torque OPEL GT-R 1973 Manual PDF
[x] Cancel search | Manufacturer: OPEL, Model Year: 1973, Model line: GT-R, Model: OPEL GT-R 1973Pages: 625, PDF Size: 17.22 MB
Page 272 of 625
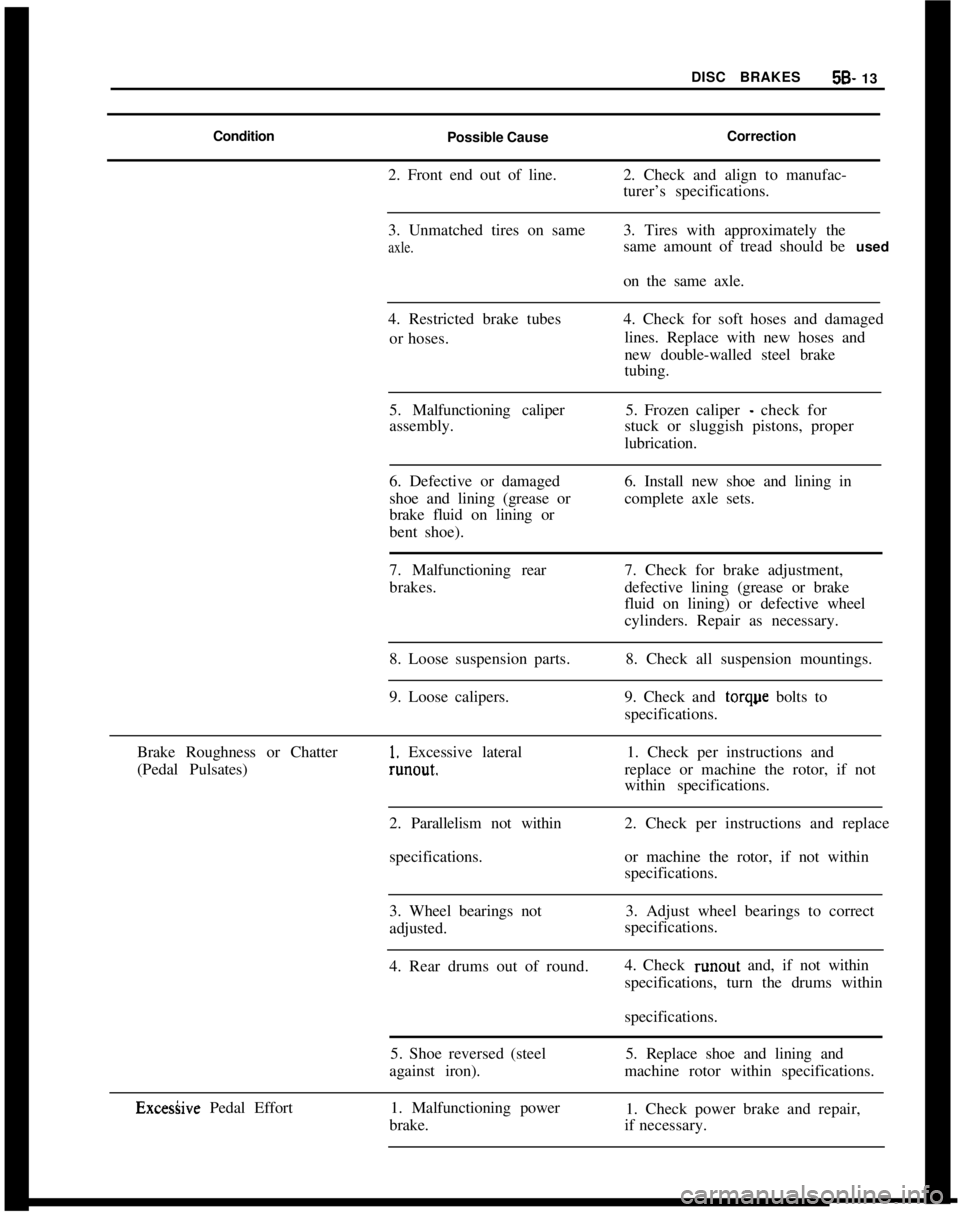
DISC BRAKES5B- 13
Condition
Possible CauseCorrection
2. Front end out of line.2. Check and align to manufac-
turer’s specifications.
3. Unmatched tires on sameaxle.3. Tires with approximately the
same amount of tread should be used
on the same axle.
4. Restricted brake tubes
or hoses.4. Check for soft hoses and damaged
lines. Replace with new hoses and
new double-walled steel brake
tubing.
5. Malfunctioning caliper
assembly.5. Frozen caliper
- check for
stuck or sluggish pistons, proper
lubrication.
6. Defective or damaged
shoe and lining (grease or
brake fluid on lining or
bent shoe).6. Install new shoe and lining in
complete axle sets.
7. Malfunctioning rear
brakes.7. Check for brake adjustment,
defective lining (grease or brake
fluid on lining) or defective wheel
cylinders. Repair as necessary.
8. Loose suspension parts.
9. Loose calipers.8. Check all suspension mountings.
9. Check and torque bolts to
specifications.
Brake Roughness or Chatter
(Pedal Pulsates)
1. Excessive lateralrunout.1. Check per instructions and
replace or machine the rotor, if not
within specifications.
2. Parallelism not within
specifications.2. Check per instructions and replace
or machine the rotor, if not within
specifications.
3. Wheel bearings not
adjusted.3. Adjust wheel bearings to correct
specifications.
4. Rear drums out of round.4. Check runout and, if not within
specifications, turn the drums within
specifications.
5. Shoe reversed (steel
against iron).5. Replace shoe and lining and
machine rotor within specifications.
ExcesGve Pedal Effort1. Malfunctioning power
brake.1. Check power brake and repair,
if necessary.
Page 275 of 625
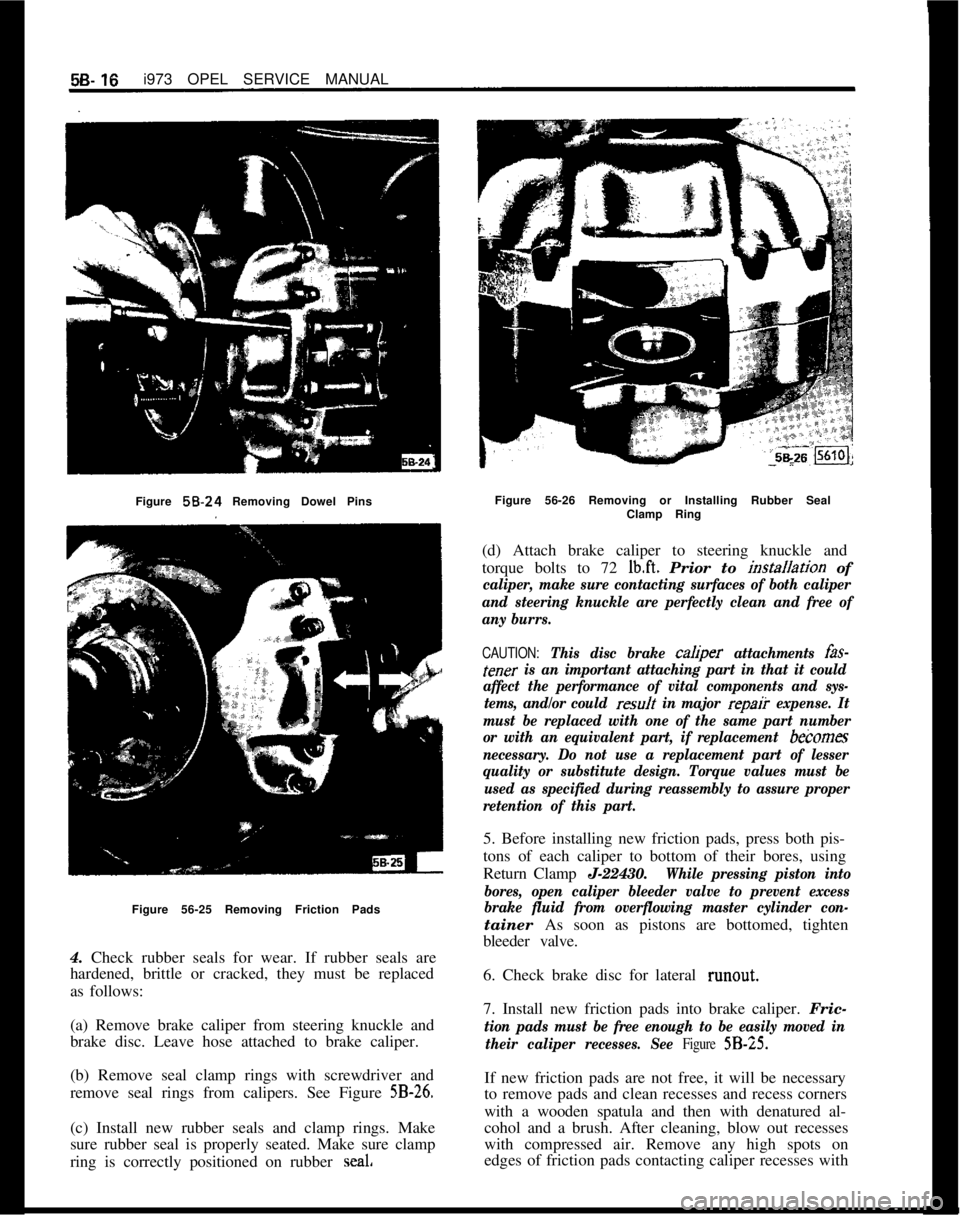
5B- 19i973 OPEL SERVICE MANUAL
Figure
56-24 Removing Dowel Pins
Figure 56-25 Removing Friction Pads
4. Check rubber seals for wear. If rubber seals are
hardened, brittle or cracked, they must be replaced
as follows:
(a) Remove brake caliper from steering knuckle and
brake disc. Leave hose attached to brake caliper.
(b) Remove seal clamp rings with screwdriver and
remove seal rings from calipers. See Figure
5B-26.(c) Install new rubber seals and clamp rings. Make
sure rubber seal is properly seated. Make sure clamp
ring is correctly positioned on rubber seal,Figure 56-26 Removing or Installing Rubber Seal
Clamp Ring
(d) Attach brake caliper to steering knuckle and
torque bolts to 72
Ib.ft. Prior to installation of
caliper, make sure contacting surfaces of both caliper
and steering knuckle are perfectly clean and free of
any burrs.
CAUTION: This disc brake caliper attachments fas-
tener is an important attaching part in that it could
affect the performance of vital components and sys-
tems, and/or could
result in major repair expense. It
must be replaced with one of the same part number
or with an equivalent part, if replacement
becomes
necessary. Do not use a replacement part of lesser
quality or substitute design. Torque values must be
used as specified during reassembly to assure proper
retention of this part.5. Before installing new friction pads, press both pis-
tons of each caliper to bottom of their bores, using
Return Clamp J-22430.
While pressing piston into
bores, open caliper bleeder valve to prevent excess
brake fluid from overflowing master cylinder con-tainer As soon as pistons are bottomed, tighten
bleeder valve.
6. Check brake disc for lateral runout.
7. Install new friction pads into brake caliper. Fric-
tion pads must be free enough to be easily moved in
their caliper recesses. See
Figure X3-25.If new friction pads are not free, it will be necessary
to remove pads and clean recesses and recess corners
with a wooden spatula and then with denatured al-
cohol and a brush. After cleaning, blow out recesses
with compressed air. Remove any high spots on
edges of friction pads contacting caliper recesses with
Page 276 of 625
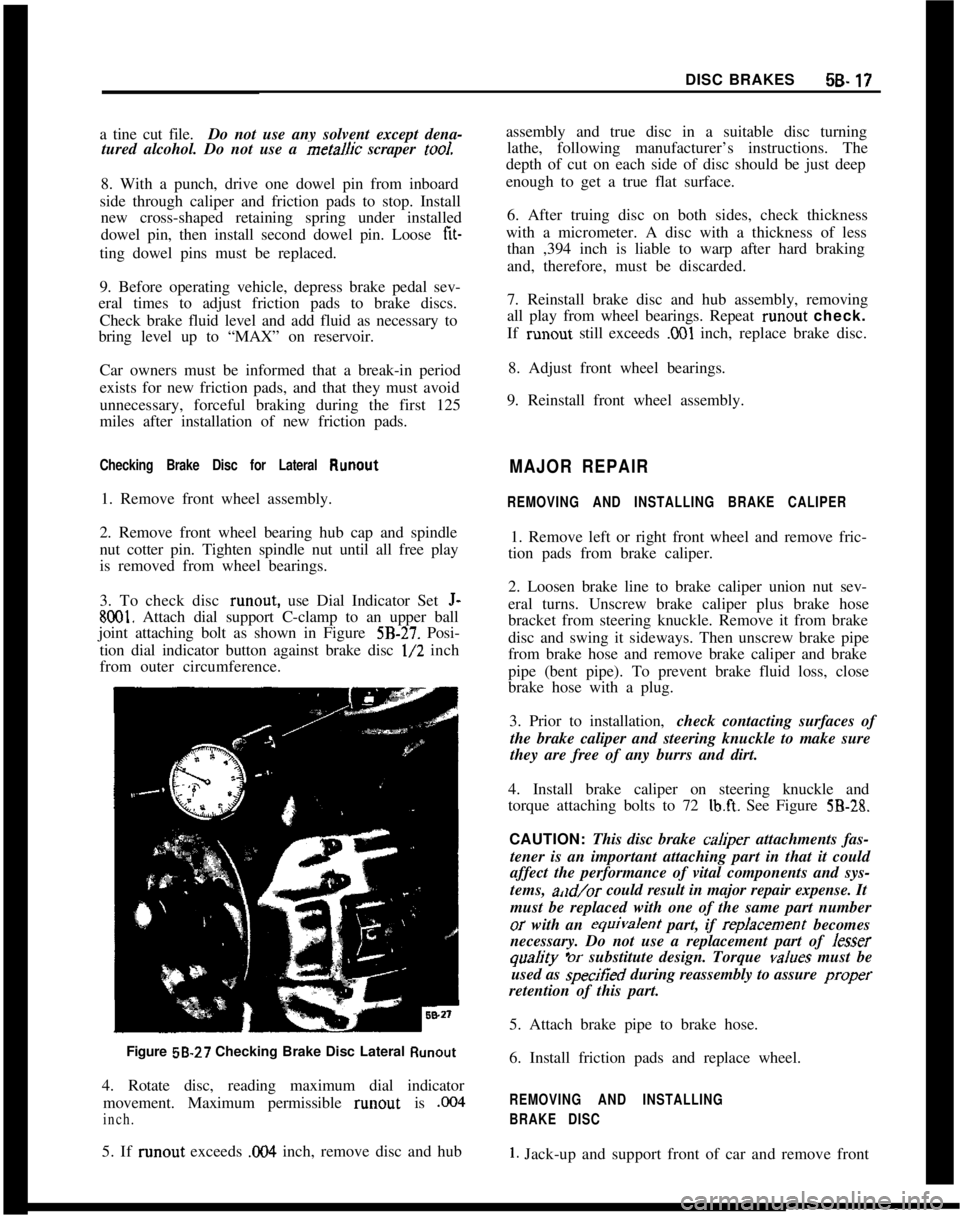
DISC BRAKES58.17a tine cut file.Do not use any solvent except dena-
tured alcohol. Do not use a
metaIJic scraper too/.8. With a punch, drive one dowel pin from inboard
side through caliper and friction pads to stop. Install
new cross-shaped retaining spring under installed
dowel pin, then install second dowel pin. Loose tit-
ting dowel pins must be replaced.
9. Before operating vehicle, depress brake pedal sev-
eral times to adjust friction pads to brake discs.
Check brake fluid level and add fluid as necessary to
bring level up to “MAX” on reservoir.
Car owners must be informed that a break-in period
exists for new friction pads, and that they must avoid
unnecessary, forceful braking during the first 125
miles after installation of new friction pads.
Checking Brake Disc for Lateral Runout1. Remove front wheel assembly.
2. Remove front wheel bearing hub cap and spindle
nut cotter pin. Tighten spindle nut until all free play
is removed from wheel bearings.
3. To check disc runout, use Dial Indicator Set
J-
8001. Attach dial support C-clamp to an upper ball
joint attaching bolt as shown in Figure
5B-27. Posi-
tion dial indicator button against brake disc
l/2 inch
from outer circumference.
Figure 58-27 Checking Brake Disc Lateral
Runout4. Rotate disc, reading maximum dial indicator
movement. Maximum permissible runout is
,004
inch.5. If runout exceeds
0% inch, remove disc and hubassembly and true disc in a suitable disc turning
lathe, following manufacturer’s instructions. The
depth of cut on each side of disc should be just deep
enough to get a true flat surface.
6. After truing disc on both sides, check thickness
with a micrometer. A disc with a thickness of less
than ,394 inch is liable to warp after hard braking
and, therefore, must be discarded.
7. Reinstall brake disc and hub assembly, removing
all play from wheel bearings. Repeat runout check.
If runout still exceeds
,001 inch, replace brake disc.
8. Adjust front wheel bearings.
9. Reinstall front wheel assembly.
MAJOR REPAIR
REMOVING AND INSTALLING BRAKE CALIPER1. Remove left or right front wheel and remove fric-
tion pads from brake caliper.
2. Loosen brake line to brake caliper union nut sev-
eral turns. Unscrew brake caliper plus brake hose
bracket from steering knuckle. Remove it from brake
disc and swing it sideways. Then unscrew brake pipe
from brake hose and remove brake caliper and brake
pipe (bent pipe). To prevent brake fluid loss, close
brake hose with a plug.
3. Prior to installation,check contacting surfaces of
the brake caliper and steering knuckle to make sure
they are free of any burrs and dirt.
4. Install brake caliper on steering knuckle and
torque attaching bolts to 72
lb.ft. See Figure 5B-28.CAUTION: This disc brake
cah@er attachments fas-
tener is an important attaching part in that it could
affect the performance of vital components and sys-
tems, a,ld/or could result in major repair expense. It
must be replaced with one of the same part numberor with an equivafent part, if repfacement becomes
necessary. Do not use a replacement part of Jesser
quaJity ‘or substitute design. Torque vafues must be
used as specitied during reassembly to assure proper
retention of this part.
5. Attach brake pipe to brake hose.
6. Install friction pads and replace wheel.
REMOVING AND INSTALLING
BRAKE DISC
1. Jack-up and support front of car and remove front
Page 278 of 625
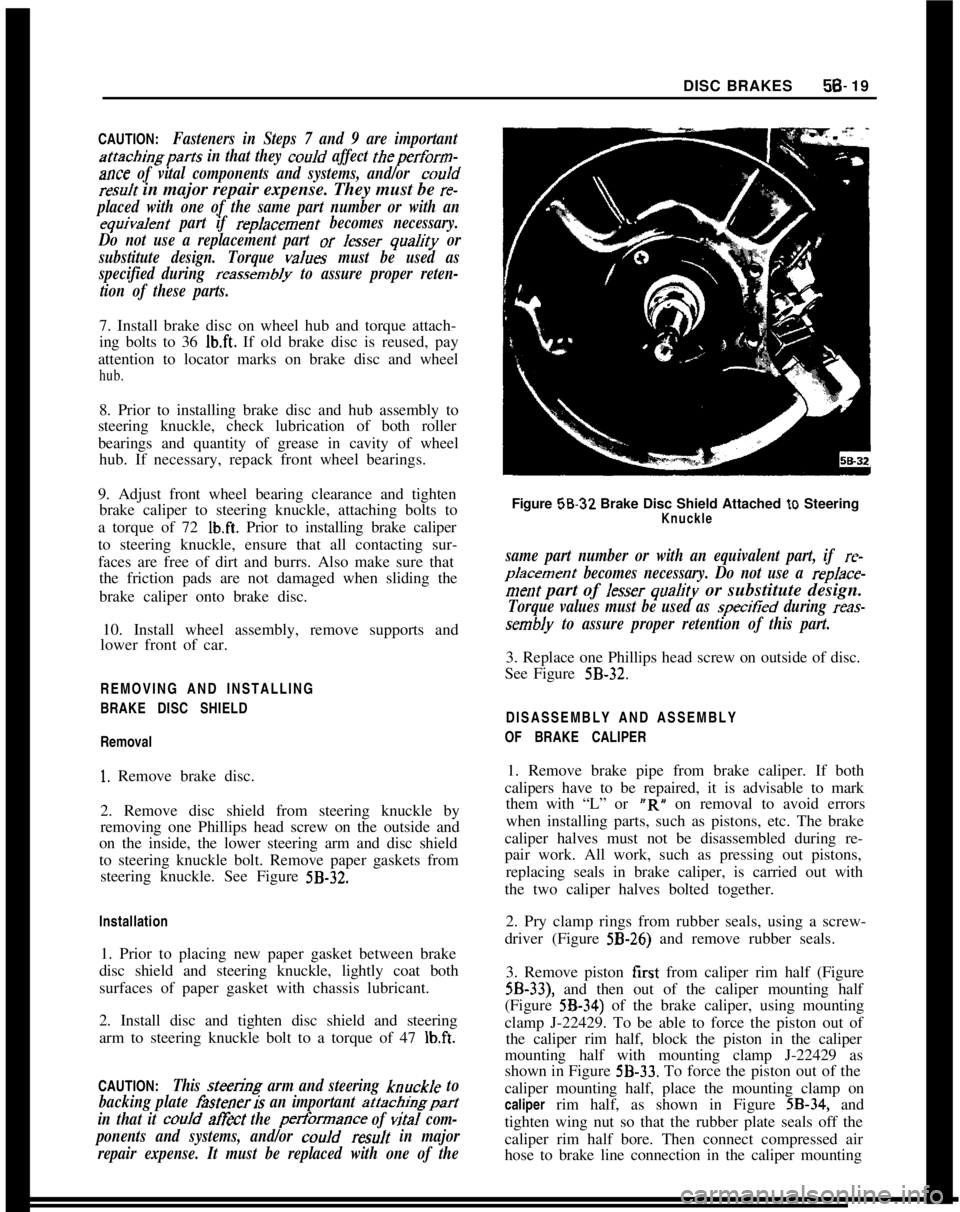
DISC BRAKES5B- 19
CAUTION:
Fasteners in Steps 7 and 9 are important
attachingparts in that they cooId affect theperfom-
ante of vital components and systems, and/or couJd
resuJt in major repair expense. They must be re-
placed with one of the same part number or with an
equivaJent part if repJacement becomes necessary.
Do not use a replacement part
or Jesser quaJity or
substitute design. Torque
vaJues must be used as
specified during
reassembJy to assure proper reten-
tion of these parts.7. Install brake disc on wheel hub and torque attach-
ing bolts to 36
Ib.ft. If old brake disc is reused, pay
attention to locator marks on brake disc and wheel
hub.8. Prior to installing brake disc and hub assembly to
steering knuckle, check lubrication of both roller
bearings and quantity of grease in cavity of wheel
hub. If necessary, repack front wheel bearings.
9. Adjust front wheel bearing clearance and tighten
brake caliper to steering knuckle, attaching bolts to
a torque of 72
lb.ft. Prior to installing brake caliper
to steering knuckle, ensure that all contacting sur-
faces are free of dirt and burrs. Also make sure that
the friction pads are not damaged when sliding the
brake caliper onto brake disc.
10. Install wheel assembly, remove supports and
lower front of car.
REMOVING AND INSTALLING
BRAKE DISC SHIELD
Removal
1. Remove brake disc.
2. Remove disc shield from steering knuckle by
removing one Phillips head screw on the outside and
on the inside, the lower steering arm and disc shield
to steering knuckle bolt. Remove paper gaskets from
steering knuckle. See Figure
5B-32.Installation
1. Prior to placing new paper gasket between brake
disc shield and steering knuckle, lightly coat both
surfaces of paper gasket with chassis lubricant.
2. Install disc and tighten disc shield and steering
arm to steering knuckle bolt to a torque of 47
lb.ft.CAUTION:
This steen;Og arm and steering knuckJe to
backing plate
fisteneris an important attachingpart
in that it
couJd at&t the performance of viral com-
ponents and systems, and/or
couJd resuJt in major
repair expense. It must be replaced with one of theFigure 58-32 Brake Disc Shield Attached
to SteeringKnuckle
same part number or with an equivalent part, if re-
pJacement becomes necessary. Do not use a rep/ace-
merit part of Jesser quaJity or substitute design.
Torque values must be used as specitied during reas-
sembly to assure proper retention of this part.3. Replace one Phillips head screw on outside of disc.
See Figure
5B-32.DISASSEMBLY AND ASSEMBLY
OF BRAKE CALIPER
1. Remove brake pipe from brake caliper. If both
calipers have to be repaired, it is advisable to mark
them with “L” or “R” on removal to avoid errors
when installing parts, such as pistons, etc. The brake
caliper halves must not be disassembled during re-
pair work. All work, such as pressing out pistons,
replacing seals in brake caliper, is carried out with
the two caliper halves bolted together.
2. Pry clamp rings from rubber seals, using a screw-
driver (Figure
5B-26) and remove rubber seals.
3. Remove piston first from caliper rim half (Figure
5B-33), and then out of the caliper mounting half
(Figure
5B-34) of the brake caliper, using mounting
clamp J-22429. To be able to force the piston out of
the caliper rim half, block the piston in the caliper
mounting half with mounting clamp J-22429 as
shown in Figure
5B-33. To force the piston out of the
caliper mounting half, place the mounting clamp on
caliper rim half, as shown in Figure
5B-34, and
tighten wing nut so that the rubber plate seals off the
caliper rim half bore. Then connect compressed air
hose to brake line connection in the caliper mounting
Page 280 of 625
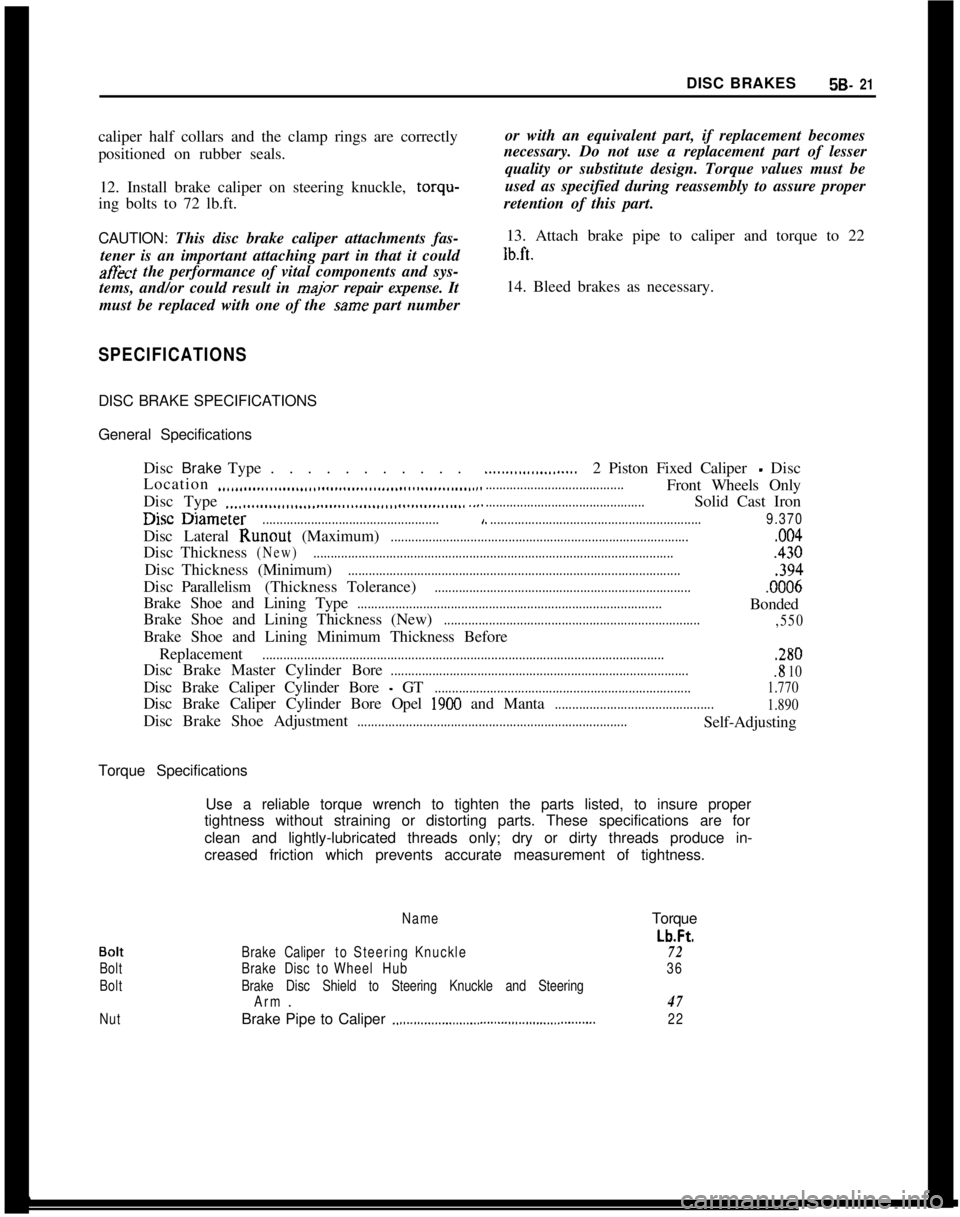
DISC BRAKES5B- 21caliper half collars and the clamp rings are correctly
positioned on rubber seals.
12. Install brake caliper on steering knuckle, torqu-
ing bolts to 72 lb.ft.or with an equivalent part, if replacement becomes
necessary. Do not use a replacement part of lesser
quality or substitute design. Torque values must be
used as specified during reassembly to assure proper
retention of this part.
CAUTION: This disc brake caliper attachments fas-
tener is an important attaching part in that it couldatExt the performance of vital components and sys-
tems, and/or could result in
ma@r repair expense. It
must be replaced with one of the
same part number13. Attach brake pipe to caliper and torque to 22
lb.ft.14. Bleed brakes as necessary.
SPECIFICATIONSDISC BRAKE SPECIFICATIONS
General Specifications
DiscBrakeType. . . . . . . . . . .
Location
..,,.,..__....__.,,.,,,................,,,................,....Disc Type
.._.......................................................I.-. -.
......................2 Piston Fixed Caliper - Disc
........................................Front Wheels Only
..............................................Solid Cast Iron
useuameter...................................................,..............................................................9.370Disc Lateral Runout (Maximum)
......................................................................................,004DiscThickness
(New).........................................................................................................430DiscThickness(Minimum)
................................................................................................,394DiscParallelism(ThicknessTolerance)
...........................................................................0006Brake Shoe and Lining Type
........................................................................................Bonded
Brake Shoe and Lining Thickness (New)
..........................................................................
,550Brake Shoe and Lining Minimum Thickness Before
Replacement
....................................................................................................................,280Disc Brake Master Cylinder Bore
.......................................................................................8 10Disc Brake Caliper Cylinder Bore
- GT..........................................................................1.770Disc Brake Caliper Cylinder Bore Opel
1900 and Manta..............................................
1.890Disc Brake Shoe Adjustment
..............................................................................Self-Adjusting
Torque Specifications
Use a reliable torque wrench to tighten the parts listed, to insure proper
tightness without straining or distorting parts. These specifications are for
clean and lightly-lubricated threads only; dry or dirty threads produce in-
creased friction which prevents accurate measurement of tightness.
Bolt
Bolt
Bolt
NutName
BrakeCalipertoSteeringKnuckle
BrakeDisctoWheelHub
Brake Disc Shield to Steering Knuckle and Steering
Arm.
Brake Pipe to Caliper
.,.,...............................,......................Torque
Lb.Ft.
72
36
47
22
Page 290 of 625
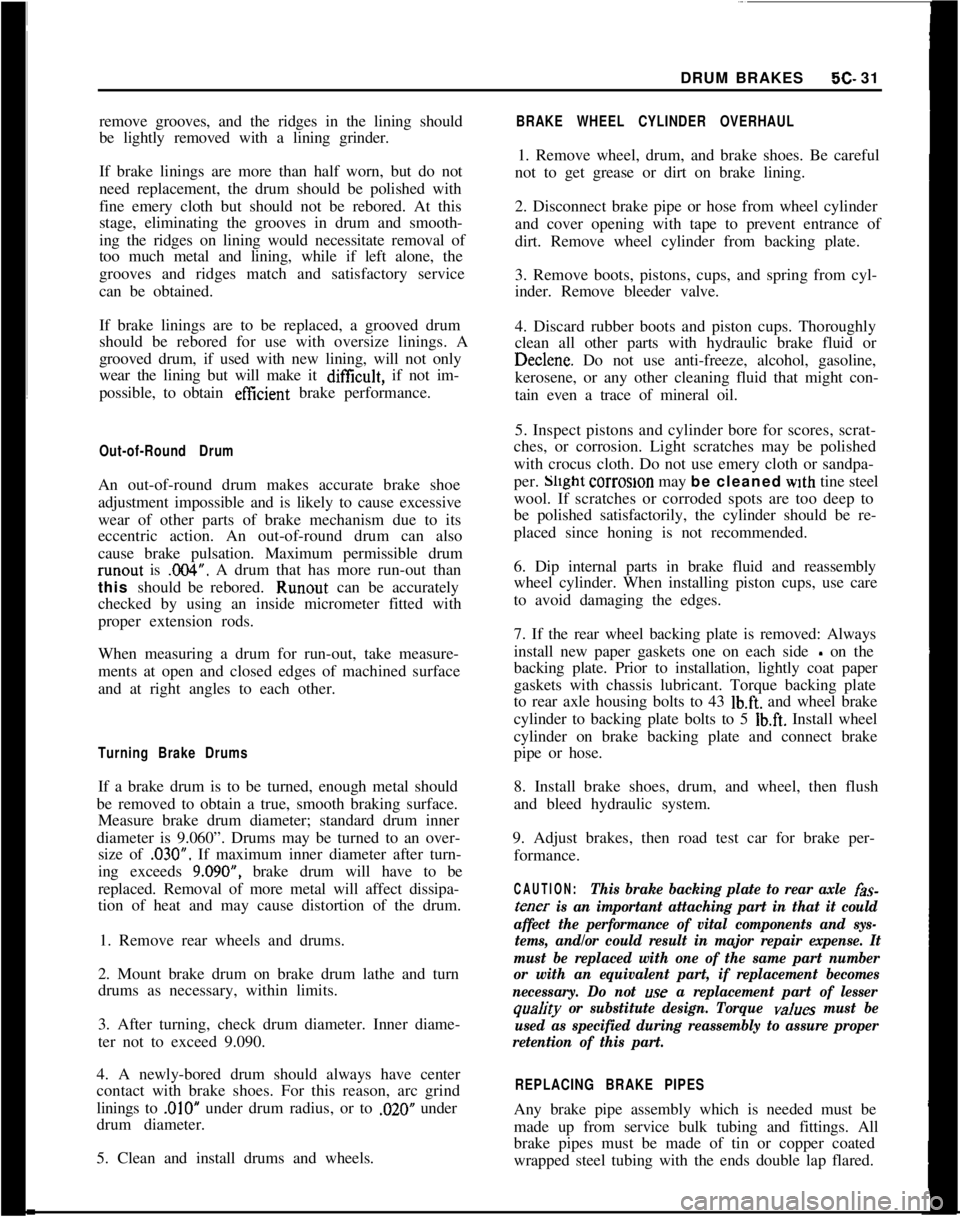
DRUM BRAKES5c- 31
remove grooves, and the ridges in the lining should
be lightly removed with a lining grinder.
If brake linings are more than half worn, but do not
need replacement, the drum should be polished with
fine emery cloth but should not be rebored. At this
stage, eliminating the grooves in drum and smooth-
ing the ridges on lining would necessitate removal of
too much metal and lining, while if left alone, the
grooves and ridges match and satisfactory service
can be obtained.
If brake linings are to be replaced, a grooved drum
should be rebored for use with oversize linings. A
grooved drum, if used with new lining, will not only
wear the lining but will make it
diff%xlt, if not im-
possible, to obtain etXcient brake performance.
Out-of-Round DrumAn out-of-round drum makes accurate brake shoe
adjustment impossible and is likely to cause excessive
wear of other parts of brake mechanism due to its
eccentric action. An out-of-round drum can also
cause brake pulsation. Maximum permissible drumrunout is 004”. A drum that has more run-out than
this should be rebored. Runout can be accurately
checked by using an inside micrometer fitted with
proper extension rods.
When measuring a drum for run-out, take measure-
ments at open and closed edges of machined surface
and at right angles to each other.
Turning Brake DrumsIf a brake drum is to be turned, enough metal should
be removed to obtain a true, smooth braking surface.
Measure brake drum diameter; standard drum inner
diameter is 9.060”. Drums may be turned to an over-
size of ,030”. If maximum inner diameter after turn-
ing exceeds 9.090”, brake drum will have to be
replaced. Removal of more metal will affect dissipa-
tion of heat and may cause distortion of the drum.
1. Remove rear wheels and drums.
2. Mount brake drum on brake drum lathe and turn
drums as necessary, within limits.
3. After turning, check drum diameter. Inner diame-
ter not to exceed 9.090.
4. A newly-bored drum should always have center
contact with brake shoes. For this reason, arc grind
linings to
.OlO” under drum radius, or to ,020” under
drum diameter.
5. Clean and install drums and wheels.
BRAKE WHEEL CYLINDER OVERHAUL1. Remove wheel, drum, and brake shoes. Be careful
not to get grease or dirt on brake lining.
2. Disconnect brake pipe or hose from wheel cylinder
and cover opening with tape to prevent entrance of
dirt. Remove wheel cylinder from backing plate.
3. Remove boots, pistons, cups, and spring from cyl-
inder. Remove bleeder valve.
4. Discard rubber boots and piston cups. Thoroughly
clean all other parts with hydraulic brake fluid orDeclene. Do not use anti-freeze, alcohol, gasoline,
kerosene, or any other cleaning fluid that might con-
tain even a trace of mineral oil.
5. Inspect pistons and cylinder bore for scores, scrat-
ches, or corrosion. Light scratches may be polished
with crocus cloth. Do not use emery cloth or sandpa-
per.
Shght corro~on may be cleaned wth tine steel
wool. If scratches or corroded spots are too deep to
be polished satisfactorily, the cylinder should be re-
placed since honing is not recommended.
6. Dip internal parts in brake fluid and reassembly
wheel cylinder. When installing piston cups, use care
to avoid damaging the edges.
7. If the rear wheel backing plate is removed: Always
install new paper gaskets one on each side
- on the
backing plate. Prior to installation, lightly coat paper
gaskets with chassis lubricant. Torque backing plate
to rear axle housing bolts to 43
lb.ft. and wheel brake
cylinder to backing plate bolts to 5
lb.ft. Install wheel
cylinder on brake backing plate and connect brake
pipe or hose.
8. Install brake shoes, drum, and wheel, then flush
and bleed hydraulic system.
9. Adjust brakes, then road test car for brake per-
formance.
CAUTION:This brake backing plate to rear axle fis-
tener is an important attaching part in that it could
affect the performance of vital components and sys-
tems, and/or could result in major repair expense. It
must be replaced with one of the same part number
or with an equivalent part, if replacement becomes
necessary. Do not
use a replacement part of lesser
quahty or substitute design. Torque v&es must be
used as specified during reassembly to assure proper
retention of this part.
REPLACING BRAKE PIPESAny brake pipe assembly which is needed must be
made up from service bulk tubing and fittings. All
brake pipes must be made of tin or copper coated
wrapped steel tubing with the ends double lap flared.
Page 291 of 625
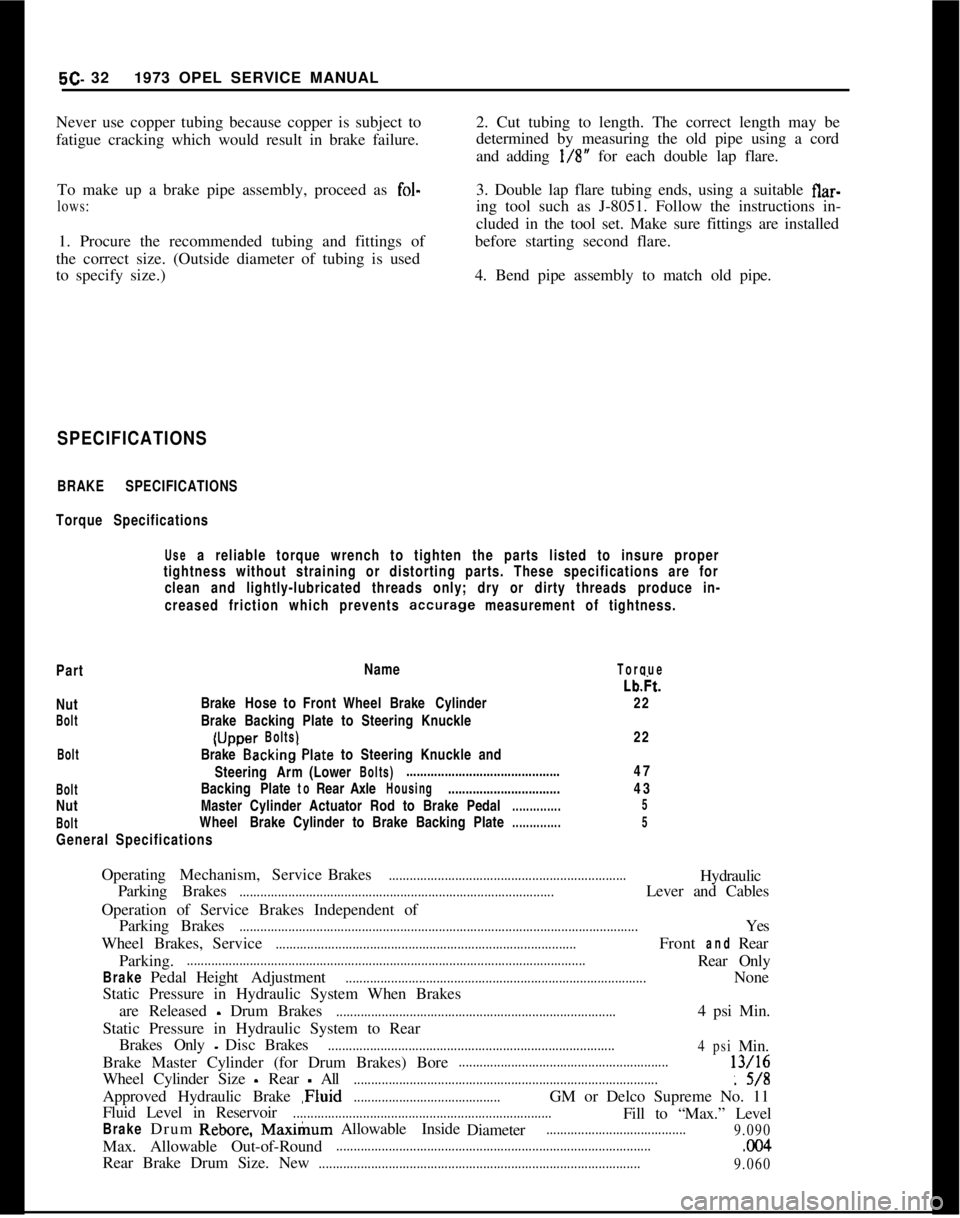
5C- 321973 OPEL SERVICE MANUAL
Never use copper tubing because copper is subject to
fatigue cracking which would result in brake failure.2. Cut tubing to length. The correct length may be
determined by measuring the old pipe using a cord
and adding l/8” for each double lap flare.
To make up a brake pipe assembly, proceed as fol-
lows:3. Double lap flare tubing ends, using a suitable flar-
ing tool such as J-8051. Follow the instructions in-
cluded in the tool set. Make sure fittings are installed
1. Procure the recommended tubing and fittings of
the correct size. (Outside diameter of tubing is used
to specify size.)before starting second flare.
4. Bend pipe assembly to match old pipe.
SPECIFICATIONS
BRAKE SPECIFICATIONS
Torque Specifications
Use a reliable torque wrench to tighten the parts listed to insure proper
tightness without straining or distorting parts. These specifications are for
clean and lightly-lubricated threads only; dry or dirty threads produce in-
creased friction which prevents
accurage measurement of tightness.
PartName
TorqueNut
BoltBrakeHose to Front WheelBrake Cylinder
Brake Backing Plate to Steering Knuckle(Uccer
Bolts)Lb&.
22
22...BoltBrake Backing’Plate to Steering Knuckle and
SteeringArm(Lower
Bolts)............................................
BoltBackingPlatetoRearAxleHousing................................
NutMaster Cylinder Actuator Rod to BrakePedal
..............
BoltWheelBrake Cylinder to Brake Backing Plate
..............
General Specifications47
43
5
5OperatingMechanism,ServiceBrakes
....................................................................Hydraulic
Parking Brakes
..........................................................................................Lever and Cables
Operation of Service Brakes Independent of
ParkingBrakes
..................................................................................................................Yes
WheelBrakes,Service
......................................................................................FrontandRear
Parking.
..................................................................................................................Rear Only
BrakePedalHeightAdjustment......................................................................................None
Static Pressure in Hydraulic System When Brakes
are Released
- Drum Brakes................................................................................4 psi Min.
Static Pressure in Hydraulic System to Rear
BrakesOnly
-DiscBrakes..................................................................................
4psiMin.
Brake Master Cylinder (for Drum Brakes) Bore
............................................................13/16
Wheel Cylinder Size
- Rear - All.......................................................................................: 5/8
Approved Hydraulic Brake ,Fluid
..........................................GM or Delco Supreme No. 11
Fluid Level in Reservoir
..........................................................................Fill to “Max.” Level
BrakeDrumRebore,Max&urnAllowable Inside
Diameter........................................
9.090Max. Allowable Out-of-Round
...........................................................................................CKl4Rear Brake Drum Size. New
............................................................................................
9.060
Page 293 of 625
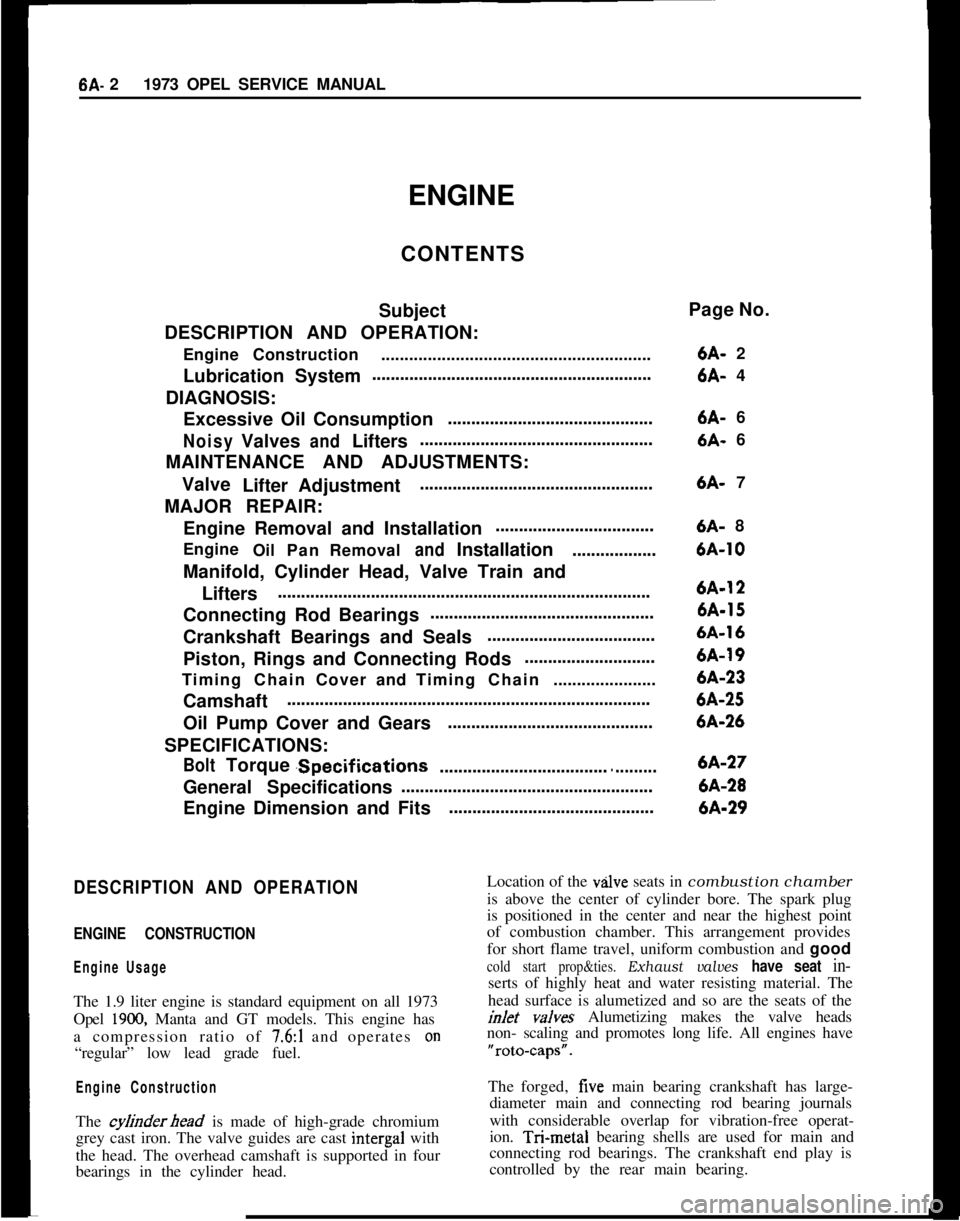
6A- 21973 OPEL SERVICE MANUAL
ENGINE
CONTENTS
Subject
DESCRIPTION AND OPERATION:
EngineConstruction..........................................................
LubricationSystem............................................................
DIAGNOSIS:
Excessive Oil Consumption............................................NoisyValvesandLifters..................................................
MAINTENANCE AND ADJUSTMENTS:
Valve
LifterAdjustment..................................................
MAJOR REPAIR:
Engine Removal and Installation..................................
Engine
OilPanRemoval
andInstallation..................
Manifold, Cylinder Head, Valve Train and
Lifters................................................................................
Connecting Rod Bearings................................................
Crankshaft Bearings and Seals....................................
Piston, Rings and Connecting Rods............................
TimingChainCoverandTimingChain......................
Camshaft..............................................................................
Oil Pump Cover and Gears............................................
SPECIFICATIONS:
BoltTorque.Specifications
..............................................General Specifications......................................................
Engine Dimension and Fits............................................Page No.
6A- 2
6A- 4
6A- 6
6A- 6
6A- 7
6A- 86A-106A-126A-156A-166A-196A-236A-256A-266A-276A-286A-29
DESCRIPTION AND OPERATION
ENGINE CONSTRUCTION
Engine UsageThe 1.9 liter engine is standard equipment on all 1973
Opel
1900, Manta and GT models. This engine has
a compression ratio of
7.6:1 and operates on“regular” low lead grade fuel.
Engine ConstructionThe
cyfinderhead is made of high-grade chromium
grey cast iron. The valve guides are cast intergal with
the head. The overhead camshaft is supported in four
bearings in the cylinder head.Location of the
vzllve seats in combustion chamber
is above the center of cylinder bore. The spark plug
is positioned in the center and near the highest point
of combustion chamber. This arrangement provides
for short flame travel, uniform combustion and good
cold start prop&ties. Exhaust valves have seat in-serts of highly heat and water resisting material. The
head surface is alumetized and so are the seats of the
inlet v&es Alumetizing makes the valve heads
non- scaling and promotes long life. All engines have“rota-caps”.
The forged, five main bearing crankshaft has large-
diameter main and connecting rod bearing journals
with considerable overlap for vibration-free operat-
ion. T&metal bearing shells are used for main and
connecting rod bearings. The crankshaft end play is
controlled by the rear main bearing.
Page 302 of 625
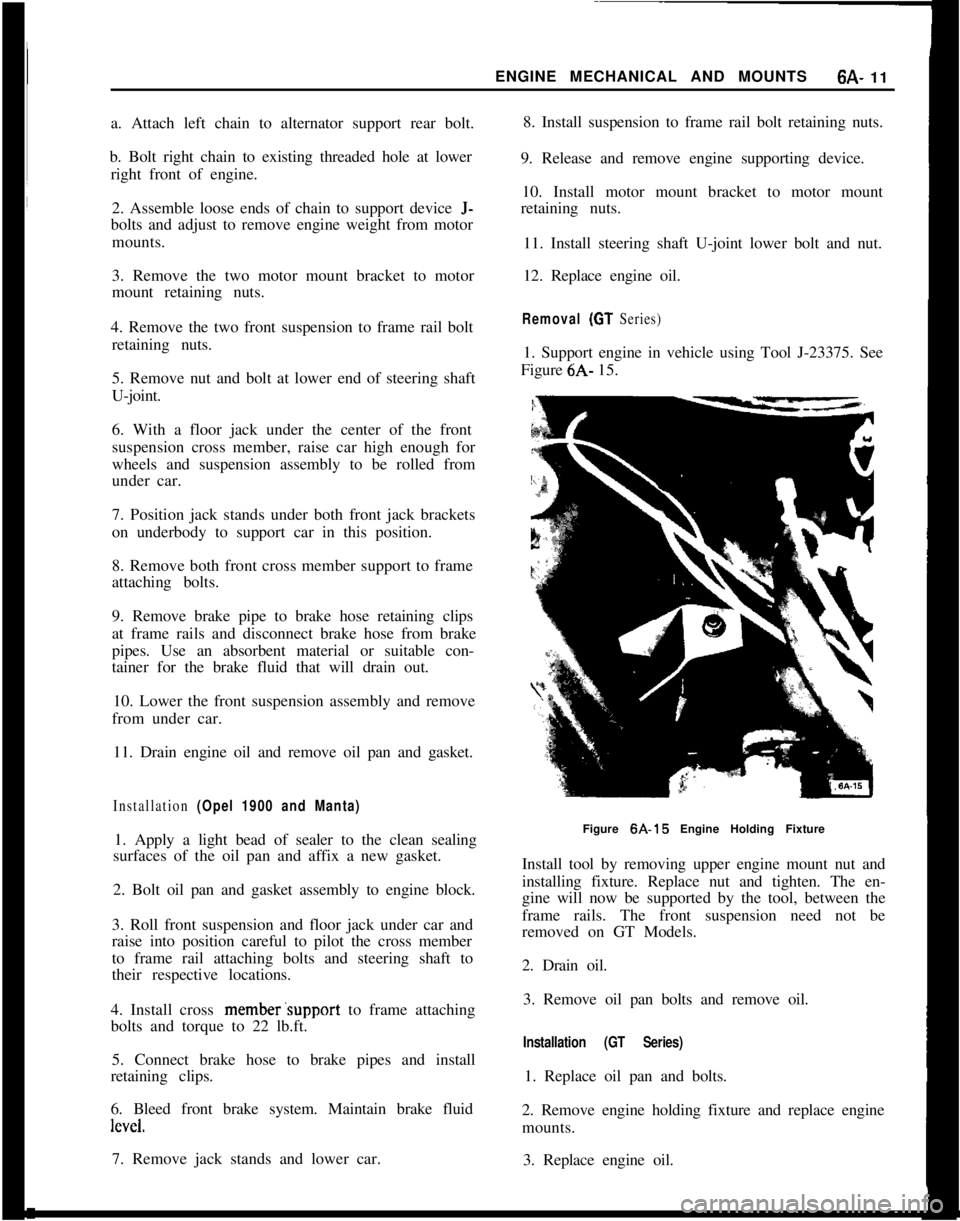
ENGINE MECHANICAL AND MOUNTS6A- 11
a. Attach left chain to alternator support rear bolt.
b. Bolt right chain to existing threaded hole at lower
right front of engine.
2. Assemble loose ends of chain to support device J-bolts and adjust to remove engine weight from motor
mounts.
3. Remove the two motor mount bracket to motor
mount retaining nuts.
4. Remove the two front suspension to frame rail bolt
retaining nuts.
5. Remove nut and bolt at lower end of steering shaft
U-joint.
6. With a floor jack under the center of the front
suspension cross member, raise car high enough for
wheels and suspension assembly to be rolled from
under car.
7. Position jack stands under both front jack brackets
on underbody to support car in this position.
8. Remove both front cross member support to frame
attaching bolts.
9. Remove brake pipe to brake hose retaining clips
at frame rails and disconnect brake hose from brake
pipes. Use an absorbent material or suitable con-
tainer for the brake fluid that will drain out.
10. Lower the front suspension assembly and remove
from under car.
11. Drain engine oil and remove oil pan and gasket.
Installation (Opel 1900 and Manta)1. Apply a light bead of sealer to the clean sealing
surfaces of the oil pan and affix a new gasket.
2. Bolt oil pan and gasket assembly to engine block.
3. Roll front suspension and floor jack under car and
raise into position careful to pilot the cross member
to frame rail attaching bolts and steering shaft to
their respective locations.
4. Install cross member’support to frame attaching
bolts and torque to 22 lb.ft.
5. Connect brake hose to brake pipes and install
retaining clips.
6. Bleed front brake system. Maintain brake fluid1Wd.
7. Remove jack stands and lower car.8. Install suspension to frame rail bolt retaining nuts.
9. Release and remove engine supporting device.
10. Install motor mount bracket to motor mount
retaining nuts.
11. Install steering shaft U-joint lower bolt and nut.
12. Replace engine oil.
Removal (GT Series)1. Support engine in vehicle using Tool J-23375. See
Figure 6A- 15.
Figure 6A-15 Engine Holding Fixture
Install tool by removing upper engine mount nut and
installing fixture. Replace nut and tighten. The en-
gine will now be supported by the tool, between the
frame rails. The front suspension need not be
removed on GT Models.
2. Drain oil.
3. Remove oil pan bolts and remove oil.
Installation (GT Series)1. Replace oil pan and bolts.
2. Remove engine holding fixture and replace engine
mounts.
3. Replace engine oil.
Page 303 of 625
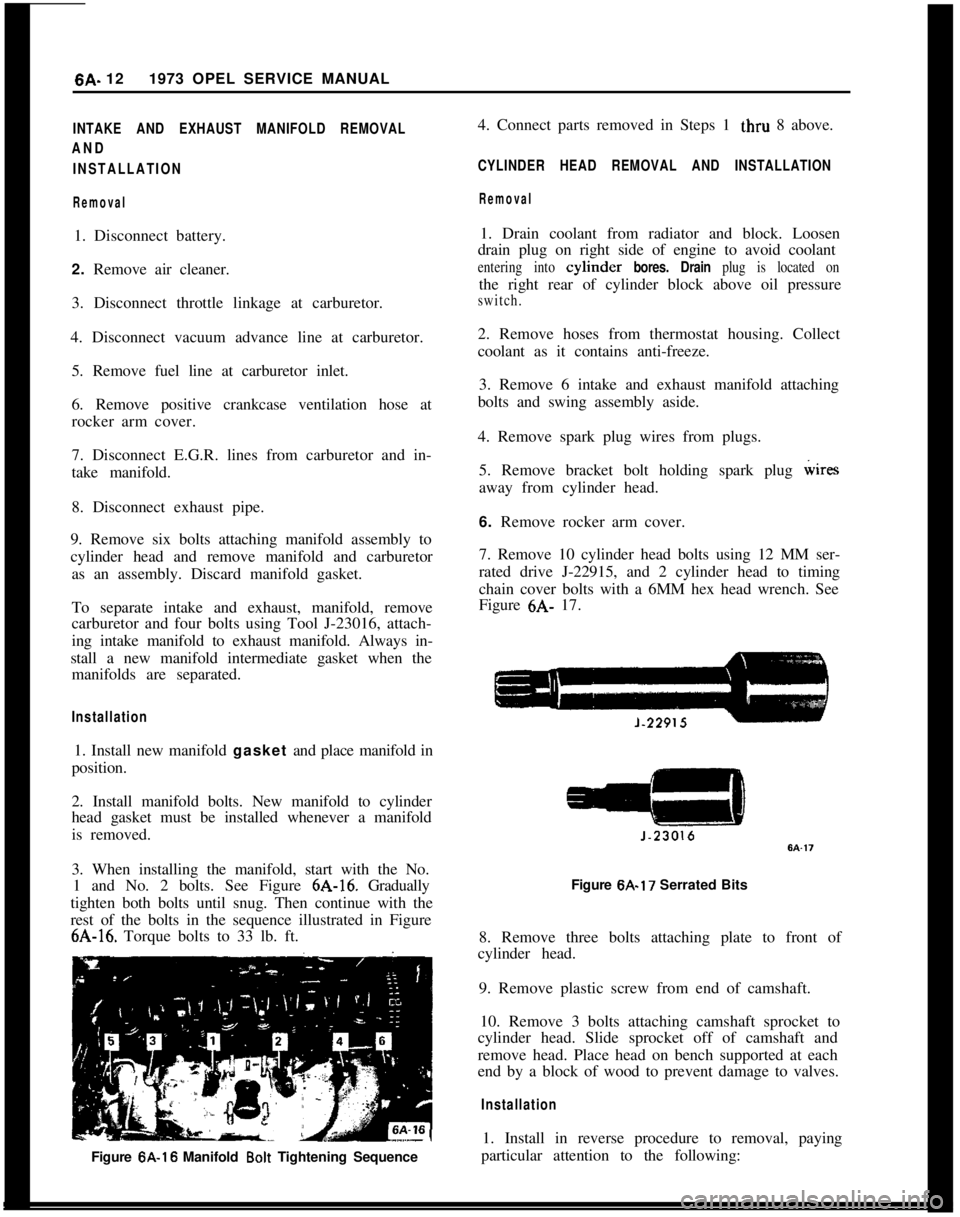
6A- 121973 OPEL SERVICE MANUALINTAKE AND EXHAUST MANIFOLD REMOVAL
AND
INSTALLATION
Removal1. Disconnect battery.
2. Remove air cleaner.
3. Disconnect throttle linkage at carburetor.
4. Disconnect vacuum advance line at carburetor.
5. Remove fuel line at carburetor inlet.
6. Remove positive crankcase ventilation hose at
rocker arm cover.
7. Disconnect E.G.R. lines from carburetor and in-
take manifold.
8. Disconnect exhaust pipe.
9. Remove six bolts attaching manifold assembly to
cylinder head and remove manifold and carburetor
as an assembly. Discard manifold gasket.
To separate intake and exhaust, manifold, remove
carburetor and four bolts using Tool J-23016, attach-
ing intake manifold to exhaust manifold. Always in-
stall a new manifold intermediate gasket when the
manifolds are separated.
Installation1. Install new manifold gasket and place manifold in
position.
2. Install manifold bolts. New manifold to cylinder
head gasket must be installed whenever a manifold
is removed.
3. When installing the manifold, start with the No.
1 and No. 2 bolts. See Figure 6A-16. Gradually
tighten both bolts until snug. Then continue with the
rest of the bolts in the sequence illustrated in Figure6A-16. Torque bolts to 33 lb. ft.
Figure 6A-16 Manifold
Bolt Tightening Sequence4. Connect parts removed in Steps 1 thru 8 above.
CYLINDER HEAD REMOVAL AND INSTALLATION
Removal1. Drain coolant from radiator and block. Loosen
drain plug on right side of engine to avoid coolant
entering into cylmder bores. Drain plug is located onthe right rear of cylinder block above oil pressure
switch.2. Remove hoses from thermostat housing. Collect
coolant as it contains anti-freeze.
3. Remove 6 intake and exhaust manifold attaching
bolts and swing assembly aside.
4. Remove spark plug wires from plugs.
5. Remove bracket bolt holding spark plug wires
away from cylinder head.
6. Remove rocker arm cover.
7. Remove 10 cylinder head bolts using 12 MM ser-
rated drive J-22915, and 2 cylinder head to timing
chain cover bolts with a 6MM hex head wrench. See
Figure 6A- 17.
Figure 6A-17 Serrated Bits
8. Remove three bolts attaching plate to front of
cylinder head.
9. Remove plastic screw from end of camshaft.
10. Remove 3 bolts attaching camshaft sprocket to
cylinder head. Slide sprocket off of camshaft and
remove head. Place head on bench supported at each
end by a block of wood to prevent damage to valves.
Installation1. Install in reverse procedure to removal, paying
particular attention to the following: