sensor MITSUBISHI LANCER EVOLUTION 2007 Service Manual PDF
[x] Cancel search | Manufacturer: MITSUBISHI, Model Year: 2007, Model line: LANCER EVOLUTION, Model: MITSUBISHI LANCER EVOLUTION 2007Pages: 1449, PDF Size: 56.82 MB
Page 486 of 1449
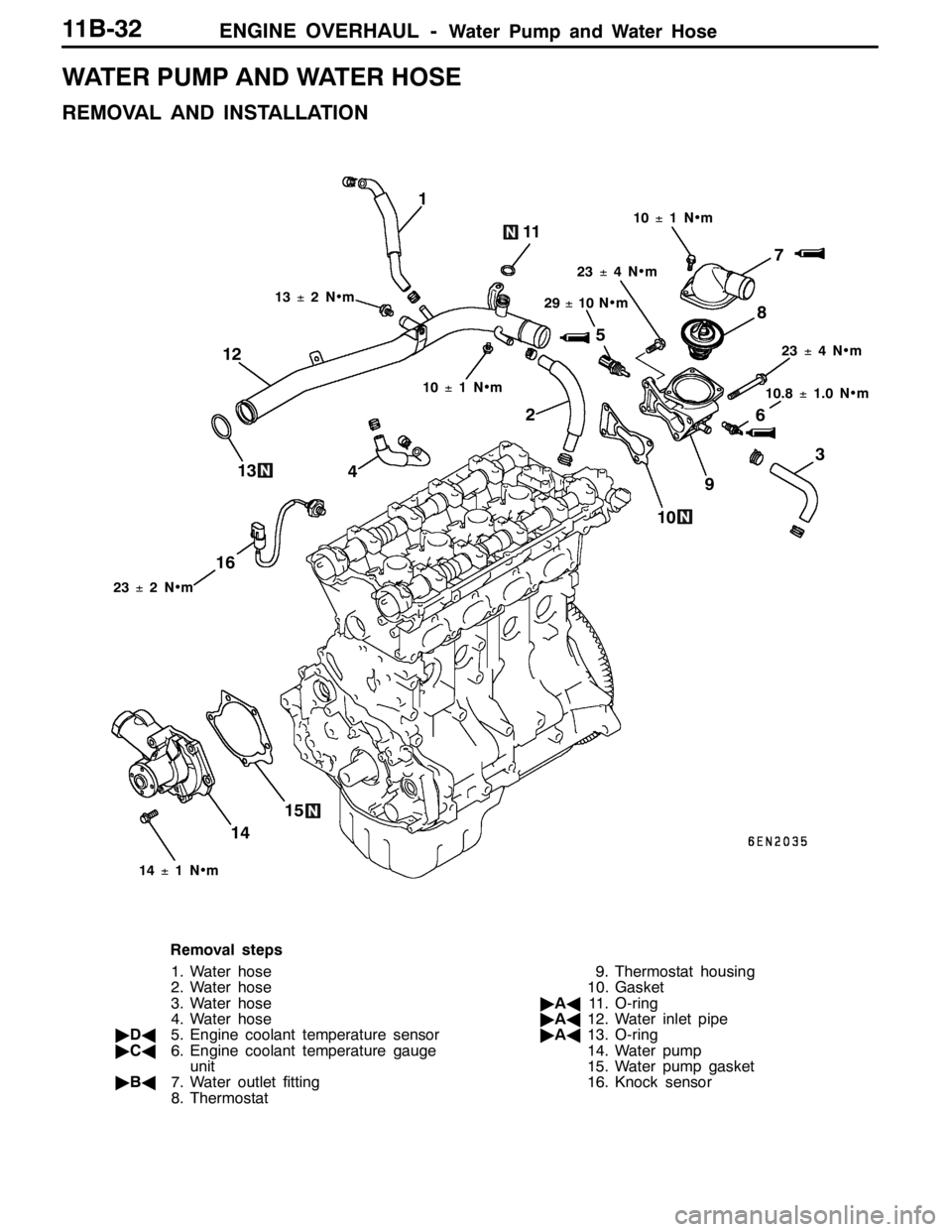
ENGINE OVERHAUL -Water Pump and Water Hose11B-32
WATER PUMP AND WATER HOSE
REMOVAL AND INSTALLATION
1
2
3
45
67
8
9
10 11
12
13
10±1N•m
14±1N•m 23±2N•m10±1N•m
13±2N•m10.8±1.0 N•m
29±10 N•m
1415 16
23±4N•m
23±4N•m
Removal steps
1. Water hose
2. Water hose
3. Water hose
4. Water hose
"DA5. Engine coolant temperature sensor
"CA6. Engine coolant temperature gauge
unit
"BA7. Water outlet fitting
8. Thermostat9. Thermostat housing
10. Gasket
"AA11. O-ring
"AA12. Water inlet pipe
"AA13. O-ring
14. Water pump
15. Water pump gasket
16. Knock sensor
Page 487 of 1449
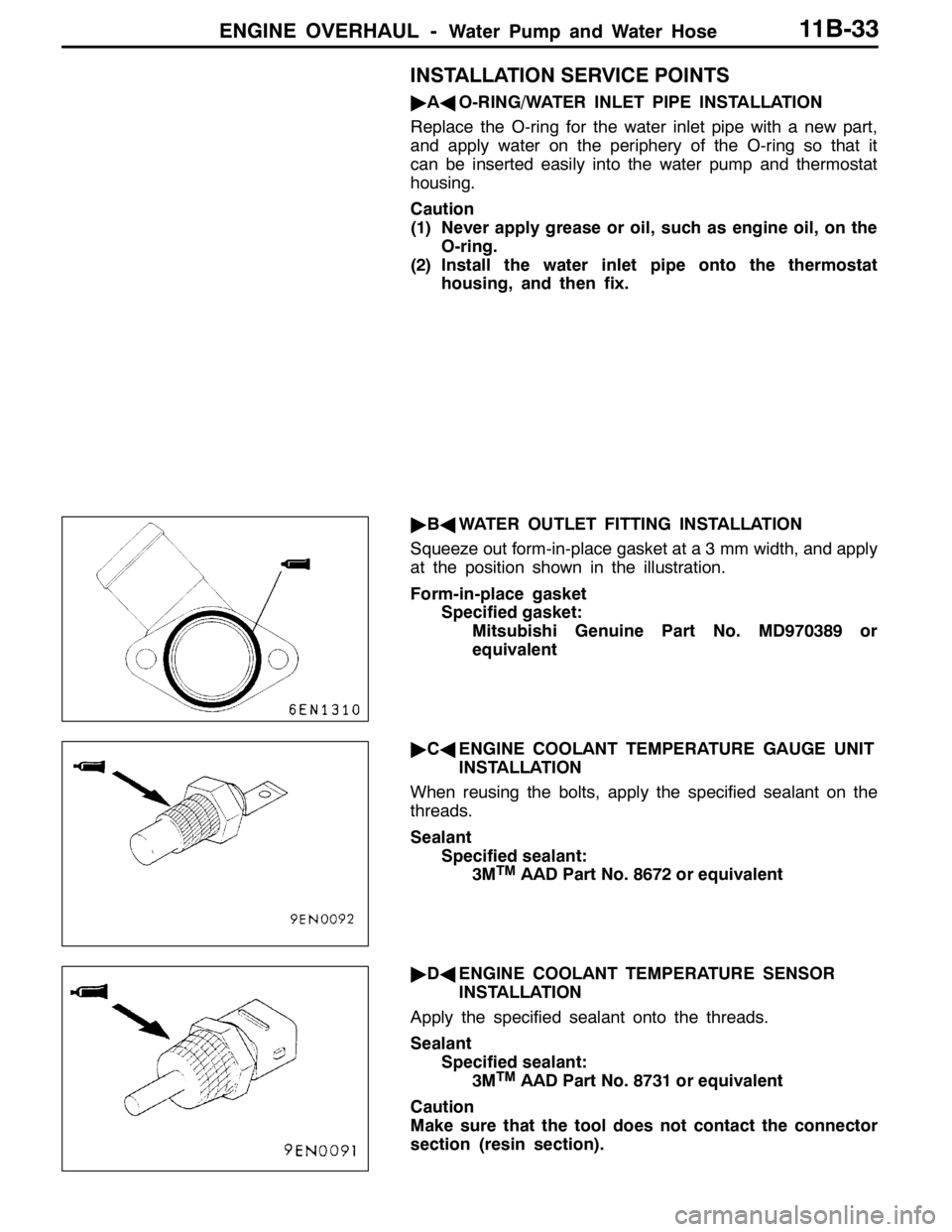
ENGINE OVERHAUL -Water Pump and Water Hose11B-33
INSTALLATION SERVICE POINTS
"AAO-RING/WATER INLET PIPE INSTALLATION
Replace the O-ring for the water inlet pipe with a new part,
and apply water on the periphery of the O-ring so that it
can be inserted easily into the water pump and thermostat
housing.
Caution
(1) Never apply grease or oil, such as engine oil, on the
O-ring.
(2) Install the water inlet pipe onto the thermostat
housing, and then fix.
"BAWATER OUTLET FITTING INSTALLATION
Squeeze out form-in-place gasket at a 3 mm width, and apply
at the position shown in the illustration.
Form-in-place gasket
Specified gasket:
Mitsubishi Genuine Part No. MD970389 or
equivalent
"CAENGINE COOLANT TEMPERATURE GAUGE UNIT
INSTALLATION
When reusing the bolts, apply the specified sealant on the
threads.
Sealant
Specified sealant:
3M
TMAAD Part No. 8672 or equivalent
"DAENGINE COOLANT TEMPERATURE SENSOR
INSTALLATION
Apply the specified sealant onto the threads.
Sealant
Specified sealant:
3M
TMAAD Part No. 8731 or equivalent
Caution
Make sure that the tool does not contact the connector
section (resin section).
Page 488 of 1449
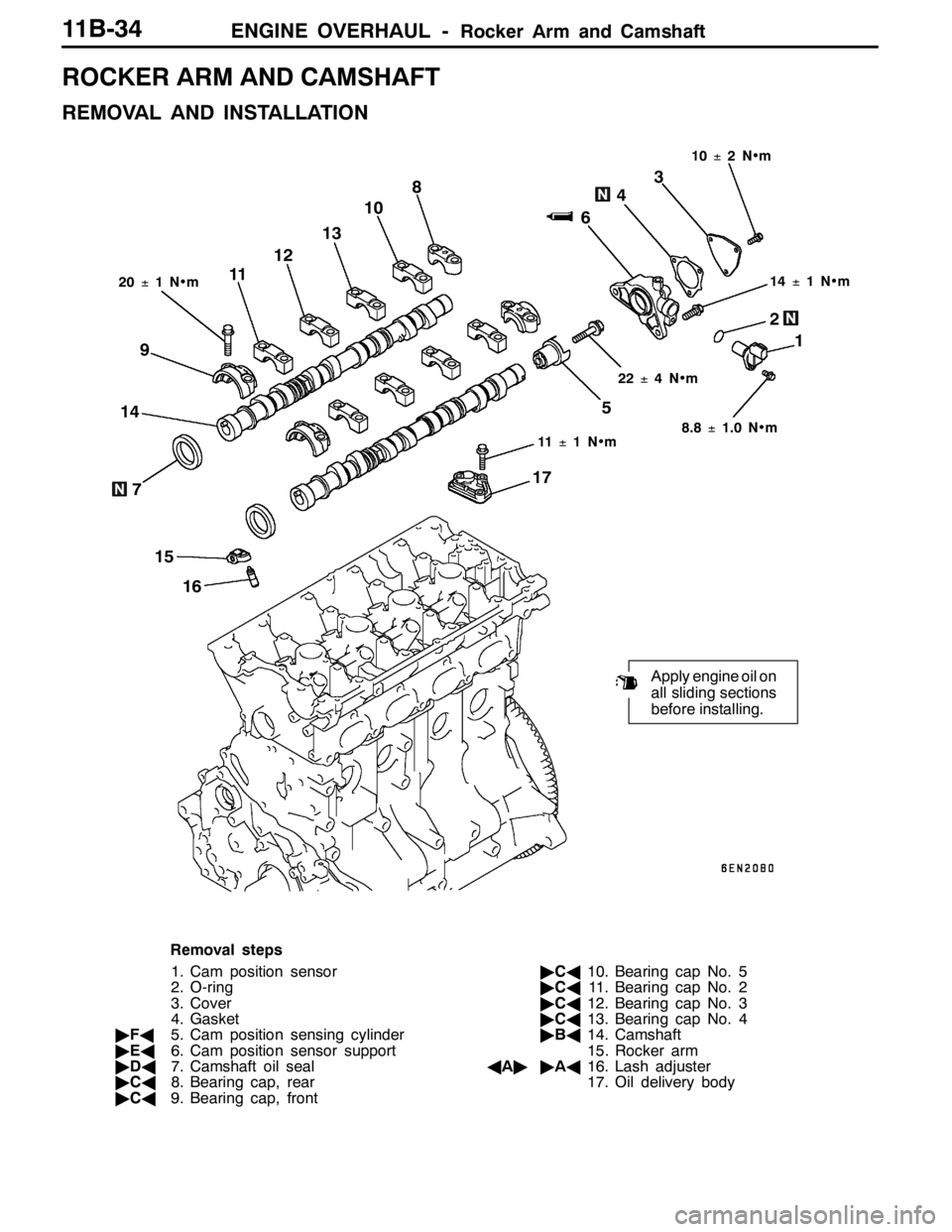
ENGINE OVERHAUL -Rocker Arm and Camshaft11B-34
ROCKER ARM AND CAMSHAFT
REMOVAL AND INSTALLATION
1 2 3
4
5 6
78
910
111213
10±2N•m
14±1N•m
22±4N•m
11±1N•m
8.8±1.0 N•m
20±1N•m
14
15
16
Apply engine oil on
all sliding sections
before installing.
17
Removal steps
1. Cam position sensor
2. O-ring
3. Cover
4. Gasket
"FA5. Cam position sensing cylinder
"EA6. Cam position sensor support
"DA7. Camshaft oil seal
"CA8. Bearing cap, rear
"CA9. Bearing cap, front"CA10. Bearing cap No. 5
"CA11. Bearing cap No. 2
"CA12. Bearing cap No. 3
"CA13. Bearing cap No. 4
"BA14. Camshaft
15. Rocker arm
AA""AA16. Lash adjuster
17. Oil delivery body
Page 490 of 1449
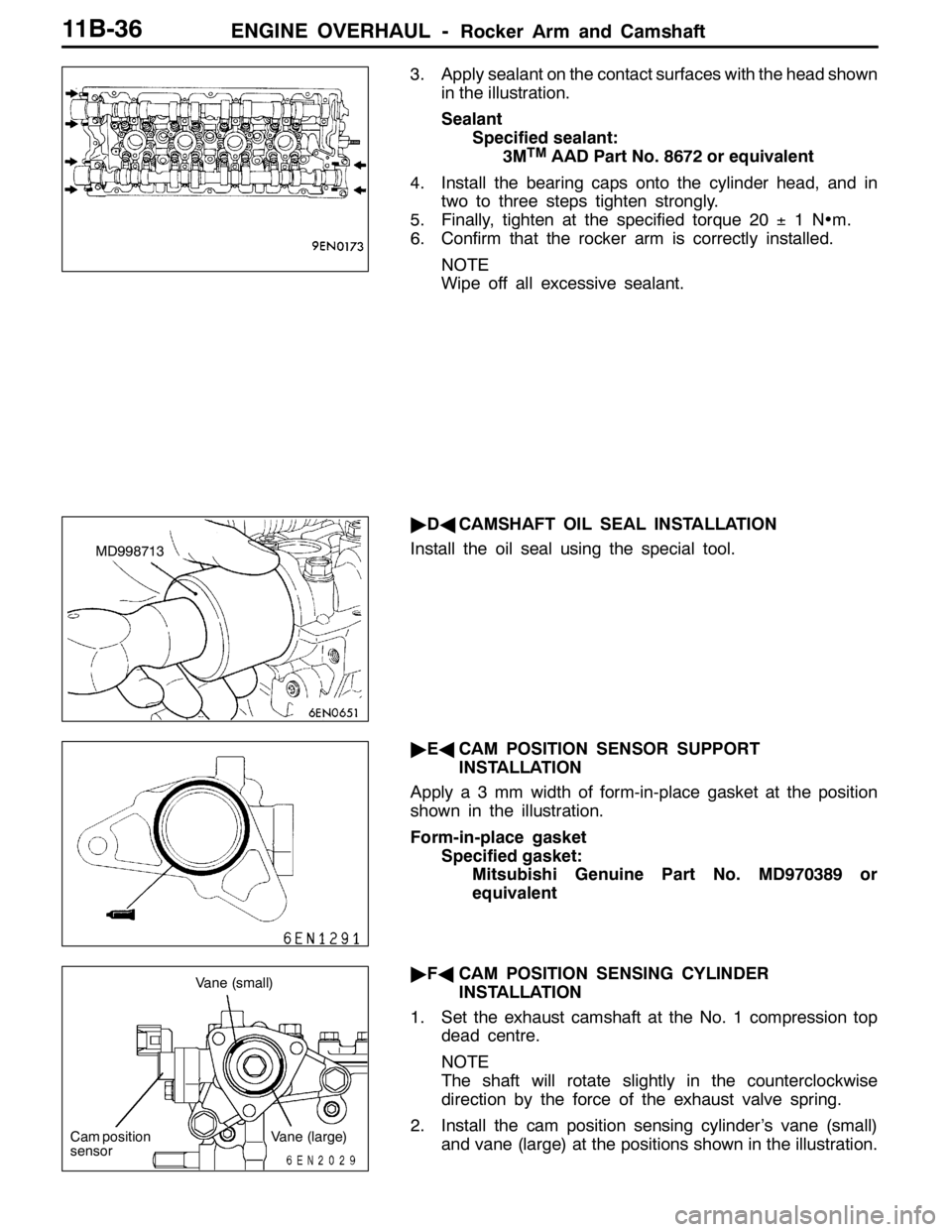
ENGINE OVERHAUL -Rocker Arm and Camshaft11B-36
3. Apply sealant on the contact surfaces with the head shown
in the illustration.
Sealant
Specified sealant:
3M
TMAAD Part No. 8672 or equivalent
4. Install the bearing caps onto the cylinder head, and in
two to three steps tighten strongly.
5. Finally, tighten at the specified torque 20±1N•m.
6. Confirm that the rocker arm is correctly installed.
NOTE
Wipe off all excessive sealant.
"DACAMSHAFT OIL SEAL INSTALLATION
Install the oil seal using the special tool.
"EACAM POSITION SENSOR SUPPORT
INSTALLATION
Apply a 3 mm width of form-in-place gasket at the position
shown in the illustration.
Form-in-place gasket
Specified gasket:
Mitsubishi Genuine Part No. MD970389 or
equivalent
"FACAM POSITION SENSING CYLINDER
INSTALLATION
1. Set the exhaust camshaft at the No. 1 compression top
dead centre.
NOTE
The shaft will rotate slightly in the counterclockwise
direction by the force of the exhaust valve spring.
2. Install the cam position sensing cylinder’s vane (small)
and vane (large) at the positions shown in the illustration.
MD998713
Vane (small)
Cam position
sensorVane (large)
Page 534 of 1449
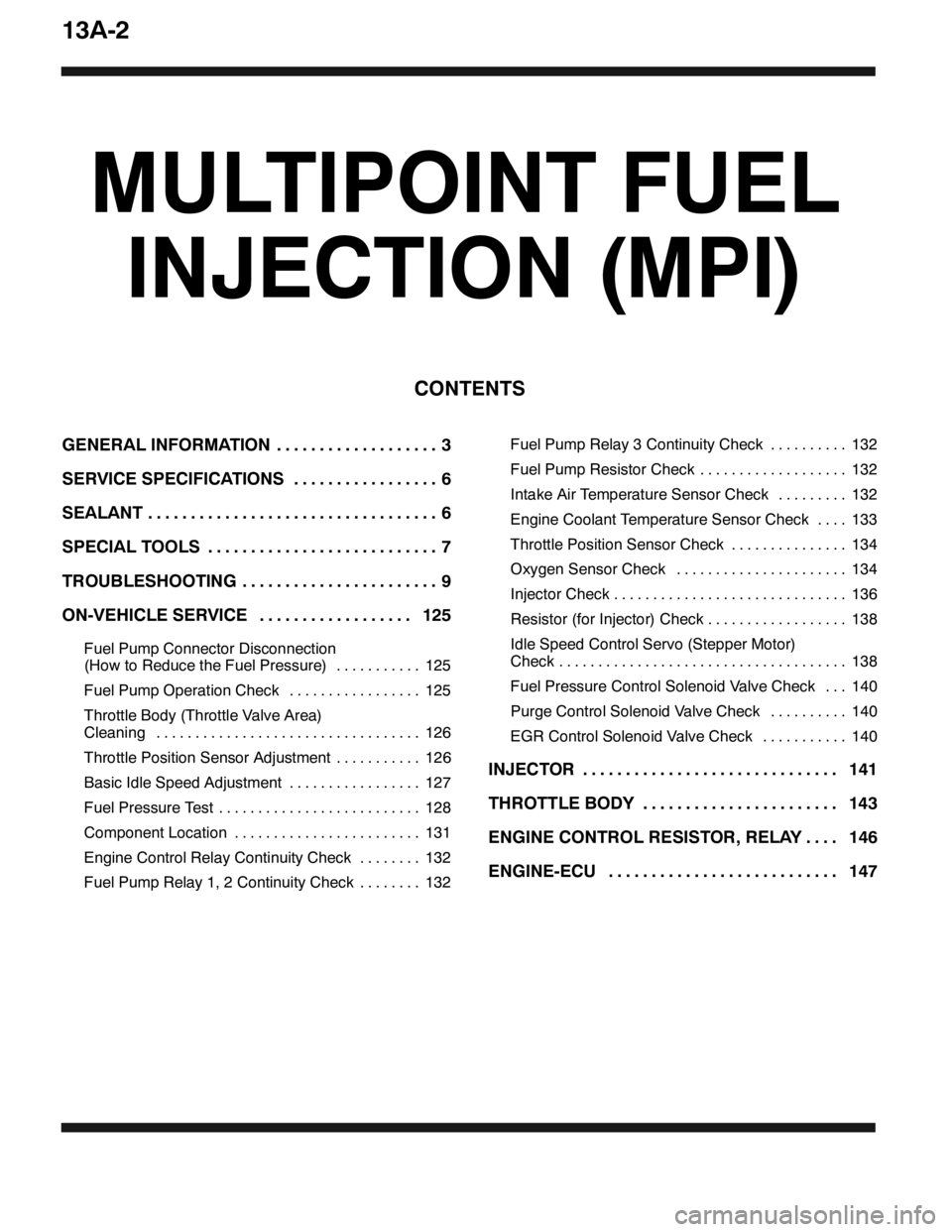
13A-2
MULTIPOINT FUEL
INJECTION (MPI)
CONTENTS
GENERAL INFORMATION 3...................
SERVICE SPECIFICATIONS 6.................
SEALANT 6..................................
SPECIAL TOOLS 7...........................
TROUBLESHOOTING 9.......................
ON-VEHICLE SERVICE 125..................
Fuel Pump Connector Disconnection
(How to Reduce the Fuel Pressure) 125...........
Fuel Pump Operation Check 125.................
Throttle Body (Throttle Valve Area)
Cleaning 126..................................
Throttle Position Sensor Adjustment 126...........
Basic Idle Speed Adjustment 127.................
Fuel Pressure Test 128..........................
Component Location 131........................
Engine Control Relay Continuity Check 132........
Fuel Pump Relay 1, 2 Continuity Check 132........Fuel Pump Relay 3 Continuity Check 132..........
Fuel Pump Resistor Check 132...................
Intake Air Temperature Sensor Check 132.........
Engine Coolant Temperature Sensor Check 133....
Throttle Position Sensor Check 134...............
Oxygen Sensor Check 134......................
Injector Check 136..............................
Resistor (for Injector) Check 138..................
Idle Speed Control Servo (Stepper Motor)
Check 138.....................................
Fuel Pressure Control Solenoid Valve Check 140...
Purge Control Solenoid Valve Check 140..........
EGR Control Solenoid Valve Check 140...........
INJECTOR 141..............................
THROTTLE BODY 143.......................
ENGINE CONTROL RESISTOR, RELAY 146....
ENGINE-ECU 147...........................
Page 535 of 1449
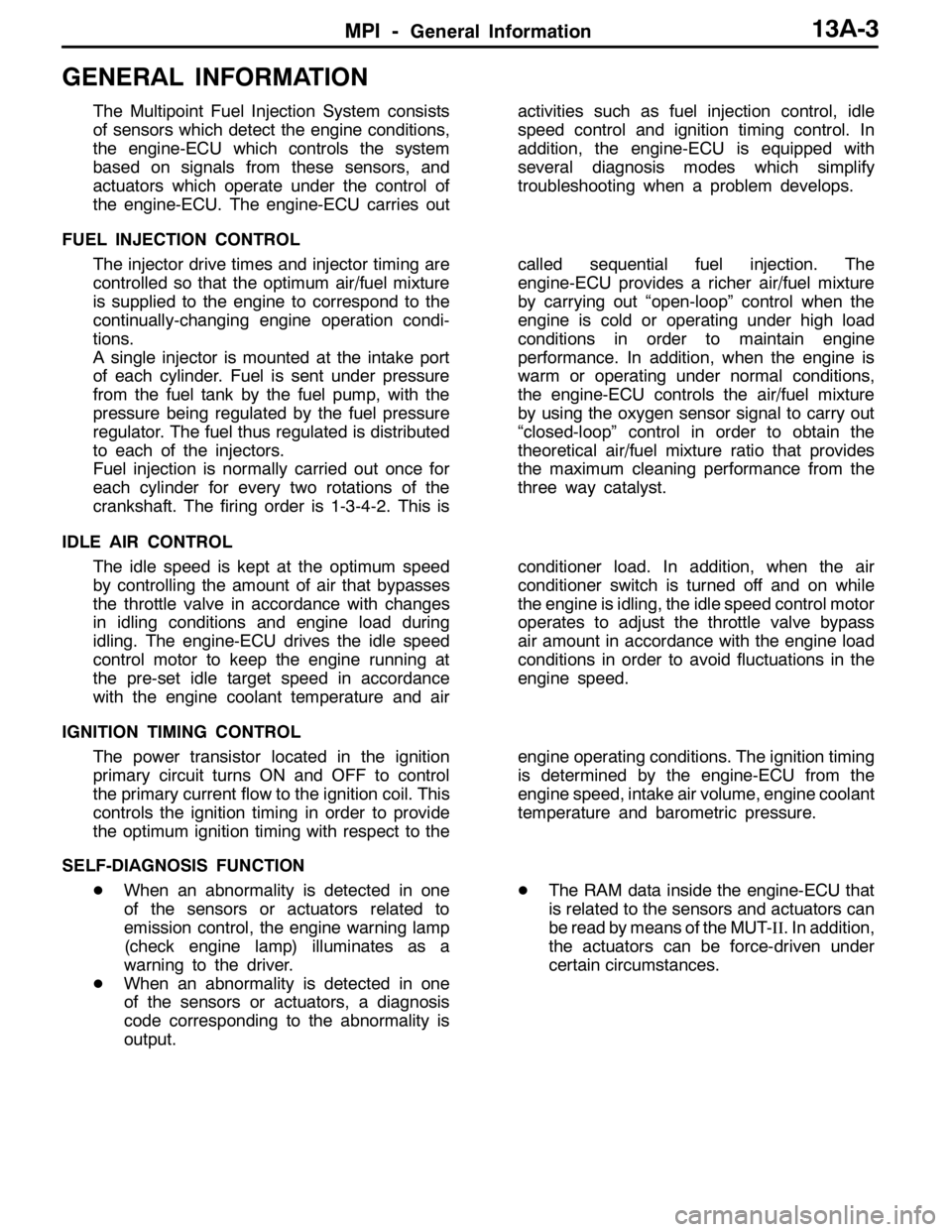
MPI -General Information13A-3
GENERAL INFORMATION
The Multipoint Fuel Injection System consists
of sensors which detect the engine conditions,
the engine-ECU which controls the system
based on signals from these sensors, and
actuators which operate under the control of
the engine-ECU. The engine-ECU carries outactivities such as fuel injection control, idle
speed control and ignition timing control. In
addition, the engine-ECU is equipped with
several diagnosis modes which simplify
troubleshooting when a problem develops.
FUEL INJECTION CONTROL
The injector drive times and injector timing are
controlled so that the optimum air/fuel mixture
is supplied to the engine to correspond to the
continually-changing engine operation condi-
tions.
A single injector is mounted at the intake port
of each cylinder. Fuel is sent under pressure
from the fuel tank by the fuel pump, with the
pressure being regulated by the fuel pressure
regulator. The fuel thus regulated is distributed
to each of the injectors.
Fuel injection is normally carried out once for
each cylinder for every two rotations of the
crankshaft. The firing order is 1-3-4-2. This iscalled sequential fuel injection. The
engine-ECU provides a richer air/fuel mixture
by carrying out “open-loop” control when the
engine is cold or operating under high load
conditions in order to maintain engine
performance. In addition, when the engine is
warm or operating under normal conditions,
the engine-ECU controls the air/fuel mixture
by using the oxygen sensor signal to carry out
“closed-loop” control in order to obtain the
theoretical air/fuel mixture ratio that provides
the maximum cleaning performance from the
three way catalyst.
IDLE AIR CONTROL
The idle speed is kept at the optimum speed
by controlling the amount of air that bypasses
the throttle valve in accordance with changes
in idling conditions and engine load during
idling. The engine-ECU drives the idle speed
control motor to keep the engine running at
the pre-set idle target speed in accordance
with the engine coolant temperature and airconditioner load. In addition, when the air
conditioner switch is turned off and on while
the engine is idling, the idle speed control motor
operates to adjust the throttle valve bypass
air amount in accordance with the engine load
conditions in order to avoid fluctuations in the
engine speed.
IGNITION TIMING CONTROL
The power transistor located in the ignition
primary circuit turns ON and OFF to control
the primary current flow to the ignition coil. This
controls the ignition timing in order to provide
the optimum ignition timing with respect to theengine operating conditions. The ignition timing
is determined by the engine-ECU from the
engine speed, intake air volume, engine coolant
temperature and barometric pressure.
SELF-DIAGNOSIS FUNCTION
DWhen an abnormality is detected in one
of the sensors or actuators related to
emission control, the engine warning lamp
(check engine lamp) illuminates as a
warning to the driver.
DWhen an abnormality is detected in one
of the sensors or actuators, a diagnosis
code corresponding to the abnormality is
output.DThe RAM data inside the engine-ECU that
is related to the sensors and actuators can
be read by means of the MUT-II. In addition,
the actuators can be force-driven under
certain circumstances.
Page 536 of 1449
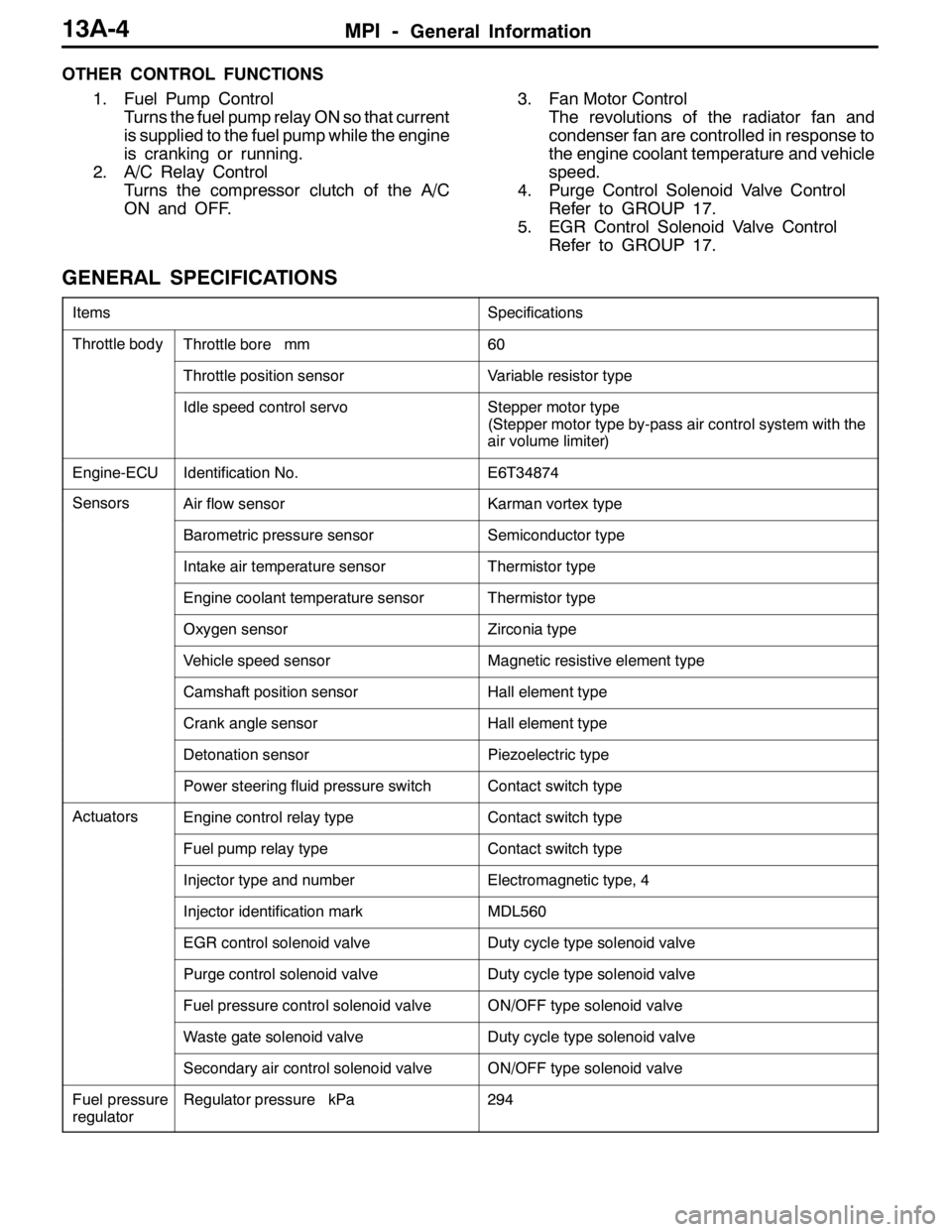
MPI -General Information13A-4
OTHER CONTROL FUNCTIONS
1. Fuel Pump Control
Turns the fuel pump relay ON so that current
is supplied to the fuel pump while the engine
is cranking or running.
2. A/C Relay Control
Turns the compressor clutch of the A/C
ON and OFF.3. Fan Motor Control
The revolutions of the radiator fan and
condenser fan are controlled in response to
the engine coolant temperature and vehicle
speed.
4. Purge Control Solenoid Valve Control
Refer to GROUP 17.
5. EGR Control Solenoid Valve Control
Refer to GROUP 17.
GENERAL SPECIFICATIONS
ItemsSpecifications
Throttle bodyThrottle bore mm60
Throttle position sensorVariable resistor type
Idle speed control servoStepper motor type
(Stepper motor type by-pass air control system with the
air volume limiter)
Engine-ECUIdentification No.E6T34874
SensorsAir flow sensorKarman vortex type
Barometric pressure sensorSemiconductor type
Intake air temperature sensorThermistor type
Engine coolant temperature sensorThermistor type
Oxygen sensorZirconia type
Vehicle speed sensorMagnetic resistive element type
Camshaft position sensorHall element type
Crank angle sensorHall element type
Detonation sensorPiezoelectric type
Power steering fluid pressure switchContact switch type
ActuatorsEngine control relay typeContact switch type
Fuel pump relay typeContact switch type
Injector type and numberElectromagnetic type, 4
Injector identification markMDL560
EGR control solenoid valveDuty cycle type solenoid valve
Purge control solenoid valveDuty cycle type solenoid valve
Fuel pressure control solenoid valveON/OFF type solenoid valve
Waste gate solenoid valveDuty cycle type solenoid valve
Secondary air control solenoid valveON/OFF type solenoid valve
Fuel pressure
regulatorRegulator pressure kPa294
Page 537 of 1449
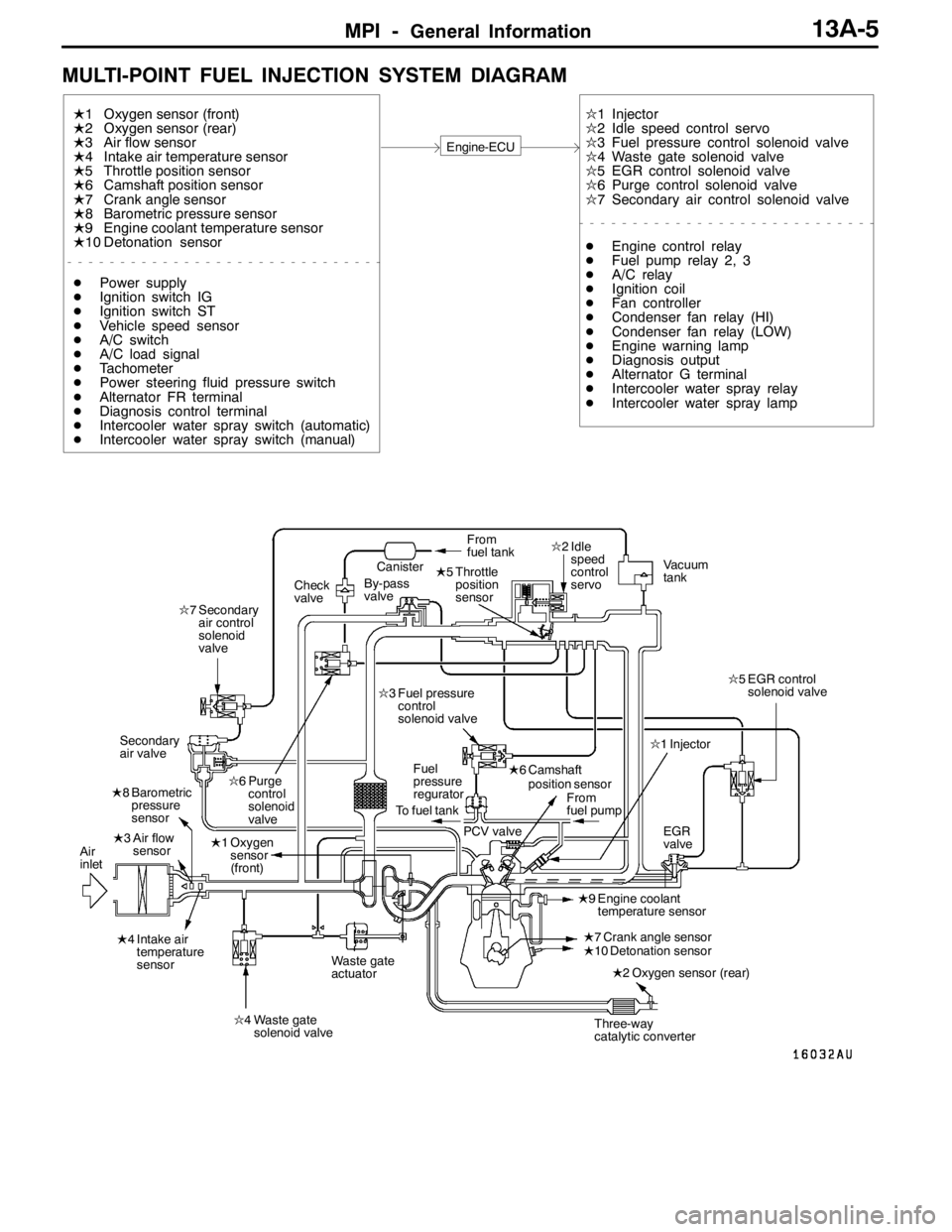
MPI -General Information13A-5
MULTI-POINT FUEL INJECTION SYSTEM DIAGRAM
L1 Oxygen sensor (front)
L2 Oxygen sensor (rear)
L3 Air flow sensor
L4 Intake air temperature sensor
L5 Throttle position sensor
L6 Camshaft position sensor
L7 Crank angle sensor
L8 Barometric pressure sensor
L9 Engine coolant temperature sensor
L10 Detonation sensor
Engine-ECU
l1 Injector
l2 Idle speed control servo
l3 Fuel pressure control solenoid valve
l4 Waste gate solenoid valve
l5 EGR control solenoid valve
l6 Purge control solenoid valve
l7 Secondary air control solenoid valve
DPower supply
DIgnition switch IG
DIgnition switch ST
DVehicle speed sensor
DA/C switch
DA/C load signal
DTachometer
DPower steering fluid pressure switch
DAlternator FR terminal
DDiagnosis control terminal
DIntercooler water spray switch (automatic)
DIntercooler water spray switch (manual)DEngine control relay
DFuel pump relay 2, 3
DA/C relay
DIgnition coil
DFan controller
DCondenser fan relay (HI)
DCondenser fan relay (LOW)
DEngine warning lamp
DDiagnosis output
DAlternator G terminal
DIntercooler water spray relay
DIntercooler water spray lamp
L1 Oxygen
sensor
(front)
L4 Intake air
temperature
sensorL5 Throttle
position
sensor
L6 Camshaft
position sensorl1 Injector l2 Idle
speed
control
servo
l6 Purge
control
solenoid
valve
Three-way
catalytic converter Canister
Air
inletVacuum
tank
Fuel
pressure
reguratorFrom
fuel tank
To fuel tank
PCV valveFrom
fuel pump
Waste gate
actuatorL2 Oxygen sensor (rear) Check
valveBy-pass
valve
l5 EGR control
solenoid valve
l4 Waste gate
solenoid valve L8 Barometric
pressure
sensor
L3 Air flow
sensorl7 Secondary
air control
solenoid
valve
Secondary
air valvel3 Fuel pressure
control
solenoid valve
EGR
valve
L9 Engine coolant
temperature sensor
L7 Crank angle sensor
L10 Detonation sensor
Page 538 of 1449
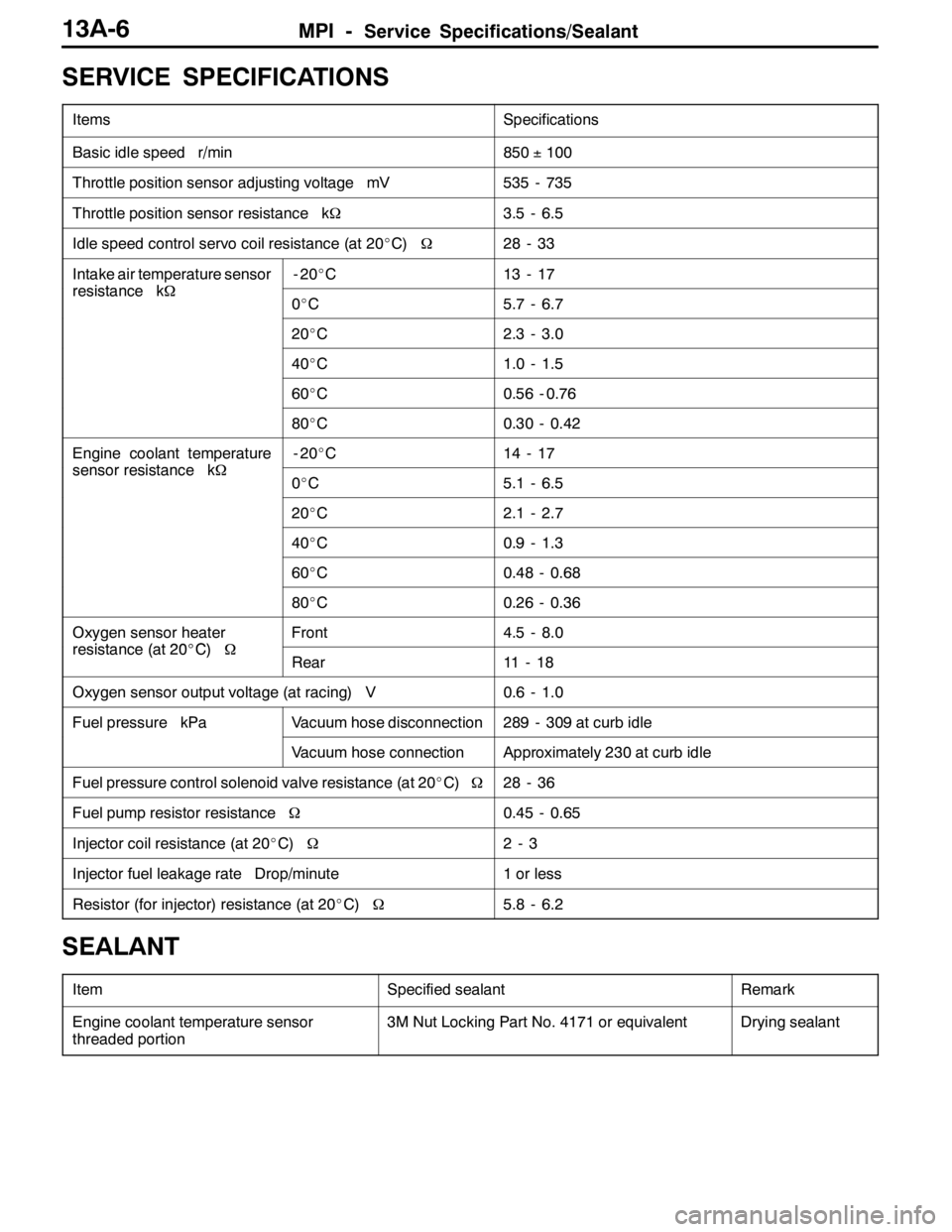
MPI -Service Specifications/Sealant13A-6
SERVICE SPECIFICATIONS
ItemsSpecifications
Basic idle speed r/min850±100
Throttle position sensor adjusting voltage mV535 - 735
Throttle position sensor resistance kΩ3.5 - 6.5
Idle speed control servo coil resistance (at 20_C)Ω28 - 33
Intake air temperature sensor
resistancekΩ
-20_C13 - 17
resistance kΩ0_C5.7 - 6.7
20_C2.3 - 3.0
40_C1.0 - 1.5
60_C0.56 - 0.76
80_C0.30 - 0.42
Engine coolant temperature
sensorresistancekΩ
-20_C14 - 17
sensor resistance kΩ0_C5.1 - 6.5
20_C2.1 - 2.7
40_C0.9 - 1.3
60_C0.48 - 0.68
80_C0.26 - 0.36
Oxygen sensor heater
resistance(at20_C)Ω
Front4.5 - 8.0
resistance (at 20_C)ΩRear11 - 1 8
Oxygen sensor output voltage (at racing) V0.6 - 1.0
Fuel pressure kPaVacuum hose disconnection289 - 309 at curb idle
Vacuum hose connectionApproximately 230 at curb idle
Fuel pressure control solenoid valve resistance (at 20_C)Ω28 - 36
Fuel pump resistor resistanceΩ0.45 - 0.65
Injector coil resistance (at 20_C)Ω2-3
Injector fuel leakage rate Drop/minute1 or less
Resistor (for injector) resistance (at 20_C)Ω5.8 - 6.2
SEALANT
ItemSpecified sealantRemark
Engine coolant temperature sensor
threaded portion3M Nut Locking Part No. 4171 or equivalentDrying sealant
Page 539 of 1449
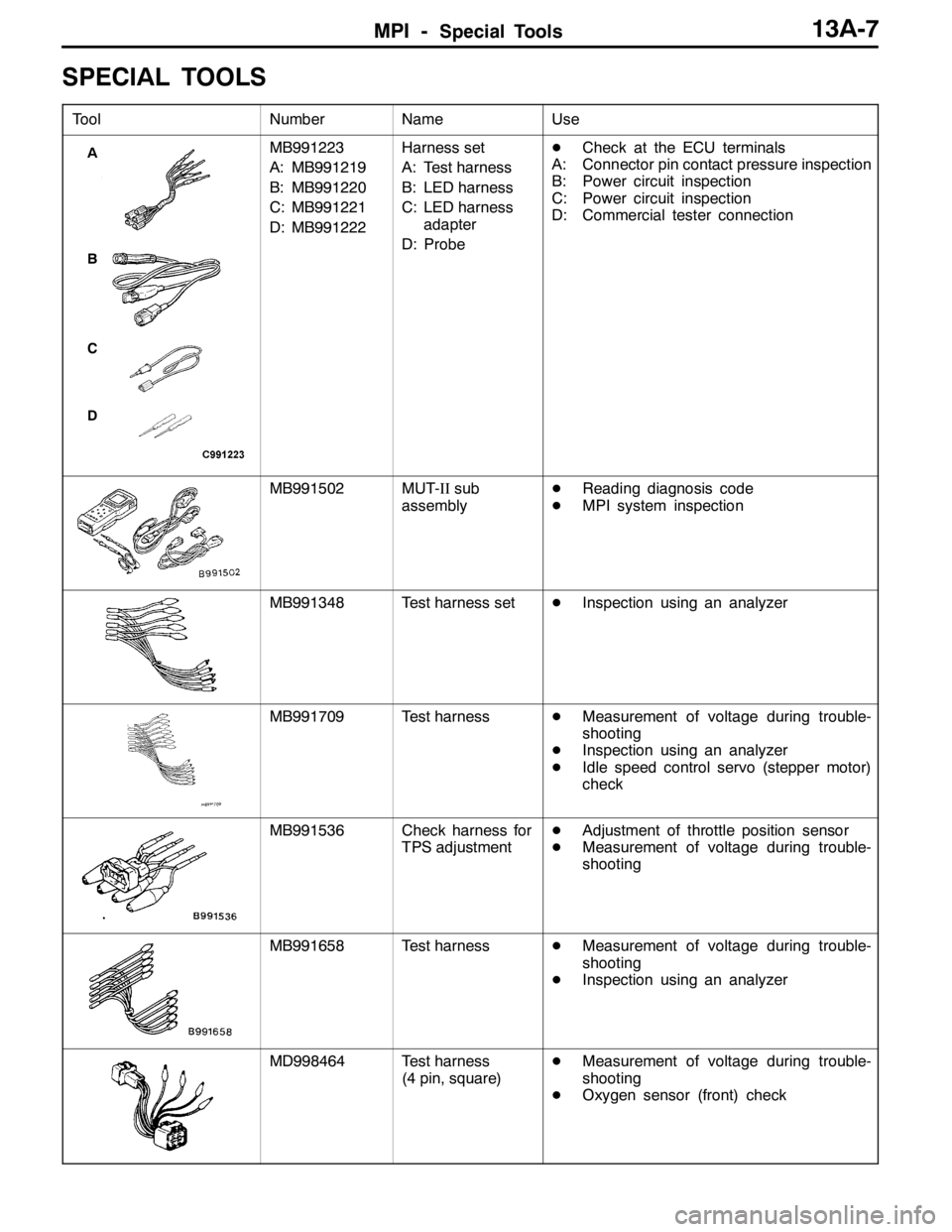
MPI -Special Tools13A-7
SPECIAL TOOLS
ToolNumberNameUse
B A
C
D
MB991223
A: MB991219
B: MB991220
C: MB991221
D: MB991222Harness set
A: Test harness
B: LED harness
C: LED harness
adapter
D: ProbeDCheck at the ECU terminals
A: Connector pin contact pressure inspection
B: Power circuit inspection
C: Power circuit inspection
D: Commercial tester connection
MB991502MUT-IIsub
assemblyDReading diagnosis code
DMPI system inspection
MB991348Test harness setDInspection using an analyzer
MB991709Test harnessDMeasurement of voltage during trouble-
shooting
DInspection using an analyzer
DIdle speed control servo (stepper motor)
check
MB991536Check harness for
TPS adjustmentDAdjustment of throttle position sensor
DMeasurement of voltage during trouble-
shooting
MB991658Test harnessDMeasurement of voltage during trouble-
shooting
DInspection using an analyzer
MD998464Test harness
(4 pin, square)DMeasurement of voltage during trouble-
shooting
DOxygen sensor (front) check