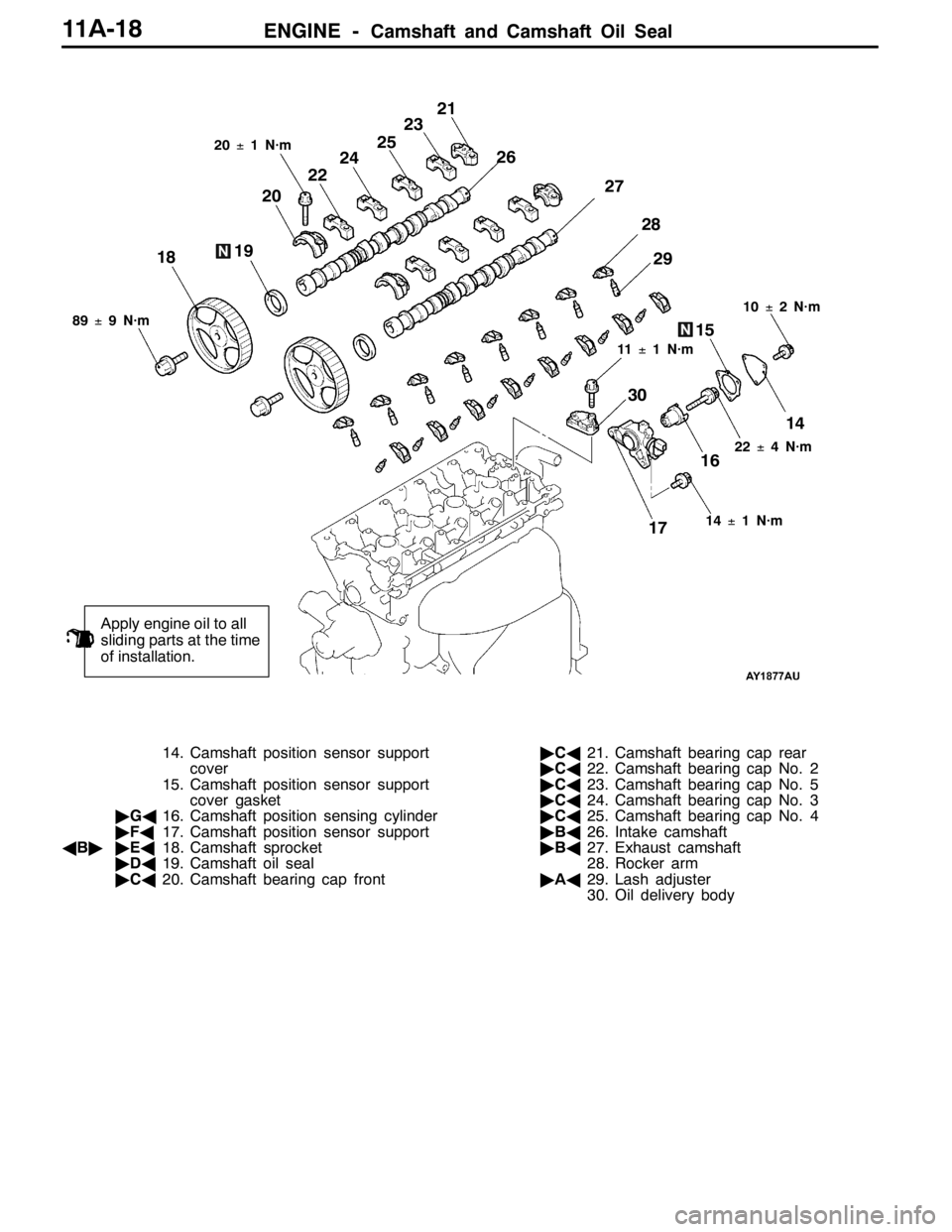
ENGINE -Camshaft and Camshaft Oil Seal11A-18
Apply engine oil to all
sliding parts at the time
of installation.
10±2 N·m
89±9 N·m20±1 N·m
22±4 N·m
14±1 N·m
28
29 27 26
20
14 15
16
17 19
18222321
2425
11±1 N·m
30
14. Camshaft position sensor support
cover
15. Camshaft position sensor support
cover gasket
"GA16. Camshaft position sensing cylinder
"FA17. Camshaft position sensor support
AB""EA18. Camshaft sprocket
"DA19. Camshaft oil seal
"CA20. Camshaft bearing cap front"CA21. Camshaft bearing cap rear
"CA22. Camshaft bearing cap No. 2
"CA23. Camshaft bearing cap No. 5
"CA24. Camshaft bearing cap No. 3
"CA25. Camshaft bearing cap No. 4
"BA26. Intake camshaft
"BA27. Exhaust camshaft
28. Rocker arm
"AA29. Lash adjuster
30. Oil delivery body
Page 428 of 1449
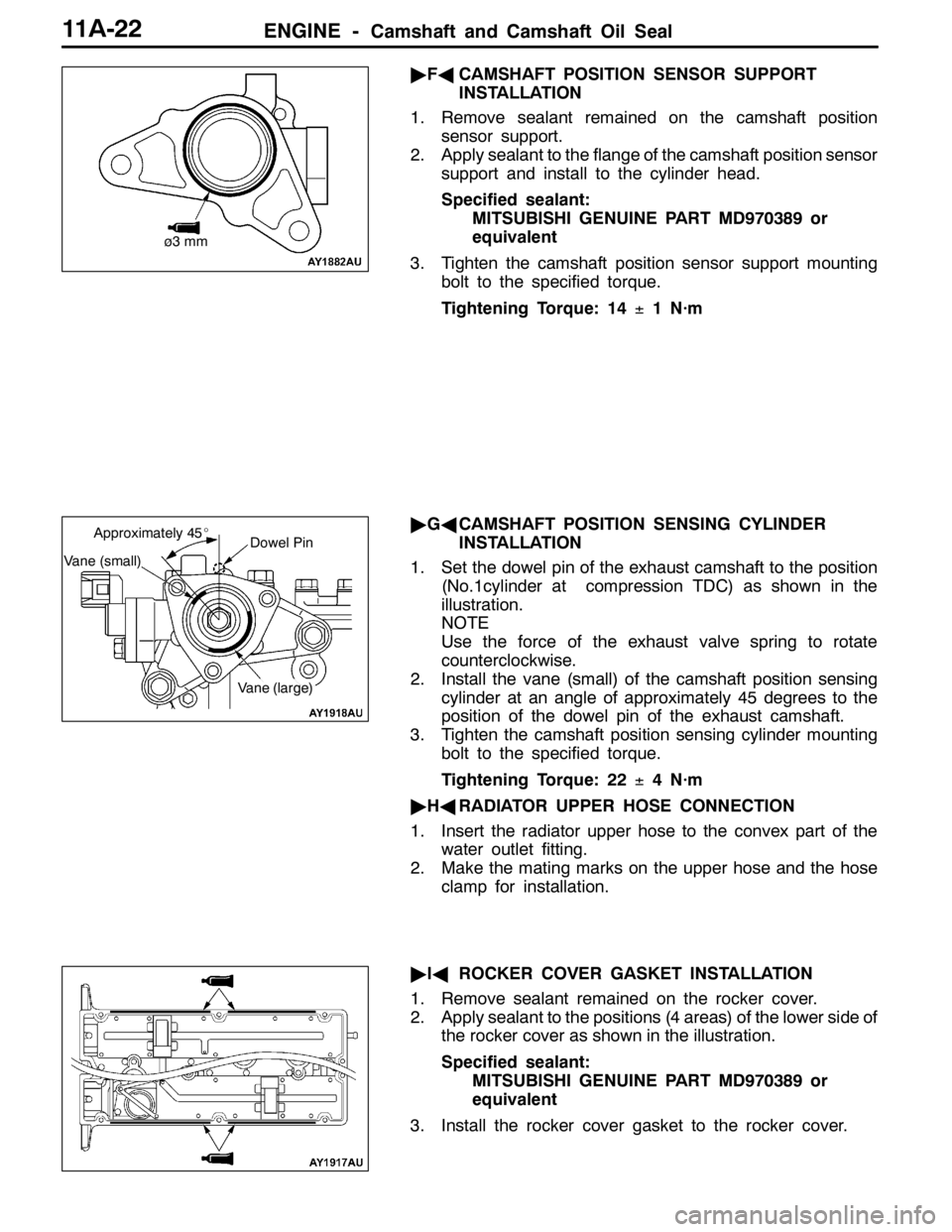
ENGINE -Camshaft and Camshaft Oil Seal11A-22
"FACAMSHAFT POSITION SENSOR SUPPORT
INSTALLATION
1. Remove sealant remained on the camshaft position
sensor support.
2. Apply sealant to the flange of the camshaft position sensor
support and install to the cylinder head.
Specified sealant:
MITSUBISHI GENUINE PART MD970389 or
equivalent
3. Tighten the camshaft position sensor support mounting
bolt to the specified torque.
Tightening Torque: 14±1 N·m
"GACAMSHAFT POSITION SENSING CYLINDER
INSTALLATION
1. Set the dowel pin of the exhaust camshaft to the position
(No.1cylinder at compression TDC) as shown in the
illustration.
NOTE
Use the force of the exhaust valve spring to rotate
counterclockwise.
2. Install the vane (small) of the camshaft position sensing
cylinder at an angle of approximately 45 degrees to the
position of the dowel pin of the exhaust camshaft.
3. Tighten the camshaft position sensing cylinder mounting
bolt to the specified torque.
Tightening Torque: 22±4 N·m
"HARADIATOR UPPER HOSE CONNECTION
1. Insert the radiator upper hose to the convex part of the
water outlet fitting.
2. Make the mating marks on the upper hose and the hose
clamp for installation.
"IAROCKER COVER GASKET INSTALLATION
1. Remove sealant remained on the rocker cover.
2. Apply sealant to the positions (4 areas) of the lower side of
the rocker cover as shown in the illustration.
Specified sealant:
MITSUBISHI GENUINE PART MD970389 or
equivalent
3. Install the rocker cover gasket to the rocker cover.
ø3 mm
Dowel Pin
Vane (small)
Approximately 45_
Vane (large)
Page 435 of 1449
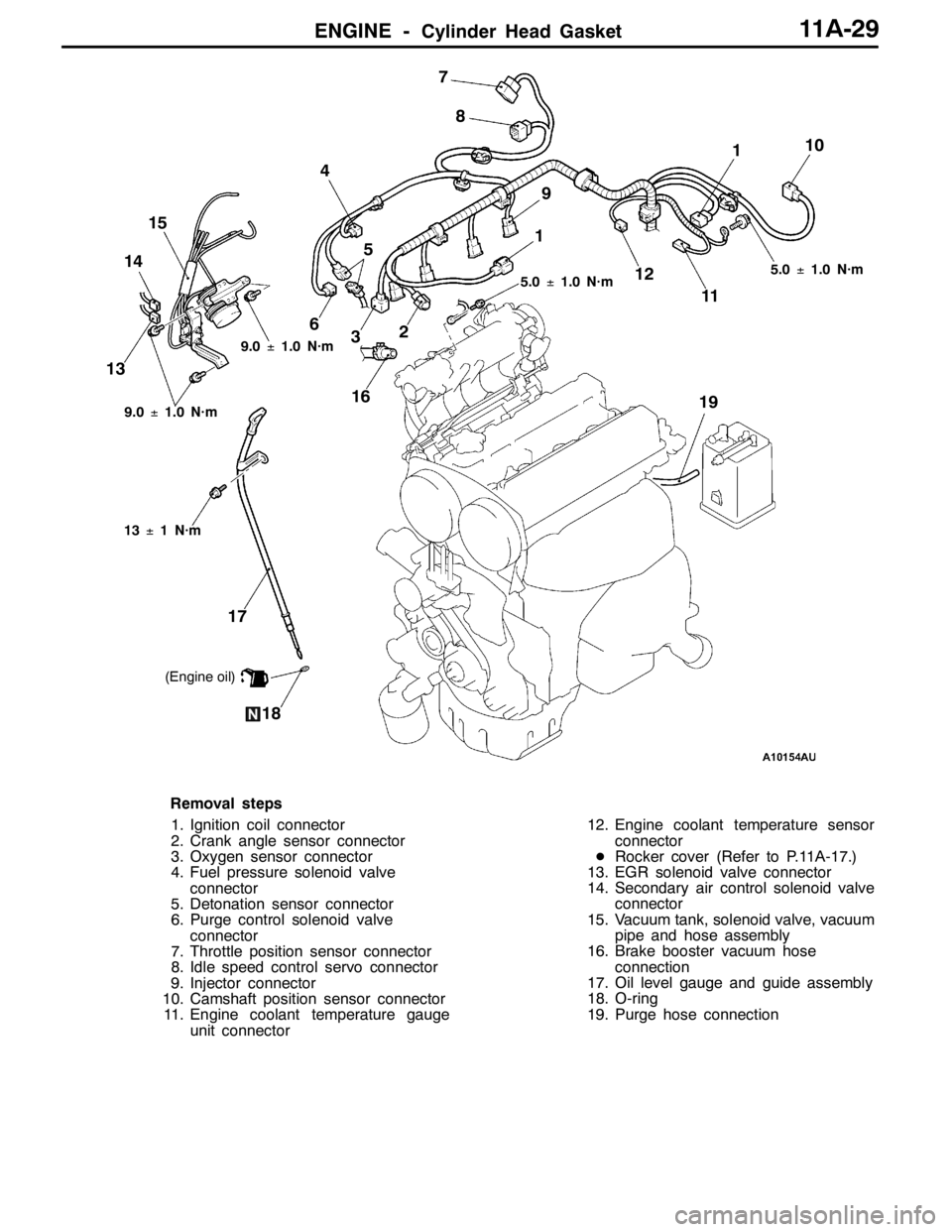
ENGINE -Cylinder Head Gasket11A-29
5.0±1.0 N·m
61
2
3 4
57
8
910
11 12
1314
13±1 N·m
15
16
17
5.0±1.0 N·m
1819
9.0±1.0 N·m
9.0±1.0 N·m
(Engine oil)
1
Removal steps
1. Ignition coil connector
2. Crank angle sensor connector
3. Oxygen sensor connector
4. Fuel pressure solenoid valve
connector
5. Detonation sensor connector
6. Purge control solenoid valve
connector
7. Throttle position sensor connector
8. Idle speed control servo connector
9. Injector connector
10. Camshaft position sensor connector
11. Engine coolant temperature gauge
unit connector12. Engine coolant temperature sensor
connector
DRocker cover (Refer to P.11A-17.)
13. EGR solenoid valve connector
14. Secondary air control solenoid valve
connector
15. Vacuum tank, solenoid valve, vacuum
pipe and hose assembly
16. Brake booster vacuum hose
connection
17. Oil level gauge and guide assembly
18. O-ring
19. Purge hose connection