OPEL GT-R 1973 Service Manual
Manufacturer: OPEL, Model Year: 1973, Model line: GT-R, Model: OPEL GT-R 1973Pages: 625, PDF Size: 17.22 MB
Page 551 of 625
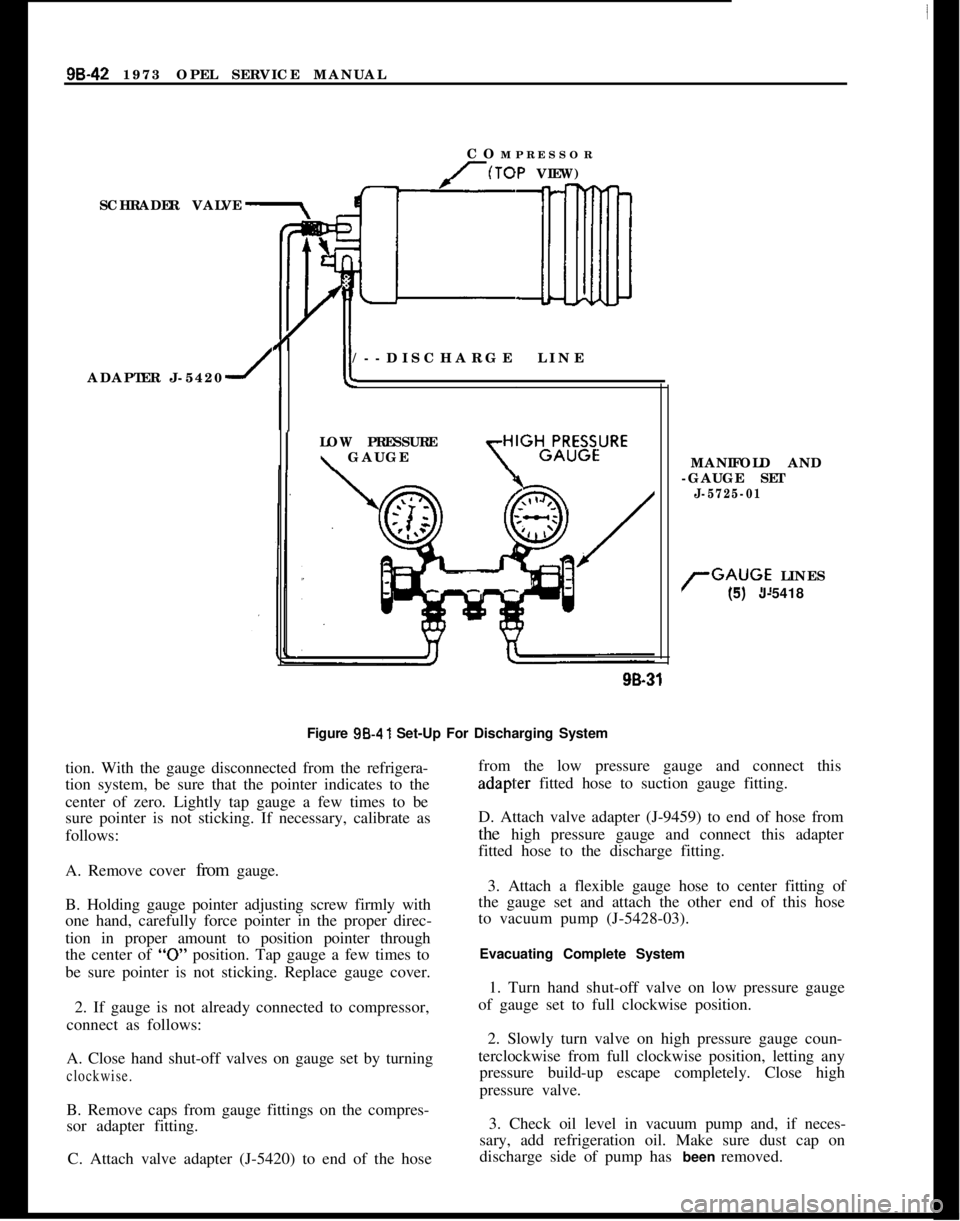
98-42 1973 OPEL SERVICE MANUAL
SCHRADER VALVE
ADAPTER J-54201COMPRESSOR(TOP VIEW)[/--DISCHARGE LINE
ILOW PRESSURE\ GAUGE
MANIFOLD AND
-GAUGE SET
J-5725-01
rGAUGE LINES
(5) J-541899-31
Figure 98.41 Set-Up For Discharging System
tion. With the gauge disconnected from the refrigera-
tion system, be sure that the pointer indicates to the
center of zero. Lightly tap gauge a few times to be
sure pointer is not sticking. If necessary, calibrate as
follows:
A. Remove cover from gauge.
B. Holding gauge pointer adjusting screw firmly with
one hand, carefully force pointer in the proper direc-
tion in proper amount to position pointer through
the center of
“0” position. Tap gauge a few times to
be sure pointer is not sticking. Replace gauge cover.
2. If gauge is not already connected to compressor,
connect as follows:
A. Close hand shut-off valves on gauge set by turning
clockwise.B. Remove caps from gauge fittings on the compres-
sor adapter fitting.
C. Attach valve adapter (J-5420) to end of the hosefrom the low pressure gauge and connect thisadapl:er fitted hose to suction gauge fitting.
D. Attach valve adapter (J-9459) to end of hose from
the high pressure gauge and connect this adapter
fitted hose to the discharge fitting.
3. Attach a flexible gauge hose to center fitting of
the gauge set and attach the other end of this hose
to vacuum pump (J-5428-03).
Evacuating Complete System
1. Turn hand shut-off valve on low pressure gauge
of gauge set to full clockwise position.
2. Slowly turn valve on high pressure gauge coun-
terclockwise from full clockwise position, letting any
pressure build-up escape completely. Close high
pressure valve.
3. Check oil level in vacuum pump and, if neces-
sary, add refrigeration oil. Make sure dust cap on
discharge side of pump has been removed.
Page 552 of 625
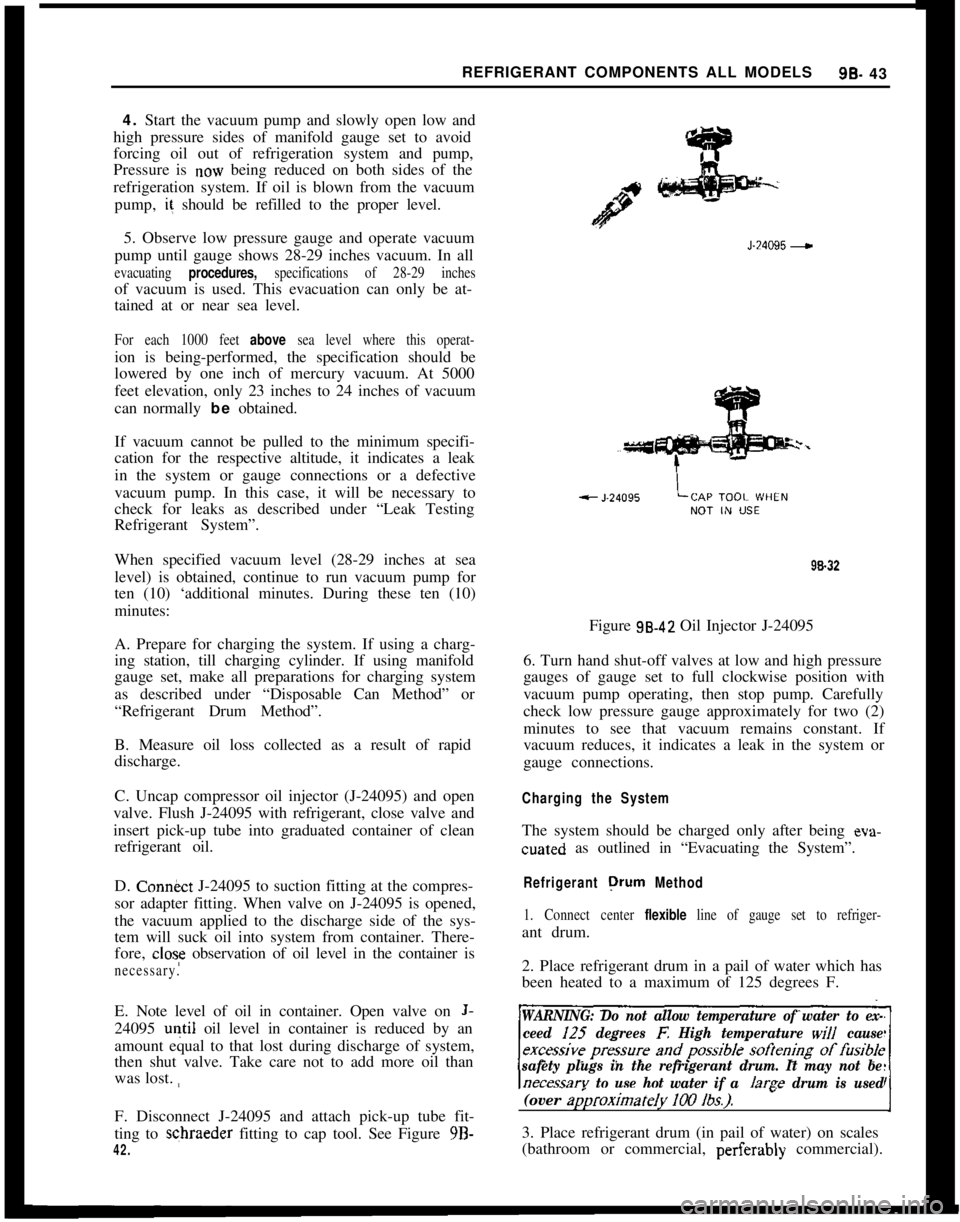
REFRIGERANT COMPONENTS ALL MODELS9B- 43
4. Start the vacuum pump and slowly open low and
high pressure sides of manifold gauge set to avoid
forcing oil out of refrigeration system and pump,
Pressure is now being reduced on both sides of the
refrigeration system. If oil is blown from the vacuum
pump, it should be refilled to the proper level.
5. Observe low pressure gauge and operate vacuum
pump until gauge shows 28-29 inches vacuum. In all
evacuating procedures, specifications of 28-29 inchesof vacuum is used. This evacuation can only be at-
tained at or near sea level.
For each 1000 feet above sea level where this operat-ion is being-performed, the specification should be
lowered by one inch of mercury vacuum. At 5000
feet elevation, only 23 inches to 24 inches of vacuum
can normally be obtained.
If vacuum cannot be pulled to the minimum specifi-
cation for the respective altitude, it indicates a leak
in the system or gauge connections or a defective
vacuum pump. In this case, it will be necessary to
check for leaks as described under “Leak Testing
Refrigerant System”.
When specified vacuum level (28-29 inches at sea
level) is obtained, continue to run vacuum pump for
ten (10) ‘additional minutes. During these ten (10)
minutes:
A. Prepare for charging the system. If using a charg-
ing station, till charging cylinder. If using manifold
gauge set, make all preparations for charging system
as described under “Disposable Can Method” or
“Refrigerant Drum Method”.
B. Measure oil loss collected as a result of rapid
discharge.
C. Uncap compressor oil injector (J-24095) and open
valve. Flush J-24095 with refrigerant, close valve and
insert pick-up tube into graduated container of clean
refrigerant oil.
D. Con&ct J-24095 to suction fitting at the compres-
sor adapter fitting. When valve on J-24095 is opened,
the vacuum applied to the discharge side of the sys-
tem will suck oil into system from container. There-
fore,
close observation of oil level in the container is
necessary.E. Note level of oil in container. Open valve on
J-24095
u+il oil level in container is reduced by an
amount equal to that lost during discharge of system,
then shut valve. Take care not to add more oil than
was lost. ,,
F. Disconnect J-24095 and attach pick-up tube fit-
ting to schraeder fitting to cap tool. See Figure 9B-
42.J-24095
-98.32
Figure 98.42 Oil Injector J-24095
6. Turn hand shut-off valves at low and high pressure
gauges of gauge set to full clockwise position with
vacuum pump operating, then stop pump. Carefully
check low pressure gauge approximately for two (2)
minutes to see that vacuum remains constant. If
vacuum reduces, it indicates a leak in the system or
gauge connections.
Charging the SystemThe system should be charged only after being eva-cuated as outlined in “Evacuating the System”.
Refrigerant orurn Method
1. Connect center flexible line of gauge set to refriger-ant drum.
2. Place refrigerant drum in a pail of water which has
been heated to a maximum of 125 degrees F.
WARNING: Do not allow temperature of water to ex-
ceed I25
degrees E High temperature will cause
safety plugs in the refrigerant drum. It may not be
necessarv to use hot water if a /arae drum is used(over
ap)roximateIy 100 lbs.).-I3. Place refrigerant drum (in pail of water) on scales
(bathroom or commercial, perferably commercial).
Page 553 of 625
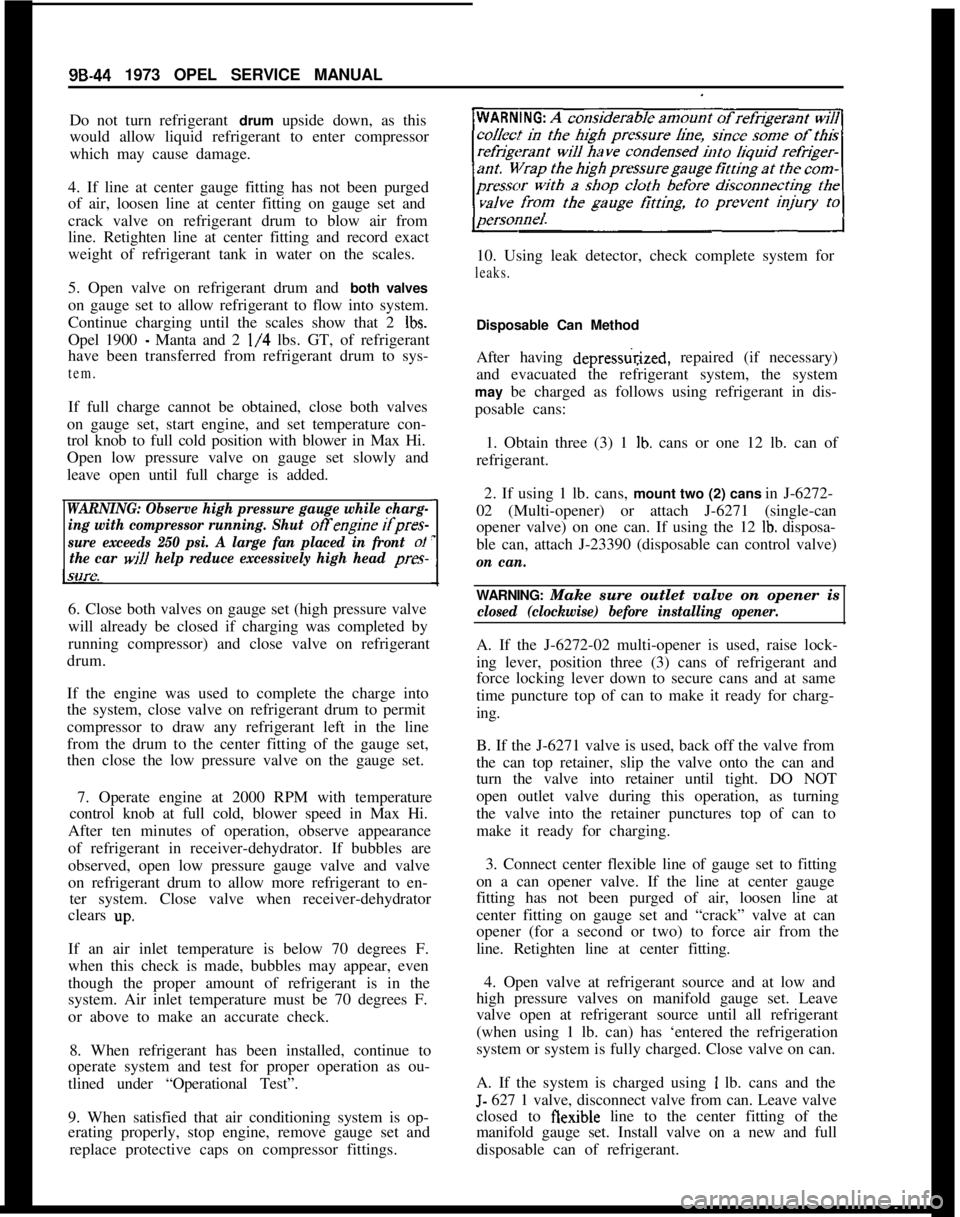
9B-44 1973 OPEL SERVICE MANUAL
Do not turn refrigerant drum upside down, as this
would allow liquid refrigerant to enter compressor
which may cause damage.
4. If line at center gauge fitting has not been purged
of air, loosen line at center fitting on gauge set and
crack valve on refrigerant drum to blow air from
line. Retighten line at center fitting and record exact
weight of refrigerant tank in water on the scales.
5. Open valve on refrigerant drum and both valves
on gauge set to allow refrigerant to flow into system.
Continue charging until the scales show that 2
Ibs.Opel 1900
- Manta and 2 l/4 lbs. GT, of refrigerant
have been transferred from refrigerant drum to sys-
tem.If full charge cannot be obtained, close both valves
on gauge set, start engine, and set temperature con-
trol knob to full cold position with blower in Max Hi.
Open low pressure valve on gauge set slowly and
leave open until full charge is added.
WARNING: Observe high pressure gauge while charg-
ing with compressor running. Shut
offengine ifpres-
sure exceeds 250 psi. A large fan placed in front
ol
the car wi// help reduce excessively high head pres-6. Close both valves on gauge set (high pressure valve
will already be closed if charging was completed by
running compressor) and close valve on refrigerant
drum.
If the engine was used to complete the charge into
the system, close valve on refrigerant drum to permit
compressor to draw any refrigerant left in the line
from the drum to the center fitting of the gauge set,
then close the low pressure valve on the gauge set.
7. Operate engine at 2000 RPM with temperature
control knob at full cold, blower speed in Max Hi.
After ten minutes of operation, observe appearance
of refrigerant in receiver-dehydrator. If bubbles are
observed, open low pressure gauge valve and valve
on refrigerant drum to allow more refrigerant to en-
ter system. Close valve when receiver-dehydrator
clears
up.If an air inlet temperature is below 70 degrees F.
when this check is made, bubbles may appear, even
though the proper amount of refrigerant is in the
system. Air inlet temperature must be 70 degrees F.
or above to make an accurate check.
8. When refrigerant has been installed, continue to
operate system and test for proper operation as ou-
tlined under “Operational Test”.
9. When satisfied that air conditioning system is op-
erating properly, stop engine, remove gauge set and
replace protective caps on compressor fittings.10. Using leak detector, check complete system for
leaks.Disposable Can Method
After having
depress&ed, repaired (if necessary)
and evacuated the refrigerant system, the system
may be charged as follows using refrigerant in dis-
posable cans:
1. Obtain three (3) 1
lb. cans or one 12 lb. can of
refrigerant.
2. If using 1 lb. cans, mount two (2) cans in J-6272-
02 (Multi-opener) or attach J-6271 (single-can
opener valve) on one can. If using the 12
lb. disposa-
ble can, attach J-23390 (disposable can control valve)
on can.WARNING: Make sure outlet valve on opener is
closed (clockwise) before installing opener.A. If the J-6272-02 multi-opener is used, raise lock-
ing lever, position three (3) cans of refrigerant and
force locking lever down to secure cans and at same
time puncture top of can to make it ready for charg-
ing.
B. If the J-6271 valve is used, back off the valve from
the can top retainer, slip the valve onto the can and
turn the valve into retainer until tight. DO NOT
open outlet valve during this operation, as turning
the valve into the retainer punctures top of can to
make it ready for charging.
3. Connect center flexible line of gauge set to fitting
on a can opener valve. If the line at center gauge
fitting has not been purged of air, loosen line at
center fitting on gauge set and “crack” valve at can
opener (for a second or two) to force air from the
line. Retighten line at center fitting.
4. Open valve at refrigerant source and at low and
high pressure valves on manifold gauge set. Leave
valve open at refrigerant source until all refrigerant
(when using 1 lb. can) has ‘entered the refrigeration
system or system is fully charged. Close valve on can.
A. If the system is charged using
1 lb. cans and the
J- 627 1 valve, disconnect valve from can. Leave valve
closed to flexible line to the center fitting of the
manifold gauge set. Install valve on a new and full
disposable can of refrigerant.
Page 554 of 625
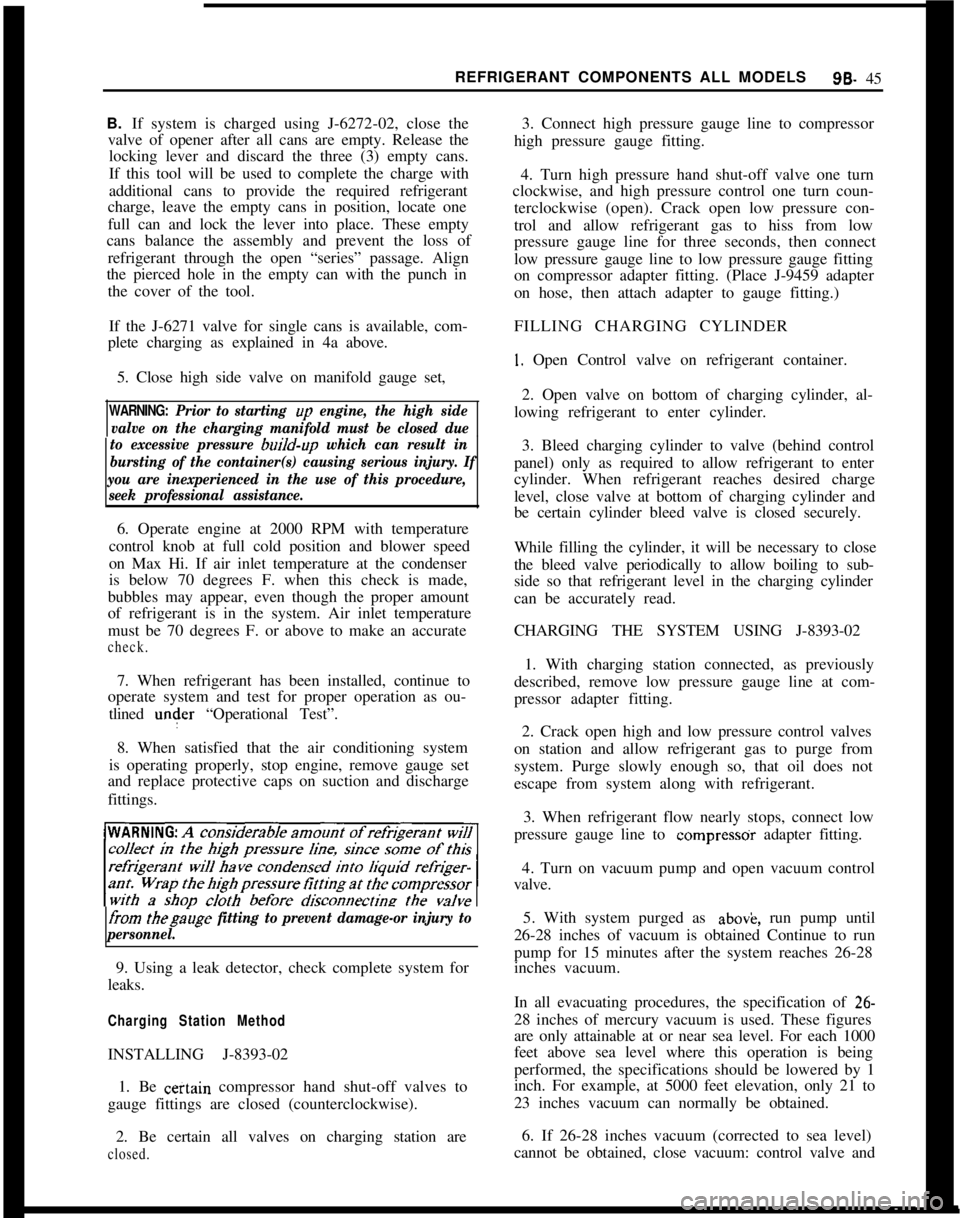
REFRIGERANT COMPONENTS ALL MODELS9t3- 45
B. If system is charged using J-6272-02, close the
valve of opener after all cans are empty. Release the locking lever and discard the three (3) empty cans.
If this tool will be used to complete the charge with
additional cans to provide the required refrigerant
charge, leave the empty cans in position, locate one
full can and lock the lever into place. These empty
cans balance the assembly and prevent the loss of
refrigerant through the open “series” passage. Align
the pierced hole in the empty can with the punch in
the cover of the tool.
If the J-6271 valve for single cans is available, com-
plete charging as explained in 4a above.
5. Close high side valve on manifold gauge set,
WARNING: Prior to starting up engine, the high side
valve on the charging manifold must be closed due
to excessive pressure
bui/d-up which can result in
bursting of the container(s) causing serious injury. If
you are inexperienced in the use of this procedure, seek professional assistance.
6. Operate engine at 2000 RPM with temperature
control knob at full cold position and blower speed
on Max Hi. If air inlet temperature at the condenser
is below 70 degrees F. when this check is made,
bubbles may appear, even though the proper amount
of refrigerant is in the system. Air inlet temperature
must be 70 degrees F. or above to make an accurate
check.
7. When refrigerant has been installed, continue to
operate system and test for proper operation as ou-
tlined
under “Operational Test”.
8. When satisfied that the air conditioning system
is operating properly, stop engine, remove gauge set
and replace protective caps on suction and discharge
fittings.
from thegauge fitting to prevent damage-or injury to
personnel.
9. Using a leak detector, check complete system for
leaks.
Charging Station Method
INSTALLING J-8393-02
-
1. Be ceitain compressor hand shut-off valves to
gauge fittings are closed (counterclockwise).
2. Be certain all valves on charging station are
closed.
3. Connect high pressure gauge line to compressor
high pressure gauge fitting.
4. Turn high pressure hand shut-off valve one turn
clockwise, and high pressure control one turn coun-
terclockwise (open). Crack open low pressure con-
trol and allow refrigerant gas to hiss from low
pressure gauge line for three seconds, then connect
low pressure gauge line to low pressure gauge fitting
on compressor adapter fitting. (Place J-9459 adapter
on hose, then attach adapter to gauge fitting.)
FILLING CHARGING CYLINDER
1. Open Control valve on refrigerant container.
2. Open valve on bottom of charging cylinder, al-
lowing refrigerant to enter cylinder.
3. Bleed charging cylinder to valve (behind control
panel) only as required to allow refrigerant to enter
cylinder. When refrigerant reaches desired charge
level, close valve at bottom of charging cylinder and
be certain cylinder bleed valve is closed securely.
While filling the cylinder, it will be necessary to close
the bleed valve periodically to allow boiling to sub-
side so that refrigerant level in the charging cylinder
can be accurately read.
CHARGING THE SYSTEM USING J-8393-02
1. With charging station connected, as previously
described, remove low pressure gauge line at com-
pressor adapter fitting.
2. Crack open high and low pressure control valves
on station and allow refrigerant gas to purge from
system. Purge slowly enough so, that oil does not
escape from system along with refrigerant.
3. When refrigerant flow nearly stops, connect low
pressure gauge line to
compress& adapter fitting.
4. Turn on vacuum pump and open vacuum control
valve.
5. With system purged as
abovk, run pump until
26-28 inches of vacuum is obtained Continue to run
pump for 15 minutes after the system reaches 26-28
inches vacuum.
In all evacuating procedures, the specification of
26.
28 inches of mercury vacuum is used. These figures
are only attainable at or near sea level. For each 1000
feet above sea level where this operation is being
performed, the specifications should be lowered by 1
inch. For example, at 5000 feet elevation, only 21 to
23 inches vacuum can normally be obtained.
6. If 26-28 inches vacuum (corrected to sea level)
cannot be obtained, close vacuum: control valve and
Page 555 of 625
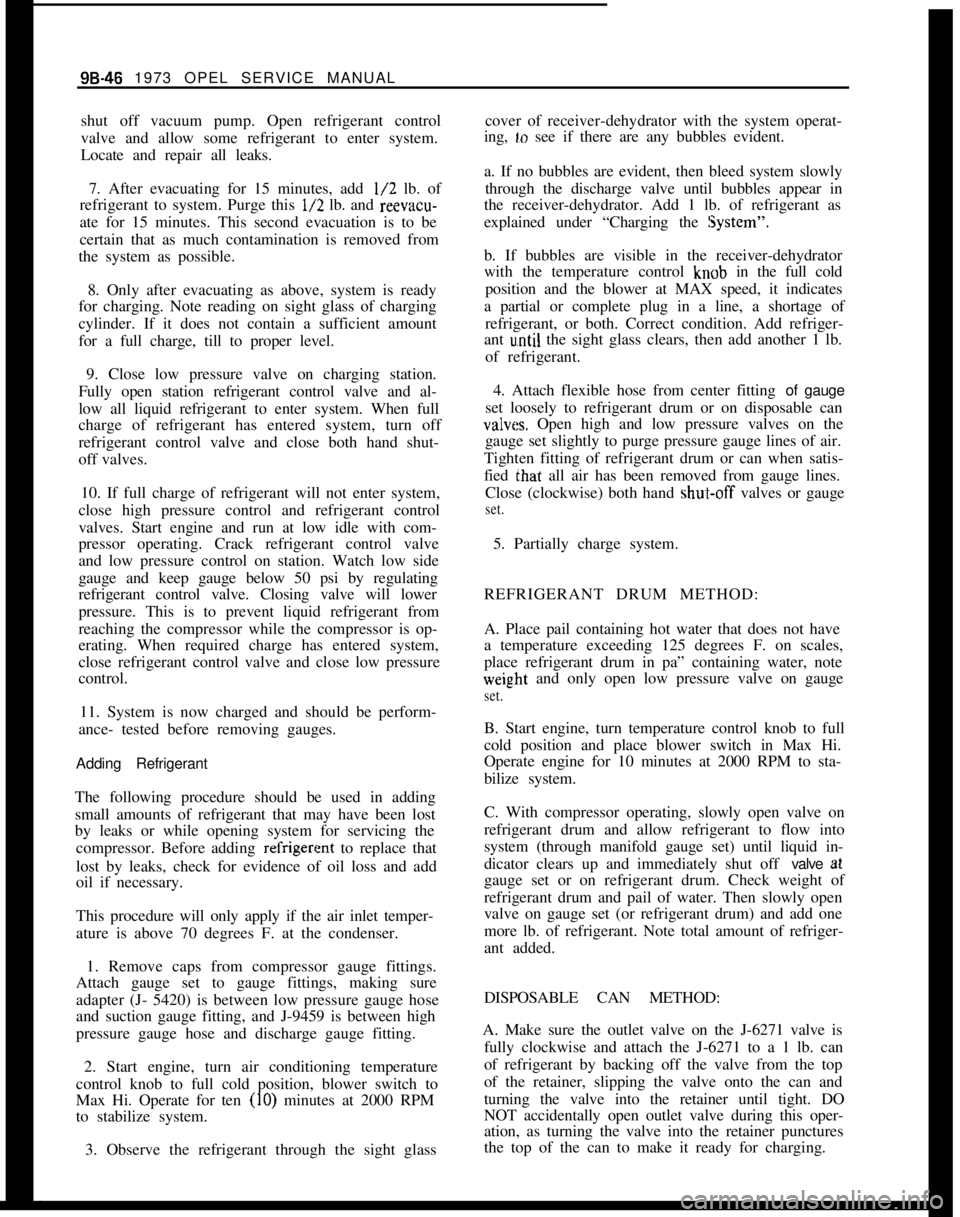
98-46 1973 OPEL SERVICE MANUAL
shut off vacuum pump. Open refrigerant control
valve and allow some refrigerant to enter system.
Locate and repair all leaks.
7. After evacuating for 15 minutes, add l/2 lb. of
refrigerant to system. Purge this
l/2 lb. and reevacu-
ate for 15 minutes. This second evacuation is to be
certain that as much contamination is removed from
the system as possible.
8. Only after evacuating as above, system is ready
for charging. Note reading on sight glass of charging
cylinder. If it does not contain a sufficient amount
for a full charge, till to proper level.
9. Close low pressure valve on charging station.
Fully open station refrigerant control valve and al-
low all liquid refrigerant to enter system. When full
charge of refrigerant has entered system, turn off
refrigerant control valve and close both hand shut-
off valves.
10. If full charge of refrigerant will not enter system,
close high pressure control and refrigerant control
valves. Start engine and run at low idle with com-
pressor operating. Crack refrigerant control valve
and low pressure control on station. Watch low side
gauge and keep gauge below 50 psi by regulating
refrigerant control valve. Closing valve will lower
pressure. This is to prevent liquid refrigerant from
reaching the compressor while the compressor is op-
erating. When required charge has entered system,
close refrigerant control valve and close low pressure
control.
11. System is now charged and should be perform-
ance- tested before removing gauges.
Adding Refrigerant
The following procedure should be used in adding
small amounts of refrigerant that may have been lost
by leaks or while opening system for servicing the
compressor. Before adding refrigerent to replace that
lost by leaks, check for evidence of oil loss and add
oil if necessary.
This procedure will only apply if the air inlet temper-
ature is above 70 degrees F. at the condenser.
1. Remove caps from compressor gauge fittings.
Attach gauge set to gauge fittings, making sure
adapter (J- 5420) is between low pressure gauge hose
and suction gauge fitting, and J-9459 is between high
pressure gauge hose and discharge gauge fitting.
2. Start engine, turn air conditioning temperature
control knob to full cold position, blower switch to
Max Hi. Operate for ten
(IO) minutes at 2000 RPM
to stabilize system.
3. Observe the refrigerant through the sight glasscover of receiver-dehydrator with the system operat-
ing,
IO see if there are any bubbles evident.
a. If no bubbles are evident, then bleed system slowly
through the discharge valve until bubbles appear in
the receiver-dehydrator. Add 1 lb. of refrigerant as
explained under “Charging the
ISystem”.b. If bubbles are visible in the receiver-dehydrator
with the temperature control krlob in the full cold
position and the blower at MAX speed, it indicates
a partial or complete plug in a line, a shortage of
refrigerant, or both. Correct condition. Add refriger-
ant
u~ntil the sight glass clears, then add another 1 lb.
of refrigerant.
4. Attach flexible hose from center fitting of gauge
set loosely to refrigerant drum or on disposable can
valvxs. Open high and low pressure valves on the
gauge set slightly to purge pressure gauge lines of air.
Tighten fitting of refrigerant drum or can when satis-
fied ihat all air has been removed from gauge lines.
Close (clockwise) both hand shut-off valves or gauge
set.5. Partially charge system.
REFRIGERANT DRUM METHOD:
A. Place pail containing hot water that does not have
a temperature exceeding 125 degrees F. on scales,
place refrigerant drum in pa” containing water, note
weig,ht and only open low pressure valve on gauge
set.B. Start engine, turn temperature control knob to full
cold position and place blower switch in Max Hi.
Operate engine for 10 minutes at 2000 RPM to sta-
bilize system.
C. With compressor operating, slowly open valve on
refrigerant drum and allow refrigerant to flow into
system (through manifold gauge set) until liquid in-
dicator clears up and immediately shut off valve ai
gauge set or on refrigerant drum. Check weight of
refrigerant drum and pail of water. Then slowly open
valve on gauge set (or refrigerant drum) and add one
more lb. of refrigerant. Note total amount of refriger-
ant added.
DISPOSABLE CAN METHOD:
A. Make sure the outlet valve on the J-6271 valve is
fully clockwise and attach the J-6271 to a 1 lb. can
of refrigerant by backing off the valve from the top
of the retainer, slipping the valve onto the can and
turning the valve into the retainer until tight. DO
NOT accidentally open outlet valve during this oper-
ation, as turning the valve into the retainer punctures
the top of the can to make it ready for charging.
.
Page 556 of 625
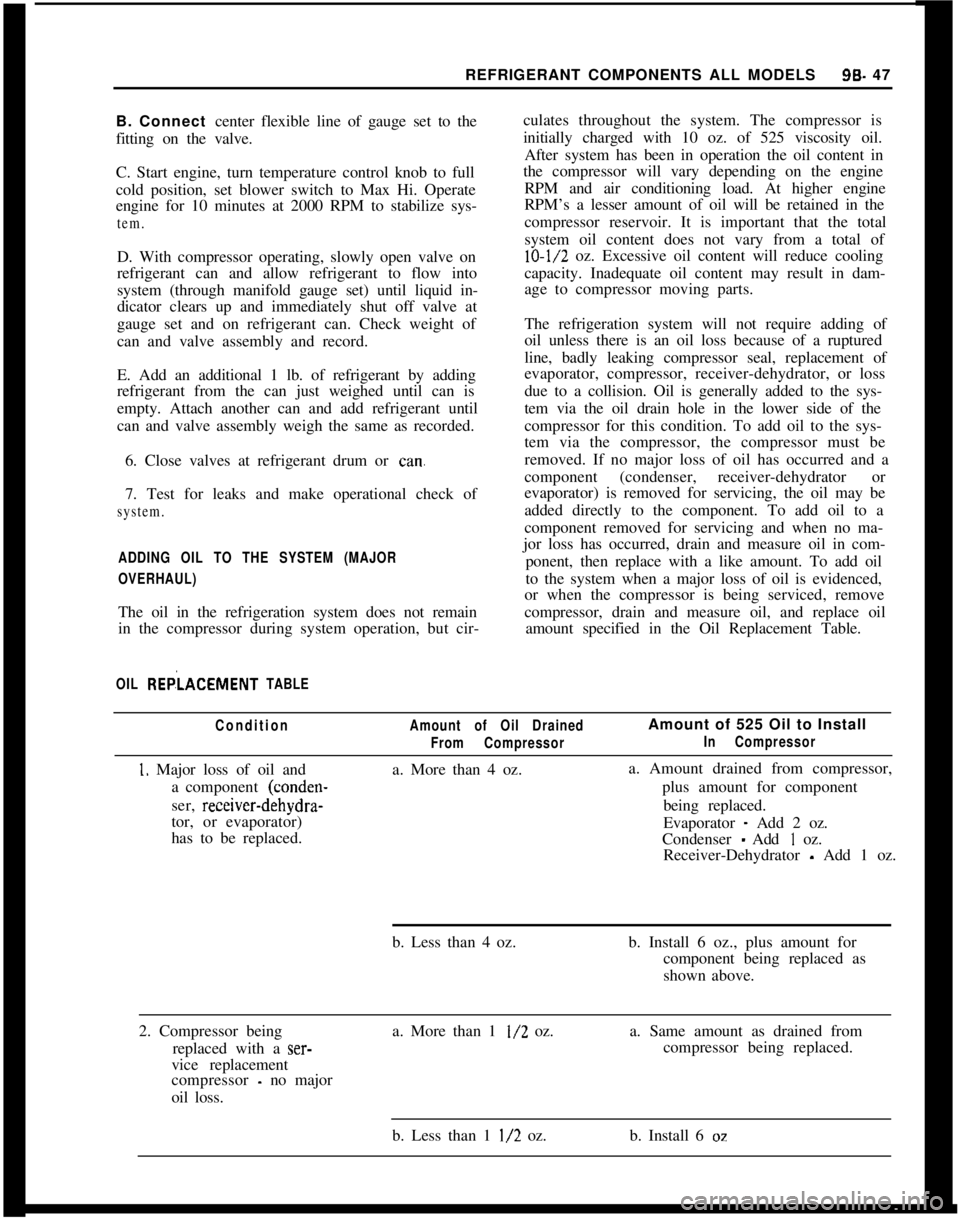
REFRIGERANT COMPONENTS ALL MODELS9a- 47
B. Connect center flexible line of gauge set to the
fitting on the valve.
C. Start engine, turn temperature control knob to full
cold position, set blower switch to Max Hi. Operate
engine for 10 minutes at 2000 RPM to stabilize sys-tem.D. With compressor operating, slowly open valve on
refrigerant can and allow refrigerant to flow into
system (through manifold gauge set) until liquid in-
dicator clears up and immediately shut off valve at
gauge set and on refrigerant can. Check weight of
can and valve assembly and record.
E. Add an additional 1 lb. of refrigerant by adding
refrigerant from the can just weighed until can is
empty. Attach another can and add refrigerant until
can and valve assembly weigh the same as recorded.
6. Close valves at refrigerant drum or
can,7. Test for leaks and make operational check of
system.
ADDING OIL TO THE SYSTEM (MAJOR
OVERHAUL)The oil in the refrigeration system does not remain
in the compressor during system operation, but cir-culates throughout the system. The compressor is
initially charged with 10 oz. of 525 viscosity oil.
After system has been in operation the oil content in
the compressor will vary depending on the engine
RPM and air conditioning load. At higher engine
RPM’s a lesser amount of oil will be retained in the
compressor reservoir. It is important that the total
system oil content does not vary from a total of10-l/2 oz. Excessive oil content will reduce cooling
capacity. Inadequate oil content may result in dam-
age to compressor moving parts.
The refrigeration system will not require adding of
oil unless there is an oil loss because of a ruptured
line, badly leaking compressor seal, replacement of
evaporator, compressor, receiver-dehydrator, or loss
due to a collision. Oil is generally added to the sys-
tem via the oil drain hole in the lower side of the
compressor for this condition. To add oil to the sys-
tem via the compressor, the compressor must be
removed. If no major loss of oil has occurred and a
component (condenser,receiver-dehydrator or
evaporator) is removed for servicing, the oil may be
added directly to the component. To add oil to a
component removed for servicing and when no ma-
jor loss has occurred, drain and measure oil in com-
ponent, then replace with a like amount. To add oil
to the system when a major loss of oil is evidenced,
or when the compressor is being serviced, remove
compressor, drain and measure oil, and replace oil
amount specified in the Oil Replacement Table.
OIL REP,‘LACEMENT TABLE
Condition
1. Major loss of oil and
a component (conden-
ser, receiver-dehydra-
tor, or evaporator)
has to be replaced.
Amount of Oil Drained
From Compressora. More than 4 oz.Amount of 525 Oil to Install
In Compressora. Amount drained from compressor,
plus amount for component
being replaced.
Evaporator
- Add 2 oz.
Condenser
- Add I oz.
Receiver-Dehydrator
- Add 1 oz.
b. Less than 4 oz.b. Install 6 oz., plus amount for
component being replaced as
shown above.
2. Compressor being
replaced with a
ser-vice replacement
compressor
- no major
oil loss.a. More than 1
l/2 oz.a. Same amount as drained from
compressor being replaced.
b. Less than 1
l/2 oz.b. Install 6 oz
Page 557 of 625
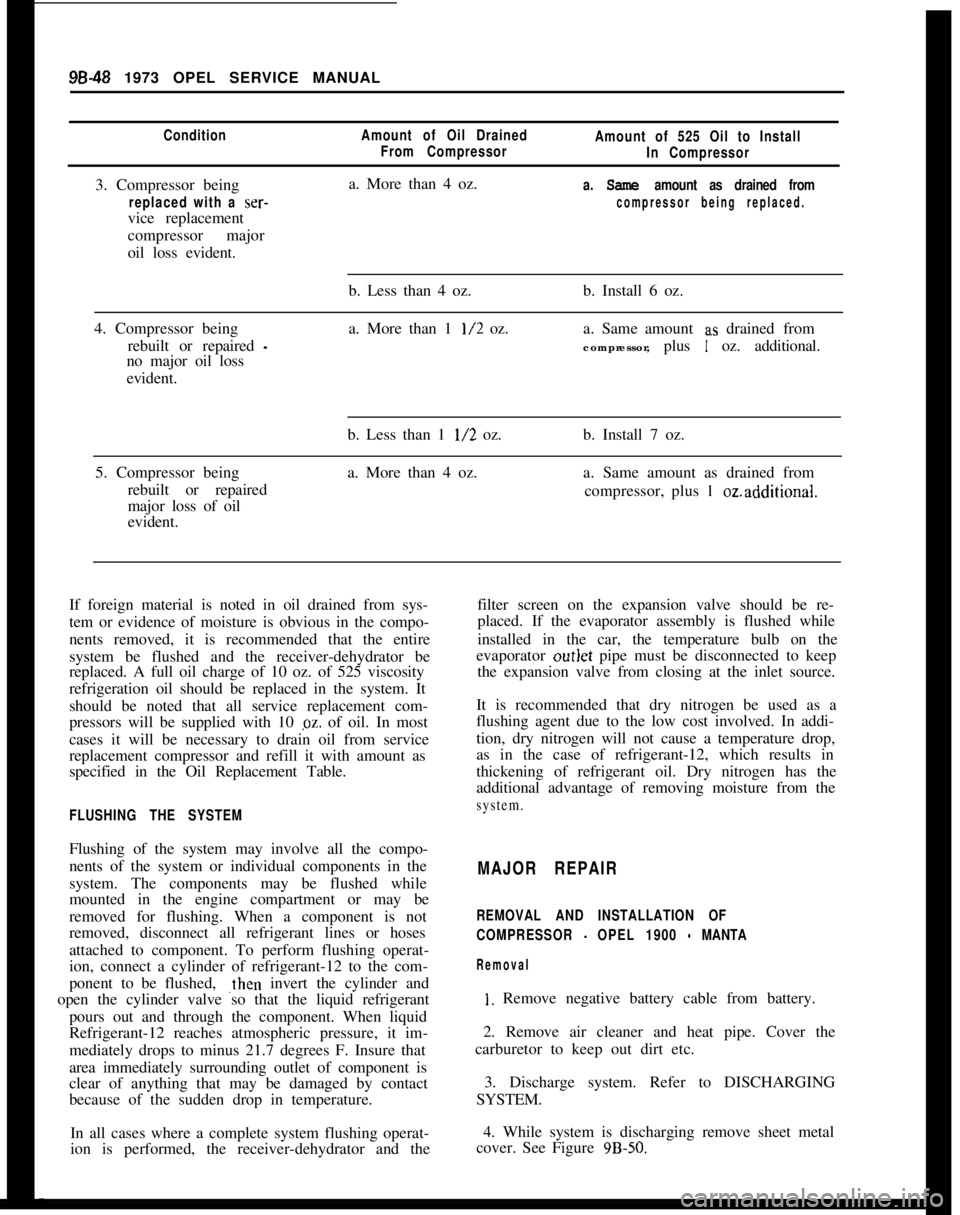
98-48 1973 OPEL SERVICE MANUALCondition3. Compressor being
replaced with a ser-vice replacement
compressor major
oil loss evident.
Amount of Oil Drained
From Compressora. More than 4 oz.Amount of 525 Oil to Install
In Compressor
a.
Same amount as drained from
compressor being replaced.4. Compressor being
rebuilt or repaired
-no major oil loss
evident.b. Less than 4 oz.
a. More than 1
l/2 oz.b. Install 6 oz.
a. Same amount a.s drained from
compressor, plus
1 oz. additional.
5. Compressor being
rebuilt or repaired
major loss of oil
evident.b. Less than 1
l/2 oz.
a. More than 4 oz.b. Install 7 oz.
a. Same amount as drained from
compressor, plus 1
ozadditional.If foreign material is noted in oil drained from sys-
tem or evidence of moisture is obvious in the compo-
nents removed, it is recommended that the entire
system be flushed and the receiver-dehydrator be
replaced. A full oil charge of 10 oz. of 525 viscosity
refrigeration oil should be replaced in the system. It
should be noted that all service replacement com-
pressors will be supplied with 10 pz. of oil. In most
cases it will be necessary to drain oil from service
replacement compressor and refill it with amount as
specified in the Oil Replacement Table.filter screen on the expansion valve should be re-
placed. If the evaporator assembly is flushed while
installed in the car, the temperature bulb on the
evaporator outlet pipe must be disconnected to keep
the expansion valve from closing at the inlet source.
FLUSHING THE SYSTEMIt is recommended that dry nitrogen be used as a
flushing agent due to the low cost involved. In addi-
tion, dry nitrogen will not cause a temperature drop,
as in the case of refrigerant-12, which results in
thickening of refrigerant oil. Dry nitrogen has the
additional advantage of removing moisture from thesystem.Flushing of the system may involve all the compo-
nents of the system or individual components in the
system. The components may be flushed while
mounted in the engine compartment or may be
removed for flushing. When a component is not
removed, disconnect all refrigerant lines or hoses
attached to component. To perform flushing operat-
ion, connect a cylinder of refrigerant-12 to the com-
ponent to be flushed, ,then invert the cylinder and
open the cylinder valve so that the liquid refrigerant
pours out and through the component. When liquid
Refrigerant-12 reaches atmospheric pressure, it im-
mediately drops to minus 21.7 degrees F. Insure that
area immediately surrounding outlet of component is
clear of anything that may be damaged by contact
because of the sudden drop in temperature.MAJOR REPAIR
REMOVAL AND INSTALLATION OF
COMPRESSOR
- OPEL 1900 - MANTA
Removal
I. Remove negative battery cable from battery.
2. Remove air cleaner and heat pipe. Cover the
carburetor to keep out dirt etc.
3. Discharge system. Refer to DISCHARGING
SYSTEM.
In all cases where a complete system flushing operat-4. While system is discharging remove sheet metal
ion is performed, the receiver-dehydrator and thecover. See Figure
9B-50.
Page 558 of 625
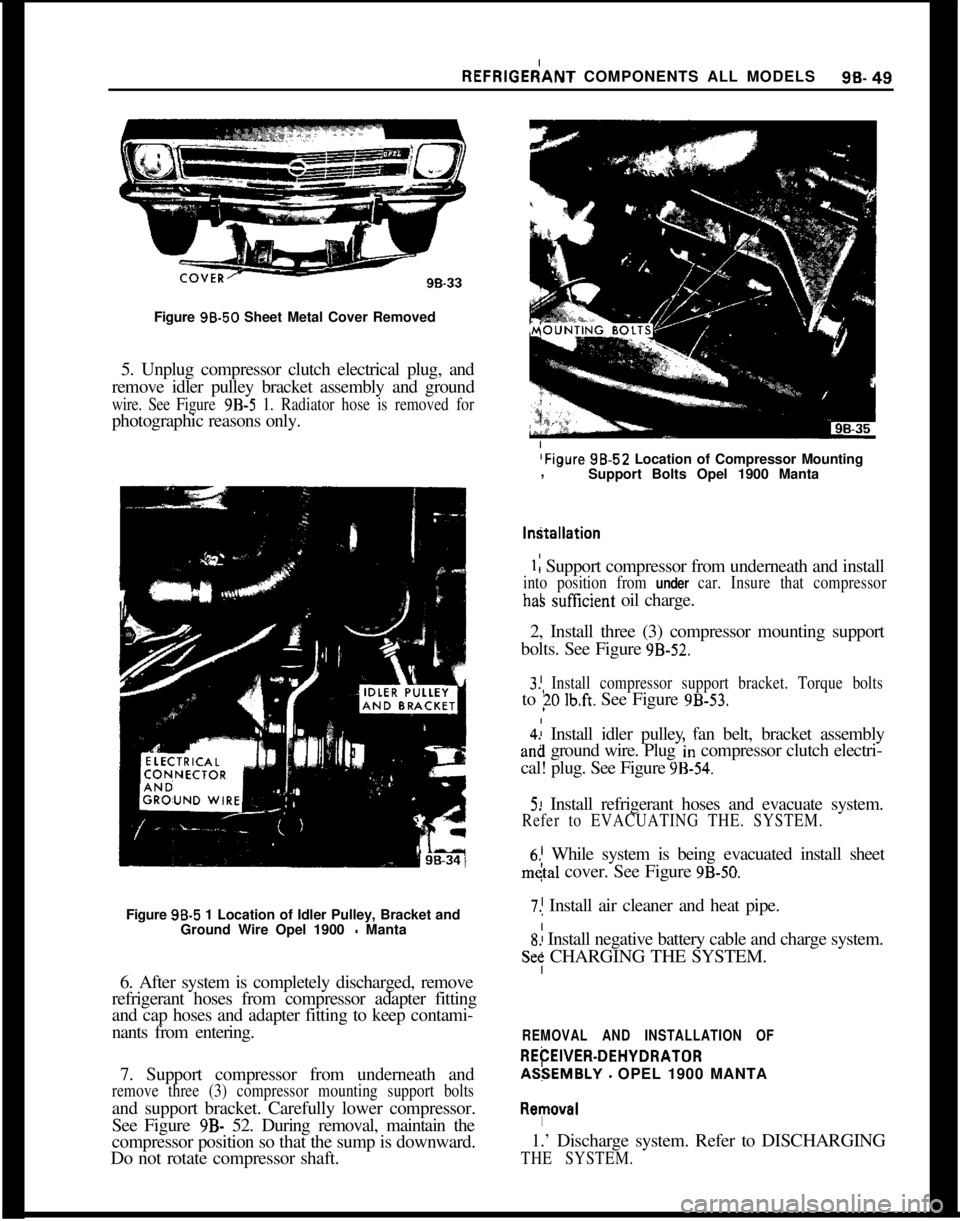
REFRlGEdANT COMPONENTS ALL MODELS96-49Figure 96.50 Sheet Metal Cover Removed
5. Unplug compressor clutch electrical plug, and
remove idler pulley bracket assembly and ground
wire. See Figure 9B-5 1. Radiator hose is removed forphotographic reasons only.
(Figure 98.52 Location of Compressor Mounting
,
Support Bolts Opel 1900 Manta
I
Figure 98-5 1 Location of Idler Pulley, Bracket and
Ground Wire Opel 1900
- Manta
6. After system is completely discharged, remove
refrigerant hoses from compressor adapter fitting
and cap hoses and adapter fitting to keep contami-
nants from entering.
7. Support compressor from underneath and
remove three (3) compressor mounting support boltsand support bracket. Carefully lower compressor.
See Figure
9B- 52. During removal, maintain the
compressor position so that the sump is downward.
Do not rotate compressor shaft.
1: Support compressor from underneath and install
into position from under car. Insure that compressor
haS sutXcient oil charge.
2, Install three (3) compressor mounting support
bolts. See Figure
9B-52.I
3! Install compressor support bracket. Torque boltsto
?O lb.ft. See Figure 9B-53.
4.: Install idler pulley fan belt, bracket assemblyan8 ground wire. Plug
‘In compressor clutch electri-
cal! plug. See Figure
9B-54.
5! Install refrigerant hoses and evacuate system.
Refer to EVACUATING THE. SYSTEM.
6.’ While system is being evacuated install sheet
m&l cover. See Figure 9B-50.
7.1 Install air cleaner and heat pipe.
S! Install negative battery cable and charge system.
Se: CHARGING THE SYSTEM.
REMOVAL AND INSTALLATION OF
REtiEWEFt-DEHYDRATORAS:EMBLY
- OPEL 1900 MANTA
I
R~l!lOV~lI1.’ Discharge system. Refer to DISCHARGING
THE SYSTEM.
Page 559 of 625
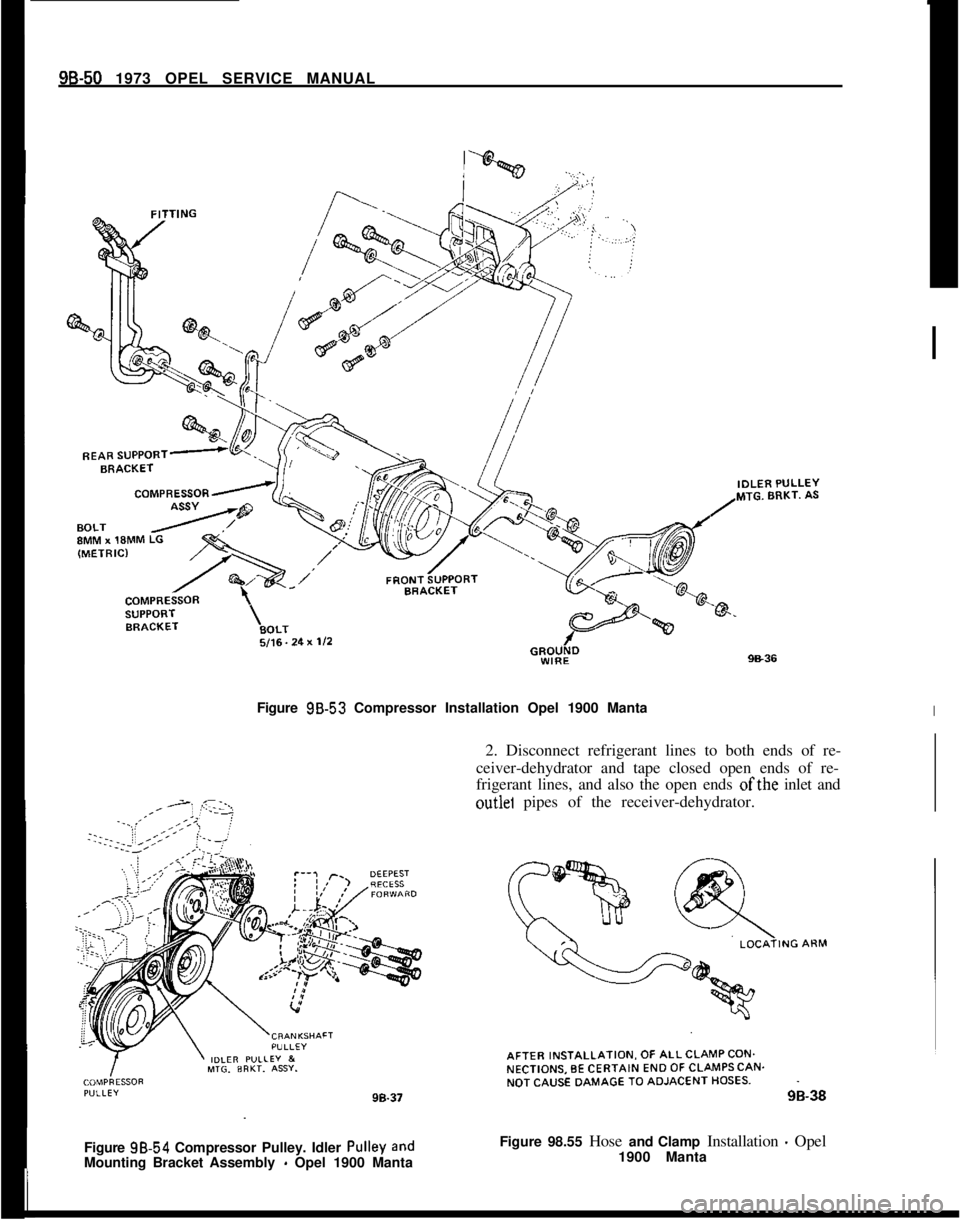
96-50 1973 OPEL SERVICE MANUALIFigure 98.53 Compressor Installation Opel 1900 Manta
I2. Disconnect refrigerant lines to both ends of re-
ceiver-dehydrator and tape closed open ends of re-
frigerant lines, and also the open ends ofthe inlet andoutlel pipes of the receiver-dehydrator.
IFigure 98.54 Compressor Pulley. Idler
Pulley andFigure 98.55 Hose and Clamp Installation - Opel
Mounting Bracket Assembly
- Opel 1900 Manta1900 Manta
Page 560 of 625
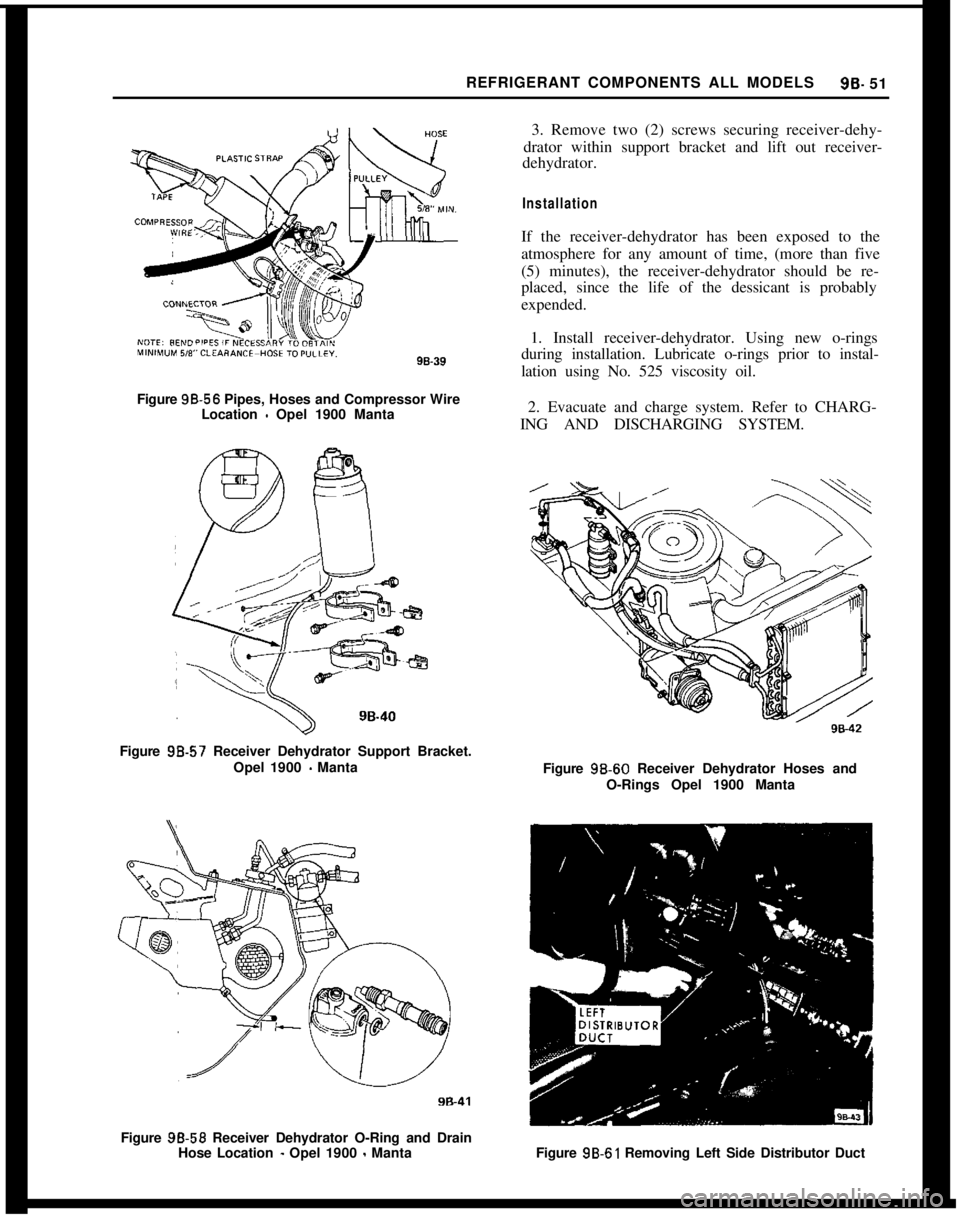
REFRIGERANT COMPONENTS ALL MODELSSB- 51
3. Remove two (2) screws securing receiver-dehy-
drator within support bracket and lift out receiver-
dehydrator.
InstallationIf the receiver-dehydrator has been exposed to the
atmosphere for any amount of time, (more than five
(5) minutes), the receiver-dehydrator should be re-
placed, since the life of the dessicant is probably
expended.
1. Install receiver-dehydrator. Using new o-rings
during installation. Lubricate o-rings prior to instal-
lation using No. 525 viscosity oil.
Figure 98.56 Pipes, Hoses and Compressor Wire
Location
- Opel 1900 Manta2. Evacuate and charge system. Refer to CHARG-
ING AND DISCHARGING SYSTEM.
Figure 98.57 Receiver Dehydrator Support Bracket.
Opel 1900
- Manta
Figure 98-59 Receiver Dehydrator O-Ring and Drain
Hose Location
- Opel 1900 - MantaFigure 9B-60 Receiver Dehydrator Hoses and
O-Rings Opel 1900 Manta
Figure 9B-61 Removing Left Side Distributor Duct