NISSAN PULSAR 1987 Service Manual
Manufacturer: NISSAN, Model Year: 1987, Model line: PULSAR, Model: NISSAN PULSAR 1987Pages: 238, PDF Size: 28.91 MB
Page 41 of 238
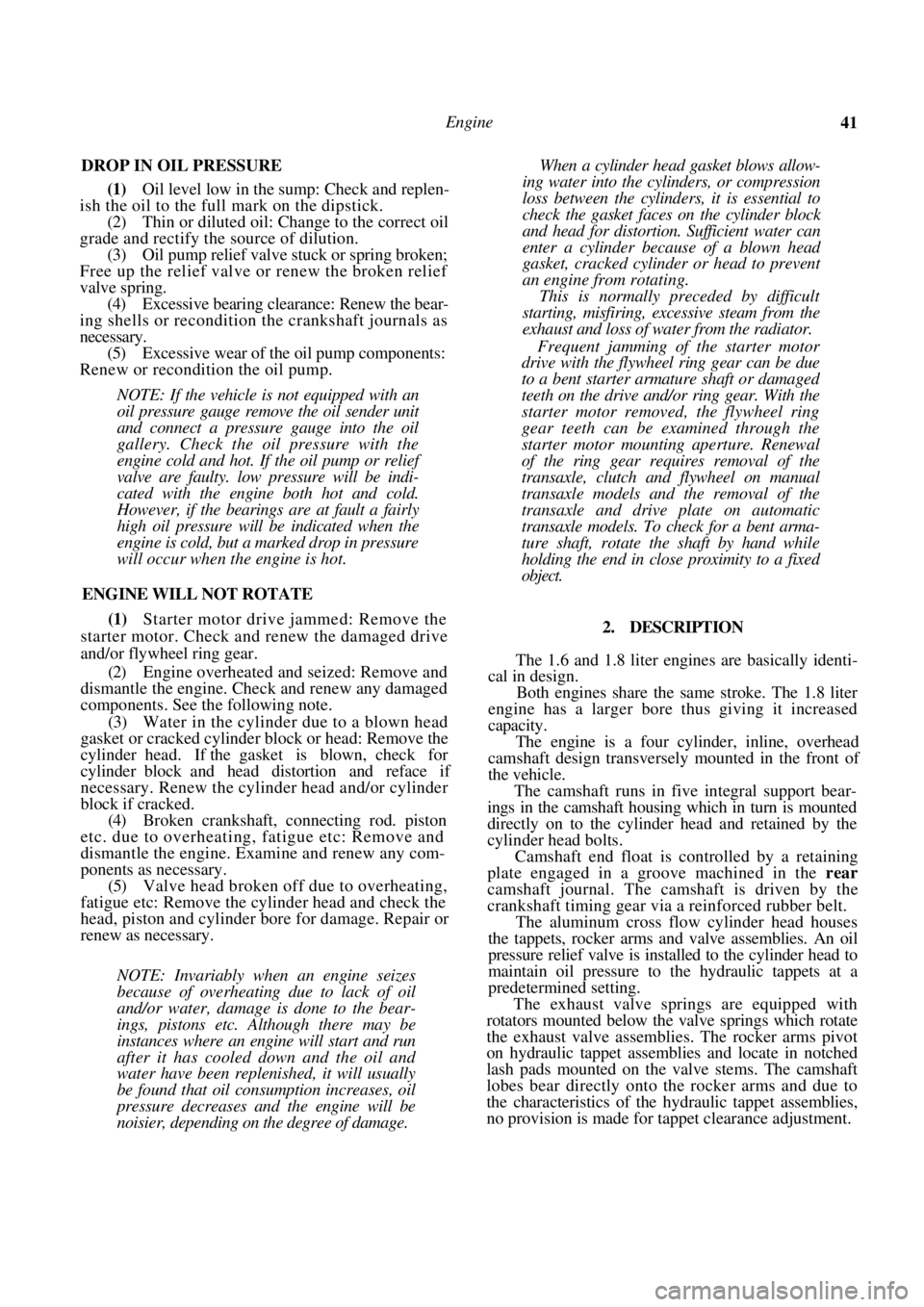
Engine 41
DROP IN OIL PRESSURE
(1) Oil level low in the sump: Check and replen-
ish the oil to the full mark on the dipstick.
(2) Thin or diluted oil: Change to the correct oil
grade and rectify the source of dilution. (3) Oil pump relief valve stuck or spring broken;
Free up the relief valve or renew the broken relief
valve spring. (4) Excessive bearing clearance: Renew the bear-
ing shells or recondition the crankshaft journals as
necessary.
(5) Excessive wear of the oil pump components:
Renew or recondition the oil pump.
NOTE: If the vehicle is not equipped with an
oil pressure gauge re move the oil sender unit
and connect a pressure gauge into the oil
gallery. Check the oil pressure with the
engine cold and hot. If the oil pump or relief
valve are faulty. low pressure will be indi-
cated with the engine both hot and cold.
However, if the bearings are at fault a fairly
high oil pressure will be indicated when the
engine is cold, but a marked drop in pressure
will occur when the engine is hot.
ENGINE WILL NOT ROTATE
(1) Starter motor drive jammed: Remove the
starter motor. Check and renew the damaged drive
and/or flywheel ring gear.
(2) Engine overheated an d seized: Remove and
dismantle the engine. Check and renew any damaged
components. See the following note.
(3) Water in the cylinder due to a blown head
gasket or cracked cylinder block or head: Remove the
cylinder head. If the gasket is blown, check for
cylinder block and head distortion and reface if
necessary. Renew the cylinder head and/or cylinder
block if cracked.
(4) Broken crankshaft, connecting rod. piston
etc. due to overheating, fatigue etc: Remove and
dismantle the engine. Examine and renew any com-
ponents as necessary. (5) Valve head broken off due to overheating,
fatigue etc: Remove the cylinder head and check the
head, piston and cylinder bore for damage. Repair or
renew as necessary.
NOTE: Invariably when an engine seizes
because of overheating due to lack of oil
and/or water, damage is done to the bear-
ings, pistons etc. Although there may be
instances where an engine will start and run
after it has cooled down and the oil and
water have been replenished, it will usually
be found that oil consumption increases, oil
pressure decreases and the engine will be
noisier, depending on the degree of damage.
When a cylinder head gasket blows allow-
ing water into the cylinders, or compression
loss between the cylinders, it is essential to
check the gasket faces on the cylinder block
and head for distortion. Sufficient water can
enter a cylinder because of a blown head
gasket, cracked cylinder or head to prevent
an engine from rotating.
This is normally preceded by difficult
starting, misfiring, excessive steam from the
exhaust and loss of water from the radiator.
Frequent jamming of the starter motor
drive with the flywheel ring gear can be due
to a bent starter armature shaft or damaged
teeth on the drive and/or ring gear. With the
starter motor removed, the flywheel ring
gear teeth can be examined through the
starter motor mounting aperture. Renewal
of the ring gear requires removal of the
transaxle, clutch and flywheel on manual
transaxle models and the removal of the
transaxle and drive plate on automatic
transaxle models. To check for a bent arma-
ture shaft, rotate the shaft by hand while
holding the end in close proximity to a fixed
object.
2. DESCRIPTION
The 1.6 and 1.8 liter engines are basically identi-
cal in design.
Both engines share the same stroke. The 1.8 liter
engine has a larger bore thus giving it increased
capacity.
The engine is a four cylinder, inline, overhead
camshaft design transversely mounted in the front of
the vehicle.
The camshaft runs in five integral support bear-
ings in the camshaft housing which in turn is mounted
directly on to the cylinder head and retained by the
cylinder head bolts.
Camshaft end float is controlled by a retaining
plate engaged in a groove machined in the rear
camshaft journal. The camshaft is driven by the
crankshaft timing gear vi a a reinforced rubber belt.
The aluminum cross flow cylinder head houses
the tappets, rocker arms a nd valve assemblies. An oil
pressure relief valve is installed to the cylinder head to
maintain oil pressure to the hydraulic tappets at a
predetermined setting.
The exhaust valve springs are equipped with
rotators mounted below the valve springs which rotate
the exhaust valve assemblies. The rocker arms pivot
on hydraulic tappet assemblies and locate in notched
lash pads mounted on the valve stems. The camshaft
lobes bear directly onto the rocker arms and due to
the characteristics of the hydraulic tappet assemblies,
no provision is made for tappet clearance adjustment.
Page 42 of 238
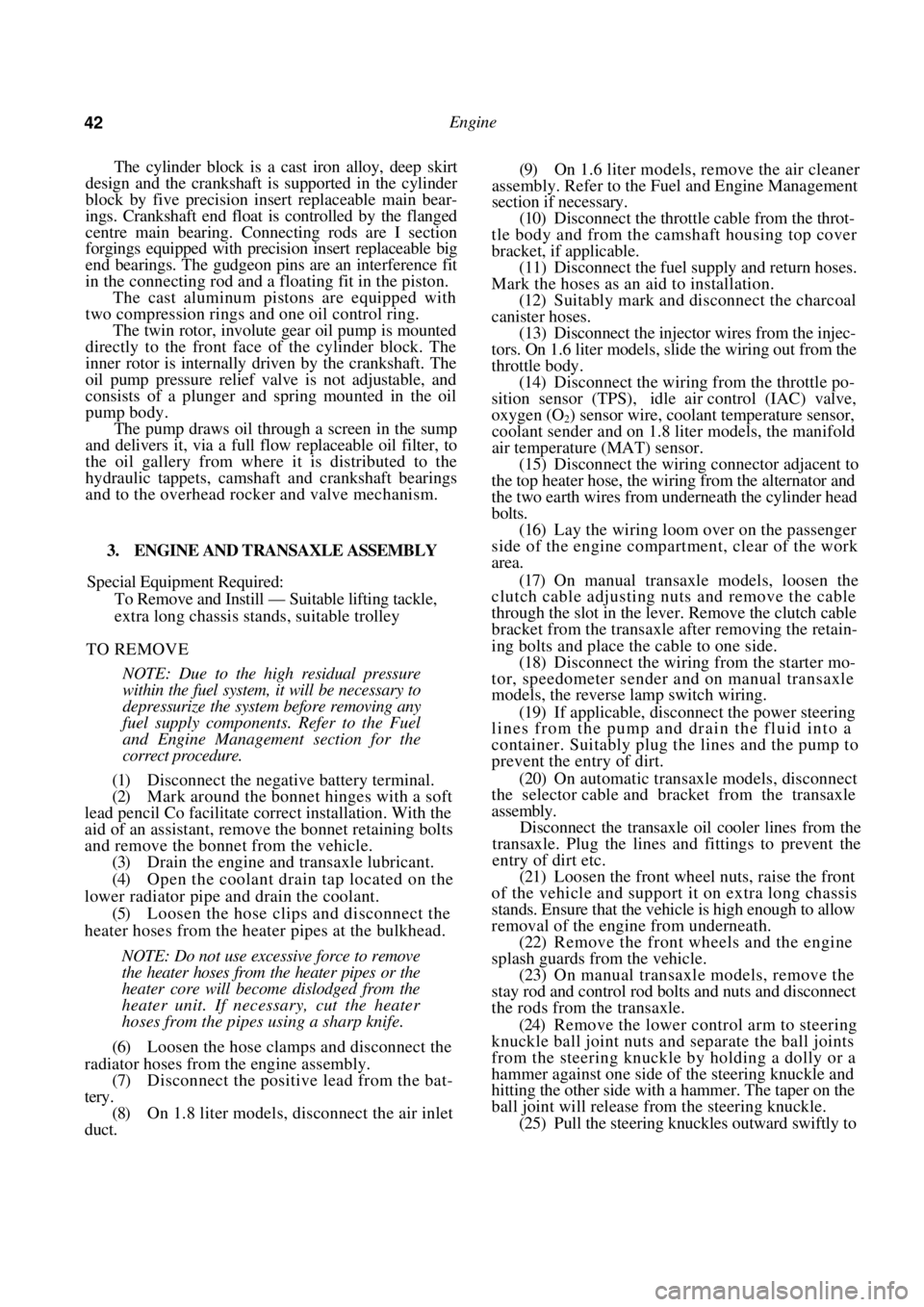
42 Engine
The cylinder block is a cast iron alloy, deep skirt
design and the crankshaft is supported in the cylinder
block by five precision insert replaceable main bear-
ings. Crankshaft end float is controlled by the flanged
centre main bearing. Connecting rods are I section
forgings equipped with precision insert replaceable big
end bearings. The gudgeon pins are an interference fit
in the connecting rod and a floating fit in the piston.
The cast aluminum pistons are equipped with
two compression rings and one oil control ring.
The twin rotor, involute gear oil pump is mounted
directly to the front face of the cylinder block. The
inner rotor is internally driven by the crankshaft. The
oil pump pressure relief valve is not adjustable, and
consists of a plunger and spring mounted in the oil
pump body.
The pump draws oil through a screen in the sump
and delivers it, via a full flow replaceable oil filter, to
the oil gallery from where it is distributed to the
hydraulic tappets, camshaft and crankshaft bearings
and to the overhead rocker and valve mechanism.
3. ENGINE AND TRANSAXLE ASSEMBLY
Special Equipment Required:
To Remove and Instill — Suitable lifting tackle,
extra long chassis stands, suitable trolley
TO REMOVE
NOTE: Due to the high residual pressure
within the fuel system, it will be necessary to
depressurize the system before removing any
fuel supply components. Refer to the Fuel
and Engine Management section for the
correct procedure.
(1) Disconnect the negative battery terminal.
(2) Mark around the bonnet hinges with a soft
lead pencil Co facilitate correct installation. With the
aid of an assistant, remove the bonnet retaining bolts
and remove the bonnet from the vehicle.
(3) Drain the engine and transaxle lubricant.
(4) Open the coolant drain tap located on the
lower radiator pipe and drain the coolant. (5) Loosen the hose clips and disconnect the
heater hoses from the heater pipes at the bulkhead.
NOTE: Do not use excessive force to remove
the heater hoses from the heater pipes or the
heater core will become dislodged from the
heater unit. If necessary, cut the heater
hoses from the pipes using a sharp knife.
(6) Loosen the hose clamps and disconnect the
radiator hoses from the engine assembly. (7) Disconnect the positive lead from the bat-
tery. (8) On 1.8 liter models, disconnect the air inlet
duct.
(9) On 1.6 liter models, remove the air cleaner
assembly. Refer to the Fuel and Engine Management
section if necessary. (10) Disconnect the throttle cable from the throt-
tle body and from the camshaft housing top cover
bracket, if applicable. (11) Disconnect the fuel supply and return hoses.
Mark the hoses as an aid to installation. (12) Suitably mark and disconnect the charcoal
canister hoses. (13) Disconnect the injector wires from the injec-
tors. On 1.6 liter models, slide the wiring out from the
throttle body. (14) Disconnect the wiring fr om the throttle po-
sition sensor (TPS), idle air control (IAC) valve,
oxygen (O
2) sensor wire, coolant temperature sensor,
coolant sender and on 1.8 liter models, the manifold
air temperature (MAT) sensor. (15) Disconnect the wiring connector adjacent to
the top heater hose, the wiring from the alternator and
the two earth wires from underneath the cylinder head
bolts. (16) Lay the wiring loom over on the passenger
side of the engine compar tment, clear of the work
area.
(17) On manual transaxle models, loosen the
clutch cable adjusting nuts and remove the cable
through the slot in the lever. Remove the clutch cable
bracket from the transaxle after removing the retain-
ing bolts and place the cable to one side.
(18) Disconnect the wiring from the starter mo-
tor, speedometer sender and on manual transaxle
models, the reverse lamp switch wiring.
(19) If applicable, disconnect the power steering
lines from the pump and drain the fluid into a
container. Suitably plug the lines and the pump to
prevent the entry of dirt.
(20) On automatic transaxle models, disconnect
the selector cable and bracket from the transaxle
assembly.
Disconnect the transaxle oil cooler lines from the
transaxle. Plug the lines and fittings to prevent the
entry of dirt etc.
(21) Loosen the front wheel nuts, raise the front
of the vehicle and support it on extra long chassis
stands. Ensure that the vehicle is high enough to allow
removal of the engine from underneath. (22) Remove the front wheels and the engine
splash guards from the vehicle.
(23) On manual transaxle models, remove the
stay rod and control rod bolts and nuts and disconnect
the rods from the transaxle.
(24) Remove the lower control arm to steering
knuckle ball joint nuts and separate the ball joints
from the steering knuckle by holding a dolly or a
hammer against one side of the steering knuckle and
hitting the other side with a hammer. The taper on the
ball joint will release fr om the steering knuckle.
(25) Pull the steering knuckles outward swiftly to
Page 43 of 238
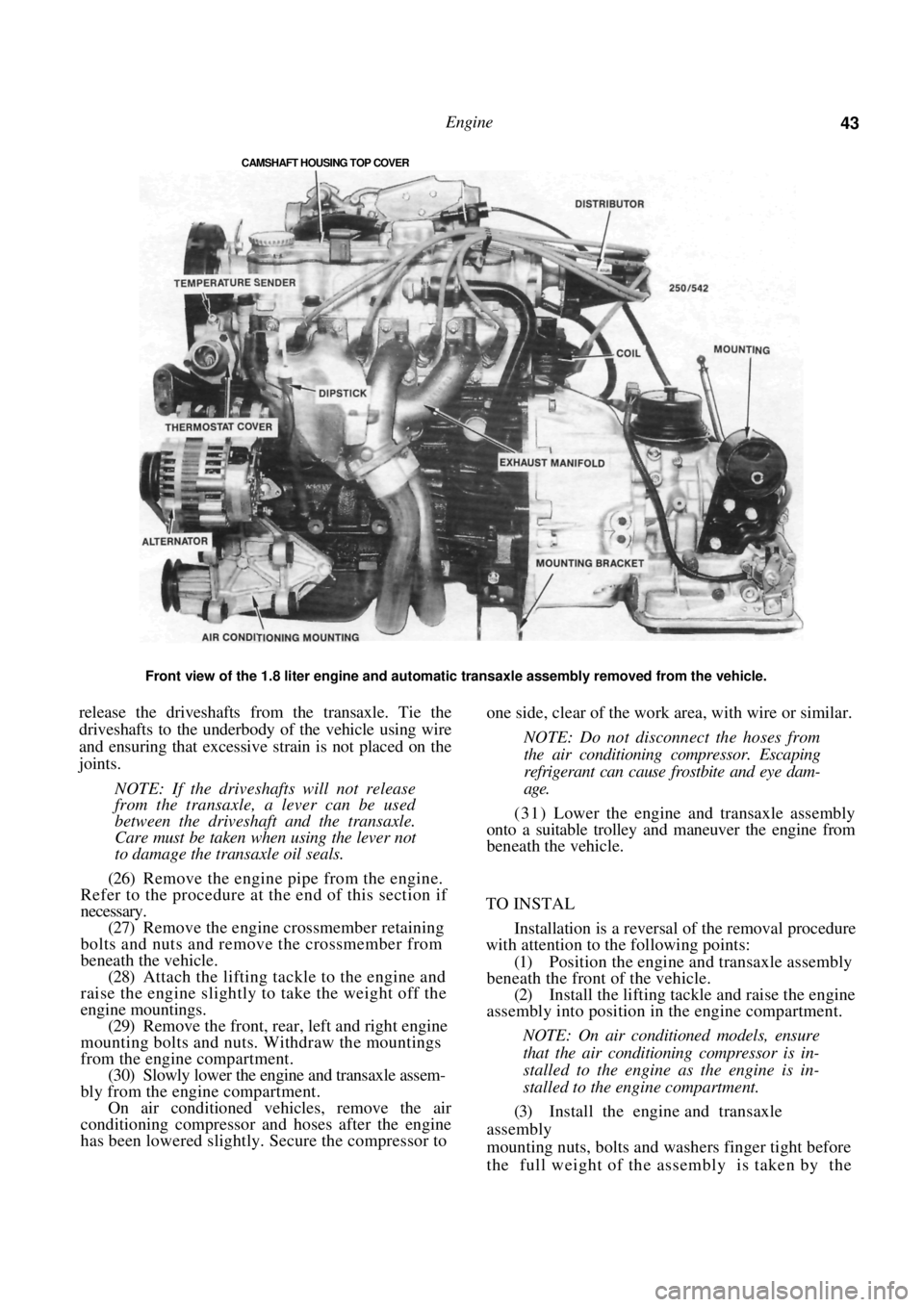
Engine 43
CAMSHAFT HOUSING TOP COVER
Front view of the 1.8 liter engine and automatic transaxle assembly removed from the vehicle.
release the driveshafts from the transaxle. Tie the
driveshafts to the underbody of the vehicle using wire
and ensuring that excessive st rain is not placed on the
joints.
NOTE: If the driveshafts will not release
from the transaxle, a lever can be used
between the driveshaft and the transaxle.
Care must be taken when using the lever not
to damage the transaxle oil seals.
(26) Remove the engine pipe from the engine.
Refer to the procedure at the end of this section if
necessary.
(27) Remove the engine crossmember retaining
bolts and nuts and remove the crossmember from
beneath the vehicle. (28) Attach the lifting tackle to the engine and
raise the engine slightly to take the weight off the
engine mountings. (29) Remove the front, rear, left and right engine
mounting bolts and nuts. Withdraw the mountings
from the engine compartment. (30) Slowly lower the engine and transaxle assem-
bly from the engine compartment. On air conditioned vehicles, remove the air
conditioning compressor an d hoses after the engine
has been lowered slightly. Secure the compressor to
one side, clear of the work area, with wire or similar.
NOTE: Do not disconnect the hoses from
the air conditioning compressor. Escaping
refrigerant can cause frostbite and eye dam-
age.
( 3 1 ) Lower the engine and transaxle assembly
onto a suitable trolley and maneuver the engine from
beneath the vehicle.
TO INSTAL
Installation is a reversal of the removal procedure
with attention to the following points:
(1) Position the engine and transaxle assembly
beneath the front of the vehicle.
(2) Install the lifting tackle and raise the engine
assembly into position in the engine compartment.
NOTE: On air conditioned models, ensure
that the air conditioning compressor is in-
stalled to the engine as the engine is in-
stalled to the engine compartment.
(3) Install the engine and transaxle
assembly
mounting nuts, bolts and washers finger tight before
the full weight of the assembly is taken by the
Page 44 of 238
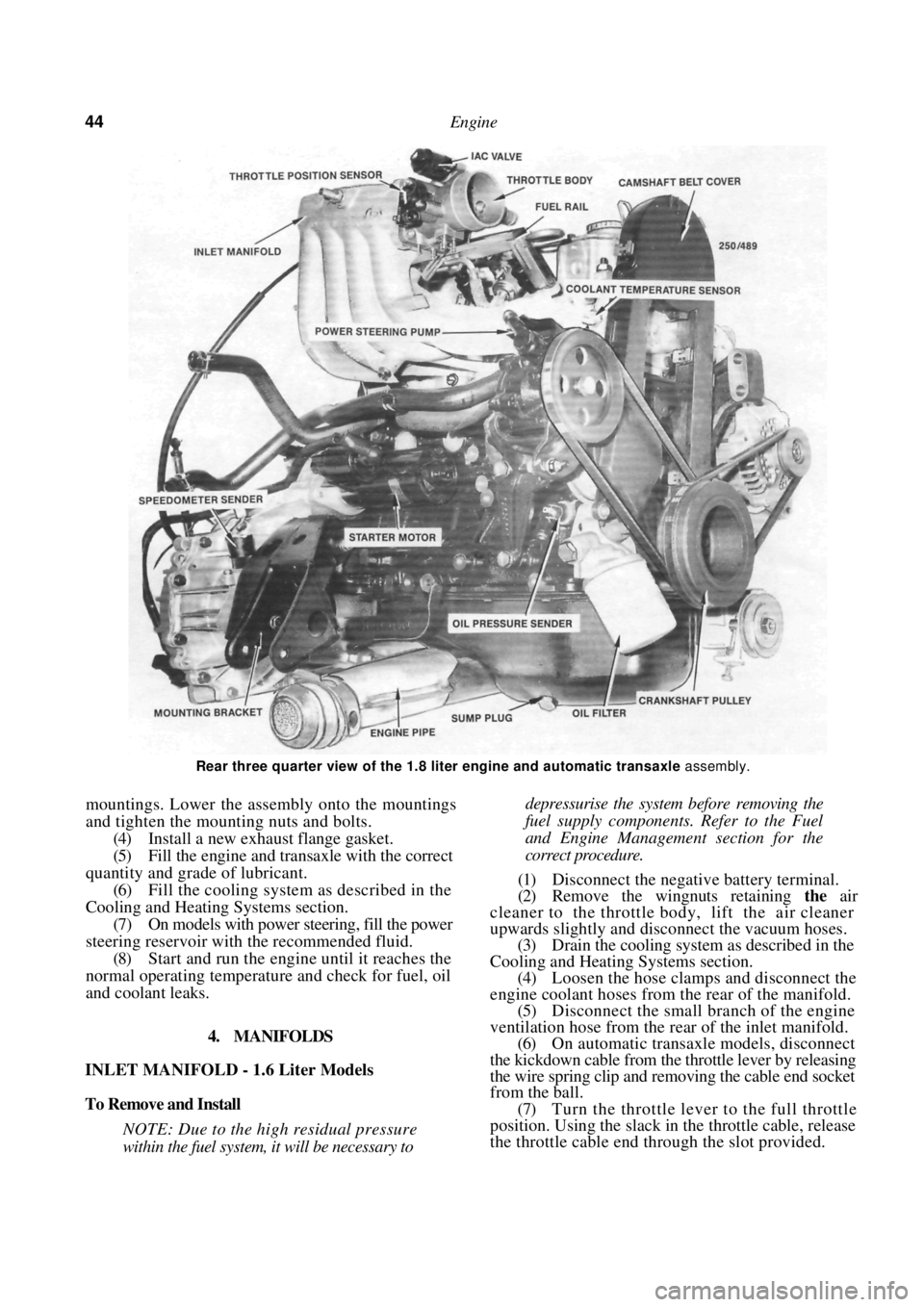
44 Engine
Rear three quarter view of the 1.8 liter engine and automatic transaxle assembly.
mountings. Lower the assembly onto the mountings
and tighten the mounting nuts and bolts.
(4) Install a new exhaust flange gasket.
(5) Fill the engine and transaxle with the correct
quantity and grade of lubricant. (6) Fill the cooling system as described in the
Cooling and Heating Systems section. (7) On models with power steering, fill the power
steering reservoir with the recommended fluid.
(8) Start and run the engine until it reaches the
normal operating temperatur e and check for fuel, oil
and coolant leaks.
4. MANIFOLDS
INLET MANIFOLD - 1.6 Liter Models
To Remove and Install
NOTE: Due to the high residual pressure
within the fuel system, it will be necessary to
depressurise the system before removing the
fuel supply components. Refer to the Fuel
and Engine Management section for the
correct procedure.
(1) Disconnect the negative battery terminal.
(2) Remove the wingnuts retaining the air
cleaner to the throttle body, lift the air cleaner
upwards slightly and disconnect the vacuum hoses. (3) Drain the cooling system as described in the
Cooling and Heating Systems section. (4) Loosen the hose clamps and disconnect the
engine coolant hoses from the rear of the manifold.
(5) Disconnect the small branch of the engine
ventilation hose from the rear of the inlet manifold. (6) On automatic transaxle models, disconnect
the kickdown cable from the throttle lever by releasing
the wire spring clip and re moving the cable end socket
from the ball.
(7) Turn the throttle lever to the full throttle
position. Using the slack in the throttle cable, release
the throttle cable end thr ough the slot provided.
Page 45 of 238

Engine 45
Installed view of the inlet manifold. 1.6 liter models. Air
cleaner removed.
(8) Remove the bolts retaining the throttle cable
bracket to the inlet manifold and place the bracket
with cable(s) attached to one side.
(9) Suitably mark the supply and return fuel
hoses and disconnect them from the throttle body.
(10) Suitably mark and disconnect the air pre-
heat, map sensor, charcoal canister and brake booster
vacuum hoses from the throttle body. (11) Disconnect the electrical connector from the
throttle body. (12) Remove the inlet manifold nuts and with-
draw the inlet manifold assembly. Discard the gasket. Installation is a reversal of the removal procedure
with attention to the following points:
(1) Ensure that all the carbon and old gasket
material is cleaned from the manifold and cylinder
head faces. (2) Check the face of the manifold for distortion
using a straight edge and a feeler gauge. (3) Use a new gasket and ensure that the mani-
fold retaining nuts are tightened to the specified
torque in a spiral pattern from the centre outwards. (4) Connect the vacuum hoses, the throttle cable
and where applicable, the kickdown cable. Adjust the
throttle cable as outlined in the Fuel and Engine
Management section and the kickdown cable as
described in the Automatic Transaxle section. (5) Fill the cooling system as described in the
Cooling and Heating Systems section. (6) Start the engine and check for air, fuel and
water leaks.
INLET MANIFOLD - 1.8 Liter Models
To Remove and Install
NOTE: Due to the high residual pressure
within the fuel system, it will be necessary to
depressurise the system before removing any
fuel supply components. Refer to the Fuel
and Engine Management section for the
correct procedure.
(1) Disconnect the negative battery terminal.
(2) Loosen the hose clamp and disconnect the
air inlet duct from the throttle body. (3) Suitably mark and disconnect the vacuum
hoses from the throttle body. (4) On automatic transaxle models disconnect
the kickdown cable from the throttle lever by releasing
the wire spring clip and re moving the cable and socket
from the ball. (5) Turn the throttle lever to the full throttle
position. Using the slack in the throttle cable, release
the throttle cable end thr ough the slot provided.
(6) Remove the bolts retaining the throttle cable
bracket to the inlet manifold and place the bracket
with cable(s) attached to one side. (7) Disconnect the wiring connectors from the
idle air control (IAC) valve and the throttle position
sensor (TPS).
(8) Disconnect the wiring connectors from the
fuel injectors and manifold air temperature (MAT)
sensor.
NOTE: A small screwdriver or similar tool
can be used to release the wire spring clips
on the injector connectors.
(9) Suitably mark and disconnect the fuel supply
and return lines from the fuel rail. (10) Remove the inlet manifold nuts and with-
draw the inlet manifold assembly. Discard the gasket. Installation is a reversal of the removal procedure
with attention to the following points:
View of the inlet manifold removed from the engine.
Page 46 of 238
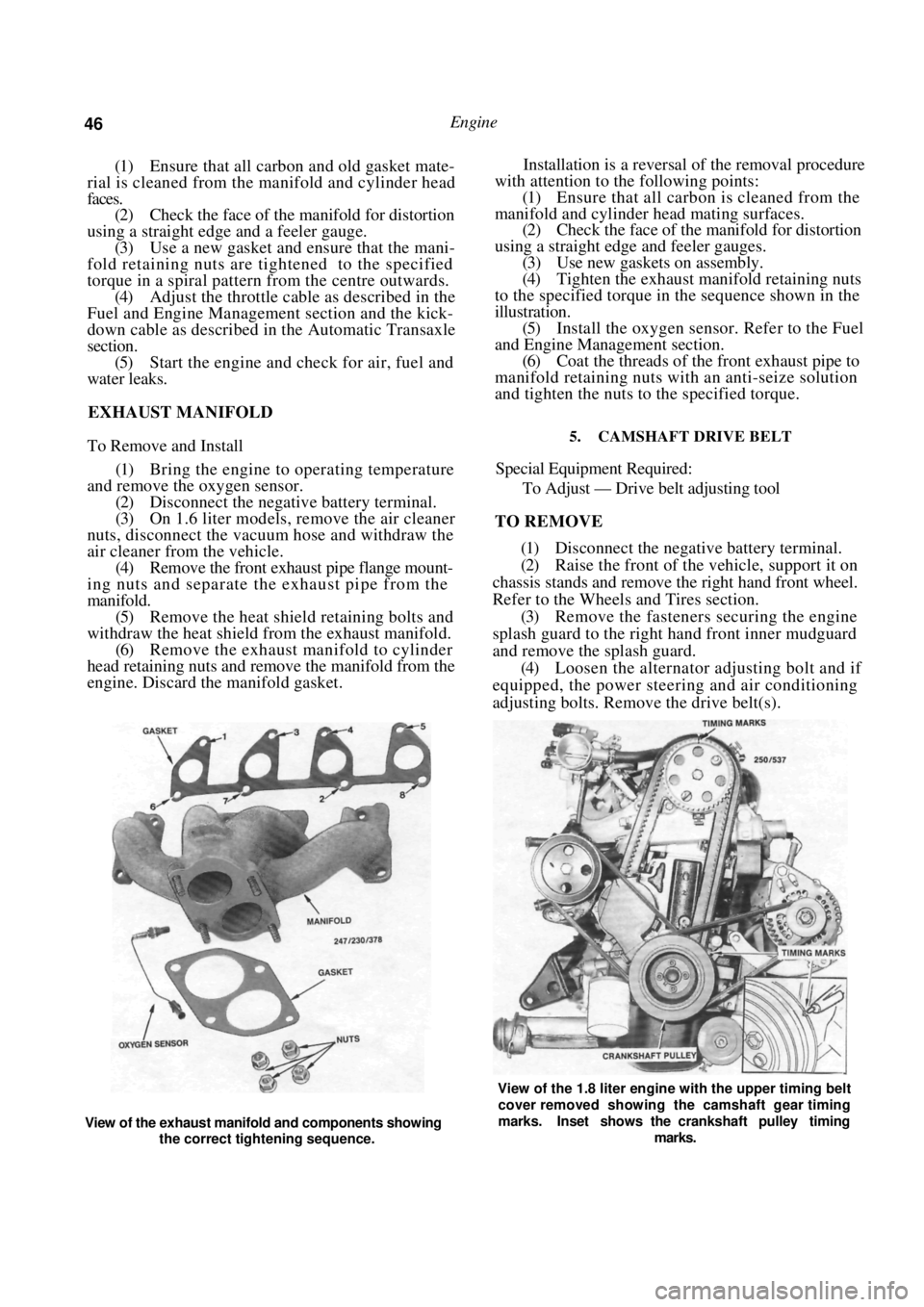
46 Engine
(1) Ensure that all carbon and old gasket mate-
rial is cleaned from the manifold and cylinder head
faces. (2) Check the face of the manifold for distortion
using a straight edge and a feeler gauge. (3) Use a new gasket and ensure that the mani-
fold retaining nuts are tightened to the specified
torque in a spiral pattern from the centre outwards. (4) Adjust the throttle cabl e as described in the
Fuel and Engine Management section and the kick-
down cable as described in the Automatic Transaxle
section.
(5) Start the engine and check for air, fuel and
water leaks.
EXHAUST MANIFOLD
To Remove and Install
(1) Bring the engine to operating temperature
and remove the oxygen sensor.
(2) Disconnect the negative battery terminal.
(3) On 1.6 liter models, remove the air cleaner
nuts, disconnect the vacuum hose and withdraw the
air cleaner from the vehicle. (4) Remove the front exhaust pipe flange mount-
ing nuts and separate the exhaust pipe from the
manifold. (5) Remove the heat shield retaining bolts and
withdraw the heat shield from the exhaust manifold. (6) Remove the exhaust manifold to cylinder
head retaining nuts and remove the manifold from the
engine. Discard the manifold gasket. Installation is a reversal of the removal procedure
with attention to the following points:
(1) Ensure that all carbon is cleaned from the
manifold and cylinder head mating surfaces. (2) Check the face of the manifold for distortion
using a straight edge and feeler gauges. (3) Use new gaskets on assembly.
(4) Tighten the exhaust manifold retaining nuts
to the specified torque in the sequence shown in the
illustration. (5) Install the oxygen sensor. Refer to the Fuel
and Engine Management section. (6) Coat the threads of the front exhaust pipe to
manifold retaining nuts with an anti-seize solution
and tighten the nuts to the specified torque.
5. CAMSHAFT DRIVE BELT
Special Equipment Required:
To Adjust — Drive belt adjusting tool
TO REMOVE
(1) Disconnect the negative battery terminal.
(2) Raise the front of the vehicle, support it on
chassis stands and remove the right hand front wheel.
Refer to the Wheels and Tires section. (3) Remove the fasteners securing the engine
splash guard to the right hand front inner mudguard
and remove the splash guard. (4) Loosen the alternator adjusting bolt and if
equipped, the power steering and air conditioning
adjusting bolts. Remove the drive belt(s).
View of the exhaust manifold and components showing
the correct tightening sequence.
View of the 1.8 liter engine with the upper timing belt
cover removed showing the camshaft gear timing
marks. Inset shows the crankshaft pulley timing
marks.
Page 47 of 238
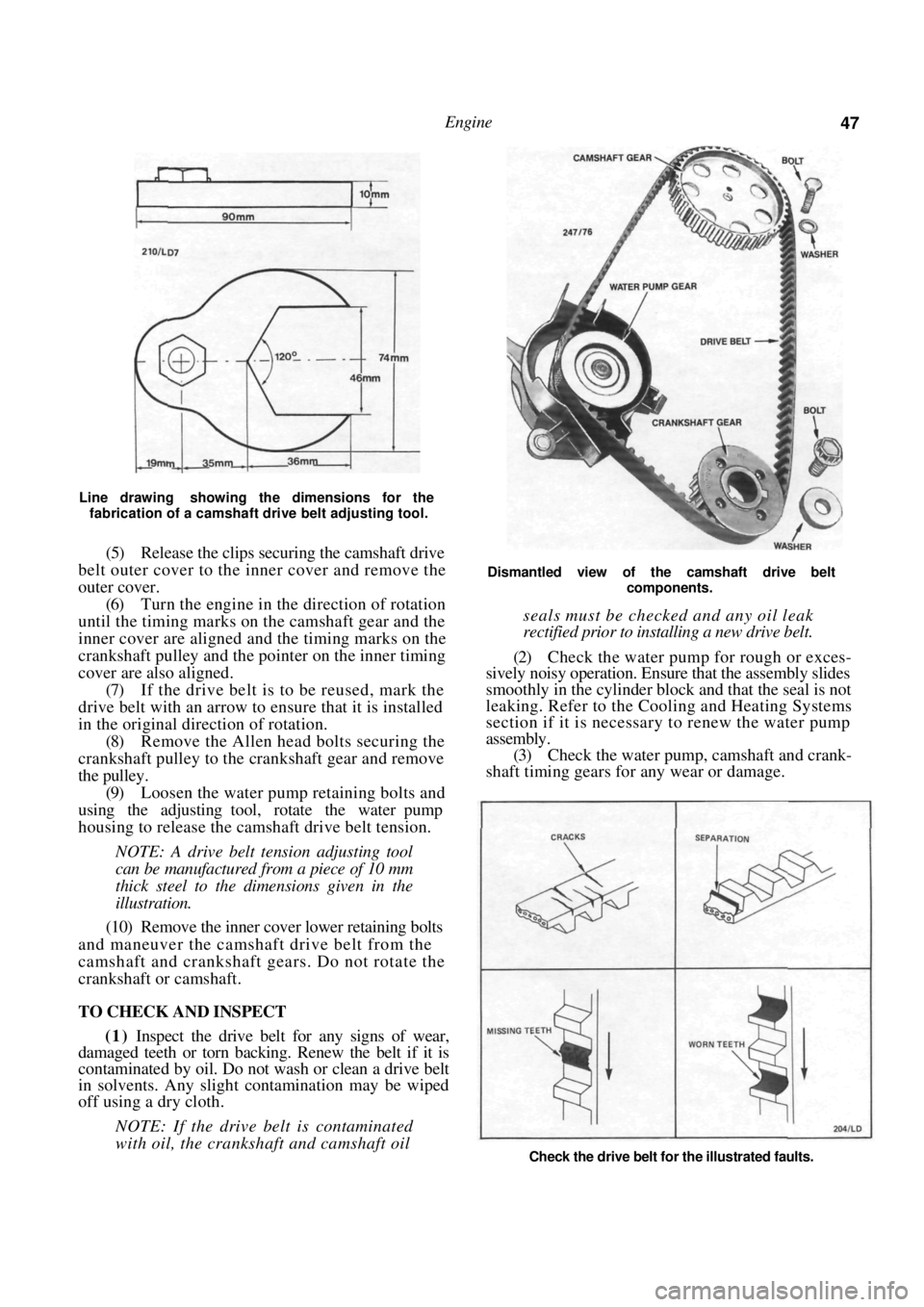
Engine 47
Line drawing showing the dimensions for the fabrication of a camshaft drive belt adjusting tool.
(5) Release the clips securing the camshaft drive
belt outer cover to the inner cover and remove the
outer cover.
(6) Turn the engine in the direction of rotation
until the timing marks on the camshaft gear and the
inner cover are aligned and the timing marks on the
crankshaft pulley and the pointer on the inner timing
cover are also aligned.
(7) If the drive belt is to be reused, mark the
drive belt with an arrow to ensure that it is installed
in the original direction of rotation. (8) Remove the Allen head bolts securing the
crankshaft pulley to the crankshaft gear and remove
the pulley. (9) Loosen the water pump retaining bolts and
using the adjusting tool, rotate the water pump
housing to release the camsh aft drive belt tension.
NOTE: A drive belt tension adjusting tool
can be manufactured from a piece of 10 mm
thick steel to the dimensions given in the
illustration.
(10) Remove the inner cover lower retaining bolts
and maneuver the camshaft drive belt from the
camshaft and crankshaft gears. Do not rotate the
crankshaft or camshaft.
TO CHECK AND INSPECT
(1) Inspect the drive belt for any signs of wear,
damaged teeth or torn backing. Renew the belt if it is
contaminated by oil. Do not wash or clean a drive belt
in solvents. Any slight contamination may be wiped
off using a dry cloth.
NOTE: If the drive belt is contaminated
with oil, the crankshaft and camshaft oil
Dismantled view of the camshaft drive belt
components.
seals must be checked and any oil leak
rectified prior to installing a new drive belt.
(2) Check the water pump for rough or exces-
sively noisy operation. Ensure that the assembly slides
smoothly in the cylinder bloc k and that the seal is not
leaking. Refer to the Cooling and Heating Systems
section if it is necessary to renew the water pump
assembly. (3) Check the water pump, camshaft and crank-
shaft timing gears for any wear or damage.
Check the drive belt for the illustrated faults.
Page 48 of 238
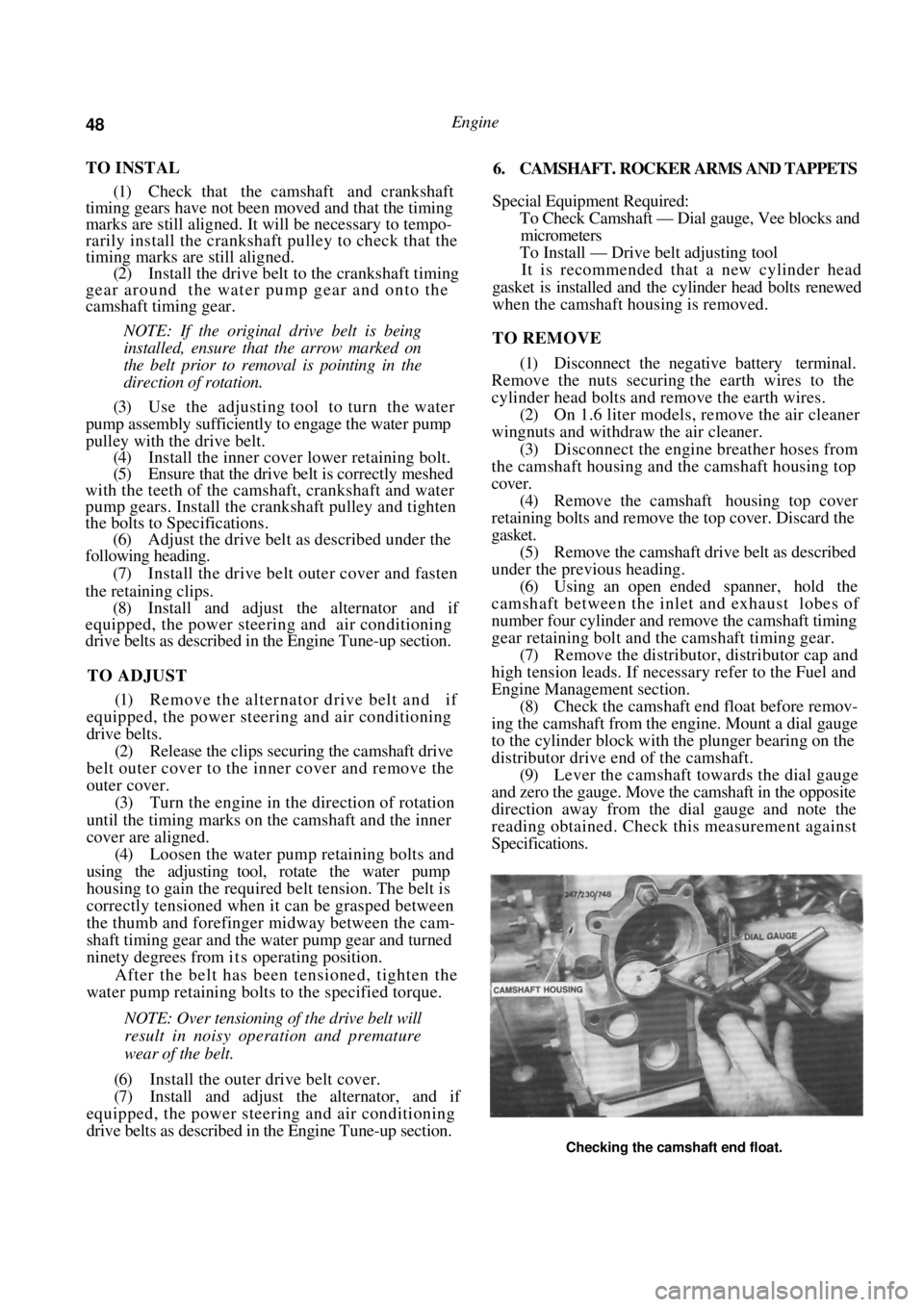
48 Engine
TO INSTAL
(1) Check that the camshaft and crankshaft
timing gears have not been moved and that the timing
marks are still aligned. It will be necessary to tempo-
rarily install the crankshaft pulley to check that the
timing marks are still aligned. (2) Install the drive belt to the crankshaft timing
gear around the water pump gear and onto the
camshaft timing gear.
NOTE: If the original drive belt is being
installed, ensure that the arrow marked on
the belt prior to removal is pointing in the
direction of rotation.
(3) Use the adjusting tool to turn the water
pump assembly sufficiently to engage the water pump
pulley with the drive belt. (4) Install the inner cover lower retaining bolt.
(5) Ensure that the drive be lt is correctly meshed
with the teeth of the camshaft, crankshaft and water
pump gears. Install the crankshaft pulley and tighten
the bolts to Specifications. (6) Adjust the drive belt as described under the
following heading.
(7) Install the drive belt outer cover and fasten
the retaining clips. (8) Install and adjust the alternator and if
equipped, the power steeri ng and air conditioning
drive belts as desc ribed in the Engine Tune-up section.
TO ADJUST
(1) Remove the alternator drive belt and if
equipped, the power steering and air conditioning
drive belts. (2) Release the clips securing the camshaft drive
belt outer cover to the inner cover and remove the
outer cover. (3) Turn the engine in the direction of rotation
until the timing marks on the camshaft and the inner
cover are aligned. (4) Loosen the water pump retaining bolts and
using the adjusting tool, rotate the water pump
housing to gain the required belt tension. The belt is
correctly tensioned when it can be grasped between
the thumb and forefinger midway between the cam-
shaft timing gear and the water pump gear and turned
ninety degrees from i t s operating position.
After the belt has been tensioned, tighten the
water pump retaining bolts to the specified torque.
NOTE: Over tensioning of the drive belt will
result in noisy operation and premature
wear of the belt.
(6) Install the outer drive belt cover.
(7) Install and adjust the alternator, and if
equipped, the power steering and air conditioning
drive belts as desc ribed in the Engine Tune-up section. 6. CAMSHAFT. ROCKER ARMS AND TAPPETS
Special Equipment Required:
To Check Camshaft — Dial gauge, Vee blocks and
micrometers
To Install — Drive belt adjusting tool
It is recommended that a new cylinder head
gasket is installed and the cylinder head bolts renewed
when the camshaft housing is removed.
TO REMOVE
(1) Disconnect the negative battery terminal.
Remove the nuts securing the earth wires to the
cylinder head bolts and remove the earth wires.
(2) On 1.6 liter models, remove the air cleaner
wingnuts and withdraw the air cleaner.
(3) Disconnect the engine breather hoses from
the camshaft housing and the camshaft housing top
cover. (4) Remove the camshaft housing top cover
retaining bolts and remove the top cover. Discard the
gasket.
(5) Remove the camshaft dr ive belt as described
under the previous heading. (6) Using an open ended spanner, hold the
camshaft between the inle t and exhaust lobes of
number four cylinder and remove the camshaft timing
gear retaining bolt and the camshaft timing gear.
(7) Remove the distributor, distributor cap and
high tension leads. If necessary refer to the Fuel and
Engine Management section. (8) Check the camshaft end float before remov-
ing the camshaft from the engine. Mount a dial gauge
to the cylinder block with the plunger bearing on the
distributor drive end of the camshaft. (9) Lever the camshaft towards the dial gauge
and zero the gauge. Move the camshaft in the opposite
direction away from the dial gauge and note the
reading obtained. Check this measurement against
Specifications.
Checking the camshaft end float.
Page 49 of 238
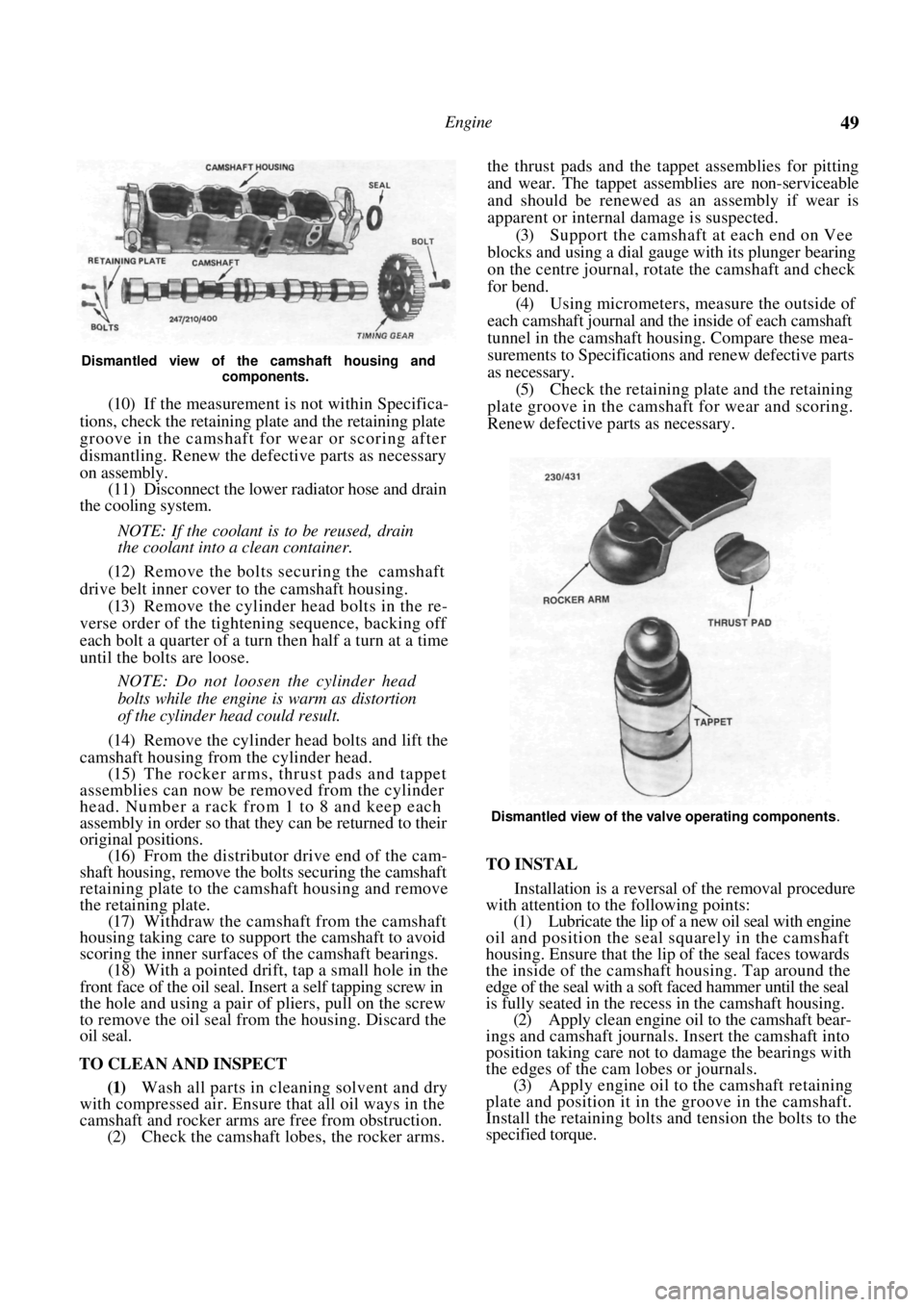
Engine 49
Dismantled view of the camshaft housing and components.
(10) If the measurement is not within Specifica-
tions, check the retaining plate and the retaining plate
groove in the camshaft for wear or scoring after
dismantling. Renew the defective parts as necessary
on assembly. (11) Disconnect the lower radiator hose and drain
the cooling system.
NOTE: If the coolant is to be reused, drain
the coolant into a clean container.
(12) Remove the bolts securing the camshaft
drive belt inner cover to the camshaft housing. (13) Remove the cylinder head bolts in the re-
verse order of the tighten ing sequence, backing off
each bolt a quarter of a turn then half a turn at a time
until the bolts are loose.
NOTE: Do not loosen the cylinder head
bolts while the engine is warm as distortion
of the cylinder head could result.
(14) Remove the cylinder head bolts and lift the
camshaft housing from the cylinder head. (15) The rocker arms, thrust pads and tappet
assemblies can now be removed from the cylinder
head. Number a rack from 1 to 8 and keep each
assembly in order so that they can be returned to their
original positions.
(16) From the distributor drive end of the cam-
shaft housing, remove the bolts securing the camshaft
retaining plate to the camshaft housing and remove
the retaining plate. (17) Withdraw the camshaft from the camshaft
housing taking care to supp ort the camshaft to avoid
scoring the inner surfaces of the camshaft bearings.
(18) With a pointed drift, tap a small hole in the
front face of the oil seal. Insert a self tapping screw in
the hole and using a pair of pliers, pull on the screw
to remove the oil seal from the housing. Discard the
oil seal.
TO CLEAN AND INSPECT
(1) Wash all parts in cleaning solvent and dry
with compressed air. Ensure that all oil ways in the
camshaft and rocker arms are free from obstruction.
(2) Check the camshaft lobes, the rocker arms. the thrust pads and the ta
ppet assemblies for pitting
and wear. The tappet assemblies are non-serviceable
and should be renewed as an assembly if wear is
apparent or internal damage is suspected.
(3) Support the camshaft at each end on Vee
blocks and using a dial gauge with its plunger bearing
on the centre journal, rotate the camshaft and check
for bend. (4) Using micrometers, measure the outside of
each camshaft journal and the inside of each camshaft
tunnel in the camshaft housing. Compare these mea-
surements to Specifications and renew defective parts
as necessary. (5) Check the retaining plate and the retaining
plate groove in the camshaft for wear and scoring.
Renew defective parts as necessary.
Dismantled view of the valve operating components.
TO INSTAL
Installation is a reversal of the removal procedure
with attention to the following points:
(1) Lubricate the lip of a new oil seal with engine
oil and position the seal squarely in the camshaft
housing. Ensure that the li p of the seal faces towards
the inside of the camshaft housing. Tap around the
edge of the seal with a soft faced hammer until the seal
is fully seated in the recess in the camshaft housing. (2) Apply clean engine oil to the camshaft bear-
ings and camshaft journals. Insert the camshaft into
position taking care not to damage the bearings with
the edges of the cam lobes or journals. (3) Apply engine oil to the camshaft retaining
plate and position it in the groove in the camshaft.
Install the retaining bolts and tension the bolts to the
specified torque.
Page 50 of 238
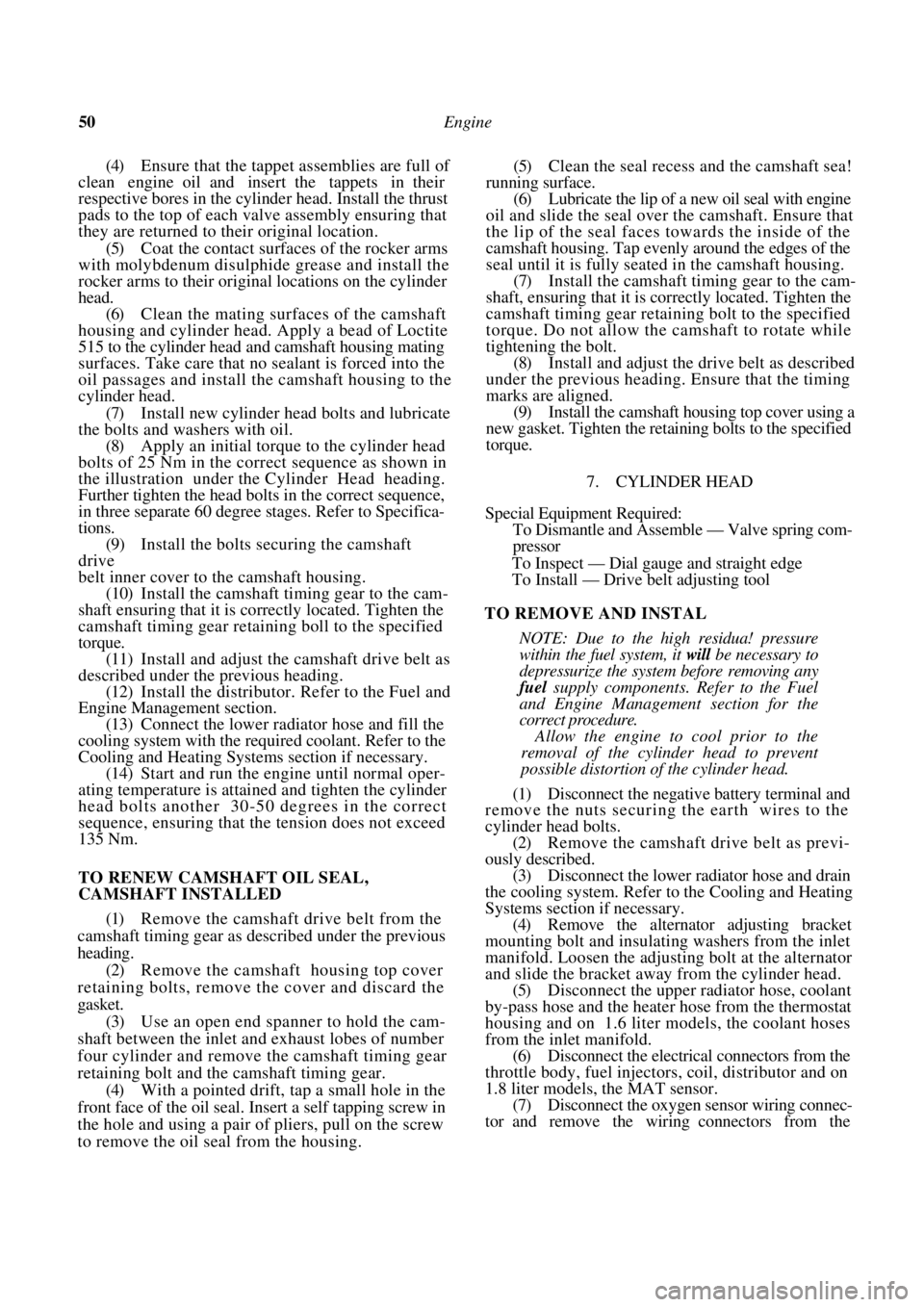
50 Engine
(4) Ensure that the tappet assemblies are full of
clean engine oil and insert the tappets in their
respective bores in the cylinde r head. Install the thrust
pads to the top of each valve assembly ensuring that
they are returned to their original location.
(5) Coat the contact surfaces of the rocker arms
with molybdenum disulphide grease and install the
rocker arms to their origin al locations on the cylinder
head. (6) Clean the mating surfaces of the camshaft
housing and cylinder head. Apply a bead of Loctite
515 to the cylinder head and camshaft housing mating
surfaces. Take care that no sea lant is forced into the
oil passages and install the camshaft housing to the
cylinder head.
(7) Install new cylinder head bolts and lubricate
the bolts and washers with oil.
(8) Apply an initial torque to the cylinder head
bolts of 25 Nm in the corr ect sequence as shown in
the illustration under the Cylinder Head heading.
Further tighten the head bolts in the correct sequence,
in three separate 60 degree stages. Refer to Specifica-
tions. (9) Install the bolts securing the camshaft
drive
belt inner cover to the camshaft housing. (10) Install the camshaft timing gear to the cam-
shaft ensuring that it is correctly located. Tighten the
camshaft timing gear retain ing boll to the specified
torque. (11) Install and adjust the camshaft drive belt as
described under the previous heading. (12) Install the distributor. Refer to the Fuel and
Engine Management section.
(13) Connect the lower radiat or hose and fill the
cooling system with the required coolant. Refer to the
Cooling and Heating Systems section if necessary. (14) Start and run the engine until normal oper-
ating temperature is attained and tighten the cylinder
head bolts another 30-50 degrees in the correct
sequence, ensuring that the tension does not exceed
135 Nm.
TO RENEW CAMSHAFT OIL SEAL,
CAMSHAFT INSTALLED
(1) Remove the camshaft drive belt from the
camshaft timing gear as described under the previous
heading.
(2) Remove the camshaft housing top cover
retaining bolts, remove the cover and discard the
gasket.
(3) Use an open end spanner to hold the cam-
shaft between the inlet and exhaust lobes of number
four cylinder and remove the camshaft timing gear
retaining bolt and the camshaft timing gear. (4) With a pointed drift, tap a small hole in the
front face of the oil seal. Insert a self tapping screw in
the hole and using a pair of pliers, pull on the screw
to remove the oil seal from the housing.
(5) Clean the seal recess and the camshaft sea!
running surface. (6) Lubricate the lip of a new oil seal with engine
oil and slide the seal over the camshaft. Ensure that
the lip of the seal faces to wards the inside of the
camshaft housing. Tap evenly around the edges of the
seal until it is fully seated in the camshaft housing.
(7) Install the camshaft timing gear to the cam-
shaft, ensuring that it is co rrectly located. Tighten the
camshaft timing gear retain ing bolt to the specified
torque. Do not allow the camshaft to rotate while
tightening the bolt. (8) Install and adjust the drive belt as described
under the previous heading. Ensure that the timing
marks are aligned. (9) Install the camshaft hou sing top cover using a
new gasket. Tighten the retaining bolts to the specified
torque.
7. CYLINDER HEAD
Special Equipment Required:
To Dismantle and Assemble — Valve spring com-
pressor
To Inspect — Dial gauge and straight edge
To Install — Drive belt adjusting tool
TO REMOVE AND INSTAL
NOTE: Due to the high residua! pressure
within the fuel system, it will be necessary to
depressurize the system before removing any
fuel supply components. Refer to the Fuel
and Engine Management section for the
correct procedure.
Allow the engine to cool prior to the
removal of the cylinder head to prevent
possible distortion of the cylinder head.
(1) Disconnect the negative battery terminal and
remove the nuts securing the earth wires to the
cylinder head bolts.
(2) Remove the camshaft drive belt as previ-
ously described.
(3) Disconnect the lower radiator hose and drain
the cooling system. Refer to the Cooling and Heating
Systems section if necessary. (4) Remove the alternator adjusting bracket
mounting bolt and insulating washers from the inlet
manifold. Loosen the adjusting bolt at the alternator
and slide the bracket away from the cylinder head. (5) Disconnect the upper radiator hose, coolant
by-pass hose and the heater hose from the thermostat
housing and on 1.6 liter m odels, the coolant hoses
from the inlet manifold. (6) Disconnect the electrica l connectors from the
throttle body, fuel injectors, coil, distributor and on
1.8 liter models, the MAT sensor. (7) Disconnect the oxygen sensor wiring connec-
tor and remove the wiring connectors from the