torque OPEL GT-R 1973 Manual Online
[x] Cancel search | Manufacturer: OPEL, Model Year: 1973, Model line: GT-R, Model: OPEL GT-R 1973Pages: 625, PDF Size: 17.22 MB
Page 304 of 625
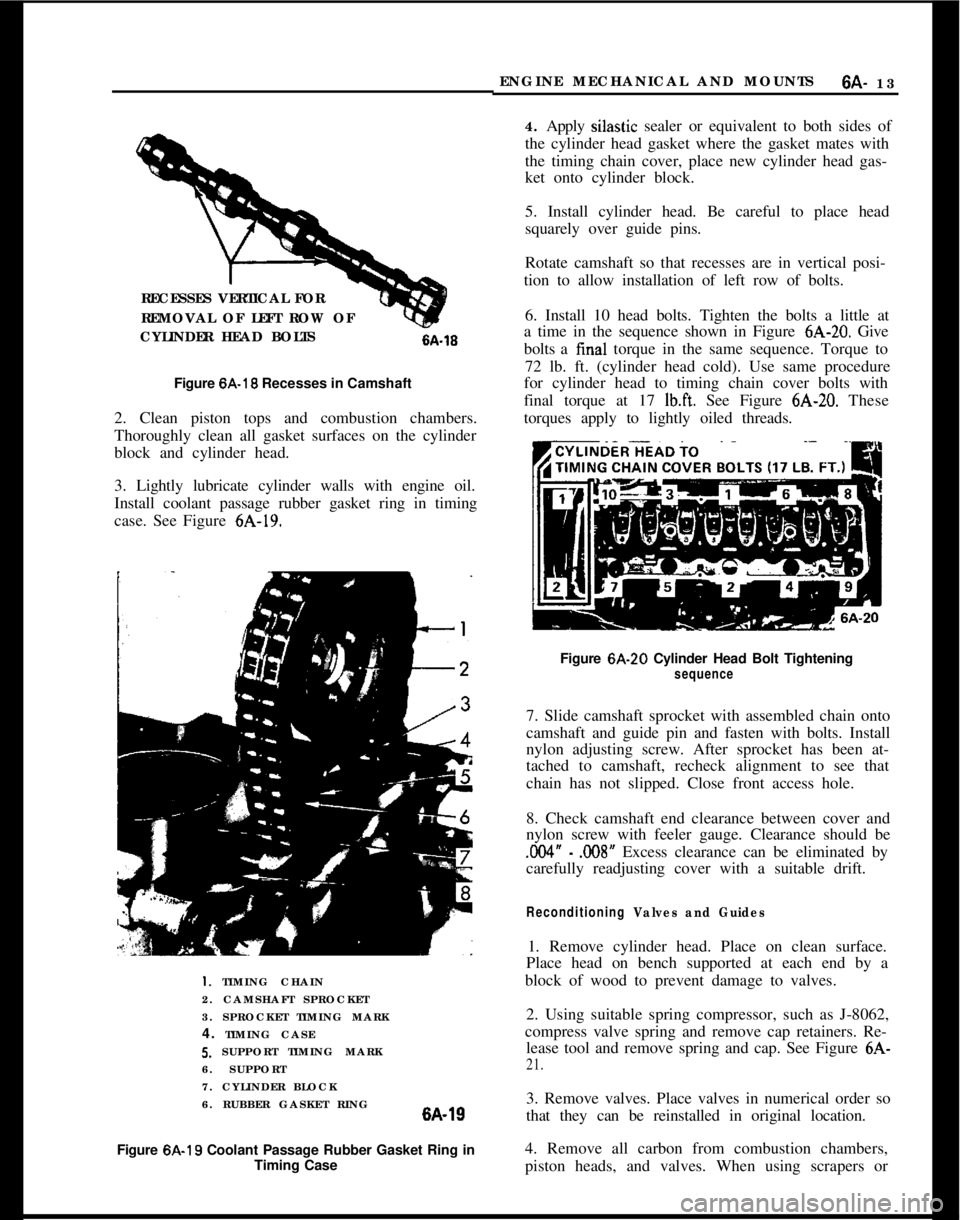
RECESSES VERTICAL FOR
REMOVAL OF LEFT ROW OF
CYLINDER HEAD BOLTS6A-16
Figure 6A-18 Recesses in Camshaft
2. Clean piston tops and combustion chambers.
Thoroughly clean all gasket surfaces on the cylinder
block and cylinder head.
3. Lightly lubricate cylinder walls with engine oil.
Install coolant passage rubber gasket ring in timing
case. See Figure 6A-19.I. TIMING CHAIN
2. CAMSHAFT SPROCKET
3. SPROCKET TIMING MARK
4. TIMING CASE5. SUPPORT TIMING MARK
6. SUPPORT
7. CYLINDER BLOCK
6. RUBBER GASKET RING6A-19
Figure 6A-19 Coolant Passage Rubber Gasket Ring in
Timing CaseENGINE MECHANICAL AND MOUNTS
6A- 13
4. Apply silastic sealer or equivalent to both sides of
the cylinder head gasket where the gasket mates with
the timing chain cover, place new cylinder head gas-
ket onto cylinder block.
5. Install cylinder head. Be careful to place head
squarely over guide pins.
Rotate camshaft so that recesses are in vertical posi-
tion to allow installation of left row of bolts.
6. Install 10 head bolts. Tighten the bolts a little at
a time in the sequence shown in Figure 6A-20. Give
bolts a final torque in the same sequence. Torque to
72 lb. ft. (cylinder head cold). Use same procedure
for cylinder head to timing chain cover bolts with
final torque at 17
lb.ft. See Figure 6A-20. These
torques apply to lightly oiled threads.
Figure 6A-20 Cylinder Head Bolt Tightening
sequence7. Slide camshaft sprocket with assembled chain onto
camshaft and guide pin and fasten with bolts. Install
nylon adjusting screw. After sprocket has been at-
tached to camshaft, recheck alignment to see that
chain has not slipped. Close front access hole.
8. Check camshaft end clearance between cover and
nylon screw with feeler gauge. Clearance should be
.004” - .008” Excess clearance can be eliminated by
carefully readjusting cover with a suitable drift.
Reconditioning Valves and Guides1. Remove cylinder head. Place on clean surface.
Place head on bench supported at each end by a
block of wood to prevent damage to valves.
2. Using suitable spring compressor, such as J-8062,
compress valve spring and remove cap retainers. Re-
lease tool and remove spring and cap. See Figure 6A-
21.3. Remove valves. Place valves in numerical order so
that they can be reinstalled in original location.
4. Remove all carbon from combustion chambers,
piston heads, and valves. When using scrapers or
Page 306 of 625
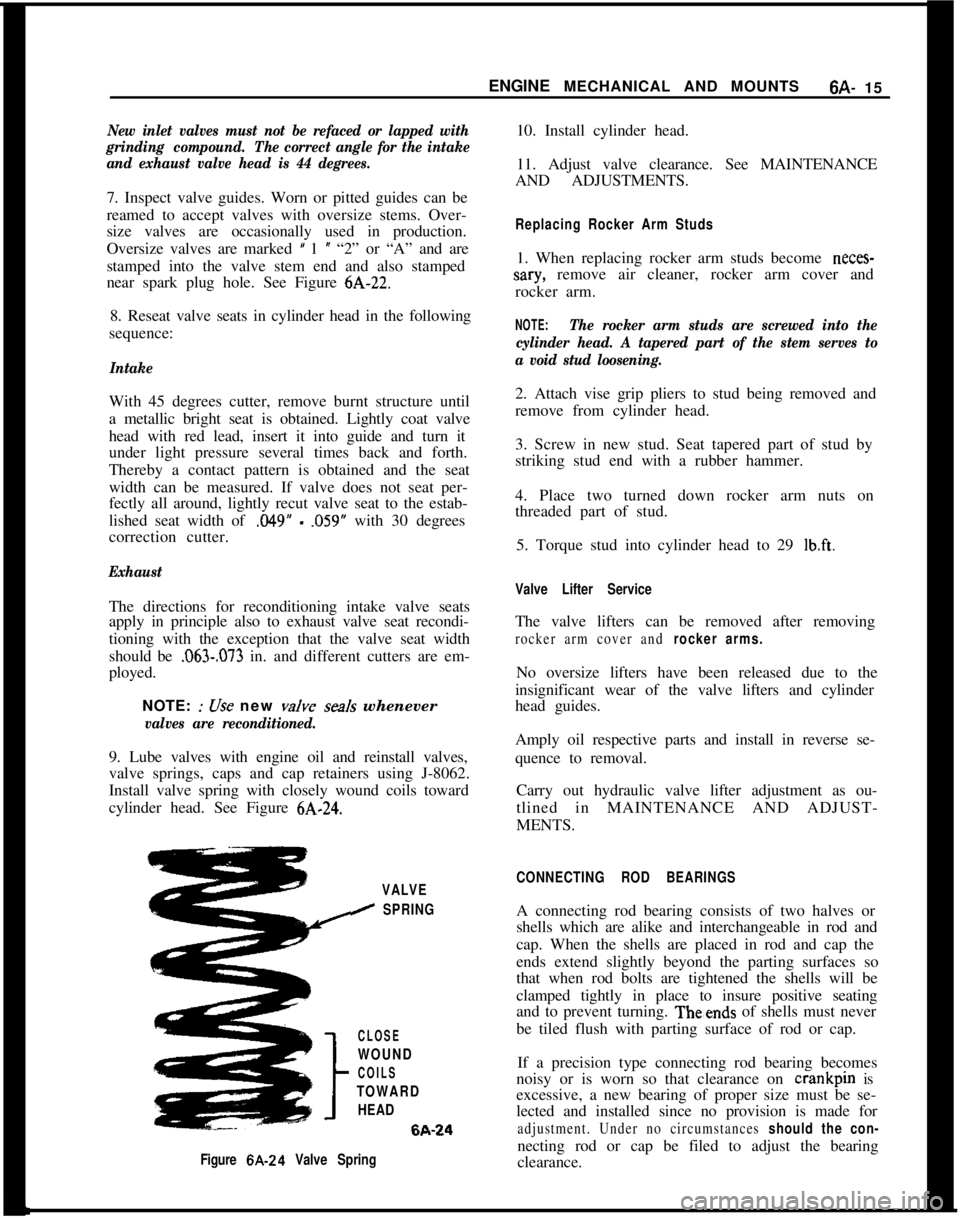
ENGINE MECHANICAL AND MOUNTS6A- 15New inlet valves must not be refaced or lapped with
grinding compound.The correct angle for the intake
and exhaust valve head is 44 degrees.10. Install cylinder head.
11. Adjust valve clearance. See MAINTENANCE
AND ADJUSTMENTS.
7. Inspect valve guides. Worn or pitted guides can be
reamed to accept valves with oversize stems. Over-
size valves are occasionally used in production.
Oversize valves are marked
’ 1 u “2” or “A” and are
stamped into the valve stem end and also stamped
near spark plug hole. See Figure 6A-22.
Replacing Rocker Arm Studs1. When replacing rocker arm studs become
neces-
sary, remove air cleaner, rocker arm cover and
rocker arm.
8. Reseat valve seats in cylinder head in the following
sequence:
Intake
NOTE:The rocker arm studs are screwed into the
cylinder head. A tapered part of the stem serves to
a void stud loosening.With 45 degrees cutter, remove burnt structure until
a metallic bright seat is obtained. Lightly coat valve
head with red lead, insert it into guide and turn it
under light pressure several times back and forth.
Thereby a contact pattern is obtained and the seat
width can be measured. If valve does not seat per-
fectly all around, lightly recut valve seat to the estab-
lished seat width of
,049” - .059” with 30 degrees
correction cutter.
ExhaustThe directions for reconditioning intake valve seats
apply in principle also to exhaust valve seat recondi-
tioning with the exception that the valve seat width
should be
.063-,073 in. and different cutters are em-
ployed.
NOTE:
: OTse new valve seals whenever
valves are reconditioned.9. Lube valves with engine oil and reinstall valves,
valve springs, caps and cap retainers using J-8062.
Install valve spring with closely wound coils toward
cylinder head. See Figure
6A-24.2. Attach vise grip pliers to stud being removed and
remove from cylinder head.
3. Screw in new stud. Seat tapered part of stud by
striking stud end with a rubber hammer.
4. Place two turned down rocker arm nuts on
threaded part of stud.
5. Torque stud into cylinder head to 29
lb.ft.
Valve Lifter ServiceThe valve lifters can be removed after removing
rocker arm cover and rocker arms.No oversize lifters have been released due to the
insignificant wear of the valve lifters and cylinder
head guides.
Amply oil respective parts and install in reverse se-
quence to removal.
Carry out hydraulic valve lifter adjustment as ou-
tlined in MAINTENANCE AND ADJUST-
MENTS.
VALVE
I SPRING
CLOSE
WOUND
COILS
TOWARD
HEAD6A-24
Figure 6A-24 Valve SpringCONNECTING ROD BEARINGSA connecting rod bearing consists of two halves or
shells which are alike and interchangeable in rod and
cap. When the shells are placed in rod and cap the
ends extend slightly beyond the parting surfaces so
that when rod bolts are tightened the shells will be
clamped tightly in place to insure positive seating
and to prevent turning. Theends of shells must never
be tiled flush with parting surface of rod or cap.
If a precision type connecting rod bearing becomes
noisy or is worn so that clearance on crankpin is
excessive, a new bearing of proper size must be se-
lected and installed since no provision is made for
adjustment. Under no circumstances should the con-necting rod or cap be filed to adjust the bearing
clearance.
Page 309 of 625
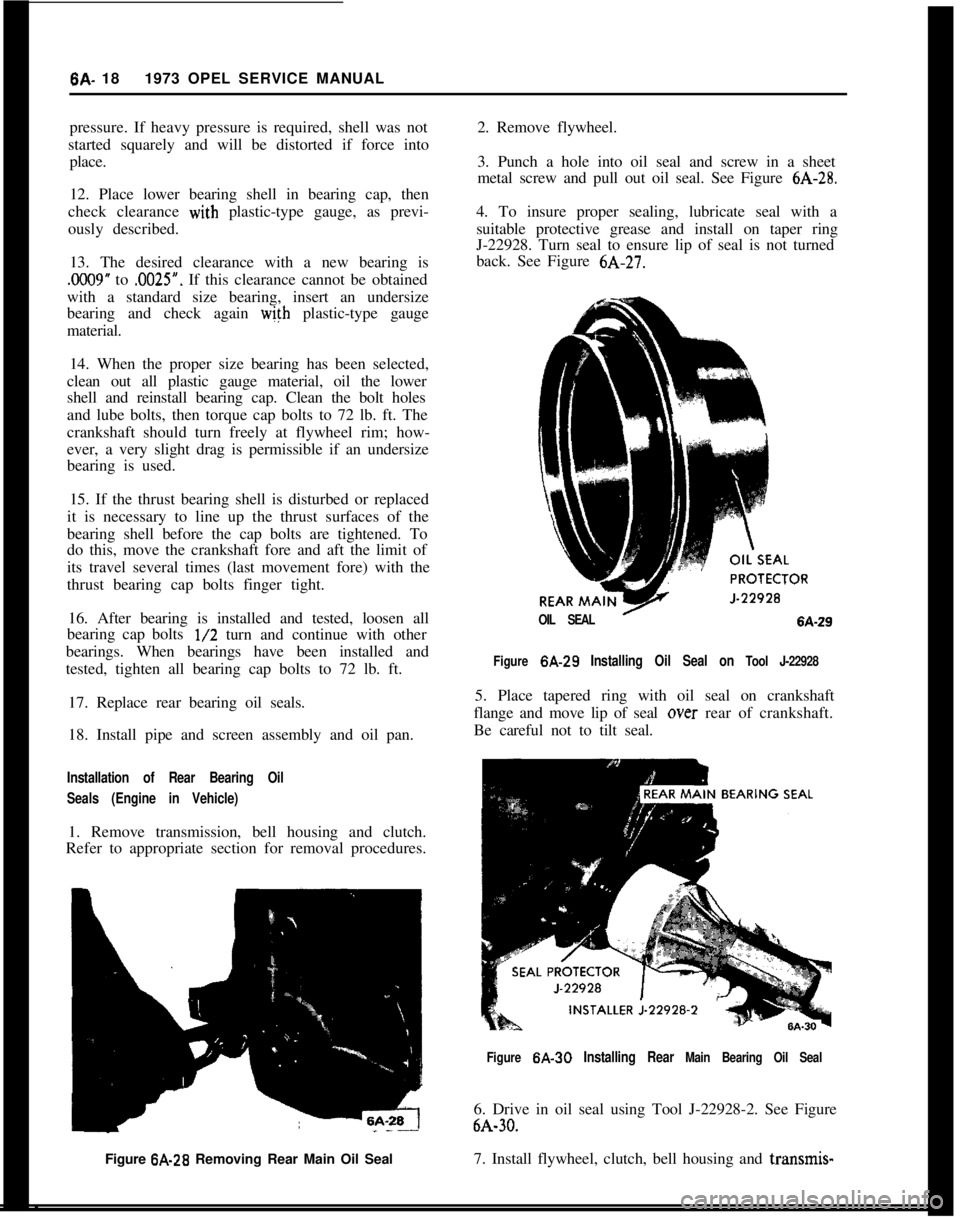
6A- 18 1973 OPEL SERVICE MANUAL
pressure. If heavy pressure is required, shell was not
started squarely and will be distorted if force into place.
12. Place lower bearing shell in bearing cap, then
check clearance
with plastic-type gauge, as previ-
ously described.
13. The desired clearance with a new bearing is
.0009” to .0025”. If this clearance cannot be obtained
with a standard size bearing, insert an undersize
bearing and check again
w&h plastic-type gauge
material.
14. When the proper size bearing has been selected,
clean out all plastic gauge material, oil the lower
shell and reinstall bearing cap. Clean the bolt holes
and lube bolts, then torque cap bolts to 72 lb. ft. The
crankshaft should turn freely at flywheel rim; how-
ever, a very slight drag is permissible if an undersize
bearing is used.
15. If the thrust bearing shell is disturbed or replaced
it is necessary to line up the thrust surfaces of the
bearing shell before the cap bolts are tightened. To
do this, move the crankshaft fore and aft the limit of
its travel several times (last movement fore) with the
thrust bearing cap bolts finger tight.
16. After bearing is installed and tested, loosen all
bearing cap bolts
l/2 turn and continue with other
bearings. When bearings have been installed and
tested, tighten all bearing cap bolts to 72 lb. ft.
17. Replace rear bearing oil seals.
18. Install pipe and screen assembly and oil pan.
Installation of Rear Bearing Oil
Seals (Engine in Vehicle)
1. Remove transmission, bell housing and clutch.
Refer to appropriate section for removal procedures.
Figure 6A-28 Removing Rear Main Oil Seal
2. Remove flywheel.
3. Punch a hole into oil seal and screw in a sheet
metal screw and pull out oil seal. See Figure
6A-28.
4. To insure proper sealing, lubricate seal with a
suitable protective grease and install on taper ring
J-22928. Turn seal to ensure lip of seal is not turned
back. See Figure
6A-27.
OIL SEAL’6A-29
Figure
6A-29 Installing Oil Seal on Tool J-22928
5. Place tapered ring with oil seal on crankshaft
flange and move lip of seal
over rear of crankshaft.
Be careful not to tilt seal.
Figure 6A-30 Installing Rear Main Bearing Oil Seal
6. Drive in oil seal using Tool J-22928-2. See Figure
6A-30.
7. Install flywheel, clutch, bell housing and transmis-
.
Page 310 of 625
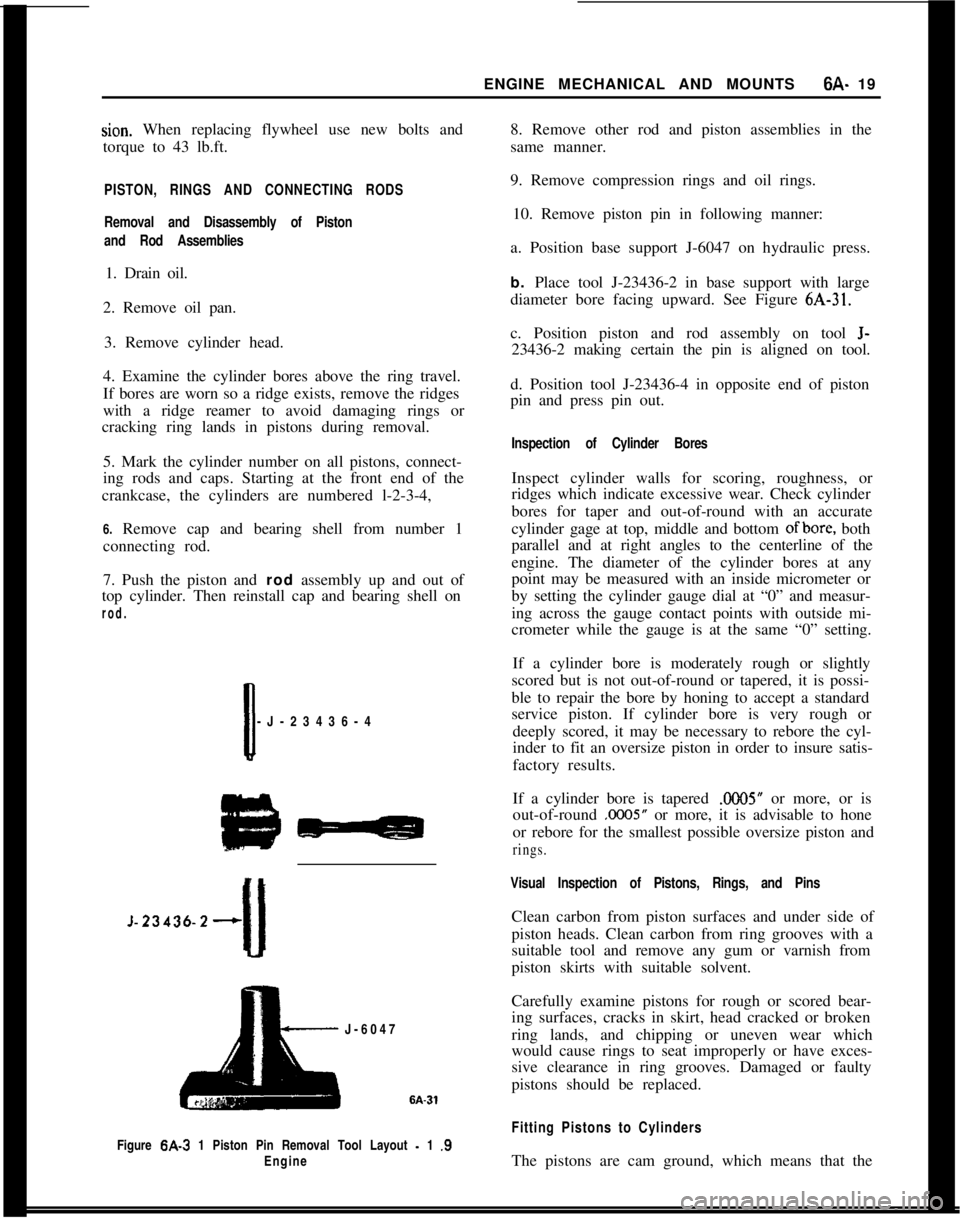
ENGINE MECHANICAL AND MOUNTS6A- 19
sion. When replacing flywheel use new bolts and
torque to 43 lb.ft.
PISTON, RINGS AND CONNECTING RODS
Removal and Disassembly of Piston
and Rod Assemblies
1. Drain oil.
2. Remove oil pan. 3. Remove cylinder head.
4. Examine the cylinder bores above the ring travel.
If bores are worn so a ridge exists, remove the ridges
with a ridge reamer to avoid damaging rings or
cracking ring lands in pistons during removal.
5. Mark the cylinder number on all pistons, connect-
ing rods and caps. Starting at the front end of the
crankcase, the cylinders are numbered l-2-3-4,
6. Remove cap and bearing shell from number 1
connecting rod.
7. Push the piston and
rod assembly up and out of
top cylinder. Then reinstall cap and bearing shell on
rod.
0
-J-23436-4
J-23436-2+
J-6047
Figure
6A-3 1 Piston Pin Removal Tool Layout - 1 .S
Engine
8. Remove other rod and piston assemblies in the
same manner.
9. Remove compression rings and oil rings.
10. Remove piston pin in following manner:
a. Position base support J-6047 on hydraulic press.
b. Place tool J-23436-2 in base support with large
diameter bore facing upward. See Figure
6A-31.
c. Position piston and rod assembly on tool
J-
23436-2 making certain the pin is aligned on tool.
d. Position tool J-23436-4 in opposite end of piston
pin and press pin out.
Inspection of Cylinder Bores
Inspect cylinder walls for scoring, roughness, or
ridges which indicate excessive wear. Check cylinder
bores for taper and out-of-round with an accurate
cylinder gage at top, middle and bottom
ofbore, both
parallel and at right angles to the centerline of the
engine. The diameter of the cylinder bores at any
point may be measured with an inside micrometer or
by setting the cylinder gauge dial at “0” and measur-
ing across the gauge contact points with outside mi-
crometer while the gauge is at the same “0” setting.
If a cylinder bore is moderately rough or slightly
scored but is not out-of-round or tapered, it is possi-
ble to repair the bore by honing to accept a standard
service piston. If cylinder bore is very rough or deeply scored, it may be necessary to rebore the cyl-
inder to fit an oversize piston in order to insure satis-
factory results.
If a cylinder bore is tapered
.ooO5” or more, or is
out-of-round
.0005” or more, it is advisable to hone
or rebore for the smallest possible oversize piston and
rings.
Visual Inspection of Pistons, Rings, and Pins
Clean carbon from piston surfaces and under side of
piston heads. Clean carbon from ring grooves with a
suitable tool and remove any gum or varnish from
piston skirts with suitable solvent.
Carefully examine pistons for rough or scored bear-
ing surfaces, cracks in skirt, head cracked or broken
ring lands, and chipping or uneven wear which
would cause rings to seat improperly or have exces-
sive clearance in ring grooves. Damaged or faulty
pistons should be replaced.
Fitting Pistons to Cylinders
The pistons are cam ground, which means that the
Page 311 of 625
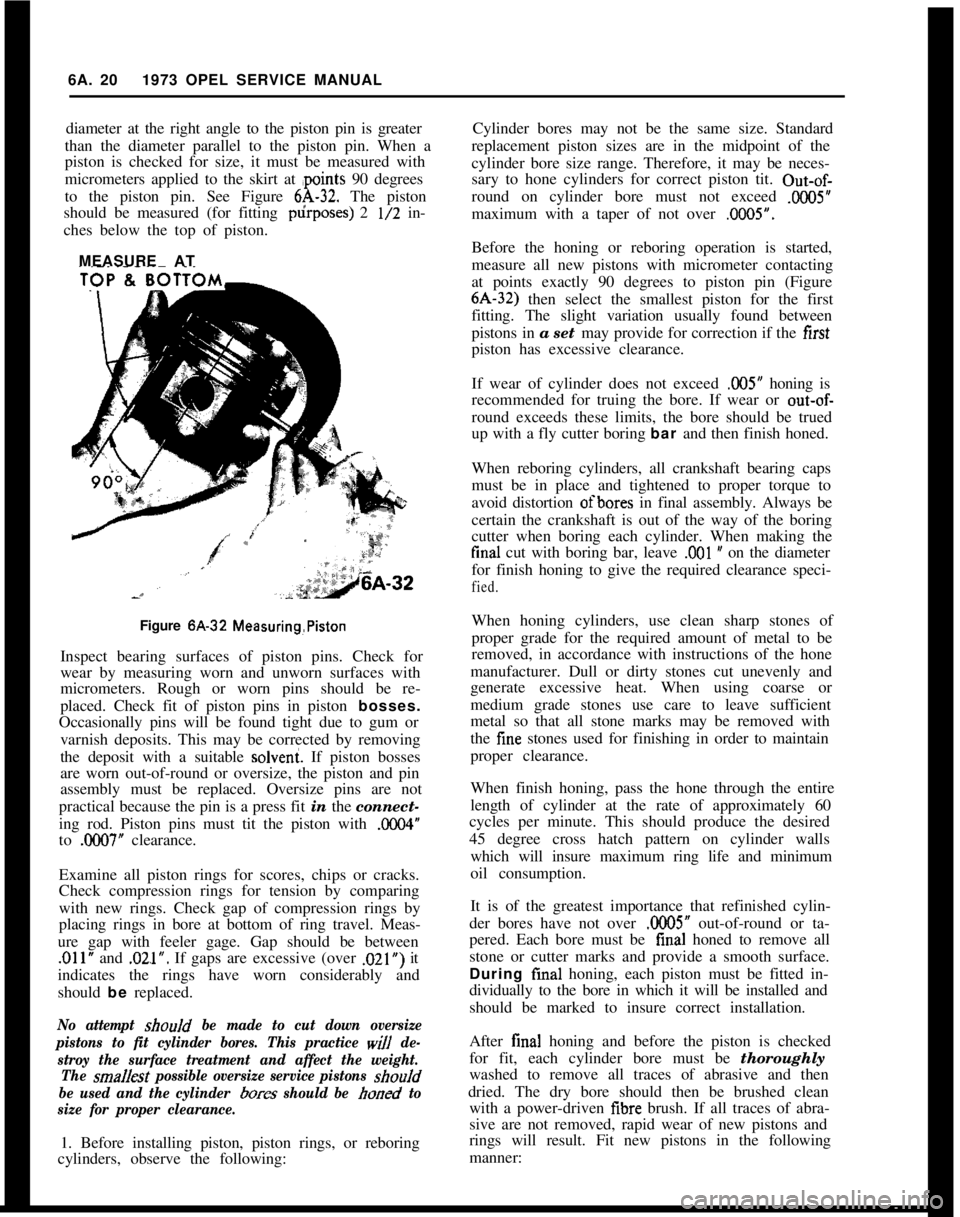
6A. 201973 OPEL SERVICE MANUAL
diameter at the right angle to the piston pin is greater
than the diameter parallel to the piston pin. When a
piston is checked for size, it must be measured with
micrometers applied to the skirt at ,points 90 degrees
to the piston pin. See Figure
6A-32. The piston
should be measured (for fitting p&poses) 2
l/2 in-
ches below the top of piston.
MEASURE AT
Figure 6A-32
Measuring,PistonInspect bearing surfaces of piston pins. Check for
wear by measuring worn and unworn surfaces with
micrometers. Rough or worn pins should be re-
placed. Check fit of piston pins in piston bosses.
Occasionally pins will be found tight due to gum or
varnish deposits. This may be corrected by removing
the deposit with a suitable solveni. If piston bosses
are worn out-of-round or oversize, the piston and pin
assembly must be replaced. Oversize pins are not
practical because the pin is a press fit in the connect-
ing rod. Piston pins must tit the piston with
0X4”to
.OCHl7” clearance.
Examine all piston rings for scores, chips or cracks.
Check compression rings for tension by comparing
with new rings. Check gap of compression rings by
placing rings in bore at bottom of ring travel. Meas-
ure gap with feeler gage. Gap should be between
,011” and .02.1”. If gaps are excessive (over .021”) it
indicates the rings have worn considerably and
should be replaced.
No attempt should be made to cut down oversize
pistons to fit cylinder bores. This practice
will de-
stroy the surface treatment and affect the weight.
The
sma/Jest possible oversize service pistons shouId
be used and the cylinder
bores should be honed to
size for proper clearance.1. Before installing piston, piston rings, or reboring
cylinders, observe the following:Cylinder bores may not be the same size. Standard
replacement piston sizes are in the midpoint of the
cylinder bore size range. Therefore, it may be neces-
sary to hone cylinders for correct piston tit. Out-of-
round on cylinder bore must not exceed
.ooO5”maximum with a taper of not over
.OilO5”.Before the honing or reboring operation is started,
measure all new pistons with micrometer contacting
at points exactly 90 degrees to piston pin (Figure6A-32) then select the smallest piston for the first
fitting. The slight variation usually found between
pistons in a set may provide for correction if the first
piston has excessive clearance.
If wear of cylinder does not exceed
.005” honing is
recommended for truing the bore. If wear or
out-of-round exceeds these limits, the bore should be trued
up with a fly cutter boring bar and then finish honed.
When reboring cylinders, all crankshaft bearing caps
must be in place and tightened to proper torque to
avoid distortion ofbores in final assembly. Always be
certain the crankshaft is out of the way of the boring
cutter when boring each cylinder. When making thefinal cut with boring bar, leave
,001 w on the diameter
for finish honing to give the required clearance speci-
fied.When honing cylinders, use clean sharp stones of
proper grade for the required amount of metal to be
removed, in accordance with instructions of the hone
manufacturer. Dull or dirty stones cut unevenly and
generate excessive heat. When using coarse or
medium grade stones use care to leave sufficient
metal so that all stone marks may be removed with
the fine stones used for finishing in order to maintain
proper clearance.
When finish honing, pass the hone through the entire
length of cylinder at the rate of approximately 60
cycles per minute. This should produce the desired
45 degree cross hatch pattern on cylinder walls
which will insure maximum ring life and minimum
oil consumption.
It is of the greatest importance that refinished cylin-
der bores have not over
.0005” out-of-round or ta-
pered. Each bore must be final honed to remove all
stone or cutter marks and provide a smooth surface.
During final honing, each piston must be fitted in-
dividually to the bore in which it will be installed and
should be marked to insure correct installation.
After final honing and before the piston is checked
for fit, each cylinder bore must be thoroughly
washed to remove all traces of abrasive and then
dried. The dry bore should then be brushed clean
with a power-driven iibre brush. If all traces of abra-
sive are not removed, rapid wear of new pistons and
rings will result. Fit new pistons in the following
manner:
Page 314 of 625
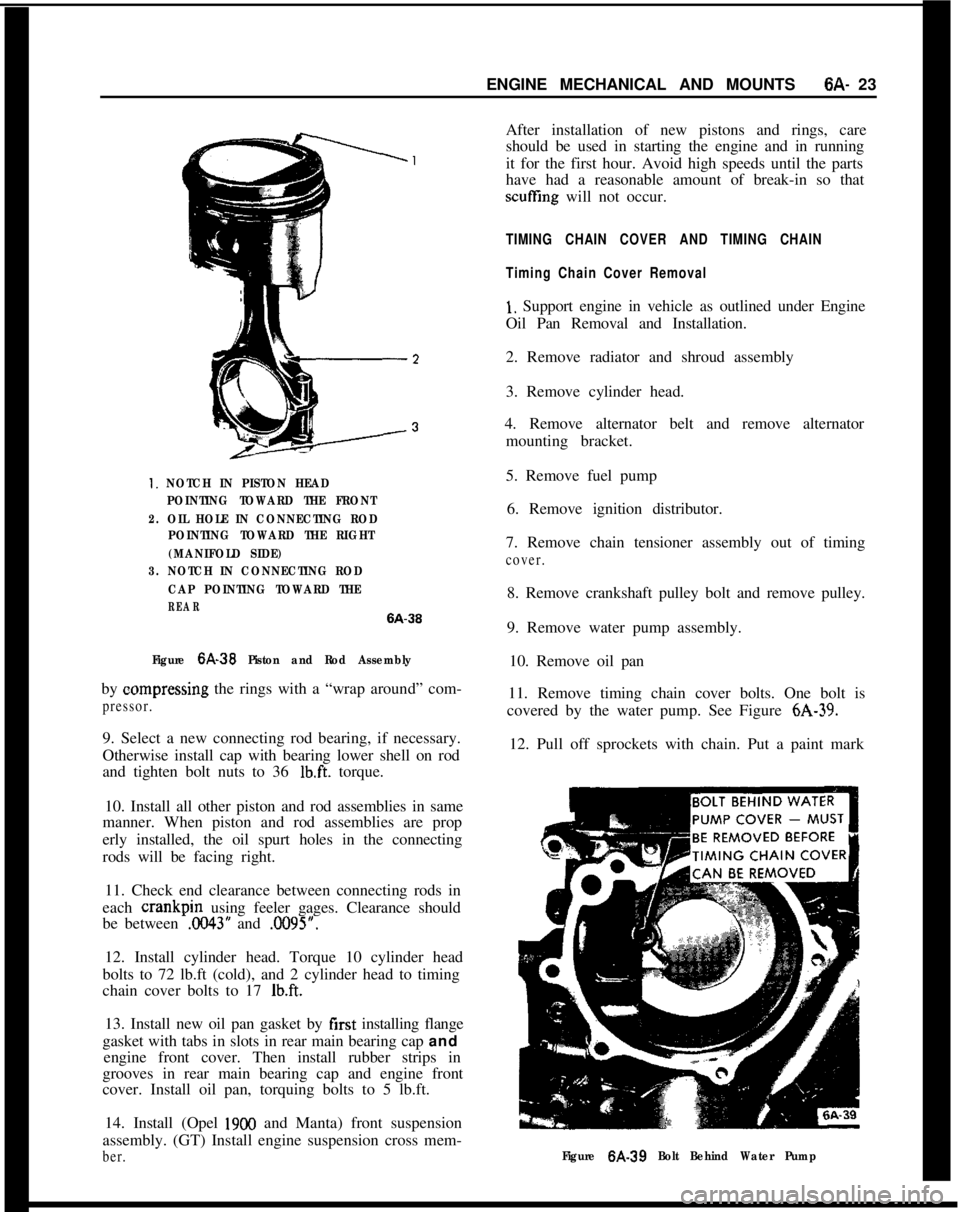
ENGINE MECHANICAL AND MOUNTS6A- 231. NOTCH IN PISTON HEAD
POINTING TOWARD THE FRONT
2. OIL HOLE IN CONNECTING ROD
POINTING TOWARD THE RIGHT
(MANIFOLD SIDE)
3. NOTCH IN CONNECTING ROD
CAP POINTING TOWARD THE
REAR6A-36
Figure
6A-39 Piston and Rod Assemblyby oompressing the rings with a “wrap around” com-
pressor.9. Select a new connecting rod bearing, if necessary.
Otherwise install cap with bearing lower shell on rod
and tighten bolt nuts to 36
lb.ft. torque.
10. Install all other piston and rod assemblies in same
manner. When piston and rod assemblies are prop
erly installed, the oil spurt holes in the connecting
rods will be facing right.
11. Check end clearance between connecting rods in
each crankpin using feeler gages. Clearance should
be between
.0043” and .0095”.
12. Install cylinder head. Torque 10 cylinder head
bolts to 72 lb.ft (cold), and 2 cylinder head to timing
chain cover bolts to 17
lb.ft.13. Install new oil pan gasket by first installing flange
gasket with tabs in slots in rear main bearing cap and
engine front cover. Then install rubber strips in
grooves in rear main bearing cap and engine front
cover. Install oil pan, torquing bolts to 5 lb.ft.
14. Install (Opel
1900 and Manta) front suspension
assembly. (GT) Install engine suspension cross mem-
ber.After installation of new pistons and rings, care
should be used in starting the engine and in running
it for the first hour. Avoid high speeds until the parts
have had a reasonable amount of break-in so that
scuffling will not occur.
TIMING CHAIN COVER AND TIMING CHAIN
Timing Chain Cover Removal
1, Support engine in vehicle as outlined under Engine
Oil Pan Removal and Installation.
2. Remove radiator and shroud assembly
3. Remove cylinder head.
4. Remove alternator belt and remove alternator
mounting bracket.
5. Remove fuel pump
6. Remove ignition distributor.
7. Remove chain tensioner assembly out of timing
cover.8. Remove crankshaft pulley bolt and remove pulley.
9. Remove water pump assembly.
10. Remove oil pan
11. Remove timing chain cover bolts. One bolt is
covered by the water pump. See Figure 6A-39.
12. Pull off sprockets with chain. Put a paint mark
Figure 6A-39 Bolt Behind Water Pump
Page 316 of 625
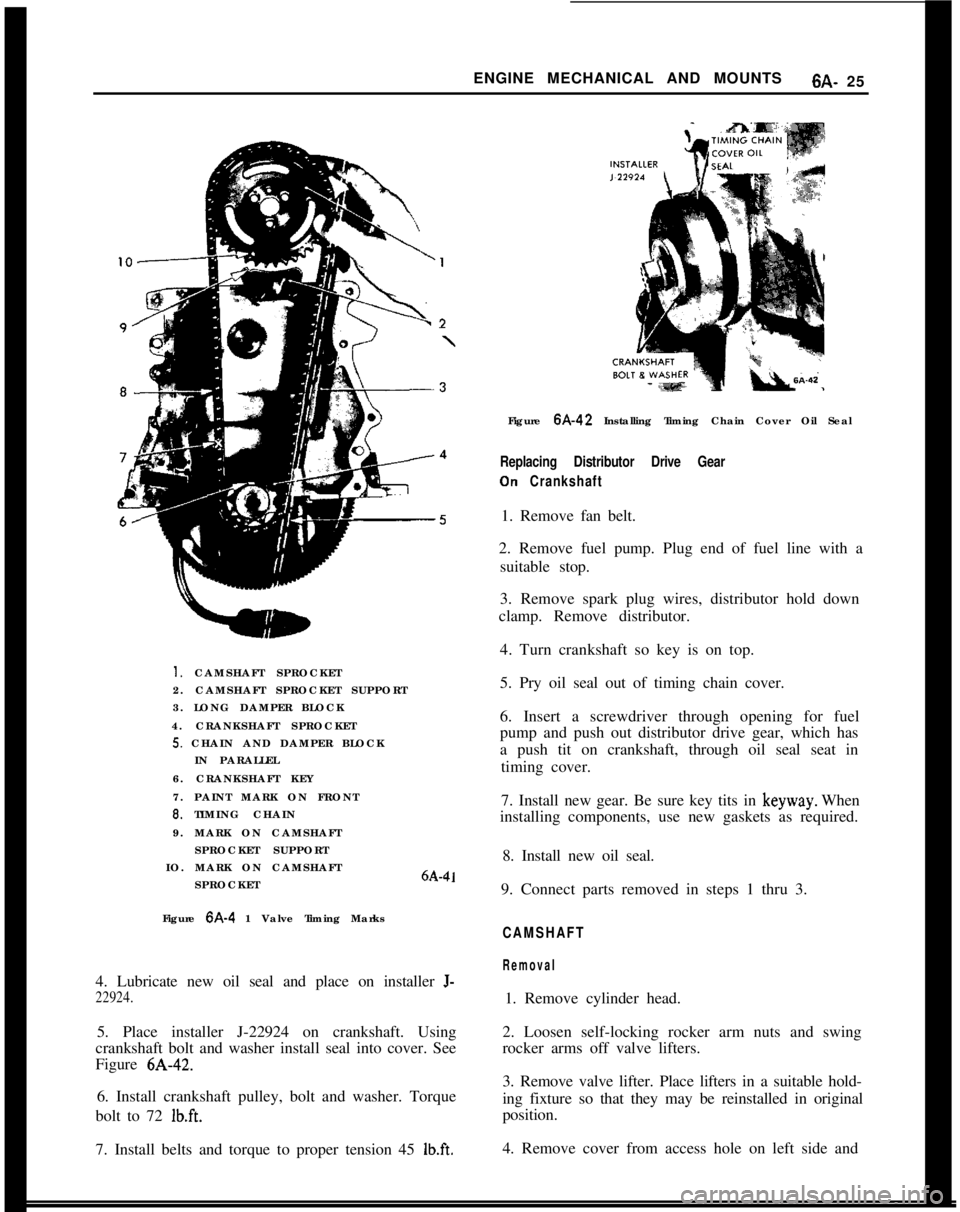
ENGINE MECHANICAL AND MOUNTS6A- 251, CAMSHAFT SPROCKET
2. CAMSHAFT SPROCKET SUPPORT
3. LONG DAMPER BLOCK
4. CRANKSHAFT SPROCKET
5. CHAIN AND DAMPER BLOCK
IN PARALLEL
6. CRANKSHAFT KEY
7. PAINT MARK ON FRONT
8. TIMING CHAIN
9. MARK ON CAMSHAFT
SPROCKET SUPPORT
IO. MARK ON CAMSHAFT
SPROCKET
6A-41Figure 6A-4 1 Valve Timing Marks
Removal4. Lubricate new oil seal and place on installer
J-
22924.1. Remove cylinder head.
5. Place installer J-22924 on crankshaft. Using
crankshaft bolt and washer install seal into cover. See
Figure 6A-42.2. Loosen self-locking rocker arm nuts and swing
rocker arms off valve lifters.
6. Install crankshaft pulley, bolt and washer. Torque
bolt to 72
Ib.ft.3. Remove valve lifter. Place lifters in a suitable hold-
ing fixture so that they may be reinstalled in original
position.
7. Install belts and torque to proper tension 45
lb.ft.4. Remove cover from access hole on left side andFigure 6A-42 Installing Timing Chain Cover Oil Seal
Replacing Distributor Drive Gear
On Crankshaft1. Remove fan belt.
2. Remove fuel pump. Plug end of fuel line with a
suitable stop.
3. Remove spark plug wires, distributor hold down
clamp. Remove distributor.
4. Turn crankshaft so key is on top.
5. Pry oil seal out of timing chain cover.
6. Insert a screwdriver through opening for fuel
pump and push out distributor drive gear, which has
a push tit on crankshaft, through oil seal seat in
timing cover.
7. Install new gear. Be sure key tits in
keyway. When
installing components, use new gaskets as required.
8. Install new oil seal.
9. Connect parts removed in steps 1 thru 3.
CAMSHAFT
Page 318 of 625
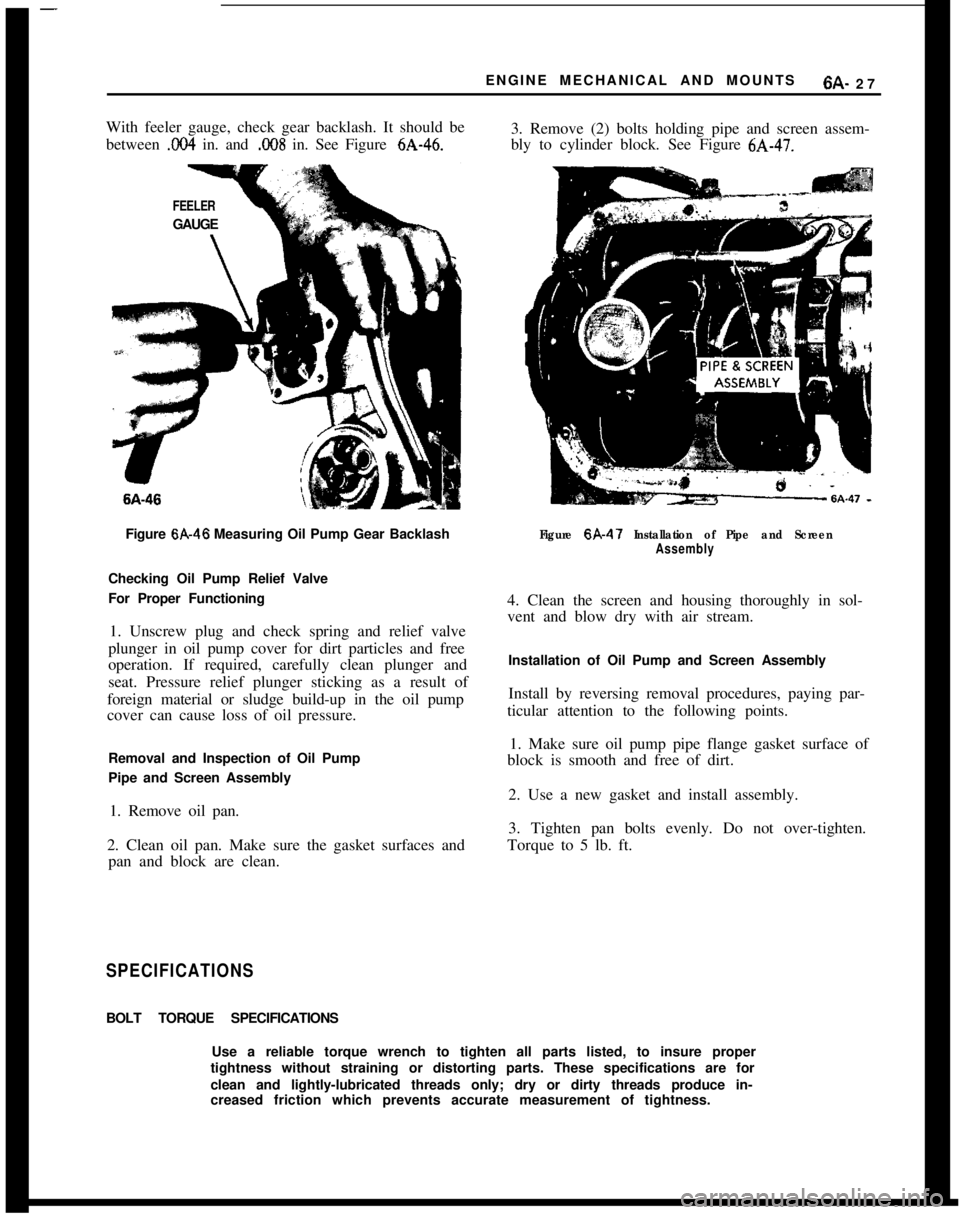
ENGINE MECHANICAL AND MOUNTS6A- 27
With feeler gauge, check gear backlash. It should be
between
.I?04 in. and .C!OS in. See Figure 6A-46.3. Remove (2) bolts holding pipe and screen assem-
bly to cylinder block. See Figure 6A-47.
FEELERGAUGE6A-46
Figure 6A-46 Measuring Oil Pump Gear Backlash
Checking Oil Pump Relief Valve
For Proper Functioning
1. Unscrew plug and check spring and relief valve
plunger in oil pump cover for dirt particles and free
operation. If required, carefully clean plunger and
seat. Pressure relief plunger sticking as a result of
foreign material or sludge build-up in the oil pump
cover can cause loss of oil pressure.
Removal and Inspection of Oil Pump
Pipe and Screen Assembly
1. Remove oil pan.
2. Clean oil pan. Make sure the gasket surfaces and
pan and block are clean.
Figure 6A-47 Installation of Pipe and Screen
Assembly4. Clean the screen and housing thoroughly in sol-
vent and blow dry with air stream.
Installation of Oil Pump and Screen Assembly
Install by reversing removal procedures, paying par-
ticular attention to the following points.
1. Make sure oil pump pipe flange gasket surface of
block is smooth and free of dirt.
2. Use a new gasket and install assembly.
3. Tighten pan bolts evenly. Do not over-tighten.
Torque to 5 lb. ft.
SPECIFICATIONSBOLT TORQUE SPECIFICATIONS
Use a reliable torque wrench to tighten all parts listed, to insure proper
tightness without straining or distorting parts. These specifications are for
clean and lightly-lubricated threads only; dry or dirty threads produce in-
creased friction which prevents accurate measurement of tightness.
Page 319 of 625
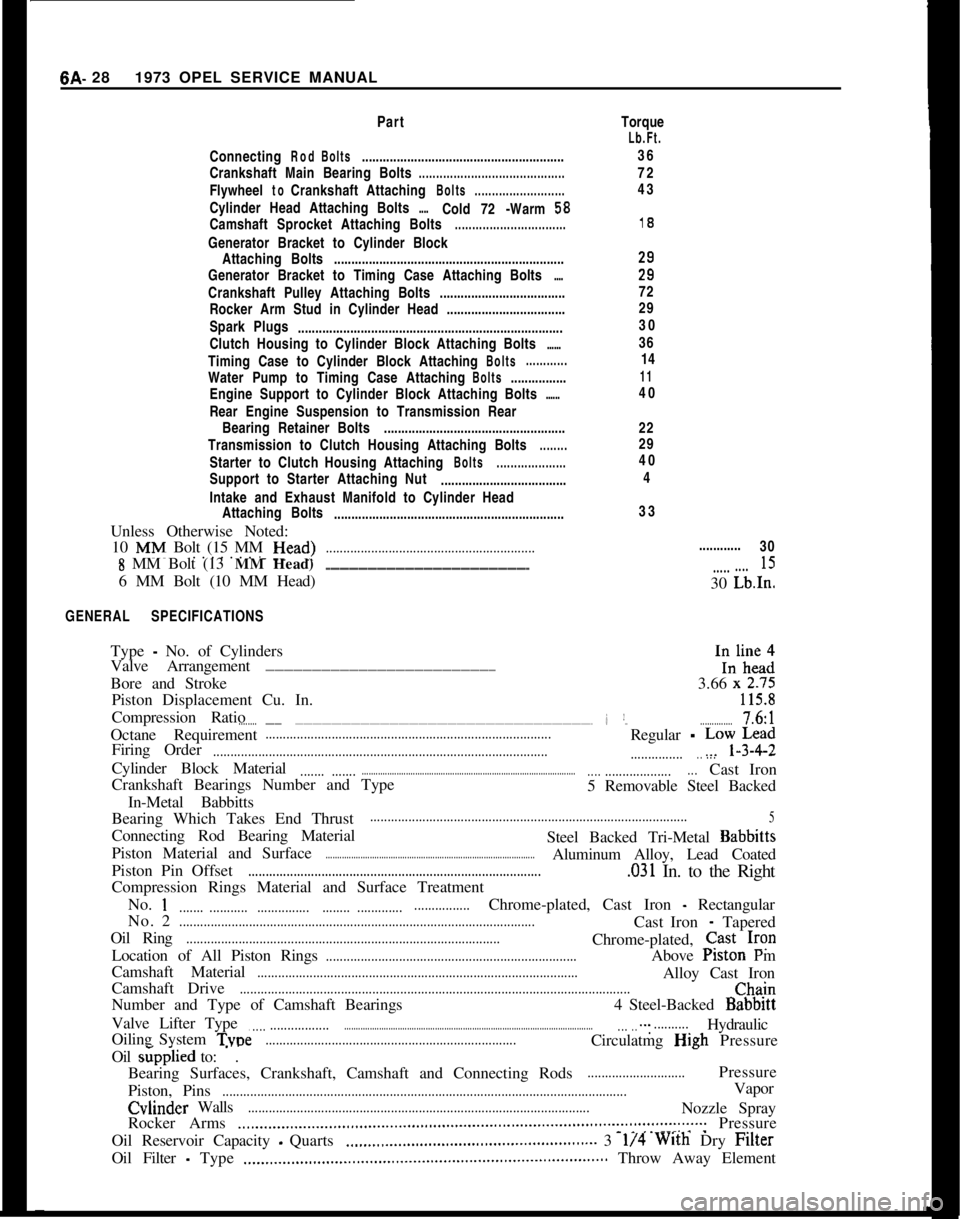
6A- 28 1973 OPEL SERVICE MANUAL
Part
ConnectingRod Bolts..........................................................
Crankshaft Main Bearing Bolts
..........................................
FlywheeltoCrankshaft AttachingBolts..........................
Cylinder Head Attaching Bolts....Cold 72 -Warm 58
Camshaft Sprocket Attaching Bolts................................
Generator Bracket to Cylinder Block
Attaching Bolts ..................................................................
Generator Bracket to Timing Case Attaching Bolts
....
Crankshaft Pulley Attaching Bolts ....................................
Rocker Arm Stud in Cylinder Head ..................................
Spark Plugs ........................................................................\
....
Clutch Housing to Cylinder Block Attaching Bolts
......
Timing Case to Cylinder Block AttachingBolts ............
Water Pump to Timing Case AttachingBolts................
Engine Support to Cylinder Block Attaching Bolts
......
Rear Engine Suspension to Transmission Rear Bearing Retainer Bolts ....................................................
Transmission to Clutch Housing Attaching Bolts
........
Starter to ClutchHousing AttachingBolts....................
Support to Starter Attaching Nut
....................................
Intake and Exhaust Manifold to Cylinder Head Attaching Bolts ..................................................................
Unless Otherwise Noted:
10
@i Bolt (15 MM Hall.....................................................................- -
36
72
43
18
;i
72
29
30
36
14
11
40
22
29
40
4
33 ............30
8 MM Bolt (13 MM Head)........................................................................\
........................................................................\
........................................15
6 MM Bolt (10 MM Head)
30 Lb.In.
Torque
Lb.Ft.
GENERAL SPECIFICATIONS
Type - No. of Cylinders
Valve Arrangement........................................................................\
........................................................................\
......................................................I;nlinzai
Bore and Stroke Piston Displacement Cu. In.
........
3.66 x1:;:;
Compression Ratio......................................................................................\
........................................................................\
........................................................................\
........................................ \fô \
²…..............7.6:1Octane Requirement........................................................................\
..........
Firing Order........................................................................\
........................
Regular - Lo;-?::
....................Cylinder Block Material....... ...............................................................................\
..............................................Cast Iron
Crankshaft Bearings Number and Type 5 Removable Steel Backed
In-Metal Babbitts
Bearing Which Takes End Thrust
........................................................................\
...................5
Connecting Rod Bearing Material
........................................................................\
..................
Steel Backed Tri-Metal Babbttts
Piston Material and Surface Aluminum Alloy, Lead Coated
Piston Pin Offset
........................................................................\
............,031 In. to the RightCompression Rings Material and Surface Treatment
No.
1....... ........... ............... ........ ............. ................Chrome-plated, Cast Iron
- Rectangular
No. 2
........................................................................\
..............................Cast Iron - Tapered
Oil Ring
........................................................................\
..................Chrome-plated, Cast Ir?n
Location of All Piston Rings
........................................................................\
Above Ptston Pm
Camshaft Material
........................................................................\
....................Alloy Cast Iron
Camshaft Drive........................................................................\
........................................Chajn
Number and Type of Camshaft Bearings 4 Steel-Backed Babbttt
Valve Lifter Type
..............................................................................................\
..........................................~..........Hydraulic
Oiling System Tvoe........................................................................\
Circulatmg High Pressure
Oil
&ppiied to: - .
Bearing Surfaces, Crankshaft, Camshaft and Connecting Rods............................Pressure
Piston, Pins
........................................................................\
............................................Vapor
Cvlinder Walls........................................................................\
..........................Nozzle Spray
Rocker Arms _,,,..,,....,._..___.,,..,,..............,,,,...,.......,..,,,.,.,,.....\
....,,...,.,.................~...... Pressure
Oil Reservoir Capacity
- Quarts .,,,...,,__.,,..,..,,..,...,..,,,...,,..............,,,... 3 l/4 With Dry Fdter
Oil Filter
- Type ,,....,__.,,...,....,....,,..,,,..,,...........,........................\
............ Throw Away Element
Page 325 of 625
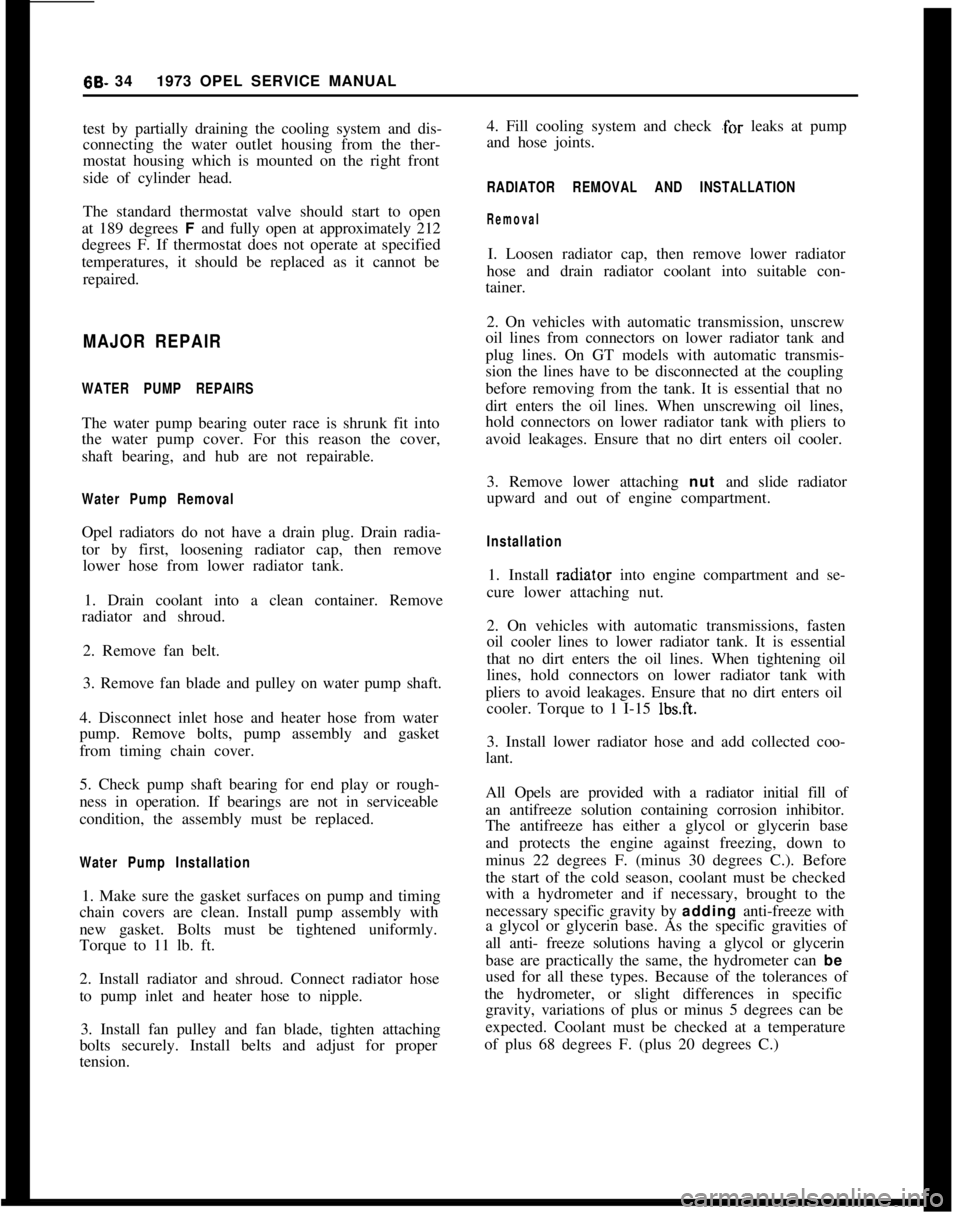
6B- 341973 OPEL SERVICE MANUAL
test by partially draining the cooling system and dis-
connecting the water outlet housing from the ther-
mostat housing which is mounted on the right front
side of cylinder head.
The standard thermostat valve should start to open
at 189 degrees F and fully open at approximately 212
degrees F. If thermostat does not operate at specified
temperatures, it should be replaced as it cannot be
repaired.MAJOR REPAIR
WATER PUMP REPAIRSThe water pump bearing outer race is shrunk fit into
the water pump cover. For this reason the cover,
shaft bearing, and hub are not repairable.
Water Pump RemovalOpel radiators do not have a drain plug. Drain radia-
tor by first, loosening radiator cap, then remove
lower hose from lower radiator tank.
1. Drain coolant into a clean container. Remove
radiator and shroud.
2. Remove fan belt.
3. Remove fan blade and pulley on water pump shaft.
4. Disconnect inlet hose and heater hose from water
pump. Remove bolts, pump assembly and gasket
from timing chain cover.
5. Check pump shaft bearing for end play or rough-
ness in operation. If bearings are not in serviceable
condition, the assembly must be replaced.
Water Pump Installation1. Make sure the gasket surfaces on pump and timing
chain covers are clean. Install pump assembly with
new gasket. Bolts must be tightened uniformly.
Torque to 11 lb. ft.
2. Install radiator and shroud. Connect radiator hose
to pump inlet and heater hose to nipple.
3. Install fan pulley and fan blade, tighten attaching
bolts securely. Install belts and adjust for proper
tension.4. Fill cooling system and check
,for leaks at pump
and hose joints.
RADIATOR REMOVAL AND INSTALLATION
RemovalI. Loosen radiator cap, then remove lower radiator
hose and drain radiator coolant into suitable con-
tainer.
2. On vehicles with automatic transmission, unscrew
oil lines from connectors on lower radiator tank and
plug lines. On GT models with automatic transmis-
sion the lines have to be disconnected at the coupling
before removing from the tank. It is essential that no
dirt enters the oil lines. When unscrewing oil lines,
hold connectors on lower radiator tank with pliers to
avoid leakages. Ensure that no dirt enters oil cooler.
3. Remove lower attaching nut and slide radiator
upward and out of engine compartment.
Installation1. Install radiat,or into engine compartment and se-
cure lower attaching nut.
2. On vehicles with automatic transmissions, fasten
oil cooler lines to lower radiator tank. It is essential
that no dirt enters the oil lines. When tightening oil
lines, hold connectors on lower radiator tank with
pliers to avoid leakages. Ensure that no dirt enters oil
cooler. Torque to 1 I-15
lbs.ft.3. Install lower radiator hose and add collected coo-
lant.
All Opels are provided with a radiator initial fill of
an antifreeze solution containing corrosion inhibitor.
The antifreeze has either a glycol or glycerin base
and protects the engine against freezing, down to
minus 22 degrees F. (minus 30 degrees C.). Before
the start of the cold season, coolant must be checked
with a hydrometer and if necessary, brought to the
necessary specific gravity by adding anti-freeze with
a glycol or glycerin base. As the specific gravities of
all anti- freeze solutions having a glycol or glycerin
base are practically the same, the hydrometer can be
used for all these types. Because of the tolerances of
the hydrometer, or slight differences in specific
gravity, variations of plus or minus 5 degrees can be
expected. Coolant must be checked at a temperature
of plus 68 degrees F. (plus 20 degrees C.)