SSANGYONG KORANDO 1997 Service Manual PDF
Manufacturer: SSANGYONG, Model Year: 1997, Model line: KORANDO, Model: SSANGYONG KORANDO 1997Pages: 2053, PDF Size: 88.33 MB
Page 71 of 2053
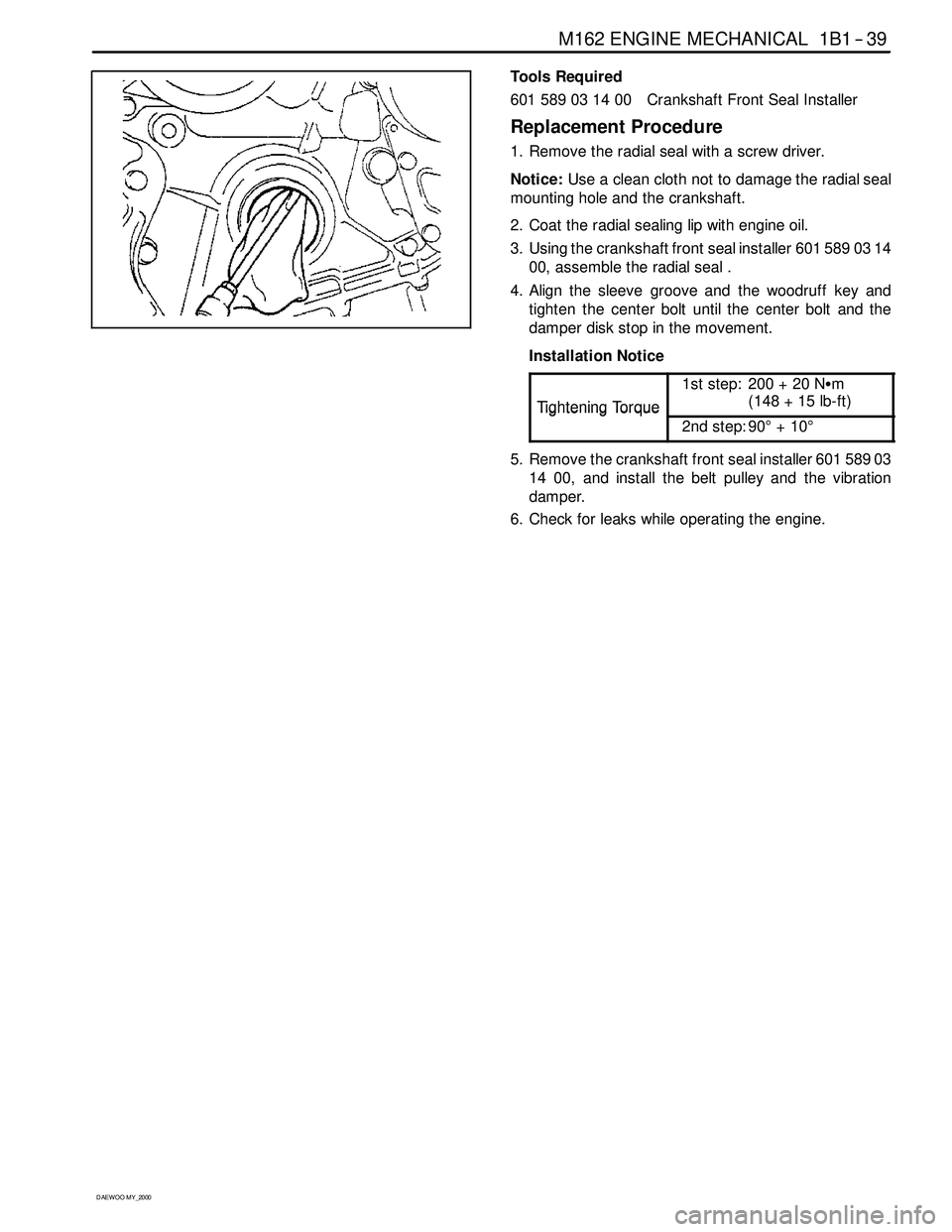
M162 ENGINE MECHANICAL 1B1 -- 39
D AEW OO M Y_2000
Tools Required
601 589 03 14 00 Crankshaft Front Seal Installer
Replacement Procedure
1. Remove the radial seal with a screw driver.
Notice:Use a clean cloth not to damage the radial seal
mounting hole and the crankshaft.
2. Coat the radial sealing lip with engine oil.
3. Using the crankshaft front seal installer 601 589 03 14
00, assemble the radial seal .
4. Align the sleeve groove and the woodruff key and
tighten the center bolt until the center bolt and the
damper disk stop in the movement.
Installation Notice
Ti
ghteningTo rque
1st step: 200 + 20 NSm
(148 + 15 lb-ft)
TighteningTorque
2nd step: 90°+10°
5. Remove the crankshaft front seal installer 601 589 03
14 00, and install the belt pulley and the vibration
damper.
6. Check for leaks while operating the engine.
Page 72 of 2053
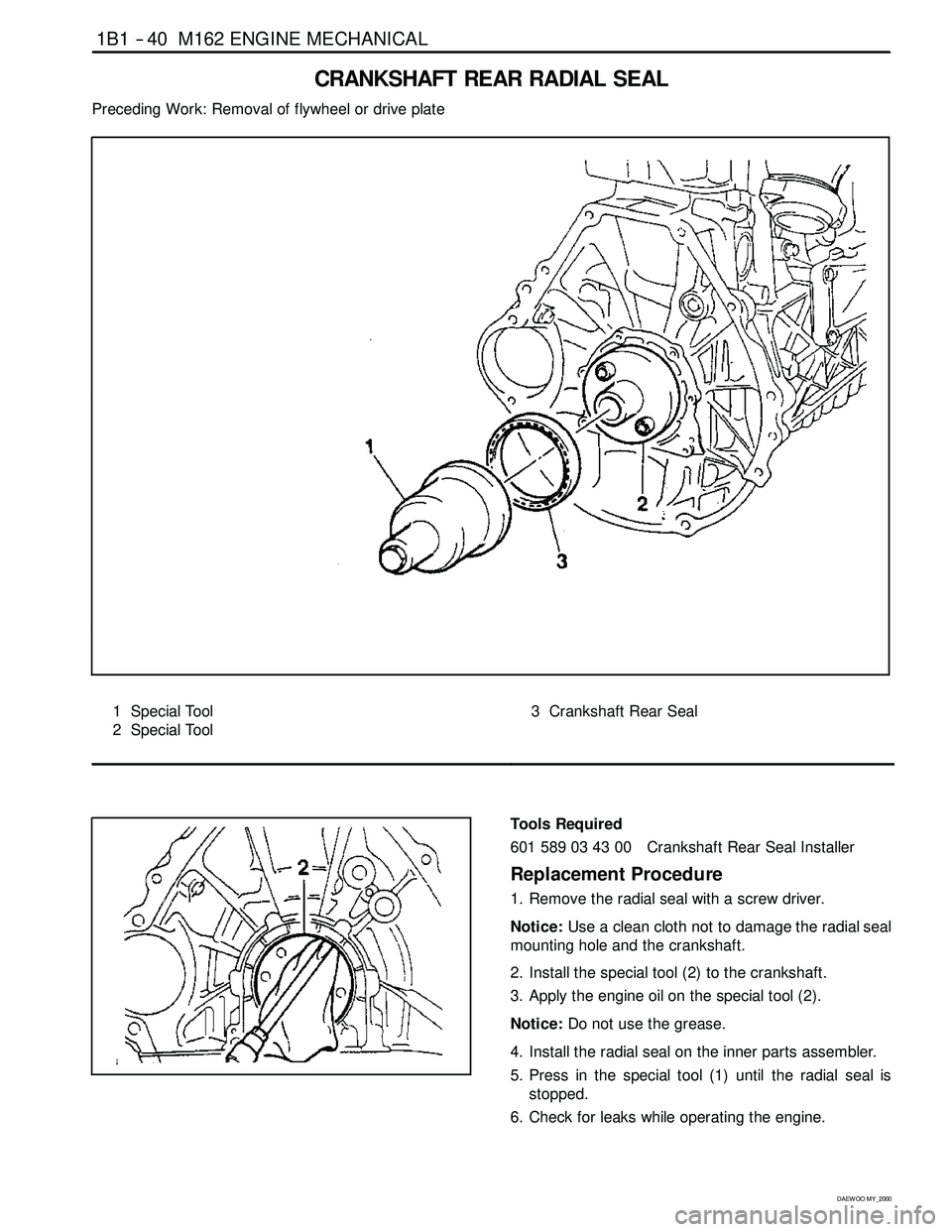
1B1 -- 40 M162 ENGINE MECHANICAL
D AEW OO M Y_2000
CRANKSHAFT REAR RADIAL SEAL
Preceding Work: Removal of flywheel or drive plate
1 Special Tool
2 Special Tool3 Crankshaft Rear Seal
Tools Required
601 589 03 43 00 Crankshaft Rear Seal Installer
Replacement Procedure
1. Remove the radial seal with a screw driver.
Notice:Use a clean cloth not to damage the radial seal
mounting hole and the crankshaft.
2. Install the special tool (2) to the crankshaft.
3. Apply the engine oil on the special tool (2).
Notice:Do not use the grease.
4. Install the radial seal on the inner parts assembler.
5. Press in the special tool (1) until the radial seal is
stopped.
6. Check for leaks while operating the engine.
Page 73 of 2053
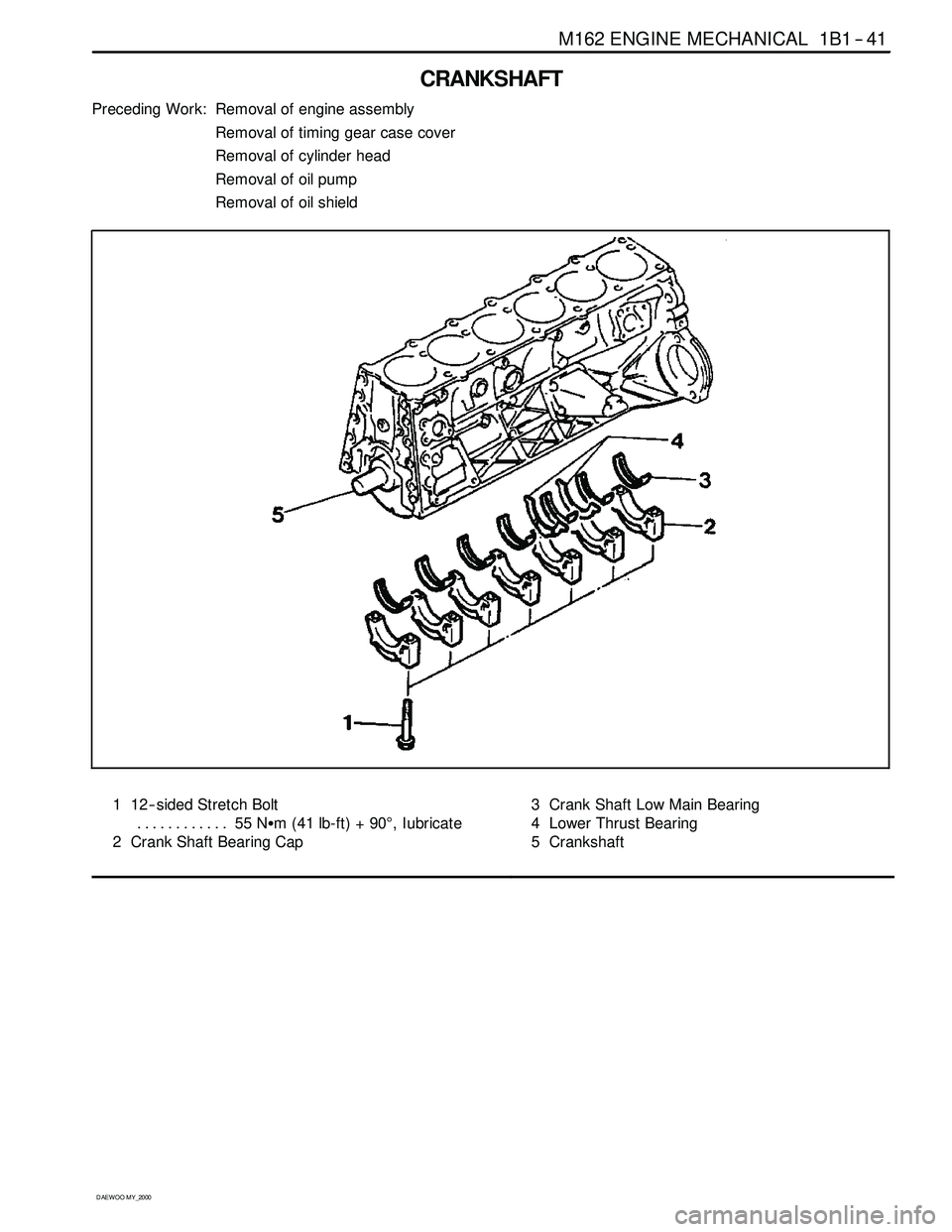
M162 ENGINE MECHANICAL 1B1 -- 41
D AEW OO M Y_2000
CRANKSHAFT
Preceding Work: Removal of engine assembly
Removal of timing gear case cover
Removal of cylinder head
Removal of oil pump
Removal of oil shield
1 12-- sided Stretch Bolt
55 NSm (41 lb-ft) + 90°, Iubricate ............
2 Crank Shaft Bearing Cap3 Crank Shaft Low Main Bearing
4 Lower Thrust Bearing
5 Crankshaft
Page 74 of 2053
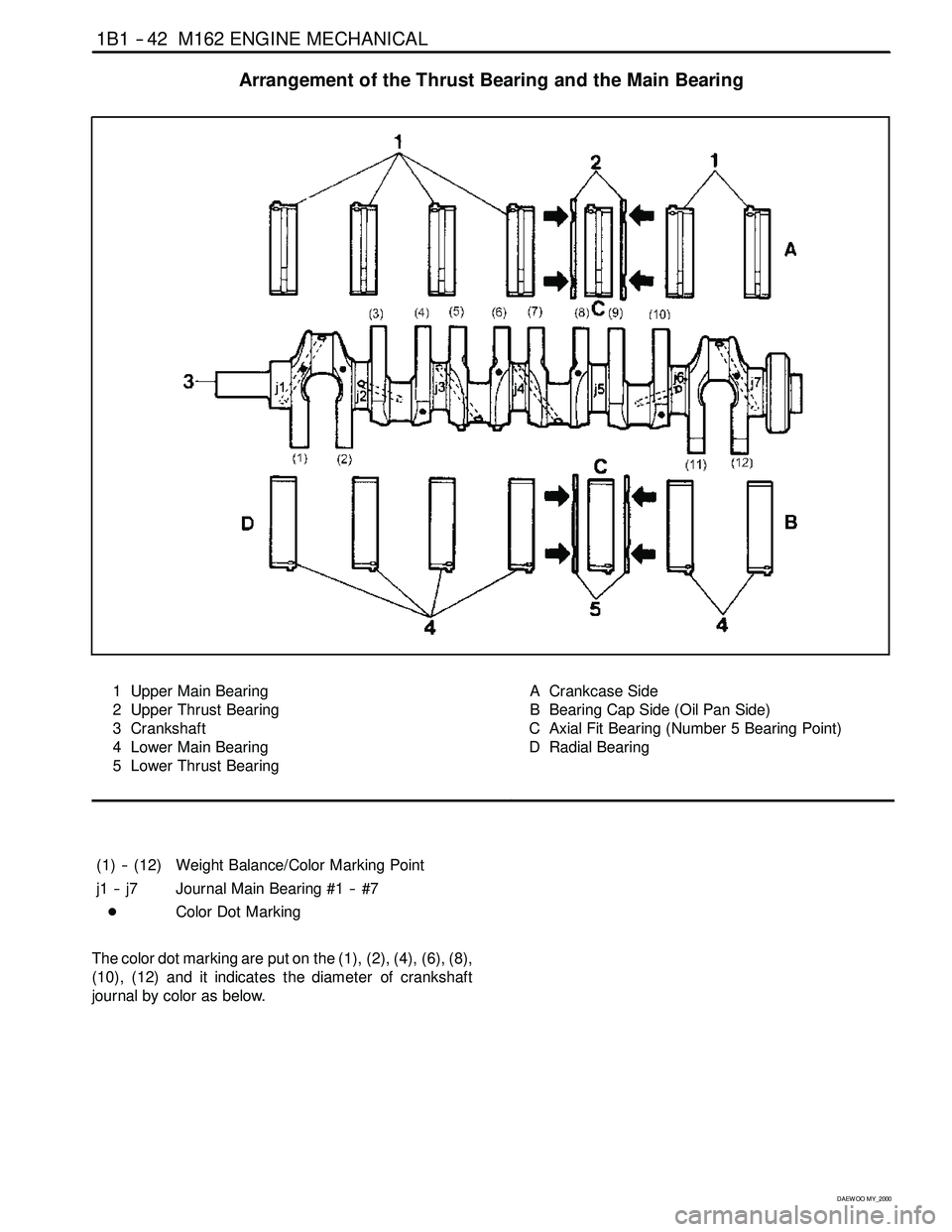
1B1 -- 42 M162 ENGINE MECHANICAL
D AEW OO M Y_2000
Arrangement of the Thrust Bearing and the Main Bearing
1 Upper Main Bearing
2 Upper Thrust Bearing
3 Crankshaft
4 Lower Main Bearing
5 Lower Thrust BearingA Crankcase Side
B Bearing Cap Side (Oil Pan Side)
C Axial Fit Bearing (Number 5 Bearing Point)
D Radial Bearing
(1) -- (12) Weight Balance/Color Marking Point
j1 -- j7 Journal Main Bearing #1 -- #7
DColor Dot Marking
The color dot marking are put on the (1), (2), (4), (6), (8),
(10), (12) and it indicates the diameter of crankshaft
journal by color as below.
Page 75 of 2053
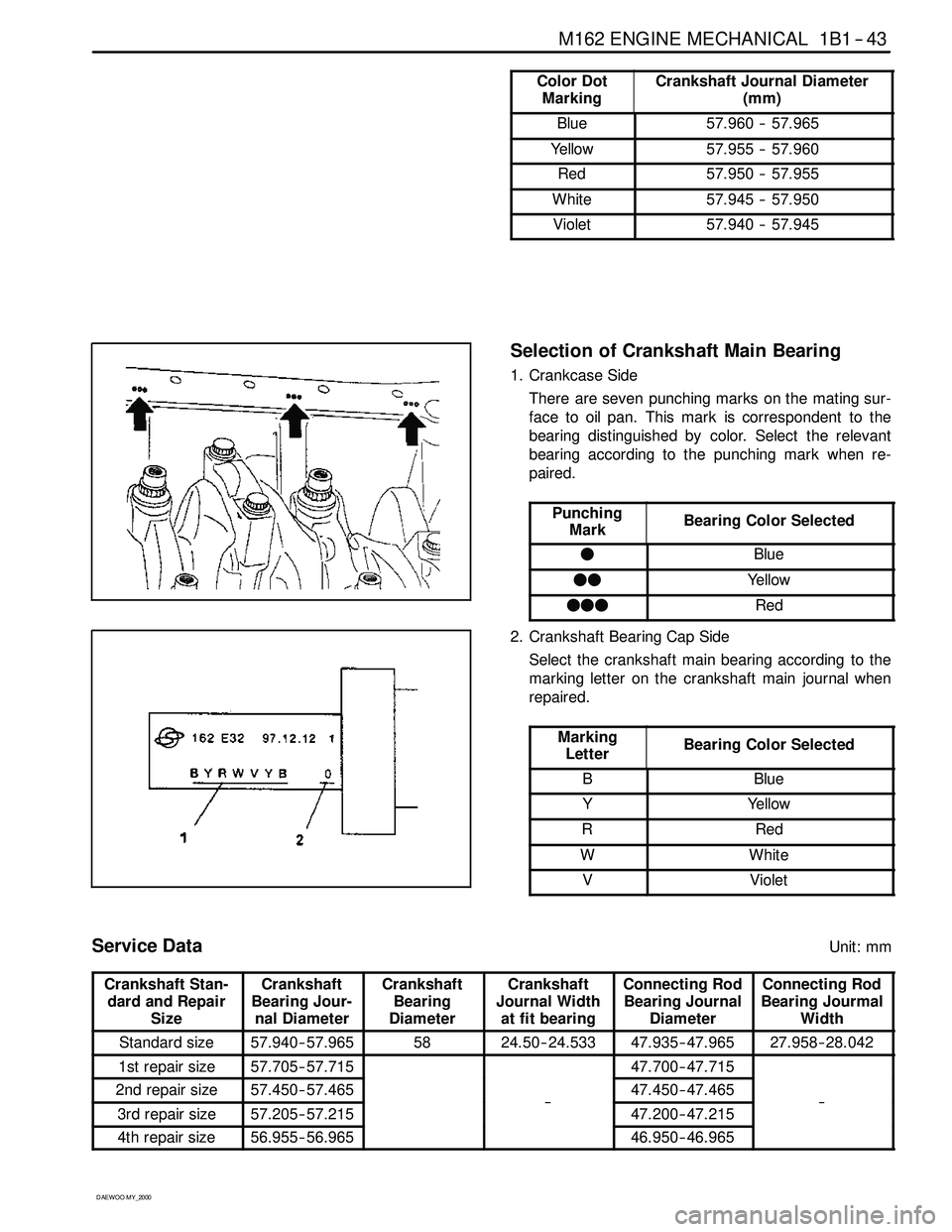
M162 ENGINE MECHANICAL 1B1 -- 43
D AEW OO M Y_2000
Color Dot
MarkingCrankshaft Journal Diameter
(mm)
Blue57.960 -- 57.965
Yellow57.955 -- 57.960
Red57.950 -- 57.955
White57.945 -- 57.950
Violet57.940 -- 57.945
Selection of Crankshaft Main Bearing
1. Crankcase Side
There are seven punching marks on the mating sur-
face to oil pan. This mark is correspondent to the
bearing distinguished by color. Select the relevant
bearing according to the punching mark when re-
paired.
Punching
Mark
Bearing Color Selected
FBlue
FFYellow
FFFRed
2. Crankshaft Bearing Cap Side
Select the crankshaft main bearing according to the
marking letter on the crankshaft main journal when
repaired.
Marking
Letter
Bearing Color Selected
BBlue
YYellow
RRed
WWhite
VViolet
Service DataUnit: mm
Crankshaft Stan-
dard and Repair
SizeCrankshaft
Bearing Jour-
nal DiameterCrankshaft
Bearing
DiameterCrankshaft
Journal Width
at fit bearingConnecting Rod
Bearing Journal
DiameterConnecting Rod
Bearing Jourmal
Width
Standard size57.940-- 57.9655824.50-- 24.53347.935-- 47.96527.958-- 28.042
1st repair size57.705-- 57.71547.700-- 47.715
2nd repair size57.450-- 57.46547.450-- 47.465
3rd repair size57.205-- 57.215--47.200-- 47.215--
4th repair size56.955-- 56.96546.950-- 46.965
Page 76 of 2053
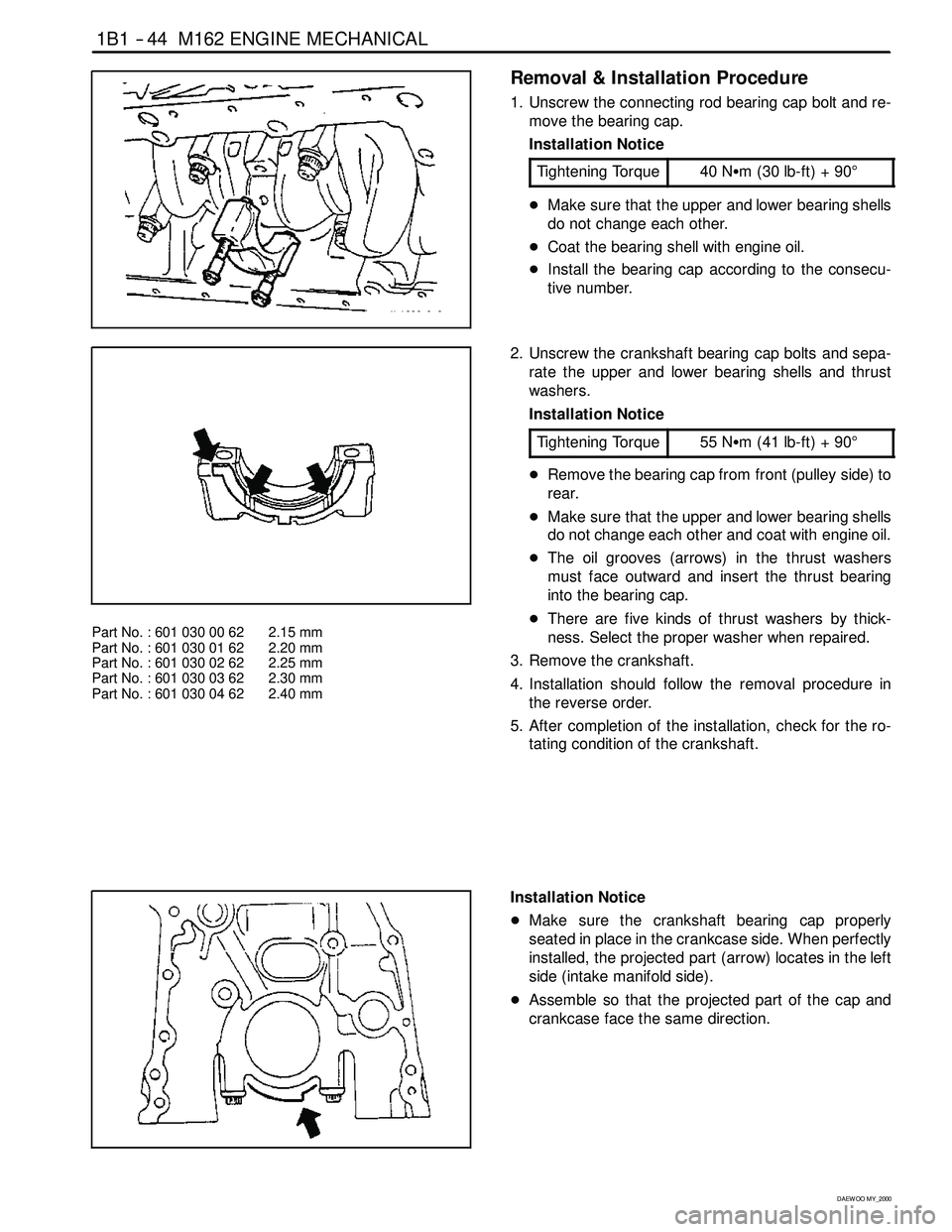
1B1 -- 44 M162 ENGINE MECHANICAL
D AEW OO M Y_2000
Removal & Installation Procedure
1. Unscrew the connecting rod bearing cap bolt and re-
move the bearing cap.
Installation Notice
Tightening Torque
40 NSm (30 lb-ft) + 90°
DMake sure that the upper and lower bearing shells
do not change each other.
DCoat the bearing shell with engine oil.
DInstall the bearing cap according to the consecu-
tive number.
Part No. : 601 030 00 62 2.15 mm
Part No. : 601 030 01 62 2.20 mm
Part No. : 601 030 02 62 2.25 mm
Part No. : 601 030 03 62 2.30 mm
Part No. : 601 030 04 62 2.40 mm
2. Unscrew the crankshaft bearing cap bolts and sepa-
rate the upper and lower bearing shells and thrust
washers.
Installation Notice
Tightening Torque
55 NSm (41 lb-ft) + 90°
DRemove the bearing cap from front (pulley side) to
rear.
DMake sure that the upper and lower bearing shells
do not change each other and coat with engine oil.
DThe oil grooves (arrows) in the thrust washers
must face outward and insert the thrust bearing
into the bearing cap.
DThere are five kinds of thrust washers by thick-
ness. Select the proper washer when repaired.
3. Remove the crankshaft.
4. Installation should follow the removal procedure in
the reverse order.
5. After completion of the installation, check for the ro-
tating condition of the crankshaft.
Installation Notice
DMake sure the crankshaft bearing cap properly
seated in place in the crankcase side. When perfectly
installed, the projected part (arrow) locates in the left
side (intake manifold side).
DAssemble so that the projected part of the cap and
crankcase face the same direction.
Page 77 of 2053
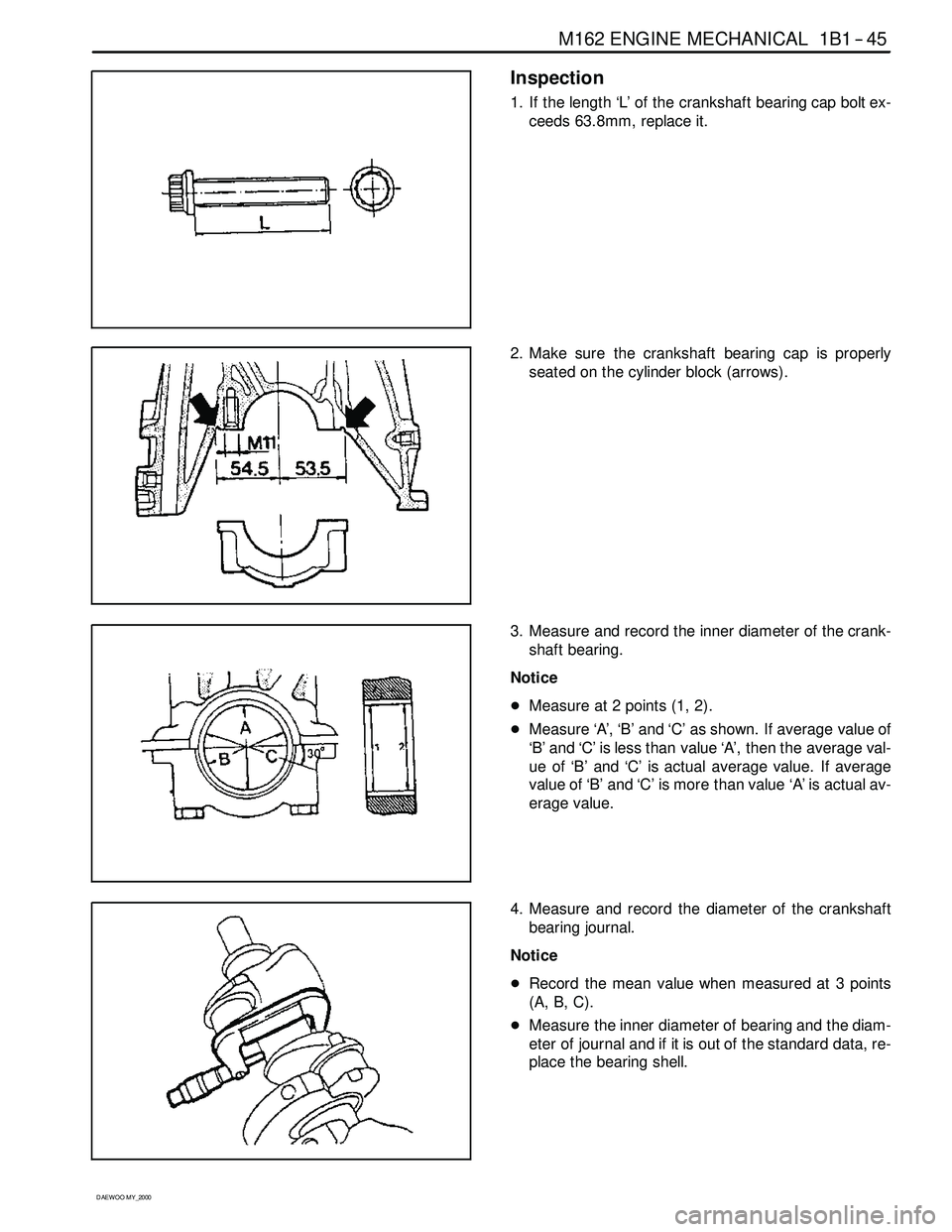
M162 ENGINE MECHANICAL 1B1 -- 45
D AEW OO M Y_2000
Inspection
1. If the length ‘L’ of the crankshaft bearing cap bolt ex-
ceeds 63.8mm, replace it.
2. Make sure the crankshaft bearing cap is properly
seated on the cylinder block (arrows).
3. Measure and record the inner diameter of the crank-
shaft bearing.
Notice
DMeasure at 2 points (1, 2).
DMeasure ‘A’, ‘B’ and ‘C’ as shown. If average value of
‘B’ and ‘C’ is less than value ‘A’, then the average val-
ue of ‘B’ and ‘C’ is actual average value. If average
value of ‘B’ and ‘C’ is more than value ‘A’ is actual av-
erage value.
4. Measure and record the diameter of the crankshaft
bearing journal.
Notice
DRecord the mean value when measured at 3 points
(A,B,C).
DMeasure the inner diameter of bearing and the diam-
eter of journal and if it is out of the standard data, re-
place the bearing shell.
Page 78 of 2053
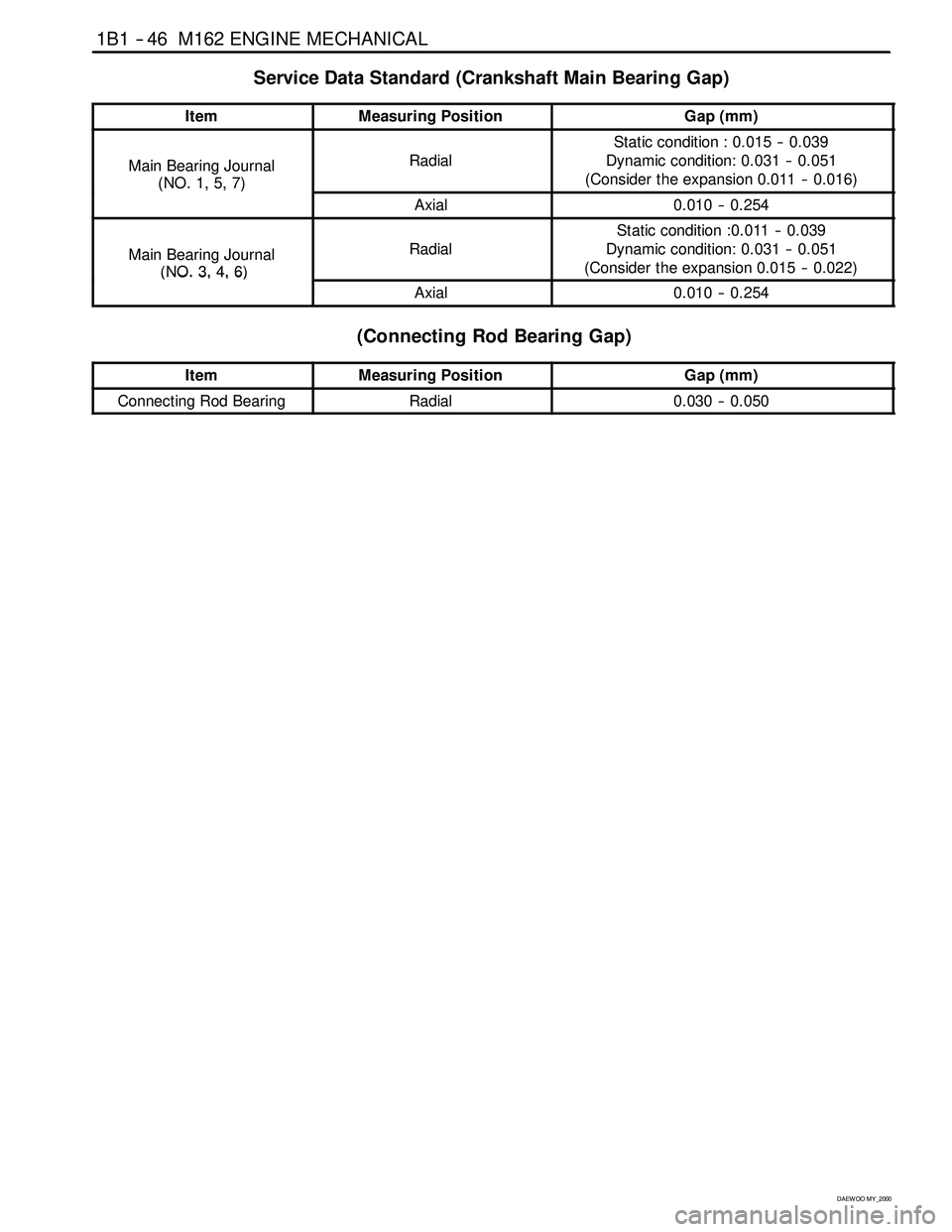
1B1 -- 46 M162 ENGINE MECHANICAL
D AEW OO M Y_2000
Service Data Standard (Crankshaft Main Bearing Gap)
ItemMeasuring PositionGap (mm)
Main Bearing Journal
(NO.1,5,7)
Radial
Static condition : 0.015 -- 0.039
Dynamic condition: 0.031 -- 0.051
(Consider the expansion 0.011 -- 0.016)
(NO.1,5,7)
Axial0.010 -- 0.254
Main Bearing Journal
(NO. 3,4,6)
Radial
Static condition :0.011 -- 0.039
Dynamic condition: 0.031 -- 0.051
(Consider the expansion 0.015 -- 0.022)
(NO.3,4,6)
Axial0.010 -- 0.254
(Connecting Rod Bearing Gap)
ItemMeasuring PositionGap (mm)
Connecting Rod BearingRadial0.030 -- 0.050
Page 79 of 2053
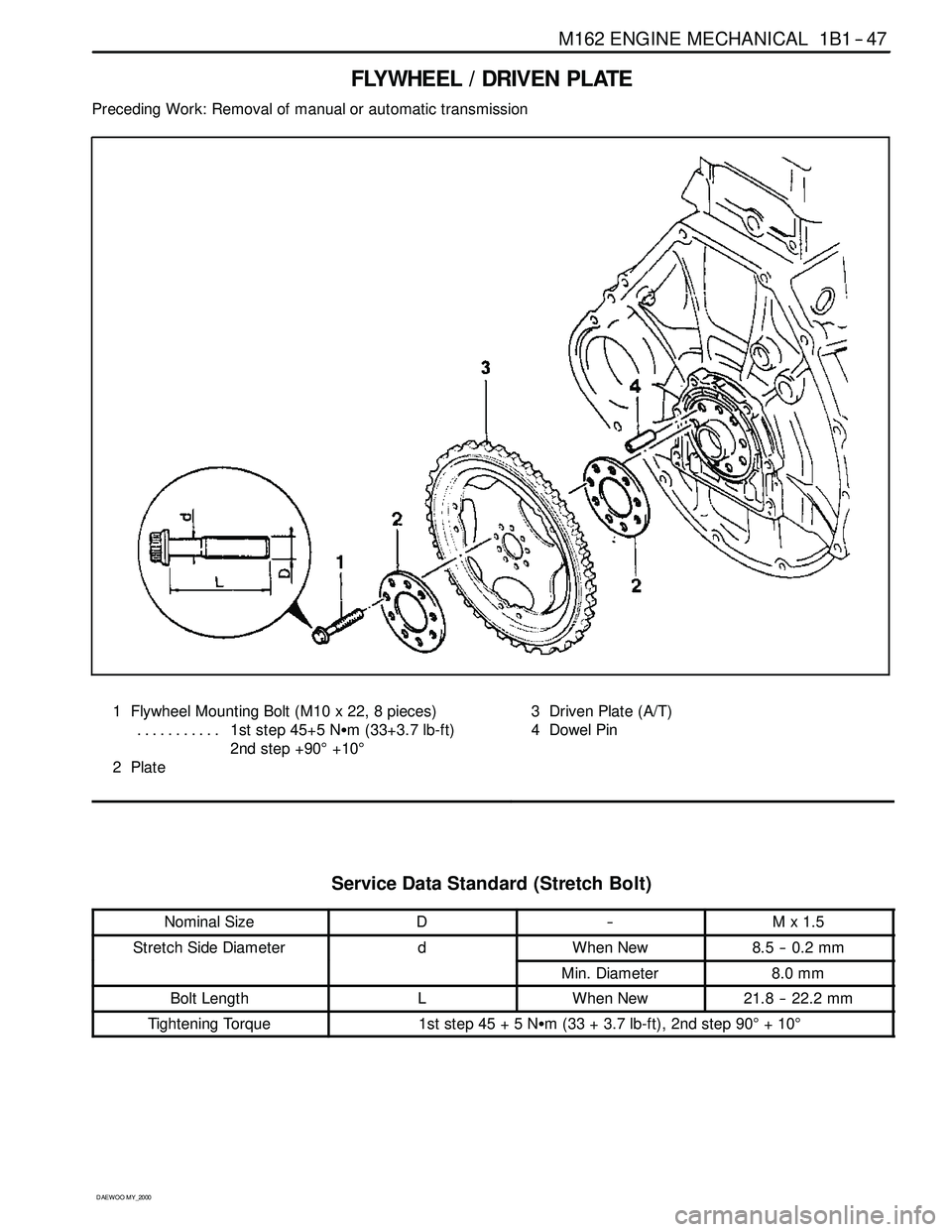
M162 ENGINE MECHANICAL 1B1 -- 47
D AEW OO M Y_2000
FLYWHEEL / DRIVEN PLATE
Preceding Work: Removal of manual or automatic transmission
1 Flywheel Mounting Bolt (M10 x 22, 8 pieces)
1st step 45+5 NSm (33+3.7 lb-ft) ...........
2nd step +90°+10°
2Plate3 Driven Plate (A/T)
4 Dowel Pin
Service Data Standard (Stretch Bolt)
Nominal SizeD--Mx1.5
Stretch Side DiameterdWhen New8.5 -- 0.2 mm
Min. Diameter8.0 mm
Bolt LengthLWhen New21.8 -- 22.2 mm
Tightening Torque1ststep45+5NSm (33 + 3.7 lb-ft), 2nd step 90°+10°
Page 80 of 2053
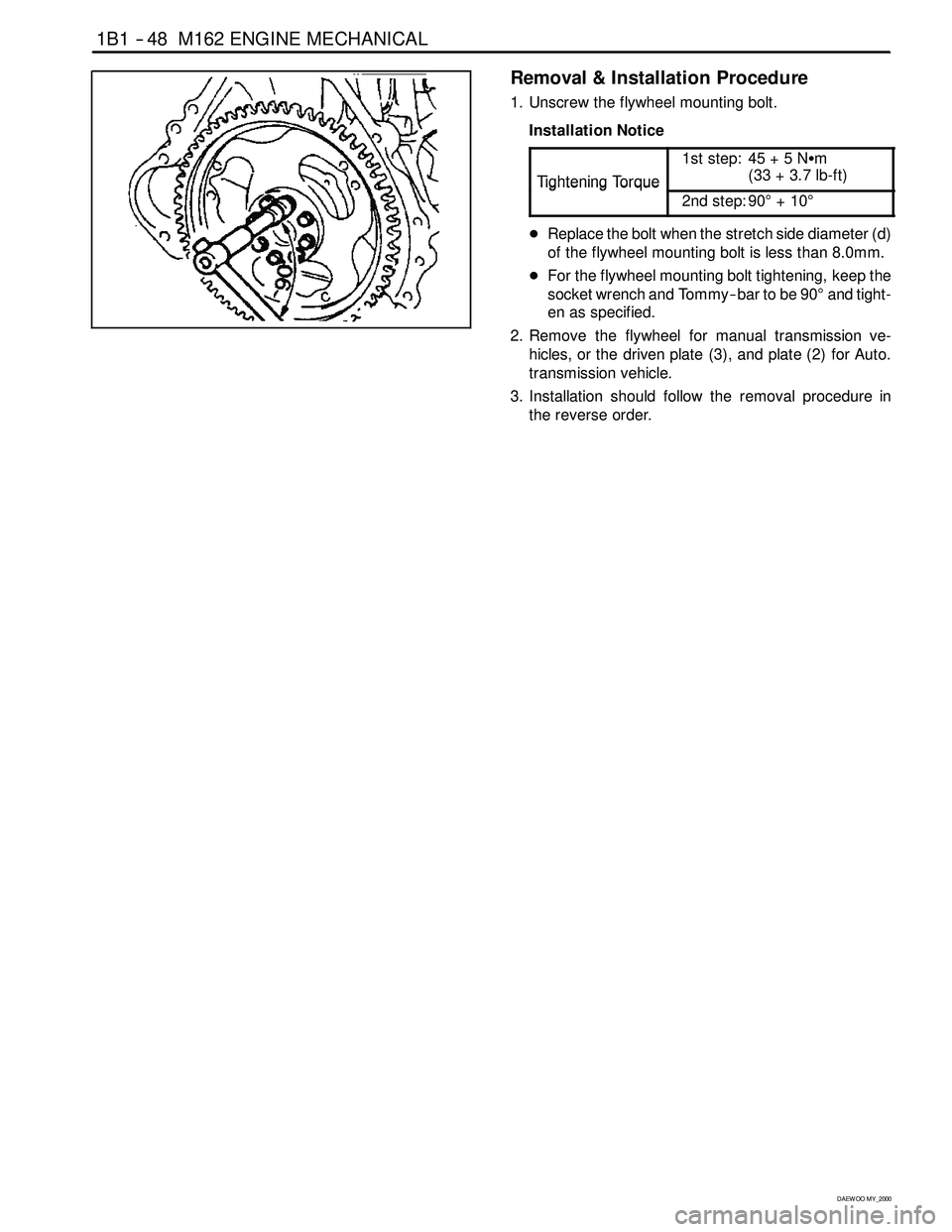
1B1 -- 48 M162 ENGINE MECHANICAL
D AEW OO M Y_2000
Removal & Installation Procedure
1. Unscrew the flywheel mounting bolt.
Installation Notice
Ti
ghteningTo rque
1st step: 45 + 5 NSm
(33+3.7lb-ft)
TighteningTorque
2nd step: 90°+10°
DReplace the bolt when the stretch side diameter (d)
of the flywheel mounting bolt is less than 8.0mm.
DFor the flywheel mounting bolt tightening, keep the
socket wrench and Tommy -- bar to be 90°and tight-
en as specified.
2. Remove the flywheel for manual transmission ve-
hicles, or the driven plate (3), and plate (2) for Auto.
transmission vehicle.
3. Installation should follow the removal procedure in
the reverse order.